第二章 机械加工精度及控制(5-7节)
机械加工精度控制
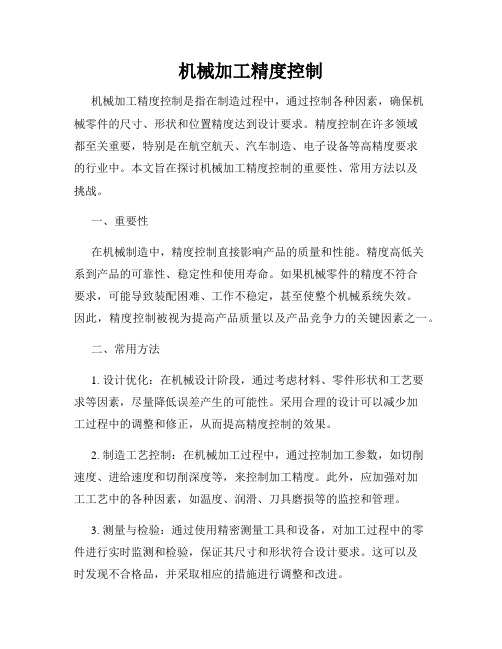
机械加工精度控制机械加工精度控制是指在制造过程中,通过控制各种因素,确保机械零件的尺寸、形状和位置精度达到设计要求。
精度控制在许多领域都至关重要,特别是在航空航天、汽车制造、电子设备等高精度要求的行业中。
本文旨在探讨机械加工精度控制的重要性、常用方法以及挑战。
一、重要性在机械制造中,精度控制直接影响产品的质量和性能。
精度高低关系到产品的可靠性、稳定性和使用寿命。
如果机械零件的精度不符合要求,可能导致装配困难、工作不稳定,甚至使整个机械系统失效。
因此,精度控制被视为提高产品质量以及产品竞争力的关键因素之一。
二、常用方法1. 设计优化:在机械设计阶段,通过考虑材料、零件形状和工艺要求等因素,尽量降低误差产生的可能性。
采用合理的设计可以减少加工过程中的调整和修正,从而提高精度控制的效果。
2. 制造工艺控制:在机械加工过程中,通过控制加工参数,如切削速度、进给速度和切削深度等,来控制加工精度。
此外,应加强对加工工艺中的各种因素,如温度、润滑、刀具磨损等的监控和管理。
3. 测量与检验:通过使用精密测量工具和设备,对加工过程中的零件进行实时监测和检验,保证其尺寸和形状符合设计要求。
这可以及时发现不合格品,并采取相应的措施进行调整和改进。
4. 质量管理系统:建立完善的质量管理体系,包括质量控制标准、工艺规范和检验要求等。
通过建立有效的质量保证措施,全面提高机械加工精度控制水平。
三、挑战机械加工精度控制面临许多挑战。
首先是技术难题,如高速加工、复杂形状零件等对机械加工精度提出了更高要求。
其次是装备条件限制,如设备刚性不足、磨损、热变形等会影响精度控制的效果。
此外,人为因素也是一个不可忽视的挑战,操作员的技能水平和经验对精度控制的结果有着重要影响。
为了应对这些挑战,需要不断加强技术研发,提高机械设备的精度和稳定性。
同时,加强人员培训和管理,提高操作人员的技能水平和质量意识。
此外,还应加强与供应商的合作,共同解决技术和设备问题,提高机械加工精度控制的整体水平。
机械制造工艺学课件:机械加工精度及其控制
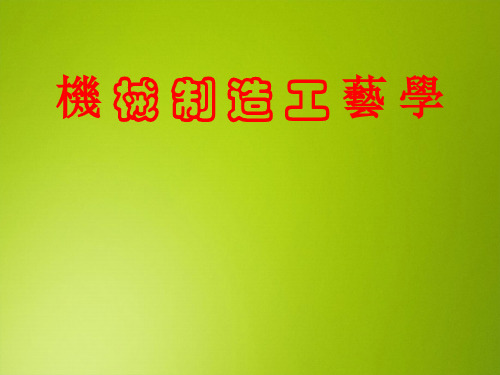
1)控制環境溫度 2)採用熱平衡措施 3)大型設備季節性的調整
4.1.6工件內應力對加工精度的影響
(1) 毛坯製造中產生的內應力
(2) 冷校直過程中產生的內應力
4.1.7 測量誤差
3.12測.量測條量件方儀的法器影的精響影度響的影響 1)測直人量接為儀與因器間素的接工測作量原、理接,觸製與造非精接度觸,測測量量、精主度動。與考 被慮測動“量測阿力量貝、原、視則靜力態”、。與分動辨態力測、量技、術絕水對準與、相責對任測心量等等。。 2)測量環境
48EI
y
L3
2)機床(夾具)部件的剛度
機床部件的變形曲線及其特點
機械製造品質分析與控制
(三次加載與卸載變形曲線的特點)
① 變形曲線是非線性的。不符合虎克定律,反映出 部件的變形不僅僅是彈性變形。
② 加載曲線與卸載曲線不重合。表明在加卸載過程 中有能量消耗。
③ 卸載後變形曲線不能回到起始點。表明在變形過 程中存在塑性變形和殘餘變形。
機械制造工藝學
機械加工精度及其控制
4.1 機械加工精度 4.2 工藝過程的統計分析
4.1 機械加工精度 4.1.1 概述
1.加工精度與加工誤差
機械製造品質分析與控制
加工精度是指加工後零件表面的實際尺寸、形 狀、位置三種幾何參數與圖紙要求的理想幾何參數 的符合程度。
加工誤差是指加工後零件實際尺寸、形狀、位 置三種幾何參數與理想幾何參數的偏離數值。
2. 加工經濟精度
機械製造品質分析與控制
指在正常加工條件下(採用符合品質標準的加工設備、 工藝裝備和標準技術等級的工人)所能保證的加工精度 和表面品質。
3. 原始誤差
機械製造品質分析與控制
加工精度概述及加工原理误差和调整误差
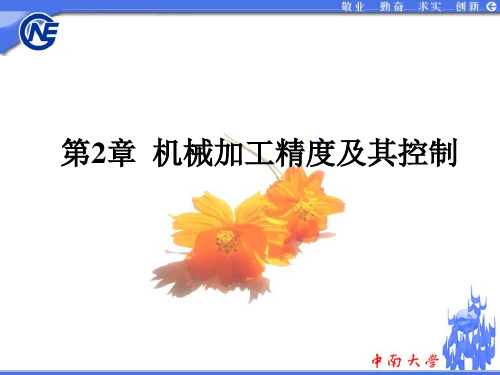
2.1 概述 2.1.1 机械加工精度 零件加工后的实际几何参数(尺寸、形状和表面的相互位置)与理 想零件的几何参数相符合的程度。 机械加工误差:零件加工后的实际几何参数(尺寸、形状和表面间的 相互位置)与理想零件的几何参数相偏离的程度。 包含3方面:尺寸精度、形状精度和位置精度。 联系:一般形状公差应限制在位置公差之内,而位置公差一般也应 限制在尺寸公差之内。
2.2.2 调整误差
由于调整不准确而产生的误差。工艺系统的调整有两种基本方式(M-2), 不同的调整方式有不同的误差来源。 1.试切法调整 试切法加工中,经过反复地试切、测量、调整,直至符合规定的尺寸要 求才正式切削整个待加工表面。这时引起调整误差的因素有以下3方面: (1)测量误差 指量具本身的精度、测量方法或使用条件下的误差(如 温度影响、操作者的细心程度)等;
(5)测量误差、工件毛坯内应力而引起的加工误差„ „
加工过程中可能出现的种种原始误差归纳如下:
图2 加工过程中的原始误差
2.1.3 误差的敏感方向 对加工精度影响最大的那个方向(即通过切削刃的加工表面的法向)
如图3,车削时工件的回转轴心是O,刀 尖正确位置在A,设某一瞬时由于各种原始 误差的影响,使刀尖位移到A′,则: 原始误差: δ =AA’
机械加工时,工艺系统的误差称为原始误差(“因”,根源),加 工误差是“果”,是表现。提高和保证加工精度的问题就是控制和减小 原始误差的问题。
2.1.2 影响始误差
上工序存在以下一些原始误差: (1)工件的装夹误差:包括定位误差和夹紧误差; (2)调整误差:包括夹具和定位菱形销的位置调整误差、对刀调整误差; (3)机床、刀具、夹具的制造误差; (4)工艺系统动误差:包括切削力、切削热、磨擦引起的工艺系统的变形和 磨损;
机械制造工艺与机床夹具 第2版 教学课件 吴年美 吴拓 第二章 机械加工精度
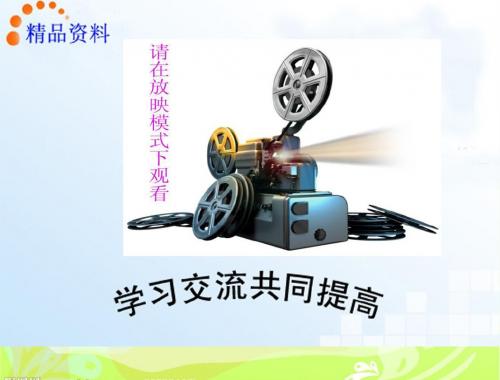
而且毛坯结构越复杂、壁厚越不均,散热的条件差别越大,毛坯内
部产生的残余应力也越大。
第二节 影响加工精度的因素及其分析
(2)冷校直带来的残余应力 直工艺进行校直。 某些刚度低的零件,如细长轴、曲轴和
丝杠等,由于机加工产生弯曲变形不能满足精度要求,常采用冷校
第二节 影响加工精度的因素及其分析
图2-12 冷校直引起的残余应力 a)冷校直方法 b)加载时残余应力的分布 c)卸载后残余应力的分布
教材其余课件及动画素材请查阅在线教务辅导网 在线教务辅导网:
QQ:349134187 或者直接输入下面地址:
第二章
机械加工精度
第二章 机械加工精度 第一节 概 述
第二节 影响加工精度的因素及其分析 第三节 加工误差的综合分析 第四节 保证和提高加工精度的主要途径
证工件位置精度的安装方法。
第二节 影响加工精度的因素及其分析
图2-1 原始误差
一、加工原理误差
第二节 影响加工精度的因素及其分析
加工原理误差是指采用了近似的成形运动或近似的切削刃轮廓进行 加工而产生的误差。 二、工艺系统的几何误差 1.机床几何误差 (1)机床主轴误差。 1)主轴回转误差。
图2-2 主轴回转轴线的运动误差
一、加工误差的性质 根据一批工件加工误差出现的规律,可将影响加工精度的误差因素 按其性质分为两类: (1)系统误差 (2)随机误差 在顺序加工的一批工件中,若加工误差的大小和方向 在顺序加工的一批工件中,其加工误差的大小和方向 都保持不变或按一定规律变化,这类误差统称为系统误差。 的变化是无规律的,称为随机误差,例如,毛坯误差的复映、残余 应力引起的变形误差和定位、夹紧误差等都属于随机误差。 二、加工误差的数理统计方法
机械加工精度

夹具安装法是指通过夹具保证工件加工表面与定 位基准面之间位置精度的安装方法。这种方法定位迅 速方便,定位精度高且稳定,但专用夹具的制造周期 长,费用高,因此主要用于成批、大量生产。
(3)机床控制法
机床控制法是指利用机床本身所设置的保证相对 位置精度的机构来保证工件位置精度的方法,例如坐 标镗床和数控机床等。
自动控制法生产率高,加工精度稳定,加工柔 性好,能适应多品种生产,是目前机械制造的发展 方向和计算机辅助制造(CAM)的基础。
2.形状精度的获得方法
(1)成形运动法
成形运动法是指使刀具相对于工件作有规律的 切削成形运动,从而获得所要求形状精度的方法, 如2.1节中所介绍的轨迹法、成形法、展成法和相切 法等。成形运动法主要用于加工圆柱面、圆锥面、 平面、球面、回转曲面、螺旋面和齿形面等。
(2)非成形运动法
非成形运动法是指通过对加工表面形状的检测, 由工人对其进行相应的修整加工,以获得所要求形状 精度的方法。非成形运动法生产率较低,但当零件形 状精度要求很高或表面形状比较复杂时,常采用此方 法。
3.位置精度的获得方法
(1)找正安装法
找正是指用工具或仪表根据工件上的有关基准, 找出工件在加工或装配时正确位置的过程。用找正 法安装工件称为找正安装。找正安装可分为划线找 正安装和直接找正安装两种。
试切法的生产率较低,对操作者的技术水平要求 较高,主要用于单件、小批量生产。
(2)调整法
调整法是指预先调整好刀具相对于工件加工 表面的位置,并在加工过程中保持这一位置不产率较高,对操作工的要求不高,但 对调整工的要求较高,主要用于成批、大量生产。
(3)定尺寸刀具法
一、尺寸、形状和位置精度
工件的加工精度包括尺寸精度、形状精度和位 置精度三部分内容。
2 机械加工精度及其控制
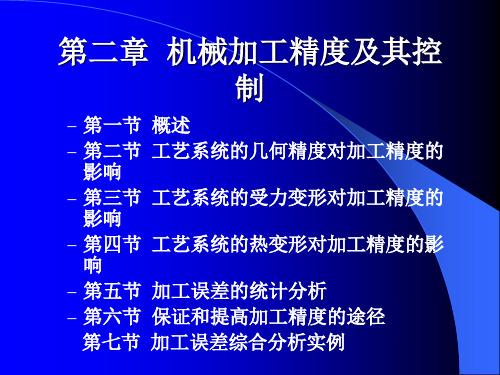
(尺寸、形状和表面间的相互位置)对理想 几何参数的偏离程度。
尺寸、形状和位置精度
零件的加工精度包含:尺寸精度、形状 精度和位置精度。
三者之间是有联系:
•形状公差应限制在位置公差之内,而位置误差 一般也应限制在尺寸公差之内 •当尺寸精度要求高时,相应的位置精度、形状 精度也要求高 •形状精度要求高时,相应的位置精度和尺寸精 度有时不一定要求高
因此,机床在安装时应有良好的基础。并严格
进行测量和校正,而且在使用期间还应定期复 校和调整
导轨磨损造成导轨误差
使用程度不同及受力不均,导轨沿全长上 各段的磨损量不等,并且在同一横截面上 各导轨面的磨损量也不相等。导轨磨损会 引起床鞍在水平面和垂直面内发生位移, 且有倾斜,从而造成刀刃位置误差。
减小导向误差的措施
直接保证工件在加工过程中的回转精 度而不依赖于主轴,是保证工件形状精度 的最简单而又有效的方法。 图2-18、2-19
(三)机床传动链的传动误差
1.传动链精度分析
– 传动链的传动误差是指内联系的传动链中首
末两端传动元件之间相对运动的误差。它是 螺纹、齿轮、蜗轮以及其它按展成原理加工 时,影响加工精度的主要因素。 – 由于所有的传动件都存在误差,因此,各传 递件对工件精度影响总和 为各传动元件所 引起末端元件转角误差的迭加:
统计分析法:
• 以生产中一批工件的实测结果为基础,运用数 理统计方法进行数据处理 • 质量有问题时,判断误差性质,找出误差规律 • 以指导我们解决有关的加工精度问题
第二节 工艺系统的几何精度对 加精度的影响
一、加工原理误差 二、调整误差 三、机床误差 四、夹具的制造误差与磨损 五、刀具的制造误差与磨损
Ry y
Rz (Z ) / D
第二章 机械加工精度及其控制
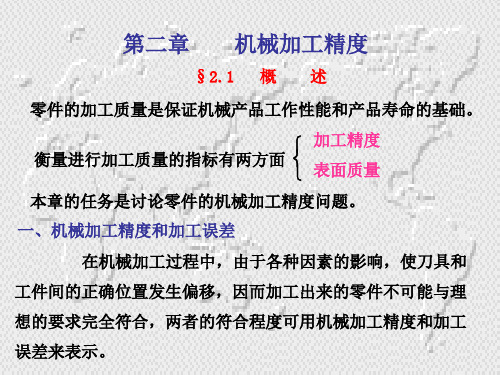
如图,车削时工件的回转轴线为O,刀尖正确位置在A。设某一瞬时 由于各种原始误差的影响,使刀尖位移到A’,AA’即为原始误差δ,它与OA间 的夹角为φ,由此引起工件加工后的半径由R0=OA变为R=OA’,故半径上的 加工误差△R 为:
可以看出:
当原始误差的方向恰为加工表面的法向方向(φ =0°)时,引起的加工误差最大; 当原始误差的方向恰为加工表面的切线方向(φ =90°)引起的加工误差最小。
1)用定程机构调整时,调整精度取决于行程挡块、靠模及凸 轮等机构的制造精度和刚度;
2)用样件或样板调整时,调整精度取决于样件或样板的制造、 安装和对刀精度;
3)工艺系统初调好以后,—般要试切几个工件,并以其平均 尺寸作为判断调整是否准确的依据。由于试切加工的工件数 (称为抽样件数)不可能太多,不能完全反映整批工件切削过程 中的各种随机误差,故试切加工几个工件的平均尺寸与总体尺 寸不能完全符合,也造成加工误差。
4. 主轴回转运动误差的影响因素
影响主轴回转运动 误差的主要因素
主轴的误差:制造 轴承的误差:圆度、波度(主轴颈与内孔) 轴承的间隙:影响油膜厚度; 与轴承配合零件的误差:轴颈和箱体轴承孔 主轴系统的径向不等刚度和热变形等
对于不同类型的机床,其影响因素也各不相同。(滑动轴承)
工
刀
件
具
回
回
(2)当形状精度要求高时,相应的位置精度和尺寸精度不 一定要求高。
4、加工精度与加工成本和生产效率的关系 一般地,加工精度要求↑ ,加工成本↑ ,生产效率↓ 。 5、研究加工精度的目的
研究加工精度的目的、就是弄清各种原始误差对加 工精度影响的规律,掌握控制加工误差的方法,以获得预期 的加工精度,必要时能指出进一步提高加工精度的途径。
机械制造工艺学第二章 机械加工精度及其控制
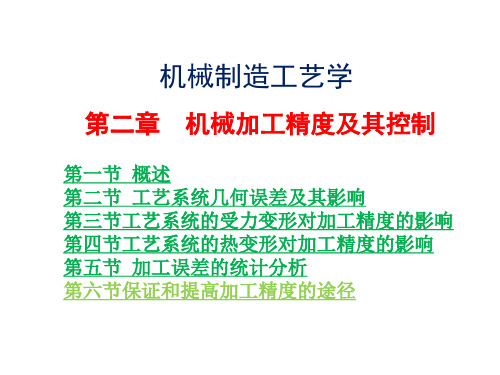
工 艺
k jc
FP y jc
, kdj
FP ydj
, k jj
FP y jj
, kgj
FP y gj
系
统 刚
kxt
Fp yxt
Fp
Fp Fp Fp
Fp
度
k jc kdj k jj kgj
分 工艺系统刚度计算
析 的一般式为:
kxt
1
1
1
1
1
k jc kdj k jj kgj
(二)机床部件的刚度测定
毛坯误差复映规律
ap Fp Yxt 加工误差
当毛坯有尺寸、形状误差或位置误差时,加工后工件仍会有 同样性质的加工误差。(每次走刀后加工误差将逐步减少) 以车削短圆柱工件外圆为例:
毛坯存在的圆度误差△m=ap1-ap2
工件产生圆度误差△g=y1 -y2
△m越大,△g越大
毛坯形状误差复映
工 切削分力Fp可表示为:
的 的变形量。该措施常用在各类轴承的调整中。
措
施
3)提高机床部件的刚度
减
小
工
艺
系
统
受
力
变
形
采用辅助支承提高
的 措
机床部件的刚度
施
4)工艺措施
减 合理选择切削用量、加工顺序,平衡大砂轮, 小 序前分选,变形补偿或变形转移等。
工 艺 系 统 受 力 变 形 的 措 施
变形补偿法
采用补偿或转移变形的方法
工艺系统的刚度会随着受力点位置的变化而变化。
细长零件:刚度低,工艺系统的变形主要取决于零件的变形。 (车削棒料会产生腰鼓形加工误差) 短粗工件:工件刚度较大,变形小,工艺系统的变形主要取决 于机床、刀架和刀具的变形。(车削棒料会产生鞍形加工误差)
- 1、下载文档前请自行甄别文档内容的完整性,平台不提供额外的编辑、内容补充、找答案等附加服务。
- 2、"仅部分预览"的文档,不可在线预览部分如存在完整性等问题,可反馈申请退款(可完整预览的文档不适用该条件!)。
- 3、如文档侵犯您的权益,请联系客服反馈,我们会尽快为您处理(人工客服工作时间:9:00-18:30)。
二级
三级 四级
工序能力勉强
工序能力不足 工序能力很差
二、分布图分析法
◆ 工件合格率估算
y
面积计算
0 TL
3σ
μ
x 3σ TU 公差带
Δ
T 工件合格率估计
【例题7.1】 检查一批在卧式镗床上精镗后的活塞销孔直径。图纸规定 尺寸与公差为
280 0.015 ,抽查件数n=100,分组数k=6。测量尺寸、分
d xmax xmin R k 1 k 1
d 组界: xmin ( j 1)d 2
( j 1,2,3,...... k)
各组中值: xmin ( j 1)d 3) 统计各组数据,整理成频数表
表2-2 分组数k的选定 n
k
25-40
6
40-60
7
60-100
30
28 30 50 38
36 49 51 38 34
36 52 32 42 38 40 44 34 42 47 40 36 20 16 53 30 49 18 38 38
表2-4 频数分布表
组号 组界(um) 中心值(x1) 1 2 3 13.5-18.5 18.5-23.5 23.5-28.5 16 21 26 频数统计 ┯ 一 正 ┰ 正 ┰ 一 频数 频率(%) 频率密度(%/um) 3 7 8 3 7 8 0.6 1.4 1.6
◆ 运用数理统计原理和方法,根据被测质量指标的统计性
质,对工艺过程进行分析和控制。
二、分布图分析法
(一)实验分布图(直方图)
加工一批零件,抽取其中一定数量的工件进行测量,这批 工件称为样本,其件数 n 称为样本容量。
由于随机性误差的存在,加工尺寸的实际数值是各不相同的, 在一定范围内变动,这种现象称为尺寸分散,用 x 表示。
y
0 差数模分布 z y
x
0
x
瑞利分布
二、分布图分析法
分布图应用
◆ 判断加工性质 判断是否存在明显变值系统误差; 判断是否存在常值系统误差及常值系统误差的大小。 ◆ 确定工序能力 工序能力 工序能力系数 式中 T——公差值 ;
CP T 6
σ——误差分布的标准差。
二、分布图分析法
2
4
6 8 10 12 14 工件序号 a)
控制限 公 差 带 T
ቤተ መጻሕፍቲ ባይዱ
-σ 0 μ
+σ z x(z)
x ~ N ( 0, 1 )
(z=0) 正态分布曲线
二、分布图分析法
分布函数
1 F ( x) 2
x
e
1 x 2
2
dx
y F(z)
F(x)— 正态分布曲线上下积分限间包 含的面积,它表征了 随机变量x落在区间 (-∞,x)上的概率。
公差带中心:
Am 60 0.025 60.025
直方图
1 n X X i 37.25m n i 1
S 1 n ( X i X ) 2 9.06m n 1 i 1
6S 6 9.06 54.36m
工件尺寸分散中心: 60 0.03725 60.037
分布图分析法的缺点
分布图分析法不能反映误差的变化趋势。
加工中,由于随机性误差和系统性误差同时存在,
在没有考虑到工件加工先后顺序的情况下,很难把随
机性误差和变值系统性误差区分开来。 由于在一批工件加工结束后,才能得出尺寸分布情 况,因而不能在加工过程中起到及时控制质量的作用。
三、点图分析法
4
5 6 7 8 9
28.5-33.5
33.5-38.5 38.5-43.5 43.5-48.5 48.5-53.5 53.5-58.5
31
36 41 46 51 56
正正┰一
正正正┰一 正正正一 正正正一 正正 一
13
26 16 16 10 1
13
26 16 16 10 1
2.6
5.2 3.2 3.2 2 0.2
◆ 形位误差的分布 差数模分布:正态分布大于零 的部分与小于零的部分对零轴线 映射后的迭加,如对称度、直线 与平面的平行度、相邻周节误差 等 瑞利分布:二维正态分布,在 只考虑平面向量模情况下转换成 为一维分布,如同轴度、直线与直 线平行度、端面圆跳动误差等( 不考虑系统误差) 瑞利综合分布:上述误差在考 虑系统误差的情况下,其误差分 布接近瑞利综合分布
样本尺寸或偏差的最大值与最小值之差,称为极差 R
R xmax xmin
把测得的数据记录下来,按尺寸大小将整批工件进行分组, 分组数为 k ,每一组中的零件尺寸处在一定的间隔范围内,组距 为 d 。同一误差组零件数量称为频数 mi,频数与样本容量之比称 为频率 fi。 mi R fi d n k 1
1) 单值点图
分析工艺过程的稳定性,通常采用单值点图。 工艺过程的稳定性: 1. 从误差角度分析: a)如果加工尺寸有波动,平均值和标准差S也波动,即使主要是随机 误差,系统误差影响很小→正常波动→工艺过程稳定。 b)如果加工中,有影响较大的变值系统误差,或随机误差明显变化, →异常波动→工艺过程不稳定。 2. 从数学角度分析: 如果总体分布参数(如μ,σ)保持不变→工艺过程稳定。
1
2 3 4 5 6
27.992~27.994
27.994~27.996 27.996~27.998 27.998~28.000 28.000~28.002 28.002~28.004
27.993
27.995 27.997 27.999 28.001 28.003
4
16 32 30 16 2
4/100
一、加工误差的性质
随机误差
◆ 顺序加工一批工件时,其大小和方向随机变化的加工误差为 随机误差。 ◆ 随机误差是工艺系统中大量随机因素共同作用而引起的。 ◆ 随机误差服从统计学规律。
◆ 如毛坯余量或硬度不均,引起切削力的随机变化而造成的加 工误差;定位误差;夹紧误差;残余应力引起的变形等。
加工误差的统计分析
结果分析:
部分工件的尺寸超出了公差范围,有17.47%的废品(工件的实际尺 寸分散范围0.012mm比公差带0.015mm小,也就是说实际加工能力比图
纸要求的要高:Cp=1.11,即T>6σ。
由于有△系统=0.0054的存在而产生废品,设法将分散中心调整到与公 差范围中心重合,具体的调整方法是将镗刀的伸出量调短些,以减少镗刀 受力变形产生的加工误差。
组间隔、频数和频率见表。求实际分布曲线图、工艺能力及合格率,分 析出现废品的原因并提出改进意见。
解: 零件实际尺寸分散范围: =最大孔径一最小孔径
组 尺寸范围 组中值Xj 频数mi 频率mi/n
活塞销孔直径测且结果
=28.04-27.992=0.012mm;
样本平均值(分散范围中心): 1 k X X i mi 27.9979 mm n i 1
16/100 32/100 30/100 16/100 2/100
零件尺寸公差为
T 0 (-0.015) 0.015
公差范围中心 常值系统误差
LM 28-
0.015 27.9925 2
系统 LM X 0.0054 mm
1 k ( X i X ) 2 mi 0.002244 mm 样本标准差 S n 1 i 1
y
(频数)
最大极限尺寸:
Amin 60 0.06 60.06
最小极限尺寸:
Amin 60 0.01 60.01
公差值:
T 0.06 0.01 0.05
13.5 10 (公差带下限) 37.25 (平均偏差) 35 (公差带中心)
x 58.5 (偏差值)
60 (公差带上限)
二、分布图分析法
◆ 非正态分布 双峰分布:两次调整下加工的工
y
件或两台机床加工的工件混在一起 平顶分布:工件瞬时尺寸分布呈
正态,其算术平均值近似成线性变 化(如刀具和砂轮均匀磨损)
0 y b)平顶分布 x 0 y a)双峰分布 x
偏向分布:如工艺系统存在显著
的热变形,或试切法加工孔时宁小 勿大,加工外圆时宁大勿小
工艺能力系数:
Cp
T 0.015 1.11 6S 6 0.002244
工艺能力勉强 查P76表2-5可得F=0.3253;
废品率:由 Z X X 28 27.9979 0.9358
S 0.002244
Q废品率 0.5-F 0.5 0.3253 0.1747 17.47%
§2.5 加工误差的统计分析
加工误差的性质 分布图分析法 点图分析法 机床调整尺寸
一、加工误差的性质
加工误差统计特性
加工误差 常值系统误差 系统误差 变值系统误差 随机误差
系统误差
顺序加工一批工件时,其大小和方向均不改变,或按一定规 律变化的加工误差为系统误差。
◆ 常值系统误差——其大小和方向均不改变。如机床、夹具、刀 具的制造误差,工艺系统在静力作用下的受力变形,调整误差, 机床、夹具、量具的磨损等因素引起的加工误差。 ◆ 变值系统误差——误差大小和方向按一定规律变化。如机床、 夹具、刀具在热平衡前的热变形,刀具磨损等因素引起的加工误 差。
如果总体分布参数(如μ,σ)发生变动→工艺过程不稳定。 本章介绍:单值点图和 x R 图
三、点图分析法
单值点图
工 件 尺 寸 0 控制限 公 差 带 T
按加工顺序逐个地测量一批
工件的尺寸,以工件序号为横 坐标,以工件的加工尺寸为纵
坐标,就可作出单值点图。
工 件 尺 寸 A O B A′ O′ B′