铝土矿焙烧_碱浸脱硅新工艺
工艺流程题解题方法

2、元素及化合物型工艺(冶金型工艺):以矿物为原料,粉碎、 煅烧、酸浸、调节PH值除杂、制备所需物质。如:铁矿石、铜矿 石等为原料的系列制备。考察重点:已学、陌生方程式的书写、水 解知识的运用。
3、实验型工艺(溶液制备物质型):利用物质溶解度受 温度影响不同,某一物质在某温度下溶解度较其它物质均 小,使反应得以发生。考察重点:分离、提纯的知识。如: 由溶液到晶体的操作:
广东高考:重点考察第2、3种的综合应用。
工艺题的常考点: 一、一些操作: 1、粉碎、研磨的目的 2、如何提高浸取率 3、为何要加热、为何要控制在一定的温度范围 4、如何获取恒定温度 5、如何洗涤,用何试剂、如何操作、如何判断洗涤干净 6、为何选用双氧水做氧化剂 7、如何调节PH 8、如何防水解 9、分离提纯的操作 二、考察方程式的书写,已知的、陌生的 三、计算:焓变、K、得失电子守恒的计算。
(1)“浸出”步骤中,为提高镁的浸出率,可采取的措施有 (要求写出两条)。
(2)滤渣I的主要成分有 。 (3)从滤液Ⅱ中可回收利用的主要物质有 。
(4)Mg(ClO3)2在农业上可用作脱叶剂、催熟剂,可采用复分 解反应制备:
MgCl2+2NaClO3===Mg(ClO3)2+2NaCl 已知四种化合物的溶解度(S)随温度(T)变化曲线如下图所示:
2.(09广东高考)(12分)某工厂生产硼砂过程中产生的固体 废料,主要含有MgCO3、MgSiO3、 CaMg(CO3)2、Al2O3 和Fe2O3等,回收其中镁的工艺流程如下:
高铁铝土矿铝铁硅分离技术的研究
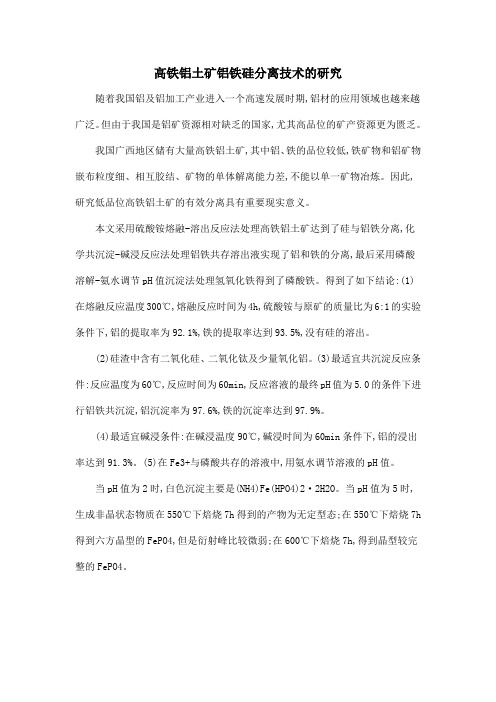
高铁铝土矿铝铁硅分离技术的研究
随着我国铝及铝加工产业进入一个高速发展时期,铝材的应用领域也越来越广泛。
但由于我国是铝矿资源相对缺乏的国家,尤其高品位的矿产资源更为匮乏。
我国广西地区储有大量高铁铝土矿,其中铝、铁的品位较低,铁矿物和铝矿物嵌布粒度细、相互胶结、矿物的单体解离能力差,不能以单一矿物冶炼。
因此,研究低品位高铁铝土矿的有效分离具有重要现实意义。
本文采用硫酸铵熔融-溶出反应法处理高铁铝土矿达到了硅与铝铁分离,化学共沉淀-碱浸反应法处理铝铁共存溶出液实现了铝和铁的分离,最后采用磷酸溶解-氨水调节pH值沉淀法处理氢氧化铁得到了磷酸铁。
得到了如下结论:(1)在熔融反应温度300℃,熔融反应时间为4h,硫酸铵与原矿的质量比为6:1的实验条件下,铝的提取率为92.1%,铁的提取率达到93.5%,没有硅的溶出。
(2)硅渣中含有二氧化硅、二氧化钛及少量氧化铝。
(3)最适宜共沉淀反应条件:反应温度为60℃,反应时间为60min,反应溶液的最终pH值为5.0的条件下进行铝铁共沉淀,铝沉淀率为97.6%,铁的沉淀率达到97.9%。
(4)最适宜碱浸条件:在碱浸温度90℃,碱浸时间为60min条件下,铝的浸出率达到91.3%。
(5)在Fe3+与磷酸共存的溶液中,用氨水调节溶液的pH值。
当pH值为2时,白色沉淀主要是(NH4)Fe(HPO4)2·2H2O。
当pH值为5时,生成非晶状态物质在550℃下焙烧7h得到的产物为无定型态;在550℃下焙烧7h 得到六方晶型的FePO4,但是衍射峰比较微弱;在600℃下焙烧7h,得到晶型较完整的FePO4。
国内外高硅铝土矿焙烧预脱硅工艺的评述

国内外高硅铝土矿焙烧预脱硅工艺的评述高硅铝土矿是一种重要的铝土矿石,其含有较高的硅和铝元素,是铝生产的重要原料之一。
然而,高硅铝土矿中的硅元素会影响铝的提取效率,因此需要进行预脱硅处理。
目前,国内外对高硅铝土矿的焙烧预脱硅工艺进行了广泛的研究和应用,本文将对其进行评述。
一、国内高硅铝土矿焙烧预脱硅工艺国内高硅铝土矿焙烧预脱硅工艺主要有热浸法、氧化焙烧法、碳酸钠焙烧法、氯化钠焙烧法等。
其中,热浸法是一种较为常用的方法,其主要原理是将高硅铝土矿与热水混合,使硅酸盐水解生成硅酸和水,从而达到预脱硅的目的。
氧化焙烧法则是将高硅铝土矿在高温氧化气氛下进行焙烧,使硅元素被氧化成为气态二氧化硅,从而实现预脱硅。
碳酸钠焙烧法和氯化钠焙烧法则是将高硅铝土矿与碳酸钠或氯化钠混合后进行焙烧,使硅元素与碳酸钠或氯化钠反应生成硅酸钠或氯化硅,从而实现预脱硅。
二、国外高硅铝土矿焙烧预脱硅工艺国外高硅铝土矿焙烧预脱硅工艺主要有氧化焙烧法、碳酸钠焙烧法、氯化钠焙烧法、氧化还原焙烧法等。
其中,氧化焙烧法和碳酸钠焙烧法与国内工艺类似,但氯化钠焙烧法则是将高硅铝土矿与氯化钠混合后进行焙烧,使硅元素与氯化钠反应生成氯化硅,从而实现预脱硅。
氧化还原焙烧法则是将高硅铝土矿在还原气氛下进行焙烧,使硅元素被还原成为固态硅,从而实现预脱硅。
三、评述从国内外高硅铝土矿焙烧预脱硅工艺的研究和应用情况来看,各种工艺均有其优缺点。
热浸法操作简单,但对设备要求较高;氧化焙烧法预脱硅效果好,但能耗较高;碳酸钠焙烧法和氯化钠焙烧法成本较低,但对环境污染较大;氧化还原焙烧法预脱硅效果好,但操作复杂。
因此,在实际应用中需要根据具体情况选择合适的工艺。
总的来说,高硅铝土矿焙烧预脱硅工艺是铝生产中不可或缺的环节,其研究和应用对于提高铝生产效率和降低成本具有重要意义。
未来,随着科技的不断进步和环保意识的提高,高硅铝土矿焙烧预脱硅工艺将会得到更加深入的研究和应用。
国内外铝土矿选矿脱硅技术现状及发展前景

・42・第十届全国氧化铝学术会议论文集国内外铝土矿选矿脱硅技术现状及发展前景晏唯真(中国铝业郑州研宄院,河南郑州450041擒薹:随着船工业和耐戈材料工业、化学工业、磨料庭其他工业的高速发展和优质铝土矿贵潭的日苴减少,铝土矿选矿已引起世界各国的广泛t视。
应用经济备理的选矿肚硅方法提高档土矿的铝硅比.正提高中低品位铝土矿质量,克分利用侣土矿青谭的有蛀才涪。
本文主要从化学琏矿脱硅、抽理选矿脱硅、生轴选矿脱硅、联奢漉程脱硅等几十方面舟拓国内外侣土矿选矿脱硅技术.分折现有铝土矿选矿脱硅技术存在的同意.并时夺后袁固铝土矿选矿脱硅的炭展前景进行了探讨。
美■硼:柘土矿}选矿由脱硅铝土矿主要用于生产氧化铝并进一步生产金属铝。
世界上90%以上的氧化铝是由铝土矿生产的,除炼铝外,铝土矿还广泛应用于耐火材料、研磨、化工产品、水泥建材工业等领域。
世界铝土矿资源丰富。
【11据估计,铝土矿储量为245亿吨,而资源(包括储量和潜在储量)为350—400亿吨,主要分布在澳大利亚、几内亚、巴西、越南、牙买加、印度、圭亚那、苏里南、印尼、希腊及中国。
世界主要产铝土矿国家探明储量列于下表。
国家睫大刺亚几内亚巴西越南牙买加印度圭亚那储量,亿l56.256.028.020252001007.0随着铝工业的高速发展,世界铝土矿开采量迅速增长,【211949年时仅7.9Mt/a(1Mt/a=l百万吨/年),1980年最高达91.36Mt/a,由于优质铝土矿急剧减少,人们不得不利用劣质铝土矿资源,特别是铝资源缺乏的发达国家,因此,铝土矿选矿问题引起了人们普遍的关注和重视。
美国和前苏联从二十世纪三、四十年代就开始了铝土矿选矿脱硅技术研究,我国在二十世纪七十年代也开始了铝土矿选矿脱硅技术研究,现在,铝士矿选矿脱硅已成为我国氧化铝生产技术研究发展的方向之一。
1铝土矿选矿脱硅的任务1.1铝土矿的类型世界上的铝土矿主要有三种类型,国外的铝土矿大多数为三水铝石型,欧洲以一水软铝石为主,希腊为一水硬铝石一一水软铝石,前苏联则各种类型铝土矿都有。
铝土矿浮选脱硅流程概述

铝土矿浮选脱硅流程概述下载温馨提示:该文档是我店铺精心编制而成,希望大家下载以后,能够帮助大家解决实际的问题。
文档下载后可定制随意修改,请根据实际需要进行相应的调整和使用,谢谢!并且,本店铺为大家提供各种各样类型的实用资料,如教育随笔、日记赏析、句子摘抄、古诗大全、经典美文、话题作文、工作总结、词语解析、文案摘录、其他资料等等,如想了解不同资料格式和写法,敬请关注!Download tips: This document is carefully compiled by theeditor. I hope that after you download them,they can help yousolve practical problems. The document can be customized andmodified after downloading,please adjust and use it according toactual needs, thank you!In addition, our shop provides you with various types ofpractical materials,such as educational essays, diaryappreciation,sentence excerpts,ancient poems,classic articles,topic composition,work summary,word parsing,copy excerpts,other materials and so on,want to know different data formats andwriting methods,please pay attention!铝土矿浮选脱硅流程概述一、引言铝土矿是生产氧化铝的主要原料,而硅是铝土矿中的主要杂质之一。
二十世纪四十年代

二十世纪四十年代,匈牙利、前南斯拉夫和奥地利的高硅铝土矿就是劳塔厂通过焙烧的方法进行处理的,这个厂位于德国。
在700~1000℃的环境中焙烧铝土矿,之后再90℃的条件下,用苛性碱(10%)将焙烧矿溶出。
使铝土矿焙烧脱硅率达到最高的80%的最佳温度是900!~1000摄氏度,同时,精矿的A/S从之前的四点五提高到了二十,将三氧化二铝的损失率维持在百分之五以下。
但是,这种处理方法也存在着诸多问题,在溶出环节,由于较大的液固比,使得该方法存在溶出时间太长,物料流量较大,溶出液中二氧化硅含量过低,使后续工艺复杂化的缺陷。
另外铝土矿产地的不同对于该环节也有较大的影响,因为含硅矿物的形态及晶格差异会脱硅效果的差异。
国外铝土矿焙烧预脱硅研究已有近五十年的历史,但尚未见工业应用,主要原因是传统的焙烧预脱硅方法要使用高浓度碱液,液固比太大,物料流量大,烧碱消耗高,且焙烧后的铝土矿需要较高的溶出温度[i]。
上世纪五十年代,铝土矿预焙烧脱硅工艺研究在我国开始兴起,以提高铝土矿原矿的A/S 比为目的。
相关实验研究最早是在鞍山开始的,在鞍山竖炉里焙烧铝土矿,但是,得到的结果是脱硅效果既不明显也不稳定。
后来有人采用其他方法也未取得较好的效果。
之后对于铝土矿预焙烧脱硅的研究中断了一段时间。
1980年前后,又有大量的科研人员进行了大量的实验,得到了一些新的结论。
仇振琢曾对于山东的铝土矿和产于山西的铝土矿焙烧脱硅效果做过对比试验,焙烧温度在1000摄氏度到1200摄氏度间,温度在1100摄氏度效果更好[ii]。
实验研究证明,在焙烧温度升高的情况下,从高岭石分解所得γ-三氧化二铝往α-三氧化二铝晶形的转化幅度增加,所得产物在碱液中也越稳定,减少了三氧化二铝的消耗。
在高温,低压的环境下做预脱硅实验,浸出液的液固比也会较大幅度的降低。
浸出周期缩短为原来的四分之一,三氧化二铝的消耗也几乎为零,而且还有百分之六十左右的脱硅率。
刘今等人用含有高岭石及一水硬铝石的山西普铝矿进行化学脱硅小型实验:原矿的化学成分为:60.41%AL2O3、12.83%SIO2DUNAHO、6.13%Fe2O3,铝硅比为AL2O3/SIO2=4.7,粒度为-74μm,实验温度控制在600 ~1100℃的范围内,溶出温度为90℃和120℃,Na2O浓度为77.5g/l[iii]。
铝土矿工艺流程

铝土矿工艺流程
铝土矿是一种重要的铝资源,其主要成分是氧化铝和硅酸盐类物质。
铝土矿的工艺流程主要包括矿石选矿、矿石破碎、矿浆制备、脱铝和尾矿处理等环节。
首先是矿石选矿。
从矿石中提取有价值的矿石物质是铝土矿工艺流程的首要环节。
一般采用重选和浮选相结合的方式进行矿石选矿,通过重力和浮力的作用分离出铝土矿和其他杂质。
接下来是矿石破碎。
选矿后的矿石需要经过破碎处理,一般采用颚式破碎机、圆锥破碎机等设备将矿石破碎成一定粒度的颗粒,以便进行后续的工艺处理。
然后是矿浆制备。
经过破碎的矿石进一步进行磨矿,将矿石磨细成一定粒度的矿浆。
磨矿一般采用湿式磨矿,将矿石与水进行混合磨矿,通过磨矿可以充分释放出铝土矿中的有价值物质。
接下来是脱铝。
脱铝是铝土矿工艺流程中最关键的环节之一。
脱铝一般采用氢氧化钠法或碱浸法,将矿浆与氢氧化钠等碱性物质反应,使铝土矿中的氧化铝转化为可溶性钠铝酸盐,并通过过滤等方法分离出钠铝溶液。
最后是尾矿处理。
脱铝后剩余的尾矿称为赋存矿,其中含有一定量的铝和硅酸盐。
为了综合利用资源和保护环境,在工艺流程的最后一步,对尾矿进行处理。
一般采用采取浸出、浮选等方法,使得尾矿中的有价值物质得到回收利用。
综上所述,铝土矿工艺流程主要包括矿石选矿、矿石破碎、矿浆制备、脱铝和尾矿处理等环节。
通过这些环节的处理,可以充分提取铝土矿中的有价值物质,并对尾矿进行处理,实现资源的综合利用和环境的保护。
铝土矿工艺流程的优化和改进,能够提高铝土矿的开采利用效率,为铝工业的发展提供支持。
氧化铝的生产工艺流程

氧化铝的生产工艺流程氧化铝是一种重要的无机化工原料,广泛应用于陶瓷、电子、铝合金、媒体过滤等领域。
下面以氧化铝的工业生产工艺流程为例,介绍其详细流程。
首先,氧化铝的生产通常从铝土矿的选矿开始。
铝土矿是一种含有氧化铝的矿石,通过破碎、磨矿等工艺将铝土矿石细碎,并通过重选、浮选等方式选取出合格的含铝矿石。
接下来,将选矿好的铝土矿石送入钠熔炉进行浸出反应,也就是将其与熔融的氢氧化钠进行反应。
反应温度通常在220-240摄氏度,反应时间根据矿石的性质会有所不同。
在反应过程中,铝土矿中的氧化铝与氢氧化钠反应生成氢氧化铝,并生成相应的矿化液。
随后,将矿化液进行离固分离,将其与蒸发分离进行结晶。
首先将矿化液加热蒸发,使溶液中的水分逐渐蒸发,然后通过结晶器进行结晶。
结晶过程通常采用分级结晶,即先进行粗结晶,然后进行细结晶。
在结晶完成后,将结晶好的氢氧化铝进行固液分离。
常用的分离方式有压滤和离心分离,将氢氧化铝沉淀进行固液分离,得到含有氧化铝的湿氢氧化铝。
最后,将湿氢氧化铝进行干燥和焙烧处理,使其转化为氧化铝颗粒。
湿氢氧化铝经过预烧干燥,然后进入回转窑进行焙烧。
焙烧温度通常在1000-1200摄氏度范围内,焙烧时间也会根据产品要求和矿石性质有所变化。
最终,经过焙烧处理的氧化铝经过再次冷却后,即可得到成品氧化铝。
成品根据不同要求可进行研磨、筛分和包装等处理,得到底细度和颗粒度适宜的氧化铝产品。
综上所述,氧化铝的生产工艺流程主要包括矿石的选矿、浸出反应、结晶分离、固液分离、干燥焙烧等环节。
每个环节都需要精确的控制条件和设备来保证产品的质量和效率。
随着技术的不断进步,氧化铝的生产工艺也在不断优化和改进。
- 1、下载文档前请自行甄别文档内容的完整性,平台不提供额外的编辑、内容补充、找答案等附加服务。
- 2、"仅部分预览"的文档,不可在线预览部分如存在完整性等问题,可反馈申请退款(可完整预览的文档不适用该条件!)。
- 3、如文档侵犯您的权益,请联系客服反馈,我们会尽快为您处理(人工客服工作时间:9:00-18:30)。
摘 要 : 针对中 、低铝硅比的一水硬铝石2高岭石型铝土矿 ,进行了回转窑焙烧和常压碱浸脱硅试验研究 ,结果表明 :该工艺是可行 的 ,其焙烧工艺条件为 :焙烧温度 1 050~1 100 ℃,焙烧时间 15~20 min ;常压碱浸脱硅工艺条件为 :Na2Ok 浓度为 100~150 gΠL ,液固 比 4~5 的条件下 ,溶出温度为 90 ℃左右 ,溶出时间为 2 h。此时脱硅率达 55. 20 % ,精矿铝硅比 (AΠS) 为 9. 9 ,与加压溶出条件下取得 的脱硅效果相当 。而采用两段溶出脱硅能够提高焙烧矿的脱硅率 ,显著缩短溶出时间 :当第一 、二段溶出时间均为 30 min 时 ,焙烧 矿的脱硅率可达 59. 65 %。高压拜耳法溶出试验表明 :经过焙烧脱硅得到的铝精矿的脱硅率比原矿高 。 关键词 : 铝土矿 ; 回转窑 ; 焙烧脱硅 ; 常压溶出
我国铝土矿资源丰富 ,储量达 24 亿 t ,但从矿石的 类型来看 ,98 %的铝土矿为一水硬铝石 ,且大多数铝硅 比为 4~7 。由于矿石铝硅比低 ,目前我国氧化铝的生 产主要采用联合法和烧结法 ,与拜耳法相比 ,这两种方 法能耗高 、生产流程长 、工艺复杂 ,使得我国氧化铝工 业经济效益低 ,国际市场竞争力差 。
表 1 铝土矿 X 衍射线定量分析结果Π%
一水硬铝石 高岭石
赤铁矿
锐钛矿
α2石英
62. 15
19. 36
6. 80
2. 86
4. 58
① 基金项目 : 国家重点基础研究发展规划 (973 计划) 项目 ( G1999064901) 收稿日期 : 2002204214 第一作者 女 副教授
© 1994-2007 China Academic Journal Electronic Publishing House. All rights reserved.
2 试验结果与分析
2. 1 回转窑的焙烧制度 铝土矿焙烧的好坏直接影响到后续碱浸脱硅的效
果 ,控制好焙烧条件 ,有利于提高焙烧矿的脱硅率 。 焙烧温度和焙烧时间是影响铝土矿焙烧效果的重
要因素 ,只有通过两者相互配合 ,才能取得好的焙烧效 果 。在溶出温度 140 ℃,溶出时间 20 min ,液固比 LΠS = 3 ,碱浓度 Na2Ok = 100 gΠL 的高压溶出条件下 ,回转 窑的焙烧制度对脱硅率的影响如图 1 、2 和表 2 所示 。
由图 1 可见 ,在焙烧温度较低 (1 000~1 050 ℃) 时 ,随着焙烧时间的延长 ,焙烧矿的脱硅率升高 ;而在 较高的温度 (1 200 ℃) 时 ,随着焙烧时间的延长 ,焙烧 矿的 脱 硅 率 降 低 。由 图 2 可 知 , 焙 烧 时 间 较 短 ( 10 min) 时 ,随着焙烧温度的升高 ,焙烧矿的脱硅率升高 ; 而在较长的焙烧时间 (40 min) 时 ,随着焙烧温度的升 高 ,焙烧矿的脱硅率降低 。当温度为 1 050~1 100 ℃、 时间为 15~20 min ,都能取得较高的脱硅率 。因此 ,适 宜的焙烧温度为 1 050~1 100 ℃,焙烧时间为 15~20 min ,此时脱硅率可达 55. 61 % ,精矿铝硅比为 9. 92 。
Desilication of Bauxite by Roasting2alkali Leaching ———Ne w Process
FAN Xiao2hui , J IANG Tao ,QIU Guan2zhou ,LI Guang2hui ( Department of Mineral Processing Engineering , Central South University , Changsha 410083 , Hunan , China)
Abstract : A test is made of desilication of the diaspore2kaolin type bauxide by rotary kiln roasting normal pressure alkali leaching. The results show that the process is feasible. Its roasting process conditions are as follows : T = 1 050 ~1 100 ℃, and t = 15~20 min , and its normal pressure alkali leaching conditions are as follows : Na2Ok concentration of 100~150 gΠL , a LΠS ratio of about 4~5 , a digestion temperature of 2 h. Under the above conditions , the desilication ratio is 55. 20 % and the AΠS ratio is 9. 9. These results is equal to the ones obtained by pressure digestion. Two2stage digestion can improve the desilication ration of roasted ore and reduce greatly the digestion time. When the times of the 1st and 2nd stages are 30 min , respectively , the desilication ratio of roasted ore is up to 59. 69 %. The digestion test by the Bayer process shows that the de2 silication ratio of aluminium concentrate obtained by roasting desilication is higher than the one of run2of2mine ore. Key words : bauxite ; rotary kiln ; desilication roasting ; normal pressure digestion
0. 76
0. 68
0. 74
0. 81
40
0. 71
0. 70
0. 80
0. 68
0. 64
由表 2 可知 ,在各种试验条件下 ,Al2O3 的损失率
均在 0. 6 %~0. 9 %之间 ,与未经焙烧处理的铝土矿的 Al2O3 的损失率 (0. 33 %) 接近[2] 。因此 ,除了铝土矿中
本身存在少量的可溶性 Al2O3 外 ,焙烧2碱浸脱硅工艺 不会带来氧化铝的附加损失 。
焙烧矿的溶出脱硅试验在 XJ T 加热搅拌浸出装 置中进行 。将焙烧矿置于一定浓度的苛性碱溶液中 , 搅拌一定时间溶出脱硅 ,试验过程采用电热装置供热 , 温度采用自动控制器控制 。同时 ,保持搅拌槽中矿浆 的体积不变 ,以保证溶出过程中液固比的恒定 。试验 结束 后 立 即 进 行 过 滤 , 滤 液 取 样 化 验 分 析 SiO2 和 Al2O3 的浓度 ,并计算脱硅率 。
第 22 卷第 3 期 2002 年 9 月
矿 冶 工 程
MINING AND METALL URGICAL ENGINEERING
Vol . 22 №3 September 2002
①
铝土矿焙烧2碱浸脱硅新工艺
范晓慧 , 姜 涛 , 邱冠周 ,李光辉
(中南大学 矿物工程系 ,湖南 长沙 410083)
2. 2 常压溶出制度 加压溶出具有溶出时间短 、生产效率高等优点 ,但
是该工艺的矿浆温度要超过 140 ℃,反应器必须能耐 一定的压力 ,而且生产中需要消耗大量的蒸汽来加热 矿浆 。另外 ,温度越高 ,溶出过程中的钠硅渣的生长速 度越快 ,数量越多 ,同时导致焙烧矿的脱硅率降低 。如 果在低温 、常压的条件下也能脱硅 ,那么就减少生产中 蒸汽的消耗量 ,并使生产更为容易 。因此 ,研究了在低 温 、常压的条件下溶出脱硅的工艺条件 。试验用的焙 烧矿是经回转窑焙烧后的矿石 ,焙烧温度 1 100 ℃,焙 烧时间 20 min 。 2. 2. 1 溶出温度和溶出时间 在适宜的 Na2Ok 浓度 (100~150 gΠL) 和液固比 (4~5) 条件下 ,观察了溶出温 度和时间对脱硅率和精矿铝硅比的影响 ,如图 3 和图 4 所示 。
© 1994-2007 China Academic Journal Electronic Publishing House. All rights reserved.
第3期
范晓慧等 : 铝土矿焙烧2碱浸脱硅新工艺
85
已完全满足拜耳工艺要求 。原矿和铝精矿的拜耳法溶 出试验结果 (见表 4) 表明 :铝精矿中 Al2O3 的理论溶出 率 、实际溶出率和相对溶出率都有大幅度的提高 。表明 铝土矿经焙烧后不会影响其 Al2O3 的高压溶出性能 。
1. 1 原料条件 试验中所用的铝土矿为山西铝厂烧结法生产用的
普铝矿 ,矿石中 Al2O3 60. 12 % ,SiO2 13. 65 % ,铝硅比为 4. 4 ,属中低铝硅矿石 ,原料粒度为 0~20 mm。
铝土矿中矿物组成如表 1 所示 。铝土矿中硅主要 以高岭石和天然的α2石英两种形式存在 。
84
矿 冶 工 程
第 22 卷
1. 2 研究方法 铝土矿的焙烧在 /○300 mm ×1 400 mm 的回转窑上