Analysis of failed aircraft wheel assembly
Info-Note-5-Doc9803alltext航线安全审计.en
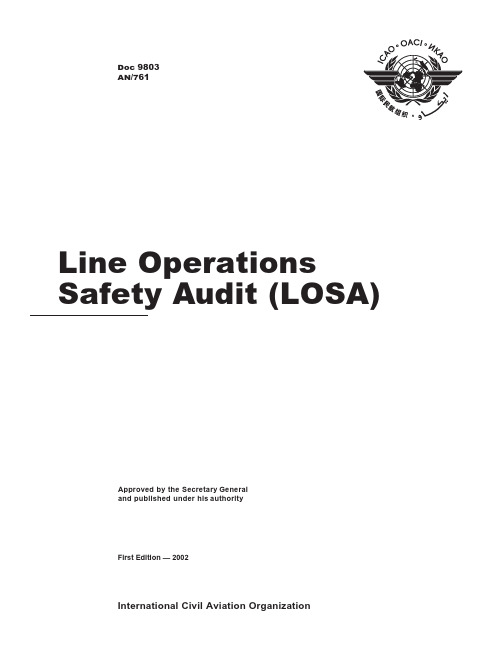
Approved by the Secretary General and published under his authorityLine OperationsSafety Audit (LOSA)First Edition — 2002Doc 9803AN/761AMENDMENTSThe issue of amendments is announced regularly in the ICAO Journal and in the monthly Supplement to the Catalogue of ICAO Publications and Audio-visual Training Aids, which holders of this publication should consult. The space below is provided to keep a record of such amendments.RECORD OF AMENDMENTS AND CORRIGENDA AMENDMENTS CORRIGENDANo.DateapplicableDateenteredEnteredby No.Dateof issueDateenteredEnteredbyTABLE OF CONTENTSPage PageForeword . . . . . . . . . . . . . . . . . . . . . . . . . . . . . . . . . .(v) Acronyms and Abbreviations . . . . . . . . . . . . . . . . .(vi) Introduction. . . . . . . . . . . . . . . . . . . . . . . . . . . . . . . .(vii) Chapter 1.Basic error management concepts. .1-11.1Introduction . . . . . . . . . . . . . . . . . . . . . . . . .1-11.2Background . . . . . . . . . . . . . . . . . . . . . . . . .1-2Reactive strategies. . . . . . . . . . . . . . . . . .1-2Combined reactive/proactive strategies. .1-2Proactive strategies . . . . . . . . . . . . . . . . .1-41.3 A contemporary approach to operationalhuman performance and error. . . . . . . . . . .1-51.4The role of the organizational culture . . . .1-71.5Conclusion. . . . . . . . . . . . . . . . . . . . . . . . . .1-7 Chapter2.Implementing LOSA . . . . . . . . . . . . .2-12.1History of LOSA. . . . . . . . . . . . . . . . . . . . .2-12.2The Threat and Error Management Model.2-1Threats and errors defined. . . . . . . . . . . .2-1Definitions of crew error response . . . . .2-4Definitions of error outcomes. . . . . . . . .2-4Undesired Aircraft States . . . . . . . . . . . .2-42.3LOSA operating characteristics . . . . . . . . .2-5Observer assignment . . . . . . . . . . . . . . . .2-7Flight crew participation. . . . . . . . . . . . .2-72.4How to determine the scope of a LOSA . .2-72.5Once the data is collected. . . . . . . . . . . . . .2-82.6Writing the report . . . . . . . . . . . . . . . . . . . .2-82.7Success factors for LOSA. . . . . . . . . . . . . .2-8Chapter3.LOSA and the safety changeprocess (SCP) . . . . . . . . . . . . . . . . . . . . . . . . . . . . . .3-13.1Introduction . . . . . . . . . . . . . . . . . . . . . . . . .3-13.2 A constantly changing scene. . . . . . . . . . . .3-13.3One operator’s example of an SCP . . . . . .3-2 Chapter4.How to set up a LOSA —US Airways experience . . . . . . . . . . . . . . . . . . . . . .4-14.1Gathering information. . . . . . . . . . . . . . . . .4-14.2Interdepartmental support . . . . . . . . . . . . . .4-14.3LOSA steering committee. . . . . . . . . . . . . .4-1Safety department . . . . . . . . . . . . . . . . . .4-1Flight operations and trainingdepartments . . . . . . . . . . . . . . . . . . . . . . .4-2Pilots union . . . . . . . . . . . . . . . . . . . . . . .4-24.4The key steps of a LOSA. . . . . . . . . . . . . .4-2Goals . . . . . . . . . . . . . . . . . . . . . . . . . . . .4-2Action plan . . . . . . . . . . . . . . . . . . . . . . .4-24.5The keys to an effective LOSA . . . . . . . . .4-4Confidentiality and no-jeopardy. . . . . . .4-4The role of the observer . . . . . . . . . . . . .4-54.6Promoting LOSA for flight crews . . . . . . .4-5 Appendix A — Examples of the various forms utilized by LOSA . . . . . . . . . . . . . . . . . . . . . . . . . . .A-1 Appendix B — Example of an introductory letterby an airline to its flight crews. . . . . . . . . . . . . . . .B-1 Appendix C — List of recommended readingand reference material. . . . . . . . . . . . . . . . . . . . . . .C-1FOREWORDThe safety of civil aviation is the major objective of the International Civil Aviation Organization (ICAO). Consider-able progress has been made in increasing safety, but additional improvements are needed and can be achieved. It has long been known that the majority of aviation accidents and incidents result from less than optimum human per-formance, indicating that any advance in this field can be expected to have a significant impact on the improvement of aviation safety.This was recognized by the ICAO Assembly, which in 1986 adopted Resolution A26-9 on Flight Safety and Human Factors. As a follow-up to the Assembly Resolution, the Air Navigation Commission formulated the following objective for the task:“To improve safety in aviation by making States more aware and responsive to the importance of Human Factors in civil aviation operations through the provision of practical Human Factors materials and measures, developed on the basis of experience in States, and by developing and recommending appropriate amendments to existing material in Annexes and other documents with regard to the role of Human Factors in the present and future operational environments. Special emphasis will be directed to the Human Factors issues that may influence the design, transition and in-service use of the future ICAO CNS/A TM systems.”One of the methods chosen to implement Assembly Resolution A26-9 is the publication of guidance materials, including manuals and a series of digests, that address various aspects of Human Factors and its impact on aviation safety. These documents are intended primarily for use by States to increase the awareness of their personnel of the influence of human performance on safety.The target audience of Human Factors manuals and digests are the managers of both civil aviation administrations and the airline industry, including airline safety, training and operational managers. The target audience also includes regulatory bodies, safety and investigation agencies and training establishments, as well as senior and middle non-operational airline management.This manual is an introduction to the latest information available to the international civil aviation community on the control of human error and the development of counter-measures to error in operational environments. Its target audience includes senior safety, training and operational personnel in industry and regulatory bodies.This manual is intended as a living document and will be kept up to date by periodic amendments. Subsequent editions will be published as new research results in increased knowledge on Human Factors strategies and more experience is gained regarding the control and management of human error in operational environments.ACRONYMS AND ABBREVIATIONS ADS Automatic Dependent SurveillanceA TC Air Traffic ControlCFIT Controlled Flight Into TerrainCNS/A TM Communications, Navigation and Surveillance/Air Traffic Management CPDLC Controller-Pilot Data Link CommunicationsCRM Crew Resource ManagementDFDR Digital Flight Data RecorderETOPS Extended Range Operations by Twin-engined AeroplanesFAA Federal Aviation AdministrationFDA Flight Data AnalysisFMS Flight Management SystemFOQA Flight Operations Quality AssuranceICAO International Civil Aviation OrganizationLOSA Line Operations Safety AuditMCP Mode Control PanelQAR Quick Access RecorderRTO Rejected Take-OffSCP Safety Change ProcessSOPs Standard Operating ProceduresTEM Threat and Error ManagementUTTEM University of Texas Threat and Error ManagementINTRODUCTION1.This manual describes a programme for the management of human error in aviation operations known as Line Operations Safety Audit (LOSA). LOSA is proposed as a critical organizational strategy aimed at developing countermeasures to operational errors. It is an organizational tool used to identify threats to aviation safety, minimize the risks such threats may generate and implement measures to manage human error in operational contexts. LOSA enables operators to assess their level of resilience to systemic threats, operational risks and front-line personnel errors, thus providing a principled, data-driven approach to prioritize and implement actions to enhance safety.2.LOSA uses expert and highly trained observers to collect data about flight crew behaviour and situational factors on “normal” flights. The audits are conducted under strict no-jeopardy conditions; therefore, flight crews are not held accountable for their actions and errors that are observed. During flights that are being audited, observers record and code potential threats to safety; how the threats are addressed; the errors such threats generate; how flight crews manage these errors; and specific behaviours that have been known to be associated with accidents and incidents.3.LOSA is closely linked with Crew Resource Management (CRM) training. Since CRM is essentially error management training for operational personnel, data from LOSA form the basis for contemporary CRM training refocus and/or design known as Threat and Error Man-agement (TEM) training. Data from LOSA also provide a real-time picture of system operations that can guide organizational strategies in regard to safety, training and operations. A particular strength of LOSA is that it identifies examples of superior performance that can be reinforced and used as models for training. In this way, training inter-ventions can be reshaped and reinforced based on successful performance, that is to say, positive feedback. This is indeed a first in aviation, since the industry has traditionally collected information on failed human performance, such as in accidents and incidents. Data collected through LOSA are proactive and can be immediately used to prevent adverse events.4.LOSA is a mature concept, yet a young one. LOSA was first operationally deployed following the First LOSA Week, which was hosted by Cathay Pacific Airways in Cathay City, Hong Kong, from 12 to 14 March 2001. Although initially developed for the flight deck sector, there is no reason why the methodology could not be applied to other aviation operational sectors, including air traffic control, maintenance, cabin crew and dispatch.5.The initial research and project definition was a joint endeavour between The University of Texas at Austin Human Factors Research Project and Continental Airlines, with funding provided by the Federal Aviation Admin-istration (FAA). In 1999, ICAO endorsed LOSA as the primary tool to develop countermeasures to human error in aviation operations, developed an operational partnership with The University of Texas at Austin and Continental Airlines, and made LOSA the central focus of its Flight Safety and Human Factors Programme for the period 2000 to 2004.6.As of February 2002, the LOSA archives contained observations from over 2 000 flights. These observations were conducted within the United States and internationally and involved four United States and four non-United States operators. The number of operators joining LOSA has constantly increased since March 2001 and includes major international operators from different parts of the world and diverse cultures.7.ICAO acts as an enabling partner in the LOSA programme. ICAO’s role includes promoting the importance of LOSA to the international civil aviation community; facilitating research in order to collect necessary data; acting as a cultural mediator in the unavoidably sensitive aspects of data collection; and contributing multicultural obser-vations to the LOSA archives. In line with these objectives, the publication of this manual is a first step at providing information and, therefore, at increasing awareness within the international civil aviation community about LOSA.8.This manual is an introduction to the concept, methodology and tools of LOSA and to the potential remedial actions to be undertaken based on the data collected under LOSA. A very important caveat must be introduced at this point: this manual is not intended to convert readers into instant expert observers and/or LOSA auditors. In fact, it is strongly recommended that LOSA not be attempted without a formal introduction to it for the(viii)Line Operations Safety Audit (LOSA)following reasons. First, the forms presented in Appendix A are for illustration purposes exclusively, since they are periodically amended on the basis of experience gained and feedback obtained from continuing audits. Second, formal training in the methodology, in the use of LOSA tools and, most important, in the handling of the highly sensitive data collected by the audits is absolutely essential. Third, the proper structuring of the data obtained from the audits is of paramount importance.9.Therefore, until extensive airline experience is accumulated, it is highly desirable that LOSA training be coordinated through ICAO or the founding partners of the LOSA project. As the methodology evolves and reaches full maturity and broader industry partnerships are developed, LOSA will be available without restrictions to the international civil aviation community.10.This manual is designed as follows:•Chapter 1 includes an overview on safety, and human error and its management in aviationoperations. It provides the necessary backgroundinformation to understand the rationale for LOSA.•Chapter 2 discusses the LOSA methodology and provides a guide to the implementation of LOSAwithin an airline. It also introduces a model of crewerror management and proposes the error classi-fication utilized by LOSA, which is essentiallyoperational and practical.•Chapter 3 discusses the safety change process that should take place following the implementation ofLOSA.•Chapter 4 introduces the example of one operator’s experience in starting a LOSA.•Appendix A provides examples of the various forms utilized by LOSA.•Appendix B provides an example of an introductory letter by an airline to its flight crews.•Appendix C provides a list of recommended reading and reference material.11.This manual is a companion document to the Human Factors Training Manual (Doc 9683). The cooperation of the following organizations in the production of this manual is acknowledged: The University of Texas at Austin Human Factors Research Project, Continental Airlines, US Airways and ALPA, International. Special recognition is given to Professor Robert L. Helmreich, James Klinect and John Wilhelm of The University of Texas at Austin Human Factors Research Project; Captains Bruce Tesmer and Donald Gunther of Continental Airlines; Captains Ron Thomas and Corkey Romeo of US Airways; and Captain Robert L. Sumwalt III of US Airways and of ALPA, International.Chapter 1BASIC ERROR MANAGEMENT CONCEPTS1.1INTRODUCTION1.1.1Historically, the way the aviation industry has investigated the impact of human performance on aviation safety has been through the retrospective analyses of those actions by operational personnel which led to rare and drastic failures. The conventional investigative approach is for investigators to trace back an event under consideration to a point where they discover particular actions or decisions by operational personnel that did not produce the intended results and, at such point, conclude human error as the cause. The weakness in this approach is that the conclusion is generally formulated with a focus on the outcome, with limited consideration of the processes that led up to it. When analysing accidents and incidents, investigators already know that the actions or decisions by operational personnel were “bad” or “inappropriate”, because the “bad” outcomes are a matter of record. In other words, investigators examining human performance in safety occurrences enjoy the benefit of hindsight. This is, however, a benefit that operational personnel involved in accidents and incidents did not have when they selected what they thought of as “good” or “appropriate” actions or decisions that would lead to “good” outcomes.1.1.2It is inherent to traditional approaches to safety to consider that, in aviation, safety comes first. In line with this, decision making in aviation operations is considered to be 100 per cent safety-oriented. While highly desirable, this is hardly realistic. Human decision making in operational contexts is a compromise between production and safety goals (see Figure 1-1). The optimum decisions to achieve the actual production demands of the operational task at hand may not always be fully compatible with the optimumFigure 1-1.Operational Behaviours — Accomplishing the system’s goals1-2Line Operations Safety Audit (LOSA)decisions to achieve theoretical safety demands. All production systems — and aviation is no exception —generate a migration of behaviours: due to the need for economy and efficiency, people are forced to operate at the limits of the system’s safety space. Human decision making in operational contexts lies at the intersection of production and safety and is therefore a compromise. In fact, it might be argued that the trademark of experts is not years of experience and exposure to aviation operations, but rather how effectively they have mastered the necessary skills to manage the compromise between production and safety. Operational errors are not inherent in a person, although this is what conventional safety knowledge would have the aviation industry believe. Operational errors occur as a result of mismanaging or incorrectly assessing task and/or situ-ational factors in a specific context and thus cause a failed compromise between production and safety goals.1.1.3The compromise between production and safety is a complex and delicate balance. Humans are generally very effective in applying the right mechanisms to successfully achieve this balance, hence the extraordinary safety record of aviation. Humans do, however, occasionally mismanage or incorrectly assess task and/or situational factors and fail in balancing the compromise, thus contributing to safety breakdowns. Successful compromises far outnumber failed ones; therefore, in order to understand human performance in context, the industry needs to systematically capture the mechanisms underlying suc-cessful compromises when operating at the limits of the system, rather than those that failed. It is suggested that understanding the human contribution to successes and failures in aviation can be better achieved by monitoring normal operations, rather than accidents and incidents. The Line Operations Safety Audit (LOSA) is the vehicle endorsed by ICAO to monitor normal operations.1.2BACKGROUNDReactive strategiesAccident investigation1.2.1The tool most often used in aviation to document and understand human performance and define remedial strategies is the investigation of accidents. However, in terms of human performance, accidents yield data that are mostly about actions and decisions that failed to achieve the successful compromise between production and safety discussed earlier in this chapter.1.2.2There are limitations to the lessons learned from accidents that might be applied to remedial strategies vis-à-vis human performance. For example, it might be possible to identify generic accident-inducing scenarios such as Controlled Flight Into Terrain (CFIT), Rejected Take-Off (RTO), runway incursions and approach-and-landing acci-dents. Also, it might be possible to identify the type and frequency of external manifestations of errors in these generic accident-inducing scenarios or discover specific training deficiencies that are particularly related to identified errors. This, however, provides only a tip-of-the-iceberg perspective. Accident investigation, by definition, concen-trates on failures, and in following the rationale advocated by LOSA, it is necessary to better understand the success stories to see if they can be incorporated as part of remedial strategies.1.2.3This is not to say that there is no clear role for accident investigation within the safety process. Accident investigation remains the vehicle to uncover unanticipated failures in technology or bizarre events, rare as they may be. Accident investigation also provides a framework: if only normal operations were monitored, defining unsafe behaviours would be a task without a frame of reference. Therefore, properly focused accident investigation can reveal how specific behaviours can combine with specific circumstances to generate unstable and likely catastrophic scenarios. This requires a contemporary approach to the investigation: should accident investigation be restricted to the retrospective analyses discussed earlier, its contribution in terms of human error would be to increase existing industry databases, but its usefulness in regard to safety would be dubious. In addition, the information could possibly provide the foundations for legal action and the allocation of blame and punishment.Combined reactive/proactive strategies Incident investigation1.2.4 A tool that the aviation industry has increasingly used to obtain information on operational human perform-ance is incident reporting. Incidents tell a more complete story about system safety than accidents do because they signal weaknesses within the overall system before the system breaks down. In addition, it is accepted that incidents are precursors of accidents and that N-number of incidents of one kind take place before an accident of the same kind eventually occurs. The basis for this can be traced back almost 30 years to research on accidents from different industries, and there is ample practical evidence that supports this research. There are, nevertheless, limitationsChapter 1.Basic error management concepts1-3on the value of the information on operational human performance obtained from incident reporting.1.2.5First, reports of incidents are submitted in the jargon of aviation and, therefore, capture only the external manifestations of errors (for example, “misunderstood a frequency”, “busted an altitude”, and “misinterpreted a clearance”). Furthermore, incidents are reported by the individuals involved, and because of biases, the reported processes or mechanisms underlying errors may or may not reflect reality. This means that incident-reporting systems take human error at face value, and, therefore, analysts are left with two tasks. First, they must examine the reported processes or mechanisms leading up to the errors and establish whether such processes or mechanisms did indeed underlie the manifested errors. Then, based on this relatively weak basis, they must evaluate whether the error manage-ment techniques reportedly used by operational personnel did indeed prevent the escalation of errors into a system breakdown.1.2.6Second, and most important, incident reporting is vulnerable to what has been called “normalization of deviance”. Over time, operational personnel develop infor-mal and spontaneous group practices and shortcuts to circumvent deficiencies in equipment design, clumsy pro-cedures or policies that are incompatible with the realities of daily operations, all of which complicate operational tasks. These informal practices are the product of the collective know-how and hands-on expertise of a group, and they eventually become normal practices. This does not, however, negate the fact that they are deviations from procedures that are established and sanctioned by the organization, hence the term “normalization of deviance”. In most cases normalized deviance is effective, at least temporarily. However, it runs counter to the practices upon which system operation is predicated. In this sense, like any shortcut to standard procedures, normalized deviance carries the potential for unanticipated “downsides” that might unexpectedly trigger unsafe situations. However, since they are “normal”, it stands to reason that neither these practices nor their downsides will be recorded in incident reports.1.2.7Normalized deviance is further compounded by the fact that even the most willing reporters may not be able to fully appreciate what are indeed reportable events. If operational personnel are continuously exposed to sub-standard managerial practices, poor working conditions and/or flawed equipment, how could they recognize such factors as reportable problems?1.2.8Thus, incident reporting cannot completely reveal the human contribution to successes or failures in aviation and how remedial strategies can be improved to enhance human performance. Incident reporting systems are certainly better than accident investigations in understanding system performance, but the real challenge lies in taking the next step — understanding the processes underlying human error rather than taking errors at face value. It is essential to move beyond the visible manifestations of error when designing remedial strategies. If the aviation industry is to be successful in modifying system and individual per-formance, errors must be considered as symptoms that suggest where to look further. In order to understand the mechanisms underlying errors in operational environments, flaws in system performance captured through incident reporting should be considered as symptoms of mismatches at deeper layers of the system. These mismatches might be deficiencies in training systems, flawed person/technology interfaces, poorly designed procedures, corporate pressures, poor safety culture, etc. The value of the data generated by incident reporting systems lies in the early warning about areas of concern, but such data do not capture the concerns themselves.Training1.2.9The observation of training behaviours (during flight crew simulator training, for example) is another tool that is highly valued by the aviation industry to understand operational human performance. However, the “production”component of operational decision making does not exist under training conditions. While operational behaviours during line operations are a compromise between production and safety objectives, training behaviours are absolutely biased towards safety. In simpler terms, the compromise between production and safety is not a factor in decision making during training (see Figure 1-2). Training behaviours are “by the book”.1.2.10Therefore, behaviours under monitored conditions, such as during training or line checks, may provide an approximation to the way operational personnel behave when unmonitored. These observations may contribute to flesh out major operational questions such as significant procedural problems. However, it would be incorrect and perhaps risky to assume that observing personnel during training would provide the key to understanding human error and decision making in unmonitored operational contexts.Surveys1.2.11Surveys completed by operational personnel can also provide important diagnostic information about daily operations and, therefore, human error. Surveys1-4Line Operations Safety Audit (LOSA)provide an inexpensive mechanism to obtain significant information regarding many aspects of the organization, including the perceptions and opinions of operational personnel; the relevance of training to line operations; the level of teamwork and cooperation among various employee groups; problem areas or bottlenecks in daily operations; and eventual areas of dissatisfaction. Surveys can also probe the safety culture; for example, do personnel know the proper channels for reporting safety concerns and are they confident that the organization will act on expressed concerns? Finally, surveys can identify areas of dissent or confusion, for example, diversity in beliefs among particular groups from the same organization regarding the appropriate use of procedures or tools. On the minus side, surveys largely reflect perceptions. Surveys can be likened to incident reporting and are therefore subject to the shortcomings inherent to reporting systems in terms of understanding operational human performance and error. Flight data recording1.2.12Digital Flight Data Recorder (DFDR) and Quick Access Recorder (QAR) information from normal flights is also a valuable diagnostic tool. There are, however, some limitations about the data acquired through these systems. DFDR/QAR readouts provide information on the frequency of exceedences and the locations where they occur, but the readouts do not provide information on the human behaviours that were precursors of the events. While DFDR/QAR data track potential systemic problems, pilot reports are still necessary to provide the context within which the problems can be fully diagnosed.1.2.13Nevertheless, DFDR/QAR data hold high cost/efficiency ratio potential. Although probably under-utilized because of cost considerations as well as cultural and legal reasons, DFDR/QAR data can assist in identifying operational contexts within which migration of behaviours towards the limits of the system takes place.Proactive strategiesNormal line operations monitoring1.2.14The approach proposed in this manual to identify the successful human performance mechanisms that contribute to aviation safety and, therefore, to the design of countermeasures against human error focuses on the monitoring of normal line operations.Figure 1-2.Training Behaviours — Accomplishing training goals。
汽车维修指南.pdf_1702090030.2560523说明书

IndexAccessoriesInstallation.................................. 110ACCESSORY (Ignition KeyPosition)........................................ 52AddingAutomatic TransmissionFluid................................ 184, 185Brake Fluid................................. 187Clutch Fluid................................ 189Engine Coolant........................... 176Engine Oil...................................171Manual Transmission Fluid..... 186Power Steering Fluid................. 189Windshield Washer Fluid......... 183Additional Safety Information........ 19Door Locks................................... 20Driving with Pets......................... 20Head Restraint Position.............. 19Seat-back Position........................ 19Storing Cargo Safely................... 20Additives, Engine Oil..................... 173AdjustmentsMirrors.......................................... 71Head Restraints (65)Seats ................... 60Steering Wheel ........... 46Airbag (SRS) ............... 12Air Cleaner Element ........ 190Air Conditioning ............ 80Maintenance ............ 202Usage ................... 80Air Pressure, Tires .......... 205Alcohol and Drugs ........... 28Alcohol in Gasoline ......... 126Antifreeze ................ 176Anti-lock Brakes (ABS)Description ............. 149Indicator L i g h t........ 37, 150Operation ............... 149Anti-theft Steering Column Lock 52Anti-theft System ........... 122Appearance Care ........... 223Ashtray .................... 76Audio System ............... 87Automatic Speed C o n t r o l...... 48Automatic Transmission ..... 142Capacity, Fluid .......... 258Checking Fluid Level ..... 184Shifting ................ 142Shift Lever Position Indicator . 143Shift Lever Positions ............. 143Shift Lock Release . (146)BatteryCharging System Light ........... 36Jump Starting ........................... 240Maintenance ............................ 197Specifications .......................... 259Before Driving ............................. 125Belts, Seat ....................................... 5Beverage Holder ........................... 75Body Repair ................................. 229BrakesAnti-lock System (ABS) ........... 149Break-in, New Linings ..............126Fluid ................................................186Light, Burned-out .................... 211Parking ..................................... 73System Indicator ...................... 36Wear Indicators (148)CONTINUEDIndexBrakes, ABSDescription (149)Operation (149)System Indicator.................. 37, 150 Braking System (148)Break-in, New Car (126)Brightness Control, Instruments (43)Brights, Headlights (42)Bulb ReplacementBack-up Lights (215)Brake Lights (215)Ceiling Light (219)Front Parking Lights (214)Front Side Marker Lights (214)Headlights (211)High-mount Brake Light (218)License Plate Lights (218)Rear Side Marker Lights (217)Specifications (259)Turn Signal Lights (213)Bulbs, Halogen (212)Cables, Jump Starting With (240)Capacities Chart............................. 258Carbon Monoxide Hazard.. (29)Cargo, Loading (135)Cassette PlayerCare (121)Operation........................ 91, 98, 118CAUTION, Explanation of (ii)CD Changer...........................101, 114CD Player (112)Certification Label (256)Chains (210)Change OilHow to (173)When to (164)Changing a Flat Tire (233)Changing Engine Coolant (178)Charging System Indicator.... 36, 246Check Engine Light (37)CheckingAutomatic TransmissionFluid (184)Battery Condition (197)Brake Fluid (187)Clutch Fluid (189)Drive Belts (203)Engine Coolant (132)Engine Oil (130)Fuses (249)Manual Transmission Fluid (186)Power Steering Fluid (189)Checklist, Before Driving (138)Child Safety (21)Cigarette Lighter (76)Cleaner, Air (190)CleaningAluminum Wheels (225)Carpeting (226)Exterior (224)Fabric (226)Interior (226)Seat Belts (227)Vinyl (226)Window (227)Clock, Setting the (74)Clutch Fluid (189)CO in the Exhaust (264)Cold Weather, Starting in (140)Compact Spare (232)Consumer Information* (268)Controls, Instruments and..............33IndexCoolantAdding.........................................176Checking..................................... 132Proper Solution.......................... 176Temperature Gauge.................... 40Corrosion Protection..................... 228Crankcase Emission ControlSystem......................................... 264Cruise Control Operation............... 48Customer Relations Office.. (268)DANGER, Explanation of................. ii Dashboard........................................ 34Daytime Running Lights................. 42Dead Battery, What to Do............ 240Defects, Reporting Safety............. 271DEXRON ® III AutomaticTransmission Fluid.................... 184Dimensions..................................... 258Dimming the Headlights................ 42DipstickAutomatic Transmission .. 184, 185Engine Oil................................... 130Directional Signals (43)Disabled, Towing Your Car If...... 254Disc Brake Wear Indicators......... 148Disposal of Used Oil...................... 175DoorsLocking and Unlocking............... 53Power Door Locks....................... 53DOT Tire Quality Grading........... 262Downshifting, 5-speed ManualTransmission.............................. 141Drive Belts...................................... 203Driving............................................ 137Economy..................................... 133In Bad Weather.......................... 151In Foreign Countries.. (127)Economy, Fuel............................... 133Emergencies on the Road............. 231Battery, Jump Starting.............. 240Changing a Flat Tire................. 233Charging System Indicator...... 246Checking the Fuses................... 250Low Oil Pressure Indicator...... 245Malfunction Indicator Lamp.... 247Manually Closing Moonroof. (248)Overheated Engine................... 243Emergency Brake............................ 73Emergency Flashers....................... 45Emission Controls......................... 264EngineBelts.............................................203Coolant Temperature Gauge ..... 40Malfunction IndicatorLamp................................. 37, 247Oil Pressure Indicator......... 36, 245Oil, What Kind to Use............... 171Overheating................................ 243Specifications............................. 259Ethanol in Gasoline ....................... 127Evaporative Emission Controls.... 264Exhaust Fumes................................ 29Expectant Mothers, Use of SeatBelts by.........................................11Exterior, Cleaning the. (224)Fabric, Cleaning............................. 226Fan, Interior.. (80)CONTINUEDIndexFeatures, Comfort andConvenience................................. 79Filling the Fuel Tank..................... 128FilterOil................................................ 173First Gear, Shifting........................ 1455-speed Manual TransmissionChecking Fluid Level................ 1865-speed Manual TransmissionShifting the................................. 140Flashers, Hazard Warning.............. 45Flat Tire, Changing a.................... 233FluidsAutomatic Transmission .. 184, 185Brake........................................... 187Clutch.......................................... 189Manual Transmission............... 186Power Steering........................... 189Windshield Washer................... 183FM Stereo RadioReception.................................... 110Folding Rear Seat............................ 66Foreign Countries, Driving in...... 127Four-way Flashers........................... 45Front End, Towing byEmergency Wrecker (254)Fuel ................................................ 126Fill Door and Cap . (128)Gauge ................................................ 40Octane Requirement ................. 126Oxygenated ................................. 126Tank, Filling the ...................... 128Fuses, Checking the ..................... 250Gas Mileage, Improving. (133)Gasohol........................................... 126Gasoline.......................................... 126Gauge............................................ 40Octane Requirement................. 126Tank, Filling the......................... 128Gas Station Procedures................. 128GaugesEngine Coolant Temperature .... 40Fuel................................................ 40Gearshift Lever PositionsAutomatic Transmission........... 1435-speed ManualTransmission.......................... 141Glass Cleaning............................... 227Glove Box.. (59)Halogen Headlight Bulbs ............ 211Hazard Warning Flashers ............ 45Headlights ................................... 42Daytime Running Lights ......... 42High Beam Indicator .. (38)High Beams, Turning on ......... 42Low Beams, Turning on .......... 42Reminder Chime ..................... 42Replacing Halogen Bulbs ....... 211Turning on ............................ 42Head Restraints ............................ 65Heating and Cooling ..................... 80High Altitude, Starting at ............ 140High-Low Beam Switch ................ 42Hood, Opening the .. (129)Hot Coolant, Warning about ........ 177Hydraulic Clutch ........................ 189Hydroplaning ............................. 152Identification Number, Vehicle.... 256If Your Car Has to be Towed.......254IndexIgnitionKeys ........................................... 51Switch ......................................... 52Timing Control System ............ 265Indicator Lights, InstrumentPanel ............................................... 35Infant Restraint ............................. 23Inflation, Proper Tire .................. 205Inside Mirror .............................. 71Inspection, Tire ............................ 207Instrument Panel ........................... 34Instrument Panel Brightness ......... 43Interior Cleaning ........................ 226Interior Lights ............................. 77Introduction .. (i)Jacking up the Car (235)Jack, Tire (233)Jump Starting (240)Keys............................................ 51Label, Certification........................ 256Lane Change, Signaling.................. 43Lap Belt............................................... 7Lap/Shoulder Belts........................... 6Leaking of Exhaust into Car.......... 29Lighter, Cigarette............................ 76LightsBulb Replacement..................... 211Indicator........................................ 35Parking.......................................... 42Turn Signal................................... 43Loading Cargo................................ 135LOCK (Ignition Key Position)....... 52LocksAnti-theft Steering Column........ 52Fuel Fill Door............................. 128Glove Box..................................... 59Power Door.................................. 53Trunk............................................ 58Low Coolant Level......................... 132Lower Gear, Downshifting to a.... 141Low Oil Pressure Indicator.... 36, 245Lubricant Specifications Chart (258)Luggage (135)Maintenance................................... 159Owner Maintenance Checks.... 168Record.................................. 166-167Required Indicator....................... 40Safety........................................... 160Schedule.............................. 164-165Malfunction Indicator Lamp.. 37, 247Manual Transmission.................... 141Manual Transmission Fluid ......... 186Maximum Shift Speeds......... 142, 146Meters, Gauges................................ 39Methanol in Gasoline.................... 127Mirrors, Adjusting........................... 71Moonroof.......................................... 70Closing Manually....................... 248Operation.. (70)Neutral Gear Position.................... 144New Vehicle Break-in ................... 126Normal Shift Speeds. (141)CONTINUED。
Native Instruments MASCHINE MK3 用户手册说明书
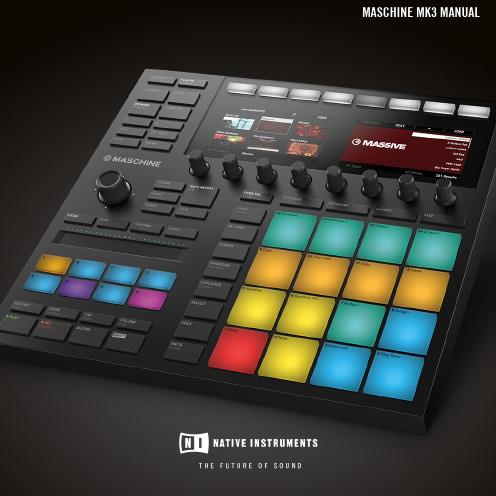
The information in this document is subject to change without notice and does not represent a commitment on the part of Native Instruments GmbH. The software described by this docu-ment is subject to a License Agreement and may not be copied to other media. No part of this publication may be copied, reproduced or otherwise transmitted or recorded, for any purpose, without prior written permission by Native Instruments GmbH, hereinafter referred to as Native Instruments.“Native Instruments”, “NI” and associated logos are (registered) trademarks of Native Instru-ments GmbH.ASIO, VST, HALion and Cubase are registered trademarks of Steinberg Media Technologies GmbH.All other product and company names are trademarks™ or registered® trademarks of their re-spective holders. Use of them does not imply any affiliation with or endorsement by them.Document authored by: David Gover and Nico Sidi.Software version: 2.8 (02/2019)Hardware version: MASCHINE MK3Special thanks to the Beta Test Team, who were invaluable not just in tracking down bugs, but in making this a better product.NATIVE INSTRUMENTS GmbH Schlesische Str. 29-30D-10997 Berlin Germanywww.native-instruments.de NATIVE INSTRUMENTS North America, Inc. 6725 Sunset Boulevard5th FloorLos Angeles, CA 90028USANATIVE INSTRUMENTS K.K.YO Building 3FJingumae 6-7-15, Shibuya-ku, Tokyo 150-0001Japanwww.native-instruments.co.jp NATIVE INSTRUMENTS UK Limited 18 Phipp StreetLondon EC2A 4NUUKNATIVE INSTRUMENTS FRANCE SARL 113 Rue Saint-Maur75011 ParisFrance SHENZHEN NATIVE INSTRUMENTS COMPANY Limited 5F, Shenzhen Zimao Center111 Taizi Road, Nanshan District, Shenzhen, GuangdongChina© NATIVE INSTRUMENTS GmbH, 2019. All rights reserved.Table of Contents1Welcome to MASCHINE (25)1.1MASCHINE Documentation (26)1.2Document Conventions (27)1.3New Features in MASCHINE 2.8 (29)1.4New Features in MASCHINE 2.7.10 (31)1.5New Features in MASCHINE 2.7.8 (31)1.6New Features in MASCHINE 2.7.7 (32)1.7New Features in MASCHINE 2.7.4 (33)1.8New Features in MASCHINE 2.7.3 (36)2Quick Reference (38)2.1Using Your Controller (38)2.1.1Controller Modes and Mode Pinning (38)2.1.2Controlling the Software Views from Your Controller (40)2.2MASCHINE Project Overview (43)2.2.1Sound Content (44)2.2.2Arrangement (45)2.3MASCHINE Hardware Overview (48)2.3.1MASCHINE Hardware Overview (48)2.3.1.1Control Section (50)2.3.1.2Edit Section (53)2.3.1.3Performance Section (54)2.3.1.4Group Section (56)2.3.1.5Transport Section (56)2.3.1.6Pad Section (58)2.3.1.7Rear Panel (63)2.4MASCHINE Software Overview (65)2.4.1Header (66)2.4.2Browser (68)2.4.3Arranger (70)2.4.4Control Area (73)2.4.5Pattern Editor (74)3Basic Concepts (76)3.1Important Names and Concepts (76)3.2Adjusting the MASCHINE User Interface (79)3.2.1Adjusting the Size of the Interface (79)3.2.2Switching between Ideas View and Song View (80)3.2.3Showing/Hiding the Browser (81)3.2.4Showing/Hiding the Control Lane (81)3.3Common Operations (82)3.3.1Using the 4-Directional Push Encoder (82)3.3.2Pinning a Mode on the Controller (83)3.3.3Adjusting Volume, Swing, and Tempo (84)3.3.4Undo/Redo (87)3.3.5List Overlay for Selectors (89)3.3.6Zoom and Scroll Overlays (90)3.3.7Focusing on a Group or a Sound (91)3.3.8Switching Between the Master, Group, and Sound Level (96)3.3.9Navigating Channel Properties, Plug-ins, and Parameter Pages in the Control Area.973.3.9.1Extended Navigate Mode on Your Controller (102)3.3.10Navigating the Software Using the Controller (105)3.3.11Using Two or More Hardware Controllers (106)3.3.12Touch Auto-Write Option (108)3.4Native Kontrol Standard (110)3.5Stand-Alone and Plug-in Mode (111)3.5.1Differences between Stand-Alone and Plug-in Mode (112)3.5.2Switching Instances (113)3.5.3Controlling Various Instances with Different Controllers (114)3.6Host Integration (114)3.6.1Setting up Host Integration (115)3.6.1.1Setting up Ableton Live (macOS) (115)3.6.1.2Setting up Ableton Live (Windows) (116)3.6.1.3Setting up Apple Logic Pro X (116)3.6.2Integration with Ableton Live (117)3.6.3Integration with Apple Logic Pro X (119)3.7Preferences (120)3.7.1Preferences – General Page (121)3.7.2Preferences – Audio Page (126)3.7.3Preferences – MIDI Page (130)3.7.4Preferences – Default Page (133)3.7.5Preferences – Library Page (137)3.7.6Preferences – Plug-ins Page (145)3.7.7Preferences – Hardware Page (150)3.7.8Preferences – Colors Page (154)3.8Integrating MASCHINE into a MIDI Setup (156)3.8.1Connecting External MIDI Equipment (156)3.8.2Sync to External MIDI Clock (157)3.8.3Send MIDI Clock (158)3.9Syncing MASCHINE using Ableton Link (159)3.9.1Connecting to a Network (159)3.9.2Joining and Leaving a Link Session (159)3.10Using a Pedal with the MASCHINE Controller (160)3.11File Management on the MASCHINE Controller (161)4Browser (163)4.1Browser Basics (163)4.1.1The MASCHINE Library (163)4.1.2Browsing the Library vs. Browsing Your Hard Disks (164)4.2Searching and Loading Files from the Library (165)4.2.1Overview of the Library Pane (165)4.2.2Selecting or Loading a Product and Selecting a Bank from the Browser (170)4.2.2.1[MK3] Browsing by Product Category Using the Controller (174)4.2.2.2[MK3] Browsing by Product Vendor Using the Controller (174)4.2.3Selecting a Product Category, a Product, a Bank, and a Sub-Bank (175)4.2.3.1Selecting a Product Category, a Product, a Bank, and a Sub-Bank on theController (179)4.2.4Selecting a File Type (180)4.2.5Choosing Between Factory and User Content (181)4.2.6Selecting Type and Character Tags (182)4.2.7List and Tag Overlays in the Browser (186)4.2.8Performing a Text Search (188)4.2.9Loading a File from the Result List (188)4.3Additional Browsing Tools (193)4.3.1Loading the Selected Files Automatically (193)4.3.2Auditioning Instrument Presets (195)4.3.3Auditioning Samples (196)4.3.4Loading Groups with Patterns (197)4.3.5Loading Groups with Routing (198)4.3.6Displaying File Information (198)4.4Using Favorites in the Browser (199)4.5Editing the Files’ Tags and Properties (203)4.5.1Attribute Editor Basics (203)4.5.2The Bank Page (205)4.5.3The Types and Characters Pages (205)4.5.4The Properties Page (208)4.6Loading and Importing Files from Your File System (209)4.6.1Overview of the FILES Pane (209)4.6.2Using Favorites (211)4.6.3Using the Location Bar (212)4.6.4Navigating to Recent Locations (213)4.6.5Using the Result List (214)4.6.6Importing Files to the MASCHINE Library (217)4.7Locating Missing Samples (219)4.8Using Quick Browse (221)5Managing Sounds, Groups, and Your Project (225)5.1Overview of the Sounds, Groups, and Master (225)5.1.1The Sound, Group, and Master Channels (226)5.1.2Similarities and Differences in Handling Sounds and Groups (227)5.1.3Selecting Multiple Sounds or Groups (228)5.2Managing Sounds (233)5.2.1Loading Sounds (235)5.2.2Pre-listening to Sounds (236)5.2.3Renaming Sound Slots (237)5.2.4Changing the Sound’s Color (237)5.2.5Saving Sounds (239)5.2.6Copying and Pasting Sounds (241)5.2.7Moving Sounds (244)5.2.8Resetting Sound Slots (245)5.3Managing Groups (247)5.3.1Creating Groups (248)5.3.2Loading Groups (249)5.3.3Renaming Groups (251)5.3.4Changing the Group’s Color (251)5.3.5Saving Groups (253)5.3.6Copying and Pasting Groups (255)5.3.7Reordering Groups (258)5.3.8Deleting Groups (259)5.4Exporting MASCHINE Objects and Audio (260)5.4.1Saving a Group with its Samples (261)5.4.2Saving a Project with its Samples (262)5.4.3Exporting Audio (264)5.5Importing Third-Party File Formats (270)5.5.1Loading REX Files into Sound Slots (270)5.5.2Importing MPC Programs to Groups (271)6Playing on the Controller (275)6.1Adjusting the Pads (275)6.1.1The Pad View in the Software (275)6.1.2Choosing a Pad Input Mode (277)6.1.3Adjusting the Base Key (280)6.1.4Using Choke Groups (282)6.1.5Using Link Groups (284)6.2Adjusting the Key, Choke, and Link Parameters for Multiple Sounds (286)6.3Playing Tools (287)6.3.1Mute and Solo (288)6.3.2Choke All Notes (292)6.3.3Groove (293)6.3.4Level, Tempo, Tune, and Groove Shortcuts on Your Controller (295)6.3.5Tap Tempo (299)6.4Performance Features (300)6.4.1Overview of the Perform Features (300)6.4.2Selecting a Scale and Creating Chords (303)6.4.3Scale and Chord Parameters (303)6.4.4Creating Arpeggios and Repeated Notes (316)6.4.5Swing on Note Repeat / Arp Output (321)6.5Using Lock Snapshots (322)6.5.1Creating a Lock Snapshot (322)6.5.2Using Extended Lock (323)6.5.3Updating a Lock Snapshot (323)6.5.4Recalling a Lock Snapshot (324)6.5.5Morphing Between Lock Snapshots (324)6.5.6Deleting a Lock Snapshot (325)6.5.7Triggering Lock Snapshots via MIDI (326)6.6Using the Smart Strip (327)6.6.1Pitch Mode (328)6.6.2Modulation Mode (328)6.6.3Perform Mode (328)6.6.4Notes Mode (329)7Working with Plug-ins (330)7.1Plug-in Overview (330)7.1.1Plug-in Basics (330)7.1.2First Plug-in Slot of Sounds: Choosing the Sound’s Role (334)7.1.3Loading, Removing, and Replacing a Plug-in (335)7.1.3.1Browser Plug-in Slot Selection (341)7.1.4Adjusting the Plug-in Parameters (344)7.1.5Bypassing Plug-in Slots (344)7.1.6Using Side-Chain (346)7.1.7Moving Plug-ins (346)7.1.8Alternative: the Plug-in Strip (348)7.1.9Saving and Recalling Plug-in Presets (348)7.1.9.1Saving Plug-in Presets (349)7.1.9.2Recalling Plug-in Presets (350)7.1.9.3Removing a Default Plug-in Preset (351)7.2The Sampler Plug-in (352)7.2.1Page 1: Voice Settings / Engine (354)7.2.2Page 2: Pitch / Envelope (356)7.2.3Page 3: FX / Filter (359)7.2.4Page 4: Modulation (361)7.2.5Page 5: LFO (363)7.2.6Page 6: Velocity / Modwheel (365)7.3Using Native Instruments and External Plug-ins (367)7.3.1Opening/Closing Plug-in Windows (367)7.3.2Using the VST/AU Plug-in Parameters (370)7.3.3Setting Up Your Own Parameter Pages (371)7.3.4Using VST/AU Plug-in Presets (376)7.3.5Multiple-Output Plug-ins and Multitimbral Plug-ins (378)8Using the Audio Plug-in (380)8.1Loading a Loop into the Audio Plug-in (384)8.2Editing Audio in the Audio Plug-in (385)8.3Using Loop Mode (386)8.4Using Gate Mode (388)9Using the Drumsynths (390)9.1Drumsynths – General Handling (391)9.1.1Engines: Many Different Drums per Drumsynth (391)9.1.2Common Parameter Organization (391)9.1.3Shared Parameters (394)9.1.4Various Velocity Responses (394)9.1.5Pitch Range, Tuning, and MIDI Notes (394)9.2The Kicks (395)9.2.1Kick – Sub (397)9.2.2Kick – Tronic (399)9.2.3Kick – Dusty (402)9.2.4Kick – Grit (403)9.2.5Kick – Rasper (406)9.2.6Kick – Snappy (407)9.2.7Kick – Bold (409)9.2.8Kick – Maple (411)9.2.9Kick – Push (412)9.3The Snares (414)9.3.1Snare – Volt (416)9.3.2Snare – Bit (418)9.3.3Snare – Pow (420)9.3.4Snare – Sharp (421)9.3.5Snare – Airy (423)9.3.6Snare – Vintage (425)9.3.7Snare – Chrome (427)9.3.8Snare – Iron (429)9.3.9Snare – Clap (431)9.3.10Snare – Breaker (433)9.4The Hi-hats (435)9.4.1Hi-hat – Silver (436)9.4.2Hi-hat – Circuit (438)9.4.3Hi-hat – Memory (440)9.4.4Hi-hat – Hybrid (442)9.4.5Creating a Pattern with Closed and Open Hi-hats (444)9.5The Toms (445)9.5.1Tom – Tronic (447)9.5.2Tom – Fractal (449)9.5.3Tom – Floor (453)9.5.4Tom – High (455)9.6The Percussions (456)9.6.1Percussion – Fractal (458)9.6.2Percussion – Kettle (461)9.6.3Percussion – Shaker (463)9.7The Cymbals (467)9.7.1Cymbal – Crash (469)9.7.2Cymbal – Ride (471)10Using the Bass Synth (474)10.1Bass Synth – General Handling (475)10.1.1Parameter Organization (475)10.1.2Bass Synth Parameters (477)11Working with Patterns (479)11.1Pattern Basics (479)11.1.1Pattern Editor Overview (480)11.1.2Navigating the Event Area (486)11.1.3Following the Playback Position in the Pattern (488)11.1.4Jumping to Another Playback Position in the Pattern (489)11.1.5Group View and Keyboard View (491)11.1.6Adjusting the Arrange Grid and the Pattern Length (493)11.1.7Adjusting the Step Grid and the Nudge Grid (497)11.2Recording Patterns in Real Time (501)11.2.1Recording Your Patterns Live (501)11.2.2The Record Prepare Mode (504)11.2.3Using the Metronome (505)11.2.4Recording with Count-in (506)11.2.5Quantizing while Recording (508)11.3Recording Patterns with the Step Sequencer (508)11.3.1Step Mode Basics (508)11.3.2Editing Events in Step Mode (511)11.3.3Recording Modulation in Step Mode (513)11.4Editing Events (514)11.4.1Editing Events with the Mouse: an Overview (514)11.4.2Creating Events/Notes (517)11.4.3Selecting Events/Notes (518)11.4.4Editing Selected Events/Notes (526)11.4.5Deleting Events/Notes (532)11.4.6Cut, Copy, and Paste Events/Notes (535)11.4.7Quantizing Events/Notes (538)11.4.8Quantization While Playing (540)11.4.9Doubling a Pattern (541)11.4.10Adding Variation to Patterns (541)11.5Recording and Editing Modulation (546)11.5.1Which Parameters Are Modulatable? (547)11.5.2Recording Modulation (548)11.5.3Creating and Editing Modulation in the Control Lane (550)11.6Creating MIDI Tracks from Scratch in MASCHINE (555)11.7Managing Patterns (557)11.7.1The Pattern Manager and Pattern Mode (558)11.7.2Selecting Patterns and Pattern Banks (560)11.7.3Creating Patterns (563)11.7.4Deleting Patterns (565)11.7.5Creating and Deleting Pattern Banks (566)11.7.6Naming Patterns (568)11.7.7Changing the Pattern’s Color (570)11.7.8Duplicating, Copying, and Pasting Patterns (571)11.7.9Moving Patterns (574)11.7.10Adjusting Pattern Length in Fine Increments (575)11.8Importing/Exporting Audio and MIDI to/from Patterns (576)11.8.1Exporting Audio from Patterns (576)11.8.2Exporting MIDI from Patterns (577)11.8.3Importing MIDI to Patterns (580)12Audio Routing, Remote Control, and Macro Controls (589)12.1Audio Routing in MASCHINE (590)12.1.1Sending External Audio to Sounds (591)12.1.2Configuring the Main Output of Sounds and Groups (596)12.1.3Setting Up Auxiliary Outputs for Sounds and Groups (601)12.1.4Configuring the Master and Cue Outputs of MASCHINE (605)12.1.5Mono Audio Inputs (610)12.1.5.1Configuring External Inputs for Sounds in Mix View (611)12.2Using MIDI Control and Host Automation (614)12.2.1Triggering Sounds via MIDI Notes (615)12.2.2Triggering Scenes via MIDI (622)12.2.3Controlling Parameters via MIDI and Host Automation (623)12.2.4Selecting VST/AU Plug-in Presets via MIDI Program Change (631)12.2.5Sending MIDI from Sounds (632)12.3Creating Custom Sets of Parameters with the Macro Controls (636)12.3.1Macro Control Overview (637)12.3.2Assigning Macro Controls Using the Software (638)12.3.3Assigning Macro Controls Using the Controller (644)13Controlling Your Mix (646)13.1Mix View Basics (646)13.1.1Switching between Arrange View and Mix View (646)13.1.2Mix View Elements (647)13.2The Mixer (649)13.2.1Displaying Groups vs. Displaying Sounds (650)13.2.2Adjusting the Mixer Layout (652)13.2.3Selecting Channel Strips (653)13.2.4Managing Your Channels in the Mixer (654)13.2.5Adjusting Settings in the Channel Strips (656)13.2.6Using the Cue Bus (660)13.3The Plug-in Chain (662)13.4The Plug-in Strip (663)13.4.1The Plug-in Header (665)13.4.2Panels for Drumsynths and Internal Effects (667)13.4.3Panel for the Sampler (668)13.4.4Custom Panels for Native Instruments Plug-ins (671)13.4.5Undocking a Plug-in Panel (Native Instruments and External Plug-ins Only) (675)13.5Controlling Your Mix from the Controller (677)13.5.1Navigating Your Channels in Mix Mode (678)13.5.2Adjusting the Level and Pan in Mix Mode (679)13.5.3Mute and Solo in Mix Mode (680)13.5.4Plug-in Icons in Mix Mode (680)14Using Effects (681)14.1Applying Effects to a Sound, a Group or the Master (681)14.1.1Adding an Effect (681)14.1.2Other Operations on Effects (690)14.1.3Using the Side-Chain Input (692)14.2Applying Effects to External Audio (695)14.2.1Step 1: Configure MASCHINE Audio Inputs (695)14.2.2Step 2: Set up a Sound to Receive the External Input (698)14.2.3Step 3: Load an Effect to Process an Input (700)14.3Creating a Send Effect (701)14.3.1Step 1: Set Up a Sound or Group as Send Effect (702)14.3.2Step 2: Route Audio to the Send Effect (706)14.3.3 A Few Notes on Send Effects (708)14.4Creating Multi-Effects (709)15Effect Reference (712)15.1Dynamics (713)15.1.1Compressor (713)15.1.2Gate (717)15.1.3Transient Master (721)15.1.4Limiter (723)15.1.5Maximizer (727)15.2Filtering Effects (730)15.2.1EQ (730)15.2.2Filter (733)15.2.3Cabinet (737)15.3Modulation Effects (738)15.3.1Chorus (738)15.3.2Flanger (740)15.3.3FM (742)15.3.4Freq Shifter (743)15.3.5Phaser (745)15.4Spatial and Reverb Effects (747)15.4.1Ice (747)15.4.2Metaverb (749)15.4.3Reflex (750)15.4.4Reverb (Legacy) (752)15.4.5Reverb (754)15.4.5.1Reverb Room (754)15.4.5.2Reverb Hall (757)15.4.5.3Plate Reverb (760)15.5Delays (762)15.5.1Beat Delay (762)15.5.2Grain Delay (765)15.5.3Grain Stretch (767)15.5.4Resochord (769)15.6Distortion Effects (771)15.6.1Distortion (771)15.6.2Lofi (774)15.6.3Saturator (775)15.7Perform FX (779)15.7.1Filter (780)15.7.2Flanger (782)15.7.3Burst Echo (785)15.7.4Reso Echo (787)15.7.5Ring (790)15.7.6Stutter (792)15.7.7Tremolo (795)15.7.8Scratcher (798)16Working with the Arranger (801)16.1Arranger Basics (801)16.1.1Navigating Song View (804)16.1.2Following the Playback Position in Your Project (806)16.1.3Performing with Scenes and Sections using the Pads (807)16.2Using Ideas View (811)16.2.1Scene Overview (811)16.2.2Creating Scenes (813)16.2.3Assigning and Removing Patterns (813)16.2.4Selecting Scenes (817)16.2.5Deleting Scenes (818)16.2.6Creating and Deleting Scene Banks (820)16.2.7Clearing Scenes (820)16.2.8Duplicating Scenes (821)16.2.9Reordering Scenes (822)16.2.10Making Scenes Unique (824)16.2.11Appending Scenes to Arrangement (825)16.2.12Naming Scenes (826)16.2.13Changing the Color of a Scene (827)16.3Using Song View (828)16.3.1Section Management Overview (828)16.3.2Creating Sections (833)16.3.3Assigning a Scene to a Section (834)16.3.4Selecting Sections and Section Banks (835)16.3.5Reorganizing Sections (839)16.3.6Adjusting the Length of a Section (840)16.3.6.1Adjusting the Length of a Section Using the Software (841)16.3.6.2Adjusting the Length of a Section Using the Controller (843)16.3.7Clearing a Pattern in Song View (843)16.3.8Duplicating Sections (844)16.3.8.1Making Sections Unique (845)16.3.9Removing Sections (846)16.3.10Renaming Scenes (848)16.3.11Clearing Sections (849)16.3.12Creating and Deleting Section Banks (850)16.3.13Working with Patterns in Song view (850)16.3.13.1Creating a Pattern in Song View (850)16.3.13.2Selecting a Pattern in Song View (850)16.3.13.3Clearing a Pattern in Song View (851)16.3.13.4Renaming a Pattern in Song View (851)16.3.13.5Coloring a Pattern in Song View (851)16.3.13.6Removing a Pattern in Song View (852)16.3.13.7Duplicating a Pattern in Song View (852)16.3.14Enabling Auto Length (852)16.3.15Looping (853)16.3.15.1Setting the Loop Range in the Software (854)16.4Playing with Sections (855)16.4.1Jumping to another Playback Position in Your Project (855)16.5Triggering Sections or Scenes via MIDI (856)16.6The Arrange Grid (858)16.7Quick Grid (860)17Sampling and Sample Mapping (862)17.1Opening the Sample Editor (862)17.2Recording Audio (863)17.2.1Opening the Record Page (863)17.2.2Selecting the Source and the Recording Mode (865)17.2.3Arming, Starting, and Stopping the Recording (868)17.2.5Using the Footswitch for Recording Audio (871)17.2.6Checking Your Recordings (872)17.2.7Location and Name of Your Recorded Samples (876)17.3Editing a Sample (876)17.3.1Using the Edit Page (877)17.3.2Audio Editing Functions (882)17.4Slicing a Sample (890)17.4.1Opening the Slice Page (891)17.4.2Adjusting the Slicing Settings (893)17.4.3Live Slicing (898)17.4.3.1Live Slicing Using the Controller (898)17.4.3.2Delete All Slices (899)17.4.4Manually Adjusting Your Slices (899)17.4.5Applying the Slicing (906)17.5Mapping Samples to Zones (912)17.5.1Opening the Zone Page (912)17.5.2Zone Page Overview (913)17.5.3Selecting and Managing Zones in the Zone List (915)17.5.4Selecting and Editing Zones in the Map View (920)17.5.5Editing Zones in the Sample View (924)17.5.6Adjusting the Zone Settings (927)17.5.7Adding Samples to the Sample Map (934)18Appendix: Tips for Playing Live (937)18.1Preparations (937)18.1.1Focus on the Hardware (937)18.1.2Customize the Pads of the Hardware (937)18.1.3Check Your CPU Power Before Playing (937)18.1.4Name and Color Your Groups, Patterns, Sounds and Scenes (938)18.1.5Consider Using a Limiter on Your Master (938)18.1.6Hook Up Your Other Gear and Sync It with MIDI Clock (938)18.1.7Improvise (938)18.2Basic Techniques (938)18.2.1Use Mute and Solo (938)18.2.2Use Scene Mode and Tweak the Loop Range (939)18.2.3Create Variations of Your Drum Patterns in the Step Sequencer (939)18.2.4Use Note Repeat (939)18.2.5Set Up Your Own Multi-effect Groups and Automate Them (939)18.3Special Tricks (940)18.3.1Changing Pattern Length for Variation (940)18.3.2Using Loops to Cycle Through Samples (940)18.3.3Using Loops to Cycle Through Samples (940)18.3.4Load Long Audio Files and Play with the Start Point (940)19Troubleshooting (941)19.1Knowledge Base (941)19.2Technical Support (941)19.3Registration Support (942)19.4User Forum (942)20Glossary (943)Index (951)1Welcome to MASCHINEThank you for buying MASCHINE!MASCHINE is a groove production studio that implements the familiar working style of classi-cal groove boxes along with the advantages of a computer based system. MASCHINE is ideal for making music live, as well as in the studio. It’s the hands-on aspect of a dedicated instru-ment, the MASCHINE hardware controller, united with the advanced editing features of the MASCHINE software.Creating beats is often not very intuitive with a computer, but using the MASCHINE hardware controller to do it makes it easy and fun. You can tap in freely with the pads or use Note Re-peat to jam along. Alternatively, build your beats using the step sequencer just as in classic drum machines.Patterns can be intuitively combined and rearranged on the fly to form larger ideas. You can try out several different versions of a song without ever having to stop the music.Since you can integrate it into any sequencer that supports VST, AU, or AAX plug-ins, you can reap the benefits in almost any software setup, or use it as a stand-alone application. You can sample your own material, slice loops and rearrange them easily.However, MASCHINE is a lot more than an ordinary groovebox or sampler: it comes with an inspiring 7-gigabyte library, and a sophisticated, yet easy to use tag-based Browser to give you instant access to the sounds you are looking for.What’s more, MASCHINE provides lots of options for manipulating your sounds via internal ef-fects and other sound-shaping possibilities. You can also control external MIDI hardware and 3rd-party software with the MASCHINE hardware controller, while customizing the functions of the pads, knobs and buttons according to your needs utilizing the included Controller Editor application. We hope you enjoy this fantastic instrument as much as we do. Now let’s get go-ing!—The MASCHINE team at Native Instruments.MASCHINE Documentation1.1MASCHINE DocumentationNative Instruments provide many information sources regarding MASCHINE. The main docu-ments should be read in the following sequence:1.MASCHINE Getting Started: This document provides a practical approach to MASCHINE viaa set of tutorials covering easy and more advanced tasks in order to help you familiarizeyourself with MASCHINE.2.MASCHINE Manual (this document): The MASCHINE Manual provides you with a compre-hensive description of all MASCHINE software and hardware features.Additional documentation sources provide you with details on more specific topics:▪Controller Editor Manual: Besides using your MASCHINE hardware controller together withits dedicated MASCHINE software, you can also use it as a powerful and highly versatileMIDI controller to pilot any other MIDI-capable application or device. This is made possibleby the Controller Editor software, an application that allows you to precisely define all MIDIassignments for your MASCHINE controller. The Controller Editor was installed during theMASCHINE installation procedure. For more information on this, please refer to the Con-troller Editor Manual available as a PDF file via the Help menu of Controller Editor.▪Online Support Videos: You can find a number of support videos on The Official Native In-struments Support Channel under the following URL: https:///NIsupport-EN. We recommend that you follow along with these instructions while the respective ap-plication is running on your computer.Other Online Resources:If you are experiencing problems related to your Native Instruments product that the supplied documentation does not cover, there are several ways of getting help:▪Knowledge Base▪User Forum▪Technical Support▪Registration SupportYou will find more information on these subjects in the chapter Troubleshooting.1.2Document ConventionsThis section introduces you to the signage and text highlighting used in this manual. This man-ual uses particular formatting to point out special facts and to warn you of potential issues. The icons introducing these notes let you see what kind of information is to be expected:This document uses particular formatting to point out special facts and to warn you of poten-tial issues. The icons introducing the following notes let you see what kind of information can be expected:Furthermore, the following formatting is used:▪Text appearing in (drop-down) menus (such as Open…, Save as… etc.) in the software and paths to locations on your hard disk or other storage devices is printed in italics.▪Text appearing elsewhere (labels of buttons, controls, text next to checkboxes etc.) in the software is printed in blue. Whenever you see this formatting applied, you will find the same text appearing somewhere on the screen.▪Text appearing on the displays of the controller is printed in light grey. Whenever you see this formatting applied, you will find the same text on a controller display.▪Text appearing on labels of the hardware controller is printed in orange. Whenever you see this formatting applied, you will find the same text on the controller.▪Important names and concepts are printed in bold.▪References to keys on your computer’s keyboard you’ll find put in square brackets (e.g.,“Press [Shift] + [Enter]”).►Single instructions are introduced by this play button type arrow.→Results of actions are introduced by this smaller arrow.Naming ConventionThroughout the documentation we will refer to MASCHINE controller (or just controller) as the hardware controller and MASCHINE software as the software installed on your computer.The term “effect” will sometimes be abbreviated as “FX” when referring to elements in the MA-SCHINE software and hardware. These terms have the same meaning.Button Combinations and Shortcuts on Your ControllerMost instructions will use the “+” sign to indicate buttons (or buttons and pads) that must be pressed simultaneously, starting with the button indicated first. E.g., an instruction such as:“Press SHIFT + PLAY”means:1.Press and hold SHIFT.2.While holding SHIFT, press PLAY and release it.3.Release SHIFT.Unlabeled Buttons on the ControllerThe buttons and knobs above and below the displays on your MASCHINE controller do not have labels.。
惠普彩色激光打印机 Pro M454 和惠普彩色激光多功能一体机 Pro M479 维修手册说明书
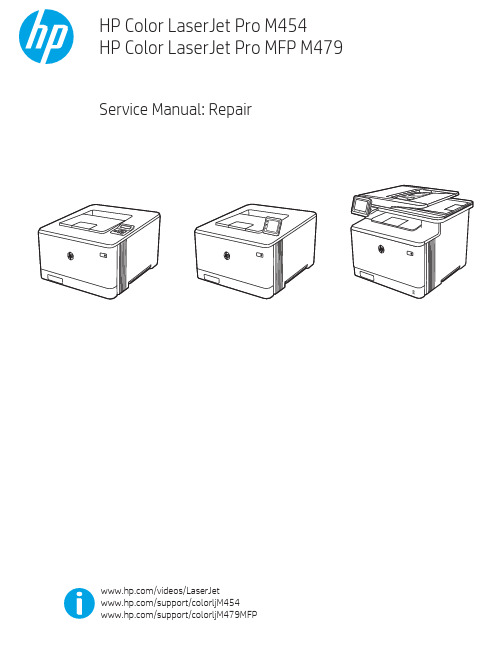
Table -1 Revision history Revision number 1
Revision date 6/2019
Revision notes HP LaserJet Pro M454 HP LaserJet Pro MFP M479 Repair manual initial release
Additional service and support for HP internal personnel HP internal personnel, go to one of the following Web-based Interactive Search Engine (WISE) sites: Americas (AMS) – https:///wise/home/ams-enWISE - English – https:///wise/home/ams-esWISE - Spanish – https:///wise/home/ams-ptWISE - Portuguese – https:///wise/home/ams-frWISE - French Asia Pacific / Japan (APJ) ○ https:///wise/home/apj-enWISE - English ○ https:///wise/home/apj-jaWISE - Japanese ○ https:///wise/home/apj-koWISE - Korean ○ https:///wise/home/apj-zh-HansWISE - Chinese (simplified)
Find information about the following topics ● Service manuals ● Service advisories ● Up-to-date control panel message (CPMD) troubleshooting ● Install and configure ● Printer specifications ● Solutions for printer issues and emerging issues ● Remove and replace part instructions and videos ● Warranty and regulatory information
ACARS系统常见故障及处理方法

ACARS系统常见故障及处理方法acars系统是飞机通信寻址和报告系统的简称,它的目的是通过飞机和航空公司基地之间的双向数据传输,从而加强航空公司对飞机的监控能力和指挥能力。
同时acars系统也即将成为caac的适航要求的项目。
系统组成acars系统主要由机载设备和地面设备共同组成,其中机载设备由acars管理组件、综合表明控制器(idc-900)、第三部甚高频通信系统、飞机特性组件(apm由地面收发站和数据处理站、航空公司处理和分析终端等组成(见图1)。
以上系统中的任一环节存在问题,都可能造成acars系统不能正常工作。
acars系统故障的情况常见故障及处理方法acars系统的故障主要整体表现在系统中的机载设备有关硬、硬件问题和人员采用问题等方面。
1.线路问题2.软件问题2021年12月以来,波音两架737-300飞机b2971和b2972相继发生位置报异常现象,表现为不断无规律地下发位置报,1秒内会下发数份报(正常情况每隔8分钟发一份)造成公司地面终端数据堵塞。
经分析,其最大可能性是acars管理组件内部的软件出现异常,通过重新输入acars系统的软件,故障消失。
但使用同一软件的其他飞机都没有此类故障,其根本原因应该在于acars管理组件本身的工作不稳定,从而造成其内部的软件出现异常。
3.硬件问题主要表现在acars管理组件mu故障和综合显示控制器idc-900故障以及打印机故障。
其中idc-900故障表现为按钮失效或过热黑屏(此时自动报文正常,只是无法人工收发报文),而mu故障则会导致无法正常收发报文。
以上都可通过更换相应的硬件设备排除故障。
4.人员采用问题acars系统收发的每类报文都配有独特的标签,同时地面上发到飞机的报文地址根据需要也可变更,可发送到mcdu或idc-900显示,也可直接发送到打印机打印,另外需要人员随时监控报文情况,随时应答。
如果工作人员工作不认真可能造成失误。
公司机组就曾多次反映收不到地面上发的报文,排除acars系统软硬件方面的问题,发现主要是上发的报文地址设置不正确、报文标签有误导致飞机上的mu组件拒收报文和地面人员没有及时应答。
Indradrive 系列 故障代码
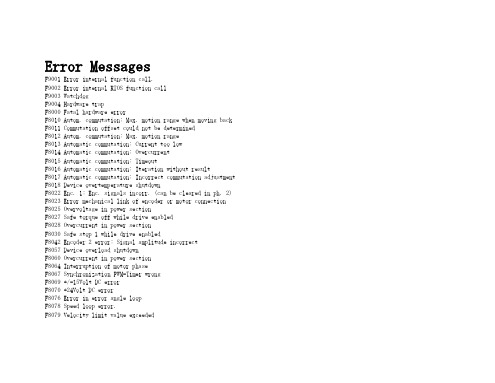
Error MessagesF9001 Error internal function call.F9002 Error internal RTOS function callF9003 WatchdogF9004 Hardware trapF8000 Fatal hardware errorF8010 Autom. commutation: Max. motion range when moving back F8011 Commutation offset could not be determinedF8012 Autom. commutation: Max. motion rangeF8013 Automatic commutation: Current too lowF8014 Automatic commutation: OvercurrentF8015 Automatic commutation: TimeoutF8016 Automatic commutation: Iteration without resultF8017 Automatic commutation: Incorrect commutation adjustment F8018 Device overtemperature shutdownF8022 Enc. 1: Enc. signals incorr. (can be cleared in ph. 2) F8023 Error mechanical link of encoder or motor connectionF8025 Overvoltage in power sectionF8027 Safe torque off while drive enabledF8028 Overcurrent in power sectionF8030 Safe stop 1 while drive enabledF8042 Encoder 2 error: Signal amplitude incorrectF8057 Device overload shutdownF8060 Overcurrent in power sectionF8064 Interruption of motor phaseF8067 Synchronization PWM-Timer wrongF8069 +/-15Volt DC errorF8070 +24Volt DC errorF8076 Error in error angle loopF8078 Speed loop error.F8079 Velocity limit value exceededF8091 Power section defectiveF8100 Error when initializing the parameter handlingF8102 Error when initializing power sectionF8118 Invalid power section/firmware combinationF8120 Invalid control section/firmware combinationF8122 Control section defectiveF8129 Incorrect optional module firmwareF8130 Firmware of option 2 of safety technology defectiveF8133 Error when checking interrupting circuitsF8134 SBS: Fatal errorF8135 SMD: Velocity exceededF8140 Fatal CCD error.F8201 Safety command for basic initialization incorrectF8203 Safety technology configuration parameter invalidF8813 Connection error mains chokeF8830 Power section errorF8838 Overcurrent external braking resistorF7010 Safely-limited increment exceededF7011 Safely-monitored position, exceeded in pos. DirectionF7012 Safely-monitored position, exceeded in neg. DirectionF7013 Safely-limited speed exceededF7020 Safe maximum speed exceededF7021 Safely-limited position exceededF7030 Position window Safe stop 2 exceededF7031 Incorrect direction of motionF7040 Validation error parameterized - effective thresholdF7041 Actual position value validation errorF7042 Validation error of safe operation modeF7043 Error of output stage interlockF7050 Time for stopping process exceeded8.3.15 F7051 Safely-monitored deceleration exceeded (159)8.4 Travel Range Errors (F6xxx) (161)8.4.1 Behavior in the Case of Travel Range Errors (161)8.4.2 F6010 PLC Runtime Error (162)8.4.3 F6024 Maximum braking time exceeded (163)8.4.4 F6028 Position limit value exceeded (overflow) (164)8.4.5 F6029 Positive position limit exceeded (164)8.4.6 F6030 Negative position limit exceeded (165)8.4.7 F6034 Emergency-Stop (166)8.4.8 F6042 Both travel range limit switches activated (167)8.4.9 F6043 Positive travel range limit switch activated (167)8.4.10 F6044 Negative travel range limit switch activated (168)8.4.11 F6140 CCD slave error (emergency halt) (169)8.5 Interface Errors (F4xxx) (169)8.5.1 Behavior in the Case of Interface Errors (169)8.5.2 F4001 Sync telegram failure (170)8.5.3 F4002 RTD telegram failure (171)8.5.4 F4003 Invalid communication phase shutdown (172)8.5.5 F4004 Error during phase progression (172)8.5.6 F4005 Error during phase regression (173)8.5.7 F4006 Phase switching without ready signal (173)8.5.8 F4009 Bus failure (173)8.5.9 F4012 Incorrect I/O length (175)8.5.10 F4016 PLC double real-time channel failure (176)8.5.11 F4017 S-III: Incorrect sequence during phase switch (176)8.5.12 F4034 Emergency-Stop (177)8.5.13 F4140 CCD communication error (178)8.6 Non-Fatal Safety Technology Errors (F3xxx) (178)8.6.1 Behavior in the Case of Non-Fatal Safety Technology Errors (178)8.6.2 F3111 Refer. missing when selecting safety related end pos (179)8.6.3 F3112 Safe reference missing (179)8.6.4 F3115 Brake check time interval exceeded (181)Troubleshooting Guide | Rexroth IndraDrive Electric Drivesand ControlsI Bosch Rexroth AG VII/XXIITable of ContentsPage8.6.5 F3116 Nominal load torque of holding system exceeded (182)8.6.6 F3117 Actual position values validation error (182)8.6.7 F3122 SBS: System error (183)8.6.8 F3123 SBS: Brake check missing (184)8.6.9 F3130 Error when checking input signals (185)8.6.10 F3131 Error when checking acknowledgment signal (185)8.6.11 F3132 Error when checking diagnostic output signal (186)8.6.12 F3133 Error when checking interrupting circuits (187)8.6.13 F3134 Dynamization time interval incorrect (188)8.6.14 F3135 Dynamization pulse width incorrect (189)8.6.15 F3140 Safety parameters validation error (192)8.6.16 F3141 Selection validation error (192)8.6.17 F3142 Activation time of enabling control exceeded (193)8.6.18 F3143 Safety command for clearing errors incorrect (194)8.6.19 F3144 Incorrect safety configuration (195)8.6.20 F3145 Error when unlocking the safety door (196)8.6.21 F3146 System error channel 2 (197)8.6.22 F3147 System error channel 1 (198)8.6.23 F3150 Safety command for system start incorrect (199)8.6.24 F3151 Safety command for system halt incorrect (200)8.6.25 F3152 Incorrect backup of safety technology data (201)8.6.26 F3160 Communication error of safe communication (202)8.7 Non-Fatal Errors (F2xxx) (202)8.7.1 Behavior in the Case of Non-Fatal Errors (202)8.7.2 F2002 Encoder assignment not allowed for synchronization (203)8.7.3 F2003 Motion step skipped (203)8.7.4 F2004 Error in MotionProfile (204)8.7.5 F2005 Cam table invalid (205)8.7.6 F2006 MMC was removed (206)8.7.7 F2007 Switching to non-initialized operation mode (206)8.7.8 F2008 RL The motor type has changed (207)8.7.9 F2009 PL Load parameter default values (208)8.7.10 F2010 Error when initializing digital I/O (-> S-0-0423) (209)8.7.11 F2011 PLC - Error no. 1 (210)8.7.12 F2012 PLC - Error no. 2 (210)8.7.13 F2013 PLC - Error no. 3 (211)8.7.14 F2014 PLC - Error no. 4 (211)8.7.15 F2018 Device overtemperature shutdown (211)8.7.16 F2019 Motor overtemperature shutdown (212)8.7.17 F2021 Motor temperature monitor defective (213)8.7.18 F2022 Device temperature monitor defective (214)8.7.19 F2025 Drive not ready for control (214)8.7.20 F2026 Undervoltage in power section (215)8.7.21 F2027 Excessive oscillation in DC bus (216)8.7.22 F2028 Excessive deviation (216)8.7.23 F2031 Encoder 1 error: Signal amplitude incorrect (217)VIII/XXII Bosch Rexroth AG | Electric Drivesand ControlsRexroth IndraDrive | Troubleshooting GuideTable of ContentsPage8.7.24 F2032 Validation error during commutation fine adjustment (217)8.7.25 F2033 External power supply X10 error (218)8.7.26 F2036 Excessive position feedback difference (219)8.7.27 F2037 Excessive position command difference (220)8.7.28 F2039 Maximum acceleration exceeded (220)8.7.29 F2040 Device overtemperature 2 shutdown (221)8.7.30 F2042 Encoder 2: Encoder signals incorrect (222)8.7.31 F2043 Measuring encoder: Encoder signals incorrect (222)8.7.32 F2044 External power supply X15 error (223)8.7.33 F2048 Low battery voltage (224)8.7.34 F2050 Overflow of target position preset memory (225)8.7.35 F2051 No sequential block in target position preset memory (225)8.7.36 F2053 Incr. encoder emulator: Pulse frequency too high (226)8.7.37 F2054 Incr. encoder emulator: Hardware error (226)8.7.38 F2055 External power supply dig. I/O error (227)8.7.39 F2057 Target position out of travel range (227)8.7.40 F2058 Internal overflow by positioning input (228)8.7.41 F2059 Incorrect command value direction when positioning (229)8.7.42 F2063 Internal overflow master axis generator (230)8.7.43 F2064 Incorrect cmd value direction master axis generator (230)8.7.44 F2067 Synchronization to master communication incorrect (231)8.7.45 F2068 Brake error (231)8.7.46 F2069 Error when releasing the motor holding brake (232)8.7.47 F2074 Actual pos. value 1 outside absolute encoder window (232)8.7.48 F2075 Actual pos. value 2 outside absolute encoder window (233)8.7.49 F2076 Actual pos. value 3 outside absolute encoder window (234)8.7.50 F2077 Current measurement trim wrong (235)8.7.51 F2086 Error supply module (236)8.7.52 F2087 Module group communication error (236)8.7.53 F2100 Incorrect access to command value memory (237)8.7.54 F2101 It was impossible to address MMC (237)8.7.55 F2102 It was impossible to address I2C memory (238)8.7.56 F2103 It was impossible to address EnDat memory (238)8.7.57 F2104 Commutation offset invalid (239)8.7.58 F2105 It was impossible to address Hiperface memory (239)8.7.59 F2110 Error in non-cyclical data communic. of power section (240)8.7.60 F2120 MMC: Defective or missing, replace (240)8.7.61 F2121 MMC: Incorrect data or file, create correctly (241)8.7.62 F2122 MMC: Incorrect IBF file, correct it (241)8.7.63 F2123 Retain data backup impossible (242)8.7.64 F2124 MMC: Saving too slowly, replace (243)8.7.65 F2130 Error comfort control panel (243)8.7.66 F2140 CCD slave error (243)8.7.67 F2150 MLD motion function block error (244)8.7.68 F2174 Loss of motor encoder reference (244)8.7.69 F2175 Loss of optional encoder reference (245)Troubleshooting Guide | Rexroth IndraDrive Electric Drivesand Controls| Bosch Rexroth AG IX/XXIITable of ContentsPage8.7.70 F2176 Loss of measuring encoder reference (246)8.7.71 F2177 Modulo limitation error of motor encoder (246)8.7.72 F2178 Modulo limitation error of optional encoder (247)8.7.73 F2179 Modulo limitation error of measuring encoder (247)8.7.74 F2190 Incorrect Ethernet configuration (248)8.7.75 F2260 Command current limit shutoff (249)8.7.76 F2270 Analog input 1 or 2, wire break (249)8.7.77 F2802 PLL is not synchronized (250)8.7.78 F2814 Undervoltage in mains (250)8.7.79 F2815 Overvoltage in mains (251)8.7.80 F2816 Softstart fault power supply unit (251)8.7.81 F2817 Overvoltage in power section (251)8.7.82 F2818 Phase failure (252)8.7.83 F2819 Mains failure (253)8.7.84 F2820 Braking resistor overload (253)8.7.85 F2821 Error in control of braking resistor (254)8.7.86 F2825 Switch-on threshold braking resistor too low (255)8.7.87 F2833 Ground fault in motor line (255)8.7.88 F2834 Contactor control error (256)8.7.89 F2835 Mains contactor wiring error (256)8.7.90 F2836 DC bus balancing monitor error (257)8.7.91 F2837 Contactor monitoring error (257)8.7.92 F2840 Error supply shutdown (257)8.7.93 F2860 Overcurrent in mains-side power section (258)8.7.94 F2890 Invalid device code (259)8.7.95 F2891 Incorrect interrupt timing (259)8.7.96 F2892 Hardware variant not supported (259)8.8 SERCOS Error Codes / Error Messages of Serial Communication (259)9 Warnings (Exxxx) (263)9.1 Fatal Warnings (E8xxx) (263)9.1.1 Behavior in the Case of Fatal Warnings (263)9.1.2 E8025 Overvoltage in power section (263)9.1.3 E8026 Undervoltage in power section (264)9.1.4 E8027 Safe torque off while drive enabled (265)9.1.5 E8028 Overcurrent in power section (265)9.1.6 E8029 Positive position limit exceeded (266)9.1.7 E8030 Negative position limit exceeded (267)9.1.8 E8034 Emergency-Stop (268)9.1.9 E8040 Torque/force actual value limit active (268)9.1.10 E8041 Current limit active (269)9.1.11 E8042 Both travel range limit switches activated (269)9.1.12 E8043 Positive travel range limit switch activated (270)9.1.13 E8044 Negative travel range limit switch activated (271)9.1.14 E8055 Motor overload, current limit active (271)9.1.15 E8057 Device overload, current limit active (272)X/XXII Bosch Rexroth AG | Electric Drivesand ControlsRexroth IndraDrive | Troubleshooting GuideTable of ContentsPage9.1.16 E8058 Drive system not ready for operation (273)9.1.17 E8260 Torque/force command value limit active (273)9.1.18 E8802 PLL is not synchronized (274)9.1.19 E8814 Undervoltage in mains (275)9.1.20 E8815 Overvoltage in mains (275)9.1.21 E8818 Phase failure (276)9.1.22 E8819 Mains failure (276)9.2 Warnings of Category E4xxx (277)9.2.1 E4001 Double MST failure shutdown (277)9.2.2 E4002 Double MDT failure shutdown (278)9.2.3 E4005 No command value input via master communication (279)9.2.4 E4007 SERCOS III: Consumer connection failed (280)9.2.5 E4008 Invalid addressing command value data container A (280)9.2.6 E4009 Invalid addressing actual value data container A (281)9.2.7 E4010 Slave not scanned or address 0 (281)9.2.8 E4012 Maximum number of CCD slaves exceeded (282)9.2.9 E4013 Incorrect CCD addressing (282)9.2.10 E4014 Incorrect phase switch of CCD slaves (283)9.3 Possible Warnings When Operating Safety Technology (E3xxx) (283)9.3.1 Behavior in Case a Safety Technology Warning Occurs (283)9.3.2 E3100 Error when checking input signals (284)9.3.3 E3101 Error when checking acknowledgment signal (284)9.3.4 E3102 Actual position values validation error (285)9.3.5 E3103 Dynamization failed (285)9.3.6 E3104 Safety parameters validation error (286)9.3.7 E3105 Validation error of safe operation mode (286)9.3.8 E3106 System error safety technology (287)9.3.9 E3107 Safe reference missing (287)9.3.10 E3108 Safely-monitored deceleration exceeded (288)9.3.11 E3110 Time interval of forced dynamization exceeded (289)9.3.12 E3115 Prewarning, end of brake check time interval (289)9.3.13 E3116 Nominal load torque of holding system reached (290)9.4 Non-Fatal Warnings (E2xxx) (290)9.4.1 Behavior in Case a Non-Fatal Warning Occurs (290)9.4.2 E2010 Position control with encoder 2 not possible (291)9.4.3 E2011 PLC - Warning no. 1 (291)9.4.4 E2012 PLC - Warning no. 2 (291)9.4.5 E2013 PLC - Warning no. 3 (292)9.4.6 E2014 PLC - Warning no. 4 (292)9.4.7 E2021 Motor temperature outside of measuring range (292)9.4.8 E2026 Undervoltage in power section (293)9.4.9 E2040 Device overtemperature 2 prewarning (294)9.4.10 E2047 Interpolation velocity = 0 (294)9.4.11 E2048 Interpolation acceleration = 0 (295)9.4.12 E2049 Positioning velocity >= limit value (296)9.4.13 E2050 Device overtemp. Prewarning (297)Troubleshooting Guide | Rexroth IndraDrive Electric Drivesand Controls| Bosch Rexroth AG XI/XXIITable of ContentsPage9.4.14 E2051 Motor overtemp. prewarning (298)9.4.15 E2053 Target position out of travel range (298)9.4.16 E2054 Not homed (300)9.4.17 E2055 Feedrate override S-0-0108 = 0 (300)9.4.18 E2056 Torque limit = 0 (301)9.4.19 E2058 Selected positioning block has not been programmed (302)9.4.20 E2059 Velocity command value limit active (302)9.4.21 E2061 Device overload prewarning (303)9.4.22 E2063 Velocity command value > limit value (304)9.4.23 E2064 Target position out of num. range (304)9.4.24 E2069 Holding brake torque too low (305)9.4.25 E2070 Acceleration limit active (306)9.4.26 E2074 Encoder 1: Encoder signals disturbed (306)9.4.27 E2075 Encoder 2: Encoder signals disturbed (307)9.4.28 E2076 Measuring encoder: Encoder signals disturbed (308)9.4.29 E2077 Absolute encoder monitoring, motor encoder (encoder alarm) (308)9.4.30 E2078 Absolute encoder monitoring, opt. encoder (encoder alarm) (309)9.4.31 E2079 Absolute enc. monitoring, measuring encoder (encoder alarm) (309)9.4.32 E2086 Prewarning supply module overload (310)9.4.33 E2092 Internal synchronization defective (310)9.4.34 E2100 Positioning velocity of master axis generator too high (311)9.4.35 E2101 Acceleration of master axis generator is zero (312)9.4.36 E2140 CCD error at node (312)9.4.37 E2270 Analog input 1 or 2, wire break (312)9.4.38 E2802 HW control of braking resistor (313)9.4.39 E2810 Drive system not ready for operation (314)9.4.40 E2814 Undervoltage in mains (314)9.4.41 E2816 Undervoltage in power section (314)9.4.42 E2818 Phase failure (315)9.4.43 E2819 Mains failure (315)9.4.44 E2820 Braking resistor overload prewarning (316)9.4.45 E2829 Not ready for power on (316)。
Glider Flying Handbook说明书

Glider Flying Handbook2013U.S. Department of TransportationFEDERAL AVIATION ADMINISTRATIONFlight Standards Servicei iPrefaceThe Glider Flying Handbook is designed as a technical manual for applicants who are preparing for glider category rating and for currently certificated glider pilots who wish to improve their knowledge. Certificated flight instructors will find this handbook a valuable training aid, since detailed coverage of aeronautical decision-making, components and systems, aerodynamics, flight instruments, performance limitations, ground operations, flight maneuvers, traffic patterns, emergencies, soaring weather, soaring techniques, and cross-country flight is included. Topics such as radio navigation and communication, use of flight information publications, and regulations are available in other Federal Aviation Administration (FAA) publications.The discussion and explanations reflect the most commonly used practices and principles. Occasionally, the word “must” or similar language is used where the desired action is deemed critical. The use of such language is not intended to add to, interpret, or relieve a duty imposed by Title 14 of the Code of Federal Regulations (14 CFR). Persons working towards a glider rating are advised to review the references from the applicable practical test standards (FAA-G-8082-4, Sport Pilot and Flight Instructor with a Sport Pilot Rating Knowledge Test Guide, FAA-G-8082-5, Commercial Pilot Knowledge Test Guide, and FAA-G-8082-17, Recreational Pilot and Private Pilot Knowledge Test Guide). Resources for study include FAA-H-8083-25, Pilot’s Handbook of Aeronautical Knowledge, FAA-H-8083-2, Risk Management Handbook, and Advisory Circular (AC) 00-6, Aviation Weather For Pilots and Flight Operations Personnel, AC 00-45, Aviation Weather Services, as these documents contain basic material not duplicated herein. All beginning applicants should refer to FAA-H-8083-25, Pilot’s Handbook of Aeronautical Knowledge, for study and basic library reference.It is essential for persons using this handbook to become familiar with and apply the pertinent parts of 14 CFR and the Aeronautical Information Manual (AIM). The AIM is available online at . The current Flight Standards Service airman training and testing material and learning statements for all airman certificates and ratings can be obtained from .This handbook supersedes FAA-H-8083-13, Glider Flying Handbook, dated 2003. Always select the latest edition of any publication and check the website for errata pages and listing of changes to FAA educational publications developed by the FAA’s Airman Testing Standards Branch, AFS-630.This handbook is available for download, in PDF format, from .This handbook is published by the United States Department of Transportation, Federal Aviation Administration, Airman Testing Standards Branch, AFS-630, P.O. Box 25082, Oklahoma City, OK 73125.Comments regarding this publication should be sent, in email form, to the following address:********************************************John M. AllenDirector, Flight Standards Serviceiiii vAcknowledgmentsThe Glider Flying Handbook was produced by the Federal Aviation Administration (FAA) with the assistance of Safety Research Corporation of America (SRCA). The FAA wishes to acknowledge the following contributors: Sue Telford of Telford Fishing & Hunting Services for images used in Chapter 1JerryZieba () for images used in Chapter 2Tim Mara () for images used in Chapters 2 and 12Uli Kremer of Alexander Schleicher GmbH & Co for images used in Chapter 2Richard Lancaster () for images and content used in Chapter 3Dave Nadler of Nadler & Associates for images used in Chapter 6Dave McConeghey for images used in Chapter 6John Brandon (www.raa.asn.au) for images and content used in Chapter 7Patrick Panzera () for images used in Chapter 8Jeff Haby (www.theweatherprediction) for images used in Chapter 8National Soaring Museum () for content used in Chapter 9Bill Elliot () for images used in Chapter 12.Tiffany Fidler for images used in Chapter 12.Additional appreciation is extended to the Soaring Society of America, Inc. (), the Soaring Safety Foundation, and Mr. Brad Temeyer and Mr. Bill Martin from the National Oceanic and Atmospheric Administration (NOAA) for their technical support and input.vv iPreface (iii)Acknowledgments (v)Table of Contents (vii)Chapter 1Gliders and Sailplanes ........................................1-1 Introduction....................................................................1-1 Gliders—The Early Years ..............................................1-2 Glider or Sailplane? .......................................................1-3 Glider Pilot Schools ......................................................1-4 14 CFR Part 141 Pilot Schools ...................................1-5 14 CFR Part 61 Instruction ........................................1-5 Glider Certificate Eligibility Requirements ...................1-5 Common Glider Concepts ..............................................1-6 Terminology...............................................................1-6 Converting Metric Distance to Feet ...........................1-6 Chapter 2Components and Systems .................................2-1 Introduction....................................................................2-1 Glider Design .................................................................2-2 The Fuselage ..................................................................2-4 Wings and Components .............................................2-4 Lift/Drag Devices ...........................................................2-5 Empennage .....................................................................2-6 Towhook Devices .......................................................2-7 Powerplant .....................................................................2-7 Self-Launching Gliders .............................................2-7 Sustainer Engines .......................................................2-8 Landing Gear .................................................................2-8 Wheel Brakes .............................................................2-8 Chapter 3Aerodynamics of Flight .......................................3-1 Introduction....................................................................3-1 Forces of Flight..............................................................3-2 Newton’s Third Law of Motion .................................3-2 Lift ..............................................................................3-2The Effects of Drag on a Glider .....................................3-3 Parasite Drag ..............................................................3-3 Form Drag ...............................................................3-3 Skin Friction Drag ..................................................3-3 Interference Drag ....................................................3-5 Total Drag...................................................................3-6 Wing Planform ...........................................................3-6 Elliptical Wing ........................................................3-6 Rectangular Wing ...................................................3-7 Tapered Wing .........................................................3-7 Swept-Forward Wing ..............................................3-7 Washout ..................................................................3-7 Glide Ratio .................................................................3-8 Aspect Ratio ............................................................3-9 Weight ........................................................................3-9 Thrust .........................................................................3-9 Three Axes of Rotation ..................................................3-9 Stability ........................................................................3-10 Flutter .......................................................................3-11 Lateral Stability ........................................................3-12 Turning Flight ..............................................................3-13 Load Factors .................................................................3-13 Radius of Turn ..........................................................3-14 Turn Coordination ....................................................3-15 Slips ..........................................................................3-15 Forward Slip .........................................................3-16 Sideslip .................................................................3-17 Spins .........................................................................3-17 Ground Effect ...............................................................3-19 Chapter 4Flight Instruments ...............................................4-1 Introduction....................................................................4-1 Pitot-Static Instruments ..................................................4-2 Impact and Static Pressure Lines................................4-2 Airspeed Indicator ......................................................4-2 The Effects of Altitude on the AirspeedIndicator..................................................................4-3 Types of Airspeed ...................................................4-3Table of ContentsviiAirspeed Indicator Markings ......................................4-5 Other Airspeed Limitations ........................................4-6 Altimeter .....................................................................4-6 Principles of Operation ...........................................4-6 Effect of Nonstandard Pressure andTemperature............................................................4-7 Setting the Altimeter (Kollsman Window) .............4-9 Types of Altitude ......................................................4-10 Variometer................................................................4-11 Total Energy System .............................................4-14 Netto .....................................................................4-14 Electronic Flight Computers ....................................4-15 Magnetic Compass .......................................................4-16 Yaw String ................................................................4-16 Inclinometer..............................................................4-16 Gyroscopic Instruments ...............................................4-17 G-Meter ........................................................................4-17 FLARM Collision Avoidance System .........................4-18 Chapter 5Glider Performance .............................................5-1 Introduction....................................................................5-1 Factors Affecting Performance ......................................5-2 High and Low Density Altitude Conditions ...........5-2 Atmospheric Pressure .............................................5-2 Altitude ...................................................................5-3 Temperature............................................................5-3 Wind ...........................................................................5-3 Weight ........................................................................5-5 Rate of Climb .................................................................5-7 Flight Manuals and Placards ..........................................5-8 Placards ......................................................................5-8 Performance Information ...........................................5-8 Glider Polars ...............................................................5-8 Weight and Balance Information .............................5-10 Limitations ...............................................................5-10 Weight and Balance .....................................................5-12 Center of Gravity ......................................................5-12 Problems Associated With CG Forward ofForward Limit .......................................................5-12 Problems Associated With CG Aft of Aft Limit ..5-13 Sample Weight and Balance Problems ....................5-13 Ballast ..........................................................................5-14 Chapter 6Preflight and Ground Operations .......................6-1 Introduction....................................................................6-1 Assembly and Storage Techniques ................................6-2 Trailering....................................................................6-3 Tiedown and Securing ................................................6-4Water Ballast ..............................................................6-4 Ground Handling........................................................6-4 Launch Equipment Inspection ....................................6-5 Glider Preflight Inspection .........................................6-6 Prelaunch Checklist ....................................................6-7 Glider Care .....................................................................6-7 Preventive Maintenance .............................................6-8 Chapter 7Launch and Recovery Procedures and Flight Maneuvers ............................................................7-1 Introduction....................................................................7-1 Aerotow Takeoff Procedures .........................................7-2 Signals ........................................................................7-2 Prelaunch Signals ....................................................7-2 Inflight Signals ........................................................7-3 Takeoff Procedures and Techniques ..........................7-3 Normal Assisted Takeoff............................................7-4 Unassisted Takeoff.....................................................7-5 Crosswind Takeoff .....................................................7-5 Assisted ...................................................................7-5 Unassisted...............................................................7-6 Aerotow Climb-Out ....................................................7-6 Aerotow Release.........................................................7-8 Slack Line ...................................................................7-9 Boxing the Wake ......................................................7-10 Ground Launch Takeoff Procedures ............................7-11 CG Hooks .................................................................7-11 Signals ......................................................................7-11 Prelaunch Signals (Winch/Automobile) ...............7-11 Inflight Signals ......................................................7-12 Tow Speeds ..............................................................7-12 Automobile Launch ..................................................7-14 Crosswind Takeoff and Climb .................................7-14 Normal Into-the-Wind Launch .................................7-15 Climb-Out and Release Procedures ..........................7-16 Self-Launch Takeoff Procedures ..............................7-17 Preparation and Engine Start ....................................7-17 Taxiing .....................................................................7-18 Pretakeoff Check ......................................................7-18 Normal Takeoff ........................................................7-19 Crosswind Takeoff ...................................................7-19 Climb-Out and Shutdown Procedures ......................7-19 Landing .....................................................................7-21 Gliderport/Airport Traffic Patterns and Operations .....7-22 Normal Approach and Landing ................................7-22 Crosswind Landing ..................................................7-25 Slips ..........................................................................7-25 Downwind Landing ..................................................7-27 After Landing and Securing .....................................7-27viiiPerformance Maneuvers ..............................................7-27 Straight Glides ..........................................................7-27 Turns.........................................................................7-28 Roll-In ...................................................................7-29 Roll-Out ................................................................7-30 Steep Turns ...........................................................7-31 Maneuvering at Minimum Controllable Airspeed ...7-31 Stall Recognition and Recovery ...............................7-32 Secondary Stalls ....................................................7-34 Accelerated Stalls .................................................7-34 Crossed-Control Stalls ..........................................7-35 Operating Airspeeds .....................................................7-36 Minimum Sink Airspeed ..........................................7-36 Best Glide Airspeed..................................................7-37 Speed to Fly ..............................................................7-37 Chapter 8Abnormal and Emergency Procedures .............8-1 Introduction....................................................................8-1 Porpoising ......................................................................8-2 Pilot-Induced Oscillations (PIOs) ..............................8-2 PIOs During Launch ...................................................8-2 Factors Influencing PIOs ........................................8-2 Improper Elevator Trim Setting ..............................8-3 Improper Wing Flaps Setting ..................................8-3 Pilot-Induced Roll Oscillations During Launch .........8-3 Pilot-Induced Yaw Oscillations During Launch ........8-4 Gust-Induced Oscillations ..............................................8-5 Vertical Gusts During High-Speed Cruise .................8-5 Pilot-Induced Pitch Oscillations During Landing ......8-6 Glider-Induced Oscillations ...........................................8-6 Pitch Influence of the Glider Towhook Position ........8-6 Self-Launching Glider Oscillations During Powered Flight ...........................................................8-7 Nosewheel Glider Oscillations During Launchesand Landings ..............................................................8-7 Tailwheel/Tailskid Equipped Glider Oscillations During Launches and Landings ..................................8-8 Aerotow Abnormal and Emergency Procedures ............8-8 Abnormal Procedures .................................................8-8 Towing Failures........................................................8-10 Tow Failure With Runway To Land and Stop ......8-11 Tow Failure Without Runway To Land BelowReturning Altitude ................................................8-11 Tow Failure Above Return to Runway Altitude ...8-11 Tow Failure Above 800' AGL ..............................8-12 Tow Failure Above Traffic Pattern Altitude .........8-13 Slack Line .................................................................8-13 Ground Launch Abnormal and Emergency Procedures ....................................................................8-14 Abnormal Procedures ...............................................8-14 Emergency Procedures .............................................8-14 Self-Launch Takeoff Emergency Procedures ..............8-15 Emergency Procedures .............................................8-15 Spiral Dives ..................................................................8-15 Spins .............................................................................8-15 Entry Phase ...............................................................8-17 Incipient Phase .........................................................8-17 Developed Phase ......................................................8-17 Recovery Phase ........................................................8-17 Off-Field Landing Procedures .....................................8-18 Afterlanding Off Field .............................................8-20 Off-Field Landing Without Injury ........................8-20 Off-Field Landing With Injury .............................8-20 System and Equipment Malfunctions ..........................8-20 Flight Instrument Malfunctions ................................8-20 Airspeed Indicator Malfunctions ..........................8-21 Altimeter Malfunctions .........................................8-21 Variometer Malfunctions ......................................8-21 Compass Malfunctions .........................................8-21 Glider Canopy Malfunctions ....................................8-21 Broken Glider Canopy ..........................................8-22 Frosted Glider Canopy ..........................................8-22 Water Ballast Malfunctions ......................................8-22 Retractable Landing Gear Malfunctions ..................8-22 Primary Flight Control Systems ...............................8-22 Elevator Malfunctions ..........................................8-22 Aileron Malfunctions ............................................8-23 Rudder Malfunctions ............................................8-24 Secondary Flight Controls Systems .........................8-24 Elevator Trim Malfunctions .................................8-24 Spoiler/Dive Brake Malfunctions .........................8-24 Miscellaneous Flight System Malfunctions .................8-25 Towhook Malfunctions ............................................8-25 Oxygen System Malfunctions ..................................8-25 Drogue Chute Malfunctions .....................................8-25 Self-Launching Gliders ................................................8-26 Self-Launching/Sustainer Glider Engine Failure During Takeoff or Climb ..........................................8-26 Inability to Restart a Self-Launching/SustainerGlider Engine While Airborne .................................8-27 Self-Launching Glider Propeller Malfunctions ........8-27 Self-Launching Glider Electrical System Malfunctions .............................................................8-27 In-flight Fire .............................................................8-28 Emergency Equipment and Survival Gear ...................8-28 Survival Gear Checklists ..........................................8-28 Food and Water ........................................................8-28ixClothing ....................................................................8-28 Communication ........................................................8-29 Navigation Equipment ..............................................8-29 Medical Equipment ..................................................8-29 Stowage ....................................................................8-30 Parachute ..................................................................8-30 Oxygen System Malfunctions ..................................8-30 Accident Prevention .....................................................8-30 Chapter 9Soaring Weather ..................................................9-1 Introduction....................................................................9-1 The Atmosphere .............................................................9-2 Composition ...............................................................9-2 Properties ....................................................................9-2 Temperature............................................................9-2 Density ....................................................................9-2 Pressure ...................................................................9-2 Standard Atmosphere .................................................9-3 Layers of the Atmosphere ..........................................9-4 Scale of Weather Events ................................................9-4 Thermal Soaring Weather ..............................................9-6 Thermal Shape and Structure .....................................9-6 Atmospheric Stability .................................................9-7 Air Masses Conducive to Thermal Soaring ...................9-9 Cloud Streets ..............................................................9-9 Thermal Waves...........................................................9-9 Thunderstorms..........................................................9-10 Lifted Index ..........................................................9-12 K-Index .................................................................9-12 Weather for Slope Soaring .......................................9-14 Mechanism for Wave Formation ..............................9-16 Lift Due to Convergence ..........................................9-19 Obtaining Weather Information ...................................9-21 Preflight Weather Briefing........................................9-21 Weather-ReIated Information ..................................9-21 Interpreting Weather Charts, Reports, andForecasts ......................................................................9-23 Graphic Weather Charts ...........................................9-23 Winds and Temperatures Aloft Forecast ..............9-23 Composite Moisture Stability Chart .....................9-24 Chapter 10Soaring Techniques ..........................................10-1 Introduction..................................................................10-1 Thermal Soaring ...........................................................10-2 Locating Thermals ....................................................10-2 Cumulus Clouds ...................................................10-2 Other Indicators of Thermals ................................10-3 Wind .....................................................................10-4 The Big Picture .....................................................10-5Entering a Thermal ..............................................10-5 Inside a Thermal.......................................................10-6 Bank Angle ...........................................................10-6 Speed .....................................................................10-6 Centering ...............................................................10-7 Collision Avoidance ................................................10-9 Exiting a Thermal .....................................................10-9 Atypical Thermals ..................................................10-10 Ridge/Slope Soaring ..................................................10-10 Traps ......................................................................10-10 Procedures for Safe Flying .....................................10-12 Bowls and Spurs .....................................................10-13 Slope Lift ................................................................10-13 Obstructions ...........................................................10-14 Tips and Techniques ...............................................10-15 Wave Soaring .............................................................10-16 Preflight Preparation ...............................................10-17 Getting Into the Wave ............................................10-18 Flying in the Wave .................................................10-20 Soaring Convergence Zones ...................................10-23 Combined Sources of Updrafts ..............................10-24 Chapter 11Cross-Country Soaring .....................................11-1 Introduction..................................................................11-1 Flight Preparation and Planning ...................................11-2 Personal and Special Equipment ..................................11-3 Navigation ....................................................................11-5 Using the Plotter .......................................................11-5 A Sample Cross-Country Flight ...............................11-5 Navigation Using GPS .............................................11-8 Cross-Country Techniques ...........................................11-9 Soaring Faster and Farther .........................................11-11 Height Bands ..........................................................11-11 Tips and Techniques ...............................................11-12 Special Situations .......................................................11-14 Course Deviations ..................................................11-14 Lost Procedures ......................................................11-14 Cross-Country Flight in a Self-Launching Glider .....11-15 High-Performance Glider Operations and Considerations ............................................................11-16 Glider Complexity ..................................................11-16 Water Ballast ..........................................................11-17 Cross-Country Flight Using Other Lift Sources ........11-17 Chapter 12Towing ................................................................12-1 Introduction..................................................................12-1 Equipment Inspections and Operational Checks .........12-2 Tow Hook ................................................................12-2 Schweizer Tow Hook ...........................................12-2x。
汽车配件说明书

Indicators................................ 131 Shift Lever Positions ................. 131 Shift Lock Release..................... 134
- 1、下载文档前请自行甄别文档内容的完整性,平台不提供额外的编辑、内容补充、找答案等附加服务。
- 2、"仅部分预览"的文档,不可在线预览部分如存在完整性等问题,可反馈申请退款(可完整预览的文档不适用该条件!)。
- 3、如文档侵犯您的权益,请联系客服反馈,我们会尽快为您处理(人工客服工作时间:9:00-18:30)。
Analysis of failed aircraft wheel assemblyTakao Kobayashi,Donald A.Shockey*Center for Fracture Physics,Materials Research Laboratory,SRI International,Menlo Park,CA 94025,United StatesReceived 15November 2004;accepted 5December 2004Available online 13April 2005AbstractA failed wheel assembly from a Hawker 125-800XP corporate passenger jet was investigated to determine the root cause of the failure.Different levels of damage sustained by the 12tie bolt/nut couples that had held the flange to the wheel showed that failure was a cascading sequence that began at one couple and spread to adjacent couples.The sus-pected initiating bolt/nut couple showed stepped threads on one side of the bolt,the characteristics of which suggested that the nut had cracked,disengaged,and induced the failures of the other bolt/nut couples.Since the nut was not avail-able for examination,our conclusion that the root cause of failure was a cracked nut could not be confirmed.Somewhat later,however,a cracked nut was observed in another wheel assembly.Examination of the bolt showed similar thread deformation,supporting the initial conclusion.The nut fracture surfaces showed an intergranular region surrounded by a ductile field –most likely the crack initiation site where the grain boundaries were weak.In our expert opinion,the root cause of the wheel assembly failure was a cracked nut that may have been embrittled by hydrogen during cadmium plating.Ó2005Published by Elsevier Ltd.Keywords:Failure analysis;Fracture surfaces;Hydrogen embrittlement;Landing gear;Threaded fasteners1.IntroductionThe fleet of Raytheon Hawker 125-800XP corporate passenger jets consists of about 600aircraft.Each aircraft experiences some 400takeoff-and-landing cycles annually.The wheel assemblies are periodically inspected and new tires are periodically installed.There exists no criterion to change bolts after some period of service.Consequently,bolts typically remain in service for 4000–5000cycles.Nuts are changed after about 400cycles.1350-6307/$-see front matter Ó2005Published by Elsevier Ltd.doi:10.1016/j.engfailanal.2004.12.046*Corresponding author.Tel.:+16508592587;fax:+16508592260.E-mail address:donald.shockey@ (D.A.Shockey).Engineering Failure Analysis 13(2006)65–7466T.Kobayashi,D.A.Shockey/Engineering Failure Analysis13(2006)65–74 Wheel assembly failures are rare,but when they occur,they occur soon after a tire is replaced and the aircraft goes back into service,usually before20takeoff-and-landing cycles;some after only a few cycles. Thefleet experiencedfive failures of the main landing gear wheel assembly in the past12months.In all cases the wheelflange,which is held to the hub by12tie bolts and nuts,separated from the hub.The fail-ures were suspected to result from the nuts loosening on the bolts.In attempting to prevent wheel assembly failures,bolt and nut specifications were checked and numerous internal policy adjustments were made.The wheel manufacturer examined the bolts and nuts carefully and verified conformity to metallurgical and dimensional military specifications(Mil Spec MIL-DTL-25027H). The air station required that(1)two people verify the correct torque of the bolts,(2)two people verify that every maintenance manual step is followed,(3)only new hardware be installed at build-up,and(4)torque seals be checked to verify that the correct torque has been applied.Unfortunately,even with these new pro-cedures the problem continued.The air station asked SRI to examine the bolts and nuts from a failed wheel assembly andfind the root cause of the failure.This paper describes the procedures,observations,and conclusions of the analysis.2.Investigation of a failed wheel assemblyThe particular wheel assembly sent to us for examination had failed after15flight cycles.In the condi-tion it was received,only two of the bolts still had nuts attached,and those bolts were bent.The other10 bolts had been removed from theflange holes and the nuts were lost.We examined the12bolts visually and with a light microscope and photographed each at four90°an-gles.Four bolts were bent,including the two that still had nuts attached;four bolts exhibited stripped threads near the bolt ends;and four bolts had no damage obvious to the unaided eye.Fig.1shows a bolt from each damage category.The type and extent of damage indicated the sequence of bolt failure and the positions of the bolts rel-ative to each other in the wheelflange.The two bent bolts with washers and nuts intact were the last two bolts connecting theflange and the hub.Since the other10bolt/nut couples had failed,the separatingflange exerted large lateral stresses on the bolts,causing the bolts to bend.We designated these as Bolts#1and#2 and arbitrarily placed them in the bolt ring as shown in Fig.2.The two bent bolts without a nut(#3and#4)were bent to a lesser degree by the separatingflange,but the threads at the bolt ends were stripped when the nuts sheared off.Bolts#3and#4were probably the next pair to fail and were probably located on either side of Bolts#1 and#2.Bolt#4was probably adjacent to Bolt#2and Bolt#1was probably adjacent to Bolt#3,because the bend angles of these pairs were similar.The stripped threads were near the ends of the bolts,indicating that the nuts had already backed offseveral threads when the stripping occurred.Furthermore,the threads were stripped all around the bolts(360°).Bolts#5–#8were not bent,but their threads were stripped near the bolt ends.The locations of the stripped threads showed that the nuts had already moved to near the bolt ends when the load exerted by the partially separatedflange was exerted.Thus,these four bolts were probably located two each on either side of the four bent bolts as shown in Fig.2.We used the number of stripped threads to position these bolts.Thefinal four bolts(#9–#12),which showed no apparent thread damage,were probably thefirst to lose their nuts,and did so before theflange separated appreciably from the hub.Therefore,one of these bolt/nut couples probably started the sequence of events that led to wheel assembly failure.Pre-sumably the nut on one of these bolts loosened,caused the next-neighbor bolt/nut couples to loosen, which in turn caused their next-neighbor couples to loosen,and so on until only two bolt/nut couples(those with bent bolts)remained.Thus,wheel failure was a cascading event beginning with one bolt/nut couple.To identify the first-to-fail bolt and the probable root cause of the wheel failure,we examined the four suspect bolts (Bolts #9–#12)carefully,quantitatively characterizing the thread profiles,interrogating the thread surfaces and metallographic cross sections,and measuring hardness.2.1.Examination of bolt thread profilesWe imaged the threads of the four suspect bolts with an optical comparator,producing a profile every 15degrees around the circumference.No profile anomalies were observed on suspect Bolts #9,#11,and #12.Bolt #10,however,exhibited steps on the load-bearing faces of certain threads,indicated by the arrows in Fig.3.The steps occurred on only 7threads;threads on either side of this group of 7showed no steps.The stepped threads lay under the nut when the nut was in its tightened position.The location of the step on the thread face increased from thread to thread almost linearly with distance from the bolt end (shown more clearly in Fig.7).Fig.4shows profile images at several angular positions.The two lines on the center thread show the magnitude of the step at several angular positions.A plot of step magnitude as a function of the angle (Fig.5)shows that the steps existed on only one side of the bolt.Bolts #1–#8were examined in a similar manner.Bolts #3–#8had stripped threads,but the profile of threads adjacent to the stripped threads did not have steps similar to those found in Bolt#10.Fig.1.Photographs of bolts from each damage category:(a)bent;(b)stripped (note last four threads of Bolt #5);and (c)no apparent damage.T.Kobayashi,D.A.Shockey /Engineering Failure Analysis 13(2006)65–74672.2.Metallographic cross-section of Bolt #10We investigated these steps further by cross-sectioning Bolt #10,then polishing and etching the surface of the section.Consistent with the comparator results in Fig.3,steps were evident on certain threads,namely those that engaged the nut while the nut was in the tightened position (Fig.6).Threads on either side of the tightened nut position exhibited no steps.And,as also observed with the comparator,the steps existed on only one side of the bolt.The position of the step on the thread face shifted linearly from one thread to the other toward the bolt end (Fig.7),providing a clue about how the nut interacted with thebolt.Fig.3.Optical comparator image of threads of Bolt #10,showing the steps on threadfaces.Fig.2.Wheel flange and relative bolt positions based on bolt damage observations.68T.Kobayashi,D.A.Shockey /Engineering Failure Analysis 13(2006)65–74The optical micrograph of the three threads in Fig.8shows that the top portion of the threads was pushed to the left (toward the bolt end),producing a step on the load-bearing thread face and a protrusion and fold on the unloaded face,indicating that these threads experienced overloading from the wheel flange.2.3.Summary of Bolt #10observationsSteps on the faces of certain threads of Bolt #10were evident,as shown in Figs.3,6,7and 8.Step char-acteristics are as follows.Steps appear only on 7threads.Threads to either side have no steps.The stepped threads all lie under the nut in the tightened position.Step size (lateral dimension)is greatest on the center threads and decreases to either side.Step location on thread faces is highest near the flange,lowest near the bolt end. Steps exist only halfway around the bolt circumference;threads on the other half have nosteps.Fig.4.Optical comparator images of steps found on the threads of Bolt #10as a function of position around the axis of the bolt.T.Kobayashi,D.A.Shockey /Engineering Failure Analysis 13(2006)65–74692.4.Implications of the observationsThe steps were produced by an overload transmitted by the nut.The nut was in its tightened position when the steps were produced.Since the steps exist only around half (approximately)of thecircumference,Fig.5.Step magnitude as a function of angular position for Bolt#10.Fig.6.Macro SEM image of Bolt #10cross-section.70T.Kobayashi,D.A.Shockey /Engineering Failure Analysis 13(2006)65–74the overload was applied only on one side.This indicates that the nut split,relieved the load on the bolt threads on the split side,and overloaded the opposite side,causing plastic deformation of the threads.The progressive change in step height on successive threads and the absence of steps on the opposite side of the bolt suggest that the nut was cocked when it deformed the bolt threads.The load exerted on the bolt thread was reduced on the broken side of the nut and concentrated on the other side,and the difference in the load lines generated a moment,as shown in Fig.9.A further indication that the nut split is that the thread-stripping process was interrupted.We hypoth-esize that this interruption occurred because the nut deformed,the split widened,and the nut disengaged and fell away.We conclude that a cracked nut was the root cause of the wheel assembly failure.The nut could have contained a crack when it was fabricated,or could have acquired a crack when it was torqued during instal-lation or when the aircraft was in service (an unusually heavy landing load,for example).Moreover,the high-strength steel nut could have been weakened by hydrogen effects during the cadmium coatingprocess.Fig.7.Increasing position of step on the face of adjacentthreads.Fig.8.Metallographic image of three deformedthreads.Fig.9.Moment caused by the difference in the load lines.T.Kobayashi,D.A.Shockey /Engineering Failure Analysis 13(2006)65–747172T.Kobayashi,D.A.Shockey/Engineering Failure Analysis13(2006)65–74Unfortunately,the nut on Bolt#10was lost while the aircraft was in service and thus was not available for examination,and so the cracked-nut hypothesis could not be confirmed.3.Analysis of a cracked nut/bolt couple from a second wheel assemblySoon after reporting ourfindings and our opinion that the root cause of the wheel assembly failure was a cracked nut,we were told that a maintenance worker had newly observed a wheel assembly that had a cracked nut still on the bolt.When we were provided with the bolt and nut,we measured the bolt thread profile with the optical comparator and examined a cross-section,as we did for Bolt#10,to check for steps and determine their characteristics.We compared the results with those from Bolt#10to check our cracked-nut hypothesis.We also examined the nut fracture surfaces to seek the root cause of nut failure.3.1.Examination of second bolt threads and comparison with Bolt#10Optical comparator images of thread profiles at15°intervals were produced just as for Bolt#10.Steps on certain thread faces were evident.The two bolts were similar in that all stepped threads lay in the tight-ened nut zone(and nowhere else),and the steps were larger on one side of the bolt.However,the second bolt had onlyfive stepped threads and the steps were less severe and less localized.We sectioned the bolt axially on the90°/270°plane and polished and etched the cross-section in a2% nital solution to observe the subsurface deformation and microstructure.As with Bolt#10,the threads with steps were in the tightened nut position zone and the height of the steps above the thread groove increased from thread to thread.Higher magnification metallographic images showed that the threads at the90°position had steps about three times larger than threads at the270°position.However,the steps were smaller and less distinct than those in Bolt#10,and were not associated with clear slip lines.In summary,the deformation observed in the bolt with the split nut had similar characteristics as those found in Bolt#10.The extent of deformation in Bolt#10was greater,perhaps because the cracked nut on the second bolt had acted on the bolt for a shorter time.3.2.Examination of fracture surface of cracked nutThe fracture surfaces of the cracked nut were exposed by cutting through the wall opposite the crack. Examination with light microscopy showed no obvious signs of corrosion,fatigue,or overload failure. The macro view in Fig.10shows aflat center section surrounded by slanted shear surfaces.Linear mark-ings radiate back to an area near the base of the nut.Examination of this area at higher magnification(Fig. 10,inset)showed exposed intergranular facets,suggestive of hydrogen embrittlement.3.3.Hydrogen embrittlementThe nut specification calls for cadmium coating for protection against corrosion.To this end,the nut is placed in an acid pickling bath to clean it before electrodeposition plating.Both the pickling and plating operations subject the nut surface to atomic hydrogen,some of which diffuses into the steel.Hydrogen is attracted to the grain boundaries and weakens them.Upon application of load,a crack may initiate and propagate over time through the section.The fracture surfaces of hydrogen-affected material typically exhibit exposed grains and grain boundary cracks extending into the fracture surface.Stress is required for hydrogen cracking.Below a certain stress level,cracking will not occur.This critical level is known as the static-fatigue limit.The cracked nut suggests the nut was tightened past its static fa-tigue limit or subjected to unusually large service loads (a hard landing,for example).Hydrogen cracking can sometimes be avoided without appreciable change in hardness by baking after plating,usually at temperatures around 375–425°F in air for a suitable time,depending on the hardness,size,and finish of the nut.ASTM standards B 850-94and B 242describe bakeout procedures.For the nuts used on the Hawker wheel assemblies,the specified Rockwell C hardness is 46–50,for which a bakeout time of 20–24h is recommended.We measured the hardness of Bolt #10and the second bolt and obtained Rockwell C values of 51.9and 50.8,respectively.These hardness values differ insignificantly from the spec-ification,but are in the range of hydrogen embrittlement susceptibility and support the observation of inter-granular fracture shown in Fig.10.Thus,it appears likely that the failure of the nut was due to time-dependent hydrogen embrittlement under stresses imposed by installation or service.4.ConclusionsWe conclude that the root cause of the wheel assembly failure was a cracked nut.When the nut cracked,the load on the tie bolt was released and was taken up by the adjacent bolt/nut couples.Under the increased load,the nuts on the adjacent bolts backed off,transferring their load to the next adjacent bolt/nutcouples,Fig.10.SEM photograph of the fracture surface of the cracked nut.T.Kobayashi,D.A.Shockey /Engineering Failure Analysis 13(2006)65–747374T.Kobayashi,D.A.Shockey/Engineering Failure Analysis13(2006)65–74which then failed,and so on around the bolt ter bolt/nut couples failed more violently as theflange separated from the wheel casing,as manifested by thread stripping and bolt bending.The likely root cause of the nut cracking was hydrogen embrittlement.Hydrogen in the steel from pick-ling and cadmium coating operations may not have been sufficiently baked out,and could have resulted in crack initiation and propagation under tightening or service loads.。