FDM快速成型支撑结构自动生成算法的研究
快速成型实验报告

快速成型实验报告——花瓶一.实验目的1.掌握快速成型的基本理论。
2.了解快速成型工艺方法种类及特点。
3.掌握快速成型设备操作方法。
二.快速成型技术原理快速原型 (Rapid Prototyping, RP)技术是20世纪80年代问世的一门新兴制造技术,自问世以来,得到了迅速的发展。
由于RP技术可以使数据模型转化为物理模型,并能有效地提高新产品的设计质量,缩短新产品开发周期,提高企业的市场竞争力,因而受到越来越多领域的关注,被一些学者誉为敏捷制造技术的使能技术之一。
RP技术的基本工作过程RP技术是由CAD模型直接驱动的快速制造复杂形状三维物理实体技术的总称。
其基本过程是:1、首先设计出所需零件的计算机三维模型,并按照通用的格式存储(STL文件);2、据工艺要求选择成形方向(Z方向),然后按照一定的规则将该模型离散为一系列有序的单元,通常将其按一定厚度进行离散 (习惯称为分层 ),把原来的三维CAD模型变成一系列的层片(CLI文件);3、再根据每个层片的轮廓信息,输入加工参数,自动生成数控代码;4、最后由成形机成形一系列层片并自动将它们联接起来,得到一个三维物理实体。
这样就将一个物理实体复杂的三维加工转变成一系列二维层片的加工,因此大大降低了加工难度。
由于不需要专用的刀具和夹具,使得成形过程的难度与待成形的物理实体的复杂程度无关,而且越复杂的零件越能体现此工艺的优势。
目前快速成形技术包括一切由CAD直接驱动的成形过程。
丝状成型材料和支撑材料由供丝机构送至各自对应的喷头,并在喷头中加热至熔融态,另外加热喷头在计算机的控制下按照相关截面轮廓的信息作X-Y平面运动,同时挤压并控制液体流量,使粘稠液体均匀地铺撤在断面层上。
这样成型材料和支撑材料就被选择性地涂彼在工作台上,快速冷却后形成截面轮廓,一层成型完成后,喷头上升一截面层的高度再进行下一层的涂覆如此循环,最终形成三维产品。
熔融挤压工艺原理三.实验内容自制一个三维模型,然后通过快速成型实验将三维模型制作实物来。
浅谈FDM-3D打印机的支撑及其发展

浅谈FDM-3D打印机的支撑及其发展作者:张贝贝来源:《科学与财富》2020年第18期摘要:FDM-3D打印在成型具有悬空结构的模型时必须添加辅助的支撑结构。
为保证模型的质量,减少打印时间,支撑的位置和形状是当前研究的重点对象。
关键词:FDM;支撑结构;优化研究;引言随着科学技术的发展,越来越多的新兴技术应用到社会中,3D打印技术在其中异军突起。
3D打印属于增材制造的一种,区别于以往的减材制造,舍去了传统的刀具、夹具和昂贵的机床设备,大量减少了加工过程的工艺和工序,在 3D打印设备上能够快速、准确地制造出传统加工方法难以加工的具有复杂结构的零件,能够极大地缩短制造周期和加工工序。
但在FDM-3D打印在成型具有大跨度结构、外伸结构等悬空特征的模型时,零件容易出现变形、翘曲、坍塌等一系列问题,导致最终打印成形失败,为了解决这些问题,需要添加支撑结构辅助制造。
1 FDM打印中常用支撑的结构类型和生成方式1.1FDM打印技术的支撑主要有以下几类:a)基础支撑:主要为模型加工过程提供基础的支撑并用于校正工作平台的局部不平整,方便模型打印完成后从平台上取下,使模型底部表面平滑、整齐,并且基础支撑能够缓冲平台底板与打印模型的温度差异,在打印“薄件”时能有效的减少翘曲现象。
b)整体支撑:通过完全包围的方式成型整个模型,不用考虑模型本身的复杂程度,而且整个生成计算过程相对简单,在3D打印发展的初期使用频率较高。
整体支撑能保证模型的成型质量,但会给后期处理带来很大的麻烦,同时也会造成打印材料的大量浪费和打印成型时间的增加。
c)局部支撑:是在整体支撑基础上的一种改进措施,根据模型的结构和放置位置方向,在需要的表面添加支撑。
局部支撑的添加符合45°角原则[1],即由于受重力作用的影响,当一个物体某个面与垂直线的角度大于45°且悬空时,则有可能发生坠落。
打印过程中,材料需要经过“硬-软-硬”的相变过程,在材料没有凝固之前,因自身重力影响且没有其它支撑而下坠,导致打印模型失败。
FDM快速成型加工工艺问题研究

FDM快速成型加工工艺问题研究1. 引言1.1 研究背景FDM(快速成型加工)技术是一种广泛应用于快速原型制作和小批量生产的先进制造技术。
随着3D打印技术的快速发展,FDM技术也逐渐受到广泛关注和应用。
尽管FDM技术具有诸多优点,如成本低、制作速度快、制作过程简单等,但也存在一些问题和挑战,例如造成制品表面质量不佳、制品尺寸精度不高等。
为了进一步提高FDM技术的成型质量和效率,需要深入研究FDM技术的原理、存在的问题以及优化研究。
FDM材料的选择与性能对成型质量和制品性能也具有重要影响,需要进行深入探讨和分析。
本文旨在对FDM技术进行深入研究,探讨其存在的问题及解决方案,优化工艺参数以提高成型质量,研究不同材料对制品性能的影响,最终为FDM技术的进一步应用提供理论指导和实践经验。
1.2 研究目的FDM快速成型加工技术是一种广泛应用于原型制作和小批量生产的快速成型技术,但在实际应用中仍然存在一些问题和难点。
本文旨在通过对FDM技术的原理、存在的问题、工艺参数优化研究、材料选择与性能研究以及工艺与制品质量关系的分析,深入探讨FDM快速成型加工工艺中存在的问题,并寻求解决方案。
具体研究目的如下:1. 分析FDM技术的原理,深入了解该技术的工作原理和特点,为后续对问题的解决提供理论基础。
2. 探讨FDM技术中存在的问题,包括外形精度、强度、表面质量等方面的不足,寻找解决方案。
3. 研究FDM工艺参数的优化,提高零件的成形质量和性能。
4. 对不同材料的选择与性能进行研究,提高零件的耐用性和稳定性。
5. 分析FDM工艺与制品质量之间的关系,为进一步改进工艺提供依据。
通过以上研究目的的实现,我们希望能够为FDM快速成型加工技术的发展和应用提供有益的参考和指导。
2. 正文2.1 FDM技术原理分析不足的提示、空行等。
感谢理解。
FDM(Fused Deposition Modeling)即熔融沉积建模技术,是一种常见的快速成型加工技术。
fdm增材制造的成型原理及其优点
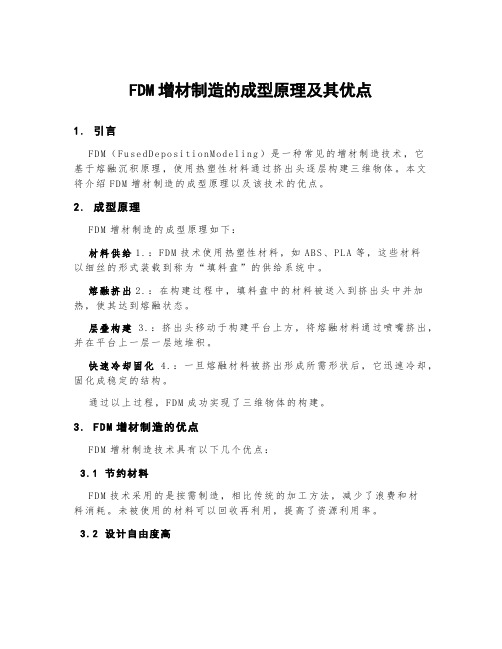
FDM增材制造的成型原理及其优点1.引言F D M(Fu se dD ep os it i on Mo de li ng)是一种常见的增材制造技术,它基于熔融沉积原理,使用热塑性材料通过挤出头逐层构建三维物体。
本文将介绍F DM增材制造的成型原理以及该技术的优点。
2.成型原理F D M增材制造的成型原理如下:材料供给1.:FD M技术使用热塑性材料,如AB S、PL A等,这些材料以细丝的形式装载到称为“填料盘”的供给系统中。
熔融挤出2.:在构建过程中,填料盘中的材料被送入到挤出头中并加热,使其达到熔融状态。
层叠构建 3.:挤出头移动于构建平台上方,将熔融材料通过喷嘴挤出,并在平台上一层一层地堆积。
快速冷却固化 4.:一旦熔融材料被挤出形成所需形状后,它迅速冷却,固化成稳定的结构。
通过以上过程,F DM成功实现了三维物体的构建。
3. FD M增材制造的优点F D M增材制造技术具有以下几个优点:3.1节约材料F D M技术采用的是按需制造,相比传统的加工方法,减少了浪费和材料消耗。
未被使用的材料可以回收再利用,提高了资源利用率。
3.2设计自由度高F D M增材制造技术可以打破传统制造工艺的限制,实现更复杂、更精细的三维结构。
设计师可以根据需求进行个性化设计,并能够快速验证原型,提高产品开发效率。
3.3快速生产F D M增材制造技术通过自动化的层叠构建过程,大大缩短了产品制造的时间。
相比传统的制造方法,F DM可以在几小时内完成一个产品,提高了生产效率。
3.4降低成本F D M增材制造技术的快速生产和节约材料的特点使其成本更低。
传统的生产过程中,频繁的工装设计和制造、中间环节的加工和运输费用都会增加成本,而FD M技术可以将这些成本降至最低。
3.5制造复杂结构F D M增材制造技术可以轻松构建复杂的结构,如薄壁结构、中空结构等。
这在一些领域,如航空航天、医疗器械等,具有重要应用价值。
4.结论F D M增材制造技术基于熔融沉积原理,通过挤出头逐层构建三维物体。
FDM快速成型加工工艺问题研究
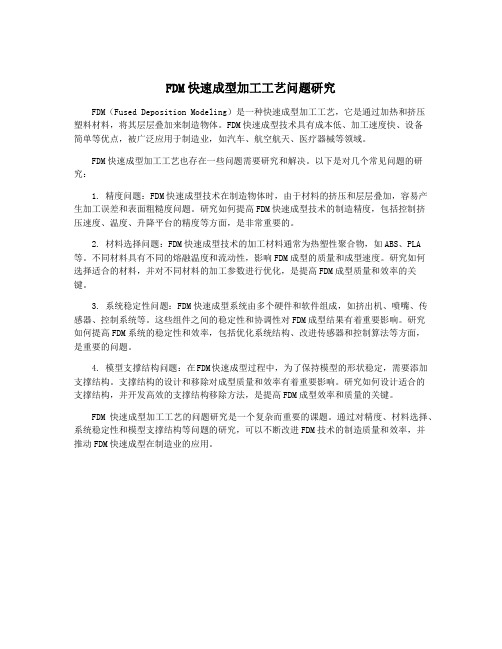
FDM快速成型加工工艺问题研究FDM(Fused Deposition Modeling)是一种快速成型加工工艺,它是通过加热和挤压塑料材料,将其层层叠加来制造物体。
FDM快速成型技术具有成本低、加工速度快、设备简单等优点,被广泛应用于制造业,如汽车、航空航天、医疗器械等领域。
FDM快速成型加工工艺也存在一些问题需要研究和解决。
以下是对几个常见问题的研究:1. 精度问题:FDM快速成型技术在制造物体时,由于材料的挤压和层层叠加,容易产生加工误差和表面粗糙度问题。
研究如何提高FDM快速成型技术的制造精度,包括控制挤压速度、温度、升降平台的精度等方面,是非常重要的。
2. 材料选择问题:FDM快速成型技术的加工材料通常为热塑性聚合物,如ABS、PLA 等。
不同材料具有不同的熔融温度和流动性,影响FDM成型的质量和成型速度。
研究如何选择适合的材料,并对不同材料的加工参数进行优化,是提高FDM成型质量和效率的关键。
3. 系统稳定性问题:FDM快速成型系统由多个硬件和软件组成,如挤出机、喷嘴、传感器、控制系统等。
这些组件之间的稳定性和协调性对FDM成型结果有着重要影响。
研究如何提高FDM系统的稳定性和效率,包括优化系统结构、改进传感器和控制算法等方面,是重要的问题。
4. 模型支撑结构问题:在FDM快速成型过程中,为了保持模型的形状稳定,需要添加支撑结构。
支撑结构的设计和移除对成型质量和效率有着重要影响。
研究如何设计适合的支撑结构,并开发高效的支撑结构移除方法,是提高FDM成型效率和质量的关键。
FDM快速成型加工工艺的问题研究是一个复杂而重要的课题。
通过对精度、材料选择、系统稳定性和模型支撑结构等问题的研究,可以不断改进FDM技术的制造质量和效率,并推动FDM快速成型在制造业的应用。
FDM 3D打印支撑结构及易于剥离方法的研究

FDM 3D打印支撑结构及易于剥离方法的研究作者:卢帅晁艳普来源:《科技创新与应用》2019年第09期摘; 要:熔融沉积成型3D打印在成型具有大跨度结构、外伸结构等悬空特征的模型时有添加辅助支撑结构的必要性。
文章针对FDM成型技术中支撑结构进行了研究,提出了熔融沉积成型3D打印支撑结构与实体模型易于剥离的方法,科研实践表明该方法对支撑结构的可去除性有较好的改善效果。
关键词:FDM;3D打印;支撑结构;易于剥离中图分类号:TH-3; ; ; ; ;文献标志码:A; ; ; ; ;文章编号:2095-2945(2019)09-0122-02Abstract: FDM 3D printing is necessary to add auxiliary support structure when forming a model with large span structure and overhanging structure. Based on FDM molding technology of the supporting structure are studied, put forward the fused deposition molding 3 d printing support structure and entity model easy to stripping method, scientific research and practice show that this method can remove sex of support structure has good improvement effect.Keywords: Fused Deposition Modeling; 3D Printing; support structure; easy stripping引言熔融沉积式(FDM)3D打印原理是打印机接收到由切片软件处理的3D数据,将材料熔化沉积,是一种分层制造、逐层累积的过程。
FDM快速成型加工工艺问题研究

FDM快速成型加工工艺问题研究一、引言FDM(Fused Deposition Modeling),即熔融沉积成型技术,是一种快速成型技术,其工艺流程主要是利用专用的3D打印机,通过计算机将设计好的三维模型切割成一层一层的二维截面,然后逐层堆叠打印材料,最终形成三维实体。
FDM技术在快速成型领域具有广泛的应用,但在实际生产过程中还存在一些问题,本文将对FDM快速成型加工工艺中的问题进行研究,以期能够提高FDM技术的应用效率和成型质量。
二、FDM快速成型加工工艺存在的问题1. 打印精度不高FDM技术在打印过程中容易受到热胀冷缩的影响,导致成品尺寸与设计尺寸存在差异,尤其在大型件的打印过程中更为明显,影响了产品的精度。
材料在堆叠成型中容易出现变形和翘曲现象,进一步影响了打印精度。
2. 表面质量不佳FDM技术在堆叠打印过程中,由于材料温度的影响和层与层之间的连接问题,导致成品表面存在明显的层状纹理和毛刺,降低了产品的外观质量。
3. 加工速度慢FDM技术在实际应用中,由于打印速度受到电机性能和材料熔化速度的限制,导致加工速度较慢,尤其在大型件的打印过程中更为明显,影响了生产效率。
4. 材料选择有限FDM技术在材料选择上存在一定的局限性,一方面受到打印机型号的限制,另一方面受到材料熔化温度的影响,导致无法满足一些特殊性能要求。
5. 设备和成本限制FDM技术的设备价格昂贵,同时耗材成本也相对较高,加之设备维护费用和操作成本,限制了FDM技术的大规模应用,影响了产业的发展。
三、针对FDM快速成型加工工艺问题的解决方法1. 提高打印精度针对FDM技术打印精度不高的问题,可以通过优化打印参数、提高材料的熔化温度和改善材料层间粘结等手段进行改进。
还可以引入先进的自动补偿技术和实时监测技术,提高成品的精度。
2. 改善表面质量针对FDM技术表面质量不佳的问题,可以通过优化打印路径、调整层厚和选择合适的材料等手段进行改进。
FDM工艺中的支撑自动生成技术研究

I D l I 型C 模H 域和支撑H l A 类型 l 零件的三维 A 模 H T I 型上手动添加支撑 I I L I 分层 l C D S 制造 文件
图 1 支撑的手动生成过程
2 基 于扫 描线 的支 撑 自动 生成 技 术 求支撑总 的原则 是 :当前层的支撑要撑住上一 层 零件本体 区域 和支撑 区域 中没有被 当前层 的零件本体 区域支撑住 的部分。其 原理图如 图4所示 。
第i 2 + 层
支撑的手动生成 方法 有 如下缺 点 : ( ) 要 求用 1 户对 成型工艺很熟悉 ,对设计人 员和设备操作人员 的
l 1 】 £f l 【 l I 州, +l J
算 ,处理难度 非常大 。 12 2 基于层片信息 的支 撑 自动生成技术 ..
基 于层片信息 的支撑 自动生成技术 的工艺过程 如
图 3所 示 。
0— — — 》 一 一 一 一 一 一 C — — — — — — —— 一 — 。 一 一 一 o —— —— — 一 一… …
() 1
{H崖 囊 H 黧 霪H霖 H 蠢 斋
图 2 基 于 S L文 件 的 支 撑 自动 生 成 技 术 T
从式 ( )可看 出 :求 支撑 的过程 中涉及 到 了直 1 线段 的求并 与求 差 的过 程 。而 线段 是用 点来 描述 的 , 两点确定一条线 段 ,则 上述的布尔运算 可用 图 5 表 来
21 0 2年 2月
机床与液压
MAC NE HI TOOL & HYDRAUL C IS
F b.2 2 e 01 Vo. 0 NO 4 14 .
- 1、下载文档前请自行甄别文档内容的完整性,平台不提供额外的编辑、内容补充、找答案等附加服务。
- 2、"仅部分预览"的文档,不可在线预览部分如存在完整性等问题,可反馈申请退款(可完整预览的文档不适用该条件!)。
- 3、如文档侵犯您的权益,请联系客服反馈,我们会尽快为您处理(人工客服工作时间:9:00-18:30)。
FDM快速成型支撑结构自动生成算法的研究
摘要: FDM系统中零件原形的加工是靠热喷头挤出熔丝逐层堆积而成的。
因此,支撑结构的添加对零件原形的制作起着至关重要的作用。
针对支撑结构的需求,采用了一种新的支撑自动生成算法。
该算法基于STL模型首先需提取待支撑区域,然后添加相应的支撑结构,最后确定待支撑区域的起点和终点。
实际应用表明,生成支撑的效果良好。
关键词: FDM系统;支撑结构;自动生成算法;STL模型
0 引言
快速成型技术(RP)是20世纪80年代后期发展起来的,由三维CAD模型直接驱动、快速生成任意复杂形状三维实体的一种新型制造技术,它高度集成了自动控制、CAD/CAM技术、数字控制技术、计算机、激光技术、新型材料科学等学科最新成果[1]。
目前,FDM快速成型设备因具有小巧、价格低廉、应用材料范围广泛、可直接制成工业产品等优点,在企业设计之中有着广泛的应用[2]。
FDM系统在加工零件原形时,当前层都是在上一层上堆积而成的,前一层对当前层起到定位和支撑的作用,随着高度的增加,层片轮廓的面积和形状都会发生变化,当上层截面大于下层截面时,使截面部分发生塌陷或变形,影响零件的成型精度,因此,支撑对零件原形的制作起着至关重要的作用[3]。
支撑添加技术有两种:一种是在绘制三维CAD模型时手动添加支撑,另外一种是由软件自动生成支撑。
支撑的手动生成技术要求用户对成型工艺很熟悉,支撑添加的质量难以保证。
所以支撑的自动生成方法是人们研究的重点,支撑自动生成算法主要有两种,分别基于多边形布尔运算和STL模型。
前者算法较复杂,可能生成多余的支撑;后者识别局部支撑,节省支撑材料,能准确添加支撑结构,是支撑自动生成技术的重点研究方向[4]。
基于以上这些情况,本文采用了基于STL模型支撑自动生成技术,待支撑面使用了间隔型薄壁支撑;由于FDN工艺中要求加工路径尽量连续和支撑稳定性,因此本文采用中心线法来生成悬吊边和悬吊点的支撑体;用投影法和干涉法确定支撑终点和起点,减少了材料使用,节省了加工时间,提高了快速成形的效率。
1 待支撑区域的识别
对待支撑区域的零件CAD模型进行分析,发现零件有3种特征时需要添加相应的支撑,它们分别是待支撑面、悬吊边、悬吊点。
1.1 待支撑面的识别
遍历STL模型中所有的三角面片,对三角面片的法向量与Z轴正方向的夹角进行判断,,如果这个夹角θ大于一定的阈值,则该三角面片需要添加支撑。
这些三角面片是独立的,面积小且数量多,不宜单独支撑,需要对这些三角面片进行整合,连接成待支撑面。
三角面片的连接方式与下面悬吊边的连接方式类似,采用种子三角面片[5]。
1.2 悬吊边的识别
,实体中存在的两个倾斜面的共边AB为悬吊边。
若判断某条边为悬吊边,首先悬吊边所在两三角形面片都是非待支撑三角面片;其次悬吊边两端点的Z坐标必须小于该三角面片的另一个点的Z坐标;最后悬吊边的两三角形面片的法向矢量之和,必须指向Z轴的负方向。
悬吊边是由零散的单个三角面片悬吊边连接成的长的宏观悬吊边。
边的连接不同于面片的合并,是必须按照点的先后顺序来连接。
首先找到悬吊边中两个端点的其中一个端点,这个端点与其他的边不共点;然后通过端点所在线的另一点,找出与其共点的边,按照这种方法就可以得到所需要的悬吊边[6]。
算法流程图3所示。
1.3 悬吊点的识别
悬吊点是指零件模型上出现的由一些面构成的孤立点,,该点的Z坐标是构成它的三角面片中最小的。
但某一顶点被判别为悬吊点,仅此一个条件是远远不够的,首先构成悬吊点的三角面片都是非悬吊三角面片;其次也是最重要的,包含悬吊点的三角形面片法矢之和不能朝上。
2 支撑结构的生成
2.1 待支撑区域支撑结构的设计
2.1.1 待支撑面支撑的添加
本文对待支撑面结构的设计采用的是间隔型薄壁支撑[7],节省材料的同时,又易于去除,支撑不容易发生坍塌,保证了它的稳定性。
该算法步骤为:首先对待支撑面在XOY平面内进行投影;然后求出这个投影多边形的最小包络矩形,在矩形内设定垂直分层线,平行于X轴或Y轴,这些线之间的距离是相同的[8],沿支撑投影的轮廓边界顺序与垂直分层线连接,形成某个分层面中的支撑,,将这些分层面中的支撑堆叠而成间隔型薄壁支撑。
当这些薄壁支撑达到一定高度时,容易发生塌陷,所以间隔型薄壁支撑应该交错添加。
2.1.2 悬吊边支撑的添加
悬吊边一般添加单臂板支撑,但是如果悬吊边的高度很高,单臂板往往不能够保证支撑的稳定性,于是就采用中心线法来生成悬吊边的支撑体,即以悬吊边为中心线生成包含中心线的矩形或多边形,,d 为支撑宽度。
生成方法是:将悬吊线向垂直方向的上方和下方偏移,再将偏移后得到的多边形连接起来,再向工作平面投影来建立支撑体[6]。
2.1.3 悬吊点支撑的添加
悬吊点通常采用十字形支撑来处理,当悬吊点的高度大于某个临界值时,十字支撑就不能起到很好的支撑作用,此时需要对其作一些变化,。
生成方法是:以悬吊点为十字的中心,然后将十字投影到工作台上,根据参数d来构建上图所示的多边形,其中多边形的中心线与 X 轴和 Y 轴平行。
2.2 支撑起点和终点的确定
当一个支撑的二维位置确定后,还要确定支撑的最高点和最低点,即终点和起点。
终点由要待加支撑区域在该位置的高度确定,先将待支撑区域在XOY平面内投影,在二维投影中,找出已经确定的第一个点的坐标(x1,y1),然后在该待加支撑面中找出包含该点坐标位置的那个三角面片,设该三角面片的法向量为n(nx,ny,nz),其中一个顶点的坐标为(x′,y′,z′),利用该三角面片的法向量和一顶点的坐标得到该三角面片所在平面的方程,即:nx(x-x′)+ny(y-y′)+nz(z-z′)=0,再把(x1,y1)坐标带入上述方程中就可以得到一个z1坐标;然后再找到第二点坐标(x2,y2),与第一个点的求法相同,将它带入上述方程,可得到一个z2坐标。
最后比较z1和z2的大小,将其中大的Z坐标作为支撑的终点[9-10]。
本文采用干涉法来确定支撑的起点,干涉法是对待支撑区域在XOY平面内投影与STL模型中上表面进行的干涉,这里的上表面指的是法矢朝上(即沿 Z 轴正方向)的面以及向上倾斜的面。
判断投影区域是否会与上表面发生干涉,首先找出低于待支撑区域边界中最低点的上表面,将它们投影在XOY平面内,若待支撑区域的投影∩上表面的投影=φ,则说明待支撑区域与上表面不发生干涉,即支撑起点从工作台开始;若待支撑区域的投影∩上表面的投影
≠φ,则说明待支撑区域和上表面发生了干涉。
发生干涉的情况又可分为两种,一种待支撑区域的投影全部落在上表面上,一种待支撑区域的投影与上表面投影有部分相交[6]。
当待支撑区域的投影落在上表面上时,支撑的起点从该上表面开始,确定方法与终点的确定类似,取比较小的Z值作为支撑的起点。
3 实验
本文利用VC++6.0对支撑的自动生成进行了开发[11],为了验证支撑结构的合理性和可靠性,把STL模型输出到3D打印机上进行加工,。
4 结论
本文通过对基于STL模型自动生成算法的研究,对待支撑面采用了薄壁型结构,生成的支撑不仅稳定,而且节省了材料;确定支撑的起点和终点,使得快速成形支撑结构简单,同时提高了效率。
实验的支撑添加效果表明,支撑填充合理,没有待支撑特征遗漏,该算法保证了零件的顺利成型。