汽车主减速器双曲面齿轮结构参数优化设计_廖林清
Ease-off拓扑修正的准双曲面齿轮齿面修形方法

Ease-off拓扑修正的准双曲面齿轮齿面修形方法聂少武; 蒋闯; 邓效忠; 苏建新; 杨建军; 王建华【期刊名称】《《中国机械工程》》【年(卷),期】2019(030)022【总页数】8页(P2709-2715,2740)【关键词】准双曲面齿轮; 共轭齿面; Ease-off修正; 拓扑修形; 加载接触分析【作者】聂少武; 蒋闯; 邓效忠; 苏建新; 杨建军; 王建华【作者单位】河南科技大学机电工程学院洛阳 471003; 河南科技大学机械装备先进制造河南省协同创新中心洛阳 471003; 拖拉机动力系统国家重点实验室洛阳471039【正文语种】中文【中图分类】TH132.410 引言准双曲面齿轮作为汽车驱动桥主减速器的关键传动元件,其齿面啮合质量影响着汽车的NVH(噪声、振动及舒适度)性能。
随着人们对汽车NVH要求的提高,齿轮企业对准双曲面齿轮啮合性能提出了更严格的要求。
齿面接触区作为一个重要指标,直接影响着准双曲面齿轮的啮合性能。
为了能够获得最佳的齿面接触区来降低驱动桥的振动和噪声,齿面修形技术在准双曲面齿轮的设计与加工中得到越来越多的应用。
齿面拓扑修形技术能够按照预置要求通过控制齿面的整个拓扑结构来修正齿面,因此该技术成为了当前研究的热点。
SHIH等[1-2]针对Face-hobbing加工方法以研齿后齿面Ease-off为目标,提出了基于Ease-off拓扑的齿面修正方法,在此基础上又提出一种能够预控啮合性能的改进Ease-off齿面拓扑修形方法。
杜进辅等[3]针对双面法加工的摆线齿准双曲面齿轮,通过在小轮共轭齿面上预置啮合性能参数,提出了齿面主动设计方法。
蒋进科等[4]通过预置传动误差参数及抛物线修形参数,提出了基于Ease-off拓扑修形的准双曲面齿轮齿面多目标优化设计方法。
牟彦铭等[5]通过预设高阶传动误差曲线和齿面接触印痕构建出了目标齿面Ease-off,提出了高重合度弧齿锥齿轮高阶传动误差设计与分析方法。
RV减速器优化设计
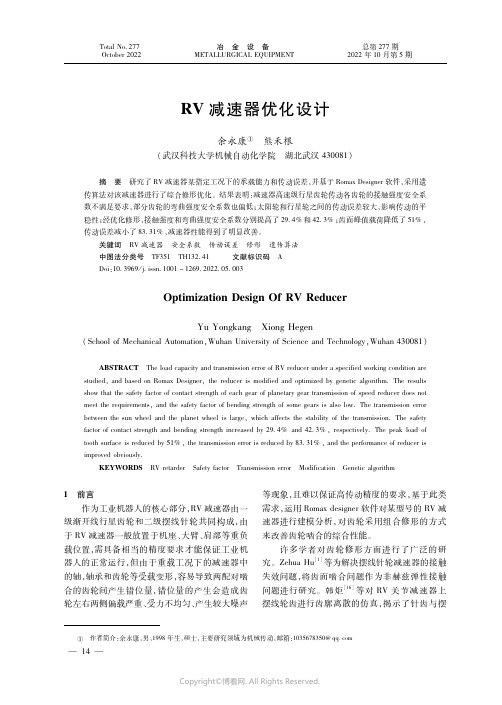
RV减速器优化设计余永康① 熊禾根(武汉科技大学机械自动化学院 湖北武汉430081)摘 要 研究了RV减速器某指定工况下的承载能力和传动误差,并基于RomaxDesigner软件,采用遗传算法对该减速器进行了综合修形优化。
结果表明:减速器高速级行星齿轮传动各齿轮的接触强度安全系数不满足要求,部分齿轮的弯曲强度安全系数也偏低;太阳轮和行星轮之间的传动误差较大,影响传动的平稳性;经优化修形,接触强度和弯曲强度安全系数分别提高了29 4%和42 3%;齿面峰值载荷降低了51%,传动误差减小了83 31%,减速器性能得到了明显改善。
关键词 RV减速器 安全系数 传动误差 修形 遗传算法中图法分类号 TF351 TH132.41 文献标识码 ADoi:10 3969/j issn 1001-1269 2022 05 003OptimizationDesignOfRVReducerYuYongkang XiongHegen(SchoolofMechanicalAutomation,WuhanUniversityofScienceandTechnology,Wuhan430081)ABSTRACT TheloadcapacityandtransmissionerrorofRVreducerunderaspecifiedworkingconditionarestudied,andbasedonRomaxDesigner,thereducerismodifiedandoptimizedbygeneticalgorithm.Theresultsshowthatthesafetyfactorofcontactstrengthofeachgearofplanetarygeartransmissionofspeedreducerdoesnotmeettherequirements,andthesafetyfactorofbendingstrengthofsomegearsisalsolow.Thetransmissionerrorbetweenthesunwheelandtheplanetwheelislarge,whichaffectsthestabilityofthetransmission.Thesafetyfactorofcontactstrengthandbendingstrengthincreasedby29 4%and42 3%,respectively.Thepeakloadoftoothsurfaceisreducedby51%,thetransmissionerrorisreducedby83 31%,andtheperformanceofreducerisimprovedobviously.KEYWORDS RVretarder Safetyfactor Transmissionerror Modification Geneticalgorithm1 前言作为工业机器人的核心部分,RV减速器由一级渐开线行星齿轮和二级摆线针轮共同构成,由于RV减速器一般放置于机座、大臂、肩部等重负载位置,需具备相当的精度要求才能保证工业机器人的正常运行,但由于重载工况下的减速器中的轴,轴承和齿轮等受载变形,容易导致两配对啮合的齿轮间产生错位量,错位量的产生会造成齿轮左右两侧偏载严重、受力不均匀、产生较大噪声等现象,且难以保证高传动精度的要求,基于此类需求,运用Romaxdesigner软件对某型号的RV减速器进行建模分析,对齿轮采用组合修形的方式来改善齿轮啮合的综合性能。
弧线等高齿高减速比准双曲面齿轮的设计与加工试验
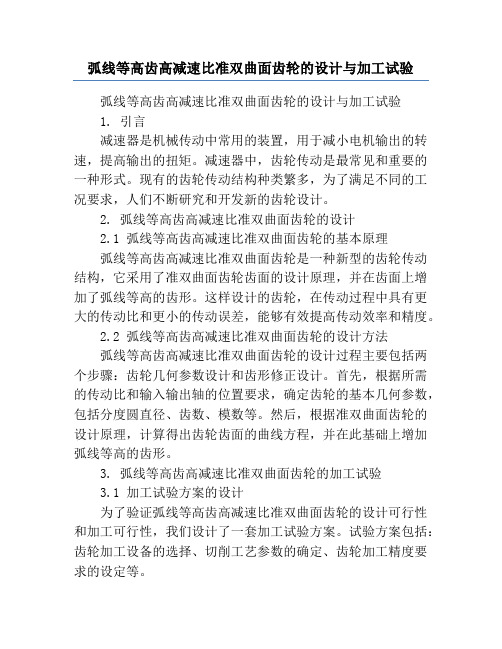
弧线等高齿高减速比准双曲面齿轮的设计与加工试验弧线等高齿高减速比准双曲面齿轮的设计与加工试验1. 引言减速器是机械传动中常用的装置,用于减小电机输出的转速,提高输出的扭矩。
减速器中,齿轮传动是最常见和重要的一种形式。
现有的齿轮传动结构种类繁多,为了满足不同的工况要求,人们不断研究和开发新的齿轮设计。
2. 弧线等高齿高减速比准双曲面齿轮的设计2.1 弧线等高齿高减速比准双曲面齿轮的基本原理弧线等高齿高减速比准双曲面齿轮是一种新型的齿轮传动结构,它采用了准双曲面齿轮齿面的设计原理,并在齿面上增加了弧线等高的齿形。
这样设计的齿轮,在传动过程中具有更大的传动比和更小的传动误差,能够有效提高传动效率和精度。
2.2 弧线等高齿高减速比准双曲面齿轮的设计方法弧线等高齿高减速比准双曲面齿轮的设计过程主要包括两个步骤:齿轮几何参数设计和齿形修正设计。
首先,根据所需的传动比和输入输出轴的位置要求,确定齿轮的基本几何参数,包括分度圆直径、齿数、模数等。
然后,根据准双曲面齿轮的设计原理,计算得出齿轮齿面的曲线方程,并在此基础上增加弧线等高的齿形。
3. 弧线等高齿高减速比准双曲面齿轮的加工试验3.1 加工试验方案的设计为了验证弧线等高齿高减速比准双曲面齿轮的设计可行性和加工可行性,我们设计了一套加工试验方案。
试验方案包括:齿轮加工设备的选择、切削工艺参数的确定、齿轮加工精度要求的设定等。
3.2 加工试验的具体步骤在符合试验方案设计的加工设备上,根据设计的齿轮几何参数和齿形修正方案,进行齿轮的加工试验。
试验中要控制好切削速度、进给速度和切削深度等工艺参数,以保证加工质量。
同时,为了检验齿轮的传动性能,还需要进行传动试验,测试齿轮的传动比和传动误差。
4. 结果与讨论通过加工试验,我们得到了一批弧线等高齿高减速比准双曲面齿轮样品。
经过测量和测试,我们发现这些齿轮具有较好的几何尺寸精度和传动性能。
其传动比稳定,传动误差较小,能够满足设计要求。
准双曲面齿轮的设计 ppt
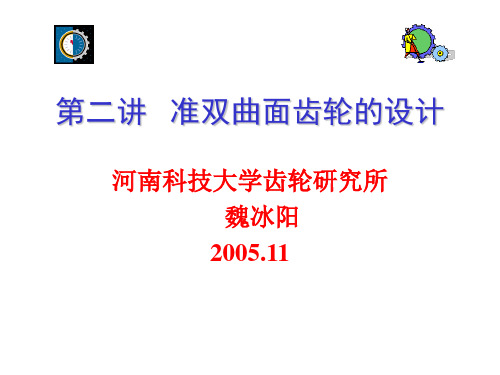
准双曲面齿轮
弧齿锥齿轮
图 2.1 准双曲面齿轮与弧齿锥齿轮对比
同等条件下准双曲面小轮比弧齿锥齿轮小 轮大得多。
2. 准双曲面齿轮概述
优点: 优点: 3) 比弧齿锥齿轮传动的重叠系数更大,传 动更加平稳,而且齿面所受的正压力小。 4) 轴线位置的偏置,使传动在空间的布置 具有了更大的自由度。如下偏可以用于降 低汽车的重心增加平稳性;也可以用来增 加车身的高度,增加汽车的越野性。
小 相 等 、符 号 相 反 。为 了 使 极 限 曲 率 半 径 符 合 标 准 刀 盘 尺 寸 ,可 以 改 变 原 设 的 大 轮 偏 置 角 ε值 。
5.准双曲面齿轮的设计过程
• 如果螺旋角不满足要求,通过改变r1 如果螺旋角不满足要求,通过改变r 来满足 • 如果极限曲率半径不符合标准刀盘 尺寸,通过改变小轮轴截面偏置角η 尺寸,通过改变小轮轴截面偏置角η 来满足 • 过程通常由计算机叠代完成
cos β 2 R1 sin δ 1 z2 r1 z2 = × = × cos β1 R2 sin δ 2 z1 r2 z1
r1 、r2 确定之后,不同的螺 旋角可以适应不同的传动比, 因此对于给定的传动比准双 曲面齿轮的节锥并不唯一, 轮齿法线可以在任意方向垂 直于轮齿切线,因此压力角 可以自由选取。
E tgη1 = ' ' r2 (tgδ2 sinΣ + cosΣ) + r1
给定大轮刀盘半径 r0=d2/(2sinδ2’)
三.准双曲面齿轮的初始参数的选取
•齿坯设计需输入的初始参数
1. 齿数的选取
• 对于准双曲面齿轮,虽然齿数可任意选定,但在一 般情况下,小轮的齿数不得小于5,小轮与大轮的 齿数和应不小于40,且大轮齿数应与小轮齿数之间 避免有公约数。表2.1为格里森推荐的不同传动比 下小轮的最少齿数。若是设计汽车用的准双曲面齿 轮,则小轮齿数可以选得较小。对于格里森调整卡 和计算程序都作了以上限制,突破上述范围将不能 进行设计计算。也有突破以上齿数限制设计的方法, 比如“非零变位”设计,小轮齿数可小到2~3齿的。
CA1090汽车驱动桥主减速器设计
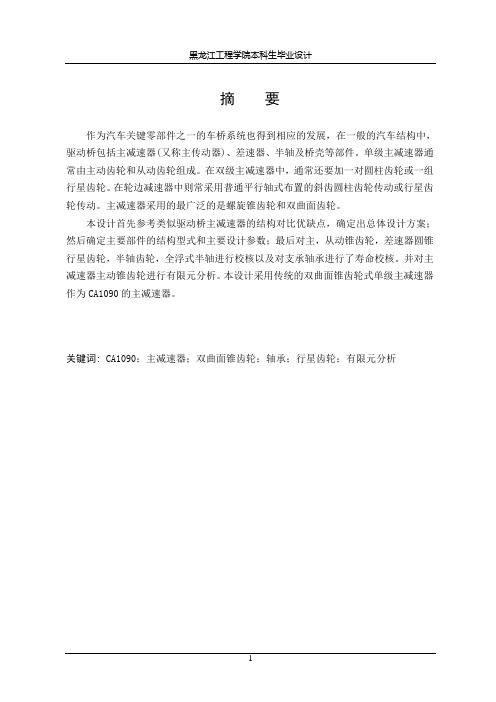
黑龙江工程学院本科生毕业设计摘要作为汽车关键零部件之一的车桥系统也得到相应的发展,在一般的汽车结构中,驱动桥包括主减速器(又称主传动器)、差速器、半轴及桥壳等部件。
单级主减速器通常由主动齿轮和从动齿轮组成。
在双级主减速器中,通常还要加一对圆柱齿轮或一组行星齿轮。
在轮边减速器中则常采用普通平行轴式布置的斜齿圆柱齿轮传动或行星齿轮传动。
主减速器采用的最广泛的是螺旋锥齿轮和双曲面齿轮。
本设计首先参考类似驱动桥主减速器的结构对比优缺点,确定出总体设计方案;然后确定主要部件的结构型式和主要设计参数;最后对主,从动锥齿轮,差速器圆锥行星齿轮,半轴齿轮,全浮式半轴进行校核以及对支承轴承进行了寿命校核。
并对主减速器主动锥齿轮进行有限元分析。
本设计采用传统的双曲面锥齿轮式单级主减速器作为CA1090的主减速器。
关键词: CA1090;主减速器;双曲面锥齿轮;轴承;行星齿轮;有限元分析1黑龙江工程学院本科生毕业设计ABSTRACTOne of the key components of a vehicle bridge system has also been a corresponding development of the automobile in the general structure, including the main gear axle (also known as the main drive device), differential, axle and axle housing and other components. Usually single-stage final drive gear and driven gear components. In the two-stage final drive, usually also add a pair of spur gear or a group of planetary gears. Reducer in the wheel is usually arranged by common parallel shaft helical gears or planetary gears. Final drive is the most widely used spiral bevel gear and hypoid gear.The drive axle design similar to the first reference to the structure of comparative advantages and disadvantages of the main gear, determined the overall design scheme; and then identify the main components of the structure type and the main design parameters; Finally, the driving and driven bevel gear, planetary gear differential cone, axle gear, full floating axle bearings were checked and were on life support check. Bevel gear final drive and initiative to the finite element method. This design uses a traditional-style hypoid bevel final drive as the CA1090 single-stage main gear.Key word: CA1090;Main Gear; Hypoid Gears; Bearing;Planetary Gear;FEA2黑龙江工程学院本科生毕业设计目录摘要 (Ⅰ)Abstract (Ⅱ)第1章绪论 (1)1.1选题的目的和意义 (1)1.2国内外研究现状 (1)1.3本次设计的主要内容 (3)第2章主减速器的设计 (4)2.1结构型式的选择 (4)2.1.1减速型式 (4)2.1.2齿轮的类型的选择 (4)2.1.3主动锥齿轮的支承形式 (7)2.1.4从动锥齿轮的支承形式及安置方法 (8)2.2基本参数选择与设计计算 (9)2.2.1计算载荷的确定 (9)2.2.2基本参数的选择 (11)2.2.3双曲面齿轮的几何尺寸计算 (15)2.2.4双曲面齿轮的强度计算 (23)2.2.5齿轮的材料及热处理 (28)2.3轴承的选择 (28)2.3.1计算转矩的确定 (28)2.3.2齿宽中点处的圆周力 (29)2.3.3双曲面齿轮所受的轴向力和径向力 (30)2.3.4轴承载荷的计算及轴承的选择 (31)2.4本章小结 (34)第3章差速器设计 (35)3.1差速器结构形式的选择 (35)3.2对称式圆锥行星齿轮差速器的差速原理 (36)3黑龙江工程学院本科生毕业设计3.3对称式圆锥行星齿轮差速器的结构 (37)3.4对称式圆锥行星齿轮差速器的设计 (38)3.4.1差速器齿轮的基本参数的选择 (38)3.4.2差速器齿轮的几何计算 (40)3.4.3差速器齿轮的强度计算 (41)3.5本章小结 (42)第4章驱动半轴的设计 (43)4.1半轴结构形式的选择 (43)4.2全浮式半轴计算载荷的确定 (44)4.3全浮式半轴的杆部直径的初选 (45)4.4全浮式半轴的强度计算 (45)4.5半轴花键的计算 (45)4.5.1花键尺寸参数的计算 (45)4.5.2花键的校核 (48)4.6本章小结 (49)第5章主动锥齿轮的有限元分析 (50)5.1有限元方法与ANSYS简介 (50)5.2主动锥齿轮的有限元分析 (50)5.2.1有限元模型的生成 (50)5.2.2划分网格 (51)5.2.3齿轮静载和约束的施加与结果分析 (52)5.3本章小结 (54)结论 (55)参考文献 (56)致谢 (57)4黑龙江工程学院本科生毕业设计第1章绪论1.1选题的目的和意义主减速器是驱动桥的重要组成部分,其性能的好坏直接影响到车辆的动力性、经济性。
工程车辆用大功率行星齿轮设计优化研究

AUTOMOBILE DESIGN | 汽车设计工程车辆用大功率行星齿轮设计优化研究1 引言行星齿轮传动具有效率高、传动平稳、抗冲击振动的特点[1]。
在传递同样的功率或转矩时,与普通的定轴轮系齿轮机构相比,行星齿轮传动机构具有体积小和重量轻的优点,更易于进行结构紧凑性布置。
行星齿轮传动通常由太阳轮、内齿圈、行星架和多个行星齿轮组成[2],其齿轮参数一般可以通过经验公式得到,但各齿轮之间的载荷强度差异巨大,强度相对薄弱的齿轮容易损坏,直接影响到行星齿轮传动装置的使用寿命[3]。
如何合理设计行星传动系统一直是车辆主机厂和变速器厂商重点关注的核心技术问题。
近年来,仿真技术与实验测试技术不断发展,为解决此类设计问题提供了便捷、高效的方法。
本文针对某实际工程问题,采用理论分析、仿真及实验相结合的方法,对某工程车辆用大功率行星齿轮开展设计优化,以提高其工作可靠性。
2 行星齿轮减速机原理及问题分析某工程车辆用大功率行星齿轮减速机的行星齿轮传动为三级传动,其传动系统原理如图1所示。
其由太阳轮、行星架、行星轮和内齿圈等零件组成,传动流程如下:一级太阳轮Z1连接电机输出轴,作为整个减速机的输入。
电机输入动力首先通过一级太阳轮Z1传递到一级行星轮Z2,其中一部分动力由Z2传递到一级内齿圈Z3,另一部分动力由Z2通过一级行星架H1传递到二级太阳轮Z4;第二级行星传动中,动力由Z4传递到二级行星轮Z5,其中一部分动力由Z5传递到二级内齿圈Z6,另一部分动力由Z5通过二级行星架H2传递到三级太阳轮Z7;第三级行星传动中,三级行星架H3固定,动力由Z7传递到三级行星轮Z8,再由Z8传递到三级内齿圈Z9。
其中第三级行星传动的承载扭矩最大,是行星齿轮减速机的核心元件,其运转状况直接决定着大功率行星齿轮减速机的使用寿命[4]。
图1 三级减速机原理图ZZZZ ZZZZZH H H工程中,一般通过耐久疲劳实验来考核齿轮传动装置的寿命[5]。
【doc】双级行星齿轮减速器的优化设计
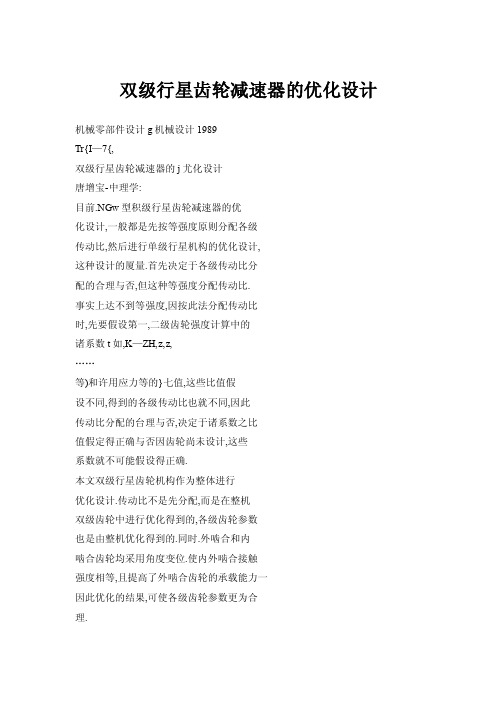
双级行星齿轮减速器的优化设计机械零部件设计g机械设计1989Tr{I—7{,双级行星齿轮减速器的j尤化设计唐增宝-中理学:目前.NGw型积级行星齿轮减速器的优化设计,一般都是先按等强度原则分配各级传动比,然后进行单级行星机构的优化设计,这种设计的厦量.首先决定于各级传动比分配的合理与否,但这种等强度分配传动比.事实上达不到等强度,因按此法分配传动比时,先要假设第一,二级齿轮强度计算中的诸系数t如,K—ZH,z,z,……等)和许用应力等的}七值,这些比值假设不同,得到的各级传动比也就不同,因此传动比分配的台理与否,决定于诸系数之比值假定得正确与否因齿轮尚未设计,这些系数就不可能假设得正确.本文双级行星齿轮机构作为整体进行优化设计.传动比不是先分配,而是在整机双级齿轮中进行优化得到的,各级齿轮参数也是由整机优化得到的.同时.外啮合和内啮合齿轮均采用角度变位.使内外啮合接触强度相等,且提高了外啮合齿轮的承载能力一因此优化的结果,可使各级齿轮参数更为合理.本院化设计中,考虑了行星齿轮安装的滚动轴承,程序自动选择满足要求的滚动轴承.这样可使优化设计结果满足行星齿轮结构设计的要求.传动简图如图l所示.二,优化数学模型罔1积鞭行星减速器传动简用'1.设计壹董确定双级行星齿轮减速器齿轮的参数有各齿轮的齿数,模数,齿宽,变位系数和单级传动比等,为了便于在几何计算之前进行配齿,配出的齿轮能使外啮合角和内啮合角在台理的范围内,达到内外啮合等强度的目的,则选用下参数作为设计变量:ZZth,BI,X_],I,il,ZI2,m2,B2,xt,盯2j式中:zZ分别为第一,二级太阳轮齿数;int,rl'l别为第一,二级齿轮模敬:B,B.分别为第一,二级齿宽:xx..分别为第一,二级太阳轮变位系数系数:.-一一.j甥Ⅱ为第一,=级齿轮外啮台角;i1为第一级传动比.2.目标函数为了减轻减速器重量和体积.降低产品成本,采用l舣级行星机构各齿轮体积之和作为目标函数.F=4[Blf也t{+T1Pda}dm卜也口+t32f也fT1P出!+dj一出口i)]'《机械设计"1989№05机槭零部件设计23式中:各量的下标l,2分别表示第—和一Z05)tg0+Z0jtg第二级的参数,t,x和Q分别表示太阳轮,tg‰,一{蜀—zx)z≥行星轮和内齿圈的参数,a表示顶圆,f表zxtg"4(一)sin2示根圆,(下同),nP表示行星轮个数.式中:zo为加工内齿轮的插刀齿数I 3.约束函数o为加工内齿轮时插刀齿顶压力'(1),边界约束角;,,z≤z≤zlo约加工内齿轮时合角.xm≤X,≤xmaxli=12'8),加工内齿轮时不产生范成顶切mmi.≤mj≤axL(下同)的限制.B_n≤B≤BnalZ021/z≥l—tg口/tga'o~i20≤≤27.『(9),结构限制条件iln≤i1≤iJl—dmddfQ0(2),齿轮宽径比的约束条件dfQ~/dfQ1一1.3≤0Bid【】一1.3≤0(dfro+6111j)/dL一1(J0.35一B/d,≤0dfpidt【i一10(3),齿轮强度约束穿牛-D一一(d…一2.5m,)『l接触强度安全系数:式中:dfQndfq2分别为第一J==二级齿圈SH—S≤o根圆直径S…一S≤od为允许的齿圈最大外径}SH一S≤odt为太阳轮允许最小根圆直径}弯曲强度安全系数:SmIn—S0为滚动轴承外径.SFi一SFx≤0SmIn—Sm,《0(i0),配齿条件:2012≤0传动比耍:一㈩1.一x【≤.一El≤l训小'一Z【l'(5),齿顶厚的约束条件..0.25一S.}./≤0装配条件:亩=堕=整数(2)0.25一S㈣≤0(6),内啮合角的约束条件为了使内外啮合齿轮接触强度相等,提l7.≤<23.5.高外啮合齿轮承载能力,内外啮合齿轮均采(7),过渡曲线干涉条件用角度变位传动,则同心条件为:外啮合齿轮副不发生过渡曲线干涉条件:tg1;Z}/z刈(tg毛,一tg1i)≥tg一4(一xx.)/(Z.sin22)tg一Z/zll(gxi—tgI)≥tg4(Il】'|c)/(Z¨n2)内啮合齿轮副不发生干涉条件:Zx,tg(zq一Zj)tg;二Z0121:Z0L—ZxL若np:3.考虑.'3)Z【1+Zx1则相邻条件能满足,故可不三,配齿计算配齿计算在行星机构优化设计中是个关24机械零部件设计《机械设计1989№05键问题,一般将公式f1~(3)作为等式约束简单处理是很难达到目的的,往往会.,产生优化不出结果的现象如前所述,为了能使外啮合和内啮合齿轮等强度,内外啮合'均应采用角度变位,并使外啮合角在23.~26.5.范围内,内啮合角在2O.左右.为了使配出的齿轮参数(齿数和变位系数】能满足上述要求,则配齿计算可按下述方法进行因z,Xti和为设计变量,给出了它们自田值,则就可由公式①算出z..并圆整为z.,对于n=3的行星机构来说,能满足装配条件的z可能有Z.2,Z3?, z.,za+,z,其中有两个值能满足装配条件.对于每一个,考虑行星齿轮的角度变位,有可琵采取的行星齿轮齿数就存在三种可能:Z_IFIX(Zq—Zt)/2Z(2JZ(1)一l(4).厶【3=厶lj2这样内齿轮齿数zq存在两种可能,行星轮齿数就存在六种可能,那未选择哪一组齿数为好呢?则根据上述内外啮合角的要求来选择一组台适的齿数和变位系数,其程序框图如图2所示.四,优化程序结构本优化设计程序由一个主程序和优化方法,配齿计算,几何计算,强度计算,目标函数和约束函数等21个子程序组成,其程序流程图如图3所示.图中K.为程序功能控制变量,KS=l为优化设计,KS=2为一般设计,KS=3只进行强度校核.本程序采用先进的约束拟牛顿法进行优化,这种方法是一种求解约束优化问题的直接解法.一方面将约束问题转化为一系列二次规划的子问题,并以每个子问韪钓解作为『e:z,.m?一I.J{害,由f计耳.z(J.K),fJl叫匠鞫臣曲』耍≤图2配齿计算程亭框图图3行星齿轮减i}器慌忙设计流程图●r■lf.f机械设计1989№05机械零部件设计25该谈线性搜索的方向,同时利尉线性搜索的五,设计实例和结果分析监控策略来确定该次迭代的步长日子,从而实现一次迭代运葬.另一方面,它在构造每一个二次飙划子问题时,采用与无约束变尺度法相似的Hessen矩阵逆阵的近靓矩阵的递推格式.这样使函数求值次数少,计算效率高,整体收敛快和可靠性高.设计变量辛的模数等在忧化时作连续变量处理,优化后采用整型点圆整法"进行圆整.,1-●,设计煤矿运输机用的NGV级行星齿轮减速器.已知输入功率Pl=127kW,输人转速nl=1000r.P.Ⅱl'总传动比为28,载荷中等冲击,电动机为原动机,太阳轮和行星轮的材料为180;MnTi,渗碳淬火,HRCA8~62,内齿圈材料为40Cr.词质处理,HB260~280,齿轮寿命为10O00小时,齿轮精度为7级优化计算结果列于表l.'.表1,齿轮主要参数毒教值●ZL】Zx】ZLlXJX0JZt:Z2Z02XI2Xx2X0/原设计19S2860.500.7120.40124.5203082●0.5700.564O.5647.0忧亿_i壁计1934曲0.85l50.79l7I'屿0"0223186O.鹎10.561O.9o36.0_齿轮主要尺寸目标函数参徼值,dl】dxLd0】dmJb】dl±dx2d0£fdfbFc呻.)原设计85.50144.O0387.O04tl2.217,60.O0l201们.21仉n574.0599.7965l0.0tSZ204110J优化设计76n0136.00撕6.00047.931lIl32?训l86.O516.O乱1.821la5.2t6717lx10' _接触强度安垒系数弯曲强度安垒系敬-参教值_tS¨llSHlSHISHl2.S¨2SH02SFcISIL?S…SFt:SrxS川2l原设计l_469J_4691.1851.2591.2591口674.4223.0532.8063.1892.1922.456●,-纯化设计'h203l.283i.1401.228i.船81.1242.9322.O262.3le2.93fii.8622.553 '从表l计算结果可知,优化设计结果.使齿轮参数比原设计更为台理,达到第一级与第二级齿轮等强度,内外啮合的接触强度也为等强度,各齿轮尺寸比原设计小,两级齿轮体积之和比原设计减,J,l,3.22%.(下转33页)垫遮丝盐兰盥盟..,塑壁壁!堕燮——.c==s.I×ly_j=而1929丽090×了180Idf.●OuulJ'N.mi11/rad)一2.计算联轴器的变形角联轴器输人功率150KW,在低速1485r,~nin时,所承受最大扭矩:T:0549.(N?叫1式中:N一输入功率(kw);T一扭矩(N?mmj,n一每分钟转数min)将已知:NelS0.kW.n=1485r.min代人上式:T=964545rN?mm根据设备在启动时动载荷和可能出现的过载情况,联轴器的计算扭矩为:=T'(N?一)其中:K一工作情况系数.对于.起动睫量不太而受冲击载菏的设备,=1.5—2.5.现取=2.0.=T=2.0x964545=1929090(N.m,联轴器在T作用下,其变形角I按扭转刚度的定义,则=争×.=×=U—l03.与国内弹性圄柱销联轴器的计算午tI比较按照嵌人式弹性联轴器的D=lT0am尺寸,它相当于弹性圈柱销联轴器(JB108一fj0)标准中的B型,其主要参数为:m=10DI=170,d=36m~,L=45m~,=6Nm{由于橡胶圈为空心,其钢柱销直径d=18v,a, 受挤压力橡胶厚度为:(d—d)/2=9假}.1.25..从以上两种联轴器的扭转刚度比较.嵌人式只有弹性圈柱销型的1/7弱.因此.在承受相同扭转力矩时,前者较后者的变形角增大7倍多.同时,由于橡胶柱的缓冲减振作,用,在承受正反转冲击载荷时,充分显示出优越性所在.并且结构简单,加工容易,维修简便,是一种较先进的弹性联轴器参考文献,1.西l』£工大教研组:机槭设计,上.下il册,人民教育出版社.2.r苏Jll-H?到台托先:机械零什,r上.F-册高等教育出咂社.(魏力)参考文献,I.华大年辞主编:机械丹析与设计,纺织工业出版杜19858.天津_^学主编:机械原理,凡民教育出版柱,19793.黄锡恺薛主编:【槭原,人民救育出舨社,1981(魏力)(上接25页参考文献t.渐开线矧{L由轮堆载麓;fJ计算靠法.GB34811.一838.机锻上程手册编}委员含编【槭工手册第l2藉齿轮传动.机械工业出版畦1980,定同样受rr曲作用,则代入有关算式:'.B-Ii岸持略l^幂夫西:江耕『屯洋.由轮减速器的结c:78030000{N?nlmrad构与汁韩?t海科技出版社.1982'4?陈直周菩编:机槭优化设计,上海科学技术出版牡L987.。
Ease-off拓扑修形准双曲面齿轮齿面多目标优化设计方法

(1.长安大学汽车学院,7 1 0 0 6 4 , 西 安 ' 2 .长安大学汽车运输安全保障技术交通行业 重点实验室,7 1 0 0 6 4 , 西 安 ' 3.西北工业大学机电学院,7 1 0 07 2 ,西安)
摘 要 :为 了 提 高 汽 车 驱 动 桥 综 合 传 动 性 能 ,提 出 基 于 ease-off拓 扑 修 形 准 双 曲 面 齿 轮 齿 面 多 目 标 优 化 设 计 方 法 。预 置 传 动 误 差 参 数 及 抛 物 线 修 形 参 数 设 计 小 轮 法 向 ease-off曲 面 ,小轮修形齿面 表 示 为 大 轮 的 共 扼 齿 面 叠 加 ease-off曲 面 。结 合 齿 面 接 触 分 析 (T C A ) 、齿 面 承 载 接 触 分 析 (L T C A )方 法 及 齿 轮 摩 擦 理 论 最 新 进 展 ,得 到 接 触 线 离 散 点 的 滑 动 速 度 、啮 合 承 载 变 形 、载荷分布及局 部 摩 擦 系 数 ,进 而 确 定 齿 面 瞬 时 咕 合 效 率 和 B l o c k 闪 温。以 承 载 传 动 误 差 幅 值 (A L T E ) 最 小 、齿面 闪 温 最小 和 平 均 咕 合 效 率 最 大 进 行 多 目 标 优 化 ,获 得 最 佳 修 形 齿 面 ,并分析齿面滑动速度与综合曲 率 半 径 的 变 化 及 重 合 度 对 咕 合 性 能 的 影 响 。算 例 表 明 :最 优 ease-off修 形 齿 面 在 咕 入 、、齿出端有足 够 的 抛 物 线 传 动 误 差 ,可 有 效 减 小 A L T E 并 降 低 安 装 误 差 的 敏 感 性 ;在 整 个 齿 高 方 向 有 一 定 的 齿 廓 修 形 且 接 触 迹 线 角 较 小 时 ,齿 轮 副 则 有 较 大 重 合 度 ,且 齿 顶 、齿 根 载 荷 向 节 线 附 近 集 中 ,而节线附 近 的 滑 动 速 度 较 小 ,导 致 接 触 线 平 均 摩 擦 系 数 下 降 ,因 此 ,啮 合 效 率 增 加 ,齿 面 闪 温 下 降 ;齿面适配 量 过 大 时 ,接 触 线 载 荷 增 加 ,摩 擦 功 耗 增 大 # 齿合效率减小。 关 键 词 :准 双 曲 面 齿 轮 ;ease-off拓 扑 修 形 ;齿 面 闪 温 & 齿合效率;承 载 传 动 误 差 ;承载接触分析 中 图 分 类 号 :T H 132 文 献 标 志 码 :A 文 章 编 号 :0253-987X (2019)06-0044-10
- 1、下载文档前请自行甄别文档内容的完整性,平台不提供额外的编辑、内容补充、找答案等附加服务。
- 2、"仅部分预览"的文档,不可在线预览部分如存在完整性等问题,可反馈申请退款(可完整预览的文档不适用该条件!)。
- 3、如文档侵犯您的权益,请联系客服反馈,我们会尽快为您处理(人工客服工作时间:9:00-18:30)。
第11卷 第5期Vol.11No.5重庆工业管理学院学报JournalofChongqingInstituteofTechnologyManagement1997年10月Oct.1997
汽车主减速器双曲面齿轮结构参数优化设计廖林清 俞 宁 郑长松(重庆工业管理学院车辆工程学院 重庆400050)
摘要 在满足强度、应力等约束条件下,以双曲面齿轮的体积和最小为目标,对汽车减速器双曲面齿轮的结构参数进行优化设计。该方法克服了传统设计凭经验确定其结构参数的不足和繁琐,具有一定的现实意义。关键词 优化设计 主减速器 双曲面齿轮
0 引言双曲面齿轮在运转平稳性、弯曲强度、接触强度、支承刚度等方面都比螺旋锥齿轮优越,因此,双曲面齿轮在小轿车、越野车、轻型载货汽车的驱动桥主减速器中得以广泛应用。但双曲面齿轮多在传动比较大(i\4.5)时被选用,较大的传动比会导致双曲面齿轮的尺寸较大,从而减小离地间隙,影响汽车的通过性。在主减速器双曲面齿轮的传统设计中,要凭经验确定其基本参数,但由于基本参数间的互相制约,特别是双曲面齿轮的计算公式繁多,其中还有几十个公式需要迭代,因此参数确定的合理与否至关重要。本文在减速器传动比给定的条件下,以双曲面齿轮的体积和最小为目标进行优化设计,合理选择双曲面齿轮的结构参数,以提高汽车的通过性。
1 优化设计的数学模型1.1 设计变量。经分析知,影响双曲面齿轮体积和的主要参数有从动齿轮分度圆直径d2,从动齿轮齿面宽F,双曲面主动齿轮偏移距E,主动齿轮端面模数m1,主动齿轮齿宽中点螺旋角B1,主动齿轮数Z1和从动齿轮齿数Z2等。因此取设计变量为: X=[Z1,Z2,d2,m1,F,E,B1]T=[X1,X2,X3,X4,X5,X6,X7]
T
1.2 目标函数。本问题是以主减速器双曲面齿轮的体积和最小为设计目标,目标函数如下: F=V1+V2=F(Z1,Z2,d2,m1,F,E,B1)
1.3 约束条件1.3.1 从动齿轮分度圆直径d2的约束。为满足汽车的通过性要求,应保证汽车所必须的离地间隙X,故对从动齿轮分度圆直径d2有约束如下: rk-d2/2-h\X(1)
式中,h)))从动齿轮到主减速器壳的间隙与主减速器壳体厚度之和rk)))汽车车轮滚动半径另外,当以I档传递Memax时,节圆直径d2应大于或等于以下两式中的较大值,即 d2\3.46Memax#ik1#i0(2)
d2\3.460.85#G2#rk(3)
式中,Memax)))发动机最大扭矩ik1)))变速器I档速比i0)))主减速比G2)))驱动桥称重当以直接档传递Memax时,d2应满足: d2\5.74Memax#i0(4)
最后,选取以I档传递Memax时和以直接档传递Memax时所算d2值中较大者,作为主减速器从动齿轮分度圆直径的下限取值。1.3.2 主、从动齿轮齿数的约束。为了得到理想的齿面重叠系数,提高传动平稳性和降低传动噪声,齿数和应选为: Z1+Z2\45(5)
同时为取得合适的离地间隙,应选择: 7[Z1[12(6)
另外,考虑Z1与Z2之间应满足一定的传动比条件,应有约束: |Z1#i0-Z2|[vZ(7)式中,vZ)))齿数调整范围,可取1或2等值1.3.3 主动齿轮端面模数m1的约束。经推导,m1应满足如下关系式:
1.3#d2Z1#i0[m1[1.5#d2Z1#i0(8)
1.3.4 从动齿轮宽F的约束。齿面过宽并不能增大齿轮的强度和寿命,反而导致因锥齿轮轮齿小端齿沟变窄而引起切削刀头顶面宽过窄以及刀尖圆角过小、轮齿小端负荷集中、装配空间减小等情况。因而按有关推荐公式取:|F-0.155d2|[k(9)k是从动齿轮齿宽F的取值变动范围,可取1或2等值。1.3.5 双曲面主动齿轮偏移距E的约束。E值过大,将导致齿面纵向滑动的增大而引起齿面的早期磨损或擦伤;E值过小,则不能充分发挥双曲面齿轮的特点。同时,当E大于d2的20%时,发生根切的机会增多,故E的约束范围可选为:[1] 0.12d2[E[0.2d2(10)
1.3.6 主动齿轮齿宽中点螺旋角B1的约束。螺旋角的大小影响齿面重叠系数、轮齿的强度和轴向力的大小。因此螺旋角应有一个适当的范围,以使齿轮的轴向力不过大而又得到最大的重叠效果。通常汽车主减速器的螺旋角Bm=35Ü~40Ü[2],对于双曲面齿轮有Bm=(B1+B2)/2,即 35Ü[(B1+B2)/2[40Ü
式中,B2)))从动齿轮齿宽中点螺旋角B2=B1-EE)))偏移角近似值
E=sin-1(2Ed2-F)
综上所述有: 35Ü[B1-12sin-1(2Ed2-F)[40Ü(11)
#13#廖林清 俞宁 郑长松:汽车主减速器双曲面齿轮结构参数优化设计1.3.7 接触强度的约束。齿面接触平均应力RH: RH=
Cpd12#M计主#k0#ks#km#kf#103
kv#F#J式中,Cp)))材料的弹性系数d1)))主动齿轮分度圆直径d1=m1Z1
k0)))超载系数,对于一般载重汽车、矿用汽车和越野车以及液力传动的各类汽车取k0=1
ks)))尺寸系数,反映材料性质的不均匀性,与齿轮尺寸及热处理状态有关。当端面模数ms
<1.6,取ks=0.5,当ms\1.6取ks=4ms25.4。km)))齿面载荷分配系数kv)))动载系数kf)))表面品质系数J)))计算接触应力用的综合系数M计主)))主动齿轮计算扭矩 M计主=M计从/(i0#Gm)i0)))主减速器传动比Gm)))主减速器传动效率
M计从)))从动齿动计算扭矩 M计从=min{MGe,MGs}MGe)))按发动机最大扭矩和传动系最低档传动比确定的主减速器从动齿轮计算扭矩[2]
MGs)))按驱动车轮打滑扭矩确定的主减速器从动齿轮计算扭矩[2]因此接触强度约束为: RH[[RH](12)
[Rn]为齿轮材料的许用接触应力1.3.8 齿轮弯曲强度的约束。主动齿轮弯曲应力Rw1的计算公式为:
Rw1=2#M计主#k0#ks#kmkv#Fc#Z1#m21#Jw1@103式中,Jw1)))主动齿轮轮齿弯曲应力的综合系数Fc)))主动齿轮齿宽,取Fc=1.1F从动齿轮弯曲应力Rw2的计算公式为:
Rw2=2#M计从#k0#ks#kmkv#F#Z2#m22#Jw2@103
式中,Jw2)))从动齿轮轮齿弯曲应力的综合系数m2)))从动齿轮大端端面模数,取m2=d2Z2,则齿轮的弯曲强度约束为:Rw1[[Rw](13)Rw2[[Rw](14)[Rw]为齿轮材料的许用弯曲应力,综上可得该问题的优化数学模型为: X=[x1,x2,,,x7]
T
minXERTF(x)=V1+V
2
#14#重庆工业管理学院学报 s#t#gu(x)\0 (u=1,2,3,,18)
2 计算实例及优化结果分析某型越野车满载总重Ga#g=20050N,其发动机最大扭矩为Memax=172N#m,变速器I档速比为i1=3.115,轮胎为6.50R15型,rk=0.375m,后驱动桥主减速器为双曲面齿轮传动,主减速比为i0=4.55,无轮边减速器。要求设计后驱动桥主减速器的双曲面齿轮。按传统常规设计方法设计的双曲面齿轮的七个参数值如下[3]:Z1=9, Z2=41, d2=223, m1=8, F=32, E=40, B1=50Ü按以上数据得到的目标函数值F=1111544(mm3)用本文建立的优化设计数学模型采用惩罚函数法,得到的最优解为:--------------OPTIMUMSOLUTION--------------IRC=2 IQU=35 IXF=174R=.200000E+00FO=.844120E+06X: .867783E+01.389865E+02.190008E+03.625851E+01.284592E+02
X: .228194E+02.467533E+02
FX=.843885E+06GX: .167783E+01.332217E+01.997648E+00.235163E-02.266433E+01
GX: .799917E+02.830078E-02.255902E-02.959895E+00.199206E+01GX: .793976E-02.341259E+02.184281E-01.151822E+02.253963E-01
GX: .618259E-01.909919E+04.369881E+03.192895E+03HX: .000000E+00
Stop-Programterminated.将有些参数进行圆整或标准化处理后有:X*=[x1,x2,x3,,x7]T=[Z1,Z2,d2,m1,F,E,B1]T
=[9,41,190,6.5,29,24,50Ü]T此时目标函数值F(X*)=861575.2(mm3)vF=F-F*F@100%=1111544-861575.21111544@100%=22.5%优化结果分析:第一,用本方法设计的双曲面齿轮的体积比常规设计的要小22.5%,这样有利于减小主减速器的体积,提高汽车的通过性。第二,比较优化设计与常规设计的结果,可以发现优化设计的偏移距E比常规设计的要小得
#15#廖林清 俞宁 郑长松:汽车主减速器双曲面齿轮结构参数优化设计