工厂精益精益布局PPT课件
第五章:精益生产--精益布局
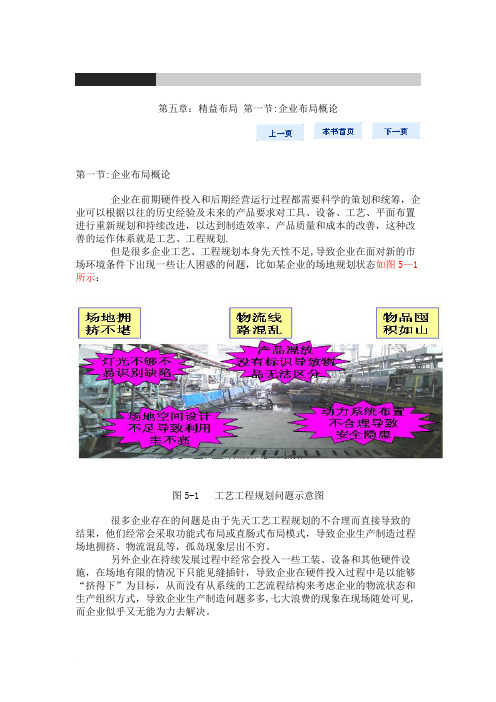
第五章:精益布局第一节:企业布局概论第一节:企业布局概论企业在前期硬件投入和后期经营运行过程都需要科学的策划和统筹,企业可以根据以往的历史经验及未来的产品要求对工具、设备、工艺、平面布置进行重新规划和持续改进,以达到制造效率、产品质量和成本的改善,这种改善的运作体系就是工艺、工程规划.但是很多企业工艺、工程规划本身先天性不足,导致企业在面对新的市场环境条件下出现一些让人困惑的问题,比如某企业的场地规划状态如图5—1所示:图5-1 工艺工程规划问题示意图很多企业存在的问题是由于先天工艺工程规划的不合理而直接导致的结果,他们经常会采取功能式布局或直肠式布局模式,导致企业生产制造过程场地拥挤、物流混乱等,孤岛现象层出不穷。
另外企业在持续发展过程中经常会投入一些工装、设备和其他硬件设施,在场地有限的情况下只能见缝插针,导致企业在硬件投入过程中是以能够“挤得下”为目标,从而没有从系统的工艺流程结构来考虑企业的物流状态和生产组织方式,导致企业生产制造问题多多,七大浪费的现象在现场随处可见,而企业似乎又无能为力去解决。
我们来看一家企业的生产现场布局结构模拟图5-2所示:图5-2 传统布局结构运行示意图通过对企业的现状布局结构进行改善,分析过程的七大浪费环节,建立一个流畅、精益的布局规划,从而为企业实现单件流模式提供条件,如图5—3所示。
图5-3 现代布局结构运行示意图精益专家解析:传统布局结构没有考虑到生产制造过程中的工艺路线的紧密程度和生产组织过程中的流动要求,严重制约着企业精益物流的运行和精益制造模式的建立,对企业生产制造现场的管理带来了很大的难度,现场混乱不堪、物流资源耗费巨大、场地拥挤无序等现象严重阻碍了“单件流”的实现,整个制造周期由于传统的布局结构而无法得到有效改善。
企业可以用“单件流”的思想实现企业现场精益布局来克服企业制造过程中所面对的问题.【读书心得】第二节: 传统布局解析国内很多企业是在社会主义市场经济刚刚建立之初才组建起来,在特定的历史环境条件下,企业面对的市场环境比较特殊,没有激烈的竞争压力,产品系列比较单一,生产规模比较小,在公司筹建的过程中没有对设备、厂房等硬件的配置和布局进行整体规划。
精益工厂布局方案ppt课件
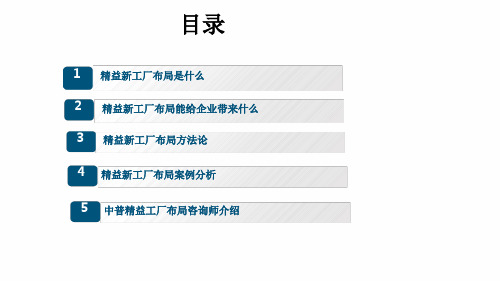
子行业)
面积:40000平方米(旧+新厂); 周规期划::15年80战天略布局 特色: Cell化,垂直整合
案例分享:CP集团新旧厂布局改造 (电子 行业)
节约指标
物料搬运距离 物料搬运停滞点 物料搬运交叉点 单位面积产出 生产周期 在线库存WIP
改善前
1800米
21 23 5000RMB/平方米 21天 80万
Lean Manufacturing
精益生产
从开发,接单到发货 整个过程的一切活动
Demand Pull 需求拉动 按用户需求生产
消除瓶颈 TOC 象河流一样 顺畅流动
Value Flow 价值流动
降低成本, 改善质量, 缩短生产周期 【明确瓶颈】 消除浪费, 创造价值
精益工厂布局方法论3:关于瓶颈管理TOC的九大原则
目录
1 精益新工厂布局是什么 2 精益新工厂布局能给企业带来什么 3 精益新工厂布局方法论 4 精益新工厂布局案例分析
5 中普精益工厂布局咨询师介绍
精益工厂布局是什么?
? 在新经济时代,企业面临用户对产品及服务极具个性化要求且需求数量少而精,竞争对手全球化的 环境。企业除了技术创新突破,管理变革,还得大力推行精益管理,提升企业自身的软实软力和核心 竞争力。而精益工厂布局是企业推行精益的综合反映之一。
原则l 追求物流的平衡流畅,而不是生产能力的平衡。追求生产能力的平衡是为了使企业的生产能力得到充分利用。
原则2 “非瓶颈”的利用程度不由其本身决定,而是由系统的“瓶颈”决定的。瓶颈资源制约着系统的产出能力,而非瓶 颈资源的充分利用不仅不能提高产销率,而且会使库存和运行费增加。
原则3 资源的“利用”U(tilization)和“活力”A(ction)不是同义词。利用是资源应该利用的程度,活力是指资源能够 利用的程度。
layout(工厂布局)(课堂PPT)
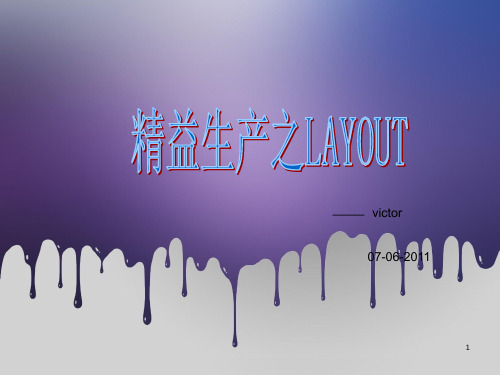
2020/4/7
4
种类
目的
特征程分析
的工艺流程
作业流程分 主要分析作业
析
者的作业流程
2020/4/7
多人通过多 台设备制造 同一产品
一人通过不 同设备或不 同工序,制造 多个产品的 过程
(1).改变包装作业流 程
打保证书
贴标签
品 质 部 出 库
2020/4/7
数外 搬
输
量观 运
入
检检 至
机
查查 电
身
脑
号
处
包
传
封
装
送
箱
加
工
改善后包装作业流程图
搬储 运存 至 成 品 仓
17
2.改变车间布局
品质部开关盒储存区
辅料存放区
包装车间开关盒 临时存放区
电脑输入出
保
证 书
包装LINE A
打
印
包装LINE B
(1).Leadtime
A.Leadtime的定义
从客户下订单到工厂交货,这个过程所花费的时间就是leadtime, 即完成某项目标所花费的流程时间
B科特尔法则
Leadtime=存货数量×生产节拍或存货数量×生产能力
C. 生产节拍
生产节拍是指每生产一个产品所需要的间隔时间
例如:一台设备的生产能力是每小时生产120个产
P4
P6
P9
P5
P7
P8
P10
工序8
产品分族矩阵
2020/4/7
33
生产线排单: Line A:生产P1产品 Line B生产P2产品 Line C生产P3产品 Line D生产P4 P6 P9产品 Line E生产P5 P7产品 Line F生产P8 P10产品
精益生产(经典完整)ppt课件

• 多品种小批量
• 订单拉动
• 准时化
• 连续流
6
制造业面临的环境
➢ 快速并准时交货 ➢ 需求品种增加,特殊定制 ➢ 不断改进质量及降低销售价格 ➢ 产品的生命周期越来越短 ➢ 无国界,中国成为世界工厂 ➢ 紧缩与通胀
问题:如何面对环境挑战?用存货?
精选ppt课件2021
7
Lean -“精益”释义
13
业务流程中的八大浪费
➢ 计划不周 ➢ 信息不全 ➢ 过程不当 ➢ 沟通不畅 ➢ 调整审批 ➢ 检验返工 ➢ 批量等待 ➢ 动作技能
精选ppt课件2021
14
从增值比看改善的空间
增值比率 =
增值时间(Value added time) 制造周期(Manufacturing cycle timXe)100%
起源于20世纪50年代丰田汽车公司,而在80年中期被欧
美企业纷纷采用。随着微利时代的来临,精益生产模式 成为企业竞争的有力武器
精选ppt课件2021
5
制造系统演化史
手工生产 大批量生产 精益生产
?
精选ppt课件2021
Henry Ford
福特首创装配线
• 大规模 • 低品种 • 工人被当成机器
TPS 和 大野耐一
案例分享 模拟演练 讨论
精选ppt课件2021
3
1Lean Manufacturing System Briefing
精益生产系统简介
➢ 制造系统的要点
➢ 精益生产五项原则
➢ 精益企业之屋?
精选ppt课件2021
4
Lean Thinking and Lean Manufacturing System 精益思维和精益生产系统
layout(工厂布局)ppt课件
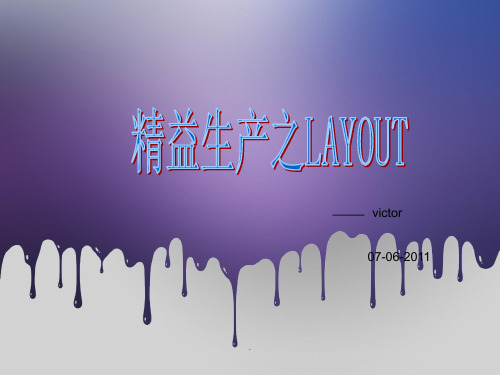
某公司产品P-.Q分析法
如上图式,按照2/8原则,可以将P1,P2,P3设计为专用生产线, 因为其量大,这样可以稳定生产,减少切换,提高品质效 率.P4~P10根据其工艺流程利用"产品分族矩阵"进行分析
分析后产品分族矩阵图
.
从上图可知: P4,P6,P9产品的工艺几乎相同 P5,P7产品的 工艺几乎相同 P8,P10产品的工艺几乎相同
.
二. 精益Layout设计原则
统一的原则 最短距离的原则 人流,物流畅通的原则 充分利用立体空间的原则 安全满意的原则 灵活机动的原则
.
三. Cell(单元)生产线布局
Cell生产式layout主要是对企业各类产品进行分类,以 相同的加工工艺流程作为一条生产线进行的layout设计
(1).Leadtime
一.Layout的定义
Layout的中文名称是“布局”,简单的说布局 就是对设备,作业台,物料,工装,半成品, 水,电,气等的综合配置。主要研究工序之间, 车间之间,部门之间及工厂整体的设备,作业 台,材料,仓库等配置与放置的合理性,已达 到整个生产系统人流与物料畅通化,流程最优 化,效率最大化的目标
螺丝 框架
B
焊接10
B单元生产人数 =40/5=8人
焊接10
#代表组
S铁芯 A
10
A单元生产人数 =10/5=2人
5
螺丝
底板
15
10
C
导线
C单元生产人数 =10/5=2人
.
Q1
某工厂收到一产品订单数量为20个,该产 品中间周转库存分别为500,600,和300个在 制品,该工厂有A,B,C三个工序,三个工序 生产能力相同,都是1秒/个,请问 1),生产该20个产品的生产周期要多少时间? 2),A,B,C三道工序的加工时间要多少时间?
精益生产(完美版)(PPT109页)
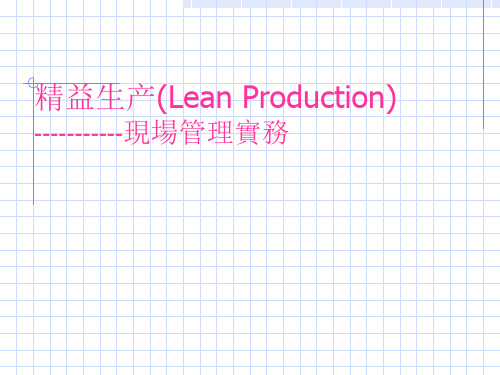
(3)消除浪费——管理的重要目的之一
Management
创造性的管理活动 提高产品和服务的附加价值
+1 增加价值
0
-1
消除浪费
最大限度地减少不增值劳动 封闭性的管理活动
精益思维(Lean Thinking)的5个基本原则
No.1 从顾客的角度而不是从某个公司、部门或机构 的角度确定价值;
No.2 确定设计、采购和生产产品的整个价值流中的 步骤,找出不增加价例 能力需求:100件/H
项目 能力 达成率 奖金 效率
工序1 100件/H
100% 标准产量奖金 个别效率合格
工序2 125件/H
125% 125%奖金 个别效率高
工序3 80件/H
80% 0
个别效率低
工序4 100件/H
80% 0
个别效率低
≠ 个别效率
整体效率
专业化作业有利于提高个别效率,不少企 业因此实行计件工资。
精益生产(Lean Production)
-----------現場管理實務
第一部分 精益生产簡介
很多精益技术源于日本企业的生产管理方法, 如看 板管理、全面质量管理(TQM)、快速换模等技术 都是 在丰田等日本公司的生产管理(NPS)中产生的。美国 的丹尼尔·琼斯教授等人通过大量细致的研究,并与 当 时欧美大量生产方式相比较后得出结论,正是这 些生 产管理方式使得日本企业(如丰田汽车公司)迅速成为 世界级的公司。这些管理思想和原则就是精益生产。
· 三不主义
77个个““零””目目标标 不良
保证
不良率高企, 批量事故多发, 忙于“救火”
· 零缺陷运动 · 工作质量 · 全员质量改善活动 · 自主研究活动 · 质量改善工具运用
精益生产培训课件(PPT 63页)
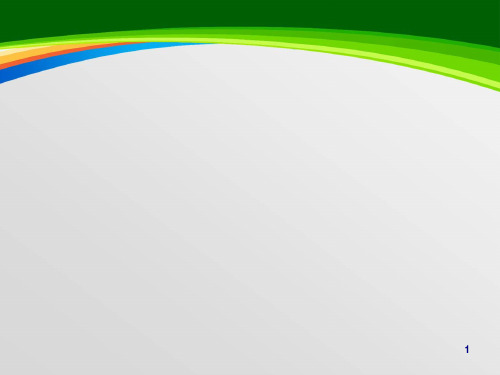
售价
成本
售价维持
5
课程指引
工业及精益生产发展历史背景
1
世界工业发展历史
2
丰田背景及模式(TPS)形成与发展过程
3
精益管理形成过程
4
工业革命与中国产业复兴差距
6
工业发展史
第一次工 业革命
18世纪60年代至 19世纪70年代
第二次工业 革命
19世纪70年代至 20世纪初
第三次科技 革命
自20世纪40~50 年代开始
定义:任何超过客户或者后道作 业需求的供应
产生原因:
•视库存为当然
•生产能力不稳定,设备配置不当或设备
能力差 •大批量生产,重视稼动 •物流混乱,呆滞物品未及时处理 •提早生产,不必要的停机 •无计划生产,生产计划不协调 •客户需求信息未了解清楚 •生产换型时间长
29
第一部分 准确识别工厂浪费
III.“七大浪费”之详介
1
第二部分 精益技术生产体系
生产方式发展的历史
工匠 单件生产
• 低产量 • 高技术工人
敏捷生产
• 整个价值链和
精益生产 供应链的协调
• 建立在同步化批 反应
同期化
量生产基础上 • 精益概念在非
批量生产 • 强调降低生产反 生产领域及整
大规模 批量生产
• 生产按照产品 应周期和库存
集中分类 • 强调资产和资源
是指通过系统结构、人 员组织、运行方式和市场 供需等方面的变革,使生 产运营系统能快速适应客 户不断增长的需要,达到 企业与市场最佳的双盈效 果。
10
精益生产的特点:
消除一切浪费,追求精益求精和不断改 善。精简并消除一切不增值的岗位。精 简产品开发设计,生产,管理中一切不 产生附加值的工作,以最优品质,最低 成本和最高效率对市场需求作出最迅速 的响应。
精益管理 工厂布局

Lean Layout精益管理(Lean Management)精益工厂布局管理Lean Layout1. 布局简介: 布局(Layout),是一个组织为实现其工作目标、效益最大化,对其工艺、部门、设施设备和工作区进行的规划和实际定位、定置。
2. 布局的意义: “结构决定功能”,每一种产品由于设计结构的差别,所具备的功能也不尽相同。
任何一个组织如果没有响应的组织架构,就不会具备相应的业务功能,达到相应效率 和产出相应效益。
所以,没有合理的布局和流程,就不可能造就高效的生产系统。
Lean Layout3. 布局的目的:人:提高工作热情;减少不必要的动作和走动。
材料:减少材料、产品的运输距离和搬运次数;减少中间制品。
Lean Layout3. 布局的目的:管理:简化管理;实现均衡生产。
利用率:提高人和设备的利用率;提高空间利用率。
Lean Layout4. 精益布局简介: 精益布局,是以现状布局为基础,通过消除人、机、料、法、环(4M1E)各个环节上的浪费,来实现五者最佳结合的布局。
5. 精益布局的应用方法: 精益布局的应用方法主要抓住“单件流”这一精益化的核心思想。
6. 实现精益布局的步骤:step1宏观布局 (定位)step2线体/物流方案 的设计step3工位局部 优化step4 布局实施step5恢复生产 (适应期)step6 产能提升Lean Layout7. 实现精益布局的步骤:7.1. 现场布局图绘制7. 实现精益布局的步骤:7.2. 根据产品族确定分析对象 确定要分析的产品对象,获取一个产品的生产工艺过程作为主线来综合考虑布局结构的合理性和通用性。
Lean Layout7. 实现精益布局的步骤:7.3. 收集过程块关键信息 获取现场实际存在的最全面的信息,他们是实现精益布局的基础条件,这些重要数据的收集可以帮助我们详细辨别生产过程中外部信息和内部信息,并通过信息的梳 理和结构化,作为精益布局实施的依据,如: 产品种类清单; 周期时间; 产品换模/换型时间; 设备有效工作时间; 生产批量大小;操作工数量; 有效工作时间;废品率;。
- 1、下载文档前请自行甄别文档内容的完整性,平台不提供额外的编辑、内容补充、找答案等附加服务。
- 2、"仅部分预览"的文档,不可在线预览部分如存在完整性等问题,可反馈申请退款(可完整预览的文档不适用该条件!)。
- 3、如文档侵犯您的权益,请联系客服反馈,我们会尽快为您处理(人工客服工作时间:9:00-18:30)。
买专用设备
满足适当的需求即可 不买泛用化设备
(3)便于作业者相互协作,异常时能停线,及时暴露问
题并改善之。
.
11
(4)步行最短,可单件流动,人员可增可减。
3.生产线的布置
思考方法
布置时需考虑「设备的配置」是指材料、 零件、制品等「物」的顺流及作业员,检 查员等「人」可以做顺畅的动作及作业
的「设备之配置」(布置).
区分
主要实施事项
物 人 设备
4.检讨.适当的「另件置场、制品置场配置及配置从作业员处可确认库存 12
的置场」(工程内为1个流).
3 Step 将长屋型改为大通铺式
大 通 铺 式 布 置
.
13
大通铺式 布置
大通铺式布置能有效利用空间,便于线与线 之间相互协作,根据各生产线产距时间调整作业 分配和人员安排,达到少人化目的。
同时,大通铺式布置容易暴露整体上的问题, 促进问题解决,从而提高整体效率。
.
16
1、柔性原则
设备配合人
弹性化 灵活化
小型化 流动化 有弹性 变换快
多样少量 短交货期
低成本
设备发展史
手工化
动力化
人使用设备
设备帮助人
机械化 自动化
智能化
人辅助设备
人适应设备
人管理设备
.
高速度 高产量 多功能 泛用化
大型化 固定化 高价化 17
设备随需求增减组合 人员物料顺畅流动
小型化 流动化 有弹性 变换快
CCC
垂直布置
(“细流而快”, 满足多样少量)
A
A
A
A
B
B
B
B
C
C
C
C
.
A
B
C
10
2 Step 采用U字型生产线
11
成品
14 13 12
10 9
8
7
材料
1
3
4
2
5
6
(1)以U字型,依逆时针方向按工艺流程排列生产。
(2)入口和出口由同一作业者负责,能够以产距时间按
标准数量进行生产及管理,也便于补充生产。
一笔画
从提高整体效率的目的出发,将前后 关联的生产线集中布置。
.
8
Step4 Step3
工厂整体布置
一笔画
整体上呈一笔画布置
Step2
将长屋型改为大通铺式
Step1
采用U字型生产线
由水平布置改为垂直布置
.
9
1 Step 由水平布置改为垂直布置
AAAAA
B
B
水平布置
(离岛式、鸟笼式 “粗流而慢”)
布置目的
将工厂的各种作业和附属设施、依照制造程序作最
适当的编排与布置。(设备、物流动线、在库区、
通路等)
.
5
生产线布置基本形式Байду номын сангаас
在一般生产系统设计中,存在着下列四 种不同的基本布置形式:
✓以产品布置 ✓以制程布置 ✓以固定位置布置 ✓以群组布置
综合以上四种基本布置形态,来探讨『如何布置工厂的
生产线』。
(1)减少各生产线的在制品数量,以减少堆积空间。 (2)物料供应采用逐组逐套的方式,避免物料过多造成 空间狭小、作业者行动不便。
.
14
4 Step 整体上呈一笔画布置
一 笔 画 布 置
.
15
(二)流线化设备设计与调整
1、柔性原则 2、实用原则 3、流动原则 4、能屈能伸原则
5、弹性原则 6、窄面原则 7、三不原则 8、成长带原则
将以上事项充分检讨后,再做『工厂建设及设备』的布置是
.
3
较妥当的。
工厂布置规划的目标
▪ 有效编排设备与工作区域的整合,使制程是直线流动, 生产一贯化。
▪ 使物料运搬的距离最短,避免有交叉重复现象发生。
▪ 维持生产作业与制程编排的弹性化,以利必要性之改 善调整。
▪ 使原物料在制程中能快速流动,避免堆积存放,造成 资金积压。
▪ 以合理有效的制程规划,减少对设备投资之重复。
▪ 建筑空间的有效利用规划。
▪ 人、设备、物流、放置方式考虑原则,并充分提升人
力绩效。
.
4
设施布置的方向与目的
布置方向
▪ 设施布置需要作长期规划。 ▪ 设施布置对产品生产成本有重大的影响、
要周详规划。 ▪ 设施布置需要由日常生产活动中不断的
改善,寻找优化的布置。
.
6
制程型布置形式
组装工厂(工程) 零件加工工厂(工程)
冲床工厂(工程)
出货场
模具进料
办公室
正门 停 车 场
完 成 品 置 场
检查区
完
成 组装工程 品
置 场
另件置场
次组装
焊接工程
另件置场
试验室
零件
零件进料
冲 模具
压 件
置场
置
场
模具 维护场
冲压工程
冲压工程
材料 置场
材料进料
.
7
一笔画的工厂布置
工厂整体布置
1.1个流 2.同期化
1.多工程化 2.多能工化
1.照工程顺序的设备配 置 2.整流化
<参考>
*配线 ·配管的施工(压气、电气、水) 1) 配线 ·配管不要在地面,因很难清扫;再 者,对材料等的运搬也有阴碍。
3-1:设备的配置「工程顺序」
布置的基本型式
基本型式
布置例
1
U字型 配置
置 完成品
场 材料
⑨⑧⑦⑥ ⑤
.
2
工厂布置规划三要素
工厂建设及设备布置应整体性的企划与检讨。
因为工厂与工厂内部之设备布置会在日常及每天的生产活动 中被利用到的。
为此:在工厂的布置时应考虑下列三项
▪ 物(原材料、零件、制品、模具、治工具、通箱等等)的 『物流』应单纯。
▪ 人(作业者、运搬者等等)的『动作/作业』应顺畅。
▪ 物品的『放置方法/置放方式』应容易了解。
稳定 速度适中
通过局部切换 适应不同加工对象 适应不同加工要求
只需更换模具刀具等 可满足各种不同产品 快速切换节省时间 实现多样少量混流生产
质量稳定
高速度
运转稳定
高产量
.
18
2、实用原则
小批量生产
细流而快
理想的设备能确保 整个生产工序环环相 扣,整个生产线畅通 无阻,无中间停滞和 多余在制品。
买基本功能设备
工厂精益布局
.
1
讲课目录
一.工厂布局 1,工厂布局规划三要素 2,工厂布局规划的目标 3,设施布置的方向与目的 4,生产线布置基本方式 5,制程型布置形式 二.一笔画工厂 3-1设备的配置以工程顺序排列 3-2不能用工程顺序配置的设备 3-3检讨布置的步骤 4.4S与目视管理 4-14S(整理整顿)的定义 4-2生产线/置场等区域要明示彻底 4-3何谓目视管理 4-4目视管理之活用 4-5目视管理化(电极管理板例) 4-6目视管理化(置场管理例) 5.优化生产线布置优点
①②③④
2
二连 配置
材料B ⑨ ⑧ ⑦ ⑥ ⑤
置下 工
场程
材料A ① ② ③ ④ ⑤
*对应每天交货数量(生产数)的变化,增减人员的配置.
<检讨布置时的要点> 1.考虑「物」的整流化,依工程顺序配置设备. 2.在订购设备阶段,要检讨「设备大小」,注意设备能容入区域内. 3.对应物品流动方法,人的动作,检讨「设备启动开关的配置」.