油液动压径向轴承设计及计算【开题报告】
液体动力润滑径向滑动轴承的设计计算

§13-5 液体动力润滑径向滑动轴承的设计计算•、动压油膜和液体摩擦状态的建立过程流体动力润滑的工作过程:起动、不稳定运转、稳定运转三个阶段起始时*0,轴颈与轴承孔在最下方位置接触1、起动时,由于速度低,轴颈与孔壁金属直接接触,在摩擦力作用下,轴颈沿孔壁向右上方爬开。
2、不稳定运转阶段,随转速上升,进入油楔腔油逐渐增多,形成压力油膜,把轴颈浮起推向左下方。
(由图b—•图c )3、稳定运转阶段(图d):油压与外载F平衡时,轴颈部稳定在某一位置上运转。
转速越高,轴颈中心稳定位置愈靠近轴孔中心。
(但当两心重合时,油楔消失,失去承载能力)(1)相对运动两表而必须形成一个收敛楔形向心轴承动压油膜形成过程(2) 被油腹分开的两表面必须有一定的相对滑动速度v 沙其运动方向必须使润滑从大口流进, 小口流出。
(3) 润滑油必须有一定的粘度,供油要充分。
V 越大,n 越大,油膜承载能力越高。
实际轴承的附加约束条件:二、最小油膜厚度h 込1、几何关系压力 PV 值 速度 最小油膜厚度温升"[p]吨]札鈕—]图13-13径向滑动轴承的几何参数和油压分布0—轴颈中心,(X—轴承中心,起始位置F与00:重合,轴颈半径-r,轴承孔半径R・•・半径间隙: (13-6-1)C = =芯=D-丘半径间隙: 2 2 (13-6)A C相对间隙:(13-7)偏心距:它=C,O1(13-8)偏心率:(13-9)以00:为极轴,任意截面处相对于极轴位置为“ 处对应油膜厚度为h,h= C(l+£cu 朝OPj. = C+e = R—r +eW=18D时:h^ = R-r-e=C-e = C(l-^) (13_10)h的推导:在厶占。
】中,根据余弦定律可得R2 =『+ (r + hY - 2叹 +/?)cos @= [(r + A) -ecos 如'+『2 2略去高阶微量 e sm,再引入半径间隙c= R—*,并两端开方得豎®¥ 去h(13-12)三. 流体动力润滑基本方程(雷诺方程)流体动力润滑基本方程(雷诺方程)是根据粘性流体动力学基本方程出发,作了一些假设条件后 简化而得的。
开题报告

第2 章实验台整体方案的设计本文设计的滑动轴承试验台由液体动压径向滑动轴承台架、电机、传动机构、加载系统、润滑系统、数据采集与处理系统等组成。
2.1滑动轴承试验台的设计要求及实现的功能2.1.1 试验台的设计要求根据技术开发协议书规定的要求如下:1.电动机的转速为1500rpm=2坝4试轴瓦的内径为200mm。
轴瓦的内径不变,轴瓦宽度为40mm,80ram,120mm,160ram,200mm的轴承两套,一套用于油润滑,一套用于油汽润滑;3.轴瓦的材料为铸造铜合金(ZcuSnl0Pbl);4.负载转速为350rpm;5.加载方式为下侧加载,压力为0—40KN可调;6.滑动轴承端面密封,循环冷却;7.宽度为120mm、160mm、200mm的轴瓦布置30个传感器,宽度为40mm和80mm的轴瓦布置10个传感器;8.被测轴瓦布置为下侧轴瓦;9.数据采集频率为10HZ;10.压力测量精度为±O.25%F·S,温度测量精度为O.2%。
2.1.2 实验台实现的功能本文设计的滑动轴承试验台基本思路是根据滑动轴承的润滑基本原理,研制用于理论研究的滑动轴承油膜压力测试、油膜温度测试、电机转速和扭矩测试的装置。
该滑动轴承试验台的设计是在调研和分析现有滑动轴承试验台的功能和性能基础上,综合运用机械设计、测试技术、信号处理等理论,借用专业的数据分析处理软件,主要实现以下功能:(1)实现以摩擦区的温度、压力为评判指标的单相流体与气体液相两相流体润滑的效果对比试验;(2)实现轴瓦内油膜压力和温度的测量;(3)实现电机和滑动轴承转速等的信号输出。
2.2试验台的总体方案设计试验台由液体动压径向滑动轴承台架、电机、传动机构、加载系统、润滑系统、数据采集系统等组成。
(1)液体动压径向滑动轴承台架:由外壳体、主轴滑动轴承座、加载传动机构润滑管路等组成,外壳体是焊接件。
壳体上方加有观察窗,以便于在实验时观察其内部工作情况。
液体动力润滑径向滑动轴承设计计算

液体动力润滑径向滑动轴承设计计算流体动力润滑的楔效应承载机理已在第四章作过简要说明,本章将讨论流体动力润滑理论的基本方程(即雷诺方程)及其在液体动力润滑径向滑动轴承设计计算中的应用。
(一)流体动力润滑的基本方程流体动力润滑理论的基本方程是流体膜压力分布的微分方程。
它是从粘性流体动力学的基本方程出发,作了一些假设条件后得出的。
假设条件:流体为牛顿流体;流体膜中流体的流动是层流;忽略压力对流体粘度的影响;略去惯性力及重力的影响;认为流体不可压缩;流体膜中的压力沿膜厚方向不变。
图12-12中,两平板被润滑油隔开,设板A 沿x 轴方向以速度v 移动;另一板B 为静止。
再假定油在两平板间沿 z 轴方向没有流动(可视此运动副在z 轴方向的尺寸为无限大)。
现从层流运动的油膜中取一微单元体进行分析。
作用在此微单元体右面和左面的压力分别为p 及p p dx x ∂⎛⎞+⎜∂⎝⎠⎟,作用在单元体上、下两面的切应力分别为τ及dy y ττ⎛⎞∂+⎜⎟∂⎝⎠。
根据x 方向的平衡条件,得:整理后得根据牛顿流体摩擦定律,得,代入上式得 该式表示了压力沿x 轴方向的变化与速度沿y 轴方向的变化关系。
下面进一步介绍流体动力润滑理论的基本方程。
1.油层的速度分布将上式改写成(a)对y 积分后得(c)根据边界条件决定积分常数C1及C2:当y=0时,v= V;y=h(h为相应于所取单元体处的油膜厚度)时,v=0,则得:代入(c)式后,即得 (d)由上可见,v由两部分组成:式中前一项表示速度呈线性分布,这是直接由剪切流引起的;后一项表示速度呈抛物线分布,这是由油流沿x方向的变化所产生的压力流所引起的。
2、润滑油流量当无侧漏时,润滑油在单位时间内流经任意截面上单位宽度面积的流量为:将式(d)代入式(e)并积分后,得(f)设在 p=p max处的油膜厚度为h0(即时当润滑油连续流动时,各截面的流量相等,由此得 :整理后得该式为一维雷诺方程。
液体动压径向滑动轴承实验指导书

液体动压径向滑动轴承实验指导书一、实验内容与目的:1.观察径向滑动轴承的摩擦现象,加深对概念的理解; 2.测绘径向滑动轴承的摩擦特性曲线,掌握测绘方法;3.测绘径向滑动轴承油膜压力曲线,求油膜承载能力。
了解复杂问题的简化处理方法。
二、实验设备的结构与工作原理:本实验有二类(二种型号)设备,它们的结构示意图如图1和图2所示:它们包括以下向个部份:可以证明,抛物面与轴直径截面所围体积与以m P 值为高的长方体的体积之比32=KdB m 。
如果我们测量是精确的;那么我们计算结果摩擦状态指示装置的原理是用一个与轴和轴瓦相连的直流电路上的灯泡来指示的。
当轴当轴在很低的转速下转动时,轴将润滑油带入轴和轴瓦之间收敛性间隙内,但由于此时的油膜厚度很薄,轴与轴瓦之间部分微观不平的凸峰处仍在接触,当轴的转速达到一定值时,轴与轴瓦之间形成的压力油膜厚度完全分开两表面之间微观不平的凸峰,油膜守全将轴与轴瓦隔开,灯泡就不亮了。
这个指示装置还有一个作用就是当指示灯亮时不能加载,以免出现油温过高烧瓦等现三、实验方法与步骤:一)操作前检查:1.调速旋钮是否逆时针旋到底;2.将百分表调零;3.察看油标,检查润滑油油位是否到位;4.使加载系统处于未加载状态;二)实验操作(在做完以上准备工作后):1.观察润滑现象:接通电源,将调速旋钮右旋将使在一定转速(300转/分左右)下旋转,再回调至200转/分左右,然后再慢慢的调到转速为零。
注意观察各种摩擦状态。
2.摩擦系数测量:①接通电源,旋转调速旋钮使轴在一定转速(300转/分)下旋转。
②用加、减载荷方法记录在不同载荷情况下百分表读数;然后再在一固定载荷(HS-A型加到40kg;HZ型加三块砝码)下,用加、减转速方法记录百分表读数。
这样就得到摩擦系数各点值。
3.油膜承载压力测量:①调节调速旋钮,将轴转速达到各试验机的最高转速(500转/分以内);②加载使轴承受一定载荷(HS-A型100kg;HZ型六块砝码),待压力表值稳定后记录各块压力表的值。
液体动压轴承实验报告

液体动压轴承实验报告一、实验目的本次实验旨在探究液体动压轴承的工作原理和性能特点,通过实验验证其在工业生产中的应用价值。
二、实验原理液体动压轴承是一种利用液体动力学原理实现轴承支撑的装置。
其工作原理是通过液体的动力学特性,使轴承内部形成一定的压力,从而支撑轴承和轴承上的负载。
液体动压轴承具有摩擦小、寿命长、可靠性高等优点,广泛应用于机械制造、航空航天、船舶制造等领域。
三、实验设备本次实验所使用的液体动压轴承试验装置主要包括:液体动压轴承、电机、转速传感器、压力传感器、温度传感器、数据采集器等。
四、实验步骤1.将液体动压轴承安装在电机上,并连接转速传感器、压力传感器、温度传感器和数据采集器。
2.启动电机,调整转速至设定值,记录转速和轴承内部压力、温度等参数。
3.逐步增加负载,记录轴承内部压力、温度等参数。
4.在不同转速和负载下,记录轴承内部压力、温度等参数,并绘制相应的曲线图。
五、实验结果通过实验,我们得到了不同转速和负载下液体动压轴承的压力、温度等参数数据,并绘制了相应的曲线图。
实验结果表明,液体动压轴承具有较好的支撑性能和稳定性能,能够满足工业生产中的要求。
六、实验结论本次实验验证了液体动压轴承的工作原理和性能特点,证明了其在工业生产中的应用价值。
液体动压轴承具有摩擦小、寿命长、可靠性高等优点,是一种理想的轴承支撑装置。
七、实验感想通过本次实验,我们深入了解了液体动压轴承的工作原理和性能特点,对于工业生产中的轴承支撑问题有了更深入的认识。
同时,我们也认识到实验操作的重要性,只有严格按照实验步骤进行操作,才能得到准确的实验结果。
液体动力润滑径向滑动轴承设计计算
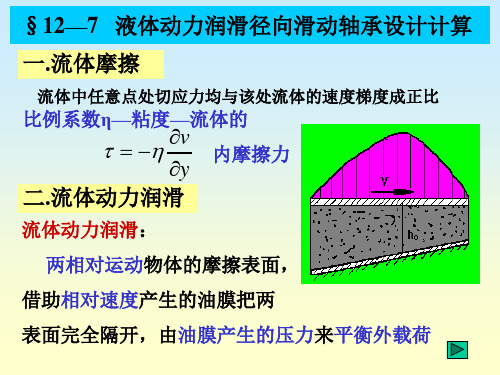
y2 x
h
2 x
直线
抛物线
2.润滑油流量
Q
h
udy
vh
h3
p
0
2 12 x
p pmax处油膜厚为h0,即h h0
p 0 Q vh0
x
2
各截面流量相等
vh0 vh h3 p
2 2 12 x
雷诺方程:
p x
6v
h3
h
h0
p
当h>h0时,x >0,p沿x方向
增大
当 h<h0时,px< 0,p沿x方向
减少
流体动力润滑的必要条件:
⑴ 流体必须有粘度,供应充分
⑵ 两表面必须有相对速度,油从大口进,小口出
⑶ 相对滑动两表面必须现成收敛的楔形油隙
四 径向滑动轴承形成流体动力润滑的过程
n=0
n≥0
n>>0
五 径向滑动轴承的几何关系和承载量系数
1 几何关系
⑴直径、半径间隙:△=D-d,δ=R-r= △/2
结果:
F
Bd 2
Cp
承载量系数Cp
Cp
3
B/2 B/2
2 1
1
cos cos0 B1 cos 3
d
cos a
d C1
2z B
2
dz
B—轴承宽度 d—轴承直径 ω—轴承角速度
η—油的粘度 C′—与B/d和 有关的系数
Cp
F 2 Bd
F 2 2vB
讨论:
Cp (, B / d) 表12—7
八 参数选择 1 宽径比 B/d=0.3~1.5
B/d↓ 运转稳定性↑,承载能力↓ 端泄↑,△t↓
高速重载取小值 低速重载取大值
液体动压轴承实验报告

液体动压轴承实验报告液体动压轴承实验报告引言:液体动压轴承是一种常见的轴承形式,其工作原理是通过液体的动压效应来支撑旋转轴的运动。
本次实验旨在通过实际操作和数据采集,验证液体动压轴承的工作原理和性能,并对其特点和应用进行分析。
实验方法:1. 实验装置搭建在实验室中,我们搭建了一个液体动压轴承实验装置。
该装置包括一个旋转轴、一个轴承座、一个液体供给系统和一个数据采集系统。
旋转轴通过轴承座固定,并通过电机驱动旋转。
液体供给系统将液体注入轴承座中,形成液体膜,支撑旋转轴的运动。
数据采集系统则用于记录实验过程中的相关参数。
2. 实验参数设定为了研究液体动压轴承的性能,我们设置了不同的实验参数。
首先是液体供给速度,即液体进入轴承座的速度。
我们分别设置了低速和高速两种情况,以模拟实际工作环境中的不同工况。
其次是液体压力,即液体在轴承座中的压力大小。
我们设置了不同的压力值,以观察液体压力对轴承性能的影响。
3. 数据采集与分析在实验过程中,我们使用数据采集系统记录了液体动压轴承的相关参数,包括轴承座压力、轴承座温度、旋转轴转速等。
通过对这些数据的分析,我们可以得出液体动压轴承的工作状态和性能指标,如轴承刚度、阻尼效应等。
实验结果:通过实验数据的采集与分析,我们得出了以下结论:1. 液体供给速度对液体动压轴承的性能有显著影响。
在低速情况下,液体膜较薄,轴承刚度较低,但阻尼效应较好;在高速情况下,液体膜较厚,轴承刚度较高,但阻尼效应较差。
因此,在实际应用中,需要根据具体工况选择合适的液体供给速度。
2. 液体压力对液体动压轴承的性能也有一定影响。
增加液体压力可以增加轴承刚度,提高轴承的负载能力。
然而,过高的液体压力也会增加能耗和摩擦损失。
因此,在设计轴承时需要权衡液体压力与能耗之间的关系。
3. 液体动压轴承具有较好的自润滑性能和减震效果。
由于液体的粘性和流动性,液体动压轴承可以在运动过程中形成液体膜,从而减小轴承和轴的接触面积,降低摩擦和磨损。
智能化液体动压轴承试验台设计开题报告

智能化液体动压轴承试验台设计1、课题研究的目的意义及国内外研究概况1.1研究背景及现状液体动压轴承是用来支撑轴及其他回转零件的一种重要部件,因其本身具有一些独特的优点:轴颈轴瓦间所特有的润滑油膜具有缓冲吸振作用,使用寿命长,结构紧凑,回转速度高等,这些优点使它在某些场合占有重要地位。
因此滑动轴承在金属切削机床、内燃机、铁路及车辆,雷达、卫星通信地面站及天文望远镜等方面的应用十分广泛[1]。
为了帮助大学学生更加深入、细致地了解和研究滑动轴承,各种滑动轴承试验台应运而生。
图1.1与1.2是现在广泛应用的实验台,但都存在实验的效率低、实验数据精度不高等缺点。
图1.1 机械式加载液体动压轴承试验台图1.2 机械式滑动摩擦试验机原理图1.2研究意义基于目前的液体动压轴承试验台普遍存在功能单一、测试数据精度低、实验数据稳定性差等问题。
近些年计算机技术的发展与应用,使教与学的形式与内容发生了变化,也改变了实验教学的模式,使实现教学改革成为可能。
将计算机辅助教学、计算机仿真等先进教学手段与技术应用于实践教学环节,科学地应用新技术,充分发挥高科技的特长,使实验室在现代化管理体制下高效运行,成为一个新课题[2]。
本课题研究的意义在于:用现代化的技术手段改造原有教学实验设备,提高试验台测试度、实验数据的可靠性及实验性能,满足教学要求。
同时也可以验证实际轴承的性能是否和设计的性能相符合;检验轴承的设计、制造和装配是否合理。
新型试验台开发完成后,可向全国高等工科院校相关专业实验室推广使用[3]。
2、课题研究的主要内容2.1基本内容由于目前广泛使用的实验台存在的诸多缺点,经过对比总结,提出了如下设计方案。
本课题重点完成实验台传动电机及调速方法选择、相应传感器的选择,其主要内容有:(1)了解液体动压轴承试验台设计研究目的,理解动压轴承的结构特点[4][5]。
确定出完整的试验系统总体方案。
(2)相关测试用传感器和电机的选定。
(3)进行油温测试,对油膜进行加热,测得油温与压力的关系。
- 1、下载文档前请自行甄别文档内容的完整性,平台不提供额外的编辑、内容补充、找答案等附加服务。
- 2、"仅部分预览"的文档,不可在线预览部分如存在完整性等问题,可反馈申请退款(可完整预览的文档不适用该条件!)。
- 3、如文档侵犯您的权益,请联系客服反馈,我们会尽快为您处理(人工客服工作时间:9:00-18:30)。
毕业设计开题报告机械设计制造及自动化油液动压径向轴承设计及计算1、选题的背景、意义流体动压径向滑动轴承具有承载能力大、功耗小、耐冲击、抗振性好、运转精度高等突出的优点。
所以,在高速、低速以及高速精密的旋转机械中应用十分普遍,而且成为旋转机械的重要部件。
比如在汽轮机组、舰船主动力机组、石油钻井机械、轧机及各类大型机床中都有广泛的应用,而且成为这类机械的关键部件之一。
在这些机器中,径向滑动轴承的性能优劣直接影响或决定了整台机器的性能和效率。
比如在汽轮发电机组中,性能优良的滑动轴承可以减少停机检修的次数,烧瓦的可能性也低得多。
轴承基本参数(轴径的长径比、半径间隙、偏心距和轴承包角等)的变化,对轴承的静动态特性会产生很大的影响。
另外,实际工作中的滑动轴承,由于加工、安装误差等因数,其工况条件与理论分析时所考虑的理想工况有很大差距,这种情况下,轴承的一些性能参数会发生变化。
2、相关研究的最新成果及动态我国轴承行业发展到现在,已具备相当的生产规模和较高的技术、质量水平。
具有一定规模的轴承企业已发展到1 500余家,职工人数壮大到近80万人,轴承年产量从1 949年的1 3.8J5套增加到目前的20多亿套,轴承品种累计从1 00多个增加至7000多个,规格达28000多个。
近1 0年来国外轴承知名公司(如SKF、FAG、NSK、NBM 、 KOYO、T JM KEN、TORRlNGTON等)先后在我国投资办厂,对我国轴承设计技术水平的提高,生产工艺和生产管理的规范、生产装备水平的现代化、产品的质量和使用性能的提高等方面起到了很大的推动作用。
2OO亿元,年出口量逾7.7亿套,出口创汇约达7亿美元,世界排名第4,满足国内所需产品品种的70%以上,满足所需数量90%以上,出口量也以较高的比例递增。
在我国跨入世界轴承生产大国行列的同时,轴承工业依然存在低、散、差的问题普通微型、小型、中小型深但另一方面,我国轴承生产企业也面临来自国外知名轴承公司的激烈竞争和挑战,其结果必将加速我国轴承工业的产业结构和严品结构的调整步伐,真可谓机遇与挑战并存、生产与发展同在。
如何抓住机遇,提高企业的生存能力,在生存的同时如何求得持续、快速的发展是摆在我国轴承行业面前不可回避、也无法回避的问题。
目前,我国轴承产量达2O亿套以上,产值已超过沟球轴承仍在大量低水平重复生产,导致严重供过于求,由于市场竞争激烈,价格大战愈演愈烈。
如果这种情况长期地持续下去,势必要影响到整个轴承行业技术改造和技术进步,影响我国的轴承产品在国际上的声誉,严重制约我国轴承工业的健康发展。
质量要求严、技术附加值高的轴承仍需要大量的进口。
例如轿车轴承、高速、准高速铁路轴承,各种进口设备维修用轴承,部分高精度、高附加值和在特殊工况条件下使用的专用轴承供应缺口较大,我国生产的轴承产品在性能与价格比、高精度、低噪音、长寿命与高可靠性等方面与国外知名企业存在着较大的差距。
在石油钻井中,滑动轴承牙轮钻头的应用日益增多,但轴承的工作环境却相当恶劣。
为了提高钻头滑动轴承的工作寿命,并为这类轴承的设计提供科学依据,针对其实际应用工况,1995年清华大学的邵天敏呻设计制造了一种IPG.2型滑动轴承实验台。
该实验台可以进行滑动轴承摩擦扭矩、摩擦系数、磨损和轴承温升的测量,也可以进行其他类型的低速、重载径向滑动轴承的实验。
利用该实验台在30kN、40kN和50kN的3种载荷条件下,对牙轮钻头镶嵌铜合金的滑动轴承进行了台架试验研究,着重考察了铜合金镶嵌区尺寸之大小对轴承摩擦磨损性能的影响。
1995年上海大学孙美丽针对全轴承的定常和非定常工作情况,设计制造了一台对中旋转、不对中旋转及混合型旋转的轴承实验台,并在此实验台上进行了这三种旋转类型的轴承内油膜分布实验研究。
该实验台具有可以调节静偏心量和动偏心量及轴颈在轴承中位置的机构,因此可以观察到不同静、动载荷搭配情况下轴承油膜破裂的情况。
该实验台电机最大转速2000rpm ,研究中使用直径φ59.00mm 和φ59.10mm 两种轴颈。
西安交通大学阳1于1995年设计制造了液压加载流体动压滑动轴承用于径向滑动轴承的静特性研究。
该实验台主轴转速可在100rpm 至3000rpm 无级调整, 实验轴承内径50mm 。
该实验台专门设计了平移机构来实现传感器对整个轴承宽 度的压力测量。
实验选用宽径比O .6、1、1.2三种规格来测量宽径比对油膜压力分布的影响。
液压加载力可在100N 至2000N 间调整,从而达到变载荷下的测量。
选取相对间隙ψ分别为O .0016、0.0022和0.0032的三种轴瓦来研究相对间隙对压力分布的影响。
1997年西安交通大学的姜歌东和徐华阳1在200mm 实验台上对300MW 汽轮 机组中的两种支承轴承(上瓦开槽圆轴承和上瓦开槽椭圆轴承)按比例缩小模型 进行了实验研究,测试了不同工况下这两种轴承的动、静特性。
通过与理论计算 值的比较,进一步证实了实验结果和理论计算的一致性,为研究不同结构径向滑 动轴承对汽轮机组稳定性的影响提供了基础。
2000年上海大学设计制作了一套较为完善的多因素固液界面滑移特性实验装置,可用于进行不同场压力、不同转速、间隙等条件下的滑移特性试验。
应用这套试验装置对金属材料及EMP 材料的边界滑移特性进行了多组对比试验。
该装置使用杠杆加载机构对轴承加径向载荷,因此加载范围仅为O .5~10KN 。
载荷最小变化量T ∆=0.5KN 。
调速系统使用变频器加变频电机的方案,但频率变化最小值为m in f ∆=o .1Hz ,电机转速最小改变值为min n ∆=3rpm ,本质上仍属于有级调速。
哈尔滨工业大学为了实现滑动轴承动压油膜承载力曲线和摩擦特性曲线的测量和描绘,于2002年设计了新型滑动轴承实验台。
通过计算机软件编程控制轴承加载力的大小,加载力在0~1000N 内可调,可调最小量10N ;计算机控制直流电机的调速,转速0~1500rpm 内可调。
采用Visual Basic 语言,在VisualC++中编制数据采集、电机控制动态连接库程序,在VB中用该程序以实现滑动轴承实验台的计算机数据采集和控制。
该实验台的创新之处在于使用步进电机和杠杆组合机构实现了连续可调加载,但仍存在所加载荷不大的缺点。
为了开发大型贯流式水轮发电机组径向轴承,2003年东方电机股份有限公司在实验台上采用φ360的模型轴承对φ1740可倾6瓦块原型轴承进行了模拟实验,最高比压为3.37MPa,最高线速度为22.62m /s。
实验台由850KW直流电机驱动,波纹管加载,可进行0--3000rpm、载荷2~1 5t的轴承实验。
在三种安装间隙下,进行了变转速、变比压、变进油温度及变进油压力实验,测得了该轴承在各种工况下稳态时油膜厚度、瓦温度、损耗、流量等,得到了该型轴承最佳性能范围。
太原科技大学于2004年研制出大型轧机油膜轴承实验台,通过使用1:8的变速器,主轴最大转速达8000rpm至10000rpm,液压缸加载,最大加载能力90t。
其加载液压缸设计成可移动的形式,因此实验轴承既可安装在中间,也可安装成悬臂形式。
该实验台可以进行油膜轴承、滚动轴承、油膜滚动复合轴承等多种轴承的实验研究。
具有超高压顶起装置,实验轴承启动时,可使用超高压油(100MPa)项起轴承,可以进行动.静压油膜轴承的研究。
2005年哈尔滨第七O三研究所设计了大型径向和推力滑动轴承实验台。
该实验台采用了径向试验轴承和推力试验轴承组合形式,为卧式结构。
在实验时只需更换试验组建和实验的主轴,就可以进行不同项目的实验。
即当实验推力轴承时,使用推力实验轴承组建与带推力盘的试验主轴;当实验径向轴承时,改用径向实验轴承组件和径向试验主轴。
两种实验共用一个驱动电机、增速齿轮箱、联轴器和润滑供油系统。
实验台主要由本体部分、液压转动与供油系统、数据检测与处理系统、电力拖动与电气空载系统等部分组成。
实验台采用静压加载,油泵额定压力为6.3MPa,额定流量为0.8L/rain,活塞直径为φ1 80mm,径向实验轴承为倒置式,实验轴承最大直径为200mm,最大宽度为200mm。
实验轴承低压供油,供油压力最高O.6MPa,最大流量为860L/min。
澳洲电力基金会出资在澳大利亚WOLLONGONG大学机械工程系建立了一个汽轮机滑动轴承实验台。
实验台可装两大型动压轴承和一个静压轴承,与国际上现流行的单轴承实验台相比,俩支承的实验台更接近于轴承的实际工作状态。
3、课题的研究内容及拟采取的研究方法(技术路线)、研究难点及预期达到的目标研究方法:采用数值方法分析液体动压径向性能,掌握液体动压径向轴承性能的数值分析方法。
根据液体润滑Reynolds方程,采用差分方法,利用Matlab语言编程,计算轴承承载力,分析轴承性能。
研究难点:学习数值分析法,学习差分法,采用差分法求解液体润滑Reynolds方程。
参考资料自学Matlab编程技术。
参考大量文献,总结前人的经验,以求最好地完成本次毕业设计。
预期达到的目标:用雷诺方程求解出所有需要的数值。
4、研究工作详细工作进度和安排2011年1月10日-2011年3月1日,完成文献综述、外文翻译(2篇)、完成开题报告。
2011年3月1日-2011年4月10日,采用差分法求解液体润滑Reynolds方程。
2011年4月10日-2011年4月30日,计算轴承承载力,分析轴承性能。
2011年4月30日-2011年5月25日,完成毕业设计说明书,准备毕业答辩。
5、参考文献1.(英)威尔逊著,尚礼等译:滑动轴承设计手册,上海科学技术文献出版社,1989年2.张直明:滑动轴承的流体动力润滑理论,高等教育出版社,19.24,19863.J.W.White,ASME Journal ofLubrication Technology,1983,105:484-490.4.M.M.Farid:Effect of Tubing on Measurements of Small TransientPressure Signals in Liquids Journal of Dynamic Systems Measurement and Control,ASME V01.1 05,NO.4,56—62,19845.董跃, 张晓阳, 赵雄, 杜伟, 董异志. 液压轴承刚度与关键参数的优化分析[J]. 机电产品开发与创新 , 2006,(05) 212-2196.周军波丁毓峰基于轴系稳定性分析的滑动轴承优化设计机械制造-2010年8期 45-497.B.A.沃斯克列辛斯基:滑动轴承计算和设计,国防工业出版社,88-99,19868.邱宣怀等——《机械设计》北京高等教育出版社9.李庆杨等——《数值分析》武汉华中工学院出版社10.张幼卿;《磨擦学》简介[J];中国机械工程;1983年05期 156-16011.岳红,王文博;《液体动压润滑向心滑动轴承的程序设计》[J];北京服装学院学报(自然科学版);1987年01期 98-12712.温诗铸,黄平. 《摩擦学原理》[M].北京:清华大学出版社,200213.陈伟,许轶超,王少梅;《精密齿轮传动系统的计算机辅助设计与实现》[J];航空计算技术;2003年01期 126-129。