辊道窑废气处理工艺
辊道窑的结构和工作原理
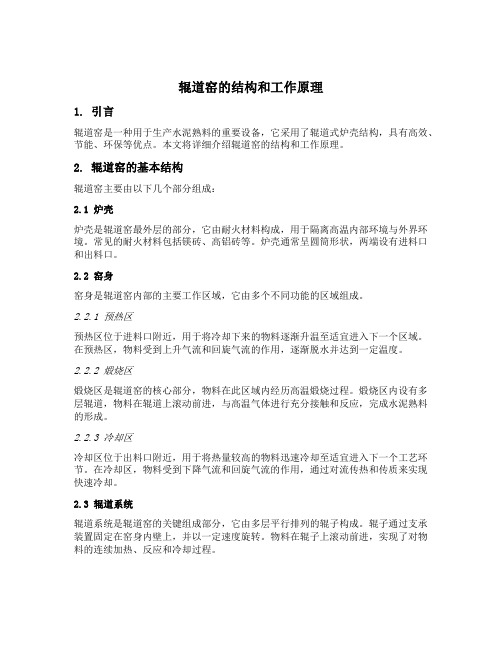
辊道窑的结构和工作原理1. 引言辊道窑是一种用于生产水泥熟料的重要设备,它采用了辊道式炉壳结构,具有高效、节能、环保等优点。
本文将详细介绍辊道窑的结构和工作原理。
2. 辊道窑的基本结构辊道窑主要由以下几个部分组成:2.1 炉壳炉壳是辊道窑最外层的部分,它由耐火材料构成,用于隔离高温内部环境与外界环境。
常见的耐火材料包括镁砖、高铝砖等。
炉壳通常呈圆筒形状,两端设有进料口和出料口。
2.2 窑身窑身是辊道窑内部的主要工作区域,它由多个不同功能的区域组成。
2.2.1 预热区预热区位于进料口附近,用于将冷却下来的物料逐渐升温至适宜进入下一个区域。
在预热区,物料受到上升气流和回旋气流的作用,逐渐脱水并达到一定温度。
2.2.2 煅烧区煅烧区是辊道窑的核心部分,物料在此区域内经历高温煅烧过程。
煅烧区内设有多层辊道,物料在辊道上滚动前进,与高温气体进行充分接触和反应,完成水泥熟料的形成。
2.2.3 冷却区冷却区位于出料口附近,用于将热量较高的物料迅速冷却至适宜进入下一个工艺环节。
在冷却区,物料受到下降气流和回旋气流的作用,通过对流传热和传质来实现快速冷却。
2.3 辊道系统辊道系统是辊道窑的关键组成部分,它由多层平行排列的辊子构成。
辊子通过支承装置固定在窑身内壁上,并以一定速度旋转。
物料在辊子上滚动前进,实现了对物料的连续加热、反应和冷却过程。
2.4 燃烧系统燃烧系统用于提供辊道窑所需的高温热源。
常见的燃料包括煤粉、石油焦、天然气等。
燃料经过燃烧设备进行燃烧,产生高温气体,通过窑头进入辊道窑内,为物料的加热提供能量。
2.5 排尘系统排尘系统用于处理辊道窑内产生的废气和粉尘。
它由除尘器、风机和排气管道等组成。
废气经过除尘器处理后,排放出去的废气符合环保要求。
3. 辊道窑的工作原理辊道窑的工作原理可以分为以下几个步骤:3.1 物料进料原料通过进料口被投入到预热区,并逐渐向下移动。
3.2 预热物料在预热区受到上升气流和回旋气流的作用,逐渐升温并脱水。
第三章辊道窑的排烟通风系统

图 32 煤烧隔焰辊道窑窑头排烟段窑体结构图 1排烟口 2水平支烟道 3支烟道闸板 4汇总烟道 5排湿孔
6隔焰板 7窑顶盖板砖 8清灰孔 9事故处理孔
2
图 33 油烧隔焰辊道窑排烟段窑体结构图 1排烟口 2排烟口闸板 3汇总烟道 4隔焰板 5排湿孔
为调节预热带升温制度,除上述采用调温喷风嘴的方式外,另一种就是在预热带除窑头 几节外全部装有烧嘴。例如意大利 WELKO 公司 FRW2000 型辊道窑,除如图 37 所示 3 节窑 前干燥带与第 4 节作排烟段外,其余每节窑体分别在两侧墙各设置 4 个烧嘴,上下方及对侧 均为错排,在同一断面上,一侧辊上设有烧嘴,另一侧则在辊下设有烧嘴,在断面上形成气 体循环,有利于断面温度均匀。这样的预热带结构与烧成带完全相同,故可统称燃烧带,它 包括了传统的预热带与烧成带。当然,预热带的烧嘴在使用上与烧成带有所不同,许多厂家 在实际使用时往往预热带前端的烧嘴未启用或仅开风管(尤其是上部烧嘴),实际上也是起到 了喷风降温作用。但不论如何,有了这些设置,就方便了升温制度的调节。
6事故处理孔 7隔焰板支柱 8挡火墙
3.1.2 明焰辊道窑的排烟
明焰辊道窑的燃烧火焰直接进入窑道内的辊道上下空间,对制品直接进行加热。为提高 热利用率,一般均采用集中排烟方式,即在窑头不远处的窑顶、窑底设置排烟口,烟气自烧 成带向预热带流动,至窑头排烟口抽出,经排烟总管、排烟机抽至烟囱排出室外。排烟口可 制成圆形,也可制成矩形。
排气孔的作用除排湿、排气外,还可起到辅助调节升温曲线的作用。预热带可能产生的 开裂缺陷主要是制品 200℃以前升温过急的干裂与 573℃左右的晶型转化危险区升温快而产生 的开裂。有学者研究,只要升温速率小于 100℃/min,即使在晶型转化温度危险区都不会产生 热应力开裂。所以,关键是控制干裂,解决干裂缺陷,一是控制入窑水分小于 1%,但实际上 较难做到,故要注意 200℃以前平稳升温。除了调节排烟支闸外,合理调节排气孔也能起到辅
辊道窑烧制陶瓷过程中NOx的排放分析及治理

O : 计算质量浓度 , 更为合理 , 计算结果见表 2 。 位 提 出, 其 生成机理 与影响 因素有 待进一 步研究 。 字 面上 本文以 N . 3 计算 结果分 析 理 解 是 由 于 原 材 料 中 含 氮 化 合 物 在 加 热 过 程 中 出 现 的 不 3
稳 定分解 . 主要受原材 料的成分影 响 。
摘 要: 针对 陶瓷行业 N O 排放 问题 , 笔者 选取 了作为 “ 陶都 ” 的佛 山 市 对 其 能 耗 、 数量较大 的辊道窑进行测试 及分析 , 得出
N 0 的排 放 数 据 , 进 而 分 析 及 提 出治 理方 法 。 分 析 得 出生 产 同 产 品. 的辊 道 窑 燃 用 天 然 气 较燃 用 其他 燃 料 生 成 的 N O 低, 选 用 天然 气 作 为 燃 料 有 利 于 降 低 N 0 排放 。
2 . 2 燃料 型 N o I 燃料 型 N O x是指 由化学结合在 燃料 中的有机 氮化物
热分解后 , 和氧化合 而生成 的 N O 。 燃 料 型 的 生 成 和 破 坏 比较 复 杂 ,简 单 来 说 燃 料 中氮 的 含 量 与 炉 内 过 剩 空 气 量
2 N 0 生成 来 源
燃 烧 生成 的 N O 主要 有 三个来 源 :热力 N O 、燃料
N O 及快速 N O 。 在 陶瓷行业 中 , 由于 原 料 的 特 殊 性 , 还 可 能 产生物料 N 0 。
是其形成 的主要影 响因素 。 在燃 料无法改善 的条件下 . 降
低过 剩空气 系数是 控制燃料 型 N O 转 化 与 生 成 的 最 主 要 措施圈 。
( 1 )
式 中: d —— 过剩空气 系数 ; 0 广 烟气 中氧 的百 分含量 ( %) 。 陶瓷行业 中, 氮氧化物排放物是 N O和 N O 的混合物 ,
废气处理工艺说明

本文汇聚以下工艺: 有机废气治理工艺、酸性气体治理工艺、国内常用烟气脱硫工艺、循环流化床锅炉脱硫工艺等。
旨在为工业企业节能提供参考,加快废气治理,还天以“蓝”装。
1、有机废气治理工艺干式过滤器先净化废气中漆雾的颗粒物及水份,避免二次污染及保护活性碳。
有机废气再通过吸附床,与活性炭接触,废气中的有机污染物被吸附在活性炭表面。
最后有机废气引入催化燃烧装置前,先通过预热器对废气进行先预热,再通过催化燃烧床内的电加热器加热废气生成无害的H2O 和CO2。
燃烧后放出大量的热量,可采用热交换器将高温尾气回收利用以减少预热能耗。
工艺特点:1. 适合处理常温、大风量、中、低浓度的有机废气;2. 不产生二次污染,设备投资及运行费用低;3. 吸附剂选用优质蜂窝状活性炭,具有使用寿命长、运行阻力低、净化效率高的特点;4. 催化低温分解,预热时间短,能耗低,催化剂使用寿命长,催化分解净化率高达97%;5. 设备运行稳定,可靠,活动件少,检修系统配备完善,操作维修方便;6. 整个运行过程中实现全自动化PLC控制,方便,可靠;7. 系统安全设施完善,配有阻火器,泄爆口,运行时出现的异常情况将报警并自动停机。
适用范围:在化工、印染、塑料、机械、仪表、电线电缆、漆装线、电机、发动机、汽车、摩托车、自行车、家电、印刷,磁带,制鞋等行业和部门所挥发或泄露出的有机废气与臭味、如苯类、醇类、酮类、醛类、脂类、醚类、烷烃类等温合有机废气的脱除、净化,均可采用本工艺。
2、酸性气体治理工艺酸性废气通过各支管将各设备、区域产生的废气收集,进入主风管,通过废气处理洗涤塔利用气体与液体间的接触,将气体中污染物传送到液体中,然后再将清洁之气体与被污染的液体分离净化,最后由防腐风机抽吸至活性炭吸附床吸附废气中的有害成分,达到达标排放的方法。
整个工艺根据现场要求可选择PP,玻璃钢等防腐材料,例如PP凤管、玻璃钢风机等。
设计工艺:废气→→PP风管→→废气处理洗涤塔→→防腐风机→→活性炭吸附床→→排放工艺特点:本工艺前后衔接合理而流畅,上一级处理单元都为下一级处理单元做了很好的铺垫,可使得整个系统长期处于正常的运行状态,保证处理效果,使废气能稳定达标排放。
辊道窑能耗分析及排气能量回收系统性能

排气能量回收系统性能优化
优化换热面积
在排气能量回收系统中,换热面积的大小直接影响到系统的 传热效果。优化换热面积可以提高系统的传热效率,从而提 高系统的性能。
采用高效传热材料
采用高效传热材料可以提高系统的传热效率,从而提高系统 的性能。例如,采用导热系数高的材料作为传热介质可以加 快热量传递的速度。
感谢您的观看
THANKS
03
提升方案
针对以上问题,提出了以下提升方案 :优化回收系统的设计,提高能量的 回收率;加强设备的维护和检修,确 保系统的稳定运行。
某水泥厂辊道窑与排气能量回收系统结合的应用案例
水泥厂辊道窑与排气能量回收系统结合的特点
该水泥厂的辊道窑与排气能量回收系统结合使用,具有较高的能源利用效率和环境保护效益。
系统,降低电能消耗。
某钢铁厂排气能量回收系统性能提升实践
01
钢铁厂排气能量回收 系统现状
该钢铁厂的排气能量回收系统在实际 运行中存在一些问题,如能量回收率 不高、系统稳定性较差等。
02
问题分析
通过对现有排气能量回收系统的运行 数据进行深入分析,发现其主要存在 的问题是回收系统的设计不合理以及 运行维护不到位。
结合方式与优势
该水泥厂采用的辊道窑与排气能量回收系统结合的方式是,将辊道窑的高温排气引入能量回收系统进行余热回收,同时将回收的能量用于生产过程,降低了能 源消耗。
应用效果
通过实际运行数据可以看出,该水泥厂的辊道窑与排气能量回收系统结合后,能源利用效率得到了显著提升,同时产品的质量和产量也得到了较大幅度的提 高。
将辊道窑使用前后的能耗数据进行对比分 析,以评估节能效果。
2. 环境影响评估
3. 生产效率评估
废气处理工艺流程

废气处理工艺流程废气处理工艺流程是指对工业生产过程中产生的废气进行处理,以减少对环境的污染和对人体健康的危害。
废气处理工艺流程的设计和实施对于保护环境、维护生态平衡具有重要意义。
下面将介绍废气处理工艺流程的一般步骤和主要技术。
首先,废气处理工艺流程的第一步是废气的收集。
工业生产过程中产生的废气需要通过管道系统被收集起来,以便进行后续的处理。
收集系统的设计需要考虑到废气的种类和产生地点,确保所有的废气都能够被有效地收集起来。
接下来,收集起来的废气需要进行预处理。
预处理的主要目的是去除废气中的颗粒物、油烟、有害气体等。
常见的预处理方法包括过滤、吸附、冷凝等。
通过预处理,废气中的有害成分可以得到有效的去除,为后续的处理工作创造条件。
然后,经过预处理的废气需要进行主要处理工艺。
主要处理工艺包括物理方法、化学方法和生物方法。
物理方法主要包括吸附、吸附、膜分离等,化学方法主要包括氧化、还原、中和等,生物方法主要包括生物滤池、生物塔等。
根据废气的成分和排放标准的要求,选择合适的处理工艺进行处理。
最后,经过主要处理工艺处理后的废气需要进行尾气处理。
尾气处理是指对处理后的废气进行最终的净化和排放。
常见的尾气处理方法包括吸收、吸附、膜分离等。
通过尾气处理,废气中的残留有害成分可以得到进一步的清除,确保排放的废气符合国家相关的排放标准。
综上所述,废气处理工艺流程包括废气收集、预处理、主要处理和尾气处理四个步骤。
通过科学合理的工艺流程设计和技术实施,可以有效地减少工业生产过程中产生的废气对环境和人体健康造成的危害,实现可持续发展的目标。
希望本文的介绍对于废气处理工艺流程的理解和实践有所帮助。
带尾气处理装置的燃气辊道窑炉的制作技术

本技术新型属于烧结设备技术领域,涉及一种带尾气处理装置的燃气辊道窑炉,预热段的顶部设有与尾气处理装置的进气管连接的排烟支管,烧成段内设有与燃气管相连的烧嘴,烧嘴的一侧设有助燃风管,冷却段内设有冷风管,冷却段的顶部设有抽热风管,抽热风管通过抽热风机与换热器的内进气口连接;进气管与窑炉顶部的排烟支管连接,进气管上设有风机,进气管与燃烧室的进气口相连,燃烧室的出气口与换热器的内进气口相连,换热器的内出气口与排气管相连,换热器的外出气管上设有引风机二;燃烧室内的烧嘴与燃气管连接;排气管上设有排烟蝶阀;对窑炉预热段和降温段尾气中的热量实现回收利用,节约能源;尾气处理设备简单,操作方便,安全可靠。
技术要求1.一种带尾气处理装置的燃气辊道窑炉,包括窑体包括依次相连的预热段(1)、烧成段(2)和冷却段(3),所述预热段(1)的顶部设有排烟支管(12),排烟支管(12)与尾气处理装置的进气管(41)连接,排烟支管(12)上设有调节阀(11);所述烧成段(2)内设有烧嘴(21),烧嘴(21)与燃气管一(22)相连,每个烧嘴(21)的一侧设有助燃风管,助燃风管与助燃风机(23)相连;所述冷却段(3)内设有冷风管(31),冷风管(31)与冷风机相连,冷却段(3)的顶部设有抽热风支管(38),抽热风支管(38)汇集于抽热风管(37),其特征在于:抽热风管(37)通过抽热风机(34)与换热器的内进气口连接;所述尾气处理装置,包括进气管(41)、燃烧室(47)、换热器(412)和排气管(45),所述进气管(41)与窑炉预热段的排烟支管(12)连接,进气管(41)上设有风机(410),进气管(41)与燃烧室(47)的进气口相连,进气管(41)与燃烧室(47)进气口之间设有主调节阀(42);所述燃烧室(47)的出气口与换热器(412)的内进气口相连,换热器(412)的底部设有排水口(415),换热器(412)的内出气口通过引风机(413)与排气管(45)相连,换热器(412)的外出气管(414)上设有引风机二(411);燃烧室(47)内设有烧嘴(43),烧嘴(43)与燃气管(48)连接;燃气管(48)的一侧设有助燃管;排气管(45)上设有排烟蝶阀。
辊道窑废气处理-技术要求

辊道窑废气处理技术要求一、废气排放相关参数此次处理的废气为1#厂房西南角16条窑炉的废气,废气参数如下:1、其中12条窑炉单台废气排放量为2100m³/h,另外4条窑炉单台废气排放量为8000 m³/h;2、正常废气排放温度约200℃,异常情况300℃,喷淋塔相关设计按最高温度设计。
3、废气经喷淋后的废水PH值约12-13。
4、废气相关元素浓度见下表:二、废气处理要求:1、废气处理方式:立式喷淋塔处理;2、喷淋塔数量:西侧8条窑炉废气合并后由1套喷淋塔处理,相对东侧8条窑炉废气合并后由1套喷淋塔处理,共2套喷淋塔;3、材质要求:喷淋塔与水接触部分采用304不锈钢,颜色为不锈钢本色;其余支架、排气管道、水管均使用碳钢,涂银灰色油漆;4、每套喷淋塔1条排气管道,排气管道高度为26米,可在厂房立柱上固定,但在墙面穿洞后需进行防水修补处理;排气管道旁需安装检修爬梯,爬梯涂黄色油漆;5、喷淋系统设计时需考虑废水的冷却,并设计冷却塔,经冷却后的废水温度应低于50℃。
6、喷淋塔采用自来水供水,需具备自动补水,并安装手动阀。
7、16条窑炉每条窑炉排气管道上均需安装单向阀及手动流量调节阀(可使用插板阀)。
8、喷淋塔水槽需设置沉淀槽,喷淋后的水经沉淀后再最后进入水泵槽内;沉淀槽上应设置人孔以方便废渣的清理;9、经喷淋处理后的废气排放需符合《大气污染物综合排放标准》(GB16297-1996)表 2 中二级标准。
三、供货范围:1. 废气处理系统:由喷淋塔、供水泵、排气风机、自动控制等组成,系统至少应包括以下部分:1.1 喷淋塔主体:结构合理,方便检修,填充物及塔内各部件均应能耐高温;1.2 供水泵:供水泵应能耐碱性及80℃以下温度;1.3 排气风机:排气风机需具备变频功能,能根据废气进气量的大小调节引风量。
1.4 排气管道:包括室外废气汇集管道(并与现有各支管连接)、经喷淋处理后排向房顶的26米高排气管道(并制作安装检修爬梯);1.5 供水管及废水排放管:由南侧自来水供水井内连接管道并安装手动阀,连接至喷淋塔;由喷淋塔连接废水排放管道至南侧工业废水井内;1.6 废气管道阀门:每条窑炉的排气管道均需各安装1个单向阀及1个插板阀,共16条窑炉;1.7成套电气柜:所有用电设备(泵,电机)共用一台电气柜。