生产线设计与布局
自动化设备中的生产线布局与规划

自动化设备中的生产线布局与规划随着科技的不断进步和工业的发展,自动化设备在生产过程中的应用越来越普遍,生产线布局和规划成为了企业提高生产效率、降低成本的重要环节。
在本文中,我们将探讨自动化设备中的生产线布局与规划,以及如何优化生产线以提高效率和质量。
一、生产线布局的重要性生产线布局是指将各个工序以最佳的方式安排在一条生产线上,形成高效、流畅的生产流程。
一个良好的生产线布局可以提高生产效率、降低人力和物力资源的浪费,从而降低生产成本,提高企业竞争力。
良好的生产线布局应遵循以下原则:1. 空间合理利用:生产线的布局应根据企业的生产规模和产品特点,合理安排各个工序的空间位置,确保生产设备之间的距离适当,防止出现拥堵或运输路径过长等问题。
2. 流程优化:生产线布局应考虑产品生产工艺的流程,合理安排工序的顺序,最大程度地减少从一道工序到下一道工序之间的等待和转移时间,提高生产效率。
3. 人员安全:生产线布局应考虑员工的人身安全,合理安排工序之间的安全通道,确保员工在操作设备时的安全性。
二、生产线规划的关键因素生产线规划是在生产线布局的基础上,进一步考虑生产能力、产量、周期、质量控制等因素,制定出具体的生产计划和控制措施。
1. 生产能力:生产能力是指生产线在单位时间内完成产品的数量,规划生产线时要充分考虑生产能力的提升和合理分配,以满足市场需求。
2. 产量与周期:根据市场需求和产品特性,制定生产线的产量和生产周期,确保生产线在规定的时间内能够完成所需产量,避免产能过剩或供需失衡的情况。
3. 质量控制:生产线规划中应考虑质量控制的环节和方法,确保生产线上的每个工序都符合质量标准,避免产品质量问题给企业带来损失。
三、生产线优化方法优化生产线是提高生产效益的关键步骤,下面介绍几种常见的生产线优化方法:1. 价值流分析:通过对生产线上的价值流进行分析,找出不必要的等待、传输和浪费环节,并进行改进,以优化生产线流程。
工厂管理中的生产线设计与布局
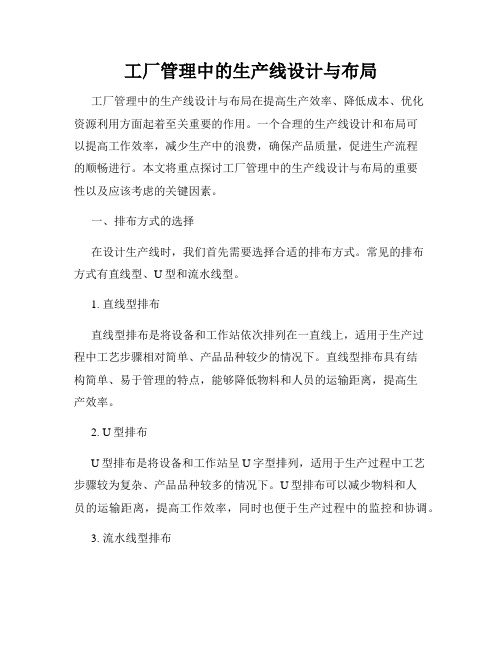
工厂管理中的生产线设计与布局工厂管理中的生产线设计与布局在提高生产效率、降低成本、优化资源利用方面起着至关重要的作用。
一个合理的生产线设计和布局可以提高工作效率,减少生产中的浪费,确保产品质量,促进生产流程的顺畅进行。
本文将重点探讨工厂管理中的生产线设计与布局的重要性以及应该考虑的关键因素。
一、排布方式的选择在设计生产线时,我们首先需要选择合适的排布方式。
常见的排布方式有直线型、U型和流水线型。
1. 直线型排布直线型排布是将设备和工作站依次排列在一直线上,适用于生产过程中工艺步骤相对简单、产品品种较少的情况下。
直线型排布具有结构简单、易于管理的特点,能够降低物料和人员的运输距离,提高生产效率。
2. U型排布U型排布是将设备和工作站呈U字型排列,适用于生产过程中工艺步骤较为复杂、产品品种较多的情况下。
U型排布可以减少物料和人员的运输距离,提高工作效率,同时也便于生产过程中的监控和协调。
3. 流水线型排布流水线型排布是将设备和工作站依次连接形成一条流水线,适用于大规模、高速、重复性生产的情况下。
流水线型排布能够最大程度地减少物料和人员运输距离,提高生产效率,但也需要注意流程的平衡性和产品的稳定性。
二、工作站布局的优化在确定排布方式后,我们需要对各个工作站的布局进行优化。
1. 工作站的顺序根据生产流程的要求和产品的特点,合理确定工作站的顺序。
需要将工作站之间的流程连接起来,确保物料的顺畅流转,并且减少生产中的等待时间。
同时,还应考虑到人员在操作过程中的便利性和安全性。
2. 工作站之间的距离工作站之间的距离应根据实际情况进行合理的确定。
如果工作站之间的距离过远,会增加物料运输的时间和成本,降低生产效率;而如果距离过近,可能会导致工作站之间的干扰和交叉污染。
因此,需要在降低运输成本和提高工作效率之间找到一个平衡点。
3. 工作站的标识和布局为了使员工能够清晰地辨认和操作,每个工作站应当配备相应的标识和说明。
自动化生产线的设计与布局

自动化生产线的设计与布局随着科技的不断进步和发展,自动化生产线在现代工业中扮演着越来越重要的角色。
自动化生产线的设计和布局是确保生产线的高效运转和产能的关键因素之一。
本文将对自动化生产线的设计与布局进行详细探讨。
自动化生产线的设计需要考虑以下几个方面:生产工艺流程、生产线的功能和要求、生产线的产能以及人机协作等因素。
在生产工艺流程方面,设计者需要了解产品的生产工艺流程,并根据这些工艺流程确定生产线的各个工作站的位置和顺序。
在考虑生产线的功能和要求时,设计者需要考虑生产线所需的机器人数量和类型,以及机器人之间的协作方式。
生产线的产能决定了生产线的设计规模和能力,需要根据产品的预计市场需求来确定。
设计者还需要考虑人机协作,即如何保证操作员与机器人的合理协调和互动,提高生产线的效率和安全性。
自动化生产线的布局也是十分重要的。
一个合理的布局可以最大限度地提高生产线的效率和产能。
在布局上,设计者需要考虑以下几个因素:物料流动、能源消耗、设备维护和人员安全等。
物料流动是生产线上最主要的流动,设计者需要确保物料流动的路径最短且顺畅,以减少生产线上的等待和拥堵。
设计者还需要考虑如何合理利用能源,尽量减少能源的浪费。
设备维护也是一个重要的因素,设计者应该为每个设备留下足够的空间,以便维护和维修。
人员安全是至关重要的,设计者需要合理安排人员工作区域,并设置必要的安全设施,保证操作员的安全。
在自动化生产线的设计和布局中,还需要考虑到工艺变化和灵活性。
由于产品和市场需求的变化,生产线的工艺可能需要不断调整和改变。
因此,设计者需要考虑生产线的灵活性,确保能够迅速适应新的工艺要求。
这意味着要在设计和布局上做到足够的灵活性和可调整性,以便在需要调整工艺时能够快速作出相应的改变。
自动化生产线的设计和布局还需要考虑到工作环境的人性化。
一个舒适、安全的工作环境对员工的效率和士气起着重要的作用。
因此,设计者需要考虑工作站的布局和操作员的工作条件,提供舒适的工作环境和符合人体工程学的工作站设计。
工厂生产线的布局与优化

工厂生产线的布局与优化工厂生产线的布局和优化是制造业中非常重要的一环。
一个合理的生产线布局可以提高工厂的生产效率,降低生产成本,提高产品质量,增加竞争力。
在本文中,我们将重点探讨工厂生产线布局与优化的相关问题,并提出一些应对方案。
一、工厂生产线布局的原则在进行工厂生产线布局时,我们应该遵循以下原则:1. 流程简化:生产线应该遵循产品制造的流程,确保产品在不同工序之间的流转顺畅,避免产生瓶颈。
2. 资源合理利用:将设备、工人和材料适当地配置在不同工序中,确保利用率最大化,减少资源的浪费。
3. 人性化设计:生产线应该为工人提供一个舒适、安全的工作环境,减少工人的体力劳动强度,提高工作效率和工作质量。
二、工厂生产线布局的具体方案1. 直线布局:直线布局是最常见的布局方式之一,适用于产品生产过程中工序数量较少的情况。
产品从开始到结束依次经过不同的工序,形成直线型的生产线。
2. U型布局:U型布局将生产线呈现为一个U字形,适用于工序较多、工序之间需要频繁转移的生产过程。
产品经过一系列的工序后,再返回起点进行下一个工序,形成一个闭环。
3. 流水线布局:流水线布局是将工序按照产品制造的顺序进行排列,每个工序之间形成流水线,使产品在不同工序之间流转顺畅,提高生产效率。
三、工厂生产线的优化除了合理的生产线布局外,工厂还可以通过一些优化措施进一步提高生产效率:1. 优化设备配置:选择性能更好的设备,提高生产线的工作效率。
同时,定期进行设备维护和保养,确保设备正常运转,减少故障和停机时间。
2. 优化作业流程:通过重新规划工序和调整作业流程,减少不必要的移动和运输,提高工人的工作效率。
3. 自动化技术应用:引入自动化设备,如机器人和自动化输送系统,实现生产过程的自动化,减少人力成本,同时提高生产速度和产品质量。
4. 应用先进的生产管理系统:通过应用先进的生产管理系统,可以实现对生产线的实时监控和管理,及时发现和解决潜在问题,提高生产线的整体效率。
工业工程中的生产线布局与优化分析

工业工程中的生产线布局与优化分析引言:工业工程是一门综合性的学科,旨在通过系统地优化和提升生产过程及其相关系统的效率和能力。
而生产线布局和优化则是工业工程中的关键环节,对于工厂的生产效率和产品质量有着重要的影响。
本文将就生产线布局和优化的原理、方法和实践经验进行分析和探讨,希望能够为工程师们在实践中提供一些有益的指导和启示。
一、生产线布局的原则和方法1.1 原则:高效利用空间、合理规划作业流程在进行生产线布局时,首要考虑的是如何最大程度地利用有限的空间,实现生产设备和工人的合理组织。
一方面,要尽可能缩短作业环节之间的距离,减少物料和信息的传递时间;另一方面,还要合理安排设备和工人的空间位置,以确保他们的作业不会相互干扰或阻碍。
1.2 方法:系统分析和模拟仿真生产线布局往往涉及到大量的数据和复杂的关系,因此,采用系统分析和模拟仿真的方法是必不可少的。
通过收集和分析生产设备、工艺流程、物料需求等相关数据,建立数学或仿真模型,可以定量评估不同布局方案的效果,及时发现潜在问题并进行调整。
二、生产线优化的关键问题2.1 作业流程的优化作业流程是生产线上最基本的环节,其优化直接影响到整个生产线的效率和效果。
在作业流程优化中,应注意以下几个关键问题:2.1.1 作业时间的平衡作业时间的平衡指的是在生产线上各个作业环节之间合理分配工作量,避免出现需要等待的环节或者拖延其他环节的情况。
通过合理安排设备和工人的配备,可以实现生产线上工作的平衡,从而提高单位时间内的产量。
2.1.2 物料流动的优化物料流动的优化是作业流程优化的核心内容之一。
通过合理设计物料传递的路径和方式,避免物料堵塞、交叉和断流等问题,可以减少生产线上的物料浪费和停机时间,进而提高生产效率和产品质量。
2.2 设备配置的优化设备配置是生产线优化的另一个关键问题。
在设备配置时,应考虑以下几个方面:2.2.1 设备的容量和效率设备的容量和效率是决定生产线生产能力的关键因素。
生产线平衡与布局

生产线平衡与布局随着现代工业生产的快速发展,生产线平衡与布局成为了企业提高生产效率和降低成本的重要手段。
生产线平衡是指在保证产品质量和生产效率的前提下,合理分配工作任务,确保各个工序之间的协调和平衡,从而提高整体生产线的效益。
一、生产线平衡的重要性生产线平衡是现代生产管理的核心之一。
通过合理分配工作任务,避免生产线上的短板和长板,实现各个工序之间的协同作业,不仅可以提高生产效率,还能够减少生产过程中的浪费和资源消耗。
生产线平衡还能够有效地降低生产成本,提高产品质量和客户满意度,提升企业的竞争力。
二、生产线平衡的方法1. 产品工艺流程分析:通过对产品的工艺流程进行细致分析,明确每个工序的操作步骤和所需时间,找出其中的瓶颈环节和不平衡之处。
2. 时间分析:对于每个工序,进行时间的详细拆分和分析,确定每个工序所需的标准时间和操作工人的数量,确保生产线上的各个工序能够相互匹配,避免出现延误和拥堵。
3. 生产线布局优化:根据产品的工艺流程和生产线的空间限制,合理规划生产线的布局,确保物料流和信息流的流畅性,避免物料的来回搬运和交叉干扰,提高生产线的效率和稳定性。
4. 产能平衡:对于不同工序之间的生产能力进行平衡,避免生产线上的短板和长板,确保生产能力充沛且合理利用资源,提高整体生产效率。
三、生产线布局的原则1. 流程连续性:生产线布局应该根据产品的工艺流程和生产要求,使产品在生产线上能够按照顺序进行加工,避免交叉作业和重复搬运,提高生产效率。
2. 空间利用最优化:在有限的生产区域内,合理规划生产线的布局,尽可能减少物料和信息的传递距离,优化物料流和信息流的路径,最大限度地利用空间资源。
3. 人力资源充分利用:根据各个工序所需的标准时间和操作工人的数量,合理分配工作任务,确保整个生产线上的人力资源充分利用,提高人员的工作效率。
4. 灵活性和可调整性:生产线的布局应该具有一定的灵活性和可调整性,能够适应不同的生产需求和变化的市场环境,随时进行优化和调整。
生产线布局规划
生产线布局规划随着全球经济的不断发展,生产线布局规划对于企业的生产效率和竞争力变得越来越重要。
一种合理的生产线布局规划可以极大地提高生产效率、降低成本、改善工作环境,并且有助于提高产品的质量和交货时间。
本文将探讨生产线布局规划的关键要素和设计原则,以及如何进行有效的生产线布局规划。
一、生产线布局规划的重要性合理的生产线布局规划可以实现以下几个方面的优势:1. 提高生产效率:通过合理的工艺安排和设备摆放,可以缩短生产周期、减少生产环节,从而提高生产效率。
2. 降低成本:合理的生产线布局规划可以减少生产线的长度,缩短物料运输距离,降低人力和设备成本。
3. 改善工作环境:通过优化布局,可以提供一个更好的工作环境,减少工人的劳动强度和疲劳程度,提高工作效率。
4. 提高产品质量:合理的生产线布局规划可以优化生产工艺流程,减少人为因素对产品质量的影响,提高产品质量。
5. 缩短交货时间:通过减少生产环节和提高生产效率,可以缩短产品的制造周期,提高交货时间,提高客户满意度。
二、生产线布局规划的关键要素在进行生产线布局规划时,需要考虑以下几个关键要素:1. 生产流程:了解生产线上的每个工序,确定生产线的整体流程,明确每个工序所需要的设备和工作人员。
2. 人力资源:根据生产流程确定所需的人力资源,包括工人数量和技能要求。
考虑工人的工作负荷和工作强度,确保人力需求与工序需求相匹配。
3. 设备布局:根据生产流程和设备要求,确定设备在生产线上的摆放位置。
确保设备之间的距离合适,物料的流动顺畅,以提高生产效率。
4. 物料流动:合理的物料流动是生产线布局规划的关键。
考虑物料从供应商到生产线的运输路径,以及从一个工序到下一个工序的物料流动路径。
减少物料运输的距离和时间,以提高生产效率。
5. 安全与环境:生产线布局规划还需要考虑工人的安全和环境保护。
确保设备的布局不会造成安全隐患,提供充足的安全通道和紧急出口。
同时,要注重环境保护,优化布局以减少对环境的影响。
甘蔗糖厂的生产线布局与设计
甘蔗糖厂的生产线布局与设计甘蔗糖厂作为食糖加工企业的重要一环,生产线布局与设计对于产品质量、生产效率和安全性至关重要。
本文将探讨甘蔗糖厂的生产线布局与设计,以满足高质量、高效率和安全的生产要求。
一、甘蔗糖厂生产线总体布局甘蔗糖厂的生产线总体布局应考虑到原料输送、加工工序和成品储存的高效衔接。
通常,甘蔗糖厂生产线的布局可分为原料处理区、榨汁区、糖液处理区、糖结晶区和成品储存区等几个主要区域。
原料处理区是对甘蔗进行预处理的区域,主要包括甘蔗清洗、剥皮和切割等工序。
这一区域应尽量靠近甘蔗采购区,以缩短原料运输距离,提高生产效率。
此外,原料处理区还应设有废渣处理设备,以便对产生的蔗渣进行处理和回收利用。
榨汁区是生产线的核心区域,通过榨汁工序将切割后的甘蔗释放出的汁液提取出来。
该区域应设有榨汁机械和相应的输送设备,以确保高效的榨汁过程。
同时,该区域还应配备出糠器和汁渣分离装置,将剩余的渣滓从汁液中分离出来,以保证榨汁产物的纯度。
糖液处理区是将榨汁区提取出的糖液进行处理的区域,主要包括澄清、脱色和浓缩等工序。
该区域应布置相应的设备,如澄清罐、离心机、蒸发器等,以便对糖液进行预处理和精炼,提高糖品质和产量。
糖结晶区是将处理过的糖液进行结晶的区域,主要包括结晶罐、搅拌设备和糖结晶器等。
该区域应设在离糖液处理区较近的位置,以便迅速将糖液转化为结晶体,并保持结晶体的纯度。
成品储存区是对已经结晶的糖进行储存和包装的区域。
该区域应配备储糖罐、包装设备和成品仓库,以确保成品的质量和保鲜。
二、生产线设备选型与安装甘蔗糖厂的生产线设备选型应考虑到处理能力、效率和稳定性等因素。
根据生产规模和需求,选择适当的设备制造商和供应商,并确保设备符合相关的质量标准和安全要求。
设备安装的过程中,应根据实际情况合理安排设备的布局,确保设备之间的联系紧密且方便操作。
同时,应确保设备与生产线布局相协调,便于操作员进行操作和维护。
三、生产线安全措施甘蔗糖厂生产线的安全性至关重要,应采取相应的措施确保生产线的正常运行和操作人员的安全。
高效生产线布局设计与优化策略
高效生产线布局设计与优化策略在当今竞争激烈的市场环境中,企业要想提高生产效率、降低成本、提升产品质量,高效的生产线布局设计与优化至关重要。
一个合理的生产线布局能够减少物料搬运、缩短生产周期、提高设备利用率,从而为企业带来显著的经济效益。
一、生产线布局设计的基本原则1、流程导向原则生产线的布局应按照产品的生产流程进行设计,使生产过程中的各个工序能够顺畅地衔接,减少不必要的迂回和倒流。
这样可以减少物料搬运的距离和时间,提高生产效率。
2、空间利用原则在设计生产线布局时,要充分考虑厂房的空间大小和形状,合理利用空间。
避免出现空间浪费或者设备布局过于拥挤的情况,以确保生产操作的便利性和安全性。
3、灵活性原则市场需求和产品种类可能会发生变化,生产线布局应具有一定的灵活性,能够方便地进行调整和改造,以适应新的生产任务和工艺要求。
4、人机工程学原则要考虑操作人员的工作环境和操作习惯,使设备的高度、操作界面的位置等符合人机工程学的要求,减轻操作人员的劳动强度,提高工作效率和舒适度。
二、生产线布局的常见类型1、直线型布局这是最简单的一种布局方式,产品按照直线顺序依次经过各个工序。
直线型布局的优点是流程清晰、易于管理,缺点是空间利用率较低,当生产工序较多时,生产线会变得很长。
2、 U 型布局U 型布局将生产线弯曲成 U 字形,操作人员可以在 U 型的内部进行操作,减少了物料搬运的距离和时间。
U 型布局具有空间利用率高、生产效率高的优点,但对操作人员的技能要求较高。
3、环形布局环形布局将生产线围成一个环形,产品在环形轨道上流动,各个工序依次进行加工。
环形布局适用于生产批量较大、工序较少的产品,但设备投资较大,维护成本较高。
4、单元式布局将生产线按照产品或工艺的特点分成若干个单元,每个单元独立完成一部分生产任务。
单元式布局具有灵活性高、适应多品种小批量生产的优点,但管理难度较大。
三、生产线布局设计的步骤1、产品和工艺分析首先要对产品的结构、性能、生产工艺等进行详细的分析,确定生产过程中的各个工序和操作要求。
生产线合理布局与优化
生产线合理布局与优化随着科学技术的不断发展,生产线在工业生产中扮演着至关重要的角色。
生产线的合理布局与优化对于提高生产效率、降低成本、提高产品质量具有重要意义。
本文将从生产线的布局原则、优化方法以及实施策略等方面进行探讨。
一、生产线布局原则1. 流程合理性原则:生产线的布局需要根据产品的生产过程来确定,要保证产品在生产线上顺畅进行。
例如,生产品种复杂但生产工序相对独立的产品可以采用分散式布局;而生产工序间存在依赖关系的产品则需要采用集中式布局。
2. 空间利用效率原则:生产线的布局应尽量节约空间,提高空间利用效率。
可以通过合理规划设备的布局方式,将生产线的空间最大限度地利用起来。
3. 运动协调性原则:生产线的布局需要考虑设备之间的运动协调性,即设备之间的移动距离、停顿时间等要尽量减少,以提高生产效率。
4. 人机适应性原则:生产线的布局需要考虑人机适应性,即将人员的工作环境设计得符合人体工程学原则,提高工作效率和工作质量。
二、生产线优化方法1. 设备优化:生产线中的设备是生产的核心,对设备进行优化可以提高生产线的效率和质量。
可以通过设备的升级换代、运行参数的调整、设备维护等手段,提高生产线的运行效率。
2. 工序优化:对于复杂的产品生产线,不同的工序之间存在着互相关联的关系。
通过优化工序的先后顺序、工序间的配合,可以提高生产线的运行效率和产品质量。
3. 供应链优化:生产线的优化不仅关乎内部流程,还需要考虑供应链的整体优化。
通过优化供应链各环节的协调,可以降低生产线的成本,并提高生产效率。
4. 信息化优化:随着信息技术的发展,生产线的信息化管理越来越重要。
通过引入信息化系统,可以对生产线进行数据分析,及时发现问题并进行处理,提高生产效率。
三、生产线优化实施策略1. 充分调研:在进行生产线优化之前,需要对整个生产线的现状进行充分的调研,了解存在的问题和不足之处。
2. 制定优化方案:根据调研结果,制定合适的生产线优化方案,包括布局调整、设备更新、工序优化等。
- 1、下载文档前请自行甄别文档内容的完整性,平台不提供额外的编辑、内容补充、找答案等附加服务。
- 2、"仅部分预览"的文档,不可在线预览部分如存在完整性等问题,可反馈申请退款(可完整预览的文档不适用该条件!)。
- 3、如文档侵犯您的权益,请联系客服反馈,我们会尽快为您处理(人工客服工作时间:9:00-18:30)。
生产线设计与设备布局爱波瑞精益管理咨询有限公司讲师:韩文成Tel:189********一、如何进行精益化生产线改造?1.现代企业制造模式的发展与变化?18世纪台位式生产20世纪初期福特流水线生产20世纪中期丰田生产方式比较项目台位式生产流水线装配生产(大批量生产方式)节拍每个工作台错开生产,但工人的速度不同不能保产品按节拍在各操作者间传输证一个节拍生产操作者技术每班工人都要学习整个流程中的所有操作每个工只需学会一个节拍内的操作所需资源每个工作台需要全套的固定设备每个工位只需一个节拍操作内的资源每个工位只需一个节拍操作做永久准备准备一个工作台进行整个流程的操作,往往需要多种准备每个部件只需要送到1个地方物流每个部件需要被送到所有台位,货架很拥挤,拿取物品容易出错质量同样的工作由许多工人来做,质量没有持续性保同样的工作由少数人来做证;操作周期长,工作很难监控工作满足感完整的装配一个产品,会有一种成就感孤立和厌烦会使工人不喜欢装配线地面需要周围空间做多种准备小空间,单独物流供给通道比较项目精益生产方式大批量生产方式生产目标追求尽善尽美尽可能好工作方式集成,多能,综合工作组分工,专门化管理方式权利下发宝塔式产品特征面向用户,生产周期短数量很大的标准化产品供货方式JIT方式,零库存大量库存缓冲产品质量由人工保证,质量高,零缺陷检验部门事后把关返修率几乎为零很大自动化柔性自动化,但尽量精简刚性自动化生产组织精简一切多余环节组织机构庞大设计方式并行工程串行模式工作关系集体主义精神相互封闭用户关系以用户为上帝,产品面向用户以用户为上帝,但产品缺少变化供应商同舟共济,生死与共互不信任,无长期打算雇员关系终身雇佣,以企业为家可以随时解雇,工作无保障2.精益化改造行动的五大原则?1.全价值链的价值最大化;2.客户第一;3.造物先育人;4.打造团队;5.现地现物;全价值链的价值最大化①全价值链描述;②价值描述;③按照客户需要的速度和品种制造产品;价值工程图客户第一①拉动其实是一种思想;②明确客户的需求;③用客户的需求拉动我们的行为。
造物先育人①人才育成的关键:确定成的标准②执行力和发现问题、解决问题的能力③正常和异常打造团队①团队的典型特征;②目标在运营中的作用;③整体效率的价值;④成就组织目标现地现物①何为主义;②具体问题具体分析;③关键在于指出行动的方法。
模式(结构·流程·标准);人(能力·热情);文化(全员参与·持续改善)主要 活动支援 活动连接 活动企业战略市场定位:成本领先,差异化经营等财务目标:资产收益率等研发 系统采购 系统制造 运营销售 营销售后 服务人力资源(选人,育人,用人,留人)财务管理(全面预算,风险防范,成本低减)基础结构(制度+流程+标准+信息化)方针管理(方针+课题+QC 活动+改善提案)品质,价格,准时交付,快速反应客户满意度客户忠诚度外部市场社会环境:安全,环保,法律法规,劳务关系等要求使命·愿景·战略品质主线(全过程的品质管理)交付主线(从图纸到产品交付运营管理)成本主线(全过程的成本管理)3.企业全价值链精益经营体系?二、精益生产线设计与设备布局1.精益生产线设计&设备布局的目标?◆物流和操作之间的区别是非常重要的:◆物流是材料从一站到另一站的移动流。
它包括许多操作工序:.◆操作是操作工移动地去执行上述工序的流程;◆布局和产线设计的目标:①消除作业以外其它非增值;②创建单件流增值作业.1.在产品生命周期,体积和类型的基础上设计生产线2. 设计小型容易移动的线内设备3. 考虑到客户的节拍时间4. 在流程指令中制成单件流5. 对浪费的传递说NO ,尽可能少用传送带2.生产线设计与设备布局20原则?6. 设计以0为目标的换模时间7. 没有孤岛操作(少人化)8. 人机工作分离9. 结合工作件的进入和出去 10. 设备宽度应该窄小11. 只放必要的材料在手臂长度范围内 12. 工作应该是从右向左流程 (逆时针)2.生产线设计与设备布局20原则?13. 机器人:微妙的机动性是很重要的14. 尽可能的低速度,(节拍15秒以上)15. 当异常发生时设备应该停止16. 机械处理方式应首选电力17. 没有仔细研究前不要自动化供应零件18. 不要同时加工几个零件19. 在新设备安置前先进行模拟20. 通过流程组织布局并且保持硬件设施灵活《生产线设计与设备布局(1)》3.生产线设计与设备布局的流程?设计 图面 Sample 制作组立顺序的 决定 测定标准时间Main·Sub 区分 稼动时间生产计划 编程制约分析 - 优先顺位(先.后) - 作业位置 - 设 备Tact Time 算定 预想不良率 等线体 balancing (工程 分割,结合)制品的大小 作业性 等 所需 工程数 所需 作业人员 人员 编程 全体 Layout 计划 线体 Layout 设计工程 间距 线体 长返送设备 选定 制 品 特 性 作 业 特 性线体 移送速度 Conveyor 的 制品 间距出动率 其它 间接要员 Layout 设计 原则空间分析 - 作业空间 - 保管空间█ 组装线体的编程顺序█ 机器加工线体编程顺序设计图面生产计划加工顺序的决定根据标准时间估计时间所需设备台数算定稼动时间良品率等担当台数的检讨担当台数的决定人员编成间接要员出勤率, 其它移送设备的选定(Conveyor, 推车等) Layout 设计Tact Time算定台数算定Line Balancing 改善检讨全体 Layout 计划Space 检讨- 设备 Space- 保管 Space- 作业 Space 3.生产线设计与设备布局的流程?节拍时间 =有效生产时间 (1) 客户需求 (2)(1) 没有计划停工的总时间.(2) 在那段时间内单元需求的数量.•产品循环应该遵守节拍时间,例如:吻合需求循环时间;•通常在生产线设计循环时间是小于节拍时间的(因为效率上面会有损失)例如: 时间: 2 x 8 小时 (480 分钟)休息: 20 分钟 / 班 节拍时间 =清洁: 10 分钟 / 班 需求:10.000 单元/周 = 0,45 钟= 27 秒 /单元2 x (480-20-10)10.000 / 54.核心技巧—确定节拍每种A 类产品(高运转)都要做;从主要的零部件开始(一个所有部件都要聚集的部件)如:汽车底盘; 不要有代表着浪费的操作工序(只有增值的工序); 应该预估没有浪费的时间 (净操作时间);在现阶段,时间是净操作时间的粗略估计(注意标准时间应该由研究部门给出,通常情况下是包含很多的浪费)。
A1 A2 A3 A4 A5 A6 灰体中心螺丝翼螺丝锥体最后螺丝16 s6 s 3 s12 s16 s3 s25 s盒SA2 4 s管子SA1 螺丝翼装配的塞子•一个流程图代表了一种可能的装配或生产顺序; •3种信息 :–兰色: 零部件; –黄色: 增值工序; –绿色: 时间.5.核心技巧—绘制流程图并预估时间6.核心技巧—LOB作业平衡分析█ 理论必要人员的计算理论必要人员(n) = ∑HT / TT (取到小数点一位)ΣHT : 对象工程的手作业时间的合计………最新的时间值,正确的时间值TT = 稼动时间/(日*SPD)稼动时间 = 规定劳动时间–非稼动时间SPD = 生产计划数量/稼动日数计算例生产计划数量 : 17,600 台/月稼动日数 : 22 日/月∑HT : 200 秒SPD : 800 台(=17,600/22) 日非稼动时间 : 20分TT : 34.5 秒理论必要人员 = 200秒/34.5秒 = 5.8名█ N : n 比率1 2 3 4 5 (1) 理论必要人员的状态∑HT = 360 TT = 80 N = 4.5 名1 2 3 4 5 6n = 6 名(2) 实际的人员配置(3)N : n 的比率 6/4.5 = 1.33实际人员是理论值的 1.33倍原因是人员过多和 Balance 不良布局和产线设计总是从PQ 分析开始; A 类产品(高运转)是半自动化生产线(维持单件流)很好的候选者; B 类产品是手动,低自动化生产线很好的候选者;C 类产品(低运转)是单工作台/手动生产线很好的候选者,零活应对许多类型产品Q : 数量P: 产品型号B (15)A2(10)C (120)(3 r e f ) A1 •3 种型号 = 一年中销售量的45%•10 种型号 = 一年中销售量的35%•15 种型号 = 一年中销售量的15%•120 种型号= 一年内5%销售量7.核心技巧—PQ 分析XXXXX X X X XXXXA B CDE F12 3 4 5 6 7 X X X XX X X X X X X X X XX X X X X工序产品类型尽可能专为一个产品家族设计一个流程流水线产品与流程矩阵8.核心技巧—PR 分析工作团队 A (有规律团队)•负责操作一台固定工序数量的线内设备; •基于产品系列C 工作内容的生产线平衡; •常规工作量,独立于产品组合。
工作团队 B(“不匀均” 团队) •负责离线工作;•负责易变化的工序 (不匀均); •由更少的工人组成;•由最有技巧的工人组成(工作量根据产品组合变化)。
生产工作内容产品家族A B CWork in Process Waiting Functional LayoutBig Batch ProductionSub AssemblyAssemblyControlWA R E H O U S E仓库 库 流程过程中的等待功能性布局 大批量生产 预装配装配检查9.核心技巧—柔性化流程性布局演化预装配 生产线布局 小批量生产仓库材料流装配控制9.核心技巧—柔性化流程性布局演化预装配 U 型布局 单件生产超市材料流装配控制包装9.核心技巧—柔性化流程性布局演化工作流程IN OUTConveyor 在一字 线体中,由于单位工程别彻底的分业化的作业实行,进行 Work 流程,作业效率高的反面 ,必然存在Line 的 Unbalance 。
还有受其影响 NO Work 和Full Work 频繁发生,稼动率容易低下,物的流动会积压,堵塞,导致追求顺畅的流程的困难。
在这样形态的Layout 中,通过稼动率 (时间 稼动率+能力 稼动率)的向上和一定的水平维持 (90% ~ 95%) 来对应生产的Timing 非常重要。
一字 线体作为一般在组立线体中常见的形态, 大型Conveyor 的直线线体中投入多数人力专担 大LOT 中心的 Batch 生产或专用设备化(自动化),谋求大量生产长处短处. 可以搬运重量物.. 有C/V引起的作业的强制力.. 分业引起的熟练容易. C/V 速度引起的生产性向上. 细微的现场监督业务没有必要. 为防止线体Stop 的Action 促进依据专门 (部门) 技能 Up,Speed 会粘住. 在大量生产中效率高.. 作业 Pace中有约束力.. 容易育成技能.- 由于作业范围狭小,初学者也可以做. . Conveyor的 7种浪费- 等待的浪费- 抓和放的浪费- 在工的浪费- 再作业, 不良的浪费- 准备交替的浪费- 不能辅助作业的浪费- 机器稼动时间中的等待的浪费. 容易发生分业引起的线体Balance LOSS. 对生产量变动的对应力下降. 工程间停滞量大,生产L/T长使在工量增加. . 工作的回报, 满意度低.. 设计一变的话 Layout 变更困难.. 大的投资必要Cell Line /U字 Line熟练的作业者在没有 Conveyor Line的 CELL内部担任全部工程的作业并执行的自己完成型方式.根据作的业形态分为1人CELL,巡回方式, 分割方式等.追求多品种少量生产.既,组立线体中一个最小单位生产组织执行从第一工程到最后工程的组立及检查,包装的生产方式.1) 符合市场需求的 Flexible 的生产Line运营2) 对应于快的 Model Change3) 对应于多品种少量生产4) 对应于高品质要求5) 生产Lead Time的逐渐节减及在工在库减少6) 作业者的职务满足度增加.. CELL 编程效率100% . CELL 的管理容易 . 确保稳定的品质(作业中可以品质保证) . 维持效率及向上.(固定度, 小量多品种). 可以排除工程间的停滞, 可以 缩短生产L/T. 可以排除非附加价值作业. . 技能继承容易.. 可以感觉到成就感, 满足感. . 高技能的能力可以用 Full 发挥. 设备投资大.(各 CELL 需要生产设备) . 需要多技能工. 作业者的能力如实地表现出来. . 容易成为自己的 Pace. . 移动(步行)距离长.. 技能者育成中需要时间. 多技能工育成中需要相当长的时间. . 由于是一个人很难找准Pace. . Space, 设备的需要量大. 生产量多的制品不适合. 治具, 检查器具等每个CELL 都需要 . 代行作业困难INOUT①②③④⑤⑥⑩⑨⑧⑦█ 形态别特征1人 CELL 方式长处短处. CELL 的管理容易 . 对应生产量变动容易. 组立大型部品或多数的部品或组立JIG, 检查JIG等需要大型场所时可以确保必要的Space.. 以最慢的作业者的Speed, 决定Cycle Time.(因为难以追越) . 需要万能工 . 帮助作业困难.. 后面的人能感觉到从其后面给的Pressure.. 因为作业者移动, 同种类的工具需要在很多处巡回方式IN OUT①②③④⑤⑥⑩⑨⑧⑦长处短处█ 形态别特征. 容易抓Line Balance. . 可以帮助作业.. 可以最小单位的多技能工 . 熟练期间较短. . 2人分割方式容易管理.(设置Religion, 帮助作业容易.). 为了Line 编程, 开始及维持的管理上费时间.. 与1人方式,巡回方式相比 Balance 容易下降.. 与Conveyor 相比没有强制力. . 与Conveyor 相比, 无论如何到达熟练的其间长分割方式IN OUT①②③④⑤⑥⑩⑨⑧⑦长处短处█ 形态别特征5.核心技巧—少人化设计•少人化 = 生产线能够适应由于操作工人数的变化而产生的产量节拍时间变化•多能工1 2 3 4 51B 2B 3B8 67•三名操作工的单元.1 2 3 4 51B 2B 3B8 67•两名操作工的单元.•把功能性设备布局变更为以流程为基础的布局,通常需要更多的设备 •小型线上设备的概念是指较小较少的通用设备; •内部研发这种类型的设备是可能的; •通常内部研发的设备有;–清洁和冲洗设备; –简单的机加操作; –小压机;–用于净化的油锅;–用吹风机和家用烤箱烘干和加热。