FMEA解析总结报告总结.doc
fmea分析
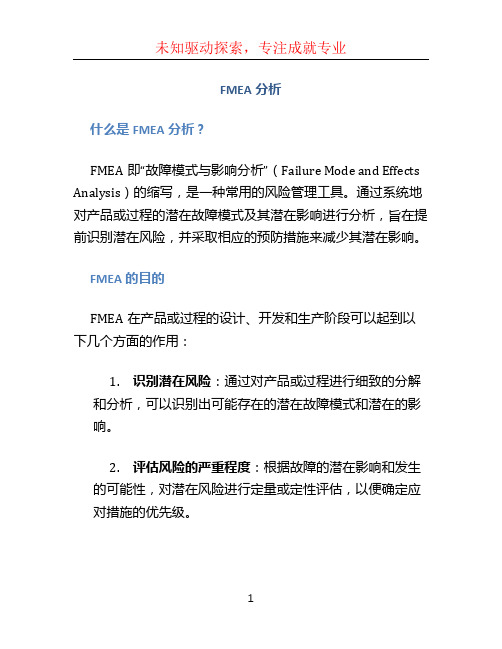
FMEA分析什么是FMEA分析?FMEA即“故障模式与影响分析”(Failure Mode and Effects Analysis)的缩写,是一种常用的风险管理工具。
通过系统地对产品或过程的潜在故障模式及其潜在影响进行分析,旨在提前识别潜在风险,并采取相应的预防措施来减少其潜在影响。
FMEA的目的FMEA在产品或过程的设计、开发和生产阶段可以起到以下几个方面的作用:1.识别潜在风险:通过对产品或过程进行细致的分解和分析,可以识别出可能存在的潜在故障模式和潜在的影响。
2.评估风险的严重程度:根据故障的潜在影响和发生的可能性,对潜在风险进行定量或定性评估,以便确定应对措施的优先级。
3.确定风险控制措施:基于评估的风险严重程度,制定相应的风险控制计划,包括预防措施、检测措施和修正措施,以减少故障发生的可能性和减轻其影响。
4.提高产品和过程可靠性:通过对潜在故障模式和影响的深入分析,可以发现设计或工艺上的问题,并提出相应的改进措施,以提高产品和过程的可靠性。
FMEA的应用步骤FMEA分析一般由以下步骤组成:1.确定FMEA的范围和对象:明确FMEA的应用范围,确定要分析的产品或过程,以及需要参与FMEA分析的团队成员和相关专家。
2.创建FMEA分析表:根据产品或过程的特征和结构,创建FMEA分析表,包括列出可能出现的故障模式、故障后果、故障发生的可能性、目前的控制措施等信息。
3.评估故障的潜在影响和可能性:对每个故障模式进行评估,确定故障的潜在影响和发生的可能性,并进行定量或定性的风险评估。
4.制定风险控制措施:根据风险评估的结果,确定相应的风险控制措施,包括预防措施、检测措施和修正措施,以减少故障的潜在影响和发生的可能性。
5.实施风险控制措施:根据制定的措施,执行相应的行动计划,包括改进设计、制定工艺规范、加强检测和监控等。
6.监控和更新FMEA分析:定期监控和评估已实施的风险控制措施的效果,及时更新FMEA分析表,以反馈和改进措施。
FMEA分析报告

FMEA分析报告FMEA(Failure Mode and Effects Analysis)是一种系统性的风险评估方法,常用于分析产品或过程中的潜在问题和可能的影响。
这篇报告将介绍FMEA分析的目的,步骤和优势,并通过一个实例进行详细说明。
一、FMEA分析的目的二、FMEA分析的步骤1.确定分析的范围:明确需要分析的产品或过程的范围和目标。
2.收集团队:组建一个多学科的团队,包括设计人员、工程师、生产人员等。
3.识别潜在的故障模式:对产品或过程进行详细审查,识别可能出现的故障模式。
4.评估故障的严重程度:分析每个故障模式可能引发的后果,评估其对产品性能和安全性的影响。
5.评估故障发生的可能性:分析每个故障模式发生的概率或频率,并将其与已有的统计数据或历史记录进行比较。
6.评估故障的检测能力:评估现有的探测和防范措施对于检测和防止故障的效果。
7.计算风险优先级:根据故障的严重程度、发生可能性和检测能力计算每个故障模式的风险优先级,确定应优先处理的故障模式。
8.制定改进措施:根据风险优先级,制定相应的改进措施,减少或消除故障的可能性和后果。
9.实施改进措施:将改进措施应用到产品设计或过程中,确保其有效性和可持续性。
10.监控和追踪效果:通过定期监测和追踪,评估改进措施的效果和持续性,并根据需要进行调整和改进。
三、FMEA分析的优势1.预测潜在问题:通过系统性的分析,FMEA能够预测产品或过程中可能出现的问题,并提前采取措施避免或降低潜在的风险。
2.提高产品质量:通过识别并改进潜在问题,FMEA能够改善产品的质量和可靠性,提高顾客满意度。
3.降低故障率和维修成本:通过消除或减少故障的可能性,FMEA能够降低产品或过程的故障率和维修成本。
4.加强团队协作:FMEA需要一个多学科的团队进行分析和讨论,促进了团队成员之间的协作和沟通。
5.持续改进:FMEA是一个持续改进的过程,通过监测和追踪改进措施的效果,不断优化和改进产品或过程。
产品设计fmea报告

产品设计fmea报告一、概述本报告旨在对产品设计过程中的潜在风险进行分析和评估,以指导设计团队制定相应的风险控制措施。
通过采用FMEA(Failure Mode and Effects Analysis)方法,我们对产品设计中可能出现的失效模式、失效影响和失效严重程度进行了详细研究,以及风险优先级的排序和风险控制建议的提出。
本报告旨在为产品设计团队提供有力依据,促进产品设计过程的高质量和安全性。
二、FMEA分析过程2.1 分析团队本次FMEA分析由产品设计团队成员组成的跨职能小组进行。
小组成员包括设计工程师、品质控制专家和生产工艺专家。
2.2 分析范围本次FMEA分析的范围涵盖了产品设计阶段的所有活动,包括需求分析、概念设计、详细设计和设计验证。
2.3 FMEA工具我们采用了FMEA表格进行分析,表格的内容包括失效模式、失效影响、失效严重程度(S)、发生概率(O)、探测能力(D)、风险优先级(RPN)和风险控制建议。
2.4 分析方法我们按照以下步骤进行FMEA分析:1. 识别失效模式:团队成员通过头脑风暴和借鉴类似产品的经验来识别可能的失效模式。
2. 评估失效影响:团队成员评估每个失效模式对产品性能、客户满意度和安全性等方面的影响。
3. 评估失效严重程度(S):根据失效影响的严重程度,我们对每个失效模式进行了权重评分。
4. 评估发生概率(O):团队成员根据经验和数据,评估每个失效模式的发生概率。
5. 评估探测能力(D):团队成员评估探测到失效模式的概率,并考虑到各种测试和检查方法的可靠性。
6. 计算风险优先级(RPN):根据S、O和D的评估结果,计算每个失效模式的RPN值。
7. 提出风险控制建议:根据RPN值和团队的专业知识,提出相应的风险控制建议。
2.5 分析结果经过团队的共同努力,我们完成了FMEA分析,并得到了以下结果:失效模式失效影响S O D RPN 风险控制建议模块失效导致整个产品无法工作产品无法正常工作10 5 8 400 设计冗余措施,提高模块可靠性设计尺寸偏差超出允许范围产品无法装配或安装8 6 9 432设计合理的公差,严格控制生产过程产品设计不符合安全标准安全隐患,可能导致事故发生9 4 7 252 与安全专家合作,确保产品符合相关安全标准... ... ... ... ... ... ...三、风险控制建议基于上述FMEA分析结果,我们提出了以下风险控制建议:1. 设计冗余措施:在产品设计中引入冗余,通过多个模块的备份实现高可靠性,即使一个模块失效,其他模块仍然能继续工作。
FMEA分析报告

微小
在源头探测问题
探测失效模式当场-操作员目视/触觉/听声方法,或
过程后-用计数型量具(go/no-go,手动扭力扳手等)
7
很小
在过程后探测问题
探测失效模式,过程后-操作员用计量值量具;或
当场-操作员用计数型量具(go/no-go,手动扭力扳手等)
6
小
在源头探测问题
探测失效模式,当场-操作员用计量值量具;或
潜在失效模式和效应分析(FMEA)
系统设计过程
系统 / 子系统 / 零部件 /项目名称:
责任者:
编号:者:
核心小组:
FMEA日期(制定)
修订
项目/
过程
步骤/
功能
要求
潜在
失效
模式
潜在
失效
后果
严
重
度
S
分类
失效
原因
现行系统/
设计/过程
控制
預防
频
度
O
现行系统/
设计/过程
十分低:不太可能
1
失效可用预防控制消除
探测度(Detection)
探测机会
准则:
以探测为过程控制的可能性
级别
探测
可能性
没有探测的机会
没有现行过程控制;无法探测或没有分析
10
几乎不可能
几乎在任何阶段都不能探测
失效模式或错误(原因)不容易探测(例:随机审核)
9
很微小
在过程后探测问题
探测失效模式,过程后-操作员目视/触觉/听声方法
8
主要功能丧失或降级
主要功能降级(项目不能运行,但不影响项目安全运行)
7
主要功能降级(项目能运行,表现水平下降)
失效模式分析(FMEA)心得报告

失效模式分析(FMEA)心得報告----報告人紀志龍一、FMEA導入的步驟:1.研究PROCESS/PRODUCT2.BRAINSTORM可能失效模3.列出每一失效模式潛在結果4.Assign嚴重度分數5.鑑定每一失效模式之原因6.Assign發生度分數7.鑑定目前偵測失效模式8.Assign難檢度分數9.計算RPN(先其風險評估)10.決定失效模式優先順序11.採取矯正行動12.重新計算RPN二、FMEA製作時機1.原型樣品前2.試產前3.產品製程變異4.製程不穩定/或能力不足三、FEMA用途1.是一種分析技術2.認明產品設計或製程上可能不良模式3.評估缺點對客戶的可能影響4.認明缺點對客戶的可能影響5.認明產生該不良模式之可能原因6.認明有關之重要製程變數7.研訂改善措施8.建立預防管制方法四、FMEA表格(上課實習內容、主要針對加油站的設立所產生的FEMA並加以預防)※R PN直愈大表示潛在風險愈高,第10項計畫之後也是回歸到矯正行動,一直到RPN 值降到最低為止。
五、結論課程中談到我們可以透過RPN、製定行動方案、降低失效模式;但QS-9000認證系統可能停止運作,改由ISO/TS 16949替代,目前是台積電最早申請通過,未來所有汔車零件相關產業都會要求通過此認證,因此他們也建議若要申請QS-9000系統倒不如直接申請ISO/TS 16949,因為ISO/TS 16949是由QS-9000(APQP、SPC、MSA、PPAP、FMEA、QSA)加上生產者特定要求及歐洲VDA-VOLUMES所組成,其內容較QS-9000更完整更詳細,也由於FEMA 太深還有許多地方不能詳盡敘述,可能須導入試RUN才能了解,未來公司也不排除申請ISO/TS 169469 ,若要實際導入建議須有專案專責負責人才行。
--完畢。
fmea心得

fmea心得FMEA (失效模式和影响分析)是一种被广泛应用于产品设计和过程优化的工具。
通过识别潜在的系统故障模式和评估它们对整体系统性能的影响,FMEA帮助我们预防和减轻潜在的风险。
在我参与的某个项目中,我们成功地应用了FMEA方法来改善产品性能和可靠性。
在这篇文章中,我将分享我对FMEA的心得体会。
首先,FMEA的核心思想是通过识别和评估潜在故障模式,预测并防止系统或过程的故障。
我们团队首先对待改进的系统进行了全面分析,识别出可能发生的故障模式。
我们将故障模式分为失效原因、失效模式和失效效应三个方面,以全面了解并评估故障风险。
例如,在我们的项目中,我们针对一种新型的电池分析了故障模式,包括电池短路、电池漏液等。
通过识别这些潜在的故障模式,我们能够有针对性地采取措施来减轻故障风险。
其次,FMEA的一个重要步骤是评估失效模式对系统性能的影响。
我们使用了一套标准化的评分系统来对失效模式进行评估,从而确定各个失效模式的优先级。
我们将失效影响的严重性、发生频率和检测能力作为评估指标,并进行评分。
例如,在我们的电池项目中,我们将漏液事件的严重性评为高级,因为它可能对用户的健康和安全造成严重危害。
通过这种评估,我们可以重点关注那些对系统性能影响最严重的失效模式,以及降低它们的发生概率。
另外,FMEA也要求制定相应的控制措施来预防和减轻潜在的故障。
在我们的项目中,我们采取了一系列的预防措施来降低电池漏液的风险。
例如,我们改进了电池的密封性,增强了电池外壳的耐腐蚀性能。
我们还加强了生产线上的检测环节,确保任何可能造成漏液的电池都能被及时发现和淘汰。
通过这些措施,我们成功地减轻了电池漏液的风险,提高了产品的可靠性。
FMEA的应用使我们的项目取得了显著的效果。
首先,通过识别和评估潜在的故障模式,我们能够及时发现并修复系统中的潜在问题,从而避免了潜在的成本和时间浪费。
其次,通过加强预防措施,我们在生产阶段能够减少故障率,提升了产品的质量和客户满意度。
FMEA 学习心得及报告

FMEA 学习心得及报告fmea学习报告及心得一、fmea学习报告:●fmea可分为dfmea,pmfea等等●fmea实施的必要条件:需要管理者的支持与监督.因为fmea实施是一个多方讨论的活动并要大量时间与资源。
设计可分为产品设计与过程设计,fmea都关注这两设计,它是一组系统化的活动,fmea目的:①发现和评价产品与过程(制造过程,装配过程)潜在的功能失效及其可能发生的后果;②寻找消除和减少潜在的功能失效发生的机会;③将整个子系统(定议顾客的产品为系统)设计过程与设计过程文件化,满足系统过程的补充;●dfmea是一种分析技术,是一个分析小组(不是个人)是要在设计的先期阶段发生的,在产品图纸发放之前完成,最终作为产品的评审标准.如整个产品开发各个阶段如有变更时要及时修改.导致产品失效的基本因素:①内部系统/子系统/零件间相互干涉;②内部系统/子系统/零件与环境相互作用;③使用一段时间后零部件的磨损;④制造差异;⑤顾客使用;●dfmea的作用:①识别潜在或现存的功能失郊模式并评估影响的严重等级;②帮助识别功能失效模式,并基于失效后果严重度的排序,优先关注严重高的失效模式;③帮助识别功能失效的机制和原因;●dfmea前的输入:在准备dfmea之前需要收集表述设计意图的文件:①顾客要求-------qfd(质量功能展开);②整个产品要求,将顾客感性的描述转化为技术指标,确认设计要求;③已知的产品要求;④制造、装配、服务和回收再利用的要求;●dfmea输出;①设计验证计划(dvp);②列出潜在的关键特性和重要特性;③列出“预防设计错误”与“探测设计错误”的设计控制,其中预防是一种方法,探测是一个动作;●dfmea规则:(重要)①dfmea时要假设所有零部件能够按照图纸和规范制造出来的。
着重在设计过程的控制。
②dfmea只考虑设计和材料规范有关的问题。
制造过程相关问题或材料错误通常在pfmea中考虑,如零部件来料不良不是dfmea考虑的.③非常关键的是,所选定系统的每个部件必须被彻底分析。
产品制程FMEA分析总结报告
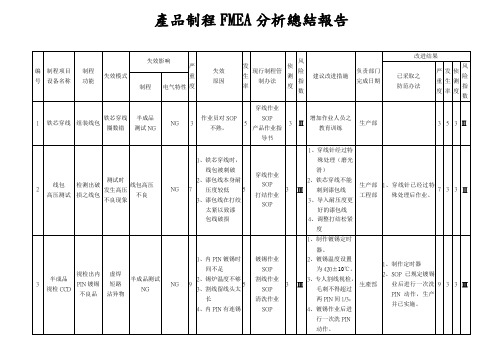
分析总结﹕
结论:
1.线包高压管控重点在于穿线针作业前需打磨处理;
2.内PIN虚焊因浸锡时间不够,导入定时器可有效管制时间;
3.内PIN短路为毛刺过长浸锡后造成相邻端子连锡,组立后导入CCD视检可有效检验毛刺;
4.外PIN端子歪斜因浸锡后产品直接放置清洗篮,超声波振动造成端子碰撞,将清洗篮更为
平放清洗治具可有效改善此问题;
5.外PIN镀锡不良为作业员镀锡手法不当所致,纠正作业员镀锡手法可有效改善此问题;
6.成品高壓因外PIN浸锡与锡面高度未管控导致漆包线被烫伤,导入限位治具、锡面管控可有效改善此问题.
產品制程FMEA 分析總結報告
風險優先係數:RPN (Risk Priority Number)名詞定義:(在客戶收到產品前,目前流程檢測出失效的能力) →(影響的)嚴重度:對客戶需求所造成之影響的重重要性[1=不嚴重~ 10=非常嚴重] →(原因的)發生度:特定原因發生並產生失效模式的頻率[1=不常發生~10=時常發生] →(現行管制能力)偵測度:現行管制計劃的偵測力[1=可偵測出來~10=不能偵測出來] ※等級尺度應由小組決定
※ 風險優先係數評點法:
→排列RPN 的優先順序,對最優先問題採取適當的措施. →RPN=(嚴重度*發生率*偵測度)1/3
C 1 : 影響機能故障的嚴重程度(嚴重度) C 2 : 故障發生的頻度(發生率)
C 3 : 故障發生檢測的難易度(偵測度) Cs : 故障評點
Cs = ( C 1˙C 2˙C 3 )1/3
表1. C 1的評價點 表2. C 2的評價點 表3. C 3的評價點 表4. C S 與故障等級之關
校准: 审核: 制定: 时间:。
- 1、下载文档前请自行甄别文档内容的完整性,平台不提供额外的编辑、内容补充、找答案等附加服务。
- 2、"仅部分预览"的文档,不可在线预览部分如存在完整性等问题,可反馈申请退款(可完整预览的文档不适用该条件!)。
- 3、如文档侵犯您的权益,请联系客服反馈,我们会尽快为您处理(人工客服工作时间:9:00-18:30)。
精品文档
潜在失效模式和效应分析
(FMEA)
系统
设计
过程
系统 /
子系统 / 零部件 / 项目名称:
责任者 : 编号:
生效日期:
页码: 第
页 / 共
页 型号 / 类型: 编制者:
核心小组:
FMEA 日期 ( 制定 )
修订
项目 /
严
现行系统 /
现行系统 / 探 风险
负责 措施执行结果
潜在
潜在
严 探 过程
重 分 失效 频
设计 / 过程 测 优先
建议 和
要求
失效 失效 设计 / 过程
采取的 重 频
步骤 / 度 类 原因
度
控制 度 数 措施
目标完成 测 R
模式
后果
控制 措施 度
度 功能
S
O
探测
D
RPN
日期
度 P
預防
S O
D N
严重度( Severity )
级别后果影响产品的严重度(客户影响)
10不能符合安全和 /潜在失效模式影响项目运行和/或涉及违反政府法规-没有警告
9 或法规要求潜在失效模式影响项目安全运行和 /或涉及违反政府法规- 带有警告8 主要功能丧失或主要功能降级(项目不能运行,但不影响项目安全运行)
7 降级
主要功能降级(项目能运行,表现水平下降)
6次级功能丧失或次级功能降级(项目能运行,但舒适/方便性的功能不运行)
5 降级
次级功能降级(项目能运行,但舒适 /方便性的功能表现水平下降)
4 烦恼外观或能听到的噪音,项目能运行,不符合,大部分客户都能察觉(大于75% )3 外观或能听到的噪音,项目能运行,不符合,很多顾客能察觉(50% )
2 外观或能听到的噪音,项目能运行,不符合,敏感顾客能察觉(小于25% )
1 没有影响未有可识别影响
频度( Occurrence )
后果级别准则:原因的发生
十分高 :持续失效10 ≥100 件 / 每 1000 件1: 10
9 50 件 / 每 1000 件1: 20
高:经常失效8 20 件 / 每 1000 件1: 50
7 10 件 / 每 1000 件1: 100
6 2 件 / 每 1000 件1: 500
中等:偶然失效 5 0.5 件 / 每 1000 件1: 2,000
4 0.1 件 / 每 1000 件1: 10,000
3 0.01 件 / 每 1000 件1: 100,000
低:很少失效
2 ≤ 0.001件 / 每 1000 件1:1,000,000 十分低:不太可能 1 失效可用预防控制消除
探测度( Detection)
探测机会准则:级探测
以探测为过程控制的可能性别可能性
没有探测的机会没有现行过程控制;无法探测或没有分析10 几乎不可
能
几乎在任何阶段都失效模式或错误(原因)不容易探测(例:随机审核)9 很微小不能探测
在过程后探测问题探测失效模式,过程后- 操作员目视 /触觉 /听声方法8 微小
在源头探测问题探测失效模式当场 - 操作员目视 /触觉 /听声方法,或7 很小
过程后- 用计数型量具( go/no-go ,手动扭力扳手等)
在过程后探测问题探测失效模式,过程后- 操作员用计量值量具;或 6 小
当场 - 操作员用计数型量具( go/no-go ,手动扭力扳手等)
在源头探测问题探测失效模式,当场 - 操作员用计量值量具;或 5 中等或错误 (原因 ) 自动控制探测缺陷零件或通知操作员(光、蜂鸣器等)
执行作业前准备和首件测定检查(只适用作业前准备的原因)
在过程后探测问题探测失效模式,过程后 - 自动控制探测缺陷零件和自动扣留零件以防止进入下工序 4 中上
在源头探测问题探测失效模式,当场 - 自动控制探测缺陷零件和自动扣留零件以防止进入下工序 3 高
错误探测和 /或问探测错误 (原因 ),当场 - 自动控制探测错误和防止产生缺陷零件 2 很高
题预防
防止错误;不采用防止错误 (原因 ),夹具、机器或零件设计1几乎肯定探测过程 /产品设计了防错法,不会产生缺陷零件。