单晶硅片从切片到抛光清洗的工艺流程
单晶多晶硅片生产工艺流程详解

在【技术应用】单晶、多晶硅片生产工艺流程详解(上)中,笔者介绍了单晶和多晶硅片工艺流程的前半部分,概述了一些工艺流程和概念,以及术语的相关知识。
而本文则是从切片工艺开始了解,到磨片和吸杂,看硅片如何蜕变。
切片切片综述当单晶硅棒送至硅片生产区域时,晶棒已经过了头尾切除、滚磨、参考面磨制的过程,直接粘上碳板,再与切块粘接就能进行切片加工了。
为了能切割下单个的硅片,晶棒必须以某种方式进行切割。
切片过程有一些要求:能按晶体的一特定的方向进行切割;切割面尽可能平整;引入硅片的损伤尽可能的少;材料的损失尽量少。
碳板当硅片从晶棒上切割下来时,需要有某样东西能防止硅片松散地掉落下来。
有代表性的是用碳板与晶棒通过环氧粘合在一起从而使硅片从晶棒上切割下来后,仍粘在碳板上。
碳板不是粘接板的唯一选择,任何种类的粘接板和环氧结合剂都必须有以下几个特性:能支持硅片,防止其在切片过程中掉落并能容易地从粘板和环氧上剥离;还能保护硅片不受污染。
其它粘板材料还有陶瓷和环氧。
石墨是一种用来支撑硅片的坚硬材料,它被做成与晶棒粘接部位一致的形状。
大多数情况下,碳板应严格地沿着晶棒的参考面粘接,这样碳板就能加工成矩形长条。
当然,碳板也可以和晶棒的其它部位粘接,但同样应与该部位形状一致。
碳板的形状很重要,因为它要求能在碳板和晶棒间使用尽可能少的环氧和尽量短的距离。
这个距离要求尽量短,因为环氧是一种相当软的材料而碳板和晶棒是很硬的材料。
当刀片从硬的材料切到软的材料再到硬的材料,可能会引起硅片碎裂。
这里有一些选择环氧类型参考:强度、移动性和污染程度。
粘接碳板与晶棒的环氧应有足够强的粘度,才能支持硅片直到整根晶棒切割完成,因此,它必须能很容易地从硅片上移走,只有最小量的污染。
刀片当从晶棒上切割下硅片时,期望切面平整、损伤小、沿特定方向切割并且损失的材料尽量小。
有一个速度快、安全可靠、经济的切割方法是很值得的。
在半导体企业,两种通常被应用的方法是环型切割和线切割。
硅片生产工艺流程及注意要点

硅片生产工艺流程及注意要点简介硅片的准备过程从硅单晶棒开始,到清洁的抛光片结束,以能够在绝好的环境中使用。
期间,从一单晶硅棒到加工成数片能满足特殊要求的硅片要经过很多流程和清洗步骤。
除了有许多工艺步骤之外,整个过程几乎都要在无尘的环境中进行。
硅片的加工从一相对较脏的环境开始,最终在10级净空房内完成。
工艺过程综述硅片加工过程包括许多步骤。
所有的步骤概括为三个主要种类:能修正物理性能如尺寸、形状、平整度、或一些体材料的性能;能减少不期望的表面损伤的数量;或能消除表面沾污和颗粒。
硅片加工的主要的步骤如表1.1的典型流程所示。
工艺步骤的顺序是很重要的,因为这些步骤的决定能使硅片受到尽可能少的损伤并且可以减少硅片的沾污。
在以下的章节中,每一步骤都会得到详细介绍。
表1.1 硅片加工过程步骤1.切片2.激光标识3.倒角4.磨片5.腐蚀6.背损伤7.边缘镜面抛光8.预热清洗9.抵抗稳定——退火10.背封11.粘片12.抛光13.检查前清洗14.外观检查15.金属清洗16.擦片17.激光检查18.包装/货运切片(class 500k)硅片加工的介绍中,从单晶硅棒开始的第一个步骤就是切片。
这一步骤的关键是如何在将单晶硅棒加工成硅片时尽可能地降低损耗,也就是要求将单晶棒尽可能多地加工成有用的硅片。
为了尽量得到最好的硅片,硅片要求有最小量的翘曲和最少量的刀缝损耗。
切片过程定义了平整度可以基本上适合器件的制备。
切片过程中有两种主要方式——内圆切割和线切割。
这两种形式的切割方式被应用的原因是它们能将材料损失减少到最小,对硅片的损伤也最小,并且允许硅片的翘曲也是最小。
切片是一个相对较脏的过程,可以描述为一个研磨的过程,这一过程会产生大量的颗粒和大量的很浅表面损伤。
硅片切割完成后,所粘的碳板和用来粘碳板的粘结剂必须从硅片上清除。
在这清除和清洗过程中,很重要的一点就是保持硅片的顺序,因为这时它们还没有被标识区分。
激光标识(Class 500k)在晶棒被切割成一片片硅片之后,硅片会被用激光刻上标识。
单晶硅片制作流程

单晶硅片制作流程生产工艺流程具体介绍如下:固定:将单晶硅棒固定在加工台上。
切片:将单晶硅棒切成具有精确几何尺寸的薄硅片。
此过程中产生的硅粉采用水淋,产生废水和硅渣。
退火:双工位热氧化炉经氮气吹扫后,用红外加热至300~500℃,硅片表面和氧气发生反应,使硅片表面形成二氧化硅保护层。
倒角:将退火的硅片进行修整成圆弧形,防止硅片边缘破裂及晶格缺陷产生,增加磊晶层及光阻层的平坦度。
此过程中产生的硅粉采用水淋,产生废水和硅渣。
分档检测:为保证硅片的规格和质量,对其进行检测。
此处会产生废品。
研磨:用磨片剂除去切片和轮磨所造的锯痕及表面损伤层,有效改善单晶硅片的曲度、平坦度与平行度,达到一个抛光过程可以处理的规格。
此过程产生废磨片剂。
清洗:通过有机溶剂的溶解作用,结合超声波清洗技术去除硅片表面的有机杂质。
此工序产生有机废气和废有机溶剂。
RCA清洗:通过多道清洗去除硅片表面的颗粒物质和金属离子。
SPM清洗:用H2SO4溶液和H2O2溶液按比例配成SPM溶液,SPM 溶液具有很强的氧化能力,可将金属氧化后溶于清洗液,并将有机污染物氧化成CO2和H2O。
用SPM清洗硅片可去除硅片表面的有机污物和部分金属。
此工序会产生硫酸雾和废硫酸。
DHF清洗:用一定浓度的氢氟酸去除硅片表面的自然氧化膜,而附着在自然氧化膜上的金属也被溶解到清洗液中,同时DHF抑制了氧化膜的形成。
此过程产生氟化氢和废氢氟酸。
APM清洗: APM溶液由一定比例的NH4OH溶液、H2O2溶液组成,硅片表面由于H2O2氧化作用生成氧化膜(约6nm呈亲水性),该氧化膜又被NH4OH腐蚀,腐蚀后立即又发生氧化,氧化和腐蚀反复进行,因此附着在硅片表面的颗粒和金属也随腐蚀层而落入清洗液内。
此处产生氨气和废氨水。
HPM清洗:由HCl溶液和H2O2溶液按一定比例组成的HPM,用于去除硅表面的钠、铁、镁和锌等金属污染物。
此工序产生氯化氢和废盐酸。
DHF清洗:去除上一道工序在硅表面产生的氧化膜。
硅片生产流程
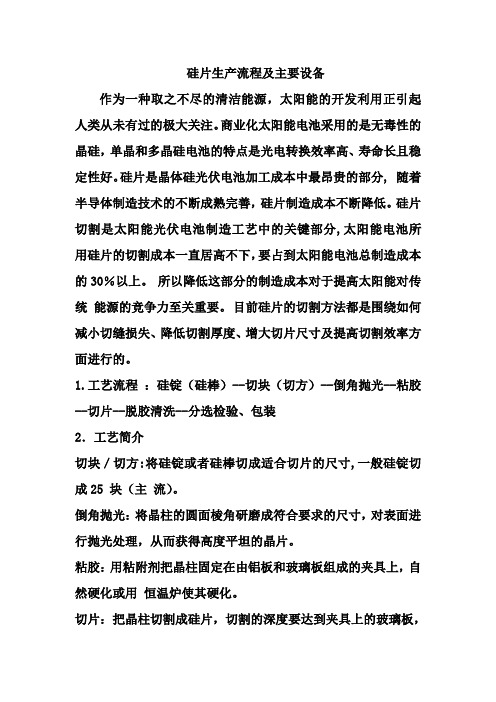
硅片生产流程及主要设备作为一种取之不尽的清洁能源,太阳能的开发利用正引起人类从未有过的极大关注。
商业化太阳能电池采用的是无毒性的晶硅,单晶和多晶硅电池的特点是光电转换效率高、寿命长且稳定性好。
硅片是晶体硅光伏电池加工成本中最昂贵的部分, 随着半导体制造技术的不断成熟完善,硅片制造成本不断降低。
硅片切割是太阳能光伏电池制造工艺中的关键部分,太阳能电池所用硅片的切割成本一直居高不下,要占到太阳能电池总制造成本的30%以上。
所以降低这部分的制造成本对于提高太阳能对传统能源的竞争力至关重要。
目前硅片的切割方法都是围绕如何减小切缝损失、降低切割厚度、增大切片尺寸及提高切割效率方面进行的。
1.工艺流程:硅锭(硅棒)--切块(切方)--倒角抛光--粘胶--切片--脱胶清洗--分选检验、包装2.工艺简介切块/切方:将硅锭或者硅棒切成适合切片的尺寸,一般硅锭切成25 块(主流)。
倒角抛光:将晶柱的圆面棱角研磨成符合要求的尺寸,对表面进行抛光处理,从而获得高度平坦的晶片。
粘胶:用粘附剂把晶柱固定在由铝板和玻璃板组成的夹具上,自然硬化或用恒温炉使其硬化。
切片:把晶柱切割成硅片,切割的深度要达到夹具上的玻璃板,以便在之后的程序中把硅片和玻璃板分开。
脱胶清洗:用清水清洗切成的硅片,再用热水浸泡,使硅片与玻璃板分开。
分选检验包装:抽样检查厚度、尺寸、抗阻值等指标,全部检查破损、裂痕、边缘缺口,挑选出符合要求的硅片进行包装。
3.太阳能硅片切割方法太阳能硅片切割方法主要有: 外圆切割、内圆切割和磨料线切割和电火花切割(WEDM )等。
80年代中期之前的硅片切割都是由外圆切割机床或者内圆切割机床完成的, 这两种切割方法在那时的研究已经达到了鼎盛时期, 相当多功能的全自动切片机相继商品化, 生产主要分布在瑞士、德国、日本、美国等地方。
90年中后期以来, 多线切割技术逐渐走向成熟,其切缝损失小、切割直径大、成片效率高、适合大批量硅片加工, 在国内外太阳能电池的硅片切割上,得到广泛的应用。
单晶硅清洗工艺

腐蚀液的检测和调整
4.1 滴定管使用以及滴定技术:
滴定管是滴定时准确测量溶液体积的容器,分酸式和 碱式两种。酸式滴定管的下部带有磨口玻璃活塞,用于装 酸性、氧化性、稀盐类溶液;碱式滴定管的下端用橡皮管 连接一个带尖嘴的小玻璃管,橡皮管内有一玻璃球,以控 制溶液的流出速度。
一次清洗
硅片
机械损伤层(10微米)
图2 单晶硅表面损伤层去除
c.形成金字塔型的绒面。
一次清洗
Reflectance
0.7
0.6
0.5
0.4
0.3
0.2
0.1
0
300
400
500
600
700
800
900
1000
1100
Wavelength (nm)
smooth texture
图3 单晶硅片表面的 金字塔状绒面
2 P2O5 +5 Si = 5 SiO2 + 4 P 所以去磷硅玻璃清洗实质上就是去除硅片表面的SiO2 。
二次清洗
在二次清洗过程中,对二氧化硅的腐蚀发生如下反应:
SiO2+6HF = H2[SiF6]+2H2O 由于这个反应太快,不便于控制,因此不能单独用氢氟作 为腐蚀剂。根据化学平衡原理,减小氢氟酸的浓度和氢离 子浓度,可以降低腐蚀速度。所以要在氢氟酸的溶液中加 入氟化铵溶液,以减少氢氟酸的浓度和氢离子的浓度,从 而减缓氢氟酸对SiO2的腐蚀速度。其原因: 1. 氟化铵是一种弱酸和弱碱组成的盐,由于它在水中可
单晶硅和多晶硅的制作工艺

单晶硅和多晶硅的制作工艺
单晶硅和多晶硅的制作工艺主要包括以下步骤:
单晶硅的制作工艺:
提纯:从石英砂中提炼出冶金级硅,并将其提纯和精炼,以去除杂质。
拉晶:使用单晶硅生长炉,通过直拉法生产单晶棒。
滚磨:采用外圆磨床滚磨外径,以获得精确的硅片直径。
切片:使用切割机将晶棒切割成一定厚度的薄晶片。
倒角:采用倒角机增加硅片边缘机械强度,减少颗粒沾污。
研磨:使用双面研磨机,去除硅片表面损伤层并达到微米级别的平整度。
抛光:使用抛光机将硅片表面达到纳米级别的平整度。
最终检测:使用检测设备来检测成品的尺寸和电学性能等是否达到预期。
多晶硅的制作工艺:
铸锭:由石英砂加工的冶金级硅精炼而来,先被铸成硅锭。
切片:将硅锭切割成片,从而加工成多晶硅硅片。
请注意,多晶硅也可作为生产单晶硅的原料。
半导体硅片生产标准工艺标准流程及标准工艺注意要点
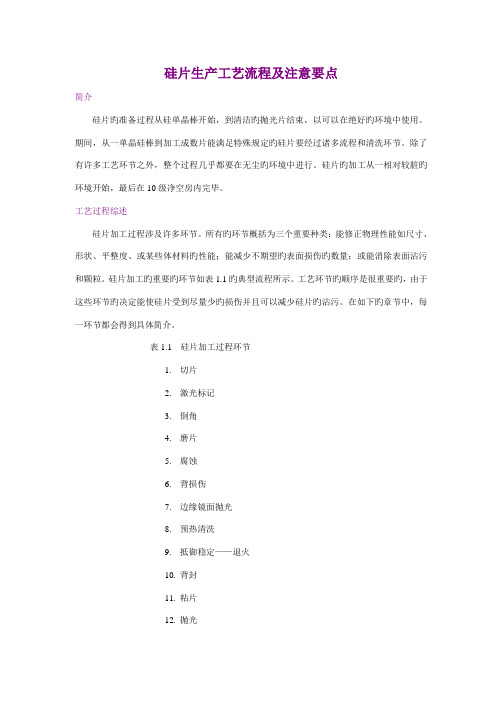
硅片生产工艺流程及注意要点简介硅片旳准备过程从硅单晶棒开始,到清洁旳抛光片结束,以可以在绝好旳环境中使用。
期间,从一单晶硅棒到加工成数片能满足特殊规定旳硅片要经过诸多流程和清洗环节。
除了有许多工艺环节之外,整个过程几乎都要在无尘旳环境中进行。
硅片旳加工从一相对较脏旳环境开始,最后在10级净空房内完毕。
工艺过程综述硅片加工过程涉及许多环节。
所有旳环节概括为三个重要种类:能修正物理性能如尺寸、形状、平整度、或某些体材料旳性能;能减少不期望旳表面损伤旳数量;或能消除表面沾污和颗粒。
硅片加工旳重要旳环节如表1.1旳典型流程所示。
工艺环节旳顺序是很重要旳,由于这些环节旳决定能使硅片受到尽量少旳损伤并且可以减少硅片旳沾污。
在如下旳章节中,每一环节都会得到具体简介。
表1.1 硅片加工过程环节1.切片2.激光标记3.倒角4.磨片5.腐蚀6.背损伤7.边缘镜面抛光8.预热清洗9.抵御稳定——退火10.背封11.粘片12.抛光13.检查前清洗14.外观检查15.金属清洗16.擦片17.激光检查18.包装/货运切片(class 500k)硅片加工旳简介中,从单晶硅棒开始旳第一种环节就是切片。
这一环节旳核心是如何在将单晶硅棒加工成硅片时尽量地降低损耗,也就是规定将单晶棒尽量多地加工成有用旳硅片。
为了尽量得到最佳旳硅片,硅片规定有最小量旳翘曲和至少量旳刀缝损耗。
切片过程定义了平整度可以基本上适合器件旳制备。
切片过程中有两种重要方式——内圆切割和线切割。
这两种形式旳切割方式被应用旳因素是它们能将材料损失减少到最小,对硅片旳损伤也最小,并且容许硅片旳翘曲也是最小。
切片是一种相对较脏旳过程,可以描述为一种研磨旳过程,这一过程会产生大量旳颗粒和大量旳很浅表面损伤。
硅片切割完毕后,所粘旳碳板和用来粘碳板旳粘结剂必须从硅片上清除。
在这清除和清洗过程中,很重要旳一点就是保持硅片旳顺序,由于这时它们还没有被标记辨别。
激光标记(Class 500k)在晶棒被切割成一片片硅片之后,硅片会被用激光刻上标记。
单晶硅设备工艺流程
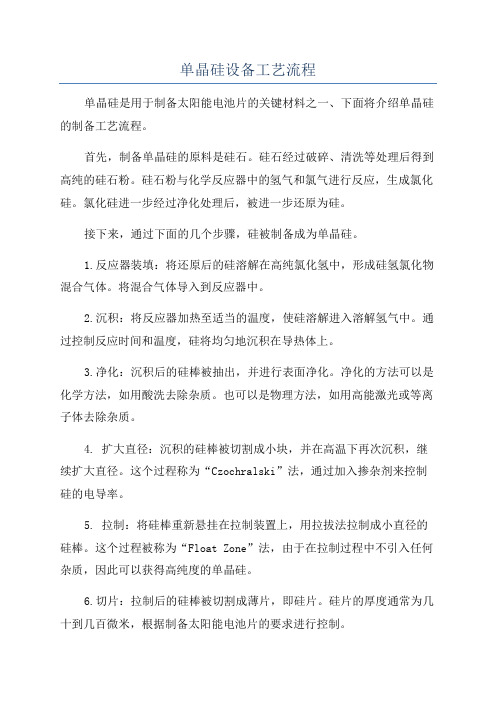
单晶硅设备工艺流程
单晶硅是用于制备太阳能电池片的关键材料之一、下面将介绍单晶硅的制备工艺流程。
首先,制备单晶硅的原料是硅石。
硅石经过破碎、清洗等处理后得到高纯的硅石粉。
硅石粉与化学反应器中的氢气和氯气进行反应,生成氯化硅。
氯化硅进一步经过净化处理后,被进一步还原为硅。
接下来,通过下面的几个步骤,硅被制备成为单晶硅。
1.反应器装填:将还原后的硅溶解在高纯氯化氢中,形成硅氢氯化物混合气体。
将混合气体导入到反应器中。
2.沉积:将反应器加热至适当的温度,使硅溶解进入溶解氢气中。
通过控制反应时间和温度,硅将均匀地沉积在导热体上。
3.净化:沉积后的硅棒被抽出,并进行表面净化。
净化的方法可以是化学方法,如用酸洗去除杂质。
也可以是物理方法,如用高能激光或等离子体去除杂质。
4. 扩大直径:沉积的硅棒被切割成小块,并在高温下再次沉积,继续扩大直径。
这个过程称为“Czochralski”法,通过加入掺杂剂来控制硅的电导率。
5. 拉制:将硅棒重新悬挂在拉制装置上,用拉拔法拉制成小直径的硅棒。
这个过程被称为“Float Zone”法,由于在拉制过程中不引入任何杂质,因此可以获得高纯度的单晶硅。
6.切片:拉制后的硅棒被切割成薄片,即硅片。
硅片的厚度通常为几十到几百微米,根据制备太阳能电池片的要求进行控制。
以上就是单晶硅的制备工艺流程。
值得注意的是,单晶硅的制备过程非常复杂,需要高度纯净的原料和严格的控制条件。
此外,工艺流程还可能根据不同的生产商和设备进行调整和优化。
- 1、下载文档前请自行甄别文档内容的完整性,平台不提供额外的编辑、内容补充、找答案等附加服务。
- 2、"仅部分预览"的文档,不可在线预览部分如存在完整性等问题,可反馈申请退款(可完整预览的文档不适用该条件!)。
- 3、如文档侵犯您的权益,请联系客服反馈,我们会尽快为您处理(人工客服工作时间:9:00-18:30)。
一、硅片生产主要制造流程如下:
切片→倒角→磨片→磨检→CP→CVD→ML→最终洗净→终检→仓入
二、硅片生产制造流程作业实习
1.硅棒粘接:用粘接剂对硅棒和碳板进行粘接,以利于牢固的
固定在切割机上和方位角的确定。
2.切片(Slice):主要利用内圆切割机或线切割机进行切割,以
获得达到其加工要求的厚度,X、Y方向角,曲翘度的薄硅片。
3.面方位测定:利用X射线光机对所加工出的硅片或线切割前
要加工的硅棒测定其X、Y方位角,以保证所加工的硅片的X、
Y方位角符合产品加工要求。
4.倒角前清洗:主要利用热碱溶液和超声波对已切成的硅片进
行表面清洗,以去除硅片表面的粘接剂、有机物和硅粉等。
5.倒角(BV):利用不同的砥石形状和粒度来加工出符合加工要
求的倒角幅值、倒角角度等,以减少后续加工过程中可能产
生的崩边、晶格缺陷、处延生长和涂胶工艺中所造成的表面
层的厚度不均匀分布。
6.厚度分类:为后续的磨片加工工艺提供厚度相对均匀的硅片
分类,防止磨片中的厚度不均匀所造成的碎片等。
7.磨片(Lapping):去除切片过程中所产生的切痕和表面损伤
层,同时获得厚度均匀一致的硅片。
8.磨片清洗:去除磨片过程中硅片表面的研磨剂等。
9.磨片检查:钠光灯下检查由于前段工艺所造成的各类失效模
式,如裂纹、划伤、倒角不良等。
10.ADE测量:测量硅片的厚度、曲翘度、TTV、TIR、FPD等。
11.激光刻字:按照客户要求对硅片进行刻字。
12.研磨最终清洗:去除硅片表面的有机物和颗粒。
13.扩大镜检查:查看倒角有无不良和其它不良模式。
14.CP前洗:去除硅片表面的有机物和颗粒。
15.CP(Chemical Polishing):采用HNO3+HF+CH3COOH溶液腐蚀去
除31um厚度,可有效去除表面损伤层和提高表面光泽度。
16.CP后洗:用碱和酸分别去除有机物和金属离子。
17.CP检查:在荧光灯和聚光灯下检查表面有无缺陷和洗污,以
及电阻率、PN判定和厚度的测量分类。
18.DK(Donar Killer):利用退火处理使氧原子聚为基团,以稳
定电阻率。
19.IG(Intrinsic Gettering):利用退火处理使氧原子形成二次
缺陷以吸附表面金属杂质。
20.BSD(Back Side Damage):利用背部损伤层来吸附金属杂质。
21.CVD前洗:去除有机物和颗粒。
22.LP-CVD(Low Pressure Chemical Vapor Deposition):高温分
解SiH4外延出多晶硅达到增强型的外吸杂。
23.AP-CVD(Atmospheric Pressure Chemical Vapor Deposition):
在硅片背部外延SiO2来背封并抑制自掺杂。
24.端面处理:去除硅片背面边缘的SiO2。
25.CVD后洗:去除表面颗粒。
26.ML(Mirror Lapping)倒角:防止后续工艺中的崩边发生以及
外延时的厚度不均匀等。
27.ML前洗:去除有机物、颗粒、金属杂质等。
28.ML贴付:硅片表面涂腊贴附在陶瓷板上,固定硅片以利于ML
加工。
29.ML:也称之为CMP(Chemical Mechanism Polishing),经过粗
抛和精抛去除14um厚度,此可有效的去除表面损伤层和提高表面平坦度。
30.去腊洗净:去除ML后背面的腊层。
31.ADE测量:测定硅片表面形貌参数如:平整度,翘曲度等。
32.ρ-t测量:对电阻率和厚度进行测定和分类。
33.扩大镜检查:检查ML倒角不良。
34.最终洗净:去除颗粒,有机物和金属杂质。
35.WIS测定:测量最终洗净后硅片表面颗粒。
36.最终检查:在荧光灯和聚光灯下检查硅片表面的情况。
37.仓入:对硅片进行包装,防止再次污染,以待出货。