钢铁的氧化处理讲解
钢铁的氧化处理
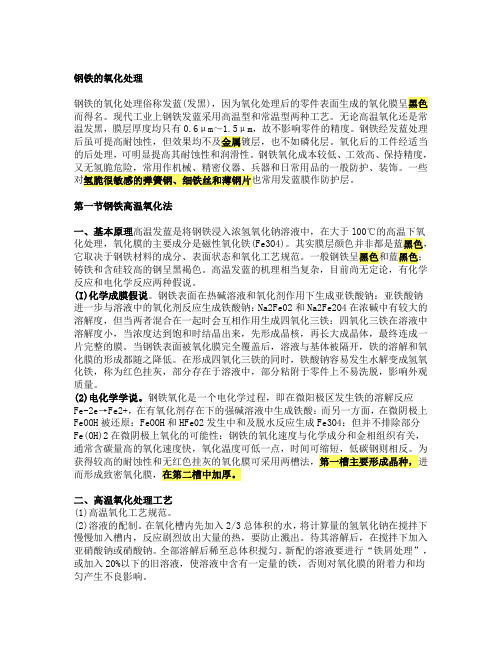
钢铁的氧化处理钢铁的氧化处理俗称发蓝(发黑),因为氧化处理后的零件表面生成的氧化膜呈黑色而得名。
现代工业上钢铁发蓝采用高温型和常温型两种工艺。
无论高温氧化还是常温发黑,膜层厚度均只有0.6μm~1.5μm,故不影响零件的精度。
钢铁经发蓝处理后虽可提高耐蚀性,但效果均不及金属镀层,也不如磷化层。
氧化后的工件经适当的后处理,可明显提高其耐蚀性和润滑性。
钢铁氧化成本较低、工效高、保持精度,又无氢脆危险,常用作机械、精密仪器、兵器和日常用品的一般防护、装饰。
一些对氢脆很敏感的弹簧钢、细铁丝和薄钢片也常用发蓝膜作防护层。
第一节钢铁高温氧化法一、基本原理高温发蓝是将钢铁浸入浓氢氧化钠溶液中,在大于l00℃的高温下氧化处理,氧化膜的主要成分是磁性氧化铁(Fe3O4)。
其实膜层颜色并非都是蓝黑色,它取决于钢铁材料的成分、表面状态和氧化工艺规范。
一般钢铁呈黑色和蓝黑色;铸铁和含硅较高的钢呈黑褐色。
高温发蓝的机理相当复杂,目前尚无定论,有化学反应和电化学反应两种假说。
(I)化学成膜假说。
钢铁表面在热碱溶液和氧化剂作用下生成亚铁酸钠:亚铁酸钠进一步与溶液中的氧化剂反应生成铁酸钠:Na2Fe02和Na2Fe2O4在浓碱中有较大的溶解度,但当两者混合在一起时会互相作用生成四氧化三铁:四氧化三铁在溶液中溶解度小,当浓度达到饱和时结晶出来,先形成晶核,再长大成晶体,最终连成一片完整的膜。
当钢铁表面被氧化膜完全覆盖后,溶液与基体被隔开,铁的溶解和氧化膜的形成都随之降低。
在形成四氧化三铁的同时,铁酸钠容易发生水解变成氢氧化铁,称为红色挂灰,部分存在于溶液中,部分粘附于零件上不易洗脱,影响外观质量。
(2)电化学学说。
钢铁氧化是一个电化学过程,即在微阳极区发生铁的溶解反应Fe-2e→Fe2+,在有氧化剂存在下的强碱溶液中生成铁酸:而另一方面,在微阴极上FeOOH被还原:FeOOH和HFe02发生中和及脱水反应生成Fe3O4:但并不排除部分Fe(OH)2在微阴极上氧化的可能性:钢铁的氧化速度与化学成分和金相组织有关,通常含碳量高的氧化速度快,氧化温度可低一点,时间可缩短,低碳钢则相反。
不同钢铁生产流程氧化-还原过程

不同钢铁生产流程氧化-还原过程钢铁是一种重要的金属材料,广泛应用于建筑、工程、机械制造、交通运输等领域。
钢铁的生产过程主要包括炼铁和炼钢两个阶段,而在这两个阶段中,氧化-还原过程是一个至关重要的环节。
1. 钢铁的生产流程1.1 炼铁阶段炼铁是从铁矿石中提取铁的过程,其主要流程包括:① 矿石的预处理:将原矿石进行破碎、筛分和洗选,去除杂质,并粉碎成粉末状。
② 熔炼还原:将矿石与焦炭和石灰石一起放入高炉中,通过燃烧产生高温,使铁矿石发生还原反应生成铁,并产生一定的熔融铁水与炉渣。
③ 高炉出铁:将高炉的铁水和炉渣分离,得到生铁。
1.2 炼钢阶段炼钢是将生铁中的碳和其他杂质除去,调整合金成分,得到合适的钢种,主要包括:① 转炉法:将生铁放入转炉中,通过吹氧、碳化钙和护炉石的作用,除去碳和其他杂质,调整钢水成分。
② 电炉法:使用电能作为加热源,将废钢或生铁熔化,通过氧化还原反应,除去杂质,得到所需的钢水。
2. 氧化-还原过程2.1 氧化过程氧化是指物质中的原子或离子与氧原子结合的过程。
在钢铁生产中,矿石的预处理和炉内燃烧过程是氧化的主要环节。
① 矿石的预处理中,矿石中的铁元素处于单质状态,通过破碎和洗选后,使其暴露在空气中,与氧气发生化学反应,发生氧化。
② 高炉内燃烧时,通过喷吹空气使焦炭燃烧产生高温,促使铁矿石中的铁元素氧化。
2.2 还原过程还原是指物质中的氧原子被还原剂夺取,转化成更低氧化态的过程。
在钢铁生产中,炼铁和炼钢过程中的还原反应是氧化-还原过程的主要环节。
① 高炉熔炼还原:在高炉内加热燃烧时,焦炭作为还原剂,夺取矿石中的氧,使铁矿石发生还原反应,生成铁。
② 转炉和电炉氧化还原:在转炉和电炉中,通过吹氧和添加还原剂,调整钢水中的碳和其他杂质含量,完成氧化还原反应。
3. 不同炼铁炼钢方法的氧化-还原过程特点3.1 高炉法高炉法是较为传统的炼铁方法,其氧化-还原过程具有以下特点:① 高炉内部温度高,燃烧强烈,氧化还原反应速度快。
45号钢表面氧化处理

45号钢表面氧化处理
45号钢是一种优质碳素结构钢,主要用于机械制造、车辆制造等领域。
其表面氧化处理可以提高其防腐性和耐磨性,延长其使用寿命。
下面介绍45号钢表面氧化处理的方法:
1.热处理法:将45号钢加热至800℃-1000℃,保温一段时间后,冷却至室温。
这种方法可以使钢表面形成一层氧化物层,具有优良的耐蚀性和耐磨性。
2.化学氧化法:采用化学方法将表面的铁离子转化为铁氧化物,形成一层致密的氧化层。
具体的处理方法包括浸泡在酸、碱、盐等溶液中,或者在高温高压下使用化学气相沉积。
3.电化学氧化法:通过电化学方法,在钢表面形成一层氧化膜。
这种方法需要使用电极,在电解液中进行电解,可以得到具有较高耐蚀性的氧化层。
总之,通过氧化处理,可以极大地提高45号钢的表面性能,提高其使用寿命,具有非常重要的应用价值。
钢铁的发黑处理(干货分享)

Na2Fe2O4+Na2FeO2+2H2O→Fe3O4↓+4NaOH
4
由于某些情况,在形成四氧化三铁氧化膜的同时,有部分铁酸钠水 解,生成红色的氧化铁的水合物(Fe2O3.mH2o),沉积在2件表面上,这 是力求避免的(这种现象一般在氢氧化钠含量高、亚硝酸钠含量低时 产生。)这种现象的产生,主要是溶液中有红色肢体状氧化铁存在的 缘故。即:
氧化处理过程中,温度对氧化膜的形成影响很大。在实际生成 中掌握温度是保证发黑质量的重要一环。钢铁制件的氧化,通常都在 溶液沸腾的温度下进行,而这一温度的高低主要与碱的浓度有关。
11
温度升高,氧化速度相应加快,氧化膜厚而致密;温度过高时,氧 化色膜泽(差F。e3温O4度)在低碱,液氧里化的不溶够解充度分提,高其,颜这色样较氧浅化,速膜度也减薄慢,,抗膜蚀层能疏力松较, 差。所以,温度应根据氧化液的成分进行选择,进槽时应取温度的下 限,出槽时应控制在温度的上限。 • 4、Fe3+影响 响很大氧。化当液溶中液氧中化的铁氧(化F铁e2O含3)量的缺含少量时对,氧(特化别膜是的新生配成的过溶程液及)质,量得影到 的氧化膜较厚,但结构很疏松,耐磨性能极差,容易剥落和擦去,这 是由于零件表面铁离子析出过多,氧化过剧的缘故。一般正常的溶液, 就碳素钢来讲,约有30%的铁离子构成氧化膜,70%的铁离子溶解在溶 液中。所以一般新配的氧化液,必须预先添加一些氧化铁(如生铁 屑)。
氧化液中加入少量的磷酸三钠,可使膜层细致,并能提高耐蚀性。 (加入量可在20~40g/L) 4、亚铁氰化钾的作用 结合氧力化好液,中减加少入褐1色~2g沉/L淀亚物铁。氰但化该钾化【学K4试Fe剂(CN有)6】毒能,使一膜般层很结少晶使细用致。,
10
四、影响氧化膜生成的主要因素
钢表面微弧氧化预处理的工艺技术分析

钢表面微弧氧化预处理的工艺技术分析钢表面微弧氧化预处理的工艺技术分析钢表面微弧氧化预处理是一种常用的工艺技术,可以提高钢材的表面硬度和耐腐蚀性。
下面将分步骤介绍这种工艺技术。
第一步:清洁表面在进行微弧氧化预处理之前,首先需要清洁钢表面。
可以使用溶剂或者碱性清洁剂将表面的油污和杂质彻底清除。
这一步骤非常重要,因为任何污物或杂质都可能对后续处理步骤产生不良影响。
第二步:浸泡预处理接下来,将清洁后的钢材浸泡在预处理液中。
预处理液通常包含碱性溶液和添加剂,用于去除钢材表面的氧化层和其他不良物质。
这个步骤的时间和温度都需要根据具体情况来确定,以确保预处理效果达到最佳。
第三步:微弧氧化处理在完成预处理步骤后,将钢材放置在微弧氧化设备中进行处理。
该设备通常由阳极和阴极组成,以及带有微弧氧化液的槽。
在设备中,通过电源给阳极和阴极施加电压,形成微弧放电。
这样可以在钢材表面形成一层致密的氧化膜。
第四步:脱膜经过微弧氧化处理后,钢材表面形成了一层坚硬的氧化膜。
然而,有时这层膜并不完美,需要进行脱膜处理。
脱膜可以通过机械研磨、化学溶解或电解腐蚀等方法来实现。
这一步骤的目的是去除氧化膜表面的不规则部分,使得钢材表面更加平整。
第五步:清洗最后,进行清洗步骤以去除任何残留物。
这一步骤可以使用水进行冲洗,也可以使用溶剂或碱性清洁剂进行清洁。
清洗后的钢材表面应该干净无污染,准备好进行后续的处理或使用。
总结起来,钢表面微弧氧化预处理的工艺技术包括清洁表面、浸泡预处理、微弧氧化处理、脱膜和清洗等步骤。
通过这些步骤的有序进行,可以有效提高钢材的表面硬度和耐腐蚀性,使其更适用于各种工业应用。
钢的表面氧化处理
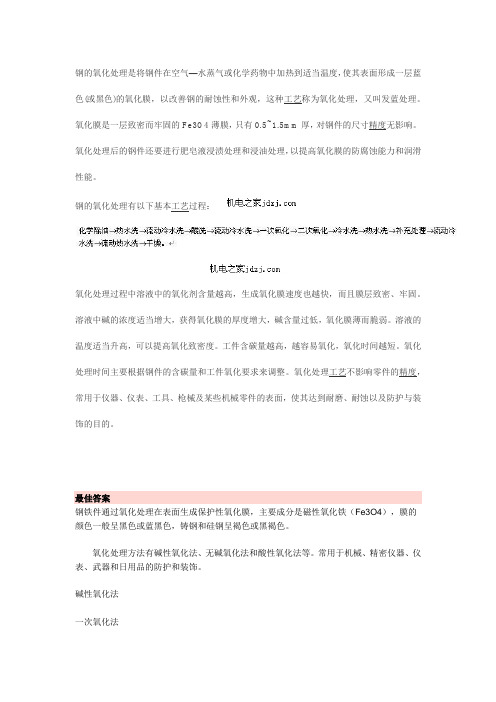
钢的氧化处理是将钢件在空气—水蒸气或化学药物中加热到适当温度,使其表面形成一层蓝色(或黑色)的氧化膜,以改善钢的耐蚀性和外观,这种工艺称为氧化处理,又叫发蓝处理。
氧化膜是一层致密而牢固的Fe3O4薄膜,只有0.5~1.5mm厚,对钢件的尺寸精度无影响。
氧化处理后的钢件还要进行肥皂液浸渍处理和浸油处理,以提高氧化膜的防腐蚀能力和润滑性能。
钢的氧化处理有以下基本工艺过程:氧化处理过程中溶液中的氧化剂含量越高,生成氧化膜速度也越快,而且膜层致密、牢固。
溶液中碱的浓度适当增大,获得氧化膜的厚度增大,碱含量过低,氧化膜薄而脆弱。
溶液的温度适当升高,可以提高氧化致密度。
工件含碳量越高,越容易氧化,氧化时间越短。
氧化处理时间主要根据钢件的含碳量和工件氧化要求来调整。
氧化处理工艺不影响零件的精度,常用于仪器、仪表、工具、枪械及某些机械零件的表面,使其达到耐磨、耐蚀以及防护与装饰的目的。
最佳答案钢铁件通过氧化处理在表面生成保护性氧化膜,主要成分是磁性氧化铁(Fe3O4),膜的颜色一般呈黑色或蓝黑色,铸钢和硅钢呈褐色或黑褐色。
氧化处理方法有碱性氧化法、无碱氧化法和酸性氧化法等。
常用于机械、精密仪器、仪表、武器和日用品的防护和装饰。
碱性氧化法一次氧化法配方1组分g/L 组分g/LNaOH 600 Na3PO4 15~20NaNO2 60开始温度为138~140℃;终止温度为148~150℃;时间为60~90min。
配方2组分g/L 组分g/LNaOH 750 NaNO2 250开始温度为138~140℃;终止温度为148~150℃;时间为60~90min。
二次氧化法配方1组分g/L 组分g/LA槽B槽NaOH 500~600 NaOH 700~800NaNO2 100~150 NaNO2 150~200温度为135~140℃;时间为10~20min。
温度为145~152℃;时间为60~90min。
氧化后处理为提高氧化膜防锈能力氧化后需进行皂化和填充处理,除需要涂装的,其他全都要用105~110℃机油、锭子油或变压器油浸渍5~10min。
钢铁的导电氧化处理工艺

钢铁的导电氧化处理工艺
钢铁导电氧化处理工艺是指利用电流作用于钢铁表面,使其形成一层具有较高电导率的氧化膜。
这种工艺可以改善钢铁的导电性能,提高其耐腐蚀性能和寿命。
以下是钢铁的导电氧化处理工艺的一般步骤:
1. 表面准备:首先,需要对钢铁表面进行清洁处理,去除油污、锈蚀等杂质,以便电流和氧化剂能够均匀地作用于钢铁表面。
2. 电极选择:根据具体情况选择适合的阳极和阴极材料,通常阳极为铅、铅合金等,阴极则为钢铁本身。
3. 定位固定:将需要处理的钢铁制品固定在阳极和阴极之间,确保电流能够均匀地通过钢铁表面。
4. 电解液配制:选择合适的电解液,通常含有含氟化物和其他添加剂,以促进氧化反应的进行。
5. 电解处理:将钢铁制品浸入电解液中,施加适当的电流和电压,使电流从阳极流向阴极,通过钢铁表面产生氧化反应。
6. 钢铁氧化:电流通过钢铁表面时,钢铁表面的金属离子与氧化剂发生氧化反
应,形成氧化膜。
氧化膜的厚度可以通过调节电流和氧化时间来控制。
7. 清洗处理:处理完毕后,需要对钢铁表面进行清洗处理,去除残留的电解液和氧化剂,以免对环境造成污染。
钢铁的导电氧化处理工艺可以应用于不同领域,如电子元器件、电工设备等,以提高钢铁材料的导电性能和耐腐蚀性能。
钢铁表面的氧化
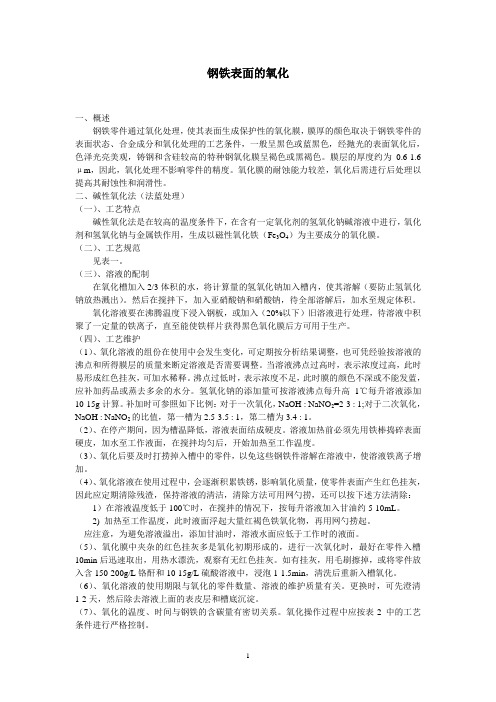
钢铁表面的氧化一、概述钢铁零件通过氧化处理,使其表面生成保护性的氧化膜,膜厚的颜色取决于钢铁零件的表面状态、合金成分和氧化处理的工艺条件,一般呈黑色或蓝黑色,经抛光的表面氧化后,色泽光亮美观,铸钢和含硅较高的特种钢氧化膜呈褐色或黑褐色。
膜层的厚度约为0.6-1.6μm,因此,氧化处理不影响零件的精度。
氧化膜的耐蚀能力较差,氧化后需进行后处理以提高其耐蚀性和润滑性。
二、碱性氧化法(法蓝处理)(一)、工艺特点碱性氧化法是在较高的温度条件下,在含有一定氧化剂的氢氧化钠碱溶液中进行,氧化剂和氢氧化钠与金属铁作用,生成以磁性氧化铁(Fe3O4)为主要成分的氧化膜。
(二)、工艺规范见表一。
(三)、溶液的配制在氧化槽加入2/3体积的水,将计算量的氢氧化钠加入槽内,使其溶解(要防止氢氧化钠放热溅出)。
然后在搅拌下,加入亚硝酸钠和硝酸钠,待全部溶解后,加水至规定体积。
氧化溶液要在沸腾温度下浸入钢板,或加入(20%以下)旧溶液进行处理,待溶液中积聚了一定量的铁离子,直至能使铁样片获得黑色氧化膜后方可用于生产。
(四)、工艺维护(1)、氧化溶液的组份在使用中会发生变化,可定期按分析结果调整,也可凭经验按溶液的沸点和所得膜层的质量来断定溶液是否需要调整。
当溶液沸点过高时,表示浓度过高,此时易形成红色挂灰,可加水稀释。
沸点过低时,表示浓度不足,此时膜的颜色不深或不能发蓝,应补加药品或蒸去多余的水分。
氢氧化钠的添加量可按溶液沸点每升高1℃每升溶液添加10-15g计算。
补加时可参照如下比例:对于一次氧化,NaOH : NaNO2=2-3 : 1;对于二次氧化,NaOH : NaNO2的比值,第一槽为2.5-3.5 : 1,第二槽为3.4 : 1。
(2)、在停产期间,因为槽温降低,溶液表面结成硬皮。
溶液加热前必须先用铁棒捣碎表面硬皮,加水至工作液面,在搅拌均匀后,开始加热至工作温度。
(3)、氧化后要及时打捞掉入槽中的零件,以免这些钢铁件溶解在溶液中,使溶液铁离子增加。
- 1、下载文档前请自行甄别文档内容的完整性,平台不提供额外的编辑、内容补充、找答案等附加服务。
- 2、"仅部分预览"的文档,不可在线预览部分如存在完整性等问题,可反馈申请退款(可完整预览的文档不适用该条件!)。
- 3、如文档侵犯您的权益,请联系客服反馈,我们会尽快为您处理(人工客服工作时间:9:00-18:30)。
27
溶液成分与处理工艺
28
碱性氧化处理
29
30
氧化后处理
• 对于不合格的氧化膜,应在酸洗溶液中除去,再重新进行氧化 处理,不允许酸洗的合金钢可用机械的方法除掉旧的氧化膜 • 不合格的氧化膜经除油后,可在10%~15%的盐酸或硫酸溶液 中退除。 (1)高温氧化后处理: • 皂化处理或重铬酸盐填充处理;
10
氧化处理的方法
• 化学氧化法
• 碱性氧化法(发蓝)
• 热氧化法 • 阳极氧化法 • 酸性氧化法(常温发蓝)
11
氧化处理之氧化前处理
• 零件表面清理的质量好坏直接影响氧化膜的质量。
• 钢件经过机械加工或者热处理后,表面有油污和氧
化皮,影响氧化膜的生成。
• 热处理后的零件可直接酸洗去除表面氧化膜,光洁
23
发黑的原理
• 在酸性条件下,钢铁表面析出Cu,与基体形成微电池,加速成 膜过程。 • 亚硒酸H2SeO3与Fe和Cu粒子反应形成黑色的膜:
• 溶解的Fe2+氧化成Fe3+,并与 反应生成黑色的 结晶参与成膜。 • 在有磷酸盐和氧化剂存在时,还可能有FeHPO3和FePO3参与 成膜,进一步提高膜层与基体的结合力和抗腐蚀性。
9
• 氧化膜生长速度和厚度取决于结晶形核速度与单个 晶核生长速度之比。 • 结晶晶核生长速度较快时:金属表面上晶核数量增 多,各晶核相互结合而形成一层连续的氧化膜(如 图a)。 • 结晶晶核生长速度较慢时:等到各结晶晶核相互结 合的时候,每一个晶核已经长大,这时形成的氧化 膜较厚,甚至形成疏松的氧化膜(如图b)
2
钢铁的氧化处理
• 概念: 将钢铁件放入含苛性钠、硝酸钠或者亚硝 酸钠溶液中处理,使零件表面生成一层很薄 的黑色氧化膜的过程,称为氧化处理,简称 发蓝,又称仪器仪表零件、液 压控制系统器件等,在其表面可以形成一层很薄的 膜层(一般0.6~1.5微米),所以对零件的尺寸和精 度都几乎没有影响,同时氧化过程中不会析氢,不 会产生氢脆。 • 钢铁件氧化处理后可提高耐蚀性,但效果不够理想, 所以如果在氧化后进行后处理,可用皂化处理或铬 酸盐钝化填充或涂油脂等,便可明显提高其耐蚀性 和润滑性。
• 《钢铁表面氧化和磷化处理问答》王尚义 著 化学工业出版社
34
度要求较高的零件可用布轮磨光或抛光。
12
氧化处理工艺—高温氧化处理
• 将钢铁浸入浓氢氧化钠溶液中,在大于l00℃的高温下氧化处
理,氧化膜的主要成分是磁性氧化铁(Fe3O4)。膜层颜色取 决于钢铁材料的成分、表面状态和氧化工艺规范。一般钢铁 呈黑色和蓝黑色;铸铁和含硅较高的钢呈黑褐色 • 单槽法:操作简单,目前广泛使用 • 双槽法:钢铁件依次在两个浓度和工艺条件不同的氧化槽中 进行两次氧化处理。氧化膜较厚,耐蚀性较高。
32
(2)满足皂化处理中的三点要求; (3)干燥处理要彻底,干燥够工件表面及孔眼、缝隙等处不能有
游离水存在;
(4)热油封闭处理的温度不可低于1050C,填充、封闭氧化膜孔 隙; (5)浸油过程若有爆裂声,说明工件的孔眼、狭缝处有水存在, 可以增加浸油时间,至无水滴爆裂声。
33
关于钢铁氧化处理还有很多知识可以作介绍,比如: • 钢铁氧化处理用设备; • 溶液的配制及各种方法处理过程中的规范性; • 氧化膜的质量检测; • 氧化膜常见缺陷及排除方法。
抗腐蚀性能。
• 被覆层具有较高的弹性。 • 抗磨强度(机械强度)是氧化膜的若干倍; • 抗腐蚀性能大大超过氧化膜。
26
无碱氧化处理的优点
• 与碱液形成的氧化膜比较: • 在氧化处理溶液中保持的时间缩短1/2~1/3; • 被覆层的抗蚀性能、附着力和机械强度比氧化膜高很多; • 工作温度100oC左右,耗能降低; • 可以同时处理黑色金属和有色金属零件; • 可以作为涂油漆层前的准备工作,油漆层与磷酸盐——氧化物 被覆层可以很好的结合。
钢铁表面的氧化处理
为什么要进行氧化处理?
• 当钢铁处于潮湿的大气中时,在它的表面上形成 了微电池,在氧的作用下钢铁表面上就形成了铁 锈。由于它非常疏松并且易吸湿,因而促使潮湿 的大气继续对钢铁进行腐蚀,直至破坏。
• 如果在钢铁表面上形成一层致密的磁性氧化铁 (Fe3O4)薄膜,就能使钢铁具有一定的抗大气腐 蚀能力,阻止钢铁表面生锈,还能起到表面装饰 的作用。
4
氧化膜生成的基本原理
在碱性溶液中,加入一定量的氧 化剂(亚硝酸钠、硝酸钠),金 属表面生成一层氧化膜(Fe3O4)。 由于溶液与金属界面形成氧化铁 的过饱和,使金属表面生成结晶 晶核,结晶晶核逐渐长大,形成 一层连续成片的氧化膜。
6
• 氧化膜形成以后,氧化过程的继续进行取决于两个因素: 界面反应速度; 参加反应物质通过氧化膜的扩散: • 有三种情况: a)仅是金属离子向外扩散,在氧化物/气体界面上进行反应; b) 仅氧向内扩散,在金属/氧化物界面上进行反应; c) 金属离子和氧两个方向相向扩散,它们在氧化膜中相遇 并进行反应 。
13
配方1:通用氧化液, 操作简单,膜层美观 光亮,但膜层较薄 配方2:氧化速度快, 膜层致密但光亮度较 差
配方1:可获得保护 性能好的蓝黑色光亮 氧化膜 配方2:可获得较厚 的黑色氧化膜
14
各组成作用
21
高温氧化处理工艺过程(双槽法)
前处理
后处理
22
氧化处理工艺—常温氧化处理
• 传统的氧化存在着碱浓度高,温度高,能耗大,生产 效率低等缺点,并且易出现红色挂灰,对于Si、Mn、 Cr、Ni含量高的合金钢,很难得到满意的外观。 • 20世纪80年代中期国内开发的发黑技术,具有节能, 效率高,成本低等有点,得到广泛应用。 • 常温发黑剂:硫酸铜和亚硒酸,加上络合剂和稳定剂 等以改善成膜条件和提高成膜质量。
• 经皂化处理后,膜的孔隙被封住,提高了抗腐蚀性能。
31
氧化后处理
• (2)碱性氧化后处理: • 碱性氧化后处理不当使膜防护性变差; • 产生原因: (1)工件氧化后清洗不彻底;(2)配制的肥皂水的水质未经软 化处理,致使溶液中产生絮状漂浮物,该漂浮物随后富集在氧 化膜的表面;(3)未经充分干燥前涂覆机油等。 处理方法: (1)氧化处理后充分的进行冷、热水清洗,除去工件表面的碱性 物质;
24
钢铁常温发黑配方
25
氧化处理工艺—无碱氧化处理
• 无碱氧化法即氧化——磷化法。 • 形成磷酸盐——氧化物被覆层。厚度约1~4 m ,膜层是在处理 过程中由于金属的部分溶解而形成。 • 可使黑色金属制品的表面呈现黑色,其外观与自碱液氧化处理 的氧化膜相同,但其被覆层与油膜或油漆膜相结合具有高度的