电力电缆制造工艺
电线电缆生产加工工艺流程

电线电缆生产加工工艺流程电线电缆是广泛应用于各个领域的电气设备,其生产加工工艺流程一般包括下面几个步骤:1.原材料准备:电线电缆的主要原材料包括导体、绝缘材料、护套材料等。
导体一般采用铜或铝等金属材料,绝缘材料可以是橡胶、聚乙烯、聚氯乙烯等。
在生产之前,需要对这些原材料进行检验和测试,确保其质量符合相关标准要求。
2.导体制造:导体是电线电缆的主要组成部分,其制造一般包括拉丝和挤压两个步骤。
首先,通过机械拉丝的方法将金属材料拉成所需的直径和长度;然后,将导体放入挤压机中,在高温下将绝缘材料覆盖在导体上。
3.绝缘层制造:绝缘层是为了保护导体,防止电线电缆发生漏电或短路等故障。
绝缘层的制造一般采用挤压或包带的方法。
挤压方法是将绝缘材料通过挤出机挤压到导体表面,形成所需的厚度;包带方法是通过固定的机器将绝缘材料缠绕在导体上,形成所需的绝缘层厚度。
4.护套制造:为了进一步保护电线电缆,阻止外界环境因素对其造成损害,需要制造护套。
护套一般采用PVC、PE等塑料材料制造,具有耐磨、耐化学腐蚀等特点。
护套的制造一般采用挤压的方法,将护套材料通过挤出机挤压到电缆外部。
5.终端接头制造:终端接头是电线电缆与设备连接的关键部分,其制造一般包括绝缘处理、绝缘套管的安装等步骤。
首先,需要对电缆导体进行绝缘处理,确保导体表面干净和光滑;然后,将绝缘套管安装到导体上,并进行压接或焊接等操作,使接头与设备连接紧密可靠。
6.检验和测试:在生产加工过程中,需要对电线电缆进行各项检验和测试,以确保其质量符合标准要求。
包括导体电阻、绝缘电阻、电力损耗、机械性能等方面的测试。
7.包装和贮存:最后,对生产好的电线电缆进行包装,以确保其在运输和贮存过程中不受损坏。
常用的包装方式包括盘装、卷装等。
以上是电线电缆生产加工的一般工艺流程,每个步骤的具体操作和细节会根据不同的产品类型和要求有所差异。
有效的生产加工工艺流程能确保电线电缆质量可靠,满足用户的使用需求。
电缆生产工序

电缆生产工序一、原材料准备电缆生产的第一步是准备原材料。
通常情况下,电缆的主要原材料包括导体、绝缘材料、护套材料和填充物。
导体通常由铜或铝制成,绝缘材料可以是聚乙烯、聚氯乙烯等,护套材料可以是聚氯乙烯或聚氨酯等。
在准备原材料的过程中,需要对原材料进行检验和测试,确保其质量符合要求。
二、导体制造导体是电缆的核心部分,负责传输电流。
导体的制造通常包括铜或铝的拉丝和绞合。
首先,将铜或铝材料加热至适当温度,然后通过模具将其拉制成所需的直径。
接下来,将多根导体绞合在一起,形成电缆的导体部分。
导体制造的关键是确保导体的直径和绞合的紧密度符合设计要求。
三、绝缘层制造绝缘层是保护导体的重要部分,防止电流泄漏和短路。
绝缘层的制造通常采用挤出工艺。
在这个过程中,将绝缘材料加热至熔化状态,然后通过挤出机将其挤出成所需的形状。
挤出后的绝缘层需要经过冷却和固化,以确保其稳定性和可靠性。
四、护套制造护套是保护电缆的外层,具有防水、耐磨和耐腐蚀等功能。
护套的制造通常采用挤出或浇注工艺。
挤出工艺与绝缘层制造类似,将护套材料加热至熔化状态,然后通过挤出机将其挤出成所需的形状。
浇注工艺则是将护套材料直接注入电缆外部,然后通过冷却和固化来形成护套。
五、填充物安装填充物的作用是填充电缆内部的空隙,增加电缆的机械强度和耐压能力。
填充物通常是一种柔软的材料,如聚丙烯蜡。
在电缆制造的过程中,填充物被注入电缆内部,并通过挤压和压实来确保其均匀分布。
六、成品检验电缆生产完成后,需要进行成品检验。
成品检验的目的是确保电缆的质量符合标准要求。
常见的成品检验项目包括外观检查、电气性能测试、机械性能测试等。
只有通过成品检验的电缆才能出厂销售。
总结:电缆生产工序包括原材料准备、导体制造、绝缘层制造、护套制造、填充物安装和成品检验等环节。
每个环节都需要严格控制和检验,以确保电缆的质量和性能符合要求。
电缆作为现代社会中不可或缺的基础设施,其生产工序的规范和严谨对于保障电力传输和通信的稳定运行至关重要。
低压电力电缆生产工艺流程
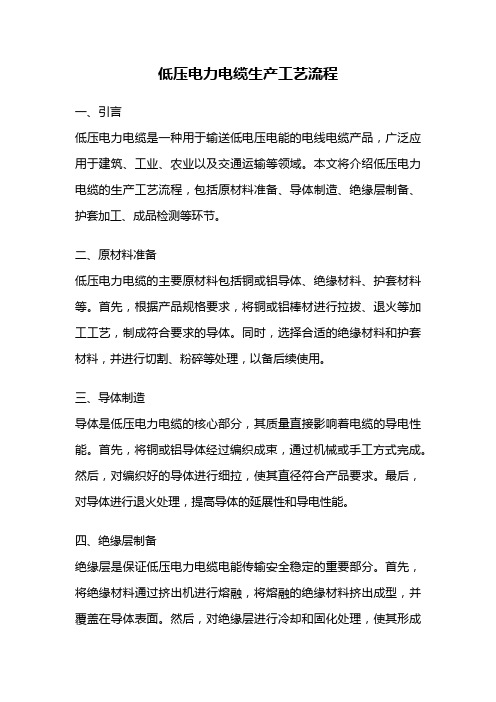
低压电力电缆生产工艺流程一、引言低压电力电缆是一种用于输送低电压电能的电线电缆产品,广泛应用于建筑、工业、农业以及交通运输等领域。
本文将介绍低压电力电缆的生产工艺流程,包括原材料准备、导体制造、绝缘层制备、护套加工、成品检测等环节。
二、原材料准备低压电力电缆的主要原材料包括铜或铝导体、绝缘材料、护套材料等。
首先,根据产品规格要求,将铜或铝棒材进行拉拔、退火等加工工艺,制成符合要求的导体。
同时,选择合适的绝缘材料和护套材料,并进行切割、粉碎等处理,以备后续使用。
三、导体制造导体是低压电力电缆的核心部分,其质量直接影响着电缆的导电性能。
首先,将铜或铝导体经过编织成束,通过机械或手工方式完成。
然后,对编织好的导体进行细拉,使其直径符合产品要求。
最后,对导体进行退火处理,提高导体的延展性和导电性能。
四、绝缘层制备绝缘层是保证低压电力电缆电能传输安全稳定的重要部分。
首先,将绝缘材料通过挤出机进行熔融,将熔融的绝缘材料挤出成型,并覆盖在导体表面。
然后,对绝缘层进行冷却和固化处理,使其形成均匀致密的绝缘膜。
五、护套加工护套是保护电力电缆免受外界环境和机械损伤的重要层。
首先,根据产品要求,选择合适的护套材料,并通过挤出机进行熔融,将熔融的护套材料挤出成型,并覆盖在绝缘层表面。
然后,对护套进行冷却和固化处理,使其具有足够的柔韧性和耐久性。
六、成品检测在低压电力电缆生产过程中,成品检测是确保产品质量合格的重要环节。
通过对成品进行导体电阻、绝缘电阻、外观质量等多项检测,确保电缆的导电性能和绝缘性能符合标准要求。
同时,对护套的耐磨、耐压等性能进行测试,以确保产品在使用过程中的可靠性和安全性。
七、包装和出厂经过成品检测合格的低压电力电缆,将进行最后的包装和出厂准备工作。
首先,对电缆进行整理和打包,确保产品外观整洁、无损伤。
然后,根据客户需求,对电缆进行标识和包装,以方便运输和使用。
最后,按照约定的交货方式和时间,将电缆出厂交付给客户。
电缆制作工艺流程

电缆制作工艺流程电缆制作工艺流程是指将金属导体、绝缘层和护套材料按照一定的工艺和流程进行组合、绝缘、编织层和覆套等工序,最终制成电力电缆或通信电缆的整个过程。
下面将详细介绍电缆制作的工艺流程。
第一步:导体制备电缆的导体一般采用铜或铝材料,首先需要将铜或铝材料进行拉丝,然后切割成合适的长度。
导体的表面通常还会经过去氧化处理,以提高导体的导电性能。
第二步:绝缘层制造绝缘层通常采用聚乙烯、聚氯乙烯等材料,经过加热和挤出工艺,将绝缘材料套在导体上。
在此过程中,要确保绝缘层的厚度均匀、没有气泡和缺陷,以保证电缆的绝缘性能。
第三步:编织层制造编织层的作用是增加电缆的机械强度和防护性能。
根据不同的用途,编织层的材料也不同,可以是金属丝、合成纤维等。
编织层的制作通常是通过成熟的编织机械进行,确保编织的密度和均匀性。
第四步:护套制造护套的主要作用是保护电缆内部的导体和绝缘层不受外部因素的损坏。
护套一般采用聚氯乙烯、聚乙烯等材料,通过挤出工艺将护套材料套在编织层上面。
护套的颜色和外观可以根据客户需求进行定制。
第五步:绝缘层测试在电缆制作的过程中,对绝缘层的质量进行必要的测试是十分重要的。
这个步骤通常包括对绝缘层的厚度、强度、绝缘电阻等性能的测试。
只有通过了绝缘层测试,才能确保电缆的质量符合要求。
第六步:打包和运输电缆制作完成后,会按照客户的需求进行打包和标识。
一般来说,电缆会根据种类、规格、长度等进行分类打包,并附上相应的标签和说明书。
然后,通过适当的运输方式将电缆送达客户的指定地点。
以上就是电缆制作的主要工艺流程。
电缆制作需要严格按照工艺和流程进行,以确保电缆具有良好的导电、绝缘和保护性能。
只有在每个环节都严格把控质量,才能生产出高品质的电缆产品。
电力电缆生产工艺流程
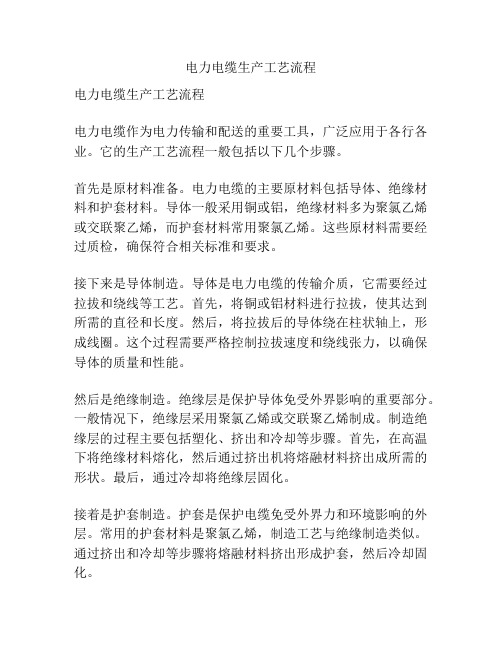
电力电缆生产工艺流程电力电缆生产工艺流程电力电缆作为电力传输和配送的重要工具,广泛应用于各行各业。
它的生产工艺流程一般包括以下几个步骤。
首先是原材料准备。
电力电缆的主要原材料包括导体、绝缘材料和护套材料。
导体一般采用铜或铝,绝缘材料多为聚氯乙烯或交联聚乙烯,而护套材料常用聚氯乙烯。
这些原材料需要经过质检,确保符合相关标准和要求。
接下来是导体制造。
导体是电力电缆的传输介质,它需要经过拉拔和绕线等工艺。
首先,将铜或铝材料进行拉拔,使其达到所需的直径和长度。
然后,将拉拔后的导体绕在柱状轴上,形成线圈。
这个过程需要严格控制拉拔速度和绕线张力,以确保导体的质量和性能。
然后是绝缘制造。
绝缘层是保护导体免受外界影响的重要部分。
一般情况下,绝缘层采用聚氯乙烯或交联聚乙烯制成。
制造绝缘层的过程主要包括塑化、挤出和冷却等步骤。
首先,在高温下将绝缘材料熔化,然后通过挤出机将熔融材料挤出成所需的形状。
最后,通过冷却将绝缘层固化。
接着是护套制造。
护套是保护电缆免受外界力和环境影响的外层。
常用的护套材料是聚氯乙烯,制造工艺与绝缘制造类似。
通过挤出和冷却等步骤将熔融材料挤出形成护套,然后冷却固化。
最后是电缆组装与测试。
在组装过程中,将绝缘导线和绝缘层一起绕包在一起,并用合适的绝缘带固定。
同时,也会根据需要制造多芯电缆,将多个导线绕包在一起。
最后,对成品电缆进行严格的测试,包括电气性能测试、物理性能测试和外观质量检查等。
综上所述,电力电缆的生产工艺流程包括原材料准备、导体制造、绝缘制造、护套制造、电缆组装与测试等步骤。
每一个步骤都需要严格控制质量和性能,确保成品电缆符合相关标准和要求。
这样才能保证电力电缆的安全可靠性,为各行各业的电力传输和配送提供支持。
电线电缆的制造工艺及所需主要设备

电线电缆的制造与大多数机电产品的生产方式是完全不同的。
机电产品通常采用将另件装配成部件、多个部件再装配成单台产品,产品以台数或件数计量。
电线电缆是以长度为基本计量单位。
所有电线电缆都是从导体加工开始,在导体的外围一层一层地加上绝缘、屏蔽、成缆、护层等而制成电线电缆产品。
产品结构越复杂,叠加的层次就越多。
一、电线电缆产品制造的工艺特性:1.大长度连续叠加组合生产方式,大长度连续叠加组合生产方式,对电线电缆生产的影响是全局性和控制性的,这涉及和影响到:(1)生产工艺流程和设备布置生产车间的各种设备必须按产品要求的工艺流程合理排放,使各阶段的半成品,顺次流转。
设备配置要考虑生产效率不同而进行生产能力的平衡,有的设备可能必须配置两台或多台,才能使生产线的生产能力得以平衡。
从而设备的合理选配组合和生产场地的布置,必须根据产品和生产量来平衡综合考虑。
(2)生产组织管理生产组织管理必须科学合理、周密准确、严格细致,操作者必须一丝不苟地按工艺要求执行,任何一个环节出现问题,都会影响工艺流程的通畅,影响产品的质量和交货。
特别是多芯电缆,某一个线对或基本单元长度短了,或者质量出现问题,则整根电缆就会长度不够,造成报废。
反之,如果某个单元长度过长,则必须锯去造成浪费3)质量管理大长度连续叠加组合的生产方式,使生产过程中任何一个环节、瞬时发生一点问题,就会影响整根电缆质量。
质量缺陷越是发生在内层,而且没有及时发现终止生产,那么造成的损失就越大。
因为电线电缆的生产不同于组装式的产品,可以拆开重装及更换另件;电线电缆的任一部件或工艺过程的质量问题,对这根电缆几乎是无法挽回和弥补的。
事后的处理都是十分消极的,不是锯短就是降级处理,要么报废整条电缆。
它无法拆开重装。
电线电缆的质量管理,必须贯串整个生产过程。
质量管理检查部门要对整个生产过程巡回检查、操作人自检、上下工序互检,这是保证产品质量,提高企业经济效益的重要保证和手段。
2.生产工艺门类多、物料流量大电线电缆制造涉及的工艺门类广泛,从有色金属的熔炼和压力加工,到塑料、橡胶、油漆等化工技术;纤维材料的绕包、编织等的纺织技术,到金属材料的绕包及金属带材的纵包、焊接的金属成形加工工艺等等。
干法交联电力电缆工艺

干法交联电力电缆工艺
干法交联电力电缆工艺是一种电力电缆制造工艺,其主要特点是在电缆绝缘层材料中添加交联剂,通过高温高压条件下进行交联反应,使绝缘层材料形成三维网络结构,从而提高电缆的耐热性、耐电性、耐化学性和机械强度。
一、交联剂的选择
交联剂是干法交联电力电缆工艺中的关键材料,其主要作用是在高温高压条件下引发交联反应。
常用的交联剂有有机过氧化物、无机过氧化物和有机过硫酸盐等。
其中,有机过氧化物因其易于分解、反应速度快等特点被广泛应用。
二、交联反应条件
干法交联电力电缆工艺的交联反应需要在高温高压条件下进行。
一般情况下,交联温度在150℃-200℃之间,交联时间在4h-8h之间。
同时,交联反应需要在惰性气氛下进行,以避免氧化反应的发生。
三、交联反应的过程
交联反应的过程可以分为三个阶段。
第一阶段是引发期,此时交联剂分解产生自由基,自由基与绝缘层材料中的分子发生反应,形成自由基中间体。
第二阶段是
传递期,此时自由基中间体在高温高压条件下进行传递反应,形成三维网络结构。
第三阶段是终止期,此时反应中的自由基中间体已经消耗殆尽,交联反应结束。
四、交联电缆的性能
干法交联电力电缆的交联层具有优异的性能,其耐热性、耐电性、耐化学性和机械强度都得到了显著提高。
同时,交联层的介电常数和介质损耗因数也得到了改善,从而提高了电缆的传输性能。
此外,交联电缆还具有良好的耐老化性能和耐湿性能,能够满足各种复杂的使用环境要求。
10kv电缆的制作工艺

10kv电缆的制作工艺
10kV电缆的制作工艺通常包括以下步骤:
1. 原材料准备:准备铜线和绝缘材料,铜线用于导电,绝缘材料用于隔离电线和周围环境。
2. 铜线制备:将铜杆通过拉拔机拉制成合适直径的铜丝。
3. 绝缘材料加工:将绝缘材料切割成合适长度和宽度的片状,用于包覆铜线。
4. 铜线绝缘:将铜线通过绝缘机,绝缘机会将绝缘材料自动包覆在铜线上。
5. 绞合:将绝缘好的铜线通过绞线机绞合成电缆芯。
6. 护套材料准备:准备护套材料,护套材料用于保护电缆芯免受机械损坏。
7. 护套:将电缆芯通过护套机,护套机会将护套材料自动包覆在电缆芯上。
8. 引线和套管:根据需要,在电缆的一端连接引线和套管,用于接入电力设备。
9. 测试:经过制作的电缆需要进行电气性能测试,以确保其符合相关标准和规范。
10. 包装和运输:完成测试后,将电缆进行包装,准备运输至需要使用的地点。
以上步骤仅为一般情况下的10kV电缆制作工艺,实际工艺可能因制造厂家和特定要求而有所差异。
制作工艺的细节也可能包括其他步骤,如屏蔽或绝缘增强等。
为了确保电缆的质量和可靠性,制作过程中还需要严格控制材料的质量和生产环境的干净度。
- 1、下载文档前请自行甄别文档内容的完整性,平台不提供额外的编辑、内容补充、找答案等附加服务。
- 2、"仅部分预览"的文档,不可在线预览部分如存在完整性等问题,可反馈申请退款(可完整预览的文档不适用该条件!)。
- 3、如文档侵犯您的权益,请联系客服反馈,我们会尽快为您处理(人工客服工作时间:9:00-18:30)。
1基本工艺流程电力电缆的制造包括许多工序,一般可分为四个主要方面:导体制造,包括1)拉丝拉细单线到所需的直径;2)绞合把多根单线绞合到一起,有时需要再包带;3)组合在HV和EHV电缆制造中,把非圆形的股块绞合成准圆形的结构;绝缘线芯制造,包括1)三层挤出:电缆绝缘线芯在这个过程中形成,包括内半导电屏蔽层、绝缘层和外半导电屏蔽层;2)交联:可在挤出后直接进行(过氧化物交联),或者在挤出后采用单独设备进行(湿法交联);3)除气:通过离线加热把过氧化物副产物去除,这通常是HV或EHV电缆的基本工序,但也是经常用于中压海底电缆;电缆护层制造,包括1)绝缘线芯包带:在此过程中,把缓冲层、保护层和阻水层绕包到挤包的绝缘线芯上;2)中性线绞包:把铜线、铜带或扁铜带包绕在电缆上;3)金属护层:施加金属的防潮和保护层;4)护套:采用聚合物护套起到机械保护(对金属箔的保护特别重要)和防腐蚀作用;5)装铠:采用高强度金属构件(钢)来保护电缆,特别是海底电缆;质量控制,包括1)原材料的操作处理;2)例行试验;3)抽样试验;3.2导体制造有些电缆制造采用直接用于屏蔽和绝缘加工的制成导体,或用铜杆或铝杆,并将其拉丝到合适的直径,然后绞合(扭结成一体)成电缆导体。
那些拉丝绞合制造导体的电缆制造必须遵循基本但重要的工艺,以确保导体获得合适的物理性能和电气性能。
由于拉丝工艺使金属产生加工硬化,因此拉丝后的线材通常必须加热以获得适当的物理性能,这个工艺叫退火。
退火可以通过感应加热过程实现。
在这个过程中,通过感应到绞线上的电流来产生热量,并提高导体的温度到正确的退火温度。
此外也可以把绞线放置到炉箱中实现退火。
退火能同时影响绞线的物理和电气性能,因此在退火过程中必须谨慎操作和监控。
必须进行定期的测试来确保绞线的特性符合规范的要求。
绞合导体是通过扭绞多根单线完成的,有多种类型的扭绞(或绞合)型式。
尽管绞合工艺相对容易完成,但必须仔细操作,以确保在绞合的过程中单线没有损伤以及绞合系数(单位长度上绞绕的次数)正确。
导体中的水分十分不受欢迎,因为水分会导致绝缘中生长水树从而使电缆过早击穿,也可导致电缆接头过早击穿。
在制造、安装或运行过程中可能使水进入导体,应考虑使用阻水结构的导体。
3绝缘线芯制造挤出绝缘电缆的生产线是一种高度精密的制造过程,运转时必须严格控制,以确保最终的产品能够可靠地运行多年。
它包括许多前后密切衔接的了工艺。
如果生产线上的任一部分有故障,就会导致生产出质量差的电缆,并可能会产生出很多米的废电缆。
在导体屏蔽料、绝缘料和绝缘屏蔽料挤出到电缆导体上后,必须进行交联。
交联(也称为硫化)是一个化学反应,它能提高这些标准的热性能和机械性能,尤其是提高高温下的强度和稳定性。
绝缘线芯制造工艺起始于绝缘和半导电材料的颗粒在挤出机内熔融的时候。
熔融是在加压的情况下进行的,压力把电缆料向十字机头输送,并在十字机头内形成电缆的各个层。
在螺杆末端和十字机头的顶部,应放置用于过滤的滤网或过滤板。
在挤出型电缆制造的早期,放置这些滤网或筛子是为了除去材料中的小颗粒,或者是熔融进程中产生的杂质。
虽然如今仍在应用滤网,但由于现今材料较好的净化特性,减小了材料对该类型滤网的需求。
实际上,如果滤网太细的话,其本身就能以焦烧或预交联的方式而产生杂质。
然而,适当尺寸(100-200μm孔径)的过滤网用来帮助稳定挤出机内熔融的均匀度以及防止在材料处理过程中从外界混入大尺寸杂质是很有益的。
在挤出型电缆制造的早期,采用二次挤出工艺来生产电缆绝缘线芯。
先同时挤出导体屏蔽和绝缘,然后交联并绕到线盘上。
经过一段时间后,再挤出导体屏蔽和绝缘,这种工艺会在绝缘和绝缘屏蔽之间形成不规则并可能遭受污染的界面。
在这个工艺中,绝缘屏蔽可能是不交联的,因此电缆只有有限的热学性能。
现在,有两种制造工艺用来在一道工序中完成所有三层的挤出。
第一种方法是1+2三层挤出工艺,它是先挤出导体屏蔽,经过较短的距离(通常是2m到5m)后,再在导体屏蔽上同时挤出绝缘和绝缘屏蔽。
第二种方法是三层共挤工艺,它是将导体屏蔽、绝缘和绝缘屏蔽同时挤出。
在这两种方法中,绝缘屏蔽都是交联的,因此电缆的高温性能有很大改善。
1+2三层挤出在其首次被推行时是一个重要的发展。
因为它能产生一个较为洁净、均匀的绝缘和绝缘屏蔽界面。
但是在这个工艺中,导体屏蔽从导体屏蔽挤出机到绝缘和绝缘屏蔽挤出机时,是暴露在空气中的。
如果不采取严格的措施保护导体屏蔽,那么导体屏蔽可能产生缺陷,降低电缆的寿命。
正是基于这个原因,三层共挤工艺被认为是更好的工艺,因为在这个工艺中导体屏蔽在绝缘挤出前不会暴露在空气中。
三层共挤工艺能产生十分洁净、均匀的导体屏蔽和绝缘界面。
在实验室对两种不同工艺生产的电缆进行了加速寿命试验。
试验结果表明,用1+2工艺生产的电缆比三层共挤工艺有更高老化速率。
在这个特定的试验中,电缆样品放置在水箱中,感应到导体上的电流以提高导体温度,在导体和绝缘屏蔽上施加较高的交流电压。
电缆在这些条件下老化规定的时间。
到了规定的时间,把电缆取出并进行交流击穿试验。
应用1+2或者三层共挤工艺生产出三层电缆绝缘后,没有交联的绝缘线芯直接进入硫化管。
在这里有完全不同的硫化工艺。
在过氧化物硫化过程中,电缆进入到一个高温高压的管道中。
这个管道很长,以便有足够的时间来完成交联过程。
尽管氮气是较好的媒质,因为热蒸汽硫化会在绝缘中产生水分和大量的微孔,但管道内可以采用蒸汽或者热氮气加压。
另一个重要的易被忽略的步骤是应充分冷却交联好的绝缘线芯,确保外部绝缘和导体的温度降低到可以离开硫化管的温度。
当电缆线芯引出硫化管时,绝缘线芯应是按照正确的制造规范和标准已进行了充分的交联和冷却。
采用湿法交联工艺,挤出机后面的管道的长度需要保证热塑性绝缘线芯充分冷却,以免导体上的绝缘偏芯(下垂)。
实际的交联或硫化过程是在挤出后离线进行的。
在所有挤出工艺中,经常采用X射线或超声波技术来检查电缆同心度和进行缺陷定位,如内导电(导体屏蔽)缺陷。
在其他层后续加工前找出重大缺陷很重要。
3.1 挤出-过氧化物硫化过氧化物硫化电缆的3种基本的电缆绝缘线芯挤出和硫化过程:CCV-悬链式连续硫化VCV-立式连续硫化MDCV-Mitsubishi Dainichi连续硫化,也叫长承模连续硫化悬链式连续硫化(CCV)CCV技术中,硫化布置成了悬链状,当它悬吊在两点之间时,象一概弦线。
导体在馈送方式与VCV相同,都是从放线架进入到储线器。
这样可以保证在连续挤出工艺不停止的情况下,当旧的线盘用完能够换一个新的导体线盘到放线架上。
储线器也为两个导体的焊接提供了时间。
通过严格地控制电缆张力来保持电缆处在硫化管的中心位置。
使用先进的自动控制系统,做到这点已经变得较为容易。
还注意确保不让已经融化但未交联的塑料聚合物在重力的作用下从导体上滴落或垂落,这个效应一般叫做“下垂”。
下垂效应随着绝缘厚度与导体尺寸的比率啬而趋于增强。
一些工艺,包括使用特殊的低融流指数聚合物、旋转电缆、绝缘表面急冷等,可以有效地减少绝缘的下垂效应。
对于大截面电缆(重电缆),还存在另一个问题。
就是施加一个很大的拉力(必须保证电缆在管中心)以及张力的控制变得困难。
这实际上限制了导体截面要小于1400~1600mm2。
CCV线上可以生产绝缘厚度最大为25mm的电缆。
悬链线的管子长度是可变的,但总长度均在160m左右。
管内的硫化媒质是加压蒸汽或高温高压的氮气。
冷却可由水或者冷却的氮气来完成。
CCV线主要用来生产MV和HV电缆。
立式连续硫化(VCV)VCV技术中,硫化管是垂直导向的。
通过控制电缆的张力维持电缆在管的中心位置。
导体的馈送方式与CCV相似。
将导体牵引到机塔顶端,该塔高度可达100m,位于一个巨大的牵引轮的正上方,然后导体经由预热器进入到三层挤出机头。
通过高温氮气加热电缆来完成硫化。
气体加压是保证过氧化物的分解物不产生充气的微孔。
VCV技术中交联管道是垂直布置的,从而确保了导体和绝缘线芯的同心度。
在生产大截面(>1600mm2)导体电缆时,VCV技术非常有效,因为在保持张力方面,不会面临和CCV技术那样的困难。
VCV线可以用来生产绝缘厚度最大约35mm的电缆。
与CCV技术相比,VCV技术不会遭受由于重力的影响而使聚合物产生低垂或从导体滴落的结果。
然而,由于昂贵的立式建设成本,VCV线要短于CCV线。
VCV线一般为80~100m,而CCV线一般为140~200m。
由于同样的电缆需要相同的硫化时间,CCV线生产速度较快。
VCV线通常只用于HV和EHV电缆。
同CCV 生产线一样,VCV线的硫化媒质也使用高温高压的氮气。
但是生产HV电缆时,由于蒸汽硫化会导致绝缘中产生水分和大量的微孔,所以氮气是首选的媒质。
长承模连续硫化(MDCV)在MDCV工艺中,硫化管是在挤出机后水平布置的。
与CCV和VCV线不同的是,硫化管中不需要使用氮气来加热和硫化电缆。
MDCV工艺要求模具的外径等于电缆外径,因此电缆可以充满管道和模具。
把聚合物加热到熔融态以及以及进行交联时,产生的热膨胀造成的压力阻止了微孔的生成。
与CCV工艺相比,由于电缆被模具全部封套,MDCV工艺没有下垂的问题。
但是,在聚合物熔融而没有交联时,保证导体中心位置非常重要。
中心位置的保持,可以通过对一短段电缆施加很大的张力,使电缆处于真正的水平位置而达到。
这也降低了对长冷却管的需求。
也可以使用特殊的高粘度聚合物。
这些特殊的方法通常用于1000mm2以上的导体。
MDCV仅用于生产HV和EHV电缆。
3.2挤出-湿法交联工艺在湿法交联工艺中,采用同CCV生产线上把经过硫化的过氧化物混合物挤出到导体上的相似方法,把绝缘线芯的混合物挤出到导体上,但不用随后通过高温高压的硫化物。
与之相反,挤出后立即用水冷却电缆。
把电缆卷绕到线盘上后,放入到较高温度(约70~75℃)和温度的房间或者水浴中来完成交联。
湿法交联只有在不存在以及有合适的催化剂的条件下才能发生,因此它完全没有过氧化物交联工艺的热激发的预硫化等情况出现。
过氧化物交联工艺中,挤出停车和过于精细的滤网都会导致焦烧。
特别是用硅烷作为交联剂的聚合物。
在电力电缆制造中,湿法交联的挤出机更适合使用滤网(100~200μm孔径),而且适应于停车时没有过氧化物那种材料焦烧的危险。
3.3硫化-概述在过氧化物硫化工艺中,通过在钢质的硫化管内施加循环的高温、高压、通常是干燥的氮气来产生热和压力。
氮气的温度量级为300℃到450℃,压力是10kg/cm2。
高温导致了过氧化物反应形成交联网状结构。
在60m之后,表面温度迅速降低到接近室温,但是导体温度的下降十分缓慢。
高压促使交联过程中释放的气体保留在熔融态聚合物中,从而避免了产生微孔。