精馏塔提留段温度单回路控制
精馏塔温度控制系统设计
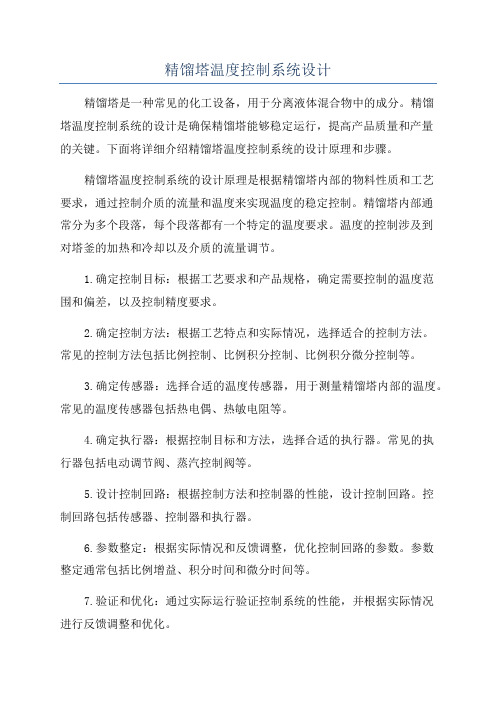
精馏塔温度控制系统设计精馏塔是一种常见的化工设备,用于分离液体混合物中的成分。
精馏塔温度控制系统的设计是确保精馏塔能够稳定运行,提高产品质量和产量的关键。
下面将详细介绍精馏塔温度控制系统的设计原理和步骤。
精馏塔温度控制系统的设计原理是根据精馏塔内部的物料性质和工艺要求,通过控制介质的流量和温度来实现温度的稳定控制。
精馏塔内部通常分为多个段落,每个段落都有一个特定的温度要求。
温度的控制涉及到对塔釜的加热和冷却以及介质的流量调节。
1.确定控制目标:根据工艺要求和产品规格,确定需要控制的温度范围和偏差,以及控制精度要求。
2.确定控制方法:根据工艺特点和实际情况,选择适合的控制方法。
常见的控制方法包括比例控制、比例积分控制、比例积分微分控制等。
3.确定传感器:选择合适的温度传感器,用于测量精馏塔内部的温度。
常见的温度传感器包括热电偶、热敏电阻等。
4.确定执行器:根据控制目标和方法,选择合适的执行器。
常见的执行器包括电动调节阀、蒸汽控制阀等。
5.设计控制回路:根据控制方法和控制器的性能,设计控制回路。
控制回路包括传感器、控制器和执行器。
6.参数整定:根据实际情况和反馈调整,优化控制回路的参数。
参数整定通常包括比例增益、积分时间和微分时间等。
7.验证和优化:通过实际运行验证控制系统的性能,并根据实际情况进行反馈调整和优化。
总之,精馏塔温度控制系统的设计是确保精馏塔能够稳定运行,提高产品质量和产量的关键。
设计步骤包括确定控制目标、控制方法、传感器和执行器的选择、设计控制回路、参数整定以及验证和优化。
合理的设计能够使温度控制更加稳定和可靠。
精馏塔塔釜温度控制系统

摘要在石油、轻工、化工等生产过程中,常常需要将原料、中间产物或粗产品中的组成部分进行分离,而精馏是最常用的方法。
精馏是石油、化工等众多生产过程中广泛应用的传质过程,通过精馏过程,使混合物料中的各组分分离,分别达到规定的纯度。
分离的机理是利用混合物中各组分的挥发度不同(沸点不同),使液相中的轻组分(低沸点)和汽相中的重组分(高沸点)相互转移,从而实现分离。
精馏装置由精馏塔、再沸器、冷凝冷却器、回流罐及回流泵等组成。
精馏塔是一个多输入多输出的多变量过程,内在机理较为复杂、动态响应迟缓、变量之间相互关联,不同的塔结构差别很大,而工艺对控制的要求又较高,所以确定精馏塔的控制方案是一个极为重要的课题。
我们此次设计就是要设计一个精馏塔温度的控制系统。
要求当物料进入精馏塔时,塔釜的温度可控并且温度恒定,保证生产的连续性。
关键词:精馏、多输入多输出、动态响应。
第1章绪论精馏塔是化工生产中分离互溶液体混合物的典型分离设备。
它是依据精馏原理对液体进行分离,即在一定压力下,利用互溶液体混合物各组分的沸点或饱和蒸汽压不同,使轻组份(即沸点较低或饱和蒸汽压较高的组分)汽化。
经多次部分液相汽化和部分气相冷凝,使气相中的轻组分和液相中的重组分浓度逐渐升高,也就是说在提馏段上升的轻组分的易挥发组分逐渐增多,难挥发组分逐渐减少,而下降液相中易挥发组分逐渐减少,难挥发组分逐渐增多,从而实现分离的目的,满足化工连续化生产的需要。
精馏塔塔釜温度控制的稳定与否直接决定了精馏塔的分离质量和分离效果,控制精馏塔的塔釜温度是保证产品高效分离,进一步得到高纯度产品的重要手段。
维持正常的塔釜温度,可以避免轻约分流失,提高物料的回收率;也可减少残余物料的污染作用。
影响精馏塔温度不稳定的因素主要是来自外界来的干扰(如进料流量,温度及成分等的变化对温度的影响)。
一般情况下精馏塔塔釜的温度,我们是通过控制精馏塔釜内灵敏板的温度来控制的。
灵敏板是当外界条件或负荷改变时精馏塔内温度变化最灵敏的一块塔板。
精馏塔的控制

精馏塔的控制12.1 概述•精馏是石油、化工等众多生产过程中广泛应用的一种传质过程,通过精馏过程,使混合物料中的各组分分离,分别达到规定的纯度。
•分离的机理是利用混合物中各组分的挥发度不同(沸点不同),使液相中的轻组分(低沸点)和汽相中的重组分(高沸点)相互转移,从而实现分离。
•精馏装置由精馏塔、再沸器、冷凝冷却器、回流罐及回流泵等组成。
精馏塔的特点精馏塔是一个多输入多输出的多变量过程,内在机理较复杂,动态响应迟缓、变量之间相互关联,不同的塔工艺结构差别很大,而工艺对控制提出的要求又较高,所以确定精馏塔的控制方案是一个极为重要的课题。
而且从能耗的角度,精馏塔是三传一反典型单元操作中能耗最大的设备。
一、精馏塔的基本关系(1)物料平衡关系总物料平衡: F=D+B (12-1) 轻组分平衡:F z f =D x D +B x B (12-2) 联立(12-1)、(12-2)可得:(2)能量平衡关系 在建立能量平衡关系时,首先要了解分离度的概念。
所谓分离度s 可用下式表示:DB D f D BB f D x x x z F D x x z D Fx --=+-=)((12-3))1()1(D B B Dx x x x s --=(12-5)可见,随着s 的增大,x D 也增大,x B 而减小,说明塔系统的分离效果增大。
影响分离度s 的因素很多,如平均相对挥发度、理论塔板数、塔板效率、进料组分、进料板位置,以及塔内上升蒸汽量V 和进料F 的比值等。
对于一个既定的塔来说:式(12-6)的函数关系也可用一近似式表示: 或可表示为:式中β为塔的特性因子由上式可以看到,随着V /F 的增加,s 值提高,也就是x D 增加,x B 下降,分离效果提高了。
由于V 是由再沸器施加热量来提高的,所以该式实际是表示塔的能量对产品成分的影响,故称为能量平衡关系式。
由上分析可见,V /F 的增加,塔的分离效果提高,能耗也将增加。
13精馏过程的控制详解

精馏塔质量指标的选取
• 想象上,产品从塔顶和塔底产出,因此塔顶或塔底的温 度最能代表产品质量。 • 其实,当分离的产品较纯时,在邻近塔顶或塔底的塔板 之间温度差已经很小。这时,塔顶或塔底温度变化 0.5℃,都可能已超出产品质量的允许范围。 • 这样选择测温点,对温度检测仪表的灵敏度和控制系统 的精度都提出了很高的要求。 • 解决这一问题的方法是选择灵敏塔板的温度作为间接质 量指标。 • 用精馏段与提馏段的灵敏板温度TR与TS近似反映塔顶、 塔底产品质量xD、xB的变化。 • 对于精密精馏塔,可用精馏段与提馏段的温差来反映塔 顶与塔底产品纯度的变化。 17
22
灵敏塔板的温度控制
• 当塔的操作受到扰动(或改变工况)时,塔内 各板的浓度都将发生变化,各塔板的温度、压 力也将同时变化。当保持压力恒定,浓度成为 温度的单值函数。 • 精馏塔从一个稳态达到新的稳态后,温度变化 最大的塔板称为灵敏塔板。 • 灵敏塔板位置的可以通过逐板计算或通过静态 模型仿真计算,依据不同操作工况下各塔板温 度分布曲线比较得出。但是,塔板效率不易估 准,所以最后还须根据实际情况,予以确定。 23
3
精馏过程与精馏塔的构造
精馏过程由精馏塔、再 沸器、冷凝器、塔顶产 品储罐(回流罐)等组 成。 精馏塔中有一系列的带 溢流孔的平板,称为塔 板。 精馏塔以进料口为分界, 分成两个塔段,进料口 以上称精馏段,进料口 以下称提馏段。
4
精馏塔的构造
• 精馏过程是根据不同物质(组分)有不同的汽化点 (冷凝点)温度,通过在每一塔板上(组分间)的不 断汽化和冷凝的热交换过程,从而将物质提纯的过程。 • 原料从进料口进入塔内,在塔内温度的作用下,一部 分液态物料被汽化上升,同时有另一部分汽态物料凝 聚而下降。 • 所有塔板都是汽液两相的传热传质过程,因此每一层 塔板的温度都可用集中参数模型描述。 • 每一层塔板成为精馏塔的一个段。尽管过程性质相同 (方程结构相同),但每层塔板模型的参数不同。
精馏塔温度-流量控制

目录 1 精馏塔控制系统介绍 ..................................................................................... 2 1.1 精馏塔原理 .......................................................................................... 2 1.2 控制要求及干扰因素 .......................................................................... 2 1.3工艺设计要求: ................................................................................... 3 2 控制方案的分析与论证 ................................................................................. 4 2.2 控制方案的设计 .................................................................................. 5 2.2.1方案选择——简单均匀控制 .................................................... 5 2.2.2 方案选择——串级控制 ........................................................... 6 3系统方框图,工艺流程简图及仪器仪表选型 .............................................. 8 3.1系统方框图 ........................................................................................... 8 3.2工艺流程图简介 ................................................................................... 9 3.3仪器仪表选型 ....................................................................................... 9 4 主体仪表设备的工艺说明及选型 ............................................................... 10 4.1控制器选择 ......................................................................................... 10 4.2本精馏塔选择正作用主副调节器 ..................................................... 10 4.3温度变送器的选择 ............................................................................. 12 4.4流量变送器选择 ................................................................................. 13 4.5电—气阀门定位器选择 ..................................................................... 15 4.6 执行器的选择 .................................................................................... 15 5 辅助仪器设备工艺说明与选型 ................................................................... 16 6设计结果概要或设计一览表 ........................................................................ 16 6.1控制算法概要 ..................................................................................... 16 7 总结 .............................................................................................................. 18 8参考文献........................................................................................................ 19 1 精馏塔控制系统介绍 1.1 精馏塔原理 精馏塔是进行精馏的一种塔式汽液接触装置,又称为蒸馏塔。有板式塔与填料塔两种主要类型。根据操作方式又可分为连续精馏塔与间歇精馏塔。 蒸汽由塔底进入,与下降液进行逆流接触,两相接触中,下降液中的易挥发(低沸点)组分不断地向蒸汽中转移,蒸汽中的难挥发(高沸点)组分不断地向下降液中转移,蒸汽愈接近塔顶,其易挥发组分浓度愈高,而下降液愈接近塔底,其难挥发组分则愈富集,达到组分分离的目的。由塔顶上升的蒸汽进入冷凝器,冷凝的液体的一部分作为回流液返回塔顶进入精馏塔中,其余的部分则作为馏出液取出。塔底流出的液体,其中的一部分送入再沸器,热蒸发后,蒸汽返回塔中,另一部分液体则作为釜残液取出。 蒸馏的基本原理是将液体混合物部分气化,利用其中各组份挥发度不同(相对挥发度)的特性,实现分离目的的单元操作。蒸馏按照其操作方法可分为:简单蒸馏、闪蒸、精馏和特殊精馏等。
精馏塔的控制要求

精馏塔的控制要求2.1 质量指标混合物分离的纯度是精馏塔控制的主要指标。
在精馏塔的正常操作中,产品质量指标就必须符合预定的要求,即保证在塔底或塔顶产品中至少有一种组分的纯度达到规定的要求,其他组分也应保持在规定的范围内,因此,应当取塔底或塔顶产品的纯度作为被控变量。
但是,在线实时监测产品纯度有一定的困难,因此,大多数情况下是用精馏塔内的“温度和压力”来间接反应产品纯度。
对于二元精馏塔,当塔压恒定时,温度与成分之间有一一对应的关系,因此,常用温度作为被控变量。
对于多元精馏塔,由于石油化工过程中精馏产品大多数是碳氢化合物的同系物,在一定的塔压下,温度与成分之间仍有较好的对应关系,误差较小。
因此,绝大多数精馏塔当塔压恒定时采用温度作为间接质量指标。
2.2 平稳操作为了保证精馏塔的平稳操作,首先必须尽可能克服进塔之前的主要可控扰动,同时缓和一些不可控的主要扰动,例如,对塔进料温度进行控制、进料量的均匀控制、加热剂和冷却剂的压力控制等。
此外,塔的进出物料必须维持平衡,即塔顶馏出物与塔底采出物之和应等于进料量,并且两个采出量的变化要缓慢,以保证塔的平稳操作。
另外,控制塔内的压力稳定,也是塔平衡操作的必要条件之一。
2.3 约束条件为了保证塔的正常、平稳操作,必须规定某些变量的约束条件。
例如,对塔内气体流速的限制,塔内气体流速过高易产生液泛,流速过低会降低塔板效率;再沸器的加热温差不能超过临界值的限制等。
3精馏塔的温度控制精馏塔控制最直接的质量指标是产品的组分,但产品组分分析周期长,滞后严重,因而温度参数成了最常用的控制指标,即通过灵敏板进行控制[3]。
3.1 精馏段温度控制精馏段温控灵敏板取在精馏段的某层塔板处,称为精馏段温控。
适用于对塔顶产品质量要求高或是气相进料的场合。
调节手段是根据灵敏板温度,适当调节回流比。
例如,灵敏板温度升高时,则反映塔顶产品组成XD下降,故此时发出信号适当增大回流比,使XD上升至合格值时,灵敏板温度降至规定值。
精馏塔的自动控制
2
1
2.保证平稳操作
第三节 精馏塔的自动控制
第三节 精馏塔的自动控制
为保证正常操作,需规定某些参数的极限值为约束条件。
第三节 精馏塔的自动控制
节能要求和经济性 在精馏操作中,质量指标、产品回收率和能量消耗均是要控制的目标。 其中质量指标是必要条件,在质量指标一定的前提下,应在控制过程中使产品产量尽量高一些,同时能量消耗尽可能低一些。
提馏段温控的主要特点与使用场合:
第三节 精馏塔的自动控制
2.精馏塔的精馏段温控
第三节 精馏塔的自动控制
以精馏段温度作为衡量产品质量的间接指标,而以改变回流量作为控制手段的方案,就称为精馏段温控。 图10-43 精馏段温控的控制方案示意图
采用了精馏段温度作为间接质量指标,因此它能较直接地反映精馏段的产品情况。当塔顶产品纯度要求比塔底严格时,一般宜采用精馏段温控方案。
为了保证塔的平稳操作,必须把进塔之前的主要可控干扰尽可能预先克服,同时尽可能缓和一些不可控的主要干扰。
为了维持塔的物料平衡,必须控制塔顶馏出液和釜底采出量,使其之和等于进料量,而且两个采出量变化要缓慢,以保证塔的平稳操作。
塔内的持液量应保持在规定的范围内。控制塔内压力稳定,对塔的平稳操作是十分必要的。
第三节 精馏塔的自动控制
一、工艺要求
1.保证质量指标
对于一个正常操作的精馏塔,一般应当使塔顶或塔底产品中的一个产品达到规定的纯度要求,另一个产品的成分亦应保持在规定的范围内。为此,应当取塔顶或塔底的产品质量作被控变量,这样的控制系统称为质量控制系统。 质量控制系统需要能测出产品成分的分析仪表。
第三节 精馏塔的自动控制
图10-44 ΔT-x曲线
温差与产品纯度之间并非单值关系。
课程设计题目2013
一、温度控制(单回路、串级、前馈—反馈、比值控制)(40)1、换热器出口温度单回路控制方案设计———————————————刘海强2、乳化物干燥器温度单回路控制方案设计———————————————胡炀3、精馏塔提馏段温度单回路控制方案设计——————————————朱隆奇4、管式加热炉出口温度单回路控制方案设计——————————————胡乔5、夹套式反应器温度单回路控制控制方案设计—————————————郭杰6、燃烧式工业窑炉温度单回路控制方案设计—————————————李旺旺7、精馏塔精馏段温度单回路控制方案设计———————————————白帅8、流化床反应器温度单回路控制方案设计———————————————赵杰9、管式热裂解反应器出口温度单回路控制方案设计———————————高强10、发酵罐温度单回路控制方案设计————————————————徐蓓阳11、换热器出口温度串级控制方案设计———————————————范浩麟12、乳化物干燥器温度串级控制方案设计13、精馏塔提馏段温度串级控制方案设计———————————————金晶14、管式加热炉出口温度串级控制方案设计—————————————蒋忠城15、夹套式反应器温度串级控制控制方案设计————————————刘原源16、燃烧式工业窑炉温度串级控制方案设计17、精馏塔精馏段温度串级控制方案设计——————————————郑小强18、流化床反应器温度串级控制方案设计———————————————王宁19、发酵罐温度串级控制方案设计——————————————————孙超20、管式热裂解反应器出口温度串级控制方案设计———————————秦涛21、换热器出口温度前馈—反馈控制方案设计————————————林康丛22、乳化物干燥器温度前馈—反馈控制方案设计———————————牛亚旭23、精馏塔提馏段温度前馈—反馈控制方案设计———————————刘学丽24、管式加热炉出口温度前馈—反馈控制方案设计——————————闫少华25、夹套式反应器温度前馈—反馈控制控制方案设计——————————卫伟26、燃烧式工业窑炉温度前馈—反馈控制方案设计———————————李帅27、精馏塔精馏段温度前馈—反馈控制方案设计———————————黎利鑫28、流化床反应器温度前馈—反馈控制方案设计29、发酵罐温度前馈—反馈控制方案设计——————————————聂日福30、管式热裂解反应器出口温度前馈—反馈控制方案设计———————陈朋印31、换热器出口温度比值控制方案设计———————————————燕子翔32、乳化物干燥器温度比值控制方案设计——————————————姜英季33、精馏塔提馏段温度比值控制方案设计——————————————田国胜34、管式加热炉出口温度比值控制方案设计35、夹套式反应器温度比值控制方案设计36、燃烧式工业窑炉温度比值控制方案设计37、精馏塔精馏段温度比值控制方案设计———————————————张锐38、流化床反应器温度比值控制方案设计39、发酵罐温度比值控制方案设计40、管式热裂解反应器原料油与蒸汽流量比值控制方案设计二、流量控制(9)1、离心泵流量单回路定值控制方案设计———————————————张华增2、离心泵流量串级定值控制方案设计3、离心泵流量前馈—反馈定值控制方案设计4、离心式压缩机气量单回路控制方案设计———————————————李通5、离心式压缩机气量串级控制方案设计6、离心式压缩机气量前馈—反馈控制方案设计7、压缩机防喘振控制方案设计———————————————————张瑾剑8、管式热裂解反应器原料油流量控制方案设计9、管式热裂解反应器蒸汽流量控制方案设计三、压力控制(7)1、锅炉出口蒸汽压力单回路控制方案设计———————————————张俊2、锅炉出口蒸汽压力串级控制方案设计———————————————陈永伟3、锅炉出口蒸汽压力前馈—反馈控制方案设计4、锅炉出口蒸汽压力比值控制方案设计5、炉膛负压单回路控制方案设计6、炉膛负压前馈—反馈控制方案设计7、离心泵压力定值控制方案设计———————————————————黄敬四、液位控制(7)1、锅炉汽包水位单回路控制方案设计2、锅炉汽包水位串级控制方案设计—————————————————白志刚3、锅炉汽包水位前馈—反馈控制方案设计——————————————王俊艳4、锅炉汽包水位比值控制控制方案设计5、单容液位控制方案设计——————————————————————刘畅6、双容液位单回路控制方案设计——————————————————武九义7、双容液位串级控制方案设计———————————————————陈天宇。
精馏塔的安全运行分析——精馏塔的温度控制实用版
YF-ED-J2159可按资料类型定义编号精馏塔的安全运行分析——精馏塔的温度控制实用版Management Of Personal, Equipment And Product Safety In Daily Work, So The Labor Process Can Be Carried Out Under Material Conditions And Work Order That Meet Safety Requirements.(示范文稿)二零XX年XX月XX日精馏塔的安全运行分析——精馏塔的温度控制实用版提示:该安全管理文档适合使用于日常工作中人身安全、设备和产品安全,以及交通运输安全等方面的管理,使劳动过程在符合安全要求的物质条件和工作秩序下进行,防止伤亡事故、设备事故及各种灾害的发生。
下载后可以对文件进行定制修改,请根据实际需要调整使用。
精馏塔通过灵敏板进行温度控制的方法大致有以下几种。
(1)精馏段温控灵敏板取在精馏段的某层塔板处,称为精馏段温控。
适用于对塔顶产品质量要求高或是气相进料的场合。
调节手段是根据灵敏板温度,适当调节回流比。
例如,灵敏板温度升高时,则反映塔顶产品组成zn下降,故此时发出信号适当增大回流比,使XD上升至合格值时,灵敏板温度降至规定值。
(2)提馏段温控灵敏板取在提馏段的某层塔板处,称为提馏段温控。
适用于对塔底产品要求高的场合或是液相进料时,其采用的调节手段是根据灵敏板温度,适当调节再沸器加热量。
例如,当灵敏板温度下降时,则反映釜底液相组成Xw变大,釜底产品不合格,故发出信号适当增大再沸器的加热量,使釜温上升,以便保持工w的规定值。
(3)温差控制当原料液中各组成的沸点相近,而对产品的纯度要求又较高时不宜采用一般的温控方法,而应采用温差控制方法。
温差控制是根据两板的温度变化总是比单一板上的温度变化范围要相对大得多的原理来设计的,采用此法易于保证产品纯度,又利于仪表的选择和使用。
精馏塔的原理及控制要求
精馏塔的原理及控制要求一、精馏原理精馏是化工生产中分离互溶液体混合物的典型单元操作,其实质是多级蒸馏,即在一定压力下,利用互溶液体混合物各组分的沸点或饱和蒸汽压不同,使轻组分(沸点较低或饱和蒸汽压较高的组分)汽化,经多次部分液相汽化和部分气相冷凝,使气相中的轻组分和液相中的重组分浓度逐渐升高,从而实现分离。
精馏过程的主要设备有:精馏塔、再沸器、冷凝器、回流罐和输送设备等。
精馏塔以进料板为界,上部为精馏段,下部为提馏段。
一定温度和压力的料液进入精馏塔后,轻组分在精馏段逐渐浓缩,离开塔顶后全部冷凝进入回流罐,一部分作为塔顶产品(也叫馏出液),另一部分被送入塔内作为回流液。
回流液的目的是补充塔板上的轻组分,使塔板上的液体组成保持稳定,保证精馏操作连续稳定地进行。
而重组分在提留段中浓缩后,一部分作为塔釜产品(也叫残液),一部分则经再沸器加热后送回塔中,为精馏操作提供一定量连续上升的蒸气气流。
精馏塔从结构上分,有板式塔和填料塔两大类。
而板式塔根据塔结构不同,又有泡罩塔、浮阀塔、筛板塔、穿流板塔、浮喷塔、浮舌塔等等。
各种塔板的改进趋势是提高设备的生产能力,简化结构,降低造价,同时提高分离效率。
填科塔是另一类传质设备,它的主要特点是结构简单,易用耐蚀材料制作,阻力小等,一般适用于直径小的塔。
在实际生产过程中,精馏操作可分为间歇精馏和连续精馏两种。
对石油化工等大型生产过程,主要是采用连续精馏。
精馏塔是一个多输入多输出的多变量过程,内在机理较复杂,动态响应迟缓缓,变量之间相互关联,不同的塔工艺结构差别很大,而工艺对控制提出的要求又较高,所以确定精馏塔的控制方案是一个极为重要的课题。
而且从能耗的角度来看,精馏塔是三传一反典型单元操作中能耗最大的设备,因此,精馏塔的节能控制也是十分重要的。
二、精馏塔的主要干扰因素精馏塔的主要干扰因素为进料状态,即进料流量F、进料组分zf ,进料温度Tf或热焓FE.此外,冷剂与加热剂的压力和温度及环境温度等因素也会影响精馏塔的平衡操作。
- 1、下载文档前请自行甄别文档内容的完整性,平台不提供额外的编辑、内容补充、找答案等附加服务。
- 2、"仅部分预览"的文档,不可在线预览部分如存在完整性等问题,可反馈申请退款(可完整预览的文档不适用该条件!)。
- 3、如文档侵犯您的权益,请联系客服反馈,我们会尽快为您处理(人工客服工作时间:9:00-18:30)。
精馏原理以及工业流程 精馏操作分为连续精馏和间歇精馏,本设计的研究对象是连续精馏的过程。连续精馏的流程装置如下图所示,其操作过程是:原料液经预热加热到一定温度后,进入精馏塔中的进料板,料液在进料板上与自塔上部下降的回流液体汇合后,在逐板下流,最后流入塔底再沸器中,液体在逐板下降的同时,它与上升的蒸汽在每层塔板上相互接触,同时进行部分汽化和部分冷凝的质量和能量的传递过程。操作时,连续从再沸器中取出的部分液体作为塔底产品,部分液体汽化产生上升蒸汽,从塔底回流入塔内出塔顶蒸汽进入冷凝器中被冷凝成液体,并将部分冷凝液用泵送回塔顶作为回流液体,其余部分经冷却器后被送出作为塔顶产品。
图连续精馏装置工艺流程图 精馏塔的特性 精馏塔的特性分为静态特性和动态特性,以二元简单精馏过程为例,说明精馏塔的基本关系。 1.2.1精馏塔的静态特性 一个精馏塔,进料与出料应保持物料平衡,即总物料量以及任一组分都符合物料平衡关系。图所示的精馏过程,其物料平衡关系为: 总物料平衡 BDF ()
轻组分平衡 BDfxBxDzF () 由式()和()联立可得: BBfDxxzDFx)( BDfDxxzxFD () 式中 F、D、B——分别为进料、顶馏出液和底馏出液流量; fz、Dx、Bx——分别为进料、顶馏出液和底馏出液中轻组分含量。 从上述关系可看出:当FD增加时将引起顶、底馏出液中轻组分含量减少,即Dx、Bx下降。而当FB
增加时将引起顶、底馏出液中轻组分含量增加。即Dx、Bx上升。 然而,在FD(或FB)一定,且fz一定的条件下并不能完全确定Dx、Bx的数值,只能确定Dx与B
x
之间的比例关系,也就是一个方程只能确定一个未知数。要确定Dx与Bx两个因数,必须建立另一个关系式:能量平衡关系。 在建立能量平衡关系时,首先要了解一个分离度的概念。所谓分离度s可用下式表示:
)1()1(DBBDxxxxs
() 从上
式可见:随着分离度s的增大,而Bx减小,说明塔系统的分离效果增大。影响分离度s的因素很多,诸如平均挥发度、理论塔板数、塔板效率、进料组分、进料板位置以及塔内上升蒸汽量V和进料量F的比值等。对于一个既定的塔来说:
)(FVfs () 式()的函数关系也可用一近似式表示:
FVIn)1()1(DBBDxxxx () 式中为塔的特性因子。 由式()、()可以看出,随着FV增加,s值提高。也就是Dx增加,Bx下降,分离效果提高了。由于V是由再沸器施加热量来提高的,所以该式实际是表示塔的能量对产品成分的影响,故称为能量平衡关系式。而且由上述分析可见:FV的增大,塔的分离效果提高,能耗也将增加。 对于一个既定的塔,包括进料组分一定,只要FD/和FV一定,这个它的分离结果,即Dx与Bx将被完成确定。也就是说,由一个塔的物料平衡关系与能量平衡关系两个方程式,可以确定塔顶和塔底组分两个待定因数。
上述结论与一般工艺书中所说保持回流比DLR一定,就确定了分离结果是一致的。 精馏塔的各种扰动因素都是通过物料平衡和能量平衡的形式来影响塔的操作。因此,弄清精馏塔中的物料平衡和能量平衡关系,为确定合理的控制方案奠定了基础。 1.2.2 精馏塔的动态特性 精馏塔是一个多变量、时变、非线性对象。对其动态特性的研究,人们已经做了不少工作。要建立整塔的动态方程,首先要对精馏塔的各部分:精馏段、提留段各塔板,进料板,塔顶冷凝器,回流罐,塔釜、
再沸器等分别建立各自得动态方程。下面以二元精馏塔第j块塔板为例说明如何建立单板动态方程。 总物料平衡:
dtdMVVLLjjjjj11
()
轻组分平衡:
dtxMdyVyVxLxLjjjjjjjjjj][1111 ()
式中:L表示回流量,下标指回流液来自哪块板; V表示上升蒸汽量,下标指来自哪一块板的上升蒸汽;
M指液相的蓄存量;
yx、分别指液相和气相中轻组分的含量,同样下标指回流液及上升蒸汽来自哪块塔板。
由于各部分的动态方程。可整理得到整塔的动态方程组。对于整个精馏塔来说是一个多容量的,相互交叉连接的复杂过程,要整理出整塔的传递函数是相当复杂的。
第2章 控制系统设计 单回路系统简介 1.单回路控制系统的结构和类型 反馈控制是基于被控量的偏差进行的,没有偏差也就不存在反馈控制。当然只要存在偏差,控制系统就不可能保持在理想控制要求上,而是在理想控制要求的附近摆动,所以反馈控制是接近理想要求,但永远也无法保持理想要求的控制。当被控对象呈现大延迟或受干扰较多,干扰频率较高时,要求系统快速反应实现控制目的时,反馈控制的效果往往不明显。
图单回路控
制系统方框图 本次课程设计我要完成精馏塔提留段温度单回路控制系统设计,单回路控制系统又称简单控制系统,是指由一个控制对象、一个检测元件及变送器、一个调节器和一个执行器所构成的闭合系统。单回路控制系统结构简单、易于分析设计,投资少、便于施工,并能满足一般生产过程的控制要求,因此在生产中得到广泛应用 2.单回路控制系统的特点 1、它由一个测量变送装置、一个控制器、一个控制阀和相应的被控对象所组成。 2、控制器是根据被控变量与给定值的偏差来进行控制的。 3、系统结构简单,所需自动化技术工具少(仪表少),投资比较低,操作维护也比较方便,3.前馈-反馈控制系统 精馏塔提留段温度控制系统设计方案 提馏段温度控制系统采用串级控制方案,该控制系统的被控对象是D308塔灵敏板的温度。由于对灵敏板的温度指标要求严格,而其影响干扰又很多,而干扰的存在会直接影响产品的质量,这里的主要干扰是进料流量,它存在容量滞后较大、负荷变化较剧烈、干扰比较频繁的问题。考虑到经济等方面的问题,采用单回路控制。 1.精馏塔提馏段被控变量的选择 被控变量的选择是控制系统设计的核心问题,选择得正确与否,会直接关系到生产的稳定操作,产品产量和质量的提高以及生产安全与劳动条件的改善等。这里对于以温度为操作指标的生产过程,就选择温度作为被控变量,因为温度具有足够大的灵敏度反映产品质量的变化。此外,选择温度作为被控变量时,考虑到了工艺的合理性和国内外仪表生产的现状。 当被控变量选定之后,下一步就要考虑选择哪个参数作为操纵变量,去克服干扰对被控变量的影响。 2.提馏段温度控制系统温度检测点选择 通常,若希望保持塔顶产品质量符合要求,也就是顶部馏出物为主要产品时,应把间接反映质量的温度检测点放在塔顶,构成所谓精馏段温度控制系统。同样,为了保证塔底产品符合质量要求,温度检测点则应放在塔底,实施提馏段温度控制系统。本设计中采用的就是后者。 采用塔底温度作为间接质量指标时,实际上把温度检测点放置在塔底是极少数的。因为在分离比较纯的产品时,邻近塔两端的各板之间温差是很小的,这时塔底的温度出现稍许变化,产品质量就可能超出允许的范围,因而必须要求温度检测装置有很高的精度与灵敏度,才能满足控制系统的要求。这一点实现起来有较大的难度。所以,在实际使用中是把温度检测点放在进料板与塔底之间的灵敏板上。 所谓灵敏板,是当塔受到干扰或控制作用时,塔内各板的组分都将发生变化,随之各塔板的温度也将发生变化,当达到新的稳态时,温度变化最大的那块塔板即称为灵敏板。 灵敏板的位置可以通过逐板计算,经比较后得出,但是,由于塔板的效率不易估准,所以还需结合实践结果加以确定。通常,先根据测算,确定灵敏板的大致位置,然后在它附近设置多个检测点,根据实际运行中的情况,从中选择最佳的测量点作为灵敏板。 3.精馏塔提馏段温度单回路控制系统设计
图精馏塔提馏段单回路温度控制方案 4.精馏塔提馏段温度单回路控制系统设计 反馈控制系统的被控对象选择精馏塔提馏段温度灵敏板,控制变量选择精馏塔精馏段灵敏板温度,操作变量选择塔顶回流的流量,通过控制蒸汽阀开度,最终实现对精馏塔提馏段温度的控制。
加热 蒸汽 θC1 进料 θ 再沸器
塔底部 第3章 硬件选型 控制器选择 在实际工业生产应用中,调节器是构成自动控制系统的核心仪表,它将来自变送器的测量信号VI与调节器的内给定或外给定信号VS进行比较,得到其偏差e,有e=VI-VS ,然后调节器对该偏差信号按某一规律进行运算,输出调节信号控制执行机构的动作,以实现对被控变量如温度、液位、压力和流量等的自动控制作用。 调节器的分类方法很多,按使用的能源来分,有气动调节器和电动调节器;按结构形式分有基地式调节器、单元组合调节器和组装式调节器。单元组合调节器有气动单元组合调节器和电动单元组合调节器。共有I型、II型和III型调节器。由于DDZ-III型调节器性能优越,易于与计算机联用。因此,本设计的调节器选择使用PID算法的DDZ-III型调节器。
图 DDZ—Ⅲ型电动调节器DTZ—2100接线端子图 执行器的选型 执行器在控制系统中的作用是接受来自控制器的控制信号,通过其本身开度的变化,从而达到控制流量的目的。 精馏塔的回流控制阀应在故障时全开来保证全回流,所以选择气关阀。 本系统采用电/气阀门定位器与气动执行机构配套使用来控制阀门开度。 如图2-6所示
① ② ③ ④ ⑤ ⑥ ⑦ ⑧ ⑨ ⑩ ○11 ○12 ○13 ○14 ○15 ○16 ○17 ○18 ○19 ○20 + 测量信号 1~5VDC - + 外给定信号4~20mA -
输出4~20mA RL 地 + - 电源24VDC