第04讲 材料成型热过程(4)
材料成形原理第4章

L
S
L
图 从柱状枝晶的外生生长转变为 等轴枝晶的内生生长
树枝晶形态:在液体内部自由形核生长,从自由能的角度看 应该是球体。但为什么又成为树枝晶的形态呢? 在近平衡状态下,多面体的棱角前沿液相中的溶质浓度梯 度较大,其扩散速度较快;而大平面前沿液相中溶质梯度较小, 其扩散速度较慢;这样棱角处晶体长大速度大,平面处较小, 近于球形的多面体逐渐长成星形,从星形再生出分枝而成树枝 状。 宏观上,平面生长、胞状生长和柱状树枝晶生长都属于晶 体自形壁生核,然后由外向内单向延伸的生长方式,称为外 生生长。而等轴晶是液体内部自由生长的,称为内生生长。
热平衡方程导出 :
GS S GLL vL
所以:
GS S GL L v L
式中 λS,λL — 固、液两相的导热系数; ρ,L — 合金的密度和结晶潜热。 单相合金晶体生长中同时受到传热和传质过程的影响,要保持 平界面生长方式,温度梯度要高,而生长速度要低。合金的性 质也有影响,C0和 愈大,k偏离1愈远,DL愈大,界面愈趋 向于平面生长。
图
立方晶系枝晶的生长方向
a)小平面生长
b)非小平面生长
(2)枝晶间距取决于潜热的散热条件,即冷却速度 一次枝晶间距:
d1 A1G
1 3
1/ 2 1/ 2 L
v
3
二次枝晶间距: 或
d 2 A2 (ts )
1 3
1
d 2 A2 T GL R
1
3
枝晶间距指的是相邻同次枝晶之间的垂直距离。主轴 间距为d1,二次分枝间距为d2,三次分枝间距为d3。在树 枝晶的分枝之间,充填着溶质含量高的晶体,产生溶质 偏析,导致材质或形成产品的性能降低。
非规则共晶:金属-非金属(非小平面-小平面)相 非金属-非金属(小平面-小平面)相
【材料成型原理--铸造】第4章 液态金属凝固过程中的传热与传质
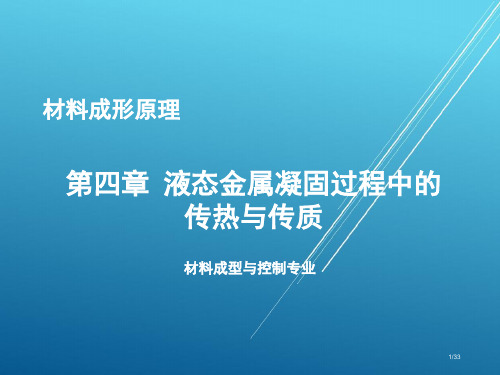
• 2、模型建立
• 温度TL时,开始凝固: • 固 度k相0C:0。百分数dfS;溶质浓
• 液相:溶质浓度几乎不变, 为C0。 • 温度降到T*时,
• 固 数f相S;:溶质浓度C*S;百分
•
液相:溶质浓 数fL。
度
C*L;百
分
28/33
• 当dfSf)S界,溶面这质处些浓固溶度相质增增将加加均d百C匀*L分扩,量散则为到:d整fS个时液,相排中出,溶使质剩量余为液(相C*(L-C1*S-) • (C*L-C*S)dfS=(1-fS)dC*L
30/33
31/33
32/33
33/33
34/33
35/33
• (二)固相无扩散,液相只有有限扩散(无对流或搅拌) 的溶质再分配
• 1、假设: • (1)合金单相凝固; • (2)固相无扩散(接近实际情况); • (3)液相有限扩散(无对流、搅拌); • (4)固液相线为直线,k0为常数; • (5)试样很长,单向放热,平面推进。
• 该两式为平衡凝固时溶质再分配的数学模型。
19/33
CS
1
C0k0 f S (1 k0 )
CL
k0
C0 f L (1 k0 )
• 3、验证 (1)开始凝固时 • 初始条件:fS0,fL1 • 则:CS=k0C0;CL=C0 (2)凝固结束时 • 初始条件:fS1,fL0 • 则:CS=C0;CL=C0/k0
凝固时间与凝固层厚度的平方成正比。
计算结果与实际接近。
适合大平板和结晶间隔小的铸件。
14/33
• 3、“折算厚度”法则
R2 t
K2
R V1 为铸件折算厚度或铸件模数。
A1
热成型方法
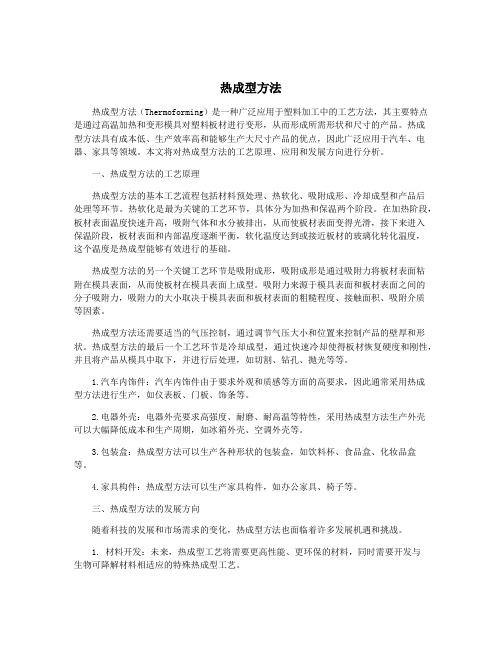
热成型方法热成型方法(Thermoforming)是一种广泛应用于塑料加工中的工艺方法,其主要特点是通过高温加热和变形模具对塑料板材进行变形,从而形成所需形状和尺寸的产品。
热成型方法具有成本低、生产效率高和能够生产大尺寸产品的优点,因此广泛应用于汽车、电器、家具等领域。
本文将对热成型方法的工艺原理、应用和发展方向进行分析。
一、热成型方法的工艺原理热成型方法的基本工艺流程包括材料预处理、热软化、吸附成形、冷却成型和产品后处理等环节。
热软化是最为关键的工艺环节,具体分为加热和保温两个阶段。
在加热阶段,板材表面温度快速升高,吸附气体和水分被排出,从而使板材表面变得光滑,接下来进入保温阶段,板材表面和内部温度逐渐平衡,软化温度达到或接近板材的玻璃化转化温度,这个温度是热成型能够有效进行的基础。
热成型方法的另一个关键工艺环节是吸附成形,吸附成形是通过吸附力将板材表面粘附在模具表面,从而使板材在模具表面上成型。
吸附力来源于模具表面和板材表面之间的分子吸附力,吸附力的大小取决于模具表面和板材表面的粗糙程度、接触面积、吸附介质等因素。
热成型方法还需要适当的气压控制,通过调节气压大小和位置来控制产品的壁厚和形状。
热成型方法的最后一个工艺环节是冷却成型,通过快速冷却使得板材恢复硬度和刚性,并且将产品从模具中取下,并进行后处理,如切割、钻孔、抛光等等。
1.汽车内饰件:汽车内饰件由于要求外观和质感等方面的高要求,因此通常采用热成型方法进行生产,如仪表板、门板、饰条等。
2.电器外壳:电器外壳要求高强度、耐磨、耐高温等特性,采用热成型方法生产外壳可以大幅降低成本和生产周期,如冰箱外壳、空调外壳等。
3.包装盒:热成型方法可以生产各种形状的包装盒,如饮料杯、食品盒、化妆品盒等。
4.家具构件:热成型方法可以生产家具构件,如办公家具、椅子等。
三、热成型方法的发展方向随着科技的发展和市场需求的变化,热成型方法也面临着许多发展机遇和挑战。
热成型工艺pptx
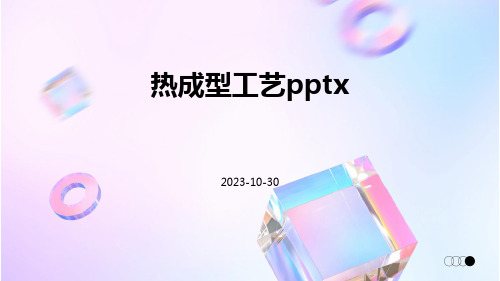
近年来,随着环保意识的不断提高,热成型工艺逐渐向绿色制造方向发展,例如采用回收塑料材料作为原料, 以及开发新的加工技术以提高生产效率和降低成本。
热成型工艺的应用范围
汽车行业
热成型工艺被广泛应用于制造汽车车身覆 盖件、仪表板、保险杠等大型塑料制品。
建筑行业
热成型工艺可制造各种类型的塑料门窗、 幕墙、扣板等建筑装饰材料。
冷却温度
冷却温度也是热成型工艺中需要严格控制的参数,冷却不当可能导致材料变形、内应力增大或者出现 气泡等缺陷。
时间控制
成型时间
成型时间太长可能导致材料变形或产生内应力,而时间太短则可能导致成型不充分或者出现缺陷。
冷却时间
冷却时间太长可能导致材料变脆或者产生内应力,而时间太短则可能导致材料未充分冷却而影响性能 。
特点
热成型工艺具有生产效率高、制造成本低、材料利用率高、 可制造大型制品等优点,但同时也存在制品精度不高、材料 性能有所损失等缺点。
热成型工艺的历史与发展
历史
热成型工艺最初起源于20世纪40年代,当时主要用于制造玻璃纤维增强塑料制品。随着材料和技术的不断发 展,热成型工艺逐渐应用于制造各种类型的塑料制品。
热成型弯曲变形
• 弯曲变形:热成型制品形状与设计不符,原因可能是材料流 动性差、模具设计不合理、冷却不均匀等。防止方法包括改 善材料流动性、优化模具设计、控制冷却速度等。
表面粗糙与橘皮状
表面粗糙
热成型制品表面不平整,原因可能是材料流 动性差、模具表面质量差等。防止方法包括 改善材料流动性、提高模具表面质量等。
热成型工艺pptx
2023-10-30
目录
• 热成型工艺简介 • 热成型工艺流程 • 热成型工艺参数控制 • 热成型工艺缺陷及防止方法 • 热成型工艺优化与发展趋势 • 热成型工艺案例展示
04第四讲:工业催化剂的制备
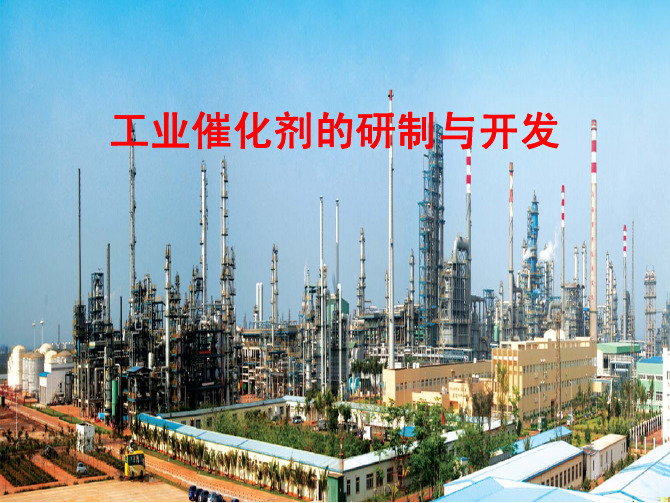
美国氰胺公司
品牌:
– Aero HDS-2钼酸钴系列 – Aero HDS-3钼酸镍系列
载体制备专利技术
– 偏铝酸钠-硫酸铝法,金属铝醋酸水解法制氢氧化铝 – 挤条成型,聚丙烯酰胺助挤剂 – 发展助滤剂,改善氢氧化铝过滤状况
浸渍技术
– 采用三氧化钼、碳酸镍、磷酸代替钼酸铵、硝酸镍配制 浸渍液 – 浸渍方法仍以喷淋细孔饱和法为主,也发展循环浸渍法
混捏方式、强度、时间
孔体积、孔分布、堆密度
挤出设备型式
双螺杆挤条机
59
钼镍磷浸渍液的配制
文献方法: 三氧化钼加入到鳞酸中,溶解后再加入碱式碳酸镍;或先 将碱式碳酸镍加入到鳞酸中,溶解后再加入三氧化钼。时 间长,要求磷酸过量,影响活性 配制的影响因素:
– – – – 三氧化钼性质:钼酸铵的性质和焙烧条件 加料的顺序 升温条件、PH值 P/MoO3, MoO3/NiO比,绘制可配制区图
金属盐
釜式操作
金属盐
T,pH控制
沉淀剂
沉淀或共沉淀法制备负载型催化剂
NaOH水溶液
NaOH水溶液
悬浮的载体 金属盐 金属盐和铝盐
可能存在的问题:
较难控制,重复性差 成核过程更易于在溶液中发生,而不是发生 在载体上 生成的金属颗粒较大,均匀性低
7
沉淀过程中的助剂
所谓添加剂是沉淀过程中非必须存在的物质, 但可能强化沉淀过程或最终产品的性质。 最广泛使用的助剂是有机物,它们可能控制孔 的形成。 例如在中孔SiO2或SiO2-Al2O3(MCM-41)的自组 装表面活性剂,如十六烷基三甲基胺。
在沸石的阳离子点引入金属
–Pt, Pd –过渡金属
精细调变孔
–KA 0.3nm, CaA 0.5nm –丝光或ZSM-5有类似作用
【精品】成形热过程陈43页PPT

61、奢侈是舒适的,否则就不是奢侈 。——CocoCha nel 62、少而好学,如日出之阳;壮而好学 ,如日 中之光 ;志而 好学, 如炳烛 之光。 ——刘 向 63、三军可夺帅也,匹夫不可夺志也。 ——孔 丘 64、人生就是学校。在那里,与其说好 的教师 是幸福 ,不如 说好的 教师是 不幸。 ——海 贝尔 65、接受挑战,就可以享受胜利的喜悦 。——杰纳勒 尔·乔治·S·巴顿
谢谢!
【精品】成形热过程陈揉进 宪法, 总体上 来说, 法律就 会更好 。—— 马克·吐 温 37、纲纪废弃之日,便是暴政兴起之 时。— —威·皮 物特
38、若是没有公众舆论的支持,法律 是丝毫 没有力 量的。 ——菲 力普斯 39、一个判例造出另一个判例,它们 迅速累 聚,进 而变成 法律。 ——朱 尼厄斯
热成型工艺讲解
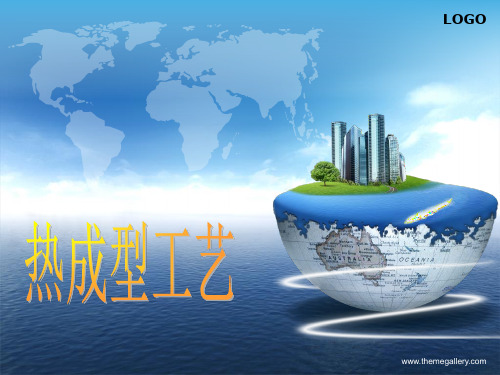
2、真空热成型
采用真空室受热软的片材紧贴模具表面而成型。但抽真空 所造成的压差不大,只适用于外形简单的制品。
3、双片材热成型
凉片材叠合在一起,中间吹气,可制大型中空制件。
4、凹凸模对压成型
将受热软化的片材放在配对你的阴、阳模之间,借助之间 的压力成型。用于ABS、PP、高分子量HDPE。制件刚性、 强度等高于一般热成型产品。
专业:XXX 姓名:LXY
2、型腔尺寸
(1)拉引深度 对于直接真空成形而言,深度对宽度之比不可超过0.5:1。若是 包模真空成形,则深度对宽度比不应超过1:1。对于有柱塞辅助、滑 动环或逆拉式之成形法,则其比率可超过1:1,甚至达2:1。然而, 一般来说,浅深度的还是比高深度的较易成形并且较佳之均匀肉厚, 如下图所示。
直接真空成形:Dmax=0.5W。 包模真空成形:Dmax=1W。 柱塞辅助,滑动环或逆拉式 法Dmax>1W到将近2W。
LOGO
目录
前言
热成型工艺的定义 热成型类型 热成型模具设计 PVC包装盒成型模具设计
前言
在市场上,热成型产品越来越多,例如杯、碟、 食品盘、玩具、帽盔,以及汽车部件、建筑装饰 件、化工设备等。 热成型与注射成型比较,具有生产效率高、设备 投资少和能制造表面积较大的产品等优点。 用于热成型的塑料主要有PS、PVC、PE、PP、PET 和纤维素(如硝酸纤维素、醋酸纤维素等)塑料, 也用于工程塑料(如ABS树脂、PC)。 热成型方法有多种,但基本上都是以真空、气压或 机械压力三种方法为基础加以组合或改进而成的。 近年来,热成型已取得新的进展,例如从挤出片 材到热成型的连续生产技术。
2、上模体
模具成型部分就是模具成型制品外形的型腔即上模体(凹模)1 材料:易加工,导热性好。一般有木材、硬石膏、陶瓷烧结物、环氧 树脂、铝合金、低碳钢等。本模具选用材料为铝合金。 在型腔设计过程中,主要考虑通气孔2的位置、数量将上模体与下模体分开,防止下模体的冷却水溢 出进入上模体,影响成型。所以在用O型密封圈密封的同时,最好在接 触面上涂上一层防水胶水,使密封的效果更好。密封隔板材料为铝板。
第三章材料成形热过程

(2)线热源时的特解
线热源可以看作是在z轴上存在无数点状 热源同时作用的情况。
线热源
如果当r≠0时,各点达到的峰值温度Tmax及 所需时间tm可用下式表示
(3)面热源时的特解
利用同样的方法,当焊件的初始温度T0≠0、 焊接端面积为F时,面热源时的特解为
5.影响焊接温度场的因素
影响焊接温度场的因素很多, 其中主要的有以下几个方面:
第一节 材料成形热过程的基本特点
本节内容包括:
一、焊接热过程的基本特点 二、凝固成形热过程的基本特点 三、塑性成形热过程的基本特点
一、焊接热过程的基本特点
焊接分为熔焊、固态焊接和固液相焊接三大类。 各类焊接的热过程特点是不同的。
熔焊是利用集中热源,对工件进行局部加热,使 之产生局部熔化,再经过冷却凝固,形成一个牢固的 接头;
3.数学解析的假定条件
焊接温度场的数学表达式为:
T=f(x、y、z、t)
(3-13)
式中T——焊件上某一点在某一瞬时的温度;
x、y、z——焊件上某一点的空间坐标;
t——时间。
假定条件
1)假定焊件的尺寸形状概括为三种典型(图3—5): a.半无限大物体(图3—5a):厚板表面堆焊可视 为此种情况; b.无限大簿板(图3—5b):x、y二个方向导热无 限,薄板对接焊接属于此种情况; c.无限长细杆(图3—5c):只有在x一个方向导 热无限,钢筋类条棒状端面焊接属于此种情况。
1.预热区内的热交换特点
(1)炉气给热以对流传热方式为主 (2)传递热量大 (3)预热区高度的变动大
1.预热区内的热交换特点
铸铁在熔化温度时的平均热容约为0.67kJ /kg·℃,熔化温度约为1200℃.设炉料的初始温度 为20℃,则预热区内所传递的热量为(1200-20) ×0.67=791kJ/kg。铸铁的熔化潜热约为230kJ/kg, 铁水的平均热容为0.96kJ/kg·℃,则铁水过热至 1400℃所需的总热量为:791+230+0.96(1400-1200) =1213kJ/kg。此时,由预热区传递的热量约占总 热量的65%左右,可见预热区内传递热量之大。
- 1、下载文档前请自行甄别文档内容的完整性,平台不提供额外的编辑、内容补充、找答案等附加服务。
- 2、"仅部分预览"的文档,不可在线预览部分如存在完整性等问题,可反馈申请退款(可完整预览的文档不适用该条件!)。
- 3、如文档侵犯您的权益,请联系客服反馈,我们会尽快为您处理(人工客服工作时间:9:00-18:30)。
区域进行的;
30 22
铸型和铸件的热物理参量还都随温度而变化,不是
固定的数值。将这些因素都考虑进去,建立一个符
合实际情况的微分方程式是很困难的。因此,用数 学分析法研究铸件的凝固过程时,必须对过程进行 合理的简化。
30
23
1、铸件在绝热铸型中凝固
砂型、石膏型、陶瓷型、熔模铸造等的铸型因其
材料的热导率远小于凝固金属的热导率,可统称 为绝热铸型。 在凝固传热中,金属铸件的温度梯度比铸型中的 温度梯度小得多。相对而言,金属中的温度梯度 可忽略不计。
图1-26 绝热铸型凝固温度分布 TL—金属液相线温度;T0一铸型初始温度; M—凝固层折算厚度 30
25
2、金属—铸型界面热阻为主的金属型中凝固
较薄的铸件在工作表面涂有涂料的金属型中铸造
时,就属于这种情况。
金属—铸型界面处的热阻较铸件和铸型中的热阻
大得多,这时,凝固金属和铸型中的温度梯度可
忽略不计,即认为温度分布是均匀的,传热过程 取决于涂料层的热物理性质。
30
15
中、高碳的岛状奥氏体,在中等冷却条件下,会形 成孪晶马氏体和部分残余奥氏体的混合物,即M-A
组元。
随着M-A组元数量的增多,韧脆转变温度将显著升
高。因此,在热影响区出现组元将会引起脆化。
30
16
4)热应变时效脆化
在制造焊接结构的过程中,不可避免地要进行各种
加工,如下料、剪切、弯曲成形、气割、矫形、锤
击、焊接和其他热加工等程序。
由这些加工引起的局部应变、塑性变形对焊接HAZ
脆化有很大的影响,由此而引起的脆化称为热应变 时效脆化。
30
17
焊接热影响区产生的热应变时效脆化可分为: ⑴ 静应变时效脆化 在室温或低温下受到预应变后产生的时效脆化现 象,叫作静应变时效脆化。它的特征是强度和硬 度增高,而塑性、韧性下降。只有钢中存在碳、 氮自由间隙原子时才会产生这种现象。 ⑵ 动应变效脆化 一般在较高温度下,特别是200~400℃温度范围的 预应变所产生的时效脆化现象称为动应时效脆化。 焊接热影响区的热应变脆化多数是由动应变时效 所引起,通常所说的“蓝脆性”就属于动应变时 效脆化现象。
30 18
关于应变时效脆化的机理至今尚未彻底清楚。多 数人认为:是碳、氮原子聚集在位错周围形成所
谓Cottrell气团,对位错产生钉扎作用所引起。
热应变时效脆化多发生在低碳钢和碳锰低合金钢
的Ar1以下亚热影响区,在金相组织上看不出明显
的变化。
焊接接头熔合区和Ar1以下的亚热影响区均可出现, 一般单道焊时易在亚热影响(Ar1以下)产生热应 变时效脆化,而多层焊易在熔合区出现热应变时
30 不同部位Trs的变化如图1-25所示。 10
Trs越高,说明脆化倾向较 大。从图中可看出,从焊
缝到热影响区韧脆转变温
度有两个峰值,即过热粗 晶区和Ac1以下(约400~ 600℃)的时效脆化区。
在900℃附近的细晶区具有 最低的脆性转变温度,说 明这个部位的韧性高,抗
图1-25 碳锰钢HAZ的脆化分布
显的温度梯度。由于此时金属—铸型界面的热阻
相对很小可忽略不计,则铸型内表面和铸件表面
温度相同。
可以认为,厚壁金属型中的凝固传热为两个相连 接的半无限大物体的传热,整个系统的传热过程 取决于铸件和铸型的热物理性质,其温度分布如
图1-28所示。
30
28
图1-28 厚壁金属型中凝固的温度分布 TL—金属液相线温度;T0—铸型初始温度; M—凝固层折算厚度
若金属无过热浇注,则界面处铸件的温度等于凝 固温度,铸型的温度保持为T0,如图1-27所示。
30 26
图1-27 以界面热阻为主的温度分布 TL—金属液相线温度;T0一铸型初始温度; M—凝固层折算厚度
30
27
3、厚壁金属型中的凝固
当金属型的涂料层很薄时,厚壁金属型中凝固金
属和铸型的热阻都不可忽略,因而两者都存在明
30
29
4、水冷金属型中的凝固
在水冷金属型中,是通过控制冷却水温度和流量
使铸型保持近似恒定的,在不考虑金属—铸型界
面热阻的情况下,凝固金属表面温度等于铸型温
度。
在这种情况下,凝固传热的主要热阻是凝固金属 的热阻,铸件中有较大的温度梯度。系统的温度 分布如图1-29所示。
30
30
图1-29 水冷薄壁金属型中凝固的温度分布 TL—金属液相线温度;T0—铸型初始温度; M—凝固层折算厚度
30
31
第一章 作业
P23:1,2,4,6
30
32
本讲小节
焊接热影响区的性能 凝固成型中的温度场
30
33
理状态有关。母材焊前调质处理的回火温度越低(即
强化程度越大),则焊后的软化程度越严重,如图124所示。
30
7
因为焊前调质时回火温度
Tt越低,析出的碳化物颗
粒越弥散细小。焊接时加 热温度在Ac1~Tt范围内 的碳化物聚集长大越明显, 因此回火软化现象越严重。
图1-24 调质钢焊接HAZ的硬度分布 A—焊前淬火+低温回火 B—焊前淬火+高温回火 C—焊前退火 1—淬火区 2—部分淬火区 3—回火区
软化”而导致HAZ的软化。
30 9
4、 焊接热影响区的脆化
热影响区脆化是热影响区在焊接热循环作用下所发
生的塑性、韧性严重下降的现象。HAZ的脆化在焊
接应力的作用下会导致接头或结构产生脆性断裂,
必须予以重视。
脆化类型: 粗晶脆化、析出相脆化、M-A脆化、热应变脆化、 氢脆化、石墨脆化 利用韧脆转变温度( Trs )作为判据,碳锰钢热影响区
脆化的能力较强。
30
11
1)粗晶脆化
对不易淬火钢,粗晶脆化主要是由于晶粒长大, 甚至形成粗大的魏氏组织。 对于易淬火钢,则主要是由于产生脆硬的孪晶马 氏体所致。 注意:脆化程度与粗晶区的马氏体类型有关。 一般来讲,低碳马氏体反而有改善粗晶区韧 性的作用。对于含碳高的高强钢在热影响区出现 的高碳马氏体(孪晶),则脆化严重。由此看来, 影响粗晶脆化的主要因素是钢种的化学成分和焊 后粗晶区的金相组织。 30 12
2、 焊接热影响区的硬度
研究表明,焊接热影响区的硬度与其力学性能密切
相关。
一般而言,随着硬度的增大,强度升高,塑性、韧
性下降,冷裂纹倾向增大。
因此,通过测定焊接热影响区的硬度分布便可间接 地估计热影响区的力学性能及抗裂性等。
30
5
图1-23为相当于20Mn钢的 低合金钢单道焊时热影响 区的硬度分布。 可以看出,在焊接热影响 区的熔合线附近硬度值最 高,远离熔合线,硬度降 低,逐渐接近于母材的硬 度水平。 这进一步说明,熔合线附 近是焊接接头中的最薄弱 处。
效脆化。
30
19
综上所述,影响热影响区脆化的因素很多,不同材 料产生脆化的原因也不相同。当热影响区的脆化严
重时,即使母材和焊缝韧性再高也是没有意义的。
为了提高焊接结构安全运行的可靠性,必须设法保 证焊接热影响区的韧性。
30
20
1.5 凝固成型中的温度场
铸件凝固过程中,许多现象都是温度的函数。因此, 研究凝固过程传热所要解决的主要问题是在不同的 时刻,铸件和铸型中的温度场变化。
30
图1-22 热影响区的力学性能 (C=0.17%, Mn=1.28%, Si=0.40%)
3
当Tm值达到1300℃附近时,强 度达到最高值(相当于粗晶过热 区); 在Tm超过1300℃的部位, 在塑性继续下降的同时,强度 也有所下降。 这可能是由于晶粒过于粗大和 晶界疏松造成的。 对于加热温度在Ac1~Ac3的不 完全重结晶区,由于晶粒大小 不均匀,σs反而降低。 在热影响区中,硬度最高、塑 图1-22 热影响区的力学性能 性最差的部位是过热区,属于 (C=0.17%, Mn=1.28%, Si=0.40%) 30 4 接头的薄弱环节。
上讲回顾
影响焊接热循环的因素 多层焊的热循环 焊接热影响区的组织分布
30
1
1.4. 2 焊接热影响区的性能
焊接热影响区组织分布的不均匀性,必然要反映在
性能上的差异。
对于一般的焊接结构来讲,主要是考虑热影响区的
硬度变化、力学性能、脆化倾向和软化现象。
30
2
1、 焊接热影响区的力学性能 采用焊接热模拟技术,研究焊 接热影响区不同部位的力学性 能。 图1-22是淬硬倾向不大的钢种 (相当于16Mn钢)热影响区的常 温力学性能。 由该图可以看出,当加热最高 温度超过900℃以后,随着加 热最高温度的升高,强度、硬 度升高,而塑性下降;
30
图1-23 相当于16Mn钢的焊接热影响区的硬度分布 材料:0.20%C,1.38%Mn,0.23%Si 焊接条件:170A,25V,150mm/min,板厚20mm
6
3、 焊接热影响区的软化
经过调质处理的高强钢和具有沉淀强化及弥散强化
的合金,在HAZ会产生不同程度的软化或失强。