异常处理流程图
品质异常处理作业流程图

对异常品处置确 定意见。
对异常品处置进 行评审签字。
30分钟内不能对 异常排除,汇报 车间主任.
对异常内容调查 同时进行异常排 除.
组织专业人员,对 现场异常处理.
对异常品处置进 行评审签字。
在60分钟内异常 不能排除,汇报生 产部长.
生产部长
异常停线2H上报 公司副总经理.
项目
发现者
发现异常品时, 立即停止作业;
对异常品进行隔
作
离\标志,联络检
业
流
程
作业者在10分钟 内向班长汇报.
检验员 检验员对隔离 的异常品确认.
填写异常处理 联络单。
品质异常处理作业流程图
工程师
组织相关人员, 进行再发防止对 策的确立和实施
班长
车间主任
异常品处置损失 超过500元 ,汇 报质量部长批准.
异常现象排除在 2个小时内不能 解决时,换线组 织生产。
现场组织资源, 对异常现场处理.
NO.
质量部长
对损失大于500元 的异常品处置, 进行评审
异常品处置损失 超过2000元 ,上 报副总批示.
标记
更改内容
更改人
更改日期
批准
审核
编制
部门间异常联络处理流程图

品质管理科
其他相关部门
1、重大生产过程不良、品质异常 2、部门间管理联络对话窗口
1、人事招聘 2、员工考核 1、一般性生产过程不良、品质异常 2、入库相关事项
1、人事考勤
1、新品品质相关事项 2、模具维修相关事项
供应商
生产相关事项联络窗口
营业部
生产管理科
1、重大生产事项、品质事项 2、营业备货计划单据 3、部门间管理联络对话窗口
制造部长 NG
生产管理科长
NG
1、成品入库相关事项 2、原材料入库相关事项
生产车间主管 NG
1、模具维修 2、耗品购入
1、新品开发、生产相关 事项 2、模具设变事项
企划开发主管 NG
生产异常处理流程

3、装配部----每月初提交上月扣供应商的工时费用明细至副总助理处。
采购部----每月初提交罚供应商款项明细至副总助理处。
由总经办分析供应商当月因异常致罚款情况。
版本:
A
文件编号:
ZJB-06
生效日期:
2012.3.17
制作:
朱秀秀
审核:
批准:
生产异常处理规定
异常单处理流程图
规定
一、所有异常单任部门完成,否则发生的费用协助部门与责任部门各承担50%。
二、来料问题责任界定(品管部):
1、装配部所发出的来料异常(一个人能加工的可不写异常),PE通知品管及采购人员现场分析处理,责任则判定为品管部,但异常单上“责任部门确认和回复”一栏则填写供应商名称。
4、奖罚规定:
A、对于重复性发生的异常:每次罚款100元;
B、对于批量型不能生产的异常:当月只限3次机会,超过3次,罚款50元/次;
C、当月异常次数(A、B项总次数)合计在3次范围内,当月给予奖励150元。
三、设计问题责任界定(工程部):
1、生产线所出现设计异常,责任部门则判定为属工程部责任,PE协助改善;
2、责任人必须去跟踪落实到位并结案,处理方案必须注明协助部门需配合完成哪些具体事项;
3、奖罚规定:
A、老产品上线后设计问题出现的异常:当月只限3次机会,超过3次,罚款50元/次
B、新产品:不计罚款。(注:新产品涉及到的模具报废需进行处罚)
过程异常处理流程图

品质工程师根据品质数据判定是否可以结案
8
材料异常 NO
品质主管 由品质给出临时 方案并主导解决
异常信息传递
9 10 11 12 编制:吴烧威
效果验证
NO
O K
由责任部门给出长 期纠正措施
上报副总,组队 分析原因
依来料异常处 理流程处理
确定处理对策
NO 品质工程师以及巡检进行监督实施,并对效果确认
结案 审核:马文虎
工作内容
1、异常包括:1、巡检人员在首件检验不良、巡线过程发现工艺 纪律不符、产品抽检不良;2、生产人员在生产过程中发现的不 符合作业SOP或产品异常等; 2、生产过程中,生产班组长、员工以及品质巡检发现异常后应 立即向所属部门报告,经主管确认后发出《生产品质异常纠偏单 》; 2、IPQC将生产异常纠偏单交给品质工程师进行分析
步骤
IPQC
1
生产部
工作流程
过程异常处理流程图
工程\研发\QE
生产副总
SQE\IQC
开始
生产过程中发生异常 发出《生产品质异常纠偏单》 2
标识/隔 离
3
责任部门认定
4 NO
5
6
作业异常Βιβλιοθήκη 工艺/设计异常生产主管确认
工程主管确认
由责任主管给 出临时方案, 并现场指导
生产部按异常解决方案
7
处理异常,并记录损失
在确认异常后,由巡检立即对生产产品进行标识/隔离,必要的 需暂时停线
品质工程师对异常现象进行确认,并认定异常责任部门,涉及到 比较专业技能的内容需寻求品质主管或相关开发工程师进行分析
《异常处理流程》PPT课件

注:整个流程涵盖了PDCA管理循环及纠正预防的管理理念
23
部门责任的判定
开发部:
1.未及时确认零件样品; 2.设计错误或疏忽; 3.设计的延误; 4.设计临时变更; 5.设计资料未及时完成; 6.设计需要修改,设计人员未得到相关负责人的确认就安
1.由主要负责人召集. 2.最终处理报告完成. 3.小组成员认同效果确认结果,以及预防措施执
行.
12
问题处理流程(8-D模式)
13
8-D的成果:
8-D首重利用团队力量,因此无论是问题分析,或是对 策执行,都希望集众人之智,完成众人之事.
8-D特别注重以问题为经验,以对策为行动,所以在最 终处理过程中,对预防工作做要求.
8-D的内容都是运用QC七大手法、问题分析模式、 统计技朮等常用工具,作业质量要求能一致,且容易被 执行.
8-D依其步骤可设定处理成员与检核时限,对权责与 效果确认,是可以被严谨安排的,而且有利于追踪.
龙头分厂生产运作流程
产品部订单
订单评审
N 工艺评估
设备 人员
产能评估
N
主生产计划拟制 (装配调度)
追溯方式亦须告知.
6
问题处理流程(8-D模式)
5W2H提问技术: Why? 为何这样做,有无必要? What? 目的是什么? Where? 哪里做?有无更合适的地方? When? 时间安排好不好? Who? 谁来做?几个人做? How to do? 这样做法有沒有更好的? How much? 这样做的成本多少?
1.召集有关人员成立小组. 2.决定小组成员负责事项. 3.确定主要负责人.
4
问题处理流程(8-D模式)
异常处理流程图
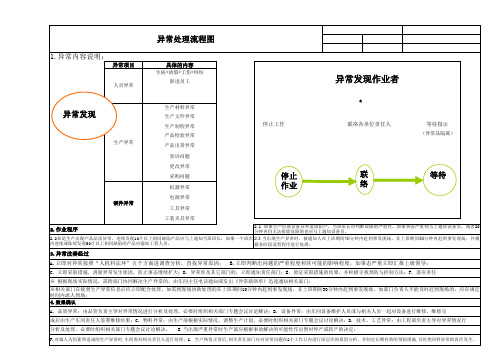
1.异常内容说明:
异常项目
人员异常
异常处理流程图
具体的内容 生病*请假*工伤*纠纷
新进员工
异常发现作业者
异常发现
生产异常
生产材料异常 生产文件异常 生产制程异常 产品检验异常 产品出货异常
停止工作
联络各单位责任人
等待指示 (异常品隔离)
客诉问题
更改异常 采购问题 机器异常
停止
联
等待
作业
络
硬件异常
电源异常 工具异常
A. 品质异常:由品管负责主导对异常情况进行分析及处理,必要时组织相关部门专题会议讨论解决;B. 设备异常:由车间设备维护人员或与相关人员一起对设备进行维修,维修完
成后由生产车间责任人签署维修结果;C. 物料异常:由生产部根据实际情况,调整生产计划,必要时组织相关部门专题会议讨论解决;D. 技术、工艺异常:由工程部负责主导对异常情况行
内连续或陆续发现50片以上相同缺陷的产品应通知工程人员。
据各阶段流程程序进行处理;
3.异常改善经过
A.立即对异常按照“人机料法环”五个方面进调查分析,杳找异常原因; B.立即判断出问题的严重程度和其可能的影响程度,如事态严重立即汇报上级领导;
C. 立即采取措施,消除异常发生原因,防止事态继续扩大;D. 异常涉及其它部门的,立即通知责任部门;E. 验证采取措施的结果,并积极寻找预防与控制方法;F. 落实责任
※ 根据现场实际情况,需跨部门协同解决生产异常的,由车间主任电话通知或发出《异常联络单》迅速通知相关部门;
※相关部门在接到生产异常信息后应立即配合处理,如需到现场协助处理的在上班期间10分钟内赶到事发现场,非上班期间30分钟内赶到事发现场。如部门负责人不能及时赶到现场的,应在规定 时间内派人到场; 4.效果确认
异常处理流程图
问题处理
品管部 各责任部 门
品管部 责任部门 人员
人员从接 到通知到 达现场时 间:10分
首件/巡 检记录/ 生产日报
钟
填写临时对策 填写纠正预防对策 对改善措施的跟进验证结果 处理结果知会相关单位
各责任部门现场对异常进行确认、分析, 制定临时对策方案,并将异常情况通知到 PMC/采购部。
各责任部 门
/
流程结束
/
/
/
序 号
流程图
检验准备
异常处理流程图
工作重点
流程开始
责任部门 责任岗位 时效性 相关表单
/
/
/
/
进料异常 物料异常
制程异常
异常 判定 填写异常联络单 作业异常
转序异常 继续作业
对物料的进料、生产制程及本单位生产完 成后的转序阶段,依相关的标准文件进行 品保部 检验和记录
1.品管人员依据相应的标准及严重程度进 行判定,可放行的继续下一工位,自己无 品质部 法判定或需要协助的呈报品质主管判定。
IQC PQC FQC 作业员 班组长
IQC PQC FQC
/
/
立即处理 /
技术异常
品管课长对问题再次确认和判定,可接受 进行下一工位,不可接受的要求QC对问题 进行统计描述,填写相关异常单。 2.品管课长对问题性质进行判定,并通知 相关责任部门到现场对问题进行分析和处 理。 3.各相关部门人员在接到通知后在规定时 间内到达现场对问题进行分析。(如出差 应指定代理人处理)
各责任部 分人员
30分钟
品质部备案,并由责任部门对异常问题填 写纠正与预防措施具体内容
责任部门
责任部门 人员
24小时
由品管部对验证暂时对策、纠正与预防措 施具体内容,并填写验证结果。验证OK后 存档。
异常处理汇报流程图
3分钟以内
设备组/行政部人员 确认原因及处理方
案
5分钟以内
备 注: 1.G.H项异
常 2.处E项理异完常毕 处理完毕后
预计6小时后会延 误
60分钟内仍未恢复 正常
10分钟以内
3.A.B.C.D 项处理完毕 后于次日 内,责任部 门将异常原 因改善对策 及处理结果 提报至副总 经理室. 4.F.项异常 处理完结后 于次日内, 生产部将异 常原因改善 对策及处理 结果提报至 计划部. 5.所有异常 当日未处理 完毕,相关 主管不得离 开. 编 制:
20分钟以内未恢复
生产部主管
60分钟以内未恢复 正常动作
工程部
主管
120分钟以内未恢复
品质部主管
正常动作
计划部主管
180分钟以内未恢 复正常动作
D
待治工具/ 原物料
FPC到当前站前12 小时仍待治工具/
原物料
生产部\采购部
FPC到站前6小时仍 待治工具/原物料
生产部主管 工程部主管 采购部负责人 计划部主管
异常处理汇报流程图
A
不合格品异 常
发现问题即上报
工艺
确认
FPC 30分钟未有处理结 生产部主管 同样总是点连续两
果
计划、品质主管
批板(含)
体系异 常
12小时内未恢复
品保部体系工程师
24小时内未恢复
质保部负责人
36小时内未恢复
48小时内恢复
管理者代表停 产整顿
C
工艺工程异 常
审核:
批准:
预计一天后会延误
市场部主管 计划部主管
预计6小时后会延误
设备部与生产部主
G
停水/电/气
制程异常处理流程图
注:执行日期以会签日期为准。
制常的通知部门及上报部门,有各分厂长知会技术部人员处理和对异常的预判, ②各部门协同配合,并遵循上下级式管理,技术部人员或现场检验员只需与责任分厂厂长进行沟通,一 直认可后,具体的指令下达则由分厂长直接对下级下达, ③现场操作人员若切实有其它造成重大异常的原因,各部门应充分分析其原因,给予判断,责任划分时 需如实考虑。 会签:
NG OK
由技术部、质保部、生产部共同分析原 因,确定责任部门或责任人并由质保部 开出《纠正措施预防表》 OK N G 责任部门或个人依据《纠正措施预防表 》的要求进行临时措施的实施 OK 检验员或技术人员对效果的确认
OK 质保部进行验证,并确认改善 效果 OK
责任厂长签字确 认
正常生产
OK 技术部制作“受控文件”即永久预防措 施 N G OK 质保部跟踪验证最终效果并判断异常是 否能关闭 OK 结案、归档
制程异常处理流程图
现场检验员/操机人员发现异常
轻微可立即纠正的异常 OK 通知班长或厂长判断是否可以 继续生产 NG
重大异常/或明确异常根本原因 OK OK 检验员开具《半成品首检巡检记录单》 或《装配厂反馈问题处理跟踪表》,由 班长或操机人员对不良品进行隔离并标 示
OK
技术部、质保部、生产部共同 给出处理措施与预防方案
品质异常处理作业流程图
客诉处理流程客户投诉作业流程客 户不满意无效有效满意8.2MRB会议流程:供应商相关部门总经理品质部工程,工艺品质工程师发生客户投诉(不符合)客户投诉信息的反馈接获客户投诉信息依投诉内容对不符合进行追溯与确认跟踪不良设备的返回原因分析及提出对策并整理成书面资料回复品质部对策实施资料汇总/整理回复投诉单位跟踪/确认/评估对策实施的有效性开立《不符合改善对策表》结案客户满意度调查来料检查反馈或制程反馈NOYESNOYESNGOKOK8.3制程异常处理品质部品质经理生产部相关部门工程/开发开品质异常单QE 工程师确认与追溯各部门会签MRB 最终判定异常单COPY 各相关单位不合格批处理标示/隔离/退货/特采/报废QE 评估是否立案并转入MRB开不符合改善对策表COPY 供应商供应商分析原因,提出对策QE 确认/评估对策的符合性QE 确认改结案制程异常反馈YES NOYESNO开品质异常单QE 工程师确认不符合事实QE 工程师确认品质QC 对不良进行确认,对不良品及嫌疑品进行围堵必要时附测试报告(可靠,检验过程的)初步确认分析制程不良提出对策并实施;书面回复品质部初步确认分析不良产生原困分析不良产生原因提出对策并实施;书面回复品质部QE 整理异常报告相关部门会签对策实施效果追踪与确认最终判定与批示结案.客诉不良品的返1.品质接到客户的2.品质窗口为定品3.DOA,RM A,客诉由4.对于功能的确认5.批量返工,由工6.对于客诉的严重1.来料产品规格书是工程承认后,给到IQC;2.品质将主导MRB会议的召开;1.首检由生产送检,生产,工程,品质签字确认;2.合同评审的评审时必须对客制化信息进行确认,工程下达SOP 给到生产,品质;;3.品质根据客制化信息制定检验标准4.品质对应只是生产部门,工程部门对生产部门的工艺,产品异常负责;生产的变更1.客户的变更及客户的客制化信息变更工程必须下达给到生产,品质人员;2.品质设3.不能解决的问4.一码多料问题,由PMC整理后,在总监会议进行检讨;最终判定重大品质异常1.批量异常(同样问题5%以上)2.。