Chapter 5 Synthesis of Planar Linkages
机械原理复习重点
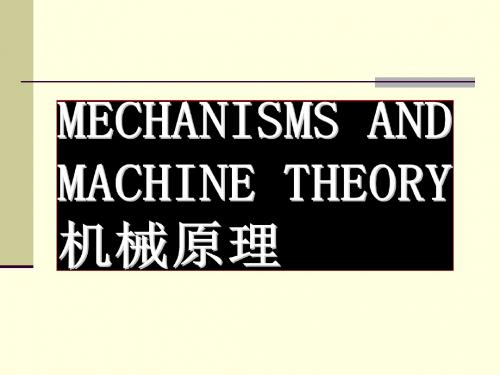
•The composition of principle and structure analysis
2.1 The composition of a mechanism Links
Fixed links
Links 构件 Kinematic pairs 运动副
固定构件 ------- Frames 机架
从动件运动规律的设计 凸轮机构基本尺寸的设计 凸轮机构轮廓曲线的设计 绘制凸轮机构工作图
(4)Making Cam Mechanism Drawing
复习重点 1、常用运动规律的特点,刚性冲击,柔性冲击,S-δ曲 线绘制 2、凸轮轮廓设计原理—反转法,自锁、压力角与基 圆半径的概念
例题.如图所示,偏置直动滚子从动件盘形凸轮机构,已知凸轮实际轮廓 线为一圆心在O点的偏心圆,其半径为R. 从动件的偏距为e。 1).分析凸轮顺时针转动时,图示从动件偏置方向是否合理? 2).标出当从动件从图示位置升到位移s时,对应凸轮的转角及凸轮 机构的压力角。 解:1)图示偏置方向为正偏置,偏置方向合理。
Driving links 主动件
Moving links 活动构件
Driving links have their own indepen-dent motion characteristics the other moving links are called as Driven links 从动件
If all lower pairs in a four-bar linkage are revolute pairs, as shown in the following Fig, the linkage is called a revolute four-bar linkage, which is the basic form of four-bar linkages.
含有萘酰亚胺的菁染料太阳能电池敏化剂的合成

含有萘酰亚胺的菁染料太阳能电池敏化剂的合成詹文海 花建丽 金樱华 武文俊 田禾*(华东理工大学精细化工研究所结构可控先进功能材料及其制备教育部重点实验室 上海 200237)摘 要 通过Click反应把萘酰亚胺化合物连接到含有醛基的吲哚上,再通过醛基和吲哚碘盐的Knoevenagel缩合反应合成出带有萘酰亚胺部分的菁染料,用NMR、MS、元素分析、UV_Vis等方法对其结构和性能进行了表征和测试。
关键词 菁染料 萘酰亚胺 太阳能电池敏化染料 合成Synthesis of Novel Naphthalimide_containing Cyanine Dye Utilized as Solar Cell SensitizerZhan Wenhai,Hua Jianli,Jin Yinghua,Wu Wenjun,Tian He*(Laboratory for Advanced Materials and Institute of Fine Chemicals,East China University of Science&T echnology,Shanghai200237)Abstract Two novel cyanine dyes containing naphthali mide have been syn thesized by Knoevenagel condensation reaction between i ndole iodide and naphthali mide_indoles generated from naphthalimides and indole via Click reaction andcharacterized by NMR,MS,elemental analysis,UV_Vis absorption spectra etc.Key words Naphthalimide,Cyanine dye,Solar cell sensitizer,Synthesis目前,染料敏化太阳能电池的光电转换效率已经超过了10%,达到了实用的要求。
英文文献中的关键词以及重要句子
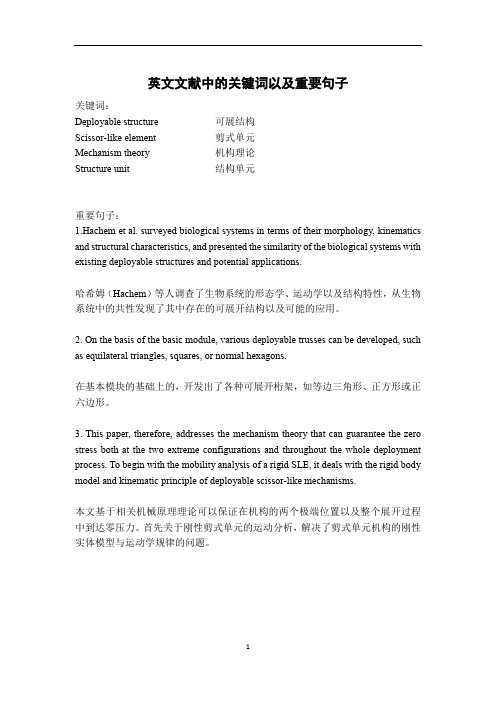
英文文献中的关键词以及重要句子关键词:Deployable structure 可展结构Scissor-like element 剪式单元Mechanism theory 机构理论Structure unit 结构单元重要句子:1.Hachem et al. surveyed biological systems in terms of their morphology, kinematics and structural characteristics, and presented the similarity of the biological systems with existing deployable structures and potential applications.哈希姆(Hachem)等人调查了生物系统的形态学、运动学以及结构特性,从生物系统中的共性发现了其中存在的可展开结构以及可能的应用。
2. On the basis of the basic module, various deployable trusses can be developed, such as equilateral triangles, squares, or normal hexagons.在基本模块的基础上的,开发出了各种可展开桁架,如等边三角形、正方形或正六边形。
3. This paper, therefore, addresses the mechanism theory that can guarantee the zero stress both at the two extreme configurations and throughout the whole deployment process. To begin with the mobility analysis of a rigid SLE, it deals with the rigid body model and kinematic principle of deployable scissor-like mechanisms.本文基于相关机械原理理论可以保证在机构的两个极端位置以及整个展开过程中到达零压力。
构造地质学双语9 lineation

Chapter 5 Lineation and foliationFoliations and lineations are mesoscopic (handspecimen to outcrop) penetrative (occur throughout)features that characterize volumes of rocks and are related to larger-scale mappable features such as folds and faults. They are clues to large scale geometry, kinematics, strain at the microscopic level, and conditions of deformation.Part one: LineationLineation is parallel alignment of elongate linear fabric elements in a rock body. We use these features because they contain the most kinematic information. In other words, the most strain and stress history of the rock is most recorded in these structures. According its causes, lineation can be classified into primary and secondary lineation. Primary lineation is those formed during the formation of rocks, such as ropy structure in lava flows and linear alignment of phenocrysts and xenoliths (flow lineation) in plutonic rocks. Secondary lineations are those formed after the formation of rocks. The lineations discussed here are secondary lineations. From the viewpoint of observation, lineation can be classified as small scale and large-scale lineations.1.Small scale lineation●Stretching lineations: An important type of lineation is formed by the parallel alignmentof a set of objects that have acquired an elongate shape as a result of deformation.Individual detrital grains or fragments of any size may be deformed and/or rotated, to define a lineation. Extension lineations are generally inclined to the related fold axes at an angle close to 90° (transverse lineations) but locally may be parallel to the fold axis. Ina given area it is commonly one or the other.●Crenulation Lineation: is expressed as bundles of very small, closely spaced fold hinges(crests and troughs). Best developed in strongly anisotropic rocks, such as phyllites and schists.●Intersection Lineation: The intersection of any two planar structures forms a line. If manysuch intersections are present in a rock they constitute an intersection lineation. Commonintersections include bedding-cleavage intersections and intersections between two foliations of different generation. In cylindrically folded rocks, intersection lineation are subparallel to the fold axis.●Mineral Lineation: Metamorphic minerals often grow with a preferred crystallographicand dimensional orientation, i.e. with their long axes in parallel alignment. Mineral lineations are delineated by the long axes of individual, elongate or platy crystals (for example amphibole crystals) or mineral aggregates aligned and sub-parallel within a foliation plane. They are a penetrative element of the rock fabric, commonly parallel to other types of lineation, and serve to reinforce them. Mineral lineations may be parallel or inclined to the axes of related folds.rge scale lineations●Boudins -sausage-shaped segments of extended competent layers surrounded by lesscompetent matrix. If ductility contrast is large, boudins will be subangular withrectangular forms. As ductility contrasts diminish, boudins become more lens-shaped inprofile.'Boudin', 'boudinage', from a French word for sausage, describes the way that layers of rock break up under extension. Imagine the hand, fingers together, flat on thetable, encased in soft clay and being squeezed from above, as being like a layer ofrock. As the spreading clay moves the fingers (sausages) apart, the most mobile rockfractions (ore-making fluids) are drawn or squeezed into the developing gaps. In thatsimple analogy for rock deformation for which the term was coined almost a hundred years ago, is a model for mineral exploration which is as simple as it is controversial, and which is ignored by the consensusBoudinage depicts the periodical segmentation of pre-existing bodies, generally more competent than the rock surrounding them, when they are inhomogeneously stretched during deformation. Typically, a strong layer or dyke is broken up into a series of elongate and aligned blocks (whose cylinder-like shape motivated the name boudin).Boudin profiles are variable, with rectangular, rhomboidal shapes being common. In low-grade rocks, boudins are usually separated and form a pull-apart structure or gap, which is generally mineralised.. At higher grades, and in unconsolidated rocks, the competent layers have generally not broken through; narrow, thinned necks separate and alternate with boudins of relatively still, thick layers and the resulting structure is known as pinch-and-swell. Pinch-and-swell and pull-apart structures may be combined at any level since they really depend on the ductility contrast between the strong bed and its matrix.Boudins are commonly linear and aligned parallel to the axes of related folds.However, stretching may take place in two directions in the plane of layering.Segmentation in these two directions produces nearly equidimensional boudins rather than the elongate forms. This process is referred to as chocolate-tablet boudinage.Structures similar to boudins and pinch-and-swells may occur in certain zones of homogeneous strongly foliated rocks with no apparent lithological contrast between the boudins and the host rocks. These generally long lens-shaped structures are described as foliation boudinage.Boudins (and mullions) tend to be large in size and are commonly restricted to certain layers or, in the case of mullions, are restricted even to certain surfaces in a deformed sequence. Thus at outcrop scale they are a non-penetrative feature.A boudin axis can be measured, like a fold axis, as the nearest approximation to aline that, if moved parallel to itself, generates the boudin form. The neckline connects points of minimum layer-thickness. The length of a boudin is measured parallel to the boudin axis. The width and the thickness are dimensions orthogonal to this axis.●Pencil structure - formed by the intersection of bedding parallel foliationand cleavage,such that the rock breaks up into elongated, square sided "pencils". Pencil structure forms in weakly deformed shales or mudstone, representing an early stage in the development of slaty cleavage●Mullions are coarse structures formed in the original rock material as opposed tosegregated or introduced material. The mullion is a columnar corrugation of the surface ofa competent layer, at any size. These long features are remarkably cylindrical. They havea ribbed or grooved appearance, often cuspate in shape with broad smoothly curvedconvex surfaces separated by narrow, sharp, inward-closing hinges. The individual surface features are very persistent along the length of the mullion.●Rodding: is a morphological term for elongate, cylindrical and monomineralic bodies ofsome segregated mineral (quartz, calcite, pyrite, etc.) enclosed in metamorphic rocks ofall grades. In profile, rods may have any outline, from elliptical to irregular to that of a dismembered fold.3.Observation and measurement of lineations(1)Differentiate the primary and secondary lineation(2)Determine the types of lineation.(3)Measure its orientation. And find out its relationship with associated large scalestructures. Be sure that only those measured on the foliation plane is the reallineation.(4)As one of the important kinematic marker, lineation can show the movementdirection of materials during deformation as well as the strain state. In most cases,the directions of stretching lineation and mineral lineation are parallel to the X axisof strain ellipsoid. And the directions of boudins ,mullions, intersectionlineations ,pencil lineation and crenulation lineation are parallel to the Y-axis ofstrain ellipsoid.Part two: foliationFoliation are any type of planar fabric in rock, including bedding, cleavage, schistosity. Foliations are penetrative (occur throughout) in samples at 10's of cm scale. Thus faults are not foliations, nor are fractures and joints because the latter are simply fractures and not related to internal structure of rock.According to the formation and evolution procedure, foliation can be divided into two basic types:●Primary foliation includes layers in sedimentary rocks and flow banding and flowfoliations in igneous rocks.●Secondary foliations are usually associated with deformed metamorphic rocks andinclude (in increasing grade and grain size) slaty cleavage, phyllitic structure,schistosity and gneissic foliation.Cleavage is a secondary foliation formed under low grade metamorphic conditions (or less) that allows the rock to split along planes. Here ,we will discuss mainly on cleavage. Other types of foliation, such as phyllitic structure and schistosity will be introduced in petrology course.1. The structure of cleavageCleavage is a foliation that forms in relatively low-grade metamorphic rocks. One of the most important feature of cleavage is its domain structure. That is, the cleavage consists of cleavage domains and microlithons, each of which has a unique composition and geometry●Cleavage domains (M-domains) are thin zones of concentrated, strongly aligned, platyminerals(mica) or insoluble oxide and clay residue.●Microlithons(Q-domains) are lenticular or tabluar zones with less abundant platyminerals that exhibit a weak to strong alignment. It is usually the result of concentrationof quartz.2. Types of cleavageThere are many different kinds of classification of cleavages. Here we will only introduce the Powell’s classification. According to Powell’s classification scheme, cleavage is broken out into two main categories: continuous and spaced, depending on whether there are distinguishable, distinct cleavage domains in the rock: if no distinct domains, if distinct domains are present spaced. Scales of cleavage development from about .01 mm to approaching 1 m ,∙< 1 mm = Continuous∙> 1 mm = Spaced(1)Continuous cleavage is where the domains (microlithons) between the cleavage surfaces are too fine to observe with the naked eye. These are further broken down into fine and coarse. (2)Disjunctive cleavage obviously, is the opposite where the microlithons between the cleavage surfaces are large enough to be seen plainly. However, there are two general categories of spaced cleavage: spaced and crenulation.●Spaced cleavage consists of an array of parallel to anastomosing, stylolitic to smooth,fracture-like partings common in slightly deformed sedimentary rocks.●Crenulation spaced cleavage cuts a preexisting continuous cleavage inherent to the rock.Crenulation cleavage is characterized by microscale kinking of an earlier fabric. In symmetric crenulation cleavage the boundaries between adjacent zones are approximate planes of symmetry. In sigmoidal or asymmetric crenulation cleavage, the relict earlier foliation is bent into a sigmoidal shape. Pressure solution(压溶)can also enhance crenulation cleavage, resulting in a concentration of mica in the cleavage domains (M-domains) and a concentration of quartz in the hinge zones of microlithons (Q-domains).Fig: Fold with axial plane foliation and boudins developed on limbs3. Observation and measurement of cleavage● Distinguish the layer and cleavage● Observe carefully the geometrical pattern and its structure.● Measure its orientation.● Determine the strain state of deformed rocks. In general, cleavage is perpendicular todirection of maximum shortening, or in other words , parallel to the maximum flattening of strain ellipsoid, that is , the XY plane. For example, the axial planar cleavage is always approximately parallel to axial surfaces of folds, showing that the cleavage is perpendicular to direction of maximum shortening.Determine the generations of different phases of cleavage. Usually, we use the S O to stand for the sedimentary bedding , S1 the earliest developed cleavage, and so on.。
Chapter 5 Clayden Organics 大学有机化学

Electrophile accept electrons into empty low-energy orbitals represented by one of the following:
Curly arrows represent reaction mechanisms
Nucleophiles
Nucleophiles are either (i) negatively charged, (ii) neutral species with lone pair(s) of electrons, (iii) carbon with lone pairs of electrons
Bond polarity
Polarity can arise from σ bonds too.
An electronegative element bonded to an electropositive element causes bond polarization. The negative end of the dipole is attracted to the electropositive end
(v) σ bonds too can act as nucleophiles
(vi) compounds with carbon-metal bonds
Electrophiles
Electrophiles are neutral or positively charged species with an empty atomic orbital (the opposite of a lone pair) or a low-energy antibonding orbital
连杆机构外文文献翻译、中英文翻译、外文翻译
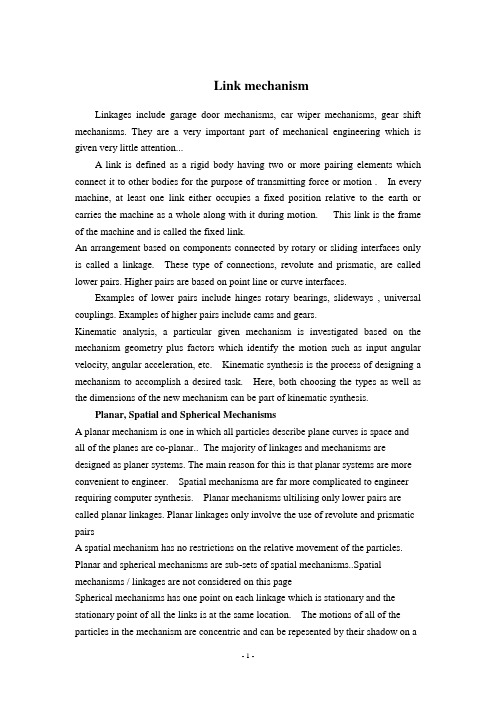
Link mechanismLinkages include garage door mechanisms, car wiper mechanisms, gear shift mechanisms. They are a very important part of mechanical engineering which is given very little attention...A link is defined as a rigid body having two or more pairing elements which connect it to other bodies for the purpose of transmitting force or motion . In every machine, at least one link either occupies a fixed position relative to the earth or carries the machine as a whole along with it during motion. This link is the frame of the machine and is called the fixed link.An arrangement based on components connected by rotary or sliding interfaces only is called a linkage. These type of connections, revolute and prismatic, are called lower pairs. Higher pairs are based on point line or curve interfaces.Examples of lower pairs include hinges rotary bearings, slideways , universal couplings. Examples of higher pairs include cams and gears.Kinematic analysis, a particular given mechanism is investigated based on the mechanism geometry plus factors which identify the motion such as input angular velocity, angular acceleration, etc. Kinematic synthesis is the process of designing a mechanism to accomplish a desired task. Here, both choosing the types as well as the dimensions of the new mechanism can be part of kinematic synthesis.Planar, Spatial and Spherical MechanismsA planar mechanism is one in which all particles describe plane curves is space and all of the planes are co-planar.. The majority of linkages and mechanisms are designed as planer systems. The main reason for this is that planar systems are more convenient to engineer. Spatial mechanisma are far more complicated to engineer requiring computer synthesis. Planar mechanisms ultilising only lower pairs are called planar linkages. Planar linkages only involve the use of revolute and prismatic pairsA spatial mechanism has no restrictions on the relative movement of the particles. Planar and spherical mechanisms are sub-sets of spatial mechanisms..Spatial mechanisms / linkages are not considered on this pageSpherical mechanisms has one point on each linkage which is stationary and the stationary point of all the links is at the same location. The motions of all of the particles in the mechanism are concentric and can be repesented by their shadow on aspherical surface which is centered on the common location..Spherical mechanisms/linkages are not considered on this pageMobilityAn important factor is considering a linkage is the mobility expressed as the number of degrees of freedom. The mobility of a linkage is the number of input parameters which must be controlled independently in order to bring the device to a set position. It is possible to determine this from the number of links and the number and types of joints which connect the links...A free planar link generally has 3 degrees of freedom (x , y, θ ). One link is always fixed so before any joints are attached the number of degrees of freedom of a linkage assembly with n links = DOF = 3 (n-1)Connecting two links using a joint which has only on degree of freedom adds two constraints. Connecting two links with a joint which has two degrees of freedom include 1 restraint to the systems. The number of 1 DOF joints = say j 1 and the number of joints with two degrees of freedom = say j 2.. The Mobility of a system is therefore expressed as mobility = m = 3 (n-1) - 2 j 1 - j 2Examples linkages showing the mobility are shown below..A system with a mobility of 0 is a structure. A system with a mobility of 1 can be fixed in position my positioning only one link. A system with a mobility of 2 requires two links to be positioned to fix the linkage position..This rule is general in nature and there are exceptions but it can provide a very useful initial guide as the the mobility of an arrangement of links...Grashof's LawWhen designing a linkage where the input linkage is continuously rotated e.g. driven by a motor it is important that the input link can freely rotate through complete revolutions. The arrangement would not work if the linkage locks at any point. For the four bar linkage Grashof's law provides a simple test for this conditionGrashof's law is as follows:For a planar four bar linkage, the sum of the shortest and longest links cannot be greater than the sum of the remaining links if there is to becontinuous relative rotation between two members.Referring to the 4 inversions of a four bar linkage shown below ..Grashof's law states that one of the links (generally the shortest link) will be able to rotate continuously if the following condition is met...b (shortest link ) + c(longest link) < a + dFour Inversions of a typical Four Bar LinkageNote: If the above condition was not met then only rocking motion would be possible for any link..Mechanical Advantage of 4 bar linkageThe mechanical advantage of a linkage is the ratio of the output torque exerted by the driven link to the required input torque at the driver link. It can be proved that the mechanical advantage is directly proportional to Sin( β ) the angle between the coupler link(c) and the driven link(d), and is inversely proportional to sin( α ) the angle between the driver link (b) and the coupler (c) . These angles are not constant so it is clear that the mechanical advantage is constantly changing.The linkage positions shown below with an angle α = 0 o and 180 o has a near infinite mechanical advantage. These positions are referred to as toggle positions. These positions allow the 4 bar linkage to be used a clamping tools.The angle β is called the "transmission angle". As the value sin(transmission angle) becomes small the mechanical advantage of the linkage approaches zero. In these region the linkage is very liable to lock up with very small amounts of friction. When using four bar linkages to transfer torque it is generally considered prudent to avoid transmission angles below 450 and 500.In the figure above if link (d) is made the driver the system shown is in a locked position. The system has no toggle positions and the linkage is a poor design Freudenstein's EquationThis equation provides a simple algebraic method of determining the position of an output lever knowing the four link lengths and the position of the input lever. Consider the 4 -bar linkage chain as shown below..The position vector of the links are related as followsl1 + l2 + l3 + l4 = 0Equating horizontal distancesl 1cos θ 1 + l 2cos θ 2 + l 3cos θ 3 + l 4cos θ 4 = 0Equating Vertical distancesl 1sin θ 1 + l 2sin θ 2 + l 3sin θ 3 + l 4sin θ 4 = 0Assuming θ 1 = 1800then sin θ 1= 0 and cosθ 1 = -1 Therefore- l 1 + l 2cosθ 2 + l 3cosθ 3 + l 4cos θ 4 = 0and .. l 2sin θ 2 + l 3sin θ 3 + l 4sin θ 4 = 0Moving all terms except those containing l 3 to the RHS and Squaring both sidesl 32 cos 2θ 3 = (l 1 - l 2cos θ 2 - l 4cos θ 4 ) 2l 32 sin 2θ 3 = ( - l 2sin θ 2 - l 4sin θ 4) 2Adding the above 2 equations and using the relationshipscos ( θ 2 - θ 4) = cos θ 2cos θ 4+ sin θ 2sin θ 4 ) and sin2θ + cos2θ = 1the following relationship results..Freudenstein's Equation results from this relationship asK 1cos θ 2 + K2cos θ 4 + K 3= cos ( θ 2 - θ 4 )K1 = l1 / l4K2 = l 1 / l 2K3 = ( l 32 - l 12 - l 22 - l 2 4 ) / 2 l 2 l 4This equation enables the analytic synthesis of a 4 bar linkage. If three position of the output lever are required corresponding to the angular position of the input lever at three positions then this equation can be used to determine the appropriate lever lengths using three simultaneous equations...Velocity Vectors for LinksThe velocity of one point on a link must be perpendicular to the axis of the link, otherwise there would be a change in length of the link.On the link shown below B has a velocity of v AB= ω.AB perpendicular to A-B." The velocity vector is shown...Considering the four bar arrangement shown below. The velocity vector diagram is built up as follows:∙As A and D are fixed then the velocity of D relative to A = 0 a and d are located at the same point∙The velocity of B relative to a is v AB= ω.AB perpendicular to A-B. This is drawn to scale as shown∙The velocity of C relative to B is perpedicular to CB and passes through b∙The velocity of C relative to D is perpedicular to CD and passes through d∙The velocity of P is obtained from the vector diagram by using the relationship bp/bc = BP/BCThe velocity vector diagram is easily drawn as shown...Velocity of sliding Block on Rotating LinkConsider a block B sliding on a link rotating about A. The block is instantaneously located at B' on the link..The velocity of B' relative to A = ω.AB perpendicular to the line. The velocity of B relative to B' = v. The link block and the associated vector diagram is shown below..Acceleration Vectors for LinksThe acceleration of a point on a link relative to another has two components:∙1) the cen tripetal component due to the angular velocity of the link.ω 2.Length∙2) the tangential component due to the angular acceleration of the link....∙The diagram below shows how to to construct a vector diagram for the acceleration components on a single link.The centripetal acceleration ab' = ω 2.AB towards the centre of rotation. The tangential component b'b = α. AB in a direction perpendicular to the link..The diagram below shows how to construct an acceleration vector drawing for a four bar linkage.∙For A and D are fixed relative to each other and the relative acceleration = 0 ( a,d are together )∙The acceleration of B relative to A are drawn as for the above link∙The centripetal acceleration of C relative to B = v 2CB and is directed towards B ( bc1 )∙The tangential acceleration of C relative to B is unknown but its direction is known∙The centripetal acceleration of C relative to D = v 2CD and is directed towards d( dc2)∙The tangential acceleration of C relative to D is unknown but its direction is known.∙The intersection of the lines through c1 and c 2 locates cThe location of the acceleration of point p is obtained by proportion bp/bc =BP/BC and the absolute acceleration of P = apThe diagram below shows how to construct and acceleration vector diagram for a sliding block on a rotating link..The link with the sliding block is drawn in two positions..at an angle dωThe velocity of the point on the link coincident with B changes from ω.r =a b 1to ( ω + dω) (r +dr) = a b 2The change in velocity b1b2has a radial component ωr d θ and a tangential component ωdr + r dωThe velocity of B on the sliding block relative to the coincident point on the link changes from v = a b 3 to v + dv = a b 4.The change in velocity = b3b4 which has radial components dv and tangential components v d θThe total change in velocity in the radial direction = dv- ω r d θRadial acceleration = dv / dt = ω r d θ / dt = a - ω2 rThe total change in velocity in the tangential direction = v dθ + ω dr + r αTang ential acceleration = v dθ / dt + ω dr/dt + r d ω / dt= v ω + ω v + r α = α r + 2 v ωThe acceleration vector diagram for the block is shown belowNote : The term 2 v ω representing the tangential acceleration of the block relative to the coincident point on the link is called the coriolis component and results whenever a block slides along a rotating link and whenever a link slides through a swivelling block连杆机构连杆存在于车库门装置,汽车擦装置,齿轮移动装置中。
机械工程专业英语考试必备
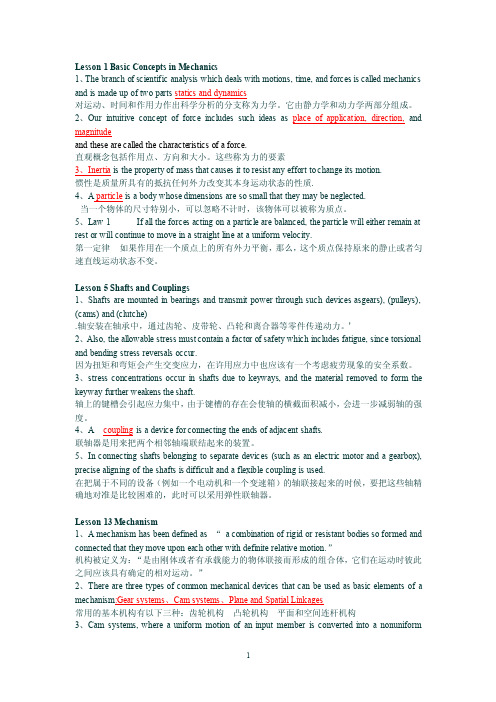
Lesson 1 Basic Concepts in Mechanics1、The branch of scientific analysis which deals with motions, time, and forces is called mechanics and is made up of two parts statics and dynamics对运动、时间和作用力作出科学分析的分支称为力学。
它由静力学和动力学两部分组成。
2、Our intuitive concept of force includes such ideas as place of application, direction,and magnitudeand these are called the characteristics of a force.直观概念包括作用点、方向和大小。
这些称为力的要素3、Inertia is the property of mass that causes it to resist any effort to change its motion.惯性是质量所具有的抵抗任何外力改变其本身运动状态的性质.4、A particle is a body whose dimensions are so small that they may be neglected.当一个物体的尺寸特别小,可以忽略不计时,该物体可以被称为质点。
5、Law 1 If all the forces acting on a particle are balanced, the particle will either remain at rest or will continue to move in a straight line at a uniform velocity.第一定律如果作用在一个质点上的所有外力平衡,那么,这个质点保持原来的静止或者匀速直线运动状态不变。
专业英语课文翻译
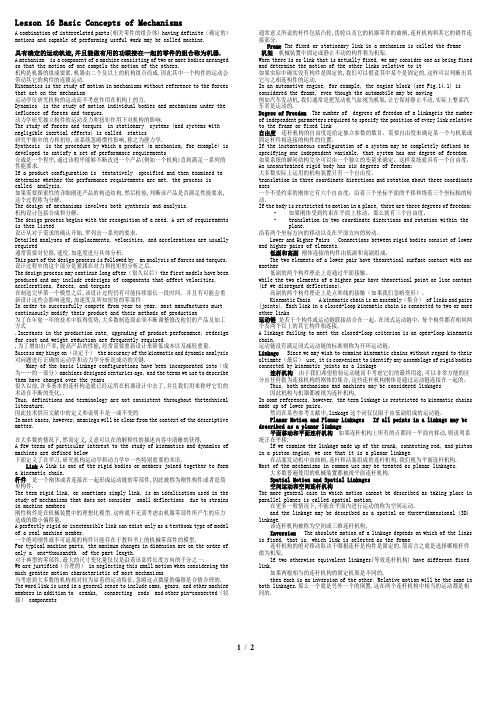
Lesson 16 Basic Concepts of MechanismsA combination of interrelated parts(相关零件的组合体) having definite(确定的)motions and capable of performing useful work may be called machine.具有确定的运动轨迹,并且能做有用的功联接在一起的零件的组合称为机器.A mechanism is a component of a machine consisting of two or more bodies arranged so that the motion of one compels the motion of the others.机构是机器的组成要素.机器由二个及以上的机构组合而成.因此其中一个构件的运动会带动其它的构件的连锁运动.Kinematics is the study of motion in mechanisms without reference to the forces that act on the mechanism运动学仅研究机构的运动而不考虑作用在机构上的力.Dynamics is the study of motion individual bodies and mechanisms under the influence of forces and torques.动力学研究独立构件的运动及力和扭矩作用下对机构的影响.The study of forces and torques in stationary systems (and systems with negligible inertial effects) is called statics研究平衡中的力和扭矩,该系统忽略惯性影响,称之为静力学.Synthesis is the procedure by which a product (a mechanism, for example) is developed to satisfy a set of performance requirements合成是一个程序,通过该程序能够不断改进一个产品(例如一个机构)直到满足一系列的性能要求.If a product configuration is tentatively specified and then examined to determine whether the performance requirements are met, the process is called analysis.如果需要探索性的详细阐述产品的构造结构,然后检验,判断该产品是否满足性能要求,这个过程称为分解.The design of mechanisms involves both synthesis and analysis.机构设计包括合成和分解.The design process begins with the recognition of a need. A set of requirements is then listed设计从对于需求的确认开始,罗列出一系列的要求.Detailed analyses of displacements, velocities, and accelerations are usually required通常需要对位移,速度,加速度进行具体分析.This part of the design process is followed by an analysis of forces and torques. 设计过程中的这个部分是紧跟在对力和扭矩的分析之后.The design process may continue long after(很久以后)the first models have been produced and may include redesigns of components that affect velocities, accelerations, forces, and torques在制造完毕第一个模型之后,该设计过程仍有可能持续很长一段时间. 并且有可能会重新设计这些会影响速度,加速度及所知扭矩的零部件In order to successfully compete from year to year, most manufactures must continuously modify their product and their methods of production为了在年复一年的技术中取得优势,大多数制造商必须不断调整修改他们的产品及加工方式.Increases in the production rate, upgrading of product performance, redesign for cost and weight reduction are frequently required,为了增加出产率,提高产品的性能,经常需要重新设计来降低成本以及减轻重量. Success may hinge on(决定于) the accuracy of the kinematic and dynamic analysis 对问题进行正确的运动学和动力学分析是成功的关键.Many of the basic linkage configurations have been incorporated into(成为……的一部分)machines designed centuries ago, and the terms we use to describe them have changed over the years很久以前,许多基本的连杆构造就已经运用在机器设计中去了,并且我们用来称呼它们的术语在不断的变化,.Thus, definitions and terminology are not consistent throughout thetechnical literature.因此技术供应文献中的定义和说明不是一成不变的In most cases, however, meanings will be clear from the context of the descriptive matter.在大多数的情况下,然而定义,义意可以在的解释性的描述内容中清晰的获得,A few terms of particular interest to the study of kinematics and dynamics of machines are defined below下面定义了在学习,研究机构运动学和动力学中一些特别重要的术语.Link A link is one of the rigid bodies or members joined together to form a kinematic chain.杆件是一个刚体或者连接在一起形成运动链的零部件,因此被称为刚性构件或者是简单构件.The term rigid link, or sometimes simply link, is an idealization used in the study of mechanisms that does not consider small deflections due to strains in machine members刚性构件是在机械装置中的理想化模型.这样就不无需考虑由机器零部件所产生的应力造成的微小偏移量.A perfectly rigid or inextensible link can exist only as a textbook type of model of a real machine member.一个绝对刚性或不可延展的构件只能存在于教科书上的机械零部件的模型.For typical machine parts, the maximum changes in dimension are on the order of only a one-thousandth of the part length.对于典型的零部件,最大的尺寸变化量仅仅是沿着该部件长度方向的千分之一.We are justified(合理的) in neglecting this small motion when considering the much greater motion characteristic of most mechanisms当考虑到大多数的机构相对较为显着的运动特征,忽略这点微量的偏移是合情合理的. The word link is used in a general sense to include cams, gears, and other machine members in addition to cranks, connecting rods and other pin-connected(铰接) components通常意义所说的杆件包括凸轮,齿轮以及它的机器零件的曲柄,连杆机构和其它的销件连接部分.Frame The fixed or stationary link in a mechanism is called the frame机架机械装置中固定或静止不动的构件称为机架.When there is no link that is actually fixed, we may consider one as being fixed and determine the motion of the other links relative to it如果实际中确实没有构件是固定的,我们可以假设其中某个是固定的,这样可以判断出其它与之相连构件的运动.In an automotive engine, for example, the engine block (see Fig.14.1) isconsidered the frame, even though the automobile may be moving例如汽车发动机,我们通常是把发动机气缸视为机架,让它保持静止不动,实际上整部汽车者是运动的.Degree of Freedom The number of degrees of freedom of a linkageis the number of independent parameters required to specify the position of every link relative to the frame or fixed link自由度连杆机构的自由度是给定独立参数的数目,需要自由度来确定某一个与机架或固定杆件相连接的构件的位置,If the instantaneous configuration of a system may be completely defined bespecifying one independent variable, that system has one degree of freedom如果系统的瞬间结构完全可以由一个独立的变量来确定,这样系统就具有一个自由度,An unconstrained rigid body has six degrees of freedom:大多数实际上运用的机构装置只有一个自由度。
- 1、下载文档前请自行甄别文档内容的完整性,平台不提供额外的编辑、内容补充、找答案等附加服务。
- 2、"仅部分预览"的文档,不可在线预览部分如存在完整性等问题,可反馈申请退款(可完整预览的文档不适用该条件!)。
- 3、如文档侵犯您的权益,请联系客服反馈,我们会尽快为您处理(人工客服工作时间:9:00-18:30)。
(2) Converting a turning pair into a sliding pair If the radius of the pin D is increased to a length of lDC, and the rocker 3 is made a slider with a curve which radius is lDC, then this mechanism becomes a curve slider crank mechanism shown in Fig 5-4b. If the lDC were made infinite in length, then point C would have rectilinear motion and link 3 could be replaced Fig.5-4 by a slider, as shown in Fig 5-4c.
r pivots A and B relative to the frame 2, this linkage is called a double rotating block
mechanism shown in Fig 5-3b. It can also be called Oldham linkage, and it is used to connect two shafts having parallel misalignment. (13)Sine linkage This linkage can also be called a Scotch yoke linkage, in which the crank 2 rotates about its pivot. Acompletely, and link 4 reciprocates in the fixed link 1 to produce a simple harmonic motion. It is shown in Fig 5-3c. (14)Tangent linkage In a tangent mechanism, the side link 2 oscillates about its pi
5.1 Characteristics and Types of Planar Linkages
1.The Characteristics of Planar Linkages
1) A linkage has a simple structure and it is easy to manufacture, so it has a low cost. 2) The pressure in a lower pair with surface contact is lower, so the linkage has a large load capacity. 3) A linkage can achieve various motions by designing its dimensio ns of the links.
Fig.5-3 Types of four-bar linkages with two sliding pairs (含有两个移动副的四杆机构类型)
3.Evolution and Mutation of Planar Linkages
(1)Inversion of a four bar linkage Different mechanisms can be obtained by fix ing different links of a mechanism. This is known as inversion. The principle is t hat the relative motion between links of a four bar linkage does not change in di
the coupler becomes a slider in shape.
(8) Rocking block linkage The crank rotates completely while the block only oscillat es about its pivot center C, this linkage is called rock block linkage shown in Fig 5-2c.
(6) Slider crank linkage This linkage is shown in Fig 5-2a, in which side link 1 is a cra nk, and the other side link 3 is a slider. Turning pairs A and B are full turning pairs, a nd C is oscillating turning pair. (7) Rotating guide bar linkage If both the side link 2 and side link 4 can rotate com pletely, this linkage is called a rotating guide bar linkage shown in Fig 5-2b, in which
It is widely used in hydraulic cylinder mechanism.
(9) Sliding guide bar linkage If the guide link 4 reciprocates along the axis of the fix ed block, and the other side link 2 oscillates about the pivot C, the linkage is called a
Evolution from turning r to sliding pair(转动副向移 动副的演化)
(3) Expansion of pin size in a turning pair If we increase the size of the crank pin B shown in Fig 5-5a until it is larger than the length of the crank, this enlarged crank pin is called an eccentric disk and can be used to replace the crank shown in Fig 5-5a. The crank consists of a circular disk with center B, which is pivoted off center at A to the frame. The disk rotates inside the ring end of coupler 2.
(11) Double slider crank linkage In a four bar linkage, if two side links 1 and 3 beco me sliders which are reciprocating along each axis of cross frame, and the two pairs
sliding guide bar linkage shown in Fig 5-2d. It can be used in some water pumps.
(10) Rocking guide bar linkage If the link 2 can rotates about pivot B completely, an d the link 4 oscillates about the pivot A shown in Fig 5-2e, this linkage is called a roc king guide bar linkage. It is used in machine tools such as shapers.
of the same kind are adjacent, it is known as a double slider crank linkage shown in
Fig 5-3a. This linkage can draw ellipses. (12) Double rotating block linkage If two sliders are rotating completely about thei
vot A, the other link 4 reciprocates along its axis, and the link 3 is a slider in shape. I
t is also called the Rapsons slide linkage. The displacement of link 4 has a tangent m otion.
4) A linkage can transmit motion within a long distance.
5) It is difficult to perform precision motion; this is a disadvantage of linkages.
2.Types of Planar Linkages
Fig.5-1 Types of four-bar linkages(铰链四杆机构的类型)
Fig.5-2 Types of four-bar linkages with a sliding pair(含有一个移动副的四杆机构 类型)
(1) Crank rocker linkage If a four bar linkage shown in Fig 5-1a is designed so that link 1 can rotate continuously while link 3 only oscillates through an angle, it is call ed a crank rocker linkage. (2) Double crank linkage Both link 2 and link 4 in Fig 5-1b can rotate continuously