DIN 50938-2000 铁和钢的黑色氧化涂层.要求和试验方法
工件的发黑质量与检测
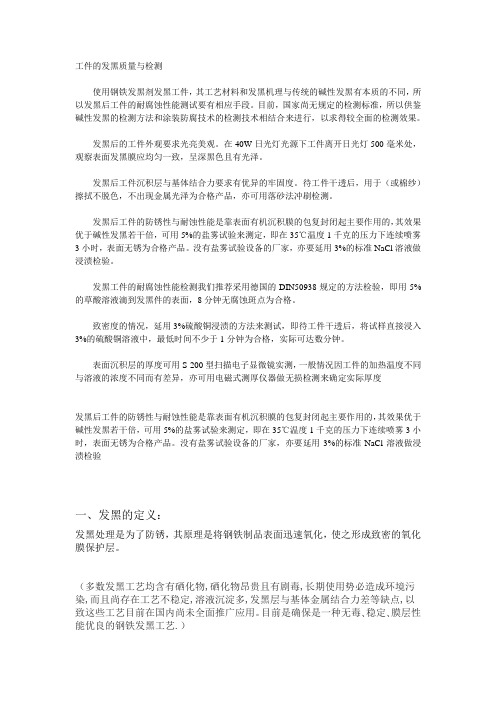
工件的发黑质量与检测使用钢铁发黑剂发黑工件,其工艺材料和发黑机理与传统的碱性发黑有本质的不同,所以发黑后工件的耐腐蚀性能测试要有相应手段。
目前,国家尚无规定的检测标准,所以供鉴碱性发黑的检测方法和涂装防腐技术的检测技术相结合来进行,以求得较全面的检测效果。
发黑后的工件外观要求光亮美观。
在40W日光灯光源下工件离开日光灯500毫米处,观察表面发黑膜应均匀一致,呈深黑色且有光泽。
发黑后工件沉积层与基体结合力要求有优异的牢固度。
待工件干透后,用于(或棉纱)擦拭不脱色,不出现金属光泽为合格产品,亦可用落砂法冲刷检测。
发黑后工件的防锈性与耐蚀性能是靠表面有机沉积膜的包复封闭起主要作用的,其效果优于碱性发黑若干倍,可用5%的盐雾试验来测定,即在35℃温度1千克的压力下连续喷雾3小时,表面无锈为合格产品。
没有盐雾试验设备的厂家,亦要延用3%的标准NaCl溶液做浸渍检验。
发黑工件的耐腐蚀性能检测我们推荐采用德国的DIN50938规定的方法检验,即用5%的草酸溶液滴到发黑件的表面,8分钟无腐蚀斑点为合格。
致密度的情况,延用3%硫酸铜浸渍的方法来测试,即待工件干透后,将试样直接浸入3%的硫酸铜溶液中,最低时间不少于1分钟为合格,实际可达数分钟。
表面沉积层的厚度可用S-200型扫描电子显微镜实测,一般情况因工件的加热温度不同与溶液的浓度不同而有差异,亦可用电磁式测厚仪器做无损检测来确定实际厚度发黑后工件的防锈性与耐蚀性能是靠表面有机沉积膜的包复封闭起主要作用的,其效果优于碱性发黑若干倍,可用5%的盐雾试验来测定,即在35℃温度1千克的压力下连续喷雾3小时,表面无锈为合格产品。
没有盐雾试验设备的厂家,亦要延用3%的标准NaCl溶液做浸渍检验一、发黑的定义:发黑处理是为了防锈,其原理是将钢铁制品表面迅速氧化,使之形成致密的氧化膜保护层。
(多数发黑工艺均含有硒化物,硒化物昂贵且有剧毒,长期使用势必造成环境污染,而且尚存在工艺不稳定,溶液沉淀多,发黑层与基体金属结合力差等缺点,以致这些工艺目前在国内尚未全面推广应用。
金属表面发黑(发蓝)工艺介绍
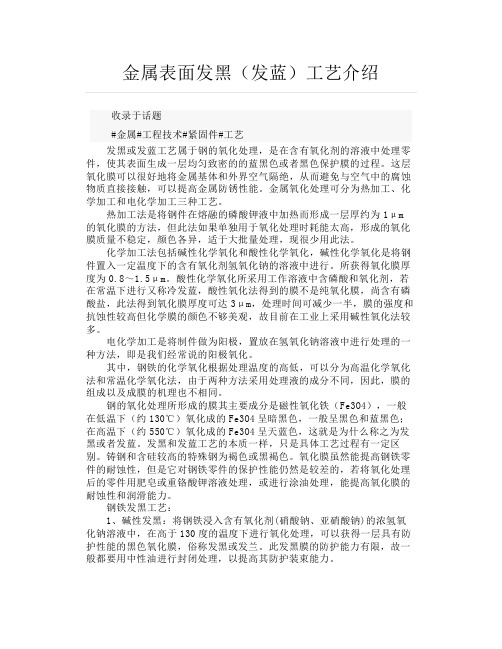
金属表面发黑(发蓝)工艺介绍收录于话题#金属#工程技术#紧固件#工艺发黑或发蓝工艺属于钢的氧化处理,是在含有氧化剂的溶液中处理零件,使其表面生成一层均匀致密的的蓝黑色或者黑色保护膜的过程。
这层氧化膜可以很好地将金属基体和外界空气隔绝,从而避免与空气中的腐蚀物质直接接触,可以提高金属防锈性能。
金属氧化处理可分为热加工、化学加工和电化学加工三种工艺。
热加工法是将钢件在熔融的磷酸钾液中加热而形成一层厚约为1μm 的氧化膜的方法,但此法如果单独用于氧化处理时耗能太高,形成的氧化膜质量不稳定,颜色各异,适于大批量处理,现很少用此法。
化学加工法包括碱性化学氧化和酸性化学氧化,碱性化学氧化是将钢件置入一定温度下的含有氧化剂氢氧化钠的溶液中进行。
所获得氧化膜厚度为0.8~1.5μm。
酸性化学氧化所采用工作溶液中含磷酸和氧化剂,若在常温下进行又称冷发蓝,酸性氧化法得到的膜不是纯氧化膜,尚含有磷酸盐,此法得到氧化膜厚度可达3μm,处理时间可减少一半,膜的强度和抗蚀性较高但化学膜的颜色不够美观,故目前在工业上采用碱性氧化法较多。
电化学加工是将制件做为阳极,置放在氢氧化钠溶液中进行处理的一种方法,即是我们经常说的阳极氧化。
其中,钢铁的化学氧化根据处理温度的高低,可以分为高温化学氧化法和常温化学氧化法,由于两种方法采用处理液的成分不同,因此,膜的组成以及成膜的机理也不相同。
钢的氧化处理所形成的膜其主要成分是磁性氧化铁(Fe3O4),一般在低温下(约130℃)氧化成的Fe3O4呈暗黑色,一般呈黑色和蓝黑色;在高温下(约550℃)氧化成的Fe3O4呈天蓝色,这就是为什么称之为发黑或者发蓝。
发黑和发蓝工艺的本质一样,只是具体工艺过程有一定区别。
铸钢和含硅较高的特殊钢为褐色或黑褐色。
氧化膜虽然能提高钢铁零件的耐蚀性,但是它对钢铁零件的保护性能仍然是较差的,若将氧化处理后的零件用肥皂或重铬酸钾溶液处理,或进行涂油处理,能提高氧化膜的耐蚀性和润滑能力。
铸铁及钢件的发黑处理

铸铁及钢件的发黑处理铸铁及钢件的发黑处理一、发黑技术的种类:钢制件的表面发黑处理,也有被称之为发蓝的。
磷化发黑主要是指中温磷化发黑,也叫特种磷化液,这一工艺是需要加温到55摄氏度左右,适用于铸铁、中碳钢、高碳钢等材料,易于操作,得到黑色或是黑灰色磷化膜。
化学镀黑镍,适用于不锈钢、电镀镍等镀件上的直接镀镍,也适用于铝、铝合金的直接镀镍,目前这种工艺很受市场欢迎。
现在市场上最常用的发黑技术其实是以下两种碱性发黑与常温发黑,传统发黑(既碱性发黑),这种传统的钢铁发黑(发兰)是在135-150摄氏度的碱性溶液中进行的,处理时间长达1-1.5小时,能耗高,效率低,污染重,目前很多企业已经正在换用现在流行的钢铁常温发黑剂,它不仅发黑质量好,无污染,也很节能,大大提高了企业的工作效率。
弥补了传统发黑的缺陷;要注意的是常温发黑工艺对于低碳钢的效果不太好,表面效果也不是很好,但是A3钢用碱性发黑好一些。
还有一种发黑是蒸汽发黑,比较适用于冶金产品。
二、常温发黑工艺的介绍:作用与用途钢铁常温发黑剂具有溶液稳定、发黑时间短色泽适宜、使用工艺方便简单,原材料充足、成本低等优点,特别是发黑膜层的附着力,抗腐蚀能力明显优于原产品。
它具有无污染、省能源、无钢型选择性等特点。
为解决长期存在的碱性高温发黑污染大、耗能高,选择钢性等问题开辟了新的途径,为各厂家钢铁制品发黑处理提供了理想的先进工艺。
本产品广泛用于机械零件、标准件、工艺产品、弹簧等工业部门的钢铁零部件表面发黑装饰及防护处理。
主要特点主要特点:(颜色黑,附着力好,防腐性高,做工时间短)1、节约能源。
发黑完全不需用电,同碱性高温发黑比,节电100%。
2、提高工效。
碱性发黑需40-80分钟,本发黑剂只需1-5分钟。
3、发黑成本低。
设备简单、只需塑料、陶瓷槽、盆即可,而且操作容易。
4、工艺适应性强。
对钢性无选择,含碳量不同和表面加状态不同的钢铁零件均能获得整体表面颜色的一致效果,而且发黑后的工件,既可脱水油封闭;又可热浸油封闭。
(整理)DIN50902-金属材料防腐涂层.
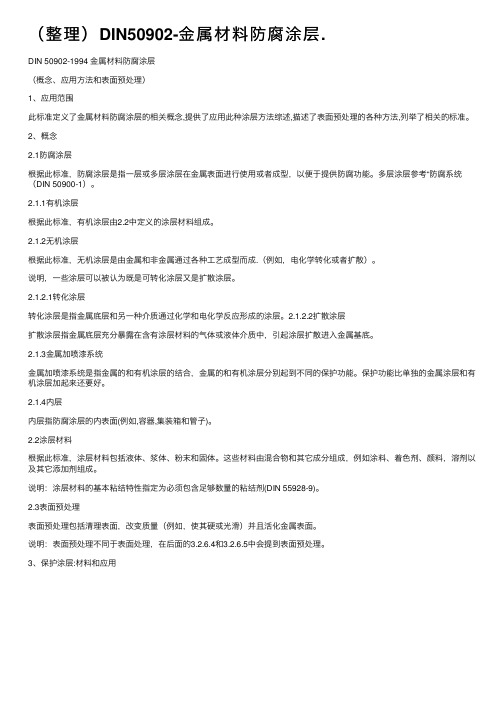
(整理)DIN50902-⾦属材料防腐涂层.DIN 50902-1994 ⾦属材料防腐涂层(概念、应⽤⽅法和表⾯预处理)1、应⽤范围此标准定义了⾦属材料防腐涂层的相关概念,提供了应⽤此种涂层⽅法综述,描述了表⾯预处理的各种⽅法,列举了相关的标准。
2、概念2.1防腐涂层根据此标准,防腐涂层是指⼀层或多层涂层在⾦属表⾯进⾏使⽤或者成型,以便于提供防腐功能。
多层涂层参考“防腐系统(DIN 50900-1)。
2.1.1有机涂层根据此标准,有机涂层由2.2中定义的涂层材料组成。
2.1.2⽆机涂层根据此标准,⽆机涂层是由⾦属和⾮⾦属通过各种⼯艺成型⽽成.(例如,电化学转化或者扩散)。
说明,⼀些涂层可以被认为既是可转化涂层⼜是扩散涂层。
2.1.2.1转化涂层转化涂层是指⾦属底层和另⼀种介质通过化学和电化学反应形成的涂层。
2.1.2.2扩散涂层扩散涂层指⾦属底层充分暴露在含有涂层材料的⽓体或液体介质中,引起涂层扩散进⼊⾦属基底。
2.1.3⾦属加喷漆系统⾦属加喷漆系统是指⾦属的和有机涂层的结合,⾦属的和有机涂层分别起到不同的保护功能。
保护功能⽐单独的⾦属涂层和有机涂层加起来还要好。
2.1.4内层内层指防腐涂层的内表⾯(例如,容器,集装箱和管⼦)。
2.2涂层材料根据此标准,涂层材料包括液体、浆体、粉末和固体。
这些材料由混合物和其它成分组成,例如涂料、着⾊剂、颜料,溶剂以及其它添加剂组成。
说明:涂层材料的基本粘结特性指定为必须包含⾜够数量的粘结剂(DIN 55928-9)。
2.3表⾯预处理表⾯预处理包括清理表⾯,改变质量(例如,使其硬或光滑)并且活化⾦属表⾯。
说明:表⾯预处理不同于表⾯处理,在后⾯的3.2.6.4和3.2.6.5中会提到表⾯预处理。
3、保护涂层:材料和应⽤4、表⾯预处理⽅法5、保护性系统的选择5.1总则涂层系统提供的保护程度依靠它的特性和腐蚀载荷(DIN 50900-3和DIN 55928-1),有许多种腐蚀,或者通过腐蚀环境进⾏识别(⼤⽓腐蚀,底层腐蚀,⽔线腐蚀或化学腐蚀),或者通过腐蚀⾏为进⾏识别(冲刷腐蚀、应⼒腐蚀、空蚀或腐蚀疲劳)。
发黑工艺及检验规范
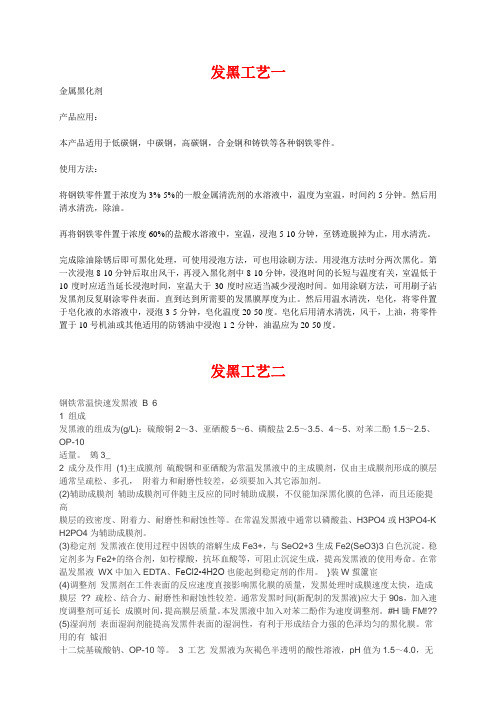
发黑工艺一金属黑化剂产品应用:本产品适用于低碳钢,中碳钢,高碳钢,合金钢和铸铁等各种钢铁零件。
使用方法:将钢铁零件置于浓度为3%-5%的一般金属清洗剂的水溶液中,温度为室温,时间约5分钟。
然后用清水清洗,除油。
再将钢铁零件置于浓度60%的盐酸水溶液中,室温,浸泡5-10分钟,至锈迹脱掉为止,用水清洗。
完成除油除锈后即可黑化处理,可使用浸泡方法,可也用涂刷方法。
用浸泡方法时分两次黑化。
第一次浸泡8-10分钟后取出风干,再浸入黑化剂中8-10分钟,浸泡时间的长短与温度有关,室温低于10度时应适当延长浸泡时间,室温大于30度时应适当减少浸泡时间。
如用涂刷方法,可用刷子沾发黑剂反复刷涂零件表面。
直到达到所需要的发黑膜厚度为止。
然后用温水清洗,皂化,将零件置于皂化液的水溶液中,浸泡3-5分钟,皂化温度20-50度。
皂化后用清水清洗,风干,上油,将零件置于10号机油或其他适用的防锈油中浸泡1-2分钟,油温应为20-50度。
发黑工艺二钢铁常温快速发黑液B 61 组成发黑液的组成为(g/L):硫酸铜2~3、亚硒酸5~6、磷酸盐2.5~3.5、4~5、对苯二酚1.5~2.5、OP-10适量。
鵕3_2 成分及作用(1)主成膜剂硫酸铜和亚硒酸为常温发黑液中的主成膜剂,仅由主成膜剂形成的膜层通常呈疏松、多孔,附着力和耐磨性较差,必须要加入其它添加剂。
(2)辅助成膜剂辅助成膜剂可伴随主反应的同时辅助成膜,不仅能加深黑化膜的色泽,而且还能提高膜层的致密度、附着力、耐磨性和耐蚀性等。
在常温发黑液中通常以磷酸盐、H3PO4或H3PO4-K H2PO4为辅助成膜剂。
(3)稳定剂发黑液在使用过程中因铁的溶解生成Fe3+,与SeO2+3生成Fe2(SeO3)3白色沉淀。
稳定剂多为Fe2+的络合剂,如柠檬酸,抗坏血酸等,可阻止沉淀生成,提高发黑液的使用寿命。
在常温发黑液WX中加入EDTA、FeCl2•4H2O也能起到稳定剂的作用。
}装W蜇籚宦(4)调整剂发黑剂在工件表面的反应速度直接影响黑化膜的质量,发黑处理时成膜速度太快,造成膜层?? 疏松、结合力、耐磨性和耐蚀性较差。
钢管钢铁等零件的发黑处理简介.pdf

钢管钢铁等零件的发黑处理简介Via 常州精密钢管博客1 概述:1.1 钢铁制品在空气中与氧接触,表面会形成一层氧化物薄膜。
但自然成膜大多数不够致密完整,因而也不能防止金属继续被氧化腐蚀。
而发黑处理,是人为形成致密氧化膜的化学方法,在钢铁制品的防腐处理中常被应用。
1.2 钢铁氧化处理方法很多,有碱性氧化法、无碱氧化法、高温气体氧化法和电化学氧化法等。
工业上,曾经广泛采用的是碱性氧化法。
1.3 碱性氧化法的特点是,色泽美观、无氢脆、有弹性、膜层厚(0.5-1.5μm),对零件的尺寸和精度无显著影响,对零件残余应力也有一定消除作用。
1.4 发黑处理:是将钢铁金属零件浸没在很浓的碱和氧化剂的溶液中,在一定温度下加热、氧化,使金属表面生成一层均匀致密而且与基体金属表面结合牢固的四氧化三铁薄膜的工艺。
这层薄膜,对金属表面的防腐有很好的作用。
由于实际生产中受各种因素的影响,这层薄膜的颜色有蓝黑色、黑色、蓝色(所以有时又称发蓝)等等。
1.5 发黑处理的目的主要有以下三点:一是对金属表面起防锈作用。
二是增加金属的美观光泽。
三是部分消除工件的残余应力。
2 氧化膜形成的基本原理2.1 原理:钢铁零件在很浓的火碱(NaOH)和氧化剂(亚硝酸钠NaNO2或硝酸钠NaNO3)溶液中加热,开始表面受到NaOH的微腐蚀作用,析出亚铁离子,亚铁离子与火碱和氧化剂起作用,生成亚铁酸钠(Na2FeO2)和铁酸钠(Na2Fe2O4),然后再由铁酸钠与亚铁酸钠进一步起作用,生成四氧化三铁(Fe3O4)。
其化学反应方程式如下:在氧化剂的存在下,铁与碱作用生成亚铁酸钠:3Fe+NaNO2+5NaOH→3Na2FeO2+NH3↑+H2O亚铁酸钠向溶液里扩散与氧化剂相遇,进一步氧化成铁酸钠(Na2Fe2O4):8Na2FeO2+NaNO3+6H2O→4Na2Fe2O4+NH3↑+9NaOH或:6Na2FeO2+NaNO2+5H2O→3Na2Fe2O4+NH3↑+7NaOH铁酸钠与未被氧化的亚铁酸钠作用,生成四氧化三铁(Fe3O4)保护膜:Na2Fe2O4+Na2FeO2+H2O→Fe3O4↓+4NaOH由于某些情况,在形成四氧化三铁膜的同时,有部分铁酸钠水解,生成红色的氧化铁水合物(Fe2O3▪mH2O)沉淀于工件表面上,表现为红锈或棕绣。
金属表面 发黑处理 工艺
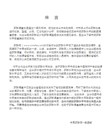
金属表面发黑处理工艺金属表面发黑处理工艺2010年06月14日星期一上午09:38一定是钢或是铁的零件!合金件不在此列!)有的朋友喜欢DIY零件、配件。
但是在完工后往往还要面临表面处理的问题,或者是不满意原来的颜色,特别是需要达到真狗的表面颜色与防锈效果,就更需要这个步骤啦!特别是有些配件的外型比较敏感,不方便给厂家直接处理。
所以今天整理了一些资料在结合自己的心得,贴出来给兄弟们共享!钢铁零件的表面处理一般有--碱性氧化法和酸性氧化法两种。
酸性氧化法也称为"发蓝"。
目的是使金属表面形成一层氧化膜,以防止金属表面被腐蚀,酸性氧化法也称为"磷化处理"(国际上大多军工企业均采取此法),其具有比发蓝更好的抗磨损性与抗腐蚀性。
钢铁制品表面经"发蓝"处理后所形成的氧化膜,其主要成分是四氧化三铁。
呈黑蓝色或深黑色。
下面就来介绍一下在家中如何操作这两种处理。
一、碱性氧化法"发蓝"药液1.配方(化工店都有卖):硝酸钠50~100克氢氧化钠600~700克亚硝酸钠100~200克水1000克2.制法:按配方计量后,在搅拌条件下,依次把各料加入其中,溶解,混合均匀即可。
(我是使用一个弃置不用的铁桶)3.流程:(1)金属表面一定要洗净和干燥、除油以后,才能进行"发篮"处理。
建议使用洗衣粉水刷洗,再浸泡1:100的稀盐酸1-5分钟除油除杂质。
(2)把要处理的零件置入铁桶中与溶液一起"煮"约1小时即可。
(3)金属"发蓝"处理后,最好用热肥皂水漂洗数分钟,再用冷水冲洗。
然后,又用热水冲洗,吹于。
最后表面涂敷机油进行封闭保护即可。
二、酸性氧化法"磷化处理"药液1.配方(化工店都有卖):磷酸3~10克硝酸钙80~100克过氧化锰10~15克水1000克2.制法与流程同碱性发蓝相同。
(整理)喷塑、发黑、电镀、磷化、阳极氧化-检验标准
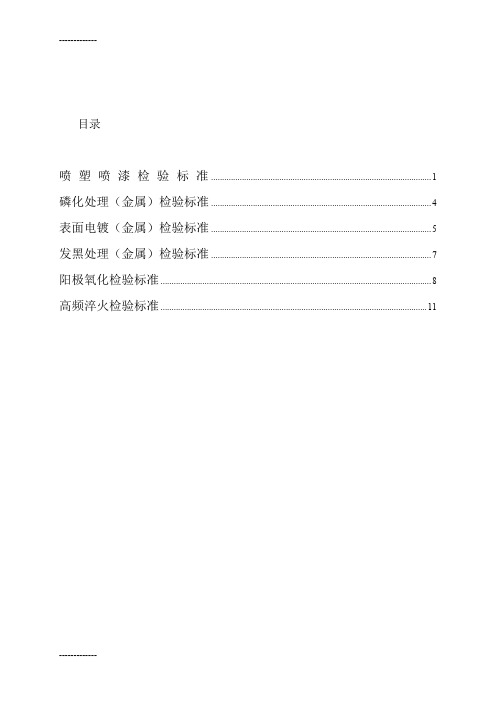
目录喷塑喷漆检验标准 (1)磷化处理(金属)检验标准 (4)表面电镀(金属)检验标准 (5)发黑处理(金属)检验标准 (7)阳极氧化检验标准 (8)高频淬火检验标准 (11)喷塑喷漆检验标准1、目的规范检验操作,发现、控制不良品,防止批不良品输入下道工序。
同时给检验工作提供引导及接收标准。
2、范围适用于进料、外协制品回厂、成品的检验接收及顾客退货的挑选检验。
3、定义喷塑、喷漆件检验过程的参照标准。
4、职责4.1 质量部负责不合格的发现、记录和标识,组织处理不合格品。
4.2 采购部负责进料中不合格品与供应商的联络。
5、工作程序外观(目测)5.1 喷涂种类(如:塑粉或漆)、颜色与图纸要求及客户、我司、供应商三方确认的色板是否一致。
5.2 一般情况下,产品喷涂表面外观在使用时要求100%进行检验,检验方式依据本标准。
进料、外协回厂或过程验收则采用抽检,抽检操作方式依据《抽检规范》。
特殊产品根据产品的具体要求检验。
5.3 外观缺陷:有缩孔、针孔、杂质点、漏底、涂层厚度明显不均、流泪、预处理不良有锈、表面有污斑、不光滑、不平整、桔皮、花斑、凹坑等。
5.4 外观和颜色检验的环境:5.4.1 色板采用客户样件或经客户认可的签样。
5.4.2 应在标准光源对色灯箱CAC-600箱内(无设备条件时则要求在天然散射光线或光照度不低于2×40w光源环境下),以目视方法进行。
光照度通常在D65(特殊情况下用F/A,其次高标准要求时用CWF/TL84),背景颜色为中灰色。
5.4.3 检查距离:被测品与眼睛的距离为500mm,检验时在±15°范围内旋转。
5.5表面粗糙度应达到设计要求的表面粗糙度值。
涂膜附着力(划格实验)5.6 涂膜附着力检验(基体金属为铁、钢、铝及铝合金):5.6.1 采用划格—胶带粘贴法测定漆膜附着力,每批次以一件或两件检验则可。
不合格时可用加严检验。
5.6.2 检验方法:使用锋利刃口的刀片(刃口宽要求0.05mm,刃口达到0.1mm时必须重新磨刃口),沿能确保得到直线切口的导向器,刃口在相对涂面35-45度角,均速划线。
- 1、下载文档前请自行甄别文档内容的完整性,平台不提供额外的编辑、内容补充、找答案等附加服务。
- 2、"仅部分预览"的文档,不可在线预览部分如存在完整性等问题,可反馈申请退款(可完整预览的文档不适用该条件!)。
- 3、如文档侵犯您的权益,请联系客服反馈,我们会尽快为您处理(人工客服工作时间:9:00-18:30)。
N02 207 Textile Systems001-en Technical Design Manual Browning DIN 50938 Page 1/1 Release: S. Liefert DTTNS 2003-10-21 Change:The following standard is used at Rieter:DIN 50938: April 2000, pages 1 - 5Black Oxide Treatment of Steel ComponentsRequirements and TestingRecommendations and Engineering Drawing Notation:Designation for a black oxide coating following DIN 50 938 on a steel (Fe) part, process group (A) bath black oxide and post-treatment by greasing, oiling or other lubricants (T4).ICS 25.220.20Brünieren von Bauteilen aus Eisenwerkstoffen –Anforderungen undPrüfverfahrenIn keeping with current practice in standards published by the International Organization for Standardization (ISO), a comma has been used throughout as the decimal marker.ForewordThis standard has been prepared by Technical Committee Chemische und elektrochemische Überzüge of the Normenausschuss Materialprüfung (Materials Testing Standards Committee).AmendmentsThis standard differs from the November 1987 edition in that it has been harmonized with DIN EN 1403 and DIN 50960-1, and it has been editorially revised.Previous editionsDIN 50938: 1973-12, 1987-11.Ref.No.DIN 50938:2000-04English price group 06Sales No.010612.01DEUTSCHE NORM April 200050938{Continued on pages 2 to 5.©No part of this translation may be reproduced without the prior permission ofDIN Deutsches Institut für Normung e.V., Berlin. Beuth Verlag GmbH , 10772Berlin, Germany,has the exclusive right of sale for German Standards(DIN-Normen).Black oxide treatment of ferrous productsRequirements and testing Translation by DIN-Sprachendienst.In case of doubt, the German-language original should be consulted as the authoritative text.SupersedesNovember 1987 edition.1ScopeThis standard specifies requirements for and methods of testing black oxide coatings produced on ferrous components by a chemical reaction during an immersion process. This process provides iron and steel (i.e.cast iron, unalloyed and low-alloy steel) components with uniform black coatings while substantially retain-ing their dimensional accuracy. The purpose of this treatment is to give the material a particular appearance and to increase its corrosion resistance even without aftertreatment. The degree of protection provided is,however, low.The standard does not cover semi-finished products and fasteners. Threaded articles shall be coated as agreed.2Normative referencesThis standard incorporates, by dated or undated reference, provisions from other publications. These normative references are cited at the appropriate places in the text, and the titles of the publications are listed below. For dated references, subsequent amendments to or revisions of any of these publications apply to this standard only when incorporated in it by amendment or revision. For undated references, the latest edition of the publication referred to applies.DIN 50017Artificial climates in technical applications – Condensation water test atmospheresDIN 50902Protective coatings on metals – Concepts, application methods and surface preparation DIN 50960-1Electroplated and chemically applied coatings – Designation and information in technicaldocumentationDIN EN 1403Corrosion protection of metals – Electrodeposited coatings – Method of specifying generalrequirementsPage2DIN50938:2000-04DIN EN ISO2064Metallic and other non-organic coatings – Definitions and conventions concerning the meas-urement of thicknessISO4519: 1980Electrodeposited metallic coatings and related finishes – Sampling procedures for inspec-tion by attributes3Concepts3.1Black oxide coatingA thermally produced dark-brown to black oxide conversion coating produced by immersion of a component in alkaline salt solution (cf. DIN50902) to which reducing agents or other reagents may have been added. The saturation of the colour obtained depends on the nature of the base metal (substrate), the heat treatment, the surface preparation and the composition and type of treatment bath.3.2Significant surfaceUnless otherwise agreed, significant surface is an area on a product that can be touched with a ball 20mm in diameter.*)4Designation4.1GeneralThe designation shall include the following information:a)The word ‘coating’;b)the number of this standard;c) a hyphen;d)the chemical symbol of the base metal or the main component of the alloy;NOTE: It is recommended that the standard designation of the base material follow the symbol of the base metal.e) a solidus;f)any additional symbols to denote further treatments to be carried out shall be separated by solidi andgive the sequence in which the coatings are applied (see subclauses 4.2, 4.3 and 4.4). If a specific treatment is not required and thus need not be referred to in the designation, this shall be indicated by a double solidus.4.2Coating methodsThere are three black oxide coating methods, each resulting in a different mean mass of coating per unit area (see table 1). These shall be designated as follows:single-bath coating: A;two-bath coating: B;three-bath coating: C.Table 1:Approximate mean mass per unit area of black oxide coatingsDesignation of Approximate mean mass percoating method unit area of coating, in g/m2A4,5B5,5C6,54.3Heat treatmentThe heat treatment shall be designated by the following:a)the letter ‘H’;b)the minimum heat treatment temperature, expressed in°C, in brackets;c)the treatment time, in hours.Designation of heat treatment carried out for three hours at a minimum temperature of 190°C:HT(190)3*)Translator’s note. In DIN EN ISO2064, ‘significant surface’ is defined as ‘The part of an article covered or to be covered by the coating and for which the coating is essential for serviceability or appearance’.Page3DIN50938:2000-044.4Supplementary treatmentsAny supplementary treatments shall be designated as in table 2.Table 2: Designation of supplementary treatments applied to black oxide coatingsSymbol Type of treatmentT1Application of paints, varnishes, pow-der coatings or similar materialsT4Application of grease, oil or other lubri-cantsT5Application of waxT10Application of water-displacing anti-corrosive agentsNOTE: The symbols conform to the standard designations for supplementary treatment for electrodeposited coatings as in DIN EN1403, except for T10.Designation of a black oxide coating on a steel (Fe) component that has not been heat-treated, but has undergone the single-bath coating process (A) and then waxed (T5):Coating DIN50938 – Fe//A/T55Order detailsThe customer shall provide the following information:a)the designation of the coating (see clause 4);b)whether heat treatment is required prior to coating (see subclause 4.3);c)the significant surface (e.g. by providing a suitably marked specimen);d)the quality, state and appearance of the base metal if they may affect the serviceability and appearanceof the coating;e)the location of unavoidable defects (e.g. attachment points);f)details of sampling, the acceptable quality level or any test requirement differing from those in ISO4519(see clause 7).The customer may provide the following supplementary information:g)any special requirements or conditions relating to the surface preparation of the components;h)any special requirements relating to the reprocessing of discarded components;i)any other special requirements (e.g. regarding roughness).6Procedure6.1Preparation of surfacesThe surfaces of the components to be coated shall be carefully degreased and any scale, oxide and other impurities removed. To prevent the temperature of the bath dropping sharply, the components may be preheated in water at 60°C to 80°C.6.2Main treatmentOne or more coating stages shall be carried out in boiling alkaline oxidizing solution at about 135°C to 145°C, optionally with reducing agents or other substances added to the bath. Depending on the composition, con-centration and temperature of the solution, the coatings will develop in immersion times of between five and twenty minutes. The coating time will also depend on the nature and quality of the components.The suppliers’ operating and safety instructions shall be observed when making up and using the bath. The condition of the bath shall be continuously checked by monitoring the boiling point, which is dependent on concentration. If necessary, this point shall be adjusted to the required value by carefully adding water or coating salt. No other bath checks are generally needed. In some cases, the quality of the coating may be improved by adding other salts to the bath.In the case of the multi-bath methods, the second immersion and, where necessary, the third immersion shall be carried out in separate baths, the boiling point of each bath being about 5°C higher than that of the preceding bath, with a rinse in cold water between baths.After coating, the components shall be rinsed, first in cold, stationary water, then thoroughly in cold, running water and finally in hot water at 60°C to 80°C.Page4DIN50938:2000-046.3Drying and supplementary treatmentAfter rinsing, the components shall be dried immediately in an oven at about 120°C or in hot air. Drying is unnecessary if there is to be an aftertreatment with hot saponifiable oil at about 120°C, in oil emulsions at 80°C to 95°C or with hot, molten wax. If the components are to be aftertreated in water-displacing anti-corrosion agents, they shall be treated while cold to minimize the loss of solvent by evaporation.Supplementary treatments serve to increase the degree of protection. To meet special requirements, paints or similar coatings may be applied.7Testing the untreated coatingThe test to be used to assess the quality of the coating or of the bath shall be agreed on a case-by-case basis. Unless otherwise agreed, the samples shall be collected as specified in ISO4519 (see clause 5, item f)).For accuracy experiments, the samples taken shall measure at least 50mm×50mm×1mm, be of the same material grade, have a surface texture as similar as possible to that of the component to be coated and have received the same treatment prior to coating.7.1AppearanceThe black oxide coating shall cover the surface of the base metal evenly and completely, and its colour shall be uniform and as black as possible. There shall be no brownish or greenish spots due to an excessive concentration or contamination of the coating bath. If a coated component that has not been aftertreated is wiped with a clean white cloth, no colour shall appear on the cloth, except in the case of cast materials and hardened components.7.2Determining the degree of protection by exposure to a standard atmosphereThe anti-corrosive effect of the coating shall be determined by suspending components or specimens that have not been aftertreated, but dried as described in subclause 6.3, in the DIN50017–KK standard atmosphere. This test may be commenced immediately after the specimens have been dried and cooled to ambient tempera-ture.Table 3:Minimum exposure times in DIN50017–KK testCoating method Minimum time with no signs of corrosion, in hoursA24B48C72The minimum exposure time shall be as specified in table 3, after which not more than 1% of the surface of the component tested shall be covered with rust, unless otherwise agreed. Slight changes in hue shall be ignored. When components having highly contoured surfaces are tested, the minimum exposure time shall be agreed on a case-by-case basis. To prevent edge corrosion, sharp edges shall be coated with acid-resistant paint after coating and prior to being placed in the test chamber. Any corrosion at such points shall be ignored.7.3Determining the degree of protection with acetic acid at ambient temperature7.3.1Test solution20% (m/m) aqueous solution of analytical grade acetic acid, CH3COOH.7.3.2ProcedureAfter coating, the components or specimens shall not be aftertreated, but dried as specified in subclause 6.3 and cooled to ambient temperature. About four drops of the test solution shall then be applied to a flat area of the coated specimen or component. The time taken for the surface of this area to be exposed shall not be less than that specified in table 4.When components having highly contoured surfaces are to be tested, full immersion with amended times may be agreed.Table 4:Minimum exposure times in acetic acid testCoating method Minimum exposure time,in minutesA10 B20 C30Page 5DIN 50938:2000-04Table 5:Assessment of oxalic acid test7.4Determining the degree of protection with oxalic acid at ambient temperature7.4.1Test solution5% (m/m ) aqueous solution of analytical grade oxalic acid, C 2H 2O 4.2H 2O.7.4.2ProcedureAfter coating, the components or specimens shall not be aftertreated, but only dried as specified in subclause6.3 and cooled to ambient temperature. About three drops of the test solution shall then be applied to a flat area of the coated specimen or component.After eight minutes’ exposure, the test solution shall be rinsed off with water and the affected area evaluated visually as in table 5.7.5Determining the mass per unit area7.5.1Test solutionChemically pure 1mo l /l hydrochloric acid with a commercial inhibitor added, the inhibitor being chosen so that the loss in mass, m 0, determined as specified in subclause 7.5.2, is less than 0,5g/m 2.An adequate inhibitory action is achieved, for example, if a 4% (m/m ) solution of hexamethylenetetramine,C 6H 12N 14, in 1mo l /l hydrochloric acid is used.7.5.2ProcedureThe coated, dried specimen or component shall be weighed (mass m 1) after the area of the surface, A , has been determined.The specimen or component shall then be immersed in the test solution at ambient temperature until the coating has been dissolved. It shall then be removed, rinsed, dried and reweighed (mass m 2).To determine the loss in mass of steel due to the action of the test solution containing inhibitor, m 0, uncoated test sheets or components made of the same material shall be weighed (mass m 3), treated for the same time as the coated component with test solution, dried and reweighed (mass m 4).The loss in mass, m 0, is given by equation (1):m 0=m 3–m 4(1)The value of m 0 shall be taken into account when calculating the loss in mass, D m , of the coated part, using equation (2):D m =m 1–m 2+m 0(2)The mass per unit area, m A , in g/m 2, is given by equation (3):10×=A m m D A (3)where m is in mg and A is in cm².8Test reportThe test report shall refer to this standard and include the following details:a)type and designation of coated component;b)type and designation of coating;c)type and results of testing as described in clause 7.Appearance of exposedQuality of coating coating areaGrey with light-grey halo Inadequate Black to brownish blackGood with exposed halo 1)1)Even good quality coatings may have verybright halos due to metal being exposed at theboundary of the area to which the solution wasapplied. However, assessment shall be basedsolely on the area covered by the drops.。