pumping_nylon第一章:该做的和不该做的
《吉他教程》pumping_nylon_第二章:左手

“失败的准备就是在准备失败。
”左手手指按弦的位置和精确度让手指让成一种强而有力的“站姿”,并且将手指放在恰当的位置使它拥有最大的控制范围和灵活性是十分必要的。
从下面的插图你可以看出,左手手指并不总是用指尖正中按弦,而应该采用下列的更有效的位置:1食指用指尖左边按弦2中指用指尖正中稍微偏左部分按弦3无名指用指尖正中稍微偏右部分按弦4小指用指尖右边按弦这样按弦可以使手左右两边更多的肌肉参与进来,不仅仅是为了四根手指更有力(尽管这也是它的好处之一),同时也使整只手更平衡,更有力,更牢固。
他也可以使手指更灵巧。
注意看每只手的第二关节,它们并不相互接触!不仅不要接触,还要留出一定的空间。
这样可使手得到扩张,并在必要时可以快速移动。
保持第二关节不接触,这比单纯的撑开手指有更大的锻炼肌肉的效果,本书的关键词是“节约”:节约影响,节约能量,节约动作。
大拇指应该在中指的下方,这有助于平衡拇指和其它手指的压力,得到类似老虎钳的效果。
压弦﹑放松;压弦﹑放松为了使你的左手熟悉上述的按弦姿势,尤其是你初次接触这个姿势的话,做下面的练习。
压弦/放松练习把左手按照上一页所说的放好(注意不要忽略拇指)。
四根手指分别按在随便某根弦的一到四品(我建议从第三根弦开始)。
按下四个品,然后放开(释放压力),但手指保持放在弦上。
通过这种“弦上放松”确保手指位置固定,继续按下四个品,然后放松。
按弦﹑放松,按弦﹑放松,一直这样保持手指不离弦地做一定次数。
这个练习的重点是记住手指按弦(提供压力),还有放松(完全释放压力)时的感觉。
四根手指必须同时按弦,同时放松。
感觉一下前面说的老虎钳一般的效果。
感受一下压力是怎样平均分配到四根手指和拇指的。
当你重复这个练习很多遍并且掌握到诀窍后,尝试四根指头逐根按下。
同样从前面说的那个位置开始——四指触到弦但不压下去。
手指变换虽然看上去很简单,但我们刚刚接触到了拥有一只灵活的左手的关键开端:控制手指的按弦和放松。
古典吉他完全自学的书

古典吉他完全自学的书以下是一些古典吉他完全自学的书籍推荐:1. "Solo Guitar Playing Book 1" by Frederick Noad - 适合初学者,介绍了基本的技巧和指法,并提供了一系列的练习和曲目。
2. "The Christopher Parkening Guitar Method - Volume 1" by Christopher Parkening and David Brandon - Christopher Parkening 是一位著名的古典吉他演奏家,他的教学方法很清晰易懂。
这本书适合初级和中级学生,并包括了一些经典曲目的乐谱。
3. "Pumping Nylon: The Classical Guitarist's Technique Handbook" by Scott Tennant - 这是一本关于古典吉他技巧的经典手册。
书中包含了大量的练习和建议,适合不同水平的学习者。
4. "Grade by Grade - Classical Guitar: Grade 1" by Janet Dowsett and David Burden - 这本书是《ABRSM 古典吉他等级考试》的指定教材之一。
书中包含了不同难度的曲目和技巧练习。
5. "The Art of Classical Guitar Playing" by Charles Duncan - 这是一本经典的古典吉他教材,适合初学者和中级学生。
书中介绍了各种技巧和乐谱。
这些书籍提供了各种不同级别的教学材料和练习,适合自学古典吉他。
同时,建议结合在线视频教程或找一位古典吉他老师进行指导,以获得更好的学习效果。
林菲尔·拜肯斯朗电动液

SAM400 & 650 PERKINS DIESEL ENGINE DRIVENIM568 April, 1997Mar ‘95Mar ‘95Mar.‘93for selecting a QUALITY product by Lincoln Electric.We want you to take pride in operating this Lincoln Electric Company product •••as much pride as we have in bringing this product to you!Read this Operators Manual completely before attempting to use this equipment.Save this manual and keep it handy for quick reference.Pay particular attention to the safety instructions we have provided for your protection.The level of seriousness to be applied to each is explained below:vv(1)Consult applicable federal, state and local laws regardingspecific requirements for use on public highways.SPEED CONTROL LEVERManually allows the engine to run at its high idle speed controlled by the governor or at the factory set low idle speed.When welding or using auxiliary power the speed control lever must be in the “RUN”position.T o reduce the engine to low idle speed when not welding or not using auxiliary power place the speed control lever in the “IDLE”position notch.ENGINE TEMPERATURE GAUGEDisplays the coolant temperature in the engine block. OIL PRESSURE GAUGEDisplays the oil pressure to the engine.When the engine starts running, watch for the oil pressure to build up.If no pressure shows within 30 seconds, stop the engine and consult the engine instruction manual. BATTERY CHARGING AMMETERDisplays the current going from the charging alternator into the batteries.It is normal for charging current to be high (above 15 amps) after starting or when the batter-ies are ‘low’on charge.ENGINE HOUR METER(Factory Installed Optional Feature)The optional engine hour meter records the total run-ning time on the engine in hours.It can be used to keep a record of maintenance on the engine and or welder. ENGINE PROTECTION SYSTEMThe engine protection system shuts down the engine under high coolant temperature or low oil pressure conditions by allowing the fuel solenoid valve to close.place.3.Remove the two screws on the top end of the wirefeeder nameplate.4.Position the “Portable Field Control”mounting slotsover these holes and replace the screws.5.Route the leads with the LN-5 or LN-6 control cableback to the power source.MOUNTING ON LN-71.Remove the top screws on the side of the LN-7 con-trol box cover.(This is the left side when facing the nameplate).2.Position the “Portable Field Control”on the side ofthe control box with the mounting slots over these holes and replace the screws.3.Route the leads with the LN-7 control cable back tothe power source.OUTPUT STUDSWith the Engine OFF connect the work cable to the “T o Work”stud.A.For Stick Electrode Welding1.Connect the electrode cable to the “Stick”studand the work cable to the “T o Work”stud.Connect the “T AP”lead in the SAM650 to theappropriate stud to adjust current and the arccharacteristics as described under “Currentand Voltage Controls.”2.Install the “Portable Field Control”.B.Automatic or Semiautomatic WeldingFor all automatic welding processes, connect the welding power cable from the wire feeder to the “Connect to Auto.Equipment”stud.Connect the “T AP”lead in the SAM650 to the appropriate stud to adjust current and the arc characteristics as described under “Current and Voltage Controls.”1.LN-7, LN-8, LN-9, NA-3, NA-5, LT-7 and LT-56 Wire Feeders.a.Make the connections exactly as speci-fied on the connection wiring diagramincluded in the wire feeder InstructionManual.b.Install the “Portable Field Control”whenusing an LN-7.CURRENT AND VOLTAGE CONTROLS Constant Voltage WeldingThe SAM-400 “Current Control”is NOT in the circuit when the ‘Electrode Polarity’switch is set for constant voltage welding.Set the open circuit voltage (OCV) needed for the par-ticular application with the “Constant Voltage Control”located to the left of the nameplate.Adjust the final welding voltage with either the wire feeder voltage con-trol or the “Portable Field Control”.Set the welding cur-rent with “Amps”or “Wire Feed Speed”control on the wire feeder.Low Range Feature (SAM400 K1279-1 only) --Extends the output voltage range of the SAM400 welder down to 12 volts for constant voltage welding. The maximum output current is not to exceed the rat-ing of the machine.The Low Range Feature provides a two-position manual switch which allows the operator to set his machine for normal welding or for low voltage welding.Factory installed only.On the SAM650 connect the “T ap”lead inside the machine to the appropriate “Innershield”stud for”Min. (Flat) Slope.”“Med.Slope”or “Max.Slope”.Low voltage (below 20 volts) low current welding often requires “Max.Slope”to adjust the weld metal droplet size for minimum spatter and to control puddle fluidity and bead shape.Innershield and other spray transfer type processes generally operate with “Med.Slope”.A Hot Start circuit on all models operates automatical-ly whenever the toggle switch is set on “Constant Voltage.”It increases the open circuit voltage by sev-eral volts until the arc is established -- then the voltage automatically drops to normal welding voltage.When the wire feeder is started before the arc is started, the voltmeter indicates a voltage several volts higher than welding voltage.T o read actual welding voltage, the arc must be established.Constant Voltage Welding With Variable Inductance Control:SAM-400 Only.Variable inductance or slope control is usually desir-able for low voltage (below 20 volts) applications and is sometimes useful in other constant voltage jobs.To introduce this control into the circuit, set the “Electrode Polarity”switch to “Variable Voltage”and the toggle switch to “Constant Voltage”.Then the “Current Control”acts as the variable inductance control. Normally this control must be kept within the 8 to 1 o’clock range.To Set The Controls -- Stick Weldinga.Make the coarse setting of welding heat with theSAM400 “Current Control”or the SAM650“T ap’”lead.b.Adjust for the desired arc characteristics with the“Variable Voltage Control”.For a soft arc desired for most welding keep this control between 7 and High.For a more digging arc, set it lower.c.If remote control is NOT desired leave the“Portable Field Control”on “High”.For remote con-trol, leave the “Variable Voltage Control”near “High”and make the adjustments described in paragraph “b”above with the “Portable Field Control”.Remember, increasing either the “Variable Voltage Control”or “Portable Field Control”setting also increases the current.To Set The Controls -- Submerged Arca.The open circuit voltage (OCV) is generally notcritical in submerged arc welding.Therefore, the “Variable Voltage Control”can usually be left between 7 and “High”-- no future adjustments are needed.b.Set SAM400 “Current Control”so the calibrationon the higher scale is a little above the current desired.Set the SAM650 “T ap”lead to the stud with the lowest current range that still provides the desired current.c.Make the final current adjustment with either thewire feeder current control or the “Portable Field Control”.Set the arc voltage with the wire feeder control.Consult the following illustrations for examples of how to set the machine.STARTING WELDERS WITH DEAD BATTERIES Array DO NOT attempt to start a SAM engine driven welder by driving the welding generator as a starter motor using the output of another welder.In addition to the possibility of damaging the machines, starting a SAM engine welder without using its starting circuit elimi-nates the operation of the flashing circuit.This can cause the generator to fail to produce any output. AUXILIARY POWERAn alternator generates 2 KVA of 120/240 volt 60 Hertz AC power.It is available either from #31 and #32 on the terminal strip or from the receptacles on the Control Panel.Be careful not to overload this circuit. The auxiliary power receptacle should only be used with three wire grounded type plugs or approved dou-ble insulated tools with two wire plugs.The alternator is protected by thermostats and fuses. DUTY CYCLEDuty cycle is based on a ten minute period and opera-tion in an ambient temperature of 104°F(40°C).The SAM400 is NEMA rated at 60% duty cycle.The SAM650 is NEMA rated at 80% duty cycle.Duty cycle is based on a ten minute period.Therefore, a 60% duty cycle welder can be operated at nameplate rated out-put for 6 minutes (8 minutes for 80% duty cycle) out of every 10 minute period without overheating.The auxiliary power can be used continuously (100% duty cycle) within its rated current capacities.STARTING INSTRUCTIONSBe sure all Pre-Operation Maintenance has been per-formed.(See Installation Section of this manual.)T o start the engine, set the speed control lever in the “RUN”position.Place ignition toggle switch in the “ON”position.Push in the engine protection system reset button (if so equipped).Engage the starter button. When the engine starts running, observe the oil pres-sure.If no pressure shows within 30 seconds, stop the engine and consult the engine operating manual.T o stop the engine, place the ignition toggle switch in the “OFF”position.When an engine is started for the first time, some of the oil will be needed to fill the passages of the lubricatingsystem.Therefore, on initial starting, run the engine forK799 Hi-Freq™-Provides high frequency plus a gas valve for TIG welding.A water valve is available as an option.Requires 115 volt AC input.Cannot be used with optional meters connected, or in constant voltage mode.(Limited to 250A - 60% Duty Cycle).K802-D Power Plug Kit -For SAM welders with stan-dard 2KVA of AC auxiliary power.Kit includes male plugs for each auxiliary receptacle.K805-1 Ether Start Kit -Injects ether for starting aid. Recommended only when engines are frequently started at temperatures under 10°F (-12°C).Ether cylinder is not included.K767-1 Undercarriage -A 4-wheel steerable under-carriage for in-plant and yard towing1with E78-14 load range (B) tubeless tires.Mounts directly to welder base.1For highway use, consult applicable federal, state and local laws regarding possible requirements for brakes, lights, fenders, etc.Linc-Thaw™- Includes meter and fuse to protect the welder when thawing frozen water pipes.(L2964-[ ] Specify SAM400 or SAM650)K704(SAM400 only) Standard Accessory Kit -Includes electrode and work cables, headshield, work clamp and electrode holder.K865(SAM400 only) Engine Hour Meter Kit -(Standard on K1279-1).Keeps track of how long engine has been eful for following recom-mended maintenance schedules on machine.SAM400 only:Inspect the oil bath air filter daily - more often in dusty conditions.When necessary clean and fill the oil bath. The filter should never be removed while the engine is running.PERIODIC MAINTENANCE1.Blow out the welder and controls with an air hose atleast once every two months.In particularly dirty locations, this cleaning may be necessary once a e low pressure air to avoid driving dirt into the insulation.2.The SAM400 current control reactor brushes areself-lubricating and should not be greased.Keep the contacts clean.This control should be moved from maximum to minimum daily to prevent the controls from sticking.3.See the engine Instruction Manual for periodicengine maintenance information.Change the crankcase oil at regular intervals using the proper grade of oil as recommended in the engine operat-ing manual.Change the oil filter in accordance with the instructions in the engine operating manual.When the filter is changed add one quart of oil to the crankcase to replace the oil held in the filter dur-ing operation.4.Belts tend to loosen after the first 30 or 40 hours ofoperation.Check the cooling fan belt and tighten if necessary.DO NOT OVER TIGHTEN.BEARING MAINTENANCEThis welder is equipped with a double-shielded ball bearing having sufficient grease to last indefinitely under normal service.Where the welder is used con-stantly or in excessively dirty locations, it may be nec-essary to add one-half ounce of grease per year.A pad of grease one inch wide, one inch long and one inch high weighs approximately one-half ounce.Over greasing is far worse than insufficient greasing. When greasing the bearings, keep all dirt out of the area.Wipe the fittings completely clean and use clean equipment.More bearing failures are caused by dirt introduced during greasing than from insufficient grease.Arcing or excessive exciter brush wear indicates a pos-sible misaligned shaft.Have an authorized Field Service Shop check and realign the shaft. COOLING SYSTEMThe SAM welders are equipped with a pressure radia-tor.Keep the radiator cap tight to prevent loss of coolant.Clean and flush the cooling system periodi-cally to prevent clogging the passage and overheating the engine.When antifreeze is needed, always use the permanent type.CONTACTOR MAINTENANCEWhere the output contactor is operated frequently when tacking or making short welds, turn the engine off and inspect the contactor every three months:1.be sure the mating surfaces of silver contacts arenot worn and all make contact at approximately the same time.2.Make sure the springs and holders are not brokenor out of adjustment.Approximate spring com-pression after making contact is 1/8”.Less than 1/16”compression indicates worn contacts that should be replaced.3.Make sure the moving contact or other movingparts are not binding.4.Check interlock contacts and springs.Be suremounting screws are tight.NOTE A:If at any time either of the Control (PC) boards is replaced, follow the calibration procedure outlined later in this sec-tion under “Control P.C.Board Calibration Procedure”.The open circuit voltage will be out of range if trimmers are not properly set.If both trimmers are set at minimum, the machine might lose excitation.NOTE B:When making continuity checks, use the 1K (X1000) or next higher range.NOTE C:Do not replace PC boards without following outlined procedure for indicated trouble -- damage may result due to other defective parts.DC on SAM400 machines or 45±1 volts forSAM650 machines.Recheck to make surereadings fall within limits.T rimmer #4 set-ting is dependent on T rimmer #3.B.Constant Voltage1.Place toggle switch in constant voltageposition.2.T urn constant voltage rheostat and portablefield control to high.3.Set T rimmer #1 so that OCV is 60±1 voltsDC on SAM400 machines or 68±1 volts forSAM650 machines.4.T urn constant voltage rheostat and portablefield control to low.5.Set T rimmer #2 so that OCV is 21±0.5 voltsDC on SAM400 machines or 22±0.5 voltsfor SAM650 machines.Recheck to makesure readings fall within limits.T rimmer #2setting is dependent on T rimmer #1.N O T E :T h i s d i a g r a m i s f o r r e f e r e n c e o n l y .I t m a y n o t b e a c c u r a t e f o r a l l m a c h i n e s c o v e r e d b y t h i s m a n u a l.T h e s p e c i f i c d i a g r a m f o r a p a r t i c u l a r c o d e i s p a s t e d i n s i d e t h e m a c h i n e o n o n e o f t h e e n c l o s u r e p a n e l s .Now Available...12th EditionThe Procedure Handbook of Arc WeldingWith over 500,000 copies of previous editions published since 1933, the Procedure Handbook is considered by many to be the “Bible”of the arc welding industry.This printing will go fast so don’t delay.Place your order now using the coupon below.The hardbound book contains over 750 pages of welding infor-mation, techniques and procedures.Much of this material has never been included in any other book.A must for all welders, supervisors, engineers and designers.Many welding instructors will want to use the book as a reference for all students by taking advantage of the low quan-tity discount prices which include shipping by 4th class parcel post.$15.00postage paid U.S.A.MainlandHow To Read Shop DrawingsThe book contains the latest information and application data on the American Welding Society Standard Welding Symbols.Detailed discussion tells how engineers and drafts-men use the “short-cut”language of symbols to pass on assembly and welding information to shop personnel.Practical exercises and examples develop the reader’s ability to visualize mechanically drawn objects as they will appear in their assembled form.187 pages with more than 100 illustrations.Size 8-1/2”x 11”Durable, cloth-covered board binding.$4.50postage paid U.S.A.MainlandNew Lessons in Arc WeldingLessons, simply written, cover manipulatory techniques;machine and electrode characteristics;related subjects, such as distortion;and supplemental information on arc welding applications, speeds and costs.Practice materials, exercises,questions and answers are suggested for each lesson.528 pages, well illustrated, 6”x 9”size, bound in simulated,gold embossed leather.$5.00postage paid U.S.A.MainlandNeed Welding Training?The Lincoln Electric Company operates the oldest and most respected Arc Welding School in the United States at its corporate headquarters in Cleveland, Ohio.Over 100,000students have graduated.Tuition is low and the training is “hands on”For details write:Lincoln Welding School 22801 St.Clair Ave.Cleveland, Ohio 44117-1199.and ask for bulletin ED-80 or call 216-383-2259 and ask for the Welding School Registrar.Lincoln Welding SchoolBASIC COURSE $700.005 weeks of fundamentalsThere is a 10%discount on all orders of $50.00 or more for shipment at one time to one location.Orders of $50 or less before discount or orders outside of North America must be prepaid with charge, check or money order in U.S. Funds Only.Prices include shipment by 4th Class Book Rate for U.S.A. Mainland Only.Please allow up to 4 weeks for delivery.UPS Shipping for North America Only.All prepaid orders that request UPS shipment please add:$5.00For order value up to $49.99$10.00For order value between $50.00 & $99.99$15.00For order value between $100.00 & $149.00For North America invoiced orders over $50.00 & credit card orders, if UPS is requested, it will be invoiced or charged to you at cost.Outside U.S.A. Mainland order must be prepaid in U.S. Funds.Please add $2.00 per book for surface mail or $15.00 per book for air parcel post shipment.METHOD OF PAYMENT:(Sorry, No C.O.D.Orders)CHECK ONE:Name:_______________________________________________Address:_______________________________________________Ohio 44117-1199216-361-5901.JapaneseChineseKoreanArabicREAD AND UNDERSTAND THE MANUFACTURER’S INSTRUCTION FOR THIS EQUIPMENT AND THE CONSUMABLES TO BE USED AND FOLLOW YOUR EMPLOYER’S SAFETY PRACTICES.SE RECOMIENDA LEER Y ENTENDER LAS INSTRUCCIONES DEL FABRICANTE PARA EL USO DE ESTE EQUIPO Y LOS CONSUMIBLES QUE VA A UTILIZAR, SIGA LAS MEDIDAS DE SEGURIDAD DE SU SUPERVISOR.LISEZ ET COMPRENEZ LES INSTRUCTIONS DU FABRICANT EN CE QUI REGARDE CET EQUIPMENT ET LES PRODUITS A ETRE EMPLOYES ET SUIVEZ LES PROCEDURES DE SECURITE DE VOTRE EMPLOYEUR.LESEN SIE UND BEFOLGEN SIE DIE BETRIEBSANLEITUNG DER ANLAGE UND DEN ELEKTRODENEINSATZ DES HER-STELLERS. DIE UNFALLVERHÜTUNGSVORSCHRIFTEN DES ARBEITGEBERS SIND EBENFALLS ZU BEACHTEN.JapaneseChineseKoreanArabicLEIA E COMPREENDA AS INSTRUÇÕES DO FABRICANTE PARA ESTE EQUIPAMENTO E AS PARTES DE USO, E SIGA AS PRÁTICAS DE SEGURANÇA DO EMPREGADOR.。
曼昆微观经济学经济学十大原理 英文版
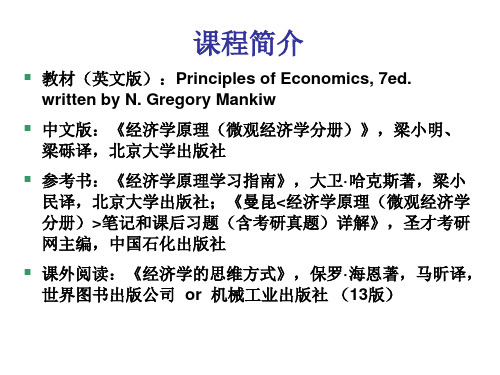
教材(英文版):Principles of Economics, 7ed.
written by N. Gregory Mankiw
中文版:《经济学原理(微观经济学分册)》,梁小明、
梁砾译,北京大学出版社
参考书:《经济学原理学习指南》,大卫· 哈克斯著,梁小
民译,北京大学出版社;《曼昆<经济学原理(微观经济学 分册)>笔记和课后习题(含考研真题)详解》,圣才考研 网主编,中国石化出版社
万美元时,高中篮球明星科 比.布赖恩特(Kobe Bryant )决定不读大学而直接进入 职业篮球联盟( NBA )。
TEN PRINCIPLES OF ECONOMICS
11
Examples:
Choice A B C D E Revenue 200$ 150$ 180$ 201$ 200$ opportunity cost 201$ 201$ 201$ 200$ 201$
1
CHAPTER
1
Ten Principles of Economics (经济学十大原理)
Economics
PRINCIPLES OF
N. Gregory Mankiw
© 2015 CUFE
In this chapter, look for the answers to these questions:
society gets the most from its scarce resources
Equality:经济成果在社会成员中公平分配的特性 when
prosperity is distributed uniformly among society’s members.
Tradeoff: To achieve greater equality, income could be
1-2007_-_Y_F_Han_-_PreparationofnanosizedMn3O4SBA15catalystforcomplet[retrieved-2016-11-15]
![1-2007_-_Y_F_Han_-_PreparationofnanosizedMn3O4SBA15catalystforcomplet[retrieved-2016-11-15]](https://img.taocdn.com/s3/m/9d89122483c4bb4cf7ecd13a.png)
Preparation of nanosized Mn 3O 4/SBA-15catalyst for complete oxidation of low concentration EtOH in aqueous solution with H 2O 2Yi-Fan Han *,Fengxi Chen,Kanaparthi Ramesh,Ziyi Zhong,Effendi Widjaja,Luwei ChenInstitute of Chemical and Engineering Sciences,1Pesek Road,Jurong Island 627833,Singapore Received 11May 2006;received in revised form 18December 2006;accepted 29May 2007Available online 2June 2007AbstractA new heterogeneous Fenton-like system consisting of nano-composite Mn 3O 4/SBA-15catalyst has been developed for the complete oxidation of low concentration ethanol (100ppm)by H 2O 2in aqueous solution.A novel preparation method has been developed to synthesize nanoparticles of Mn 3O 4by thermolysis of manganese (II)acetylacetonate on SBA-15.Mn 3O 4/SBA-15was characterized by various techniques like TEM,XRD,Raman spectroscopy and N 2adsorption isotherms.TEM images demonstrate that Mn 3O 4nanocrystals located mainly inside the SBA-15pores.The reaction rate for ethanol oxidation can be strongly affected by several factors,including reaction temperature,pH value,catalyst/solution ratio and concentration of ethanol.A plausible reaction mechanism has been proposed in order to explain the kinetic data.The rate for the reaction is supposed to associate with the concentration of intermediates (radicals: OH,O 2Àand HO 2)that are derived from the decomposition of H 2O 2during reaction.The complete oxidation of ethanol can be remarkably improved only under the circumstances:(i)the intermediates are stabilized,such as stronger acidic conditions and high temperature or (ii)scavenging those radicals is reduced,such as less amount of catalyst and high concentration of reactant.Nevertheless,the reactivity of the presented catalytic system is still lower comparing to the conventional homogenous Fenton process,Fe 2+/H 2O 2.A possible reason is that the concentration of intermediates in the latter is relatively high.#2007Elsevier B.V .All rights reserved.Keywords:Hydrogen peroxide;Fenton catalyst;Complete oxidation of ethanol;Mn 3O 4/SBA-151.IntroductionRemediation of wastewater containing organic constitutes is of great importance because organic substances,such as benzene,phenol and other alcohols may impose toxic effects on human and animal anic effluents from pharmaceu-tical,chemical and petrochemical industry usually contaminate water system by dissolving into groundwater.Up to date,several processes have been developed for treating wastewater that contains toxic organic compounds,such as wet oxidation with or without solid catalysts [1–4],biological oxidation,supercritical oxidation and adsorption [5,6],etc.Among them,catalytic oxidation is a promising alternative,since it avoids the problem of the adsorbent regeneration in the adsorption process,decreases significantly the temperature and pressure in non-catalytic oxidation techniques [7].Generally,the disposalof wastewater containing low concentration organic pollutants (e.g.<100ppm)can be more costly through all aforementioned processes.Thus,catalytic oxidation found to be the most economical way for this purpose with considering its low cost and high efficiency.Currently,a Fenton reagent that consists of homogenous iron ions (Fe 2+)and hydrogen peroxide (H 2O 2)is an effective oxidant and widely applied for treating industrial effluents,especially at low concentrations in the range of 10À2to 10À3M organic compounds [8].However,several problems raised by the homogenous Fenton system are still unsolved,e.g.disposing the iron-containing waste sludge,limiting the pH range (2.0–5.0)of the aqueous solution,and importantly irreversible loss of activity of the reagent.To overcome these drawbacks raised from the homogenous Fenton system,since 1995,a heterogeneous Fenton reagent using metal ions exchanged zeolites,i.e.Fe/ZSM-5has proved to be an interesting alternative catalytic system for treating wastewater,and showed a comparable activity with the homogenous Fenton system [9].However,most reported heterogeneous Fenton reagents still need UV radiation during/locate/apcatbApplied Catalysis B:Environmental 76(2007)227–234*Corresponding author.Tel.:+6567963806.E-mail address:han_yi_fan@.sg (Y .-F.Han).0926-3373/$–see front matter #2007Elsevier B.V .All rights reserved.doi:10.1016/j.apcatb.2007.05.031oxidation of organic compounds.This might limit the application of homogeneous Fenton system.Exploring other heterogeneous catalytic system considering the above disadvantages,is still desirable for this purpose.Here,we present an alternative catalytic system for the complete oxidation of organic com-pounds in aqueous solution using supported manganese oxide as catalyst under mild conditions,which has rarely been addressed.Mn-containing oxide catalysts have been found to be very active for the catalytic wet oxidation of organic effluents (CWO)[10–14],which is operated at high air pressures(1–22MPa)and at high temperatures(423–643K)[15].On the other hand,manganese oxide,e.g.MnO2[16],is well known to be active for the decomposition of H2O2in aqueous solution to produce hydroxyl radical( OH),which is considered to be the most robust oxidant so far.The organic constitutes can be deeply oxidized by those radicals rapidly[17].The only by-product is H2O from decomposing H2O2.Therefore,H2O2is a suitable oxidant for treating the wastewater containing organic compounds.Due to the recent progress in the synthesis of H2O2 directly from H2and O2[18,19],H2O2is believed to be produced through more economical process in the coming future.So,the heterogeneous Fenton system is economically acceptable.In this study,nano-crystalline Mn3O4highly dispersed inside the mesoporous silica,SBA-15,has been prepared by thermolysis of organic manganese(II)acetylacetonate in air. We expect the unique mesoporous structure may provide add-itional function(confinement effect)to the catalytic reaction, i.e.occluding/entrapping large organic molecules inside pores. The catalyst as prepared has been examined for the complete oxidation of ethanol in aqueous solution with H2O2,or to say, wet peroxide oxidation.Ethanol was selected as a model organic compound because(i)it is one of the simplest organic compounds and can be easily analyzed,(ii)it has high solu-bility in water due to its strong hydrogen bond with water molecule and(iii)the structure of ethanol is quite stable and only changed through catalytic reaction.Presently,for thefirst time by using the Mn3O4/SBA-15catalyst,we investigated the peroxide ethanol oxidation affected by factors such as temperature,pH value,ratio of catalyst(g)and volume of solution(L),and concentration of ethanol in aqueous solution. In addition,plausible reaction mechanisms are established to explain the peroxidation of ethanol determined by the H2O2 decomposition.2.Experimental2.1.Preparation and characterization of Mn3O4/SBA-15 catalystSynthesis of SBA-15is similar to the previous reported method[20]by using Pluronic P123(BASF)surfactant as template and tetraethyl orthosilicate(TEOS,98%)as silica source.Manganese(II)acetylacetonate([CH3COCH C(O)CH3]2Mn,Aldrich)by a ratio of2.5mmol/gram(SBA-15)werefirst dissolved in acetone(C.P.)at room temperature, corresponding to ca.13wt.%of Mn3O4with respect to SBA-15.The preparation method in detail can be seen in our recent publications[21,22].X-ray diffraction profiles were obtained with a Bruker D8 diffractometer using Cu K a radiation(l=1.540589A˚).The diffraction pattern was taken in the Bragg angle(2u)range at low angles from0.68to58and at high angles from308to608at room temperature.The XRD patterns were obtained by scanning overnight with a step size:0.028per step,8s per step.The dispersive Raman microscope employed in this study was a JY Horiba LabRAM HR equipped with three laser sources(UV,visible and NIR),a confocal microscope,and a liquid nitrogen cooled charge-coupled device(CCD)multi-channel detector(256pixelsÂ1024pixels).The visible 514.5nm argon ion laser was selected to excite the Raman scattering.The laser power from the source is around20MW, but when it reached the samples,the laser output was reduced to around6–7MW after passing throughfiltering optics and microscope objective.A100Âobjective lens was used and the acquisition time for each Raman spectrum was approximately 60–120s depending on the sample.The Raman shift range acquired was in the range of50–1200cmÀ1with spectral resolution1.7–2cmÀ1.Adsorption and desorption isotherms were collected on Autosorb-6at77K.Prior to the measurement,all samples were degassed at573K until a stable vacuum of ca.5m Torr was reached.The pore size distribution curves were calculated from the adsorption branch using Barrett–Joyner–Halenda(BJH) method.The specific surface area was assessed using the BET method from adsorption data in a relative pressure range from 0.06to0.10.The total pore volume,V t,was assessed from the adsorbed amount of nitrogen at a relative pressure of0.99by converting it to the corresponding volume of liquid adsorbate. The conversion factor between the volume of gas and liquid adsorbate is0.0,015,468for N2at77K when they are expressed in cm3/g and cm3STP/g,respectively.The measurements of transmission electron microscopy (TEM)were performed at Tecnai TF20S-twin with Lorentz Lens.The samples were ultrasonically dispersed in ethanol solvent,and then dried over a carbon grid.2.2.Kinetic measurement and analysisThe experiment for the wet peroxide oxidation of ethanol was carried out in a glass batch reactor connected to a condenser with continuous stirring(400rpm).Typically,20ml of aqueous ethanol solution(initial concentration of ethanol: 100ppm)wasfirst taken in the round bottomflask(reactor) together with5mg of catalyst,corresponding to ca.1(g Mn)/30 (L)ratio of catalyst/solution.Then,1ml of30%H2O2solution was introduced into the reactor at different time intervals (0.5ml at$0min,0.25ml at32min and0.25ml at62min). The total molar ratio of H2O2/ethanol is about400/1. Hydrochloric acid(HCl,0.01M)was used to acidify the solution if necessary.NH4OH(0.1M)solution was used to adjust pH to9.0when investigating the effect of pH.The pH for the deionized water is ca.7.0(Oakton pH meter)and decreased to 6.7after adding ethanol.All the measurements wereY.-F.Han et al./Applied Catalysis B:Environmental76(2007)227–234 228performed under the similar conditions described above if without any special mention.For comparison,the reaction was also carried out with a typical homogenous Fenton reagent[17], FeSO4(5ppm)–H2O2,under the similar reaction conditions.The conversion of ethanol during reaction was detected using gas chromatography(GC:Agilent Technologies,6890N), equipped with HP-5capillary column connecting to a thermal conductive detector(TCD).There is no other species but ethanol determined in the reaction system as evidenced by the GC–MS. Ethanol is supposed to be completely oxidized into CO2and H2O.The variation of H2O2concentration during reaction was analyzed colorimetrically using a UV–vis spectrophotometer (Epp2000,StellarNet Inc.)after complexation with a TiOSO4/ H2SO4reagent[18].Note that there was almost no measurable leaching of Mn ion during reaction analyzed by ICP(Vista-Mpx, Varian).3.Results and discussion3.1.Characterization of Mn3O4/SBA-15catalystThe structure of as-synthesized Mn3O4inside SBA-15has beenfirst investigated with powder XRD(PXRD),and the profiles are shown in Fig.1.The profile at low angles(Fig.1a) suggests that SBA-15still has a high degree of hexagonal mesoscopic organization even after forming Mn3O4nanocrys-tals[23].Several peaks at high angles of XRD(Fig.1b)indicate the formation of a well-crystallized Mn3O4.All the major diffraction peaks can be assigned to hausmannite Mn3O4 structure(JCPDS80-0382).By N2adsorption measurements shown in Fig.2,the pore volume and specific surface areas(S BET)decrease from 1.27cm3/g and937m2/g for bare SBA-15to0.49cm3/g and 299m2/g for the Mn3O4/SBA-15,respectively.About7.7nm of mesoporous diameter for SBA-15decreases to ca.6.3nm for Mn3O4/SBA-15.The decrease of the mesopore dimension suggests the uniform coating of Mn3O4on the inner walls of SBA-15.This nano-composite was further characterized by TEM. Obviously,the SBA-15employed has typical p6mm hex-agonal morphology with the well-ordered1D array(Fig.3a). The average pore size of SBA-15is ca.8.0nm,which is very close to the value(ca.7.7nm)determined by N2adsorption. Along[001]orientation,Fig.3b shows that the some pores arefilled with Mn3O4nanocrystals.From the pore A to D marked in Fig.3b correspond to the pores from empty to partially and fullyfilled;while the features for the SBA-15 nanostructure remains even after forming Mn3O4nanocrys-tals.Nevertheless,further evidences for the location of Mn3O4inside the SBA-15channels are still undergoing in our group.Raman spectra obtained for Mn3O4/SBA-15is presented in Fig.4a.For comparison the Raman spectrum was also recorded for the bulk Mn3O4(97.0%,Aldrich)under the similar conditions(Fig.4b).For the bulk Mn3O4,the bands at310,365, 472and655cmÀ1correspond to the bending modes of Mn3O4, asymmetric stretch of Mn–O–Mn,symmetric stretch of Mn3O4Fig.1.XRD patterns of the bare SBA-15and the Mn3O4/SBA-15nano-composite catalyst.(a)At low angles:(A)Mn3O4/SBA-15,(B)SBA-15;and (b)at high angles of Mn3O4/SBA-15.Fig.2.N2adsorption–desorption isotherms:(!)SBA-15,(~)Mn3O4/SBA-15.Y.-F.Han et al./Applied Catalysis B:Environmental76(2007)227–234229groups,respectively [24–26].However,a downward shift ($D n 7cm À1)of the peaks accompanying with a broadening of the bands was observed for Mn 3O 4/SBA-15.For instance,the distinct feature at 655cm À1for the bulk Mn 3O 4shifted to 648cm À1for the nanocrystals.The Raman bands broadened and shifted were observed for the nanocrystals due to the effect of phonon confinement as suggested previously in the literature [27,28].Furthermore,a weak band at 940cm À1,which should associate with the stretch of terminal Mn O,is an indicative of the existence of the isolated Mn 3O 4group [26].The assignment of this unique band has been discussed in our previous publication [22].3.2.Kinetic study3.2.1.Blank testsUnder a typical reaction conditions,that is,20ml of 100ppm ethanol aqueous solution (pH 6.7)mixed with 1ml of 30%H 2O 2,at 343K,there is no conversion of ethanol was observed after running for 120min in the absence of catalyst or in the presence of bare SBA-15(5mg).Also,under the similar conditions in H 2O 2-free solution,ethanol was not converted for all blank tests even with Mn 3O 4/SBA-15catalyst (5mg)in the reactor.It suggests that a trace amount of oxygen dissolved in water or potential dissociation of adsorbed ethanol does not have any contribution to the conversion of ethanol under reaction conditions.To study the effect of low temperature evaporation of ethanol during reaction,we further examined the concentration of ethanol (100ppm)versus time at different temperatures in the absence of catalyst and H 2O 2.Loss of ca.5%ethanol was observed only at 363K after running for 120min.Hence,to avoid the loss of ethanol through evaporation at high temperatures,which may lead to a higher conversion of ethanol than the real value,the kinetic experiments in this study were performed at or below 343K.The results from blank tests confirm clearly that ethanol can be transformed only by catalytic oxidation during reaction.3.2.2.Effect of amount of catalystThe effect of amount of catalyst on ethanol oxidation is presented in Fig.5.Different amounts of catalyst ranging from 2to 10mg were taken for the same concentration of ethanol (100ppm)in aqueous solution under the standard conditions.It can be observed that the conversion of ethanol increases monotonically within 120min,reaching 15,20and 12%for 2,5and 10mg catalysts,respectively.On the other hand,Fig.5shows that the relative reaction rates (30min)decreased from 0.7to ca 0.1mmol/g Mn min with the rise of catalyst amount from 2to 10mg.Apparently,more catalyst in the system may decrease the rate for ethanol peroxidation,and a proper ratio of catalyst (g)/solution (L)is required for acquiring a balance between the overall conversion of ethanol and reaction rate.In order to investigate the effects from other factors,5mg (catalyst)/20ml (solution),corresponding to 1(g Mn )/30(L)ratio of catalyst/solution,has been selected for the followedexperiments.Fig.4.Raman spectroscopy of the Mn 3O 4/SBA-15(a)and bulk Mn 3O 4(b).Fig.3.TEM images recorded along the [001]of SBA-15(a),Mn 3O 4/SBA-15(b):pore A unfilled with hexagonal structure,pores B and C partially filled and pore D completely filled.Y.-F .Han et al./Applied Catalysis B:Environmental 76(2007)227–2342303.2.3.Effect of temperatureAs shown in Fig.6,the reaction rate increases with increasing the reaction temperature.After 120min,the conversion of ethanol increases from 12.5to 20%when varying the temp-erature from 298to 343K.Further increasing the temperature was not performed in order to avoid the loss of ethanol by evaporation.Interestingly,the relative reaction rate increased with time within initial 60min at 298and 313K,but upward tendency was observed above 333K.3.2.4.Effect of pHIn the pH range from 2.0to 9.0,as illustrated in Fig.7,the reaction rate drops down with the rise of pH.It indicates that acidic environment,or to say,proton concentration ([H +])in the solution is essential for this reaction.With considering our target for this study:purifying water,pH approaching to 7.0in the reaction system is preferred.Because acidifying the solution with organic/inorganic acids may potentially causea second time pollution and result in surplus cost.Actually,there is almost no effect on ethanol conversion with changing pH from 5.5to 6.7in this system.It is really a merit comparing with the conventional homogenous Fenton system,by which the catalyst works only in the pH range of 2.0–5.0.3.2.5.Effect of ethanol concentrationThe investigation of the effect of ethanol concentration on the reaction rate was carried out in the ethanol ranging from 50to 500ppm.The results in Fig.8show that the relative reaction rate increased from 0.07to 2.37mmol/g Mn min after 120min with increasing the concentration of ethanol from 50to 500ppm.It is worth to note that the pH value of the solution slightly decreased from 6.7to 6.5when raising the ethanol concentration from 100to 500ppm.paring to a typical homogenous Fenton reagent For comparison,under the similar reaction conditions ethanol oxidation was performed using aconventionalFig.5.The ethanol oxidation as a function of time with different amount of catalyst.Conversion of ethanol vs.time (solid line)on 2mg (&),5mg (*)and 10mg (~)Mn 3O 4/SBA-15catalyst,the relative reaction rate vs.time (dash line)on 2mg (&),5mg (*)and 10mg (~)Mn 3O 4/SBA-15catalyst.Rest conditions:20ml of ethanol (100ppm),1ml of 30%H 2O 2,708C and pH of6.7.Fig.6.The ethanol oxidation as a function of temperature.Conversion of ethanol vs.time (solid line)at 258C (&),408C (*),608C (~)and 708C (!),the relative reaction rate vs.time (dash line)at 258C (&),408C (*),608C (~)and 708C (5).Rest conditions:20ml of ethanol (100ppm),1ml of 30%H 2O 2,pH of 6.7,5mg ofcatalyst.Fig.7.The ethanol oxidation as a function of pH value.Conversion of ethanol vs.time (solid line)at pH value of 2.0(&),3.5(*),4.5(~),5.5(!),6.7(^)and 9.0("),the relative reaction rate vs.time (dash line)at pH value of 2.0(&),3.5(*),4.5(~),5.5(5),6.7(^)and 9.0(").Rest conditions:20ml of ethanol (100ppm),1ml of 30%H 2O 2,708C,5mg ofcatalyst.Fig.8.The ethanol oxidation as a function of ethanol concentration.Conver-sion of ethanol vs.time (solid line)for ethanol concentration (ppm)of 50(&),100(*),300(~),500(!),the relative reaction rate vs.time (dash line)for ethanol concentration (ppm)of 50(&),100(*),300(~),500(5).Condi-tions:20ml of ethanol,pH of 6.7,1ml of 30%H 2O 2,708C,5mg of catalyst.Y.-F .Han et al./Applied Catalysis B:Environmental 76(2007)227–234231homogenous reagent,Fe 2+(5ppm)–H 2O 2(1ml)at pH of 5.0.It has been reported to be an optimum condition for this system [17].As shown in Fig.9,the reaction in both catalytic systems exhibits a similar behavior,that is,the conversion of ethanol increases with extending the reaction time.Varying reaction temperature from 298to 343K seems not to impact the conversion of ethanol when using the homogenous Fenton reagent.Furthermore,the conversion of ethanol (defining at 120min)in the system of Mn 3O 4/SBA-15–H 2O 2is about 60%of that obtained from the conventional Fenton reagent.There are no other organic compounds observed in the reaction mixture other than ethanol suggesting that ethanol directly decomposing to CO 2and H 2O.3.2.7.Decomposition of H 2O 2In the aqueous solution,the capability of metal ions such as Fe 2+and Mn 2+has long been evidenced to be effective on the decomposition of H 2O 2to produce the hydroxyl radical ( OH),which is oxidant for the complete oxidation/degrading of organic compounds [9,17].Therefore,ethanol oxidation is supposed to be associated with H 2O 2decomposition.The investigation of H 2O 2decomposition has been performed under the reaction conditions (in an ethanol-free solution)with different amounts of catalyst.H 2O 2was introduced into the reaction system by three steps,initially 0.5ml followed by twice 0.25ml at 32and 62min,the pH of 6.7is set for all experiments except pH of 5.0for Fe 2+.As shown in Fig.10,H 2O 2was not converted in the absence of catalyst or presence of bare SBA-15(5mg);in contrast,by using the Mn 3O 4/SBA-15catalyst we observed that ca.Ninety percent of total H 2O 2was decomposed in the whole experiment.It can be concluded that that dissociation of H 2O 2is mainly caused by Mn 3O paratively,the rate of H 2O 2decomposition is relatively low with the homogenous Fenton reagent,total conversion of H 2O 2,was ca.50%after runningfor 120min.Considering the fact that H 2O 2decomposition can be significantly enhanced with the rise of Fe 2+concentration,however,it seems not to have the influence on the reaction rate for ethanol oxidation simultaneously.The similar behavior of H 2O 2decomposition was also observed during ethanol oxidation.The rate for ethanol oxidation is lower for Mn 3O 4/SBA-15comparing to the conventional Fenton reagent.The possible reasons will be discussed in the proceeding section.3.3.Plausible reaction mechanism for ethanol oxidation with H 2O 2In general,the wet peroxide oxidation of organic constitutes has been suggested to proceed via four steps [15]:activation of H 2O 2to produce OH,oxidation of organic compounds withOH,recombination of OH to form O 2and wet oxidation of organic compounds with O 2.It can be further described by Eqs.(1)–(4):H 2O 2À!Catalyst =temperture 2OH(1)OH þorganic compoundsÀ!Temperatureproduct(2)2 OHÀ!Temperature 12O 2þH 2O(3)O 2þorganic compoundsÀ!Temperature =pressureproduct(4)The reactive intermediates produced from step 1(Eq.(1))participate in the oxidation through step 2(Eq.(2)).In fact,several kinds of radical including OH,perhydroxyl radicals ( HO 2)and superoxide anions (O 2À)may be created during reaction.Previous studies [29–33]suggested that the process for producing radicals could be expressed by Eqs.(5)–(7)when H 2O 2was catalytically decomposed by metal ions,such asFeparison of ethanol oxidation in systems of typical homogenous Fenton catalyst (5ppm of Fe 2+,20ml of ethanol (100ppm),1ml of 30%H 2O 2,pH of 5.0acidified with HCl)at room temperature (~)and 708C (!),and Mn 3O 4/SBA-15catalyst (&)under conditions of 20ml of ethanol (100ppm),pH of 6.7,1ml of 30%H 2O 2,708C,5mg ofcatalyst.Fig.10.An investigation of H 2O 2decomposition under different conditions.One milliliter of 30%H 2O 2was dropped into the 20ml deionized water by three intervals,initial 0.5ml followed by twice 0.25ml at 32and 62min.H 2O 2concentration vs.time:by calculation (&),without catalyst (*),SBA-15(~),5ppm of Fe 2+(!)and Mn 3O 4/SBA-15(^).Rest conditions:5mg of solid catalyst,pH of 7.0(5.0for Fe 2+),708C.Y.-F .Han et al./Applied Catalysis B:Environmental 76(2007)227–234232and Mn,S þH 2O 2!S þþOH Àþ OH (5)S þþH 2O 2!S þ HO 2þH þ(6)H 2O $H þþO 2À(7)where S and S +represent reduced and oxidized metal ions,both the HO 2and O 2Àare not stable and react further with H 2O 2to form OH through Eqs.(8)and (9):HO 2þH 2O 2! OH þH 2O þO 2(8)O 2ÀþH 2O 2! OH þOH ÀþO 2(9)Presently, OH radical has been suggested to be the main intermediate responsible for oxidation/degradation of organic compounds.Therefore,the rate for ethanol oxidation in the studied system is supposed to be dependent on the concentra-tion of OH.Note that the oxidation may proceed via step four (Eq.(4))in the presence of high pressure O 2,which is so-called ‘‘wet oxidation’’and usually occurs at air pressures (1–22MPa)and at high temperatures (423–643K)[15].However,it is unlikely to happen in the present reaction conditions.According to Wolfenden’s study [34],we envisaged that the complete oxidation of ethanol may proceed through a route like Eq.(10):C 2H 5OH þ OH À!ÀH 2OC 2H 4O À! OHCO 2þH 2O(10)Whereby,it is believed that organic radicals containing hydroxy-groups a and b to carbon radicals centre can eliminate water to form oxidizing species.With the degrading of organic intermediates step by step as the way described in Eq.(10),the final products should be CO 2and H 2O.However,no other species but ethanol was detected by GC and GC–MS in the present study possibly due to the rapid of the reaction that leads to unstable intermediate.Fig.5indicates that a proper ratio of catalyst/solution is a necessary factor to attain the high conversion of ethanol.It can be understood that over exposure of H 2O 2to catalyst will increase the rate of H 2O 2decomposition;but on the other hand,more OH radical produced may be scavenged by catalyst with increasing the amount of catalyst and transformed into O 2and H 2O as expressed in Eq.(3),instead of participating the oxidation reaction.In terms of Eq.(10),stoichiometric ethanol/H 2O 2should be 1/6for the complete oxidation of ethanol;however,in the present system the total molar ratio is 1/400.In other words,most intermediates were extinguished through scavenging during reaction.This may explain well that the decrease of reaction rate with the rise of ratio of catalyst/solution in the system.The same reason may also explain the decrease of reaction rate with prolonging the time.Actually,H 2O 2decomposition (ca.90%)may be completed within a few minutes over the Mn 3O 4/SBA-15catalyst as illustrated in Fig.10,irrespective of amount of catalyst (not shown for the sake of brevity);in contrast,the rate for H 2O 2decomposition became dawdling for Fe 2+catalyst.As a result,presumably,the homogenous system has relatively high concentration ofradicals.It may explain the superior reactivity of the conventional Fenton reagent to the presented system as depicted in Fig.9.Therefore,how to reduce scavenging,especially in the heterogeneous Fenton system [29],is crucial for enhancing the reaction rate.C 2H 5OH þ6H 2O 2!2CO 2þ9H 2O(11)On the other hand,as illustrated by Eqs.(1)–(4),all steps in the oxidation process are affected by the reaction temperature.Fig.6demonstrates that increasing temperature remarkably boosts the reactivity of ethanol oxidation in the system of Mn 3O 4/SBA-15–H 2O 2possibly,due to the improvement of the reactions in Eqs.(2)and (4)at elevated temperatures.In terms of Eqs.(6)and (7),acidic conditions may delay the H 2O 2decomposition but enhance the formation of OH (Eqs.(5),(8)and (9)).This ‘‘delay’’is supposed to reduce the chance of the scavenging of radicals and improve the efficiency of H 2O 2in the reaction.The protons are believed to have capability for stabilizing H 2O 2,which has been elucidated well previously [18,19].Consequently,it is understandable that the reaction is favored in the strong acidic environment.Fig.7shows a maximum reactivity at pH of 2.0and the lowest at pH of 9.0.As depicted in Fig.8,the reaction rate for ethanol oxidation is proportional to the concentration of ethanol in the range of 50–500ppm.It suggests that at low concentration of ethanol (100ppm)most of the radicals might not take part in the reaction before scavenged by catalyst.With increasing the ethanol concentration,the possibility of the collision between ethanol and radicals can be increased significantly.As a result,the rate of scavenging radicals is reduced relatively.Thus,it is reasonable for the faster rate observed at higher concentration of ethanol.Finally,it is noteworthy that as compared to the bulk Mn 3O 4(Aldrich,98.0%of purity),the reactivity of the nano-crystalline Mn 3O 4on SBA-15is increased by factor of 20under the same typical reaction conditions.Obviously,Mn 3O 4nanocrystal is an effective alternative for this catalytic system.The present study has evidenced that the unique structure of SBA-15can act as a special ‘‘nanoreactor’’for synthesizing Mn 3O 4nanocrystals.Interestingly,a latest study has revealed that iron oxide nanoparticles could be immobilized on alumina coated SBA-15,which also showed excellent performance as a Fenton catalyst [35].However,the role of the pore structure of SBA-15in this reaction is still unclear.We do expect that during reaction SBA-15may have additional function to trap larger organic molecules by adsorption.Thus,it may broaden its application in this field.So,relevant study on the structure of nano-composites of various MnO x and its role in the Fenton-like reaction for remediation of organic compounds in aqueous solution is undergoing in our group.4.ConclusionsIn the present study,we have addressed a new catalytic system suitable for remediation of trivial organic compound from contaminated water through a Fenton-like reaction withY.-F .Han et al./Applied Catalysis B:Environmental 76(2007)227–234233。
Pumping and Storing Breast Milk

Pumping and Storing Breast Milk You may need to express or pump breast milk to relieve engorgement, to increase your milk supply or to feed your baby breast milk with a bottle.Why and When to Pump• To soften your breasts if your baby is having trouble latching on.Pump for a few minutes and try your baby at your breast again. • To have a milk supply when your baby is unable to breastfeed or tostore breast milk.Pump every 2 to 4 hours through the day and one time at night. • To increase your milk supply.Pump every 2 to 3 hours if you are not breastfeeding, orPump between feedings as often as you can.Pump on the second breast if your baby only nurses on one side. • To prepare to return to work or school.Pump one time each day, between feedings to store extra milk.Morning is a good time to pump.Pump extra milk and store it at least 2 weeks before your return date.Pump at least every 4 hours when away.用吸奶器吸出乳汁和储存乳汁为了缓解涨奶、促进乳汁分泌或用奶瓶喂宝宝乳汁,可能需要挤出乳汁或用吸奶器吸出乳汁。
PUMPINGNYLON(跳动的尼龙)字幕(用记事本打开后,另存为SRT格式就能用了)

81
00:15:59,999-->00:16:07,000
指甲的修剪十分重要
82
00:16:08,000-->00:16:23,000
把指甲修剪成良好的形状,可以使演奏的音色饱满,
使手指拨弦的动作非常轻松
Hale Waihona Puke 83 00:16:26,000-->00:16:33,000
牢记:修剪的原则是,
96
00:21:58,000-->00:22:08,000
它有两面,共四种不同的粗细度
97
00:22:30,000-->00:22:50,000
这是一张非常细的砂纸,500#号的
不同国家可能标准不同(总之用很细的砂纸)
98
00:23:03,000-->00:23:06,000
撕下一小块
46
00:08:36,000-->00:08:39,000
是不是觉得很难受?很不自然?
47
00:08:42,000-->00:08:59,000
将手臂转向正面,左右运动手腕并握拳
这样感觉也很轻松,我们可以做很多次
48
00:09:02,000-->00:09:15,000
当我们演奏时,实际上就好比是在做握拳和松开的动作,
这两种都是可取的方法,充分的利用了指甲的边缘
87
00:18:54,000-->00:18:59,000
再强调一遍:尽可能多的使用指甲边缘
88
00:19:25,000-->00:19:40,000
从指甲左侧开始触弦,到右侧结束,
MASSAGING BREAST PUMP AND FUNNEL THEREFOR

地址:US,CH,US,,US,US 代理机构:LIPHARDT, Bernd 更多信息请下载全文后查看
专利内容由知识产权出版社提供
专利名称:MASSAGING BREAST PUMP AND FUNNEL T H EREFOR
发明人:JOHANSEN, Jean, Louise,MEYERS, Brenda, Jean,MENSCH, Alice, A.,MCCORMICK, Patrick, A.,SLAVEN, Mark, P.
申请号:EP2001011178 申请日:20010926 公开号:WO02/026290P1 公开日:200204 04
摘要:A breast pump funnel is disclosed. The funnel is shaped and dimensioned to fit a woman's breast, and has a neck to receive the nipple, a cup to fit over an inner part of the breast and a plurality of fingers extending outwardly from the cup to contact an outer part of the breast. The pump section of the brest pump is connected to the neck of the funnel to apply a varying suction to draw milk from the breast and to deliver the milk into a receiving vessel. The tips of the fingers of the funnel serve to massage the breast and stimulate the release of milk from the breast during pumping.
- 1、下载文档前请自行甄别文档内容的完整性,平台不提供额外的编辑、内容补充、找答案等附加服务。
- 2、"仅部分预览"的文档,不可在线预览部分如存在完整性等问题,可反馈申请退款(可完整预览的文档不适用该条件!)。
- 3、如文档侵犯您的权益,请联系客服反馈,我们会尽快为您处理(人工客服工作时间:9:00-18:30)。
该做的和不该做的
关于你的手
在专注于书里的技巧练习之前,让我们先打好基础。
有不少的演奏家,虽然使用一些别扭的动作、姿势和技术,但得到了奇妙的效果。
一般来说,他们的哲学是做一天和尚撞一天钟——得过且过。
我写这本书时一直都尽力避免死板地要求大家手如何放,怎样坐等等,但有些根本性的错误必须避免,一些基本事实也需要指出。
手必须保持一种既放松,又兴奋的状态;这意味着必须避免不必要的紧张,同时又得做好准备随时进行演奏,在完成弹奏后也要马上放松。
要做到这些,你的手需要尽可能地保持自然的姿势,同时须与弦保持一定角度。
为了以上目的,两手的手腕必须与手臂保持自然平直,但不能生硬。
下面的插图将说明这一点。
手腕顶部与手臂平直,注意不是手掌底部这里手腕太弯,影响了肌腱的自
如运动
尝试一下这样做:保持手腕弯曲,然后握拳。
感觉不舒服吧?为了使手指有效,舒适和长时间地工作,手的肌腱(就像电缆)必须可以很自由地在腕关节转动。
手腕处有许多小骨头通过,拳头弯得太厉害会增加肌腱的负担,甚至会造成无法补救的损伤!
下面的插图将说明这条原则同样适用于左手
手腕越平直,手越灵巧手弯得太厉害,使演奏十分困难
对左手拇指来说,较为明智的做法是放在中指的后面。
这有点像老虎钳,可以稳定均
匀地分布手的压力。
关于你的身体
你的身体同样需要保持在一个放松的状态。
当你坐下来后,尝试想象你的颈﹑脊椎延长到天花板,轻轻地把你的身体吊起来(刚好使你不会向前倒)。
然后放松全身肌肉,使身体好像固定在这个位置。
这样就把身体放在一个舒适的位置。
注意不要耸肩。
看看下图的持琴姿势。
持琴姿势----三角形
吉他与身体接触的三个点构成一个三角形
1 胸膛的下部(靠近胸骨)
2左大腿的上侧
3右大腿的内侧
当然,如果你用左手弹吉它的话就该反转方向。
当你的右手前臂放在吉他上时,这个三角形就稳定了。
这些都很基础,没错。
但它能使你在弹奏吉它时拥有最好的角度。
为了弹出美妙的音色,特别是在演奏会这样的场合,必须避免将吉他背板平贴在你的腹部,以免影响背板的正常振动,因为吉他这件乐器具有很强的方向性(对着音孔的方向音色最好)。
这个三角形还能使吉它的声音传得很远,因为它防止吉他向着地面。