第四章 复合材料制备工艺
第四章第二节金属基复合材料(MMC)制备工艺
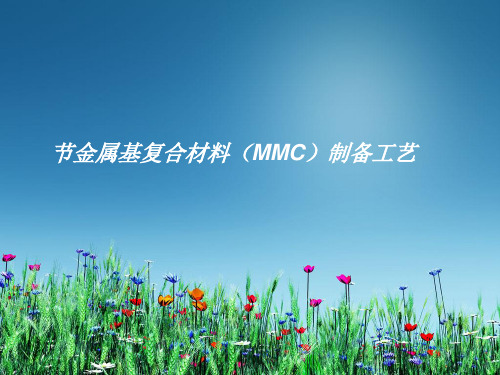
8.3.3液态法(非连续增强相金属基复合材料制备工艺) (1)压铸法
在压力的作用下,将液态或半液态金属以一定速度充填 压铸模型腔或增强材料预制体的空隙中,在压力下快速凝固 成型。
(2)半固态复合铸造 将颗粒加入半固态的金属熔体中,通过搅拌使颗粒在基
体中分布均匀,并取得良好的界面结合,然后将半固态复合 材料注入模具进行压铸成型。
1.3.4 原位(In situ)生长(复合)法 增强相从基体中直接生成,生成相的热力学稳定
性好,不存在基体与增强相之间的认识润湿和界面反 应等问题,基体与增强相结合良好,较好的解决了界 面相容性问题。
(1)共晶合金定向凝固 :共晶合金定向凝固要求合 金成分为共晶或接近共晶成分,开始为二元合金,后 发展为三元单变共晶,以及有包晶或偏晶反应的两相 结合。定向凝固时,参与共晶反应的 和 相同时从 液相中生成,其中一相以棒状(纤维状)或层片状规 则排列生成(上图)。
金属基复合材料的界面优化以及界面设计一般有以下 几种途径:
2.4.2.1增强剂的表面改性处理 增强材料的表面改性(涂层)处理可起到以下作用:
(1)改善增强剂的力学性能,保护增强剂的外来物理 和化学损伤(保护层);
(2)改善增强剂与基体的润湿性和粘着性(润湿层); (3)防止增强剂与基体之间的扩散、渗透和反应(阻挡层) (4)减缓增强剂与基体之间因弹性模量、热膨胀系数等的
2.4.2.2金属基体改性(添加微量合金元素) 在金属基体中添加某些微量合金元素以改善增
与基体的润湿性或有效控制界面反应。 (1)控制界面反应。 (2)增加基体合金的流动性,降低复合材料的制备
温度和时间。 (3)改善增强剂与基体的润湿性。
2.4.3金属基复合材料的性能
复合材料
聚合物基复合材料复习要点 热固性复合材料成型工艺
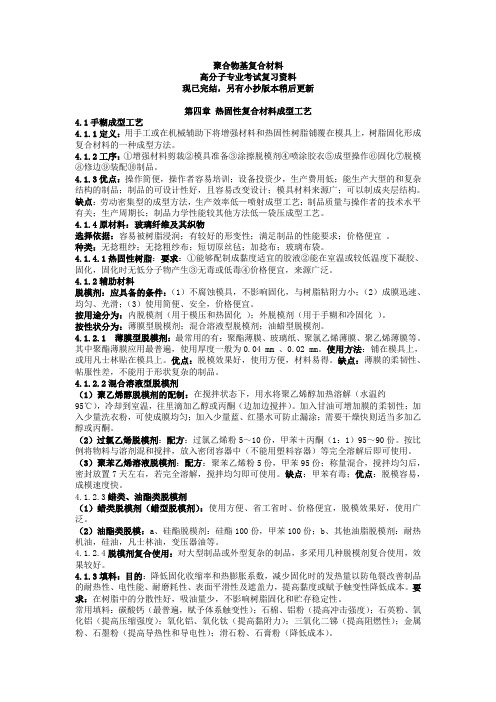
聚合物基复合材料高分子专业考试复习资料现已完结,另有小抄版本稍后更新第四章热固性复合材料成型工艺4.1手糊成型工艺4.1.1定义:用手工或在机械辅助下将增强材料和热固性树脂铺覆在模具上,树脂固化形成复合材料的一种成型方法。
4.1.2工序:①增强材料剪裁②模具准备③涂擦脱模剂④喷涂胶衣⑤成型操作⑥固化⑦脱模⑧修边⑨装配⑩制品。
4.1.3优点:操作简便,操作者容易培训;设备投资少,生产费用低;能生产大型的和复杂结构的制品;制品的可设计性好,且容易改变设计;模具材料来源广;可以制成夹层结构。
缺点:劳动密集型的成型方法,生产效率低—喷射成型工艺;制品质量与操作者的技术水平有关;生产周期长;制品力学性能较其他方法低—袋压成型工艺。
4.1.4原材料:玻璃纤维及其织物选择依据:容易被树脂浸润;有较好的形变性;满足制品的性能要求;价格便宜。
种类:无捻粗纱;无捻粗纱布;短切原丝毡;加捻布;玻璃布袋。
4.1.4.1热固性树脂:要求:①能够配制成黏度适宜的胶液②能在室温或较低温度下凝胶、固化,固化时无低分子物产生③无毒或低毒④价格便宜,来源广泛。
4.1.2辅助材料脱模剂:应具备的条件:(1)不腐蚀模具,不影响固化,与树脂粘附力小;(2)成膜迅速、均匀、光滑;(3)使用简便、安全,价格便宜。
按用途分为:内脱模剂(用于模压和热固化);外脱模剂(用于手糊和冷固化)。
按性状分为:薄膜型脱模剂;混合溶液型脱模剂;油蜡型脱模剂。
4.1.2.1 薄膜型脱模剂:最常用的有:聚酯薄膜、玻璃纸、聚氯乙烯薄膜、聚乙烯薄膜等。
其中聚酯薄膜应用最普遍,使用厚度一般为0.04 mm 、0.02 mm。
使用方法:铺在模具上,或用凡士林贴在模具上。
优点:脱模效果好,使用方便,材料易得。
缺点:薄膜的柔韧性、帖服性差,不能用于形状复杂的制品。
4.1.2.2混合溶液型脱模剂(1)聚乙烯醇脱模剂的配制:在搅拌状态下,用水将聚乙烯醇加热溶解(水温约95℃),冷却到室温,往里滴加乙醇或丙酮(边加边搅拌)。
复合材料的制备方法

树脂传递模塑成型—优缺点
• 优点 • 1) 制品纤维含量可较高,未被树脂浸的部分非常少; • 2) 闭模成型,生产环境好; • 3) 劳动强度较低,对工人技术熟练程度的要求也比手糊与喷射成
型低; • 4) 制品两面光,可作有表面胶衣的制品,精度也比较高; • 5) 成型周期较短; • 6) 产品可大型化; • 7) 强度可按设计要求具有方向性; • 8) 可与芯材、嵌件一体成型 • 9) 相对注射设备与模具成本较低。 • 缺点 • 1) 不宜制作较小产品 • 2) 因要承压,故模具较手糊与喷射工艺用的模具要重和复杂,价
聚酯树脂 加热
固化
切
喷
引发剂 静态混合
割 喷
射 成
辊压
枪
型
促进剂
喷射成型工艺流程图
喷射工艺参数选择
• ①树脂含量 喷射成型的制品中,树脂含量 控制在60%左右。
• ②喷雾压力当树脂粘度为0.2Pa·s,树脂罐 压力为~时,雾化压力为~,方能保证组 分混合均匀
• ③喷枪夹角不同夹角喷出来的树脂混合交 距不同,一般选用20°夹角,喷枪与模具 的距离为350~400mm。改变距离,要高 速喷枪夹角,保证各组分在靠近模具表面 处交集混合,防止胶液飞失。
第二阶段-中间保温阶段
• 这一阶段的作用是使胶布在较低的反应速 度下进行固化。保温过程中应密切注意树 脂的流胶情况。当流出的树脂已经凝胶, 不能拉成细丝时,应立即加全压。
第三阶段-升温阶段
目的在于提高反应温度,加快固化速度。 此时,升温速度不能过快,否则会引起 暴聚,使固化反应放热过于集中,导致 材料层间分层。
复合材料的制备

复合材料的制备复合材料是由两种或两种以上的材料组成的新材料,具有优良的综合性能,被广泛应用于航空航天、汽车、建筑等领域。
复合材料的制备是一个复杂的过程,需要严格的工艺控制和精密的操作。
本文将介绍复合材料的制备过程及其相关技术要点。
首先,复合材料的制备需要选择合适的基体材料和增强材料。
基体材料通常是树脂,如环氧树脂、酚醛树脂等,而增强材料则可以是玻璃纤维、碳纤维、芳纶纤维等。
这两种材料的选择需要考虑到复合材料所需的性能和使用环境,以及制备工艺的要求。
其次,制备复合材料需要进行预处理工艺。
对于基体材料和增强材料,都需要进行表面处理,以提高其与树脂的粘接性能。
对于玻璃纤维和碳纤维等增强材料,通常需要进行表面处理,如打磨、涂覆分散剂等,以增加其表面粗糙度和活性基团的含量,从而提高其与树脂的结合强度。
接下来是复合材料的成型工艺。
成型工艺是制备复合材料的关键环节,包括手工层叠成型、压模成型、注塑成型等多种方法。
其中,压模成型是最常用的方法之一,通过在模具中施加压力,使树脂充分浸润增强材料,然后经过固化,最终得到复合材料制品。
最后是复合材料的固化工艺。
在成型完成后,需要对复合材料进行固化处理,以提高其力学性能和热性能。
固化工艺通常包括自然固化和热固化两种方法,其中热固化是最常用的方法。
通过在一定的温度和时间条件下对复合材料进行热处理,使树脂得到充分的交联,从而提高复合材料的强度和刚度。
综上所述,复合材料的制备是一个复杂的过程,需要严格的工艺控制和精密的操作。
只有在选材、预处理、成型和固化等各个环节都严格把关,才能制备出具有优良性能的复合材料制品。
希望本文能够对复合材料的制备过程有所帮助,为相关领域的工程师和研究人员提供参考和借鉴。
复合材料制备工艺及其性能研究
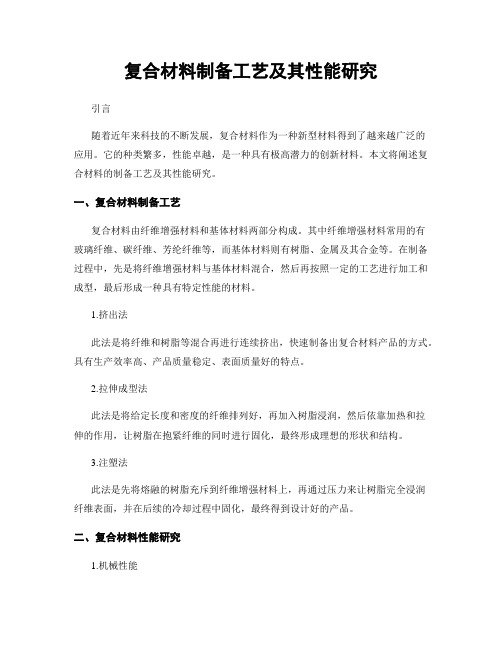
复合材料制备工艺及其性能研究引言随着近年来科技的不断发展,复合材料作为一种新型材料得到了越来越广泛的应用。
它的种类繁多,性能卓越,是一种具有极高潜力的创新材料。
本文将阐述复合材料的制备工艺及其性能研究。
一、复合材料制备工艺复合材料由纤维增强材料和基体材料两部分构成。
其中纤维增强材料常用的有玻璃纤维、碳纤维、芳纶纤维等,而基体材料则有树脂、金属及其合金等。
在制备过程中,先是将纤维增强材料与基体材料混合,然后再按照一定的工艺进行加工和成型,最后形成一种具有特定性能的材料。
1.挤出法此法是将纤维和树脂等混合再进行连续挤出,快速制备出复合材料产品的方式。
具有生产效率高、产品质量稳定、表面质量好的特点。
2.拉伸成型法此法是将给定长度和密度的纤维排列好,再加入树脂浸润,然后依靠加热和拉伸的作用,让树脂在抱紧纤维的同时进行固化,最终形成理想的形状和结构。
3.注塑法此法是先将熔融的树脂充斥到纤维增强材料上,再通过压力来让树脂完全浸润纤维表面,并在后续的冷却过程中固化,最终得到设计好的产品。
二、复合材料性能研究1.机械性能复合材料具有良好的机械性能,如高强度、高硬度、高韧性、高刚性等。
与传统钢铁相比,复合材料的密度更小,同时具有更高的比强度,更大的应变能力,因此广泛应用于航空航天、民用工程、汽车等领域。
2.热学性能复合材料的热学性能表现出良好的稳定性和耐高温性。
其隔热、保温、防高温等性能在高温环境下表现出良好的表现,因此广泛应用于航空航天、电子设备等领域。
3.化学性能复合材料具有良好的化学稳定性,耐酸碱腐蚀、不易变形。
因此在化学行业中,常在不同工艺的产品制备中使用到复合材料。
结语复合材料的制备工艺及其性能研究是当今最重要的研究领域之一。
随着社会的发展和需求的不断增长,复合材料的应用领域也越来越广泛。
未来,复合材料的制备和应用,还将成为一个朝阳行业,有着巨大的潜力和前景。
复合材料工艺
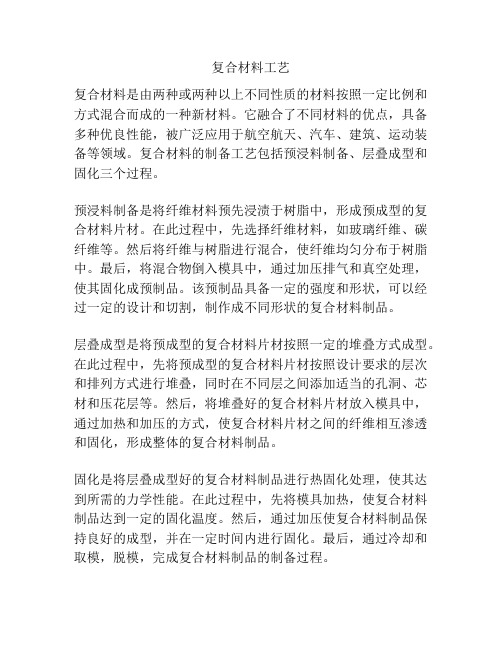
复合材料工艺复合材料是由两种或两种以上不同性质的材料按照一定比例和方式混合而成的一种新材料。
它融合了不同材料的优点,具备多种优良性能,被广泛应用于航空航天、汽车、建筑、运动装备等领域。
复合材料的制备工艺包括预浸料制备、层叠成型和固化三个过程。
预浸料制备是将纤维材料预先浸渍于树脂中,形成预成型的复合材料片材。
在此过程中,先选择纤维材料,如玻璃纤维、碳纤维等。
然后将纤维与树脂进行混合,使纤维均匀分布于树脂中。
最后,将混合物倒入模具中,通过加压排气和真空处理,使其固化成预制品。
该预制品具备一定的强度和形状,可以经过一定的设计和切割,制作成不同形状的复合材料制品。
层叠成型是将预成型的复合材料片材按照一定的堆叠方式成型。
在此过程中,先将预成型的复合材料片材按照设计要求的层次和排列方式进行堆叠,同时在不同层之间添加适当的孔洞、芯材和压花层等。
然后,将堆叠好的复合材料片材放入模具中,通过加热和加压的方式,使复合材料片材之间的纤维相互渗透和固化,形成整体的复合材料制品。
固化是将层叠成型好的复合材料制品进行热固化处理,使其达到所需的力学性能。
在此过程中,先将模具加热,使复合材料制品达到一定的固化温度。
然后,通过加压使复合材料制品保持良好的成型,并在一定时间内进行固化。
最后,通过冷却和取模,脱模,完成复合材料制品的制备过程。
在复合材料的制备工艺中,还需要注意一些关键技术,如温度控制、压力控制和时间控制等。
温度控制是为了使复合材料能够在恰当的温度下进行固化,从而达到所需的力学性能。
压力控制是为了使复合材料能够在适当的压力下,实现纤维相互渗透和固化。
时间控制是为了保证复合材料能够在适当的时间内进行固化,并取模。
总而言之,复合材料的制备工艺是一个综合性的过程,需要综合考虑材料的选择、预浸料制备、层叠成型和固化等多个环节。
只有掌握了合适的工艺和技术,才能够制备出满足工程要求的复合材料制品。
复合材料的制备及应用分析

复合材料的制备及应用分析复合材料是由两种或两种以上的不同材料组成的一种新型材料,它是一种将不同的材料进行合理地组合,以形成想要的特殊性能的新材料。
复合材料可以是纤维增强塑料,碳纤维增强复合材料等,由于其具有高强度、高刚度、高耐腐蚀性、低密度等特点,已被广泛应用于航空、船舶、汽车、建筑等领域,成为现代工业技术的重要组成部分。
一、复合材料制备技术复合材料的制备涉及到多种技术,其中包括纤维增强塑料成型、层板成型、铸造、钣金成型、注塑成型等多种方式。
其中,纤维增强塑料成型技术是一种应用最为广泛的制备技术。
1、手层叠加法手层叠加法是最简单的复合材料制备工艺,通常通过将预浸渍的纤维层一层层地叠加在模具中来制作成型件。
手层叠加法可以利用复合材料的线性材料特性,或选择适当的层厚度、叠加方向和纤维性质,从而获得所需的强度和刚度。
2、自动化层叠加法自动化层叠加法的原理与手层叠加法相同,但它使用的是自动化设备,其实现方式可以是各种,包括将预浸渍的纤维层喷涂到热压模具上、利用熔体将预先切割好的纤维增强材料纤维融合、自动化激光或者机械加工预渲染的纤维增强塑料等等。
3、自动化成型法自动化成型法是通过自动化设备将预先切割好的复合材料放入热压模中,进行成型制造的技术。
利用热和压力,这种技术可以在短时间内形成无缝的结构件。
自动化成型法广泛应用于大型、复杂的结构件,包括飞机翼、机身等。
4、预浸型复合材料预浸型复合材料是一种制造复合材料的高效技术。
它通常是通过将预先浸渍过的纤维加固材料与之结合,然后将其固化,使得它失去一部分基成分,获得更高的耐腐蚀性和高强度。
与先进的手工布置系统相比,预浸型复合材料的生产效率更高。
二、复合材料的应用领域由于复合材料具有高强度、高刚度、耐腐蚀性和较低的密度等特点,它被广泛应用于航空、船舶、汽车、建筑等领域。
1、航空工业由于复合材料具有优异的强度和轻量化的特点,它已被广泛应用于航空工业的制造中,包括飞机和航天器的结构,发动机等。
复合材料的制备方法与工艺

复合材料的重要领域之一。
复合材料中至关重要、且为该领域的研究者 非常感兴趣的课题。
将最终制品的制造与复合材料的成形一起完 成。
4. 复合材料的制造方法
主要的液相工艺
压挤铸造与压挤渗透 喷雾沉积 热喷射 浆体铸造 定向凝固共晶 金属的定向氧化
引人陶瓷颗粒并使其分布均匀。采用这种 方法制造铝基复合材料,陶瓷颗粒尺寸可 小到10μm,增强相的体积分数可达25%。
(2)熔体浸渗铸造与挤压铸造法
即前面已经介绍过的压挤铸造与压挤渗透。 挤压铸造法:先用机械搅拌法制备复合浆料,
然后将液态复合浆料倒入挤压模(需预热)内, 起动液压机,使液态浆料在一定的比压下凝 固成形。
金属基复合材料的制备成形
4.3.1主要的液相工艺
1)压挤铸造与压挤渗透(无压熔浸)
对液体状态的基体加压,使之进入由强化体材料组 成的预成形体。
预成形体的制备 长纤维的编织 短纤维的悬浮液体内沉积 颗粒材料的成形与预烧结
压力熔浸(无压熔浸)
将熔融的金属压力熔浸于成形模具内的预成形体(可 以由长纤维、短纤维或所颗粒构成)而成形。
预烧结
维持形状 具有一定的强度
压 挤 渗 透 的 设 备
与压力铸造相比
压头连续移动
弥补收缩
移动速度慢
外加压力大
压力熔浸成形设备
压挤渗透双压头
保证熔体压力;避免孔隙;避免 不完全渗透
采用双重压头
PCAL* f
* fCL2 f 4
f 1 fCL
2 1 2
CVD(化学气相 沉积)
CVI(化学气相 渗透)
塑料基复合材料的制备成形
- 1、下载文档前请自行甄别文档内容的完整性,平台不提供额外的编辑、内容补充、找答案等附加服务。
- 2、"仅部分预览"的文档,不可在线预览部分如存在完整性等问题,可反馈申请退款(可完整预览的文档不适用该条件!)。
- 3、如文档侵犯您的权益,请联系客服反馈,我们会尽快为您处理(人工客服工作时间:9:00-18:30)。
32
PMC的界面 1.3.3 PMC的界面 (1)PMC的界面特点: (1)PMC的界面特点: 的界面特点 (A)大多数界面为物理粘结,结合强度较低, )大多数界面为物理粘结,结合强度较低, 结合力主要来自如色散力、偶极力、 结合力主要来自如色散力、偶极力、氢键等物理 粘结力。偶联剂与纤维的结合(化学反应或氢键) 粘结力。偶联剂与纤维的结合(化学反应或氢键) 也不稳定,可能被环境( 也不稳定,可能被环境(水、化学介质等)破坏。 化学介质等)破坏。 (B)PMC的界面一般在较低温度下使用,其界面可保持相对稳定。 PMC的界面一般在较低温度下使用,其界面可保持相对稳定。 的界面一般在较低温度下使用 (C)PMC中增强剂本身一般不与基体材料反应。 PMC中增强剂本身一般不与基体材料反应。 中增强剂本身一般不与基体材料反应
26
喷射成型原理图
27
(9)树脂传递成型:先将增强剂置于模具中形成 树脂传递成型: 一定形状,再将树脂注射进入模具、 一定形状,再将树脂注射进入模具、浸渍并固化 的一种复合材料生产工艺, 的一种复合材料生产工艺,是FRP(纤维增强塑 ( 料)的主要成型工艺之一。 的主要成型工艺之一。 特点是:污染小,为闭模操作系统, 特点是:污染小,为闭模操作系统,另外在制品 可设计性、可方向性增强、 可设计性、可方向性增强、制品综合性能方面优 于SMC、BMC。 SMC、BMC。
4
聚合物复合材料与几种金属材料的力学性能比较
GFRP 强热 纤维 强热固 ( 钢) , g/cm3 强 ,G Pa 强 CFRP 碳纤维 强热 强热 固 钢 铝 钛
2.0 1.2 600
1.6 1.8 1120 130 81 0.2
5
7.8 1.4 180 210 27 12
2.8 0.48 170 77 27 23
23
挤出成型工艺示意图
24
(7)注射成型 注射成型是热塑性塑料制品的常用成型方法, 注射成型是热塑性塑料制品的常用成型方法, 多用于短纤维增强塑料制品生产。 多用于短纤维增强塑料制品生产。增强纤维主要 为短切纤维,纤维含量通常有 % 两种。 为短切纤维,纤维含量通常有20% 、30%两种。 两种
4. 5 1. 0 210 110 25 9.0
G
Pa
,G
42 21 8
G
热 胀系数 (10-6/K)
1.3 聚合物复合材料的制备工艺 聚合物基复合材料的工艺特点
材料的形成与制品的成型是同时完成的
树脂基复合材料的成型比较方便
树脂的流动性
6
聚合物基复台材料的制造技术
预浸料的制造
制件的铺层
固化
制件的后处理与机械加工
16
17
(2)压力成型: )压力成型: a.袋压成型: 袋压成型: 袋压成型 真空袋成型; 真空袋成型; 压力袋成型 ;
袋压成型是最早最广泛用于预浸料成型的工艺之一 袋压成型是最早最广泛用于预浸料成型的工艺之一。将 预浸料成型的工艺之一。 铺层铺放在模具中,依次铺上脱膜布、吸胶层、 铺层铺放在模具中,依次铺上脱膜布、吸胶层、隔离膜袋 膜等, 热压下固化。经过所需的固化周期后, 膜等,在热压下固化。经过所需的固化周期后,材料形成 具有一定结构形状的构件 。
18
b.热压罐成型 热压罐成型 工艺过程: 工艺过程:铺层被装袋并抽真空以排除包埋的空气或其它挥 发物,在真空条件下在热压罐中加热、加压固化。 发物,在真空条件下在热压罐中加热、加压固化。固化压力 通常在0.35 0.7MPa。 通常在0.35 - 0.7MPa。 1- 橡皮囊; 橡皮囊; 2-成型套; 成型套; 成型套 3-模具; 模具; 模具 4-毛坯; 毛坯; 毛坯 5-弓形夹; 弓形夹; 弓形夹 6-热压罐; 热压罐; 热压罐 7-底板; 底板; 底板
7
8
1.3.1 预浸料 / 预混料制备 预浸料是指定向排列的连续纤维(单向、织物) 预浸料是指定向排列的连续纤维(单向、织物) 是指定向排列的连续纤维 浸渍树脂后所形成的厚度均匀的薄片状半成品 浸渍树脂后所形成的厚度均匀的薄片状半成品。 薄片状半成品。 预混料是指不连续纤维浸渍树脂或与树脂混合后 预混料是指不连续纤维浸渍树脂或与树脂混合后 是指不连续纤维 所形成的较厚的片(SMC、GMT)团状(BMC)或粒状 所形成的较厚的片(SMC、GMT)团状(BMC) 半成品以及注射模塑料(IMC)。 半成品以及注射模塑料(IMC)。 SMC片状模塑料; GMT玻璃毡增强热塑性塑料 玻璃毡增强热塑性塑料; SMC片状模塑料; GMT玻璃毡增强热塑性塑料; 片状模塑料 BMC团状模塑料; IMC颗粒状注射模塑料 颗粒状注射模塑料; BMC团状模塑料; IMC颗粒状注射模塑料; 团状模塑料
25
(8)喷射成型 这是一种半机械化成型技术。 这是一种半机械化成型技术。它是将混有引 发剂的树脂和混有促进剂的树脂分别从喷枪两侧 发剂的树脂和混有促进剂的树脂分别从喷枪两侧 喷出或混合后喷出,同时将纤维用切断器切断并 喷出或混合后喷出, 从喷枪中心喷出,与树脂一起均匀地沉积在模具 从喷枪中心喷出, 上,待材料在模具上沉积一定厚度后,用手辊压 待材料在模具上沉积一定厚度后, 实,除去气泡并使纤维浸透树脂,最后固化成制 除去气泡并使纤维浸透树脂, 品。
c.IMC(颗粒状注射模塑料)制造: c.IMC(颗粒状注射模塑料)制造: 颗粒状注射模塑料 IMC一般使用双螺杆挤出机制造, IMC一般使用双螺杆挤出机制造,由切割机 一般使用双螺杆挤出机制造 切断,长度一般为3 6mm 6mm。 切断,长度一般为3–6mm。
15
1.3.2 成型工艺
(1)手糊成型 ) 用于制备热固性树脂复合材料的一种最原始、 用于制备热固性树脂复合材料的一种最原始、最简单 的成型工艺。 的成型工艺。 a.用手工将增强材料的纱或毡铺放在模具中, a.用手工将增强材料的纱或毡铺放在模具中, 用手工将增强材料的纱或毡铺放在模具中 b.通过浇、刷或喷的方法加上树脂; 纱或毡也可在铺放前 b.通过浇、刷或喷的方法加上树脂; 通过浇 用树脂浸渍,用橡皮辊或涂刷的方法赶出其中的空气。 用树脂浸渍,用橡皮辊或涂刷的方法赶出其中的空气。 c.如此反复,直到所需厚度。 c.如此反复,直到所需厚度。 如此反复 固化通常在常温、常压下进行,也可适当加热,或常温时加入催 固化通常在常温、常压下进行,也可适当加热, 常温 下进行 化剂或促进剂以加快固化。 化剂或促进剂以加快固化。
28
树脂传递成型示意图
29
30
31
树脂基复合材料的性能特点
树脂基复合材料作为一种复合材料, 树脂基复合材料作为一种复合材料,是由两个或两 个以上的独立物理相,包含基体材料(树脂) 个以上的独立物理相,包含基体材料(树脂)和增强材 料所组成的一种固体产物。 料所组成的一种固体产物。树脂基复合材料具有如下的 特点: 特点: (1)各向异性(短切纤维复合材料等显各向同 )各向异性( 性); (2)不均质(或结构组织质地的不连续性); )不均质(或结构组织质地的不连续性); (3)呈粘弹性行为; )呈粘弹性行为; (4)纤维(或树脂)体积含量不同,材料的物理 )纤维(或树脂)体积含量不同, 性能差异; 性能差异; (5)影响质量因素多,材料性能多呈分散性。 )影响质量因素多,材料性能多呈分散性。 表征其复合后材料的性能。 表征其复合后材料的性能。
9
(1)预浸料制备: )预浸料制备:
a.热固性预浸料制备 浸料的制备分轮鼓缠绕法和列陈排铺法; 按浸渍树脂状态分湿法(溶液预浸法)和干法(热熔预浸法)。 b.热塑性预浸料制造 预浸渍技术:溶液预浸和熔融预浸两种,其特点是预浸料中 树脂完全浸渍纤维。 后浸渍技术:膜层叠、粉末浸叠、纤维混杂,纤维混编等, 其特点是预浸料中树脂以粉末、纤维成包层等形式存在,对 纤维的完全浸渍要在复合材料成型过程中完成。
站长素材
站长素材
第四章 复合材料制备工艺
第一节 聚合物基复合材料
2
1.1 聚合物复合材料的分类 纤维增强(FRC) 1.1.1 纤维增强(FRC) (1)按纤维形态: 连续纤维和非连续纤维; 按纤维形态: 连续纤维和非连续纤维; (2)按铺层方式:单向;织物;三维; 按铺层方式:单向;织物;三维; (3)按纤维种类:玻璃纤维;碳纤维; 按纤维种类:玻璃纤维;碳纤维; 芳纶(Kevlar)纤维;混杂纤维; 芳纶(Kevlar)纤维;混杂纤维; 晶须增强(WRC) 1.1.2 晶须增强(WRC) 粒子增强(PRC) 1.1.3 粒子增强(PRC)
12
(2)预混料制造 a.SMC(片状模塑料) BMC(团状模塑料)制造: a.SMC(片状模塑料)和BMC(团状模塑料)制造: 片状模塑料 团状模塑料 可直接进行模压成型而不需要事先进行固化、 可直接进行模压成型而不需要事先进行固化、 干燥等其它工序的纤维增强热固性模塑料。 干燥等其它工序的纤维增强热固性模塑料。 组成:包括短切玻璃纤维、树脂、引发剂、 组成:包括短切玻璃纤维、树脂、引发剂、 固化剂或催化剂、填料等。 固化剂或催化剂、填料等。 SMC一般用专用SMC机组制造; SMC一般用专用SMC机组制造; 一般用专用SMC机组制造 BMC用捏合法制造。 BMC用捏合法制造。 用捏合法制造
10
11
膜层叠是将增强剂与树脂薄膜交替铺层,在高温高压
下使树脂熔融并浸渍纤维,制成平板或其它一些形状简 单的制品。 增强剂一般采用织物,使之在高温、高压浸渍过程 中不易变形。 具有适用性强、工艺及设备简单等优点。
粉末浸渍是将热塑性树脂制成粒度与纤维直径相当的
微细粉末,通过流态化技术使树脂粉末直接分散到纤维 束中,经热压熔融即可制成充分浸渍的预浸料。 粉末浸渍的预浸料有一定柔软性,铺层工艺性好,比 膜层叠技术浸渍质量高,成型工艺性好,被广泛采用
21
(5)模压成型:对模模压成型是最普通的模压成型技术。 模压成型:对模模压成型是最普通的模压成型技术。 它一般分为三类:坯料模压、片状模塑料模压和块状塑料 它一般分为三类:坯料模压、 模压。 模压。