催化裂解生产低碳烯烃技术
催化裂解生产低碳烯烃技术

催化裂解生产低碳烯烃技术乙烯和丙烯是最重要的石油化工原料之一。
蒸汽裂解技术问世60多年来一直是生产乙烯和联产丙烯的主要技术。
可是,近20多年来随着乙烯和丙烯的需求逐年增加,丙烯/乙烯需求比呈上升趋势,丙烯/乙烯产出比呈下降趋势。
预计今后若干年全球丙烯需求的增速在5%以上,高于乙烯需求的增速,裂解原料的比例不会有大的变化,因此蒸汽裂解生产的丙烯不能满足需求的现状还将持续下去。
多年来,市场需求不足的丙烯主要由炼油厂常规催化裂化和高苛刻度催化裂化副产的丙烯提供。
虽然近20多年来,出现了多种多产丙烯的专用技术,而且有一些已经工业应用,但由于种种原因,这些专用技术生产的数量有限,丙烯供应的紧张状况并未得到根本缓解。
预计今后20年间石油和天然气仍然是人类需求最主要的能源,石油和天然气液仍将是石化原料的主要来源。
由于原料资源、价格、水资源、技术、投资和生产成本等多种因素的影响,预计丙烷脱氢、甲醇制烯烃等专用技术生产低碳烯烃会有一些增加,但不会增加很多,能够增加较多的仍然是石脑油蒸汽裂解/催化裂解和减压瓦斯油/常压渣油催化裂化/催化裂解。
1蒸汽裂解生产低碳烯烃技术工业应用的现状据统计,到2009年底全球有58个国家的216座石油化工厂建有蒸汽裂解装置,乙烯生产能力为13297.4万吨/年。
蒸汽裂解的原料和产品收率如表1所列。
蒸汽裂解的产品收率因原料和裂解深度而异。
裂解深度低(较低的温度和压力),丙烯和所有副产品的收率都提高。
以乙烷为原料,裂解深度高,生产1t 乙烯用原料1.24t,丙烯/乙烯产出比为0.024;以丙烷为原料,裂解深度中到高,生产1t乙烯用原料2.18~2.67t,丙烯/乙烯产出比为0.37~0.45;以丁烷为原料,裂解深度高,生产1t乙烯用原料2.65t,丙烯/乙烯产出比为0.41;以石脑油为原料,裂解深度中到高,生产1t乙烯用原料2.60~3.80t,丙烯/乙烯产出比为0.40~0.57;以常压瓦斯油为原料,裂解深度中到高,生产1t乙烯用原料3.60~4.09t,丙烯/乙烯产出比为0.54~0.62。
低碳烯烃裂解工艺技术

低碳烯烃裂解工艺技术低碳烯烃裂解工艺技术是一种能够高效利用原油资源的重要方法,它通过对轻质石油馏分进行分解,得到高附加值的烯烃产品。
本文将介绍低碳烯烃裂解工艺技术的原理、流程以及应用。
低碳烯烃裂解工艺技术的原理是利用高温和催化剂对轻质石油馏分进行裂解,将长链烃分子分解为短链烃分子的过程。
烯烃是一种含有双键的烃类化合物,具有良好的反应性和广泛的应用前景。
因此,低碳烯烃裂解工艺技术能够在石油加工过程中产生大量的烯烃产品,满足不同行业的需求。
低碳烯烃裂解工艺技术的流程包括预热和分解两个主要步骤。
在预热阶段,原料馏分通过热交换器进行加热,使其达到裂解所需的温度。
在分解阶段,加热的原料馏分进入反应器中,与催化剂接触反应,产生热量和高碳烷烃,经过冷却和精馏,最终得到烯烃产品。
低碳烯烃裂解工艺技术具有以下几个优势。
首先,它能够高效利用原油资源,减少能源消耗和环境污染,符合可持续发展的要求。
其次,它能够生产多种不同类型的烯烃产品,满足不同行业的需求,例如乙烯和丙烷等用于化工行业,丁烯用于合成胶、塑料和合成橡胶行业。
第三,低碳烯烃裂解工艺技术具有较高的生产能力和经济效益,可以提高石油企业的竞争力和盈利能力。
低碳烯烃裂解工艺技术在石油加工行业中得到了广泛的应用。
许多国家和地区的炼油企业都引入了该技术,以提高产能和产值。
例如,中国的石油炼油巨头中国石化通过对低碳烯烃裂解工艺技术的应用,大幅提高了乙烯和丙烷的产量,为国内的化工行业提供了稳定的原料供应。
此外,该技术还被应用于新能源领域,例如生物质能源和生物燃料的转化,为可再生能源的发展提供了技术支持。
总之,低碳烯烃裂解工艺技术是一种高效利用原油资源的重要方法。
它通过对轻质石油馏分进行有效分解,产生各种高附加值的烯烃产品,满足不同行业的需求。
该技术具有高生产能力和经济效益,已在石油加工行业和新能源领域得到了广泛的应用。
随着技术的不断进步和优化,低碳烯烃裂解工艺技术有望在未来发挥更为重要的作用。
新技术新装置提高炼能——石脑油催化裂解(ACO)生产低碳烯烃

一 一 一 魍 ~ 一 一 l ‘
是 为了提 高 处理 柴油 和渣 油原 料时 丙 烟气 处理 和余热回收。
原料 由提 升 管底 部进 入 ,并 与热 再 生催 化 剂混 合 。原料 气化 后与 催化
裂解装置 ( 主要在中东 )采用 乙烷作为 裂解原料 ,而它是不产生任何丙烯 的, 因此单纯地依靠扩大乙烯产 品生产来增 产丙烯 ,看上去不能满足市场需求 。同 样 ,催化裂化装置主要是 为了生产更多 的燃料 ( 汽油和柴油 ),新建 的催化裂 化装置可能也不会满 足市场对丙烯的需 求 ,尽管一些炼 油厂 倾向于在操作上选 择较为苛刻的生产条件 ,增加产量来满 足市场 。因此 ,丙烯将需要新的生产来
来 ,并送往反应后的油气中。汽提后 的 催化剂送到再生器 ,在这 里 ,因裂解反
裂解为低分子量产品 ,如汽油 , 轻柴油
源 ,以满足未来 的需求 。
和煤 油。反应器 ( 转化炉 )包括 四个部 应生成并附着在催化剂表面上 的焦碳在
分 : 一 、提升管, 反应器 , 这里物料 空气作用下燃烧 。再生后的催化剂被送 在
催 化 制 丙烯 及
与催化混合 ,并气
降器 ,这里主要是通过旋风 分离使催化 化和裂解反应需要的热量 。F C C 的附属
R 公司的催化裂化工艺
剂是从气体产品 中分离出来 ;三 、汽提
系统包括空气 ,烟气处理 ,余热回收和 催化剂贮存。反应后 的油气通常是进入
剂一起在提升管 内向上流动 ,并发 生裂 解反应 。在提升管末端 ,气体产 品和催 化剂在沉降器 中的旋风分离器中分 离。
催化剂进入汽提器 ,通过蒸汽或氮气把
的F C C 装置 类似。主要 是通过 在提 升管 夹带在催化剂孔隙 中的气体产物分离 出
石脑油催化裂解制烯烃技术经济分析

石脑油催化裂解制烯烃技术经济分析石脑油催化裂解制烯烃技术经济分析摘要:石脑油的工业角色重要,是石化的主要原料。
文章通过探讨催化裂解工艺产生的经济效益,采用技术经济分析方式探究我国的能源问题,对石脑油的催化裂解制烃技术进行了分析。
关键词:石脑油;烯烃;催化裂解技术;经济分析催化裂解技术对原料有一定的要求,通常制取烯烃的主要原料轻质石油烃比如石脑油、天然气、轻柴油等,这些均是石油和化学工业结合的产品。
面对我国原油重质化、劣质化较严重以及轻质油品如汽、煤油等的需求上升,以往的缺乏原料成本巨大的制烯烃手段制约性较强。
如今,一种新的催化裂解制烯烃工艺改造了传统的蒸汽裂解、流化催化裂化工艺,吸收了两者的益处,经济效益显著。
一、催化裂解技术概述催化裂解工艺主要是指在有催化剂的前提下,高温裂解石油烃类生产乙烯、丙烯、丁烯等低碳烯烃以及轻质芳烃的过程。
通过催化剂从而使得反应过程的活化能降低,反应温度降低,提高了低碳烯烃产率和轻质芳香烃产率以及裂解产品的灵活的分布。
催化裂解工艺主要呈现三个特征:一是正碳离子反应机理、自由基反应机理两者作用的结果,裂解产物中的乙烯比例高于传统催化裂化后的乙烯;二是其催化裂化深度更高,气体的产率大于催化裂化,芳烃含量大;三是反应温度很高,分子量大的气体产物会进行二次反应。
低碳烯烃在氢转移的过程中产生烷烃,或者在聚合反应、芳构化反应中生成汽柴油馏分。
催化裂解的反应机理。
在催化裂解的过程中,既有催化裂化反应又有热裂解反应,不同的催化剂和裂解工艺,裂解反应的机理不一样。
自由基反应机理主要在以Ca-Al系列为催化剂的高温裂解环节中;正碳离子反应机理主要在以酸性沸石分子筛为催化剂的低温裂解环节中;两者共同发挥作用主要在以双酸性中心的沸石催化剂的中温裂解环节中。
二、技术经济分析概述技术经济分析主要是对不同的技术工艺比较后,选择最合适、最经济的方案,为国民经济建设提供依据。
分析主要坚持以下一些原则:政策、技术、经济结合;企业经济效益、国家社会效益结合;当前经济效益和长远经济效益结合;定性分析、定量分析结合;单项评价、综合评价结合;动态分析、静态分析结合;预测分析、统计分析结合;价值量分析、实物量分析结合。
先进炼油化工技术催化裂解技术(DCC)
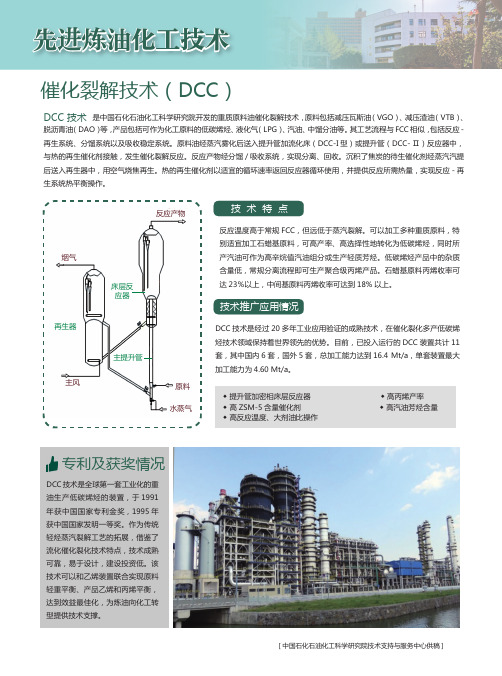
催化裂解技术(DCC)
DCC 技术 是中国石化石油化工科学研究院开发的重质原料油催化裂解技术,原料包括减压瓦斯油(VGO)、减压渣油(VTB)、脱沥青油(DAO)等,产品包括可作为化工原料的低碳烯烃、液化气(LPG)、汽油、中馏分油等。
其工艺流程与FCC 相似,包括反应-再生系统、分馏系统以及吸收稳定系统。
原料油经蒸汽雾化后送入提升管加流化床(DCC-I 型)或提升管(DCC-Ⅱ)反应器中,与热的再生催化剂接触,发生催化裂解反应。
反应产物经分馏/吸收系统,实现分离、回收。
沉积了焦炭的待生催化剂经蒸汽汽提后送入再生器中,用空气烧焦再生。
热的再生催化剂以适宜的循环速率返回反应器循环使用,并提供反应所需热量,实现反应-再生系统热平衡操作。
DCC 油生产低碳烯烃的装置,于[中国石化石油化工科学研究院技术支持与服务中心供稿]反应产物烟气原料
水蒸气主风再生器床层反应器主提升管
先进炼油化工技术。
催化裂解生产低碳烯烃技术在工业中的应用
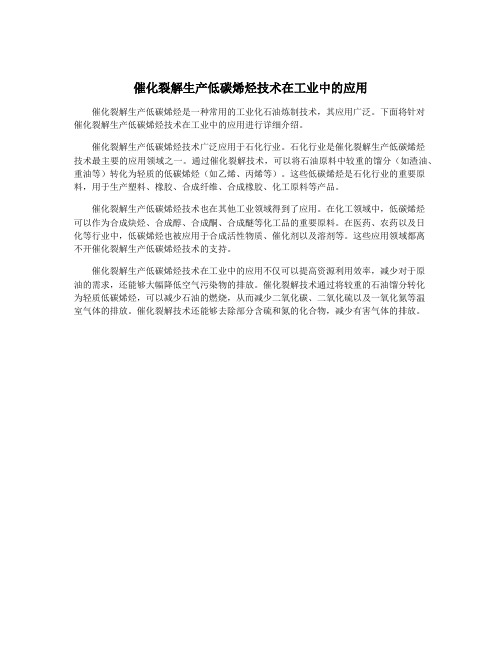
催化裂解生产低碳烯烃技术在工业中的应用
催化裂解生产低碳烯烃是一种常用的工业化石油炼制技术,其应用广泛。
下面将针对
催化裂解生产低碳烯烃技术在工业中的应用进行详细介绍。
催化裂解生产低碳烯烃技术广泛应用于石化行业。
石化行业是催化裂解生产低碳烯烃
技术最主要的应用领域之一。
通过催化裂解技术,可以将石油原料中较重的馏分(如渣油、重油等)转化为轻质的低碳烯烃(如乙烯、丙烯等)。
这些低碳烯烃是石化行业的重要原料,用于生产塑料、橡胶、合成纤维、合成橡胶、化工原料等产品。
催化裂解生产低碳烯烃技术也在其他工业领域得到了应用。
在化工领域中,低碳烯烃
可以作为合成炔烃、合成醇、合成酮、合成醚等化工品的重要原料。
在医药、农药以及日
化等行业中,低碳烯烃也被应用于合成活性物质、催化剂以及溶剂等。
这些应用领域都离
不开催化裂解生产低碳烯烃技术的支持。
催化裂解生产低碳烯烃技术在工业中的应用不仅可以提高资源利用效率,减少对于原
油的需求,还能够大幅降低空气污染物的排放。
催化裂解技术通过将较重的石油馏分转化
为轻质低碳烯烃,可以减少石油的燃烧,从而减少二氧化碳、二氧化硫以及一氧化氮等温
室气体的排放。
催化裂解技术还能够去除部分含硫和氮的化合物,减少有害气体的排放。
催化裂解制烯烃工艺及催化剂研究进展

催化裂解制烯烃工艺及催化剂研究进展摘要:低碳烯烃(乙烯、丙烯、丁烯和丁二烯等)是非常重要的基本有机化工原料,特别是乙烯的生产能力常被视为一个国家和地区石油化工发展水平的标志。
由于储能电池技术井喷式发展和环保要求进一步严格,电动汽车凭借行驶过程近零污染、节能、低使用成本的优势,替代燃油汽车成为不可逆转的发展趋势,随之而来将是交通用油消费量急剧下降。
因此,石油加工企业应提前布局实现由“燃油型”向“化工型”转型升级。
关键词:催化裂解制;烯烃工艺;催化剂引言低碳奥氏体是生产聚合物(聚乙烯和聚丙烯)的主要化学材料之一,也是石化工业的主要产品之一。
目前国内乙烯和丙烯供应不足,乙烯自给率约为64%,丙烯自给率约为77%,仍需大量进口。
此外,丙烯/乙烯需求比率上升,而产量比率下降。
随着化学工业的发展,对低碳奥氏体的需求迅速增长,其产量已成为经济发展的重要指标。
低碳奥氏体主要是通过热裂解或催化裂解获得的,其中热裂解技术是制造低碳奥氏体的主要技术,但热裂解反应温度高,二氧化碳排放量大;催化裂化反应温度低、目标产物收率高已成为近年来该技术的发展和应用前景。
用于生产低碳烯丙烯的原料可以是乙烷,丙烷,丁烷,也可以是轻/重型油脂,汽油,减压柴油等。
由于催化剂是影响催化裂解过程的重要因素,因此本文综述了轻质(轻油)作为低碳奥氏体催化剂生产率原料的研究进展。
1.催化性能影响因素制备方法对催化性能的影响,制备方法影响着金属颗粒在载体上的分散程度、载体与金属的相互作用力以及金属颗粒大小,从而影响催化剂的性能。
甲烷催化裂解反应中常用的制备方法有浸渍法、熔融法和共沉淀法等。
Guo等使用浸渍法和共沉淀法制备了一种由混合金属氧化物和氧化铝负载的Ni基催化剂。
研究发现与共沉淀法相比,浸渍法制备的催化剂中Ni颗粒发生了团聚。
这主要是因为在共沉淀法制备的催化剂中,Ni与载体之间的强相互作用力抑制了Ni颗粒的团聚。
Lazaro等比较了浸渍法和熔融法制备的Ni/TiO2催化剂的活性,研究发现浸渍法制备的催化剂初始活性较高,氢气产率为80%,但在反应200分钟后氢气产率迅速下降至40%。
以乙烯和丙烯为代表的低碳烯烃是重要的基础有机化工原料

以乙烯和丙烯为代表的低碳烯烃是重要的基础有机化工原料。
随着化学工业的发展,对低碳烯烃的需求日益增长。
目前的工业生产中,低碳烯烃的生产基本上依赖石油资源。
在世界范围内,石油资源贮量愈来愈少,通过煤或天然气为原料经由甲醇或二甲醚制取乙烯和丙烯等低碳烯烃工艺(MTO/MTP)近年来受到广泛关注。
甲醇制取低碳烯烃研究主要包括以乙烯和丙烯为主要产物的MTO技术和以丙烯为主要产物的MTP技术。
MTO工艺使用催化剂以SAPO-34分子筛为主,MTP工艺使用催化剂以ZSM-5分子筛为主,通过所使用分子筛的不同择形性能调控甲醇裂解产物中乙烯与丙烯的相对含量。
甲醇制取低碳烯烃是一强放热反应,生成低碳烯烃过程中产生大量的反应热,导致催化剂积炭失活速率加快,须使用具有催化剂连续再生的流化床反应器(如MTO工艺),或将甲醇原料部分转化为二甲醚以降低反应过程中的热效应(如MTP工艺)。
实际生产中,常用,尺等稀释剂对原料进行稀释,以降低整个反应的热效应,大量的水汽化和冷凝,增加能耗,同时降低生产效率。
在石油烃蒸汽裂解生产乙烯与炼油厂的催化裂化过程中,C4及C4以上烯烃是主要的副产物,针对目前乙烯和丙烯紧缺的现状,通过催化裂解将其转化为低碳烯烃(乙烯和丙烯)成为综合利用C4及C4以上烯烃的主要研究方向。
C4及C4以上烯烃催化裂解所用催化剂以ZSM-5分子筛为主,该过程是一较强吸热反应,为保持整个反应过程的平稳进行,常在原料中加入水蒸汽作为稀释剂或热载体。
甲醇制取低碳烯烃反应与C4及以上烯烃裂解所用催化剂均是以分子筛为主的固体酸催化剂,且二者目的产物相同,如果将这2个反应放在同一反应器中进行,则可以将甲醇裂解所释放的反应热提供给C4及以上烯烃裂解反应,从而使能量得到有效利用,避免二者单独反应时存在的热量移出与供入问题。
二者的共裂解会减轻反应系统的热负荷,对提高反应系统的稳定性和改善催化剂使用寿命有利,还可省掉或减少反应系统中水蒸汽用量。
- 1、下载文档前请自行甄别文档内容的完整性,平台不提供额外的编辑、内容补充、找答案等附加服务。
- 2、"仅部分预览"的文档,不可在线预览部分如存在完整性等问题,可反馈申请退款(可完整预览的文档不适用该条件!)。
- 3、如文档侵犯您的权益,请联系客服反馈,我们会尽快为您处理(人工客服工作时间:9:00-18:30)。
催化裂解生产低碳烯烃技术乙烯和丙烯是最重要的石油化工原料之一。
蒸汽裂解技术问世60多年来一直是生产乙烯和联产丙烯的主要技术。
可是,近 20 多年来随着乙烯和丙烯的需求逐年增加,丙烯/乙烯需求比呈上升趋势,丙烯/乙烯产出比呈下降趋势。
近 10 年来的情况如表 1 所列。
2010 年乙烯的需求约为 1.15 亿吨,丙烯的需求约为7000万吨,丙烯/乙烯需求比上升到0.61,而丙烯/乙烯产出比下降到0.34。
预计2011年丙烯的需求将增长5%,达到7350万吨,丙烯/乙烯的产出比还会下降。
表 1 全球丙烯/乙烯的需求比和蒸汽裂解装置的丙烯/乙烯产出比预计今后若干年全球丙烯需求的增速在5%以上,高于乙烯需求的增速,裂解原料的比例不会有大的变化,因此蒸汽裂解生产的丙烯不能满足需求的现状还将持续下去。
多年来,市场需求不足的丙烯主要由炼油厂常规催化裂化和高苛刻度催化裂化(石油化工厂称催化裂解,以下称催化裂解)副产的丙烯提供。
虽然近 20 多年来,出现了多种多产丙烯的专用技术,而且有一些已经工业应用,但由于种种原因,这些专用技术生产的数量有限,丙烯供应的紧张状况并未得到根本缓解。
据统计,2003 年全球丙烯的需求约为 5630 万吨,其中67%来自蒸汽裂解装置,30%来自炼油厂的催化裂化装置,2%来自丙烷脱氢装置,1%来自其它装置。
据统计,2010年全球丙烯的需求约为7000万吨,其中54%来自蒸汽裂解装置,37%来自炼油厂的催化裂化和催化裂解装置,9.5%来自烯烃易位、丙烷脱氢和C4~C8 烯烃裂解,0.5%来自其它装置。
预计今后20 年间石油和天然气仍然是人类需求最主要的能源,石油和天然气液仍将是石化原料的主要来源。
由于原料资源、价格、水资源、技术、投资和生产成本等多种因素的影响,预计丙烷脱氢、甲醇制烯烃等专用技术生产低碳烯烃会有一些增加,但不会增加很多,能够增加较多的仍然是石脑油蒸汽裂解/催化裂解和减压瓦斯油 /常压渣油催化裂化/催化裂解。
本文主要介绍石脑油催化裂解和炼油厂减压瓦斯油 /常压渣油催化裂解技术工业应用的进展。
1 蒸汽裂解生产低碳烯烃技术工业应用的现状据统计,到 2009 年底全球有 58 个国家的 216座石油化工厂建有蒸汽裂解装置,乙烯生产能力为13297.4 万吨/年。
蒸汽裂解的原料和产品收率如表 2 所列。
表 2 蒸汽裂解的原料和典型产品收率(一次通过,质量分数, %)①100 万吨/年乙烯大型裂解装置的能耗。
蒸汽裂解的产品收率因原料和裂解深度而异。
裂解深度低(较低的温度和压力),丙烯和所有副产品的收率都提高。
以乙烷为原料,裂解深度高,生产1t 乙烯用原料1.24 t,丙烯/乙烯产出比为 0.024;以丙烷为原料,裂解深度中到高,生产1t乙烯用原料 2.18~2.67 t,丙烯/乙烯产出比为 0.37~0.45;以丁烷为原料,裂解深度高,生产1t 乙烯用原料2.65 t,丙烯/乙烯产出比为 0.41;以石脑油为原料,裂解深度中到高,生产1t 乙烯用原料 2.60~3.80 t,丙烯/乙烯产出比为 0.40~0.57;以常压瓦斯油为原料,裂解深度中到高,生产1t乙烯用原料 3.60~4.09t,丙烯/乙烯产出比为 0.54~0.62。
通常,以轻石脑油为原料,产出比约为0.4;以轻瓦斯油为原料,产出比约为0.6。
2009 年全球蒸汽裂解装置所用的原料,石脑油约占50%,乙烷约占30%,其它原料(丙烷、丁烷和常压瓦斯油等)约占20%。
欧洲和亚洲国家所用的原料主要是石脑油。
西欧国家所用的原料中石脑油约占72%,中欧和中国所用的石脑油约占80%。
美国乙烷用量约为56%,丙烷约为18%,丁烷约为3%,石脑油和常压瓦斯油约为23%。
中东国家(沙特、伊朗、科威特、卡塔尔和阿联酋)所用的原料主要是乙烷。
乙烷约占71%,石脑油约占15%,丙烷约占12%,丁烷约占2%。
鉴于这种情况,蒸汽裂解装置的丙烯/乙烯产出比远低于丙烯/乙烯需求比,蒸汽裂解装置生产的丙烯远不能满足需求。
为了改变这种状况,多年来许多国家的石化工作者都在想方设法开发新技术,提高丙烯收率,直至 2010 年才有所进展。
其中最重要并有望在工业上推广应用的就是石脑油催化裂解技术。
2 石脑油催化裂解多产低碳烯烃技术石脑油催化裂解是石油化工领域的一项前沿技术,正在进行示范装置试验,即将工业应用。
近二十多年来,不少国家都投入大量人力、物力、财力潜心研究,都进展不大,但在 2010 年有了突破。
美国 KBR 公司与韩国化工技术研究院合作开发的石脑油催化裂解( ACO)技术在韩国 SK 能源公司蔚山炼油厂建设的示范装置于 2010 年 10 月开始运转。
2011 年 1 月报道,运转得到满意结果,达到了丙烯+乙烯,特别是丙烯高收率的预期。
据介绍,该石脑油催化裂解新技术的产品收率如表 3 所列。
表 3 石脑油催化裂解与蒸汽裂解的产品收率(摩尔分数, %)与蒸汽裂解相比,催化裂解的优点如下:一是丙烯/乙烯产出比提高,可以接近 1.0;二是能多产15%~25%乙烯+丙烯,决定于操作条件;三是裂解汽油中芳烃含量高 20%~25%;四是每吨乙烯的生产成本约可减少 90 美元;五是规模经济性好,催化裂解单反应器乙烯+丙烯生产能力可达 150 万吨/年,而目前成熟的蒸汽裂解炉单炉乙烯最大生产能力约为 20 万吨/年,乙烯+丙烯生产能力约为 30 万吨/年。
催化裂解技术采用 KBR 公司开发的正流型催化裂化反应系统和韩国化工技术研究院开发的专用催化剂,将石脑油选择性催化转化为丙烯和乙烯。
反应系统的结构是正流型,有提升管、紧固式旋风分离器和第三级分离器以及专用的催化剂再生系统,在许多方面非常类似于炼油厂的催化裂化装置。
但也有一些不同的特点:一是骤冷换热器,反应器顶部流出物冷却与裂解炉类似,产生高压蒸汽,因此工艺能效提高,而这种换热器在催化裂化装置上是没有和不能使用的,因为催化裂化反应流出物中有大量油浆会发生严重的结垢;二是热平衡,催化裂解是吸热反应,因为原料油轻,催化剂上的生焦量不足以满足反应需要的热量,为保持热平衡,必须向反应系统提供热量, KBR 公司专门设计的催化剂与燃料连续燃烧系统已通过示范试验;三是催化剂/反应产物分离,虽然旋风分离器非常有效,但总会有一些催化剂细粉被反应产物带入反应器, KBR 公司专门设计的催化剂细粉脱除系统已通过示范试验。
催化裂解技术的关键是专用催化剂。
韩国化工技术研究院专门开发的催化剂机械性能、水热稳定性和生产低碳烯烃的选择性都比较好。
KBR公司称,根据其 Superflex 技术在南非 Seeunda 合成油厂工业装置的应用情况,预计石脑油催化裂解的中试结果能够在示范装置/工业装置上重复。
催化裂解工艺的回收系统采用前脱丙烷流程,生产聚合级乙烯和丙烯。
流程的大部分都类似于蒸汽裂解装置典型的回收系统,但也有一些不同的特点,如在反应流出物中有一些微量杂质如氮氧化物、氧和其它杂质,都必须脱除。
这些技术问题在催化裂解的工艺流程中都已经解决。
KBR 公司称,因为催化裂解的乙烯+丙烯收率比传统的蒸汽裂解高 15%~25%,而且提高的部分主要是丙烯。
鉴于市场需求丙烯的增速高于乙烯,所以催化裂解的产品收率与分布更适合于今后若干年市场的需求。
催化裂解技术可以用于替代计划新建的蒸汽裂解装置,也可用于原有蒸汽裂解装置的扩能改造。
KBR 公司称,示范装置运行稳定和成功以后,希望与中国、中东或南美的生产厂家合作建设工业装置。
KBR公司称,已与潜在用户洽谈技术转让方案,预计2011年可以达成工业规模催化裂解项目协议。
3 炼油厂减压瓦斯油/常压渣油催化裂解多产低碳烯烃技术此项技术已经成熟,有望进一步扩大工业应用。
炼油厂催化裂化装置的主产品是汽油,丙烯是副产品。
催化裂化装置多产丙烯有两种方法:一种是采用择形沸石ZSM-5助剂的常规催化裂化;另一种是采用特殊配方专用催化剂的催化裂解。
两种方法的产品收率如表 4 所列。
表 4 催化裂化多产丙烯两种方法的产品收率(摩尔分数,%)表 5 催化轻汽油中的烯烃选择性裂化的产品收率(摩尔分数,%)采用择形沸石 ZSM-5 助剂多产丙烯的常规催化裂化主要是将用主催化剂生成的催化裂化轻汽油中的烯烃选择性裂化为 C3/C4 烯烃。
这种择形沸石助剂选择性裂化的产品收率如表 5 所列。
美国炼油厂于 20 世纪 80 年代中期首先使用ZSM-5 助剂提高催化裂化汽油的辛烷值。
当时ZSM-5 助剂的添加量只占装置催化剂藏量的 2%,因为用ZSM-5 助剂可使催化轻汽油中的烯烃转化为丙烯和丁烯。
到了 90 年代美国炼油厂使用 ZSM-5助剂的催化裂化装置越来越多,大多数装置都添加2%~5%的ZSM-5 助剂,使丙烯收率提高 2%~3%而达到 6%~7%。
由于长期以来,美国丙烯的市场价格大约是汽油的 1.9 倍,炼厂为提高经济效益, ZSM-5 助剂的用量进一步增加,丙烯收率也进一步提高。
与此同时, ZSM-5 助剂的品种也由低活性和中活性发展到高活性和超高活性。
国际市场供应ZSM-5 助剂的生产商很多,但选择形裂化效果最好、工业应用最多的是 Grace Davison 公司的高活性助剂OlefinsMax 和超高活性助剂 OlefinSultra。
前者2001 年问世,含 25%用磷改性的 ZSM-5 小晶粒;后者 2003 年问世,含 40%用磷改性的 ZSM-5 小晶粒。
高活性和超高活性助剂的问世,使催化裂化多产丙烯的收率进一步提高。
但是,多产丙烯就少产汽油,也使汽油中的芳烃含量增加、密度变大。
由于催化裂化汽油是炼油厂成品汽油的主要组分,为确保生产合格的清洁汽油产品,美国和西欧炼油厂的催化裂化装置用 ZSM-5 助剂多产丙烯,一般都控制丙烯收率在 10%左右。
其主要原因有三:一是多用 ZSM-5 助剂会使催化裂化主催化剂稀释,转化率下降,从而使主催化剂添加量增加,成本上升;二是要得到合格的清洁汽油产品,催化裂化汽油组分的芳烃不能过多,密度不能过大;三是不能突破催化裂化装置反应器/主分馏塔、湿气处理或处理多产的 C3 和 C4 烯烃(回收丙烯或烷基化)能力的极限[14]。
这项技术主要用在美国和西欧。
减压瓦斯油 /常压渣油催化裂解技术是在用ZSM-5 助剂多产丙烯的常规催化裂化技术基础上发展起来的生产更多丙烯( >15%)的新技术。
与常规催化裂化技术的主要区别是,采用更高的提升管反应温度( 530~600 ℃)、更高的剂油比( 12~20)和更低的烃分压,并采用特殊配方的专用催化剂,使一次裂化和择形裂化结合,使催化汽油中的多碳烯烃更多地转化为乙烯、丙烯和丁烯,还可以与ZSM-5 助剂一起使用提高生产低碳烯烃的灵活性。