布局及生产线设计
工厂管理中的生产线设计与布局
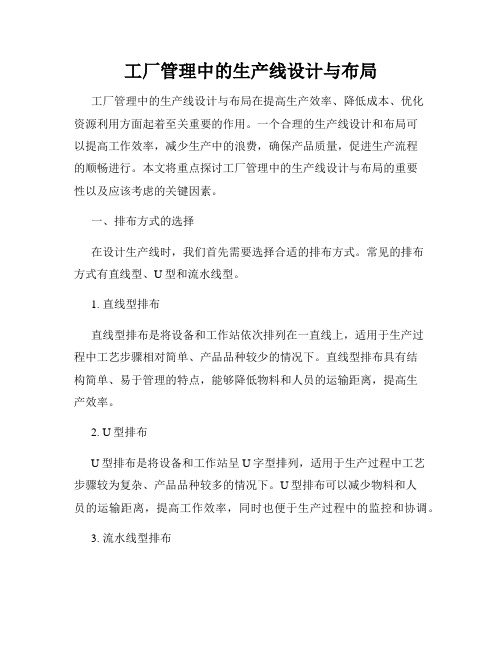
工厂管理中的生产线设计与布局工厂管理中的生产线设计与布局在提高生产效率、降低成本、优化资源利用方面起着至关重要的作用。
一个合理的生产线设计和布局可以提高工作效率,减少生产中的浪费,确保产品质量,促进生产流程的顺畅进行。
本文将重点探讨工厂管理中的生产线设计与布局的重要性以及应该考虑的关键因素。
一、排布方式的选择在设计生产线时,我们首先需要选择合适的排布方式。
常见的排布方式有直线型、U型和流水线型。
1. 直线型排布直线型排布是将设备和工作站依次排列在一直线上,适用于生产过程中工艺步骤相对简单、产品品种较少的情况下。
直线型排布具有结构简单、易于管理的特点,能够降低物料和人员的运输距离,提高生产效率。
2. U型排布U型排布是将设备和工作站呈U字型排列,适用于生产过程中工艺步骤较为复杂、产品品种较多的情况下。
U型排布可以减少物料和人员的运输距离,提高工作效率,同时也便于生产过程中的监控和协调。
3. 流水线型排布流水线型排布是将设备和工作站依次连接形成一条流水线,适用于大规模、高速、重复性生产的情况下。
流水线型排布能够最大程度地减少物料和人员运输距离,提高生产效率,但也需要注意流程的平衡性和产品的稳定性。
二、工作站布局的优化在确定排布方式后,我们需要对各个工作站的布局进行优化。
1. 工作站的顺序根据生产流程的要求和产品的特点,合理确定工作站的顺序。
需要将工作站之间的流程连接起来,确保物料的顺畅流转,并且减少生产中的等待时间。
同时,还应考虑到人员在操作过程中的便利性和安全性。
2. 工作站之间的距离工作站之间的距离应根据实际情况进行合理的确定。
如果工作站之间的距离过远,会增加物料运输的时间和成本,降低生产效率;而如果距离过近,可能会导致工作站之间的干扰和交叉污染。
因此,需要在降低运输成本和提高工作效率之间找到一个平衡点。
3. 工作站的标识和布局为了使员工能够清晰地辨认和操作,每个工作站应当配备相应的标识和说明。
生产线布局(超详细)
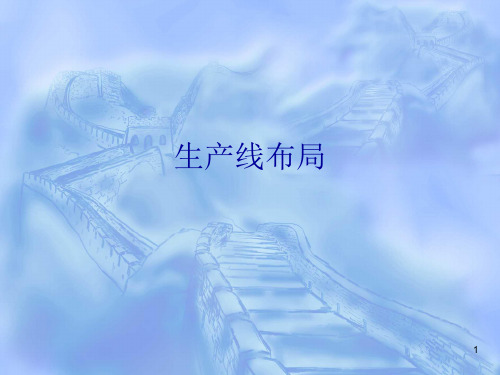
= 0.007 分钟/产品
换句话说,每分钟生产140单位的产品。
1/30/2019 40
产品原则布局
4.进行作业活动分配(作业活动分配到各工作站) 5.向工作站分配作业(作业活动在工作站内分配) 6.评估装配线平衡后的效率 E=T/(Na × Ct)
E——装配线平衡效率 T——完成作业所需的时间总量 Na——实际工作站数 Ct——生产节拍
就生产而言E是怎样的 数值较好?
7.如果不理想,重复第4步骤
1/30/2019 41
产品原则布局
作业 时间(S) 45 11 描述 安装后轮支架,拧紧四个螺 母 插入后轴 作业前提条件 —— A
案例 一玩具厂的玩具 车在流水线上 作业,每天需 生产500辆, 每天生产时间 为420分钟, 生产步骤及时 间如左表:
3 铸造 4 缝纫
5 小型玩具 转配线 6 大型玩具 转配线
7 喷漆 8 机械装配 线
20
工艺原则布局
次数
车 间 之 间 的 流 动 表
1/30/2019
1 1 2 3 4 5 6 7 8
2 3 175 50 0
4 0 100 17
5 30 75 88 20
6 200 90 125 5 0
7 20 80 99 0 180 347
6σ=?
4
6σ标准
PPM等于 多少?
σ
PPM 308,537 66,807 6,210 233 3.4
缺陷减少5倍
2 3 4 5 6
缺陷减少11倍
缺陷减少26倍
缺陷减少68倍
5
鉴别七大浪费
一、生产产生的不良引起的浪费
任何产品的不良都是浪费的一个主要来源。
车间布局与机加生产线

作台和自动换刀装置,能完成工件多方位、多面、多工序得 加工,以减少工件得安装次数,减少安装定位误差。主要用于 中小批量生产,加工各种形状复杂、精度要求高得工件,特别 就是能迅速灵活地加工出符合市场需要得一定范围内得产品, 但建立这种生产线投资大,技术要求高。
❖ 在生产线中,工件以一定得生产节拍,按照工艺顺序经过各个工 位,完成其预定得工艺过程,从而成为合乎设计要求得零件。
按生产品种分类
• 1)单一产品生产线 由具有一定自动化程度得高效专用加工装备、工艺装
置、输送装备和辅助装备等组成。 按产品得工艺流程布局,工件沿固定得生产路线从一台
设备输送到下一台设备,接受加工、检验、清洗等。 生产效率高,产品质量稳定,适用于大批大量生产。但
夹具沿斜下方返回得方案时,返回通道设置在卧式机床得 尾部,这种布局适用于尺寸较小得工件和随行夹具。
• 在受到车间面积或排 屑要求得限制时,或 由于有立式机床而不 能采用水平返回、正 上方返回、正下方返 回等方案时,可考虑 采用随行夹具沿生产 线斜上方或斜下方返 回得布局型式。
用架空机械手输送工件时生产线得布局
其专用性强,投资大,不易进行改造以适应其她产品得生产。
按生产品种分类
• 2)成组产品可调生产线 由按成组技术设计制造得可调得专用加工装备等组成。 按成组工艺流程布局,具有较高得生产效率和自动化程
度,用于结构和工艺相似得成组产品得生产。 适用于批量生产,当产品更新时,生产线可进行改造或
重组以适应产品得变化。
工件直接输送时生产线得布局
➢ (3) 旁通式 优点就是可以配置三面或立卧复合得四面加工机床,以提
生产线布局(超详细)_图文
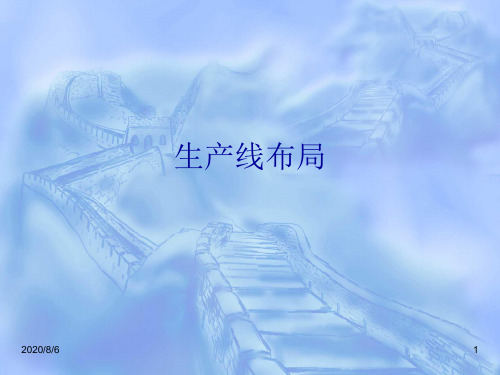
工艺原则布局
权重代码 密切程度
A
绝对必要
E
特别重要
I
重要
O
普通的
U
不重要的
X
不予考虑的
2020/8/6
线代号
29
工艺原则布局
▪ 医院相关图
1
3
5
2
4
6
2020/8/6
30
工艺原则布局
▪ 医院总体合理布局图
1
4
65
2
3
2020/8/6
31
工艺原则布局
▪ 布局方法 设部门或工艺有n个
布局方案=n!
▪ 使用范围:
• 批量小 • 体积大
▪ 布局特点
• 以产品为中心 • 不考虑物流成本和复杂程度
2020/8/6
18
工艺原则布局
▪ 定义:
• 将相似的设备或功能集中放在一起的布局方式 • 也称车间布局,如车床车间
▪ 使用范围
• 生产设备密集型 • 设备专业性 • 自动化程度高 • 资本密集型 • 产品重量轻
2020/8/6
次数
1 1 2 3 4 5 6 7 8
23 175 50
0
45 0 30 100 75 17 88
20
678 200 20 25 90 80 90 125 99 180 5 0 25 0 180 187
347 103 7
21
▪ 玩具厂各车间年物流成本示意图
2020/8/6
22
工艺原则布局
1. 采用了看板管理,拉动生产方式 2. 车间布局U型布局; 3. 不同类型的机器摆放在一块; 4. 实现了单件流的生产; 5. 机器小型化 ; 6. 工序中间很少甚至没有库存; 7. 实现了作业标准化; 8. 对工人实行了多技能培训; 9. 具有完善的作业改善活动制度
生产管理制度中的产能规划与生产线布局

生产管理制度中的产能规划与生产线布局在现代工业生产中,高效的产能规划和合理的生产线布局是企业能否保持竞争力和持续发展的关键因素之一。
产能规划是指根据市场需求和企业资源状况,制定合理的生产计划,确保企业能够按时交付产品,并且最大化地利用资源。
而生产线布局则是指如何合理地安排生产线的位置和各个工位之间的关系,以提高生产效率和降低成本。
本文将从产能规划和生产线布局两个方面来探讨生产管理制度中的重要性。
一、产能规划产能规划是企业在生产管理中的重要环节,它直接关系到企业能否按时交付产品,以及如何最大化地利用资源。
合理的产能规划可以帮助企业提高生产效率,降低生产成本,提高产品质量,增强竞争力。
首先,产能规划需要根据市场需求来确定生产计划。
企业应该根据市场需求的变化情况,合理地制定生产计划。
如果市场需求突然增加,企业应该及时调整生产计划,增加产能,以满足市场需求。
相反,如果市场需求下降,企业应该适当减少产能,避免库存积压和资源浪费。
其次,产能规划需要充分考虑企业的资源状况。
企业在制定生产计划时,必须考虑到自身的资源状况,包括人力资源、物料资源、设备资源等。
只有合理地利用这些资源,才能够实现高效的生产。
例如,如果企业的设备资源有限,那么在制定生产计划时就应该考虑到设备的利用率,避免出现设备闲置或者过载的情况。
最后,产能规划需要与供应链管理相结合。
在现代企业中,供应链管理是非常重要的一环。
企业应该与供应商和分销商保持紧密的合作关系,共同制定产能规划。
只有通过与供应链的有效协作,企业才能够实现供需的平衡,避免出现供应链中的瓶颈和断点,确保产品能够按时交付。
二、生产线布局生产线布局是指如何合理地安排生产线的位置和各个工位之间的关系,以提高生产效率和降低成本。
一个合理的生产线布局可以提高生产效率,减少物料和人力的运输成本,降低生产周期,增加产品质量。
首先,生产线布局需要考虑到生产流程的连贯性。
在设计生产线布局时,应该将生产流程的各个环节合理地连接起来,避免出现生产过程中的等待和堵塞。
高效生产线布局设计与优化策略

高效生产线布局设计与优化策略在当今竞争激烈的市场环境中,企业要想提高生产效率、降低成本、提升产品质量,高效的生产线布局设计与优化至关重要。
一个合理的生产线布局能够减少物料搬运、缩短生产周期、提高设备利用率,从而为企业带来显著的经济效益。
一、生产线布局设计的基本原则1、流程导向原则生产线的布局应按照产品的生产流程进行设计,使生产过程中的各个工序能够顺畅地衔接,减少不必要的迂回和倒流。
这样可以减少物料搬运的距离和时间,提高生产效率。
2、空间利用原则在设计生产线布局时,要充分考虑厂房的空间大小和形状,合理利用空间。
避免出现空间浪费或者设备布局过于拥挤的情况,以确保生产操作的便利性和安全性。
3、灵活性原则市场需求和产品种类可能会发生变化,生产线布局应具有一定的灵活性,能够方便地进行调整和改造,以适应新的生产任务和工艺要求。
4、人机工程学原则要考虑操作人员的工作环境和操作习惯,使设备的高度、操作界面的位置等符合人机工程学的要求,减轻操作人员的劳动强度,提高工作效率和舒适度。
二、生产线布局的常见类型1、直线型布局这是最简单的一种布局方式,产品按照直线顺序依次经过各个工序。
直线型布局的优点是流程清晰、易于管理,缺点是空间利用率较低,当生产工序较多时,生产线会变得很长。
2、 U 型布局U 型布局将生产线弯曲成 U 字形,操作人员可以在 U 型的内部进行操作,减少了物料搬运的距离和时间。
U 型布局具有空间利用率高、生产效率高的优点,但对操作人员的技能要求较高。
3、环形布局环形布局将生产线围成一个环形,产品在环形轨道上流动,各个工序依次进行加工。
环形布局适用于生产批量较大、工序较少的产品,但设备投资较大,维护成本较高。
4、单元式布局将生产线按照产品或工艺的特点分成若干个单元,每个单元独立完成一部分生产任务。
单元式布局具有灵活性高、适应多品种小批量生产的优点,但管理难度较大。
三、生产线布局设计的步骤1、产品和工艺分析首先要对产品的结构、性能、生产工艺等进行详细的分析,确定生产过程中的各个工序和操作要求。
生产线的布局规划与设计
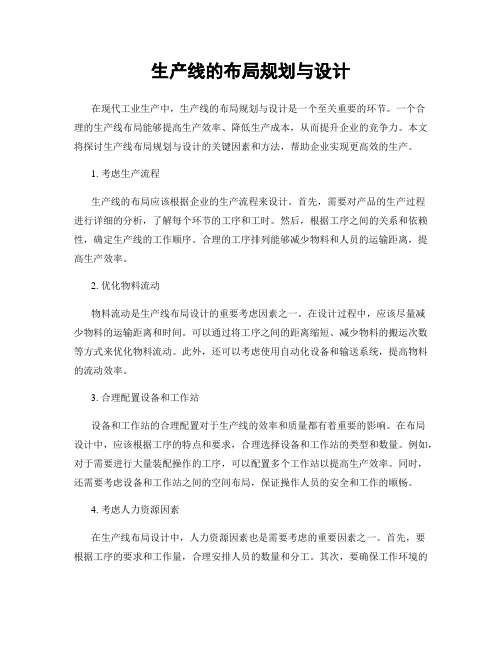
生产线的布局规划与设计在现代工业生产中,生产线的布局规划与设计是一个至关重要的环节。
一个合理的生产线布局能够提高生产效率、降低生产成本,从而提升企业的竞争力。
本文将探讨生产线布局规划与设计的关键因素和方法,帮助企业实现更高效的生产。
1. 考虑生产流程生产线的布局应该根据企业的生产流程来设计。
首先,需要对产品的生产过程进行详细的分析,了解每个环节的工序和工时。
然后,根据工序之间的关系和依赖性,确定生产线的工作顺序。
合理的工序排列能够减少物料和人员的运输距离,提高生产效率。
2. 优化物料流动物料流动是生产线布局设计的重要考虑因素之一。
在设计过程中,应该尽量减少物料的运输距离和时间。
可以通过将工序之间的距离缩短、减少物料的搬运次数等方式来优化物料流动。
此外,还可以考虑使用自动化设备和输送系统,提高物料的流动效率。
3. 合理配置设备和工作站设备和工作站的合理配置对于生产线的效率和质量都有着重要的影响。
在布局设计中,应该根据工序的特点和要求,合理选择设备和工作站的类型和数量。
例如,对于需要进行大量装配操作的工序,可以配置多个工作站以提高生产效率。
同时,还需要考虑设备和工作站之间的空间布局,保证操作人员的安全和工作的顺畅。
4. 考虑人力资源因素在生产线布局设计中,人力资源因素也是需要考虑的重要因素之一。
首先,要根据工序的要求和工作量,合理安排人员的数量和分工。
其次,要确保工作环境的舒适和安全,为操作人员提供良好的工作条件。
此外,还可以考虑使用人机协作的方式,将一些重复性和繁琐的工作交给自动化设备完成,提高工作效率和质量。
5. 不断优化改进生产线的布局规划与设计并非一成不变,随着企业的发展和生产需求的变化,需要不断进行优化和改进。
定期评估生产线的效率和质量,并根据评估结果进行相应的调整和改进。
此外,还可以借鉴其他企业的经验和成功案例,学习他们的布局设计思路和方法,进一步提升自己的生产线效能。
总结生产线的布局规划与设计是一个综合性的任务,需要考虑多个因素的综合影响。
精益物流-生产线设计与布局
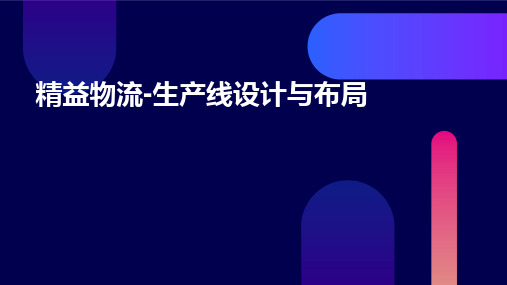
绿色环保的生产线设计与布局
环保材料
选用环保、可再生材料,降低生产过程中的环境 污染。
节能减排
优化生产线设计和工艺流程,降低能源消耗和排 放污染物。
废弃物回收与处理
建立废弃物回收和处理系统,实现生产废弃物的 减量化、资源化和无害化处理。
高柔性生产线设计与布局
模块化设计
采用模块化设计理念,使生产线能够快速适应不同产品、不同生 产批量的需求。
详细描述
产品-作业单位法首先对产品的特点和工艺 要求进行分析,然后根据这些信息将生产线 划分为不同的作业单位。每个作业单位负责 完成特定的生产任务,以提高生产效率。这 种方法有利于提高生产的灵活性和适应性。
作业分析法
总结词
作业分析法是对生产线上的各项作业进行分 析,了解作业的特性和需求,以提高生产效 率。
02
生产线设计与布局的重要性
提高生产效率
优化生产线布局
通过合理安排设备和工位的位置,减少物料搬运距离,降低操作 时间,提高生产效率。
标准化操作
制定标准化的操作流程和作业指导书,确保员工能够快速、准确地 完成工作,减少生产过程中的停顿和等待时间。
引入自动化和智能化设备
采用自动化和智能化设备可以大幅提高生产效率,减少人工干预和 操作时间。
可重构性
提高生产线的可重构性,便于生产线在产品升级换代时的快速调 整和优化。
Hale Waihona Puke 高度集成与协同实现生产线各环节的高度集成与协同,提高生产线的整体运行效 率和灵活性。
THANK YOU
详细描述
整体性原则要求在生产线设计与布局时,要全面考虑生产流程的各个环节,确保 设备、人员、物料等资源的合理配置和高效利用。这包括对生产线的整体产能、 生产节拍、工艺流程等进行优化,以提高生产效率和产品质量。
- 1、下载文档前请自行甄别文档内容的完整性,平台不提供额外的编辑、内容补充、找答案等附加服务。
- 2、"仅部分预览"的文档,不可在线预览部分如存在完整性等问题,可反馈申请退款(可完整预览的文档不适用该条件!)。
- 3、如文档侵犯您的权益,请联系客服反馈,我们会尽快为您处理(人工客服工作时间:9:00-18:30)。
节拍时间 =
(1) 可用生产时间 (2) 客户需求
举例
时间
休息 清洗 需求
(1) 不包括规定的停工的总时间, (2) 在规定时间内所需生产的部件数量
2 x 8 h (480 min)
20 分钟 / 班 10 分钟 / 班 10.000 件/周
2 x (480-20-10) 节拍时间 = 10.000 / 5
= 0,45 min = 27 sec /unit
少人化及多能工
• 2名操作员工的单元线
6
1
2345
7
8
1B 2B 3B
• 3名操作员工的单元线
6
1
2
3
4
5
7
8
•单元生产线设计
–操作员在统一区域进行作业 –操作员采用非孤岛式作业 –设备输入及输出位置紧邻 –自动作业与手工作业分开
•多技能员工
–督导负责培训多技能操作员工 –督导必须非常熟悉(JI)
I.1.布局及生产线设计
I. 生产流动
5. 低成本自动化 4. 快速切换 3. 标准作业 2. 线边物料
1.工厂布局和生
产线设计
• 介绍; • PQ分析; • 流程图及时间估算; • 功能布局 vs. 流程布局及生产线数量; • 单件流生产线; • 节拍时间; • 少人化(SHOJINKA)及多技能工; • 线平衡;生产线; • 工位设计;
• 空箱出口(第二层)
• 5S管理
Waste Bin
Waste Hole
工作指导培训 –运用培训计划及作业分解表培
训操作员
1B 2B 3B
Time (sec)
生产线平衡
不平衡遍布所有生产线 = 操作员压力 = 不平衡
生产线节拍=操作员平均节拍
A
B
操作员1
CA
B
CA
B
C
操作员2
操作员3
不平衡集中型工位
生产线节拍=操作员节拍
Time (sec)
A
B
C
操员1
Std WS
A
B
C
操作员2
"MURA" WS
A
B
C
操作员3
Std WS
Std WS
Std WS
Std WS
Std WS
Std WS
工作站设计
• 由于容器位置不合理造成许多操 作员的动作浪费;
• 无固定位置用于安放容器 • 容器不适用于前端供应 • 5S薄弱
• 所有部件应放置在操作员触手 可及的位置
• 小型容器及可以前端供应的两 箱系统
案例分析 Antares
视频 OSLV GK Work
OSLV
介绍
• 区分流程及作业非常重要 • 流程是将物料从一点流到另一点的物流,
其中包括许多作业。 • 物料运输; • 物料批次等待; • 物料转化; • 物料检查;
• 作业就是操作员工执行以上流程的活动; • 布局及生产线设计目标
• 消除无附加值的作业 • 创建具有附加值的单件流
功能型 vs 流程型布局
功能型布局
Functional Layout Big Batch Production
Sub子As组sem装bly 线
Asse组mb装ly
W A R E H
U S E
检Con验trol
Work in 在待制Pr品oc等essWaiting
功能型 vs 流程型布局
生产线布局 小批量生产
仓库
子组装线
组装
检验
物流
单件流生产线
单元布局 单件流生产
包装 物料流
检验
子组装
组装
Supermarket
单件流生产线
改善前(直通率/效率低)
改善后(直通率/效率高)
Transport distance = 28 m
节拍时间
• 生产周期时间应遵循节拍时间, 如,与需求周期相对应; • 通常生产线设计周期时间小于节拍时间(由于效率损失)
Q: 数量
(3 ref)
P.Q. 分析
A1
A2 (10)
• 3 种 = 年销售额45%的产品 • 10 种 = 年销售额35%的产品 • 15 种 = 年销售额15%的产品 • 120 种 = 年销售额5%的产品
B (15)
C (120)
P: 产品种类
• 布局及生产线设计先从PQ 分析开始 • A类(大量)适宜于半自动的生产线(保持单件流) • B类适宜于手动,自动化程度较低的生产线 • C类(低速)适宜于单工作站 / 手工生产线,可灵活运用