高压扭转处理后铝铁界面微观组织及性能研究
《高压扭转工艺对Al-Zn-Mg-Cu合金组织与性能的研究》范文
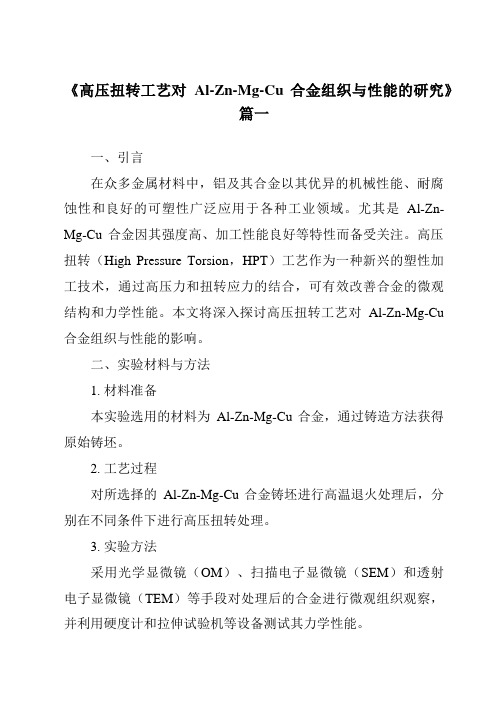
《高压扭转工艺对Al-Zn-Mg-Cu合金组织与性能的研究》篇一一、引言在众多金属材料中,铝及其合金以其优异的机械性能、耐腐蚀性和良好的可塑性广泛应用于各种工业领域。
尤其是Al-Zn-Mg-Cu合金因其强度高、加工性能良好等特性而备受关注。
高压扭转(High Pressure Torsion,HPT)工艺作为一种新兴的塑性加工技术,通过高压力和扭转应力的结合,可有效改善合金的微观结构和力学性能。
本文将深入探讨高压扭转工艺对Al-Zn-Mg-Cu合金组织与性能的影响。
二、实验材料与方法1. 材料准备本实验选用的材料为Al-Zn-Mg-Cu合金,通过铸造方法获得原始铸坯。
2. 工艺过程对所选择的Al-Zn-Mg-Cu合金铸坯进行高温退火处理后,分别在不同条件下进行高压扭转处理。
3. 实验方法采用光学显微镜(OM)、扫描电子显微镜(SEM)和透射电子显微镜(TEM)等手段对处理后的合金进行微观组织观察,并利用硬度计和拉伸试验机等设备测试其力学性能。
三、高压扭转工艺对组织的影响1. 晶粒结构变化高压扭转处理后,Al-Zn-Mg-Cu合金的晶粒尺寸明显减小,呈现出更为细小的晶粒结构。
这有利于提高合金的强度和韧性。
2. 微观结构变化高压扭转过程中,合金内部出现大量的位错和亚晶界,这些位错和亚晶界的形成有助于提高合金的塑性和抗疲劳性能。
此外,合金中第二相粒子的分布也变得更加均匀,有利于提高合金的力学性能。
四、高压扭转工艺对性能的影响1. 硬度变化经过高压扭转处理后,Al-Zn-Mg-Cu合金的硬度显著提高。
这主要归因于晶粒细化、位错和亚晶界的形成以及第二相粒子的均匀分布等因素的综合作用。
2. 拉伸性能变化高压扭转处理后,合金的抗拉强度和延伸率均有所提高。
这表明高压扭转工艺能够有效地改善合金的塑性和韧性。
此外,经过高压扭转处理的合金在拉伸过程中表现出更好的均匀变形行为。
五、讨论与展望通过对Al-Zn-Mg-Cu合金进行高压扭转处理,我们发现该工艺能够显著改善合金的微观结构和力学性能。
《热机械处理2197铝锂合金的微观组织及性能研究》范文
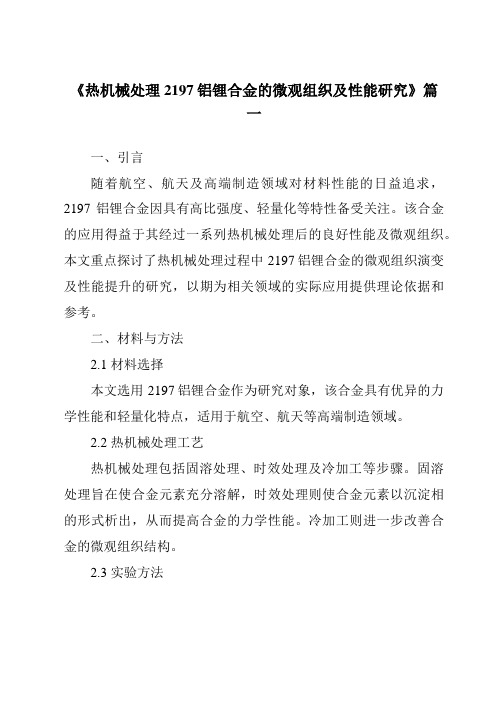
《热机械处理2197铝锂合金的微观组织及性能研究》篇一一、引言随着航空、航天及高端制造领域对材料性能的日益追求,2197铝锂合金因具有高比强度、轻量化等特性备受关注。
该合金的应用得益于其经过一系列热机械处理后的良好性能及微观组织。
本文重点探讨了热机械处理过程中2197铝锂合金的微观组织演变及性能提升的研究,以期为相关领域的实际应用提供理论依据和参考。
二、材料与方法2.1 材料选择本文选用2197铝锂合金作为研究对象,该合金具有优异的力学性能和轻量化特点,适用于航空、航天等高端制造领域。
2.2 热机械处理工艺热机械处理包括固溶处理、时效处理及冷加工等步骤。
固溶处理旨在使合金元素充分溶解,时效处理则使合金元素以沉淀相的形式析出,从而提高合金的力学性能。
冷加工则进一步改善合金的微观组织结构。
2.3 实验方法通过金相显微镜、扫描电镜、透射电镜等手段观察合金的微观组织结构;采用硬度计、拉伸试验机等设备测试合金的力学性能;结合热力学软件对合金的热处理过程进行模拟分析。
三、结果与讨论3.1 微观组织结构经过热机械处理后,2197铝锂合金的微观组织结构发生了显著变化。
固溶处理使合金元素充分溶解,形成均匀的固溶体;时效处理过程中,合金元素以沉淀相的形式析出,形成强化相;冷加工则使合金晶粒细化,提高材料的力学性能。
3.2 力学性能经过热机械处理后,2197铝锂合金的硬度、抗拉强度和延伸率均得到显著提高。
其中,固溶处理使合金硬度提高,时效处理使合金的抗拉强度达到峰值,冷加工则进一步提高延伸率。
此外,热机械处理还能改善合金的疲劳性能和抗腐蚀性能。
3.3 模拟分析通过热力学软件对2197铝锂合金的热处理过程进行模拟分析,结果表明:合理的热机械处理工艺参数可以有效地促进合金元素在固溶体中的溶解和沉淀相的析出,从而改善合金的微观组织结构和力学性能。
此外,模拟分析还为优化热机械处理工艺提供了理论依据。
四、结论本文通过对2197铝锂合金进行热机械处理,研究了其微观组织演变及性能提升。
纯铁、Q235钢和5083铝合金深冷冲击微结构演变与力学性能研究

纯铁、Q235钢和5083铝合金深冷冲击微结构演变与力学性能研究相较于传统粗晶材料,超细晶材料具有更为优异的力学性能和应用前景。
强烈塑性变形法,如等通道转角挤压和高压扭转,可制备较大尺寸的全致密超细晶块体材料。
相较于常见的强烈塑性变形法,大载荷冲击法设备简单、操作便捷,并且可以有效细化晶粒。
本文采用光学显微镜(OM)、透射电子显微镜(TEM)、背散射电子衍射(EBSD)、X射线衍射(XRD)和力学性能测试等手段研究大载荷冲击和热处理对体心立方结构工业纯铁、Q235B碳素结构钢和面心立方结构5083铝合金微结构以及力学性能的影响,结论如下:(1)深冷大载荷冲击工业纯铁内部产生高密度位错形成位错胞等,晶粒细化机制主要为位错滑移细化和晶粒破碎细化,抗拉强度提高75.6%,而塑性和韧性有所降低。
580℃退火时发生再结晶,板条状渗碳体球化。
球化渗碳体有一定弥散强化作用且较板条状渗碳体其塑性更好,因此材料具有高强韧特性。
620℃退火时强度、塑形和韧性均优于原材料,分别提高8.13%、15.5%和215.7%。
(2)深冷大载荷冲击Q235B钢颗粒直径由25μm细化至8μm,内部存在高密度位错,相互缠结堆积形成位错胞或者位错墙,晶粒细化机制与工业纯铁相同。
深冷和常温大载荷冲击Q235B钢抗拉强度提高64.6%,塑性和韧性有所降低。
由于深冷抑制动态回复,造成深冷冲击试样内部位错密度、晶粒细化程度更高,所以深冷冲击强化效果优于常温冲击。
(3)深冷大载荷冲击5083铝合金基体析出更多第二相,弥散强化增强,同时内部产生较多位错,形成纳米尺度第二相以及台阶状晶界阻碍位错运动,其细化机制主要为位错滑移细化,抗拉强度提高38.4%,塑性和韧性降低。
深冷大载荷冲击5083铝合金在200℃-250℃退火时,较多第二相在晶界析出,抗拉强度降低,塑形和韧性提高。
350℃退火时,第二相析出减少,弥散增强效果减弱,塑性和韧性明显增强,强度和塑性优于原材料,分别提高8.68%和70.68%。
《高压扭转工艺对Al-Zn-Mg-Cu合金组织与性能的研究》范文
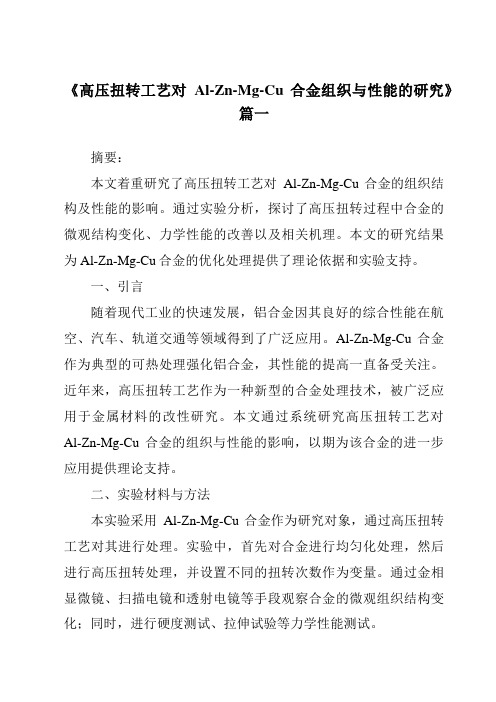
《高压扭转工艺对Al-Zn-Mg-Cu合金组织与性能的研究》篇一摘要:本文着重研究了高压扭转工艺对Al-Zn-Mg-Cu合金的组织结构及性能的影响。
通过实验分析,探讨了高压扭转过程中合金的微观结构变化、力学性能的改善以及相关机理。
本文的研究结果为Al-Zn-Mg-Cu合金的优化处理提供了理论依据和实验支持。
一、引言随着现代工业的快速发展,铝合金因其良好的综合性能在航空、汽车、轨道交通等领域得到了广泛应用。
Al-Zn-Mg-Cu合金作为典型的可热处理强化铝合金,其性能的提高一直备受关注。
近年来,高压扭转工艺作为一种新型的合金处理技术,被广泛应用于金属材料的改性研究。
本文通过系统研究高压扭转工艺对Al-Zn-Mg-Cu合金的组织与性能的影响,以期为该合金的进一步应用提供理论支持。
二、实验材料与方法本实验采用Al-Zn-Mg-Cu合金作为研究对象,通过高压扭转工艺对其进行处理。
实验中,首先对合金进行均匀化处理,然后进行高压扭转处理,并设置不同的扭转次数作为变量。
通过金相显微镜、扫描电镜和透射电镜等手段观察合金的微观组织结构变化;同时,进行硬度测试、拉伸试验等力学性能测试。
三、高压扭转工艺对Al-Zn-Mg-Cu合金组织的影响1. 微观结构观察通过金相显微镜、扫描电镜和透射电镜的观察,发现随着高压扭转次数的增加,Al-Zn-Mg-Cu合金的晶粒尺寸逐渐减小,晶界更加清晰,晶内亚结构更加明显。
这表明高压扭转工艺能够有效地细化合金的晶粒,改善其微观结构。
2. 第二相分布高压扭转工艺对Al-Zn-Mg-Cu合金中的第二相分布也有显著影响。
随着扭转次数的增加,第二相颗粒更加均匀地分布在基体中,这有利于提高合金的力学性能。
四、高压扭转工艺对Al-Zn-Mg-Cu合金性能的影响1. 硬度测试通过对合金进行硬度测试发现,随着高压扭转次数的增加,Al-Zn-Mg-Cu合金的硬度逐渐提高。
这主要是由于合金晶粒的细化以及第二相的均匀分布,使得合金的硬度得到提高。
《热机械处理2197铝锂合金的微观组织及性能研究》范文
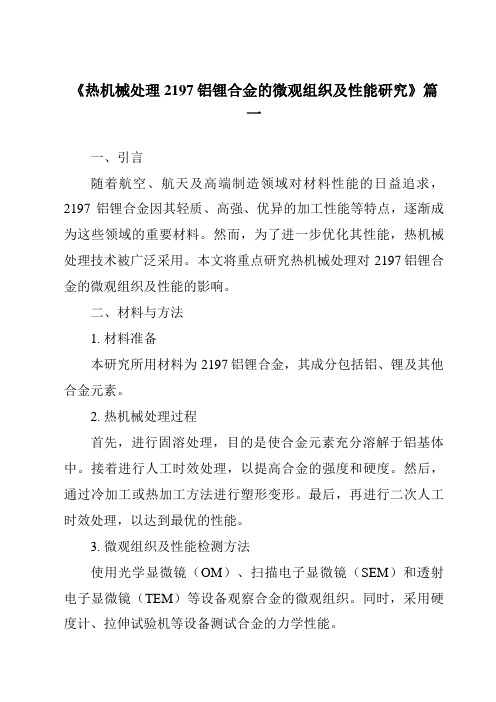
《热机械处理2197铝锂合金的微观组织及性能研究》篇一一、引言随着航空、航天及高端制造领域对材料性能的日益追求,2197铝锂合金因其轻质、高强、优异的加工性能等特点,逐渐成为这些领域的重要材料。
然而,为了进一步优化其性能,热机械处理技术被广泛采用。
本文将重点研究热机械处理对2197铝锂合金的微观组织及性能的影响。
二、材料与方法1. 材料准备本研究所用材料为2197铝锂合金,其成分包括铝、锂及其他合金元素。
2. 热机械处理过程首先,进行固溶处理,目的是使合金元素充分溶解于铝基体中。
接着进行人工时效处理,以提高合金的强度和硬度。
然后,通过冷加工或热加工方法进行塑形变形。
最后,再进行二次人工时效处理,以达到最优的性能。
3. 微观组织及性能检测方法使用光学显微镜(OM)、扫描电子显微镜(SEM)和透射电子显微镜(TEM)等设备观察合金的微观组织。
同时,采用硬度计、拉伸试验机等设备测试合金的力学性能。
三、结果与讨论1. 微观组织分析通过OM、SEM和TEM观察发现,经过热机械处理后,2197铝锂合金的晶粒尺寸明显减小,晶界清晰,析出相数量增多且分布均匀。
这表明热机械处理有效改善了合金的微观组织。
2. 力学性能分析经过硬度计和拉伸试验机测试,发现经过热机械处理的2197铝锂合金具有更高的硬度、抗拉强度和延伸率。
这表明热机械处理显著提高了合金的力学性能。
3. 影响因素分析(1)固溶处理:固溶处理温度和时间对合金元素的溶解程度有显著影响,从而影响后续的时效处理效果。
(2)人工时效处理:时效处理的温度和时间对析出相的数量、大小和分布有重要影响,进而影响合金的性能。
(3)冷/热加工方法:不同的塑形变形方法对合金的微观组织和性能也有一定影响。
(4)二次人工时效处理:二次时效处理可以进一步优化合金的性能,使其达到最优状态。
四、结论本研究通过热机械处理技术对2197铝锂合金进行了处理,并对其微观组织和性能进行了深入研究。
《热机械处理2197铝锂合金的微观组织及性能研究》范文

《热机械处理2197铝锂合金的微观组织及性能研究》篇一一、引言随着现代航空、航天工业的飞速发展,轻质高强度的金属材料需求日益增长。
2197铝锂合金以其优异的综合性能,在航空航天领域得到了广泛的应用。
热机械处理作为改善金属材料性能的重要手段,对2197铝锂合金的微观组织和性能具有显著影响。
本文旨在研究热机械处理对2197铝锂合金的微观组织及性能的影响,为进一步优化该合金的性能提供理论依据。
二、材料与方法1. 材料本文所研究的材料为2197铝锂合金。
该合金具有低密度、高强度、良好的耐腐蚀性等优点,在航空航天领域具有广泛的应用前景。
2. 热机械处理方法热机械处理包括固溶处理、时效处理和形变热处理等过程。
本文采用固溶处理和时效处理两种方法,对2197铝锂合金进行热机械处理。
3. 实验方法通过金相显微镜、扫描电镜、透射电镜等手段,观察合金的微观组织;采用硬度计、拉伸试验机等设备,测试合金的力学性能。
三、结果与分析1. 微观组织观察经过热机械处理后,2197铝锂合金的微观组织发生了显著变化。
固溶处理后,合金中的第二相粒子溶解,晶界变得清晰;时效处理后,析出相在晶界和晶内形成,对合金的性能产生重要影响。
2. 力学性能测试(1)硬度:经过固溶处理后,合金的硬度有所降低;而经过时效处理后,硬度得到显著提高。
这表明时效处理能够促进合金中析出相的形成,从而提高合金的硬度。
(2)拉伸性能:经过热机械处理后,2197铝锂合金的抗拉强度和延伸率均有所提高。
其中,形变热处理能够进一步提高合金的拉伸性能。
这表明热机械处理能够改善合金的塑性变形能力,从而提高其拉伸性能。
3. 分析与讨论热机械处理能够显著改善2197铝锂合金的微观组织和性能。
固溶处理使合金中的第二相粒子溶解,晶界变得清晰,有利于提高合金的塑性和韧性;时效处理则促进析出相的形成,提高合金的硬度和强度。
此外,形变热处理能够进一步优化合金的微观组织,提高其拉伸性能。
这些变化对于改善2197铝锂合金的力学性能、耐腐蚀性和疲劳性能等方面具有重要意义。
时效态高强铝合金热变形行为及微观组织演变

时效态高强铝合金热变形行为及微观组织演变李萍;陈慧琴【摘要】采用热力模拟试验方法对具有时效态和过时效态初始组织的新型 Al-Zn-Mg-Cu 高强铝合金试样进行了热压缩实验,分析了在热变形过程中的流变行为和微观组织演变。
研究结果表明,时效态与过时效态试样都具有动态回复型流变应力曲线特征,且相同变形条件下时效态试样的流变应力高于过时效态流变应力,平均应力指数值分别为6.4525和5.6459,热变形激活能值分别为247.457 kJ/ mol 和178.252 kJ/ mol.两种状态试样热变形组织演变基本规律为:高温条件下,析出相溶入基体组织,晶粒长大倾向高;当变形程度较大时(60%~80%),可以获得细小的晶粒组织;低温变形条件下,析出相含量较高,晶粒长大倾向小。
比较发现,高温变形过程中,时效态试样晶粒长大倾向小,变形程度较大时晶粒组织更加细小均匀;而过时效态试样晶粒组织经历了变形较小时的粗化到变形较大时的细化。
%Hot-compression experiments of new Al-Zn-Mg-Cu alloy with as-aged and as-overaged starting structures were carried out by thermo-mechanical modeling testing method. Hot-deformation Behavior and microstructure evo-lution of the alloy with as-aged and as-overaged starting structures have been analyzed. The results indicate that both samples have the dynamic recovery flow stress curves with higher stress of as-aged samples at the same de-formation conditions. The average stress exponents are 6. 4525 and 5. 6459 respectively,and the average hot-de-formation active energy are 247. 457 kJ/ mol and 178. 252 kJ/ mol respectively for the as-aged and the as-overaged samples. Microstructure evolutions during hot deformation of both samples are that precipitatedphases dissolved in-to the matrix,and grain grows fast during deformation at higher temperature;while refined grains can be obtained when high reduction is great than 60% ~ 80% . However,the content of precipitated phases is higher,and grain grows slowly during deformation at lower temperature. By comparing analyses,it is shown that refined grains after lager strain are smaller and more uniform for the as-aged samples due to lower grain growth rate at the high temper-ature deformation conditions;while grain coarsening occurs at small strain and grain refining presents at large strain for the as-overaged samples at high-temperature deformation processes.【期刊名称】《太原科技大学学报》【年(卷),期】2014(000)005【总页数】6页(P358-363)【关键词】高强铝合金;热变形;流变应力;微观组织【作者】李萍;陈慧琴【作者单位】太原科技大学,太原 030024;太原科技大学,太原 030024【正文语种】中文【中图分类】TG146.2+高强铝合金是航天航空领域的主要结构材料[1]。
高压扭转纯铝的晶界结构研究
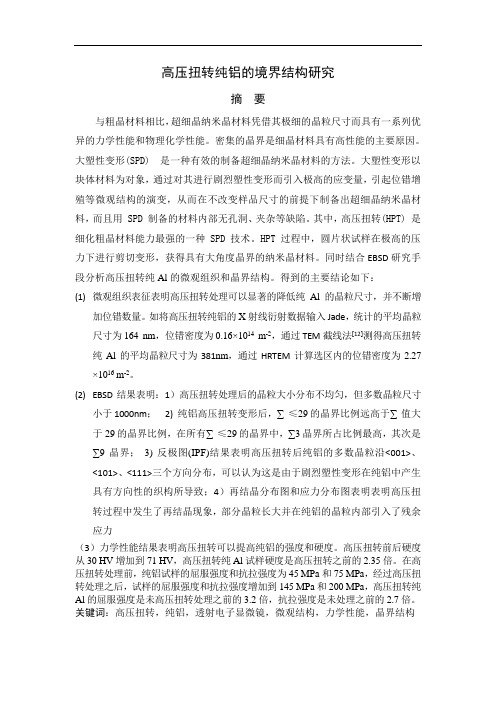
高压扭转纯铝的境界结构研究摘要与粗晶材料相比,超细晶纳米晶材料凭借其极细的晶粒尺寸而具有一系列优异的力学性能和物理化学性能。
密集的晶界是细晶材料具有高性能的主要原因。
大塑性变形(SPD) 是一种有效的制备超细晶纳米晶材料的方法。
大塑性变形以块体材料为对象,通过对其进行剧烈塑性变形而引入极高的应变量,引起位错增殖等微观结构的演变,从而在不改变样品尺寸的前提下制备出超细晶纳米晶材料,而且用 SPD 制备的材料内部无孔洞、夹杂等缺陷。
其中,高压扭转(HPT) 是细化粗晶材料能力最强的一种 SPD 技术。
HPT 过程中,圆片状试样在极高的压力下进行剪切变形,获得具有大角度晶界的纳米晶材料。
同时结合EBSD研究手段分析高压扭转纯Al的微观组织和晶界结构。
得到的主要结论如下:(1)微观组织表征表明高压扭转处理可以显著的降低纯Al的晶粒尺寸,并不断增加位错数量。
如将高压扭转纯铝的X射线衍射数据输入Jade,统计的平均晶粒尺寸为164 nm,位错密度为0.16×1014m-2,通过TEM截线法[12]测得高压扭转纯Al的平均晶粒尺寸为381nm,通过HRTEM计算选区内的位错密度为2.27 ×1016 m-2。
(2)EBSD结果表明:1)高压扭转处理后的晶粒大小分布不均匀,但多数晶粒尺寸小于1000nm;2) 纯铝高压扭转变形后,∑≤29的晶界比例远高于∑值大于29的晶界比例,在所有∑≤29的晶界中,∑3晶界所占比例最高,其次是∑9晶界;3) 反极图(IPF)结果表明高压扭转后纯铝的多数晶粒沿<001>、<101>、<111>三个方向分布,可以认为这是由于剧烈塑性变形在纯铝中产生具有方向性的织构所导致;4)再结晶分布图和应力分布图表明表明高压扭转过程中发生了再结晶现象,部分晶粒长大并在纯铝的晶粒内部引入了残余应力(3)力学性能结果表明高压扭转可以提高纯铝的强度和硬度。
- 1、下载文档前请自行甄别文档内容的完整性,平台不提供额外的编辑、内容补充、找答案等附加服务。
- 2、"仅部分预览"的文档,不可在线预览部分如存在完整性等问题,可反馈申请退款(可完整预览的文档不适用该条件!)。
- 3、如文档侵犯您的权益,请联系客服反馈,我们会尽快为您处理(人工客服工作时间:9:00-18:30)。
Interfacial microstructures and properties of aluminumalloys/galvanized low-carbon steel under high-pressuretorsionYang Liu a ,Xiufang Bian a ,⇑,Kai Zhang a ,Chuncheng Yang a ,Le Feng a ,Hyoung Seop Kim b ,Jing Guo b ,caKey Laboratory for Liquid-solid Structural Evolution and Processing of Materials,Ministry of Education,Shandong University,Jinan 250061,PR China bDepartment of Materials Science and Engineering,Pohang University of Science and Technology,Pohang 790-784,South Korea cCollege of Mechanical and Electronic Engineering,Shandong Agricultural University,Taian 271018,PR Chinaa r t i c l e i n f o Article history:Received 5May 2014Accepted 24July 2014Available online 8August 2014Keywords:Aluminum alloys Low-carbon steel Hot-dipping InterfaceHigh pressure torsiona b s t r a c tA new composite processing technology characterized by hot-dip Zn–Al alloy process was developed to achieve a sound metallurgical bonding between Al–7wt%Si alloy (or pure Al)castings and low-carbon steel inserts,and the variations of microstructure and property of the bonding zone were investigated under high-pressure torsion (HPT).During hot-dipping in a Zn–2.2wt%Al alloy bath,a thick Al 5Fe 2Zn x phase layer was formed on the steel surface and retarded the formation of Fe–Zn compound layers,resulting in the formation of a dispersed Al 3FeZn x phase in zinc coating.During the composite casting process,complex interface reactions were observed for the Al–Fe–Si–Zn (or Al–Fe–Zn)phases formation in the interfacial bonding zone of Al–Si alloy (or Al)/galvanized steel reaction couple.In addition,the results show that the HPT process generates a number of cracks in the Al–Fe phase layers (consisting of Al 5Fe 2and Al 3Fe phases)of the Al/aluminized steel interface.Unexpectedly,the Al/galvanized steel interface zone shows a good plastic property.Beside the Al/galvanized steel interface zone,the microhardnesses of both the interface zone and substrates increased after the HPT process.Ó2014Elsevier Ltd.All rights reserved.1.IntroductionAluminum alloys and steels are indispensable engineering materials because they have good mechanical properties and rela-tively low material costs in many applications [1].As a result of more stringent requirements for improved fuel economy and emissions,there is a growing trend to substitute light alloy for con-ventional steel or cast iron in the automotive industry [2].Bimetal-lic composites consisting of light alloys and steels/cast iron can meet the need for high strength and reduce weight to improve fuel economy and emissions,so they possess a great potential for future developments in automotive technology [3–5].In order to produce a bimetallic composite with good mechan-ical properties,several composite casting techniques have been applied.The chemical reaction is difficultly triggered between Al and iron when pure Al melt is directly poured to surround the iron insert without pretreatment [6].Viala et al.[7,8]manufactured bimetallic automotive components consisting of light alloys and cast iron by using the combination of Al-Fin process and gravity casting.Bouayad et al.[9]produced such bimetallic composites using high pressure die casting.The crucial point in the composite casting techniques is the liquid/solid interface between light alloys and ferrous metals substrate.A good wettability of solid substrates is essential in achieving good metallurgical bonding at the inter-face.In order to improve the wettability of solid substrates,an interlayer coated on the substrate surface has been a common approach.The Al-Fin process is a method of coating Al alloys on the sur-face of ferrous metals by hot-dipping [7].The Al-Fin bond is a bond between an Al alloy and a ferrous metal.The effect of hot-dipping bath composition on the morphology of the interfacial bonding zone is important.The addition of Silicon into the Al alloy bath has a significant influence on the continuous intermediate layer,which not only produces flat morphology from the classical ton-gue-shaped one in the interface between the intermediate layer and the steel substrate,but also affects the growth of the interme-diate layer [10–12].In the liquid/solid diffusion couple,Si deceler-ates the growth of g phase in the intermediate layer.In contrast,Springer et al.[13]presented that Si can accelerate the growth of g phase in the intermediate layer for the solid/semisolid diffusion couples.The effect of Mn on the interface has also been studied.Choi et al.[14]found that additional content Mn can make the thickness of the intermetallic layer increase comparing to the Al alloy without Mn at the interface between a low Si Al alloy and STD61steel.Our previous work [15]has also demonstrated that/10.1016/j.matdes.2014.07.0530261-3069/Ó2014Elsevier Ltd.All rights reserved.⇑Corresponding author.Tel.:+8653188392748;fax:+8653188395011.E-mail address:xfbian@ (X.Bian).the addition of Mn facilitated the formationa-Al15(Fe x Mn1Àx)3Si2phases and the growthmetallurgical bonding layer at the Al–7wt%which can improve the properties of the Al/FeOn the other hand,there are manyalloys can also serve as a good interlayerjoint of dissimilar metals[16–19].Variousinvestigated for coating the zinc or zinc alloysurface of the base metal,such asplating[17],and hot-dipping[18,19].The zinclayer can not only protect the base metal fromimprove the wettability of the base metal.environment and conditions for interfacesimilar metals.Zinc coating on steel is alsoapplications especially in the automotivecorrosion resistance of steel used for carmany studies have been reported to join Al alloy to zinc-basedcoated steel by laser welding-brazing(LWB),friction stir welding (FSW),cold metal transfer(CMT),laser-tungsten inert gas(TIG) hybrid welding,etc.[21–25],but very little work has been done on the composite casting.How to achieve an excellent metallurgi-cal bonding between Al alloys and low-carbon steel still is quite a challenging subject.In this study a new composite processing technology character-ized by an auxiliary hot-dip Zn–Al alloy process was developed in order to achieve a sound metallurgical bonding between Al alloy or pure Al and low-carbon steel.In order to extent the application sphere of the Al/steel bimetal composite under high pressure envi-ronment,the variations of microstructure and properties were investigated for the Al/aluminized steel and the Al/galvanized steel samples after high-pressure torsion(HPT)process.2.Experimental procedureSteel samples(diameter3mmÂlength100mm)were cut out from a low-carbon steel bar(containing0.06–0.12wt%C)coated a pure zinc coating by electroplating.Prior to immersing the sam-ples in liquid Zn–2.2wt%Al bath at723±10K for various time,all the surface of the steel samples were polished in order to remove surface ZnO layers and cleaned in ethanol.The thickness of the electroplated zinc coating was approximately5l m after polishing. Then,the hot-dip galvanized steel samples were moved away from the liquid Zn–Al bath and fastened rapidly on a permanent mould preheated at473K,respectively.Si,0.3–0.45wt.%Mg,0.2wt.%Ti, and Al)was poured into the mould at993±10K.These liquid Zn–Al alloy,Al and Al–Si alloy were melted in an intermediate fre-quency furnace and held at a setting temperature in a resistance furnace.The Al/steel samples were cut into small disks(diameter 10Âlength1.5mm)for the HPT process.These small disks were placed in a circular shallow hole of the lower HPT anvil,as shown in Fig.1[26].Then,the lower anvil with the disk sample was raised to contact the upper anvil having the same shallow hole at the cen-ter.While applying a pressure of5GPa at room temperature,the lower anvil was rotated at a rotation speed of1rpm and the rota-tion was terminated after1turn.In order to evaluate the effect of the HPT process on the strength of the bonding interface,the Vick-ers micro-hardness test(model DHV-1000)was performed along the thickness direction of the original and treated samples with a low indentation load of10g.For the composition and microstructure analyses,vertical or horizontal cross sections were prepared by successive grinding and polishing.The vertical and horizontal cross section samples were cut from the Al–Si alloy or Al/galvanized steel composite and mounted using epoxy by a mounting press.In order to further analyze the interfacial bonding zone,the interfacial microstructure of each sample was examined using an optical microscope(OM) and scanning electron microscopy(SEM).The phases were chemi-cally characterized to evaluate the nature of the intermetallics using energy dispersive spectroscopy(EDS).3.Results3.1.Growth and microstructure of the hot-dip galvanized coatingThe hot-dip Zn–Al alloy process is a vital step for achieving a sound metallurgical bonding between Al alloy castings and steel inserts,so it is essential to study the growth and microstructure of the hot-dip galvanized coating.Fig.2exhibits SEM images of the vertical section of the steel sample after hot-dipping in Zn–2.2wt%Al melt at723K for300s and the thicknesses of the hot-dip galvanized coating and the dif-fusion layer as a function of hot-dip time.The average thickness of the light gray Zn–Al coating on the surface of the steel substrate is approximately292l m.The diffusion layer consisting of some dark gray phases was formed in the interface between the Zn–Al coating and steel substrate after hot-dipping.The dark gray phase exhibits continuously graded morphology and is strongly attached to the steel substrate.However,some pores exist in the region adjacent to the steel substrate.They are attributable to the steel particles dissolved from the steel substrate during hot-dipping and departed during grinding and polishing.The other parts of the dark gray phases exhibit dispersive distribution in the Zn–Al coating.The microstructure of the interface between the Zn–Al coating and steel substrate can be observed clearly in Fig.2(b).The chemical compositions of these interfacial phases were identified using spot scanning of SEM-EDS,as shown in Table1.According to the char-acterization of the ternary solid phase in Al–Fe–Zn system[27,28], the continuous layered phases were identified as Al5Fe2Zn x,and the dispersive phases were identified as Al3FeZn x.It can be seen that the average thickness of the hot-dip galvanized coating increases with increasing hot-dip time,and the average thickness of the diffusion layer presents the same trend(Fig.2(c)).3.2.Observation of the Al/galvanized steel and Al–Si/galvanized steel interfaces after pouringThe objective of this part is to analyse the effect of the different composition of the Al melts on the microstructure forming at the Al alloy casting/galvanized steel insert interface.Fig.3presents the optical micrographs of the Al–Si/galvanized steel and Al/galvanized steel interfaces obtained from the samples poured from Al–Si alloy and pure Al melts,respectively.TheFig.1.Schematic of the HPT process.288galvanized steel samples were obtained by hot-dipping the steel bar in Zn–2.2wt%Al bath at723K for300s.The layered microstructure was formed at the Al–Si/galvanized steel and Al/galvanized steel interfaces.A number of largedistributed in the Al substrate(Fig.3(b)).However,hardly any the large layered phases distributedsubstrate(Fig.3(a)).Fig.4shows the magnified SEM images ofsteel and Al–Si/galvanized steel interface obtainedpoured at993K and the linear scanning analysisThe chemical compositions of the Al–Si/galvanizedgalvanized steel samples obtained from hot-dipping in the Zn–2.2wt.%Al melt at723K for300s;(b)the magnified view of thicknesses of the hot-dip galvanized coating and the diffusion layer as a function of hot-dipping time.Table1analysis for the Zn–Al/steel interface using SEM-EDS from the(b).Compositions(at.%)PhaseFe Zn–90.18Zn23.028.44Al3FeZn x26.38 6.18Al5Fe2Zn x100–FeOptical micrographs of(a)Al–Si/galvanized steel and(b)Al/galvanized steel interfaces obtained from the sample poured atAl/galvanized steel interfacial phases were identified by spot scan-ning using SEM-EDS,as shown in Table 2.The Al–Si/galvanized steel interface consists of a continuous Al 5Fe 2Zn x phase layer,a continuous Al 8(Fe,Zn)2Si phase layer and a discontinuous needle-like Al 5(Fe,Zn)Si phase layer,as shown in Fig.4(a).These phases were identified using the analysis of linear scanning from Fig.4(b)and the result of spot scanning from Table 2using SEM-EDS.The Al/galvanized steel interface consists of a continuous Al 5Fe 2Zn x phase layer and some layered Al 3FeZn x phases,as shown in Fig.4(c).These phases were identified by the analysis of linear scanning from Fig.4(d)and the result of spot scanning from Table 2using SEM-EDS.3.3.Analysis of the Al/aluminized steel and Al/galvanized steel interfaces after HPTIn order to study the effect of high pressure on the Al casting/steel insert interface,the HPT process was performed on the Al–Si/aluminized steel and Al/aluminized steel samples.And meanwhile,the variation of microstructure and properties werealso investigated for the Al/aluminized steel and Al/aluminized steel interface after the HPT process.Fig.5shows the macro and enlarged SEM images of the samples after the HPT process.Fig.5(a)presents the sample hot-dipped in pure Al bath at 993K for 300s before pouring fresh pure Al at 993K,followed by HPT.A classical ‘‘tongue-like’’interface zone was found.The intermetallic compound layer is made up of Al 5Fe 2and Al 3Fe phases [12].The thickness of the samples decreased from 1.5mm to 0.9mm under the pressure of 5GPa at room tempera-ture.The Al/aluminized steel interface deformed to arc-shaped,as shown in Fig.5(a).The Al/galvanized steel interface has also severely deformed under the vertical load and horizontal torsion,as shown in Fig.5(b).This sample was hot-dipped in Zn–2.2wt%Al bath at 723K for 300s,followed by pouring fresh pure Al at 993K and HPT.The Al/galvanized steel interface formed a relatively thinner intermetallic compound layer (containing the Al 5Fe 2Zn x and Al 3FeZn x phases)than the Al/aluminized steel inter-face,which enhances plastic performance.According to the enlarged SEM images,there are a number of cracks in the intermetallic compound layer of the Al/aluminized steel interface after the HPT process (see Fig.5(c)).It is because the brittle Al 5Fe 2and Al 3Fe phases are hard to bear the pressure of 5GPa.In contrast,the relatively thinner Al 5Fe 2Zn x and Al 3FeZn x phase layers have a good plastic ductility to restrain the crack formation (see Fig.5(d)).However,the steel/compound and com-pound/Al interfaces have not been broken after the HPT process (see Fig.5(e)).The particle phases formed in the Al substrate are more homogeneously distributed after the HPT process.Its diame-ter is approximately 1l m (Fig.5(f)).The microhardnesses of the Al/aluminized steel and Al/galva-nized steel interfaces are shown in Fig.6both before and after the HPT process.Besides the intermetallic compound layer attheimages of the bonding interface obtained from pouring at 993K and the analysis of linear scanning:(a)Al–Si/galvanized steel;arrow in Fig.4(a);(c)Al/galvanized steel;(d)the analysis of linear scanning along the red arrow in Fig.4(c).(For interpretation legend,the reader is referred to the web version of this article.)Table 2Chemical analyses for the Al–Si/galvanized steel and Al/galvanized steel interfaces using SEM-EDS analysis from selected regions in Fig.4(a)and (c).Composition (at.%)PhaseAlFe Si Zn 168.2512.6016.22 2.93Al 5(Fe,Zn)Si 268.0819.0310.80 2.08Al 8(Fe,Zn)2Si 365.4324.660.948.97Al 5Fe 2Zn x 468.5524.90– 6.55Al 5Fe 2Zn x 575.2519.87–4.88Al 3FeZn xenlarged SEM images of the samples after the HPT process:(a),(c),(e)Al/aluminized steel and(b),(d),(f)Al/galvanized Fig.6.Microhardnesses of the interfaces of(a)Al/aluminized steel and(b)Al/galvanized steel both before and after the HPT process.Al/galvanized steel interface,the HPT process increased the microhardness of the Al/aluminized steel interfaces and substrates.4.DiscussionDissimilar metal composite casting is a powerful joining method that has a great relevance for industrial applications.A good wettability of the surface of steel substrates is essential in realizing this process.Wetting is a strong function for interfacial metallurgical reactions and can only be achieved by eliminating the natural oxide layer[17].Electrogalvanizing coating is generally applied in order to protect the surface of steel substrates from oxi-dation in air and improve the wettability of steel substrates.Also, the hot-dip galvanizing treatment makes possible a metallurgical reaction between liquid Al alloy and solid steel.These processes guarantee a good metallurgical bonding interface between Al alloy and steel.At the beginning of the hot-dip galvanizing step,the tempera-ture of the steel surface rapidly increases up to approximately 723K.The electrogalvanizing coating meltsfirstly,and then the liquid alloy very efficiently protects the steel from oxidation by air,hence no new zinc or steel oxide is developed at the Zn–Al alloy/steel interface.A metallurgical reaction occurs between the steel surface and Zn–Al alloy and the gradual diffusion of the free atoms into the steel substrate becomes possible.During hot-dipping at723K,both metallurgical reaction and dissolution simultaneously proceed at the Zn–Al alloy/steel inter-face.The formation of intermediate phases is a complex process. There mainly form Al5Fe2Zn x phase and Al3FeZn x phase at the interface between Zn–Al alloy and steel.The reaction process is described as follows.At the beginning,a number of Al atoms gather around the steel surface and diffuse into the steel substrate,which results in chemical reaction proceeding at the liquid–solid inter-face(for example,2Fe+5[Al]Zn+xZn?Al5Fe2Zn x)[28].This reac-tion rapidly induces the formation and growth of a continuous Al5Fe2Zn x phase layer on the steel surface,which inhibits the for-mation of Fe–Zn compound[29,30].According to Fig.2(b),a tenta-tive inference is that Al atoms diffuse from the Zn–Al bath to the steel substrate along grain boundaries to form Al5Fe2Zn x phase. With growing the Al5Fe2Zn x phase,then,some iron particles simul-taneously dissociates from the steel substrate and dissolve into Zn–Al bath.Meanwhile,the Al atoms gather around the free iron particles.According to the study of phase equilibrium in Ref.[31] and the Al–Fe–Zn isothermal section at723K[32],the Al3FeZn x phase can arise as a product of the following chemical reactions: 5½AlZnþ2FeþxZn!Al5Fe2Zn x;ð1Þ½AlZnþxZnþAl5Fe2Zn x!2Al3FeZn x:ð2ÞSome Zn atoms dissolve into the Al3Fe phase to form solid solution. At last,a number of dispersed Al3FeZn x phases are formed in the Zn–Al coating during solidifying.The growth of these compounds is controlled by a diffusion process of Al atoms and Fe atoms.It is similar to the growth of intermetallic compounds in Al–Fe system in Refs.[33,34].With increasing the hot-dip time,the thickness of the diffusion layer increased,as shown in Fig.2(c).The hot-dip pro-cess makes the steel preheat to723K and forms an Al–Fe phase layer at the Zn–Al alloy/steel interface,which is a vital step to form a metallurgical bonding interface.It is beneficial to fuse the Zn–Al coating on the surface of steel during subsequent pouring and improve the wetting of the steel surface by Al alloy melts.When the steel samples are moved from the Zn–Al bath to the mold,the Zn–Al alloy coating/steel substrate interface state rapidly changes.Therefore,a sufficiently fast transfer is required.Never-theless,a thin oxidation layer cannot be avoided on the surface of the hot-dip galvanized steel.When the fresh Al–Si alloy or pure Al is rapidly poured into the mould at993K,the oxidationfilm is not strong enough to withstand the impact by the liquidflowing onto it and then,the Zn–Al coating is remelted and dissolves in the liquid Al–Si alloy or pure Al.The diffusion layer also partly dis-solves in the liquid Al–Si alloy or pure Al.At the same time,the Fe content of the liquid Al–Si alloy or pure Al in the vicinity of the steel surface rapidly approaches saturation under the combined effects of thermodynamics and kinetics.With decreasing the pour-ing temperature,the maximum solubility of Fe in the alloy decreased[35].As a result,the intermetallic compound layer forms rapidly again and grows.The morphology of the intermetallic compound layer is shown in Fig.3.When the Al–Si alloy is poured,three intermetallic compounds,Al5(Fe,Zn)Si,Al8(Fe,Zn)2Si,and Al5Fe2Zn x,are formed (Fig.4(a)).Taking into account published or recently acquired data on the Al–Fe–Si system[7,36–38],the formation of the Al–Fe–Si phases during solidification in the interface zone can take place through the following reactions:LþAl3FeZn x!Al8ðFe;ZnÞ2SiþAlð3ÞL!Al8ðFe;ZnÞ2SiþAlð4ÞLþAl8ðFe;ZnÞ2Si!Al5ðFe;ZnÞSiþAlð5ÞL!Al5ðFe;ZnÞSiþAlþSið6ÞWhen the pure Al is poured,only Al5Fe2Zn x and Al3FeZn x phases are formed(Fig.4(c)).This is consistent with the interface of the hot-dip aluminized steel[13].In this process,the Zn–Al coating is also remelted during pouring,which promotes steel atoms and Al5Fe2 Zn x phase transferring to the Al melt.Consequently,some layered morphology forms at the Al/galvanized steel interface(see Fig.3).In general,the HPT process is used to provide grain refinement of hard-to-deform materials[39]or promote solid-state reactions [26].In this study,we tried to study the effects of high pressure on the microstructure and mechanical properties of the Al/steel interface by performing the HPT.So we investigated the variation of microstructure and properties for the Al/aluminized steel and Al/galvanized steel composite samples after the HPT process.The HPT process makes the Al/aluminized steel and Al/galvanized steel composite samples deform severely(see Fig.5).For the Al/alumi-nized steel interface,a number of cracks form in the thick interme-tallic compound layer after the HPT process(see Fig.5(c)).It is because Al5Fe2and Al3Fe phases are difficult to bear the pressure of5GPa,although the HPT process can improve the property of substrate by grain refinement.The HPT process improved the microhardness of substrate significantly(see Fig.6(a)).The HPT process severely deforms the Al/galvanized steel interface,but the interfacial microstructure is not broken(see Fig.5(d)and(f)). The abnormal deformation of steel insert may be due to the off-center positioning in the sample and torsion processing,as shown in Fig.5(b).In addition,the severe abnormal deformation also reflects a good plastic performance of the Al/galvanized steel inter-face.Fig.6(b)exhibits that both Al and steel substrates are strengthened after the HPT process.However,the hardness of the interfacial zone decreased.Meanwhile,a number of the particle phases are formed with homogeneous distribution in Al alloy sub-strate after the HPT process.Some particle phases may be formed from the fragmented needle phase after the HPT process.The oth-ers may be attributed to the severe plastic deformation which induced the solid solution of Fe atoms in Al substrate gathering and then transforming to Al–Fe particle phases.The new composite processing technology characterized by hot-dip Zn–Al alloy on the surface of low-carbon steel achieves a sound metallurgical bonding between the Al alloys and low-carbon steel.This composite fabrication approach has an important signif-icance and practical value for the development of liquid–solid composite materials.292Y.Liu et al./Materials and Design64(2014)287–2935.ConclusionsA hot-dip galvanizing treatment was applied in order to form a sound metallurgical bonding interface between pure Al or Al–Si alloy and low-carbon steel.In addition,the variations of micro-structure and properties were investigated for the Al/aluminized steel and Al/galvanized steel samples after the HPT process.The following conclusions were obtained.1)Electrogalvanized pure zinc coating can improve the wetta-bility of surface of the steel substrate.It enhances the forma-tion of a good metallurgical bonding layer at the interface between Zn–Al coating and steel substrate.With increasing hot-dip time,the average thickness of the diffusion layer consisting of Al5Fe2Zn x and Al3FeZn x phases increases.2)The hot-dip galvanizing treatment promotes the liquid–solidreaction between Al–Si alloy(or pure Al)and low-carbon steel during pouring Al–Si alloy(or pure Al),so that the Al5 (Fe,Zn)Si,Al8(Fe,Zn)2Si,and Al5Fe2Zn x(Al5Fe2Zn x and Al3Fe Zn x)intermetallic compounds were formed in the interface zones.3)The Al/galvanized steel interface has the better plastic prop-erty than Al/aluminized steel interface under high pressure environment.In addition,the HPT process strengthens the substrates of the Al–Si alloy(or pure Al)and steel. AcknowledgmentsThe authors are grateful for thefinancial support from the National Natural Science Foundation of China(Grant No. 51371107)and Scientific and Technological Project of Shandong Province(Grant No.2013GGX10217).Guo Jing was supported by the national research foundation of Korea through the Korea-China Young Scientist Exchange Program.References[1]Crane FAA,Charles JA,Furness J.Selection and use of engineeringmaterials.Butterworth-Heinemann;1997.[2]Cole GS,Sherman AM.Lightweight materials for automotive applications.Mater Charact1995;35:3–9.[3]Yang Y,Zhang XM,Li ZH,Li QY.Adiabatic shear band on the titanium side inthe Ti/mild steel explosive cladding interface.Acta Mater1996;44:561–5. [4]Sierra G,Peyre P,Deschaux Beaume F,Stuart D,Fras G.Galvanised steel toaluminium joining by laser and GTAW processes.Mater Charact2008;59: 1705–15.[5]Zhe M,Dezellus O,Gardiola B,Braccini M,Viala JC.Chemical changes at theinterface between low carbon steel and an Al–Si alloy during solution heat treatment.J Phase Equilib2011;32:486–97.[6]Li WZ,Bian XF.Metallographic study of interface achieved by aluminum–ironcompound casting.Chin J Mech Eng2011;47:67–72.[7]Viala JC,Peronnet M,Barbeau F,Bosselet F,Bouix J.Interface chemistry inaluminium alloy castings reinforced with iron base posites Part A 2002;33:1417–20.[8]Sacerdote-Peronnet M,Guiot E,Bosselet F,Dezellus O,Rouby D,Viala JC.Localreinforcement of magnesium base castings with mild steel inserts.Mater Sci Eng A2007;445:296–301.[9]Bouayad A,Gerometta C,Radouani M,Radouani M,Saka A.Interfacecharacterization in aluminum alloy casting reinforced with SG iron inserts.J Adv Res Mech Eng2010;1:226–31.[10]Cheng WJ,Wang CJ.Effect of silicon on the formation of intermetallic phases inaluminide coating on mild steel.Intermetallics2011;19:1455–60.[11]Pietrowski S,Szymczak T.Effect of silicon concentration in bath on thestructure and thickness of grey cast iron coating after alphinising.Arch Mater Sci Eng2007;28:437–40.[12]Zhang K,Bian XF,Li YM,Liu Y,Yang CC.New evidence for the formation andgrowth mechanism of the intermetallic phase formed at the Al/Fe interface.J Mater Res2013;28:3279–87.[13]Springer H,Kostka A,Payton EJ,Raabe D,Kaysser-Pyzalla A,Eggeler G.On theformation and growth of intermetallic phases during interdiffusion between low-carbon steel and aluminum alloys.Acta Mater2011;59:1586–600. [14]Choi SW,Kim YC,Kim CW,Cho JI,Kang CS,Kim YM.Effect of Mn on theInteraction between Die Casting Steel and Al Alloy.In:ICAA13:13th International Conference on Aluminum Alloys.John Wiley&Sons,Inc.;2012.p.225–9.[15]Liu Y,Bian XF,Yang JF,Zhang K,Feng L,Yang CC.An investigation ofmetallurgical bonding in Al–7Si/gray iron bimetal composites.J Mater Res 2013;28:3190–8.[16]Cheng XL,Gao YM,Fu HG,Xing JD,Bai BZ.Microstructural characterizationand properties of Al/Cu/Steel diffusion bonded joints.Met Mater Int 2010;16:649–55.[17]Papis KJM,Hallstedt B,Löffler JF,Uggowitzer PJ.Interface formation inaluminium–aluminium compound casting.Acta Mater2008;56:3036–43. [18]Zhao LM,Zhang ZD.Effect of Zn alloy interlayer on interface microstructureand strength of diffusion-bonded Mg–Al joints.Scripta Mater2008;58:283–6.[19]Liu LM,Zhao LM,Xu RZ.Effect of interlayer composition on the microstructureand strength of diffusion bonded Mg/Al joint.Mater Design2009;30:4548–51.[20]Song GM,Vystavel T,van der Pers N,De Hosson JTM,Sloof WG.Relationbetween microstructure and adhesion of hot dip galvanized zinc coatings on dual phase steel.Acta Mater2012;60:2973–81.[21]Laukant L,Wallmann C,Müller M,Korte M,Stirn B,Haldenwanger HG,et al.Fluxless laser beam joining of aluminium with zinc coated steel.Sci Technol Weld Joi2005;10:219–26.[22]Chen YC,Nakata K.Effect of the surface state of steel on the microstructure andmechanical properties of dissimilar metal lap joints of aluminum and steel by friction stir welding.Metall Mater Trans B2008;39:1985–92.[23]Yang SL,Zhang J,Lian J,Lei YP.Welding of aluminum alloy to zinc coated steelby cold metal transfer.Mater Design2013;49:602–12.[24]Tan CW,Li LQ,Chen YB,Guo ser-tungsten inert gas hybrid welding ofdissimilar metals AZ31B Mg alloys to Zn coated steel.Mater Design 2013;49:766–73.[25]Ma JJ,Harooni M,Carlson B,Kovacevic R.Dissimilar joining of galvanized high-strength steel to aluminum alloy in a zero-gap lap joint configuration by two-pass laser welding.Mater Design2014;58:390–401.[26]Oh-ishi K,Edalati K,Kim HS,Hono K,Horita Z.High-pressure torsion forenhanced atomic diffusion and promoting solid-state reactions in the aluminum–copper system.Acta Mater2013;61:3482–9.[27]Ghuman ARP,Goldstein JI.During the hot dipping of iron in0to10pct Al–Znbaths at450–700°C.Metall Trans1971;2:2903–14.[28]O’dell S,Charles J,Vlot M,Randle V.Modelling of iron dissolution during hotdip galvanising of strip steel.Mater Sci Tech2004;20:251–6.[29]Marder AR.The metallurgy of zinc-coated steel.Prog Mater Sci2000;45:191–271.[30]Blumenau M,Norden M,Friedel F,Peters K.Reactive wetting during hot-dipgalvanizing of high manganese alloyed steel.Surf Coat Tech 2011;205:3319–27.[31]Perrot P,Tissier JC,Dauphin JY.Stable and metastable equilibria in the Fe–Zn–Al system at450°C.Zeitschrift für Metallkunde1992;83:786–90.[32]Raghavan V.Al–Fe–Zn(aluminum–iron–zinc).J Phase Equilib2003;24:546–50.[33]Kobayashi S,Yakou T.Control of intermetallic compound layers at interfacebetween steel and aluminum by diffusion-treatment.Mater Sci Eng A 2002;338:44–53.[34]Lee JM,Kang SB,Sato T,Tezuka H,Kamio A.Evolution of iron aluminide in Al/Fe in situ composites fabricated by plasma synthesis method.Mater Sci Eng A 2003;362:257–63.[35]Bai K,Wu P.Assessment of the Zn–Fe–Al system for kinetic study ofgalvanizing.J Alloy Compd2002;347:156–64.[36]Raghavan V.Al–Fe–Si(Aluminum–Iron–Silicon).J Phase Equilib Diff2009;30:184–8.[37]Tanihata H,Sugawara T,Matsuda K,Matsuda K,Ikeno S.Effect of casting andhomogenizing treatment conditions on the formation of Al–Fe–Si intermetallic compounds in6063Al–Mg–Si alloys.J Mater Sci1999;34:1205–10.[38]Liu ZK,Chang YA.Thermodynamic assessment of the Al–Fe–Si system.MetallMater Trans A1999;30:1081–95.[39]Al-Fadhalah KJ,Alhajeri SN,Almazrouee AI,Langdon TG.Microstructure andmicrotexture in pure copper processed by high-pressure torsion.J Mater Sci 2013;48:4563–72.Y.Liu et al./Materials and Design64(2014)287–293293。