转炉烟气复合除尘系统的制作流程
转炉案例介绍:转炉一次烟气(含大量煤气)系统流程
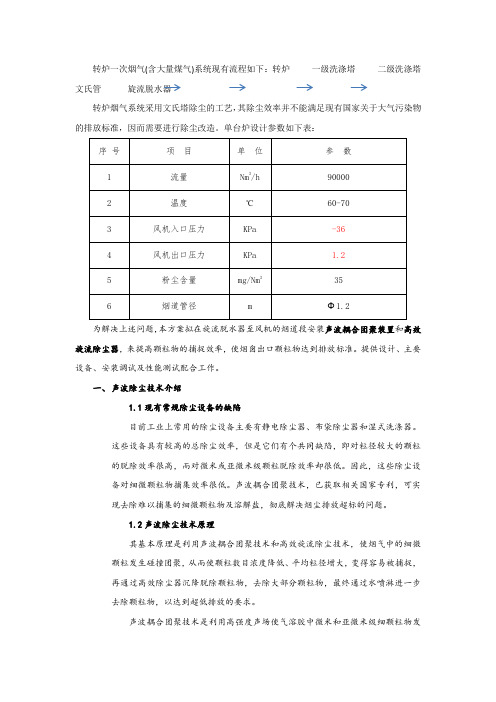
转炉一次烟气(含大量煤气)系统现有流程如下:转炉一级洗涤塔二级洗涤塔文氏管旋流脱水器转炉烟气系统采用文氏塔除尘的工艺,其除尘效率并不能满足现有国家关于大气污染物的排放标准,因而需要进行除尘改造。
单台炉设计参数如下表:为解决上述问题,本方案拟在旋流脱水器至风机的烟道段安装声波耦合团聚装置和高效旋流除尘器,来提高颗粒物的捕捉效率,使烟囱出口颗粒物达到排放标准。
提供设计、主要设备、安装调试及性能测试配合工作。
一、声波除尘技术介绍1.1现有常规除尘设备的缺陷目前工业上常用的除尘设备主要有静电除尘器、布袋除尘器和湿式洗涤器。
这些设备具有较高的总除尘效率,但是它们有个共同缺陷,即对粒径较大的颗粒的脱除效率很高,而对微米或亚微米级颗粒脱除效率却很低。
因此,这些除尘设备对细微颗粒物捕集效率很低。
声波耦合团聚技术,已获取相关国家专利,可实现去除难以捕集的细微颗粒物及溶解盐,彻底解决烟尘排放超标的问题。
1.2声波除尘技术原理其基本原理是利用声波耦合团聚技术和高效旋流除尘技术,使烟气中的细微颗粒发生碰撞团聚,从而使颗粒数目浓度降低、平均粒径增大,变得容易被捕捉,再通过高效除尘器沉降脱除颗粒物,去除大部分颗粒物,最终通过水喷淋进一步去除颗粒物,以达到超低排放的要求。
声波耦合团聚技术是利用高强度声场使气溶胶中微米和亚微米级细颗粒物发生相对运动并进而提高它们的碰撞团聚速率,由于颗粒表面存在着很强的范德华吸引力,一旦颗粒发生了碰撞,它们便十分可能粘附而形成较大一级的团聚物,使细颗粒物在很短的时间范围内,粒径分布从小尺寸向大尺寸方向迁移,颗粒数目浓度减少,进而增强后续除尘(除雾)设施的脱除效率,原理见下图:声波团聚处理示意 粒运动轨迹图1.3声波团聚技术的应用前景利用声波团聚技术,可去除难以捕集的细微颗粒物及溶解盐,从源头做到深度去除。
多效声波装置应用于烟气深度除尘系统优点: (1)声波团聚技术具有适应性强,可靠性高; (2)一次性投资低,运行及维护费用低; (3)施工周期短,几乎不占“0”米面积;(4)不产生二次污染等诸多优点,可替代其它除尘方式,达到烟气超低排放的要求,同时声波不会对用户设施产生任何的副作用,对用户运行维护不会增加任何的负担。
转炉除尘工艺流程
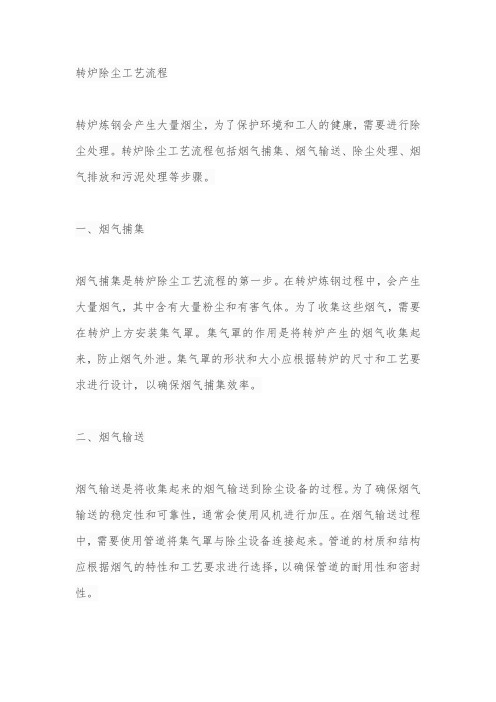
转炉除尘工艺流程转炉炼钢会产生大量烟尘,为了保护环境和工人的健康,需要进行除尘处理。
转炉除尘工艺流程包括烟气捕集、烟气输送、除尘处理、烟气排放和污泥处理等步骤。
一、烟气捕集烟气捕集是转炉除尘工艺流程的第一步。
在转炉炼钢过程中,会产生大量烟气,其中含有大量粉尘和有害气体。
为了收集这些烟气,需要在转炉上方安装集气罩。
集气罩的作用是将转炉产生的烟气收集起来,防止烟气外泄。
集气罩的形状和大小应根据转炉的尺寸和工艺要求进行设计,以确保烟气捕集效率。
二、烟气输送烟气输送是将收集起来的烟气输送到除尘设备的过程。
为了确保烟气输送的稳定性和可靠性,通常会使用风机进行加压。
在烟气输送过程中,需要使用管道将集气罩与除尘设备连接起来。
管道的材质和结构应根据烟气的特性和工艺要求进行选择,以确保管道的耐用性和密封性。
三、除尘处理除尘处理是转炉除尘工艺流程的核心环节。
在除尘处理过程中,通常会采用湿法除尘或干法除尘两种方法。
湿法除尘是通过水雾将烟气中的粉尘沉降下来,达到净化烟气的目的。
干法除尘是通过过滤器将烟气中的粉尘过滤掉,从而达到净化烟气的目的。
具体的除尘工艺应根据钢厂的实际情况和工艺要求进行选择,以达到最佳的除尘效果。
四、烟气排放经过除尘处理后的烟气可以排放到大气中。
在排放前,应对烟气进行监测,以确保排放的烟气符合环保标准。
如果监测发现烟气中有超标的有害气体,需要对排放的烟气进行处理,以达到环保要求。
另外,还需要对排放的烟气进行降温处理,以防止烟气温度过高引起周围环境的热污染。
五、污泥处理转炉除尘工艺流程中会产生大量的污泥,需要进行处理。
污泥处理的目的是将污泥中的有用物质回收利用,同时减少污泥对环境的影响。
具体的污泥处理方法应根据污泥的性质和钢厂的实际情况进行选择,常见的污泥处理方法包括脱水、堆肥、焚烧等。
处理后的污泥可以用于填埋、土地改良等用途,以实现资源的循环利用。
转炉、混铁炉除尘系统设计方案
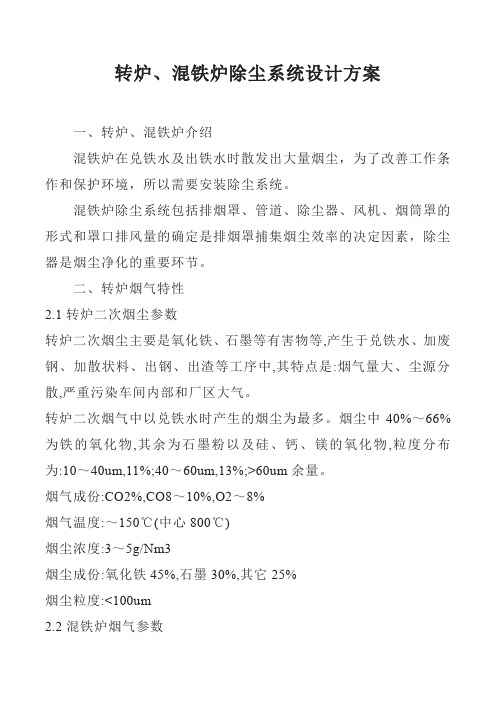
转炉、混铁炉除尘系统设计方案一、转炉、混铁炉介绍混铁炉在兑铁水及出铁水时散发出大量烟尘,为了改善工作条作和保护环境,所以需要安装除尘系统。
混铁炉除尘系统包括排烟罩、管道、除尘器、风机、烟筒罩的形式和罩口排风量的确定是排烟罩捕集烟尘效率的决定因素,除尘器是烟尘净化的重要环节。
二、转炉烟气特性2.1转炉二次烟尘参数转炉二次烟尘主要是氧化铁、石墨等有害物等,产生于兑铁水、加废钢、加散状料、出钢、出渣等工序中,其特点是:烟气量大、尘源分散,严重污染车间内部和厂区大气。
转炉二次烟气中以兑铁水时产生的烟尘为最多。
烟尘中40%~66%为铁的氧化物,其余为石墨粉以及硅、钙、镁的氧化物,粒度分布为:10~40um,11%;40~60um,13%;>60um余量。
烟气成份:CO2%,CO8~10%,O2~8%烟气温度:~150℃(中心800℃)烟尘浓度:3~5g/Nm3烟尘成份:氧化铁45%,石墨30%,其它25%烟尘粒度:<100um2.2混铁炉烟气参数混铁炉烟气含尘浓度:兑铁水时久2~5g/Nm3,出铁水时约1g/Nm3。
烟尘成分:C30%~45%;TFe40%~50%;其它3%~12%。
烟气密度:113kg/Nm3。
烟气温度(沿铁水口垂直中心):兑铁水口中心~1200℃,兑铁水口上部2~3m300~500℃,出铁水口上部160~200℃。
烟尘粒度:从混铁炉排出的烟尘,粒度大于20um的粉尘80%以上,粒度小于20um的粉尘不足20%。
烟尘粒度组成如下表所列。
三、转炉二次烟气除尘3.1除尘工艺流程二次烟气除尘采用干法除尘工艺。
流程是:含烟尘气体→炉前及炉后排烟罩→除尘管道→布袋除尘器→除尘风机→消声器→烟囱→大气。
3.2排烟罩转炉二次烟气排烟罩分炉前排烟罩和炉后排烟罩。
炉前排烟罩设置在炉前防烟室内,炉后排烟罩设置在炉后防烟室侧。
采用管道连接为一体。
炉前烟尘捕集器为方形管道,设置在转炉上部防烟室内,在转炉进料口位置下方开口捕集烟气,分左右两部分。
浅析转炉烟气干法除尘工艺技术
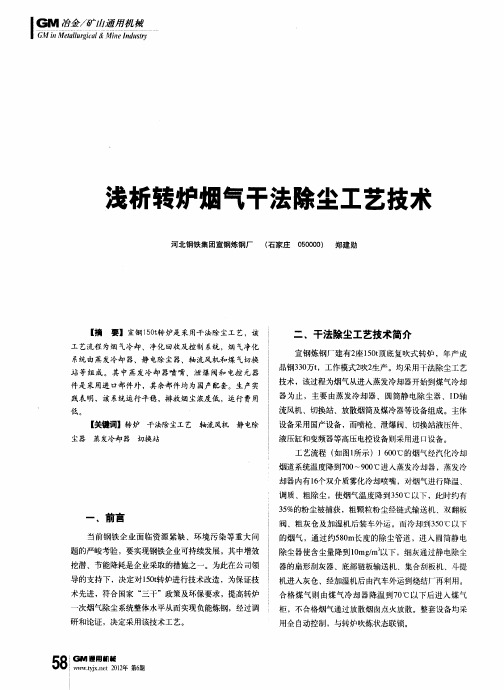
一
的烟气,通过约50 长度的除尘管道,进人圆筒静电 8m
除尘器使含 尘量 降到 lmg ,细灰通过静 电除尘 O / 以下 m 器的扇形刮灰器 、底部链板输 送机 、 合刮板机 、斗提 集 机进入灰仓 、经加湿机后 由汽车外运到烧结 厂再利用 。
除尘 :重 力和 离心 力作 用 。蒸发冷 却器 进 口处水
()轴流风机 轴 流风机 为干法净 化 回收 系统提 3 供动力来源 ,它将转炉在生产过程 中产生的烟气和灰尘 吸到除尘器内 ,通过除尘器对转炉烟气进行净化 ,净化 后的转炉烟气分别送往煤气柜或者排放到大气内。
采 用轴流 风机 是 由于干 法净化 回收 系统 的 系统阻
滴对 通过 的烟 尘进行润湿并将粗颗粒分离 出去 ,达到初 步除尘的 目的。而 沉积在蒸发冷却器底部的粉尘则 由链 式输送机 排出。 烟 气调 质 :蒸发 后 的水蒸 汽 中含有 大量 的带 电负 离子 , 有效提 高烟 气中的电离效果 ,粉尘中水分的增 可
作原理如下 。
图1 工艺流程
高压 硅整流 变压 器和 其控制 系统 ,施 加给放 电极 负 的高压 ,使 得在放 电极 和收 尘极之 间形 成 负高压 电 场 。当含尘烟 气进入静 电除 尘器后 ,带电离子 的气体 则 被 电离 ,在 电场 力的作用下 ,向极性相 反的方 向运动 。 气体正离子很快被放 电极捕集 ,而大量 气体 负离子在 电 场力作用下 向收尘极运动 ,气体 负离子在运动过程 中与 粉尘碰撞并附着在粉尘上 ,使粉尘荷 电,荷 电粉尘 向收 尘极运动直至被收尘极捕获 。
【 关键词l转炉 干法除尘工艺 轴流风机 静 电除
尘器 蒸发冷却器 切换站
烟气除尘工艺流程

烟气除尘工艺流程
《烟气除尘工艺流程》
在工业生产过程中,烟气是不可避免地产生的,而其中含有的颗粒物和污染物质对环境和人体健康都有一定的危害。
因此,烟气除尘工艺成为工业生产中非常重要的环保措施之一。
下面我们将介绍一下烟气除尘工艺的基本流程。
首先是预处理阶段,对烟气进行冷却和湿化处理,以适应后续的除尘处理工艺。
其次是除尘器的选择,一般采用的是静电除尘、布袋除尘、电除尘、湿式电除尘等多种方法。
其中,静电除尘器是将带电粒子和气体分离的一种设备,通过高压电场产生的电场力使颗粒物被集中带电,再通过电极板和除尘器壁面的带电金属网收集下来。
而布袋除尘器则是通过将含尘气体通过滤袋导致颗粒物沉降在滤袋上,净化气体通过滤袋后被排放。
至于湿式电除尘和电除尘,分别是通过湿式方式和电场力将颗粒物从气流中去除。
接下来是后处理阶段,对除尘后的废气进行进一步处理,以确保排放的气体符合环保要求。
例如,可采用活性炭吸附、湿式脱硫等技术进行进一步的污染物处理。
通过以上工艺流程,烟气中的颗粒物和污染物质得以有效去除,保障了环境的清洁和人体健康。
同时,随着科技的不断进步和环保要求的提高,烟气除尘工艺也在不断完善和创新,为工业生产的环保发展提供了更加可靠和高效的解决方案。
转炉二次除尘

钢梁、钢支架,对原有平台、屋架、钢柱 和室外管道支架进行加固、改造处理。 新增加部分支架。
结构形式
增加的转炉二次除尘及混铁炉除尘设施,
基础采用钢筋混凝土独立结构或桩基。 30m烟囱采用钢结构;管道支架采用钢 结构。 风机房采用框架结构,基础采用钢筋混 凝土独立结构或桩基。 仪表中控室采用砖混结构,基础为钢筋 混凝土独立柱基或桩基。
项目实施后达到的目标
大气污染物:转炉烟气以及混铁炉烟气经过干式
净化除尘系统后,含尘量<50mg/m3,达标排放。 经除尘处理,转炉和混铁炉操作台的含尘量 <10mg/m3,符合国家卫生标准。 固体污染物 :净化捕集后的烟尘,成分以铁氧 化物为主,其余为石灰粉及石墨碳片,加湿处理 后由汽车运输至烧结车间进行配料利用,没有废 物外排。
方案一图纸
推荐方案
根据施工难度、管道改造数量、对周围建
筑的影响及占地等各方面综合考虑,建议 采用方案一。 总用地面积4500m2, 总建筑面积650m2, 建构筑占地面积1400m2, 道路面积900m2, 建筑密度31.1%, 绿化面积900m2, 绿化率为20.0%。
低速四个档位。 转炉二次除尘风机速度控制信号由转炉氧枪 的提升、下降决定。 当转炉氧枪提起时,给转炉二次收尘风机一 个提速信号;当转炉氧枪降下时,给出转炉 收尘风机延时2min的降速信号。转炉炉后烟 罩阀门开、关由转炉倾动决定,当转炉向后 倾动达到出钢侧时阀门打开;当转炉由后倾 状态回到垂直位时,阀门关闭。
炉前烟尘捕集器
设置在炉前防烟室内,挡火门内侧上部,固
定于钢支柱上。 烟尘捕集器为矩形的烟气管道,在转炉进料 口位置下方开口捕集烟气,分左右两部分, 并设置活动挡烟帘。 炉前烟尘捕集器采用耐热材料制作,内部衬 耐火材料。 活动挡烟帘采用铁链及无缝钢管制作。
转炉湿法一次除尘的原理

转炉湿法一次除尘的原理转炉湿法一次除尘是一种常用的工业烟气净化技术,适用于钢铁冶炼等高温烟气处理过程中的颗粒物和废气治理。
该技术主要通过在烟气中加入水喷淋,利用水的吸附作用,将大部分的颗粒物和有毒气体捕集并去除,进而净化烟气,保护环境和人们的健康。
转炉湿法一次除尘的原理和过程如下:1. 烟气进入上部排烟筒:烟气从转炉排出后,进入上部排烟筒,进入除尘器系统。
排烟筒中设置出口阀门,通过调节阀门的开启程度可调节烟气的流速和烟道压降。
2. 喷水系统:在进入除尘器之前,烟气会通过灭火器喷水系统。
该系统主要通过调节水的喷淋量和角度,将烟气中的颗粒物湿化,使其变得更易沉积在水滴上。
3. 除尘轮:烟气进入除尘器之后,会遇到除尘轮。
除尘轮是一个旋转的金属片,通过高速旋转搅拌烟气和水滴,使颗粒物与水滴进行充分接触和湿化,同时也增加了烟气的涡流,促进颗粒物的沉降。
4. 引导板:为了增加除尘效果,除尘器中还设置了一系列的引导板。
引导板有助于改变烟气的流动方向,使烟气在除尘器中停留更长的时间,增加颗粒物与水滴的接触机会。
5. 水滴与颗粒物的接触和混合:在除尘轮和引导板的作用下,烟气中的颗粒物与喷洒的水滴充分接触和混合。
水滴中的溶解金属离子可以与灰尘中的无机物相结合形成水溶解物,以及可溶解气体和有机物的吸附效果。
6. 颗粒物的沉降和去除:由于水滴中的重力作用以及旋转力的作用,颗粒物会与水滴混合物一起快速沉降,并通过排水系统进行排除。
除尘器中设置了集水槽和排水管道,将带有颗粒物的水送入沉淀池和过滤装置,再经过处理后排放或回收。
7. 净化后的烟气排出:经过除尘处理后,烟气中的大部分颗粒物和废气得以去除,烟气成为更加清洁和无害的排放物。
转炉湿法一次除尘的优点包括:除尘效果好,可以同时去除颗粒物和有毒气体;低能耗,不需要额外的能量供应;操作简单,维护方便;净化效果稳定,可靠性高。
然而,转炉湿法一次除尘也存在一些缺点,如水的消耗量大,对水源的依赖性较强;处理后的废水需要进一步处理或回收;对于细颗粒物的去除效果相对较差等。
转炉烟气净化系统的综和治理待续

转炉烟气净化系统的综合治理一、工艺流程及设备简况 (2)二、存在的主要问题 (4)三、原因分析及改进措施 (4)1、主要原因分析 (4)2、主要改进措施 (11)四、系统的综合治理 (12)五、改造治理效果 (13)六、后期跟踪和继续研究的问题 (13)一、工艺流程及设备简况鞍钢一炼钢厂转炉烟气净化系统(一次除尘系统)为双文湿法烟气净化系统。
冶炼过程中产生的高温烟气经固定烟罩、汽化冷却烟道降温后,进入一级文氏管(以下简称“一文”)进行降温和粗除尘,经一级90°弯头脱水器脱水后,进入二级文氏管(以下简称“二文”)进行精除尘,之后烟气依次进入二级90°弯头脱水器和折流板脱水器脱水后,进行煤气回收或点火放散。
一文和二文所排污水经由高架污水流槽流向污环水处理系统,污水经过污环水处理后重新给一文、二文供水,由此形成一个循环水流程。
其工艺流程如图1。
图1 转炉烟气净化系统工艺流程一文的主要作用是降温和粗除尘,可使温度为800-1000℃的烟气到达文氏管喉口处时很快冷却到70-80℃,除尘效率为95%左右;二文的R-D阀是精除尘设备,除尘精度达到99.9%,因此二文除尘效率可达99.9%。
文氏管降温除尘原理:烟气流经文氏管的收缩段时,因截面积逐渐收缩而被加速,高速紊流的烟气在喉口冲击由喷嘴喷入的雾状水幕,使之雾化成更细小的水滴,细小的水滴吸收烟气的热量而蒸发成水雾并使烟气降温,水雾经过喉口后变成大颗粒的含尘液滴,由于污水的密度比烟气大的多,又经过扩张段降低了烟气速度,再经过文氏管后面脱水器利用重力、惯性力和离心力的沉降作用,使含尘水滴与烟气分离,从而达到净化烟气的目的。
一文的收缩段外侧安装有一个溢流水箱(溢流盆),水箱内的水始终保持满溢状态,溢出的水沿着收缩段内壁流下形成一层水膜,对一文收缩段起降温保护作用,溢流盆的作用如下:(1)溢流水在文氏管收缩段内壁形成一层水膜,从而防止烟尘在管壁上的干湿交界处结垢造成堵塞;(2)溢流盆为开口式,一旦发生爆炸可以泄压;(3)调节汽化冷却烟道因热胀冷缩而引起的设备位移变形;文氏管除尘器的除尘过程可分为雾化、凝聚和脱水三个环节。
- 1、下载文档前请自行甄别文档内容的完整性,平台不提供额外的编辑、内容补充、找答案等附加服务。
- 2、"仅部分预览"的文档,不可在线预览部分如存在完整性等问题,可反馈申请退款(可完整预览的文档不适用该条件!)。
- 3、如文档侵犯您的权益,请联系客服反馈,我们会尽快为您处理(人工客服工作时间:9:00-18:30)。
本技术新型涉及一种转炉烟气复合除尘系统,所述转炉烟气复合除尘系统包括:汽化冷却烟道,所述汽化冷却烟道的入口端连接至转炉;蒸发冷却器,所述蒸发冷却器的烟气入口与所述汽化冷却烟道的出口端连接;静电除尘器,所述静电除尘器的烟气入口与所述蒸发冷却器的烟气出口连通;风机,所述风机的入口与所述静电除尘器的烟气出口连通;烟气冷却器,所述烟气冷却器的入口与所述风机的出口连通;煤气柜,所述煤气柜通过设置有第一阀门的管道与所述烟气冷却器的出口连通;放散烟筒,所述放散烟筒通过设置有第二阀门的管道与所述烟气冷却器的出口连通。
权利要求书1.一种转炉烟气复合除尘系统,其特征在于,所述转炉烟气复合除尘系统包括:汽化冷却烟道,所述汽化冷却烟道的入口端连接至转炉;蒸发冷却器,所述蒸发冷却器的烟气入口与所述汽化冷却烟道的出口端连接;静电除尘器,所述静电除尘器的烟气入口与所述蒸发冷却器的烟气出口连通;风机,所述风机的入口与所述静电除尘器的烟气出口连通;烟气冷却器,所述烟气冷却器的入口与所述风机的出口连通;煤气柜,所述煤气柜通过设置有第一阀门的管道与所述烟气冷却器的出口连通;放散烟筒,所述放散烟筒通过设置有第二阀门的管道与所述烟气冷却器的所述出口连通。
2.根据权利要求1所述的转炉烟气复合除尘系统,其特征在于,将所述风机的出口与所述烟气冷却器的入口连通的管道设置有氧气分析仪和一氧化碳分析仪。
3.根据权利要求1所述的转炉烟气复合除尘系统,其特征在于,所述第一阀门和所述第二阀门均为杯形阀。
4.根据权利要求1所述的转炉烟气复合除尘系统,其特征在于,所述烟气冷却器使用雾化喷水对其中的烟气进行冷却,雾化喷水量由电脑自动控制。
5.根据权利要求1所述的转炉烟气复合除尘系统,其特征在于,经过所述烟气冷却器排出的烟气的温度介于60℃至90℃之间。
6.根据权利要求1所述的转炉烟气复合除尘系统,其特征在于,所述蒸发冷却器设置有粗除尘灰输送装置,用于排出所述蒸发冷却器中产生的除尘灰。
7.根据权利要求1所述的转炉烟气复合除尘系统,其特征在于,所述静电除尘器设置有细除尘灰输送装置,用于排出所述静电除尘器中产生的除尘灰。
8.根据权利要求1至7中的任一项所述的转炉烟气复合除尘系统,其特征在于,所述放散烟筒与所述烟气冷却器之间的距离小于所述煤气柜与所述烟气冷却器之间的距离。
技术说明书转炉烟气复合除尘系统技术领域本技术新型涉及冶金行业除尘技术领域,具体地涉及一种转炉烟气复合除尘系统。
背景技术冶金行业炼钢生产中,转炉炼钢属于集散式作业,在一个冶炼周期内烟气量、烟气含尘量及烟气的组分一直在变化中。
一次除尘分为湿法除尘、干法除尘和半干法除尘。
湿法除尘由于吨钢耗新水高、风机阻力大、污水处理量大等先天缺陷,已基本淘汰;半干法除尘污水处理有所减少,但仍然产生二次水污染;干法静电除尘与湿法除尘相比有着明显的节水、节电、维护量低、外排粉尘含量低的优势,受到越来越多的关注。
现行的干法静电除尘运行工艺流程为:转炉烟气经过汽化冷却系统,温度降至800-1100℃后进入蒸发冷却器。
蒸发冷却器内有雾化冷却喷嘴对烟气进行降温、调质、粗除尘,使温度降低到230-280℃,同时有30-40%的粉尘在蒸发冷却器的作用下被捕捉,形成的粗颗粒粉尘被送到粗灰仓外运。
经冷却、粗除尘和调质后的烟气进入静电除尘器,烟气经静电除尘器除尘后含尘量降至10mg/m3以下。
静电除尘器收集的细灰送到细灰仓外运,经过静电除尘器精除尘的合格烟气经过煤气冷却器降温到70℃以下进入煤气柜,不合格烟气通过火炬装置放散。
整套系统采用自动控制,并与转炉的控制相关联。
这种干法静电除尘工艺流程特点为:不合格烟气没有经过煤气冷却器直接放散。
煤气冷却器的作用有三:首先,将煤气在冷却器内冷却到70℃以下;其次,通常的电除尘设施对2.5微米(PM2.5)以下的细颗粒物作用很小,对1微米(PM1.0)以下的超细颗粒物没有作用,在煤气冷却过程中的电除尘器中已经离子化的粉尘颗粒被冷却水捕集下来,起到了辅助的煤气净化作用;另外,在煤气冷却过程中转炉烟气中含有0.1-0.5%的硫化物、包括二氧化硫等被冷却水捕集下来,起到脱硫的作用。
因此没有经过煤气冷却器直接放散的不合格烟气还含有少量的粉尘和硫化物,长期排放对环境会造成不利影响。
实用新型内容本技术新型的目的是至少解决上述问题之一,该目的通过以下技术方案实现:本技术新型提出一种转炉烟气复合除尘系统,所述转炉烟气复合除尘系统包括:汽化冷却烟道,所述汽化冷却烟道的入口端连接至转炉;蒸发冷却器,所述蒸发冷却器的烟气入口与所述汽化冷却烟道的出口端连接;静电除尘器,所述静电除尘器的烟气入口与所述蒸发冷却器的烟气出口连通;风机,所述风机的入口与所述静电除尘器的烟气出口连通;烟气冷却器,所述烟气冷却器的入口与所述风机的出口连通;煤气柜,所述煤气柜通过设置有第一阀门的管道与所述烟气冷却器的出口连通;放散烟筒,所述放散烟筒通过设置有第二阀门的管道与所述烟气冷却器的所述出口连通。
优选地,将所述风机的出口与所述烟气冷却器的入口连通的管道设置有氧气分析仪和一氧化碳分析仪。
进一步优选地,所述第一阀门和所述第二阀门均为杯形阀。
进一步优选地,所述烟气冷却器使用雾化喷水对其中的烟气进行冷却,雾化喷水量由电脑自动控制。
进一步优选地,经过所述烟气冷却器排出的烟气的温度介于60℃至90°C之间。
进一步优选地,所述蒸发冷却器设置有粗除尘灰输送装置,用于排出所述蒸发冷却器中产生的除尘灰。
进一步优选地,所述静电除尘器设置有细除尘灰输送装置,用于排出所述静电除尘器中产生的除尘灰。
更进一步优选地,,所述放散烟筒与所述烟气冷却器之间的距离小于所述煤气柜与所述烟气冷却器之间的距离。
本技术新型的优点在于:通过调整静电除尘的工艺流程,优化相关工艺参数,发挥煤气冷却器的除尘净化作用,将煤气冷却器设置在放散烟筒的上游,使得放散的烟气先经过煤气冷却器进行湿法除尘,进一步去除烟尘及硫化物后进行放散,减少雾霾的发生,保护环境,解决背景技术中存在的问题。
附图说明通过阅读下文优选实施方式的详细描述,各种其他的优点和益处对于本领域普通技术人员将变得清楚明了。
附图仅用于示出优选实施方式的目的,而并不认为是对本技术新型的限制。
而且在整个附图中,用相同的参考符号表示相同的部件。
在附图中:图1示出了根据本技术新型实施方式的转炉烟气复合除尘系统的原理示意图。
具体实施方式下面将参照附图更详细地描述本公开的示例性实施方式。
虽然附图中显示了本公开的示例性实施方式,然而应当理解,可以以各种形式实现本公开而不应被这里阐述的实施方式所限制。
相反,提供这些实施方式是为了能够更透彻地理解本公开,并且能够将本公开的范围完整的传达给本领域的技术人员。
根据本技术新型的实施方式,提出一种转炉烟气复合除尘系统。
如图1所示,本技术新型的转炉烟气复合除尘系统包括:汽化冷却烟道2、蒸发冷却器3、静电除尘器5、风机7、烟气冷却器10、煤气柜13和放散烟筒14。
其中,汽化冷却烟道2的入口端连接至转炉1。
蒸发冷却器3的烟气入口与汽化冷却烟道2的出口端连接。
静电除尘器5的入口与蒸发冷却器3的烟气出口连通。
风机7的入口与静电除尘器5的烟气出口连通。
烟气冷却器10的入口与风机7的出口连通。
烟气冷却器10的出口分别与煤气柜13和放散烟筒14连通。
其中,煤气柜13通过设置有第一阀门11的管道与烟气冷却器10的出口连通;放散烟筒14通过设置有第二阀门的管道与烟气冷却器10的出口连通。
根据本技术新型的实施方式,蒸发冷却器3设置有粗除尘灰输送装置4,粗除尘灰输送装置4与蒸发冷却器3的除尘灰出口连接,用于排出蒸发冷却器3中产生的除尘灰;静电除尘器5设置有细除尘灰输送装置6,细除尘灰输送装置6与静电除尘器5的除尘灰出口连接,用于排出静电除尘器5中产生的除尘灰。
根据本技术新型的优选的实施方式,连通风机7的出口与烟气冷却器10的入口的管道设置有氧气分析仪8和一氧化碳分析仪9,以消除或至少降低冷却水对数据分析的影响。
优选地,第一阀门11和第二阀门12均为杯形阀。
优选地,第一阀门11和第二阀门12能够根据氧气分析仪8测得的氧气浓度和一氧化碳分析仪9测得的一氧化碳浓度执行开启、关闭以及在开启状态下的开度。
根据本技术新型的优选的实施方式,在烟气冷却器10的出口位置设置有额外的氧气分析仪和一氧化碳分析仪,使得第一阀门11和第二阀门12还能够根据由烟气冷却器10处理过的烟气中的氧气和一氧化碳的浓度确定开启、关闭以及在开启状态下的开度,由此控制通过煤气柜13回收的煤气量和通过放散烟筒排放的烟气量。
根据本技术新型的优选地实施方式,烟气冷却器10使用雾化喷水对其中的烟气进行冷却,雾化喷水量由电脑自动控制,例如可以根据氧气分析仪8测得的氧气浓度和一氧化碳分析仪9测得的一氧化碳浓度控制烟气冷却器10中的雾化喷水量。
优选地,烟气冷却器10的入口处可以设置温度传感器,使得烟气冷却器10能够根据进入其中的烟气的氧气浓度、一氧化碳浓度和烟气温度确定雾化喷水量,从而实现对进入其中的烟气进行除尘脱硫。
优选地,经由烟气冷却器10排出的烟气的温度介于60℃至90℃。
根据本技术新型的优选地实施方式,放散烟筒14设置在尽可能靠近烟气冷却器10的位置,从而减少放散烟气的降温,有利于烟气的扩散和排放。
煤气柜13设置在尽可能远离烟气冷却器10的位置,从而能够进一步降低回收的煤气的温度。
优选地,放散烟筒14与烟气冷却器10之间的距离小于煤气柜与烟气冷却器10之间的距离。
具体地,在转炉炼钢过程中,转炉1中的烟气在风机7的抽引作用下,经过汽化冷却烟道2使烟气温度降至800-1100℃并进入蒸发冷却器3;蒸发冷却器3对烟气进行降温、调质、粗除尘,使烟气温度降低到230-280℃,同时有30-40%的粉尘在蒸发冷却器3的作用下被捕捉;经冷却、粗除尘和调质后的烟气进入静电除尘器5,烟气经静电除尘器5除尘后含尘量降至10mg/m3以下,静电除尘器5出口烟气温度控制在120-160℃;经过静电除尘器5除尘的烟气通过设置在风机7与烟气冷却器10之间的氧气分析仪8和一氧化碳分析仪9对其中的氧气和一氧化碳含量进行精确分析,并进入烟气冷却器10进行最后的除尘脱硫,从烟气冷却器10排出的烟气的温度降到60-90℃,合格烟气进入煤气柜13,不合格烟气通过放散烟筒14放散。
整套转炉烟气复合除尘系统采用自动控制,与转炉自身的控制相关联。
以上所述,仅为本技术新型较佳的具体实施方式,但本技术新型的保护范围并不局限于此,任何熟悉本技术领域的技术人员在本技术新型揭露的技术范围内,可轻易想到的变化或替换,都应涵盖在本技术新型的保护范围之内。
因此,本技术新型的保护范围应以所述权利要求的保护范围为准。