金属切削原理与道具第三章 金属切削的变形过程
合集下载
精品课件-金属切削与机床-第3章

第3章 金属切削的基本规律
图3-3 切屑的形态 (a) 带状切削;(b) 节状切屑;(c) 粒状切屑;(d) 崩粹切屑
第3章 金属切削的基本规律
3.1.2 切削变形区及变形程度 1. 切削变形区 通常切削区域被划分为三个变形区。第Ⅰ变形区是切削刃
前面的切削层内的区域,第Ⅱ变形区是切屑底层与前刀面的接 触的区域,第Ⅲ变形区是后刀面与已加工表面接触的区域,如 图3-4所示。这三个变形区相互关联、相互影响、互相渗透。
第3章 金属切削的基本规律
图3-2 切屑形成过程 (a) 切屑形成过程;(b) 切削形成示意图
第3章 金属切削的基本规律
2. 切屑的类型 根据剪切滑移后形成切屑的外形不同,切屑分为四种类型。 (1) 带状切屑: 是指切屑层经塑性变形后被刀具切离,其外 形呈连续不断的带状,沿前刀面流出,底面光滑,而背面毛茸, 如图3-3(a)所示。 (2) 节状切屑:是指切屑层在塑性变形过程中,剪切面上局 部切应力达到材料强度极限而产生局部断裂,使切屑外形呈锯齿, 形成节状,如图3-3(b)所示。 (3) 粒状切屑:是指在剪切面上产生的切应力超过材料强度 极限,切屑被剪切断裂,形成粒状,如图3-3(c)所示。 (4) 崩碎切屑:是指在切削脆性材料时,切屑层未经塑性变 形突然崩裂成颗粒状,如图3-3(d)所示。
f=(p/4)-(b-go) (3-1)
第3章 金属切削的基本规律 图3-5 剪切角
第3章 金属切削的基本规律
2) 第Ⅱ变形区 当切屑沿前刀面流出时,切屑与前刀面接触的区域为第Ⅱ 变形区。在第Ⅱ变形区内,沿前刀面流出的切屑,其底层受到 强烈地挤压与磨擦,继续进行剪切滑移变形;切屑底层的晶粒 趋向与前刀面平行而成纤维状,接近前刀面的切屑流动速度降 低,形成滞流层。
金属切削原理与刀具设计课件3金属切削过程
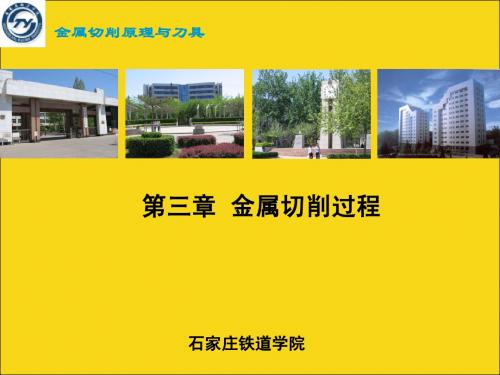
相对滑移系数
cos 0 S y sin cos( 0 )
γ0
(3-3)
当γ0 = 0~30°,Λh ≥1.5时, Λh与ε相近 ε主要反映第Ⅰ变形区 的变形, Λh 还包含了第 Ⅱ变形区的影响。
M
φ
O
图3-9 相对滑移系数
3.4 切屑与前刀面的摩擦变形
特点
切屑类型
带状切屑
Real
挤裂切屑
Real
பைடு நூலகம்
节状切屑
Real
崩碎切屑
Real
图3-5 切屑形态照片
3.3 切屑类型与变形系数
切屑控制
为使切削过程正常进行和保证已加工表面质量,应使切 屑卷曲和折断。 切屑的卷曲是切屑基本变形或经过卷屑槽使之产生附加 变形的结果(图3-6)
断屑是对已变形的切屑再附加一次变形(常需有断屑装置, 图3-7)
(3-5)
3.7 硬脆非金属材料切屑形成机理
脆性材料切削过程
◆ 大规模挤裂与小规模挤裂交替进行(图3-13)
a)
b)
c)
d)
e)
图3-12 硬脆材料切削过程
a)大规模挤裂(大块破碎切除) b)空切 c)小规模挤裂(小块破碎切除) d)小规模挤裂(次小块破碎切除) e)重复大规模挤裂(大块破碎切除)
局部剪切应力达到断 剪切应力完全达 到断裂强度 裂强度 加工塑性材料, 切削速度较低, 进给量较大, 刀具前角较小 切削过程欠平稳, 表面粗糙度欠佳 工件材料硬度较 高,韧性较低, 切削速度较低
影响
切削力波动较大, 切削力波动大,有 切削过程不平稳, 冲击,表面粗糙度 表面粗糙度不佳 恶劣,易崩刀
3.3 切屑类型与变形系数
cos 0 S y sin cos( 0 )
γ0
(3-3)
当γ0 = 0~30°,Λh ≥1.5时, Λh与ε相近 ε主要反映第Ⅰ变形区 的变形, Λh 还包含了第 Ⅱ变形区的影响。
M
φ
O
图3-9 相对滑移系数
3.4 切屑与前刀面的摩擦变形
特点
切屑类型
带状切屑
Real
挤裂切屑
Real
பைடு நூலகம்
节状切屑
Real
崩碎切屑
Real
图3-5 切屑形态照片
3.3 切屑类型与变形系数
切屑控制
为使切削过程正常进行和保证已加工表面质量,应使切 屑卷曲和折断。 切屑的卷曲是切屑基本变形或经过卷屑槽使之产生附加 变形的结果(图3-6)
断屑是对已变形的切屑再附加一次变形(常需有断屑装置, 图3-7)
(3-5)
3.7 硬脆非金属材料切屑形成机理
脆性材料切削过程
◆ 大规模挤裂与小规模挤裂交替进行(图3-13)
a)
b)
c)
d)
e)
图3-12 硬脆材料切削过程
a)大规模挤裂(大块破碎切除) b)空切 c)小规模挤裂(小块破碎切除) d)小规模挤裂(次小块破碎切除) e)重复大规模挤裂(大块破碎切除)
局部剪切应力达到断 剪切应力完全达 到断裂强度 裂强度 加工塑性材料, 切削速度较低, 进给量较大, 刀具前角较小 切削过程欠平稳, 表面粗糙度欠佳 工件材料硬度较 高,韧性较低, 切削速度较低
影响
切削力波动较大, 切削力波动大,有 切削过程不平稳, 冲击,表面粗糙度 表面粗糙度不佳 恶劣,易崩刀
3.3 切屑类型与变形系数
金属切削原理 3第三章 金属切削的变形过程
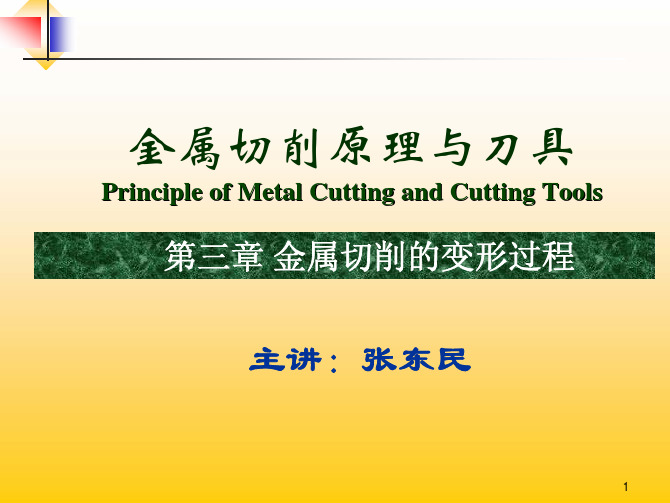
25
二、剪切角φ与前刀面摩擦角β的关系
剪切角Φ可衡量切屑变形程度,如果能建立 φ=(γ0,β)的理论公式,对预测切屑变形程度和切削 力的大小有重要的实际意义。 最大主应力方向与最大剪应力方向夹角为π/4。
φ + β −γ0 = φ= π π
4
4 4 ω为合力与切削速度方向的夹角,称作用角
− (β − γ 0 ) =
金属切削原理与刀具
Principle of Metal Cutting and Cutting Tools
第三章 金属切削的变形过程
主讲:张东民
1
第三章 金属切削的变形过程
3.1 研究金属切削变形过程的意义和方法 3.2 金属切削层的变形 3.3 前面上的挤压与摩擦及其对切屑变形的影响 3.4 积屑瘤的形成及其对切削过程的影响 3.5 影响切屑变形的主要因素 3.6 切屑的类型 3.7 3-14 作用在切屑上的力
a) 切屑受到来自工件和刀具的作用力 b) 切屑作为隔离体的受力分析
刀具与切屑之间的作用力分析如图3-14所示。 在直角自由切削的前提下,作用在切屑上的力有:前面对其作用的 法向力Fn和摩擦力Ff,剪切面上的剪切力Fs和法向力Fns,两对力的 合力分别为Fr 和 Fr′。 假设这两个合力相互平衡(严格地讲,这两个合力不共 线,有一个使切屑弯曲的力矩),Fr称为切屑形成力, φ是剪切角;β是Fn与Fr之间的夹角,称为摩擦角; 24 γo是刀具前角。
π
−ω
1.前角γ0 ↑,Φ ↑,变形减小。在保证切削刃强度前提 下,增大刀具前角利于改善切削过程。 2.摩擦角β↑,Φ↓ ,变形增大↑ 。提高刀具刃磨质量 ,施加切削液以减少前刀面上的摩擦对切削有利。
26
三、前刀面上的摩擦
二、剪切角φ与前刀面摩擦角β的关系
剪切角Φ可衡量切屑变形程度,如果能建立 φ=(γ0,β)的理论公式,对预测切屑变形程度和切削 力的大小有重要的实际意义。 最大主应力方向与最大剪应力方向夹角为π/4。
φ + β −γ0 = φ= π π
4
4 4 ω为合力与切削速度方向的夹角,称作用角
− (β − γ 0 ) =
金属切削原理与刀具
Principle of Metal Cutting and Cutting Tools
第三章 金属切削的变形过程
主讲:张东民
1
第三章 金属切削的变形过程
3.1 研究金属切削变形过程的意义和方法 3.2 金属切削层的变形 3.3 前面上的挤压与摩擦及其对切屑变形的影响 3.4 积屑瘤的形成及其对切削过程的影响 3.5 影响切屑变形的主要因素 3.6 切屑的类型 3.7 3-14 作用在切屑上的力
a) 切屑受到来自工件和刀具的作用力 b) 切屑作为隔离体的受力分析
刀具与切屑之间的作用力分析如图3-14所示。 在直角自由切削的前提下,作用在切屑上的力有:前面对其作用的 法向力Fn和摩擦力Ff,剪切面上的剪切力Fs和法向力Fns,两对力的 合力分别为Fr 和 Fr′。 假设这两个合力相互平衡(严格地讲,这两个合力不共 线,有一个使切屑弯曲的力矩),Fr称为切屑形成力, φ是剪切角;β是Fn与Fr之间的夹角,称为摩擦角; 24 γo是刀具前角。
π
−ω
1.前角γ0 ↑,Φ ↑,变形减小。在保证切削刃强度前提 下,增大刀具前角利于改善切削过程。 2.摩擦角β↑,Φ↓ ,变形增大↑ 。提高刀具刃磨质量 ,施加切削液以减少前刀面上的摩擦对切削有利。
26
三、前刀面上的摩擦
第三章 金属切削变形过程

(3-6)
(3-7)
(3-8)
下图表示ε与Λh的曲线关系。 (1)变形系数并不等于剪应变ε; (2)当 h 1.5时, ε与Λh成正比; (3)当Λh=1时,剪应变并不等于零; (4) Λh 相同,γo不同, ε也不同; (5)当 h 1.2 时,不能用Λh表示变形程度。
§3-4
3.切削速度 (1) 切削塑性材料时 有积屑瘤时,Ⅱ区:Vc↑→Λ h↓ Ⅲ区:Vc↑→Λ h↑ 无积屑瘤时,Ⅰ区: Vc↑无明显。 Ⅳ区:Vc s h (2)切削脆性材料时,Vc对Λ h无明显影响 4.切削厚度 (1)Vc>200m/min时
hD F h
§3-3 变形系数和剪应变 切削变形程度的衡量
实践证明,切屑厚度hch大于切削层厚度 hD ,而切屑长 度Lch小于切削层长度Lc,可见,金属发生切削变形, 那么怎样衡量切削变形呢? 一、切削变形系数Λh : 切屑厚度与切削层厚度之比,称为厚度变形系数Λhα: 切削层长度Lc 与切削长度之比,称为长度变形系数Λhl, 即: hch lc ha hl hD lch
4
4
o
(3-13)
上式即所谓李和谢弗公式。 结论: (1)当γo增大时,Φ角增大,变形减少。 (2)当β增大时,Φ角减少,变形增大。 两公式不完全相同,原因如下: 1.刀具钝圆半径rn的存在影响Φ的大小 2.剪切面不是平面,而是有一定宽度的变形区 3.金属内部杂质缺陷对变形有影响 4.用平均β (μ)表示刀—屑摩擦与实际不符
一、摩擦面的实际接触面积
1.峰点型接触 2.紧密型接触 图3-18 图3-19
二、峰点的冷焊与摩擦力
由于接触峰点发生了塑性变形破坏了其上的吸附膜和 保护膜,使峰点处的金属间直接接触,同时温度较高, 从而使峰点冷焊,其结点称冷焊结。 当两物体相对滑动时,这些冷焊结被剪,为保持原 接触面积,又有一些新峰点接触,形成新冷焊结。所以 滑动摩擦是不断更换冷焊结的过程,冷焊结被剪形成抗 剪力,即为摩擦力的一部分;另一部分,耕犁力P :是 较硬一方在软方表面划出一道沟痕所受阻力。 摩擦力 较小可略
金属切削原理与刀具

第四章 切削条件的合理选择
第一节 工件材料的切削加工性 第二节 切削液 第三节 刀具几何参数的合理选择 第四节 切削用量的合理选择
第一节 工件材料的切削加工性
“指对某种材料进行加工的难易程度”
相对加工性:Kr
Kr
V60 (V60 ) j
改善材料切削加工性的主要途径
1、热处理,改变材料的组织和机械性能 2、合理选用刀具材料 3、调整材料的化学成分
f
0.14
a0.04 p
三、影响切削温度的因素
3. 刀具几何参数对切削温度的影响 控制切削温度的措施
γO ↗
1、正确使用切削液
θ ℃↙
2、合κ理选r 择↗切削用量
在满足工艺要求的前提下,取小的
θ ℃↗
vc较大的
ap、f
3、γ改O↗r善ε刀↗具几θ何℃条↙件:
θ ℃↙
第四节 刀具磨损
一、刀具的磨损形式:
二、刀具磨损的原因
4. 氧化磨损: 刀具上的表面膜被切屑或工件表面划擦掉后,在高温 下(700~800℃)与空气中的氧作用产生松脆氧化物, 造成刀具磨损。
综上所述:
三、刀具磨损过程与磨损标准
11、、刀具磨损过程
2、刀具磨损标准(磨损限度)
“指后刀面磨损带中间部分平均磨损量允许达到的 最大磨损尺寸”。以VB表示
2、产生条件: ①中等速度切削塑性材料。
②切削区的温度、压力和界 面状况符合在刀面上发生 冷焊的条件。
2、特点: ①硬度是工件材料的2~3.5倍,
可以代替刀具切削。
②周而复始的生长、脱落。
3. 对切削过程的影响:
4、精加工控制积屑瘤的措施
①
积屑瘤代替刀刃进行切削,保护 了刀刃,增大了前角。
电子教案与课件:金属切削原理与机床 第三章 金属切削过程的基本理论

重点是切削变形程度的表示方法、切削热的计算及影 响因素分析、切削力的影响因素、刀具磨损与破损的原因 和刀具耐用度的选择。
难点是切削力与切削热影响因素分析。
第三章 金属切削过程的基本理论
在金属切削过程中,始终存在着刀具切削工件和 工件材料抵抗切削的矛盾,从而产生一系列物理现象, 如切削变形、切削力、切削热与切削温度以及有关刀 具的磨损与刀具寿命、卷屑与断屑等。
第三章 金属切削过程的基本理论
教学目的与要求: 通过本章的学习,掌握金属切削变形、切削力、切削
热和刀具的破损与磨损的原因和刀具耐用度的基本概念。 教学内容摘要:
本章主要介绍切削变形区、变形程度的表示方法、切 削热的产生与传出、计算、对切削加工的影响;切削力的 作用与影响因素;刀具磨损与破损的形态、磨损的原因和 刀具耐用度的选用。 教学重点与难点:
前角对变形系数的影响
切削速度对摩擦系数的影响
前角对摩擦系数的影响
切削速度对变形系数的影响
进给量对变形系数的影响
4、切削厚度
切削厚度ac增加时,μ也略为下降, 如10钢的ac从0.1mm增大到0.18mm,μ 从0.74降至0.72。因为ac增加后正应 力也随之增大。在一般切削速度范 围内,前角γ0愈大,则μ值愈大。因 为随着γ0增大,正应力减小,故μ增 加。
第二节 积屑瘤与切屑的类型
• 一、积屑瘤的形成及其对切削过程的影 响
• 二、切屑的形态
一、积屑瘤的形成及其对切削过程的影响
1、什么是积屑瘤
在一定速度范围下,切削塑性金属材料形成带 状切屑时, 常在刀具前刀面靠近切削刃的部位粘结 一些工件材料, 形成一块硬度很高的楔块,称之为 积屑瘤,或称刀瘤。
2、积屑瘤对起削过程的影响
三、影响切屑变形和摩擦系数的主要因素
难点是切削力与切削热影响因素分析。
第三章 金属切削过程的基本理论
在金属切削过程中,始终存在着刀具切削工件和 工件材料抵抗切削的矛盾,从而产生一系列物理现象, 如切削变形、切削力、切削热与切削温度以及有关刀 具的磨损与刀具寿命、卷屑与断屑等。
第三章 金属切削过程的基本理论
教学目的与要求: 通过本章的学习,掌握金属切削变形、切削力、切削
热和刀具的破损与磨损的原因和刀具耐用度的基本概念。 教学内容摘要:
本章主要介绍切削变形区、变形程度的表示方法、切 削热的产生与传出、计算、对切削加工的影响;切削力的 作用与影响因素;刀具磨损与破损的形态、磨损的原因和 刀具耐用度的选用。 教学重点与难点:
前角对变形系数的影响
切削速度对摩擦系数的影响
前角对摩擦系数的影响
切削速度对变形系数的影响
进给量对变形系数的影响
4、切削厚度
切削厚度ac增加时,μ也略为下降, 如10钢的ac从0.1mm增大到0.18mm,μ 从0.74降至0.72。因为ac增加后正应 力也随之增大。在一般切削速度范 围内,前角γ0愈大,则μ值愈大。因 为随着γ0增大,正应力减小,故μ增 加。
第二节 积屑瘤与切屑的类型
• 一、积屑瘤的形成及其对切削过程的影 响
• 二、切屑的形态
一、积屑瘤的形成及其对切削过程的影响
1、什么是积屑瘤
在一定速度范围下,切削塑性金属材料形成带 状切屑时, 常在刀具前刀面靠近切削刃的部位粘结 一些工件材料, 形成一块硬度很高的楔块,称之为 积屑瘤,或称刀瘤。
2、积屑瘤对起削过程的影响
三、影响切屑变形和摩擦系数的主要因素
金属切削第三章解析
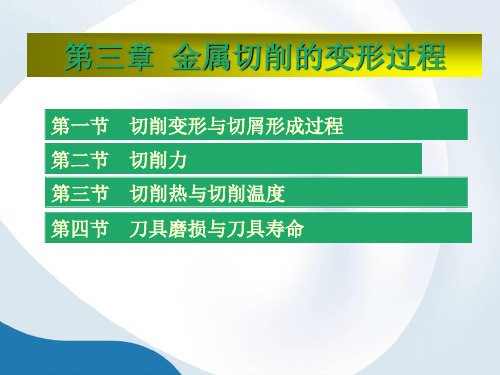
• 在这过程中产生一系列现象,如形成切屑、切削 力、切削热与切削温度、刀具磨损等,它们产生 的根本原因时切削过程中的弹性变形和塑性变形
• 金属切削变形过程的研究是金属切削原理的基础 理论研究。是适应生产发展的需要,有助于保证 加工质量,提高生产率和降低成本。
研究切削变形的实验方法
侧面变形观察法 高速摄影法 快速落刀法 SEM观察法 光弹性、光塑性实验法 其它方法,如:X射线衍射等
第II变形区内金属的挤压变形
切屑沿前刀面排出时进一步受到前刀面的挤压和 摩擦,使靠近前刀面的金属纤维化,基本与前刀面平 行。
第Ⅲ变形区:
➢刀工接触区。
➢已加工表面受到刀具刃口钝圆和后刀面挤压和摩 擦,晶粒进一步剪切滑移。
➢有时也呈纤维化,其方向平行已加工表面,也产 生加工硬化和回弹现象。
➢三个变形区汇集在切削刃附近,应力集中而又复 杂。三个变形区内的变形又相互影响。
• 通常加工塑性金属材料,切削厚度较小,切削速度 较高,刀具前角较大时得到。
• 切削力波动很小,切削过程平稳,已加工表面粗糙 度较小。
2、挤裂切屑
• 外侧面呈锯齿状,内侧面有时有裂纹 • 加工塑性金属材料,切削厚度较大,切削速
度较低,刀具前角较小时得到。加工硬化较 大,在局部剪应力超过破裂强度。
• 切削力波动较大,切削过程产生一定的振动, 已加工表面较粗糙。
摩擦。此变形区的变形是造成前刀面磨损和产生积屑瘤的
主要原因。
➢ 第Ⅲ变形区:已加工面受到后刀面挤压与摩擦,产生变 形。此区变形是造成已加工面加工硬化和残余应力的主要 原因。
切 削 变 形 金 相 显 微 照 片
第Ⅰ变形区:
➢从OA线(始滑移线)金属开始发生剪切变形,到 OM线(终滑移线)金属晶粒剪切滑移基本结束, AOM区域叫第一变形区。 ➢是切屑变形的基本区,其特征是晶粒的剪切滑移 ,伴随产生加工硬化。
• 金属切削变形过程的研究是金属切削原理的基础 理论研究。是适应生产发展的需要,有助于保证 加工质量,提高生产率和降低成本。
研究切削变形的实验方法
侧面变形观察法 高速摄影法 快速落刀法 SEM观察法 光弹性、光塑性实验法 其它方法,如:X射线衍射等
第II变形区内金属的挤压变形
切屑沿前刀面排出时进一步受到前刀面的挤压和 摩擦,使靠近前刀面的金属纤维化,基本与前刀面平 行。
第Ⅲ变形区:
➢刀工接触区。
➢已加工表面受到刀具刃口钝圆和后刀面挤压和摩 擦,晶粒进一步剪切滑移。
➢有时也呈纤维化,其方向平行已加工表面,也产 生加工硬化和回弹现象。
➢三个变形区汇集在切削刃附近,应力集中而又复 杂。三个变形区内的变形又相互影响。
• 通常加工塑性金属材料,切削厚度较小,切削速度 较高,刀具前角较大时得到。
• 切削力波动很小,切削过程平稳,已加工表面粗糙 度较小。
2、挤裂切屑
• 外侧面呈锯齿状,内侧面有时有裂纹 • 加工塑性金属材料,切削厚度较大,切削速
度较低,刀具前角较小时得到。加工硬化较 大,在局部剪应力超过破裂强度。
• 切削力波动较大,切削过程产生一定的振动, 已加工表面较粗糙。
摩擦。此变形区的变形是造成前刀面磨损和产生积屑瘤的
主要原因。
➢ 第Ⅲ变形区:已加工面受到后刀面挤压与摩擦,产生变 形。此区变形是造成已加工面加工硬化和残余应力的主要 原因。
切 削 变 形 金 相 显 微 照 片
第Ⅰ变形区:
➢从OA线(始滑移线)金属开始发生剪切变形,到 OM线(终滑移线)金属晶粒剪切滑移基本结束, AOM区域叫第一变形区。 ➢是切屑变形的基本区,其特征是晶粒的剪切滑移 ,伴随产生加工硬化。
电子课件-《金属切削原理与刀具(第五版)》-B01-3509 第三章

不易断屑;反之,易断屑。 2)主偏角κr 在背吃刀量ap 和进给量f已选定的条件下,
主偏角κr越大,切削厚度ac越大,故切屑卷曲应力越大,越 易断屑。
3)刃倾角λs
①当λs为正值时,使切屑流向待加工表面或与后面相碰
形成“C”形切屑,也可能呈螺旋屑而甩断;
②当λs为负值时,切屑流向已加工表面或过渡表面,容
ቤተ መጻሕፍቲ ባይዱ容易卷屑、断屑
而宽度LBn大则卷曲半径rch较大,产生的弯曲应力不易使 切屑折断。
断屑槽宽度LBn必须与进给量f和背吃刀量ap联系起来考虑。 进给量小,槽应窄些
背吃刀量小,槽宽也应适当减小
第三章 切削加工的主要规律
3)断屑槽的斜角(τ)
a)外斜式
b)平行式
c)内斜式
第三章 切削加工的主要规律
第三节 积屑瘤
以中等切削速度切削钢料或其他塑性金属材料时,经 常会有一小块呈楔状的金属(工件材料)牢固地黏结在靠 近刀刃的前面上,这就是积屑瘤,也称为刀瘤。
积屑瘤及其对加工的影响
第三章 切削加工的主要规律
一、积屑瘤的形成
切削塑性金属材料时,在一定条件下,切屑沿前面流出时, 由于切屑与前面之间的强烈挤压与摩擦,使切屑底层的一部分 金属产生“滞流”现象,当滞流层与前面的摩擦力大于材料内 部的结合力时,则使滞流层从切屑母体中分离,并牢固地黏结 (冷焊)在靠近刀刃的前面上。积屑瘤在切削过程中是不稳定 的,它因不断层积长大,又因局部脱落而减小。
(1)切削用量 切削用量中对断屑影响最大的是进给量f,其次是背
吃刀量ap和切削速度v。
1)进给量 f 进给量f加大,切削厚度αc按比例增大, 切削变形增大,切屑易折断。
但要注意,随着进给量的增大,工件表面粗糙度值将会 增大。
主偏角κr越大,切削厚度ac越大,故切屑卷曲应力越大,越 易断屑。
3)刃倾角λs
①当λs为正值时,使切屑流向待加工表面或与后面相碰
形成“C”形切屑,也可能呈螺旋屑而甩断;
②当λs为负值时,切屑流向已加工表面或过渡表面,容
ቤተ መጻሕፍቲ ባይዱ容易卷屑、断屑
而宽度LBn大则卷曲半径rch较大,产生的弯曲应力不易使 切屑折断。
断屑槽宽度LBn必须与进给量f和背吃刀量ap联系起来考虑。 进给量小,槽应窄些
背吃刀量小,槽宽也应适当减小
第三章 切削加工的主要规律
3)断屑槽的斜角(τ)
a)外斜式
b)平行式
c)内斜式
第三章 切削加工的主要规律
第三节 积屑瘤
以中等切削速度切削钢料或其他塑性金属材料时,经 常会有一小块呈楔状的金属(工件材料)牢固地黏结在靠 近刀刃的前面上,这就是积屑瘤,也称为刀瘤。
积屑瘤及其对加工的影响
第三章 切削加工的主要规律
一、积屑瘤的形成
切削塑性金属材料时,在一定条件下,切屑沿前面流出时, 由于切屑与前面之间的强烈挤压与摩擦,使切屑底层的一部分 金属产生“滞流”现象,当滞流层与前面的摩擦力大于材料内 部的结合力时,则使滞流层从切屑母体中分离,并牢固地黏结 (冷焊)在靠近刀刃的前面上。积屑瘤在切削过程中是不稳定 的,它因不断层积长大,又因局部脱落而减小。
(1)切削用量 切削用量中对断屑影响最大的是进给量f,其次是背
吃刀量ap和切削速度v。
1)进给量 f 进给量f加大,切削厚度αc按比例增大, 切削变形增大,切屑易折断。
但要注意,随着进给量的增大,工件表面粗糙度值将会 增大。
- 1、下载文档前请自行甄别文档内容的完整性,平台不提供额外的编辑、内容补充、找答案等附加服务。
- 2、"仅部分预览"的文档,不可在线预览部分如存在完整性等问题,可反馈申请退款(可完整预览的文档不适用该条件!)。
- 3、如文档侵犯您的权益,请联系客服反馈,我们会尽快为您处理(人工客服工作时间:9:00-18:30)。
o 4
Lee and Shaffer公式:
4 ( o )
4
由Lee and Shaffer公式知:
o o ↑→ ↑→切削变形↓——应尽量增大 ↑→ ↓→切削变形↑——应尽量减小 该公式仅是理论分析。只能定性地解释问题, 定量上有出入
金属切削原理与刀具
——山东理工大学机械工程学院
李志永 2015年2月
第三章 金属切削的变形过程
本章主要内容
研究切削变形的意义和方法
切削层的变形 前刀面的挤压和摩擦 积屑瘤 切屑变形规律 切屑的类型、卷曲和折断
爱国 者导 弹
§ 3.1 研究金属切削变形过程的 意义和方法
研究金属切削变形过程的意义
认识和掌握金属切削的规律,用以提高切削效 率、降低成本、保证质量。 19世纪以来,大批学者从不同方面进行研究, 科学地揭示和解释了金属切削过程的种种现象和 规律。 各行业对机械产品的需求促使人们不断地探索 和研究新问题。
§ 3.2 金属切削层的变形
第一变形区的剪切变形
切屑 M 终滑移线
A
大小? Φ剪切角 始滑移线:τ=τs O 刀具
切屑根部金相照片
§ 3.2 金属切削层的变形
第Ⅰ变形区的剪切变形程度分析 剪切角 φ :
剪切面与切削速度之间的夹角。
M
γ0
相对滑移系数
cos 0 S y sin cos( 0 )
3.1.5 硬脆非金属材料切屑形成机理
脆性材料切削过程
◆ 大规模挤裂与小规模挤裂交替进行(图3-13)
a)
b)
c)
d)
e)
图3-13 硬脆材料切削过程
a)大规模挤裂(大块破碎切除) b)空切 c)小规模挤裂(小块破碎切除) d)小规模挤裂(次小块破碎切除) e)重复大规模挤裂(大块破碎切除)
flash
hD
τ
ΔhD
变形情况
A 点以上部分沿前刀面 流出,形成切屑; A 点 以下部分受挤压和摩擦 留在加工表面上,并有 弹性恢复。
A
C E F
σn
τ
图3-12 已加工表面变形
应力分布
A点前方正应力最大,剪应力为 0。 A点两侧正应力逐渐减小,剪应力逐渐增大,继而减小。
Δh
3.1.5 硬脆非金属材料切屑形成机理
加工塑性材料, 切削速度较低, 进给量较大, 刀具前角较小 切削过程欠平稳, 表面粗糙度欠佳 工件材料硬度较 高,韧性较低, 切削速度较低
影响
切削过程平稳, 表面粗糙度小, 妨碍切削工作, 应设法断屑
切削力波动较大, 切削力波动大,有 切削过程不平稳, 冲击,表面粗糙度 表面粗糙度不佳 恶劣,易崩刀
φ
O
相对滑移系数
§ 3.2 金属切削层的变形
变形系数
切削层经塑性变形后,厚度增加,长度缩小,宽度 基本不变。可用其表示切削层变的变形程度。 ◆ 厚度变形系数 ach h ac ◆ 长度变形系数 LD L Lch ◆ 自由切削宽度变形可忽略
Lch LD
切屑与切削层尺寸
L h
Fs Fr cos( o )
理论切削力(合力):
理论切削力计算
Fr Fs cos( o ) Ac sin cos( o )
§3.3 前刀面的挤压与摩擦及其 对切削变形的影响
剪切角 与前刀面摩擦角 的关系 根据材料力学结论:主应力方向(Fr)与最大剪 应力方向的夹角为 4 。
脆性断裂条件
G>GC
(3-4)
式中 G —— 裂纹扩展单位长度时释放的能量(应变能 释放率); GC ——裂纹扩展单位长度时所需的能量(裂纹扩 展阻力)。 对于Ⅰ型(张开型)裂纹,在平面应变条件下,脆性断 裂条件为: K1>K1C 式中 K1 —— 应力强度因 子; K1C —— K1临界值。
(3-5)
名称 带状切屑 挤裂切屑 单元切屑 崩碎切屑
简图
形态 变形 形成 条件
带状,底面光滑 ,背面呈毛茸状
节状,底面光滑有裂 纹,背面呈锯齿状
粒状
不规则块状颗粒
未经塑性变形即 被挤裂 加工硬脆材料, 刀具前角较小
剪切滑移尚未达 到断裂程度
加工塑性材料, 切削速度较高, 进给量较小, 刀具前角较大
局部剪切应力达到断 剪切应力完全达 到断裂强度 裂强度
2.5
200
2.0
h
0
1.5 0 20 40 60 80 100
切削45钢时切削速度与积屑瘤、 、粗糙度关系
120 140 v(m/min)
§3.5 切削变形的变化规律
工件材料影响切削变形
→ ↑→ ↓ 工件材料硬度HB↑→ ↓ 实验结果见图3-23 有积屑瘤的速度范围 前角影响切削变形 内,切削速度通过积屑瘤 o ↑→ ↓ 形成的实际 o 影响 。 实验结果见图3-24 实际 o ↑→ ↓
刀具
积屑瘤的影响
实际前角增大 增大切削厚度 粗糙度值增大 影响刀具耐用度
抑制积屑瘤的办法:p45(5种办法)
§3.4 积屑瘤的形成及其对切削的影响
切削速度与积屑瘤和变形系数的关系
表面粗糙度Rz(μm) 积屑瘤高度 h(μm) 28 24
600
变形系数
3.0
Rz
20
16 12 8 4
400
§ 3.2 金属切削层的变形
剪切角与变形系数的关系
ach OM sin(90 o ) cos( o ) ac OM sin sin
相对滑移与变形系数的关系
2 2sin o 1 cos o
γ0
φ
当 o= 0~30°, ≥1.5时, 与ε相近。 ε主要反映第Ⅰ变形区的变形, 还包含了第Ⅱ变形区的影响。
具体到每个磨粒,不一 定三个阶段均有
图3-14 磨屑形成过程
a)平面示意图 b)截面示意图
切削速度影响切削变形
v↑→ ↓(无积屑瘤的速度范围内) 实验结果见图3-25
f ↑→ ↓(无积屑瘤的速度范围内) 实验结果见图3-26
切削厚度影响切削变形
§3.6 切屑类型及其变化
切屑类型
带状切屑
挤裂切屑
节状切屑
切屑形态照片
崩碎切屑
§3.6 切屑类型及其变化
切屑类型及形成条件
lfi lfo
பைடு நூலகம்
切屑与前刀面的摩擦
§3.3 前刀面的挤压与摩擦 及其对切削变形的影响
前刀面的摩擦 外摩擦特性
外摩擦力与摩擦系数和正压力有关与接触面积无关。 摩擦系数为定值。
内摩擦特性
内摩擦系数为变值。
Ff
s
s Af 1 s 工件材料剪切屈服强度 Fn av Af 1 av 内摩擦部分的平均正应力, 切屑与前刀面的摩擦
切屑的折断
切削过程中变形程度超过了材料的断裂应变造成折断。 多数情况下切屑的卷曲变形不足以使切屑折断。 需用断屑台或卷屑槽使切屑产生附加变形撞到工件或后刀 面折断。 螺卷状切屑甩断。
卷屑槽形状 (图3-35)
3.1.4 已加工表面的变形
变形原因
切削刃存在刃口圆弧, 导致挤压和摩擦,产生 第Ⅲ变形区。
flash
3.1.6 磨削机理
磨削特点
★ 磨粒切削刃几何形状不确定(通常刃口前角为-60~ -85°) ★ 磨粒及切削刃随机分布 ★ 磨削厚度小(<几μm),磨削速度高,磨削点瞬时温 度高(达1000℃以上)
3.1.6 磨削机理
磨屑形成过程
★ 弹性变形:磨粒在工件 表面滑擦而过,不能切入 工件 ★ 塑性变形:磨粒切入工 件,材料向两边隆起,工 件表面出现刻痕(犁沟) ,但无磨屑产生 ★ 切削:磨削深度、磨削 点温度和应力达到一定数 值,形成磨屑,沿磨粒前 刀面流出
变形系数求法
§3.3 前刀面的挤压与摩擦 及其对切削变形的影响
第二变形区特点 强 烈 的 挤 压 与 摩擦 切 屑 底 层 纤 维 化,流动缓慢甚 至停滞 切屑弯曲
切削部位三个变形区
由摩擦而产生的热量使接触区域温度升高 本变形区的变形也影响第一区变形
§3.3 前刀面的挤压与摩擦 及其对切削变形的影响
研究过程采用了多种方法
侧面变形观察法、高速摄影法 快速落刀法、扫描电镜显微观察法等
切削变形实验设备与录像装置
§ 3.2 金属切削层的变形
挤压与切削(塑性材料切削为例)
切屑的形成与切离过程,是切削 层受到刀具前刀面的挤压而产生以 滑移为主的塑性变形过程。 正挤压:金属材料受挤压时,最大 剪应力方向与作用力方向约成45° 偏挤压:金属材料一部分受挤压时 , OB 线以上金属由于母体阻碍,不 能沿AB线滑移,而只能沿OM线滑移 切削:与偏挤压情况类似。弹性变 形→剪切应力增大,达到屈服点→产 生塑性变形,沿 OM 线滑移 → 剪切应 力与滑移量继续增大,达到断裂强度 →切屑与母体脱离。
作用在切屑上的力 取切屑为隔离体,作用在 剪切面和底面的力平衡 直角自由切削时各力的作 用角度如图 切削层面积:
Ac ac aw
剪切必需的力:
切平面
前刀面
作用在切屑上的力
Fs Ac sin
§3.3 前刀面的挤压与摩擦 及其对切削变形的影响
作用在切屑上的力 两处作用力平衡,汇集于 刀刃前方如图 由几何关系得:
§3.7 切屑的卷曲与折断
切屑控制
为使切削过程正常进行和保证已加工表面质量,应使切 屑卷曲和折断。 切屑的卷曲是切屑基本变形或经过卷屑槽使之产生附加 变形的结果。
断屑是对已变形的切屑再附加一次变形(常需有断屑装 置)。
Lee and Shaffer公式:
4 ( o )
4
由Lee and Shaffer公式知:
o o ↑→ ↑→切削变形↓——应尽量增大 ↑→ ↓→切削变形↑——应尽量减小 该公式仅是理论分析。只能定性地解释问题, 定量上有出入
金属切削原理与刀具
——山东理工大学机械工程学院
李志永 2015年2月
第三章 金属切削的变形过程
本章主要内容
研究切削变形的意义和方法
切削层的变形 前刀面的挤压和摩擦 积屑瘤 切屑变形规律 切屑的类型、卷曲和折断
爱国 者导 弹
§ 3.1 研究金属切削变形过程的 意义和方法
研究金属切削变形过程的意义
认识和掌握金属切削的规律,用以提高切削效 率、降低成本、保证质量。 19世纪以来,大批学者从不同方面进行研究, 科学地揭示和解释了金属切削过程的种种现象和 规律。 各行业对机械产品的需求促使人们不断地探索 和研究新问题。
§ 3.2 金属切削层的变形
第一变形区的剪切变形
切屑 M 终滑移线
A
大小? Φ剪切角 始滑移线:τ=τs O 刀具
切屑根部金相照片
§ 3.2 金属切削层的变形
第Ⅰ变形区的剪切变形程度分析 剪切角 φ :
剪切面与切削速度之间的夹角。
M
γ0
相对滑移系数
cos 0 S y sin cos( 0 )
3.1.5 硬脆非金属材料切屑形成机理
脆性材料切削过程
◆ 大规模挤裂与小规模挤裂交替进行(图3-13)
a)
b)
c)
d)
e)
图3-13 硬脆材料切削过程
a)大规模挤裂(大块破碎切除) b)空切 c)小规模挤裂(小块破碎切除) d)小规模挤裂(次小块破碎切除) e)重复大规模挤裂(大块破碎切除)
flash
hD
τ
ΔhD
变形情况
A 点以上部分沿前刀面 流出,形成切屑; A 点 以下部分受挤压和摩擦 留在加工表面上,并有 弹性恢复。
A
C E F
σn
τ
图3-12 已加工表面变形
应力分布
A点前方正应力最大,剪应力为 0。 A点两侧正应力逐渐减小,剪应力逐渐增大,继而减小。
Δh
3.1.5 硬脆非金属材料切屑形成机理
加工塑性材料, 切削速度较低, 进给量较大, 刀具前角较小 切削过程欠平稳, 表面粗糙度欠佳 工件材料硬度较 高,韧性较低, 切削速度较低
影响
切削过程平稳, 表面粗糙度小, 妨碍切削工作, 应设法断屑
切削力波动较大, 切削力波动大,有 切削过程不平稳, 冲击,表面粗糙度 表面粗糙度不佳 恶劣,易崩刀
φ
O
相对滑移系数
§ 3.2 金属切削层的变形
变形系数
切削层经塑性变形后,厚度增加,长度缩小,宽度 基本不变。可用其表示切削层变的变形程度。 ◆ 厚度变形系数 ach h ac ◆ 长度变形系数 LD L Lch ◆ 自由切削宽度变形可忽略
Lch LD
切屑与切削层尺寸
L h
Fs Fr cos( o )
理论切削力(合力):
理论切削力计算
Fr Fs cos( o ) Ac sin cos( o )
§3.3 前刀面的挤压与摩擦及其 对切削变形的影响
剪切角 与前刀面摩擦角 的关系 根据材料力学结论:主应力方向(Fr)与最大剪 应力方向的夹角为 4 。
脆性断裂条件
G>GC
(3-4)
式中 G —— 裂纹扩展单位长度时释放的能量(应变能 释放率); GC ——裂纹扩展单位长度时所需的能量(裂纹扩 展阻力)。 对于Ⅰ型(张开型)裂纹,在平面应变条件下,脆性断 裂条件为: K1>K1C 式中 K1 —— 应力强度因 子; K1C —— K1临界值。
(3-5)
名称 带状切屑 挤裂切屑 单元切屑 崩碎切屑
简图
形态 变形 形成 条件
带状,底面光滑 ,背面呈毛茸状
节状,底面光滑有裂 纹,背面呈锯齿状
粒状
不规则块状颗粒
未经塑性变形即 被挤裂 加工硬脆材料, 刀具前角较小
剪切滑移尚未达 到断裂程度
加工塑性材料, 切削速度较高, 进给量较小, 刀具前角较大
局部剪切应力达到断 剪切应力完全达 到断裂强度 裂强度
2.5
200
2.0
h
0
1.5 0 20 40 60 80 100
切削45钢时切削速度与积屑瘤、 、粗糙度关系
120 140 v(m/min)
§3.5 切削变形的变化规律
工件材料影响切削变形
→ ↑→ ↓ 工件材料硬度HB↑→ ↓ 实验结果见图3-23 有积屑瘤的速度范围 前角影响切削变形 内,切削速度通过积屑瘤 o ↑→ ↓ 形成的实际 o 影响 。 实验结果见图3-24 实际 o ↑→ ↓
刀具
积屑瘤的影响
实际前角增大 增大切削厚度 粗糙度值增大 影响刀具耐用度
抑制积屑瘤的办法:p45(5种办法)
§3.4 积屑瘤的形成及其对切削的影响
切削速度与积屑瘤和变形系数的关系
表面粗糙度Rz(μm) 积屑瘤高度 h(μm) 28 24
600
变形系数
3.0
Rz
20
16 12 8 4
400
§ 3.2 金属切削层的变形
剪切角与变形系数的关系
ach OM sin(90 o ) cos( o ) ac OM sin sin
相对滑移与变形系数的关系
2 2sin o 1 cos o
γ0
φ
当 o= 0~30°, ≥1.5时, 与ε相近。 ε主要反映第Ⅰ变形区的变形, 还包含了第Ⅱ变形区的影响。
具体到每个磨粒,不一 定三个阶段均有
图3-14 磨屑形成过程
a)平面示意图 b)截面示意图
切削速度影响切削变形
v↑→ ↓(无积屑瘤的速度范围内) 实验结果见图3-25
f ↑→ ↓(无积屑瘤的速度范围内) 实验结果见图3-26
切削厚度影响切削变形
§3.6 切屑类型及其变化
切屑类型
带状切屑
挤裂切屑
节状切屑
切屑形态照片
崩碎切屑
§3.6 切屑类型及其变化
切屑类型及形成条件
lfi lfo
பைடு நூலகம்
切屑与前刀面的摩擦
§3.3 前刀面的挤压与摩擦 及其对切削变形的影响
前刀面的摩擦 外摩擦特性
外摩擦力与摩擦系数和正压力有关与接触面积无关。 摩擦系数为定值。
内摩擦特性
内摩擦系数为变值。
Ff
s
s Af 1 s 工件材料剪切屈服强度 Fn av Af 1 av 内摩擦部分的平均正应力, 切屑与前刀面的摩擦
切屑的折断
切削过程中变形程度超过了材料的断裂应变造成折断。 多数情况下切屑的卷曲变形不足以使切屑折断。 需用断屑台或卷屑槽使切屑产生附加变形撞到工件或后刀 面折断。 螺卷状切屑甩断。
卷屑槽形状 (图3-35)
3.1.4 已加工表面的变形
变形原因
切削刃存在刃口圆弧, 导致挤压和摩擦,产生 第Ⅲ变形区。
flash
3.1.6 磨削机理
磨削特点
★ 磨粒切削刃几何形状不确定(通常刃口前角为-60~ -85°) ★ 磨粒及切削刃随机分布 ★ 磨削厚度小(<几μm),磨削速度高,磨削点瞬时温 度高(达1000℃以上)
3.1.6 磨削机理
磨屑形成过程
★ 弹性变形:磨粒在工件 表面滑擦而过,不能切入 工件 ★ 塑性变形:磨粒切入工 件,材料向两边隆起,工 件表面出现刻痕(犁沟) ,但无磨屑产生 ★ 切削:磨削深度、磨削 点温度和应力达到一定数 值,形成磨屑,沿磨粒前 刀面流出
变形系数求法
§3.3 前刀面的挤压与摩擦 及其对切削变形的影响
第二变形区特点 强 烈 的 挤 压 与 摩擦 切 屑 底 层 纤 维 化,流动缓慢甚 至停滞 切屑弯曲
切削部位三个变形区
由摩擦而产生的热量使接触区域温度升高 本变形区的变形也影响第一区变形
§3.3 前刀面的挤压与摩擦 及其对切削变形的影响
研究过程采用了多种方法
侧面变形观察法、高速摄影法 快速落刀法、扫描电镜显微观察法等
切削变形实验设备与录像装置
§ 3.2 金属切削层的变形
挤压与切削(塑性材料切削为例)
切屑的形成与切离过程,是切削 层受到刀具前刀面的挤压而产生以 滑移为主的塑性变形过程。 正挤压:金属材料受挤压时,最大 剪应力方向与作用力方向约成45° 偏挤压:金属材料一部分受挤压时 , OB 线以上金属由于母体阻碍,不 能沿AB线滑移,而只能沿OM线滑移 切削:与偏挤压情况类似。弹性变 形→剪切应力增大,达到屈服点→产 生塑性变形,沿 OM 线滑移 → 剪切应 力与滑移量继续增大,达到断裂强度 →切屑与母体脱离。
作用在切屑上的力 取切屑为隔离体,作用在 剪切面和底面的力平衡 直角自由切削时各力的作 用角度如图 切削层面积:
Ac ac aw
剪切必需的力:
切平面
前刀面
作用在切屑上的力
Fs Ac sin
§3.3 前刀面的挤压与摩擦 及其对切削变形的影响
作用在切屑上的力 两处作用力平衡,汇集于 刀刃前方如图 由几何关系得:
§3.7 切屑的卷曲与折断
切屑控制
为使切削过程正常进行和保证已加工表面质量,应使切 屑卷曲和折断。 切屑的卷曲是切屑基本变形或经过卷屑槽使之产生附加 变形的结果。
断屑是对已变形的切屑再附加一次变形(常需有断屑装 置)。