工装培训教材
PPAP完整版培训教材

PPAP完整版培训教材什么是PPAP?PPAP (ProductionPart Approval Process) 是汽车及航空航天⾏业⽤于批准⽣产件的⼀个流程。
对于汽车⾏业,PPAP要求由AIAG主导的《PPAP⼿册》进⾏规范。
简单来说顾客对供应商的产品、⽣产条件、⽣产过程等⽅⾯的书⾯约定与认可况顾客不要求通知的情况顾客不要求通知的情在下列情况下不要求通知顾客和提交(如:PSW)。
供应商有责任跟踪更改和/或改进,并更新任何受到影响的PPAP⽂件。
注:任何情况下,⼀旦影响顾客产品的装配性、成型、功能、性能和/或耐久性,便要求通知顾客。
1.对部件及图纸的更改,内部制造或由分供应商制造,不影响到提供给顾客产品的设计记录;2.⼯装在同⼀⼯⼚内移动(⽤于等效的设备,过程流程不改变,不拆卸⼯装),或设备在同⼀⼯⼚内移动(相同的设备、过程流程不改变);3.设备⽅⾯的更改(具有相同的基本技术或⽅法的相同的过程流程);4.同样的量具更换;5. 重新平衡操作⼯的作业含量,对过程流程不引起更改;6.导致减少PFMEA的RPN值的更改(过程流程没有更改);7.只对散装材料:I.对批准产品DFMEA(配⽅范围、包装设计)更改;II.对PFMEA(过程参数)的更改;III.不会严重影响到特殊特性(包括在批准的规范限值内改变⽬标值点)的更改;IV.对批准的商品成分的更改(在化学提纯服务(CAS)系列中CAS数字没有改变);V.⽣产不涉及特殊特性的原材料的分供应商⽣产现场发⽣变化;VI.不涉及特殊特性的原材料的新货源;VII.加严的顾客/销售接受容差限值。
顾客提交要求-证明的等级1 提交等级供应商必须按照顾客要求的等级,提交该等级规定的项⽬和/或记录;等级1-只向顾客提交保证书(对指定的外观项⽬,还应提供⼀份外观批准报告);等级2-向顾客提交保证书和产品样品及有限的⽀持数据;等级3-向顾客提交保证书和产品样品及完整的⽀持数据;等级4-提交保证书和顾客规定的其它要求;等级5-在供应商制造⼚备有保证书、产品样品和完整的⽀持性数据以供评审。
焊装工装夹具培训教材.pptx
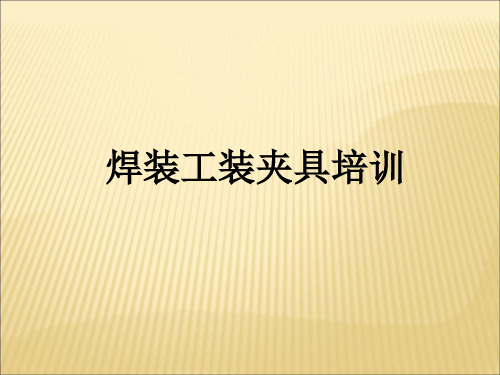
(二)工位器具的种类
料箱 料车 料架 料架
工具柜 踏台
垃圾车 工艺小车
(三)工位器具保养
1、 保持工位器具的清洁,一般一周要彻 底的清扫一次。
2 、在移动工位器具时,发现轮子下有异 物应及时清理。
3 、要定时给轮子加油。
二、什么是夹具
定义:夹具是一种保证产品质量并便利和 加速工艺过程的一种工艺装备,是用于 定位和夹紧的一种附加装置。 夹具又称卡具。从广义上说,在工 艺过程中的任何工序,用来迅速、方便、 安全地安装工件的装置,都可称为夹具。 例如焊接夹具、检验夹具、装配夹具、 机床夹具等。
C、夹紧力的着力点:不能产生力矩,一般应使着力点 正好位于定位支撑之上或尽量使着力点位于几个支撑所组成 的定位面内,并应使夹紧力作用在零件钢度最大的位置。
装焊夹具
三、装焊夹具
机械部分、 控制部分
装焊夹具 由于车身零件是薄钢板件,其刚性差,
所以在装焊过程中必须将工件固定到专用 夹具上,以保证各零件相互之间搭接面贴 合以及相对位置准确。
未定位前的工件相当于自由刚体,是无法进行加 工的,因此,为了使工件在夹具中有一个正确位置, 必须对影响工件加工表面位置精度的自由度加以限 制。
(四)六个自由度的概念
要使工件在夹具中的位置完全确定,其充分 必要条件是将工件靠置在按一定要求布置的6个支 承面上,使工件的6个自由度全部被限制,其中每 个支承点相应地限制一个自由度。这就是六点定 位规则,又称“六点定律”。6个支承点的分布方 式,与工件的形状有关
各种工艺装备。
(一)工装的种类:
包括:夹具、模具、刀具、辅助工具及测
量工具,在焊装车间还泛指工位器具、
吊具等。
夹具:顾名思义,用以装夹工件(或引导刀具)ቤተ መጻሕፍቲ ባይዱ装置。 模具:用以限定生产对象的形状和尺寸的装置。
FMEA_培训教材[1]
![FMEA_培训教材[1]](https://img.taocdn.com/s3/m/3411f1af55270722192ef7c8.png)
PPT文档演模板
FMEA_培训教材[1]
什么是FMEA
在产品设计阶段和过程设计阶段,对构成产 品的子系统、零件,对构成过程的各个工序 逐一进行分析,找出所有潜在的失效模式, 并分析其可能的后果,从而预先采取必要的 措施,以提高产品的质量和可靠性的一种系 统化的活动。
PPT文档演模板
FMEA_培训教材[1]
OEM:分析产品和主机厂装配过程之间的关系对于有效的 FMEA非常关键。
供应链:包括组装、装配、热处理、喷漆、电镀、焊接或其 它精加工服务等。
法规:对安全和环境方面明确要求并监控其实施的政府机构。
明确顾客有助于定义功能、要求和规范,并能帮助确定相关失 效模式的后果。
PPT文档演模板
FMEA_培训教材[1]
PPT文档演模板
FMEA_培训教材[1]
PPT文档演模板
FMEA_培训教材[1]
PPT文档演模板
FMEA_培训教材[1]
缺陷可能性及影响分析
FMEA编号:
产品系统 FMEA
过程系统 FMEA
共 页第 页
类型/型号/生产/批号:
制表:
日期:
系统编号/系统元素: 功能/任务:
零件号
负责人:
部门:
• 由纽约广告代理的老板Alex F Osborn在1930年发 明,其前提是在一般的讨论中,人们害怕别人批评 而约束自己,因此而不能产生有创意的点子。
• 脑力风暴包括创造一种氛围,让人们感到无拘无束, 此时人们可能提出在平时认为不太可能提出的解决 方案,但往往收到意想不到的效果。
PPT文档演模板
FMEA_培训教材[1]
FMEA的类型
SFMEA —— 对产品开发、过程策划综合评估,通过系统、 子系统不同层次展开,自上而下逐级分析,更注重整体性、 逻辑性。
第五版FMEA培训教材-fmea 第五版

一、FMEA的开发与发展
怎样才能不失败或减少失败?
简单,可以采用 FMEA的方法!
一、FMEA的开发与发展
20世纪50年代,美国格鲁曼公司开发了FMEA,用以 飞机制造业的发动机故障预防,取得较好成果。
20世纪80年代中期,美国汽车工业将FMEA运用于生产 过程中。
90年代,美国汽车工业将FMEA纳入QS9000标准。
二、新版FMEA的介绍
FMEA是一套面向团队的系统的,定性分析方法,其目的是: l评估产品/过程中失效的潜在技术风险 l分析失效的起因和影响 l记录预防和探测措施 l针对降低风险的措施提出建议
技术风险(FMEA) 是否对产品和过程中的 潜在失效进行分析?
在本手册范围中
财务风险 采取纠正措施后产品是 否有利润可图?
二、新版FMEA的介绍
5、产品和过程FMEA在三种情况下使用。 ① 新设计,新技术,或新过程。
FMEA 的范围包括完整的设计、技术和过程。 ②现有设计和过程的新应用
FMEA 的范围包含新环境,新场地、新应用或使用概况(包括工作周期、法规要求等 )下的现有设计和过程。应关注于新环境,新场地或新应用对现有设计或过程的影响
和纠正措施
在产品开发启动 之前的概念阶段 开始FMEA计划; 从DFMEA到PFMEA 的信息流, DFMEA和PFMEA应 在同一时间段内 执行,以便优化 产品和过程设计
在充分理解设 计概念后 , 启动DFMEA
在充分理解生 产概念时 , 启动PFMEA
在用于报价 的设计规范 发布之前, 完成DFMEA分 析
二、新版FMEA的介绍
6. DFMEA
DFMEA是一种主要由设计责任工程师/团队使用的分析技术,用于确保在将零件交付生产之前,尽 可能考虑并解决潜在失效模式及其相关失效起因或机理。
FMEA培训教材4版new

FMEA手册的历程: 第一版:1993年2月 第二版:1995年2月 第三版:2001年7月 第四版:2008年6月 第四版的主要变动:
-强调FMEA的过程和结果需要管理者支持、关注和评审; -改进了严重度、发生频度、探测度的评级表; -不再强调“标准表格”; -建议不要把RPN作为风险评估的首要方法。使用RPN阀值是一种
SOP
………
批量爬 坡
2TP
100 初步设计
1000 A样件
仅有思维、图纸
10000
图纸释 放
100000
OTS样 件
有思维、图纸、 模具、检具、设 备、试制场所等
小批量 确认
有思维、图纸、模具、 检具、设备、人员、厂 房、仓储等
时间阶段
10 11 12 1 2 3 4 5 6 7 8 9 10 11 12 1
23
FMEA 成 功 的 条 件
适时性:在“时间之窗”关闭之前
+
小组的努力:集体的智慧
24
适时性
成功实施FMEA项目的最重要因素之一
FMEA是预防性的 不是反应性的
应当尽量避免失效 而不是等着顾客提出申诉
25
成功实施FMEA项目的最重要因素之一是时间性。其含义 是指“事件发生前”的措施,而不是“事实出现后”的演练。为 实现最大价值,FMEA必须在产品或过程失效模式被纳入到产品 或过程之前进行。事先花时间很好地完成FMEA分析,能够最容 易、低成本地对产品或过程进行更改,从而最大程度地降低后期 更改的危机。FMEA能够减少或消除实施可能会带来更大隐患的 预防/纠正性更改的机会。
FMEA由多功能小组开发,小组规模会根据设计的复杂性和 公司的规模大小而有所不同。小组要有相关的技术知识、足够的 时间,以及管理者批准的权限。
IATF16949培训教材-最新版
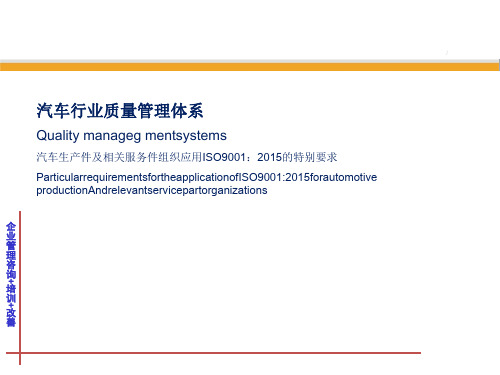
售后市场零件
并非由OEM为服务件应用要采购或放行的替换零件,可能控照或未按照原始设备规范进行生产。 企
业 管 理
授权 对某(些)人的成文件许可,规定了其在组织内部授予或拒绝权限或制裁有关权利上和责任。
咨
询 挑战(原版)件
培
具有已知规范,经校准并且可追溯到标准的零件,其预期结果(通过或不通过)用于确认防错装
1. 噪音改善和防护,车间安 装风冷水循环系统。
2. 策划员工年度培训计划
结果评审
验收完成
企 业 管 理 咨 询 培 训 改 善
++
1
4.3确定质量管理体系的范围 组织应明确质量管理体系的边界和适用性,以确定其范围。 在确定范围时,组织应考虑: a)各种内部和外部因素,见4.1; b)相关方的要求,见4.2; c)组织的产品和服务。 如果本标准中全部要求适用于组织确定的质量管理体系范围,组织应实施本标准的全部要求。
企 业 管 理 咨 询 培 训 改 善
++
++
1.范围 2.规范性引用文件 3.术语和定义
4.组织环境 4.1 理解组织及其环境 4.2 理解相关方的需求和期望 4.3 确定质量管理体系范围 4.4 质量管理体系及其过程
5.领导作用
企 业
5.1 领导作用和承诺 5.2 方针
管
5.3 组织的角色、职责和权限
++
1
组织背景
认知了解需求
企业综合介绍 企业战略规划
企业文化系统
公司介绍、组织结构、发展历程、发明专利、知识产权、荣誉成绩、科技创新。
商业模式:客户细分、价值主张、渠道通路、客户关系、关键业务、核心资源、重要伙伴、成本结构。 战略管理:维持优势、结构控制、治理管理。
DFLZM、QRQE、QRQC培训教材
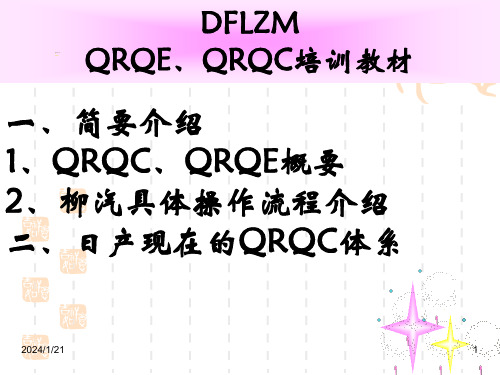
2024/1/21
14
▪ 从柳汽正式运行的一年情况看效果较明显, 现场质量问题的处理速度得到较大提高, 整车一次下线合格率由40%提高到60%以 上,VES评审问题点也下降了50%,在此
活动过程中由于形成详细记录,对每一车
型出现问题、处理措施以及效果等一目了
然,一方面可避免重复问题的发生,另一
方面在新车开发过程中可以借鉴,避免出 现相同错误,QRQE活动过程本身就是一 个技术资源积累的过程。
▪ 1、每日15:00~16:00由各车间组织班组长对前 一工作日质量处理情况进行检查落实,同时通报 当天质量问题发生情况,并初步划分责任班组, (质量信息来源:整车检验、VES、PDI、一次下 线合格率统计、车间VES以及车间内部工序间质 量问题反馈)。
▪ 2、班长在第二天早会将问题落实到责任人,提出 改善措施及完成时间,下一次QRQC会在目视板 上公布完成情况,并绘制完成率的图表。
始整合生产过程品质提升活动。
2024/1/21
3
QRQC是指:
①以目标的达成为目标
②用源头对策来提高品质
源头对策是指? ③本工序工艺品质的完全保
证其核心组织为
为提高品质快速进行 PDCA循环
P
A
D
C
QRQC
(Quick Response Quality Control)
2024/1/21
4
▪ QRQC的特点:
▪ 当时的日产是? ▪ 对竞争对手的关注不够,只有自尊心很强 ▪ 官僚主义 先讨论 后行动
▪ 行动起来! ▪ 在讨论好坏之前,首先行动,采取措施 ▪ 打破部门间的隔阂 ▪ 迅速采取灵活的行动
2024/1/21
2
迅速采取源头对策是我们的紧急课题
汽车关键装配工序培训教材要点

轻卡一厂关键工序上岗和复审培训教材大纲1。
关键工序的概述 (2)1.1关键工序相关定义 (2)1.2轻卡一厂关键工序清单 (3)1。
3关键工序管理制度 (4)2。
关键工序影响因素 (5)2。
1关键工序影响因素概述 (5)2.2人员对关键工序的影响 (5)2。
3关键工序技能培训 (6)2。
4工具设备对关键工序的影响 (6)2。
5作业方法对关键工序的影响 (10)2.6测量系统对关键工序的影响 (11)3.工具设备使用及保养知识 (12)3.1风动工具的使用及保养要求 (12)3.2扭力扳手的使用及保养要求 (12)3.3轻卡一厂现场使用的测量工具介绍 (15)1。
关键工序的概述关键工序,顾名思义,就是指关键件的加工制造和关键部位的装配调整工序。
关键工序控制的好坏,直接影响到我们产品的质量,甚至是车辆的安全和我们的品牌形象。
因此关键工序的管理一定是我们质量管理工作的重中之重.轻卡一厂作为宽体卡车的装配单位,一些工序点生产过程控制的好坏,直接影响到正台车辆的品质,为此,在轻卡一厂的生产现场并根据其工序点的重要度以及控制的难易程度,我们把一些工序点作为关键工序点进行控制,为了我们的员工在操作关键工序时能够了解并掌握关键工序点的操作要领并能够在对岗位质量认识上得到提高,我们结合专业厂实际编写关键工序培训教材,供关键工序新上岗培训和已上岗员工复审培训时员工的教材。
1.1关键工序相关定义1。
1.1、关键工序:关键工序是指关键件(指由其损坏或故障会引起对人身生命有直接影响的汽车事故或重大车辆灾祸的零件)的加工制造工序和关键部位(维持关键件机能的装配部位和完成关键件功能动作的部位)的装配调整工序.1。
1.2、质量特性:质量特性是指产品、过程或体系与要求有关的固有特性。
1.1.3、拧紧扭矩:扭矩是使物体绕轴心旋转或产生旋转趋势的物理量,扭矩=力X力臂。
当螺母和螺栓锁紧时会产生张力到螺栓上,这个力称为预紧力,它直接决定螺栓螺母连接可靠性。
- 1、下载文档前请自行甄别文档内容的完整性,平台不提供额外的编辑、内容补充、找答案等附加服务。
- 2、"仅部分预览"的文档,不可在线预览部分如存在完整性等问题,可反馈申请退款(可完整预览的文档不适用该条件!)。
- 3、如文档侵犯您的权益,请联系客服反馈,我们会尽快为您处理(人工客服工作时间:9:00-18:30)。
第四章:工装知识第一节:模具常识一、一般模具组成二、影响模具寿命的因素三、对冷冲模具用钢使用性能的基本要求四、模具安装、拆卸:A:单动模具安装B:双动模具安装C:单动模具卸下D:双动模具卸下E:模具的联合安装五、模具的一级保养:A:装模时的保养B:生产中的保养C:生产后的保养六、模具的二级保养:七、生产操作中的注意事项:八、模具修理:第二节:检具常识一、检具的构造:二、检具的制作工艺:第四章:工装知识冲压车间的工装包括模具、检具以及工位器具,这里我们将对模具和检具的常识向大家介绍一下,而工位器具的知识我们将不进行叙述。
第一节:模具常识一、一般模具的组成:1.工作零件:是完成冲压工作的零件;包括凸模和凹模等零件。
2.定位零件:是保证送料时有良好的导向和控制送料的进距;主要包括挡料销、定位销、侧刃等零件。
3.压料、卸料、顶料零件:这些零件的作用是保证在冲压工序完成后将制件和废料的排除;主要包括卸料板、顶料器、气动顶料装置等零件。
4.导向零件:是保证上模与下模相对运动时有精确的导向,使凸模、凹模间有均匀的间隙,提高冲压件的质量;包括导柱、导套、导板等零件。
5.安装、固定零件:这些零件的作用是使上述四部份联成整体,保证各零件间的相对位置,并使模具能安装在压力机上;包括上模板、下模板、模柄、固定板、垫板、螺钉、圆柱销等。
6.缓冲零件:包括卸料弹簧、聚氨脂橡胶和氮气缸等。
7.安全零件及其它辅助零件:主要有安全侧销、安全螺钉、工作限制器、存放限制器、上下料架、废料滑槽、起重棒、吊耳等。
安全侧销:主要作用是防止上模压料板紧固螺钉松动或断裂,导致压料板落下,造成人员、工装的重大损失。
存放限制器:主要作用是防止模具弹性元件长期受压而失效和防止刃口长期接触影响刃口的寿命。
(一般采用聚氨脂橡胶)工作限制器:主要作用是限制凸凹模的吃入深度。
二、影响模具寿命的因素:1.冲压工艺及冲模设计的影响及提高冲模寿命的措施:(1)冷冲压用原材料的影响。
例如:原材料厚度公差不符合要求、材料性能波动、表面质量差和不干净等:A.冲压前应对原材料的牌号、厚度、表面质量进行严格检查B.保证材料表面质量和清洁(2)排样和搭边的影响:排样方法与搭边值对模具寿命影响非常大,不必要的往复送料排样法和过小的搭边值往往是造成模具急剧磨损和凸凹模啃伤的重要原因。
(3)模具导向结构和导向精度的影响:必要和可靠的导向,对于减小工作零件的磨损,避免凸凹模啃伤极为有效。
(4)模具几何参数的影响:凸凹模的形状、间隙和圆角半径不仅对冲压件成形影响极大,而对模具的磨损影响也很大。
2.模具的材料的影响:模具的材料性质及热处理质量对模具寿命的影响是影响模具寿命诸因素中最重要的因素。
3.模具的热加工和表面强化的影响4.模具加工工艺的影响:模具加工后模具的表面粗糙度对模具的寿命影响很大,所以要根据制件情况,合理的选择加工工艺。
5.压力机的精度与刚性的影响6.模具的使用、维护和保养的影响7.正确使用、维护和保管模具是提高模具寿命的重要方面。
它包括模具正确安装与调整;注意保持模具的清洁和合理的润滑;防止误送料、上双料;严格控制凸模进入凹模的深度,控制校正弯曲、整形等工序中上模的下死点位置;及时的打磨、抛光等。
三、对冷冲模具用钢使用性能的基本要求:1.具有高硬度和强度,以保证模具在工作过程中抗压、耐磨、不变形、抗粘合;2.具有高耐磨性,以保证模具在长期工作中,其形状和尺寸公差在一定范围内变化,不因过分磨损而失效;3.具有足够的韧性,以防止模具在冲击负荷下产生脆性断裂;4.热处理变形小,以保证模具在热处理时不因过大变形而报废;5.有较高的热硬性,以保证模具在高速冲压或重负荷冲压工序中不因温度升高而软化。
四、模具安装、拆卸:模具的安装和拆卸是一名冲压工一项非常关键的技能,它基本上用到了压力机所有的操作:装模高度调整、微调、工作台夹紧与放松、工作台开出等。
从模具的角度看,在模具安装和拆卸的过程中很容易出现工装事故,容易对模具产生致命的伤害,另外装模调整的合理性对模具使用寿命、稳定性及冲压件的质量都有着非常直接的关系。
还有从生产的角度看,熟练掌握装卸模具的工作要领有利于缩短换模时间,从而提高劳动生产率。
以下就是模具安装和拆卸的程序以及注意事项进行叙述和说明:A、单动模具安装:1.工作台开出并清擦干净:开出前清擦工作台导轨,将废料等杂物清理干净,检查模具台两侧是否有物品超宽,以防止工作台开出时与压机主柱相干涉,引发事故。
工作台所停的位置要合理,以方吊模和放模为标准,但要与导轨的挡块留一定的安全距离;2.单动拉延模根据《作业指导书》把顶杆装好并确保顶杆长度一致:根据《作业指导书》上的顶杆图选用顶杆和顶杆位置,放好顶杆后要进行检查,保证顶杆的位置和长度的一致性,为了使模具摆放位置准确,根据《作业指导书》在模具相应的位置上放置定位销。
另外顶杆孔的盖板要定置摆放,以防丢失;3.模具吊上工作台并将中心与压机的工作台中心对齐:模具放置前要将模具的底面及上表面清擦干净,模具放好后检查各安装槽与压机T形槽的对齐情况,以方便安装;4.工作台开进并夹紧:工作台开进前对压力机底座进行清擦,工作台开进时一定要开到位后方可落下和夹紧;5.调好模具的安装高度(模具的安装高度=模具存放高度+10cm);6.单动拉延模在离模具上表面20-30cm处试顶杆,顶杆正确后将气垫落下;7.将滑块开至滑块底面与模具上表面触后,将上模螺钉装上并锁紧,下模螺钉放上即可,切记不要锁紧;8.滑块开到上死点,将留模样件取出,取下存放限置器;9.对模具进行清擦润滑;10.精调装模高度,滑块空行程两次后将模具合上,锁紧下模螺钉(空行程时注意模具各部份的工作情况是否正常,如有异常及时通知模修工);11.单动拉延模要调整好气垫压力值;12.首件调试合格后投入生产,填写《模具日点检表》和《自检记录表》。
B、双动模具安装:1.工作台开进与夹紧的步骤与单动模具相同;2.调整好模具的安装高度。
(双动模的安装高度是在模具的装模高度的基础上加上调整值,调整值一般在0.5-2.5之间);3.将滑块开到下死点(注意液压垫压力表的表值),将内外滑块夹紧器放松,并检查放松情况,待确认放松后用微调点动将滑块开到上死点。
由于操作人员无法看见内滑块内部的情况,故在滑块下行时一定要有专人看内滑块压力表的表值,当指针有动时,说明内滑块与模具已经接触,如果此时不在下死点,就应向上调整装模高度。
注:滑块夹紧器放松后,操作人员一定要逐个检查夹紧器的放松情况,以保证工作安全;4.安装螺钉,锁紧上模螺钉后将滑块开到下死点;5.将内外滑块夹紧后把滑块开到上死点,对模具进行清擦和润滑;6.滑块空行程二次后用微调将模具合上,锁紧下模。
空行程过程中模具的凸、凹模之间不应墩死,以保护模具型面不受损害;7.首件调试合格填写《工装日点检表》和《自检记录表》。
C、单动模具卸下:1.认真检查模具各部位是否完好、废料是否清除干净,并将模具各部位清擦干净;2.存放限置器放上,合模(使存放限置器轻微受力变形,若是刚性存放限置器则在快接触时使用装模高度调整)后将上下模具螺钉卸下;3.将滑块开到上死点后,工作台放松并开出;4.模具吊至存放地,清理工作台。
D、双动模具卸下:1.认真检查模具各部位并清擦干净,零件归位;2.将装模高度调整到模具的安装高度后将滑块开到下死点;安装高度为模具安装放松垫板时压机的装模高度;3.将内外滑块放松后滑块开至上死点,卸下安装螺钉。
夹紧器放松后一定要逐个对夹紧器进行检查;4.滑块开到下死点后将内外滑块夹紧。
夹紧器夹紧后一定要逐个对夹紧器进行检查;5.滑块开到上死点,将工作台放松并开出;6.模具吊至存放地,并清擦工作台面;7.模具吊回存放地点,用塑料布盖在模具上表面上。
E、模具的联合安装:联合安装指的是在一个工作台面上,同时安装两个或两个以上的模具进行生产。
其优点有:提高设备的使用率、生产效率高、制造成本低等;但其存在装卸不方便,模具制造要求高,另外生产的安全性下降等缺点。
模具联合安装的条件:①模具的闭合高度要求必须等高;②联合安装后冲压力的中心必须与压机的压力中心重合;③生产中操作必须方便。
五、模具的一级保养:模具的一级保养指的是在生产中操作人员对模具进行的日常保养,主要内容为清擦、润滑和检查。
A、装模时的保养:1.装模前要对模具的上下表面进行清擦,保证模具安装面和压机工作台面不受压伤及模具在生产中上下安装面的平行度;2.模具装好后将模具打开,将模具各部分清擦干净,特别是导向机构,对于表面件模具,其型面要清擦干净,以保证制件的质量;3.对模具各滑动部份进行润滑,涂润滑脂;4.模具各部份的检查,特别是安全件。
如:安全侧销、安全螺钉、侧护板、冲孔废料道等。
B、生产中的保养:1.生产中定期对模具的相应部分进行涂油。
如:拉延模的压料圈、圆角;修边模的刀口部位;翻边刀块部分等;2.定期对修边冲孔模的小孔废料道进行废料的清理。
C、生产后的保养:1.生产结束后要对模具进行全面的检查;2.对模具进行全面的清擦,保证模具的清洁度;3.将模具内的废料清理干净,保证废料盒中无废料;4.将模具的使用状态和使用后的情况如实地反馈到《模具使用工作传票》上。
六、模具的二级保养:模具的二级保养指的是根据模具的技术状态和复杂程度而制定的对模具进行的定期系统的保养。
此项保养工作由模修人员完成,并根据保养情况作好记录。
以下就不同的零件叙述其二保的要求和方法:A、拉延模凸模、凹模:拉延模的凸、凹模主要出现的问题是拉毛及型面的压坑,保养时主要对模具的圆角拉毛部位进行抛光。
如果出现压坑要对模具进行补焊,再进行修顺;B、导向零件(导柱、导套及导板等):模具在工作中会出现拉痕等现象。
产生的主要原因有润滑油脏及导向间隙偏等。
导向零件产生拉痕时,采取用油石推顺后抛光的办法进行消除;C、修边刀口:模具在使用过程中刀口部分易出现崩刃和刃口塌陷现象,此时要对模具损坏的部位进行补焊修配;D、弹簧等弹性零件:在使用过程中,弹簧是模具最易损坏的零件之一,通常出现断裂和变形现象。
采取的办法就是更换,但是更换过程中一定要注意弹簧的规格和型号,弹簧的规格型号通过颜色、外径和长度三项确定,只有在此三项都相同的情况下才可以更换;E、冲头、冲套:模具上使用的冲头、冲套大部分都采用标准件,模具在使用过程中冲头易出现折断、弯曲和啃坏现象,冲套一般都是啃坏的。
冲头和冲套的损坏一般都用相同规格的零件进行更换。
冲头的参数主要有工作部分尺寸、安装部分尺寸、长度尺寸等;F、紧固零件:检查紧固零件是否松动、损坏现象。
采取的办法就是找相同规格的零件进行更换;G、压料及卸料零件:压料零件如压料板、优力胶等,卸料零件如卸料板、气动顶料装置等。