ACSP_AESOP_ANZAPS_APSA简介_bc69c1bf_6efd_4
亚克勒夫GC35数字压力传感器用户说明书

PIP #: TR-PI-105Applicable to:GC35PROGRAMMING PLANT AIR LINE PRESSURE CONTROL ON THE GC35 INDICATING PRESSURE TRANSMITTERThe GC35 Digital Pressure Transmitter is compact and flexible with many usages. It can be easily programmed to monitor and control plant air line pressure. The GC 35 can be acquired with many different ranges but for this application a transmitter with 0 to 150 psi range shall be selected, 4-20 mA analog output, and one switch PNP.Figure 1 - GC35 Pressure TransmitterPlant Line Compressor Pressure Control Example:This example demonstrates the control of a plant air line compressor application with a full loaddischarge pressure of 100 psi and an unload discharge pressure of 110 psig by controlling the 4-20 mA output signal with a programmable regulator. Also, to shut down the compressor and activate an audible warning alarm if line pressure exceeds 115 psi by using an external relay normally opened to turn on the audible alarm and normally closed to shut down the compressor.Figure 2 – GC35 Pressure Transducer Installation ExampleInstallation:Connect transmitter, analog output, compressor shutdown and audible warning buzzer switches per application, diagrams below and manual instructions.Figure 3 – GC35 Pressure Transducer WiringFigure 4 – GC35 Pressure Transducer Switch and Analog Output WiringCOMPRESSED AIRPlant Line Compressor Pressure Control Settings Method:Procedure to program the GC35 transmitter to control plant air line pressure. Offset analog output from 0 psi to 100 psi. That, is 66.7 % of full range corresponding to 100 psi (4 mA). Scale down the upper range from 150 psi to 110 psi. 73.3% of full scale is equivalent to 110 psi (20 mA). Subsequently, set switches set point and dead bands.GC35 Transmitter Function Setting Method:∙ Press and hold MODE button for more than three seconds to get into program mode.∙ Press UP or Down arrow to make changes.∙ Press and release MODE button to select changes and to walk through the menu.∙ Continue to step-1 after power-on message.∙ Press and hold MODE button for more than three seconds to return tomeasuring mode.Step 1∙ CAP To select hysteresis (HYS) or Window comparator (yin). ∙ Select HYS to control analog output. ∙ Press UP or Down arrow to display HYS.∙ Press and release MODE button to select and move to the next step.Step 2∙ oPC To select switch type (NPN or PNP).∙ It is a matter of preference. PNP switch shall be used for thisapplication.∙ Press UP or Down arrow to display PNP.∙ Press and release MODE button to select and move to the next step.Step 3∙ FiL To enter filter selection. Filter selection, there are five filterselections (F1 to F5).∙ Use the filter function to improve analog output and difficult to readdisplay if pressure oscillates.∙ Press UP or Down arrow until F1 is displayed (pressure fluctuation isnot anticipated).∙ Press and release MODE button to select and move to the next step.Step 4∙ ECo To turn ON or OFF power saver.∙ Press Up or Down arrow until EoF is displayed (power saver off). ∙ Press and release MODE button to select and move to the next step.Step 5∙ LrG To select ring LED light. There are two options Lr0 to turn off ringlight or Lr1 to turn on ring light.∙ Press Up or Down arrow until Lr1 is display.∙ Press and release MODE button to select and move to the next step.Step 6∙ Uni To select units (arbitrary or psi).∙ Press Up or Down arrow until PSI is displayed.∙ Press and release MODE button to select and move to the next step.Step 7∙ A-L To enter analog output zero reference corresponding to 4 mA. ∙ The operational range is from 100 to 110 psi. Therefore, set 100 psias the zero reference 4 mA analog output (66.7% of full range). ∙ Press Up or Down arrow until 66.7 is displayed.∙ Press and release MODE button to select and move to the next step.Step 8∙ A-H To enter span analog output reference corresponding to 20 mA. ∙ The operational range is from 100 to 110 psi. Therefore, set 110 psias the span 20 mA analog output (73.3% of full range). ∙ Press UP or Down arrow until 73.3 is displayed.∙ Press and release MODE button to select and move to the next step.GC35 Transmitter Switch Set Point and Dead Band Settings Method:∙ Press and hold MODE button less than three seconds to get into program mode.∙ Press UP or Down arrow to make changes.∙ Press and release MODE button to select changes and to move to the next step.∙ Continue to step-1 after once in program mode.∙ Press and hold MODE button for more than three seconds to return to measuring mode.Step 1∙ US1 To select in use (USE) or not in use (noU).∙ Press UP or Down until USE is displayed to configure output switch. ∙ Press and release MODE button to select and move to the next step.Step 2∙ A1 To enter output 1 switch set point. ∙ Set switch to change state at 115 psi. ∙ Press UP or Down until 115.0 is displayed.∙Press and release MODE button to select and move to the next step.Step 3∙ B1 To enter dead band.∙ Set 5 psi dead band to deactivate at 110 psi. ∙ Press UP or Down until 5.0 is displayed.∙Press and release MODE button to select and move to the next step.Step 4∙ On1 To delay switch turn on.∙ Delay switch turn on shall not be used for this application. ∙ Press Up or Down arrow until 0.00 is displayed.∙ Press and release MODE button to select and move to the next step.Step 5∙ OF1 To delay switch turn off.∙ Delay switch turn off shall not be used for this application. ∙ Press Up or Down arrow until 0.00 is displayed.∙Press and release MODE button to select and move to the next step.Step 6∙ SAv To save set point, dead band, and on/off time delay. ∙Set point, dead band, and on/off time delay can be stored onstorage S-1 or S-2 (save set point, dead band, and on/off time delay on S1).∙ Press UP or Down arrow until S-1 is displayed.∙ Press and release MODE button to select and move to the next step.Step7∙Lod To load set point, dead band, and on/off time delay.∙Load set point, dead band, and on/off time delay can store onstorage L-1 or L-2 (load set point, dead band, and on/off timedelayonL1).∙Press UP or Down arrow until L-1 is displayed.∙Press and release MODE button to select and move to the next step.Step8∙LoP Loop check mode allows program and analog output verificationwith the transmitter pressurized or non-pressurized. It simulates theprocess and allows for troubleshooting.∙Press Up or Down arrow to simulate pressure values.∙After verification press and hold MODE button for more than threeseconds to return to measuring mode.Function Verification:The GC35 loop-check allows program, switch and analog output verification with the transmitterpressurized or non-pressurized.Analog Output Test:Confirm analog output wiring per figure 3 and 4 diagrams or installation and maintenance instructions.Analog output can be tested during loop check mode or measurement mode. Change loop check value or apply equivalent pressure to test the analog output (see results below for reference).∙Connect amp-meter per manual instructionsor diagram above.∙Press the Up or Down arrow until 100.0 isdisplayed or apply 100 psi.∙Verify amp meter reading (4.00 mA).∙100 psi corresponds to 0% FS analog signal(4 mA at 100 psi).Switching Verification:Ensure switch wiring per figure 3 and 4 diagrams or installation & maintenance instructions. Switch verification can be tested during measurement mode or loop check. Change loop check value or apply equivalent pressures (see results below for reference).∙Press the Up or Down arrow until 105.0 isdisplayed or apply 105 psi.∙Verify amp meter reading (12.00 mA).∙105 psi corresponds to 50% FS analog signal(12 mA at 105 psi).∙Press the Up arrow until 110.0 is displayedor apply 110 psi.∙Verify amp meter reading (20.0 mA).∙110 psi corresponds to 100% FS analogsignal (20 mA at 110 psi).∙ A 290 ohms resistor shall be use as theswitch load to verify switch. Wire switch permanual instructions or figure above.∙Press the Up or Down arrow until 100.0 isdisplayed or apply 100 psi.∙Switch is in normal state (OFF)∙Place voltmeter leads across resistor and verify voltage reading (0 V dc).∙Press the Up arrow until 115.0 is displayed or increase pressure up to 115 psi.∙Switch turns ON.∙Verify voltmeter reading (28 VDC).∙External relay energizes.∙Relay normally closed switch opens - compressor shuts down.∙Relay normally open closes - audible alarm turns ON.∙Press the Down arrow until 110.0 is displayed or decrease pressure to 110 psi. ∙Verify voltage reading (0 V dc).∙Switch changes to normal state (OFF).。
赛普拉斯CP2104-EK评估板用户手册说明书

Rev. 0.8 1/21Copyright © 2021 by Silicon LaboratoriesCP2104-EK1. Kit ContentsThe CP2104 Evaluation Kit contains the following items:⏹ CP2104 Evaluation Board ⏹ RS232 Serial Cable ⏹ USB Cable ⏹ Quick Start Guide2. Relevant DocumentationApplication notes can be found on the Interface Application Notes page for all fixed-function devices:/interface-appnotes .⏹ AN721: USBXpress™ Device Configuration and Programming Guide — Customize the VID, PID,serial number, and other parameters stored in the CP2104 one-time programmable ROM.⏹ AN197: Serial Communications Guide for CP210x — Programming guide for using the Virtual COM Port (VCP) drivers.⏹ AN169: USBXpress® Programmer's Guide — Programming guide for using the USBXpress drivers.⏹ AN220: USB Driver Customization — VCP or USBXpress driver customization tool.⏹ AN223: Runtime GPIO Control for CP210x — Programming guide and DLL for runtime control of the CP2104 GPIO pins.⏹ AN571: CP210x Virtual COM Port Interface — USB interface details for CP210x devices.3. Software SetupThe software packages and documentation for the CP2104 kit can be found on the device page (h ttps:///interface/usb-bridges/classic/device.cp2104) and include the following:⏹ CP210x Drivers (Software & Tools Tab)⏹ USBXpress Host SDK (Software & Tools Tab)⏹ Documentation: (Tech Docs Tab)● CP2104 data sheet● CP2104 evaluation kit user's guide (this document)3.1. USBXpress Driver Development KitThe Silicon Laboratories USBXpress ® Development Kit provides a complete host software solution for interfacing to CP210x devices. No USB protocol or host device driver expertise is required. Instead, a simple, high-level Application Program Interface (API) for the host software is used to provide complete USB connectivity. The USBXpress Development Kit includes Windows device drivers, Windows device driver installer, host interface function library (host API) provided in the form of a Windows Dynamic Link Library (DLL). See Application Note AN169,“USBXpress® Programmer's Guide” for detailed information on using the USBXpress drivers.The USBXpress drivers are available here: https:///developers/direct-access-drivers .Click the USBXpress Development Kit link in the Downloads section to download the USBXpress drivers. Run the installer and follow the steps to install the software to the desired location. The default installation directory is C:\SiliconLabs\MCU\USBXpress_SDK .Further installation instructions for the WinCE drivers can be found in the ReadMe.txt file contained inside the driver package.CP2104-EK4. CP2104 Hardware InterfaceThe evaluation board is connected to a PC as shown in Figure 1.1.Connect one end of the USB cable to a USB Port on the PC.2.Connect the other end of the USB cable to the USB connector on the CP2104 evaluation board.3.Connect one end of the RS232 serial cable to the DB-9 connector on the CP2104 evaluation board .4.Connect the other end of the RS232 serial cable to the target serial device.Figure 1.Hardware SetupCP2104 EKSerial DeviceCP2104 USB-to-UART Bridge1234CP2104-EK5. CP2104 Software InterfaceIf the Virtual COM Port drivers are used, the CP2104 will appear as a COM port in the Device Manager, as shown in Figure 2. The CP2104 will always use the lowest available COM port for operation. For instance, if COM ports 1and 2 are in use by other peripherals and applications, the CP2104 will use COM 3.The CP2104 functions identically to a COM port from the reference point of both the host application and the serial device, and it can support serial device control requests defined in the Microsoft Win32® Communications API.Examples for how to communicate with the device as a serial COM port are includedin AN197 on the /interface-appnotes page or in the USBXpress Host SDK.If the USBXpress drivers are used, the CP2104 will appear as a USB USBXpress device as shown in Figure 2.Examples for how to communicate with the device using the USBXpress interface are included in AN169 on the /interface-appnotes page.Figure 2.CP2104 in Device ManagerCP2104-EK6. Target BoardThe CP2104 Evaluation Kit includes an evaluation board with a CP2104 device pre-installed for evaluation and pre-liminary software development. Numerous input/output (I/O) connections are provided to facilitate prototyping using the evaluation board. Refer to Figure3 for the locations of the various I/O connectors.⏹ P1 USB connector for USB interface⏹ P2 DB9 connector for RS232 interface⏹ J1 UART signal access connector⏹ J2, J3 GPIO access connector⏹ J4 Power connector⏹ DS0–DS3 Green GPIO LEDs⏹ DS4 Red SUSPEND indicator LEDFigure3.CP2104 Evaluation Board with Default Shorting Blocks Installed6.1. LED Headers (J2, J3)Connectors J2 and J3 are provided to allow access to the GPIO pins on the CP2104. Place shorting blocks on J2 and J3 to connect the GPIO pins to the four green LEDs DS0–DS3. These LEDs can be used to indicate active communications through the CP2104. Table1 shows the LED corresponding to each header position.Table 1. J2 and J3 LED LocationsLED PinsDS0J3[3:4]DS1J3[1:2]DS2J2[3:4]DS3J2[1:2]6.2. Universal Serial Bus (USB) Interface (P1)A Universal Serial Bus (USB) connector (P1) is provided to facilitate connections to the USB interface on the CP2104. See Table2 for the USB pin definitions.Table 2. USB Connector Pin DescriptionsPin #Description1VBUS2D-3D+4GND (Ground)CP2104-EK6.3. UART Signals (P2, J1)An RS232 transceiver circuit and DB9 connector (P2) are provided on the evaluation board to connect the CP2104virtual serial port to external serial devices. See Table 3 for the RS232 P2 pin descriptions. The J1 connector is provided to facilitate direct access to the CP2104’s UART signals. Shorting blocks on J1 are required to connect the UART signals to P2. See Table 4 for J1 pin descriptions.6.4. Power Connector (J4)This header (J4) is included on the evaluation board to provide several power options. The following describes the function of each pin:⏹ Pins 1–2: Connects CP2104 VIO input (Pin 5) to CP2104 VDD (Pin 6). Remove the shorting block to powerVIO from an external source.⏹ Pins 3–4: Connects the main +3V net to the CP2104 VDD (Pin 6). The main +3V net powers the other components (four green LEDs and RS232 Sipex Part) on the evaluation board.Table 3. RS232 Pin DescriptionsPin Signal CP2104 Direction Description 1DCD Input Data Carrier Detect 2RXD Input Receive Data 3TXD Output Transmit Data 4DTR OutputData Terminal Ready5GND Ground 6DSR Input Data Set Ready 7RTS Output Request to Send 8CTS Input Clear to Send 9RIInput Ring IndicatorTable 4. J1 Pin DescriptionsPins Signal CP2104 Direction Description 1–2TXD Output Transmit Data 3–4RXD Input Receive Data 5–6DTR Output Data Terminal Ready7–8RI Input Ring Indicator 9–10DCD Input Data Carrier Detect 11–12DSR Input Data Set Ready 13–14CTS Input Clear to Send 15–16RTSOutputRequest to SendCP2104-EK 7. SchematicCP2104-EKD OCUMENT C HANGE L ISTRevision 0.1 to Revision 0.2⏹Updated "6.4. Power Connector (J4)" on page 5 to reflect the updated schematic.⏹Updated J4 in Figure 4, “CP2104 Evaluation Board Schematic,” on page 6.Revision 0.2 to Revision 0.3⏹Updated "7. Schematic" on page 6.Revision 0.3 to Revision 0.4⏹Updated "2.1.1. Virtual COM Port Driver Installation for Windows" on page 1.⏹Updated "2.2.1. USBXpress Installation for Windows" on page 2.⏹Removed “2.2.2. USBXpress Installation for Windows 98SE” on page 2.Revision 0.4 to Revision 0.5⏹Updated Figure 3 with shorting blocks installed.Revision 0.5 to Revision 0.6⏹Updated "3. Software Setup" on page 1.Revision 0.6 to Revision 0.7⏹Updated “1. Kit Contents” to change CD-ROM to DVD.⏹Added “2. Relevant Documentation”.⏹Updated “3. Software Setup” to point to the drivers on the website.⏹Updated Figure 1 and Figure 2.Revision 0.7 to Revision 0.8⏹Updated "Kit Contents" on page 1 to remove DVD.⏹Updated "Relevant Documentation" on page 1.⏹Updated "Software Setup" on page 1.IoT Portfolio/IoTSW/HW/simplicityQuality/qualitySupport & Community/communitySilicon Laboratories Inc.400 West Cesar Chavez Austin, TX 78701USADisclaimerSilicon Labs intends to provide customers with the latest, accurate, and in-depth documentation of all peripherals and modules available for system and software implementers using or intending to use the Silicon Labs products. Characterization data, available modules and peripherals, memory sizes and memory addresses refer to each specific device, and “Typical” parameters provided can and do vary in different applications. Application examples described herein are for illustrative purposes only. Silicon Labs reserves the right to make changes without further notice to the product information, specifications, and descriptions herein, and does not give warranties as to the accuracy or completeness of the included information. Without prior notification, Silicon Labs may update product firmware during the manufacturing process for security or reliability reasons. Such changes will not alter the specifications or the performance of the product. Silicon Labs shall have no liability for the consequences of use of the information supplied in this document. This document does not imply or expressly grant any license to design or fabricate any integrated circuits. The products are not designed or authorized to be used within any FDA Class III devices, applications for which FDA premarket approval is required, or Life Support Systems without the specific written consent of Silicon Labs. A “Life Support System” is any product or system intended to support or sustain life and/or health, which, if it fails, can be reasonably expected to result in significant personal injury or death. Silicon Labs products are not designed or authorized for military applications. Silicon Labs products shall under no circumstances be used in weapons of mass destruction including (but not limited to) nuclear, biological or chemical weapons, ormissiles capable of delivering such weapons. Silicon Labs disclaims all express and implied warranties and shall not be responsible or liable for any injuries or damages related to use of a Silicon Labs product in such unauthorized applications.Trademark InformationSilicon Laboratories Inc.®, Silicon Laboratories®, Silicon Labs®, SiLabs® and the Silicon Labs logo®, Bluegiga®, Bluegiga Logo®, ClockBuilder®, CMEMS®, DSPLL®, EFM®, EFM32®, EFR, Ember®, Energy Micro, Energy Micro logo and combinations thereof, “the world’s most energy friendly microcontrollers”, Ember®, EZLink®, EZRadio®, EZRadioPRO®, Gecko®, Gecko OS, Gecko OS Studio, ISOmodem®, Precision32®, ProSLIC®, Simplicity Studio®, SiPHY®, Telegesis, the Telegesis Logo®, USBXpress®, Zentri, the Zentri logo and Zentri DMS, Z-Wave®, and others are trademarks or registered trademarks of Silicon Labs. ARM, CORTEX, Cortex-M3 and THUMB are trademarks or registered trademarks of ARM Holdings. Keil is a registered trademark of ARM Limited. Wi-Fi is a registered trademark of the Wi-Fi Alliance. All other products or brand names mentioned herein are trademarks of their respective holders.。
PCSC SIM Series Controller 控制器型号指南
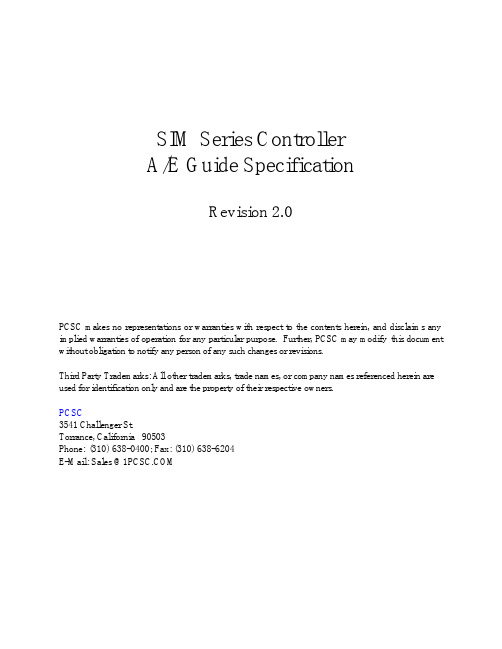
SIM Series ControllerA/E Guide SpecificationRevision 2.0PCSC makes no representations or warranties with respect to the contents herein, and disclaims any implied warranties of operation for any particular purpose. Further, PCSC may modify this document without obligation to notify any person of any such changes or revisions.Third Party Trademarks: All other trademarks, trade names, or company names referenced herein are used for identification only and are the property of their respective owners.PCSC3541 Challenger St.Torrance, California 90503Phone: (310) 638-0400; Fax: (310) 638-6204E-Mail:***************1. System Characteristics1.1 Logical Processing Controller (LPC)1.1.A The Logical Processing Controller is used as the sub-component to the SecurityManagement System for the purpose of initiating all decision making criteria as itrelates to the cardholders, readers, and associated hardware connected.Decisions made by the LPC are uploaded to the host computer as historicalevents. Each LPC shall:1.1.B The LPC shall be listed for Underwriters Laboratory (UL):1.1.B.1 UL294 (Access Control System)1.1.B.2 UL1076 (Proprietary Alarm Monitoring System)1.1.B.3 CE Mark1.1.C Support year 2000 compliance without the need for future software orhardware updates.1.1.D Operate without the need for the host to be on-line. No decisions shall bereliable on the host.1.1.E Utilize RS485 multi-point communications to the host for communicationsintegrity. Any system that cannot maintain communications integrity when one ormore LPC is off-line shall not be accepted.1.1.F Have the ability of supporting a minimum of 4 individual readers within a singleenclosure with the ability of expanding to 8 readers while consuming only oneterminal address.1.1.G Have a minimum of 32 inputs and 4 outputs expandable to 66 input points and28 output relays and 8 voltage outputs.1.1.H Include a request-to-exit and door status contact input for each reader withoutthe need for additional modules.1.1.I Detect “forced entry” and “door left open”. A separate action is required foreach.1.1.J Allow mapping of readers to any output address within the same controller.1.1.K Support up to 64 time periods1.1.K.1 A total of 7 start/7 stop intervals, per time period, shall be included.1.1.L Support up to 999 authorization groups1.1.L.1 Each authorization group shall include one (1) time period.1.1.L.2 Each cardholder shall support four (4) authorization groups.1.1.L.3 Each authorization group shall have an alphanumeric description.1.1.M Support up to 365 user selected holidays.1.1.N Allow all unused door logic, such as door strike relays, request-to-exit inputs,and door status inputs to be assigned as general-purpose points.1.1.O Support optional modules for additional customization of inputs and outputs.The following modules shall be available:1.1.O.1 Output Point Module. A minimum of 16 additional output pointsshall be provided1.1.O.2 Combination Module. Where inputs and outputs are necessarywithin the same enclosure, a combination of 16 inputs and 16outputs shall be provided.1.1.P Support a minimum of 8,000 and expandable to 20,000 cardholderassignments.1.1.Q Support a minimum of 4,000 historical transactions in the event communicationsto the host is disrupted.1.1.Q.1 Each LPC transaction shall be time-stamped with the following:1.1.Q.1.a Date (Month, Day, Year)1.1.Q.1.b Time (Hours, Minutes)1.1.Q.1.c Message Text1.1.R Support the downloading of cardholder names in addition to the cardholdernumber.1.1.S Support “reader detection” in the event the reader has been removed or cut.No additional wires or switches shall be used. An alarm condition shall beannunciated.1.1.T Backup programmed data for a minimum of five (5) years without AC power.1.1.U Maintain historical information for a minimum of five (5) years without ACpower.1.1.V Support direct or voice grade 3002 phone line connection1.1.W Automatically adjusts for daylight savings time and leap year independent of thehost system.1.1.X Be supplied with battery backup for a period of four (4) hours.1.1.Y Support a variety of reader technologies. Only non-proprietary readers shall beapproved. Include manufacturer, model number and cut sheet with proposal.1.1.Y.1 Readers shall be provided with the ability of showing a red andgreen LED.1.1.Y.2 The LPC shall show the following characteristics using the bi-colorLED’s:1.1.Y.2.a Power LED (constant red LED)1.1.Y.2.b Card data being processed (fast blink red and greenLEDs)1.1.Y.2.c Access authorized (solid green LED)1.1.Y.2.d Denied access (constant red after card data processing)1.1.Y.2.e Escort authorized (Slow blink red and green LED’s)1.1.Y.2.f Two man rule (slow blink red/green LED’s)1.1.Y.3 Card read errors of four (4) or more within one minute shall bereported to the host.1.1.Z Support the following card/reader technologies as a minimum:1.1.Z.1 Magnetic Stripe1.1.Z.2 Proximity1.1.Z.3 Biometrics1.1.Z.4 Wiegand1.1.Z.5 Protech Barium Ferrite1.1.Z.6 Vehicle Identification1.1.Z.7 Bar Code1.1.Z.8 Keypad1.1.AA Support multiple technologies simultaneously.1.1.BB Support card plus pin, card, or pin only type readers Support a minimum of three (3) “Card Classes” which can be utilized withUser Programmable Logic to interact with external devices or functions, suchas lights, sirens, or HVAC.1.1.DD Integrate each physical input independent of its polarity.1.1.EE Maintain the expiration date for each cardholder. Once the date is reachedthe card will automatically be disabled. No access shall be authorized.1.1.FF Maintain a second expiration date for each cardholder. This date shall beused to prevent access to a unique group of readers, such as parking lots orrecreational facilities. Once the date has expired the card shall be disabledonly for this group of readers.1.1.GG Maintain three (3) access times for each door location; Standard, Long, andEgress.1.1.GG.1 STANDARD access time shall be used for the majority of thecardholders and shall support a range from 0-254 seconds.1.1.GG.2 LONG access time shall be assigned to cardholders who requireextra time to enter/exit a location, such a delivery persons, or tomeet American with Disabilities Act (ADA) requirements. The Longaccess time shall support from 0-254 seconds. A Long shunt timeshall also be required to prevent a door held open alarm exceedingthe standard shunt time. The time shall not require additionalhardware nor be dependent on the host for the decision.1.1.GG.3 EGRESS time shall be used for request to exit devices and support atime between 0 - 254 seconds.1.1.HH Have the ability to maintain an automatic door unlock during specific hoursand days.1.1.II Be required to activate the automatic unlock only after the first valid cardaccess at that location within a pre-defined period of time.1.1.JJ Support three (3) “zones” of Anti-Passback; Building, Department, Parking.1.1.KK Support three (3) “levels” of Anti-Passback; Strict, Soft, and Lenient.1.1.KK.1 STRICT Anti-Passback prevents access after the first attempt andforwards a message to the host. An exit reader shall be used to exitthe door location.1.1.KK.2 SOFT Anti-Passback authorizes access with the use of the card thesecond time using an “in” reader. An event message shall beforwarded to the host indicating entry/exit out of sequence.1.1.KK.3 LENIENT Anti-Passback uses the Entry/Exit criteria, but allowsautomatic sequencing between Department and Building Status if notin proper sequence.1.1.LL Utilize User Programmable Logic (UPL) for the manipulation of inputs, cardstatus, outputs, and elevators.1.1.LL.1 Each LPC shall allow the following inputs to trigger UPL:1.1.LL.1.a Card Access / Card Denied1.1.LL.1.b P hysical Input Point1.1.LL.1.c Time periods1.1.LL.2 Each LPC shall support the following computations for UPL:1.1.LL.2.a Increment Count (range 0-65000)1.1.LL.2.b D ecrement Count (range 0-65000)1.1.LL.2.c Increment by Seconds or Minutes (0-65000)1.1.LL.2.d D ecrement by Seconds or Minutes (0-65000)1.1.LL.2.e Clear1.1.LL.2.f Reset1.1.LL.2.g Flip/Flop (Flip output toggle)1.1.LL.3 Each LPC shall support the following results from UPL:1.1.LL.3.a Activate / De-Activate1.1.LL.3.b S hunt / Un-Shunt1.1.LL.3.c Pause / Resume (suspend/restore)1.1.LL.3.d O verride for 1 Cycle1.1.LL.4 Escort/Visitor Control1.1.LL.4.a Maintain the assignment of access cards for VisitorControl. Each visitor shall be assigned an “EscortRequired” status requiring an employee or “EscortCapable” cardholder to grant a valid entry. The decisionshall not be dependent on the host.1.1.LL.4.b A ll visitor badges shall expire automatically at midnight ofthe date issued without operator intervention. Based uponprogrammed expiration date.1.1.LL.5 Two-Person Minimum Occupancy Rule (TPMOR) for high securityapplications.1.1.LL.5.a The TPMOR feature requires the first two- (2) people tobadge into an area at the same time before access isgranted. An exit reader shall be used for decrementingthe count.2 Execution2.1 The supplier shall install all system components and appurtenances in accordance withthe manufacturer’s instructions, and shall furnish all necessary interconnections, services,and adjustments required for a complete and operable system as specified and shown.Control signal, communications, and data transmission lines grounding shall be installedas necessary to preclude ground loops, noise, and surges from adversely affectingsystem operation. Provide mounting hardware as required. .2.2 All low voltage wiring outside the control console, cabinets, boxes and similarenclosures, shall be plenum rated where required by code. Cable not pulled throughconduits or placed in raceways, outlet boxes, junction boxes, or similar fittings withother building wiring.2.3 The supplier shall perform system testing to ensure it is operable to the manufacturer’sspecifications. The test report shall be submitted to the customer for approval and sign-off.3 Warranty3.1 The access control system shall be warranted for a period of one (1) year from the dateof acceptance.3.2 The supplier shall provide all services required to maintain the system in an operationalstate as specified by the manufacturer for a period of one (1) year after acceptance.3.3 The system supplier shall include a line item bill of materials included in the project andthe warranty associated with each.3.4 The system supplier shall maintain equipment stock for any high-usage equipment.。
Samtec 微型抗摧断系统说明书

I N T E R C O N N E C T S O L U T I O N S G U I D ERugged contact systems, flexible power interconnects and rugged signal integrity create the foundation of Samtec’s micro rugged solutions for high cycle, high speed, high power and harshenvironment applications. Samtec’s rugged products are offered in conjunction with full engineering support, online tools and a service attitude that is unmatched in the connector industry.HIGH SPEEDS TO 56 Gbps PAM4EDGE RATE ®CONTACT DESIGN INCREASES WEAR LIFE EXPERTISE IN SIGNAL INTEGRITY DESIGN & ANALYSIS1,000+MATING CYCLES TIGER EYE ™ HEAT-TREATED BeCu CONTACTS MULTIPLE POINTS OF CONTACTFOR HIGH-RELIABILITY3 TO 60 AMPS CONFIGURABILITY OF POWER & SIGNAL SPACE-SAVING FORM FACTORRUGGED CONTACT SYSTEMFLEX POWERRUGGED SIGNAL INTEGRITY2RUGGED CONTACT SYSTEMSTiger Eye ™ contact system for high-reliability in rugged applications1,000+ mating cycles 0.80 mm to 2.00 mm pitchBoard-to-board, discrete wire and IDC cable assembliesRUGGED SIGNAL INTEGRITY SYSTEMSEdge Rate ® contact system for rugged signal integrity performance Performance to 56 Gbps PAM4 0.50 mm, 0.635 mm and 0.80 mm pitch Edge card and ultra-micro connectorsFLEXIBLE POWER SYSTEMSUltra-micro power to 17 A and incredible design flexibilityIndividually shrouded contactsSmall form factor, high power systems to 60 A Board-to-board and cable assembliesSEALED I/O SYSTEMSIP67 and IP68 rated for dust and water Variety of circular shell sizes with power, power/signal pinoutsRectangular designs for space savings Rugged latchingModified & Custom Solutions ...........................................................................................................................................Rugged Features .............................................................................................................................................................Power Integrity & Extended Life Product ™ .........................................................................................................................Severe Environment Testing ............................................................................................................................................Solutionator ®...................................................................................................................................................................Technology Centers .. (181920212223)4-78-1112-1516-17HIGH-RELIABILITY • MULTI-FINGER BeCu CONTACT • HIGH MATING CYCLESComponents (ISD2/CC81)& tooling available: /toolingEMI shielded 2.00 mmTiger Eye ™ discrete wire assembly(SS2SD/ST2M)2.00 mm PITCH TIGER EYE ™• Tiger Eye ™ is Samtec's most ruggedcontact system rated to 1,000+ mating cycles • Wide range of stack heights• Right-angle mating headers available • Optional screw downs, weld tabs and locking clips• Discrete wire assemblies available in 24-30 AWG PVC or Teflon ® wire 4/tigereyeOptional strain relief and variety of wiring optionsTCSD/EHTT2M/S2MTMM/SMMT2M/S2MMetal latching and screw down optionsS2SD/T2Mper pin3.8 ARight-angle availableVariety of stack heightsSurface mount or through-holeTFM/SFMSurface mount or through-hole tailsSFSST/TFMScrew down and retention latching options6-12 mm stack heightsHigh-density four row designMOLC/FOLC1.27 mm PITCH TIGER EYE ™• Screw down, locking clip, friction latching and weld tab ruggedizing options • Shrouded, polarized and keyed• Discrete wire assemblies available in single or double row, 28 and 30 AWG PVC or Teflon ® wire • Cable components (ISDF/CC03) and tooling availableLocking for increased unmating force (SFML/TFML)IDC cable assemblies withrugged strain relief (FFSD/FFMD, FFTP/FMTP)5Dupont ™ Teflon ® is a registered trademark of the E.I. du Pont de Nemours and Company or its affiliates./tigereyeTIGER EYE ™ CONTACT SYSTEM• Multi-finger design with several points of contact for high-reliability• Smooth, flat mating area increases mating cycles and lowers contact resistance • Heat-treated BeCu for the best combination of mechanical and electrical properties • Surface mount, micro slot tail increases solder surface area for higher joint strengthper pin3.2 ATEM/SEMVertical and right-angle mating headers0.80 mm PITCH TIGER EYE ™• Micro pitch and slim body for space-savings • 6 mm, 7 mm and 10 mm stack heights • Locking clip, alignment pins and weld tab ruggedizing features• Discrete wire assembly available with 32 AWG Teflon ® wire• Extended Life Product ™ testing availableRugged latching system for increased withdrawal forceSESDT/ TEM-L16HIGH-RELIABILITY • MULTI-FINGER BeCu CONTACT • HIGH MATING CYCLES/tigereyeComponents (ISDE/CC396) and tooling available: /toolingLocking for increased unmating force(SEML)TEMS/ SEMSCompatible with UMPT/UMPS for power/signal flexibilityper pin2.9 ATEM/ SEM1.00 mm PITCH CABLE SYSTEM• Crimp-style dual leaf contact system for reliable wire-to-board connection• 28 and 30 AWG cable options in PVC or Teflon®7/tigereye Components (ISS1, ISD1/CC09; T1SS, T1SD, T1PS, T1PD/T1M137-X) and tooling available: /tooling Dual leaf contact system for a reliable connectionT1PSTS1SDS1SS/ T1MT1SDS1SSTPanel-to-BoardCable-to-CableCable-to-BoardCustom solutions available (twisted pair cable shown):**************• Rugged positive latching for increased retention • Socket or terminal, single or double row assemblies • Vertical and right-angle mating headersOPTIMIZED FOR SI PERFORMANCE • INCREASED CONTACT WIPE • HIGH CYCLES 0.635 mm PITCH EDGE RATE®•Extremely slim 2.5 mm body width•Up to 120 positions in a 2-row design•5 mm stack height with others in development•Compatible with UMPT/UMPS for flexiblepower/signal solutions8ERX5ERX6ERX8 Sockets shown actual size at 40 total positions /edgerate0.50 mm PITCH EDGE RATE®•1.00 mm contact wipe for a reliable connection • Rugged friction locks and weld tabs available •Up to 40% PCB savings vs. ERM8/ERF8•Compatible with UMPT/UMPS for flexiblepower/signal solutionsStack Height Flexibility(Actual Size in mm)79101112ERM5/ERF5Right-angleavailable12 mmstack height7 mmstack heightERM6/ERF6Signal/power combinationwith UMPT/UMPSJ lead for easeof processingERM8/ERF87 mmstack heightRight-angle & edge mount available0.80 mm PITCH EDGE RATE ®• 1.50 mm extended wipe• Rugged metal latching for increased retention force • 360º shielding option reduces EMI • Compatible with UMPT/UMPS for flexible power/signal solutions• Cost-effective metal solder lock in development for a more secure connection to the boardStack Height Flexibility (Actual Size in mm)* In development 78*91011121314151618179Mating Cable Assemblies (ERCD/ERDP Series)360º shieldingSignal/power combination with UMPT/UMPS10 mmstack height with latching14 mmstack height with latching/edgerateEDGE RATE ® CONTACT SYSTEM• Smooth milled mating surface reduces wear and increases durability• Lower insertion and withdrawal forces • Robust when “zippered” during unmating• Minimized parallel surface area reduces broadside coupling and crosstalk • Designed, simulated and optimized for 50 Ω and 100 Ω systemsUP TO 56 Gbps PAM4 • CHOICE OF PITCH • EDGE RATE ® CONTACTS/edgecard0.80 mm & 1.00 mm PITCH SYSTEMS• High-speed Edge Rate ® contact system • Vertical, right-angle and edge mount • Power/signal combo to 60 A per power bank • Pass-through applicationHIGH-DENSITY EDGE CARD• Justification beam enables use of standard PCB tolerance • 0.50 mm ultra-fine pitch with up to 300 total I/Os • PCIe ® Gen 4 compatibleMICRO EDGE CARDS• 0.635 mm, 0.80 mm, 1.00 mm, 1.27 mm and 2.00 mm pitch • Optional rugged weld tabs, board locks and solder locks • Solutions for 1.60 mm (.062") and 2.36 mm (.093") thick cardsMisalignment mitigation(HSEC1-DV)56 Gbps with differentialpair (HSEC8-DP)PCI-SIG ® , PCI Express ® and the PCIe ® design marks are registered trademarks and/or service marks of PCI-SIG.HSEC8HSEC1-DVHSEC8-PV MEC5Beam ensures card and body are flushMEC1MEC6MECFHIGH-DENSITY • HIGH-RETENTION CONTACTS • SLIM ROW-TO-ROW DESIGNSLSSLSEMHERMAPHRODITIC RAZOR BEAM ™ INTERFACES• High-retention, high-speed Razor Beam ™ contacts • 0.50 mm, 0.635 mm and 0.80 mm pitch• EMI shielding available to limit signal degradation and optimize performanceRight-angle available formicro backplane applicationsFLOATING CONNECTORS• Provides 0.50 mm contact float in the X and Y axes to compensate for misalignment • 5 mm and 7 mm stack heights • Micro 0.50 mm pitchONE-PIECE INTERFACES• Robust design and mechanical hold-downs for high-shock and vibration applications • Optional rugged weld tabs and locking clips • 1.00 mm, 1.27 mm and 2.54 mm pitch designs5 - 12 mmstack height flexibilityLSHMFT5/FS5SEIFSISIBSIR1Profiles from1.65 mm to 10 mm11/micro17.1 A PER BLADE • MICRO 2.00 mm PITCH • DESIGN FLEXIBILITY MICRO 2.00 mm PITCH• Design flexibility as a power-only system or atwo-piece system for power/signal applications•Use with Samtec’s high-speed connector systemsfor a unique power/signal system (see chart)12SIGNAL CONNECTORMATED HEIGHT5 mm7 mm8 mm10 mmADM6/ADF6XBTE/BSE, BTH/BSH, BTS/BSS X XERM5/ERF5X XERM6/ERF6XERM8/ERF8X XLPAM/LPAF XQMS/QFS XQRM8/QRF8X XQTE/QSE, QTH/QSH,QTS/QSS X XSEAM/SEAF, SEAM8/SEAF8X XST4/SS4, ST5/SS5XTEM/SEM X XUMPT/UMPS/powerCREEPAGE CLEARANCEUMPT/UMPS 1.65 mm 2.20 mm•Tin or 10 µ" Gold plated power blades; 30 µ" Gold platingavailable to meet specific regulations•Selectively loading contacts achieves customer specificcreepage and clearance requirements; contact **************Choice of2, 3, 4 and 5position countsOptionalweld tabs5-10 mm stackheights available17.1 A/bladeUMPT/UMPS compared to othersmall form factor power solutions23 A/bladeper bladeTerminals shown actual size at 4 positions28.8 A/blade58.7 A/blade13P H A S E 15 Position,5 mm Stack HeightVertical UMPT & UMPS SeriesPOSITIONSSTACK HEIGHTS2, 3, 4, 55, 7, 8,10P H A S E 26 Position,9 mm Stack HeightVertical UMPT & UMPS SeriesPOSITIONSSTACK HEIGHTS6, 7, 8, 9, 106, 9, 11, 12, 14,16P H A S E 310 Position Right-AngleRight-Angle UMPT SeriesPOSITIONSOPTIONS2, 3, 4, 5, 6, 7, 8, 9, 10Latch for mating with cable assemblyP H A S E 44 Position Cable Assembly andUMPT Right-Angle with Staged BladesCable Assembly with LatchPOSITIONSMATES2, 3, 4, 5, 6, 7, 8, 9, 10UMPT Series vertical and right-angle with latch/powerLength, width and height shown actual sizeSamtec now offers power simulation that can calculate temperature increase in the connector area; contact *************************** for more details.SMALL FORM FACTORS • 10–60 A PER PIN/BLADE • INDIVIDUALLY SHROUDED CONTACTSMMSD/ IPL1MINI MATE ® & POWER MATE ®• Individually shrouded contacts for electrical and mechanical protection• .100" (2.54 mm) and .165" (4.19 mm) pitch • Discrete wire assemblies with 16-30 AWG PVC or Teflon ® cable• Selectively loading contacts achieves customer specific creepage and clearance requirements; contact **************14Metal or plasticrugged latching system/powerEXTREME POWER• AC or DC power, AC-DC combos and split power options (ET60T/ET60S)• High-density, double stacked power blades (LPHT/LPHS)• Selectively loading contacts achieves customer specific creepage and clearance requirements; contact **************3 or 5 signal rows in the same form factorLow 7.5 mm profile designCREEPAGECLEARANCE IPT1/IPS1MMSS(T)/MMSD(T) 2.55 mm 4.27 mm3.05 mm1.91 mm IPBT/IPBS PMSS(T)/PMSD(T)per pin10.3 ACREEPAGECLEARANCE LPHT/LPHS ET60T/ET60S5.63 mm 3.02 mm2.69 mm 1.87 mmET60T/ET60SLPHT/LPHSPMSDT/ IPBTIPT1/IPS1IPBT/IPBSRugged guide postsComponents and tooling availablePOWERSTRIP ™ SYSTEM• 23.5 A/blade to 58.7 A/blade (1 blade powered) • 5.00 mm and 6.35 mm pitch• Discrete wire assemblies with 10-16 AWG cable • Selectively loading contacts achieves customer specific creepage and clearance requirements; contact **************15MPT/MPSUPT/UPSMPTC/ MPSCPESS/PETMPSS/ MPTVertical and right-anglePower only or power/signal combinationsRugged latching system/power“Hinging” for 90º mating radius, ideal for blind mating (FMPT/FMPS)Discrete wire components (IMS5,IMSC5/CC46,CC81; IPS6/CC10) and tooling available: /toolingHermaphroditic power system with rugged screw downs (MPPT, UPPT)CREEPAGE CLEARANCE PET/PES/PETC/ PESC/PESS 3.66 mm 2.95 mm 5.80 mm2.71 mm 1.51 mm3.31 mm MPT/MPS/MPTC/ MPSC/MPSS/MPPT UPT/UPS/UPPTDual blade contactsCCP/CCRFLEXIBLE SEALED CIRCULAR SYSTEMS• Metal or plastic, 12 mm, 16 mm and 22 mm shells • Flexible pin configuration, gender and panel interface termination• Bayonet-style latching systems meet IP68 requirements • Cost-effective crimp version available• Mini push-pull latching system meets IP67 requirements for dust and waterproof sealing16Crimp 12 mm shellIP67 & IP68 • BAYONET/PUSH-PULL CIRCULARS • SPACE-SAVING RECTANGULARSKitted components for efficient field assembly/sealedMCP/MCRACP/ACRACP/ACRMini push-pull system16 mm size metal shell22 mm size plastic shell17SCPU25-45% panel area savings/sealedSEALED RECTANGULARS• Space saving design • Meets IP68 requirements • USB and Ethernet signal systems • Rugged dust caps available• 1 or 2-port vertical and right-angle panel mount socketsTHREADED CIRCULARS• Meets IP68 requirements for dust and waterproof sealing • Rugged overmold design• USB, Mini USB and Ethernet signal systems • 10 and 17 shell sizes• Rugged dust caps and panel-to-board termination availableRCERCUAudibleclick positive latching for quick connect/disconnectVertical or right-angleRPCURPBURPBEUSB type A and B10 or 17 shell sizeEthernet meets CAT3, CAT5 and CAT5eSCRESSCPESCRUSWILLINGNESS, SUPPORT & EXPERTISE18ExpressModificationsEngineeredCustoms23%5%Customs and Modifications make up about 28% of Samtec’s total sales92% do not require engineering or tooling chargesA substantial percentage of eachMicro Rugged product segment is customTiger Eye ™Edge Rate ®Edge Card PowerSealed I/O19%9%44%30%8%INDUSTRY LEADING CUSTOMER SERVICE FLEXIBLE IN-HOUSE MANUFACTURING SIGNAL INTEGRITYEXPERTISEEngineered CustomMulti-power staging, power/signal combo, header/socket combo, custom bodyExpress ModificationStandard PowerStrip ™ cable with non-standard end 2 optionFLEXIBLE SOLUTIONS• Full engineering, design and prototype support • Design, simulation and processing assistance • Quotes and samples turned around in 24 hours • Flexible, quick-turn manufacturing • Dedicated Application Specific Product engineers and technicians• Modified or custom options for board level connectors and cable assemblies including: contacts, bodies, stamping, plating, wiring, molding, ruggedizing features and much moreContact the Application Specific Products Group at ************** for express modifications or engineered customs.19OPTIONS FOR HIGH-RELIABILITY, HIGH-RETENTION AND HIGH-CYCLE LIFERUGGEDIZING OPTIONSWELD TABSSignificantly increase sheer resistance of connectorto PCBSHIELDING360° shielding reduces EMIGUIDE POSTSEasy and secure matingBOARD STANDOFFSPrecision machined standoffs for 5 mm to 25 mm board spacingSCREW DOWNS Secure mechanical attachment to the boardBOARD LOCKSBoards are mechanicallylocked togetherRETENTION PINSIncrease unmating forceby up to 50%FRICTION LOCKSMetal or plastic friction locks increase retention/withdrawal forcePOSITIVE LATCHINGManually activated latches increase unmating forceby up to 200%JACK SCREWS Ideal for high normal force, zippering and other ruggedapplicationsEDGE RATE ®Designed for Signal Integrity Superior Impedance Control Reduced Broadside CouplingTIGER BEAM ™Best CostReliable Performance Post & Beam ContactBLADE & BEAMMating/Alignment “Friendly”Cost-effectiveTIGER CLAW ™Dual Wipe Contact Pass-through ApplicationsUltra-low ProfileTIGER EYE ™High-reliability High Mating Cycles Multi-finger ContactCONTACT SYSTEMS20POWER INTEGRITY SERVICES• • • • • /powerintegrity EXTENDED LIFE PRODUCT ™• • • • /ELP**************POWER INTEGRITYCERTIFIEDCREEPAGECLEARANCEPITCHTYPECONTACTSERIES*0.50 mm Q Series ® Strip Blade & Beam QSH/QTH Basic Strip Blade & Beam BSH/BTH 0.635 mmQ Series ® Strip Blade & Beam QSS/QTS Basic Strip Blade & Beam BSS/BTS 0.80 mmEdge Rate ® Strip Edge Rate ®ERF8/ERM8Edge CardEdge Rate ®HSEC8Q Rate ®StripEdge Rate®QRM8/QRF8Q Series ® Strip Blade & Beam QSE/QTE Basic Strip Blade & Beam BSE/BTE StripTiger Eye ™SEM/TEM 1.00 mm StripTiger Claw ™CLM/FTMH 1.27 mmSEARAY ™ArrayEdge Rate®SEAF/SEAM Strip Tiger Eye ™SFM/TFM Strip Tiger Claw ™CLP/FTSH Strip Tiger Beam™FLE/FTSH 2.00 mm Strip Tiger Eye ™SMM/TMM Strip Tiger Claw ™CLT/TMMH 2.54 mmStrip Tiger Claw™SSM/TSM StripTiger Claw ™BCS/TSW* Tested socket/terminal combination shown. Other mating headers also available. Contact Samtec if header design you need is not shown.10 YEAR MFGEXTENDED LIFEPRODUCTHIGH MATINGCYCLES21Severe Environment Testing is a new Samtec initiative to test our products beyond typical industry standards and specifications, many set forth by common requirements for rugged industries. Several of our products will undergo additional testing to ensure they are more than suitable for industrial, military, automotive and other extreme applications.PRODUCTS TO BE TESTED:• Rugged Tiger Eye ™ connectors• Hermaphroditic Razor Beam ™ connectors• SEARAY ™ high-density arrays• Edge Rate ® rugged signal integrity connectors• AcceleRate ® HD ultra-micro connectors• Ultra Micro Power systems• High-speed coax and twinax cable assembliesPlease contact ************** for more information and test results when available.TESTING WILL INCLUDE:• Higher mating cycle testing• Intense shock and vibration• Altitude testing• ESD testing• Temperature cycling• And morePRND NETWORK vs. MIL-PRF-83401 PERFORMANCE TEST OR CONDITION MIL-PRF-83401VISHAY FOIL RESISTORS C Typical Resistance Temp Characteristic ppm/ºC ± 50± 2Tracking to Reference Element (-55 to +125 ºC)ppm/ºC ± 5± 2Max Ambient Temp at Rated Wattage ± 70 ºC Max Ambient Temp at Zero Power ± 125 ºC Thermal Shock and Power Conditioning ± 0.25 % ± 0.03 %± 0.015 % ± 0.015 %Low Temperature Operation ∆R ∆Ratio ± 0.10 % ± 0.02 %± 0.01 % ± 0.01 %Short Time Overload ∆R ∆Ratio ± 0.10 % ± 0.02 %± 0.01 % ± 0.01 %Terminal Strength ∆R ∆Ratio ± 0.10 % ± 0.03 %± 0.01 % ± 0.01 %Resistance to Soldering Heat ∆R ∆Ratio ± 0.10 % ± 0.02 %± 0.01 % ± 0.01 %Moisture Resistance ∆R ∆Ratio ± 0.20 % ± 0.02 %± 0.01 % ± 0.01 %Shock (Specified Pulse)∆R ∆Ratio ± 0.25 % ± 0.03 %± 0.01 % ± 0.01 %Vibration, High Frequency ∆R ∆Ratio ± 0.25 % ± 0.03 %± 0.01 % ± 0.01 %Load Life (Per EEE-INST-002) (+70 ºC, Full Power, 2000 hours)∆R ∆Ratio ± 0.10 % ± 0.03 %± 0.05 % ± 0.02 %+25 ºC Power Rating (1000 hours)∆R ∆Ratio ± 0.10 % ± 0.03 %± 0.01 % ± 0.01 %High Temperature Exposure (+125 ºC, 100 hours)∆R ∆Ratio ± 0.10 % ± 0.03 %± 0.01 % ± 0.01 %Low Temperature Storage ∆R ∆Ratio ± 0.10 % ± 0.02 %± 0.01 % ± 0.01 %Insulation Resistance 10,000 MΩResistance Tolerance and, when applicable, Resistance Ratio Accuracy ± 0.1 % (B)± 0.5 % (D) ± 1.0 % (F)± 0.1 % (B)± 0.5 % (D)22•Wide variety of search parameters and filters: creepage and clearance (power), pitch, stack height, etc. •Easily sort results to find the right mated set•Live chat with engineers for custom options•Immediately download models and open Specs KitQUICKLY BUILD MATED SETS ONLINETo build your mated set, visit /solutionatorSAMTEC TECHNOLOGY CENTERS ENABLE COMPLETE SYSTEM OPTIMIZATION FROM SILICON-TO-SILICON™HIGH–SPEEDCABLE MICROELECTRONICSADVANCEDINTERCONNECTSOPTICSSYSTEM SIGNALINTEGRITYPRECISION RFSamtec's Technology Centers offer high-level design and development of advanced interconnect systems and technologies, along with industry-leading signal integrity expertise which allows us to provide effective strategies and technical support for optimizing the entire serial channel of high-performance systems. Because Samtec's Technology Centers are not limited by the boundaries of traditional business units,we are able to work in a fully integrated capacity that enables true collaboration and innovation to support the demands of today, and the challenges of tomorrow.In-house R&D manufacturingof precision extruded cableand assembliesAdvanced IC packaging design, support and manufacturing capabilities R&D, design, developmentand support of micro opticalengines and assembliesRF interconnect design anddevelopment expertise, withtesting to 65 GHzHigh precision stamping,plating, molding andautomated assemblyFull channel signal and powerintegrity analysis, testing andvalidation services /tech-centers23UNITED STATES • NORTHERN CALIFORNIA • SOUTHERN CALIFORNIA • SOUTH AMERICA • UNITED KINGDOM GERMANY • FRANCE • ITALY • NORDIC/BALTIC • BENELUX • ISRAEL • INDIA • AUSTRALIA / NEW ZEALAND SINGAPORE • JAPAN • CHINA • TAIWAN • HONG KONG • KOREANOVEMBER 2018。
Micrel KSZ8851-16MLL 48-pin单端口以太网控制器与非PCI接口评估板用户指南

KSZ8851-16MLL48-pin Single-Port Ethernet ControllerWith 8-bit or 16-bit Non-PCI InterfaceEvaluation Board User’s GuideRevision 1.1August 2010© Micrel, Inc. 2007All rights reservedMicrel is a registered trademark of Micrel and its subsidiaries in theUnited States and certain other countries. All other trademarks are theproperty of their respective owners.The information furnished by Micrel in this datasheet is believed to be accurate and reliable. However, no responsibility is assumed by Micrel for its use. Micrel reserves the right to change circuitry and specifications at any time without notification to the customer. Micrel Products are not designed or authorized for use as components in life support appliances, devices or systems where malfunction of a product can reasonably be expected to result in personal injury. Life support devices or systems are devices or systems that (a) are intended for surgical implant into the body or (b) support or sustain life, and whose failure to perform can be reasonably expected to result in a significant injury to the user.Micrel, Inc. August 6, 2010A Purchaser's use or sale of Micrel Products for use in life support appliances, devices or systems is at Purchaser's own risk and Purchaser agrees to fully indemnify Micrel for any damages resulting from such use or sale.Revision HistoryRevisionDateSummary of Changes1.0 2/20/2008 Initial Release1.1 8/6/2010Add JP8 for connection between VDD_IO and 1.8V (if VDD_IO is 1.8V). Changed the LED pulled up to 3.3V.Table of Contents1.0Introduction (5)2.0Board Features (5)3.0Evaluation Kit Contents (5)4.0Hardware Description (6)4.1Host Interface (7)4.2Jumper Setting & Definition (8)4.3Power Supply and Test Point Definition (9)4.4RJ-45 Connector and Transformer (9)4.5EEPROM and LED Indicators (9)4.6Board Reset (10)5.0Bill of Materials (11)Micrel, Inc. August 6, 2010List of FiguresFigure 1. KSZ8851-16MLL Evaluation Board (6)Figure 2. KSZ8851-16MLL-Eval Host Interface Connection with Spirent SmartBits (7)List of TablesTable 1. Header JP1 – Host Interface Connection for SD[15:0] (7)Table 2. Header JP1 – Host Interface Connection for Control and Power (8)Table 3. KSZ8851-16MLL-Eval Jumper Definition (8)Table 4. KSZ8851-16MLL-Eval Test Point Definition (9)Table 5. KSZ8851-16MLL EEPROM Format (9)Table 6. KSZ8851-16MLL-Eval Port Status LED Definition (10)Table 7. KSZ8851-16MLL-Eval LED Definition (10)Micrel, Inc. August 6, 20101.0 IntroductionThe KSZ8851-16MLL-Eval Evaluation Board is intended to provide a convenient and fast way to evaluate or demonstrate the functionality and performance of this new Single-Port Ethernet Controller KSZ8851-16MLL device from Micrel.The KSZ8851-16MLL comes with a 48-pin, lead-free LQFP (7mm x 7mm) package and provides an ideal solution for applications requiring high-performance from single-port Ethernet Controller with 8-bit or 16-bit generic processor interface. The KSZ8851-16MLL offers the most cost-effective solution for adding high-throughput Ethernet connectivity to traditional embedded systems.This evaluation board is designed as a stand alone without microcontroller or M16C on board. By default the KSZ8851-16MLL-Eval board comes with an operation of 16-bit bus mode, Little Endian mode and disabled EEPROM for KSZ8851-16MLL device. Customer may wire the board for his desired interface. The purpose is to provide a simple tool that can be used to evaluate the KSZ8851-16MLL device by connecting via headers to customer provided Microcontroller or Non-PCI hardware platform.Micrel provides a basic software driver based on the 8 or 16-bit bus solution and different operating system platforms to evaluate the KSZ8851-16MLL functionality and performance. The software includes a configuration utility to allow quick and easy device setup, initialization and transmit/receive packet. All KSZ8851-16MLL configuration pins and host interface signals are accessible either by jumpers, test points or headers.2.0 Board Features•One KSZ8851-16MLL 48-pin Single-Port Ethernet Controller with shared data bus for host interface•Single +5V/GND power input from headers•RJ-45 Jack for Fast Ethernet cable interface•HP Auto-MDIX for automatic detection and correction for straight-through and crossover cables•Two on board LDO voltage regulators, one for VDD_IO and the other for VDD_A3.3•One AT93C46 for external EEPROM interface•Two LED indicators for port status and activity•One LED indicator for 3.3V output ready•One LED indicator for Power Management Event (PME) output status•Jumpers to configure strapping pins and VDD_IO voltage option•Headers to wire the host interface from external hardware platform•Manual reset button for quick reboot after re-configuration of strapping pins3.0 Evaluation Kit ContentsThe KSZ8851-16MLL Evaluation Kit includes the following hardware:•KSZ8851-16MLL Evaluation BoardThe KSZ8851-16MLL Data Sheet and Hardware Design Package with the following collaterals that can be downloaded from Micrel’s website at •KSZ8851-16MLL Eval Board Schematic (PDF and OrCAD DSN file)•KSZ8851-16MLL Eval Board Gerber File (PDF version included)•KSZ8851-16MLL Eval Board User’s Guide (this document and included BOM)•KSZ8851-16MLL IBIS ModelMicrel, Inc. August 6, 20104.0 Hardware DescriptionThe KSZ8851-16MLL-Eval (shown in Figure 1) comes in a compact form factor and plugs directly into industry standard test equipment such as Spirent SmartBits, the other side of board is wired to external host interface through headers. Configuration of the KSZ8851-16MLL is accomplished through on-board jumper selections and/or by register access via the host shared data/control bus Interface.Figure 1. KSZ8851-16MLL Evaluation Board (Rev 1.1)Other features include a RJ-45 Jack for Fast Ethernet cable connection, transformer (Pulse H1102) to block DC level and provide a true AC coupling, EEPROM (Atmel AT93C46) to load MAC address when it is enabled, jumper to select LDO output for VDD_IO voltage, programmable LED indicators for reporting port link status and activity, and a manual reset button for quick reboot after re-configuration of strapping pins.The KSZ8851-16MLL-Eval receives +5V DC input power supply from its Headers JP1.Micrel, Inc. August 6, 2010Micrel, Inc. August 6, 20104.1 Host InterfaceThe KSZ8851-16MLL-Eval board receives +5V power from the header JP1 (pin 1/3). Figure 2 shows the Host interface connection with Spirent SmartBits for system set-up and performance test.Figure 2. KSZ8851-16MLL-Eval Host Interface Connection with Spirent SmartBitsThe KSZ8851-16MLL-Eval has a 40-pin header (JP1) for Host interface to external any Non-PCI hardware platform. Table 1 lists Shared Data SD[15:0] pin outs for the Host interface on header JP1. Table 2 lists the rest of control signals and power/ground pin outs for the Host interface on header JP1.16-Bit Bus Mode (pin 1 pull-up) 8-Bit Bus Mode (pin 1 pull down) Pin # (JP1) Shared Data Bus Signal CMD = 0 (low) CMD = 1 (high) CMD = 0 (low) CMD = 1 (high) 20 SD0 D0 x (don’t care) D0 A0 19SD1D1 x (don’t care) D1 A1 18 SD2 D2 A2 D2 A2 17 SD3 D3 A3 D3 A3 16 SD4 D4 A4 D4 A4 15 SD5 D5 A5 D5 A5 14 SD6 D6 A6 D6 A6 13 SD7 D7 A7 D7 A7 12 SD8 D8 x (don’t care) GND GND 11 SD9 D9 x (don’t care) GND GND 10 SD10 D10 x (don’t care) GND GND 9SD11D11 x (don’t care) GND GND 8 SD12 D12 BE0 GND GND 7 SD13 D13 BE1 GND GND 6 SD14 D14 BE2 GND GND 5 SD15D15BE3GNDGNDTable 1. Header JP1 – Host Interface Connection for SD[15:0]Pin # (JP1) Power & ControlSignal NamesDescription1, 3 5.0V_IN +5V power supply inputs for this board 2, 4, 21, 22, 25,26, 29, 33, 34, 37, 38, 39, 40 GND Groundinputs/pins23 CPU_CSN Chip Select input from host CPU24 CPU_RSTN Reset input from host CPU27 CPU_PME Power Management Event output to host CPU28 CPU_CMD Command type input from host CPU31 CPU_INTRN Interrupt output to host CPU35 CPU_WRN Write input from host CPU36 CPU_RDN Read input from host CPU30, 32 Spares For customer to useTable 2. Header JP1 – Host Interface Connection for Control and Power4.2 Jumper Setting & DefinitionThe KSZ8851-16MLL-Eval does not require any jumper for normal operation except the VDD_IO option. During power-up, the KSZ8851-16MLL is configured using the chip’s internal pull-up and pull-down resistors with its default strapping pin values which will set this device in operation of 16-bit bus mode, little endian and without EEPROM. Jumpers are provided to override the default settings, allowing for quick configuration and re-configuration of the board. To override the default settings, simply select and close the desired jumper setting(s) and toggle the on-board manual reset button (S1) for the new setting(s) to take effect.The KSZ8851-16MLL-Eval jumper settings are defined in Table 3 below.Jumper Definition Setting DescriptionJP2 EED_IO OFF (Default) OFF: EEPROM is not presentON: EEPROM is presentJP3 3.3V ON (Default) ON: to select 3.3V for VDD_IO (JP5 and JP6 must be OFF)OFF: De-select 3.3VJP4 EESK OFF (Default) OFF: Little EndianON: Big EndianJP5 2.5V OFF (Default) ON: to select 2.5V for VDD_IO (JP3 and JP6 must be OFF)OFF: De-select 2.5VJP6 1.8V OFF (Default) ON: to select 1.8V for VDD_IO (JP3 and JP5 must be OFF)OFF: De-select 1.8VJP7 P1LED1 OFF (Default) OFF: 16-Bit bus modeON: 8-Bit bus modeJP8 VDD_IO OFF (Default) OFF: VDD_IO = 2.5V or 3.3VON: VDD_IO = 1.8VTable 3. KSZ8851-16MLL-Eval Jumper DefinitionMicrel, Inc. August 6, 2010Power Supply and Test Point DefinitionThe KSZ8851-16MLL-Eval is supplied from external +5.0V DC power through a jumper (pin 1 and 3 at JP1), this +5.0V DC input is converted to both +3.3V with a Micrel LDO voltage regulator (U3, MIC5209BM) for VDD_A3.3 analog power and VDD (option for 3.3V, 2.5V or 1.8V) with a Micrel LDO voltage regulator (U5, MIC5209BM) for VDD_IO digital power. The KSZ8851-16MLL contains an internal +1.8V LDO, to provide its core, analog and PLL voltages.The KSZ8851-16MLL-Eval has four test points. They are defined in the following Table 4.Test Point DefinitionTP1 Power supply measurement for VDD_IOTP2 Power supply measurement for VDD_A3.3TP3 1.8V digital core voltage output measurement fromKSZ8851-16MLL internal LDOTP4 External power supply 5.0V_IN measurementTable 4. KSZ8851-16MLL-Eval Test Point Definition4.3 RJ-45 Connector and TransformerThe RJ-45 Jack (J1) connects to standard CAT-5 Ethernet cable to interface with 10Base-T/100Base-TX Ethernet devices. The LAN interface on the KSZ8851-16MLL is connected to a transformer (T1) with 50 ohm termination resistors for both TX+/- and RX+/- differential pairs. The line side of the transformer is connected to the RJ-45 connectors (J1).J1 also supports Auto-MDIX and Auto-Negotiation / Forced Modes.4.4 EEPROM and LED IndicatorsIt is optional in the KSZ8851-16MLL to use an external EEPROM. The EED_IO (JP2) must be pulled high (ON) to use external EEPROM.An external serial EEPROM with a standard microwire bus interface is used for non-volatile storage of information such as the host MAC address. The KSZ8851-16MLL can detect if the EEPROM is either a 1KB (93C46) or 4KB (93C66) EEPROM device. The EEPROM must be organized as 16-bit mode.The KSZ8851-16MLL EEPROM format is given in Table 5.WORD 15 8 7 00H Reserved1H Host MAC Address Byte 2 Host MAC Address Byte 12H Host MAC Address Byte 4 Host MAC Address Byte 33H Host MAC Address Byte 6 Host MAC Address Byte 54H – 6H Reserved7H-3FH Not used for KSZ8851-16MLL (available for user to use)Table 5. KSZ8851-16MLL EEPROM FormatMicrel, Inc. August 6, 2010A dual LED indicator (LED1) is located adjacent to the RJ-45 Connector (J1). The top LED is connected to P1LED1 (pin 1) and bottom LED is connected to P1LED0 (pin 2) of the KSZ8851-16MLL.The two LEDs are programmable to LED mode ‘0’ or ‘1’ via register 0xC6 bits [9], and are defined in the following Table 6.LED Mode0 (Default) 1LED1 (Top) 100BT ACTLED1 (Bottom) LINK/ACT LINKTable 6. KSZ8851-16MLL-Eval Port Status LED DefinitionTable 7 shows the rest of LEDs definition.LED Color DescriptionLED2 Green Power Management Event (PME) StatusLED3 Red 3.3V Power available indicatorTable 7. KSZ8851-16MLL-Eval LED Definition4.5 Board ResetThe KSZ8851-16MLL-Eval generates a reset signal from the reset circuitry during power up. It also provides a push button S1 reset circuit to reset the KSZ8851-16MLL device. During power up, the board is automatically reset. User can also press reset button S1 on the board for a manual reset.Micrel, Inc. August 6, 2010KSZ8851-16MLL-Eval Evaluation Board User’s Guide Rev. 1.1 Micrel, Inc.August 6, 201011/11 5.0 Bill of MaterialsKSZ8851-16MLL Eval Board (Revision 1.1)。
斯派克ICP-AES 操作流程.

宁波博禄德电子有限公司ICP仪器的操作流程文件编号:文件编制单位:品管部拟定日期:2006年3月4日编制人:页次:1页说明:对于在分析软件上的每一步操作都得保存。
具体操作方法一. 装配ICP 仪器:1.同水循环仪器的连接:ICP 主机上的input 接口对应水循环器上的out 接口,另一ICP 的out接口对应着水循环器上的input 接口,且水循环器上的 out 接口上要安装好水过滤器。
2.同氩气的连接:氩气的管子接到ICP 主机上的Argon 接口上,且氩气的气压通过减压装置来调节,一般控制在0.8 ba 。
3.同抽风机的连接:抽风机的两抽风管,前管吸收矩管放出的热量,后管吸收发生器放出的热量。
4.同UPS 的连接 5.废水箱的安装6.雾化器,雾化室,矩管,泵软管的安装 7.ICP 同PC 的接口,且Hardlock USB 软件保护装置要插到PC 的USB接口上。
8.ICP 地线的连接二. 建方法流程:1.方法信息的设置:在measurement info界面⑴.在界面下方的method data control 面板中,选择New ,新建一个方法,并输入方法的名称和描述内容。
⑵.设置参数:Nebulizer Type (雾化器的类型):有Crossflow (交叉雾化器)和Modi-lichte (理查得雾化器),本仪器使用Crossflow.Application(应用类型):针对不同的情况,有不同的选择,一般选择NormalDefault Unit :对单位的设置No.of Measurements :测量次数一般为3次 Data Transport :数据储存要求,“None ”不储存,“Region ofinterest ”储存指定的分析谱线,“Complete Spectrum ”储存所 有的数据,一般选择Complete SpectrumMin Corr Coefficament :校正线性参数,一般为0。
AVOCENT ACS 6000 ADVANCED CONSOLE SERVER A 下一代控制台管

1y y Secure in-band and out-of-bandnetwork remote management y y Streamline installation andconfiguration with Zero Touch Provisioning y y Access to remote andunreachable locations using automatic network failover to cellular (and failback) capability y y Eliminates adaptors forCyclades™ and Cisco® pin-out conversions y y Compliance with datacenter access and securitypolicies – customizable, multiple access levels y y Integrated powermanagement – support for MPH2™ Rack PDUs and third-party power support y y Compatible with next-generationnetwork standards – IPv6y y Centralized managementusing Avocent DSView management software y y Strong dial-up and securedial-back using optionalbuilt-in modem y y Automatic event tracking andnotification of fault conditions y y Regulatory compliance andeasy trouble shooting – online and off-line data logging with time stamps y y FIPS 140-2 compliance: Basedon the FIPS 140-2 validated cryptographic module(s) (Certificate #1747)High-Performance Design and Advanced FeaturesThe Avocent ACS 6000 advanced console server series offers upgraded and advanced features that deliver scalable and high performance solutions for IT administrators. The console server features a high-speed processor platform with dual gigabit-Ethernet ports for redundancy and optional built-in modem. In addition, they feature an internal temperature sensor for device-level monitoring and configurable pin-outs for serial ports. The Avocent ACS 6000 advanced console server also offers robust software features to meet the requirements of the most demanding data center management applications. Features include automated discovery tools to ease identification of servers, routers, switches and power devices connected to any serial port, saving time at initialconfiguration and installation. To comply with existing data center network access policy, the Avocent ACS 6000 advanced console server provides customizable, multiple access levels for secure management.The console servers provide a complete solution for secure, remote control withadvanced console server features such as enhanced security, data logging and event monitoring. In addition, the Avocent ACS 6000 advanced console server supports next-generation network standards such as Internet Protocol version 6 (IPv6). Available in 4-, 8-, 16-, 32- and 48-port models that fit in 1U of rack space with single and dual, AC and DC power options. With or without modem, the ACS 6000 console server helpsmaximize IT asset productivity while providing scalability and reducing operational costs.The Avocent® ACS 6000 advanced console server series integrates cutting edgetechnologies, adaptive services and secure enterprise communications in order to offer IT professionals and network operations center (NOC) personnel the ability to perform secure, remote data center management and out-of-band management of IT assets from anywhere in the world. Using a hardened Linux® operating system and DSView™ management software, the Avocent ACS 6000 provides optimal performance, security,reliability, and a complete out-of-band management solution.Avocent® ACS 6048 Advanced Console ServerApplicationsy y Secure console and power managementy y Server and network management y y Secure access to test and development lab environments y y Telco central office and remote facilities2AV-12315 (R11/16) | Vertiv Headquarters, 1050 Dearborn Drive, Columbus, OH, 43085, USA© 2016 Vertiv Co. All rights reserved. Vertiv and the Vertiv logo are trademarks or registered trademarks of Vertiv Co. All other names and logos referred to are trade names, trademarks or registered trademarks of their respective owners. While every precaution has been taken to ensure accuracy and completeness herein, Vertiv Co. assumes no responsibility, and disclaims all liability, for damages resulting from use of this information or for any errors or omissions. Specifications are subject to change without notice.Hardware SpecificationsCPU PPC440EPx @ 533 MHz (PowerPC with Security Acceleration Engine)Memory128 MB NAND flash (embedded ICs on motherboard); 256 MB DDR-2 memory (embedded ICs on motherboard)Interfaces2 Gigabit (10/100/1000BT) Ethernet interfaces on RJ45; 1 RS-232 serialconsole port on RJ45; 1 AUX RS232 port on RJ45 OR internal modem V.92 port on RJ45 (RJ11 compatible); RS232 ports on RJ45; 1 USB 2.0 Host on Type A connector PowerInternal 100–240 VAC, 50/60 Hz Optional –48 VDC power supply; optional dual entry, redundant AC and DC power supplies Power UsageNominal voltage 120VAC: Typical 0.17A, 20W; Maximum 0.25A, 30WNominal voltage 230VAC: Typical 0.1A, 23W; Maximum 0.15A, 35W Nominal voltage -48VDC (20% tolerance); Typical 0.5A Operating Temp.32° to 122°F (0° to 50°C)Storage Temp.–4° to 158°F (–20° to 70°C)Humidity 20% to 80% noncondensing Non-Operating Humidity 5% to 80% relative humidityDimen-sions (W x D x H) 17.250 x 9.5 D x 1.75 in. (43.82 x 24.13 x 4.45 cm)Weight 6.6 lbsCertifi-cationsEmissions and Immunity: FCC Class B; CE Class A (EU); ICES-003 (Canada); VCCI (Japan); C-Tick (Australia); Customs Union (CU)Safety: UL (USA); cUL (Canada); EN-60950 (EU); CB; Customs Union (CU)In addition, the following certifications forspecific models: KCC (Korea)** Only specific models are certified to theabove certificationsFeaturesOperating System y y Embedded LinuxAccessibilityy y Zero Touch Provisioning (ZTP)y y In-band (Ethernet) and out-of-band (dial-upmodem) supporty y Built-in modem connectivityy y Allows for alternative access interfaces, such asmodem (v.92) or 4G through USB device Availabilityy y Automatic Ethernet failover using second gigabitEthernet port as the secondary portACS6008SAC-G2ACS 6000 8-port unit single AC power supplyACS6008DAC-G2ACS 6000 8-port unit dual AC power supplyACS6008MDAC-G2ACS 6000 8-port unit dual AC power supply with built-in modem ACS6016SAC-G2ACS 6000 16-port unit single AC power supplyACS6016DAC-G2ACS 6000 16-port unit dual AC power supplyACS6016MDAC-G2ACS 6000 16-port unit dual AC power supply with built-in modem ACS6032SAC-G2ACS 6000 32-port unit single AC power supplyACS6032DAC-G2ACS 6000 32-port unit dual AC power supplyACS6032MDAC-G2ACS 6000 32-port unit dual AC power supply with built-in modem ACS6048SAC-G2ACS 6000 48-port unit single AC power supplyACS6048DAC-G2ACS 6000 48-port unit dual AC power supplyACS6048MDAC-G2ACS 6000 48-port unit dual AC power supply with built-in modemDC Power Supply ModelsACS6008SDC-G2ACS 6000 8-port unit single DC power supplyACS6008MSDC-G2ACS 6000 8-port unit single DC power supply with built-in modem ACS6032DDC-G2ACS 6000 32-port unit dual DC power supplyACS6032MDDC-G2ACS 6000 32-port unit dual DC power supply with built-in modem ACS6048DDC-G2ACS 6000 48-port unit dual DC power supplyACS6048MDDC-G2ACS 6000 48-port unit dual DC power supply with built-in modemy y Dual power supplyy y Internal modem supporty y USB port support for modems, fiber and storage Securityy y The FIPS mode of operation uses an embeddedFIPS 140-2 certified OpenSSL cryptographic module (Certificate #1051)y y Preset security profiles–secure, moderate and open y y Custom security profilesy y X.509 SSH certificate support y y SSHv1 and SSHv2y y Local, RADIUS, TACACS+, LDAP/AD, NIS andKerberos authenticationy y Two-factor authentication (RSA SecurID®)y y One-Time Password (OTP) authentication y y Local, backup-user authentication supporty y PAP/CHAP and Extensible Authentication Protocol(EAP) authentication (for dial-up lines)y y Group authorization:TACACS+, RADIUS and LDAP; Port access; Power access; Appliance privilege y y I P packet and security filtering y y User-access lists per port y y System event syslog y y I PSec with NAT traversal support y y IP forwarding support y y Secure factory defaults y y S trong password enforcement Console Managementy y Sun break-safe (Solaris Ready Certified)y y Break-over SSH supporty y Off-line data buffering – local and remote (NFS/Syslog/DSView software)y y Level-based syslog filters y y T ime stamp and rotations for data buffering y y U nlimited number of simultaneous sessions y y S imultaneous access on the same port (portsniffing) with ability to toggley y Configurable event notification (e-mail, pager,SNMP trap)y y C ustomizable, global time zone supporty y Multiple and customizable user levels of access Port Accessy y Directly by server name or device name y y CLI Commandy y Simultaneous Telnet and SSH access y y HTTP/HTTPSSystem Managementy y Configuration wizard in Web for first-time users y y Auto-discovery for automatic deployment y y Command line interface (CLI)y y Web Management Interface (HTTP/HTTPS)y y SNMPy y Internal temperature sensorCablingy y CAT-5 compatible adapters for simpler cabling†y y Configurable Cyclades and Cisco pin-outs for serialports Upgradesy y Upgrades available on FTP site, no charge y y TFTP support for network bootOrdering DetailsAC Power Supply ModelsACS6004SAC-G2ACS 6000 4-port unit single AC power supplyACS6004DAC-G2ACS 6000 4-port unit dual AC power supplyACS6004MDAC-G2ACS 6000 4-port unit dual AC power supply with built-in modem。
ICP-AES(美国热电teva操作软件初级和中级说明书)
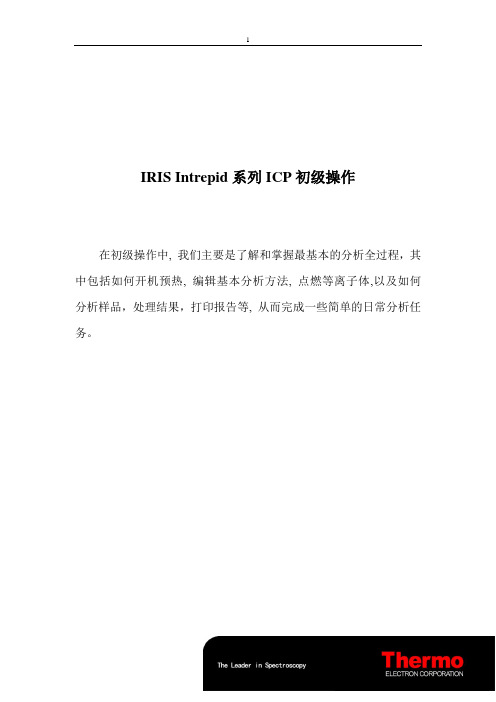
IRIS Intrepid系列ICP初级操作在初级操作中, 我们主要是了解和掌握最基本的分析全过程,其中包括如何开机预热, 编辑基本分析方法, 点燃等离子体,以及如何分析样品,处理结果,打印报告等, 从而完成一些简单的日常分析任务。
一.日常操作1. 开机预热2. 制定分析方案3. 编辑分析方法4. 点火操作5. 谱线校准6. 建立标准曲线并分析样品7. 熄火并返回待机状态8. 完全关机二.常见故障与排除三.日常维护一. 日常操作1、开机预热1)确认有足够的氩气用于连续工作。
(储量≥1瓶)2)确认废液收集桶有足够的空间用于收集废液。
3)打开氩气钢瓶的总开关(开到最大),并调节分压在0.5—0.7Mpa之间。
4)打开稳压电源开关,检查电源是否稳定,观察约1分钟。
5)打开主机电源。
(右侧下方红色刀闸)注意仪器自检动作。
此时光室开始预热。
6)打开电脑,待自检完成后,双击“TEVA”图标,进入操作软件主窗口,单击右下脚点火图标,进入等离子体控制面板,检查通讯及连锁保护开关是否正常。
若有红灯警示,则需要作相应的检查。
如果一切正常,可进行下一步操作。
2、制定分析方案1)确定样品是否适用于ICP分析。
ICP主要以常量和微量分析为主,在没有基体干扰的情况下,样品溶液中元素的含量一般不应小于5*DL(检出限),在有基体干扰的情况下,样品溶液中元素的含量一般不应小于5*5*DL。
2)确定样品分解方法(溶样方法)确保所测的元素能够完全分解,并溶解在溶液中。
尽可能用HNO3或HCL分解样品。
尽量不用H2SO4和H3PO4,会降低雾化效率。
如果用HF酸的话,一定要赶尽,以避免损坏雾化器和影响B、Na、Si、Al等元素的测定。
3)配制工作曲线(混标)浓度之间相差2—5倍一般用2—3点两个常见错误: a).所有分析元素的浓度都一致, 这样省事, 但不科学, 应该根据不同元素的浓度范围, 制定其相应的标准溶液浓度。
b).标准曲线点与点之间相隔太近, 如2, 4, 6,8…,完全没有必要。