干式变压器制造工艺要点
干式变压器的生产工艺

干式变压器的生产工艺干式变压器是一种无油、无气体绝缘的变压器,其生产工艺主要包括选材、绕制、绝缘处理、组装和测试等环节。
首先,在干式变压器的生产中,选材是非常重要的一环。
核心材料的选用直接影响到变压器的性能,常见的核心材料主要有铁氧体和非晶合金。
铁氧体具有饱和磁感应强度高、饱和磁导率高、品质因数高等优点,而非晶合金可以更好地减小变压器的负载损耗和短路阻抗。
此外,绝缘材料的选用也非常重要,常见的绝缘材料主要有绝缘纸、绝缘漆和绝缘片等。
其次,绕制是干式变压器生产的核心环节之一。
绕制包括高压绕组和低压绕组的绕制。
高压绕组由多层绕组线圈叠放而成,主要用于传递和分配电压。
低压绕组则由单层绕组线圈绕成,用于传递和分配电流。
在绕制过程中,需要注意各绕组的绕向、绕组的层间绝缘以及导线的良好接触等问题。
绝缘处理是为了保证干式变压器中的各部件之间具有良好的电气绝缘性能。
常用的绝缘处理方法有浸渍绝缘、涂覆绝缘和包覆绝缘等。
其中,浸渍绝缘是将整个变压器进行浸渍,以增强绝缘性能;涂覆绝缘是将绝缘漆均匀地涂覆在各部件表面,以形成坚固的绝缘层;而包覆绝缘是将绝缘材料包覆在导线表面,以增强通气暴露的导线的绝缘性能。
组装是干式变压器生产的一项重要环节。
在组装过程中,需要注意各部件的安装位置和顺序,确保各部件之间的间隙不超过规定的范围,以保证变压器的机械强度和绝缘性能。
同时,还需要进行各项连接时的质量检测和控制,确保连接的牢固和可靠。
最后,干式变压器生产过程还需要进行一系列的测试,包括绝缘电阻测试、局部放电测试、耐压试验和负载损耗测试等。
通过这些测试,可以验证干式变压器的绝缘性能、电气性能和机械性能,确保其质量符合标准要求。
综上所述,干式变压器的生产工艺包括选材、绕制、绝缘处理、组装和测试等环节。
在每个环节中,都需要严格控制质量,确保干式变压器的性能和可靠性。
干式变压器制造工艺流程

干式变压器制造工艺流程
干式变压器制造主要由原材料检验入库、变压器的组装、线圈的制造、总装配、温控系统的制作调试几大部分组成。
这几部分在变压器制造过程中几乎是同步进行的。
各部件加工完成后进行总装配。
一、原材料、配件、外购件入库
包括金属零件、高低压铜导线(铜箔)、硅钢片绝缘零件、金属结构件、黑色金属、配件、附件的检验入库。
二、变压器部件制作
1、铁芯制造,其中包括硅钢片剪切、硅钢片的预叠、铁芯装配、铁芯绑扎及入炉干燥、铁芯试验。
2、线圈的制造
①首先是绝缘件制作与准备。
②通过分段圆筒式高压线圈绕制、箔式线圈绕制、环氧浇注模具表面处理、环氧树脂浇注、环氧树脂浇注线圈烘焙固化、浇注式线圈脱模、线圈表面处理等一系列工艺流程的加工后线圈转装配工序待进行器身组装。
3、器身装配,其中包括绝缘件装配,器身入炉干燥(绝缘电阻测量)、线圈的套装、插板及夹铁、引线装配、器身半成品做试验。
三、总装配,
1、器身的整理与紧固、铁芯对地绝缘电阻的测量、检查器身清洁度及各零部件的紧固程度,分接线及引线绝缘距离。
2、温控系统,风机的制作、安装、调试。
3、送检,作变压器出厂项目试验,试验合格后按包装、运输及贮存工艺,办理入库手续。
干式变压器制造工艺流程

干式变压器制造工艺流程1.外部设备检测:在开始制造干式变压器之前,需要对各种外部设备进行检测。
这些外部设备包括绝缘子、配电柜、控制柜、冷却设备等。
通过进行各项检测,可以确保这些外部设备的质量和正常工作。
2.铁芯制造:铁芯是干式变压器的重要组成部分,它用于电磁感应和传导磁场。
铁芯的制造一般采用硅钢铁芯。
首先需要选取合适的硅钢带,然后通过剪切、冲压和堆叠等工艺,将硅钢带制造成所需的铁芯形状。
最后对铁芯进行热处理,以提高其磁导率和减小磁滞损耗。
3.线圈制造:线圈是干式变压器的另一个重要组成部分,它负责电能的传输和变换。
制造线圈可以分为绕线和绝缘处理两个环节。
首先,根据设计要求,将导线按照预定的匝数和座子数绕制成线圈。
绕制线圈时需要注意导线的间隙和绝缘层的质量。
绕制完成后,对线圈进行绝缘处理,防止相互短路和绝缘击穿。
4.组装:组装是将铁芯和线圈组合在一起,形成干式变压器的主体结构。
首先将铁芯安装到变压器的外壳或结构中,保证铁芯的位置和角度的准确性。
接下来,将线圈安装到铁芯上,并与外部的端子盘和引线相连。
在组装的过程中,需要注意线圈和铁芯的绝缘和固定,以保证变压器的性能和安全性。
5.测试:在干式变压器制造完成后,需要进行一系列的测试来验证其性能和质量。
这些测试包括试验电路的连通性测试、耐压试验、绝缘电阻测试、负载容量测试、短路电流测试等。
测试完成后,对测试结果进行评估和分析,以确保干式变压器的性能符合要求。
以上是干式变压器制造的基本工艺流程。
该流程包括外部设备检测、铁芯制造、线圈制造、组装和测试等环节,每个环节都需要严格把控和操作,以确保干式变压器的质量和性能。
同时,制造过程中还需要采取各种措施,保证制造环境的洁净度和干燥度,以提高干式变压器的绝缘性能和可靠性。
变压器的生产工艺及流程

前言伴随国民经济的飞速发展,我国能源的使用量也在逐年升高。
对于能源的勘探和开采有了更高的要求。
变压器为保证开采进度的顺利开展起着重要的作用,因此提高变压器的整体质量和性能就势在必行。
通过在华鑫变压器公司的实习工作,使我对变压器有了更深入的了解和掌握。
对其各个作业级工艺流程进行分析研究,结合目前的生产工艺结合先进的科学技术,对其生产工艺技术进行不断改进,解决生产环节中由于设备更新不及时、工艺不够规范等等带来的影响发展的因素。
生产过程中,每道工序流程都是十分重要的部分,它不仅关系到生产的进度,而且还直接关系到变压器的整体质量和其性能。
所以说对于每一个作业的流程在不断的技术革新中,改进生产工艺流程,提高变压器质量,体现变压器自身价值所在。
每一道工序、每一道工艺技术都要重视。
目录摘要²²²²²²²²²²²²²²²²²²²²²²²²²²²²²²² 1 Abstract²²²²²²²²²²²²²²²²²²²²²²²²²²²²²² 2 1.绪论²²²²²²²²²²²²²²²²²²²²²²²²²²²²²² 3 1.1课题背景²²²²²²²²²²²²²²²²²²²²²²²²²² 3 1.2概况²²²²²²²²²²²²²²²²²²²²²²²²²²²² 3 2.R型变压器的工艺流程²²²²²²²²²²²²²²²²²²²²²² 43. R性卷铁芯变压器性能特点²²²²²²²²²²²²²²²²²²²² 44. R型卷铁芯结构特点及操作工艺²²²²²²²²²²²²²²²²²² 55. R型变压器现场生产工艺操作及注意事项²²²²²²²²²²²²²² 6 5.1铁芯的制造²²²²²²²²²²²²²²²²²²²²²²²²² 65. 1.1硅钢片的纵剪下料的操作过程步骤及注意事项²²²²²²² 6 5. 1.2曲线开料的操作过程步骤及注意事项²²²²²²²²²²² 75. 1. 3 铁芯卷绕的操作过程步骤及注意事项²²²²²²²²²² 9 5. 1. 4铁芯的退火工艺的操作过程步骤及注意事项²²²²²²²²105.2绕组的绕制²²²²²²²²²²²²²²²²²²²²²²²²²125. 2.1低压线圈的绕制具体操作及要求²²²²²²²²²²²²²135. 2.2高压线圈的绕制具体操作及要求²²²²²²²²²²²² 14 5. 3器身的组装²²²²²²²²²²²²²²²²²²²²²²²²²14 5. 3. 1出头的包扎要求及具体操作工艺²²²²²²²²²²²²²15 5. 3.2引线、出头的焊接要求及具体操作工艺²²²²²²²²²²16 5.4浸漆固化处理²²²²²²²²²²²²²²²²²²²²²²²²16 5. 4. 1浸漆工艺及操作过程²²²²²²²²²²²²²²²²²²175. 4. 2固化处理的具体工艺操作过程²²²²²²²²²²²²²²18 5.5进壳完好处理²²²²²²²²²²²²²²²²²²²²²²²²18 5.5. 1器身装入变压器壳的具体操作过程及注意事项²²²²²²²18 5.5. 2接线腔的安装操作及要求²²²²²²²²²²²²²²²²18 6.变压器的设计原理²²²²²²²²²²²²²²²²²²²²²²²²19 7.其它种类变压器制作介绍²²²²²²²²²²²²²²²²²²²²²207.1简述叠铁芯变压器的制作过程²²²²²²²²²²²²²²²²²20 7.2几种绕组的绕制方式的介绍²²²²²²²²²²²²²²²²²²21 8. R型变压器部分材料的分析²²²²²²²²²²²²²²²²²²²²228.1 NOMEX纸的性能特点²²²²²²²²²²²²²²²²²²²²²22 8.2变压器绝缘材料及特点概况²²²²²²²²²²²²²²²²²²23 9. 变压器的发展²²²²²²²²²²²²²²²²²²²²²²²²²²23 10.结论²²²²²²²²²²²²²²²²²²²²²²²²²²²²²2411. 参考文献²²²²²²²²²²²²²²²²²²²²²²²²²²²2512. 致谢²²²²²²²²²²²²²²²²²²²²²²²²²²²²²26变压器的生产工艺及流程摘要本文主要对变压器的生产过程进行了阐述。
轨道交通干式变压器生产工艺流程
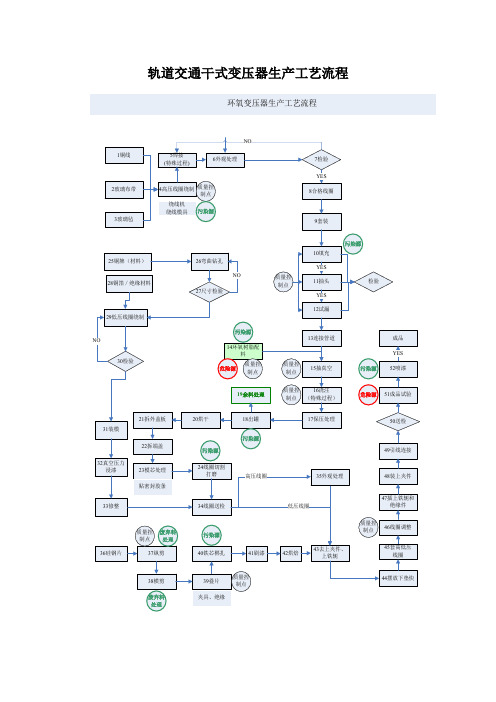
轨道交通干式变压器生产工艺流程
主要工艺流程的操作程序
1、铁心硅钢片横剪操作程序
吊装卷料→调整设备→输入数据→穿引片料→试剪→检验→剪切→抽检→卸料
2、铁心硅钢片纵剪操作程序
调刀→调整导向装置→穿引片料→试剪→检验→调整分料条→调整收卷装置→剪切→检验→卸料。
3、低压箔式线圈操作流程
铜箔上料→层绝缘上料→端绝缘上料→上模→引线焊接→线圈绕制→引线焊接→拆模
4、高压线圈绕制流程
准备绕线模→将合格的导线放在线盘搁架上→上模→绕制→检查整理线圈→卸下线圈→焊接接线柱
5、浇注操作程序
检查绕组→绕组干燥→清洁观察孔→浇注罐预热→进罐→抽真空→混料罐升温→配胶→混料→循环水加热→搅拌→抽真空→保压→注胶→卸真空→出罐
6、绝缘装配操作流程
拆上夹件及上铁轭→套装低高压绕组→装上铁轭→装上夹
件→整理
7、高低压引线装配操作流程
修剪出线头→焊接→整理→制作并安装高、低压引线。
注:以上流程中→表示控制点。
干式变压器制造工艺流程
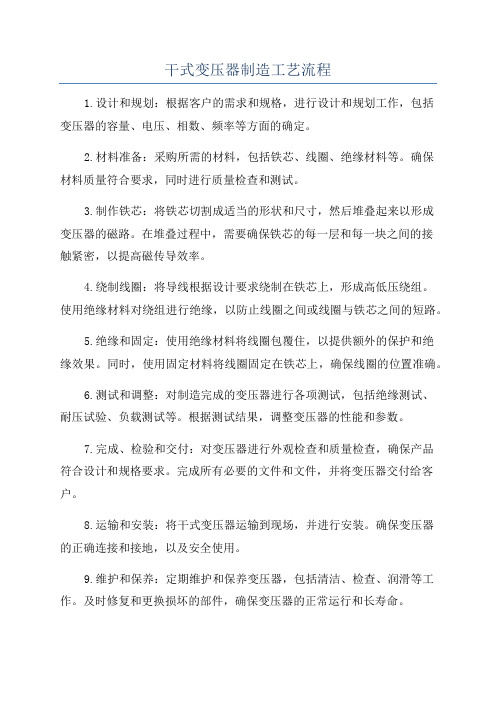
干式变压器制造工艺流程
1.设计和规划:根据客户的需求和规格,进行设计和规划工作,包括
变压器的容量、电压、相数、频率等方面的确定。
2.材料准备:采购所需的材料,包括铁芯、线圈、绝缘材料等。
确保
材料质量符合要求,同时进行质量检查和测试。
3.制作铁芯:将铁芯切割成适当的形状和尺寸,然后堆叠起来以形成
变压器的磁路。
在堆叠过程中,需要确保铁芯的每一层和每一块之间的接
触紧密,以提高磁传导效率。
4.绕制线圈:将导线根据设计要求绕制在铁芯上,形成高低压绕组。
使用绝缘材料对绕组进行绝缘,以防止线圈之间或线圈与铁芯之间的短路。
5.绝缘和固定:使用绝缘材料将线圈包覆住,以提供额外的保护和绝
缘效果。
同时,使用固定材料将线圈固定在铁芯上,确保线圈的位置准确。
6.测试和调整:对制造完成的变压器进行各项测试,包括绝缘测试、
耐压试验、负载测试等。
根据测试结果,调整变压器的性能和参数。
7.完成、检验和交付:对变压器进行外观检查和质量检查,确保产品
符合设计和规格要求。
完成所有必要的文件和文件,并将变压器交付给客户。
8.运输和安装:将干式变压器运输到现场,并进行安装。
确保变压器
的正确连接和接地,以及安全使用。
9.维护和保养:定期维护和保养变压器,包括清洁、检查、润滑等工作。
及时修复和更换损坏的部件,确保变压器的正常运行和长寿命。
以上是干式变压器制造工艺流程的大致描述。
在整个制造过程中,需要严格的质量控制和符合国家标准的要求,以确保制造出的干式变压器具有良好的性能和可靠性。
干式变压器结构设计与制造工艺分析
干式变压器结构设计与制造工艺分析摘要:随着我国电力技术的突飞猛进以及工业制造水平的日益提升、创新发展,干式变压器因其低噪音、低损耗、维护成本低、性能更稳定的特点被广泛应用在各种电力工程配送系统领域。
本文主要探讨干式变压器结构设计与制造工艺,以为设计及制造变压器时缺陷预防和降低变压器能量损耗提供一些参考。
关键词:干式变压器;结构设计;制造工艺引言干式变压器是一种不需要变压器油来进行工作的变压器类型,干式变压器更高效、清洁卫生,使用面积大,在电力系统中受到了大家的高度重视。
随着我国电网建设范围的扩大和用电量的增加,干式变压器在电力系统中的数量也在不断的增加。
不仅如此,干式变压器的使用性能也随着电力发展要求的提高得到了更高的优化。
虽然干式变压器的使用能够有效的降低电力运输过程中的电能损耗,但变压器本身工作过程中产生的能量损耗仍旧在整个电力系统中占据着较大的比例。
据统计,电力系统中来源于变压器的电力损耗占10%。
在全国用电背景下,10%的电量损耗所造成的经济损失也是一笔较大的数目。
研究干式变压器结构设计及制造工艺的优化对降低电力系统经济损失有着重要的意义。
一、结构设计要点及优化从理论上分析,干式变压器与传统变压器在工作原理、基本结构等方面均类似,不管那种类型的变压器的核心部件--铁心均是采用相同的材质。
这两种类型变压器也就在绝缘材料、冷却介质材质的选择上各有侧重。
故而干式变压器与传统油浸式变压器在优化设计的方面大同小异,唯一不同的是在铁心直径、电压比、绝缘材料的选择等方面在合理选择与不同型号干式变压器相匹配的通用件和标准件,并在标准要求的技术上,使用与之相适应的干式变压器设计软件对内部结构设计及制造工艺加以优化。
(一)干变压器结构分析干式变压器主要由硅钢片组成的铁芯和环氧树脂浇注的线圈组成,高低压线圈之间放置绝缘筒增加电气绝缘,并由垫块支撑和约束线圈,其零部件搭接的紧固件均有防松性能。
(二)内部结构重要部件的设计优化1.铁芯铁心是干式变压器中重要的磁路部件。
毕业论文干式变压器制造工艺
摘要干式变压器具有低噪声、低损耗、低局放、免维护、高可靠性、无污染、难燃防火等特征,从而在工矿企业、城镇居民、电站、机场、地铁等领域都得到了广泛应用。
本文介绍了SCB系列的干式变压器的工作原理及工业上SCB系列的干式变压器的生产工艺检测,并做了一些简单的分析。
关键词:干式变压器工业流程生产工艺AbstractDry type transformer with low noise and low loss and low bureau, maintenance, high reliability, pollution-free, flame retardant, which features such as fire prevention in industrial and mining enterprises, urban residents, power stations, airports, railway and fields have been widely applied. The paper introduces SCB series dry type transformer and working principle of the industry of SCB series dry type transformer production process testing, and do some simple analysis.Keyword: Dry type transformer industrial process production process目录1 SCB系列干式变压器的基本知识 (4) (3) (3) (3) (3) (4) (5)2 铁心工艺 (6) (6) (9) (11) (12) (13) (14)3、绕组工艺 (14) (14) (17)4 浇注工艺 (19)5 SC总装配工艺 (22)6 检测 (26) (26) (27) (27) (27) (27) (27)总结 (28)致谢 (29)参考文献 (30)1 SCB系列干式变压器的基本知识变压器是用来改变交流电压大小的电气设备。
变压器制造工艺(3篇)
第1篇一、引言变压器是电力系统中不可或缺的设备,其作用是将高压电能转换为低压电能,以满足各类用电设备的需要。
随着我国电力工业的快速发展,变压器制造技术也得到了长足的进步。
本文将从变压器制造工艺的各个方面进行详细介绍,包括材料选择、结构设计、制造过程、质量控制等。
二、材料选择1. 硅钢片:硅钢片是变压器铁芯的主要材料,其性能直接影响变压器的损耗和效率。
优质硅钢片应具备以下特点:低损耗、高导磁率、良好的机械性能和耐腐蚀性。
2. 铝或铜:变压器绕组通常采用铝或铜作为导线材料。
铝具有重量轻、成本低、导电性能好等优点,但机械强度较差;铜具有较高的导电性能和机械强度,但成本较高。
3. 绝缘材料:绝缘材料是保证变压器正常运行的重要部分,包括绝缘纸、绝缘漆、绝缘油等。
绝缘材料应具备良好的绝缘性能、耐热性能、耐油性能和耐老化性能。
4. 其他材料:变压器制造过程中,还需要使用各种辅助材料,如绑带、垫圈、螺栓等,这些材料应具备良好的机械性能和耐腐蚀性。
三、结构设计1. 铁芯:铁芯是变压器的磁路部分,由硅钢片叠压而成。
铁芯结构设计应满足以下要求:高导磁率、低损耗、良好的散热性能。
2. 绕组:绕组是变压器的电路部分,由导线绕制而成。
绕组设计应满足以下要求:足够的导电性能、良好的绝缘性能、合理的几何尺寸。
3. 外壳:外壳是变压器的保护部分,通常采用钢板或铸铁制成。
外壳设计应满足以下要求:足够的强度、良好的密封性能、便于安装和维护。
四、制造过程1. 铁芯制造:首先将硅钢片剪切成所需尺寸,然后进行叠压,叠压过程中应注意硅钢片的清洁和整齐。
叠压完成后,进行去毛刺、校平、涂漆等工序。
2. 绕组制造:根据设计图纸,将导线绕制在绕线机上,绕制过程中应注意线圈的均匀性、绝缘层的厚度和绝缘性能。
3. 组装:将铁芯、绕组、外壳等部件进行组装,组装过程中应注意各部件的尺寸和位置,确保变压器结构的稳定性。
4. 热处理:对变压器进行热处理,以提高其机械性能和耐腐蚀性能。
干式变压器生产过程及工艺要求
干式变压器生产过程及工艺要求干式变压器是一种常见的变压器类型,它具有很多优点,如无需维护、无油污染、可靠性高等。
那么,干式变压器是如何生产的呢?下面将介绍干式变压器的生产过程及相关工艺要求。
干式变压器的生产过程一般包括以下几个步骤:设计、制造、组装、测试和交付。
首先,设计师需要根据用户的需求和要求进行变压器的设计。
设计要考虑到变压器的额定功率、电压等级、绝缘材料、冷却方式等因素。
设计完成后,制造部门将根据设计图纸和规范要求进行制造。
制造过程包括铁心制造、绕组制造、绝缘处理等工序。
铁心制造是制造干式变压器的重要环节,它要求铁心的质量好、磁导率高。
绕组制造时,要求绕组的导体选取合适,绕组的绝缘处理要符合相关标准。
在组装过程中,首先将铁心和绕组组装在一起,然后安装绝缘件和外壳,最后进行固定和紧固。
组装过程要求严格按照规范进行,以确保变压器的质量。
接下来,对变压器进行测试。
测试过程中,要对变压器的绝缘电阻、电压比、空载损耗、短路阻抗等进行检测,以验证变压器的性能是否符合要求。
最后,将测试合格的变压器进行包装和交付。
干式变压器的生产过程中,有一些重要的工艺要求需要注意。
首先,材料的选择要合理。
铁心材料应具有低磁阻、低损耗、高饱和磁感应强度等特性;绕组导体应选用优质的电解铜或铝;绝缘材料应具有良好的绝缘性能和耐热性。
其次,制造过程要精细化。
铁心的制造要求铁芯接缝平整、水平度好;绕组的制造要求导线排列整齐,绝缘层厚度均匀。
此外,绝缘处理要严格按照规范进行,以确保绝缘性能良好。
最后,测试过程要准确可靠。
测试设备要精确,测试过程要规范,以保证测试数据的准确性。
干式变压器的生产过程及工艺要求是一个复杂而精细的过程。
从设计、制造、组装到测试,每个环节都需要严格按照规范进行,以确保干式变压器的质量和性能符合要求。
只有这样,才能生产出可靠、高效的干式变压器,满足用户的需求。
- 1、下载文档前请自行甄别文档内容的完整性,平台不提供额外的编辑、内容补充、找答案等附加服务。
- 2、"仅部分预览"的文档,不可在线预览部分如存在完整性等问题,可反馈申请退款(可完整预览的文档不适用该条件!)。
- 3、如文档侵犯您的权益,请联系客服反馈,我们会尽快为您处理(人工客服工作时间:9:00-18:30)。
干式(环氧)变压器制造工艺要点干式变压器的发展的速度相当的快,可以用雨后春笋这个词来描写全国的变压器厂家中增加干式变压器生产的速度。
这当中不乏制作精良上规模的大型制造厂家,也有起步较晚,仅能生产几个品种的小厂,但是干式变压器(特别是环氧变压器)的制造方法不外乎几种,随着市场的剧烈竞争,优胜劣汰,要在干式变压器行业中站稳脚跟,了解干式变压器的制造工艺中的要点是相当重要的。
下面就本人在生产实践中的一些体会与大家分享。
一、了解干式变压器的行业标准及本公司(企业)目前干式产品的制造水平的定位,简单的说就是本企业在行业中排名。
1.1产品性能的先进性,其中起码包括损耗(空载和负载)/耐热等级/使用环境/起载使用时间/特殊试验(特别是冷热冲击燃烧性能试验)。
1.2了解本企业的优势和劣势,从而扬长避短。
1.3了解市场的动向,各类干式变压器的需求量、原材料的涨跌趋势。
二、干式变压器生产中一些最关键的技术指标的控制,如产品的局放指标、噪音的分贝量、生产成本。
当然上面这些指标都是在完成技术鉴定所有及形式试验的基础上再着重提高解决的问题。
生产过程中离不开人、机、料、法、环,下面将从五个方面进行论述。
2.1:由于今天主要讲述干式变压器制造工艺的要点,那么我们假定贵公司的设计方案是最佳的,这里所说的最佳就是说符合目前贵公司的生产人员、现有的机械设备、目前现有的加工方法和生产环境,总之适合本公司的技术才是最好的。
这样就需要有好的工艺人员将设计的要求,根据本公司机、料和环境,编制出行之有效的工艺方案供实施。
工艺人员必须有一定的设计知识,确保技术条件能够不折不扣的执行(举例如焊接等)工艺人员必须了解本公司的设备现状(举例如浇注的能力和规模)为了保证产品的局部放电值稳定在一个恒定的范围内。
这里先将产品的一些指标如何来判别是设计的问题还是工艺的问题做一个展开,还是举局放的例子。
如产品在样机试制时,局放值是稳定的(10kv都能控制在5pc以下)到了批量生产时,产品的局放值发生了很大的波动,有时相当好,有时大了许多,这样的情况我们就说工艺不稳定,同样如果我们试制的时候是以630KV A为试验依据,现在批量生产时生产了几台2500KV A,且设计的原理和数据的选取是机械的套用630KV A的数据,这时几台产品的局放值都有相同倍数的升高,这从工艺的研究角度说,是设计存在一定的偏差。
所以不同的问题就要从不同的切入点着手解决,这可能就是工艺人员不同于设计人员的方面,而且这方面的知识是通过长时间的节累来到达的。
工艺人员必须对公司内部使用的设备、人员的技能、过程控制、原材料的使用等各方面有全面的了解,并对本公司和行业中生产中出现过问题有详尽的了解,才能进行得心应手的处理。
另外当然是从事产品加工的第一线人员的素质,这些人有很好的技能,了解加工过程中的要点以及由于操作不当可能产生的问题。
他们对制造过程中的质量控制点、特殊和关键过程的控制是严格按照工艺流程来进行的。
不能等产品制造出来后,再去找原因,这样所花的人力和物力就会成倍的增加。
生产过程中应有每道工序详细记录单,这样一旦出现问题就可以做到有帐可查,很容易地将问题进行层别,找到问题的真正原因。
当然这里不能忽略严格把关的检验人员,当生产和质量发生矛盾时,往往一些单位以牺牲质量来保全产量,认为如不能及时交货将会影响公司的信誉度,但是如果你反过来想一想,一旦产品达到现场,出现问题后就不是光光赔款的问题,你的产品可能在这个区域被封杀(举北变的例子和橘子的例子)2.2机:干式变压器的厂家使用的设备的好坏直接影响到产品的质量,这里来说不外乎分3大类型。
首先是线圈绕制设备,当然这里就分高低压绕线机,其中有自动排线的高低压绕线机,箔式绕线机(单头双头)其中现在都配备了自动纠偏的装置,使线圈绕制完成后端部相当的平整,这就有效的控制了端部绝缘的尺寸。
线圈绕制过程中外径及各层线圈的尺寸控制也是至关重要,这直接关系到导线的长度,从而和线圈的绝缘电阻有关联,一台产品中又和线圈的相电阻平衡有关,绕圈的直径过大,环氧浇注时的包封厚度变小,外层绝缘可能裸露且相间的绝缘水平下降,反之如果线圈绕制时外径偏小,包封层变厚,线圈表面就容易开裂。
我们总是说线圈是整台变压器的心脏,如果心脏有毛病这台变压器的使用寿命将大大缩短,特别是环氧浇注产品一旦试验数据不能满足设计要求,将不可逆转。
就会给企业带来很大的损失。
再说剪切线:从最简单的剪板机到小型的斜剪线,再到国产的斜剪线,以下就是国外的全自动剪切线,国内变压器厂公认的有乔格的剪切线—自动堆垛—有步进功能—配备自动绑扎叠片功能(就是将一台铁心自动碓成:上、下、旁柱和中柱。
但是这当中最重要的还是控制以下几个方面:铁片的剪切精度、铁片的冲孔精度、特别是铁心的毛刺,可以这么说变压器行业中始终将横剪和纵剪的毛刺作为质量控制点,实际上从这点上每个企业应该将其作为自觉的行为,你想:如果毛刺大—叠片系数变小—最后导致—增加内线圈的内径—增加外线圈的内容—外线圈变大—增加相间距离—增加上下轭的长度—产品成本明显加大。
另外由于铁片毛刺大,片与片之间有间隙—加大了产品的噪音。
当然剪片的精度对铁心的影响也是很大的,我们在检查铁心时检验产品的端面的平整度,实际关键应该考核接缝处的间隙,这样才能有效的控制铁耗。
当然变压器加工设备中浇注设备是相当重要的,从产品的类型来看有带填料和不带填料两大类,从搅拌的形式来分有静态混料和动态混料两种,从制造商来分,有全进口、主要元器件进口国内组装、国内引进技术全部在国内生产(元器件大总值发为进口元件)和全部由国内制造,当然价格从高到低,质量也是依次递减。
从上面的设备来年,最重要的几点为:配料的准确性、混料的均匀性、混合料脱气的完全性(根据时间进行展开)当然对于缠绕式产品(ABB)和浸漆型的关键需要有旋转烘房和真空浸漆设备这道工序控制产品的真空度是至关重要的,但是真空度到底控制在什么程度是和你的产品密切有关,首先必须控制原材料的饱和蒸汽压,一旦超出,就会将混合料的一些有效成分抽除,从而改变了材料的原有性能。
2.3料:直接和产品的成本有关,到底是采用什么材料,它的性能如何,日本在战后的工业迅速发展,得益于价值工程,因为它所使用的原材料的寿命周期控制得相当的精确。
你的产品定位,绝缘等级的确定和原材料的选用密切有关,当然这里主要包括硅钢片、导线、绝缘材料(含环氧混合料)三大类,一旦你的公司所定变压器的等级是F级,那么所有的材料都要围绕满足这个绝缘等级而定,当然你必须了解产品的热点分布,所有的材料都应满足耐热等级。
为了产品使用的安全性能,你还必须进行冷热冲击试验、低温通电试验等一系列的形型式试验。
另外你必须了解使用的导线是否能够满足在一定温度下的正常使用(可以通过向外推移的方法得出导线的使用寿命)绝缘材料的选取是相当重要的,你所用的玻璃纤维制品必须使用无碱无蜡硅烷化处理的材料,你使用的填料(如二氧化硅)也必须满足电工级的要求,否则会对产品的局放有一定的影响。
你还需了解环氧混合料的收缩率,从而保证线圈的各项指标。
工艺上还需要配合技术条件,给出采购规范,从材料的源头上就对产品进行控制,当然这里还需从各渠道了解供货单位的诚心度,对本公司有能力的检验的材料需要建立进料检验,对于没有条件的试验项目,应根据原材料的重要程度,制定委外试验的周期。
环氧混合料的选择,当然首先必须符合耐热等级,当然不同的产品,如一般的配变和接地消弧产品他们之间就有不同的区别,前者长期使用但过电流较小,后者则相反,所以在选择产品的玻璃化温度时(Tg)时就要进行统盘的考虑,这类物质一般单位不具备试验的仪器设备,所以在选择供应商时必须慎之又慎,要看供应商的信誉及供货的及时性,当然性价比是最重要。
还有一类材料是玻璃纤维材料,对于它们来说虽然在整个浇注体内起到增强作用,但是选料时必须注意下列几点。
玻璃纤维材料一定是无碱无蜡的,因为碱性的材料和环氧浇注的反应是异常的(一般的环氧固化剂是一个酸酐),同时玻璃纤维材料如果有蜡的话,就不能有效的跟混合料进行结合,相互间有一个界而,根本起不到增强的作用。
另外所说的硅烷化处理,就是指玻璃纤维材料在丝加工阶段用硅烷机进行了处理,使玻璃纤维制品形成很多的化学键,可以有效地和环氧混合料进行化学键的结合,从而提升了产品强度。
2.4法:就是加工的方法,这当然就是工艺啦。
上海到北京可以乘飞机也可以坐动力,还可以坐长途车,这就告诉我们,要加工一台变压器有很多的方法的组合,哪一个是最符合本企业的,那它近阶段就是最好的。
光从线圈的加工来看,就有带填料和不带填料的两种,当然还有缠绕式,浸渍型的。
那种最好,我说都好。
一个企业里有时也为采用有填料和无填料的产品争论的喋喋不休。
实际上它们的工艺都是成熟的,就看你偏重哪一方面。
我单位20世纪末引进了德国HTT 技术,当时我们认为它有许多特点:模具结构相当的新颖、结构设计相当的合理,填料的配比相对适当,产品的表面相当光洁,这实际上是符合目前客户的需求,模具结构新颖简单实用,这就给加工带来方便,加工周期也相应缩短,由于结构合理,材料的利用率就高,产品的局放能够有效地得到控制,而采用了带填料的方法,浇注成本明显降低,员工的专业操作技能相对要求不高(线圈装模),产品表面的收缩痕明显减少(相对无填料)现在来看更有一个优势,就是在进行燃烧试验时其性能明显由于无填料的(填料的比重越大燃烧试验的优势越大),同时就是这种技术,在国内首创使用聚甲醛的小气道棒,使产品的气道的设置的位置可以根据产品要求可以随心所欲的放置。
由于使用该种气道棒,使制造成本大大降低,原来使用的气道板是一个直径一套气道板,无论是加工周期还是加工费用都远远高于聚甲醛气道棒,同时整个线圈在绕制时的重量也明显下降,同时改变了大气道板四个连接处的温度,使线圈的内外散热面积大幅度的增加,真正起到降温的目的。
同时选用德国HTT的技术,它的模具结构是即简单又节约成本,同时加工周期大为缩短。
(记得当时签订合同时,德国专家告诉我们:两个人一天在简单的设备下能够加工高低压两套(六个模具)当时觉得很惊讶,但事实就是如此,现在此线圈的外径能够做到1500高度在1800左右,基本满足所有浇注的变压器的要求。
以铝代铜的加工要求:这一条放在加工方法上也不是最合适,实际上它和设计理念也有很大的关系,现在变压器行业的竞争如此的激励,要想在市场上占据先机或取得一定的份额,就要降低成本。
目前最有成效的方法就是采用以铝带铜的方法,从原理和实际的情况来看,使用铝材替代是切实可行的,从环氧浇注的角度,我们知道铜的膨胀系数为:17.1(1/℃×106),而铝的膨胀系数为:23.6(1/℃×106),存环氧树脂固化剂浇注体系的膨胀系数约为:50-70(1/℃×106),如果50%的石英粉的浇注体的膨胀系数为:23(1/℃×106),同样采用50%的玻璃纤维增强材料的膨胀系数为:22(1/℃×106),由上而的数据可以看出铝导线的膨胀系数和环氧(加石英粉或玻璃纤维)的加强材料的膨胀系数相当的接近,这就提示我们,该产品在成型后或人今后的使用时,随着温度的变化,铝材和环氧加强混合料的膨胀系数基本一致,也就是说不容易产生开裂等问题,相反,由于铜材和环氧加强混合料的膨胀系数存在一定的距离,就比较容易产生开裂等问题,那么是不是所有的产品都可以以铝代铜呢,回答是否定的,就举一个简单的例子,如100kva的35kv级的产品,原来使用的导线就很细,虽然换成铝导线时截面会大些,但是相对来说还是很细,在线圈绕制国产中我们总是要求将线圈绕得紧实,这样导线就很容易被拉稀,使产品达不到设计的要求,在接单时我们要将产品的性能原原本本的告诉客户:采用铝导线的工艺是相当成熟的,我国第一台环氧变压器就是采用铝导线进行绕制,那是在70年代,一台西门子的铝箔变压器在上海展览馆(当时还是中苏友好大厦),展览结束后,上海变压器厂将其买下,进行了解剖,这台变压器采用的是铝箔结构,但当时国内根本没有厂家市场这么薄的铝箔,所以就用铝导线进行替代,到如今西门子公司一贯坚持使用铝材,包括现在的济南志友一直在孜孜不倦的使用相当成熟的铝材浇注工艺。