产品表面起泡不良8D分析报告2017-3-7
8d分析报告
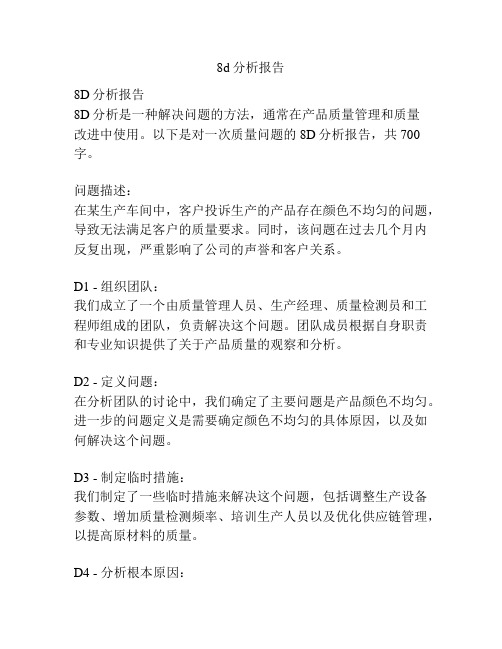
8d分析报告8D分析报告8D分析是一种解决问题的方法,通常在产品质量管理和质量改进中使用。
以下是对一次质量问题的8D分析报告,共700字。
问题描述:在某生产车间中,客户投诉生产的产品存在颜色不均匀的问题,导致无法满足客户的质量要求。
同时,该问题在过去几个月内反复出现,严重影响了公司的声誉和客户关系。
D1 - 组织团队:我们成立了一个由质量管理人员、生产经理、质量检测员和工程师组成的团队,负责解决这个问题。
团队成员根据自身职责和专业知识提供了关于产品质量的观察和分析。
D2 - 定义问题:在分析团队的讨论中,我们确定了主要问题是产品颜色不均匀。
进一步的问题定义是需要确定颜色不均匀的具体原因,以及如何解决这个问题。
D3 - 制定临时措施:我们制定了一些临时措施来解决这个问题,包括调整生产设备参数、增加质量检测频率、培训生产人员以及优化供应链管理,以提高原材料的质量。
D4 - 分析根本原因:通过观察和数据分析,我们发现颜色不均匀的主要原因是生产设备的不稳定性。
我们的设备在生产过程中存在一些变量(如温度、压力等)失控的问题,导致产品颜色不均匀。
D5 - 制定长期纠正措施:为了解决该问题,我们决定进行以下长期纠正措施:1. 更新生产设备,以提高稳定性和可控性。
2. 增加设备的自动化程度,减少人工操作的影响。
3. 增加对设备进行定期维护和保养的频率,确保设备始终处于最佳状态。
4. 培训生产人员,提高他们对设备操作和质量控制的认识和能力。
D6 - 实施纠正措施:根据制定的长期纠正措施,我们开始升级生产设备,并进行相应的测试和调整,以确保设备的稳定性和可控性。
同时,我们还加强了对生产人员的培训,并建立了定期维护和保养计划。
D7 - 观察结果:在纠正措施实施后,我们对产品进行了多次质量检测,并获得了一致的良好结果。
产品颜色均匀且符合客户的要求,解决了颜色不均匀的问题。
D8 - 预防措施:为了避免类似问题的再次发生,我们制定了以下预防措施:1. 进一步加强对生产设备的监控和维护,及时发现和解决潜在问题。
外观不良8D报告
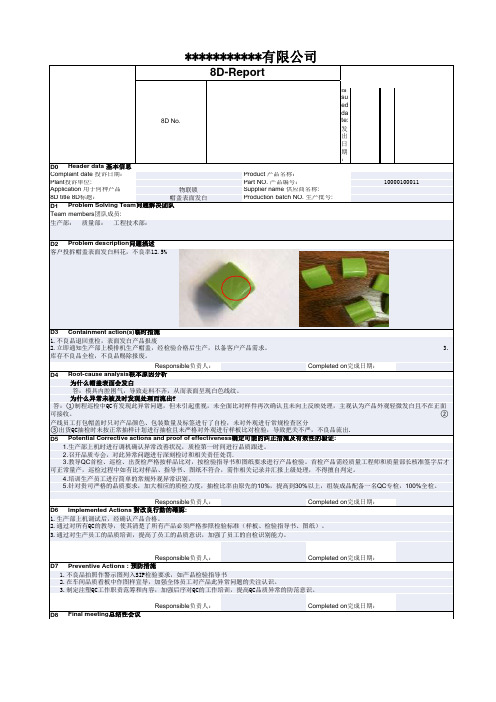
Is su ed da te:发出日期:D0D1D2D3D4D5D6D7D81.不良品退回重检,表面发白产品报废2.立即通知生产部上模排机生产帽盖,经检验合格后生产,以备客户产品需求。
3.库存不良品全检,不良品赐除报废。
客户投拆帽盖表面发白料花,不良率12.5%8D No.Final meeting 总结性会议Preventive Actions : 预防措施 1.不良品拍照作警示图列入SIP检验要求,如产品检验指导书2.在车间品质看板中作图样宣导,加强全体员工对产品此异常问题的关注认识。
3.制定注塑QC工作职责范筹和内容,加强后序对QC的工作培训,提高QC品质异常的防范意识。
Responsible 负责人:Completed on 完成日期:1.生产部上机调试后,经确认产品合格。
2.通过对所有QC的教导,使其清楚了所有产品必须严格参照检验标准(样板、检验指导书、图纸)。
3.通过对生产员工的品质培训,提高了员工的品质意识,加强了员工的自检识别能力。
Responsible 负责人:Completed on 完成日期:Responsible 负责人:Completed on 完成日期:Implemented Actions 對改良行動的確認: 1.生产部上机时进行调机确认异常改善状况,质检第一时间进行品质跟进。
2.召开品质专会,对此异常问题进行深刻检讨和相关责任处罚.3.教导QC 首检、巡检、出货检严格按样品比对,按检验指导书和图纸要求进行产品检验。
首检产品需经质量工程师和质量部长核准签字后才可正常量产,巡检过程中如有比对样品、指导书、图纸不符合,需作相关记录并汇报上级处理,不得擅自判定。
4.培训生产员工进行简单的常规外观异常识别。
5.针对贵司严格的品质要求,加大相应的质检力度,抽检比率由原先的10%,提高到30%以上,组装成品配备一名QC 专检,100%全检。
Root-cause analysis 根本原因分析 为什么帽盖表面会发白答:模具内腔困气,导致走料不齐,从而表面呈现白色线纹。
品质8D报告

品质8D报告一、问题描述:在企业的生产过程中,出现了以下品质问题:某批次产品出现严重的外观缺陷,导致产品无法出货,给企业带来了经济损失以及声誉损害。
经初步分析,问题出现的原因可能是在生产过程中存在某种工艺不符合标准,需要进一步调查和解决。
二、问题分析:1. 客户投诉:我们收到了多起客户的投诉,反映产品外观存在明显的缺陷,无法满足其需求。
2. 制程分析:通过对生产过程进行分析,发现某个工序的操作和控制不严谨,导致产品出现外观缺陷。
3. 数据分析:通过对相关数据的统计和分析,发现该批次产品的外观缺陷率远高于合格率,表明存在严重的品质问题。
三、紧急行动:为了尽快解决该问题,我们立即采取了以下紧急行动:1. 停产:首先,我们立即停止了该批次产品的生产,确保不会继续生产出具有外观缺陷的产品。
2. 问题隔离:我们将已生产的有缺陷产品进行隔离,确保不会流入销售流通渠道。
3. 调查组成立:我们组成了专门的调查组,由质量部门、生产部门和工艺工程师等组成,负责深入调查问题产生的原因。
四、问题根本原因分析:经过深入调查和分析,我们得出以下问题根本原因:1. 工艺不合理:某个工序的工艺参数没有正确设定,导致产品出现外观缺陷。
2. 人员操作不规范:在该工序的操作过程中,操作人员没有按照标准操作规程进行操作,导致产品品质受损。
五、问题解决措施:为了彻底解决该问题,我们制定了以下解决措施:1. 工艺优化:我们对该工序的工艺进行了再优化,确保工艺参数的正确设定,减少产品出现外观缺陷的可能性。
2. 培训与管理:我们将对操作人员进行培训,加强对操作规程的宣传和培训,确保操作人员能够规范操作,提升产品品质。
六、措施实施及效果评估:1. 工艺优化:我们在工艺参数设定上进行了调整,确保符合标准工艺要求。
经过多批次的生产验证,发现外观缺陷明显减少,产品品质得以提升。
2. 培训与管理:我们对操作人员进行了培训,加强了对操作规程的管理。
在后续生产中,通过严格的检查和培训反馈,发现操作人员的操作规范性明显提高,产品品质得到有效控制。
产品质量问题8D分析报告(模板)

供应商名称问题来源零件图号
问题负责人
小组成员
批准人完成时间结果确认
①②
完成时间结果确认
人员设备
物料方法环境测量
完成时间
结果确认
①完成时间结果确认
①完成时间结果确认
②完成时间结果确认
①
首台发动机号:
应用5W1H的分析方法,对可能产生问题的进行分析
确认整改件是否需要试装
样件-小批-批量试装①
①
②固化改进措施审视同类产品/同类工艺是否存在类似的隐患D8:整改闭环
如何实施清晰识别整改件(含批次信息/外观标识等)
——
①确认过程能力得到提升
②确认PPAP资料得到更新(含FMEA、控制计划等)
③确认相关人员得到质量培训
D6:纠正措施验证
验证结果纠正措施已经被验证了吗? 如何验证的?通过统计证据/假设检验来验证。
要求对问题零件的纠正措施逐
个验证。
D7:预防措施
如何实施————
D5:永久纠正措施
改进措施(针对故障主因的整改、数据说话)
对问题发生的原因进行改进
D4:根本原因
排查结果D3:临时遏制措施如何实施D1:小组成员
编制人D2:问题描述
问题图片
产品质量问题8D分析报告
通知编号零件名称需试装
首台发动机号:
确认整改件是否需要试装
直接切换②不需试装。
如何用8D方法分析解决产品质量问题

一、8个基本原则(8 Discipline ) 1、D1建立分析解决问题小组 2、D2描述问题 3、D3实施并验证临时措施 4、D4确定并验证根本原因 5、D5选择及验证永久纠正措施 6、D6执行及验证永久纠正措施 7、D7预防再发生措施 8、D8团队激励(或客户确认效果)
第八步骤: D8团队激励(客户确认效果) 目的: 承认小组(或团队)的集体努力,对小组 工作进行总结并祝贺。 关键要点: 有选择的保留重要文档 ; 流览小组工作,将心得形成文件 ; 了解小组对解决问题的集体力量,及对解 决问题作出的贡献 ; 必要的物质、精神奖励。
第八步骤: D8客户确认效果
目的: 满足客户长远的需要,保持公司长远的利 益! 关键要点: 通报改进结果 请求客户确认 了解客户意见 跟踪改进效果
结 束 语
8D方法的运用,其实不仅在工程分析上,您 工作上,生活上碰到的很多问题,不妨也用 8D方法的逻辑来思考解决,也会取得较好的 解决办法。 而针对8D方法的运用,我公司编制了《8D 问题解决报告》的标准格式,在今后的实际 工作中和质量问题的分析解决中将加以运 用,。 要求供方对我公司反馈的质量问题也要用8D 方法分析解决,并以《8D问题解决报告》的 形式回复。
第一步骤:D1建立分析解决问题小组
若问题无法独立解决或不能彻底解决,由根据问 题可能涉及范围的部门和人员组成质量改进小组 (或团队)。 主要应包括研发设计人员、质量工程师、采购工 程师、生产一线工艺员等组成。 而小组(或团队)的成员必须有能力执行或采取 可能提出的纠正或预防措施, 例如调整机器参数,调整制造加工工艺参数、或 懂得改变加工条件、监督现场管理等。
第一步骤:D1建立分析解决问题小组
质量分析8d报告案例
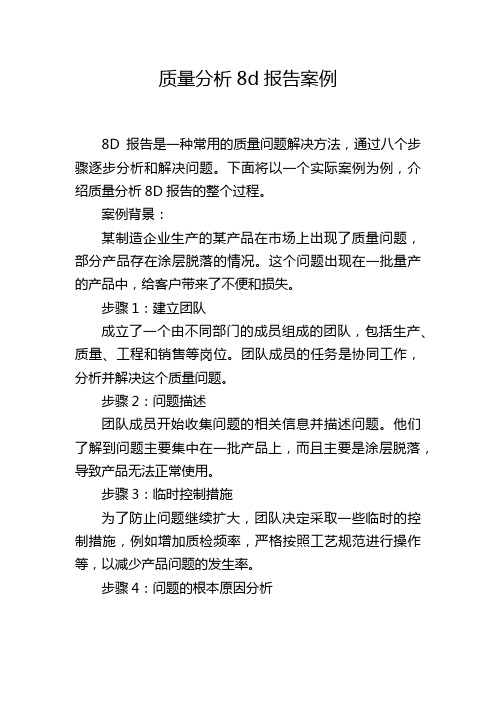
质量分析8d报告案例8D报告是一种常用的质量问题解决方法,通过八个步骤逐步分析和解决问题。
下面将以一个实际案例为例,介绍质量分析8D报告的整个过程。
案例背景:某制造企业生产的某产品在市场上出现了质量问题,部分产品存在涂层脱落的情况。
这个问题出现在一批量产的产品中,给客户带来了不便和损失。
步骤1:建立团队成立了一个由不同部门的成员组成的团队,包括生产、质量、工程和销售等岗位。
团队成员的任务是协同工作,分析并解决这个质量问题。
步骤2:问题描述团队成员开始收集问题的相关信息并描述问题。
他们了解到问题主要集中在一批产品上,而且主要是涂层脱落,导致产品无法正常使用。
步骤3:临时控制措施为了防止问题继续扩大,团队决定采取一些临时的控制措施,例如增加质检频率,严格按照工艺规范进行操作等,以减少产品问题的发生率。
步骤4:问题的根本原因分析团队成员使用常用的质量工具(如鱼骨图、5W1H分析等)进行问题的根本原因分析。
他们发现问题可能与涂层工艺、原材料质量等因素有关。
步骤5:制定长期解决方案基于问题的根本原因分析,团队成员制定了长期解决方案。
他们决定对涂层工艺进行优化,对原材料质量进行更加严格的控制。
同时,还计划对生产工艺进行改进,以提高产品的质量和可靠性。
步骤6:验证解决方案为了验证解决方案的有效性,团队进行了一系列实验和测试。
他们使用不同的涂层工艺和原材料质量进行生产,并对产品进行测试。
结果表明,解决方案确实有效,产品的质量得到了显著提升。
步骤7:实施长期解决方案基于验证结果,团队决定全面实施长期解决方案。
他们对生产流程进行调整,更新工艺规范,并与供应商合作加强原材料质量监控。
步骤8:预防措施为了防止类似问题的再次发生,团队制定了一系列预防措施。
他们决定加强内部培训,提高员工的质量意识和技能水平。
此外,还计划开展定期的质量检查和审查,以及建立质量指标和绩效评估体系。
通过以上八个步骤,团队成功解决了产品质量问题,并采取了一系列措施防止问题的再次发生。
注塑行业产品8D改善报告样板
注塑行业产品8D改善报告样板1.引言注塑行业是一种重要的加工方式,市场需求量大,但也面临着品质不稳定、交货周期长等问题。
为了提高产品质量和客户满意度,我们接受了一份客户投诉,对产品缺陷进行了分析和改善。
本报告旨在总结和展示我们使用8D方法改善产品质量的过程和结果。
2.问题描述在我们的产品中,存在以下问题:1)缺陷类型:部分产品的尺寸偏差超出了客户要求;2)缺陷数量:近期共有50件产品被客户退回,占全部生产的5%;3)缺陷原因:初步分析,根因可能是生产过程中的设备问题或操作不当。
3.8D步骤我们按照8D改善方法的步骤进行了详细的分析和改善。
3.1D1:团队成立我们成立了一个跨部门的改善团队,包括生产部门、质量部门和工程部门的成员,确保了全面性和有效性。
3.2D2:问题描述我们详细描述了产品的缺陷情况,并制定了改善目标:减少产品尺寸偏差至客户要求的范围内。
3.3D3:紧急措施为了防止更多的产品缺陷,我们立即采取了以下紧急措施:1)暂停生产线,对所有设备进行检查和维护;2)增加生产过程中的检验环节,确保产品质量;3)进行员工培训,加强操作规范和质量意识。
3.4D4:根本原因分析为了找出导致产品尺寸偏差的根本原因,我们进行了以下分析:1)检查和测试设备,发现其中一台注塑机的控制系统存在问题,导致了产品尺寸偏差;2)通过观察,发现一些操作员没有严格按照操作规程进行操作,也是导致尺寸偏差的原因之一3.5D5:纠正措施针对发现的根本原因,我们采取了以下纠正措施:1)更换注塑机的控制系统,确保其正常运行;2)对操作员进行再次培训,强调操作规程的重要性;3)设立严格的质量检查流程,确保产品的尺寸满足客户要求。
3.6D6:验证纠正措施的有效性我们重新上线生产,并对产出的产品进行了全面的尺寸检验。
结果显示,产品的尺寸偏差已经控制在客户要求的范围内。
3.7D7:预防措施为了防止类似问题的再次发生,我们制定了以下预防措施:1)定期维护设备,确保其良好的功能状态;2)加强员工培训,提高其操作规程的意识;3)强化质量管理,建立更完善的质量控制机制。
质量8d报告范本
质量8d报告范本1. 关于质量的8D报告如何写8D运用全球8D程序(简称:全球8D)是一种汽车行业处理问题的标准化方法,通过全球8D可以客观地验证、确认,以及处理问题,并且防止类似的问题再次发生,在这套方法中除了要考虑一种产品或工艺为什么会偏离其性能标准之外,还要寻求对问题的定义和理解,并且供应一种识别问题根本缘由的思路。
全球8D包括8个步骤,再加上一个预备步骤。
这些步骤被用来客观地验证、确认,以及处理问题,并且防止类似的问题再次发生。
本文针对详细车型防水膜漏水的问题,具体讲解如何应用这些步骤去处理质量问题。
D0:程序的预备对症状做出反应,定义与量化问题,确定问题能否复制了当前存在的全球8D,或者问题能否是一个新的全球8D项目,假如需要的话,选择突发大事处理措施以及执行突发大事处理措施爱护消费者,并且启动8D程序。
此案例中,症状为:某车型在工厂内做完淋雨测试后有水穿过防水膜进入车内,同样,在来自售后的反馈中,消费者也对同样问题有很大的埋怨。
经过调查,确认此症状为一个全新的问题,于是启动一个全新全球8D项目。
D1:创建工作团队创建一个小型工作团队,关键是选择合适的成员构成。
不要从同一个部门里选择全部的成员,也不要选择有相同工作职责的成员,成员有着不同的阅历和才能,可以从不同角度来考虑状况。
这个团队要具有处理指定问题的学问、威信和娴熟的技术技能,要具有在指定时间内处理问题的力量以及执行正确措施的力量,一个具有适当技术技能的相互协作的团队能处理一些甚至大多数高水平的团队成员不能单独处理的问题,而团队的工作力量需要肯定的时间去增加,要随时补充新的成员,这个工作团队必需有一个指派的监督人以及团队的领导者。
在问题处理过程中,团队的成员包括质量分析工程师、工艺工程师、售后工程师、产品工程师以及供应商质量管理工程师。
质量分析工程师担当领导者,他可以给其他成员安排任务,并对成员监督。
D2:问题描述问题描述的目的是要保持团队的关注,缩小查找根本缘由的范围。
8D报告解说及范例-课件
8D
恭贺团队及未来方向15
壹. 问题篇 1:主题选定
• 把问题具体地表现出来
• 可利用评价法选定主题
• 必要时可用二个主题以上
注意事项:
• 不要涉及太大的范围
问题分析技术与管理
• 不要太长的活动期间
8D
16
壹. 问题篇 问题的出现
• 依公司目标管理方向 • 主管的方针、上司的提示及指引 • 浪费、不均、勉强的问题 • 提高效率、质量方面 • 考虑自行可解决的问题
2)爲提高质量的目的而改变目前的状况.
• 依公司目标管理方向 • 主管的方针、上司的提示及指引 • 浪费、不均、勉强的问题 • 提高效率、质量方面
• 考虑自行可解决的问题
思考
1.大部分管理工作是致力于克服那些妨碍人们实现目标的问题。
2.不去理会发生的情况,希望问题自行解决,显然轻松很多,可是问题
是永远不可能自行解决的。
77.95 78.95 79.958D 80.95 81.95 82.95 83.9531
柏拉图 (Pareto Chart)
• 目的:为便于判断产品较重要之不良原 因所绘制之图形
• 通常先以层别法与查检表为前置作业
8D
32
• 实例
xx工程不良分析表
项目
不良数 累积不良数 比率 % 累积比率%
材料不良 96
生产设备
8D
6
壹. 问题篇 原因取向
问题的走向 目标取向
过去
现在
未来
发生型问题
(己发生的问题)
•脱线问题
•未达问题) 探索型问题
(欲想更好的问题)
•改善问题
•强化问题) 设定型问题
(今后何去何从的问题)
8D报告以及案例分析PPT课件
D1:成立处理团队
挑选并登录内部及外部小组成员 (Compaq的物料工程人员及供货商 的业务代表为外部小组成员).
挑选小组捍卫者(应由能排除小组工作 障碍的管理阶层人员担当).
挑选小组长(应为能直接投入问题处理 并承当小组责任的人).
需要供货商,客户加入团队吗 ?
8D
这些队员分别担当什么任务 ? 撰写8D之前,小组成员开会了吗 ? 采取脑力激荡来解决问题吗 ? 推敲人员的能力 - 不是有人就好
2.1 查最近冲压修模记录发觉, 11/14,2k曾因箭头模糊而将冲子高度垫高0.03mm. 确认冲子的
01 字模设计高度为0.10mm, (以下图,spec 0.10+/-0.05mm), 目前已磨损至0.07mm. 对应生产出
来的字模高度亦由本来的0.06mm降至0.03mm.故当冲压换料或调机时, 以手动方式送料, 此时 冲子可能没法完全压到下死点, 因此即会有箭头未冲出之零件产生.
8D
D6:成效验证
01
验证紧急计策及 永久计策之有效 性,应以量化表示 验证结果(如: Cpk值可达1.33, 或不良产生率降
至 0 等).
02
在永久计策 验证有效之 前,应连续进 行紧急计策.
03
追踪永久计 策实行后之 品质推移状
态
04
在没有完全掌 控问题已彻底 解决之前 , 不 要草率的结案 .
Problem description Containment plan
Describe the cause
成效验证
避免再发
恭喜你的 团队
Permanent C/A plan
Verification of effectiveness
- 1、下载文档前请自行甄别文档内容的完整性,平台不提供额外的编辑、内容补充、找答案等附加服务。
- 2、"仅部分预览"的文档,不可在线预览部分如存在完整性等问题,可反馈申请退款(可完整预览的文档不适用该条件!)。
- 3、如文档侵犯您的权益,请联系客服反馈,我们会尽快为您处理(人工客服工作时间:9:00-18:30)。
D4 根本原因分析Root Causes
3)生产影响分析验证资料附件3
生产流程:查前处理槽参数浓 度均在范围内,除12月5日高 温除油更换,电解槽无更换记 录;使用时间超出6个月有失 效风险;
D4 根本原因分析Root Causes
5)起泡不良鱼骨图分析
料
机
人
冲压件油渍过多 盐酸失效 除油剂失效 除油设计不合理
陈赛
维护
沈开文
2017-2-21
进行中
生产
沈开文
2017-2-21
进行中
检验
沈开文
2017-2-21
进行中
检验
章秋飞
2017-2-21
进行中
D6 恒久措施
NO. 问题 措施分类 槽液维护 行动 在控制计划和作业指导书中增加槽液维护更换周期,并形成 规范处理记录; 根据产线空间评估高温除油槽油脂分离溢流装置的可行性; 负责人 姜志敏 预计完成日期 2017-3-17 跟踪状态 编制中
是
2
高温除油
浮油过多带出 1.查验浓度分析记录; 1.查高温除油槽浓度分析结果OK; 交叉污染 2.目视检查槽内油渍情况; 2.槽体内表面浮油严重,有带出污染风险;
电解除油剂 1.查验浓度分析记录; 失效 2.检查除油槽维护记录; 浮油杂质污染 1.查验分析记录正常; 2.电解槽更换最近的时间 为2016年6月,长时间未进行槽体清洗,有杂质影响 除油减弱风险;
2
D1 问题描述
问题描述 球铰TX0001261起泡不良
发生日期
2017-2-13
发生地点
出货检验区
客户投诉数量
3件
客户投诉批次
2017-1-13
对应生产线
鑫汇达镀锌线
事情严重度
严重
客 户 端 不 良 测 试 数 据 与 不 良 图 示 证 据
是否重复发生
第一次发生
其它
无
3
二、成立小组 Team
D7 团队庆祝
附件: 图示
配槽 改造为镀锌
水洗更换
钝化
吹干 烘干 下挂 挑选 包装检验 交付 存放 不良流出 很大
D4 根本原因分析Root Causes
•(2)起泡产生原因现场验证;
步骤 操作说明 影响因素 验证方法 确认结果 是否要因?
1
原料
冲压件 油渍过多
1.目视检查槽内油渍情况;
环形线当前非球铰专线生产,其它冲压件晚班生产, 量较大多油渍,有污染下工序
设备
贺南海
2017-4-15
设备 1 球铰产品镀层 起泡
增加镀锌线一条,冲压件和球铰分开生产;原新车间镀锡线 改造为镀锌线; 防止园区供给盐酸存储中浓度和硝酸混入,制定园区三酸采 购协议并配备专用存储桶,实施单独采购单独供给; 制定标准化原材料进厂检测规范,对盐酸等原材料实行周期 性检测; 标准化结合力和高温烘烤检测频率和容量,结合力每班一次 ,每次2件,高温烘烤每日一次,每次2件。
1.1.除油槽使用时间过 1.基材表面油渍未清理 长; 1.1电解除油槽未定义 1.1电解槽杂质含量过多; 镀锌层与基材表 干净; 1.2兆亮园区三酸混存污 更换时间; 1.2盐酸含硝酸根过多; 面粘合不牢 2.镀层表面太光亮,易 染; 1.2.供应商用于购买 2.光亮剂过量添加 起泡; 2.调整溶液么有量化添 三酸周转桶未清洗; 加标准,员工加过多;
改善后生产批次 20170221生产批 20170224生产批 20170225生产批 20170227生产批 20170301生产批 20170302生产批 20170303生产批 20170304生产批 20170305生产批 外观检验结果 OK OK OK OK OK OK OK OK OK 高温测试结合力 8款精磨球铰有2款小气泡 6款精磨球铰有1款小气泡 4款精磨球铰有1款小气泡 OK OK OK OK OK OK 放置24H检查外观 有气泡 挑选后发货 有气泡 挑选后发货 有气泡 挑选后发货 有气泡 挑选后发货 无气泡 部分发货 无气泡 部分发货 无气泡 部分发货 无气泡 部分发货 无气泡 客户反馈 有气泡 有气泡 有气泡 有气泡 无气泡 无气泡 无气泡 无气泡
当前已完成约4 2017-2-14 万件挑选,不良 1940件 2月21日更换高 温除油,更换酸 2017-2-15 洗,2月28日更 换电解,再次更 换酸洗 2017-3-1 进行中
生产排配 1 球铰产品镀层 起泡
油渍过重的冲压件如威孚,磐吉奥等产品实施线外除油处理 后上线; 每日进行除油槽浮油打捞 生产参数镀锌工序电压原5V,降至4.2V,光亮剂添加改为每天 2次按照KAH消耗补加; 每日生产产品高温烘烤抽检2次,每次2件,采用试制废品替 代; 每日生产产品现场放置1天后进行100%挑选
产品外观百检未 起泡是产品存放过程中 对镀锌产品高温烘烤试验 发现;结合力检 产生的,结合力检查只 没有标准化。 Outflow cause 测抽检未发现 抽检首件/每天;
流出原因
系统原因
产品失效评估控 制不足
PFMEA策划经验不足
D4 根本原因分析Root Causes
6)起泡不良分析结论
此不良主要是因为电解除油槽长时间未进行清理更换,以及酸洗原材料硝酸盐污染,导 致除油及去氧化皮效果减弱,产品表面局部存在未清洗彻底和油渍交叉带出入下工序槽且残 存工件表面,导致镀层与基材结合不良起泡; 根本主因确定为: 1.产线非专用,其它汽车件大量生产导致油渍集中悬浮于高温除油槽,局限于设备设计-高 温除油槽油脂溢流效果差导致油带出污染下工序; 2.电解槽未定义更换清洗频次,长时间使用,油渍杂质污染,效果较弱; 3.盐酸失效,园区存储不规范导致三酸交叉污染;
否
6
镀锌
1.光亮剂过多 1.赫尔槽试验; ,电流过大; 2.槽液分析; 2.杂质过多;
否
D4 根本原因分析Root Causes
3)生产影响分析验证资料附件1
2017-2-15从现场产品抽查结果分析,精加工产品存 在起泡;
D4 根本原因分析Root Causes
3)生产影响分析验证资料附件2
起泡检验方法为高温测试和百格测 试法;按照测试方法进行现场每款 产品抽查发现TX001076镀层脱落
鑫汇达电镀
产品表面起泡不良8D分析报告
报告编制:姜志敏
2017-2-21 更新2017-3-7
目录
D1-问题描述 ------------------------------------------------------------------- 3 D2-成立8D小组 --------------------------------------------------------------- 4 D3-临时围堵对策实施 ------------------------------------------------------- 5 D4-根本原因分析 ------------------------------------------------------------- 6 D5-临时措施实施 ------------------------------------------------------------- 7
黄伟奇
2017-4-5
进行中
原料
黄伟奇
2017-4-5
进行中
检验
姜志敏
2017-3-17
检验
章秋飞
2017-2-21
进行中
D7 恒久措施验证
1. 断点日期: 断点控制2017年03月01日 2. 控制文件更新: 2.1PFMEA,CP增加起泡失效模式控制点; 2.2前处理作业指导书更新; 2.3化学原材料检验规范制作并实施; 3. 产品验证:连续5个批次追踪产品质量合格率
OC
Leader
Name
贺南海
Title
总经理
黄伟奇 沈开文
章秋飞
Member
项目经理 生产技术经理
质量工程师 生产计划 体系工程师 时代新材道事业部 博戈SQE
陈赛 姜志敏 周同理 杨兵
4
D3 临时的围堵措施
SUSPECT QTY 可疑产品数 CONTAINMENT ACTION 处理方法 NG QTY. 不良品数 CONFIRMED BY 确认人 IMPLEMENT DATE 执行日期
5
D4 根本原因分析Root Causes
•(1)起泡产生原因可疑点分析
产品电镀生产简易流程与不良关联分析 步骤 1 2 3 4 5 6 操作说明 原材料入厂检验 人工擦洗 上挂 前处理 镀锌 出光 油渍氧化皮未处理干净 光亮剂过量,电流过大 很大 很大 影响因素 冲压件油渍 影响度 很大
7
8 9 10 11 12 13 14
否
3
电解除油
是
4
酸洗
1.查验纯度分析记录; 1.盐酸纯度分析委外测试中; 2.目视检查槽内油渍情况; 2.槽体内表面浮油严重,有带出污染风险;
是
5
镀前水洗
浮油污染; 1.目视检查槽内油渍情况; 1.槽体内表面有浮油,有吸附于工件表面造成影响; 1.赫尔槽试验结果显示有偏多,目前已停止添加光亮 剂,降低电流20%;2.春节进行槽液杂质处理(活性 炭,锌粉以及电解),且槽液分析杂质离子Cu,Gr,Pb 等未超标;
LOCATION 位置
时代新材弹性本部 博戈仓库 在途品 鑫汇达仓库
约20000件 约80000件 0 660
100% 挑选 100% 挑选 / 放置3天全部挑选
截止3月2日1663 截止3月7日约挑20000 发现不良830件 / 40
姜志敏 李顺兰 陈赛 章秋飞
2017-2-20 2017-2-20 2017-2-14 2017-2-14