TPS 精益生产用语及解释
TPS精益生产从入门到精通

TPS精益生产从入门到精通TPS(Toyota Production System)是一种由丰田汽车公司所发展的生产管理体系,也被称为精益生产。
它的核心理念是通过最大限度地减少浪费来提高效率和质量。
TPS的原则之一是追求连续流动。
这意味着在制造产品时要避免生产过程中的停滞和等待。
通过优化流程和减少库存,可以实现连续流动,从而减少了不必要的等待时间和物料浪费。
另一个重要的原则是及时制造。
这意味着只在顾客需求到来时才进行生产,尽量避免过度生产和库存积压。
这可以通过提高供应链的灵活性和可视化生产过程来实现。
TPS还强调标准化工作方法和持续改进。
通过制定和遵守标准工作程序,可以提高工作效率和一致性。
同时,TPS鼓励员工参与到持续改进的过程中,通过找出问题并提出解决方案来不断优化生产流程。
为了实现这些原则,TPS使用了多种工具和技术。
以下是一些常见的工具和技术:1. 价值流图:用于识别整个生产过程中的价值流和非价值流,并帮助找出改进的机会。
2. Kaizen活动:通过小规模的改进项目来不断优化生产过程。
这些改进可以是改善工作环境、减少浪费、提高质量等。
3. Jidoka:该概念旨在将质量问题早期发现,并在生产过程中停下来解决问题,确保不良品不会进入下一个环节。
4. 5S整理法:通过整理、整顿、清扫、清洁和纪律来改进工作环境和工作效率。
精通TPS需要时间和实践。
开始学习TPS的第一步是了解其核心原则和基本概念。
接下来,可以尝试应用一些常见的工具和技术来改善生产过程。
通过不断地实践和反思,可以进一步深化对TPS的理解和应用。
总结起来,TPS(精益生产)是一种通过减少浪费、追求连续流动、及时制造和持续改进来提高效率和质量的生产管理体系。
通过学习和应用TPS的原则和工具,可以逐步提升对TPS的理解和应用能力。
实践了很多年,丰田生产系统(Toyota Production System, TPS)已经成为许多企业追求精益生产的范本。
精益生产TPS的基本内容.doc

精益生产TPS的基本内容1精益生产TPS的基本内容精益生产好比一幢大厦,该大厦的地基是IQM的组织体系,对从市场调查、设计开发、采购、工艺策划、生产制造、检验和试验、包装和贮存、销售和发运、安装调试、技术服务和维护,以及用后废弃物的后处置全过程的管理,则是精益生产模式的屋顶,支撑这幢大厦屋顶的三根支柱就是所施行的以协作方式工作的“并行工程,’(CE)、成组技术(GT)和准时生产制(JIT)。
1.并行工程并行工程(Concurrent Engineering CE)是集成地和并行地设计产品及相关各种过程的系统化工作模式,它要求产品设计人员在设计一开始就考虑产品生命周期中从概念形成到产品报废处理的所有因素,包括质量、成本、进度计划和客户要求等。
即要充分地考虑加工、装配、质量检验、检验、维护与成本在内的所有因素。
传统的新产品开发是按串行顺序进行的,即在产品图纸设计完成后,必须进行样机试制。
根据试制样机过程中发现的问题,再对图纸进行修改;与此同时还需调整试制工艺规程和设计、制造必要的工装模具和专用设备;然后进一步投人小批生产,考核工艺规程和工装设备的正确性,必要时得进行适当的修改和改进,只有在小批量试制通过验证后,才能正式进行批量生产。
因而存在着开发周期长和后期发现的问题往往无法得到解决的难题。
特别是对于面向订单的单件、小批量生产企业,这种串行式设计,反馈信息始终滞后于过程的传递,返工的浪费会造成很大的损失。
而并行工程则不然,反馈信息能在过程传递之前送到前工序的各个环节,使之能及时修改,以避免不必要的浪费。
并行工程具有“并行性”、“整体性”、“协同性”和“集成性”等诸多特点。
在时序方面,将时间上先后的作业实施过程转化为同时考虑和尽可能同步处理的作业方式结合在一起进行,从而缩短了开发周期,降低了成本。
采用并行工程,其设计周期一般可以缩短20%~40%。
并行工程的工作流程。
以协作的团队工作方式开展的并行工程设计,由于团队人员具有相当高的责任感,在设计过程中,只有各方人员协商一致的情况下才会正式绘制工程图纸,所有的问题都会解决得比较彻底,从而为提高设计质量和缩短产品开发周期创造了有利的条件。
TPS理念名词解释
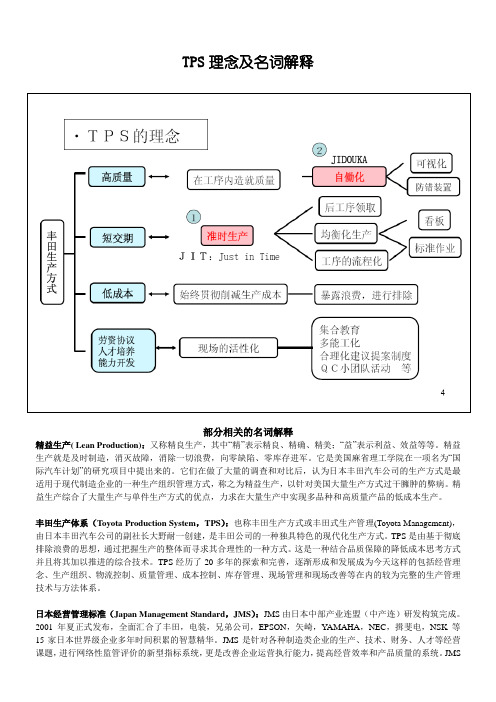
TPS理念及名词解释讲座二:TPS推进与企业管理革新及企业文化的确立企业问题解決思路梳理经营与管理的价值观時間管理TPS在经营和管理上的构造丰田方式体系(成本・量・质量・人及各种手段方法之间的关系)自働化的目的与手段「標準作業」JMS的目的生产现场的日常管理行动内容管理者监督者(主要指工段长,组长)的定位(位置)意识变革与行动部分相关的名词解释精益生产( Lean Production):又称精良生产,其中“精”表示精良、精确、精美;“益”表示利益、效益等等。
精益生产就是及时制造,消灭故障,消除一切浪费,向零缺陷、零库存进军。
它是美国麻省理工学院在一项名为“国际汽车计划”的研究项目中提出来的。
它们在做了大量的调查和对比后,认为日本丰田汽车公司的生产方式是最适用于现代制造企业的一种生产组织管理方式,称之为精益生产,以针对美国大量生产方式过干臃肿的弊病。
精益生产综合了大量生产与单件生产方式的优点,力求在大量生产中实现多品种和高质量产品的低成本生产。
丰田生产体系(Toyota Production System,TPS):也称丰田生产方式或丰田式生产管理(Toyota Management),由日本丰田汽车公司的副社长大野耐一创建,是丰田公司的一种独具特色的现代化生产方式。
TPS是由基于彻底排除浪费的思想,通过把握生产的整体而寻求其合理性的一种方式。
这是一种结合品质保障的降低成本思考方式并且将其加以推进的综合技术。
TPS经历了20多年的探索和完善,逐渐形成和发展成为今天这样的包括经营理念、生产组织、物流控制、质量管理、成本控制、库存管理、现场管理和现场改善等在内的较为完整的生产管理技术与方法体系。
日本经营管理标准(Japan Management Standard,JMS):JMS由日本中部产业连盟(中产连)研发构筑完成。
2001年夏正式发布,全面汇合了丰田,电装,兄弟公司,EPSON,矢崎,Y AMAHA,NEC,揖斐电,NSK等15家日本世界级企业多年时间积累的智慧精华。
tps用语
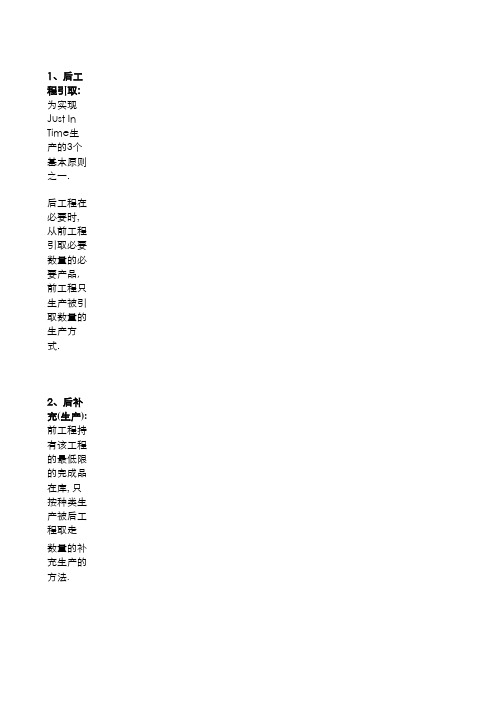
1、后工程引取: 为实现Just In Time生产的3个基本原则之一.后工程在必要时,从前工程引取必要数量的必要产品,前工程只生产被引取数量的生产方式.2、后补充(生产): 前工程持有该工程的最低限的完成品在库, 只按种类生产被后工程取走数量的补充生产的方法.3、安东: 是督促相关人员采取行动的情报窗,一眼就可以判断现时点的异常场所的电光表示盘.除异常表示外,也有表示进度的作业指示(品质检查、刀具更换、部品搬运等)安东.4、一个流动(生产): 按照工程顺序,一个(或一台)一个加工、组装,一个一个向下一道工序流动的方式.5、内段取: 在生产准备作业阶段,不停止生产线、机械设备的运转,就不能更换模具、刀具以及治具等作业.6、AB控制:为了使工程之间或工程内的标准手持量总是保持一定量,将2个位置(A点、B点)的制品的有无,作为各搬送机可以移动的条件及可以从工序搬出制品的条件的控制结构.①搬送机可以移动的条件……A点有制品,B点无制品;②可以从工序中搬出标准手持的条件……A点有制品,B点无制品;7、改善: 找出人(劳动力)、物(材料使用量及材料、制品的在库)、设备或者是生产结构等相关的浪费(到处都有),运用智慧尽量不产生费用,迅速地将浪费一个一个排除的一系列活动.对于人工作业的改善,作业改善必须要优先于设备的改善. 并且,改善不是特定人员的业务,是全体作业人员从各自不同的立场,能够作到的、并且是应该执行的工作.8、可动率:需要运转设备时(看板来时),设备正常运转状态的概率.相当于对设备及其保全状态的信赖性.理想状态是100%.9、稼動率:为了完成后工程所需要的生产量,按照该设备能力,针对满负荷运转时的定时能力所需要的比例. 根据销路决定稼动率.10、看板: 为实现Just In Time生产的管理道具.看板的作用:①生产、搬运的指示情报②目视化管理的道具Ⅰ.抑制生产过剩;Ⅱ检知工程的进展;③工程、作业改善的道具看板按功能进行分类:行动开始看板引取看板11、行动开始看板: 在生产工序,指示生产开始着手而使用的看板 ,分为工程内看板及信号看板.12、工程内看板: 工程内指示生产开始使用的看板.按照被后工程取走的顺序,只对被后工程引取的量进行补充生产的开始行动的看板.13、信号看板: 一条生产线加工多种制品,需要占用若干段取时间的批量生产工序所使用的行动看板.由于它的形状是三角形的,因此统称为三角看板.主要应用于冲压、铸造高压、树脂成型等工序.14、引取看板: 是对后工程向前工程引取部品的时机及引取量进行指示的看板.有工程间引取看板、外注部品纳入看板两种.15、工程间引取看板(搬运看板): 在公司内部,后工程从前工程引取必要部品而使用的看板.16、外注部品纳入看板(外注看板):从订货方纳入部品时使用的看板.采购由订货方执行,工序只是通过外注看板将偏差的部分纳入,因此基本上与工程间引取看板相同,可以后工程引取.17、临时看板:由于型保全,机械设备的修理,并且由于稼动日等的不同,需要比通常的生产量多的部品的生产及搬运的指示看板.明确记载有限期限,只使用1次使用后回收.使用红色的斜线,与其他识别.18、看板循环:取决于部品的纳入频度(几日几次)及从取回看板的车次开始,有几次从晚来的车次纳入的循环称为看板循环.19、QC工程表:为实现将品质目标造入工程的目的,将融合各工程特性的管理项目,以设定的规格、基准为基础,决定由谁、用什么样的方法检查,点检,管理的方法.20、工程的流动化:是实现Just In Time生产的基本原则之一.消除工程内与工程间的物的停滞,实行一个流动生产.21、工程别能力表:各工程加工部品时,为体现各工程的生产能力,通过记入手作业时间,设备的自动运转时间及刀具更换时间等,计算出工程能力的图表.22、5个为什么:所谓5W1H(WHY,WHAT,WHERE,WHEN,WHO,HOW)是作为工程分析的现状调查的视点而使用,并且除此之外WHY不止1〃2次,而是为什么,为什么……通过问5次为什么来追求真因.23、多回搬运:是增加部品单位的搬运频度的搬运方法,目的是减少前后工程的在库量.但它是单纯增加车辆的运行次数,而不降低装载效率,多回搬运是进行混载搬运,车辆的运行总数不增加.24、混载搬运:用1辆车,装载多种部品的搬运方法.混载搬运不会降低搬运效率(搬运车辆的总体运行次数不会增加),可以多回搬运并且降低前后工程的在库量.另外对应生产的变动,运行次数的增减变动很容易.25、循环时间:作业者1人,在其所持有的工程,按照规定的作业顺序,完成一轮作业所需要的时间.26、标准作业:以人的动作为中心,按照没有浪费的顺序,高效生产的作法,丰田生产方式称为标准作业,生产节拍〃作业顺序〃标准手持构成它的3要素.27、作业顺序:标准作业的3要素之一,作业者能够最有效率地生产良品的作业顺序.28、生产节拍:一个部品或者是1台,在多长时间内应该生产出来的时间值。
什么是精益生产管理TPS
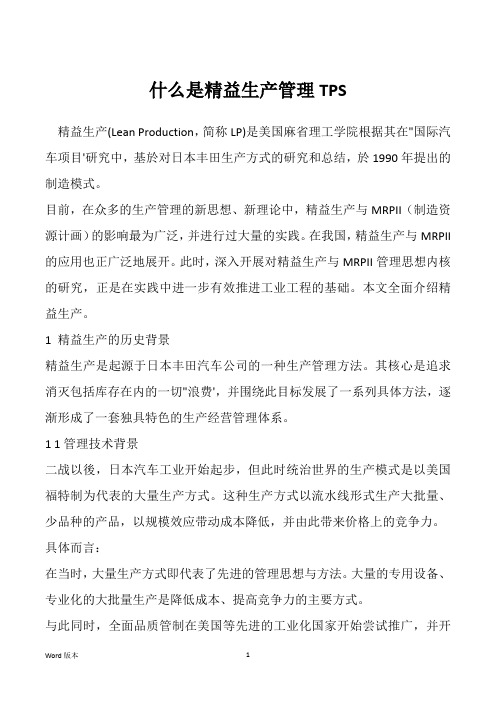
什么是精益生产管理TPS精益生产(Lean Production,简称LP)是美国麻省理工学院根据其在"国际汽车项目'研究中,基於对日本丰田生产方式的研究和总结,於1990年提出的制造模式。
目前,在众多的生产管理的新思想、新理论中,精益生产与MRPII(制造资源计画)的影响最为广泛,并进行过大量的实践。
在我国,精益生产与MRPII 的应用也正广泛地展开。
此时,深入开展对精益生产与MRPII管理思想内核的研究,正是在实践中进一步有效推进工业工程的基础。
本文全面介绍精益生产。
1 精益生产的历史背景精益生产是起源于日本丰田汽车公司的一种生产管理方法。
其核心是追求消灭包括库存在内的一切"浪费',并围绕此目标发展了一系列具体方法,逐渐形成了一套独具特色的生产经营管理体系。
1 1管理技术背景二战以後,日本汽车工业开始起步,但此时统治世界的生产模式是以美国福特制为代表的大量生产方式。
这种生产方式以流水线形式生产大批量、少品种的产品,以规模效应带动成本降低,并由此带来价格上的竞争力。
具体而言:在当时,大量生产方式即代表了先进的管理思想与方法。
大量的专用设备、专业化的大批量生产是降低成本、提高竞争力的主要方式。
与此同时,全面品质管制在美国等先进的工业化国家开始尝试推广,并开始在实践中体现了一定的效益。
生产中库存控制的思想(以MRPII思想为主)也开始提出,但因技术原因未能走向实用化。
1 2丰田式生产方式发展的环境当美国汽车工业处於发展的顶点时,日本的汽车制造商们是无法与其在同一生产模式下进行竞争的。
丰田汽车公司从成立到1950年的十几年间,总产量甚至不及福特公司一天的产量。
与此同时,日本企业还面临需求不足与技术落後等严重困难,加上战後日本国内的资金严重不足,也难有大规模的资金投入以保证日本国内的汽车生产达到有竞争力的规模。
此外,丰田汽车公司在叁观美国的几大汽车厂之後还发现,在美国企业管理中,特别是人事管理中,存在着难以被日本企业接受之处。
TPS常用概念
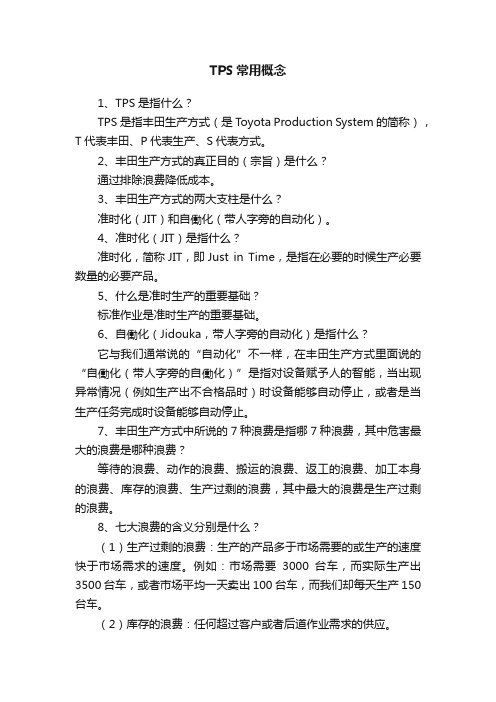
TPS常用概念1、TPS是指什么?TPS是指丰田生产方式(是Toyota Production System 的简称),T代表丰田、P代表生产、S代表方式。
2、丰田生产方式的真正目的(宗旨)是什么?通过排除浪费降低成本。
3、丰田生产方式的两大支柱是什么?准时化(JIT)和自働化(带人字旁的自动化)。
4、准时化(JIT)是指什么?准时化,简称JIT,即Just in Time,是指在必要的时候生产必要数量的必要产品。
5、什么是准时生产的重要基础?标准作业是准时生产的重要基础。
6、自働化(Jidouka,带人字旁的自动化)是指什么?它与我们通常说的“自动化”不一样,在丰田生产方式里面说的“自働化(带人字旁的自働化)”是指对设备赋予人的智能,当出现异常情况(例如生产出不合格品时)时设备能够自动停止,或者是当生产任务完成时设备能够自动停止。
7、丰田生产方式中所说的7种浪费是指哪7种浪费,其中危害最大的浪费是哪种浪费?等待的浪费、动作的浪费、搬运的浪费、返工的浪费、加工本身的浪费、库存的浪费、生产过剩的浪费,其中最大的浪费是生产过剩的浪费。
8、七大浪费的含义分别是什么?(1)生产过剩的浪费:生产的产品多于市场需要的或生产的速度快于市场需求的速度。
例如:市场需要3000台车,而实际生产出3500台车,或者市场平均一天卖出100台车,而我们却每天生产150台车。
(2)库存的浪费:任何超过客户或者后道作业需求的供应。
(3)作业等待的浪费:人员以及设备等资源的空闲。
例如:生产线因缺件或设备损坏,导致生产线停线,人员在等待开线;或者由于上下工序作业时间不一样,下工序完成一个产品了而上工序还没完成造成下工序在等待。
(4)搬运的浪费:对物料的任何移动。
(5)动作的浪费:对产品不产生价值的任何人员和设备的动作。
(6)加工本身的浪费:亦称为“过分加工的浪费”,一是指多余的加工;另一方面是指超过顾客要求以上的精密加工,造成资源的浪费。
精益生产术语解释
精益生产术语解释1.及时生产(JIT)只在客户需要的时间,生产客户需要的产品和数量,同时,使用最少的原材料、设备、人力和空间。
通过即时生产,实现多品种、小批量的生产,消除生产现场中的无效劳动与浪费,最大限度地获取利润和效益。
2.单件流(One pieceflow)是指从毛坯投入到成品产出的整个制造加工过程,零件始终处于不停滞、不堆积、不超越,每个工序按节拍一个一个的流动的生产方法。
该方式可以消除库存的浪费并且及时发现异常。
3.拉动生产/推动生产以客户需求为拉动,按照设定的生产节拍,从后工位向前工位拉动生产,这是准时化生产的原理之一。
而推动是不顾客户需求只顾自己生产的生产线,该生产线必定会出现大量的库存和浪费。
4.节拍(Takt Time)是指相继完成两件在制品或产品之间的时间间隔,通常以“秒”为单位。
节拍的设立与遵从可以消除过量生产、库存及等待的浪费。
5.5S5S是精益生产的重要基础。
没有良好的5S,精益生产无从谈起。
6.标准作业指导书(SOS)所有的作业必须有标准,所有标准的作业必须有相关的规范描述。
标准作业指导书(SOS)详细地描述了每一个工序的作业规范和要求。
7.物料传递员(W/S)又称水蜘蛛 (Water spider) 简写为 (WS), 是精益生产线上专门从事物料、工具、生产看板及其他工装夹具的准备和传递的人员。
物流传递员所从事的工作通常是不增加产品价值的浪费,精益生产通过安排专门的物流传递员是为了有效剔除其他作业人员的不增加价值的作业(即浪费),提高作业员的生产效率,从而保证及达到精益生产线整体最优的目的8.7大浪费(7wastes)精益生产的核心是不断地识别和剔除制造过程中的各种浪费活动,精益生产定义了七种消耗了资源但是又不产生价值活动,这七种浪费包括:∙不良品的浪费∙生产过剩的浪费∙库存的浪费∙多余动作的浪费∙运输的浪费∙等待的浪费∙加工及流程的浪费9.自働化(Jidoka)将人的智能转化成自働机械,使机器能够自己识别和判断生产过程出现的缺陷和异常,并且在请求帮助时自动停机。
丰田精益生产词汇及理念汇编(邱)
精益词汇汇编-基础篇精益词汇——ONE:是Optimization Never Ending 的第一个英文字母缩写,意思是:改善永无止境。
它是通过学习丰田生产方式,结合中集实情,具有中集特色的精益生产管理模式。
精益词汇——TPS:是Toyota Production System 的头一个字母,意思是:丰田生产方式。
精益词汇——JIT:是Just In Time的第一个英文字母缩写,意思是:准时化生产,即在必要的时间里生产出必要数量的必要产品,丰田生产方式的两大支柱之一。
精益词汇-—自働化:丰田生产方式的两大支柱之一,强调人员自主化,即人员与机械设备的有机配合行为。
精益词汇——PDCA循环:是英语单词Plan(计划)、Do(执行)、Check(检查)和Action(行动)的第一个字母,又叫戴明环,是能使任何一项活动有效进行的一种合乎逻辑的工作程序。
精益词汇——3S整理(Seiri)、整顿(Seiton)、清扫(Seiso)。
“3S”活动的对象是现场的“环境",它对生产现场环境全局进行综合考虑,围绕现场物品的“使用价值”展开,并制订切实可行的计划与措施,从而达到规范化管理。
整理:区分“要”和“不要",不要的移出去,节约空间.整顿:对“要"的东西进行定置,节约寻找时间。
清扫:清除脏污,美化环境,确保物品随时可用.精益词汇——OJD:On The Job Development 的第一个英文字母缩写,意思为在工作中成长、发展。
是丰田人才育成的方法,强调“通过工作”培养员工,以及“通过实践"进行学习。
精益词汇—-QCQUALITY CONTROL的第一个英文字母缩写,中文意义是品质控制,是为达到品质要求所采取的作业技术和活动;QC的七大工具:检查表、层别法、柏拉图、因果图、散布图、直方图、管制图. 精益词汇—-标准化作业:标准化作业就是在作业系统调查分析的基础上,将现行作业方法的每一操作程序和每一动作进行分解,以科学技术、规章制度和实践经验为依据,以安全、质量效益为目标,对作业过程进行改善,从而形成一种优化作业程序,逐步达到安全、准确、高效、省力的作业效果。
精益生产专业名词解释
精益生产专业名词解释TPS(Toyota Production System)------丰田生产系统IE (Industrial Engineering)工业工程WIP(WORK IN PROCESS)------在制品库存7S(Seiri、Seiton、Seiso、Standardize、Sustain、Satety、Save) ------整理、整顿、清扫、清洁、素养、安全、微笑SOP(Standard Operation Procedure)-------标准作业指导书T/T(Takt Time)-------(节拍时间)作业人员一天或一月的有效工作时数除以市场一天或一月的确定订单数C/T -------(周期时间)在制品加工时间,不含休息时间;L/T-------(前置时间)在制品加工总时间,含休息时间及其它所有等待浪费时间MCT------设备自动加工时间(自设备启动开始,到设备完全停止为止)SOP-------作业标准(含时间量度)KPI(Key Performance Indication)------重要绩效指JIT (Just In Time) -----即时化管理PDCA(Plan、Do、Check、Action )------计划、行动、检查、实施Bottleneck------瓶颈Line Balance ------生产线平衡TPM(Total Production Management)------全面生产管理TQM(Total Quality Management)------全面品质管理QE (quality engineering)------ 品质工程人员QIT(Quality Improvement Team)------ 品质改善小组CAM(Computer-aided-manufacturing)------计算机辅助制造CAD(Computer-aided-design)------计算机辅助设计CAE(Computer-aided-engineering)------计算机辅助工程CAPP(Computer-aided-process planning)------计算机辅助工艺编制QCC(Quality Control Circle)------品管圈QE(Quality Engineering) ------品质工程。
丰田生产方式(tps)用语整理及解说
文章主题:丰田生产方式(TPS)用语整理及解说在整理和解释丰田生产方式(TPS)的用语之前,我们首先需要了解什么是丰田生产方式。
丰田生产方式是一种由日本汽车制造商丰田公司创建的生产方式,旨在通过最大化价值、减少浪费和持续改进来提高生产效率和产品质量。
该方式是基于提供最大的价值,包括产品质量、交付时间和成本效益。
下面我们来整理和解释一些与丰田生产方式相关的关键用语:1. Just-in-Time(即时生产):即时生产是丰田生产方式中的一个关键概念,它要求在制造过程中尽可能减少库存,并在需要时按需生产。
这有助于减少浪费,提高生产效率,因为产品不需要存储很长时间,也能更快地交付给客户。
2. Kaizen(改善):Kaizen是丰田生产方式中的另一个重要概念,意味着持续改善。
这意味着每个员工都应该不断寻求改进的机会,包括生产流程、工作环境和产品质量。
通过持续改善,公司能够逐步提高生产效率和产品质量。
3. Jidoka(自动停机):Jidoka是丰田生产方式中的一项质量控制技术,它能够自动停止生产线,以防止次品产品进入下一个生产阶段。
这有助于提高产品质量,减少退货和重新制造成本。
4. Poka-Yoke(防错):Poka-Yoke是一种设计技术,旨在通过减少人为错误来提高生产效率和产品质量。
这包括使用特殊的工具、模具和设备,以确保员工在生产过程中不会出现错误。
5. Andon(安灯):Andon是一种用于指示生产线状态和问题的信号系统。
它可以帮助员工及时发现生产中的问题,并立即采取措施来解决。
以上是一些与丰田生产方式相关的关键用语,这些概念对于了解和实施丰田生产方式都至关重要。
通过对这些用语的整理和解释,我们可以更好地理解丰田生产方式的核心原理和重要概念。
总结回顾:通过对丰田生产方式中关键用语的整理和解说,我们深入了解了这一生产方式的基本原理和核心概念。
即时生产、改善、自动停机、防错和安灯等用语,都是丰田生产方式极为重要的组成部分。
- 1、下载文档前请自行甄别文档内容的完整性,平台不提供额外的编辑、内容补充、找答案等附加服务。
- 2、"仅部分预览"的文档,不可在线预览部分如存在完整性等问题,可反馈申请退款(可完整预览的文档不适用该条件!)。
- 3、如文档侵犯您的权益,请联系客服反馈,我们会尽快为您处理(人工客服工作时间:9:00-18:30)。
後工程引取り
ジャストインタイム生産をするための3つの基本原則の1つであり、後工程が必要なときに、必要なものを必要なだけ前工程から引取ってくることをいう。
(⇒後補充生産:3頁)
后工程拿取方式
为了进行JIT生产所要遵循的3个基本原则之一、当后工程需要时、在必要的时候只从前工程拿取必要的东西的方法.称为后工程拿取方式.
(⇒后补充生産:3页)
後補充(生産)
前工程が、最小限のその工程の完成品在庫(店)をもち、後工程に引取られた分だけ、種類毎に造って補充する方法をいう。
(⇒後工程引取り:1頁)
后补充(生产)
前工程,只保持其工程的最小限度的完成品在库、只提供后工程
所需要的部分、逐个品种的制造并进行补充的方法.叫做后补充.
(⇒后工程拿取:1頁)
アンドン
関係者へのアクションを促すための情報の窓で、現時点の異常場所を一目で判断できるようにした電光表示盤である。
異常表示のほかに、作業の指示(品質チェック、刃具交換、部品運搬など)、進度表示をするものもある。
(⇒目で見る管理:155頁)
信号灯
是催促相关者采取行动的情报窗口,一看就能够判断出现在有异常发生之场所的电光表示板.除异常之外、也有用来表示作业指示(品质确认、更换刀具、部品搬运等) 、作业进度的.
(⇒目视管理:155頁)
一個流し(生産)
工程順に一個又は、一台ずつ加工・組み付けをし、一個ずつ次工程に流すやり方をいう。
(⇒工程の流れ化:39頁)
一个流程(生产)
工程的顺序是逐个或逐台地进行加工或组装、并一个一个地流给下一个工程的做法叫作一个流程.
(⇒工程的流程化:39页)
内段取り
段取り替え作業のうち、ラインや機械整備の運転を止めなければできない型・刃具・そして治具類の交換などの作業をいう。
(⇔ 外段取り:77頁)
(⇒ 段取り替え時間:89頁) 内段取
在段取更换作业中,如果不停止生产线及机器设备的运转就无法进行模型 刀具以及治具类交换等的作业称为内段取.
(⇔ 外段取:77页)
(⇒ 段取更换时间:89页)
AB 制御
工程間あるいは工程内の標準手持ち量が、常に一定量に保持されるように、各搬送機の、動いてもよい条件及び、工程から製品を搬出できる条件を、2個所(A 点、B 点)の製品の有無により制御する仕組みをいう。
AB 制御
工程间或工程内的标准持有量通常保持一定量、各搬运机的即使运转也好的条件及从工程能够搬出部品的条件依据2个地方(A 点,B 点)的制品有无来进行控制的方式称为AB 制御
搬送機が動いてもよい条件 ケースI A 点 --- 製品有り B 点 --- 製品無し
----
-
A 点
B 点 コンベア(搬送機)
改善
人(労力)、物(材料使用量及び材料・製品の在庫)、設備あるいは生産の仕組み等に関するムダ(いたるところに存在している)を見つけ、知恵を出し、できる限り費用をかけずに、迅速にムダを一つずつ排除していく一連の活動をいう。
人手作業における改善では、設備改善よりも、作業改善を優先して行わなくてはいけない。
なお、改善は、特定の人の業務ではなく、全従業員がそれぞれの立場で行うことができるものであり、行うべきものである。
(⇒ムダ:135頁)
改善
找出人(劳动力) 、物(材料使用量及材料制品的在库) 、设备或生产结构等方面存在的浪费(存在于所有地方)、想办法、尽量在不增加费用的情况下、迅速地把不良一个一个地排除下去的一系列活动称为改善.
在对手工作业进行改善时与改善设备相比必须优先进行作业的改善.
另外,改善不是特定人员的业务是所有从业人员在各自的立场上都能够进行的也是必须进行的事情.
(⇒浪費:135頁)
可動率
設備を運転したいとき(かんばんが来た時)に、正常に動いてくれる状態の確率である。
これは、設備とその保全によってもたらされる信頼性に相当し、常に100%が理想である。
(⇒稼働率:17頁)
可动率
想要运转设备时(来KANBAN时),能够保持正常运转状态的确率.
这与设备及其保全所带来的信赖性相当,通常100%是理想的.
(⇒稼动率:17页)
稼働率
後工程に必要な(売れに結びついた)生産量を加工するのに、その設備能力でフル操業した時の、定時能力に対する需要の割合をいう。
売れ行きによって、稼働率は決まるものである。
(⇒可動率:15頁)
稼动率
为了加工出后工程所必要的生产量、在设备能力的最大限度工作时、对于定时能力所需要的比例.
依销售情况决定稼动率
(⇒可动率:15页)
仕掛けかんばん
生産工程での生産着手(仕掛け)指示に使うかんばんであり、
工程内かんばんと信号かんばんがある。
开始生产KANBAN
是在生产工程用于指示着手生产(开始生产)所使用的KANBAN、
有工程内KANBAN和信号KANBAN.
工程内かんばん
工程内の仕掛け指示に用いるかんばんである。
後工程に引取られた量だけを、引取った順に後補充生産するよう仕掛けるために使うかんばんである。
(⇒後補充生産:3頁、信号かんばん:25頁)
工程内KANBAN
是工程内用于开始作业指示的KANBAN.
只是被后工程领取的量按领取的顺序进行后补充生产时为了开始生产而使用的KANBAN. (⇒后补充生产:3页、信号KANBAN:25页)
信号かんばん
1つのラインで、多種類の品物を加工しており、段取り替えに若干の時間を要するロット生産工程での仕掛けに用いるかんばんである。
三角形をしているので、通称、三角かんばんと呼ばれる。
プレス、ダイキャスト、樹脂成形工程などで、主に用いられる。
(⇒工程内かんばん:23頁)(付表:C)
信号KANBAN
一个生产线上、生产多种类的产品的批量生产工程需要若干段取切替时间、在生产开始时使用的KANBAN.
因为是三角形、所以通常称为三角KANBAN.
主要用于冲压机、模铸、树脂成形等工程.
(⇒工程内KANBAN:23頁)(付表:C)
引取りかんばん
後工程が、前工程へ部品を引取りにいくタイミングと引取り量を指示するかんばんであり、工程間引取りかんばん、外注部品納入かんばんがある。
(⇒かんばん:19頁)
领取KANBAN
后工程去前工程领取部品时,指示时机和领取量的KANBAN,有工程间领取KANBAN、外注部品纳入KANBAN。
(⇒KANBAN:19页)
工程間引取りかんばん
<=運搬かんばん>
社内で、後工程が前工程から必要なものを引取るために用いるかんばんである。
(⇒後工程引取り:1頁、外注部品納入かんばん:31頁)
工程间领取KANBAN
〈=搬运KANBAN〉
在社内、后工程为了从前工程领取必要的部品所使用的KANBAN。
(⇒后工程领取:1页、外注部品纳入KANBAN:31页)
外注部品納入かんばん
仕入先から納入される部品に用いられるかんばんである。
納入は、仕入先が行うが、工程ではずれた分だけの外注かんばんで納入されるため、基本的には、工程間引取りかんばんと同じ、後工程引取りができる。
(⇒後工程引取り:1頁、工程間引取りかんばん:29頁)
(付表:C)
外注部品纳入KANBAN
从供应商纳入的部品所使用的KANBAN。
虽然纳入由供应商进行、但因为只是工程不足的部分用外注KANBAN纳入、所以、基本上与工程间领取KANBAN相同、能够后工程领取。
(⇒后工程领取:1页、工程间领取KANBAN:29页)
(付表:C)
臨時かんばん
型保全、機械設備の修理、そして稼働日の違いなどにより、通常の生産分より多く必要とする部品の生産及び運搬を指示するかんばんをいう。
有効期限を明記し、1回だけ使用し使用後回収する。
赤色の斜線
を入れ他と識別する。
(⇒かんばん:19頁)
臨時かんばん
所谓临时看板就是指模型的保全、机器设备的修理以及稼动日的差异等情况下比通常的生产数量多出来的必要的部品的生产指示看板和搬运指示看板。
要明确记入有效期限、只使用一回使用后回收。
还要划上红色斜线与其他的进行识别。
QC工程表
目標とする品質のものを工程で造り込むために、各工程の特性に合わせた管理項目を、設定された規格や基準に基づき、誰がどのような方法で検査・チェックし、管理していくかなどを決めたものである。
(⇒作業標準:51頁)
QC工程表
以品质在工程中制造出来为目标、结合各工程的特性设定管理项目、
依据规格和基准、决定出由谁按什么样的方法进行检查、确认和有没有持续进行管理等。
(⇒作业标准:51页)。