大型钢锭中的非金属夹杂物
ASTM_E45-1997钢中非金属夹杂物评定方法中文[1]
![ASTM_E45-1997钢中非金属夹杂物评定方法中文[1]](https://img.taocdn.com/s3/m/31d090226edb6f1afe001f17.png)
ASTM E45-05 钢中夹杂物含量的评定方法1 范围1.1 本标准的试验方法为测定锻钢中非金属夹杂物含量的方法。
宏观试验法包括微蚀、断口、台阶和磁粉法。
显微试验法通常包括5种检测。
根据夹杂物形状而不是化学特点,显微法将夹杂物划分为不同类型。
这里主要讨论了金相照相技术,它允许形状类似的夹杂物之间略有不同。
这些方法在主要用来评定夹杂物的同时,某些方法也可以评估诸如碳化物、氮化物、碳氮化物、硼化物和金属间化合物的组成。
除了钢以外,其它合金在有些情况下也可以应用这些方法。
根据这些方法在钢中的应用情况,将分别给予介绍。
1.2 本标准适用于人工评定夹杂物含量。
其他ASTM标准介绍了用JK评级图的自动法(ASTM E1122 )和图像分析法(ASTM E1245 )。
1.3 按照钢的类型和性能要求,可以采用宏观法或显微法,也可以将二者结合起来,以得到最佳结果。
1.4 这些试验方法仅仅为推荐方法,对任何级别的钢而言,这些方法都不能作为合格与否的判据。
1.5 本标准未注明与安全相关的事项,如果有的话,也只涉及本标准的使用。
标准使用者应建立适当的安全和健康操作规程,并且在使用标准前应确定其适用性。
2 参考文献2.1 ASTM标准:A 295 高碳耐磨轴承钢技术条件A 485 强淬透性耐磨轴承钢技术条件A 534 耐磨轴承用渗碳钢技术条件A 535 特种性能的滚珠和滚柱轴承钢技术条件A 756 耐磨轴承用不锈钢技术条件A 866 耐磨轴承用中碳钢技术条件D 96 用离心法分离原油中水和沉淀物的试验方法E 3 制备金相试样指南E 7 金相显微镜术语E 381 钢棒,钢坯,钢锭和锻件的宏观试验法E 709 磁粉检测指南E 768 自动测定钢中夹杂物的试样的制备和评定操作规程E 1122 用自动图像分析法获得JK夹杂物等级的操作规程E 1245 用自动图像分析法确定金属中夹杂物或第二相含量的操作规程2.2 SAE标准:J421,磁粉法测定钢的清洁度等级J422,钢中夹杂物评定的推荐操作规程2.3 航空材料技术条件2300,高级飞行性能钢的清洁度:磁粉检测程序2301,飞行性能钢的清洁度:磁粉检测程序2303,飞行性能钢的清洁度:耐腐蚀马氏体钢磁粉检测程序2304,特种飞行性能钢的清洁度:磁粉检测程序2.4 ISO标准:ISO 3763,锻钢——非金属夹杂物的宏观评定法ISO 4967,钢——使用标准图谱的非金属夹杂物显微评定方法2.5 ASTM附加标准:钢中夹杂物评级图Ⅰ-r和评级图Ⅱ低碳钢的4张显微照片3 术语3.1 定义:3.1.1 本标准中用到的定义,见ASTM E7 。
钢中非金属夹杂物介绍

• • • • • • • • • • • • • • • • • • • • • • • • • • • • • • • •
激励学生学习的名言格言 220、每一个成功者都有一个开始。勇于开始,才能找到成功的路。 221、世界会向那些有目标和远见的人让路(冯两努——香港著名推销商) 222、绊脚石乃是进身之阶。 223、销售世界上第一号的产品——不是汽车,而是自己。在你成功地把自己推销给别人之前,你必须百分之百的把自己推销给自己。 224、即使爬到最高的山上,一次也只能脚踏实地地迈一步。 225、积极思考造成积极人生,消极思考造成消极人生。 226、人之所以有一张嘴,而有两只耳朵,原因是听的要比说的多一倍。 227、别想一下造出大海,必须先由小河川开始。 228、有事者,事竟成;破釜沉舟,百二秦关终归楚;苦心人,天不负;卧薪尝胆,三千越甲可吞吴。 229、以诚感人者,人亦诚而应。 230、积极的人在每一次忧患中都看到一个机会,而消极的人则在每个机会都看到某种忧患。 231、出门走好路,出口说好话,出手做好事。 232、旁观者的姓名永远爬不到比赛的计分板上。 233、怠惰是贫穷的制造厂。 234、莫找借口失败,只找理由成功。(不为失败找理由,要为成功找方法) 235、如果我们想要更多的玫瑰花,就必须种植更多的玫瑰树。 236、伟人之所以伟大,是因为他与别人共处逆境时,别人失去了信心,他却下决心实现自己的目标。 237、世上没有绝望的处境,只有对处境绝望的人。 238、回避现实的人,未来将更不理想。 239、当你感到悲哀痛苦时,最好是去学些什么东西。学习会使你永远立于不败之地。 240、伟人所达到并保持着的高处,并不是一飞就到的,而是他们在同伴们都睡着的时候,一步步艰辛地向上爬 241、世界上那些最容易的事情中,拖延时间最不费力。 242、坚韧是成功的一大要素,只要在门上敲得够久、够大声,终会把人唤醒的。 243、人之所以能,是相信能。 244、没有口水与汗水,就没有成功的泪水。 245、一个有信念者所开发出的力量,大于99个只有兴趣者。 246、环境不会改变,解决之道在于改变自己。 247、两粒种子,一片森林。 248、每一发奋努力的背后,必有加倍的赏赐。 249、如果你希望成功,以恒心为良友,以经验为参谋,以小心为兄弟,以希望为哨兵。 250、大多数人想要改造这个世界,但却罕有人想改造自己。
钢中非金属夹杂物的分类
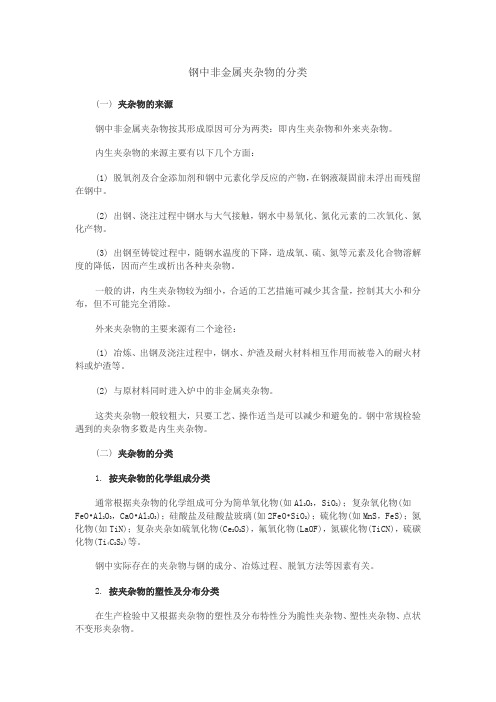
(4)半塑性夹杂物指各种复相的铝硅酸盐夹杂。基底铝硅酸盐有范性,热加工时延伸变形,但其中包含着的析出相如Al2O3等是脆性的,加工时保持原状或只是拉开距离。
除此之外,夹杂物还可根据化学稳定性的不同,分为易溶于稀酸,甚至在水中就能分解的不稳定夹杂物和在热的浓酸中才能溶解的稳定夹杂物。或按照钢的类型和成分分类等。
钢中非金属夹杂物的分类
(一)夹杂物的来源
钢中非金属夹杂物按其形成原因可分为两类:即内生夹杂物和外来夹杂物。
内生夹杂物的来源主要有以下几个方面:
(1) 脱氧剂及合金添加剂和钢中元素化学反应的产物,在钢液凝固前未浮出而残留在钢中。
(2) 出钢、浇注过程中钢水与大气接触,钢水中易氧化、氮化元素的二次氧化、氮化产物。
钢中实际存在的夹杂物与钢的成分、冶炼过程、脱氧方法等因验中又根据夹杂物的塑性及分布特性分为脆性夹杂物、塑性夹杂物、点状不变形夹杂物。
(1)塑性夹杂物热变形时具有良好的范性,沿变形方向延伸成条带状。属于这类的夹杂物有硫化物及含SiO2量较低的铁锰硅酸盐等。
(2)脆性夹杂物热加工时形状和尺寸都不变化,但可沿加工方向成串或点链状排列。属于这类的夹杂物有Al2O3,Cr2O3等。
(3) 出钢至铸锭过程中,随钢水温度的下降,造成氧、硫、氮等元素及化合物溶解度的降低,因而产生或析出各种夹杂物。
一般的讲,内生夹杂物较为细小,合适的工艺措施可减少其含量,控制其大小和分布,但不可能完全消除。
外来夹杂物的主要来源有二个途径:
(1) 冶炼、出钢及浇注过程中,钢水、炉渣及耐火材料相互作用而被卷入的耐火材料或炉渣等。
(2) 与原材料同时进入炉中的非金属夹杂物。
钢中非金属夹杂对质量的影响及控制措施
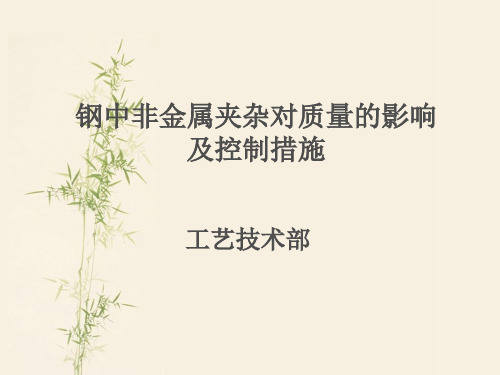
1) 液体钢的脱氧产物; 2) 钢液从浇注温度冷却到凝固温度过程中,由
于温度的降低使溶液中溶质的溶解度降低,
即钢水温度的变化使反应平衡移动,重新析 出脱氧产物;
3) 钢液冷凝时发生溶质树枝形偏析所析出的脱 氧产物;
4) 固相线温度以下钢继续冷却或者由于相变的
缘故,引起的夹杂物重新析出。
1.2
1.5
按化学成分分类
FeS、MnS
A类夹杂:硫化物
B类夹杂: 氧化铝、氧化铁 Al2O3+FeO C类夹杂:硅酸盐、氮化物 2MnO.SiO2 TiN、BN、NbN等 D类夹杂:球状氧化物类 小型氧化物 FeO、MnO、TiO2等
Ds类夹杂:单个大型球状氧化物类
1.6
钢中夹杂物的形貌
25
2.2夹杂物的检测
1.钢材出厂检验:
• • • ASTM标准(A、B、C、D、Ds类夹杂物); 用户标准(SKF、米其林、贝卡尔特等); 分析检验手段:光学显微镜。
2.科学研究:
• • 光学显微镜; 扫描电镜(+EDS);
•
• •
投射电镜(+EPMA、EDS);
图像分析; PDA(Pulse Distribution Analysis)。
炼钢钢坯
氧化铝+硫化钙
氧化铝
15102486N
氧化铁 视场50X
硫化钙
氧化铝
轧钢钢板
氮化物
2、非金属夹杂物对性能影响
使用性能的影响: 1、疲劳性能↓ 2、冲击韧性↓ 塑性↓ 3、耐腐蚀性↓
对工艺性能的影响: 1 、对锻造和冷加工、淬火加热和焊接过程 易开裂。 2 、轧制后表面质量以及磨削后零件表面粗 糙度降低。
金属冶炼过程中的非金属夹杂物控制

扫描电镜(SEM)
总结词
扫描电镜是一种高分辨率的显微镜,能够观察金属材料表面和内部的微观结构,适用于非金属夹杂物的检测和表 征。
详细描述
扫描电镜利用电子束扫描金属材料的表面,通过收集和分析反射回来的电子信号,形成高分辨率的图像。该方法 能够观察夹杂物的形貌、大小、分布和成分等信息,具有较高的精度和分辨率。
对金属材料性能的影响
力学性能
非金属夹杂物会降低金属的力学性能,如强度、韧性、疲劳寿命等 。夹杂物的存在会导致应力集中,降低材料的抗拉强度和疲劳极限 。
物理性能
非金属夹杂物对金属的物理性能也有显著影响。例如,夹杂物会降 低金属的导电性、导热性和磁性等。
工艺性能
非金属夹杂物还会影响金属的加工性能,如焊接、热处理、塑性加工 等。夹杂物的存在可能导致焊缝开裂、热处理时组织不均匀等问题。
X射线衍射(XRD)
总结词
X射线衍射是一种用于分析金属材料 晶体结构和相组成的检测方法,可以 用于非金属夹杂物的鉴别和定量分析 。
详细描述
X射线衍射利用X射线照射金属材料, 通过分析衍射图谱来判断材料的晶体 结构和相组成。该方法能够鉴别夹杂 物的矿物组成和含量,具有较高的精 度和可靠性。
04
非金属夹杂物的控制技术与实践
金属冶炼过程中的非金属 夹杂物控制
汇报人:可编辑 2024-01-06
目录
• 非金属夹杂物的基本概述 • 非金属夹杂物的来源与控制策略 • 非金属夹杂物检测与表征技术 • 非金属夹杂物的控制技术与实践 • 非金属夹杂物控制的效果评估与优化建议 • 案例分析:某钢厂非金属夹杂物控制实践
01
非金属夹杂物的基本概述
定期检查熔炼炉内衬,确保其完 好无损,防止剥落物混入金属溶 液。
钢中非金属夹杂物的鉴定

钢中非金属夹杂物的鉴定随着现代工程技术的发展,对钢的综合性能要求也日趋严格,相应地对钢的材质要求也越来越高。
非金属夹杂物作为独立相存在于钢中,破坏了钢基体的连续性,加大了钢中组织的不均匀性,严重影响了钢的各种性能。
例如,非金属夹杂物导致应力集中,引起疲劳断裂[1-3];数量多且分布不均匀的夹杂物会明显降低钢的塑性、韧性、焊接性以及耐腐蚀性;钢中呈网状存在的硫化物会造成热脆性。
因此,夹杂物的数量和分布被认定是评定钢材质量的一个重要指标,并且被列为优质钢和高级优质钢出厂的常规检测项目之一。
非金属夹杂物的性质、形态、分布、尺寸及含量不同,对钢性能的影响也不同。
所以提高金属材料的质量,生产出洁净钢,或控制非金属夹杂物性质和要求的形态,是冶炼和铸锭过程中的一个艰巨任务。
而对于金相分析工作者来说,如何正确判断和鉴定非金属夹杂物也因此变得十分重要。
1 钢中非金属夹杂物的来源分类1.1 内生夹杂物钢在冶炼过程中,脱氧反应会产生氧化物和硅酸盐等产物,若在钢液凝固前未浮出,将留在钢中。
溶解在钢液中的氧、硫、氮等杂质元素在降温和凝固时,由于溶解度的降低,与其他元素结合以化合物形式从液相或固溶体中析出,最后留在钢锭中,它是金属在熔炼过程中,各种物理化学反应形成的夹杂物[10-15]。
内生夹杂物分布比较均匀,颗粒也较小,正确的操作和合理的工艺措施可以减少其数量和改变其成分、大小和分布情况,但一般来说是不可避免的。
1.2 外来夹杂物钢在冶炼和浇注过程中悬浮在钢液表面的炉渣、或由炼钢炉、出钢槽和钢包等内壁剥落的耐火材料或其他夹杂物在钢液凝固前未及时清除而留于钢中。
它是金属在熔炼过程中与外界物质接触发生作用产生的夹杂物[10-15]。
如炉料表面的砂土和炉衬等与金属液作用,形成熔渣而滞留在金属中,其中也包括加入的熔剂。
这类夹杂物一般的特征是外形不规则,尺寸比较大,分布也没有规律,又称为粗夹杂。
这类夹杂物通过正确的操作是可以避免的。
钢中的非金属夹杂物

什么是非金属夹杂?钢中非金属夹杂物,如氧化物、硫化物、硅酸盐、氮化物等一般都呈独立相存在,主要是由炼钢中的脱氧产物和钢凝固时由于一系列物化反应所形成的各种夹杂物组成。
非金属夹杂的影响非金属夹杂物的存在,破坏了钢基体的连续性,使钢组织的不均匀性增大。
一般来说钢中非金属夹杂物,对钢的性能产生不良影响,如降低钢的塑性、韧性和疲劳性能,使钢的冷热加工性能乃至某些物理性能变坏等。
因此评定钢中夹杂物类别、级别对保证钢材质量十分重要。
分类按夹杂物的化学成分:氧化物、硫化物及氮化物。
根据夹杂物的可塑性:塑性夹杂物、脆性夹杂物、不变形夹杂物及半塑性夹杂物。
● 塑性夹杂物钢中塑性夹杂物在钢经受加工变形时具有良好塑性,沿着钢的流变方向延伸成条带状。
● 脆性夹杂物指那些不具有塑性的简单氧化物和复杂氧化物以及氮化物。
●不变形夹杂物这类夹杂物在铸态的钢中呈球状,而在钢凝固并经形变加工后,夹杂物保持球形不变。
● 半塑性夹杂物指各种多相的铝硅酸盐夹杂物。
其中作为基底的夹杂物(铝硅酸盐玻璃)一般当钢在热加工时具有塑性,但是在这基底上分布的析出相晶体(如Al2O3、尖晶石类氧化物)的塑性很差。
钢经热变形后,塑性夹杂物相(基底)随钢变形而延伸,但脆性的夹杂物相不变形,仍保持原来形状,只是彼此之间的距离被拉长。
按夹杂物的来源:内生夹杂物、外来夹杂物。
● 内生夹杂物在钢的熔炼、凝固过程中,脱氧、脱硫产物,以及随温度下降,S、O、N等杂质元素的溶解度下降,于是这些不溶解的杂质元素就形成非金属化合物在钢中沉淀析出,最后留在钢锭中。
内生夹杂物分布相对均匀,颗粒一般比较细小。
可以通过合理的熔炼工艺来控制其数量、分布和大小等,但一般来讲内生夹杂物总是存在的。
● 外来夹杂物炉衬耐火材料或炉渣等在钢的冶炼、出钢、浇铸过程中进入钢中来不及上浮而滞留在钢中称为外来夹杂物。
其特征是:外形不规则、尺寸比较大,偶尔在这里或在那里出现,正确的操作可以避免或减少钢中外来夹杂物的入侵。
钢中非金属夹杂物控制研究进展
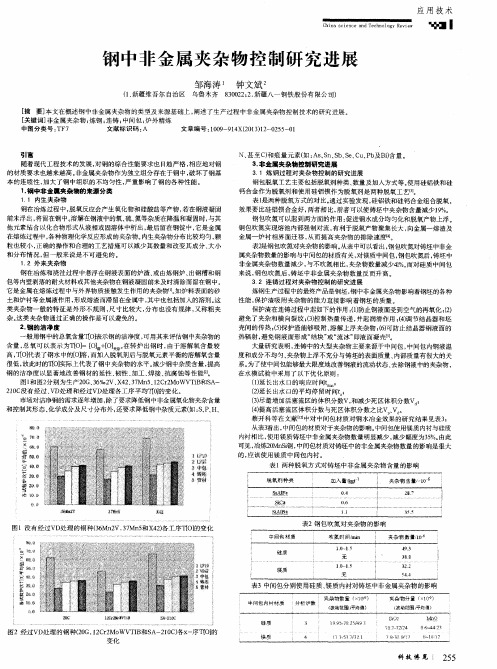
N、 甚至c ) 和痕 量 元素 ( 如: As 、 S n 、 S b、 S e 、 C u 、 P b 及B i ) 含量 。 3 . 非 金属夹 杂 物控制 研 究进展 3 1 炼钢过 程对 夹杂物 控制 的研 究进展
钢包脱 氧工 艺主 要包括 脱氧剂 种类 、 数量 及 加入方 式等 。 使用硅 铝铁 和硅 钙 合金 作为 脱氧 剂和 使用 硅铝 钡作 为脱 氧剂 是 两种脱 氧 工艺 。 表1 是两 种脱 氧方 式的对 比。 通过 实验 发现 , 硅铝 铁和硅 钙合 金组合 脱氧 , 效果 要 比硅 铝钡 合金好 , 两者相 比, 前者 可以使 铸坯 中夹杂 物含 量减 少 1 9 %。 钢 包 吹氮可 以起到 两方 面的作用 : 促进钢 水成分 均匀 化和脱 氧产 物上浮 。 钢包 吹氮 实现熔 池 内部强 制对 流 , 有 利于脱 氧产 物聚 集长 大 , 向金属 一熔 渣及 金属 一 炉衬 相界 面迁 移 , 从 而提高 夹 杂物 的排 除速 度[ 4 1 。 表 堤 钢包 吹氮对夹杂 物 的影响。 从表 中可 以看出 , 钢包 吹氮对铸坯 中非 金 属夹 杂物数量 的影 响与 中间包 的材 质有关 , 对镁质 中间包 , 钢包 吹氮 后 , 铸坯中 非 金属夹 杂物 数量减 少 , 与不 吹氮相 比, 夹杂 物数量 减少4 1 %。 而对 硅质 中 间包
钢在冶 炼过程 中, 脱 氧反应 会产 生氧化 物和 硅酸盐 等产 物 , 若 在钢 液凝 固 前未 浮出 , 将 留在 钢 中。 溶解 在钢液 中 的氧 、 硫、 氮 等杂质在 降温和 凝 固时, 与 其 他元 素结 合 以化合 物形 式从液 相或 固溶体 中析 出 , 最后 留在钢 锭 中 , 它 是金 属 在熔 炼过程 中 , 各 种物理 化学 反应形成 的夹杂 物。 内生夹杂 物分布 比较 均匀 , 颗 粒 也较小 , 正确 的操作 和合理 的工 艺措 施可 以减少 其数量 和 改变其 成分 、 大 小
- 1、下载文档前请自行甄别文档内容的完整性,平台不提供额外的编辑、内容补充、找答案等附加服务。
- 2、"仅部分预览"的文档,不可在线预览部分如存在完整性等问题,可反馈申请退款(可完整预览的文档不适用该条件!)。
- 3、如文档侵犯您的权益,请联系客服反馈,我们会尽快为您处理(人工客服工作时间:9:00-18:30)。
大型钢锭中的非金属夹杂物
二次炼钢技术的充分使用已使重要的大型锻件用钢的纯净度产生了飞跃的进步。
与之相应的铸锭技术和措施也已取得了较大的发展和广泛地应用。
这些成就解决了重要大锻件用大型钢锭中的气体、夹杂物和偏析问题。
它代表了当代大型锻件的质量水平。
然而,由于二次炼钢技术与铸锭技术的高成本的限制,不可能全部覆盖普通大锻件的生产中。
再者,制造厂家力图用简单、恰当地工艺方法生产出符合技术要求的大锻件。
这样,在普通大锻件生产中,对上述影响锻件质量的问题,仍具有普遍意义。
关于钢中夹杂物的生成和去除以及它在锻压、热处理过程中的变化,对锻件性能的影响等问题;已经在第一节中进行了讨论,这里着重讨论钢锭中的夹杂物。
钢液经过出钢注入钢包中以及随后浇注到钢锭模中,其中非金属夹杂物根据斯托克斯定律不断的上浮。
但是,由于出钢和浇注时钢液的搅动,对耐火材料的浸蚀和钢液的二次氧化过程,钢液中夹杂物又不断增加。
实际上钢液中非金属夹杂物的变化不大。
因之,要求钢液在钢包中必须有足够长的静置时间,以促使较大尺寸的夹杂物上浮,对减少夹杂物是有利的。
氧化铝夹杂和一部分硅酸盐类夹杂在钢液凝固以前,是以固体顆粒的形式悬浮于钢液中。
而硫化物夹杂和一部分硅酸盐夹杂是在钢液的凝固过程中不断析出的。
凝固中由于钢锭模壁冷却产生搅动等的影响,悬浮于钢液中的氧化物等难熔夹杂物在钢锭中的分布是不均匀的。
而硫化物夹杂则主要决定于偏析过程,在正偏析区富集更多的硫化物,越向钢锭中心和越接近冒口,硫化物夹杂的含量越高。
上述是夹杂物在钢锭中的一般情况。
而目前在普通大锻件用大型钢锭的生产中,时而发现有粗大、密集的夹杂物。
其大小往往达到几毫米,现在它完全可以里超声波探伤的方法检测出来。
粗大的夹杂物具有最大的危害性。
根据断裂力学的概念,当夹杂物的尺寸超过某一临界尺寸时,作为现成裂缝可能在应力作用下,使锻件疲劳断裂。
较小的来杂物单个存在时,危害性不大。
但是当成链状或团状的密集状态时,则危害性大大增加。
所以,在大锻件技术标准中,对粗大夹杂物和密集夹杂物都作了严格的限制。
这些粗大的夹杂物主要是氧化物类夹杂,其成分除含有大量的SiO2和AI203,以及MnO、FeO以外,还发现有CaO和MgO。
后者的存在,证明了这些夹杂物是耐火材料被浸蚀而混入钢液的结果。
资料[103]研究分析了大气浇注的39个45.7t到87t钢锭的30Cr2MoV钢中的三种粗大堆积夹杂物:粘连片状夹杂、堆聚粗颗粒夹杂和大块硅酸盐夹杂。
它们的存在是引起锻件探伤致废的主要原因。
粘连片状夹杂,其组成是以铝的氧化物为主,含有一些SiO2和MnO,可见到硅酸盐颗粒与铝酸盐颗粒粘连混杂。
A1203是脱氧过程以固态直接从钢液中结晶出来。
_它上浮时和由钢液氧化形成的硅酸盐薄膜在表面相结合,受钢流搅动而又卷入钢内,在钢液中形成粘连片状。
锻件检验中可发现不同程度的缺陷。
堆聚颗粒夹杂:其组成是A1203为主的夹杂物,形态呈规则的棱角形结晶。
另外有高透明的玻璃质,它是含有SiO2硅酸盐。
其中Ca0、Na20的含量也较多。
它是在高温钢液流动性良好的条件下产生的,故以颗粒状存在于钢中。
探伤发现当量尺寸约在Φ2?4mm 范围内。
大块硅酸盐夹杂:其组成含有CaO 20%~40%、较多的Na20、较少的Al203、Si02 和MnO,表明大块硅酸盐来自飘浮在钢锭模钢液表面的渣液。
锻件探伤可发现不同程度的缺陷。
这些粗大夹杂物的堆聚,尤其在钢锭水口端的堆聚,除了结晶下沉或缓凝富集是凝固过程中的普遍规律,此外还有钢流或下落的硬壳将夹杂物带入底部所形成。
资料[104]认为铸锭工艺的改善是防止形成钢中粗大夹杂物的关键。
如:防止钢液的二次氧化措施;研究改变粉渣的组成、加入
方法;冒口发热剂的选择与应用;防止表面浮渣混入等。
资料[105]对真空铸锭的4个锭身直径3404mm、高度3810mm的3.5%NiCrMoV钢锭的研究认为:钢锭底部存在的粗大夹杂物是由冒口最初凝固的渣壳和保温帽周壁的塌陷物掉入锭身造成的。
只要保持冒口渣壳和侧壁在钢锭凝固以前不道破损,就不至出现那些粗大的夹杂物。
大型钢锭中的粗大夹杂物问题,在采用恰当的铸锭工艺和防止浇注过程中的污染措施以后,是可以解决的。