风险评价准则和各检查分析表填写实例
安全检查分析记录表(风险评价)
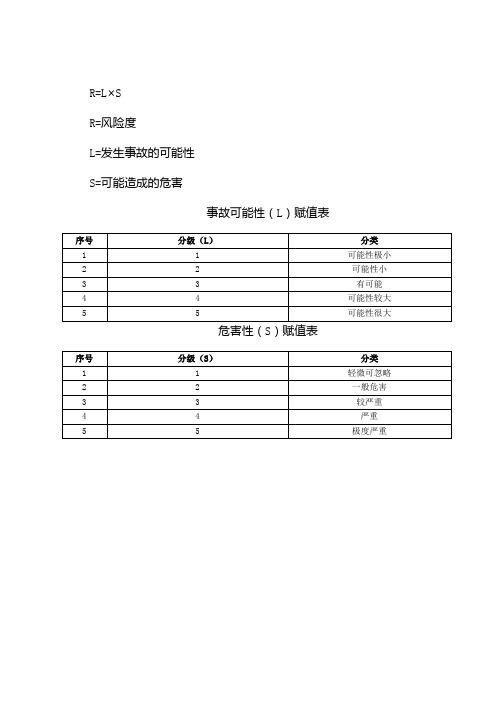
R=L×SR=风险度L=发生事故的可能性S=可能造成的危害事故可能性(L)赋值表安全检查(SCL)分析记录表SB011编号:SB013 设备名称:分液罐分析人员:分析日期:2010.4.7编号:SB004设备名称:原料罐分析人员:分析日期:2010.4.8编号:SB003设备名称:精制塔分析人员:郭立杰沙林赵博孙亚强分析日期:2010.4.8编号:SB009设备名称:原料泵分析人员:分析日期:2010.4.8编号:SB001 设备名称:聚合釜分析人员:分析日期:2010.4.8编号:SB002 设备名称:闪蒸釜分析人员:分析日期:2010.4.8编号:SB017 设备名称:气柜分析人员:分析日期:2010.4.8编号:SB006设备名称:起重机分析人员:分析日期:2010.4.13安全检查(SCL)分析记录表编号:SB012设备名称:氮气加热炉分析人员:分析日期:2010.4.12安全检查(SCL)分析记录表编号:SB019设备名称:活化剂储罐分析人员:分析日期:2010.4.12安全检查(SCL)分析记录表编号:SB021 设备名称:碱罐分析人员:分析日期:2010.4.14安全检查(SCL)分析记录表编号:SB007 设备名称:真空泵分析人员:分析日期:2010.4.15安全检查(SCL)分析记录表编号:SB018设备名称:丙烯换热器分析人员:分析日期:2010.4.15安全检查(SCL)分析记录表编号:SB014设备名称:集中供油分析人员:分析日期:2010.4.15安全检查(SCL)分析记录表编号:SB008设备名称:热水泵分析人员:分析日期:2010.4.8安全检查(SCL)分析记录表编号:SB010 设备名称:碱渣泵分析人员:分析日期:2010.4.15安全检查(SCL)分析记录表编号:SB015设备名称:甲醇,MTBE罐分析人员:分析日期:2010年4月15安全检查(SCL)分析记录表编号:SB020 设备名称:电离器分析人员:分析日期:2010年4月14日安全检查(SCL)分析记录表编号:SB016设备名称:配碱罐分析人员:分析日期:2010年4月8日单位:聚丙烯审核人:审核日期:安全检查(SCL)分析记录表编号:SB024 设备名称:无碱脱臭塔分析人员:分析日期:2010年4月5日安全检查(SCL)分析记录表编号:SB027设备名称:安全用品分析人员:分析日期:2010年4月22日单位:聚丙烯审核人:审核日期:安全检查(SCL)分析记录表编号:SB027设备名称:安全用品分析人员:分析日期:2010年4月22日单位:聚丙烯审核人:审核日期:安全检查(SCL)分析记录表编号:SB028设备名称:聚丙烯自动包装分析人员:分析日期:2010年4月22日单位:聚丙烯审核人:审核日期:。
安全风险评价判定准则
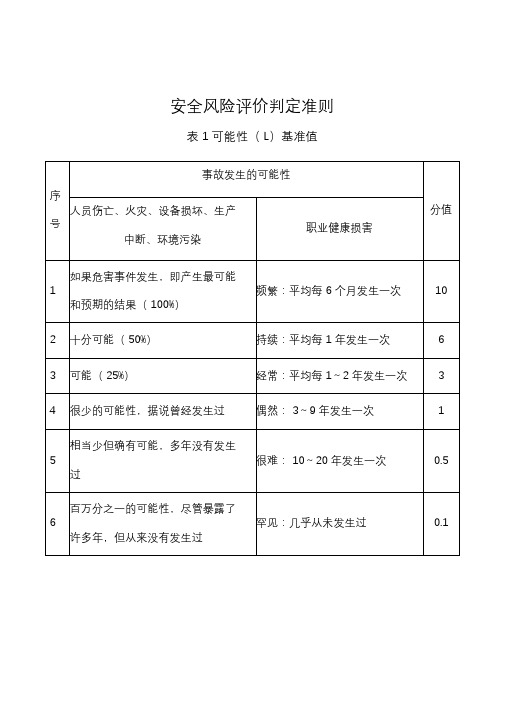
政府要求整顿。
职业健康
损害
造成1~2例无法复原的严重职业病;
造成3~9例以上很难治愈的职业病。
3
人员伤亡
造成重伤1~2人。
25
设备损坏
造成设备或财产损失在50万元到100万元 之间。
生产中断
造成内部统计事故。
环境污染
影响到周边居民及生态环境,引起居民抗 争。
职业健康
损害
造成1~2例难治愈或造成3~9例可治愈的 职业病;
安全风险评价判定准则
表1可能性(L)基准值
序
号
事故发生的可能性
分值
人员伤亡、火灾、设备损坏、生产
中断、环境污染
职业健康损害
1
如果危害事件发生,即产生最可能
和预期的结果(100%)
频繁:平均每6个月发生一次
10
2
十分可能(50%)
持续:平均每1年发生一次
6
3
可能(25%)
经常:平均每1~2年发生一次
3
的可能性)
暴露期低于正常允许水平
0.5
表3后果(C)基准值
序号
事故可能造成后果的严重程度
分值
1
人员伤亡
造成死亡≥3人;或重伤≥10人。
100
设备损坏
造成设备或财产损失≥1000万元。
生产中断
造成较大以上电力安全事故。
环境污染
造成大范围环境破坏;
造成人员死亡、环境恢复困难;
严重违反国家环境保护法律法规。
造成9例以上与职业有关的疾病。
4
人员伤亡
造成轻伤3人以上。
15
序号
事故可能造成后果的严重程度
分值
风险辨识、评估、分析表1

安全风险评估分析表(1)评估分析项目:生产作业过程评估时间:2012.6.30.评估分析内容存在的风险和隐患描述风险建议整改措施或方案S L RR评估人员:安全风险评估分析表(2)评估分析项目:物料出入库及存放评估时间:2012.6.30.评估分析内容存在的风险和隐患描述风险建议整改措施或方案S L RR1材料购买运输购买的原材料不合格导致产品质量审核供应商、查看原材料检测报告运输车辆运输货物超载超长超宽导致交通事故签订运输协议,严禁违章运输2材料出入库搬运操作不当导致人员受伤按操作规程正确操作叉车操作不当、货物放置不当导致人员砸伤叉车操作人员持证上岗,货物堆码整齐出入库验收错误严格按标准验收,复合3储存管理雨淋日晒,物料氧化储存仓库避免雨水4成品出入库搬运操作不当导致人员受伤按操作规程正确操作叉车操作不当、货物放置不当导致人员砸伤叉车操作人员持证上岗,货物堆码整齐出入库验收错误严格按标准验收,复合5成品销售运输销售的产品不合格导致客户产品质量审核相关部门产品检测报告运输车辆运输货物超载超长超宽导致交通事故签订运输协议,严禁违章运输评估人员:安全风险评估分析表(3)评估分析项目:设备设施、器材评估时间:2012.6.30.评估分析内容存在的风险和隐患描述风险建议整改措施或方案S L RR评估人员:安全风险评估分析表(4)评估分析项目:厂区/车间通道评估时间:2012.6.30.评估分析内容存在的风险和隐患描述风险建议整改措施或方案S L RR1.车辆行驶车速过快导致交通事故厂区内限速5公里/时2物料运送叉车超载超宽导致生产事故按规定运送物料,每次可运2T3人员通行车间行走未注意警示标志导致意外伤害注意警示标志没按规定的安全路线走导致生产意外伤害注意厂内及车间安全行走路线4应急疏散疏散路线不合理、不畅通、无秩序导致混乱、碰撞人员受伤选择合适、安全、易于疏散的应急通道位置、确保应急安全出口的门能随时打开,告知员工且能够安全使用疏散通道疏散照明如果不合理、不够充分导致混乱、碰撞人员受伤确保照明覆盖全部疏散路线,充分照明,确保疏散应急照明是双回路供电的疏散标识位置不当、不易辨别导致混乱、碰撞人员受伤检查疏散通道标识位置是否合理,安全出口、紧急电话位置是否便捷,确保正确且易于别识、理解评估人员:安全风险评估分析表(5)评估分析项目:作业环境评估时间:2012.6.30.评估分析内容存在的风险和隐患描述风险建议整改措施或方案S L RR评估人员:。
风险评估和监测记录表(填写范表)

安全的。偶然食用少量的受 DEHP 或 DINP 污染的食品不会对健康造成
危害。
DEHP 和 DINP 急性毒性均较低。通常情况下,人群日常暴露水平极低,
已经发生的健康影响
对人体健康尚无明显影响。但是,部分邻苯二甲酸酯类物质具有内分泌 干扰作用,长期大量摄入将影响生殖和发育,目前尚无证据表明邻苯二
发现,绝大部分 DEHP 在 24 小时~48 小时内会随尿液或粪便排出体外。
48 小时内停止摄入含有 DEHP 的产品,体内 DEHP 浓度便会快速下降。
动物实验还发现,DINP 在体内会被迅速代谢,72 小时内有 85%由粪便
排出,其余部分则由尿液排出。世界卫生组织、美国食品与药品监管局
和欧盟分别认为,终身每人每天摄入 1.5 毫克、2.4 毫克和 3.0 毫克及以 下的 DEHP 是安全的。DINP 的毒性更低,即使每天摄入 9.0 毫克,也是
表示,当局还将每天公布相关检测结果。
美国有关部门表示,已对相关台湾生产的食品进行筛检,以避免进口问
国内外已有的管理措施
题产品,同时,他们正在研究受影响产品未来申请进入美国时,必须检
附台湾核发的合格证明。
韩国禁止台湾疑似有塑化剂的食品进口。
菲律宾政府已向民众提出警告,并要求台湾地区提供详细清单,用以追
表格编号:C-025-01 风险评估时间 风险评估目的
风险评估和监测记录表
评估塑化剂对烘烤食品的影响及我公司的预防措施
姓名
职务
姓名
职务
参与评估人员及职务
外部专家 评估模式 风险来源和性质
相关检验数据和结论
□ 非应急评估 ■ 应急评估
风险名称 进入食物链方式
邻苯二甲酸二(2-乙基)己基酯(DEHP)、邻苯 二甲酸二异壬酯(DINP)等。 邻苯二甲酸酯类物质严禁违法添加到食品中
风险评价分析表

风险评估名称
生产工艺风险评估
所属部门
组长/日期
小组成员/日期
批准人/日期
1、称量工序:
步骤
子步骤
序号
可能的失败因素
可能性
严重性
可检测性
风险指数
控制措施计划
称量
称量
称量
人员
1
着装不规范
不能有效隔离毛发和人体表皮代谢物脱落(3)
对环境及物料造成污染(3)
2
18
*制定详细的人员进出洁净区流程;
3
36
称量前必须核实批生产指令规定量
12
物料品名、规格、批号、检验单号与生产指令规定不一致
所称量的物料与批生产指令不符(1)
造成产品不合格(5)
4
20
称量前必须双人复核物料标识
13
未按规定先称辅料、后称主料称量
主料的生物活性会污染辅料(2)
造成物料报废(5)
2
20
严格执行《称量岗位操作规程》
14
未经双人复核
6
气流形式、压差调整不当
气流形式压差不符合设计要求(2)
洁净区的洁净度达不到规范要求(5)
1
10
逐一检查房间气流形式和压差,确认气流形式,压差
7
初中效过滤器压差不当
不能有效过滤颗粒(3)
引起产品污染。(5)
1
15
初中效安装压差表,操作人员定时监测压差,按更换操作规程进行更换。
8
温湿度调整不当
温湿度达不到设计要求(2)
高效过滤器泄露或安装不合格
高效过滤器安装不当或高效透过率不符合要求(2)
洁净区的洁净度和微生物不符合规范要求(5)
ISO9001-2015--风险辨识和风险评价表(举例)
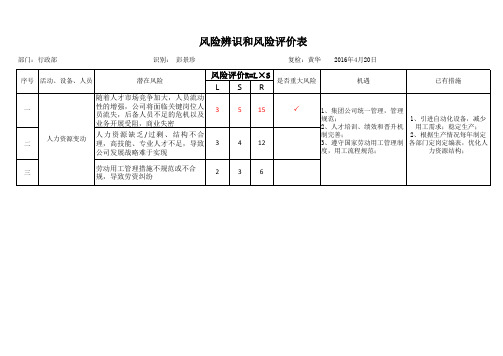
P
3
4
12
1、集团公司统一管理,管理 规范; 1、引进自动化设备,减少 2、人才培训、绩效和晋升机 用工需求;稳定生产; 制完善; 2、根据生产情况每年制定 3、遵守国家劳动用工管理制 各部门定岗定编表,优化人 度,用工流程规范; 力资源结构;
三
2
3
6
风险辨识和风险评价表
部门:行政部 序号 活动、设备、人员 识别: 彭景珍 潜在风险 复检:黄华 2016年4月20日 机遇 已有措施
风险评价R=L×S
L
3
S
5
R
15
是否重大风险
一
二
人力资源变动
随着人才市场竞争加大,人员流动 性的增强,公司将面临关键岗位人 员流失,后备人员不足的危机以及 业务开展受阻,商业失密 人力资源缺乏/过剩、结构不合 理,高技能、专业人才不足,导致 公司发展战略难于实现 劳动用工管理措施不规范或不合 规,导致劳资纠纷
风险评分表填写说明1
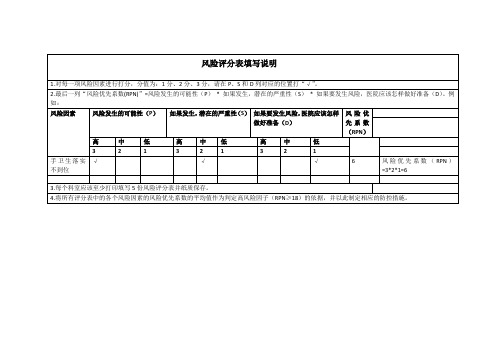
1.对每一项风险因素进行打分,分值为:1分、2分、3分,请在P、S和D列对应的位置打“√”。
2.最后一列“风险优先系数(RPN)”=风险发生的可能性(P)*如果发生,潜在的严重性(S)*如果要发生风险,医院应该怎样做好准备(D)。例如:
风险因素
风险发生的可能性(P)
如果发生,潜在的严重性(S)
如果要发生风险,医院应该怎样做好准备(D)
风险优先系数(RPN)
高中Biblioteka 低高中低
高
中
低
3
2
1
3
2
1
3
2
1
手卫生落实不到位
√
√
√
6
风险优先系数(RPN)=3*2*1=6
3.每个科室应该至少打印填写5份风险评分表并纸质保存。
4.将所有评分表中的各个风险因素的风险优先系数的平均值作为判定高风险因子(RPN≥18)的依据,并以此制定相应的防控措施。
风险评价方法说明与举例
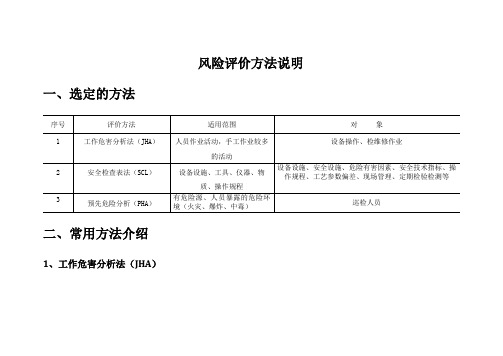
主要
后果
以往发生频率及现有安全控制措施
L
S
R
建议改进措施
偏差发生频率
管理措施
胜任程度/设备现状
安全设施
- 1、下载文档前请自行甄别文档内容的完整性,平台不提供额外的编辑、内容补充、找答案等附加服务。
- 2、"仅部分预览"的文档,不可在线预览部分如存在完整性等问题,可反馈申请退款(可完整预览的文档不适用该条件!)。
- 3、如文档侵犯您的权益,请联系客服反馈,我们会尽快为您处理(人工客服工作时间:9:00-18:30)。
公司安全检查(SCL)表
单位:装置/设备/设施:成品油铁路装油栈桥、流体装卸臂、ps活动梯、装油鹤管、阀门日期:
序号检查项目检查标准产生偏差的主要后果
现有安全控制措施
L S R
风险等
级
建议改进措施
发生
频率
管理措施
员工
胜任
程度
安全设施
1 装油栈台护栏完好、消防和防
滑设备齐全、接地良
好、无放置其它物品、
栈台清洁。
人身伤害(滑倒、跌
落)、引发火灾或爆炸
(接地不良)、影响应
急救援。
定期巡检和现
场监护
胜任
配备消防器材,备
有应急物资和设备
2 1 2 2
加强管理和安
全教育
2 流体装卸臂设备完好、运行正常螺母松动、旋转臂不
灵活、接头渗漏。
定期巡检和现
场监护
胜任
配备消防器材,备
有应急物资和设备
1 1 1
加强管理和安
全教育
3 装油鹤管设备及附件完好、运
行正常
节气阀失灵或损坏泄
漏
定期巡检和现
场监护
胜任
配备消防器材,备
有应急物资和设备
1 1 1 1
加强管理和安
全教育
4 ps活动梯设备完好、运行正常螺母松动、旋转臂不
灵活、人身伤害(滑
倒、跌落)
定期巡检和现
场监护
胜任
配备消防器材,备
有应急物资和设备
1 1 1 1
加强管理和安
全教育
5 阀门设备完好、运行正常螺母松动、开关不灵、
法兰损坏漏油
定期巡检和现
场监护
胜任
配备消防器材,备
有应急物资和设备
1 1 1 1
加强管理和安
全教育
6 栈桥严格执行栈桥门禁制
度
人身伤害(油气中
毒)、引发火灾或爆炸
定期巡检和现
场监护
胜任
配备消防器材,备
有应急物资和设备
2 1 2 2
加强管理和安
全教育
审核人员及职务:分析人员及职务:
预先危险分析(PHA)记录表
单位:分析对象:装油工岗位、驾驶员岗位、厨师岗位分析人员及岗位:日期:
序号危害原因主要后果现有控制措施L S R 建议改正/控制措施
1 装油工岗位:人身
伤害和生产事。
现场管理、巡查不到位;三违、隐
患整改不及时。
人身伤害(滑倒、
跌落、中毒)、引发
火灾或爆炸
配备消防器材,备有应急物
资和设备;有现场管理制度
和专职巡查人员。
2 1 2 加强管理和安全教育
2 驾驶员岗位:交通
事故、财产损失。
违反车辆管理规定、违反交通法
规,车辆维修不及时。
人身伤亡和财产损
失。
GPS定位管理 1 1 1 加强管理和安全教育
3 职工食堂:食物中
毒、火灾、人身伤
害
违反职工食堂管理规定
食物中毒、液化气
引发的火灾或爆
炸、机械引发的人
身伤害。
有严格的管理制度;有应急
预案
1 1 1 加强管理和安全教育
预先危险分析(PHA)记录表
单位:分析对象:装油工岗位、驾驶员岗位、厨师岗位分析人员及岗位日期:2014.08.16
序号危害原因主要后果现有控制措施L S R 建议改正/控制措施
1 装油工岗位:人身
伤害和生产事。
现场管理、巡查不到位;三违、隐
患整改不及时。
人身伤害(滑倒、
跌落、中毒)、引发
火灾或爆炸
配备消防器材,备有应急物
资和设备;有现场管理制度
和专职巡查人员。
2 1 2 加强管理和安全教育
2 驾驶员岗位:交通
事故、财产损失。
违反车辆管理规定、违反交通法
规,车辆维修不及时。
人身伤亡和财产损
失。
GPS定位管理 1 1 1 加强管理和安全教育
3 职工食堂:食物中
毒、火灾、人身伤
害
违反职工食堂管理规定
食物中毒、液化气
引发的火灾或爆
炸、机械引发的人
身伤害。
有严格的管理制度;有应急
预案
1 1 1 加强管理和安全教育
评价准则
风险(R)=可能性(L)×后果严重性(S)1)危害发生的可能性L判定准则:
表1:危害发生可能性L判定
等级标准
5
在现场没有采取防范、监测、保护、控制措施,或危害的发生不能被发现(没有监测系统),或在正常情况下经常发生此类事故或事件。
4
危害的发生不容易被发现,现场没有检测系统,也未发生过任何监测,或在现场有控制措施,但未有效执行或控制措施不当,或危害常发生或在预期情况下发生。
3
没有保护措施(如没有保护装置、没有个人防护用品等),或未严格按操作程序执行,或危害的发生容易被发现(现场有监测系统),或曾经作过监测,或过去曾经发生类似事故或事件,或在异常情况下类似事故或事件。
2
危害一旦发生能及时发现,并定期进行监测,或现场有防范控制措施,并能有效执行,或过去偶尔发生事故或事件。
1
有充分、有效的防范、控制、监测、保护措施,或员工安全卫生意识相当高,严格执行操作规程。
极不可能发生事故或事件。
2)危害后果严重性S判定准则:
表2:危害后果严重性S判定
等级法律、法规及其他要求人员
财产损
失/万元
停工公司形象
5 违反法律、法规和标准死亡>50 部分装置(>2套)
或设备停工
重大国际
国内影响
4 潜在违反法规和标准丧失劳动能力>2
5 2套装置停工、或
设备停工
行业内、省
内影响
3 不符合上级公司或行业的
安全方针、制度、规定等
截肢、骨折、听力
丧失、慢性病
>10
1套装置停工或设
备
地区影响
2
不符合公司的安全操作
程序、规定
轻微受伤、间歇
不舒服
<10
受影响不大,几乎
不停工
公司及周
边范围
1 完全符合无伤亡无损失没有停工形象没有受损
3)风险等级R判定准则及控制措施:
表3:风险等级判定准则及控制措施R
风险度等级应采取的行动/控制措施实施期限
21~25巨大风险
在采取措施降低危害前,不能继续作业,
对改进措施进行评估
立刻
15~16重大风险
采取紧急措施降低风险,建立运行控制程
序,定期检查、测量及评估
立即或近期整改
6~12中等
可考虑建立目标、建立操作规程,加强培
训及沟通
2年内治理
1~5可接受
可考虑建立操作规程、作业指导书但需定
期检查或无需采用控制措施,但需保存记录
有条件、有经费时
治理
注:R=L×S—危险性或风险度(危险性分值)
L——发生事故的可能性大小(发生事故的频率)
S——一旦发生事故会造成的损失后果。
4)风险评估表
严重性
可能性
1 2 3 4 5
1 1
2
3
4 5
2 2 4 6 8 10
3 3 6 9 12 15
4 4 8 12 16 20
5 5 10 15 20 25。