GMP体系文件物料平衡管理规程
GMP物料平衡与收率

实施《药品生产质量管理规范》(GMP)的一个重要目标是减少可能存在的混淆和交叉污染,保证药品质量。
物料平衡是生产管理过程中防止差错、混淆的一项重要措施,加强物料平衡的管理,有利于及时发现物料的误用和非正常流失,确保药品的质量。
我国《药品生产质量管理规范》(1998年修订) 第六十七条明确规定“每批产品应按产量和数量的物料平衡进行检查,如有显著差异,必须查明原因,在得出合理解释,确认无潜在质量事故后,方可按正常产品处理”。
因此,每批产品在生产过程中各个关键工序都应进行物料平衡的计算,印刷性包装材料在使用时也应进行数额平衡的计算以达到防止差错的目的。
1.物料平衡与收得率物料平衡是指产品或物料的理论产量或理论用量与实际产量或用量之间的比较,并适当考虑可允许的正常偏差。
根据物料平衡的概念,可得出物料平衡的计算公式:实际产量或用量物料平衡= ×100 %理论产量或用量物料平衡与收得率是两个不同的概念,在应用上是有所区别的,收得率的计算是为了取得批次生产产品(中间产品) 的收得比率进行成本核算,收得率的计算有时会有很大的差别,因为生产过程中产品的数量会受到多种因素的影响,如内包材质量、人员操作、机器原因以及批次数量的大小都会改变废品数的数量。
当生产过程处在正常受控的情况下,物料平衡的计算结果是相对比较稳定的,应接近100%。
一旦生产过程中物料出现差错,物料平衡的结果将超出正常范围,所以物料平衡比收得率更能体现差错的发生。
下面举一实例说明物料平衡在生产中的应用:有一批银翘散进行分装,计算产品投入的理论产量为20000袋,分装后中间产品数为19400袋,清场后得到产品的废料量为5600袋,同时进行收得率和物料平衡的计算,得到收得率为97%,物料平衡为125%。
由计算结果可看出,产品的收得率在正常范围内而物料平衡大大超出100%,出现了异常情况,可见该批产品在生产过程中可能出现差错,所以应对整个分装工序的每一个步骤进行认真查找,核对数据,检查出差错发生的原因,如可能是生产前投料量计算错误,或前批产品废品数未及时清除,或其他批号产品混入本批产品产生混批。
药品GMP物料平衡管理作业指导书

ABC药品有限公司药品生产质量管理体系生产管理文件2020年最新版编制: 日期:审核: 日期:批准: 日期:发放范围:公司各部门2020年01月01日生效目录序号内容页码1目的 (3)2 适用范围 (3)3职责 (3)4 内容 (3)5 记录要求 (4)5 培训 (4)文件更改履历 (5)1 目的建立物料平衡管理规定,明确检查标准,严格进行收率控制,防止生产过程中发生差错和混淆。
2 范围各车间各主要工序。
3 责任车间主任、工艺员、班组长、质监员有按本规定执行的责任。
4 内容4.1 建立物料平衡检查标准,掌握生产过程中物料收率变化,进行严格的收率控制,使之在合理范围之内,这是防止差错和混淆的有效方法之一。
4.2 物料平衡计算单位:固体制剂车间制粒、整粒总混、压片、胶囊填充工序以重量为单位计算,其它工序以数量为单位计算。
4.3 需要计算物料平衡的主要工序:a.制粒 b.整粒总混 c.压片 d.胶囊填充 e.内包 f.外包4.4 物料平衡计算的基本公式:理论值:为按照所用原料(包装材料)理论产量(在生产中无任何损失或差错的情况下得出的最大数量)。
实际值:为生产过程中实际产出量。
4.5 物料平衡标准:固体制剂车间各工序中间产品、成品的物料平衡值定为理论值的95へ100%,凡物料平衡值在此范围之内,均属正常,经车间工艺员检查签字、质监员复核签字,方可递交下工序。
4.6 偏差处理凡物料平衡值高于或低于允许范围者,应立即贴上“待检”标志,不能递交下工序,并填写偏差通知单,报车间主任及质监员按“偏差处理程序”进行调查,采取处理措施,并详细记录。
文件更改履历文件更改履历。
物料平衡管理规定-

9 文件变更历史
版本号 0 1
生效日期
变更描述 为规范公司物料平衡的管理而起草该文件 根据公司组织机构调整进行换版
2
根据2010版GMP要求及公司组织机构调整换
版
变更人
ICH Q7a
2000年11月
《药品生产质量管理规范》 2010年修订
《兽药生产质量管理规范》 2002年6月
3 术语
物料平衡:产品或物料实际产量或实际用量及收集到的损耗之和与 理论产量或理论用量之间的比较,并考虑可允许的偏差范围。
4 职责
4.1 各生产单位负责本单位物料平衡的管理。
4.2 质量保证部负责对公司各产品生产单位物料平衡管理情况的监 督、检查、确认。
5 管理规定
5.1 为了避免和及时发现差错与混淆,各产品生产单位每个关键工序 要计算平衡率、进行物料平衡控制。
5.2 每个产品各关键工序的批生产记录以及工艺规程中都必须明确规 定平衡率的计算方法以及平衡率合格范围。
5.3 平衡率计算的基本要求
5.3.1 平衡率计算:
实际值+可回收量+抽样量
理论值 平衡率= ×100%
Байду номын сангаас
其中:理论值:按照所用的原料(辅料、包装材料)量,在生产中 无任何损失或差错的情况下得出的最大数量。
实际值:生产过程中实际产出量。
抽样量:生产过程中抽取样品量。
可回收量:结余料与尾料、落地粉、污粉等。
..2 平衡率合格范围的确定方法 由生产单位收集20~25批连续正常生产产品的各关键工序平衡率数 据,按照数理统计方法计算出平衡率合格范围。
5.4.3 每年应由质量保证部驻车间质量员对各工序平衡率及产品的总 体物料平衡进行总结,为工艺改进、技术革新及技术标准文件的修订提 供参考。
GMP物料平衡管理规程
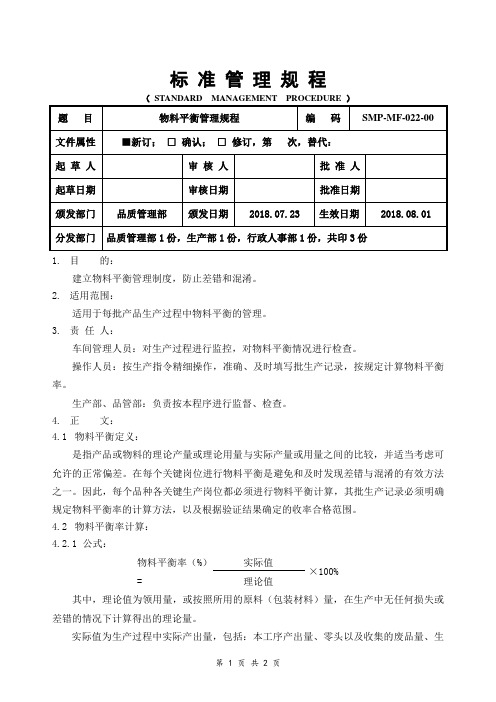
标准管理规程(STANDARD MANAGEMENT PROCEDURE )1.目的:建立物料平衡管理制度,防止差错和混淆。
2.适用范围:适用于每批产品生产过程中物料平衡的管理。
3.责任人:车间管理人员:对生产过程进行监控,对物料平衡情况进行检查。
操作人员:按生产指令精细操作,准确、及时填写批生产记录,按规定计算物料平衡率。
生产部、品管部:负责按本程序进行监督、检查。
4.正文:4.1物料平衡定义:是指产品或物料的理论产量或理论用量与实际产量或用量之间的比较,并适当考虑可允许的正常偏差。
在每个关键岗位进行物料平衡是避免和及时发现差错与混淆的有效方法之一。
因此,每个品种各关键生产岗位都必须进行物料平衡计算,其批生产记录必须明确规定物料平衡率的计算方法,以及根据验证结果确定的收率合格范围。
4.2物料平衡率计算:4.2.1公式:物料平衡率(%)= 实际值×100% 理论值其中,理论值为领用量,或按照所用的原料(包装材料)量,在生产中无任何损失或差错的情况下计算得出的理论量。
实际值为生产过程中实际产出量,包括:本工序产出量、零头以及收集的废品量、生产中取样量(检品)、不合格品量等。
无法收集的不合格物料(如捕尘系统、真空系统、管道系统中的残余物等)除外。
1.1.1在生产过程中如有跑料、散袋后跌落在地上的物料,应及时通知车间主任及QA,并详细记录损失数量和过程。
其损失数量加在实际值的范围之内计算。
4.2.2上工序移交下来的有效物料并经复核的数量,为下工序计算的理论值。
4.2.3需进行物料平衡率计算的主要岗位:称量、配料、压片、包衣、铝塑、包装。
4.2.4物料平衡计算单位:4.2.5制剂成品:以万瓶、万罐、万片/万粒计算。
4.2.6固体用铝箔、PVC以重量(kg)计算,其他内包材和外包装材料以张、只计算。
4.3制定物料平衡限度方法:采用根据设备、设施情况估计一定范围,再积累一定数量批次产品的物料平衡率数据,对数据进行统计计算而得出平衡限度。
制药企业生产过程物料管理规程(GMP)

目的:本程序依据《药品生产质量管理规范》(2010修订版)规定了生产过程物料的管理程序。
范围:本程序适用于生产过程中各物料的管理。
职责:质量管理部、生产部内容:1原、辅料1.1分厂生产班组根据生产作业指令,由领料人员填写限额领料单,经分厂厂长签字后,领料单可作为领料凭证。
1.2领料人员依据领料单,于原料库、领取所需物料,现场检查包装情况并核对品名、批次、规格、状态标识、数量,如有不符不得领用。
1.3送料人员应及时将分厂领取的原料、运至相应工序,生产前逐件检查核对。
1.4原料在生产加工过程中不得直接接触地面。
3包装材料3.1分厂包装班班长依据批包装指令填写限额领料单,经分厂厂长复核签字后,交包材库备料。
3.2分厂包装班班长于包材库领取包材,检查合格状态标志及外包装,核对品名、数量、规格、编号及配套情况,如有疑问,待核实后再领取。
3.3包装材料计量或计数发放3.4领料人员应及时将领取的包装材料送至工序中并当面检查外包装的完好性,核对品名、规格、编号、合格状态标志、数量,经双方确认后,领料人员在库房台帐中签字。
3.5包材领至分厂,由分厂包装班班长负责管理、标识并登记台帐及发放使用情况,对需打码的包材负责打码后各类包材数量的登记。
3.6包装前根据批包装指令,核对所领包装物料是否与批包装指令一致,有疑问,应立即停止,待确认后执行。
3.7包装过程包装材料分类定位定置管理并严格标识。
3.8班组长负责班组实际使用情况,每班结束后,及时清点包材数量,做好记录,每批结束后,应及时清点数量,做好退料交接。
3.9已经印有批号而未使用的包材,按销毁管理程序进行;未印码的包材按规定退库。
4中间产品4.1分厂之间及工序之间,领取中间产品时,必须双方进行当面核对状态标志、品名、规格、批次、数量,如有疑问,应停止领交,经确认后,继续进行交、领料。
4.2中间产品必须按品种、批次交中间站管理,不能留在工序中以免发生差错,中间站所存放物料,应有明显的状态标志,不同品种、批次之间要有一定距离,并按规定挂状态标志。
GMP物料平衡管理规程

页码:文件编号:生效日期: 再版日期:第1页/共2页SMP-PM-01003-1标准管理规程STANDARD MANAGEMENT PROCEDURESubject题目:物料平衡管理规程Issued by颁发部门:质量部Written by起草人:Date日期:Dept. Head Approval 部门主管审核:Date日期:QA Director Approval QA 主管审核:Date日期:Approved by批准:Date日期:Dispense分发:总经理、质量部、生产部、商务部、行政人事部1.目的建立物料平衡的管理规程,严格物料管理,防止物料流失,控制成品率;防止差错和混药事故的发生。
2.适用范围适用于每批产品生产过程中物料平衡的管理。
3.责任者生产部、各生产车间、商务部、质量部相关人员。
4.内容4.1.在每个关键工序计算收率、进行物料平衡,是避免和及时发现差错与混料的有效方法之一。
因此,每个品种各关键生产工序的批生产记录(批包装记录)都必须明确规定收率的计算方法,以及根据验证结果确定的收率合格范围。
4.2.收率计算的基本要求:4.2.1.收率计算:实际值收率=─────────×100%理论值其中:理论值:按照所用的原料(包装材料)量,在生产中无任何损失或差错的情况下得出的最大数量。
实际值:生产过程中实际产出量,包括:本工序产出量、生产中取得样品量(检品)4.2.2.在生产过程中如有跑料现象和可见损耗,应及时通知车间管理人员及QA部门QA检查员,并详细记录跑料可见损耗过程及数量。
跑料和可见损耗数量也应计入物料平衡之中,加在实际值的范围之内。
页码:文件编号:生效日期: 再版日期:第2页/共2页SMP-PM-01003-1标准管理规程STANDARD MANAGEMENT PROCEDURESubject题目:物料平衡管理规程Issued by颁发部门:质量部4.2.3.如若实际收率在规定的收率范围内,即视为物料平衡合格,一般收率应在97%-101%之间。
中药制剂在GMP认证中的物料平衡问题
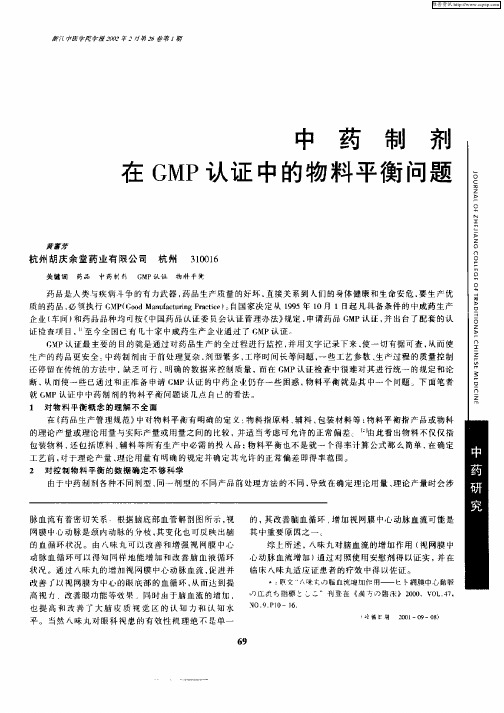
药 品是人类 与疾病 斗争 的有 力武 器 . 品生产 质量的好 坏 , 药 直接关 系到人们 的身体 健康 和生命安危 , 要生 产优 质的药 品 , 必须 执行 G P G o au c r gPat e 。 M ( odM n f t i r i ) 自国家决定 从 19 年 l a un cc 95 O月 1日起 凡具备条 件 的 中成药生 产 企业 ( 间) 车 和药 品品种 均 呵按 《 中国药 品认 证委 员会认证 管理办 法》 定 , 规 申请 药品 G P认 证 . 出 台了配套 的认 M 并 证 检查项 目. 今 全 国已有几十家 中成药 生产企 、 通过 了 G P认证 。 至 【 M G P认证最 主要 的 目的就 是通过 对药 品生 产 的全 过程进 行监 控 , M 并用 文字记 录下来 , 使一切 有据可 查 , 而使 从 生产 的药 品更 安全 中药制 剂 由于前处理 复杂 , 型繁 多 , 剂 工序 时间长等 问题 , 些工艺 参数 产过程 的质量 控制 一 生 还 停 留在传统 的方法 中 , 缺乏 可行 、 明确 的数 据来 控制质量 . 而在 G 认 证检 查 中很难 对其进行 统一 的规定 和论 MP 断 . 而使一 些 已通 过和正 准备 申请 G P认证 的中药企 业仍 存一些 困惑 , 从 M 物料平 衡就 是其 中一个 问题 。下 面笔者 就 G P认证 中中药 制 剂的物料平 衡 问题谈 几 点 自己的看法 。 M
及 许 多问题 。 以常 见的剂型丸剂 、 片剂 为倒 : 先说 丸剂 , 丸剂糊 浓 蜡
类型 , 冰蜜丸. 不同 的产 品 由于原药材 性质 的不 同 , 细粉所需 的炼 蜜量 就不 同 , 大补 阴丸 和六 味地黄 丸 , 其 如 大补 阴丸 的质量标 准 【 法 ] 制 中规定 : …每 lo … og粉末加炼 蜜 1 ~1g与适量 的水 , 0 5 泛丸 .… ・; - 味地黄 丸 的质量 标 准【 法] 制 中规定 : ……每 10 粉末加炼 蜜 3 4 g 0g 0~ 5 与适量 的水 , 丸 , 泛 …… 。 即使是 同一产 品 , 由于不 同批次 的原 药材 其所需 的炼蜜也 有所不 同 。 可见对 于水 蜜丸其 炼蜜量 的多少是确 定每 次理论产量 的关键 所在 。 片剂 . 片剂 可分 为浸 膏片 、 浸膏 片和全 粉片 , 慢 膏 片和半幔 膏片 的物料平衡 与其投料 方式 密切相 关 , 半 是以膏 投料还是 以料投 料 的问题 。就 这 问题 国家标准也 在 不断 的加 以修改使 其更科 学更合 理。比如复方 丹参 片 , 19 在 95年版《 国药 典》 中 复 方 丹参片质 量标准 中规定 : 处方 ] 参浸膏 2 三七 1- 冰片 .制 法 ] 【 丹 1g 5 4g 1 [ 以上 三味 , 丹参 浸膏 系取丹参 提取 三次, 第一 次加 乙醇 回流 15 时 , .小 滤过 , 滤液 回收 乙醇 , 缩至相对 密度为 13 (5 0Cj 第二 次加 5 %乙醇 回 浓 .0 5 ~6  ̄ ; 0 流 15 时 . .小 滤过 ; 第三次 加水 回流 2 时 , 小 滤过 , 并第 二 、 合 三次滤 液 , 回收 乙醇 , 浓缩 至相对 密度为 14 (5~ . 5 0 6 ℃) 与第一 次的浓缩液 合并 , 0 , 混匀 , 成相对 密度为 13 ~13 (5~ 0£ 的缦 膏 . 制 .5 .9 5 6 a l 即得 。 三七 粉碎成 细粉 , 将 与 丹 参浸膏 拌匀 . 干燥 . 制成 颗粒 , 将冰 片研 细 , 上述 颗粒混匀 . 制成 10 与 压 0 0片 , 或包糖 衣 . 即得 牲 此标 准 中是 以 膏 投料 , 即根据 丹参 浸膏 的量来折算 所投 的j七 的量和冰 片的量 , 由于每批浸膏 得率 的不同 , 每批产 品 的理论 产量 都要求技 术人员进 行正 确 的折 算和控制 。往 20 00年版《 中国药 典》 复方 丹参片 的质量标 准 中规 定 :处方 ] 【 丹参 40 5g 三七 11 冰片 .制法 ] 4g [ 以上 三味 , 丹参 提取三次 , 第一 次加乙 醇 回流 15小时 , 过 ; 液 回收 乙醇 . . 滤 滤 浓缩至 相对 密度为 13 c5 0C】 第 二次加 5 %乙醇 回流 15 。 5 ~6  ̄ ; 0 . 小时 , 滤过 : 三次加水 回流 2 时 , 第 小 滤过 , 合并 第二 、 三 次滤 液 . 回收 乙醇 , 浓缩 至相对 密度为 14 (5 0 , .0 5 ~6 ℃) 与第一 次的浓 缩液合并 , 混匀 , 制成相 对密度 为 13 ~13 5 . 9 (5 l 5 ℃ 的浸膏 。将 { 七粉碎 成细粉 , 与丹 参清膏拌匀 , 下燥 . 成颗粒 , 冰片研 细 , 制 将 与上述 颗粒混 匀 , 压制 成 10 00 片, 或包 糖衣或 薄 膜表 , 即得 。 牲 此标 准 中复方丹参 片的投料更 改为 以料投料 , 这更 有利 于复方 丹参 片生产过程 的控 制 , 也使 物料 平衡 的控制更 严格更合 理 。中药制 剂中还有许 多其他 的剂型 , 都涉 及类似 的问题 , 因此中药生 产 企业 在进 行物料平衡 的规 定时 部要进行科 学 的摸 索 ,同时在生 产工艺 、设备 的不 断更新 、改进 中,数据 也应 随之 改。G | IP的实施 向我们 提出 了一 个新 的概念一 验证 ,  ̄ 即证 明任何 程序 、 生产过程 、 设备 、 料 、 物 活动或 系统确 实能达
GMP对物料及生产管理的要求

(七)管理制度和记录
物料管理制度应全面、具体、操作性强、批 准程序齐全、存档规范。 记录原始、真实、准确、完整、有可追溯性。
(八)几点工作建议
1、认真学习贯彻国家有关规定,了解掌握政策, 做好培训,便于做好物料管理工作; 2、供应、仓库、质量、生产等有关管理部门相互 配合,理清程序、分清职责、衔接紧密,保证物料 管理,降低成本; 3、出现问题及时准确查找原因,尽可能减少损失。 4、新版GMP的学习
一、范围与内容概述
生产管理是企业一切管理的基础和关键,良 好的生产作业管理系统和严密的控制系统, 将成为企业在不断增强的经济竞争中得以生 存的重要因素。 生产管理的目标:稳定的产品质量、可靠的 交货期、降低时间、空间、人力、资金等成 本,具有良好的“柔性”生产能力。
二、物料管理
(三)物料的发放和使用
3、批号:不同药品有不同“批”的划分原则, 见GMP附录。分为: 无菌药品、非无菌药品、原料药、生物制品、 放射性药品、中药制剂、中药饮片、医用氧、 (药用辅料)等 4、货位号
(三)物料的发放和使用
记录: 1、货位卡:内容包括各项物料编号,品名、规格、 生产厂家、供货商、检验单号、入出库时间、数量 (包括退库、取样)、结存数、来源、去向、发货 人、领料人等 2、分类账:按物料类别或库房分类设置台账,日清 月结,盘亏盘盈。 3、做到账、卡、物相符
(四)供应商审计
与供应商签订采购合同,保证供货质量。包 括:名称、规格/标准、数量、包装等药品信 息
(五)特殊管理药品
麻醉药品、精神药品的采购、验收、储存、保管、 发放、使用、销毁按《麻醉药品和精神药品管理条 例》(国务院第442号令)执行。强调安全意识, 杜绝非法生产、经营活动。 (GMP4401*) 毒性药品(药材)管理按照《医疗用毒性药品管理 办法》(GMP4401*、4410*) 菌毒种按规定验收、储存、保管、使用、销毁 (GMP4402*)
- 1、下载文档前请自行甄别文档内容的完整性,平台不提供额外的编辑、内容补充、找答案等附加服务。
- 2、"仅部分预览"的文档,不可在线预览部分如存在完整性等问题,可反馈申请退款(可完整预览的文档不适用该条件!)。
- 3、如文档侵犯您的权益,请联系客服反馈,我们会尽快为您处理(人工客服工作时间:9:00-18:30)。
目的:建立一个物料平衡的工作标准,掌握生产过程中物料平衡,进行严格的收率控制,防止发生差错和出现混药现象。
范围:产品生产过程中的各个关键工序
责任人:岗位操作人员、车间管理人员、质量保证部、生产制造部。
内容:
1、在每个关键工序计算收率,进行物料平衡是避免或及时发现差错与混药的有效方法之一,因此,每个品种关键生产工序的批生产记录(批包装记录)都必须明确规定物料平衡的计算方法,以及根据验证结果确定收率范围。
2、物料平衡计算的基本要求
2.1 物料平衡计算公式:物料平衡=(产出量+尾料量)/(总投入量)× 100%
产出量:生产过程中实际产出量,不包括收集的废品量,生产中取得样品量(检品),丢弃的不合格物料。
尾料量:生产过程中产生的药头数量等。
总投入量:生产过程实际投入的数量。
2.2 在生产过程中如有跑料现象,应及时通知车间管理人员及质量保证部质量监督员,并详细记录跑料过程及数量。
跑料量也应计入物料平衡中,加在实际范围之内。
3、物料平衡计算单位
3.1 固体以重量计算。
3.2 液体以体积或重量计算。
4、数据处理
4.1 凡物料平衡在规定范围之内,经质监员审核,可以递交下道工序。
4.2 凡物料平衡高于或低于合格范围,应立即贴“待查”标志,不能递交下道工序,并填写偏差通知单,通知车间管理人员及质监员按“生产过程偏差处理管理规程”进行调查处理,并如实记录。
4.3 质量保证部会同生产制造部定期对各工序收率及产品的总体物料平衡进行
核算,并进行回顾性验证,为工艺改进、技术革新及技术文件的修订提供参考。