丁苯橡胶的塑炼和混炼
橡套软电缆生产工序:开炼和混炼工艺文件

开炼机橡胶塑炼:
本卡片适用于橡皮绝缘电缆的素炼工序。
2工艺技术要点:
2.1塑炼胶应用国标1#,绝缘胶种应采用内芯胶,护套胶种应采用外皮胶。
2.2塑炼用丁苯胶应采用含有25%以上苯乙烯的松香丁苯或充油丁苯。
2.3天然胶塑炼前应用水将外皮冲洗干净,并在30C —60C 的环境中温胶24~36小时。
2.4天然橡胶和丁苯橡胶掺合应均匀,塑炼胶应表面光滑,贴辊面应有亮皱纹。
2.5塑炼过程中的辊温、辊距应符合工艺卡规定。
密炼机橡胶塑炼和密炼:
XXX 公司
橡套软电缆橡胶开炼和混炼工序
工艺卡片
开炼机橡胶混炼:
XXX 公司
橡套软电缆橡胶开炼和混炼工序
工艺卡片
XXX公司橡套软电缆橡胶开炼和混炼工序文件编号| Q/JY.GK03-2020
工艺卡片共3页n—第页。
塑炼与混炼
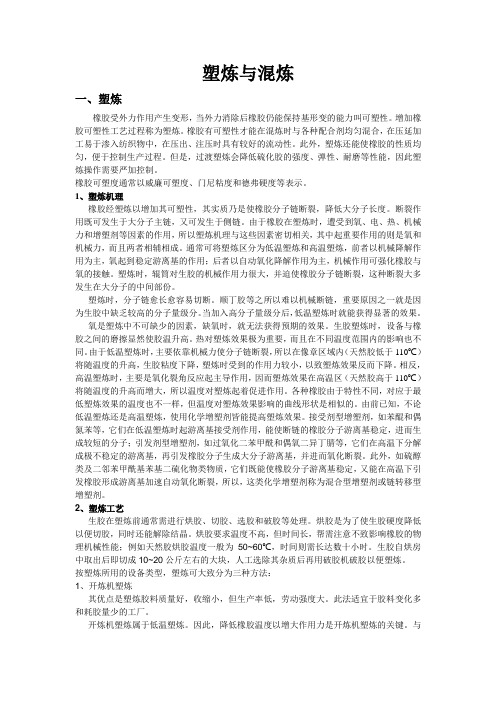
塑炼与混炼一、塑炼橡胶受外力作用产生变形,当外力消除后橡胶仍能保持基形变的能力叫可塑性。
增加橡胶可塑性工艺过程称为塑炼。
橡胶有可塑性才能在混炼时与各种配合剂均匀混合,在压延加工易于渗入纺织物中,在压出、注压时具有较好的流动性。
此外,塑炼还能使橡胶的性质均匀,便于控制生产过程。
但是,过渡塑炼会降低硫化胶的强度、弹性、耐磨等性能,因此塑炼操作需要严加控制。
橡胶可塑度通常以威廉可塑度、门尼粘度和德弗硬度等表示。
1、塑炼机理橡胶经塑炼以增加其可塑性,其实质乃是使橡胶分子链断裂,降低大分子长度。
断裂作用既可发生于大分子主链,又可发生于侧链。
由于橡胶在塑炼时,遭受到氧、电、热、机械力和增塑剂等因素的作用,所以塑炼机理与这些因素密切相关,其中起重要作用的则是氧和机械力,而且两者相辅相成。
通常可将塑炼区分为低温塑炼和高温塑炼,前者以机械降解作用为主,氧起到稳定游离基的作用;后者以自动氧化降解作用为主,机械作用可强化橡胶与氧的接触。
塑炼时,辊筒对生胶的机械作用力很大,并迫使橡胶分子链断裂,这种断裂大多发生在大分子的中间部份。
塑炼时,分子链愈长愈容易切断。
顺丁胶等之所以难以机械断链,重要原因之一就是因为生胶中缺乏较高的分子量级分。
当加入高分子量级分后,低温塑炼时就能获得显著的效果。
氧是塑炼中不可缺少的因素,缺氧时,就无法获得预期的效果。
生胶塑炼时,设备与橡胶之间的磨擦显然使胶温升高。
热对塑炼效果极为重要,而且在不同温度范围内的影响也不同。
由于低温塑炼时,主要依靠机械力使分子链断裂,所以在像章区域内(天然胶低于110℃)将随温度的升高,生胶粘度下降,塑炼时受到的作用力较小,以致塑炼效果反而下降。
相反,高温塑炼时,主要是氧化裂角反应起主导作用,因而塑炼效果在高温区(天然胶高于110℃)将随温度的升高而增大,所以温度对塑炼起着促进作用。
各种橡胶由于特性不同,对应于最低塑炼效果的温度也不一样,但温度对塑炼效果影响的曲线形状是相似的。
丁苯橡胶加工方式

丁苯橡胶加工方式丁苯橡胶是一种合成橡胶,由苯乙烯和丁二烯经过共聚反应制得。
它具有优异的物理性能和化学稳定性,被广泛应用于橡胶制品的加工中。
丁苯橡胶的加工方式多种多样,下面将就其中几种常见的加工方式进行介绍。
1. 混炼加工:混炼是将丁苯橡胶与其他添加剂进行混合的过程。
在混炼加工中,首先将丁苯橡胶与填充剂(如炭黑、白炭黑等)以及增塑剂、防老剂等添加剂一同放入混炼机中进行搅拌和加热。
通过加热和搅拌,丁苯橡胶与添加剂充分混合,形成均匀的混炼胶料。
混炼胶料可以直接用于模压、挤出等加工方式。
2. 挤出加工:挤出是将丁苯橡胶通过挤出机进行挤出成型的过程。
在挤出加工中,首先将混炼好的丁苯橡胶胶料放入挤出机的料斗中,通过加热和压力,将橡胶胶料从模头中挤出形成所需的截面形状。
挤出加工可以用于制造各种橡胶制品,如密封条、管道等。
3. 模压加工:模压是将丁苯橡胶通过模具进行压制成型的过程。
在模压加工中,首先将混炼好的丁苯橡胶胶料放入预热的模具中,然后通过加热和压力,将橡胶胶料压制成模具所需的形状。
模压加工可以用于制造各种橡胶制品,如密封件、垫片等。
4. 压延加工:压延是将丁苯橡胶通过辊筒进行压制成型的过程。
在压延加工中,首先将混炼好的丁苯橡胶胶料放入预热的压延机中,通过辊筒的旋转和压力,将橡胶胶料压延成所需的厚度。
压延加工可以用于制造橡胶板、橡胶地垫等。
5. 注塑加工:注塑是将丁苯橡胶通过注塑机进行注塑成型的过程。
在注塑加工中,首先将混炼好的丁苯橡胶胶料放入注塑机的料斗中,通过加热和压力,将橡胶胶料注入模具中,形成所需的形状。
注塑加工可以用于制造各种橡胶制品,如按钮、手柄等。
以上是丁苯橡胶的几种常见加工方式,每种加工方式都有其适用的场合和优势。
在实际生产中,根据不同的产品需求和工艺要求,选择合适的加工方式,能够更好地发挥丁苯橡胶的性能,制造出高质量的橡胶制品。
部分常见橡胶的塑炼特性
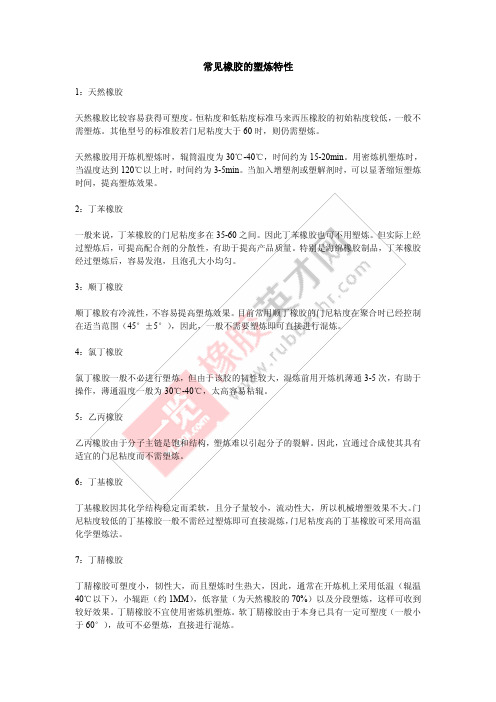
常见橡胶的塑炼特性1:天然橡胶天然橡胶比较容易获得可塑度。
恒粘度和低粘度标准马来西压橡胶的初始粘度较低,一般不需塑炼。
其他型号的标准胶若门尼粘度大于60时,则仍需塑炼。
天然橡胶用开炼机塑炼时,辊筒温度为30℃-40℃,时间约为15-20min。
用密炼机塑炼时,当温度达到120℃以上时,时间约为3-5min。
当加入增塑剂或塑解剂时,可以显著缩短塑炼时间,提高塑炼效果。
2:丁苯橡胶一般来说,丁苯橡胶的门尼粘度多在35-60之间。
因此丁苯橡胶也可不用塑炼。
但实际上经过塑炼后,可提高配合剂的分散性,有助于提高产品质量。
特别是海绵橡胶制品,丁苯橡胶经过塑炼后,容易发泡,且泡孔大小均匀。
3:顺丁橡胶顺丁橡胶有冷流性,不容易提高塑炼效果。
目前常用顺丁橡胶的门尼粘度在聚合时已经控制在适当范围(45°±5°),因此,一般不需要塑炼即可直接进行混炼。
4:氯丁橡胶氯丁橡胶一般不必进行塑炼,但由于该胶的韧性较大,混炼前用开炼机薄通3-5次,有助于操作,薄通温度一般为30℃-40℃,太高容易粘辊。
5:乙丙橡胶乙丙橡胶由于分子主链是饱和结构,塑炼难以引起分子的裂解。
因此,宜通过合成使其具有适宜的门尼粘度而不需塑炼。
6:丁基橡胶丁基橡胶因其化学结构稳定而柔软,且分子量较小,流动性大,所以机械增塑效果不大。
门尼粘度较低的丁基橡胶一般不需经过塑炼即可直接混炼,门尼粘度高的丁基橡胶可采用高温化学塑炼法。
7:丁腈橡胶丁腈橡胶可塑度小,韧性大,而且塑炼时生热大,因此,通常在开炼机上采用低温(辊温40℃以下),小辊距(约1MM),低容量(为天然橡胶的70%)以及分段塑炼,这样可收到较好效果。
丁腈橡胶不宜使用密炼机塑炼。
软丁腈橡胶由于本身已具有一定可塑度(一般小于60°),故可不必塑炼,直接进行混炼。
丁苯橡胶装置生产工艺流程解析

03 .
凝聚和分离
Coagulation and separation
凝聚过程
丁苯橡胶装置
Styrene butadiene rubber device
生产工艺流程
Production process flow
凝聚过程
Coagulation process
凝聚过程是物质从混乱到有 序的转化过程,也是自然界
聚合反应条件控制
丁苯橡胶装置生产工艺流程解析 聚合反应条件控制是丁苯橡胶装置生产的关键环节。以下是聚合反应条件控制的几个主要方面: 1. 聚合反应温度控制 聚合反应温度是影响橡胶分子量及分子量分布的重要因素。温度过低会导致反应速率缓慢,影响生产效率;温度 过高则可能导致凝胶化,严重影响产品质量。因此,需要精确控制聚合反应温度,以确保生产效率和产品质量的 稳定。 2. 聚合反应压力控制 聚合反应压力也是影响橡胶分子量及分子量分布的重要因素。 压力过低可能导致凝胶化,影响产品质量;压力过高则可能导致设备损坏,增加能耗。因此,需要精确控制聚合 反应压力,以确保生产效率和产品质量的稳定。 3. 聚合反应时间控制 聚合反应时间也是影响橡胶分子量及分子量分布的重要因素。 时间过短可能导致反应不充分,影响产品质量;时间过长则可能导致凝胶化,影响生产效率。因此,需要精确控 制聚合反应时间,以确保产品质量的稳定和生产效率的提高。 4. 聚合反应物料配比控制 聚合反应物料配比也是影响橡胶分子量及分子量分布的重要因素。 物料配比不合理可能导致凝胶化,影响产品质量;物料配比过高则可能导致生产效率降低,增加能耗。因此,需 要精确控制聚合反应物料配比,以确保产品质量的稳定和生产效率的提高。
04 .
产品后处理
Product post-processing
天然橡胶和丁苯橡胶共混工艺流程

天然橡胶和丁苯橡胶共混工艺流程天然橡胶和丁苯橡胶是两种常见的橡胶材料,它们分别具有不同的特性和用途。
然而,通过将它们进行共混,可以获得既具有天然橡胶的弹性和耐磨性,又具有丁苯橡胶的耐候性和耐油性的优质橡胶材料。
本文将介绍天然橡胶和丁苯橡胶共混的工艺流程。
首先,天然橡胶和丁苯橡胶的共混工艺涉及到橡胶的预处理和混炼两个主要过程。
首先是橡胶的预处理,包括橡胶的清洗、粉碎和筛分。
清洗是将橡胶中的杂质去除,以确保橡胶的质量。
粉碎是将橡胶块破碎成小颗粒,便于混炼过程中的加工。
筛分则是对橡胶颗粒进行分级,以获得一定大小的颗粒用于混炼。
接下来是橡胶的混炼过程。
混炼通过将天然橡胶和丁苯橡胶与一定比例的填料、硫化剂和促进剂混合,并在高温下进行加热和搅拌,使橡胶分子链间相互交联,形成均匀的混合物。
填料的选择可以根据需求来决定,比如碳黑可以增加橡胶的耐磨性和强度,而硅酸盐可以提高橡胶的耐热性和电绝缘性。
硫化剂和促进剂则用于在混炼过程中引发橡胶的硫化反应,使橡胶具有弹性和耐用性。
在混炼过程中,需要控制好温度、时间和搅拌参数,以确保橡胶混合物的均匀性和品质。
高温会促使橡胶分子链的运动和交联反应,但过高的温度会导致橡胶热分解和变质。
搅拌的目的是将所有成分充分混合,形成均匀的橡胶胶料。
混炼过程需要进行多次循环,以获得最佳的混合效果。
混炼完成后,橡胶混合物需要进行硫化处理。
硫化是将橡胶混合物加热到一定温度下,使硫化剂引发橡胶分子链间的交联反应,形成三维的网络结构。
硫化反应使橡胶具有优良的弹性和耐磨性,提高其使用寿命和适用范围。
硫化过程需要控制好温度和时间,以确保橡胶硫化反应的充分进行。
最后,硫化完成后,需要对橡胶制品进行去脱模和检验。
去脱模是将橡胶制品从模具中取出,并对其进行修整和清洗。
检验包括外观检查和物理性能测试,以确保橡胶制品的质量和符合规定的标准。
总结起来,天然橡胶和丁苯橡胶共混工艺流程包括橡胶的预处理、混炼、硫化处理和检验等多个环节。
橡胶试验胶料配料、混炼操作规程
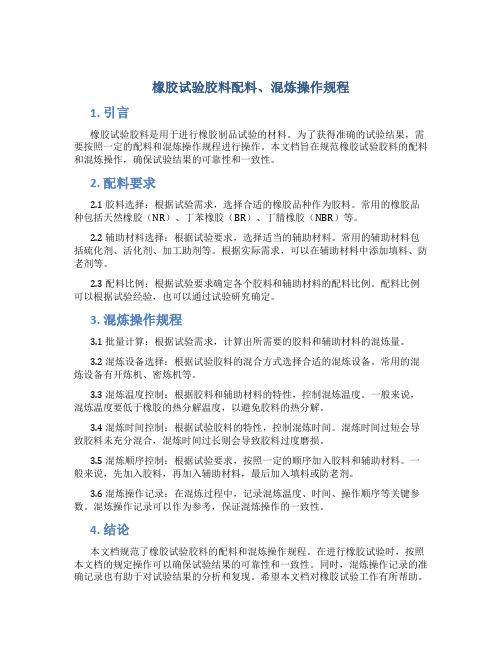
橡胶试验胶料配料、混炼操作规程1. 引言橡胶试验胶料是用于进行橡胶制品试验的材料。
为了获得准确的试验结果,需要按照一定的配料和混炼操作规程进行操作。
本文档旨在规范橡胶试验胶料的配料和混炼操作,确保试验结果的可靠性和一致性。
2. 配料要求2.1 胶料选择:根据试验需求,选择合适的橡胶品种作为胶料。
常用的橡胶品种包括天然橡胶(NR)、丁苯橡胶(BR)、丁腈橡胶(NBR)等。
2.2 辅助材料选择:根据试验要求,选择适当的辅助材料。
常用的辅助材料包括硫化剂、活化剂、加工助剂等。
根据实际需求,可以在辅助材料中添加填料、防老剂等。
2.3 配料比例:根据试验要求确定各个胶料和辅助材料的配料比例。
配料比例可以根据试验经验,也可以通过试验研究确定。
3. 混炼操作规程3.1 批量计算:根据试验需求,计算出所需要的胶料和辅助材料的混炼量。
3.2 混炼设备选择:根据试验胶料的混合方式选择合适的混炼设备。
常用的混炼设备有开炼机、密炼机等。
3.3 混炼温度控制:根据胶料和辅助材料的特性,控制混炼温度。
一般来说,混炼温度要低于橡胶的热分解温度,以避免胶料的热分解。
3.4 混炼时间控制:根据试验胶料的特性,控制混炼时间。
混炼时间过短会导致胶料未充分混合,混炼时间过长则会导致胶料过度磨损。
3.5 混炼顺序控制:根据试验要求,按照一定的顺序加入胶料和辅助材料。
一般来说,先加入胶料,再加入辅助材料,最后加入填料或防老剂。
3.6 混炼操作记录:在混炼过程中,记录混炼温度、时间、操作顺序等关键参数。
混炼操作记录可以作为参考,保证混炼操作的一致性。
4. 结论本文档规范了橡胶试验胶料的配料和混炼操作规程。
在进行橡胶试验时,按照本文档的规定操作可以确保试验结果的可靠性和一致性。
同时,混炼操作记录的准确记录也有助于对试验结果的分析和复现。
希望本文档对橡胶试验工作有所帮助。
Reference[1] 橡胶制品试验胶的混炼操作规程和配料规定,中国橡胶工业协会[2] 橡胶试验方法,中国标准出版社。
丁苯橡胶的合成工艺

丁苯橡胶的合成工艺
丁苯橡胶(NBR)的合成工艺包括以下几个步骤:
1. 选材:选择适当的乙烯基与丁烯基的聚合物,按一定比例混合。
丁烯基可以从丁烯基甲基酮或丁烯基甘油醚中获得。
2. 聚合反应:将选择的乙烯基和丁烯基聚合物与过氧化苯并富勒烯(C60)或双苯对甲苯磺酸二苯铅等催化剂混合,进行聚合反应。
该反应可以在高温下进行,通常在75-95C之间。
3. 纯化:将聚合物溶解在溶剂中,如苯酚,然后通过沉淀或萃取的方式将杂质去除,使得得到的聚合物更纯净。
4. 合成橡胶:将纯化后的聚合物分散在橡胶糖浆中,然后通过搅拌、加热等方式使其形成橡胶状物质。
5. 混炼:将合成的橡胶与添加剂(如硫化剂、硬化剂、填充剂等)混合,然后通过机械搅拌、炼胶机等设备进行混炼,使其浸渍均匀。
6. 硫化:将混炼后的橡胶模具中,经过一定时间和温度的硫化处理,使橡胶分子间的交联结构形成,从而提高橡胶的强度和耐磨性。
7. 切割和包装:将硫化后的橡胶切割成所需的尺寸和形状,然后进行包装,以便运输和使用。
这是丁苯橡胶的一般合成工艺,具体的合成条件和步骤可能会因不同的制备方法和产品要求而有所不同。
- 1、下载文档前请自行甄别文档内容的完整性,平台不提供额外的编辑、内容补充、找答案等附加服务。
- 2、"仅部分预览"的文档,不可在线预览部分如存在完整性等问题,可反馈申请退款(可完整预览的文档不适用该条件!)。
- 3、如文档侵犯您的权益,请联系客服反馈,我们会尽快为您处理(人工客服工作时间:9:00-18:30)。
丁苯橡胶的塑炼和混炼
宋啸
北京石油化工学院高063班
摘要:简单介绍了乳聚丁苯橡胶的塑炼和混炼方法。
关键词:丁苯橡胶塑炼混炼
丁苯橡胶是产量最大的通用合成橡胶,是橡胶工业的骨干产品,它是合成橡胶第一大品种,综合性能良好,价格低,在多数场合可代替天然橡胶使用,主要用于轮胎工业,汽车部件、胶管、胶带、胶鞋、电线电缆以及其它橡胶制品。
下面介绍丁苯橡胶的两种加工技术——塑炼和混炼。
1 丁苯橡胶的塑炼
丁苯橡胶可以通过调节平均分子量来改善其加工性能,一般来说,丁苯橡胶的门尼粘度多在35—60之间。
因此丁苯橡胶也可不用塑炼。
但实际上经过塑炼后,可增进配合剂的分散性,有助于提高产品质量。
特别是海绵橡胶创品,丁苯橡胶经过塑炼后,容易发泡,且泡孔大小均匀。
因此,丁苯橡胶与天然橡胶一样,塑炼也是重要工艺之一。
1.1塑炼与分子量分布
丁苯橡胶的加工性能不仅受微观结构如顺式、反式及乙烯型等的影响,而且也受其平均分子量与分子量分布的影响。
经过塑炼后,橡胶分子量中的大分子发生解聚,使得平均分子量降低,加工性能改善。
研究表明丁苯橡胶比在相同条件下薄通的天然橡胶塑炼效果小,但高粘度的丁苯橡胶有较明显的塑炼效果。
1.2塑炼条件对塑炼效果的影响
丁苯橡胶塑炼时,炼胶机的辊筒转速、速比、辊距及橡胶混度等各种条件对塑炼效果均有影响。
辊筒速比愈大,亦即前后辊筒平均转速愈快,则塑炼效果亦愈大。
此时也意味着橡胶通过辊缝次数愈多,塑炼效果愈好。
另外根据炼胶机的塑炼条件,存在一定的极限粘度。
随着辊筒平均转速的增加,辊距的减小及橡胶温度的降低极限粘度值也低。
要想在某个极限粘度以下进行塑炼时,需要变换塑炼条件以适应低极限粘度要求。
辊筒大小对塑炼效果没有多大影响,而辊距大小确有显著影响。
辊筒温度愈低,塑炼效果越大。
辊距愈小,速比愈大,塑炼橡胶的门尼粘度愈低。
1.3塑炼条件与凝胶生成
塑炼温度对丁苯橡胶的塑炼效果影响颇大,当塑炼辊温超过120o C时,会迅速产生凝胶。
在150o C时凝胶生成可高达44.3%,一般认为,在这么高温度下生成的凝胶属于自动氧化类型。
凝胶含量与门尼粘度之间不一定成比例,在凝胶含量非常高时,会出现假门尼现象,门尼粘度反而会低。
另外辊筒收缩性与凝胶含量关系也不大,与上述门尼现象相似。
1.4塑炼对硫化橡胶的影响
对不同塑炼程度的丁苯橡胶1502和丁苯橡胶1507进行温炼,其硫化橡胶橡胶物理性能要有所变化,研究结果表明,在塑炼过度时有降低抗张强度的趋向。
2 丁苯橡胶的混炼
丁苯橡胶混炼系指在其塑炼胶中均匀混入硫化剂、补强剂、软化剂等配合剂的作业。
混炼胶质量对最终产品物理性能有直接影响,因此要认真操作。
丁苯橡胶在设计时虽已考虑了使其易于加工,但由于聚合温度、乳化剂种类、结合苯乙烯含量及凝聚剂种类等制造条件的变化,也会产生种种性质上的差别。
因此日本工业标准(JIS)在丁苯橡胶的试验方法中规定了
详细的标准混炼方法。
2.1 JIS规定的丁苯橡胶混炼方法
丁苯橡胶胶料用试验开放式炼胶机混炼,按下述操作顺序进行。
(1)塑炼胶在辊距0.20±0.05毫米下薄通2次(不包辊)。
(2)放大辊距到1.4±0.1毫米,胶料包辊以后,进行左右交替3/4搁胶。
(3)加硕脂酸。
(4)均匀分批加入炭黑。
当炭黑加入一半之后,将辊距放大到1.6毫米,左右3/4捣胶各1次。
然后加入剩余炭黑,待炭黑全部加完后,将辊距放大到1.9毫米,再从两边各捣胶1次。
在炭黑没有全部混入橡胶之前,不能进进捣胶。
从辊筒上落到炼胶机底盘上的炭黑应及时收集起来加到辊筒上。
混炼No.3配方时,当硅酸钙加入一半后即从两边各作3/4捣胶,然后将混炼胶料移到后辊筒上,继续加完全部硅酸钙后进行左右3/4捣胶3次,方转入下一操作。
(5)辊距调到1.9毫米,加其它配合剂,向时要注意防止飞扬。
(6)从左右两方进行3/4捣胶3次。
(7)从辊筒上将胶料刻下,辊距调到0.75±0.15毫米,再使整个胶料通过辊距6次。
(8)混炼胶在7毫米厚度下出片、过秤,重量误差应在配方量的±1%以内。
(9)混炼胶冷却2小时后,用试验开放式炼胶机在辊距0.20±0.05毫米下薄通10次,然后将辊距调到1.4毫米使胶科包到前辊筒上,按3/4捣胶左右往返3次后下片,胶片收缩后的厚度约为2.2毫米,放置1—6小时后送去硫化。
所谓3/4捣胶是将胶料在辊筒工作面长度之3/4处切断后,使胶落到底盘上,至辊缝间无积胶后再翻捣上去,这种操作左右交替一次约30秒钟。
在混炼No.10配方时要将辊距调到1.9毫米时再包辊,胶料进行不割胶的塑炼。
2.2 混炼条件对物理性能的影响
前已述及,即使规定了丁苯橡胶的标准混炼方法,但实际上还会由于设备条件如炼胶机的规格、辊筒速比、回转速度等,以及人为因素如辊距、混炼温度、混炼时间和加料顺序等的变化而产生硫化橡胶物理性能上的波动。
分析其原因不外乎炼胶过程中使橡胶分子链断裂,配合剂分散不匀或配合剂中水分影响以及聚合物凝胶和结合凝胶(填充剂凝胶)的生成等。
一般来说,薄通得好时物理性能提高。
另外,炭黑及白炭黑等配合剂中的水分会缩短焦烧时间与加快硫化速度。
在密炼机混炼时,混炼温度、混炼时间、转子速度、上顶栓压力以及加料方法等对配合剂的分散性和加工性及硫化橡胶的物理性能等都有一定影响。
在丁苯橡胶中混炼炭黑或白炭黑等活性补强剂时,由于混炼条件变化会生成结合凝胶。
一般是炼胶温度提高则凝胶生成也多。
将炭黑混炼胶薄片在不同温度下加热一小时生成的结合凝胶量随温度提高而急剧增加。
结合凝胶可提高胶料定伸强度与抗张强度,但凝胶量大时会降低加工性能。
2.3 母炼胶法
橡胶配合中某些用量较少的配合剂。
例如着色剂或者混炼中容易飞扬而污染环境的炭黑,以及难于混炼操作的油等,往往是将其预先与丁苯橡胶胶乳混合共凝聚成湿法母炼胶,或者将丁苯橡胶(干胶)与配合剂用密炼机混炼制成干法母炼胶后再行使用。
在湿法母炼胶中有着色剂母炼胶、木质素母烁胶,炭黑母炼胶、油母炼胶(充油橡胶)、高苯乙烯母炼胶等。
干法母炼胶有炭黑母炼胶、白填充刑母炼胶及着色剂母炼胶等。
使用母炼胶的优点是配合剂分散性好,可提高混炼效率,节约电能,并防止因配合剂飞
扬而污染环境。
湿法炭黑母炼胶比干法分散性好,各项物理性能亦好。
3 结语
丁苯橡胶是橡胶工业的骨干产品,它是合成橡胶第一大品种,综合性能良好,价格低,在多数场合可代替天然橡胶使用,有着广阔的发展前景,主要用于轮胎工业,汽车部件、胶管、胶带、胶鞋、电线电缆以及其它橡胶制品。
参考文献
[1]梅野昌,杉原喜四郎,等.丁苯橡胶加工技术[M].化学工业出版社,1983,6.
[2]张洪林.乳聚丁苯橡胶的生产技术进展[J].中国橡胶,2009,(08).
[3]周明,武爱军,孙步均,贾刚治.乳聚丁苯橡胶改性技术研究进展[J].石油化工应用,2008,(04).
[4]钱伯章.我国丁苯橡胶技术和新产品开发进展[J].上海化工,2009,(05).
[5]张洪林,于鹏.乳聚丁苯橡胶生产技术进展[J].橡胶科技市场,2008,(18).
[6]范仁德.我国橡胶工业发展现状及2009年对橡胶的需求情况[J].中国橡胶,2009,(08).。