材料成型技术基础2
[材料成型工艺技术基础]韩建民版第二章答案
![[材料成型工艺技术基础]韩建民版第二章答案](https://img.taocdn.com/s3/m/da2719133c1ec5da50e27077.png)
[材料成型工艺技术基础]韩建民版第二章答案1.何谓塑性变形?单晶体、多晶体塑性变形的机理各是什么?金属在外力的作用下,内部产生应力,该应力使原子偏离其原来的平衡位置,当应力超过金属材料的屈服极限,外力去除后,原子达到新的平衡状态,金属恢复不到原来的形状和尺寸,产生的永久变形。
单晶体: 晶体在切应力作用下,晶体的一部分与另一部分沿着一定的晶面彼此以刚性的整体相对滑移,滑移的距离为原子间距的整数倍。
多晶体:内部每个晶粒相互协调和配合,当外力达到一定值后晶界发生变形和破碎,其中既有晶内的滑移变形,也有晶间的滑动和转动。
2.何谓冷变形,何谓热变形,冷变形后金属的组织和性能会产生怎么样的变化,热变形后金属的组织和性能会产生怎么样的变化?金属锻造在升温变形过程中,金属原子获得能量,将低温变形中出现的应力吸收,微结构中碎晶形核等生长,将变形晶粒全部消失,这个温度就是再结晶温度,此温度以下的就是冷变形,以上的就是热变形。
冷变形后,晶粒在外力作用下倍扭曲拉长,随着变化逐渐成纤维状,有些晶粒破碎成碎晶,这种结构的晶格对进一步变形有阻碍作用,使金属的的强度和硬度升高,而塑性和韧性下降;热变形后,冷变形过程中出现的碎晶或杂志为核心形核并长大,直到全部冷变形晶粒消失为止,消除加工硬化,这个过程是再结晶不是相变,其晶粒均匀生长细化,塑性增加。
3.为什么规定锻造温度范围?碳钢合理的始锻温度和终锻温度应在铁碳合金状态图的什么位置?锻造温度范围是指始锻温度和终锻温度之间的一段温度间隔。
确定锻造温度的基本原则是,就能保证金属在锻造温度范围内具有较高的塑性和较小的变形抗力,并得到所要求的组织和性能。
锻造温度范围应尽可能宽一些,加热温度太低,表面会开裂,或者内部裂纹,加热温度过高,导致钢坯过烧,无法成型产品。
碳钢的锻造温度范围如图(铁-碳状态图)中的阴影线所示:钢的始锻温度主要受过热的限制,合金结构钢和合金工具钢的始锻温度主要受过热和过烧温度的限制。
材料成型技术基础习题答案
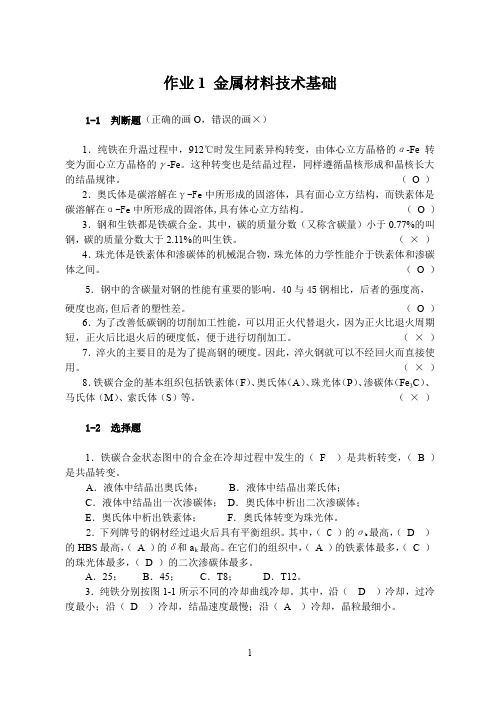
作业1 金属材料技术基础1-1 判断题(正确的画O,错误的画×)1.纯铁在升温过程中,912℃时发生同素异构转变,由体心立方晶格的α-Fe转变为面心立方晶格的γ-Fe。
这种转变也是结晶过程,同样遵循晶核形成和晶核长大的结晶规律。
(O )2.奥氏体是碳溶解在γ-Fe中所形成的固溶体,具有面心立方结构,而铁素体是碳溶解在α-Fe中所形成的固溶体,具有体心立方结构。
(O )3.钢和生铁都是铁碳合金。
其中,碳的质量分数(又称含碳量)小于0.77%的叫钢,碳的质量分数大于2.11%的叫生铁。
(×)4.珠光体是铁素体和渗碳体的机械混合物,珠光体的力学性能介于铁素体和渗碳体之间。
(O )5.钢中的含碳量对钢的性能有重要的影响。
40与45钢相比,后者的强度高,硬度也高,但后者的塑性差。
(O )6.为了改善低碳钢的切削加工性能,可以用正火代替退火,因为正火比退火周期短,正火后比退火后的硬度低,便于进行切削加工。
(×)7.淬火的主要目的是为了提高钢的硬度。
因此,淬火钢就可以不经回火而直接使用。
(×)8.铁碳合金的基本组织包括铁素体(F)、奥氏体(A)、珠光体(P)、渗碳体(Fe3C)、马氏体(M)、索氏体(S)等。
(×)1-2 选择题1.铁碳合金状态图中的合金在冷却过程中发生的(F )是共析转变,(B )是共晶转变。
A.液体中结晶出奥氏体;B.液体中结晶出莱氏体;C.液体中结晶出一次渗碳体;D.奥氏体中析出二次渗碳体;E.奥氏体中析出铁素体;F.奥氏体转变为珠光体。
2.下列牌号的钢材经过退火后具有平衡组织。
其中,( C )的σb最高,(D )的HBS最高,(A )的δ和a k最高。
在它们的组织中,(A )的铁素体最多,( C )的珠光体最多,(D )的二次渗碳体最多。
A.25;B.45;C.T8;D.T12。
3.纯铁分别按图1-1所示不同的冷却曲线冷却。
其中,沿( D )冷却,过冷度最小;沿(D )冷却,结晶速度最慢;沿(A )冷却,晶粒最细小。
材料成型技术基础课程设计
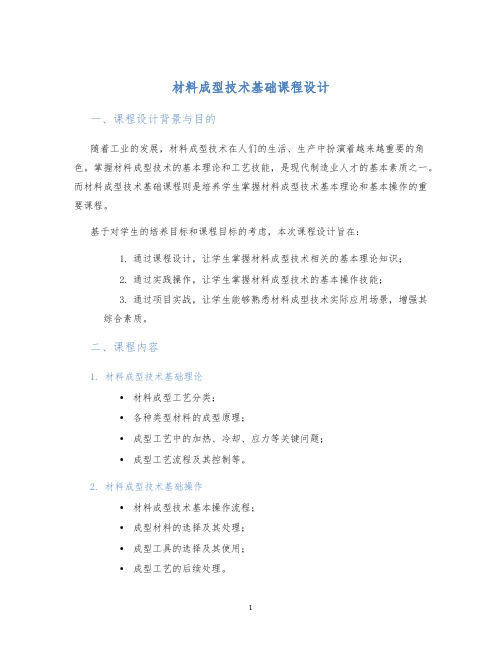
材料成型技术基础课程设计一、课程设计背景与目的随着工业的发展,材料成型技术在人们的生活、生产中扮演着越来越重要的角色。
掌握材料成型技术的基本理论和工艺技能,是现代制造业人才的基本素质之一。
而材料成型技术基础课程则是培养学生掌握材料成型技术基本理论和基本操作的重要课程。
基于对学生的培养目标和课程目标的考虑,本次课程设计旨在:1.通过课程设计,让学生掌握材料成型技术相关的基本理论知识;2.通过实践操作,让学生掌握材料成型技术的基本操作技能;3.通过项目实战,让学生能够熟悉材料成型技术实际应用场景,增强其综合素质。
二、课程内容1. 材料成型技术基础理论•材料成型工艺分类;•各种类型材料的成型原理;•成型工艺中的加热、冷却、应力等关键问题;•成型工艺流程及其控制等。
2. 材料成型技术基础操作•材料成型技术基本操作流程;•成型材料的选择及其处理;•成型工具的选择及其使用;•成型工艺的后续处理。
3. 项目案例实战•通过案例实战,让学生了解材料成型技术在实际应用场景中的应用;•培养学生解决实际问题的能力;•提高学生的团队合作能力。
三、课程设计流程1. 理论学习(1周)•学生通过教师授课、资料阅读、讨论等方式学习材料成型技术相关的基本理论知识;•教师通过出题测试等方式对学生的知识掌握情况进行评估。
2. 实践操作(2周)•学生通过实践操作,掌握材料成型技术的基本操作技能;•教师引导学生深入探讨操作过程中遇到的关键问题,并进行讲解和解答;•教师通过考核实习成绩等方式对学生的实践操作情况进行评估。
3. 项目案例实战(3周)•学生以小组形式完成一项材料成型技术项目实战任务;•教师通过对项目进度、成果等方面的考核,对学生的综合素质进行评估;•学生针对项目进行收尾报告,形成项目实践总结。
四、考核及评估方式为确保课程设计效果,教师将针对不同环节制定考核及评估方式:•期中考试:考核学生对材料成型技术基础理论的掌握情况,占总评成绩的30%;•实践操作成绩:考核学生对材料成型技术基础操作技能的掌握情况,占总评成绩的30%;•项目实战成绩:考核学生运用材料成型技术解决实际问题的能力及团队协作能力,占总评成绩的40%。
材料成型技术基础

材料成型技术基础材料成型技术是指将原材料通过一定的加工方式,制造成为具有特定形状、尺寸和性能的产品的过程。
材料成型技术是现代工业制造的基础,它在各个领域都有着广泛的应用,如汽车、机械、电子、建筑等。
本文将对材料成型技术的基础知识进行介绍。
1. 基本概念材料成型技术包括各种加工方式,如锻造、铸造、挤压、拉伸、滚压、剪切、锯切等。
这些加工方式都是通过对原材料的物理和化学变化,使其得到所需的形状和性能,从而实现产品的制造。
2. 锻造锻造是一种通过对金属材料进行加热和压制,使其改变形状和性能的加工方式。
锻造可以分为自由锻造和模锻造两种。
自由锻造是指将金属材料加热至一定温度后,用锤头或压力机对其进行压制,从而使其改变形状和性能。
模锻造是指将金属材料放入特定的模具中进行加热和压制,从而使其得到所需的形状和性能。
3. 铸造铸造是一种通过将液态金属材料倒入特定的模具中,使其冷却固化后得到所需的形状和性能的加工方式。
铸造可以分为压力铸造和重力铸造两种。
压力铸造是指将液态金属材料通过高压喷射进入模具中,从而得到所需的形状和性能。
重力铸造是指将液态金属材料倒入模具中,通过重力作用使其冷却固化,从而得到所需的形状和性能。
4. 挤压挤压是一种通过将金属材料通过模具中的小孔挤出,从而得到所需的形状和性能的加工方式。
挤压可以分为冷挤压和热挤压两种。
冷挤压是指将金属材料在室温下通过模具中的小孔挤出,从而得到所需的形状和性能。
热挤压是指将金属材料加热至一定温度后,通过模具中的小孔挤出,从而得到所需的形状和性能。
5. 拉伸拉伸是一种通过将金属材料拉伸,使其改变形状和性能的加工方式。
拉伸可以分为冷拉伸和热拉伸两种。
冷拉伸是指将金属材料在室温下拉伸,从而得到所需的形状和性能。
热拉伸是指将金属材料加热至一定温度后,拉伸,从而得到所需的形状和性能。
6. 滚压滚压是一种通过将金属材料通过辊轮的滚动,使其改变形状和性能的加工方式。
滚压可以分为冷滚压和热滚压两种。
材料成形技术基础
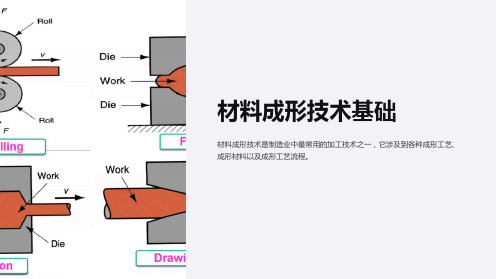
电子制造
材料成形技术在电子设备的封装和连接中起着重要 作用。
航空航天
艺术雕塑
材料成形技术用于制造航空航天部件和航天器结构。 材料成形技术被艺术家用于创作各种雕塑作品。
材料成形技术的挑战与发展趋势
1 高性能材料
随着科技的进步,材料成形技术需要适应高性能材料的特性和要求。
材料成形技术基础
材料成形技术是制造业中最常用的加工技术之一,它涉及到各种成形工艺、 成形材料以及成形工艺流程。
成形技术定义
成形技术是通过施加力或应用热量将原始材料转化为所需形状和尺寸的加工方法。
主要成形技术分类
1 压力成形技术
将材料置于模具中,并施加压力使其变形, 如冲压、铸造等。
2 热成形技术
2 节能环保
开发符合节能环保要求的成形工艺和材料,减少资源消耗和环境污染。
3 数字化制造
利用数字化技术实现材料成形过程的自动化和智能化。
3
成形操作
按照成形工艺要求进行操作,施加力或应用热量使材料变形。
常见的成形材料
金属
如铝、钢等,用于制造汽车零部件、电子设备等。
塑料
如聚乙烯、聚丙烯等,广泛用于塑料制品的生产。
陶瓷
如瓷器、陶器等,用于制作装饰品、器皿等。
复合材料
如碳纤维增强复合材料,用于制造航空航天部件。
材料成形技术的应用领域
汽车制造
通过加热材料使其变软或熔化,然后形成所 需形状,如热压、热挤压等。
3 凝固成形技术
通过材料凝固过程中的相变来实现成形,如 注射成型、凝胶成型等。
4 仿生如3D打印、 模具复制等。
成形工艺流程
1
材料成型技术基础第2版课后习题答案
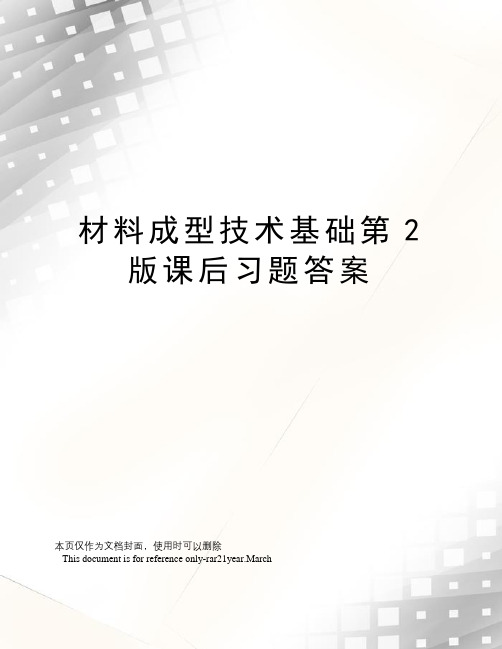
材料成型技术基础第2版课后习题答案本页仅作为文档封面,使用时可以删除This document is for reference only-rar21year.March第一章金属液态成形1.①液态合金的充型能力是指熔融合金充满型腔,获得轮廓清晰、形状完整的优质铸件的能力。
②流动性好,熔融合金充填铸型的能力强,易于获得尺寸准确、外形完整的铸件。
流动性不好,则充型能力差,铸件容易产生冷隔、气孔等缺陷。
③成分不同的合金具有不同的结晶特性,共晶成分合金的流动性最好,纯金属次之,最后是固溶体合金。
④相比于铸钢,铸铁更接近更接近共晶成分,结晶温度区间较小,因而流动性较好。
2.浇铸温度过高会使合金的收缩量增加,吸气增多,氧化严重,反而是铸件容易产生缩孔、缩松、粘砂、夹杂等缺陷。
3.缩孔和缩松的存在会减小铸件的有效承载面积,并会引起应力集中,导致铸件的力学性能下降。
缩孔大而集中,更容易被发现,可以通过一定的工艺将其移出铸件体外,缩松小而分散,在铸件中或多或少都存在着,对于一般铸件来说,往往不把它作为一种缺陷来看,只有要求铸件的气密性高的时候才会防止。
4 液态合金充满型腔后,在冷却凝固过程中,若液态收缩和凝固收缩缩减的体积得不到补足,便会在铸件的最后凝固部位形成一些空洞,大而集中的空洞成为缩孔,小而分散的空洞称为缩松。
浇不足是沙型没有全部充满。
冷隔是铸造后的工件稍受一定力后就出现裂纹或断裂,在断口出现氧化夹杂物,或者没有融合到一起。
出气口目的是在浇铸的过程中使型腔内的气体排出,防止铸件产生气孔,也便于观察浇铸情况。
而冒口是为避免铸件出现缺陷而附加在铸件上方或侧面的补充部分。
逐层凝固过程中其断面上固相和液相由一条界线清楚地分开。
定向凝固中熔融合金沿着与热流相反的方向按照要求的结晶取向进行凝固。
5.定向凝固原则是在铸件可能出现缩孔的厚大部位安放冒口,并同时采用其他工艺措施,使铸件上远离冒口的部位到冒口之间建立一个逐渐递增的温度梯度,从而实现由远离冒口的部位像冒口方向顺序地凝固。
材料成型技术基础知识点总结
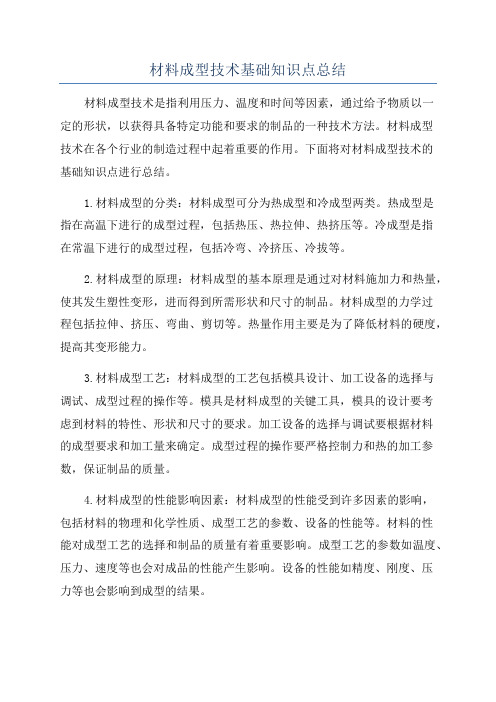
材料成型技术基础知识点总结材料成型技术是指利用压力、温度和时间等因素,通过给予物质以一定的形状,以获得具备特定功能和要求的制品的一种技术方法。
材料成型技术在各个行业的制造过程中起着重要的作用。
下面将对材料成型技术的基础知识点进行总结。
1.材料成型的分类:材料成型可分为热成型和冷成型两类。
热成型是指在高温下进行的成型过程,包括热压、热拉伸、热挤压等。
冷成型是指在常温下进行的成型过程,包括冷弯、冷挤压、冷拔等。
2.材料成型的原理:材料成型的基本原理是通过对材料施加力和热量,使其发生塑性变形,进而得到所需形状和尺寸的制品。
材料成型的力学过程包括拉伸、挤压、弯曲、剪切等。
热量作用主要是为了降低材料的硬度,提高其变形能力。
3.材料成型工艺:材料成型的工艺包括模具设计、加工设备的选择与调试、成型过程的操作等。
模具是材料成型的关键工具,模具的设计要考虑到材料的特性、形状和尺寸的要求。
加工设备的选择与调试要根据材料的成型要求和加工量来确定。
成型过程的操作要严格控制力和热的加工参数,保证制品的质量。
4.材料成型的性能影响因素:材料成型的性能受到许多因素的影响,包括材料的物理和化学性质、成型工艺的参数、设备的性能等。
材料的性能对成型工艺的选择和制品的质量有着重要影响。
成型工艺的参数如温度、压力、速度等也会对成品的性能产生影响。
设备的性能如精度、刚度、压力等也会影响到成型的结果。
5.材料成型的应用:材料成型技术广泛应用于诸多领域,如汽车制造、航空航天、电子、建筑等。
汽车制造中的车身、发动机零部件等都需要经过冲压成型、挤压成型等工艺。
航空航天中的飞机壳体、涡轮叶片等也需要通过成型工艺进行制作。
电子产品中的外壳、散热器等也需要通过成型技术来获得所需的形状。
建筑领域中的钢结构、混凝土构件等亦需要经过成型工艺来生产。
综上所述,材料成型技术是制造过程中不可或缺的一部分。
通过了解材料成型的分类、原理、工艺、性能影响因素和应用,可以更好地理解和应用材料成型技术,提高制品的质量和生产效率。
材料成型技术基础

材料成型技术基础材料成型技术基础材料成型技术是现代工业的核心技术之一,是将材料加工成所需形状、结构和性能的过程。
材料成型技术分为传统成型技术和先进成型技术两种。
前者包括热加工、冷加工、焊接等,后者则包括快速成型、激光加工、注塑成型等。
无论是哪种成型技术,都需要掌握材料成型技术基础知识才能熟练地操作和完成任务。
1.材料成型技术原理材料成型技术在原理上是通过施加压力,改变材料外观和性质。
采用不同的成型方法和工艺流程,可获得所需的形态和性能。
例如,金属冷加工依靠的是材料的塑性变形,而激光切割则是利用激光的高能量和热量来割断材料。
因此,不同成型技术的原理不同,工艺流程也不同。
2.材料成型技术分类材料成型技术主要可以分为常规材料成型技术和高级材料成型技术两类。
常规材料成型技术包括热加工、冷加工、铸造、焊接、切削等。
这些技术在工业生产中应用广泛,可以制造出各种形态的零部件和产品。
高级材料成型技术是在常规成型技术基础上,运用现代科技和工程技术发展起来的成型技术。
例如,金属材料的选择性激光烧结技术(SLS)、三维打印技术、激光切割技术和注塑成型技术等。
这些技术通常被用于制造高性能、高单价、高品质的工业产品。
3.常规材料成型技术热加工热加工技术是利用高温对材料进行塑性变形的加工方式。
通过热处理,可以使金属变得更加容易软化和延展。
热加工适合于制造大量的同样尺寸和形状的零件,例如轴、齿轮等机械元件。
冷加工冷加工技术是不需要高温处理的制造加工方法。
冷加工一般用于金属加工,由于没有热变形,冷加工一般具有更好的精度和表面光洁度。
冷加工应用广泛,例如冷拔、冷轧、冷环等。
铸造铸造是利用熔化的金属,将其注入模具中成型制品的加工方法。
铸造可以生产出各种不同尺寸和形状的零件,应用范围广泛,例如钢铁、铝合金、铜、铜合金等材料。
焊接焊接是将两个物体连接在一起的加工方式。
焊接广泛应用在车辆工业、建筑工业、航空航天工业等领域,例如电弧焊、气体保护焊、激光焊等技术。
- 1、下载文档前请自行甄别文档内容的完整性,平台不提供额外的编辑、内容补充、找答案等附加服务。
- 2、"仅部分预览"的文档,不可在线预览部分如存在完整性等问题,可反馈申请退款(可完整预览的文档不适用该条件!)。
- 3、如文档侵犯您的权益,请联系客服反馈,我们会尽快为您处理(人工客服工作时间:9:00-18:30)。
Mechanical Working
压力加工:锻压、塑性成形 定义 The metal is shaped through plastic deformation in solid state by mechanical force p90 金属材料在外力作用下产生塑性变形,获得具有一定形状、 尺寸和力学性能的毛坯或零件的生产方法
(2) 自由锻工序
基本工序、辅助工序、精整工序 基本工序:镦粗, 拔长, 冲孔(扩孔), 弯曲, 扭转, 错移, 切割 辅助工序:压钳口,倒棱,压肩
(3) 锻件分类及基本工序方案
盘类锻件: 镦粗和冲孔
筒类零件:镦粗、
冲孔、在心轴上拔长
轴类零件: 拔长、切肩和锻台阶
环类零件:镦粗、 冲孔、在心轴上扩孔
§2. 2 模 锻 Die Forging
定义:金属坯料在冲击力或压力作用下,在模锻模膛
内变形,从而获得所需形状及尺寸的锻件P98 变形特点:模膛内变形,流动受模壁限制
1. 模锻锻造设备
模(型)锻造
蒸汽—空气模锻锤 锤上模锻 Drop Forging 曲柄压力机上模锻 曲柄压力机 摩擦压力机上模锻 摩擦压力机
T< T0 Cold Working冷加工 T> T0 Hot Working 热加工:动态回复与动态再结晶
4. 热加工p93
热加工金属的组织:再结晶组织 与铸锭相比:晶粒细化,缺陷压合,致密度提高,性能提高 热加工后性能提高,但纤维组织可能具有各向异 平行于纤维组织的方向,抗拉强度提高,剪切强度很低 垂直于纤维组织的方向,抗拉强度很低,剪切强度高 问:为什么重要受力零件都采用热加工制造? 设计时应该注意什么问题?
自由锻特点: 模锻特点:
设备、工具简单, 生产率低 锻件精度低、光洁度差 通用性强,单件也能生产 只能锻形状很简单的零件
设备、工具复杂, 生产率高 锻件精度高、光洁度好 只适合大批量生产 能够锻形状复杂的零件
自由锻可锻零件重量1kg~300T,模锻可锻重量0.5~150kg的工件 国外工业发达国家,中小型自由锻件在其锻件总产量的为20-40%
对于自由锻件,确定敷 料、余量及公差后,就 可以绘制锻件图
图3-25 典型锻件图 1-敷料 ; 2-余量
(2) 坯料重量和尺寸的计算
坯料重量:G坯料=G锻件+G烧损+G料头 G锻件→由锻件体积算出;G烧损→与加热次数有关 坯料的尺寸根据坯料重量和几何尺寸确定 与选用的锻造工序有关、考虑锻造比setting ratio 碳钢,拔长锻造比≧3,镦粗锻造比≧ 2.5 合金钢为3~4,对轧材取1.3~1.5 应用镦粗工序:H/D<2.5 ,太大易弯
拔 长 模 膛
一般布置在模具的边上,用来
减小坯料某部分的截面积,增 加该部分的长度 拔长操作时,坯料送进加翻转 滚 压 模 膛
坯料长度不变,改变不同部位截面积变 滚压操作时,坯料只翻转,不送进 锻件截面相差较大时,用闭式结构
弯 曲 和 切 断 模 膛
弯曲模膛:用于弯曲的杆类模锻件 切断模膛:用于坯料上切下锻件,锻 件上切下钳口,多件锻造时分离锻件
塑性越好,材料的变形抗力越小,其可锻性越好 1. 影响可锻性的因素Variables influencing malleability 金属的本质、加工条件
金属的本质
类型
Metal types: f.c.c >b.c.c,铝铜镍>铬钼钛 化学成分: 纯金属>合金, 碳钢>合金钢, 低碳钢>高碳钢 金属的组织 相的组成及分布:固溶体>机械混合物>化合物 晶粒大小:等轴晶>柱状晶;细晶粒>粗晶粒
碳钢的锻造温度范围
第二章 锻 造 Forging
Metal is shaped between smith anvil or forgoing die by mechanical force (P97); 问:锻造为什么要加热?
锻造方法 F Forging:在抵铁之间成形 模锻 Die Forging:在模锻设备上用模具成形 胎膜锻 Swaging:在自由锻设备上用胎膜成形
用来容纳多余的金属
飞边槽的作用
阻挡金属外流,强迫金属充模
缓冲作用
预锻模膛:使坯料变形到接近于锻件的形状和尺寸 预锻模膛的作用
使金属更容易充满终锻模膛 减少终锻模膛的磨损,提高寿命
特点 :圆角斜度较大,没有飞边槽
(2) 制坯模膛
对于形状复杂的模锻件,用制坯模膛制坯 制坯模膛:初步改变毛坯形状、合理分配金属,以适应锻 件横截面积和形状的要求,使金属能更好地充满模锻模膛
组织,性能,流线、拉应力、切应力、流线沿轮廓分布,不断 p94
金属塑性成形工艺基础
金属经过压力加工时,获 得优质制品的难易程度
第三节 金属的可锻性
Malleability of the Metal
压力加工过程中, 变形 金属作用于施压工具表 面单位面积上的压力
可锻性 金属的塑性 plastic behavior of the metal 变形抗力 the resistance to deformation
胎模锻:自由锻锤
模锻设备
蒸汽—空气模锻锤 1、踏板 2、机架 3、砧座 4、操纵杆
与自由锻设备原理 相同,运动副间隙 小,动作精度高
曲柄压力机上模锻 200t~12000t
1 电动机 7 离合器 15 制动器 8 9 10 曲柄 连杆滑块 16 凸轮 14 顶料连杆 造价高, 生产效率 高, 锻件精度高
曲轴类零件:拔长、错移、锻台阶、扭转
弯曲类零件: 拔长、弯曲 锻件生产过程: 零件图→锻件图→锻造方法→锻造工艺
2. 自由锻工艺规程的制定
(1)绘制锻件图
敷料—为简化锻件形状和结构增加的一部分金属
例如一些沟槽、相差不大的台阶等 余量—为切削加工,在加工面上增加的尺寸 0.4~5mm,与锻件尺寸、加工精度有关 公差—锻件尺寸允许的变动量, ±0.3~3mm 与锻件大小,模具精度,设备状态有关
(1) 模锻模膛:金属在其中发生整体
变形,锻模抗力大 终锻模膛:使坯料最终变形到锻件 所要求的形状和尺寸 形状和尺寸 特点 结构
形状与锻件相同 尺寸放大,钢1.5% 四周设飞边槽
1-锻锤 2-上模 3-飞边槽 4-下模 5- 模垫 6,7,10-楔铁 8-分模面 9-模膛
冲孔连皮
(1) 模锻模膛 冲孔连皮:模锻不能直接冲出通 孔,上下模之间形成一薄层金属 飞边槽的形成飞边 去掉飞边和冲孔连皮,得到具有 通孔的模锻件
不应有加强筋、凸台、工 字型或空间曲面形表面
避免形成空间曲线
复杂零件 采用组合法
自由锻件的结构工艺性小结
避免具有锥体或斜面的结构 锻件有数个几何体构成时,避免形成空间曲线 改成平面与圆柱体、平面与平面相接 自由锻件上不应有加强筋、凸台、工字型 或空间曲面形表面 截面急剧变化或形状复杂的零件 应设计成几个简单模锻件的组合体
3. 金属的塑性变形规律
体积不变条件:由于塑性变形时金属密
度的变化很小,所以可认为变形前后的体 积相等 最小阻力定律:如果物体在变形过程中 其质点有向各种方向移动的可能性时,则 物体各质点将向着阻力最小的方向移动 最小阻力定律是描述塑性变形流动规 律的一种理论 金属内某一质点流动阻力最小的方向 是通过该质点向金属变形部分的周边 所作的法线方向
(3) 确定锻造工序(工步)
怎么锻(锻造工序)主要看零件是什么样的 对于自由锻件,P98, table 3-1
(4) 其它内容
根据合金确定始锻及终锻温度 确定加热规范(加热温度、保温时间) 选择锻造设备 辅助工序(校正,切飞边、冲孔连皮)
3. 自由锻件的结构工艺性
避免具有锥体或斜面的结构
三个方向中,压应力的数目越多,
金属的塑性越好 同号应力状态下引起的变形抗力 大于异号应力状态下的变形抗力
挤压时的应力状态
2. 锻造温度范围
始锻温度:低于AE线
200℃左右 why? 终锻温度:约800 ~750℃
始锻温度过高:过热、过烧(晶界氧
化、熔化), 氧化、脱碳严重 终锻温度过低:塑性差,抗力大
§2.1自由锻 Smith Forging
定义:自由锻是利用冲击力或压力使金属在上、下两
个抵铁之间变形,从而获得所需形状及尺寸的锻件 变形特点:沿变形方向可以自由流动
1. 自由锻设备与工序
(1) 自由锻设备
锻锤:依靠冲击力使金属变形,只能锻造中小锻件 小型锻件—手工锻造,空气锤 中型锻件— (<1500kg)蒸汽—空气锤 液压机:依靠静压力使金属变形,可加工大型锻件 水压机、油压机(<300T) 锻锤吨位 =落下部分总重量 = 活塞+锤头+锤杆 压力机吨位 =滑块运动到下始点时所产生的最大压力
摩擦压力机上模锻
5 电动机 6 皮带 3 飞轮 4 摩擦盘 1螺杆 2 螺母 7 滑块 8,9 导轨 10 机座
造价低,用途广泛, 适合中小锻件的小 中批量生产
2. 锻模结构——锤上模锻 Drop Forging
模膛:形成锻件基本 形状和尺寸的空腔 模膛
模锻模膛
终锻模膛 预锻模膛
延伸模膛 滚压模膛 制坯模膛 弯曲模膛 切断模膛
2. 塑性变形对金属组织和力学性能的影响Structure and
Properties of the Deformed Metals
晶体缺陷增加、晶格 畸变 ;亚结构细化:性能提高 1) 产生加工硬化(冷变形强化) work hardening:随着变形程度的 提高,金属的强度和硬度提高,塑性和韧性下降的现象 原因:位错密度提高,亚结构细化 2) 产生内应力:变形开裂,抗腐蚀性降低 → 去应力退火