A铝合金显微组织及断口分析
铝合金的显微组织与力学性能研究

铝合金的显微组织与力学性能研究近年来,随着人们对新材料的需求不断增加,铝合金作为一种轻质高强度材料,在工业领域中得到了广泛的应用。
铝合金的显微组织与力学性能之间存在着密切的关系,因此对其进行研究是至关重要的。
首先,我们来关注铝合金的显微组织。
铝合金的显微组织通常由晶粒、晶界和相组成。
晶粒是指铝合金中的晶体,其大小和形状对材料的力学性能有着重要影响。
晶界是相邻晶粒之间的界面,也称为晶粒界面,在晶界上常常存在着结构缺陷,如滑移带、孪晶等,这些缺陷对材料的塑性变形和失效起着重要作用。
相是指铝合金中存在的其他成分,如硬质相、软质相等,相的类型和分布状态直接影响材料的硬度、韧性等力学性能。
其次,铝合金的力学性能是指其在外力作用下的表现,主要包括强度、塑性和韧性等方面。
强度是材料抵抗外力破坏的能力,通常用屈服强度和抗拉强度来表示。
塑性是指材料在外力作用下发生可逆形变的能力,表现为其能够被加工成各种形状。
韧性是指材料在受到外力时能够吸收较大的能量而不发生断裂的能力,其与材料的断裂韧度有关。
然后,我们来探讨铝合金的显微组织与力学性能之间的关系。
通过控制铝合金的显微组织,可以有效地调节其力学性能。
例如,通过合理的热处理和变形加工,可以改变晶粒的形状和大小,进而调节铝合金的强度和塑性。
此外,在铝合金中添加合适的相或进行相变处理,可以改善其抗蠕变性、耐磨性等特殊应用性能。
最后,我想提到一些常见的铝合金及其显微组织与力学性能的研究成果。
例如,2024铝合金是一种高强度材料,其强度可通过固溶处理和时效处理得到进一步提高。
研究发现,适量的固溶处理和时效处理可以使该合金的塑形能力得到提高,进而增加其应用范围。
此外,7075铝合金是一种常用的超高强度材料,其显微组织中常见的硬质相可有效提高其强度和硬度。
通过对其显微组织的研究,研究人员发现了一种新型的加工方式,即等通道转角挤压(ECAP),可以显著提高7075铝合金的塑性,从而拓宽了其应用领域。
A356铝合金显微组织与断口分析报告
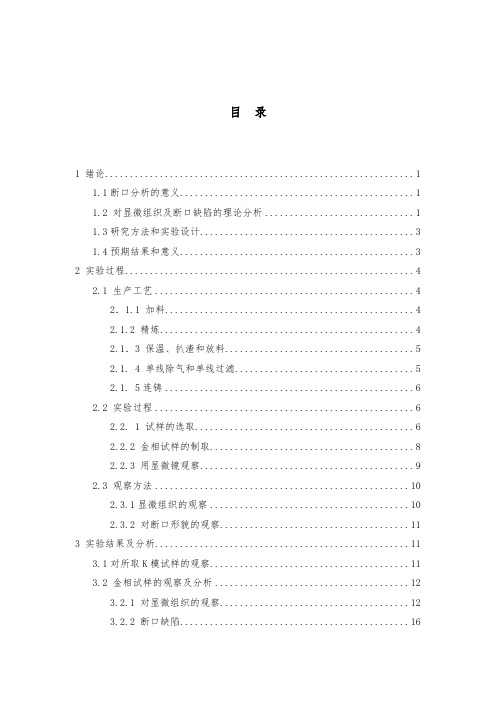
目录1 绪论 (1)1.1断口分析的意义 (1)1.2 对显微组织及断口缺陷的理论分析 (1)1.3研究方法和实验设计 (3)1.4预期结果和意义 (3)2 实验过程 (4)2.1 生产工艺 (4)2.1.1 加料 (4)2.1.2 精炼 (4)2.1.3 保温、扒渣和放料 (5)2.1. 4 单线除气和单线过滤 (5)2.1. 5连铸 (6)2.2 实验过程 (6)2.2. 1 试样的选取 (6)2.2.2 金相试样的制取 (8)2.2.3 用显微镜观察 (9)2.3 观察方法 (10)2.3.1显微组织的观察 (10)2.3.2 对断口形貌的观察 (11)3 实验结果及分析 (11)3.1对所取K模试样的观察 (11)3.2 金相试样的观察及分析 (12)3.2.1 对显微组织的观察 (12)3.2.2 断口缺陷 (16)结论 (24)致 (25)参考文献 (26)附录 (28)1 绪论1.1断口分析的意义随着现代科技的发展以及现代工业的需求,作为21世纪三大支柱产业的材料科学正朝着高比强度,高强高韧等综合性能等方向发展。
长久以来,铸造铝合金以其价廉、质轻、性能可靠等因素在工业应用中获得了较大的发展。
尤其随着近年来对轨道交通材料轻量化的要求日益迫切[1],作为铸造铝合金中应用最广的A356铝合金具有铸造流动性好、气密性好、收缩率小和热裂倾向小,经过变质和热处理后,具有良好的力学性能、物理性能、耐腐蚀性能和较好的机械加工性能[2-3],与钢轮毂相比,铝合金轮毂具有质量轻、安全、舒适、节能等,在汽车和航空工业上得到了日益广泛的应用[4]。
然而,由于其凝固收缩,同时在熔融状态下很容易溶入氢,因此铸造铝合金不可避免地包含一定数量的缺陷,比如空隙、氧化物、孔洞和非金属夹杂物等[5-7]。
这些缺陷对构件的力学性能影响较大,如含1%体积分数的空隙将导致其疲劳50%,疲劳极限降20%[8-9]。
所以研究构件中缺陷的性质、数量、尺寸和分布位置对力学性能的影响具有重要意义[10]。
综述-铝合金疲劳及断口分析报告
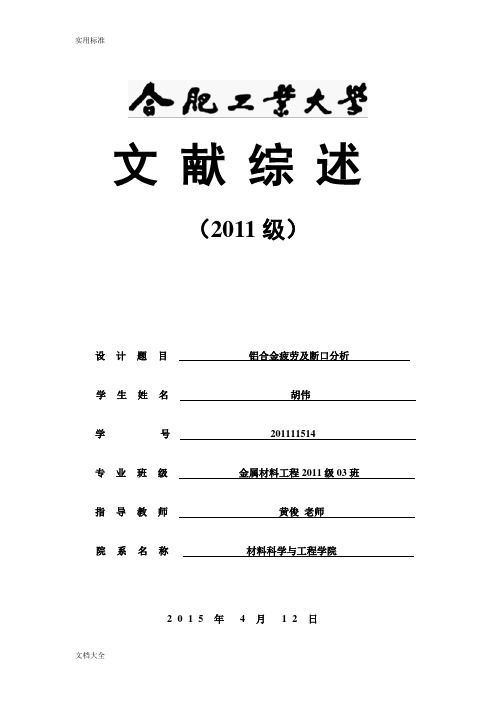
文献综述(2011级)设计题目铝合金疲劳及断口分析学生姓名胡伟学号*********专业班级金属材料工程2011级03班指导教师黄俊老师院系名称材料科学与工程学院2015年4月12日铝合金疲劳及断口分析1 绪论1.1 引言7系铝合金包括Al-Zn-Mg 系和Al-Zn-Mg-Cu 系合金,此类合金具有密度低、比强度高、良好的加工性能及优良的焊接性能等一系列优点。
随着应用在铝合金上的热处理工艺及微合金化技术的不断改进,其力学性能被大幅度强化,综合性能也得到了全面提升。
在航空航天、建筑、车辆、、桥梁、工兵装备和大型压力容器等方面都得到了广泛的应用。
现代工业的飞速发展,对7 系铝合金的强度、韧性以及抗应力腐蚀性能等提出了更高的要求。
但是,存在另外一个现象,在各行各业的领域中,铝合金设备偶尔会出现难以察觉的断裂,在断裂之前很难甚至无法察觉到一点塑性变形。
这种断裂形式,对人身以及财产安全造成了不可挽回的损失。
经过大量实验表明,这些断裂是由于材料的疲劳引起,材料在交变载荷的长期作用下,表面或者内部,尤其是内部会产生微观裂纹。
本文主要研究铝合金疲劳引起的裂纹以及疲劳断口分析,此类研究对于日后的生产安全,有重大意义。
1.2 7系铝合金的发展历史在20世纪20年代,德国的科学家研制出Al-Zn-Mg系合金,由于该合金抗应力腐蚀性能太差,并未得到产业内应用。
在20世纪30年代初一直到二战结束期间,各个国家在研究中发现,Cu元素可以提高铝合金的抗应力腐蚀性能。
在此,开发了大量Al-Zn-Mg 系合金,因此忽视了对Al-Zn-Mg 系合金的研究。
德、美、苏、法等国在Al-Zn-Mg-Cu 系合金基础上成功地开发了7075 、B93 和D。
T。
D683 等合金。
目前正广泛应用在航空航天事业上,但是强度、韧性、抗应力腐蚀性能三者之间未能实现最佳组合状态。
20世纪50年代,德国科学家公布了具有优良焊接性能的合金AlZnMg1 和AlZnMg2,引起了人们对Al-Zn-Mg系合金的重视。
A356.2铝合金轮毂拉伸性能及断口分析
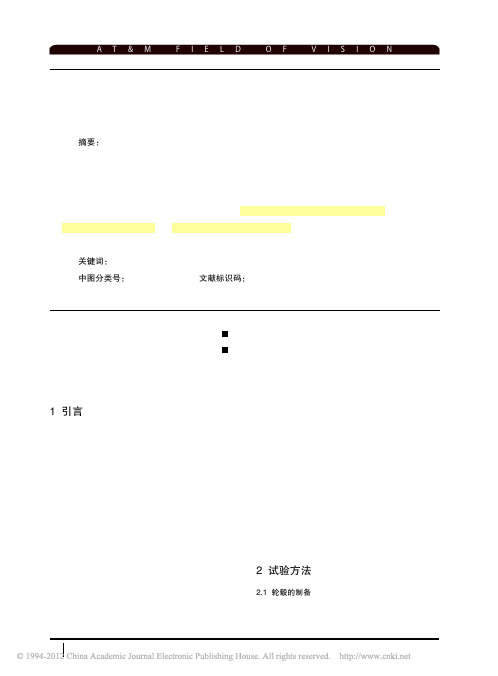
(上接第41页) 铆钉用量在5 000~8 000颗不等,平均按2元/颗计 算,仅铆钉材料成本一项就1万多元,这也是制约铝 合金客车普及的一个重要因素。
车身蒙皮的连接以粘接为主[4],在需要局部加强 的部位配以自冲铆,即粘接-自冲铆复合工艺[5],既 满足表面要求又保证了连接强度。
5 总结
观结构细化,二次枝晶臂间距较小;后凝固部分随着 保温时间延长,晶粒呈长大趋势,二次枝晶臂间距尺 寸增加。 3.2 拉伸试验
轮毂上、下轮缘在同一圆周方向上各取2个样 品,轮辐6个样品分别取自不同的辐条。相同部位不 同样品的各力学性能参数分别取平均值得出轮毂上不 同取样位置的抗拉强度、屈服强度和伸长率的对比关 系,见图3。
sintered Al-Si-Mg matrix composites[J]. Journal of Materials Engineering and Performance,1997,6(6): 785. [3]Atxaga G, Pelayo A, Iri sar ri A M. Effect of microstructure on fatigue behavior of cast Al7-Si-Mg alloy[J]. Mater Sci Tech ,2001, 17: 446. [4]Groteke D E, Designs Q C, et al. Influence of SNIF treatment on characteristics of aluminum foundry alloys [J]. AFS Transactions,1985, 181: 953- 960. [5]黄良余,张少宗. 铝合金精炼理论要点和工艺原则 [J] . 特种铸造及有色合金,1998,(2): 40- 42. [6]冉 广,周敬恩,王永芳. 铸造A356铝合金的拉伸性 能及其断口分析[J]. 稀有金属材料与工程,2006,35 (10):1620-1624. [7]张新梅,郝丽华,蒋大鸣,庞振民. A1-Mg-Si 合金 拉伸断口研究[J]. 材料工程, 1996, 5: 35-36,15.
xxx铝合金的微观组织(金相分析) 在线阅读

动态回复
ห้องสมุดไป่ตู้
动态回复应力 — 应变曲线
动态回复:位错的运 动与重组
7085 铝合金热变形中的动态回复
变形晶粒内产生等轴亚晶 组织
动态再结晶
7085 铝合金热变形中的动态再结晶
动态再结晶应力 — 应变曲线
动态再结晶: 形成大 角度晶界 + 长大
变形晶粒晶界处出现细小 等轴晶粒
7xxx铝合金的微观组织 (金相分析)
汇报人:XXX 指导老师:XXX教授
目录
一. 金相分析基础
二. 7xxx铝合金的微观组织(金相组织)
一. 金相分析基础
台式金相显微镜示意图
金相组织显示原理
试样中各组成相及其边界 具有不同物理化学性质, 利用这些差异转化为磨面 反射光强度和色彩的区别, 然后金相显微镜利用磨面 反射光的差异来成像
2. 1 多相合金的浸蚀
不同放大倍数下的珠光体 a)高倍 b)中倍 c)低倍
多相合金的浸蚀 ,除了有 单相合金反应特征外, 由 于组织中有明显的相组成 物, 电位差距较大,发生 相之间的电化学腐蚀 ,其 中一相被溶去一薄层 ,而 相界被浸蚀较深呈现凹坑, 结果在相与相界间相与相 间出现凹坑 ,从而显示出 相或组织
3. 5. 1 轧制变形铝合金的微观组织(典型组织)
等轴晶粒沿轧制方 向被拉长为纤维组
织
未溶相沿轧制方向 呈链状排列
7B50铝合金轧制变形态金相组织图 a )80% b) 90% c )95% d) 图b局部放大
部分晶界清晰 未溶相明显减少 出现再结晶晶粒
固溶时效后金相组织图
a )b )80% c )d )90%e )f )95%
铝合金的微观组织金相分析ppt课件

不同放大倍数下的珠光体 a)高倍 b)中倍 c)低倍
多相合金的浸蚀,除了有 单相合金反应特征外,由 于组织中有明显的相组成 物,电位差距较大,发生 相之间的电化学腐蚀,其 中一相被溶去一薄层,而 相界被浸蚀较深呈现凹坑, 结果在相与相界间相与相 间出现凹坑,从而显示出 相或组织
.
8
二. 7xxx铝合金的微观组织(金相分析)
热变形过程中,部分变形晶粒发生动态再结晶,形成变 形晶粒和少量再结晶晶粒混合组织
固溶过程中,温度较高,发生静态再结晶,再结晶比例 大幅增加 时效温度很低,合金一般不会发生进一步的再结晶
.
17
(2)铝合金中再结晶组织的表征方法:
OM分析:
用Graff Sargent腐蚀液进行腐蚀。此 种腐蚀液优先腐蚀晶界和亚晶界。
.
14
动态回复
动态回复应力—应变曲线
动态回复:位错的运 动与重组
7085 铝合金热变形中的动态回复
变形晶粒内产生等轴亚晶 组织
.
15
动态再结晶
7085 铝合金热变形中的动态再结晶
动态再结晶应力—应变曲线
动态再结晶:形成大 角度晶界 + 长大
变形晶粒晶界处出现细小 等轴晶粒
.
16
3. 4 变形铝合金中的再结晶组织 (1)铝合金中再结晶组织演变:
微观组织检测
固溶 + 时效
机理研究
.
性能测试
10
3. 7xxx铝合金的微观组织(金相分析) 3. 1 铸锭的金相分析
7136铝合金铸态金相组织照片
(1)晶界存在较多非平衡结晶相
(2)晶界较粗、弯曲(铸造缺陷多)
(3)存在过饱和固溶体(冷却速度快)
A356铝合金显微结构及拉伸断口分析_范宋杰
性能严重恶化 。图 2 (c) 是富铁相与共晶硅颗粒的 放大图 ,可以看到基体与共晶硅界面之间有细小裂 纹及很小的缩孔 ,细长的富铁相是断裂的 ,而不是连 续的 ,然而试样没有经过拉伸变形 ,也就是不是外力 使其断裂 ,有可能是由于热处理和热等静压过程中 , 基体相与共晶硅及富铁相的热膨胀系数不同导致局 部应力集中而形成的 ,而小缩孔则可能是由于初生
Analysis of The Microstructure and Tensile Fractogra phs of A356 Alloy
FAN So ng2jie1 ,2 , H E Guo2qiu1 ,2 , L IU Xiao2shan1 ,2 , XU Po1
(1. School of Materials Science and Engineering , Tongji U niversity , Shanghai 200092 , China ; 2. Shanghai Key Lab for R &D and Application of Metallic Functio nal Material , Shanghai 200092 , China)
参考文献 :
〔1〕Ejiofor J U , Reddy R G. Effect s of porous carbon on sintered Al2Si2Mg mat rix co mposites[J ] . Journal of Materials Engineer2 ing and Performance , 1997 , 6 (6) , 785.
基金资助 :国家自然科学基金资助项目 (50371063) ;美国通用汽车公司资助项目 ( RP - 07 - 159) ;教育部“新世纪优秀人才支 持计划”(NCET - 05 - 0388) 。
实验二 有色金属的显微组织观察与分析
实验一有色合金显微组织观察与分析一、实验目的1. 观察常见的铝合金、铜合金、镁合金及轴承合金等有色金属试样的显微组织特征。
2. 了解有色金属中合金元素对其组织和性能的影响。
二、实验说明(一)铝合金1.铸造铝合金:应用最广泛的铸造铝合金为含有大量硅的铝合金,即所谓硅铝合金。
典型的硅铝合金牌号为ZL102,含硅11~13%,在共晶成分附近,因而具有优良的铸造性能——流动性好,铸件致密,不容易产生铸造裂纹。
铸造后几乎全部得到共晶组织即粗大灰色针状的共晶硅分布在白亮色的α-Al固溶体基体上,这种粗大的针状硅晶体严重降低合金的塑性,因此通常在浇铸时向合金溶液中加入2~3%的变质剂,进行变质处理,合金共晶点向右移,原来的合金变成亚共晶,其组织为枝晶状初生α固溶体(白亮色)+细的(α+Si)共晶体(黑色),如图1-1所示,从而提高合金强度和塑性。
(a)未经变质处理(b)变质处理图1-1 铸造铝合金(ZL102)的显微组织500X2.形变铝合金:硬铝是Al-Cu-Mg系合金,是重要的形变铝合金,具有强烈的时效强化作用,经时效处理后具有很高的硬度、强度,故而称Al-Cu-Mg系合金为硬铝合金。
在Al-Cu-Mg系中,形成了CuAl2(θ相)、CuMgAl2(S相),这两个相在加热时均能溶入合金的固溶体内,并在随后的时效热处理过程中通过形成“富集区”、“过渡相”而使合金达到强化。
如图1-2所示。
(a)铸态(b)时效板材图1-2 硬铝(ZL12)的显微组织 100X(二)铜合金1. 普通黄铜普通黄金是Cu-Zn合金,其含锌量均在45%以下,根据Cu-Zn合金状态图,含锌量在32%以下的黄铜(如H80、H70)为α相固溶体的单相组织;而含锌量在32~45%之间的黄铜(H62、H59)则为(α+β)两相组织。
(1)α单相黄铜:含锌在36%以下的黄铜属单相α固溶体,典型牌号有H70。
铸态组织为α固溶体呈树枝状,经变形和再结晶退火,其组织为多边形晶粒,有退火孪晶。
铝合金解理断口
铝合金解理断口铝合金是一种常见的金属材料,具有较高的强度和良好的耐腐蚀性能。
在工程应用中,铝合金常被用作结构材料,用于制造飞机、汽车、船舶等各种工业产品。
在铝合金的加工和使用过程中,经常会出现断裂现象,即铝合金的断口。
本文将以铝合金解理断口为题,探讨铝合金断口的特点、成因和分析方法。
一、铝合金断口的特点铝合金的断口通常呈现出以下几种特点:1. 断口形状多样:铝合金的断口形状可以是平整的、粗糙的、呈现韧突的或者呈现韧性断裂的样貌。
2. 断口颜色明显:铝合金的断口颜色通常呈现出银白色或者灰黑色,有时也会有一些氧化物的颜色。
3. 断口表面有特征:铝合金的断口表面上常常可以观察到沿晶断裂、穿晶断裂或者韧突的特征。
4. 断口有裂纹:铝合金的断口上通常可以观察到裂纹的存在,有时甚至可以发现一些疲劳裂纹或者应力腐蚀裂纹。
二、铝合金断裂的成因铝合金的断裂通常有以下几个成因:1. 力学性质:铝合金的断裂与其力学性质有关,包括材料的强度、韧性、硬度等特性。
2. 加工工艺:铝合金在加工过程中可能会出现过度加工、变形不均匀、应力集中等问题,导致断裂。
3. 缺陷存在:铝合金中可能存在一些微观或者宏观的缺陷,如夹杂物、气孔、夹层等,这些缺陷会成为断裂的起始点。
4. 应力作用:外界应力的作用也是导致铝合金断裂的原因之一,如拉伸、压缩、弯曲等应力。
三、铝合金断口的分析方法对于铝合金的断口,可以通过以下几种方法进行分析:1. 断口形貌观察:通过显微镜观察铝合金的断口形貌,分析断口的特征,判断断裂类型和断裂机理。
2. 化学分析:通过对铝合金断口的化学成分进行分析,了解铝合金中的杂质含量以及可能存在的元素偏析情况。
3. 组织分析:通过金相显微镜观察铝合金的组织结构,分析晶粒大小、相分布、孪生等组织特征。
4. 断口硬度测试:通过硬度测试仪对铝合金的断口硬度进行测试,判断断裂的韧性和强度。
在进行铝合金断口分析时,需要综合运用以上多种方法,全面了解断口的特点和成因,从而准确判断断裂的原因,为改善铝合金的性能和提高产品质量提供依据。
铝合金复合板钎焊后微观组织观察实验报告
铝合金复合板钎焊后微观组织观察实验报告一、实验目的本实验旨在通过对铝合金复合板钎焊后的微观组织进行观察,了解钎焊对铝合金复合板微观组织的影响,为进一步研究铝合金复合板的加工和应用提供参考。
二、实验原理钎焊是指利用钎料与被连接材料之间相互扩散和溶解形成新的连接材料的一种焊接方法。
在铝合金复合板的钎焊过程中,由于不同材质之间存在着化学反应和扩散作用,因此会对铝合金复合板的微观组织产生影响。
三、实验步骤1. 首先准备好需要进行钎焊的铝合金复合板样品,并将其进行清洗和表面处理。
2. 将准备好的样品放入钎焊设备中,并按照设备要求进行操作。
3. 钎焊完成后,取出样品并将其进行切割。
4. 将切割后的样品进行打磨处理,使其表面平整光滑。
5. 使用光学显微镜对样品进行观察,并记录下所得到的结果。
四、实验结果与分析通过光学显微镜对铝合金复合板钎焊后的微观组织进行观察,可以得到以下结论:1. 钎焊区域的晶粒尺寸明显变小,且晶粒形状不规则。
2. 钎焊区域的晶界处存在着较多的气孔和裂纹。
3. 钎焊区域的化学成分发生了变化,出现了新的物质。
以上结论表明,在铝合金复合板的钎焊过程中,由于不同材质之间存在着化学反应和扩散作用,因此会对铝合金复合板的微观组织产生影响。
而这种影响主要表现为晶粒尺寸变小、晶界处存在气孔和裂纹以及化学成分发生变化等方面。
五、实验总结通过本次实验,我们深入了解了铝合金复合板钎焊后微观组织的特点和变化规律。
同时也发现,在铝合金复合板的加工和应用过程中,钎焊是一种非常重要的连接方法。
在实际应用中需要根据具体情况选择适当的钎料和工艺参数,以保证连接效果和材料性能的稳定。
- 1、下载文档前请自行甄别文档内容的完整性,平台不提供额外的编辑、内容补充、找答案等附加服务。
- 2、"仅部分预览"的文档,不可在线预览部分如存在完整性等问题,可反馈申请退款(可完整预览的文档不适用该条件!)。
- 3、如文档侵犯您的权益,请联系客服反馈,我们会尽快为您处理(人工客服工作时间:9:00-18:30)。
目录1 绪论 (1)1.1断口分析的意义 (1)1.2 对显微组织及断口缺陷的理论分析 (1)1.3研究方法和实验设计 (3)1.4预期结果和意义 (3)2 实验过程 (4)2.1 生产工艺 (4)2.1.1 加料 (4)2.1.2 精炼 (4)2.1.3 保温、扒渣和放料 (5)2.1. 4 单线除气和单线过滤 (5)2.1. 5连铸 (6)2.2 实验过程 (6)2.2. 1 试样的选取 (6)2.2.2 金相试样的制取 (8)2.2.3 用显微镜观察 (9)2.3 观察方法 (10)2.3.1显微组织的观察 (10)2.3.2 对断口形貌的观察 (11)3 实验结果及分析 (11)3.1对所取K模试样的观察 (11)3.2 金相试样的观察及分析 (12)3.2.1 对显微组织的观察 (12)3.2.2 断口缺陷 (15)结论 (23)致谢 (24)参考文献 (25)附录 (27)1 绪论1.1断口分析的意义随着现代科技的发展以及现代工业的需求,作为21世纪三大支柱产业的材料科学正朝着高比强度,高强高韧等综合性能等方向发展。
长久以来,铸造铝合金以其价廉、质轻、性能可靠等因素在工业应用中获得了较大的发展。
尤其随着近年来对轨道交通材料轻量化的要求日益迫切[1],作为铸造铝合金中应用最广的A356铝合金具有铸造流动性好、气密性好、收缩率小和热裂倾向小,经过变质和热处理后,具有良好的力学性能、物理性能、耐腐蚀性能和较好的机械加工性能[2-3],与钢轮毂相比,铝合金轮毂具有质量轻、安全、舒适、节能等,在汽车和航空工业上得到了日益广泛的应用[4]。
然而,由于其凝固收缩,同时在熔融状态下很容易溶入氢,因此铸造铝合金不可避免地包含一定数量的缺陷,比如空隙、氧化物、孔洞和非金属夹杂物等[5-7]。
这些缺陷对构件的力学性能影响较大,如含1%体积分数的空隙将导致其疲劳50%,疲劳极限降20%[8-9]。
所以研究构件中缺陷的性质、数量、尺寸和分布位置对力学性能的影响具有重要意义[10]。
而这些缺陷往往是通过显微组织和断口分析来研究的。
另外,通过显微组织和断口分析所得到的结果可以分析这些缺陷产生的原因,研究断裂机理,比结合工艺过程分析缺陷产生的原因,从而对改进工艺提出一定的有效措施,确定较好的生产工艺,以提高铝合金铸锭的性能。
但关于该合金的微观组织及其断口分析研究较少,研究内容深但不够综合,每篇论文多研究其部分缺陷,断口的获得多为拉伸端口。
因此,希望对A356铝合金的断口缺陷有一个较为全面的研究。
1.2 对显微组织及断口缺陷的理论分析铸件的力学性能与其微观组织有密切联系[11]。
A356合金是一个典型的Al-Si-Mg系三元合金,它是Al-Si二元合金中添加镁、形成强化相Mg2Si,通过热处理来显著提高合金的时效强化能力,改善合金的力学性能。
A356合金处于α-Al+Mg2Si+Si三元共晶系内,其平衡组织为初生α-Al+(α-Al+Si)共晶+Mg2Si。
其相图如右图1-1,在冷却时,由液相先析出α-Al铝,随着铝的析出,液相成分变至二元共晶线,发生共晶反应,反应式为:L→α-Al+Si (1)图1-1 铝硅镁三元共晶图由于A356的含Si量仅为7%,所以,液相成分在达到三元共晶点之前,液相消失,凝固完全。
凝固后的组织为初生α-Al基体+(α-Al+Si)共晶。
凝固后铝固溶体含有Si和Mg元素,在继续冷却过程中析出Si和Mg2Si(如图1-1)。
室温下的组织为初生α-Al、(α-Al+Si)共晶和Mg2Si。
冷却速度较快时,次生相Si和Mg2Si弥散细小不易分辩,而表现出α-Al和(α-Al+Si)共晶。
在实际铸造条件下(非平衡凝固),除基本相外,还可出现少量α-Al+Mg2Si+Si三元共晶体和杂质铁等构成的杂质相和一些复杂的多元共晶相[13]。
一般来说,铸造缺陷对构件的抗拉强度影响较小,但较显著影响构件的伸长率[14]。
A356铝合金内部缺陷主要有偏析、缩松、缩孔、气孔、针孔、非金属夹杂和夹渣、金属夹杂、氧化铝膜、白点等。
这些缺陷对其性能和强度有很大的影响。
因为生产铝锭的铝水是电解铝液,电解铝液的温度一般在930℃以上,是过热金属[15]电解过程产生的H2和AL2O3夹杂直接进入铝液中,会造成H2含量高和AL2O3夹杂多[16],H2产生气孔、气泡和白点缺陷的重要因素,AL2O3易形成夹渣;电解铝液中的杂质元素Fe、Si与合金中的Mn、Mg等元素作用形成Al-FeMnSi、Mg2Si等第二相,分布于晶粒内以及晶界处,影响基体连续性;铸造过程中由于清渣不彻底以及凝固过程中的选分结晶和冷却条件不当易于生成夹杂、缩松和缩孔[17];α-Al枝晶二次枝晶臂之间板片状共晶体是材料中最薄弱的区域,该区域中尺寸最大的Si颗粒首先发生断裂形成裂纹源。
由于以上因素的影响,A356铝合金容易断裂,从而影响其强度、塑韧性和力学性能。
若共晶Si呈灰色针状和片状,杂乱无章地分布在α-Al铝基体上,用光学显微镜可以看到铸造过程中的铸造缩孔、铸造气孔、氧化膜等缺陷。
1.3研究方法和实验设计大颗粒夹杂:用肉眼观察其存在形式、数量、大小和分布特点(存在区域)以及夹杂物本身的形貌和大小,并结合冶炼工艺分析其来源;检测杂质净化效果和晶粒细化效果。
显微夹杂:用金相显微镜和扫描电镜观察其存在形式、数量、大小和分布特点(存在区域)以及夹杂物本身的形貌和大小,并结合冶炼工艺分析其来源;检测杂质净化效果和晶粒细化效果。
对A356铝合金显微组织的观察主要用金相显微镜进行观察。
首先是取样:包括用长柄样勺从和料炉铝液、用短柄样勺从炉外取样以及取成品样,将取到的熔液倒入样饼模和K模得到样饼和K模试样,用上述取样方法选取不同工艺参数、不同生产阶段的试样。
将取得的试样通过切、车、銑、磨、抛等步骤制成金相试样,通过不同的放大倍率观察索取试样的显微形貌,并获得各个形貌的照片。
对于断口的观察所用试样是公司提供的,将试样断口处切下,在车床上将试样切成金相试样大小,然后通过粗磨、细磨、抛光、浸蚀制成金相试样,通过金相显微镜观察并记录观察到的缺陷,分析缺陷产生的原因。
1.4预期结果和意义1)结合企业生产需求,对A356铝合金进行金相及扫描电镜试验,对分布在初生α-Al基体上的共晶硅相、杂质相及气孔等进行观察,分析其分布特征、形貌及影响。
2)用扫描电镜观察铝合金断口形貌,并研究其断裂过程及机理。
3)将所观察的断口形貌进行分类。
2 实验过程此次实验分为三个步骤:1)生产工艺,主要是了解生产的概况,记录生产过程中的工艺参数;2)实验阶段,是关键步骤,要熟悉实验过程中的每个步骤,掌握所需的参数;3)观察方法,是对试样进行观察的总结。
2.1 生产工艺联信公司用的是魏桥铝厂提供的电解铝液,通过连铸生产A356铝合金铸锭。
该厂有四个和料炉,每炉装料量为30t,从南到北分别为1#炉、2#炉、3#炉和4#炉。
两条国内最大连铸生产线,单块铝锭规格:长:740mm;宽:105(95)mm;高:55mm;重量:约9.5Kg。
整跺铝锭规格:740×740×760mm。
每跺块数:93块。
详细工艺过程如下。
2.1.1 加料A356合金是一个典型的Al-Si-Mg系三元合金,主要成分是:Si6.5%-7.5%,Mg20%-0.40%,Cu≦0.20%,Zn≦0.10%,Mn≦0.10%,Ti≦0.20%,其他元素每种≦0.05%,其余是铝。
该厂主要生产A356.2铝合金,加料方法为:向和料炉中加铝水分为两次,真空包(最大铝量为9000㎏)运来铝水后用天车吊到炉前,打开和料炉炉门开始倒铝水,此时铝液温度在840℃-880℃,5min左右倒完,开始熔炼。
根据不同工艺设定熔炼温度和所要加的成及其用量计算加料量,如加硅、加镁、加钛、废铝锭等。
下表是A356.2铝合金的成分表。
表2.1 A356.2铝合金化学成份(%)Si Ti Mg Fe Cu Mn Zn P6.5-7.5 ≤0.20.30-0.45 ≤0.12 ≤0.1≤0.05 ≤0.05 痕迹2.1.2 精炼加料后为了快速均匀成分和温度,在和料炉中进行电磁搅拌。
搅拌时间在15-20min,根据不同工艺搅拌温度在690℃-740℃;炉内精炼是通过喷吹以氮气作为载体将精炼剂和清渣剂加入炉内的,氮气纯度大于等于99.995%,喷吹时间为5min-10min。
精炼剂和清渣剂的用量为0.1%-0.2%(与Al相比)。
精炼后取样分析,根据能谱仪结果判断各个元素含量是否合格,补加硅镁等矿石。
2.1.3 保温、扒渣和放料精炼结束后保温一段时间(一般在10min-15min),待温度均匀后开始扒渣。
该厂运用人工扒渣,扒渣时间在15min-30min,时间可长达40min,费时费力。
扒渣完成后静置5min,使成分和温度均匀。
待成分和温度符合放料条件时,打开和料炉炉门开始放料。
2.1. 4 单线除气和单线过滤铝液出和料炉后先进行在线除气,在经过过滤,之后进入结晶器开始连铸。
2.1.4.1 单线除气使用ALPUR-55旋转除气装置进行在线除气(图2-1)。
这种除气装置为双石墨转子,最大金属流量为55t/h。
ALPUR净化工艺是基于吸附净化原理,通过转子吹出精炼气体,借助旋转喷嘴产生均匀分布的微小气泡,并与反应室内的熔体充分接触反应使熔体净化。
精炼气体可以是氮气,也可以是氮气与氯气的混合气体。
图2-1 ALPUR净化铝熔体示意图2.1.4.2单线过滤过滤除渣主要是靠过滤介质的阻挡作用、摩擦力或流体的压力使杂质沉降或堵滞,从而净化熔体。
上述生产线采用CFF双级泡沫陶瓷过滤板,过滤箱安装2套平行过滤板,处理流量为55t/h。
过滤板为双层30/50ppi复合泡沫陶瓷过滤板,上层过滤板的孔隙度为30ppi,底层过滤板的孔隙度为50ppi。
CFF泡沫陶瓷过滤装置可以有效除去直径大于20um的夹渣物,过滤效率可达75%。
图2-2为泡沫陶瓷过滤装置工作示意图。
图2-2 CFF泡沫陶瓷过滤装里工作示度图2.1. 5连铸过滤后的铝液通过溜槽流入结晶器,浇铸机转速为863rpm-864rpm,开始结晶出来的坯壳先由人工导入足辊,之后进入校直段。
铝锭经过切定尺之后被切断。
铝锭的冷却是通过喷水冷却的,分三段冷却。
冷却水流速分别为0.137m/s、0.684m/s和1.478m/s;流量分别为133.7m3、401.1m3和883.1m3。
剪切后的铝锭通过机械手堆垛,最后捆扎。
2.2 实验过程对于显微组织及断口分析实验,主要工具是显微镜观察。
因此实验主要分三个步骤:1)试样的选取;2)金相试样的制备;3)观察记录。
2.2. 1 试样的选取取样时要注意取样阶段和参数,对各个试样的详细信息做记录。