全铝车身结构设计
奥迪全铝车身框架结构(ASF)
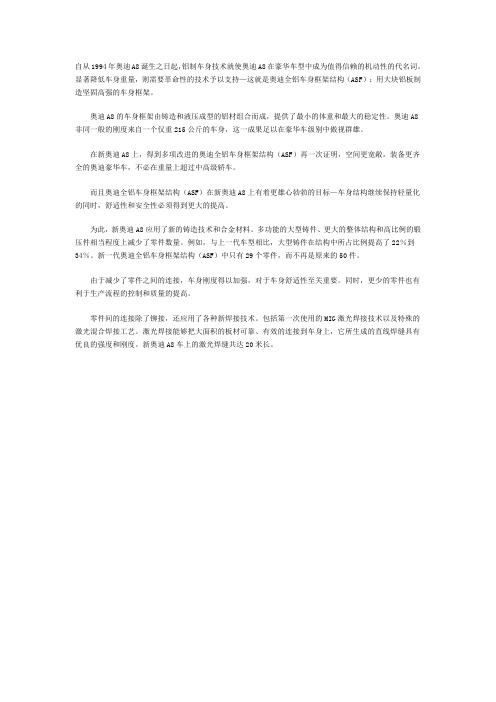
自从1994年奥迪A8诞生之日起,铝制车身技术就使奥迪A8在豪华车型中成为值得信赖的机动性的代名词。
显著降低车身重量,则需要革命性的技术予以支持—这就是奥迪全铝车身框架结构(ASF):用大块铝板制造坚固高强的车身框架。
奥迪A8的车身框架由铸造和液压成型的铝材组合而成,提供了最小的体重和最大的稳定性。
奥迪A8非同一般的刚度来自一个仅重215公斤的车身,这一成果足以在豪华车级别中傲视群雄。
在新奥迪A8上,得到多项改进的奥迪全铝车身框架结构(ASF)再一次证明,空间更宽敞,装备更齐全的奥迪豪华车,不必在重量上超过中高级轿车。
而且奥迪全铝车身框架结构(ASF)在新奥迪A8上有着更雄心勃勃的目标—车身结构继续保持轻量化的同时,舒适性和安全性必须得到更大的提高。
为此,新奥迪A8应用了新的铸造技术和合金材料。
多功能的大型铸件、更大的整体结构和高比例的锻压件相当程度上减少了零件数量。
例如,与上一代车型相比,大型铸件在结构中所占比例提高了22%到34%。
新一代奥迪全铝车身框架结构(ASF)中只有29个零件,而不再是原来的50件。
由于减少了零件之间的连接,车身刚度得以加强,对于车身舒适性至关重要。
同时,更少的零件也有利于生产流程的控制和质量的提高。
零件间的连接除了铆接,还应用了各种新焊接技术。
包括第一次使用的MIG激光焊接技术以及特殊的激光混合焊接工艺。
激光焊接能够把大面积的板材可靠、有效的连接到车身上,它所生成的直线焊缝具有优良的强度和刚度。
新奥迪A8车上的激光焊缝共达20米长。
混合动力客车全铝合金车身顶盖骨架优化设计

混合动力客车全铝合金车身顶盖骨架优化设计近年来,新能源汽车的兴起使得混合动力客车越来越受到人们的关注和推崇。
而混合动力客车的使用平稳性、燃油经济性以及车身安全性成为客户选购混合动力客车时关注的核心问题。
因此,本文将探讨混合动力客车全铝合金车身顶盖骨架优化设计,协助提高混合动力客车的使用平稳性、燃油经济性以及车身安全性。
一、全铝合金车身顶盖骨架的构造原理全铝合金车身顶盖骨架是由铝及其合金组成,形成各种结构理论与加工工艺结合成的不锈钢铝配件件与警示元件等,这些元件均被设计成稳定的整体结构,以在运动和事故中传导在车身和乘客区域的准确载荷和动态应力,从而保障驾驶人员和乘客的安全。
二、设计考虑因素混合动力客车的客户对车辆的性能和价格敏感,提高混合动力客车的使用平稳性、燃油经济性以及车身安全性是设计优化的重点,下面我们将从以下三个方面来考虑:1.减轻车身重量:减轻车身的重量将极大地提高混合动力客车的燃油经济性能以及使用效率,全铝合金车身可以协助降低车身的重量,不仅可改善混合动力客车的燃油经济性能,还有助于提高维护效率。
2.增强车身稳定性:由于混合动力客车使用车轮的动力和发动机的动力,因此车身稳定性成为整车设计的重点之一。
全铝合金车身顶盖骨架的抗弯曲性能比较优异,可以协助降低车身的变形度,提高车身的稳定性。
3.加强车身的安全性:安全性是混合动力客车设计的关键因素之一。
全铝合金车身顶盖骨架可以提升车身受撞击时的抗剧烈变形性能,减少驾驶人员和乘客在意外事故中的伤亡。
三、车身顶盖骨架设计为了实现全铝合金车身顶盖骨架的优化设计,在设计过程中需考虑到以下几个方面:1. 材料选择:对于全铝合金车身顶盖骨架的材料,最好采用6061T6铝合金材料,因为这种材料的强度与钢铁相同,但其重量却很轻。
2. 稳定性:为了提高车辆的稳定性,铝合金车身顶盖骨架在结构设计方面应采用中空结构,其断面形状宜采用“V”形,以增强其抗弯曲性能。
3. 强度:为了提高全铝合金车身顶盖骨架的强度,其内壁应以“X”形结构进行梳理,以提高其腰链强度。
论客车铝车身结构优化设计与分析
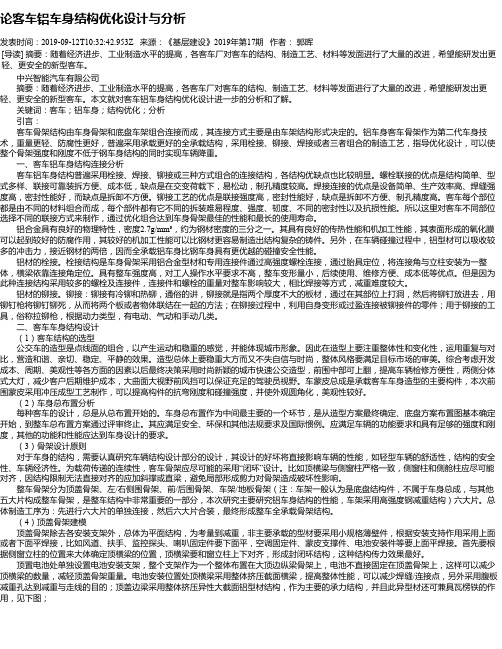
论客车铝车身结构优化设计与分析发表时间:2019-09-12T10:32:42.953Z 来源:《基层建设》2019年第17期作者:郭晖[导读] 摘要:随着经济进步、工业制造水平的提高,各客车厂对客车的结构、制造工艺、材料等发面进行了大量的改进,希望能研发出更轻、更安全的新型客车。
中兴智能汽车有限公司摘要:随着经济进步、工业制造水平的提高,各客车厂对客车的结构、制造工艺、材料等发面进行了大量的改进,希望能研发出更轻、更安全的新型客车。
本文就对客车铝车身结构优化设计进一步的分析和了解。
关键词:客车;铝车身;结构优化;分析引言:客车骨架结构由车身骨架和底盘车架组合连接而成,其连接方式主要是由车架结构形式决定的。
铝车身客车骨架作为第二代车身技术,重量更轻、防腐性更好,普遍采用承载更好的全承载结构,采用栓接、铆接、焊接或者三者组合的制造工艺,指导优化设计,可以使整个骨架强度和刚度不低于钢车身结构的同时实现车辆降重。
一、客车铝车身结构连接分析客车铝车身结构普遍采用栓接、焊接、铆接或三种方式组合的连接结构,各结构优缺点也比较明显。
螺栓联接的优点是结构简单、型式多样、联接可靠装拆方便、成本低,缺点是在交变荷载下,易松动,制孔精度较高。
焊接连接的优点是设备简单、生产效率高、焊缝强度高,密封性能好,而缺点是拆卸不方便。
铆接工艺的优点是联接强度高,密封性能好,缺点是拆卸不方便、制孔精度高。
客车每个部位都是由不同的材料组合而成,每个部件都有它不同的拆装难易程度、强度、韧度、不同的密封性以及抗损性能。
所以这里对客车不同部位选择不同的联接方式来制作,通过优化组合达到车身骨架最佳的性能和最长的使用寿命。
铝合金具有良好的物理特性,密度2.7g/mm³,约为钢材密度的三分之一。
其具有良好的传热性能和机加工性能,其表面形成的氧化膜可以起到较好的防腐作用,其较好的机加工性能可以比钢材更容易制造出结构复杂的铸件。
另外,在车辆碰撞过程中,铝型材可以吸收较多的冲击力,接近钢材的两倍,因而全承载铝车身比钢车身具有更优越的碰撞安全性能。
机动车轻量化解决处理办法全铝车身结构设计

汽车轻量化解决方案一全铝车身结构设计伍成祁摘要:解决汽车节能环保的问题,有提高传统燃油发动机的能效、发展新能汽车、应用轻量化技术三个方向。
比较以上三种技术路线,在当今发动机技术提升难度日益加大、动力电池效率不高的背景下,不论对传统燃油汽车,还是新能源汽车,汽车轻量化技术都是一项共性的基础技术。
大力发展并推进汽车轻量化技术,成为节能、减排的主导之一。
而实现汽车轻量化技术又有三个技术途径:一种“轻量化材料”要通过一种“轻量化工艺”来实现一种“轻量化结构”。
关键词:汽车轻量化全铝车身型材截面优化Stiffness Mass Efficient由于世界能源的随时枯竭与环境的日益恶化,世界各行各业都积极行动起来,根据政府的优惠政策与民众的强烈要求,在节能、环保方面进行了高投入]研发其高效节能、积极环保的产品。
汽车产业首当其冲,其汽车零部件的制造,迁联到能源、钢材、铝材、合金、塑料、橡胶、玻璃、化工、机械、电器、信息等各行各业,对汽车节能环保的要求,就是对其它相关行业的要求。
对汽车进行轻量化结构的研究,要联系相关行业的专业知识,进行综合性的研究。
一、汽车轻量化的目的n就汽车产业而言,根据汽车产品的特点,降低油耗或提高燃油效率、减少或清洁排放对环境的污染,是节能环保研发的主要目的。
从全球汽车产业来看,解决汽车节能环保问题主要采用以下三种方式:~I一是大力发展先进发动机技术,通过对传统发动机的改良和一系列汽车电子技术的应用,来提高燃烧效率,改善燃油经济性。
―I二是大力发展新能源汽车,通过研发先进新型发动机技术和推广使用气体燃料、生物质燃料、煤基燃料、高效电池等动力替代传统能源来减少汽车燃油消耗和对石油资源的依赖。
丁三是大力发展汽车轻量化技术,在保障汽车安全性和其他基本性能的前提下,通过减轻汽车自身重量降低能耗来实现节能减排的目的。
比较以上三种技术路线,在当今发动机技术提升难度日益加大、动力电池效率不高的背景下,不论对传统燃油汽车,还是新能源汽车,汽车轻量化技术都是一项共性的基础技术。
基于参数化模型的小型电动车全铝框架车身结构轻量化设计
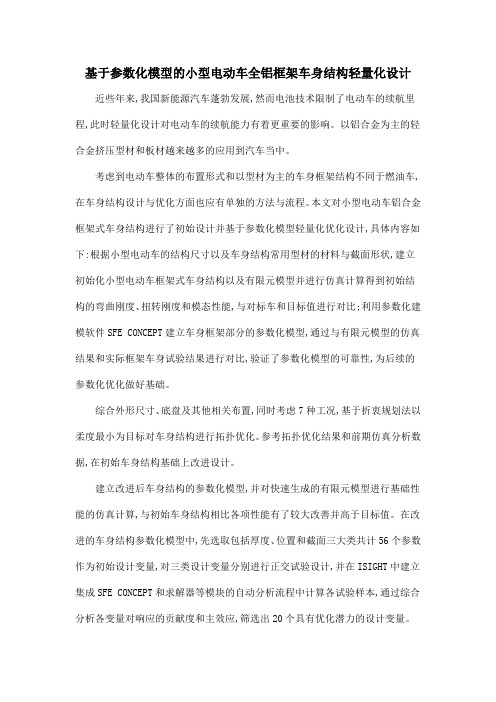
基于参数化模型的小型电动车全铝框架车身结构轻量化设计近些年来,我国新能源汽车蓬勃发展,然而电池技术限制了电动车的续航里程,此时轻量化设计对电动车的续航能力有着更重要的影响。
以铝合金为主的轻合金挤压型材和板材越来越多的应用到汽车当中。
考虑到电动车整体的布置形式和以型材为主的车身框架结构不同于燃油车,在车身结构设计与优化方面也应有单独的方法与流程。
本文对小型电动车铝合金框架式车身结构进行了初始设计并基于参数化模型轻量化优化设计,具体内容如下:根据小型电动车的结构尺寸以及车身结构常用型材的材料与截面形状,建立初始化小型电动车框架式车身结构以及有限元模型并进行仿真计算得到初始结构的弯曲刚度、扭转刚度和模态性能,与对标车和目标值进行对比;利用参数化建模软件SFE CONCEPT建立车身框架部分的参数化模型,通过与有限元模型的仿真结果和实际框架车身试验结果进行对比,验证了参数化模型的可靠性,为后续的参数化优化做好基础。
综合外形尺寸、底盘及其他相关布置,同时考虑7种工况,基于折衷规划法以柔度最小为目标对车身结构进行拓扑优化。
参考拓扑优化结果和前期仿真分析数据,在初始车身结构基础上改进设计。
建立改进后车身结构的参数化模型,并对快速生成的有限元模型进行基础性能的仿真计算,与初始车身结构相比各项性能有了较大改善并高于目标值。
在改进的车身结构参数化模型中,先选取包括厚度、位置和截面三大类共计56个参数作为初始设计变量,对三类设计变量分别进行正交试验设计,并在ISIGHT中建立集成SFE CONCEPT和求解器等模块的自动分析流程中计算各试验样本,通过综合分析各变量对响应的贡献度和主效应,筛选出20个具有优化潜力的设计变量。
利用优化拉丁方试验设计方法进行130次试验设计,根据样本点数据建立不同近似模型来表示变量与响应之间的关系。
最终通过精度对比,选用响应面近似模型代替仿真模型,采用NSGA-Ⅱ多目标优化算法,以质量最小和弯扭刚度最大为目标对车身结构进行多目标优化。
铝质车身的结构特点与维修须知

蚀
、
弹 性好
、
刚度和强 度高
、
抗 冲击性能
,
铝 质构件
不 但具 有足 够
,
用 气体 保 护 焊
优
、
加 工 成 型 性 好 和 再 生 性 高 等特 点
。
成
的强度和韧度
同 时还 具
。
为 了 使 汽 车轻 型 化 的 首 选 材 料
铝 合金 车
备 良好 的 导 热 能 力 证明
。
事实
油箱在 车身后 部 发 生碰 撞
不 相 同 。 如 车 辆 的保
轻 车 身 自重
加装载质量
、
增
降
,
着 车 身 后
、
险杠 骨架
、
加强梁 或
,
部 整 个 的
框 架
。
低 发 动机 负载
侧防撞梁等
图2 新 款 奥 迪 A 8 铝 制 车 身
,
所 使用
如
同 时还 可 以大 幅
的铝 材 都应 具 有足 够 的强 度 和 韧 度
,
此 高 的 刚 性 保 证 了
一
着 双 重 的价 值
新 款 奥迪A 8 全 铝 车 身仅
和 车 梁 的连 接 质 量
确 保 了 整个 车 身 框 架
维普资讯
的刚性
。
新A 8 的侧面 面 板 由
一
个从A 柱
。
一
直 延 伸 到 车 身后 部 的 整体 部 件 组 成
顶
一
与车
,
样
,
侧 面 面 板 也 是 由激 光 焊 接 而 成
维普资讯
铝 质 车 身 的结 构 特 点
浅谈奥迪铝车身技术

科技资讯2017 NO.23SCIENCE & TECHNOLOGY INFORMATION工 业 技 术85科技资讯 SCIENCE & TECHNOLOGY INFORMATION 1 奥迪框架结构车身发展随着人们环保意识和节能意识的提高,降低车身重量已经成为汽车发展重要趋势。
汽车行业专家认为,要降低汽车排放对于生态环境的污染,就要把汽车的效率提高,而提高汽车效率有3个主要途径:降低车身重量、降低车身风阻、提高发动机效率。
这3个主要途径中,汽车外形设计和汽车发动机技术已经非常成熟,可提高难度大、费用高。
所以,降低车身重量是最为有效的途径。
根据汽车研究机构实验证实,如果汽车整车整备重量减少5%,汽车燃油经济性可提高3%;汽车整车整备重量每减少50kg,汽车百公里油耗可以减少0.3L。
汽车使用铝制件来代替钢制件,能使汽车整车整备重量减少35%;如果汽车发动机使用铝来制造,能减轻25%的重量;使用铝制水箱比使用铜制水箱重量减少35%。
由此可见一辆汽车使用铝材来代替钢材对于车辆的减重有着非常好的效果。
为了实现车身轻量化,奥迪车身研发出一项革命性的技术-科学轻量化设计。
这一科学轻量化设计被称作奥迪框架结构车身,所谓“框架结构车身”,就是在三维立体的空间内,使用铸造件和型材件搭建一个“车架”,然后再将车身覆盖件装配到这个“车架”上。
奥迪框架结构车身采用铝件、塑料件和碳纤维件组成,使用轻量化生产工艺生产,从而使车身重量降低到难以想象的程度,同时提高了车辆的安全性。
1995年奥迪第一代全铝车身奥迪A8批量化生产。
第一代奥迪全铝车身使用型材铝制造并将车身设计成骨架式结构,这种结构设计被称为框架结构车身。
2002年,第二代奥迪框架结构车身问世。
奥迪第二代框架结构车身所有零部件均采用注塑铝件和冲压板材制造而成,采用胶粘铆接连接而成,同时使用了激光焊接,这使得车身结构变的更强。
奥迪第三代框架结构车身全部由型材铝制造而成,在生产制造方面,手工加工制造更多应用于第二代框架结构车身,而智能自动化制造更多应用于第三代框架结构车身。
汽车轻量化解决方案全铝车身结构技术
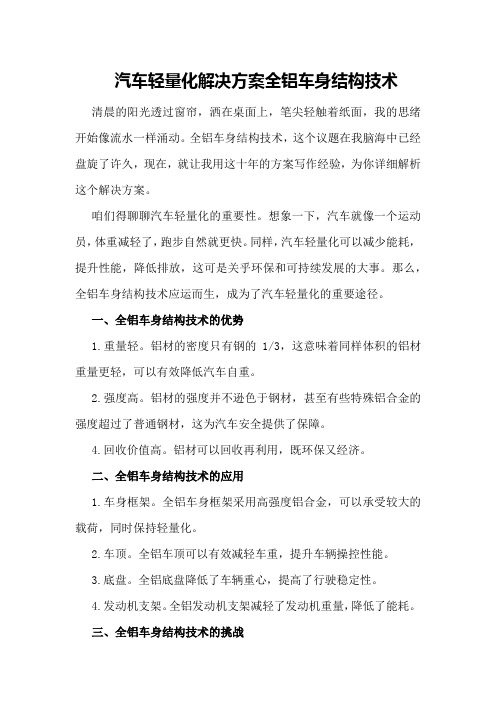
汽车轻量化解决方案全铝车身结构技术清晨的阳光透过窗帘,洒在桌面上,笔尖轻触着纸面,我的思绪开始像流水一样涌动。
全铝车身结构技术,这个议题在我脑海中已经盘旋了许久,现在,就让我用这十年的方案写作经验,为你详细解析这个解决方案。
咱们得聊聊汽车轻量化的重要性。
想象一下,汽车就像一个运动员,体重减轻了,跑步自然就更快。
同样,汽车轻量化可以减少能耗,提升性能,降低排放,这可是关乎环保和可持续发展的大事。
那么,全铝车身结构技术应运而生,成为了汽车轻量化的重要途径。
一、全铝车身结构技术的优势1.重量轻。
铝材的密度只有钢的1/3,这意味着同样体积的铝材重量更轻,可以有效降低汽车自重。
2.强度高。
铝材的强度并不逊色于钢材,甚至有些特殊铝合金的强度超过了普通钢材,这为汽车安全提供了保障。
4.回收价值高。
铝材可以回收再利用,既环保又经济。
二、全铝车身结构技术的应用1.车身框架。
全铝车身框架采用高强度铝合金,可以承受较大的载荷,同时保持轻量化。
2.车顶。
全铝车顶可以有效减轻车重,提升车辆操控性能。
3.底盘。
全铝底盘降低了车辆重心,提高了行驶稳定性。
4.发动机支架。
全铝发动机支架减轻了发动机重量,降低了能耗。
三、全铝车身结构技术的挑战1.成本较高。
相较于传统钢材,铝合金的成本较高,这无疑增加了汽车制造成本。
2.加工难度大。
铝合金的加工工艺较为复杂,对生产线的要求较高。
3.结构设计难度。
全铝车身结构的设计需要充分考虑材料的特性,这对设计师提出了更高的要求。
四、解决方案1.降低成本。
通过优化供应链,提高材料利用率,降低铝合金成本。
2.提高加工技术。
引入先进的加工设备和技术,提高铝合金的加工效率和质量。
3.加强结构设计。
结合材料特性,优化车身结构设计,提高车辆性能。
4.推广应用。
加大全铝车身结构技术的宣传力度,提高市场认可度。
写着写着,阳光已经悄然移动,时间在指尖流转。
汽车轻量化解决方案全铝车身结构技术,这个议题就像一幅画卷,在我面前缓缓展开。
- 1、下载文档前请自行甄别文档内容的完整性,平台不提供额外的编辑、内容补充、找答案等附加服务。
- 2、"仅部分预览"的文档,不可在线预览部分如存在完整性等问题,可反馈申请退款(可完整预览的文档不适用该条件!)。
- 3、如文档侵犯您的权益,请联系客服反馈,我们会尽快为您处理(人工客服工作时间:9:00-18:30)。
汽车轻量化解决方案—全铝车身结构设计摘要:解决汽车节能环保的问题,有提高传统燃油发动机的能效、发展新能汽车、应用轻量化技术三个方向。
比较以上三种技术路线,在当今发动机技术提升难度日益加大、动力电池效率不高的背景下,不论对传统燃油汽车,还是新能源汽车,汽车轻量化技术都是一项共性的基础技术。
大力发展并推进汽车轻量化技术,成为节能、减排的主导之一。
而实现汽车轻量化技术又有三个技术途径:一种“轻量化材料”要通过一种“轻量化工艺”来实现一种“轻量化结构”。
关键词:汽车轻量化全铝车身型材截面优化Stiffness Mass Efficient由于世界能源的随时枯竭与环境的日益恶化,世界各行各业都积极行动起来,根据政府的优惠政策与民众的强烈要求,在节能、环保方面进行了高投入研发其高效节能、积极环保的产品。
汽车产业首当其冲,其汽车零部件的制造,迁联到能源、钢材、铝材、合金、塑料、橡胶、玻璃、化工、机械、电器、信息等各行各业,对汽车节能环保的要求,就是对其它相关行业的要求。
对汽车进行轻量化结构的研究,要联系相关行业的专业知识,进行综合性的研究。
一、汽车轻量化的目的就汽车产业而言,根据汽车产品的特点,降低油耗或提高燃油效率、减少或清洁排放对环境的污染,是节能环保研发的主要目的。
从全球汽车产业来看,解决汽车节能环保问题主要采用以下三种方式:一是大力发展先进发动机技术,通过对传统发动机的改良和一系列汽车电子技术的应用,来提高燃烧效率,改善燃油经济性。
二是大力发展新能源汽车,通过研发先进新型发动机技术和推广使用气体燃料、生物质燃料、煤基燃料、高效电池等动力替代传统能源来减少汽车燃油消耗和对石油资源的依赖。
三是大力发展汽车轻量化技术,在保障汽车安全性和其他基本性能的前提下,通过减轻汽车自身重量降低能耗来实现节能减排的目的。
比较以上三种技术路线,在当今发动机技术提升难度日益加大、动力电池效率不高的背景下,不论对传统燃油汽车,还是新能源汽车,汽车轻量化技术都是一项共性的基础技术。
大力发展并推进汽车轻量化技术,成为节能、减排的主导之一。
汽车的轻量化,英文名:Lightweight of Automobile,涵义是“在保证汽车的强度和安全性能的前提下,尽可能地降低汽车的整备质量,从而提高汽车的动力性,减少燃料消耗,降低排气污染。
”世界节能与环境协会的研究报告指出:汽车自重每减少10%,燃油消耗可降低6%—8%,排放降低5%—6%。
而燃油消耗每减少1升,CO2排放量减少2.45kg。
燃油消耗量减少不仅有利于节约能源,也可有效减少污染物排放。
当前,由于节能和环保的需要,汽车的轻量化已经成为世界汽车发展的潮流。
伴随着技术进步,制造汽车车身的材料已经不仅仅是钢铁了,越来越多的新材料被应用到车身的制作中。
其中包括:玻璃钢、铝合金、碳纤维、塑料、高分子复合材料等等。
这些相对于钢铁比重要低得多的轻质材料,为实现汽车轻量化成为了工程师们的考量选材。
二、汽车轻量化的实施在实现汽车轻量化设计时,首先必须要确保其整体汽车结构达到国家的汽车安全标准,其次确保其使用性能达到或超越传统钢制车身的要求。
汽车轻量化设计与整车的安全性是一对矛盾体,如果为了满足各种法规的要求,保障乘员的安全,就应提高车身结构的抗弯强度、抗扭强度、侧翻强度、碰撞吸能等特性;如果为了汽车的燃油经济性、减少排放等因素考虑就应减轻车身的质量。
因此汽车车身轻量化是在保证汽车整体性能不受影响、确保车身强度、刚度和模态等结构特性要求的前提下,来减轻车身质量的一种设计趋向。
所以要求汽车轻量化设计要充分地从材料分析、结构力学、生产工艺、人体工程、工业设计、交通运输、经济效益等众多各不相同的学科紧密地联系在一起进行综合性研究开发。
汽车车身轻量化的实现,主要包括轻量化的材料使用和轻量化的结构设计,以及轻量化的制造工艺这三个方面。
前者是车身轻量化的主流,即采用轻量化的金属和非金属材料,主要是采用高强度钢材、铝镁合金、工程塑料、碳纤维、新型玻璃、陶瓷和各种复合材料;后者是利用“以结构换强度”的结构优化设计和有限元分析等方法,通过改进汽车结构,使部件薄壁化、中空化、小型化、模块化及复合化等以减小车身骨架、车身蒙皮等零部件的质量来达到轻量化目的。
实际上两者是紧密相连的,往往采用轻量化材料结合轻量化结构设计,在性能不降低的前提下获得汽车车身的轻量化。
但是,一种轻量化材料结合轻量化结构的设计方案,还需要一种优良的制造工艺来保证其完善实施。
也就是说一种轻量化材料要通过一种优良的制造工艺来实现一种轻量化结构设计。
因此,轻量化制造工艺显得特别重要。
总之,汽车轻量化的实施,还需要通过试制样车,进行试验,总结设计经验,对其轻量化设计结构进行优化与完善。
汽车车身轻量化设计中的结构优化包括:型材截面优化、连接工艺优化和结构拓扑优化。
型材截面优化和连接工艺优化,根据材料特性、受力分析、制造工艺等实践经验进行设计优化。
结构拓扑优化是在一定空间区域(骨架部件或结构整体)内寻求材料最合理分布的一种优化方法。
它的目标是根据一定的准则,在满足各种约束条件下,在结构上开孔、打洞,去除不必要的构件和材料,使结构在规定意义上达到最优,表现为“用材最小、刚度最大”设计。
由于拓扑优化设计自由度大,所以通常用于设计初期和概念设计的阶段。
三、车身的轻量化结构设计车身的轻量化设计,需要根据不同的材料选择合适的结构形式。
下面是最常用的几种车身形式,通过分析比较,选择不同的轻量化处理方法。
1)、碳纤维车身结构:碳纤维的密度要比钢材低4倍左右,而强度和硬度都是钢材的两倍。
虽然它很坚韧,但有受力向度的问题,即整体中的某些部位不太能受力,根据其材料的特点必将车身设计成一体式整体结构,这种结构设计可以营造极轻量的车身重量,但同时会有较大的发动机振荡传入车厢,其材料价格昂贵,手工张贴工艺效率低,报废期后碳纤维无法回收利用。
主要用于批量少的高端乘用车上。
如兰博基尼、法拉利等车上。
2)、玻璃钢车身结构:玻璃钢材料与碳纤维一样,呈纤维布的形状,其制作工艺大都采用手工张贴制作工艺,它集合了碳纤维所有的缺点,车身结构只能设计成一体式整体结构,由于其强度远低于碳纤维,一般只用汽车的零部件、外蒙皮等附件上。
大客车的前后围蒙皮常用玻璃钢来制作,是因为客车产量少,蒙皮面积又大,不宜开模,只能适应玻璃钢的手工工艺。
3)、铝管式车身结构。
利用铝材可挤压成型材的特点,事先挤压成各种所需截面的型材,此类车身结构的特点大都是“骨架加蒙皮”(板梁式)的形式存在,如以奥迪R8全铝车身为例,它们的ASF车身结构在外型上基本是一体式铝制蒙皮的构造,铝型材骨架本身已经勾勒了车身的线条,与一体式车身稍有不同的是少了一些一体压制的车身内板件,取而代之的是增加大量的铝型材结构分布。
根据奥迪公布的数据,使用全铝车身ASF的R8比使用传统一体式钢制车架的车辆能减轻高达40%的车架重量,与此同时整体车架的刚度也有40%的增加。
而湖南南车时代设计的高铁全铝车身却采用了骨架与蒙皮结合于一体的铝型材结构(型材式),其强度可佳,但其重量与钢结构一样重。
湖南晟通集团汽车工程研究院研制全铝车身12m公交车,采用了“板梁式”与“型材式”相结合的结构形式,在达到与钢制车身一样强度的前提下,其车身质量减少了50%,整备质量减少30%,满载质量减少了20%,其节能效果明显,达到了国内外先进技术水平。
4)、铝板式车身结构:铝板式车身结构与传统的钢板式车身结构是一样的,板材通过液压成形各种内外板,然后将内外板结合在一起,钢板车身是焊接的,而铝板车身则是通过一种环氧树脂将铝制内外板刚硬地结合起来,坚固度高得出奇,经过撞击试验,而扭曲的车身没有一处结合环氧树脂的地方崩断。
另外还能够避免以焊接方式连接铝件,可以用上薄一点的铝材,进一步的降低车架的重量。
其缺点是铝的压延性太差,液压成形工艺复杂,成本高。
如全新的(2013款)第四代揽胜全铝车身就是采用了此种结构技术与连接方式。
总之,通过以往使用经验与综合条件分析,采用铝制的“骨架+蒙皮”的车身结构设计,再配合型材截面优化、连接工艺优化和结构拓扑优化,是目前实现汽车轻量化设计的最佳解决方案。
四、骨架与蒙皮的成形工艺以下再探讨一下关于全铝车身的骨架与蒙皮制作工艺。
1)、车身骨架成形工艺车身骨架由铝合金材料通过挤压模挤压出各种断面的闭口或开口的长条形结构型材(是钢材无法办到的),可根据需要锯切任意长度。
这种铝型材还要根据车身结构需要进行变截面变形加工,达到车身结构形状的要求。
于是一种“型材液压成形”技术应声而生。
型材液压成形技术应用主要为底盘大梁、车身结构、各系统零部件的骨架变形加工,因其具备高刚性、尺寸精度与稳定性高、较为耐蚀、工件数少、制作过程简化、成本降低等优点,该技术在汽车制造业广泛应用。
此技术保证了零部件精准的尺寸和形状,在充分利用空间、赢得更多轴力度和硬度的同时,减轻了重量。
由于型材液压成形技术不仅简化了模具结构,还减少了模具副数,改善了材料严重变薄的状况,提高了产品质量,大幅度降低了生产成本,因此型材液压成形零部件需求快速增加。
2004年北美生产的典型车型中将有50%结构体零件采用型材液压成形技术制造。
以型材液压成形技术制造结构件的车型,经碰撞测试结果,其安全性比传统的“板材冲压”制造结构件要好,同时整车质量有了大幅度的降低。
因此在北美、欧洲制造的轿车、客车、高铁中,空心轻体的铝型材构件在轿车总量的比例已从15年前的10%上升到20%,而在货车、客车、专用汽车、越野吉普车等的比例已达到70%以上。
梁柱结构是车身骨架的基本承载单元,在车身总成中所占比例较高。
评价轻量化对刚度的影响程度可使用SME(Stiffness Mass Efficient)值,即“单位质量所具有的刚度值”进行比较。
SME 值越高,表明该结构在保持刚度不变的情况下轻量化效果越好,反之亦然。
比如:铝材与钢材相比,如果用铝材制作的结构件,其强度大于同等质量的钢材结构件30%。
所以说,如果保持与钢结构件同等强度前提下,其铝结构件要轻30%左右。
从结构轻量化途径考虑,在满足空间尺寸限制的前提下,我们还可以从“型材截面优化”方面来增加其结构件的强度(钢制型材无法办到的),如增加矩形截面薄壁梁的高度为提高其弯曲和扭转刚度的最佳方案,增加宽度仅能提高其扭转刚度,但改变壁厚没有效果。
如增加矩形截面薄壁梁中的筋板个数为提高其弯曲和扭转刚度的最佳方案,但改变壁厚没有效果。
如增加矩形截面薄壁梁中的筋板形状为提高其弯曲和扭转刚度的最佳方案,但改变壁厚没有效果。
如增加圆筒截面的直径为提高其弯曲和扭转刚度的最佳方案,但改变壁厚没有效果。
与上述闭口情况相反,对于任意开口截面,增加壁厚为提高其扭转刚度的最佳方案,但开口型材的扭转刚度远远小于闭口型材。