SKY2调试培训
机型飞行训练培训需求分析规范
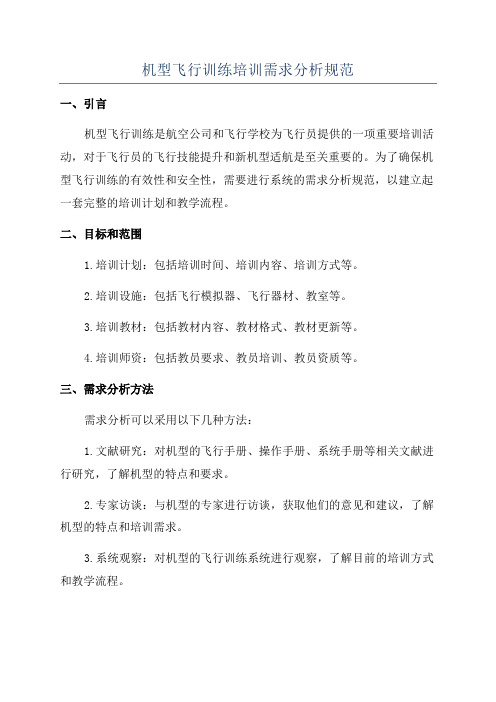
机型飞行训练培训需求分析规范一、引言机型飞行训练是航空公司和飞行学校为飞行员提供的一项重要培训活动,对于飞行员的飞行技能提升和新机型适航是至关重要的。
为了确保机型飞行训练的有效性和安全性,需要进行系统的需求分析规范,以建立起一套完整的培训计划和教学流程。
二、目标和范围1.培训计划:包括培训时间、培训内容、培训方式等。
2.培训设施:包括飞行模拟器、飞行器材、教室等。
3.培训教材:包括教材内容、教材格式、教材更新等。
4.培训师资:包括教员要求、教员培训、教员资质等。
三、需求分析方法需求分析可以采用以下几种方法:1.文献研究:对机型的飞行手册、操作手册、系统手册等相关文献进行研究,了解机型的特点和要求。
2.专家访谈:与机型的专家进行访谈,获取他们的意见和建议,了解机型的特点和培训需求。
3.系统观察:对机型的飞行训练系统进行观察,了解目前的培训方式和教学流程。
4.指标分析:通过对机型飞行训练的指标进行分析,确定培训的重点和难点。
四、需求分析内容基于上述的需求分析方法,可以得到以下几个方面的需求分析内容:1.培训计划:根据机型的特点和培训目标,确定培训时间和培训内容,制定培训计划。
2.培训设施:根据培训要求,评估现有的飞行模拟器和飞行器材是否符合培训需求,如不符合需进行设备升级或更新。
3.培训教材:编写或采购适合机型飞行训练的教材,包括操作手册、系统手册、教学演示材料等。
4.培训师资:确定教员的要求和培训计划,根据培训的特点对教员进行培训和资质认证。
五、需求分析报告需求分析报告是对机型飞行训练需求进行总结和归纳的文档,应包括以下几个部分:1.引言:介绍机型飞行训练需求分析的背景和目的。
2.目标和范围:明确需求分析的目标和范围。
无人机调试及应用

无人机调试及应用无人机调试及应用是一个非常广泛的话题,我们将在这里尝试提供一些关于无人机调试及应用的详细信息。
首先,无人机调试是指通过各种方法和工具对无人机进行测试、配置和优化,以确保其正常运行和高效工作。
无人机是由各种硬件和软件组成的复杂系统,因此它们需要正确的设置和配置才能正常工作。
调试无人机的过程可以包括以下几个方面:1. 硬件调试:这包括检查无人机的结构和构造以确保其安全和稳定。
同时,还需要调试电机、传感器等硬件设备,以确保它们的正常运行和相互协调。
2. 软件调试:无人机通常配备了各种软件,包括飞行控制系统和导航系统。
软件调试的目的是确保无人机的软件系统运行良好,并且能够正确解析和执行指令。
3. 调试无人机的操作系统:无人机的操作系统是控制整个系统的关键,它们通常是基于嵌入式系统的。
调试无人机的操作系统的目的是确保它们能够正确运行并提供无人机所需的功能和性能。
4. 调试无人机的遥控器和通信系统:无人机通常需要使用遥控器进行操控,这就需要调试遥控器和无人机之间的通信系统,以确保它们能够正确地与无人机进行通信。
5. 飞行测试:一旦无人机调试完毕,就需要进行飞行测试来验证无人机的性能和稳定性。
飞行测试可以帮助发现潜在的问题,并进行调整和优化。
总的来说,无人机调试是一个复杂和耗时的过程,需要专业的知识和经验。
调试无人机需要注意以下几个方面:1. 注意安全:无人机调试涉及到飞行测试,因此必须注意飞行安全。
飞行测试应该在安全的地方进行,并遵守当地的相关法规。
2. 理解无人机的工作原理:为了更好地调试无人机,必须深入了解无人机的工作原理和各个组件之间的相互关系。
这样才能更好地发现和解决问题。
3. 使用合适的工具和设备:调试无人机需要使用一些专业的工具和设备,如多用途测试仪、遥控器调试器等。
使用适当的工具可以更有效地进行调试。
4. 合理规划调试流程:调试无人机时应该有一个合理的计划和流程。
先进行硬件调试,确保无人机的结构和设备正常工作,然后进行软件调试和操作系统调试,最后进行飞行测试。
航空信号系统调试

航空信号系统调试
1. 系统概述
航空信号系统是飞机上的重要组成部分,用于向飞行员提供各种关键信息。
为了确保信号系统的正常运行,需要进行调试工作。
2. 调试步骤
2.1 检查硬件连接
首先,需要仔细检查航空信号系统的硬件连接情况。
确保所有连接插头都插入正确的接口,并紧固好连接螺母。
同时,检查电源线是否牢固连接,并检查电源供应是否正常。
2.2 测试信号传输
其次,需要进行信号传输测试。
通过仪器设备检测信号输入和输出的质量和准确性。
确保信号传输的稳定和可靠,在测试过程中记录并分析可能存在的问题。
2.3 调整信号参数
根据测试结果,可能需要调整信号系统的参数。
比如,调整信号的频率、幅度或相位,以达到最佳的信号传输效果。
在进行参数调整时,需要小心谨慎,并记录每次的调整。
2.4 功能测试
调试完成后,需要对整个航空信号系统进行功能测试。
确保系统正常工作,信号传输准确无误。
测试过程中,记录并分析任何异常情况,并采取相应的措施进行修复。
3. 注意事项
在进行航空信号系统调试时,需要注意以下事项:
- 根据系统规格和技术要求执行调试步骤;
- 严格按照操作手册和程序进行操作;
- 在调试过程中,小心处理灵敏的电子设备,避免损坏;
- 准备好必要的测试设备和工具,确保测试的准确性;
- 在调试前,对整个工作区进行安全检查。
4. 结论
航空信号系统调试是确保系统正常运行和信号传输准确的重要工作。
通过按照严格的步骤进行调试,可以发现并解决可能存在的问题,确保系统的可靠性和稳定性。
无人机飞行控制软件开发调试说明文档

无人机飞行控制软件开发调试说明文档背景该文档旨在向开发人员和测试人员提供关于无人机飞行控制软件开发和调试的指导和说明。
目标本文档的目标是确保无人机飞行控制软件的有效开发和高质量的调试。
通过正确的开发和调试过程,我们可以确保无人机的正常飞行和准确控制。
开发过程无人机飞行控制软件开发过程的关键步骤如下:1. 需求分析:仔细阅读和理解用户需求和规格说明,确保正确理解软件的功能和性能要求。
2. 设计阶段:基于需求分析,制定软件的整体结构和模块设计,确保软件的可靠性和可扩展性。
3. 编码实现:根据设计阶段的方案,进行软件编码实现,并确保代码的可读性和可维护性。
4. 单元测试:对每个单独的模块进行单元测试,确保模块的正确性和稳定性。
5. 综合测试:组合各个模块进行整体性能测试和功能测试,确保软件的一致性和健壮性。
6. 修复和优化:根据测试结果,修复软件中的错误和缺陷,并对软件进行优化以提高性能。
调试过程无人机飞行控制软件的调试过程需要以下步骤:1. 环境设置:确保正确设置开发和测试环境,并安装必要的软件和工具。
2. 软件部署:将编码实现的软件部署到无人机控制设备上,并确保正确配置和初始化。
3. 控制测试:通过模拟真实场景,对无人机进行各种控制测试,如起飞、降落、悬停、航行等,并记录测试结果。
4. 故障排查:如果在控制测试中发现问题或错误,需要进行故障排查并修复错误。
通过调试工具和日志分析,找到错误的根本原因。
5. 功能测试:对软件的各个功能进行测试,确保软件的功能符合需求和规格说明。
6. 性能测试:对软件的性能进行测试,如响应时间、飞行稳定性等。
7. 修复和优化:根据测试结果,修复软件中的错误和缺陷,并对软件进行优化以提高性能。
注意事项在开发和调试无人机飞行控制软件时,请注意以下事项:1. 按照软件开发和调试过程的步骤进行,遵循规范和设计原则。
2. 使用适当的工具和技术进行编码实现和调试,确保准确性和效率性。
无人机控制系统调试方案

无人机控制系统调试方案概述本文档旨在提供一份无人机控制系统的调试方案,以帮助确保无人机的正常运行和安全性。
调试是确保系统性能稳定和功能完善的重要步骤,需要遵循一系列正确的操作和步骤。
调试步骤步骤一:检查设备连接和供电确保无人机控制系统的所有设备都正确连接并获得足够的供电。
包括但不限于遥控器、飞行控制器、电机、电子速度控制器等。
检查电池电量,并确保电源连接可靠。
步骤二:检查传感器和通信模块检查无人机的各类传感器,如陀螺仪、加速度计、罗盘等,确保其正常工作。
同时,检查通信模块的正常连接,确保无人机和地面控制站之间的通信畅通。
步骤三:校准系统参数和传感器校准无人机控制系统的参数是调试的关键步骤之一。
根据无人机的具体型号和飞行控制器软件,按照相应的操作步骤进行校准。
包括但不限于校准罗盘、校准加速度计等。
步骤四:测试飞行模式和操控在安全的开阔区域,进行飞行模式和操控测试。
检查无人机的各种飞行模式,如手动模式、定高模式、定点模式等。
确保无人机能够稳定起飞、悬停、转向和降落。
步骤五:调试飞行控制参数根据无人机的性能和飞行特点,逐步调试飞行控制参数,以获得更好的飞行性能和控制稳定性。
根据实际情况,调整参数如控制增益、PID 参数等。
步骤六:记录和分析调试结果在整个调试过程中,及时记录各项操作和调试结果。
分析调试结果,针对问题进行进一步的调整和优化。
确保调试过程的记录完整、准确。
注意事项- 在调试过程中,确保安全第一,遵守相关法规和规定。
- 调试所用的飞行场地应当符合规定,必要时获得相关许可。
- 在调试过程中,注意观察无人机的状态,确保及时处理任何异常情况。
- 在调试过程中,勿将无人机飞行高度过高,以确保安全。
- 调试过程中的各项数据记录和日志应做好备份。
以上为无人机控制系统调试的基本方案,具体的操作细节可以根据无人机型号、软件版本等因素进行调整。
调试过程中需要细致的观察和分析,根据实际情况灵活应对。
SKY2-调试手册

Field Installation Manual REGEN DRIVEField Installation ManualREGEN DRIVESYSTEM:OTIS SKY Based using Bluelight machine and Rope Product and specification suited to below tableDESCRIPTION:This document is written as a guide for the adjustment of the complete OTIS SKY phase two system. The following sequence of instructions provide a guideline to the adjuster for the work to be performed from Manual Mode operation to movement of the car at high speed.Read this Document Carefully prior to removing the Elevator from Manual Operation. In keeping with the modular concept, the OTIS SKY II systems use a combination of proven components from previous systems Along with the new Otis VF variable frequency and regenerative drive.Warning:Starting up of REGEN Drive Sky II system should be performed by authorized personal only! The mechanical assembly works of the hoistway and the cab as well as the electrical installation in the hoistway and controller have to be finished to ensure successful inspection run. The encoder has to be mounted at the machine and properly connected to the drive. The electrical connections have to be completely installed and checkedSafety:In order to maintain a SAFE WORK ENVIRONMENT, follow safety rules and procedures as described in the “OTIS EMPLOYEE SAFETY HANDBOOK”This work and the information it contains (collectively referred to as ‘Work’) are the confidential property of the Otis ElevatorCompany (‘Otis’). This Work is delivered on the express condition that: it will be used or reproduced by Otis employees exclusivelyfor, or on behalf of, Otis; it will not be disclosed, reproduced, or distributed by or to others, in whole or in part, without the priorwritten consent of Otis: and, it and any copies will be promptly returned to Otis upon demand or upon termination of employment.Field Installation ManualREGEN DRIVEContents1. Preliminary checks (5)1.1. Check of safety conditions (5)1.2. Prepare for safe measurements (5)1.3. Pre-Power Up Visual Inspection (6)1.4. Insulation check: (7)1.5. GECB Indicator (8)2.Starting up in inspection (8)2.1. POWER UP (9)2.2.Parameter Setup (11)2.3.Encoder Adjustment (12)2.4.Check of Run –Direction (13)3. Pit Work/Equipment (15)4.Hoistway Work / Equipment (15)4.1.Check/Adjust the hoistway equalization (15)4.2. Statically balance the car (15)4.3. Setting the counter-balance (16)4.4. Dynamic balance the car (17)5. Prepare first Normal Run (18)5.1. Position DSBD shunt to normal (18)5.2. Check of hoistway signals (PRS-2 with RLEV/ADO) (19)6.Start up of the door system (20)6.1.Lock machine adjustment (20)6.2.START UP (20)7.Learn run (21)7.1. Learn run process (21)Field Installation ManualREGEN DRIVE7.2. Full Speed Operation (24)8.DCS – Door Check Sequence (25)9.Load Weighing adjust (27)9.1.Parameter setup (27)9.2.Offset calibration (28)9.3.Gain calibration (29)10.Final Adjustment (30)10.1. Floor Level Adjustment (30)10.2. Start Jerk, Rollback reduction (31)10.3. Check of ADO and RLV (Option) (32)10.4. Assignment for building configuration (33)10.5. Position Indicator setup (33)10.6. Turnover test for code inspection (34)Reference (35)Field Installation ManualREGEN DRIVE1. Preliminary checks1.1. Check of safety conditionsNote: The electrical connections have to be completely installed and checked.1.2. Prepare for safe measurementsField Installation ManualREGEN DRIVEField Installation ManualREGEN DRIVE1.4. Insulation check:Check the insulation of power, motor and lighting circuit.• Disconnect the line between HL1/HL2 and PE.• Check the insulation between HL1 and PE.• Check the insulation between HL2 and PE.• Check the insulation between L1-L2-L3 and PE each.• Check the insulation between U1-V1-W1 and PE each.Minimum value of insulation resistance shall be taken from Table.TableNominal circuitvoltageVTest voltage (d.c.)VInsulationresistanceMΩSELV 250 ≥ 0,25≤ 500 500 ≥ 0,5> 500 1000 ≥ 1,0When the circuit includes electronic devices, phase and neutral conductors shall be connected together during measurement.*Table refer to the EN81-1.1998 13.1.3 and GB/T 10058-1997 3.14.1Field Installation ManualREGEN DRIVE1.5. GECB Indicator*Before any operation, please make sure the LED lighting is correspond to the right status .Field Installation ManualREGEN DRIVE2.Starting up in inspection2.1. POWER UP• Warning: Hazardous voltages are present which can cause severe burns, injury or death. To prevent personal injury, no one should be standing directly in front of the controller and drive when it is being powered up.• CAUTION:Before powering up the controller, be sure all connections are correctly made, and all previous setup steps have been performed.1. Place a balance load on the platform and secure the hoistway.2. Ensure the main power is off and controller inspection switch is on INSPECTION.3. Ensure breakers F1C, F2C,F3C,F6C,F8C are off.4. Safety circuit check:In no energy status , check all the safety switches consecutively and make sure safetycircuit is through according to the wiring diagram along with controller.To the switchbridged by the ERO and TCI , please pay more attention.Checklist:Abbreviation DescriptionERO MES2 Machine room emergency stopRHS Removable wheel switchTES Top of car emergec stop switchSOS Safety overspeed switchUDLS UP and DOWN limited switchOS-1 Overspeed switch(govener)(GCS) Counterweight govener switch2BFS Oil buffer switch1BFS Second Oil buffer switchPES-2 Pit emergency stop switchPES-1 Second pit emergecy stop switch(CWS) Counter weight with safetyGTC Govener tension contactDS1-DSn Hoistway door contact(RDSn) Rear hoistway door contactGS Car door contact(RGS) Rear car door contact(EEC) Top of car emergec exitField Installation ManualREGEN DRIVE*Note:After power on,check the emergency stop button is available.(ES light on GECB is lighting and no run trend in any case including Inspction run when ES switch is pressed) 5. Confirm using a multi volt meter that each phase to phase voltage of main power is within aspecified value. Measure between each phase of main power and ground..6. Apply power to controller. Use a digital voltmeter to verify that L1, L2, & L3 terminals havethe correct voltage.7. Turn on circuit breaker check the voltages on transformers whether consistent to thetag.---*please choose the appropriate primary voltage level according to the local.8. Check the voltage before plug them and make sure that are complying with the wiringdiagram along with the controller.Measurement pointsRSL Voltage RSLVoltage Reference pointCar Link (1C) 1C:4 1C:3 (HL2) 24 VDCHall Link (1H) 1H:5 1H:4 (HL2) 24VDCHall Link (1G) 1G:5 1G:4 (HL2) 24VDCLodWeight (400M) 400M:4 400m:5(HL2) 24VDCNote:When plug the connector,ensure the main power is off.After plugging , repower.Field Installation ManualREGEN DRIVE2.2.Parameter SetupFirst of all, the version of the GDCB and GECB must be checked,the SCN must be as follow indicated or higher.• GDCB ---------AP130924CAB in service tool menu 2-1• GECB ---------GAA30780DAA in service tool menu 1-1-2-1Most parameters have already been set to default values. However, in order to enable the drive to run, the following parameters must be set according to the contract:• All parameters in service tool menu 3-1 CONTRACT• All parameters in service tool menu 3-5 PROFILERefer to Section 11 for the detailed descriptions for the parameters in the above menus. Since the Regenerative Drive is compatible with MCSS-type and TCBC-type controllers, some parameters are not applicable and do not have to be set, depending on which controller is used. The parameter Interface Type specifies the type of controller being used. If certain parameters do not have to be set, they will not be visible in the service tool.All applicable parameters noted above must be set before the drive is allowed to run. If not, the following error message will be visible in the event log:705 E2 Invalid000:00:00:00.04If this occurs, press SHIFT-ENTER to determine which parameter has not been set.Field Installation ManualREGEN DRIVE2.3.Encoder AdjustmentThe Regenerative Drive performs an automatic encoder calibration at the beginning of the first run after power-up. During the calibration, the brake remains dropped and a test current is commanded in the motor to determine the magnet position of the rotor relative to the encoder. The test lasts for about 4 seconds.During the test, a tone may be heard from the motor. This is normal and to be expected. No user intervention is required during the automatic calibration. Note that the adjustment is automatically repeated after certain faults are detected.When running the car on inspection after power-on, the inspection button must beheld in for a minimum of 5 seconds in order for the Encoder Adjustment to complete.Inspection runs are not possible until the En c oder Adjustment is complete. The brake remains dropped during the encoder calibration procedure. Note: this is applicable for PM motor only.Field Installation Manual REGEN DRIVEField Installation ManualREGEN DRIVEPressUPField Installation ManualREGEN DRIVE3. Pit Work/Equipment• Verify the buffer with Oil to the proper level.• Disassemble, clean, lubricate, and reassemble the car safeties (releasing carriage, safety lift rods, and rod arms) and, if provided, the counterweight safety.• Clean and adjust the safety releasing carrier and check that the governor will activate it. • Set the SOS switch so that it will break as lift arms move up.• While in the pit, adjust the bottom roller guides to give the safeties equal clearance from the rail. Lock up the roller guide stops.• Set the terminal limit switches to OPEN when the car sill past the terminal landing floor level 300mm.4.Hoistway Work / Equipment4.1.Check/Adjust the hoistway equalization4.2. Statically balance the carTest weights and platform balance weights (supplied) will be needed to perform this procedure. WARNING: Follow lockout/tagout procedures.1. Position elevator in bottom of hoistway (cab and counterweight even with each other).2. Remove slide guides from the top of car so the car "floats" free.3. Check the straightness of the carframe by pulling the car away from the rails, release it and watch it return.*Notes: If the carframe is true, both sides of the car will touch rails at about the same time. If one side touches rail earlier than the other, the carframe is racked or twisted andmust be straightened before continuing this procedure.4. Place test weights on platform until top of car is equally distant from rails front to back and post-wise.5. Push or pull car away from center, car should float back to its center position.6. Continue to add or reduce the test weights and position the weights on the platform to static balance the car.7. When you are satisfied with the static balance, note the position of the weights on the platform and the amount of weight used.8. Replace the top roller guides and adjust.9. Slide balance weights into channels under front and rear edges of platform equal to theField Installation ManualREGEN DRIVEweight and location of weight you added in steps 6 & 7.10. Be sure holes in weights line up so that you will be able to insert a 12mm threaded rod through them.11. Secure balance weights with 12mm threaded rod, nuts on ends of rod prevent weights from moving sideways. The J-bolt through the hook on threaded rod prevents vertical motion of weights.12. Tighten nuts holding the J-bolt until weights are snug against bottom of the channel.13. Run car to center of hoistway and repeat steps 2 and 3 (4, 5, 6, and 7 if necessary).14. The top of car should be equally distant from rails. If so, reinstall guides.15. Remove the test weights.*WARNING:The use and ownership of this work is defined in the legend upon the front page hereof.4.3. Setting the counter-balanceAfter the car has been statically balanced, the counter-balance can be set.1. Obtain the percent of counter-balance*Notes: Please set the 50% if the duty is below 1000kg and 47.5% for others(see the below the suggestion parameter.)2. Place a balanced load on the car.EXAMPLE:For a 1600kg. car with 47.5% counter-balance, the amount of test weight to add to the car fora balanced load is; 1600 x 0.475 = 760kg.3. Plug Service Tool into Drive Processor Board.4.Service Tool test 2-1-2, press “go-on” until you see “Mtr: Arms Vrms”.(See Arms below value)5. Position car in center of hoistway.6. Run car up approximately two (2) floors, and record the Service Tool readings.7. Run the car down past CWT about two (2) floors and record the Service Tool readings. Note: The “Mtr: Arms Vrms” readings on the service tool will not be steady. The readings will fluctuate during movement. Determine the average readings up and down. Add or subtract weight in the cab until Service Tool readings are close to the same. (The force needed to move the car should be the same in either direction). Add or remove weightsas necessary.8. Determine the amount of weight added or removed from the cab, add or remove the same amount weight to counterweight frame.9. Tie down weight frame.Field Installation ManualREGEN DRIVE4.4. Dynamic balance the carDynamic balance is affected by the parts of the equipment that change weight between the top and bottom of the hoistway. Some fixed positions have to be established in order to make good dynamic balance possible. In order to accomplish this, it has been found that the centre of gravity of the car, the centre of car travelling cable hanger fastening, and the centre of the compensating chains hanger fastening to the car must be in the same vertical plane of straight line.The procedure for establishing running balance is as follows:• Checks are to be made with no load in car.• Centre bottom guides so that the "throat" of the guide stand is equally spaced around the rail.• Check location of various equipment in pit with reference to centre of hoist ropes.• Check location of travelling cables and compensation chains.• Check location of hitches for travelling cables and compensation chains.• Run car from bottom to top with the top guide openings backed of with no spring tension.If the "out of balance" is found to be excessive, then the springs may need to be entirely removed.• If the rear of the car seems to have become heavy, with car at upper landing, causing the car top to lean toward the rear, it indicates the travelling cable hitch should be movedtoward the front of the car, if the top of car leans to the front of the hatch, thenthe opposite movement of the travelling cable hitch is necessary. The movementnecessary will be relatively small, so no great change in location should be required.• Always be sure to keep the centreline of the compensating chains and centreline of traveling cable hitches in the same plane, if change of cable hitch is indicated.• A situation may arise where the relocation of the travelling cable hitch on the car requires a cable loop greater than its natural loop. A compromise in the hitch location may have to be made to suit the cable loop. The cables should not ride hard against the car or be dragged by the platform as car leaves or approaches the lowest landing.• Finally, the guides at top and bottom of the car should be adjusted to keep the guides off the stops but with minimum pressure to centralise the car.Field Installation ManualREGEN DRIVEField Installation ManualREGEN DRIVE5.2. Check of hoistway signals (PRS-2 with RLEV/ADO)Field Installation ManualREGEN DRIVEThe distant is 197mm between door middle line and fix coupling, kicking-roller is just against the rail. If the out-to-out distance between the coupling and the movableField Installation ManualREGEN DRIVE7.Learn run7.1. Learn run processIf the drive is being used with TCBC-type controller (see parameter Interface Type), then the learn run has to be performed before the first normal run. The learn run must be repeated if a door zone magnet was moved. Before starting the learn run, the parameters Number of, Bottom Landing, and Landing in 1LS have to be set correctlyThe learn run can be started from anywhere in the hoistway. If the car is positioned in a door zone within 1LS, the drive assumes this is the bottom landing and starts the learn run from there. Otherwise, it performs a “find bottom landing” run before the learn run.In the “find bottom landing” run, the car is automatically moved up out of 1LS (0.2m/s) if it was positioned in 1LS. When outside of 1LS, it is moved down with 0.5m/s until it enters 1LS. Then it is moved down with 0.2m/s counting landing vanes (starting from parameter “ Landing in 1LS ”) until it enters the vane of landing 0. There it stops, ready for a learn run.For the learn run, the car runs up from the lowest LV to the highest LV zone with 0.2 m/s within the 1LS and 2LS and with 0.4m/s between the LS. The drive stores the center position of each LV zones and the length of all LV zones. The center of the lowest LV zone is set to the position of 10.000m.The learn run menu can be left during an ongoing learn run via the <MODULE>,<FUNCTION> or <SET> keys on the SVT in order to visit other SVT menus in the drive or in other components of the elevator, the learn run continues. At the end of the learn run, the learn run menu must be entered again to acknowledge the result. Also, after the completion of the “find bottom landing” run preceding a learn run, the start of the learn run must be acknowledged in the learn run menu (opportunity to verify visually that the car is in fact in the bottom landing).Field Installation ManualREGEN DRIVEField Installation ManualREGEN DRIVEField Installation Manual REGEN DRIVEField Installation ManualREGEN DRIVE8.DCS – Door Check SequenceNote:In case of failure of a hoistway door contact, the car stops on this floor and is locked. An error message is shown. After elimination of all errors, the car has to be moved to the bottom landing first before starting the DCS RUN once again,and it’s necessary of switches of LVC,LV1 and LV2 on GECB opening.Attention:The new feature Hoistway Access Detection (HAD) has been implemented to protect persons entering the hoistway and not properly following the safety instructions.If the DS contact is opened for longer than 4 seconds the TCBC will go into HAD mode, the event “0306 HWY Access” is logged.The blinking message “Switch INS” appears in the Status menu.The fault will not be cleared by switching the power off and on, the only way to bring the elevator back into normal operation is:• by ERO or• by pressing PES for at least 2 seconds.• by INS on TCIField Installation ManualREGEN DRIVEField Installation Manual REGEN DRIVEField Installation ManualREGEN DRIVEField Installation ManualREGEN DRIVE9.3.Gain calibrationField Installation ManualREGEN DRIVE10.Final Adjustment10.1. Floor Level AdjustmentField Installation ManualREGEN DRIVE10.2. Start Jerk, Rollback reductionField Installation ManualREGEN DRIVE10.3. Check of ADO and RLV (Option)Field Installation Manual REGEN DRIVEField Installation ManualREGEN DRIVE10.6. Turnover test for code inspectionField Installation ManualREGEN DRIVEReference1.GAA30780DAA_BRD : Software Release Document for GCS222MMRMCS220-C/-CX GeN2 ACD.2.GAA30780DAA_INS : List of Installation Parameters3.GAA30780DAA_IO : RSL :list of Inputs and Outputs4.GAA30780DAA_REF :Service Tool Reference List5.GAA30780DAA_STM : Service Tool Manual6. DAA26800H_CSU : OMU OTIS Memory Unit7. 55661 :Gen2 Modular Rengenerative Drive Operating Manual8. HAD adjustment manual : Along with Door Operator9. Parameters Table。
组装调试与维护

对电池进行充电。2、Fra bibliotek电放电电流:放电电流不得超过规定的最大放电电流,过大电流放电会导致容 量剧减并导致电池过热膨胀。
放电温度:电池必须在规定的工作温度范围内放电。当电池表面温度超过
70°C时,要暂时停使用,直到电池冷却到室温为止。 过放电:过放电会导致电池损坏,放电时不得使单片电池的电压低于3.6V。 3、贮存 电池应放置在阴凉的环境下贮存,长期存放电池时(超过3个月),建议置于
12、自定义舵机通道控制 13、批量航线动作任务设置 14、实时飞行航线编辑 15、F通道控制器 16、相对坐标编辑器 17、摄影测量工具包 18、仿真飞行模拟 19、飞行任务导入/导出
三
遥控器安装调试
- 21 -
遥控器,英文名(Remote Control),意思是无线电控制,通过它可 以对设备、电器等进行远距离控制。主要分为工业用遥控器和遥控模型用遥 控器两大类。
桨和木桨等。
尼龙桨
碳纤维桨
木桨
5
6
电池
电池是将化学能转化成电能的装置。在整个飞行系统中,电池作为能源储 备,为整个动力系统和其他电子设备提供电力来源。目前在多旋翼飞行器上,
一般采用普通锂电池或者智能锂电池等。
普通锂电池
智能锂电池
遥控系统
遥控系统由遥控器和接收机组成,是整个飞行系统的无线控制终端。
MODEL SEL项:如下图所示
进入后,选择NEW新建遥控器控制模式。并在TYPE中选择AIRPLANE 类型,其他所有设置保持默认。 双击LNK进入LINKAGE MENU页面并选择FUNCTION,如下图所示:
第2步:为U通道选择一个开关: 我们将第7通道和遥控器上的SC三档开关设置为控制模式切换开关(此 处为举例,用户可以根据自己的需要设置其他通道为控制模式切换开关)。 进入FUNCTION第二页,并将光标移至第7通道AUX5的CTRL位,如下图所 示:
无人机飞控训练计划

无人机飞控训练计划阶段 1: 入门。
了解无人机基本概念和术语。
在模拟器中练习基本操作(起飞、降落、悬停)。
学习安全规程和操作注意事项。
阶段 2: 基础飞行技能。
掌握无人机运动的控制(横滚、俯仰、偏航)。
练习基本的操纵技巧(例如悬停、转弯、直线飞行)。
提高空间感知能力和协调能力。
阶段 3: 进阶飞行技巧。
学习高级操纵技巧(例如翻滚、俯冲、筋斗)。
练习在不同环境中飞行(例如有风条件、窄小空间)。
了解不同无人机类型的特性和控制差异。
阶段 4: 实际应用。
应用无人机进行各种任务(例如航拍、货物运输、搜救)。
学习相关法律法规和操作限制。
培养对无人机操作的安全意识和责任感。
阶段 5: 持续改进。
定期练习和提升飞行技巧。
了解新的技术和行业趋势。
寻求有经验的飞行员指导或参与培训计划。
中文回答:无人机飞控训练计划。
阶段 1: 入门。
了解无人机基本知识和术语。
在模拟器中练习基本操作(起飞、降落、悬停)。
学习安全规程和操作注意事项。
阶段 2: 基础飞行技能。
掌握无人机运动的控制(横滚、俯仰、偏航)。
练习基本的操纵技巧(例如悬停、转弯、直线飞行)。
提高空间感知能力和协调能力。
阶段 3: 进阶飞行技巧。
学习高级操纵技巧(例如翻滚、俯冲、筋斗)。
练习在不同环境中飞行(例如有风条件、窄小空间)。
了解不同无人机类型的特性和控制差异。
阶段 4: 实际应用。
应用无人机进行各种任务(例如航拍、货物运输、搜救)。
学习相关法律法规和操作限制。
培养对无人机操作的安全意识和责任感。
阶段 5: 持续改进。
定期练习和提升飞行技巧。
了解新的技术和行业趋势。
寻求有经验的飞行员指导或参与培训计划。