工艺学复习重点Microsoft Word 文档
工艺学期末复习知识点

工序分散原则
❖ 使每个工序的加工内容尽量少些,总的工序数 目较多。 ❖优点: 1)每个工序使用的设备和工艺装备相对简单,调 整、对刀比较容易 2)对操作工人技术水平要求不高 3)工序数多、设备数多、操作工人多,占用生产 面积大 ❖应用:
h1定位误差?
Y
oo1
Td
2sin
2
△B=0(基准重合)
D
Y
Td
2sin
2
h2定位误差?
Y oo1
Td
2sin
2
B
Td 2
DY B2sTidnT2d
2
工序基准在定位面上
△ Y、△B引起h2变化方向相反
h3定位误差?
Y oo1
Td
2sin
2
B
Td 2
DY B 2sTidnT2d
2
(2)基准统一原则
同一零件的多道工序尽可能选择同 一个定位基准,称为基准统一原则。
保证各加工表面间的相互位置精度, 简化夹具设计与制造工作,降低成本, 缩短生产准备周期。
(3)自为基准原则
精加工或光整加工工序要求余量小而均 匀,选择加工表面本身作为定位基准,称为 自为基准原则。
1—磁力表座;2—百分表;3—床身;4—垫铁
3)操作安全、省力。 4)结构应尽量简单,便于制造,便于维修。
夹紧力的确定
(1)夹紧力作用点的选择 ① 夹紧力的作用点应正对定位元件或位于定位元件 所形成的支承面内 ② 夹紧力的作用点应位于工件刚性较好的部位 ③ 夹紧力作用点应尽量靠近加工表面,使夹紧稳固 可靠
(完整word版)《化工工艺学》复习资料

(完整word版)《化⼯⼯艺学》复习资料《化⼯⼯艺学》复习资料⼀、单选题。
1、化⼯⽣产过程⼀般可概括为原料预处理、化学反应和三⼤步骤。
( A )A 、产品分离及精制B 、⼯艺条件优化C 、设备与安装⼯程D 、产品⽅案设计2、化学⼯业的主要原料包括煤、⽯油、天然⽓和。
( C )A 、⾦属矿B 、化学矿C 、化学中间体D 、⼯业盐3、化⼯中常见的三烯指⼄烯、丙烯和,三苯指苯、甲苯和。
( A )A 、丁⼆烯和⼆甲苯B 、丁⼆烯和⼄苯C 、丁烯和⼆甲苯D 、丁烯和⼄苯4、为了充分利⽤宝贵的⽯油资源,要对⽯油进⾏⼀次加⼯和⼆次加⼯。
⼀次加⼯⽅法为常压蒸馏和减压蒸馏;⼆次加⼯主要⽅法有等。
( A )A 、催化重整、催化裂化、加氢裂化和焦化B 、催化重整、催化裂化、催化转化C 、催化重整、催化裂化、延迟焦化D 、催化重整、催化裂化、延迟焦化5、合成氨反应⽅程式为 H 2+3N 2→2NH 3,该反应是⼀个、、体积缩⼩的反应。
( D )A 、不可逆、吸热B 、不可逆、放热C 、可逆、吸热D 、可逆、放热6、侯⽒制碱法的主要产品是。
( C )A 、NaHCO 3和NH 4Cl ;B 、Na 2CO 3和NaClC 、Na 2CO 3和NH 4Cl ;D 、Na 2CO 3和NaHCO 37、烷烃热裂解主要反应为。
( B )A 、加氢反应和断链反应B 、脱氢反应和断链反应C 、脱氢反应和重组反应D 、加氢反应和重组反应8、转化率是针对⽽⾔的;选择性是针对⽽⾔的;收率等于转化率与选择性之积。
( D )A 、⽬的产物、中间产物B 、反应物、中间产物C 、⽬的产物、反应物D 、反应物、⽬的产物9、下列哪种⽅法不能提⾼汽油⾟烷值: ( B )A 、降低烯烃含量B 、降低芳烃含量C 、提⾼氧含量D 、添加甲基叔丁基醚10、下列关于合成氨的熔铁催化剂Fe 3O 4-Al 2O 3-K 2O 说法错误的是:。
( A )A 、Fe 3O 4是活性组分B 、Al 2O 3是结构型助催化剂C 、K 2O 是电⼦型助催化剂D 、使⽤前需升温活化⼆、填空题。
机械制造工艺学期末复习知识点.doc
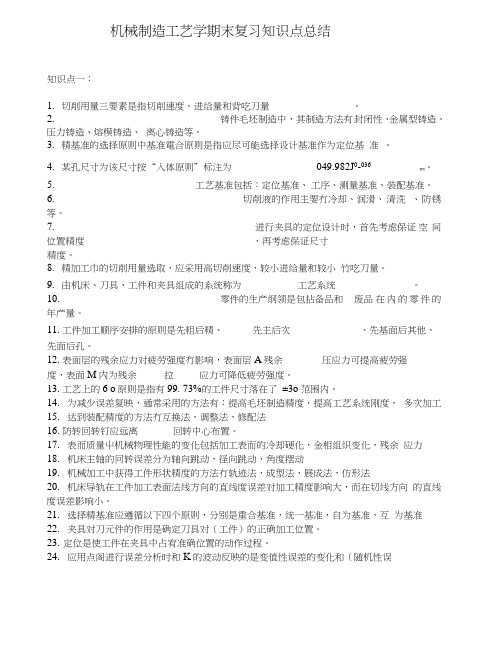
机械制造工艺学期末复习知识点总结知识点一:1.切削用量三要素是指切削速度、进给量和背吃刀量。
2.铸件毛坯制造中,其制造方法有封闭性、金属型铸造、压力铸造、熔模铸造、离心铸造等。
3.精基准的选择原则中基准電合原则是指应尽可能选择设计基准作为定位基准。
4.某孔尺寸为该尺寸按“入体原则”标注为049.982J0-036mm。
5.工艺基准包括:定位基准、工序、测量基准、装配基准。
6.切削液的作用主要冇冷却、润滑、清洗、防锈等。
7.进行夹具的定位设计时,首先考虑保证空间位置精度,再考虑保证尺寸精度。
8.精加工巾的切削用量选取,应采用高切削速度,较小进给量和较小竹吃刀量。
9.由机床、刀具、工件和夹具组成的系统称为工艺系统。
10.零件的生产纲领是包拈备品和废品在内的零件的年产量。
11.工件加工顺序安排的原则是先粗后精、先主后次、先基面后其他、先面后孔。
12.表面层的残余应力对疲劳强度冇影响,表面层A残余压应力可提高疲劳强度,表面M内为残余拉应力可降低疲劳强度。
13.工艺上的6 o原则是指有99. 73%的工件尺寸落在了±3o 范围内。
14.为减少误差复映,通常采用的方法有:提高毛坯制造精度,提高工艺系统刚度,多次加工15.达到装配精度的方法冇互换法,调整法,修配法16.防转回转钉应远离回转中心布置。
17.表而质量屮机械物理性能的变化包括加工表而的冷却硬化,金相组织变化,残余应力18.机床主轴的冋转误差分为轴向跳动,径向跳动,角度摆动19.机械加工中获得工件形状精度的方法冇轨迹法,成型法,展成法,仿形法20.机床导轨在工件加工表面法线方向的直线度误差对加工精度影响大,而在切线方向的直线度误差影响小。
21.选择精基准应遵循以下四个原则,分别是重合基准,统一基准,自为基准,互为基准22.夹具对刀元件的作用是确定刀具对(工件)的正确加工位置。
23.定位是使工件在夹具中占宥准确位置的动作过程。
24.应用点阁进行误差分析时和K的波动反映的是变值性误差的变化和(随机性误差)的分散程度。
金属工艺学复习要点

1.液态合金本身的流动能力,称为合金的流动性2.浇注温度:浇注温度越高合金的粘度下降且因过热度高,合金在铸型中保持流动的时光越长故充型能力强,反之充型能力差。
鉴于合金的充型能力随浇注温度的提高呈直线升高,因此对薄壁铸件或流动性较差的合金可适当提高其浇注温度,以防止浇不到或冷隔缺陷,但浇注温度过高,铸件容易产生缩孔,缩松,粘沙,析出性气孔,粗晶等缺陷,故浇注温度不宜过高。
3.充型能力:砂型铸造时,提高直浇道高度,使液态合金压力加大,充型能力可改善。
压力铸造,低压铸造和离心铸造时,因充型压力提高甚多,故充型能力强。
4..合金的收缩经历:液态收缩——从浇注温度到凝结开始温度之间的收缩;凝结收缩——从开始凝结到凝结结束之间的收缩;固态收缩——从凝结结束冷却到室温之间的收缩。
5.缩孔位置:扩散在铸件的上部,或最后凝结部位容积较大的孔洞。
6.判断缩孔产生位置的主意:1.画等温线发 2.画最大内接圆发3.计算机凝结模拟法7.消除缩孔的工艺措施:安放冒口和冷铁实现顺序凝结。
8.任何铸件厚壁或心部受拉应力,薄壁或表层受压应力。
9.对于不允许发生变形的重要件,必须举行时效处理。
天然时效是将铸件置于露天场地半年以上,使其缓慢的发生变形,从而使内应力消除。
人工时效是将铸铁加热到550-650举行去应力退火。
时效处理宜在粗加工之后举行,以便将粗加工所产生的内应力一并消除。
10.高温出炉,低温浇注11.下列铸件宜选用哪类铸造合金,请阐述理由:(1)车床床身:宜选用灰铸铁HT300-350 因为车床需要承受高负载(2)摩托车气缸体:铸造铝合金ZL 因为气缸要求气密性好质量要轻(3)火车轮:铸钢车轮要求耐磨性好(4)压气机曲轴:可锻铸铁或球墨铸铁因为曲轴负荷大,受力复杂(5)气缸套:球墨铸铁或孕育铸铁因为要求高负荷高速工作耐磨(6)自来水管道弯头:黑心可锻铸铁承受冲压震动扭转负荷(7)减速器涡轮:铸造锡青铜用于高负荷和高滑速工作的耐磨件12.造型材料必备性能:1 一定的强度 2 一定得透气性 3较高的耐火性 4 一定的退让性13.提高耐火性和防黏沙:铸铁涂石墨水铅粉等铸钢涂石灰粉铬铁矿粉有色金属涂滑石粉14.解决透气性和退让性措施:给砂型加锯木屑,草木粉,煤粉。
木制品加工工艺学Word版
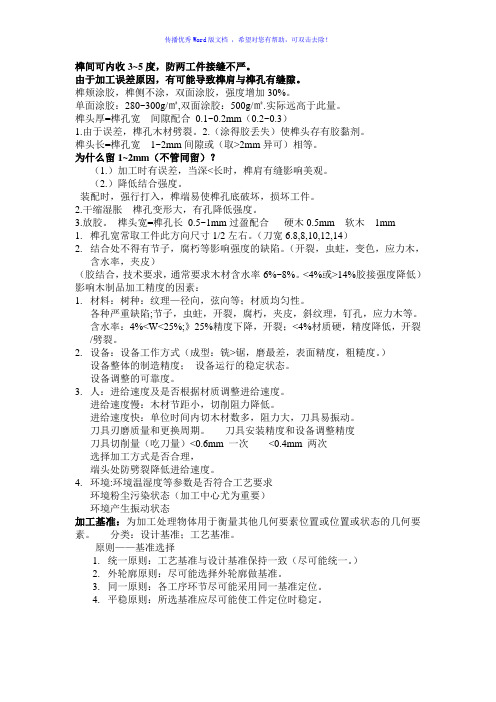
榫间可内收3~5度,防两工件接缝不严。
由于加工误差原因,有可能导致榫肩与榫孔有缝隙。
榫颊涂胶,榫侧不涂,双面涂胶,强度增加30%。
单面涂胶:280~300g/㎡,双面涂胶:500g/㎡.实际远高于此量。
榫头厚=榫孔宽间隙配合0.1~0.2mm(0.2~0.3)1.由于误差,榫孔木材劈裂。
2.(涂得胶丢失)使榫头存有胶黏剂。
榫头长=榫孔宽1~2mm间隙或(取>2mm异可)相等。
为什么留1~2mm(不管同留)?(1.)加工时有误差,当深<长时,榫肩有缝影响美观。
(2.)降低结合强度。
装配时,强行打入,榫端易使榫孔底破坏,损坏工件。
2.干缩湿胀榫孔变形大,有孔降低强度。
3.放胶。
榫头宽=榫孔长0.5~1mm过盈配合硬木0.5mm 软木1mm1.榫孔宽常取工件此方向尺寸1/2左右。
(刀宽6.8,8,10,12,14)2.结合处不得有节子,腐朽等影响强度的缺陷。
(开裂,虫蛀,变色,应力木,含水率,夹皮)(胶结合,技术要求,通常要求木材含水率6%~8%。
<4%或>14%胶接强度降低)影响木制品加工精度的因素:1.材料:树种:纹理—径向,弦向等;材质均匀性。
各种严重缺陷;节子,虫蛀,开裂,腐朽,夹皮,斜纹理,钉孔,应力木等。
含水率:4%<W<25%;》25%精度下降,开裂;<4%材质硬,精度降低,开裂/劈裂。
2.设备:设备工作方式(成型:铣>锯,磨最差,表面精度,粗糙度。
)设备整体的制造精度;设备运行的稳定状态。
设备调整的可靠度。
3.人:进给速度及是否根据材质调整进给速度。
进给速度慢:木材节距小,切削阻力降低。
进给速度快:单位时间内切木材数多,阻力大,刀具易振动。
刀具刃磨质量和更换周期。
刀具安装精度和设备调整精度刀具切削量(吃刀量)<0.6mm 一次<0.4mm 两次选择加工方式是否合理,端头处防劈裂降低进给速度。
4.环境:环境温湿度等参数是否符合工艺要求环境粉尘污染状态(加工中心尤为重要)环境产生振动状态加工基准:为加工处理物体用于衡量其他几何要素位置或位置或状态的几何要素。
工艺学重点总结
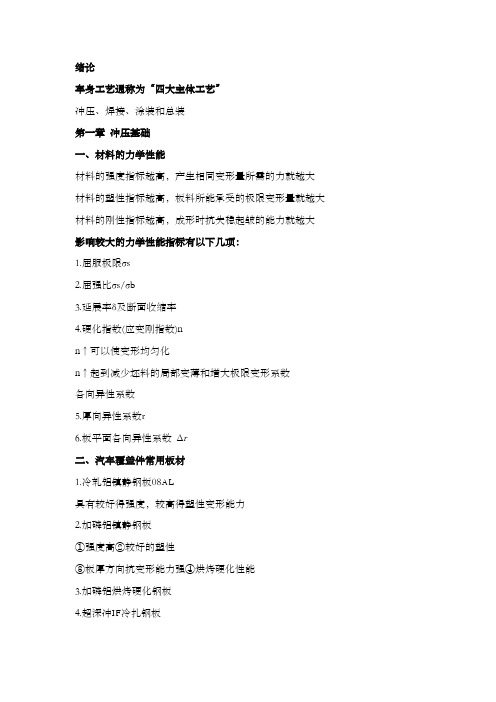
绪论车身工艺通称为“四大主体工艺”冲压、焊接、涂装和总装第一章冲压基础一、材料的力学性能材料的强度指标越高,产生相同变形量所需的力就越大材料的塑性指标越高,板料所能承受的极限变形量就越大材料的刚性指标越高,成形时抗失稳起皱的能力就越大影响较大的力学性能指标有以下几项:1.屈服极限σs2.屈强比σs/σb3.延展率δ及断面收缩率4.硬化指数(应变刚指数)nn↑可以使变形均匀化n↑起到减少坯料的局部变薄和增大极限变形系数各向异性系数5.厚向异性系数r6.板平面各向异性系数Δr二、汽车覆盖件常用板材1.冷轧铝镇静钢板08AL具有较好得强度,较高得塑性变形能力2.加磷铝镇静钢板①强度高②较好的塑性③板厚方向抗变形能力强④烘烤硬化性能3.加磷铝烘烤硬化钢板4.超深冲IF冷扎钢板5.镀锌钢板提高抗腐蚀性能6.镀熔化铝钢板提高钢的耐腐蚀性和易涂覆性第二章冲裁一、.尺寸精度间隙较小时落料:制件尺寸大于凹模口尺寸冲孔:冲孔尺寸会小于凸模尺寸间隙较大时落料:之间尺寸会小于凹模口尺寸冲孔:冲孔尺寸会大于凸模尺寸冲压件的尺寸公差按“入体”原则标注为单向公差,落料件上偏差为零,下偏差为负;冲孔件上偏差为正,下偏差为零。
凸模制造偏差取负偏差,即上偏差为0,下偏差为负;凹模制造偏差取正偏差,即上偏差为正,下偏差为0。
降低冲裁力的方法1 加热冲裁2 斜刃冲裁3 阶梯冲裁2.8 冲裁件的工艺性一、冲裁件的形状和尺寸1.冲裁件的形状尽可能设计成简单、对称,使排样时废料最少。
2.冲裁件的外形或内孔应避免尖锐的倾角,在各直线或曲线的连接处,除属于无废料冲裁或采用镶拼模结构外,宜有适当的圆角,其半径值可查表给出。
3.冲裁件的凸出悬臂和凹槽宽度不宜过小,其合理数值见图。
4.冲孔时,孔径不宜过小。
5.冲裁件的孔与孔之间、孔与边缘之间的距离不应过小,其许可值见表。
6.在弯曲件或拉深件上冲孔时,其孔壁与工件直壁之间应保持一定的距离。
二、冲裁件精度和表面粗糙度1. 冲裁件内外形尺寸精度不高于IT11级。
(完整word版)机械制造工艺学知识点汇总全(复习资料)
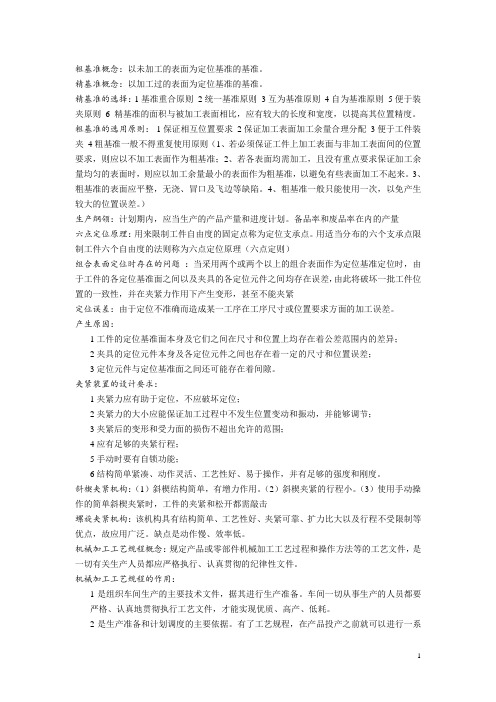
粗基准概念:以未加工的表面为定位基准的基准。
精基准概念:以加工过的表面为定位基准的基准。
精基准的选择:1基准重合原则2统一基准原则3互为基准原则4自为基准原则5便于装夹原则6 精基准的面积与被加工表面相比,应有较大的长度和宽度,以提高其位置精度。
粗基准的选用原则:1保证相互位置要求2保证加工表面加工余量合理分配3便于工件装夹4粗基准一般不得重复使用原则(1、若必须保证工件上加工表面与非加工表面间的位置要求,则应以不加工表面作为粗基准;2、若各表面均需加工,且没有重点要求保证加工余量均匀的表面时,则应以加工余量最小的表面作为粗基准,以避免有些表面加工不起来。
3、粗基准的表面应平整,无浇、冒口及飞边等缺陷。
4、粗基准一般只能使用一次,以免产生较大的位置误差。
)生产纲领:计划期内,应当生产的产品产量和进度计划。
备品率和废品率在内的产量六点定位原理:用来限制工件自由度的固定点称为定位支承点。
用适当分布的六个支承点限制工件六个自由度的法则称为六点定位原理(六点定则)组合表面定位时存在的问题:当采用两个或两个以上的组合表面作为定位基准定位时,由于工件的各定位基准面之间以及夹具的各定位元件之间均存在误差,由此将破坏一批工件位置的一致性,并在夹紧力作用下产生变形,甚至不能夹紧定位误差:由于定位不准确而造成某一工序在工序尺寸或位置要求方面的加工误差。
产生原因:1工件的定位基准面本身及它们之间在尺寸和位置上均存在着公差范围内的差异;2夹具的定位元件本身及各定位元件之间也存在着一定的尺寸和位置误差;3定位元件与定位基准面之间还可能存在着间隙。
夹紧装置的设计要求:1夹紧力应有助于定位,不应破坏定位;2夹紧力的大小应能保证加工过程中不发生位置变动和振动,并能够调节;3夹紧后的变形和受力面的损伤不超出允许的范围;4应有足够的夹紧行程;5手动时要有自锁功能;6结构简单紧凑、动作灵活、工艺性好、易于操作,并有足够的强度和刚度。
(完整word版)钳工工艺学
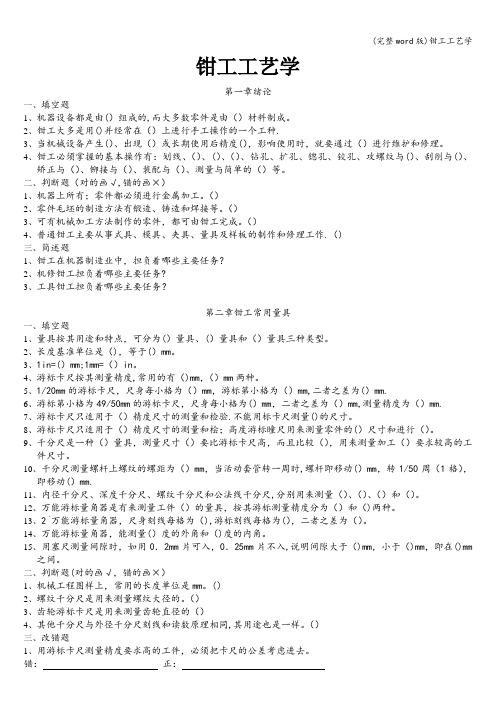
钳工工艺学第一章绪论一、填空题1、机器设备都是由()组成的,而大多数零件是由()材料制成。
2、钳工大多是用()并经常在()上进行手工操作的一个工种.3、当机械设备产生()、出现()或长期使用后精度(),影响使用时,就要通过()进行维护和修理。
4、钳工必须掌握的基本操作有:划线、()、()、()、钻孔、扩孔、锪孔、铰孔、攻螺纹与()、刮削与()、矫正与()、铆接与()、装配与()、测量与简单的()等。
二、判断题(对的画√,错的画×)1、机器上所有;零件都必须进行金属加工。
()2、零件毛坯的制造方法有锻造、铸造和焊接等。
()3、可有机械加工方法制作的零件,都可由钳工完成。
()4、普通钳工主要从事式具、模具、夹具、量具及样板的制作和修理工作.()三、简述题1、钳工在机器制造业中,担负着哪些主要任务?2、机修钳工担负着哪些主要任务?3、工具钳工担负着哪些主要任务?第二章钳工常用量具一、填空题1、量具按其用途和特点,可分为()量具、()量具和()量具三种类型。
2、长度基准单位是(),等于()mm。
3、1in=()mm;1mm=()in。
4、游标卡尺按其测量精度,常用的有()mm,()mm两种。
5、1/20mm的游标卡尺,尺身每小格为()mm,游标第小格为()mm,二者之差为()mm.6、游标第小格为49/50mm的游标卡尺,尺身每小格为()mm,二者之差为()mm,测量精度为()mm.7、游标卡尺只适用于()精度尺寸的测量和检验.不能用标卡尺测量()的尺寸。
8、游标卡尺只适用于()精度尺寸的测量和桧;高度游标瞳尺用来测量零件的()尺寸和进行()。
9、千分尺是一种()量具,测量尺寸()要比游标卡尺高,而且比较(),用来测量加工()要求较高的工件尺寸。
10、千分尺测量螺杆上螺纹的螺距为()mm,当活动套管转一周时,螺杆即移动()mm,转1/50周(1格),即移动()mm.11、内径千分尺、深度千分尺、螺纹千分尺和公法线千分尺,分别用来测量()、()、()和()。
- 1、下载文档前请自行甄别文档内容的完整性,平台不提供额外的编辑、内容补充、找答案等附加服务。
- 2、"仅部分预览"的文档,不可在线预览部分如存在完整性等问题,可反馈申请退款(可完整预览的文档不适用该条件!)。
- 3、如文档侵犯您的权益,请联系客服反馈,我们会尽快为您处理(人工客服工作时间:9:00-18:30)。
一.概念链结构:一级结构或高分子链的近程结构,它是表明单个高分子链中,各原子或者原子团的种类及其在空间的排列方式,如结构单元的化学组成,单体单元在聚合过程中的键接方式,单个高分子链的几何形状,高分子链的立体异构体,共聚物的序列结构。
聚集态结构:各个高分子链靠分子之间的相互作用力而排列的空间结构,包括高分子的非晶结构、结晶结构、取向结构、液晶结构、织态结构。
自由体积:物质的比容与分子占有体积之差。
以大小不等的空穴无规则分布在材料内部。
比容:一定温度下,单位质量的物质所占容积。
表征材料体积因热量变化的程度。
相:根据聚合物的热力学和结构特征来区分。
相形态:各相(区域)的几何形状及其尺寸区分。
添加剂:是使树脂配料能够顺利成型加工及获得所需应用性能而添加的化学品。
几何分散:两种或两种以上组分物质通过几何尺寸减小,同组分物质间距离以及不同组分物质间距离达到相近的过程。
分子级分散:两种或两种以上组分物质之间,同组分分子簇团间距离以及不同组分分子簇团间距离达到埃数量级的过程。
熔化速率W的意义:表示熔化速率的变数群,用来熔化固体的供热速率与Ts固体熔化成Tm熔体所需热速率之比。
欲W越大,必须使供热速率越大。
保压:是熔融树脂充满行腔后,螺杆头部继续作用于熔体的压力,其作用在于压实和补缩。
注射压力:在注射过程中,螺杆顶部对塑料熔体所施加的压力。
背压:又称塑化压力,是螺杆顶部熔料在螺杆转动后退时所受到的压力,其大小通过液压系统中的溢流阀调节。
塑料模具:指成型时确定塑料制品形状、尺寸所用的部件的组合,一般有浇注系统、成型零件和机构零件组成。
翘曲:指注塑制品的形状偏离模具行腔的性状,是塑料制品常见的缺陷之一。
取向:当塑料熔体受剪切应力作用并把这种剪切作用“冻结”下来,所形成的结构就是取向。
熔接缝:在注塑成型中,如果熔体前沿的特殊部分呈不均匀流动,以致流率大大降低,或者在冲模期间,在一段时间内熔体完全停滞,就会产生熔接缝。
内应力:指注塑塑料制件出模后残存在制品中的、为松弛的各种应力之和。
预压:将松散的模塑粉预先用冷压法压成质量一定的、形状规整的密实体过程,该密实体称为锭料或坯料。
;模塑粉模压法:采用由树脂、填料、固化剂、着色剂和脱模剂等构成的模塑粉为主要原料进行模压成型的方法。
模压压力:是指压机对塑料所施加的压力。
模压温度:指模压成型时所规定的模温度。
模压周期:指模具闭合、加热加压到开启模具的时间,包括闭模、排气、加压、固化和脱模。
固相成型:指塑料的熔融(或软化)温度以下(至少低于熔点10~20℃),热塑性塑料型材或坯料在压力作用下成行为制品的方法。
滑移-胶结现象:指在挤出压力逐渐建立的过程中,坯料先是在模口处静止不动,像胶结在口模上一样,待压力升至足够高时,坯料突然快速挤出直至结束,或者再压力降至足够低时重新胶结在口模入口,整个挤出过程是脉动的。
单螺杆挤出机工作点:螺杆特性曲线与机头(口模)特性方程联解的焦点即为挤出机工作点。
塑化:指将固体高分子材料转变为组成均匀,温度均匀,无可挥发性气体和空气的具有良好可塑性流体的过程。
分流梭:又叫鱼雷体,位于挤出机或注塑机的机筒或口模内的一个流线型金属块,其作用是迫使流过的熔融粉料分散成薄层而加强传热效果,借以提高塑化能力。
此术语有时候也指螺杆的平滑混炼头。
二.填空影响结晶的因素:温度和时间、应力、成核剂和溶剂结晶度X影响复杂:X越大,气密性、刚性、耐磨性、耐化学品性、耐热性越大;X越小,韧性、透明性、透气性、着色性越高;中等X,晶粒细而多对综合力学性能有利影响共聚物相形态因素:链节相容性、刚柔性、序列结构分布;组成比;受热历史;受力历史影响共混物想形态因素:组成间相容性、粘度比、弹性比;组成比;受热历史;受力历史;增容作用;交联作用影响复合材料想形态因素:基体组成间相容性、粘度比、弹性比;组成比;受热历史;受力历史;偶联作用;交联作用无内应力结构控制:1.低压控制(具体技术:注射压缩、高速低压注射成型、辅助成型)2.缓慢冷却控制(具体技术:低温成型、延长冷却时间、提高冷却介质温度)3.振动与交替运动(具体技术:交变注塑成型、螺杆振动保压、旋转挤出)4.热处理(具体技术:成型后加热至Tg附近,恒温一段时间,然后缓慢冷却)结晶性聚合物结晶形态控制:1.串晶和纤维晶(具体技术:高压成型、动态保压注射成型、高速挤出)2.球晶(具体技术:中(低)压、高温、缓慢冷却成型)3.柱晶(具体技术:较高应力场下成型《高速注射且速冷》、特殊界面处理技术)材料微观区域取向形态控制1.分子取向(具体技术:推拉注塑成型、交变注射成型、动态保压注塑成型、特殊流道设计、定向操作拉伸)2.纤维取向(具体技术:特殊流道设计、拉挤成型、纤维织物复合成型)3.区域取向(具体技术:辅助装置、高应力《压力》成型、复合成型)塑料取向结构形式:分子,纤维,晶体取向浇铸成型物料形式种类:液体树脂、熔融塑料、塑性溶胶和有机溶胶、溶解塑料、粉料。
固相成型分类:1.按成型材料分(特种塑料的固相成型、热塑性塑料型材或坯料的固相成型、粉状塑料的直接固相成型)2.按成型温度区间(冷成型、热成型、温成型)单螺杆挤出存在的问题:1.固体输送速率低;2.Qm(△P)敏感性大;3.混合均化作用有限;4.易发生固体床破碎;5.熔化速率低。
解决方案:1.采用新型螺杆;2.采用双螺杆。
三.简答成型原料配制的重要性:1.使单组份树脂能满足成型加工和制品性能要求;2.提高聚合物性价比;3.满足制品特殊性能要求;4.使聚合物各组分均与分散塑料配方设计原则:1.对制品性能应用分析,确保质量标准原则;2.原材料的分析,确保高效、节约、节能、安全环保、匹配原则;3.对成型工艺、设备、生产条件分析,确保生产协调、连续、稳定可靠原则添加剂种类:稳定剂(紫外线抗御剂、抗氧剂);增塑剂;填充剂;着色剂;润滑剂;抗静电剂;阻燃剂;防雾剂;趋避剂成型用物料配制设备:混合机:(锥形混合机、卧式混合机、筒体旋转混合机、立式混合机);混炼机:(塑炼机、密炼机、挤出机、开炼机);造粒生产线拟定原料配制工艺流程的原则:1.有利于各组分发挥功效;2.有利于环保;3.有利于提高生产效率;4.有利于延长保质期;5.有利于成型使用;6.有利于减小投资,提高经济效益。
挤出成型过程:加料—输送—压缩—塑化—定型挤出成型工艺特点:1.挤出成型生产工艺分干法和湿法;2.按加料方式,挤出过程;3.挤出成型工艺控制参数除与挤出温度、压力、速度有关外,挤出机结构参数、冷却、牵引等控制因素都会影响制品的质量;4.可生产单一塑料制品,也可生产复合制品,产品应用十分广泛;5.挤出成型工艺按用途可分为:挤出制品成型和成型用原料配制挤出成型结构特点:挤出机有加料系统、挤压系统、加热冷却系统、传动系统组成,其中挤压系统有料筒和螺杆组成挤出成型原理:挤出塑料性板、片材生产工艺流程:物料配制→加料装置→挤出机板、片机头→三辊压光机→冷却辊→牵引机→↗↘切割机→堆放滚台→厚板包(→片材卷筒包装)挤出管材生产工艺流程:物料配制→加料装置→挤出机→管材成型机头→定径套定型→冷却→牵引→切割→(扩口)→成品管材PP-R管材:PP-R:无规共聚聚丙烯,又称三型聚丙烯工艺流程:物料配制→加料装置→挤出机→管材成型机头→定径套定型→冷却→牵引→切割→(扩口)→成品管材设备:一般用单螺杆挤出机工艺控制说明:在加料段设计有一个特殊的可控温的冷却装置。
挤出温度180~210℃。
国外PP-R管材专用挤出机主机的功率100~140kw,螺杆转速最高达250r/min,产量100~350kg/h. PVC波纹管:工艺流程:→单壁波纹管机头模具↘配料→高速混合→低速混合→过筛→挤出机→↗↘→机头定型→→双壁波纹管机头模具↗→定长切割→扩管→成品(大口径)波纹成型→↗↘→牵引→卷曲残绕→成品(小口径)设备:双螺杆或单螺杆挤出机工艺控制说明:RPVC波纹管生产时机头压力36~70Mpa。
机头与挤管机头结果相似,只是口模间歇较小,口模长厚比大,其中一段不加热。
波纹成型装置主要由模具,传动和控制系统组成。
PVC缠绕管:工艺流程:→挤出造粒→单螺杆挤出机挤出带条→↘树脂、辅料→高速混合↗↘→加热缠绕→压紧→→双螺杆挤出机基础带条→↗冷却定型→抽芯→检验→成品入库设备:双螺杆或单螺杆挤出机异型材生产流程:塑料粉、粒料→挤出机→机头→定型装置→冷却装置→牵引装置→切割装置→制品设备:单螺杆和双螺杆挤出机吹塑薄膜:工艺流程:吹膜用原料→单螺杆挤出机熔融塑化→经机头挤出熔融管坯→吹胀管坯→膜泡冷却定型→膜泡折叠夹紧→牵引→双层薄膜卷曲→薄膜制品→检验合格入库设备:单螺杆挤出机注塑机螺杆与挤出机螺杆的区别:1.挤出机螺杆式连续、稳定的,而注塑机螺杆的间歇、周期性的;2.注塑机螺杆在旋转过程中有轴向运移动,即螺杆的实际长度是变化的,而挤出机螺杆的有效长度是不变的;3.挤出机螺杆的输送量的严格控制的,而注塑机螺杆的计量则不然;4.注塑机螺杆的长径比和压缩比较小,一般L/D16~20,压缩比为2~2.5且螺槽较深。
注塑制品后处理的方法及目的是什么:退火:指将制品加热到一定温度,保持足够时间,然后以适宜速度冷却目的:有效消除残余应力,使制件不易翘曲变形,尺寸稳定性较好,另外也可以使结晶更完善,提高了力学强度。
注塑成型中溢边产生的原因:1.注塑量过大;2.注塑压力大或锁模力不足;3.树脂熔体温度过高;4.模具未完全闭合,有间隙。
中空吹塑成型原理:吹塑成型是利用热塑性塑料应力-应变曲线,即在高弹态(玻璃化温度Tg与熔化温度Tm之间)易于产生大的变形,而在玻璃态以下难以变形,基本保持原来形状,将塑料制成一定形状或与制品相似形状的熔体型坯,调节型坯温度至易于变形的温度,用压缩空气胀大型坯至模具型腔内壁,冷却吹胀型坯,得到所需几何形状的中空制品。
吹胀成型过程一般分为三个阶段:型坯制备、吹胀和冷却定型。
挤出吹塑基本过程:管坯形成→合模→吹塑→冷却定型中空塑料制品的成型方法有哪些?各自的特点:1.挤出吹塑:分挤出型坯和吹胀定型两个阶段,使用挤出机;2.注射吹塑:有热坯法和冷坯法;3.拉伸吹塑:优良的韧性和耐低温冲击强度,刚度更优良,透明度和表面光泽度提高,耐蠕变强度提高,与挤出和注塑相结合;4.新型中空吹塑(浸蘸吹塑、旋转成型、culus成型:型坯挤出时使底部封接,成型为有底的型坯、连接吹塑成型:各部分具有不同性质,各段材质合理连接的整体成型、中空层夹板及夹层深拉伸成型:模具结构及其移模易控制,可拉伸成型)两种微孔结构:1.闭孔型制品应用领域:食品包装、隔振减震抗冲器件、体育器材、高压绝缘材料、保温材料等。
2.开孔型膜片:具有无数互通的微孔,应用领域:透气膜、保鲜膜、药物释放膜、分离膜、生物医疗工程用膜。