柴油机润滑系统仿真结果以及和台架实验数据的对比
增压中冷柴油机润滑系统优化设计

( aut o rnpr tnE g er g K n ig n esy f c neadTcnl yK n i u n 524 C ia Fcl Taso ao ni e n , um n i r t o i c eh o g , um n Y n a 602 ,hn ) yf ti n i U v i S e n o g n
仿真模型 ,对润滑系统的流动特性进行仿真分析 ,试验结果 与仿 真结 果基本一致 ,验证 了仿 真模型的准确性。研究表 明:该柴油机润滑系统机油泵供 给充足 ,关键摩擦副的流量 、压力满足要求 ,最小油膜厚度 明显高于许可值。在满足关
键摩擦副润滑要求的前提下 ,优化 了活塞冷却喷嘴尺寸和机油泵流量特性 ,解决了活塞冷却 喷嘴冷却过度的不足 。
i g o itn c oi o ze . n fp so o l ngn zls
Ke wo d :u b c ag d i trc oi g de e n ie;u rc t n s se ; i f w; i p e s r y r st r o h r e n e— o ln isle gn l b ai y tm ol l i o o ol r su e
柴油机润滑系统具有润滑 、冷却 、密封 、防锈及
度发动机润 滑系统设计 的需要 。基于数 值模拟的 网络
清洗等功能 ,对柴油机 的经济性 、可靠性及排 放都有
法则 将润滑系统的各个部件描述为独立的流动阻力 系 统 ,按 照润滑系统的结构 、组成模拟 网络 ,并在摩擦
smu ain mo e ft el b c to y tm ft e d ee n i ewa u l a d t efo c aa trsiso h u rc to y - i lto d lo h u r ain s se o is le gn sb it n h w h rce tc ft el b ain s s i h l i i tm r t d e . i lto e u t r d n ia t e t e u . e su y i dc tst a h u fl b c to y tm e wee su id S mu ain r s lswe ei e t lwi ts s hs T t d n i ae h tte p mp o r ain s se c h r h ui s p le u ce t . eolf w n rs u e o h e rc in c mp n n si is le gn e h e u rme t . e u p iss f inl Th i l i y o a d p e s r ft e k y fit o o e t n de e n i e me tte rq ie n s Th o mi i m i fl t ik e so e rn s i ih rt a e o nmu oli m h c n s fb a g s h g e h n rc mme d d v l e I h r mie o ei g t e l b c to e i n e au . n t e p e s fme tn h u r ain r — i q ie ns o e rcin c mp n n s t e pso o l g n zlsa dolp mp wa pi z d t e ov h x e sv o l u rme t fk y fito o o e t ,h itn c oi o ze i u so tmie o rs le te e c sie c o— n n
基于Simulink的柴油机仿真计算程序的研究及界面设计

方法 , 不用语句程序而采用模块化框 图进行编程 , 整 体应用更方便 , 可 以根据 实际需要 进行连 接组合。 而且还可编写 G U I 界面来控制所编写 的仿真程序 ,
基金项 目: 国家科 技支撑计划 8 6 3项 目( 2 0 1 2 B A F 0 1 B 0 1 ) : 船舶柴 油机关键 系统绿色制造技术 与集成应用工程 。
t h e c a l c u l a t i o n r e s u l t s b a s i c a l l y a g r e e d wi t h t h e e x p e i r me n t a l r e s u l t s ,t h u s v e i r f y i n g t h e a c c u r a c y o f
h e ≥ 一 “ d m - m a u 。 J )
’
式 中, P为缸 内工 质 压力 ; V为气 缸 工作 容 积 ; Q 为 燃 料 在气 缸 内燃烧 放 出 的热量 ; Q 为通 过 气缸 诸 壁 面传 人或 传 出 的热 量 ; m 、 m 为 流 人 流 出气 缸 的工 质质 量 ; 、 h 为进 气 门 、 排气 门处工 质 的 比焓 。 1 . 2 气 缸
柴油机的仿真计算对其研发设计及性能预测意 义重 大 , 尤其 是可 以根据 实 际仿 真 的需 求 自行 改 变 程序。以往在编写柴油机仿真计算程序时应用的都
是语句程序, 不能实现程序的模块化 。M a t l a b软件 中的 S i m u l i n k编程 环境 中提供 了一 种 新 的框 图编程
Re s e a r c h o f S i mu l a t i o n Ca l c u l a t i o n Pr o g r a m f o r Di e s e l En g i n e Ba s e d o n S i mu l i n k a n d I n t e r f a c e De s i g n
某柴油机润滑系统优化设计仿真计算

某柴油机润滑系统优化设计仿真计算兰剑;王宏大;胡必谦;胡志胜【摘要】基于Flowmaster软件建立某型柴油机润滑系统的一维仿真模型.模拟该发动机的油压分布状况,将计算结果与试验数据进行对比分析.优化计算模型,模拟润滑系统更改后的油压分布状况,评估润滑系统设计更改的可行性.【期刊名称】《汽车零部件》【年(卷),期】2015(000)003【总页数】3页(P37-39)【关键词】发动机;润滑系统;机油压力【作者】兰剑;王宏大;胡必谦;胡志胜【作者单位】安徽江淮汽车股份有限公司技术中心,安徽合肥230601;安徽江淮汽车股份有限公司技术中心,安徽合肥230601;安徽江淮汽车股份有限公司技术中心,安徽合肥230601;安徽江淮汽车股份有限公司技术中心,安徽合肥230601【正文语种】中文润滑系统压力分布是判断发动机润滑系统工作性能的关键参数,同时也是发动机安全监控的重要指标[1]。
如果发动机润滑系统油压过低,将会对发动机造成很大的损害,甚至会使发动机提前报废。
文中所计算的发动机为四缸柴油机,根据设计,需要在缸体与缸盖油道间增加一个直径2 mm的链润滑油道,因此需要评估设计更改对润滑系统的影响。
基于一维流体分析软件Flowmaster建立该柴油机润滑系统一维计算模型。
首先对原状态进行计算分析,将计算结果与试验结果进行对比分析,验证计算模型的准确性。
然后对整改的设计模型进行分析,评估整改方案的可行性。
为方便阐述,文中所涉及的压力均为绝对压力。
其中原润滑系统为方案A,整改后润滑系统为方案B。
使用Flowmaster软件对发动机润滑系统各点机油压力进行计算分析,建立润滑系统模型。
根据图1所示的润滑系统流程图,使用Flowmaster建立计算模型,计算润滑系统油压分布状况。
根据润滑系统设计原理,利用一维流体计算软件Flowmaster搭建文中计算所涉及润滑系统,如图1所示。
依据润滑系统原理图所构建计算模型如图2所示。
润滑油模拟台架试验

润滑油模拟台架试验
润滑油在评定了它们的特殊理化性能之后,一般还要进行某些模拟台架试验,包括一些发动机试验,通过之后方能投入使用。
具有极压抗磨性能的油品都要评定其极压抗磨性能。
常用的试验机有梯姆肯环块试验机、FZG齿轮试验机、法莱克斯试验机、滚子疲劳试验机等,它们都用于评定油品的耐极压负荷的能力或抗磨损性能。
评价油品极压性能应用最为普遍的试验机是四球机,它可以评定油品的最大无卡咬负荷、烧结负荷、长期磨损及综合磨损指数。
这些指标可以在一定程度上反映油品的极压抗磨性能,但是,它与实际使用性能在许多情况下均无很好的关联性。
只是由于此方法简单易行,才仍被广泛采用。
在高档的车辆齿轮油标准中,要求进行一系列齿轮台架的评定,包括低速高扭矩、高速低扭矩齿轮试验;带冲击负荷的齿轮试验;减速箱锈蚀试验及油品热氧化安定性的齿轮试验。
评定内燃机油有很多单缸台架试验方法,如皮特W-1、AV-1、AV-B和莱别克L-38单缸及国产1105、1135单缸,可以用来评定各档次内燃机油。
目前API内燃机油质量分类规格标准中,规定柴油机油用Caterpillar、Mack、Cummins、单缸及GM多缸进行评定;汽油机油则进行MS程序ⅡD(锈蚀、抗磨损)ⅢE(高温氧化)ⅤE(低温油泥)等试验。
这些台架试验,投资很大,每次试验费用
很高,对试验条件如环境控制、燃料标准等都有严格要求,不是一般试验室都能具备评定条件的,只能在全国集中设置几个评定点,来评定这些油品。
总之,由于各类油品的特性不一,使用部位又千差万别,因此必须根据每一类油品的实际情况,制定出反映油品内在质量水平的规格标准,使生产的每一类油品都符合所要求的质量指标,这样才能满足设备实际使用要求。
柴油机主轴承在不同润滑油温度下的润滑效果分析
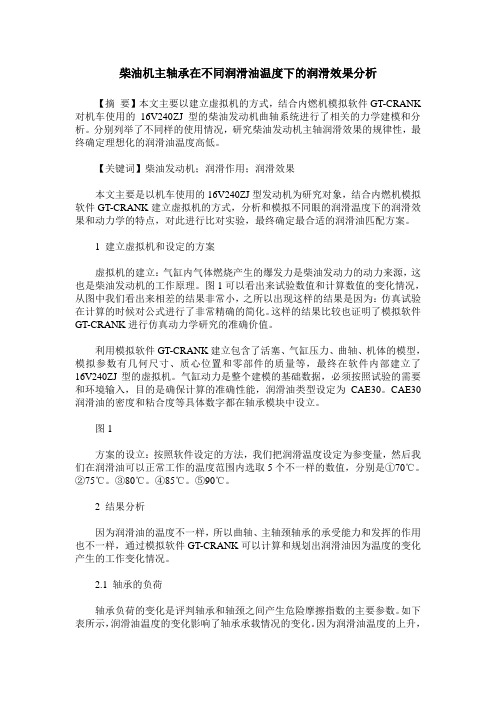
柴油机主轴承在不同润滑油温度下的润滑效果分析【摘要】本文主要以建立虚拟机的方式,结合内燃机模拟软件GT-CRANK 对机车使用的16V240ZJ型的柴油发动机曲轴系统进行了相关的力学建模和分析。
分别列举了不同样的使用情况,研究柴油发动机主轴润滑效果的规律性,最终确定理想化的润滑油温度高低。
【关键词】柴油发动机;润滑作用;润滑效果本文主要是以机车使用的16V240ZJ型发动机为研究对象,结合内燃机模拟软件GT-CRANK建立虚拟机的方式,分析和模拟不同眼的润滑温度下的润滑效果和动力学的特点,对此进行比对实验,最终确定最合适的润滑油匹配方案。
1 建立虚拟机和设定的方案虚拟机的建立:气缸内气体燃烧产生的爆发力是柴油发动力的动力来源,这也是柴油发动机的工作原理。
图1可以看出来试验数值和计算数值的变化情况,从图中我们看出来相差的结果非常小,之所以出现这样的结果是因为:仿真试验在计算的时候对公式进行了非常精确的简化。
这样的结果比较也证明了模拟软件GT-CRANK进行仿真动力学研究的准确价值。
利用模拟软件GT-CRANK建立包含了活塞、气缸压力、曲轴、机体的模型,模拟参数有几何尺寸、质心位置和零部件的质量等,最终在软件内部建立了16V240ZJ型的虚拟机。
气缸动力是整个建模的基础数据,必须按照试验的需要和环境输入,目的是确保计算的准确性能,润滑油类型设定为CAE30。
CAE30润滑油的密度和粘合度等具体数字都在轴承模块中设立。
图1方案的设立:按照软件设定的方法,我们把润滑温度设定为参变量,然后我们在润滑油可以正常工作的温度范围内选取5个不一样的数值,分别是①70℃。
②75℃。
③80℃。
④85℃。
⑤90℃。
2 结果分析因为润滑油的温度不一样,所以曲轴、主轴颈轴承的承受能力和发挥的作用也不一样,通过模拟软件GT-CRANK可以计算和规划出润滑油因为温度的变化产生的工作变化情况。
2.1 轴承的负荷轴承负荷的变化是评判轴承和轴颈之间产生危险摩擦指数的主要参数。
发动机台架对比试验实施步骤
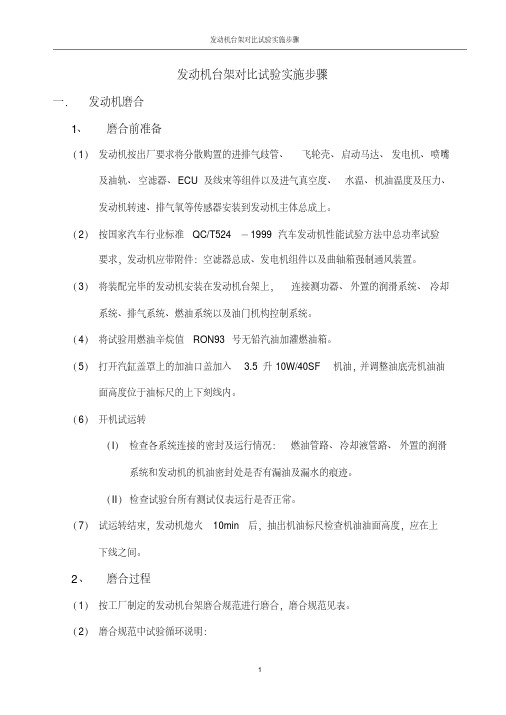
发动机台架对比试验实施步骤一.发动机磨合1、磨合前准备(1)发动机按出厂要求将分散购置的进排气歧管、飞轮壳、启动马达、发电机、喷嘴及油轨、空滤器、ECU及线束等组件以及进气真空度、水温、机油温度及压力、发动机转速、排气氧等传感器安装到发动机主体总成上。
(2)按国家汽车行业标准QC/T524-1999汽车发动机性能试验方法中总功率试验要求,发动机应带附件:空滤器总成、发电机组件以及曲轴箱强制通风装置。
(3)将装配完毕的发动机安装在发动机台架上,连接测功器、外置的润滑系统、冷却系统、排气系统、燃油系统以及油门机构控制系统。
(4)将试验用燃油辛烷值RON93号无铅汽油加灌燃油箱。
(5)打开汽缸盖罩上的加油口盖加入 3.5升10W/40SF机油,并调整油底壳机油油面高度位于油标尺的上下刻线内。
(6)开机试运转(I)检查各系统连接的密封及运行情况:燃油管路、冷却液管路、外置的润滑系统和发动机的机油密封处是否有漏油及漏水的痕迹。
(II)检查试验台所有测试仪表运行是否正常。
(7)试运转结束,发动机熄火10min后,抽出机油标尺检查机油油面高度,应在上下线之间。
2、磨合过程(1)按工厂制定的发动机台架磨合规范进行磨合,磨合规范见表。
(2)磨合规范中试验循环说明:1阶段2000rpm 运行时间30min(0.5h)负荷为02~7阶段2000~4500rpm 每阶段运行时间30min(6个阶段共3h)负荷为135×1/4=33.8N〃m8~14阶段2000~5000rpm 每阶段运行时间30min(7个阶段共3.5h)负荷为135×1/2=67.5N〃m15~21阶段2500~5500rpm每阶段运行时间30min(7个阶段共3.5h)负荷为135×3/4=101.3N〃m22~30阶段2500~5800rpm每阶段运行时间30min(9个阶段共4.5h)负荷为全负荷=135N〃m试验循环共分30个阶段,总磨合时间为15h。
某16缸柴油机润滑系统的模拟与优化

中 图分类 号 : T K 4 2 1 . 4 文 献标 志码 : A 文章 编号 : 1 6 7 3—6 3 9 7 ( 2 0 1 3 ) 0 2— 0 0 3 1— 0 5
Si mu l a t i o n a n d Opt i mi z a t i o n o f Lu br i c a t i o n S y s t e m i n a 1 6— — Cy l i n de r Di e s e l Eng i n e
us i n g t he Fl o wma s t e r s o f t wa r e a nd c a l c u l a t e d t h e p r e s s u r e a n d lo f w r a t e i n 5 k i n d s o f s p e e ds f r o m 3 2 5r /mi n t o l O 0 0r /mi n.Th e s i mu l a t i o n r e s u l t s a g r e e we l l wi t h t h e me a s u r e d d a t a a n d t h us p r o v i d e d a b a s i s or f o p t i mi z a t i o n d e s i g n o f t h e l u br ic a t i o n s y s t e m o f t h e d i e s e l e n g i n e . Th e o i l pr e s s u r e i n ma i n o i l g ll a e r y wa s i n di c a t e d n o t e n o u g h.Me a n whi l e,a s o l u t i o n c ha n g i n g a n e w pu mp wa s p r e s e n- t e d a n d t h e t e s t v a l i d a t i o n wa s a l s o c o nd u c t e d. F u r t h e r mo r e,t h e o i l lo f w a nd o i l p r e s s u r e d i s t r i b u- t i o n wa s o pt i mi z e d i n n e w p u mp. T he n e w p u mp c a n g i v e t h e a p pr o p ia r t e l u b ic r a t i o n . Ke y Wo r ds : Di e s e l En g i ne;Lu b r i c a t i o n S y s t e m ;S i mu l a t i o n Ca l c u l a t i o n
摩托车用柴油发动机动力性能的数值仿真与分析

摩托车用柴油发动机动力性能的数值仿真与分析摩托车作为一种受欢迎的交通工具,其性能对于用户体验至关重要。
柴油发动机作为摩托车的常见驱动装置,对于摩托车的动力性能起着决定性的作用。
本文将使用数值仿真的方法对摩托车用柴油发动机的动力性能进行分析与研究。
首先,我们需要明确柴油发动机的动力性能指标。
在摩托车中,常见的动力性能指标包括最大功率、最大扭矩、加速性能等。
最大功率是指发动机在单位时间内能够输出的最大功率,通常以千瓦(kW)为单位。
最大扭矩则是指发动机能够提供的最大转矩,通常以牛·米(Nm)为单位。
加速性能则是指摩托车在不同速度下的加速表现。
接下来,我们将使用数值仿真的方法来分析柴油发动机的动力性能。
数值仿真是一种基于计算机模型的仿真方法,通过运用数学模型和计算机算法对实际问题进行计算和模拟。
在摩托车用柴油发动机的数值仿真中,我们将使用计算流体力学(CFD)方法来模拟燃烧过程和气流运动,以及有限元方法来模拟发动机的结构应力和振动情况。
首先,我们需要构建柴油发动机的数值模型。
通过三维建模软件,可以将发动机的几何形状、气缸结构、进气和排气系统等进行建模,并转化为计算机可识别的网格。
然后,我们需要定义发动机的边界条件,如燃油喷射系统、进气道和排气道的工况参数等。
最后,我们将使用CFD软件对该数值模型进行求解,并获取发动机的燃烧情况、排气温度分布、气缸压力曲线等信息。
通过数值仿真,我们可以直观地了解柴油发动机的燃烧过程和燃料效率。
通过改变燃油喷射时机、喷油量和进气系统的参数,我们可以优化发动机的燃烧效率,提高最大功率和最大扭矩。
此外,我们还可以通过仿真模拟不同工况下的发动机运行状态,如低速行驶、高速行驶、长时间连续运行等,以评估发动机的可靠性和稳定性。
除了燃烧过程的仿真分析,我们还可以使用有限元分析方法对柴油发动机的结构强度和振动响应进行模拟。
通过对发动机的材料特性、结构形态和荷载条件等进行设定,可以计算发动机在工作过程中的应力和变形情况。