材料成型工艺学-轧制原理与工艺基础
材料成型原理与工艺

04
材料成求极高,需要具备轻质、高强度、 耐高温等特性。材料成型原理与工艺的发展为航空航天领域 提供了更多的选择,如钛合金、复合材料等。
这些新型材料的应用有助于减轻飞机和航天器的重量,提高 其性能和安全性。
汽车工业领域的应用
随着环保意识的提高和新能源汽车的 兴起,汽车工业对轻量化材料的需求 越来越大。
件。
锻造工艺
01
02
03
04
自由锻造
利用自由锻锤或压力机对坯料 进行锻打,形成所需形状和尺
寸的锻件。
模锻
利用模具对坯料进行锻打,使 坯料在模具中形成所需形状和
尺寸的锻件。
热锻
将坯料加热至高温后进行锻打 ,使材料易于塑性变形。
冷锻
在常温下对坯料进行锻打,适 用于塑性较差的材料。
焊接工艺
熔化焊
压力焊
材料成型原理与工艺的发展使得汽车 零部件的制造更加高效、精确,如铝 合金、镁合金等轻质材料的广泛应用 ,有助于降低汽车能耗和排放。
能源领域的应用
能源领域如核能、太阳能等需要大量的特殊材料,如耐高 温、耐腐蚀的材料。
材料成型原理与工艺的进步为能源领域提供了可靠的材料 解决方案,如高温合金、耐腐蚀涂层等,有助于提高能源 利用效率和安全性。
材料成型原理与工艺
• 材料成型原理概述 • 材料成型工艺介绍 • 材料成型原理与工艺的发展趋势 • 材料成型原理与工艺的应用前景
01
材料成型原理概述
材料成型的基本概念
材料成型是通过物理或化学手 段改变材料的形状,以达到所 需的结构和性能的过程。
材料成型涉及多种工艺和技术, 如铸造、锻造、焊接、注塑等。
泡沫金属
通过在金属基体中引入孔洞,制备 出具有轻质、高比强度的泡沫金属 材料。
第二篇轧制工艺基础

d.采用铸锭的小型生产系统的工艺过程:其 特点是通常在中、小型轧机上用冷的小钢 锭经一次加热轧制成材。 所有采用铸锭的生产工艺都是落后的,已 经或将要遭到淘汰。 不管是哪种类型,其基本工序都是:原料 准备(清理)-加热-轧制-冷却精整处理。
合金钢生产工艺流程
• 可分为冷锭和热锭以及正在发展的连铸坯三种作 业方式。 • 由于对合金钢材的表面质量和物理机械性能等技 术要求比普通碳素钢高,并且钢种特性也较复杂, 故其生产工艺过程一般也比较复杂。 • 除各工序的具体工艺规程会因钢种不同而不同以 外,在工序上比碳素钢多出了原料准备中的退火、 轧制后的热处理、酸洗等工序,以及在开坯中有 时还要采用锻造来代替轧钢等。
2.型钢生产系统:规模往往并不很大。 大型:年产100万t以上; 中型:年产30万-100万t; 小型:年产30万t以下。 3.混合生产系统: 在一个钢铁企业中可同时生产板 带钢、型钢或钢管时,称为混合系统。 • 无论在大型、中型或小型的企业中,混合系统都 比较多,其优点是可以满足多品种的需要。 • 但单一的生产系统却有利于产量和质量的提高。
钢材的冷加工生产工艺流程
• 钢材的冷加工生产工艺流程包括冷轧和冷 拔。 • 其特点是必须有加工前的酸洗和加工后的 退火相配合,以组成冷加工生产线。
有色金属(铜、铝等)及其合金轧 材生产系统及工艺流程
• 铜、铝及其合金的轧材应用比较广泛,其生产系 统规模却不大,一般是以重金属和轻金属分别自 成系统进行生产的,在产品品种上多是板带材、 型线材及管材等相混合,在加工方法上多是轧制、 挤压、拉拔等相混合,以适应于批量小,品种多 及灵活生产的特点和要求。 • 但也有专业化生产的工厂,例如电缆厂、铝箔厂、 板带材厂等。 • 有色金属及合金的轧材主要是板带材,至于型材、 管材乃至棒材则多用挤压及拉拔的方法生产。
(金属轧制工艺学)2轧制工艺基础

2020/10/4
11
碳素钢加工特性
➢ 钢的塑性一方面取决于金属本身,这主要是与组织 结构中变形的均匀程度,即与组织中相的分布、晶 界杂质的形态与分布等有关,同时也与钢的再结晶 温度有关,再结晶开始温度高、再结晶速度慢,往 往使钢的塑性变差。
➢ 另一方面,塑性还与变形条件,即与变形温度、变 形速度、变形程度及应力状态有关,其中变形温度 的影响最大,故必须了解塑性与温度的变化规律, 掌握适宜ቤተ መጻሕፍቲ ባይዱ热加工温度范围。
➢ 当高温时,由于合金钢一般熔点都较低,因而合金 钢变形抗力可能大为降低,例如,高碳钢、硅钢等 在高温时甚至比低碳钢还要软。
2020/10/4
13
碳素钢加工特性
(3)导热系数
➢随着钢中合金元素和杂质含量的增多,导热 系数几乎没有例外地都要降低。
➢钢的导热系数还随温度而变化,一般是随温 度升高而增大,但碳钢在大约800℃以下是随 温度升高而降低的。
➢ 此外,在较低的变形速度下轧制,或采用三向压应 力较强的变形过程,如采用限制宽度和包套轧制等, 都有利于金属塑性的改善。
2020/10/4
12
碳素钢加工特性
(2)变形抗力
➢ 一般地说,有色金属及合金的变形抗力比钢的要低, 随着合金含量的增加,变形抗力将提高。
合金元素尤其是碳、硅等元素的增加使铁素体强 化。合金元素,尤其是形成稳定碳化物的元素, 在钢中一般都能使奥氏体晶粒细化,使钢具有较 高的强度。合金元素还通过影响钢的熔点和再结 晶温度与速度,通过相的组成及化合物的形成, 以及通过影响表面氧化铁皮的特性等来影响变形 抗力。
轧制理论与工艺
Rolling Theory and Technology
第二篇 轧制工艺基础 Foundations of rolling technology
棒材工艺轧制原理

• 热轧生产线:热轧生产线主要包括加热炉、轧机、冷却设备等 • 冷轧生产线:冷轧生产线主要包括矫直机、剪切机、冷床等 • 在线轧制生产线:在线轧制生产线主要包括连轧机、飞剪、卷取机等
棒06材工艺轧制技术的发展与展 望
棒材工艺轧制技术的 最新进展
• 棒材工艺轧制技术的最新进展 • 高性能轧制技术:通过优化轧制工艺,提高金属的力学性能和 表面质量 • 智能化轧制技术:利用计算机技术和传感器技术,实现轧制过 程的自动化和智能化 • 环保节能轧制技术:通过优化生产工艺和设备,降低能源消耗 和环境污染
棒材工艺轧制技术的未来挑战
• 技术难题:解决棒材工艺轧制过程中的技术难题,提高 产品质量和生产效率 • 市场竞争:应对市场竞争,提高棒材工艺轧制技术的竞 争力和市场份额
THANK YOU FOR WATCHING
谢谢观看
棒材工艺轧制的基本原理及其影响因素
棒材工艺轧制的基本原理
• 金属在塑性变形过程中的晶格位错和滑移 • 通过改变金属的晶粒形状和晶粒大小来实现塑性变形
棒材工艺轧制的影响因素
• 轧制温度:影响金属的塑性和流动性 • 轧制速度:影响金属的变形速度和冷却速度 • 轧制压力:影响金属的变形程度和密度 • 轧制间隙:影响金属的变形均匀性和表面质量
轧制间隙的调整
• 自动调整:通过自动控制系统实时调整轧制间隙 • 手动调整:根据轧制过程中的实际情况手动调整轧制间 隙
棒03材工艺轧制过程中的组织性 能变化
轧制过程中的微观组织演变
金属在轧制过程中的微观组织变化
• 晶粒形状和大小的变化:轧制过程中晶粒逐渐拉长,晶 粒大小减小 • 晶格位错和滑移的产生:轧制过程中晶格位错和轧制技术的发展趋势 • 高生产效率:提高轧制速度,提高生产效率,降低生产成本 • 高质量:提高金属的力学性能和表面质量,满足市场需求 • 环保节能:降低能源消耗和环境污染,实现可持续发展
材料成形工艺学轧制理论前滑

口断面速度的关系为:
忽略宽展,则
vx
Fh Fx
vh
vx
Fh Fx
vh
hhbh hxbx
vh
hh hx
vh
中性面上的速度和出口断面
速度的关系为:
v
Fh F
vh
忽略宽展,则
2020/4/23
v
Fh F
vh
hhbh h by
vh
hh h
vh
12
4.3 平辊轧制时中性角的确定
中性角:
中性面所对应的角为中性角,在 此面上轧件运动速度与轧辊线速度 的水平分速度相等。
2020/4/23
6
3)前滑值的实验测定
❖ 如果事先在轧辊 表面上刻出距离 为LH 的两个小坑
则轧制后测量 Lh
➢即可用实验方 法计算出轧制时 的前滑值。
2020/4/23
7
4.1.2 前后滑与有关工艺参数的关系
❖ 1)体积不变定律
❖ 按秒流量体积相等的条件
BHL bhl l BH FH L bh Fh
v
h
h
Sh
vh v v
vh v
1
Sh
h cos
D(1 cos ) cos
h
1
D(1 cos ) cos h(1 cos )
h
前滑值:
Sh
(D cos
h)(1 cos )
h
2020/4/23
19
前滑值:
Sh
(D cos
h)(1 cos )
h
影响前滑值的工艺参数为轧辊直径,轧件厚度,中性角
2020口/4/2两3 方向流动的结果
4
❖ (1)后滑:轧件进入轧辊的速度υH小于 轧辊在该点处线速度 υ 的水平分量 υcosα,这种现象叫做后滑。
材料成形工艺学-轧制理论-前滑2
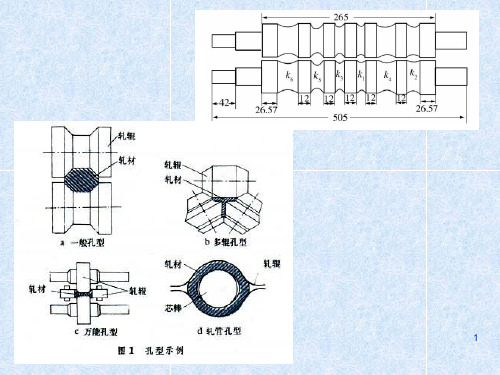
t x = fp x
积分后得到中性角公式:
sin α 1 − cos α Q1 − Q0 sin γ = − + 2 2f 4 pf b R
2011-1-2 14
前后张力相等或无前后张力时,则
sin α 1 − cos α sin γ = − 2 2f
α角很小时
1 − cos α = 2 sin
2
2011-1-2 2
剩余摩擦力的概念
轧件从开始咬入到轧制建成的过 程中,有利于轧件咬入的水平分力 Tx不断增加,而阻碍轧件咬入的水 平分力Nx不断减小,Tx-Nx的差值 愈来愈大,也就是咬入过程所要求 的靠摩擦作用的曳入力愈来愈富余。
cos ϕ
剩余摩擦力Ts Ts = Tx − N x = Nf cos ϕ − N sin ϕ
2011-1-2 23
4 影响前滑的因素
生产实践表明,影响前滑的因素很多。 归纳起来主要因素有: 压下率 轧件厚度 轧件宽度 辊径 摩擦系数 张力等等。
2011-1-2 24
1)压下率的影响
由实验曲线可见,前滑随压 , 下率的增而增, 下率的增而增,其原因是由 于压下率增加,延伸系数增 加。 当∆h=常数时,前滑增加非 常显著。咬入角不变,故前 滑有显著增加。 当 h= 常数时或H=常数时, 压下率的增加,延伸必然增 加,但这是因 ∆h 增加,所 以咬入角增大,故剩余摩擦 力减小, 两个因素的联合作用,使前 滑虽有所增加,但没有∆h= 常数时增加的显著。
轧制变形与工艺基础

第一节 轧制变形基本原理1、金属的塑性变形与弹性变形1.1 影响金属热塑性变形的主要因素影响金属热塑性变形的因素,有金属本身内部因素和加热等外部条件。
1) 钢中存在碳及其他合金元素,使钢的高温组织,除有奥氏体外,还有其他过剩相。
这些过剩相降低钢的塑性。
钢中的杂质也是影响金属热塑性变形的内在因素,钢中的硫能使钢产生热脆。
2)影响热轧时塑性变形的外部条件有加热介质和加热工艺,对碳钢而言,当变形条件相同时,变形金属的化学成分及组织结构不同,温度对塑性的影响也不同,如图1-2-1。
图中I 、II 、III 、IV 表示塑性降低区域(凹谷);1、2、3表示塑性增高区域(凸峰)。
I 区中钢的塑性很低;II 区(200-400℃)——“蓝脆”区中,钢的强度高而塑性低;III 区(850-950℃)——相变温度区又称“热脆”区,钢通常一个相塑性好,另一个相塑性较差;IV 区接近于钢的熔化温度,钢在该区加热时易发生过热或过烧,这时钢塑性最低。
所以,碳素钢热加工时的最有利的温度范围是1000-1250℃。
对合金钢而言,加热介质尤为重要。
镍含量达2-3%以上的合金钢,在含硫气氛中加热时,硫会扩散到金属中,并在晶界上形成低熔点的Ni 3S 2化合物,因而降低了金属的塑性。
含铜超过0.6%的钢,有时甚至是含铜0.2-0.3%的钢,如在强氧化气氛中较长时间的高温加热时,由于选择性氧化的结果,在钢的表面氧化铁皮下会富集一薄层熔点低于1100℃的富铜合金,这层合金在1100℃时熔化并侵蚀钢的表面层,使钢在热轧加工时开裂。
3)热轧温度选择不合适,也会给金属带来不良的影响。
当终轧温度过高时,往往会造成金属的晶粒粗大;若终轧温度过低时,又会造成晶粒沿加工方向伸长的组织,并有一定的加工硬化。
在这两种情况下,金属的性能都会变坏。
所以,合理控制金属的热轧温度范围,对获得所需要的金属组织和性能,具有重要意义。
1.2 金属的弹性变形金属晶格在受力时发生歪扭或拉长,当外力未超过原子之间的结合力时,去掉外力之后晶格便会由变形的状态恢复到原始状态,也就是说未超过金属本身弹性极限的变形叫金属的弹性变形。
(金属轧制工艺学)1轧制工艺基础
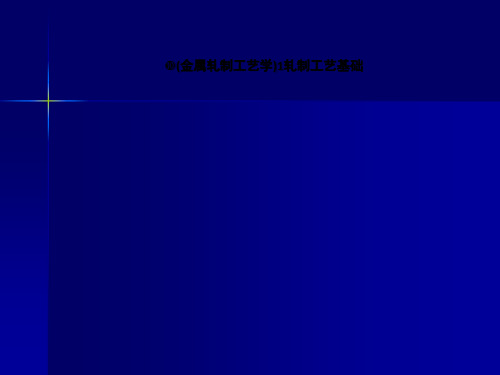
2020/7/22
24
型钢生产系统
型钢生产系统的规模往往并不很大。就 其本身规模而言又可分为大型、中型和 小型三种生产系统。
➢一般年产100万t以上的可称为大型的系统; ➢年产30万t~100万t的为中型的系统; ➢年产30万t以下的可称为小型的系统。
2020/7/22
25
混合生产系统
在一个钢铁企业中可同时生产板带钢、 型钢或钢管时,称为混合系统。
现代化的轧钢生产系统向着大型化、连续化、 自动化的方向发展,生产规模日益增大。
近年来大型化的趋向已日见消退,而投资省、 收效快、生产灵活且经济效益好的中、小型钢 厂在很多国家中却有了较快的发展。
2020/7/22
27
碳素钢的生产工艺流程
碳素钢生产工艺流程一般可分4个基本类型:
➢(1)采用连铸坯的工艺过程
➢按用途来分:
常用型钢(方钢、圆钢、扁钢、角钢、槽钢、 工字钢等)和专用型钢(钢轨、钢桩、球扁钢、 窗框钢等)。
➢按其断面形状:
简单断面型钢和复杂或异型断面型钢。
2020/7/22
9
轧材种类
型线材
➢按生产方法:
轧制型钢、弯曲型钢、焊接型钢。
➢用纵轧、横旋轧或楔横轧等特殊轧制方法 生产的各种周期断面或特殊断面钢材,又 分为:
28
碳素钢的生产工艺流程
➢ (3)采用铸锭的中型生产系统的工艺过程
其特点是:一般有Ø650~Ø900二辊或三辊开坯机,通常 采用冷锭作业及二次(或一次)加热轧制方式,这种工艺 流程不仅用来生产碳素钢材,也常用以生产合金钢材。
➢ (4)采用铸锭的小型生产系统的工艺过程
其特点是:通常在中、小型轧机上用冷的小钢锭经一次 加热轧制成材。所有采用铸锭的生产工艺都是落后的, 已经或将要遭到淘汰。
- 1、下载文档前请自行甄别文档内容的完整性,平台不提供额外的编辑、内容补充、找答案等附加服务。
- 2、"仅部分预览"的文档,不可在线预览部分如存在完整性等问题,可反馈申请退款(可完整预览的文档不适用该条件!)。
- 3、如文档侵犯您的权益,请联系客服反馈,我们会尽快为您处理(人工客服工作时间:9:00-18:30)。
z型钢:棒线材无头轧制 z特点:连续生产,提高成材率,简化控制系
统,提高产品质量
2007年10月24日 5
材料成形工艺学(中)——轧制原理
绪 论
5. 采用柔性化的轧制技术
z多品种,小批量,短交货期 → 柔性化轧
制技术:
z热轧自由程序轧制技术 z型钢自由程序轧制:无孔型平辊轧制(H 型钢延伸机组) 成品孔,成品前孔共用
2007年10月24日
ห้องสมุดไป่ตู้
23
材料成形工艺学(中)——轧制原理
1 轧制过程的基本概念
1.1 变形区基本参数
1.1.2 轧制变形的表示方法
1.1.2.1 相对变形量
H −h 100 % H b−B 100 % B l−L 100% L
H −h 100 % h b−B 100 % b l−L 100% l
ADB、CEG 流动产生宽展 变形区 横向流动
2007年10月24日
30
材料成形工艺学(中)——轧制原理
1 轧制过程的基本概念
1.2 金属在变形区内的流动规律
1.2.2 沿轧制宽度方向上的流动规律
l h
较大时(薄轧件),受表面外摩擦影响,出现单鼓变形
lh
<0.5时(厚轧件),变形不能深透到整个断面高度,出现双鼓变形
2
B1 B3
2
的平方
B1C = 2 R B1 B3
如图
18
2007年10月24日
材料成形工艺学(中)——轧制原理
1 轧制过程的基本概念
Δh DB3 = + Δ1 + Δ 2 2
B1 B3 = Δ1 + Δ 2
l ' = x1 + x0 = A2 D + B1C
;
= RΔh + 2 R(Δ1 + Δ 2 ) + 2 R(Δ1 + Δ 2 )
如图
2007年10月24日 19
材料成形工艺学(中)——轧制原理
1 轧制过程的基本概念
x0 = 2 R(Δ1 + Δ 2 )
2 l ' = RΔh + x0 + x0
如图
2007年10月24日 20
材料成形工艺学(中)——轧制原理
1 轧制过程的基本概念
1 − ν 12 Δ 1 = 2q πE1
2 1 −ν 2 Δ 2 = 2q πE 2
2007年10月24日
变形区任意断面高度
= H − D(cos α x − cos α )
= H − [D(1 − cos α ) − D(1 − cos α x )]
13
材料成形工艺学(中)——轧制原理
1 轧制过程的基本概念
1.1.1 轧制变形区及其主要参数 1.1.1.2 接触弧长(l )
接触弧长:轧件与轧辊接触的圆弧的水平投影长度
2007年10月24日
变形区 横向流动
31
Δ1-轧辊弹性压缩量 Δ2-轧件弹性压缩量
返回
返回
a)金属流动速度分布: 1、6—外端;2、5—变形 过渡区;3—后滑区;4—前 滑区
( (b)应力分布: A—A—入辊平面;B—B—出 辊平面
l h < 0.5 ~ 1.0 时金属流动速度与应力分布
返 回
2007年10月24日 3
材料成形工艺学(中)——轧制原理
绪 论
3. 提高连铸比,大力推广连铸— 连轧工 艺及短流程技术
节能,提高成材率及产品质量
短流程:薄板坯连铸连轧 异型坯 管坯连铸等
2007年10月24日 4
材料成形工艺学(中)——轧制原理
绪 论
4. 轧制过程连续化的新进展——无头轧制技术 z板带无头轧制:
变形不能深透,表面变形>中间变形 变形区形状系数 实验
2007年10月24日
柯尔巴什尼柯夫 实验
29
材料成形工艺学(中)——轧制原理
1 轧制过程的基本概念
1.2 金属在变形区内的流动规律
1.2.2 沿轧制宽度方向上的流动规律 最小阻力定律:金属沿流动阻力最小的方向流动
变形区分四个部分
{
ADGC、BDCG 流动产生延伸
2007年10月24日 6
材料成形工艺学(中)——轧制原理
绪 论
6. 轧制过程的自动控制和智能控制
z自动控制:产品质量监督和控制,提高质
量,降低成本,增加效率。
z人工智能:过程诊断,优化,控制,信息
处理
2007年10月24日
7
材料成形工艺学(中)——轧制原理
绪 论
7. 深加工
z涂镀,裁剪,切分,焊接,冷弯,机械加
'
2007年10月24日 17
材料成形工艺学(中)——轧制原理
1 轧制过程的基本概念
A2 D =
忽略
A2 O − OB3 − DB3
DB3 的平方
2
2
2
(
)
2
= R 2 − (R − DB3 )
2
A2 D = 2 R DB3
B1C = CO − OB3 − B1 B3
忽略
(
)
2
= R 2 − (R − B1 B3 )
2 ⎛ 1 −ν 12 1 −ν 2 ⎞ x0 = 8R p⎜ ⎜ πE + πE ⎟ ⎟ 1 2 ⎠ ⎝
q —压缩圆柱体单位长度上的压力, q = 2 x0 p
,
p
—平均单位压力
ν 1 ,ν 2
E1 , E 2
2007年10月24日
—轧辊和轧件的泊桑系数; —轧辊和轧件的弹性摸量 如图
21
材料成形工艺学(中)——轧制原理
Δh Δh α 1 Δh 2α - ⇒1 − 2sin = cosα= 1 1 − ⇒ sin = D 2 D 2 2 R
当α很小时取 sin
α
2
≈
α
2
Δh α= R
12
2007年10月24日
材料成形工艺学(中)——轧制原理
1 轧制过程的基本概念
1.1.1 轧制变形区及其主要参数
hx = H − (Δh − Δhx ) hx = Δhx + h = D(1 − cos α x ) + h
l = 2 R1 Δh1 = 2 R2 Δh2
Δh = Δh1 + Δh2
2007年10月24日
l=
2 R1 R2 Δh R1 + R2
15
材料成形工艺学(中)——轧制原理
1 轧制过程的基本概念
1.1.1 轧制变形区及其主要参数 1.1.1.2 接触弧长(l )
(3)轧辊和轧件产生弹性压缩时的接触弧长
按不均匀变形理论金属流动速度和应力分布 (a)金属流动速度分布:1—表面层金属流动速度;2—中心层金属流动速度;3—平 均流动速度;4—后外端金属流动速度;5—后变形过渡区金属流动速度;6—后滑区 金属流动速度;7—临界面金属流动速度;8—前滑区金属流动速度;9—前变形过渡 区金属流动速度10—前外端金属流动速度 (b)应力分布:+—拉应力;-—压应力;1—后外端;2—入辊处;3—临界面;4—出 辊处;5—前外端 返回
h ln H b ln B l ln L
24
2007年10月24日
材料成形工艺学(中)——轧制原理
1 轧制过程的基本概念
1.1 变形区基本参数
1.1.2 轧制变形的表示方法
1.1.2.1 变形系数表示
压下系数
H η= h
η = μ•β
体积不变定律
2007年10月24日
宽展系数
延伸系数
b β= B l μ= L
25
材料成形工艺学(中)——轧制原理
1 轧制过程的基本概念
1.2 金属在变形区内的流动规律
1.2.1 轧制断面高向上变形的分布
均匀变形理论(刚端理论) 不符合实际 不均匀变形理论:比较符合实际
不均运变形速度 图 和应力分布
2007年10月24日
26
材料成形工艺学(中)——轧制原理
1 轧制过程的基本概念
1 轧制过程的基本概念
1.1 变形区基本参数 简单轧制过程:
上下轧辊直径相等,转速相同,且均为主动辊、 轧制过程对两个轧辊完全对称、轧辊为刚性、轧 件除受轧辊作用外,不受其他任何外力作用、轧 件在入辊处和出辊处速度均匀、轧件的机械性质 均匀
2007年10月24日 10
材料成形工艺学(中)——轧制原理
2007年10月24日
1
材料成形工艺学(中)——轧制原理
绪 论
一、大力开发高精度轧制技术
外形尺寸——产品的最基本条件 板带:厚度,宽度,板形,版凸度,平面形状 AGC-Automatic Gauge Control 板形控制:配辊,配辊型曲线,轧制负荷分配,液压弯辊技术 控制板形的轧机: CVC-Continuously variable Crown PC-Pair Cross HC(W)-High Crown (Working roll shift) DSR-Dynamic Shape Roll
不均运变形速度图 和应力分布
2007年10月24日
27
材料成形工艺学(中)——轧制原理
1 轧制过程的基本概念
1.2 金属在变形区内的流动规律
1.2.1 轧制断面高向上变形的分布
不均匀变形理论 塔尔诺夫斯基 实验
(1)入口处 表面变形>中心变形 表层流动快,变形不均; (2)曲线1、2交点是临界面位置,在此面上,金属流动和变形均匀 (3)出口侧 中心变形>表面变形 中心层流动快; (4)曲线1水平段——粘着区 (5)存在变形过渡区,过渡区内变形也不均匀。 塔尔诺夫斯基 实验