物流成本控制中英文对照外文翻译文献
成本控制外文文献(Costcontrol,foreignliterature)
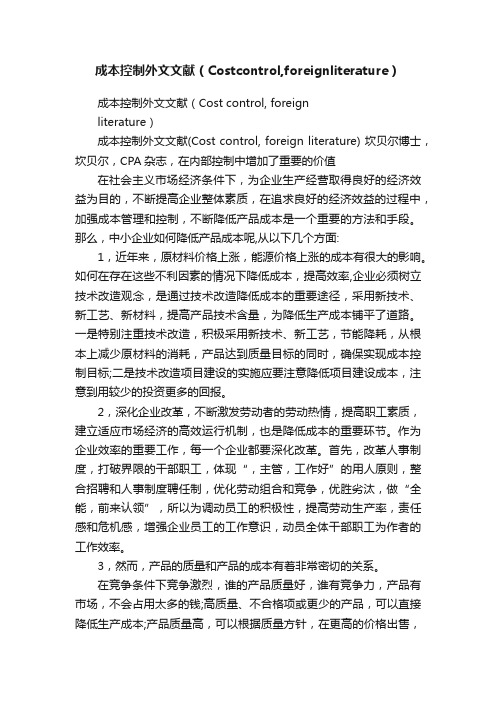
成本控制外文文献(Costcontrol,foreignliterature)成本控制外文文献(Cost control, foreignliterature)成本控制外文文献(Cost control, foreign literature) 坎贝尔博士,坎贝尔,CPA杂志,在内部控制中增加了重要的价值在社会主义市场经济条件下,为企业生产经营取得良好的经济效益为目的,不断提高企业整体素质,在追求良好的经济效益的过程中,加强成本管理和控制,不断降低产品成本是一个重要的方法和手段。
那么,中小企业如何降低产品成本呢,从以下几个方面:1,近年来,原材料价格上涨,能源价格上涨的成本有很大的影响。
如何在存在这些不利因素的情况下降低成本,提高效率,企业必须树立技术改造观念,是通过技术改造降低成本的重要途径,采用新技术、新工艺、新材料,提高产品技术含量,为降低生产成本铺平了道路。
一是特别注重技术改造,积极采用新技术、新工艺,节能降耗,从根本上减少原材料的消耗,产品达到质量目标的同时,确保实现成本控制目标;二是技术改造项目建设的实施应要注意降低项目建设成本,注意到用较少的投资更多的回报。
2,深化企业改革,不断激发劳动者的劳动热情,提高职工素质,建立适应市场经济的高效运行机制,也是降低成本的重要环节。
作为企业效率的重要工作,每一个企业都要深化改革。
首先,改革人事制度,打破界限的干部职工,体现“,主管,工作好”的用人原则,整合招聘和人事制度聘任制,优化劳动组合和竞争,优胜劣汰,做“全能,前来认领”,所以为调动员工的积极性,提高劳动生产率,责任感和危机感,增强企业员工的工作意识,动员全体干部职工为作者的工作效率。
3,然而,产品的质量和产品的成本有着非常密切的关系。
在竞争条件下竞争激烈,谁的产品质量好,谁有竞争力,产品有市场,不会占用太多的钱;高质量、不合格项或更少的产品,可以直接降低生产成本;产品质量高,可以根据质量方针,在更高的价格出售,在销售收入中的比重相对降低成本;高质量的产品,才能赢得更多的客户,增加销售,降低销售成本;产品质量高,实际上也节省了能源和原材料;产品质量高,可节省人工和管理费用,这肯定会降低成本。
第三方物流成本中英文对照外文翻译文献
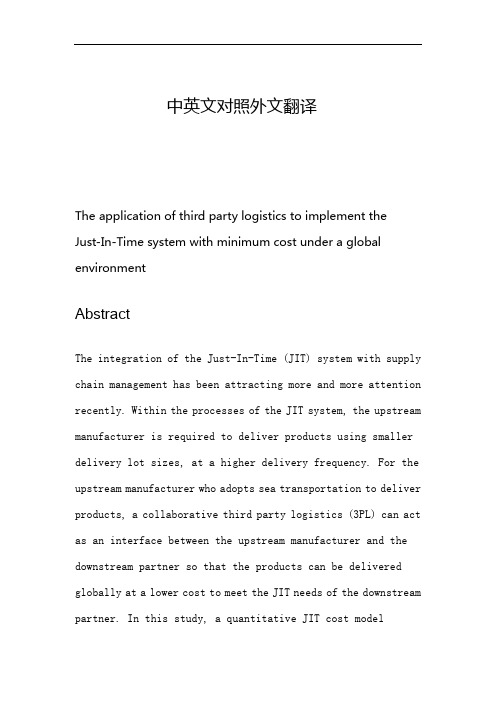
中英文对照外文翻译The application of third party logistics to implement theJust-In-Time system with minimum cost under a global environmentAbstractThe integration of the Just-In-Time (JIT) system with supply chain management has been attracting more and more attention recently. Within the processes of the JIT system, the upstream manufacturer is required to deliver products using smaller delivery lot sizes, at a higher delivery frequency. For the upstream manufacturer who adopts sea transportation to deliver products, a collaborative third party logistics (3PL) can act as an interface between the upstream manufacturer and the downstream partner so that the products can be delivered globally at a lower cost to meet the JIT needs of the downstream partner. In this study, a quantitative JIT cost modelassociated with the application of third party logistics is developed to investigate the optimal production lot size and delivery lot size at the minimum total cost. Finally, a Taiwanese optical drive manufacturer is used as an illustrative case study to demonstrate the feasibility and rationality of the model.1. IntroductionWith the globalization of businesses, the on-time delivery of products through the support of a logistics system has become more and more important. Global corporations must constantly investigate their production systems, distribution systems, and logistics strategies to provide the best customer service at the lowest possible cost.Goetschalckx, Vidal, and Dogan (2002) stated that long-range survival for international corporations will be very difficult without a highly optimized, strategic, and tactical global logistics plan. Stadtler (2005) mentions that the activities and processes should be coordinated along a supply chain to capture decisions in procurement, transportation, production and distribution adequately, and many applications of supplychain management can be found in the literature (e.g. Ha and Krishnan, 2008, Li and Kuo, 2008 and Wang and Sang, 2005). Recently, the study of the Just-In-Time (JIT) system under a global environment has attracted more attention in the Personal Computer (PC) related industries because of the tendency towards vertical disintegration. The JIT system can be implemented to achieve numerous goals such as cost reduction, lead-time reduction, quality assurance, and respect for humanity (Monden, 2002). Owing to the short product life cycle of the personal computer industry, downstream companies usually ask their upstream suppliers to execute the JIT system, so that the benefits, like the risk reduction of price loss incurred from inventory, lead times reduction, on-time delivery, delivery reliability, quality improvement, and lowered cost could be obtained (Shin, Collier, & Wilson, 2000). According to the JIT policy, the manufacturer must deliver the right amount of components, at the right time, and to the right place (Kim & Kim, 2002). The downstream assembler usually asks for higher delivery frequency and smaller delivery lot sizes so as to reduce his inventory cost in the JIT system (Kelle, khateeb, & Miller, 2003). However, large volume products are conveyed using sea transportation, using larger delivery lotsizes to reduce transportation cost during transnational transportation. In these circumstances, corporations often choose specialized service providers to outsource their logistics activities for productivity achievement and/or service enhancements (La Londe & Maltz, 1992). The collaboration of third party logistics (3PL) which is globally connected to the upstream manufacturer and the downstream assembler will be a feasible alternative when the products have to be delivered to the downstream assembler through the JIT system. In this study, the interaction between the manufacturer and the 3PL will be discussed to figure out the related decisions such as the optimal production lot size of the manufacturer and the delivery lot size from the manufacturer to the 3PL, based on its contribution towards obtaining the minimum total cost. In addition, the related assumptions and restrictions are deliberated as well so that the proposed model is implemented successfully. Finally, a Taiwanese PC-related company which practices the JIT system under a global environment is used to illustrate the optimal production lot size and delivery lot size of the proposed cost model.2. Literature reviewThe globalization of the network economy has resulted in a whole new perspective of the traditional JIT system with the fixed quantity-period delivery policy (Khan & Sarker, 2002). The fixed quantity-period delivery policy with smaller quantities and shorter periods is suitable to be executed among those companies that are close to each other. However, it would be hard for the manufacturer to implement the JIT system under a global environment, especially when its products are conveyed by transnational sea transportation globally. Therefore, many corporations are trying to outsource their global logistics activities strategically in order to obtain the numerous benefits such as cost reduction and service improvement. Hertz and Alfredsson (2003) have stated that the 3PL, which involves a firm acting as a middleman not taking title to the products, but to whom logistics activities are outsourced, has been playing a very important role in the global distribution network. Wang and Sang (2005) also mention that a 3PL firm is a professional logistics company profiting by taking charge of a part or the total logistics in the supply chain of a focal enterprise. 3PL also connects the suppliers, manufacturers, and the distributors in supply chains and provide substance movement andlogistics information flow. The core competitive advantage of a 3PL firm comes from its ability to integrate services to help its customers optimize their logistics management strategies, build up and operate their logistics systems, and even manage their whole distribution systems (Wang & Sang, 2005). Zimmer (2001) states that production depends deeply on the on-time delivery of components, which can drastically reduce buffer inventories, when JIT purchasing is implemented. When the manufacturer has to comply with the assembler under the JIT system, the inventories of the manufacturer will be increased to offset the reduction of the assembler’s inventories (David and Chaime, 2003, Khan and Sarker, 2002 and Sarker and Parija, 1996).The Economic Order Quantity (EOQ) model is widely used to calculate the optimal lot size to reduce the total cost, which is composed of ordering cost, setup cost, and inventory holding cost for raw materials and manufactured products (David and Chaime, 2003, Kelle et al., 2003, Khan and Sarker, 2002 and Sarker and Parija, 1996). However, some issues such as the integration of collaborative 3PL and the restrictions on the delivery lot size by sea transportation are not discussedfurther in their studies. For the above involved costs, David and Chaime (2003) further discuss a vendor–buyer relationship to include two-sided transportation costs in the JIT system. Koulamas, 1995 and Otake et al., 1999 describe that the annual setup cost is equal to the individual setup cost times the total number of orders in a year. McCann, 1996 and Tyworth and Zeng, 1998 both state that the transportation cost can be affected by freight rate, annual demand, and the products’ weight. Compared to the above studies which assume that the transportation rate is constant per unit, Swenseth and Godfrey (2002) assumed that the transportation rate is constant per shipment, which will result in economies of scale for transportation. Besides, McCann (1996) presented that the total logistics costs are the sum of ordering costs, holding costs, and transportation costs. A Syarif, Yun, and Gen (2002) mention that the cost incurred from a distribution center includes transportation cost and operation cost. Taniguchi, Noritake, Yamada, and Izumitani (1999) states that the costs of pickup/delivery and land-haul trucks should be included in the cost of the distribution center as well. The numerous costs involved will be formulated in different ways when the manufacturer operates the JIT system associatedwith a collaborative 3PL under a global environment. Kreng and Wang (2005) presented a cost model, which can be implemented in the JIT system under a global environment, to investigate the most appropriate mode of product delivery strategy. They discussed the adaptability of different transportation means for different kinds of products. In this study, the implementation of sea transportation from the manufacturer to the 3PL provider will be particularized, and the corresponding cost model will also be presented to obtain the minimum total cost, the optimal production lot size, and the optimal delivery lot size from the manufacturer to the 3PL provider. Finally, a Taiwanese company is used for the case study to illustrate and explore the feasibility of the model.3. The formulation of a JIT cost model associated with the 3PL Before developing the JIT cost model, the symbols and notations used throughout this study are defined below:B3PL’s pickup cost per unit product (amount per unit)Cj3PL’s cost of the j th transportation container type, where j= 1, 2, 3,…,n (amount per year)DP annual demand rate of the product (units per year)Dr annual demand of raw materials (units per year)D customers’ demand at a specific interval (units per shipment)E annual inventory holding cost of 3PL (amount per year)F transportation cost of the j th transportation containertype from the manufacturer to the 3PL, where j= 1, 2, 3, …, n (amount per lot)F freight rate from the 3PL provider to the assembler (amount per kilogram)Hp inventory holding cost of a unit of the product (amount per year)Hr inventory holding cost of raw materials per unit (amount per year)Ij average product inventory of the j th transportation container type in the manufacturer, where j= 1, 2,3, …, n (amount per year)I annual profit margin of 3PL (%)K ordering cost (amount per order)Kj number of shipments from the 3PL provider to the assembler when the delivery lot size from the manufacturer to the 3PL provider is Qj with the j th transportation container type, where j= 1, 2, 3, …, n(kj=Qj/d)M∗ optimal number of shipments that manufacturer delivers with the optimal total costactual number of shipments of the j th transportation container type with the minimum total cost, where j= 1, 2, 3, …, nMj number of shipments of the j th transportation container type, where j= 1, 2, 3, …, nnumber of shipments of the j th transportation container type with the minimum total cost, where j= 1, 2, 3, …, nN∗ optimal production lot size of the manufacturer (units per lot)optimal production lot size of the j th transportation container type, where j= 1, 2, 3, …, n(units per lot)Nj production lot size of the j th transportation container type, where j= 1, 2, 3, …, n (units per lot)Nr ordering quantity of raw material (units per order)P production rate of product (units per year)maximum delivery lot size of the j th transportation container type, where j= 1, 2, 3, …, n(units per lot)q∗ optimal delivery lot size of the manufacturer (units per lot)qj actual delivery lot size of the j th transportation container type, where j= 1, 2, 3, …,n (units per lot)Rj loading percentage of the j th transportation container type, where j= 1, 2, 3, …,n(Rj=qj/Qj)Rj real number of shipments from the 3PL provider to the assembler when the delivery lot size from the manufacturer to the 3PL provider is qj with the j th transportation container type, where j= 1, 2, 3, …,n(rj=qj/d)S setup cost (amount per setup)W weight of product (kilogram per unit)Λ quantity of raw materials required in producing one unit of a product (units)Tomas and Griffin (1996) considered that a complete supply chain should consist of five participants, including the raw materials supplier, the manufacturer, the assembler, the warehouse operator, and the consumer. This study mainly focuses on the relationships among the manufacturer, the 3PL provider and the assembler within the JIT system under a global environment. In order to achieve the fixed quantity-period JIT delivery policy, which implies that the actual delivery lot size has to be determined by identifying the downstream assembler’s needs instead of the upstream manufacture’s economical delivery lot size, higher transportation costs with higher delivery frequency are necessary. Since the JIT system are more appropriately executed among those companies that are close to each other, a collaborative 3PL connected the upstream manufacture with the downstream assembler is necessary when the products have to be delivered from the upstream manufacture to the downstream assembler by sea transportation over a long distance. This study proposes a JIT cost model to obtain the optimal production lot size, the actual delivery lot size, the most suitable transportation container type, and the exact number of shipments from the manufacturer to the 3PL provider at the minimum total cost.This study makes assumptions of the JIT system as follows: (1) There is only one assembler and only one manufacturer for each product.(2) The production rate of the manufacturer is uniform,finite, and higher than the demand rate of the assembler.(3) There is no shortage and the quality is consistent in both raw materials and products.(4) The demand for products that the assembler receives is fixed and is at regular intervals.(5) Qj is much greater than demand at a regular interval,d.(6) The transportation rates from the manufacturer to the 3PL and from the 3PL to the assembler are computed by the number of shipments and the product’s weight, respectively, and, (7) The space of the manufacturer’s warehouse is sufficient for keeping all inventories of products that the manufacturer produces.According to the above assumptions from (1), (2), (3) and (4), Fig. 1 illustrates the relationships among the manufacturer, the 3PL provider, and the assembler, where the Fig. 1 represents the inventory of manufacturer’s raw materials, the inventoryof products inside the manufacturer, the inventory of the 3PL provider, and the inventory of the assembler from top to bottom (Kreng & Wang, 2005). This study also adopts the Fig. 1 to demonstrate the collaboration of the 3PL provider which will be an interface connecting the manufacturer and the assembler. During the period T1, the inventory of products with the manufacturer will be increased gradually because the production quantity is larger than the demand quantity. However, during the period T2, the inventory of products will be decreased because the production has been stopped.中文翻译:在全球环境下第三方物流以最小的成本实现了Just-In-Time系统的应用摘要:JUST-IN-TIME(JIT)系统,供应链管理的整合,最近已经吸引了越来越多的关注。
物流外文文献翻译(DOC)

外文文献原稿和译文原稿Logistics from the English word "logistics", the original intent of the military logistics support, in the second side after World War II has been widely used in the economic field. Logistics Management Association of the United States is defined as the logistics, "Logistics is to meet the needs of consumers of raw materials, intermediate products, final products and related information to the consumer from the beginning to the effective flow and storage, implementation and control of the process of . "Logistics consists of four key components: the real flow, real storage, and management to coordinate the flow of information. The primary function of logistics is to create time and space effectiveness of the effectiveness of the main ways to overcome the space through the storage distance.Third-party logistics in the logistics channel services provided by brokers, middlemen in the form of the contract within a certain period of time required to provide logistics services in whole or in part. Is a third-party logistics companies for the external customer management, control and operation of the provision of logistics services company.According to statistics, currently used in Europe the proportion of third-party logistics services for 76 percent, the United States is about 58%, and the demand is still growing; 24 percent in Europe and the United States 33% of non-third-party logistics service users are actively considering the use of third-party logistics services. As a third-party logistics to improve the speed of material flow, warehousing costs and financial savings in the cost effective means of passers-by, has become increasingly attracted great attention.First, the advantages of using a third-party logisticsThe use of third-party logistics enterprises can yield many benefits, mainly reflected in:1, focus on core businessManufacturers can use a third-party logistics companies to achieve optimal distribution of resources, limited human and financial resources to concentrate on their core energy, to focus on the development of basic skills, develop new products in the world competition, and enhance the core competitiveness of enterprises.2, cost-savingProfessional use of third-party logistics providers, the professional advantages of mass production and cost advantages, by providing the link capacity utilization to achieve cost savings, so that enterprises can benefit from the separation of the cost structure. Manufacturing enterprises with the expansion of marketing services to participate in any degree of depth, would give rise to a substantial increase in costs, only the use of professional services provided by public services, in order to minimize additional losses. University of Tennessee in accordance with the United States, United Kingdom and the United States EXEL company EMST & YOUNG consulting firm co-organized a survey: a lot of cargo that enable them to use third-party logistics logistics costs declined by an average of 1.18 percent, the average flow of goods from 7.1 days to 3.9 days, stock 8.2% lower.3, reduction of inventoryThird-party logistics service providers with well-planned logistics and timely delivery means, to minimize inventory, improve cash flow of the enterprise to achieve cost advantages.4, enhance the corporate imageThird-party logistics service providers and customers is a strategic partnership, the use of third-party logistics provider of comprehensive facilities and trained staff on the whole supply chain to achieve completecontrol, reducing the complexity of logistics, through their own networks to help improve customer service, not only to establish their own brand image, but also customers in the competition.Second, The purpose of the implementation of logistics managementThe purpose of the implementation of logistics management is to the lowest possible total cost of conditions to achieve the established level of customer service, or service advantages and seek cost advantages of a dynamic equilibrium, and thus create competitive enterprises in the strategic advantage. According to this goal, logistics management to solve the basic problem, simply put, is to the right products to fit the number and the right price at the right time and suitable sites available to customers.Logistics management systems that use methods to solve the problem. Modern Logistics normally be considered by the transport, storage, packaging, handling, processing in circulation, distribution and information constitute part of all. All have their own part of the original functions, interests and concepts. System approach is the use of modern management methods and modern technology so that all aspects of information sharing in general, all the links as an integrated system for organization and management, so that the system can be as low as possible under the conditions of the total cost, provided there Competitive advantage of customer service. Systems approach that the system is not the effectiveness of their various local links-effective simple sum. System means that, there's a certain aspects of the problem and want to all of the factors affecting the analysis and evaluation. From this idea of the logistics system is not simply the pursuit of their own in various areas of the lowest cost, because the logistics of the link between the benefits of mutual influence, the tendency of mutual constraints, there is the turn of the relationship between vulnerability. For example, too much emphasis on packaging materials savings, it could cause damage because of their easy to transport and handling costs increased. Therefore, the systemsapproach stresses the need to carry out the total cost analysis, and to avoid the second best effect and weigh the cost of the analysis, so as to achieve the lowest cost, while meeting the established level of customer se rvice purposes.Third, China's enterprises in the use of third-party logistics problems inWhile third-party logistics company has many advantages, but not many enterprises will be more outsourcing of the logistics business, the reasons boil down to:1, resistance to changeMany companies do not want the way through the logistics outsourcing efforts to change the current mode. In particular, some state-owned enterprises, we reflow will also mean that the dismissal of outsourcing a large number of employees, which the managers of state-owned enterprises would mean a very great risk.2, lack of awarenessFor third-party logistics enterprise's generally low level of awareness, lack of awareness of enterprise supply chain management in the enterprise of the great role in the competition.3, fear of losing controlAs a result of the implementation of supply chain companies in enhancing the competitiveness of the important role that many companies would rather have a small but complete logistics department and they do not prefer these functions will be handed over to others, the main reasons it is worried that if they lose the internal logistics capabilities, customers will be exchanges and over-reliance on other third-party logistics companies.4, the logistics outsourcing has its own complexitySupply chain logistics business and companies are usually other services, such as finance, marketing or production of integrated logistics outsourcing itself with complexity. On a number of practical business, including theintegration of transport and storage may lead to organizational, administrative and implementation problems. In addition, the company's internal information system integration features, making the logistics business to a third party logistics companies have become very difficult to operate.5, to measure the effect of logistics outsourcing by many factors Accurately measure the cost of information technology, logistics and human resources more difficult. It is difficult to determine the logistics outsourcing companies in the end be able to bring the cost of how many potential good things. In addition, all the uniqueness of the company's business and corporate supply chain operational capability, is usually not considered to be internal to the external public information, it is difficult to accurately compare the inter-company supply chain operational capability.Although some manufacturers have been aware of the use of third-party logistics companies can bring a lot of good things, but in practical applications are often divided into several steps, at the same time choose a number of logistics service providers as partners in order to avoid the business by a logistics service providers brought about by dependence. Fourth, China's third-party logistics companies in the development of the problems encounteredA successful logistics company, the operator must have a larger scale, the establishment of effective regional coverage area, with a strong command and control center with the high standard of integrated technical, financial resources and business strategy.China's third-party logistics companies in the development of the problems encountered can be summarized as follows:1, operating modelAt present, most of the world's largest logistics companies take the head office and branch system, centralized headquarters-style logistics operation to take to the implementation of vertical business management. Theestablishment of a modern logistics enterprise must have a strong, flexible command and control center to control the entire logistics operations and coordination. Real must be a modern logistics center, a profit center, business organizations, the framework, the institutional form of every match with a center. China's logistics enterprises in the operating mode of the problems of foreign logistics enterprises in the management model should be from the domestic logistics enterprises.2, the lack of storage or transport capacityThe primary function of logistics is to create time and space utility theft. For now China's third-party logistics enterprises, some companies focus on storage, lack of transport capacity; other companies is a lot of transport vehicles and warehouses throughout the country little by renting warehouses to complete the community's commitment to customers. 3, network problemsThere are a few large companies have the logistics of the entire vehicle cargo storage network or networks, but the network coverage area is not perfect. Customers in the choice of logistics partner, are very concerned about network coverage and network of regional branches of the density problem. The building of the network should be of great importance to logistics enterprises.4, information technologyThe world's largest logistics enterprises have "three-class network", that is, orders for information flow, resources, global supply chain network, the global Resource Network users and computer information network. With the management of advanced computer technology, these customers are also the logistics of the production of high value-added products business, the domestic logistics enterprises must increase investment in information systems can change their market position.Concentration and integration is the third-party logistics trends in the development of enterprises. The reasons are: firstly, the company intends tomajor aspects of supply chain outsourcing to the lowest possible number of several logistics companies; the second, the establishment of an efficient global third party logistics inputs required for increasing the capital; the third Many third-party logistics providers through mergers and joint approaches to expand its service capabilities.译文物流已广泛应用于经济领域中的英文单词“物流”,军事后勤保障的原意,在二战结束后的第二面。
物流成本的管理和控制外文翻译

Why do Internet commerce firms incorporate logistics service providers in their distribution channels?: The role of transaction costs and network strengthAbstractThe Internet has redefined information-sharing boundaries in distribution channels and opened new avenues for managing logistics services. In the process, firms have started to incorporate new service providers in their commercial interactions with customers over the Internet. This paper studies conceptually and empirically why Internet commerce firms (ICFs) have established relationships with these providers. Focusing on logistics services in outbound distribution channels, we rely on transaction cost theory to reveal that low levels of asset specificity and uncertainty drive Internet commerce firms to establish these relationships. Moreover, we apply strategic network theory to show that Internet commerce firms seek these providers because they offer access to relationship networks that bundle many complementary logistics services. In addition, logistics service providers make these services available across new and existing relationships between the Internet commerce firms, their customers, and their vendors.1. IntroductionThe growth of electronic commerce has driven Internet commerce firms (ICFs) –retailers and other organizations that market products over the Web – to increasingly share market demand data with other firms so as to enrich the order fulfillment services they offer to customers (Frohlich and Westbrook, 2002). Along these efforts, ICFs have started seeking logistics service providers to tap into resources and skills that could improve their fulfillment capabilities (Dutta and Segev, 1999).These logistics service providers are not simply variants of transportation companies, and as such, they are not to be confused with what are known nowadays as third party logistics (3PL) firms. They offer logistics services, of course, but they could also enable ICFs to leverage other distribution parties’ logistical resources and skills in order to fulfill their customer orders moreeffectively. They may use their assets to take care of product returns, for instance, or work with established carriers on ―last-mile‖ deliveries. Or their value may be primarily in managing order information shared among distribution parties—e.g., centralizing inventory data, especially when products are being shipped directly from upstream echelons in the distribution channel. Logistics service providers such as Parcel Direct, for instance, participate in this kind of activity to ultimately assist ICFs in consolidating orders for drop-shipping to their customers.Past research has identified the relationships with these logistics service providers in offline settings and has positioned them within logistics triads (Larson and Gammelgaard, 2001) and extended-enterprise logistics systems (Stock et al., 2000). Yet, what is ground-breaking about these relationships for an ICF is that they are driven by their potential to (1) generate low transaction costs, (2) bundle complementary logistics services, and (3) expand the availability of those services across customers, vendors, and ―last-mile‖ delivery companies, such as UPS (Amit and Zott, 2001).The goal of this study is to conceptualize and empirically assess how these drivers shape ICF management's decisions to develop mechanisms to form and manage dyadic exchanges between their firms and focal organizations offering logistics services in outbound distribution channels. Prior literature has used the term ―governance‖ to define these me chanisms (Barney, 1999, p. 138) and has delineated governance decisions through which a firm can infuse order in exchanges with a focal provider where potential conflicts threaten to undo or upset opportunities to realize economic gains (Williamson, 1999, p. 1090). These decisions center on the extent to which firms rely on a particular governance mode for a service. Since our research context focuses on outbound distribution channels, we define such reliance as the proportion of Internet orders for which a governance mode is used for a service supporting the fulfillment of those orders. This definition is consistent with that used by John and Weitz (1988)for distribution in an offline setting.Our conceptualization and empirical assessment are unique because they recognize that governance in an exchange between an ICF and a focal logistics service provider is embedded within a networked structure that also comprises a broader collection of relational links amongother distribution-channel members (Chen and Paulraj, 2004 and Jones et al., 1997). In this context, our research is primarily concerned with ICFs’ reliance on networked governance structures. These structures have been defined as economic forms of organization that are built on reciprocal exchange patterns, enabling firms (in this case, ICFs) to obtain resources and services through dyadic relationships with other organizations (i.e., focal logistics service providers), as well as through broader relational links where these relationships exist ( Powell, 1990 and Gulati, 1998).To fulfill the goal of this study, Section 2positions our research in the strategic- and operations-management literatures. Also, it develops the theoretical foundation and hypotheses that articulate a decision-making framework for ICF reliance on networked governance structures for logistics services. Section 3 discusses methodological issues pertaining to the data collection and the operationalization of the constructs developed as part of the theoretical framework presented in Section 2. We analyze the empirical results in Section 4. Finally, we conclude in Section 5with a presentation of findings, academic and practical contributions, and future research opportunities stemming from our study.2. Theoretical frameworkBecause networked governance structures are based on linkages among interdependent firms (Powell, 1990), they constitute an alternate form of exchange (Spulber, 1996) that expands two traditional forms: perfectly competitive markets and vertically integrated hierarchies (Williamson, 1975). Theoretically, decisions to adopt such exchanges rest on costs potentially incurred by ICFs when they establish market-based linkages with focal providers to manage – i.e., plan, organize, operate, and control – logistics services (Madhok, 2002). However, these decisions are also linked to scale, skills, and resources that ICFs may obtain in broader networks of services and entities accessible through their relationships with focal providers (Doz and Hamel, 1998 and Gulati, 1998).Consequently, our assessment of these decisions integrates two distinct theoretical perspectives: transaction cost theory and strategic network theory. Transaction cost theory helps us understandhow efforts and risks in establishing links with focal logistics service providers are related to expenditures that impact ICFs’ reliance on these specialists. Through strategic network theory, and in accordance with its definition, we can establish how the access offered by focal logistics service providers to netw orked governance structures shapes ICFs’ relationships with the providers (Granovetter, 1973).This integration adds to extant literature that has independently relied on transaction cost and strategic network theories to conceptualize similar phenomena at a strategic level (e.g., Eccles, 1981, Katz and Shapiro, 1985, Granovetter, 1992 and Jones et al., 1997). The integration builds on work by Amit and Zott (2001), who used exploratory case studies to apply these theories to an Internet setting and concluded that neither of these theories can fully explain by itself value creation across different governance structures present in Internet business models. Therefore, Amit and Zott (2001) posit that transaction cost and strategic network theories complement each other in explaining the emergence of governance structures in Internet settings.Individually, transaction cost theory focuses on an exchange between two parties (e.g., an ICF and a focal logistics service provider) as a discrete event that is valuable by itself, as it reflects the choice of the most efficient governance form and hence contributes to lower the exchange costs incurred by one of the parties, i.e., the ICF. Strategic network theory complements transaction cost theory because it considers the individual dyadic exchange collectively with other relational links that may accompany that exchange (Amit and Zott, 2001). This does not mean, however, that strategic network theory would become the dominant research view, thus rendering transaction cost theory irrelevant. By articulating a framework necessary to define the choice regarding the most efficient governance form in the exchange between an ICF and its focal provider, transaction cost theory would actually pave the way for strategic network theory to define whether resources and services available through other links surrounding the ICF–provider exchange would confirm or modify that choice (Amit and Zott, 2001).Within operations management, our assessment of these theories answers calls by researchers to offer a better understanding of (1) decision-making mechanisms behind the development of relationships between firms (Mabert and Venkataramanan, 1998) and (2) managerial decisionsconcerning logistics operations in inter-firm relationships (Grover and Malhotra, 2003). As a result, our research contributes to the operations-management literature because it offers a more detailed understanding as to why firms, in this case ICFs, utilize alternative structures to incorporate solution specialists, in general, and logistics service providers, in particular, into their distribution channels.Moreover, in studying decisions about the management of inter-firm exchanges, our research conceptualization follows that introduced by Choi et al. (2001) and Choi and Hong (2002), who advocated that operational decisions around inter-organizational exchanges be positioned within larger networks of firms. However, by focusing on logistics services necessary to carry out the fulfillment of customer orders, we extend those conceptualizations from a manufacturing context to a service setting. This allows us to study not only cost considerations, but also value-adding parameters in decisions to incorporate networked governance structures to connect with other distribution-channel members.Our assessment of decisions by ICF management to form networked governance structures also contributes to literature in service operations management. With the advent of Internet commerce, experts predicted that greater opportunities for information interaction between ICFs and other distribution-channel members would lead to greater efficiency in the performance of distribution-channel services (Benjamin and Wigand, 1995). In theory, this efficiency would inevitably compel ICFs to lower their prices to compete with other organizations. Otherwise, ICFs would likely succumb to price-aggressive competitors who would be able to offer these same services to customers at relatively lower costs (Giaglis et al., 2002).In fact, Dell Computers and other ICFs have succeeded at increasing the efficiency of their distribution channels by offering wide product variety at low prices. However, evidence suggests that other ICFs have chosen not to rely exclusively on low prices to compete and instead have obtained price premiums by offering services with the support of providers in areas such as logistics (Maltz et al., 2004). After all, through logistics services, providers can add value to Internet transactions by allowing customers to obtain exact product specifications that match their needs (Boyer et al., 2002). Moreover, Internet customer satisfaction (Thirumalai and Sinha, 2005),loyalty (Heim and Sinha, 2001), and, thus, willingness to ultimately pay price premiums (Rabinovich and Bailey, 2004) are likely to be related to the availability of those services.中文翻译为什么网络电子商务公司将其分销渠道中的物流服务归于交易成本的作用和网络的力量摘要:互联网重新定义了信息共享边界的分销渠道和物流管理服务开辟了新的途径。
成本控制中英文对照外文翻译文献
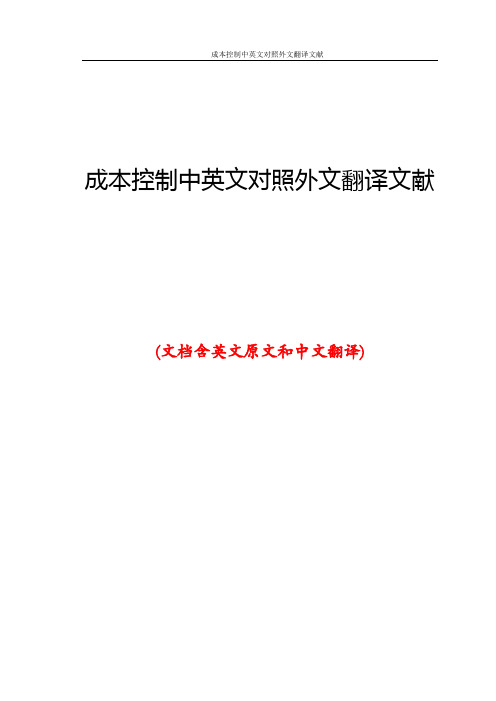
成本控制中英文对照外文翻译文献(文档含英文原文和中文翻译)原文:COST CONTROLRoger J. AbiNaderReference for Business,Encyclopedia of Business, 2nd ed.Cost control, also known as cost management or cost containment, is a broad set of cost accountingmethods and management techniques with the common goal of improving business cost-efficiency by reducing costs, or at least restricting their rate of growth. Businesses use cost control methods to monitor, evaluate, and ultimately enhance the efficiency of specific areas, such as departments, divisions, or product lines, within their operations.Control of the business entity , then, is essentially a managerial and supervisory function .Control consiets of those actions necessary to assur e that the entity’s resources and operations are focused on attaining established objectives , goals and plans. Control, exercised continuously, flags potential problems so that crises may be prevented. It also standardizeds the quantity of output , and provides managers with objective information about employee performance . Management compares actual performance to predetermined standards and takes action when necessary to correct variances from the standards.Keywords : Cost control, Applications, Control reports, Standards, Strategic Cost control, also known as cost management or cost containment, is a broad set of cost accountingmethods and management techniques with the common goal of improving business cost-efficiency by reducing costs, or at least restricting their rate of growth. Businesses use cost control methods to monitor, evaluate, and ultimately enhance the efficiency of specific areas, such as departments, divisions, or product lines, within their operations.During the 1990s cost control initiatives received paramount attention from corporate America. Often taking the form of corporate restructuring, divestmentof peripheral activities, mass layoffs,or outsourcing,cost control strategies were seen as necessary to preserve—or boost—corporate profits and to maintain—or gain—a competitive advantage. The objective was often to be the low-cost producer in a given industry, which would typically allow the company to take a greater profit per unit of sales than its competitors at a given price level.Some cost control proponents believe that such strategic cost-cutting must be planned carefully, as not all cost reduction techniques yield the same benefits. In a notable late 1990s example, chief executive Albert J. Dunlap, nicknamed "Chainsaw Al" because of his penchant for deep cost cutting at the companies he headed, failed to restore the ailing small appliance maker Sunbeam Corporation to profitability despite his drastic cost reduction tactics. Dunlap laid off thousands of workers and sold off business units, but made little contribution to Sunbeam's competitive position or share price in his two years as CEO. Consequently, in 1998 Sunbeam's board fired Dunlap, having lost confidence in his "one-trick" approach to management.COST CONTROL APPLICATIONSA complex business requires frequent information about operations in order to plan for the future, to control present activities, and to evaluate the past performance of managers, employees, and related business segments. To be successful, management guides the activities of its people in the operations of the business according to pre-established goal and objectives. Management’s guidance takestwo forms of control: (1) the management and supervision of behuvior , and (2) the evaluation of performance.Behavioral management deals with the attitudes and actions of employees. While employee behavior ultimately impacts on success, behavioral management involves certain issues and assumptions not applicable to accounting's control function. On the other hand, performance evaluation measures outcomes of employee's actions by comparing the actual results of business outcomes to predetermined standards ofsuccess. In this way management identifies the strengths it needs to maximize, and the weaknesses it seeks to rectify. This process of evaluation and remedy is called cost control.Cost control is a continuous process that begins with the proposed annual budget. The budget helps: (1) to organize and coordinate production, and the selling, distribution, service, and administrative functions; and (2) to take maximum advantage of available opportunities. As the fiscal year progresses, management compares actual results with those projected in the budget and incorporates into the new plan the lessons learned from its evaluation of current operations.Control refers to management's effort to influence the actions of individuals who are responsible for performing tasks, incurring costs, and generating revenues. Management is a two-phased process: planningrefers to the way that management plans and wants people to perform, while controlrefers to the procedures employed to determine whether actual performance complies with these plans. Through the budget process and accounting control, management establishes overall company objectives, defines the centers of responsibility, determines specific objectives for each responsibility center, and designs procedures and standards for reporting and evaluation.A budget segments the business into its components or centers where the responsible party initiates and controls action. Responsibility centersrepresent applicable organizational units, functions, departments, and divisions. Generally a single individual heads the responsibility center exercising substantial, if not complete, control over the activities of people or processes within the center and controlling the results of their activity. Cost centersare accountable only for expenses, that is, they do not generate revenue. Examples include accounting departments, human resources departments, and similar areas of the business that provide internal services. Profit centersaccept responsibility for both revenue and expenses. For example, a product line or an autonomous business unit might be considered profit centers. If the profit center has its own assets, it may also be considered an investment center,for which returns on investment can be determined. The use of responsibility centers allows management todesign control reports to pinpoint accountability, thus aiding in profit planning.A budget also sets standards to indicate the level of activity expected from each responsible person or decision unit, and the amount of resources that a responsible party should use in achieving that level of activity. A budget establishes the responsibility center, delegates the concomitant responsibilities, and determines the decision points within an organization.The planning process provides for two types of control mechanisms:Feedforward: providing a basis for control at the point of action (the decision point); andFeedback: providing a basis for measuring the effectiveness of control after implementation.Management's role is to feedforwarda futuristic vision of where the company is going and how it is to get there, and to make clear decisions coordinating and directing employee activities. Management also oversees the development of procedures to collect, record, and evaluate feedback.Therefore, effective management controls results from leading people by force of personality and through persuasion; providing and maintaining proper training, planning, and resources; and improving quality and results through evaluation and feedback.Control reports are informational reports that tell management about an entity's activities. Management requests control reports only for internal use, and, therefore, directs the accounting department to develop tailor-made reporting formats. Accounting provides management with a format designed to detect variations that need investigating. In addition, management also refers to conventional reports such as the income statement and funds statement, and external reports on the general economy and the specific industry.Control reports, then, need to provide an adequate amount of information so that management may determine the reasons for any cost variances from the original budget.A good control report highlights significant information by focusing management's attention on those items in which actual performance significantly differs from thestandard.Because key success factors shift in type and number, accounting revises control reports when necessary. Accounting also varies the control period covered by the control report toencompass a period in which management can take useful remedial action. In addition, accountingdisseminates control reports in a timely fashion to give management adequate time to act before the issuance of the next report.Managers perform effectively when they attain the goals and objectives set by the budget. With respect to profits, managers succeed by the degree to which revenues continually exceed expenses. In applying the following simple formula, managers, especially those in operations, realize that they exercise more control over expenses than they do over revenue.While they cannot predict the timing and volume of actual sales, they can determine the utilization rate of most of their resources, that is, they can influence the cost side. Hence, the evaluation of management's performance and its operations is cost control.For cost control purposes, a budget provides standard costs. As management constructs budgets, it lays out a road map to guide its efforts. It states a number of assumptions about the relationships and interaction among the economy, market dynamics, the abilities of its sales force, and its capacity to provide the proper quantity and quality of products demanded.Accounting plays a key role in all planning and control. It does this in four key areas: (1) data collection, (2) data analysis, (3) budget control and administration, and (4) consolidation and review.The accountants play a key role in designing and securing support for the procedural aspects of the planning process. In addition, they design and distribute forms for the collection and booking of detailed data on all aspects of the business.Although operating managers have the main responsibility of planning, accounting compiles and coordinates the elements. Accountants subject proposed budgets to feasibility and profitability analyses to determine conformity to accepted standards andpractices.Management relies on such accounting data and analysis to choose from several cost control alternatives, or management may direct accounting to prepare reports specifically for evaluating such options. As the Chainsaw Al episode indicated, all costs may not be viable targets for cost-cutting measures. For instance, in mass layoffs, the company may lose a significant share of its human capitalby releasing veteran employees who are experts in their fields, not to mention by creating a Decline in morale among those who remain. Thus management must identify which costs have strategic significance and which do not.To determine the strategic impact of cost-cutting, management has to weigh the net effects of the proposed change on all areas of the business. For example, reducing variable costs related directly to manufacturing a product, such as materials and transportation costs, could be the key to greater incremental profits. However, management must also consider whether saving money on production is jeopardizing other strategic interests like quality or time to market. If a cheaper material or transportation system negatively impacts other strategic variables, the nominal cost savings may not benefit the company in the bigger picture, e.g., it may lose sales. In such scenarios, managers require the discipline not to place short-term savings over long-term interests.One trend in cost control has been toward narrowing the focus of corporate responsibility centers, and thereby shifting some of the cost control function to day-to-day managers who have the most knowledge of and influence over how their areas spend money. This practice is intended to promote bottom-up cost control measures and encourage a widespread consensus over cost management strategies.Control of the business entity, then, is essentially a managerial and supervisory function. Control consists of those actions necessary to assure that the entity's resources and operations are focused on attaining established objectives, goals and plans. Control, exercised continuously, flags potential problems so that crises may be prevented. It also standardizes the quality and quantity of output, and provides managers with objectiveinformation about employee performance. Management compares actual performance to predetermined standards and takes action when necessary to correct variances from the standards.译文:成本控制成本控制成本控制,也被称为遏制成本或管理成本,一个广阔的成本管理技术,它的经济增长目标是降低成本提高企业效率。
物流成本控制论文中英文对照外文翻译
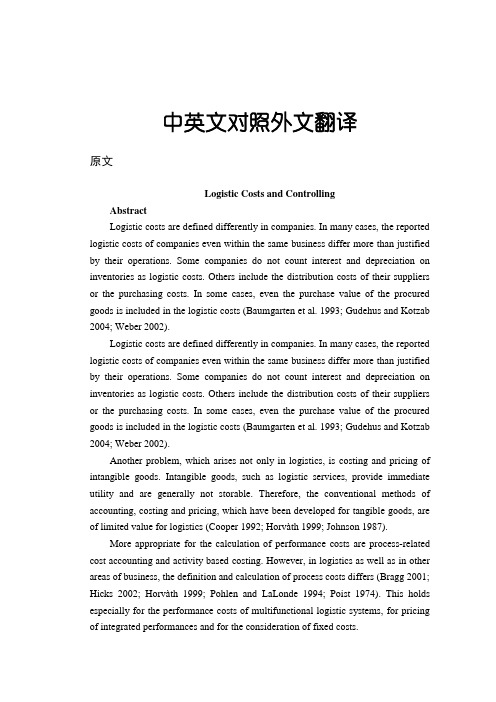
中英文对照外文翻译原文Logistic Costs and ControllingAbstractLogistic costs are defined differently in companies. In many cases, the reported logistic costs of companies even within the same business differ more than justified by their operations. Some companies do not count interest and depreciation on inventories as logistic costs. Others include the distribution costs of their suppliers or the purchasing costs. In some cases, even the purchase value of the procured goods is included in the logistic costs (Baumgarten et al. 1993; Gudehus and Kotzab 2004; Weber 2002).Logistic costs are defined differently in companies. In many cases, the reported logistic costs of companies even within the same business differ more than justified by their operations. Some companies do not count interest and depreciation on inventories as logistic costs. Others include the distribution costs of their suppliers or the purchasing costs. In some cases, even the purchase value of the procured goods is included in the logistic costs (Baumgarten et al. 1993; Gudehus and Kotzab 2004; Weber 2002).Another problem, which arises not only in logistics, is costing and pricing of intangible goods. Intangible goods, such as logistic services, provide immediate utility and are generally not storable. Therefore, the conventional methods of accounting, costing and pricing, which have been developed for tangible goods, are of limited value for logistics (Cooper 1992; Horvàth 1999; Johnson 1987).More appropriate for the calculation of performance costs are process-related cost accounting and activity based costing. However, in logistics as well as in other areas of business, the definition and calculation of process costs differs (Bragg 2001; Hicks 2002; Horvàth 1999; Pohlen and LaLonde 1994; Poist 1974). This holds especially for the performance costs of multifunctional logistic systems, for pricing of integrated performances and for the consideration of fixed costs.As long as they are defined, measured and calculated differently, logistic costs, cost rates and prices cannot be compared. Any benchmarking based on such doubtful indicators is misleading (see Sect. 4.5). Hence, reported market volumes and market shares of logistics are at best educated guesses (Baumgarten et al. 1993; Kille and Klaus 2007; Müller-Steinfahrt 1998).The situation in logistic controlling and supply chain controlling is even worse (Cooper and Kaplan 1998; Manrodt et al. 1999; Seuring 2006). Only a minority of companies records and monitors logistic costs separately and continuously (Weber 2002). Whereas in industry the total logistic costs range between 5 and 15% of turnover, in trade companies they make up between 10 and 25% of turnover (Baumgarten et al. 1993; Gudehus 1999/2007). For retailers, logistic costs can use up more than one third of the profit margin. Despite this, it is still the exception for retailers to record and monitor the logistic costs from the ramp of the suppliers to the point of sales.Logistic controlling does not only include calculation, budgeting and recording of costs, but also the monitoring of performance and quality. Controlling should consult management in the planning, set up and operation of optimal systems. To enable this, it has to determine and specify for improvements in service, performance, quality, and costs (Cooper 1992; Darkow 2001; Horvàth 1999; Johnson 1987; Weber et al. 1993, 2002).Where and with what accuracy costs, performances and quality should be recorded and monitored depends on the contribution of logistics to the value creation, on the core competencies and objectives of the company, and on current projects. In logistic controlling, as in other areas, less is more: it is better to control a small number of meaningful key performance indicators (KPI) with adequate accuracy in longer time spans, than to monitor all possible performance, quality and cost data with high precision permanently without knowing the demand for these information (Manrodt et al. 1999). For controlling, not the precision of the performance and cost data, but their practical use and application are decisive.In this chapter, the logistic costs are consistently defined, the fundamental issues of logistic costing are presented, and practicable methods for the calculation of use dependent cost rates are developed. This includes a discussion of the fixed-cost dilemma of logistics, the relationship between logistic costs and performance rates and the most effective options for reducing logistic costs. Usingthe results of this chapter, in the following chapter cost-based prices and pricing systems for logistic performances and services are derived.Cost Accounting and Performance CostingCorresponding to the stationary or structural aspect and to the dynamic or process aspect, two different types of accounting are necessary. Cost accounting for longer periods keeps a stationary point of view, while performance costing for shorter periods reflects the dynamic perspective.Logistic Cost CalculationAs the general cost calculation of a company, the logistic cost calculation comprises standard cost calculation, accompanying cost calculation and final cost calculation (Horváth 1999; Weber 2002; Wöhe and Döring 2008).Standard Cost CalculationSubjects of standard cost calculation or planned cost calculation are the future operating costs for an existing or a planned system. Results are standard logistic costs and target performance costs.Standard cost calculation is necessary for investment decisions, for planning systems, processes and projects, for cost accounting and benchmarking of future periods and for the calculation of prices and tariffs.Accompanying Cost CalculationAccompanying cost calculation aims for a continuous control of all costs caused by the execution of logistic tasks and services during the current accounting period. The result of accompanying cost calculation is information for management about the current costs and utilization of resources.Knowing the costs and the utilization of the resources allows initiating appropriate measures for reducing costs, adaptation of resources and improving capacity utilization in due time. The results of the accompanying cost calculationcan be used also for invoicing and compensation of logistic service providers, if costs-based prices have been agreed.Final Cost CalculationSubjects of final cost calculation or post calculation are the operating costs of closed periods in the past. The real logistic costs and cost rates can be compared with the respective target values and benchmarks. This allows conclusions for standard costing and pricing.Most important causes for deviations of real costs from the target values in logistics are:●Cost factors, especially personnel costs, have been planned, assumed orexpected too high or too low.●Utilization of resources, such as transport means, storage systems,machines, and production facilities, has been planned or expectedfalsely.●Empty runs of transport means and filling degrees of transport and loadunits were incorrectly planned.●The actual utilization structure of the logistic system differs from theanticipated structure.The first two reasons for differences between real and target costs are normally caused by the planner and the operator of a logistic system. A too high share of empty runs and bad utilization of storage capacities is in many cases also the result of unqualified planning or poor scheduling. However, this can be caused also by a user, who changed transport relations, demand structure or stock levels. An insufficient utilization can also be initiated by a wrong demand forecast or false information from the customers.For a dedicated logistic system, which is used for a longer period of time by one or a small number of companies based on individual contracts, the users must bear the risk of changing demand and the cost differences resulting from a deviating utilization of the ready held resources. Final cost calculation for dedicated logisticsystems can be used for the utilization based allocation of surpluses or additional costs to the different usersFor a multi-user logistic system, where tasks and services are offered on the market and used only for shorter periods of time by many different customers, the risk for changing demand and insufficient utilization is born by the logistic service provider. This risk is compensated by the chances for higher profit from better utilization or favorable demand structure. Furthermore, the service provider can influence the demand by his sales efforts and by offering utilization dependent prices. For multi-user logistic systems the structure and utilization risk are incorporated in the pricesComponents of Logistic CostsThe total logistic costs are a sum of specific logistic costs, additional logistic costs and administrative costs:●Specific logistic costs are all costs of a performance station, a profit centeror a company, which are caused by executing the genuine operativelogistic tasks transport, handling, storing and commissioning.●Additional logistic costs are caused by executing additional operative taskswhich are directly connected with the genuine logistic tasks, such aspacking, labeling, loading and unloading, quality control or handling ofempties.●Administrative logistic costs are costs for related administrative services,such as scheduling, quality management and controlling, which go alongwith the execution of logistic performances and additional services.Costs for non-logistic tasks, such as research and development, construction, production, assembling, marketing, sales and general administration, are not part of the logistic costs. Also, the costs for buying and procuring merchandise, parts, material and equipment are not logistic costs as long as they are not directly caused by the execution of logistic tasks and related services. For instance, the costs for packing sales units are production costs, whereas the costs for packing material, pallets, bins and load carriers are material costs of logistics.When designing and optimizing company logistics as well as when scheduling orders and inventories, it is necessary to keep in mind that many logistic activities also have an effect on non-logistic costs and revenues. They influence setup costs, out-of-stock costs, disruption costs and ordering costs as well as prices, profit margins and turnover. Hence, logisticians always have to bear in mind the economic principle:Logistic activities as all other activities in the company should maximize the difference between revenues and costs at lowest capital investment.Elements of Logistic Costs●Personnel costs: wages for workers and salaries for employees with logisticresponsibilities, including personal taxes, vacation, illness, absence, etc.●Space and area costs: Depreciation and interest for the owned assets andbuildings, rents and leasing fees for external buildings, halls and areas,including related heating, climate, maintenance and surveillance costs.●Route and network costs: Depreciation and interest for own and fees forexternal driveways, routes, roads, highways, railroads and transshipmentpoints●Costs for logistic equipment: Depreciation, interest and operating costs forown as well as rental fees and leasing costs for external logistic equipmentsuch as racks, forklifts, transport means, cranes, conveyors and handlingequipment, control systems and process computers, including theequipment-caused energy, cleaning, repair and maintenance costs.●Load carrier costs: Depreciation and interest for own as well as rental feesand leasing costs for external load carriers, such as pallets, bins, barrels,racks, cassettes and containers, including the costs for cleaning, repair,maintenance and empties management.●Logistic material costs: Expenditures for packing material, transportpacking, load securing, labels and other material, which is needed in orderto perform logistic tasks and services.●Logistic IT-costs: Depreciation, interest and operating costs for ownIT-systems as well as costs for external IT-systems as far as used forlogistic purposes.●Third party logistic expenses: Freights, rental fees and other expenses forlogistic service providers.●Taxes, duties and insurance fees, which accumulate during the execution oflogistic tasks and services, as far as related to logistic purposes.●Planning and project costs: Depreciation and interest on activated expensesfor planning, project management and implementation accumulated up tothe start of the economic utilization of a logistic system.●Inventory holding costs: Interest and write offs on all stationary andmoving inventories, in stocks, on buffer places and in transport.In some companies the inventory holding costs include only the interest caused by the capital commitment. Obsolescence costs as well as write-offs due to non-marketability, deterioration or stock decline are often neglected. However, the write-offs on inventories of fashion, perishable, high value or electronic goods can be as high as or even higher than the interest.译文物流成本和控制资料来源: Springer-Verlag 2009 作者:Timm Gudehus,Herbert Kotzab 物流成本定义在不同公司是不同的。
(完整word版)物流外文文献翻译
外文文献原稿和译文原稿Logistics from the English word "logistics", the original intent of the military logistics support, in the second side after World War II has been widely used in the economic field. Logistics Management Association of the United States is defined as the logistics, "Logistics is to meet the needs of consumers of raw materials, intermediate products, final products and related information to the consumer from the beginning to the effective flow and storage, implementation and control of the process of . "Logistics consists of four key components: the real flow, real storage, and management to coordinate the flow of information. The primary function of logistics is to create time and space effectiveness of the effectiveness of the main ways to overcome the space through the storage distance.Third-party logistics in the logistics channel services provided by brokers, middlemen in the form of the contract within a certain period of time required to provide logistics services in whole or in part. Is a third-party logistics companies for the external customer management, control and operation of the provision of logistics services company.According to statistics, currently used in Europe the proportion of third-party logistics services for 76 percent, the United States is about 58%, and the demand is still growing; 24 percent in Europe and the United States 33% of non-third-party logistics service users are actively considering the use of third-party logistics services. As a third-party logistics to improve the speed of material flow, warehousing costs and financial savings in the cost effective means of passers-by, has become increasingly attracted great attention.First, the advantages of using a third-party logisticsThe use of third-party logistics enterprises can yield many benefits, mainly reflected in: 1, focus on core businessManufacturers can use a third-party logistics companies to achieve optimal distribution of resources, limited human and financial resources to concentrate on their coreenergy, to focus on the development of basic skills, develop new products in the world competition, and enhance the core competitiveness of enterprises.2, cost-savingProfessional use of third-party logistics providers, the professional advantages of mass production and cost advantages, by providing the link capacity utilization to achieve cost savings, so that enterprises can benefit from the separation of the cost structure. Manufacturing enterprises with the expansion of marketing services to participate in any degree of depth, would give rise to a substantial increase in costs, only the use of professional services provided by public services, in order to minimize additional losses. University of Tennessee in accordance with the United States, United Kingdom and the United States EXEL company EMST & YOUNG consulting firm co-organized a survey: a lot of cargo that enable them to use third-party logistics logistics costs declined by an average of 1.18 percent, the average flow of goods from 7.1 days to 3.9 days, stock 8.2% lower.3, reduction of inventoryThird-party logistics service providers with well-planned logistics and timely delivery means, to minimize inventory, improve cash flow of the enterprise to achieve cost advantages.4, enhance the corporate imageThird-party logistics service providers and customers is a strategic partnership, the use of third-party logistics provider of comprehensive facilities and trained staff on the whole supply chain to achieve complete control, reducing the complexity of logistics, through their own networks to help improve customer service, not only to establish their own brand image, but also customers in the competition.Second, The purpose of the implementation of logistics management The purpose of the implementation of logistics management is to the lowest possible total cost of conditions to achieve the established level of customer service, or service advantages and seek cost advantages of a dynamic equilibrium, and thus create competitive enterprises in the strategic advantage. According to this goal, logistics management to solve the basic problem, simply put, is to the right products to fit the number and the right price atthe right time and suitable sites available to customers.Logistics management systems that use methods to solve the problem. Modern Logistics normally be considered by the transport, storage, packaging, handling, processing in circulation, distribution and information constitute part of all. All have their own part of the original functions, interests and concepts. System approach is the use of modern management methods and modern technology so that all aspects of information sharing in general, all the links as an integrated system for organization and management, so that the system can be as low as possible under the conditions of the total cost, provided there Competitive advantage of customer service. Systems approach that the system is not the effectiveness of their various local links-effective simple sum. System means that, there's a certain aspects of the problem and want to all of the factors affecting the analysis and evaluation. From this idea of the logistics system is not simply the pursuit of their own in various areas of the lowest cost, because the logistics of the link between the benefits of mutual influence, the tendency of mutual constraints, there is the turn of the relationship between vulnerability. For example, too much emphasis on packaging materials savings, it could cause damage because of their easy to transport and handling costs increased. Therefore, the systems approach stresses the need to carry out the total cost analysis, and to avoid the second best effect and weigh the cost of the analysis, so as to achieve the lowest cost, while meeting the established level of customer se rvice purposes.Third, China's enterprises in the use of third-party logistics problems in While third-party logistics company has many advantages, but not many enterprises will be more outsourcing of the logistics business, the reasons boil down to:1, resistance to changeMany companies do not want the way through the logistics outsourcing efforts to change the current mode. In particular, some state-owned enterprises, we reflow will also mean that the dismissal of outsourcing a large number of employees, which the managers of state-owned enterprises would mean a very great risk.2, lack of awarenessFor third-party logistics enterprise's generally low level of awareness, lack of awareness of enterprise supply chain management in the enterprise of the great role in thecompetition.3, fear of losing controlAs a result of the implementation of supply chain companies in enhancing the competitiveness of the important role that many companies would rather have a small but complete logistics department and they do not prefer these functions will be handed over to others, the main reasons it is worried that if they lose the internal logistics capabilities, customers will be exchanges and over-reliance on other third-party logistics companies. 4, the logistics outsourcing has its own complexitySupply chain logistics business and companies are usually other services, such as finance, marketing or production of integrated logistics outsourcing itself with complexity. On a number of practical business, including the integration of transport and storage may lead to organizational, administrative and implementation problems. In addition, the company's internal information system integration features, making the logistics business to a third party logistics companies have become very difficult to operate.5, to measure the effect of logistics outsourcing by many factorsAccurately measure the cost of information technology, logistics and human resources more difficult. It is difficult to determine the logistics outsourcing companies in the end be able to bring the cost of how many potential good things. In addition, all the uniqueness of the company's business and corporate supply chain operational capability, is usually not considered to be internal to the external public information, it is difficult to accurately compare the inter-company supply chain operational capability.Although some manufacturers have been aware of the use of third-party logistics companies can bring a lot of good things, but in practical applications are often divided into several steps, at the same time choose a number of logistics service providers as partners in order to avoid the business by a logistics service providers brought about by dependence. Fourth, China's third-party logistics companies in the development of the problems encounteredA successful logistics company, the operator must have a larger scale, the establishment of effective regional coverage area, with a strong command and control center with the high standard of integrated technical, financial resources and business strategy.China's third-party logistics companies in the development of the problems encountered can be summarized as follows:1, operating modelAt present, most of the world's largest logistics companies take the head office and branch system, centralized headquarters-style logistics operation to take to the implementation of vertical business management. The establishment of a modern logistics enterprise must have a strong, flexible command and control center to control the entire logistics operations and coordination. Real must be a modern logistics center, a profit center, business organizations, the framework, the institutional form of every match with a center. China's logistics enterprises in the operating mode of the problems of foreign logistics enterprises in the management model should be from the domestic logistics enterprises.2, the lack of storage or transport capacityThe primary function of logistics is to create time and space utility theft. For now China's third-party logistics enterprises, some companies focus on storage, lack of transport capacity; other companies is a lot of transport vehicles and warehouses throughout the country little by renting warehouses to complete the community's commitment to customers. 3, network problemsThere are a few large companies have the logistics of the entire vehicle cargo storage network or networks, but the network coverage area is not perfect. Customers in the choice of logistics partner, are very concerned about network coverage and network of regional branches of the density problem. The building of the network should be of great importance to logistics enterprises.4, information technologyThe world's largest logistics enterprises have "three-class network", that is, orders for information flow, resources, global supply chain network, the global Resource Network users and computer information network. With the management of advanced computer technology, these customers are also the logistics of the production of high value-added products business, the domestic logistics enterprises must increase investment in information systems can change their market position.Concentration and integration is the third-party logistics trends in the development ofenterprises. The reasons are: firstly, the company intends to major aspects of supply chain outsourcing to the lowest possible number of several logistics companies; the second, the establishment of an efficient global third party logistics inputs required for increasing the capital; the third Many third-party logistics providers through mergers and joint approaches to expand its service capabilities.译文物流已广泛应用于经济领域中的英文单词“物流”,军事后勤保障的原意,在二战结束后的第二面。
物流成本外文文献
物流成本外文文献Title: Literature Review on Logistics CostsIntroduction:Logistics costs play a critical role in the overall performance and competitiveness of businesses. Efficient management of logistics costs is essential for achieving operational excellence and maximizing profitability. This literature review aims to provide an overview of existing studies on logistics costs and explore potential strategies for cost reduction and optimization.1. Definition and Components of Logistics Costs:Logistics costs encompass a wide range of expenses involved in the movement, storage, and handling of goods. These costs can be categorized into several components, including transportation costs, inventory carrying costs, warehousing costs, order processing costs, and packaging costs. Understanding the different components of logistics costs is crucial for identifying areas with potential for cost reduction.2. Factors Affecting Logistics Costs:Numerous factors influence logistics costs, including distance, transportation mode, shipment size, delivery time,product value, and market demand. Furthermore, external factors such as fuel prices, labor costs, regulatory requirements, and infrastructure quality also impact logistics costs. Studying these factors can help businesses develop effective strategies to minimize expenses and enhance overall operational efficiency.3. Strategies for Cost Reduction:Several strategies have been proposed to reduce logistics costs effectively. These include optimizing transportation routes, consolidating shipments, adopting lean inventory management techniques, improving warehouse layout and operations, outsourcing non-core logistics activities, and implementing advanced technologies such as automation and data analytics. By incorporating these strategies, companies can achieve significant cost savings and improve customer service levels.4. Importance of Collaboration and Integration:Collaboration among supply chain partners, including suppliers, manufacturers, distributors, and retailers, is essential for optimizing logistics costs. By sharing information, coordinating activities, and aligning goals, supply chain partners can eliminate redundant processes,reduce transportation costs, and improve overall supply chain efficiency. Integration of logistics functions with other business processes, such as procurement, production, and sales, also leads to cost savings and improved customer satisfaction.5. Performance Measurement and Benchmarking:Accurate measurement and benchmarking of logistics costs are crucial for monitoring performance and identifying areas for improvement. Key performance indicators (KPIs) such as cost per unit, order cycle time, on-time delivery, and inventory turnover provide valuable insights into cost-effectiveness and operational efficiency. Comparing these metrics with industry benchmarks helps companies identify performance gaps and implement appropriate measures to achieve cost reduction goals.Conclusion:Effective management of logistics costs is essential for businesses to remain competitive in today's dynamic marketplace. By understanding the components and factors influencing logistics costs and adopting appropriate strategies, companies can achieve cost reduction, enhance operational efficiency, and improve customer satisfaction. Continuous measurement and benchmarking of logistics costs arecrucial for monitoring performance and identifying opportunities for further optimization.。
The-logistics-cost-物流成本控制control-外文翻译
物流成本控制The logistics cost controlWith the rapid development of science and technology and the enhancement of the trend of economic globalization, the countries of the world economy is facing unprecedented opportunities and challenges. As an important part of modern economy, modern logistics in the national economy and social development plays an important role. Logistics cost is one of the core concepts of logistics, how to calculate, and what is the difference between the traditional storage and transportation costs, these problems not only relates to how to know the current situation of logistics in China, from the macroscopic also relates to the specific calculation and evaluation of logistics practice. Control is a control system to achieve all the goals. The so-called logistics cost control is to use a particular theory, method and system on logistics each link of the expenses incurred for effective planning and management.Basic introductionTo control the logistics cost, an enterprise should according to the following steps to gradually achieve:1, you first need to understand your service object. What needs do they have? How can a higher level of service to achieve customer satisfaction? This is very important, when many companies tend to be because of lower costs and reduce the cost of the result of the customer service level is down, enterprise's sales are down, but led to rising, so that the overall costs of the loss of competitiveness. So we must first clear customer service requirements, these requirements and standards are not allowed to decrease.2, the second to get to know the composition of your logistics cost. Enterprise's logistics cost generally includes storage cost, transportation cost, information cost, managementcost, the cost must be refined. Such as storage cost: all the associated costs and warehousing activities, order cost, loss of the cargo interest, depreciation, purchase cost, inventory cost, picking cost, distribution cost, circulation processing cost, transportation cost, warehouse all kinds of facilities, equipment depreciation, labor costs, etc.; Transport costs: outside the unit transportation cost, the unit vehicle use various cost, insurance premium, and careful, oil expenses, toll fee, depreciation cost, maintenance cost and artificial cost, etc.), information cost, amortization system development, system maintenance, system related equipment depreciation cost; Cost management: all kinds of artificial cost management.3, need to understand the business area and the distribution of the current service, cost, etc. Where is the supply of goods? Where is the customer? Where is the warehouse? Now is how to service? The current situation of service? Current cost? Now the mode of transportation? Need to learn more about each piece. Through your client in where? What are their needs and quantity? Customer requirements of the supply of goods in where? The comparison of different means of transportation cost and analysis? Different carriers, service, cost comparison and analysis.4, considering the layout according to the current customers, arrange the best goods flow, analysis of different combination of cost and service. Determine the warehouse layout, determine the warehouse service customers, to determine the flow of goods, to determine the economic inventory distribution, determine the best mode of transportation, to determine the best carrier.5, will be the fourth step refinement into enterprise business process and operation specification, at the same time with all kinds of monitoring and analysis report. Analyzing the needs of customers, arrange the best inventory distribution; Analyzing thecost of change; Continuous assessment service level, the cost of all kinds of carriers, The costs of all kinds of audit.Simple write here, still relatively early shallow. Lower logistics costs is a continuing process, clear what to do first? Then what will produce what charge? After understanding the status quo? To design the best implementation pattern? Finally strengthen monitor constantly improve optimization.Basic methodLogistics cost control methods, including absolute cost control method and relative cost control method.The absolute cost controlIs control the cost within an absolute amount of the cost control method. Absolute cost control from the various cost saving, put an end to the channels of waste logistics cost control, and asked what was happening in the operation of the production process costs are included in the scope of cost control. Standard cost and budget control is the main method of absolute cost control.Relative to the cost controlBy cost and output value, profits, quality and function of factors such as comparative analysis, seek the most economic benefits under certain constraints of a kind of control method.Relative cost control to expand the field of logistics cost control, asking people in an effort to reduce logistics cost at the same time, sufficient attention and closely related to the cost factors, such as product structure, the structure of the project, quality of servicelevel, quality management, and other aspects of work, the purpose is to improve the efficiency of the control cost, both to reduce the unit product costs, improve overall economic efficiency.basic principleLogistics system cost control to carry out the following principles:(1) the right standards for the cost of logistics activities, using the standard strictly implement the cost responsibility system.(2) the combination of general and key, according to the exception principle, especially the logistics cost.(3) from top to bottom, and daily on a regular basis, combining the experts and the masses, one-way activity combination and integration process, the comprehensive logistics cost control.Basic wayTo strengthen the inventory management and reasonable control inventoryTo strengthen the inventory management, reasonable control inventory is the first task of logistics cost control. Enterprise inventory costs include holding cost, ordering or production preparation cost and shortage cost. Inventory quantity is too much, although can meet customer demand, reduce the shortage cost and ordering cost, but increase the enterprise's inventory holding cost; Inventory quantity is not enough, although can reduce inventory holding cost, but will not be normal to meet customer demand and increase the shortage cost and ordering cost. How to determine the damage neither customer service levels, nor the enterprise for holding too much inventory and increasethe cost of reasonable inventory reserves, this needs to strengthen the inventory control and enterprise can use the economic order batch method, MRP, inventory control, JIT inventory control, etc.On the whole process of supply chain management, improve the level of logistics servicesControl the logistics cost is not just the pursuit of the efficiency of logistics enterprises, the main consideration should be given more from products to end users throughout the supply chain logistics cost efficiency. With today's competition in the enterprise environment, customers put forward higher request, in addition to price more enterprises can effectively shorten the period of goods turnover, really quickly, accurately and efficiently manage the commodity, in order to achieve this goal, is just the logistics system has the efficiency of an enterprise is not enough, it need to coordinate with other enterprises and customers, transportation industry, the relationship between the efficiency of the entire supply chain activities. Therefore lower logistics costs is not just logistics departments or enterprises of the production department, is also sales and procurement departments of responsibility, also the goals to reduce logistics cost through to the enterprise all functional departments. Improve the logistics service is one of the ways to reduce logistics cost, by strengthening the logistics service to customers, contribute to the realization of sales to ensure that the enterprise benefits. , of course, at the same time as the guarantee to improve the logistics service, and to prevent excess of logistics services, more than the necessary logistics service may impede the implementation of the logistics efficiency.Through the reasonable distribution to reduce logistics costDistribution is an important link in logistics services, through the realization of the efficiency of distribution, increase the cubed out and reasonable arrangements to plan, choose reasonable transportation, can reduce the distribution cost and transportation cost. The use of logistics outsourcing to reduce logistics costLogistics outsourcing is an important means of controlling logistics cost. Enterprises logistics outsourcing to specialized third-party logistics companies, through the integration of resources, utilization, not only can reduce the enterprise investment cost and logistics cost, and can make full use of the professional and technical advantages, improve the level of logistics services. The author has some cost of logistics in China has a large enterprise must rely on a survey of logistics cost occupies a considerable proportion in the enterprise, there are a lot of enterprise logistics cost accounts for more than 20% of the cost of sales. They are in the process of practice through different forms of logistics outsourcing, fundamentally reduces the logistics cost, and makes the service quality to rise obviously, so as to get rid of the cycle in some enterprises in the past, made a lot of money, it is made for shipping company. Robust that everyone is familiar with the company to produce nationally famous for bottled purified water, mineral water, bottled water sales process occupies a considerable proportion of the logistics cost, logistics cost accounts for 39% of the cost of sales, as the change of domestic and foreign economic environment, especially the rising oil prices and the national governance of overrun overload, make the enterprise faces a lot of pressure in terms of logistics, so they choose the logistics outsourcing, mainly take personnel outsourcing, outsourcing cargo handling, service outsourcing, logistics cost after change in the cost of sales share dropped to 6.5%.Control and reduce logistics costIn the rapidly development of modern logistics technology gradually perfect logistics system software. With the aid of logistics information system, on the one hand various logistics operations or business processing can accurately and rapidly; On the other hand, the establishment of the logistics information platform, all kinds of information transmitted through the network, so that the whole process of production, circulation enterprises or departments share the resulting profits, fully cope with the possibility of demand, and adjust the business practices of different enterprises and planning, so as to effectively control the happening of the ineffective logistics cost, basically realize the logistics cost is reduced, which fully reflects the logistics of the third profit source.To sum up, the logistics cost control is a comprehensive and systematic project, to build a new control thought, from the global, to obtain good economic benefit, logistics "the third profit source" can really play a role.The domestic situationOur whole society total logistics cost of GDP, down to 21.4% since 1998, seven years in a row in the percentage, is still in the level of 21.3% by 2004. The level of developed countries and foreign logistics is about 8% ~ 10%. So far, our country's logistics industry is still in its infancy, stay in vulgar management, the level of quality and efficiency is not very ideal. The modern logistics concept to China, by contrast, has more than 20 years of history, but the logistics real attention by Chinese companies, was promoted to the height of the strategic management, practical significance of the third party logistics industry, in the 21st century has just begun.At present, the domestic enterprises in the logistics cost control, an exploration is still in the stage, the perceptual component in the majority. Put forward the importance oflogistics costs "black continent" theory, indicate that people know about logistics cost of one-sidedness of "logistics iceberg theory"; Clarify logistics cost control is the enterprise profit point of "the third profit source" hypothesis; Easy logistics cost calculation method - "ABC" logistics calculation method research achievements abroad for Chinese enterprise. It is important to our country enterprise vigilant that these theory are based in the international large-scale enterprise of research. And the logistics industry of our country basic is composed of under $5 billion small and medium-sized enterprises. The existing advanced logistics concept how to reasonable application characteristic of the economic situation in our country, has become a major subject presses for solution.Cost of logistics systemLogistics system includes transportation, warehousing, packaging, handling, distribution, circulation processing, logistics information. Standing in the perspective of enterprise, it is necessary to reduce the isn't a link in the system cost, but from a global control system cost finally. To achieve this goal, need to adjust to the whole logistics system, improvement and optimization, to provide as high as possible as low as possible in the logistics cost of logistics service quality. Logistics each subsystem in its reasonable optimization on the basis of cohesion, to adapt to each other, each other to form the best structure and the operation mechanism, can give full play to the efficiency of each subsystem, and the overall efficiency of the system is able to fully embody. In the end, to ensure that the logistics system has the ability to according to the types of goods, quantity, delivery requirements, transportation conditions, etc., make the goods as soon as possible by origin with minimal link, in the most economic route, the high quality land into the hands of users, in order to achieve the purpose of reduce logistics costs, improve the economic benefit.Mention logistic system, wal-mart (Wal - Mart) group is a must to mention. Wal-mart after 44 years of operation, already have 3 more than 000 chain stores in the United States, in overseas has 1 000 chain stores, as many as 885000 employees, is the world's biggest retail enterprise. It a cost leadership strategy covers the commodity purchase store sales all the links on the transfer process cost and cost control. The company has built 62 distribution centers, distribution service for 4 more than 000 chain stores in the world, the company sales of 80000 products, 85% of these supplies distribution center. The company in the United States more than a total of nearly 30000 domestic large container trailer, 5 more than 500 large cargo truck. Transport amount of 7.75 billion cases each year, the total travel 650 million km. Distribution center is completely automated, each commodity bar code, are marked by a dozen kilometers of conveyor belt transmission products, with a laser scanner and computer to track the storage location of each item and shipping. For reasonable scheduling of the scale of the commodity procurement, inventory, logistics and distribution management, the company has established the specialized computer management systems, satellite positioning system and TV scheduling system, and even have their own satellites. Wal-mart's logistics system is a whole system, on the one hand can guarantee adequate shelf in time, on the one hand, also will try our best to make the inventory to a minimum.The thinking of integrated logistics systemIn reality, the highest level of logistics service and the lowest logistics cost is impossible to set up at the same time, both between them there is a "law of antinomy. High levels of logistics service requires a large number of inventory, enough freight and plenty of storage, this is bound to produce high logistics costs; And lower logistics costs asking for is a small amount of inventory, low freight rates and less storage, which in turn willreduce services, reduce service levels and standards. Wal-mart in the United States to set up the logistics system from the economic scale of its existing well solve the "law of antinomy, found their own logistics service level of the highest and the lowest organic balance between the logistics cost. Automated distribution centers in the United States, it is recognized as the most advanced distribution center, to achieve the goal of high efficiency, low cost, for wal-mart implements the "everyday parity" provides reliable logistics guarantee. To enter the Chinese market, however, didn't immediately put it in the United States of wal-mart's business model copy China to come, but according to the actual situation, timely and reasonable to gradually set up purchasing center and distribution center, in order to upgrade the automation level. Wal-mart's attitude is worth pondering for Chinese companies.(1) transportation cost control. Our country enterprise is limited by the size, neither necessary nor possible in a short period of time with a large transport capacity, less likely to widely used technology such as GPS. Which requires the enterprise must fully use the existing facilities, starting from the global, strive for short transport distance, transport capacity among provinces, less operation, to reach high speed, low transportation costs, transportation, quality and efficient planning and aviation, railway, highway, waterway transport.(2) the distribution cost control. Even the strength of the wal-mart, after also didn't immediately come to China for the layout of the distribution center, but according to the development strategy of business step by step. Chinese enterprises should also follow this principle, according to the distribution network and the development of appropriate scale set up distribution centers. Some production enterprise internal logistics at present didn't have to consider to establish a distribution center, only need to optimize thestorage.(3) the rationalization of logistics facilities and equipment. Every enterprise's logistics has its own characteristics, the enterprise should be to choose the logistics equipment and logistics facilities. Warehouse is self-built or lease, you need to set up the shelf, use what kind of material, specifications of the tray, equipped with what sort of transport, handling tools and vehicles is a problem that every enterprise to consider. Does not require much and all the logistics facilities and equipment, but must be able to adapt to the characteristics of the enterprise. In the commodity circulation in wuhan from best warehousing distribution center has its own European warehouse, take the pallet racking combined with gravity shelves, multi-purpose plastic tray, with van, and four kinds of forklift, including "lumbricus" to serve the needs of logistics. In the third party logistics bureau wuhan branch is rented warehouse, use pallet racking, mainly use wooden pallet, road, rail transport, adequate equipment two forklifts, company-wide on-the-job personnel also less than 30 people.(4) information system reasonably. All the associated with logistics information flow determines the effectiveness of the logistics system, to guide the flow of operations. Contemporary social demand diversification and individuation, production type to develop in the direction of many varieties, small batch, production and processing equipment from the flowing water line of special processing equipment, to adopt a multi-function machining center of flexible manufacturing system (FMS). With a medium-sized commodities flow-through enterprise as an example, its operating varieties are more than 5, 000 at least. The resulting large amounts of information has gone far beyond the human computing ability. Logistics system in order to adapt to this change will need to implement a high degree of information. But the informatization process ofcan and should be gradual. Wal-mart in the United States to use large computers to set up the data center, and wuhan from best warehousing distribution center only used a handheld scanner, electronic counters, etc. A relatively small amount of electronic equipment. The question of whether there is no advanced information system, the key lies in whether can meet the demand of the enterprise logistics management and cost. The development of the logistics systemThe cost of logistics system not only limited to the enterprise internal control. In fact has developed into the Supply Chain enterprise logistics system (Supply Chain) an integral part. Shenlong automobile co., LTD., for example, the company quite a lot of parts by wuhan local purchasing auto parts enterprises. Dpca through qualification assessment and tender way in the selection of suppliers, and they become a community of interests, by sharing information, coordinate with each other, to ensure the dongfeng-citroen automobile spare parts supply, smooth of dpca's internal logistics operation can also help companies control purchasing cost, ensure the quality of products.In fact, the enterprise supply chain are only consider the suppliers, manufacturers, distributors, are not fully consider all stakeholders. Also includes the enterprise logistics system in the broadest sense of the upstream and downstream customers and all stakeholders. To add these factors to the enterprise logistics system, and then a new comprehensive cash flow and information flow, make up a complete enterprise V alue Chain (Value Chain). The stakeholders here refers to the main body of all affected by the enterprise business activities. A brewer, for example, it products to the customers' hands by seller, the related interests may be consumers, third party logistics enterprise, the brewery surrounding residents even by relevant government functional departments, etc. Consumer is the end of product logistics, third-party logistics can provide enterpriseswith services, factory nearby residents may claim of environmental problems caused by the enterprise, government functional departments may to the enterprise management to intervene. The enterprise value chain optimization to provide guarantee for efficient production, improve the service level of the enterprise, reasonable cost reduction, also should pay attention to the social benefits of enterprises properly. Otherwise, the enterprise internal logistics system can be affected by enterprise stakeholders and reach the purpose of the design.conclusionIn the 21st century, our country enterprise is facing the challenge of globalization, the vast majority of industry overcapacity, the buyer's purchasing power is lower than the market supply situation. In this case, the manufacturing and circulation to reduce logistics costs, improve the level of service as an important way to obtain competitive advantage. Logistics system cost reduction does not mean lower service levels at the same time. Control the logistics cost is to reduce the logistics cost to improve the level of service by the best matching point or range, so as to more effectively achieve the purpose of enterprises to reduce costs and promote corporate cutbacks. Chinese enterprises should be selectively absorb the successful experience of international logistics management research, and the theoretical circle to carry out all-round cooperation, to speed up the pace of the development of logistics in China.中文随着科学技术的快速发展和经济全球化趋势的增强,世界经济国家面临着前所未有的机遇和挑战。
物流外文文献翻译精选文档
物流外文文献翻译精选文档TTMS system office room 【TTMS16H-TTMS2A-TTMS8Q8-外文文献原稿和译文原稿Logistics from the English word "logistics", the original intent of the military logistics support, in the second side after World War II has been widely used in the economic field. Logistics Management Association of the United States is defined as the logistics, "Logistics is to meet the needs of consumers of raw materials, intermediate products, final products and related information to the consumer from the beginning to the effective flow and storage, implementation and control of the process of . "Logistics consists of four key components: the real flow, real storage, and management to coordinate the flow of information. The primary function of logistics is to create time and space effectiveness of the effectiveness of the main ways to overcome the space through the storage distance.Third-party logistics in the logistics channel services provided by brokers, middlemen in the form of the contract within a certain period of time required to provide logistics services in whole or in part. Is a third-party logistics companies for the external customer management, control and operation of the provision of logistics services company.According to statistics, currently used in Europe the proportion of third-party logistics services for 76 percent, the United States is about 58%, and the demand is still growing; 24 percent in Europe and the United States 33% of non-third-party logistics service users are actively considering the use of third-party logistics services. As a third-party logistics to improve the speed of material flow, warehousing costs and financial savings in the cost effective means of passers-by, has become increasingly attracted great attention.First, the advantages of using a third-party logisticsThe use of third-party logistics enterprises can yield many benefits, mainly reflected in:1, focus on core businessManufacturers can use a third-party logistics companies to achieve optimal distribution of resources, limited human and financial resources to concentrate on their core energy, to focus on the development of basic skills, develop new products in the world competition, and enhance the core competitiveness of enterprises.2, cost-savingProfessional use of third-party logistics providers, the professional advantages of mass production and cost advantages, by providing the link capacity utilization to achieve cost savings, so that enterprises can benefit from the separation of the cost structure. Manufacturing enterprises with the expansion of marketing services to participate in any degree of depth, would give rise to a substantial increase in costs, only the use of professional services provided by public services, in order to minimize additional losses. University of Tennessee in accordance with the United States, United Kingdom and the United States EXEL company EMST & YOUNG consulting firm co-organized a survey: a lot of cargo that enable them to use third-party logistics logistics costs declined by an average of percent, the average flow of goods from days to days, stock % lower.3, reduction of inventoryThird-party logistics service providers with well-planned logistics and timely delivery means, to minimize inventory, improve cash flow of the enterprise to achieve cost advantages.4, enhance the corporate imageThird-party logistics service providers and customers is a strategic partnership, the use of third-party logistics provider of comprehensive facilities and trained staff on the whole supply chain to achieve complete control, reducing the complexity of logistics, through their own networks to help improve customer service, not only to establish their own brand image, but also customers in the competition.Second, The purpose of the implementation of logistics managementThe purpose of the implementation of logistics management is to the lowest possible total cost of conditions to achieve the established level of customer service, or service advantages and seek cost advantages of a dynamic equilibrium, and thus create competitive enterprises in the strategic advantage. According to this goal, logistics management to solve the basic problem, simply put, is to the right products to fit the number and the right price at the right time and suitable sites available to customers.Logistics management systems that use methods to solve the problem. Modern Logistics normally be considered by the transport, storage, packaging, handling, processing in circulation, distribution and information constitute part of all. All have their own part of the original functions, interests and concepts. System approach is the use of modern management methods and modern technology so that all aspects of information sharing in general, all the links as an integrated system for organization and management, so that the system can be as low as possible under the conditions of the total cost, provided there Competitive advantage of customer service. Systems approach that the system is not the effectiveness of their various local links-effective simple sum. System means that, there's a certain aspects of the problem and want to all of the factors affecting the analysis and evaluation. From this idea of the logistics system is not simply the pursuit of their own in various areas of the lowest cost, because the logistics of the link between the benefits ofmutual influence, the tendency of mutual constraints, there is the turn of the relationship between vulnerability. For example, too much emphasis on packaging materials savings, it could cause damage because of their easy to transport and handling costs increased. Therefore, the systems approach stresses the need to carry out the total cost analysis, and to avoid the second best effect and weigh the cost of the analysis, so as to achieve the lowest cost, while meeting the established level of customer se rvice purposes.Third, China's enterprises in the use of third-party logistics problems inWhile third-party logistics company has many advantages, but not many enterprises will be more outsourcing of the logistics business, the reasons boil down to:1, resistance to changeMany companies do not want the way through the logistics outsourcing efforts to change the current mode. In particular, some state-owned enterprises, we reflow will also mean that the dismissal of outsourcing a large number of employees, which the managers of state-owned enterprises would mean a very great risk.2, lack of awarenessFor third-party logistics enterprise's generally low level of awareness, lack of awareness of enterprise supply chain management in the enterprise of the great role in the competition.3, fear of losing controlAs a result of the implementation of supply chain companies in enhancing the competitiveness of the important role that many companies would rather have a small but complete logistics department and they do not prefer these functions will be handed over toothers, the main reasons it is worried that if they lose the internal logistics capabilities, customers will be exchanges and over-reliance on other third-party logistics companies.4, the logistics outsourcing has its own complexitySupply chain logistics business and companies are usually other services, such as finance, marketing or production of integrated logistics outsourcing itself with complexity. On a number of practical business, including the integration of transport and storage may lead to organizational, administrative and implementation problems. In addition, the company's internal information system integration features, making the logistics business to a third party logistics companies have become very difficult to operate.5, to measure the effect of logistics outsourcing by many factorsAccurately measure the cost of information technology, logistics and human resources more difficult. It is difficult to determine the logistics outsourcing companies in the end be able to bring the cost of how many potential good things. In addition, all the uniqueness of the company's business and corporate supply chain operational capability, is usually not considered to be internal to the external public information, it is difficult to accurately compare the inter-company supply chain operational capability.Although some manufacturers have been aware of the use of third-party logistics companies can bring a lot of good things, but in practical applications are often divided into several steps, at the same time choose a number of logistics service providers as partners in order to avoid the business by a logistics service providers brought about by dependence.Fourth, China's third-party logistics companies in the development of the problems encounteredA successful logistics company, the operator must have a larger scale, the establishment of effective regional coverage area, with a strong command and control center with the high standard of integrated technical, financial resources and business strategy.China's third-party logistics companies in the development of the problems encountered can be summarized as follows:1, operating modelAt present, most of the world's largest logistics companies take the head office and branch system, centralized headquarters-style logistics operation to take to the implementation of vertical business management. The establishment of a modern logistics enterprise must have a strong, flexible command and control center to control the entire logistics operations and coordination. Real must be a modern logistics center, a profit center, business organizations, the framework, the institutional form of every match with a center. China's logistics enterprises in the operating mode of the problems of foreign logistics enterprises in the management model should be from the domestic logistics enterprises.2, the lack of storage or transport capacityThe primary function of logistics is to create time and space utility theft. For now China's third-party logistics enterprises, some companies focus on storage, lack of transport capacity; other companies is a lot of transport vehicles and warehouses throughout the country little by renting warehouses to complete the community's commitment to customers. 3, network problemsThere are a few large companies have the logistics of the entire vehicle cargo storage network or networks, but the network coverage area is not perfect. Customers in the choice of logistics partner, are very concerned about network coverage and network of regionalbranches of the density problem. The building of the network should be of great importance to logistics enterprises.4, information technologyThe world's largest logistics enterprises have "three-class network", that is, orders for information flow, resources, global supply chain network, the global Resource Network users and computer information network. With the management of advanced computer technology, these customers are also the logistics of the production of high value-added products business, the domestic logistics enterprises must increase investment in information systems can change their market position.Concentration and integration is the third-party logistics trends in the development of enterprises. The reasons are: firstly, the company intends to major aspects of supply chain outsourcing to the lowest possible number of several logistics companies; the second, the establishment of an efficient global third party logistics inputs required for increasing the capital; the third Many third-party logistics providers through mergers and joint approaches to expand its service capabilities.译文物流已广泛应用于经济领域中的英文单词“物流”,军事后勤保障的原意,在二战结束后的第二面。
- 1、下载文档前请自行甄别文档内容的完整性,平台不提供额外的编辑、内容补充、找答案等附加服务。
- 2、"仅部分预览"的文档,不可在线预览部分如存在完整性等问题,可反馈申请退款(可完整预览的文档不适用该条件!)。
- 3、如文档侵犯您的权益,请联系客服反馈,我们会尽快为您处理(人工客服工作时间:9:00-18:30)。
中英文翻译原文Logistics costs and controllingAbstractLogistic costs are defined differently in companies. In many cases, the reported logistic costs of companies even within the same business differ more than justified by their operations. Some companies do not count interest and depreciation on inventories as logistic costs. Others include the distribution costs of their suppliers or the purchasing costs. In some cases, even the purchase value of the procured goods is included in the logistic costs (Baumgarten et al. 1993; Gudehus and Kotzab 2004; Weber 2002).Logistic costs are defined differently in companies. In many cases, the reported logistic costs of companies even within the same business differ more than justified by their operations. Some companies do not count interest and depreciation on inventories as logistic costs. Others include the distribution costs of their suppliers or the purchasing costs. In some cases, even the purchase value of the procured goods is included in the logistic costs (Baumgarten et al. 1993; Gudehus and Kotzab 2004; Weber 2002).Another problem, which arises not only in logistics, is costing and pricing of intangible goods. Intangible goods, such as logistic services, provide immediate utility and are generally not storable. Therefore, the conventional methods ofaccounting, costing and pricing, which have been developed for tangible goods, are of limited value for logistics (Cooper 1992; Horvàth 1999; Johnson 1987).More appropriate for the calculation of performance costs are process-related cost accounting and activity based costing. However, in logistics as well as in other areas of business, the definition and calculation of process costs differs (Bragg 2001; Hicks 2002; Horvàth 1999; Pohlen and LaLonde 1994; Poist 1974). This holds especially for the performance costs of multifunctional logistic systems, for pricing of integrated performances and for the consideration of fixed costs.As long as they are defined, measured and calculated differently, logistic costs, cost rates and prices cannot be compared. Any benchmarking based on such doubtful indicators is misleading (see Sect. 4.5). Hence, reported market volumes and market shares of logistics are at best educated guesses (Baumgarten et al. 1993; Kille and Klaus 2007; Müller-Steinfahrt 1998).The situation in logistic controlling and supply chain controlling is even worse (Cooper and Kaplan 1998; Manrodt et al. 1999; Seuring 2006). Only a minority of companies records and monitors logistic costs separately and continuously (Weber 2002). Whereas in industry the total logistic costs range between 5 and 15% of turnover, in trade companies they make up between 10 and 25% of turnover (Baumgarten et al. 1993; Gudehus 1999/2007). For retailers, logistic costs can use up more than one third of the profit margin. Despite this, it is still the exception for retailers to record and monitor the logistic costs from the ramp of the suppliers to the point of sales.Logistic controlling does not only include calculation, budgeting and recording of costs, but also the monitoring of performance and quality. Controlling should consult management in the planning, set up and operation of optimal systems. To enable this, it has to determine and specify for improvements in service, performance, quality, and costs (Cooper 1992; Darkow 2001; Horvàth 1999; Johnson 1987; Weber et al. 1993, 2002).Where and with what accuracy costs, performances and quality should be recorded and monitored depends on the contribution of logistics to the value creation, on the core competencies and objectives of the company, and on current projects. In logistic controlling, as in other areas, less is more: it is better to control a small number of meaningful key performance indicators (KPI) with adequate accuracy in longer time spans, than to monitor all possible performance, quality and cost data with high precision permanently without knowing the demand for these information(Manrodt et al. 1999). For controlling, not the precision of the performance and cost data, but their practical use and application are decisive.In this chapter, the logistic costs are consistently defined, the fundamental issues of logistic costing are presented, and practicable methods for the calculation of use dependent cost rates are developed. This includes a discussion of the fixed-cost dilemma of logistics, the relationship between logistic costs and performance rates and the most effective options for reducing logistic costs. Using the results of this chapter, in the following chapter cost-based prices and pricing systems for logistic performances and services are derived.Cost Accounting and Performance CostingCorresponding to the stationary or structural aspect and to the dynamic or process aspect, two different types of accounting are necessary. Cost accounting for longer periods keeps a stationary point of view, while performance costing for shorter periods reflects the dynamic perspective.Logistic Cost CalculationAs the general cost calculation of a company, the logistic cost calculation comprises standard cost calculation, accompanying cost calculation and final cost calculation (Horváth 1999; Weber 2002; Wöhe and Döring 2008).Standard Cost CalculationSubjects of standard cost calculation or planned cost calculation are the future operating costs for an existing or a planned system. Results are standard logistic costs and target performance costs.Standard cost calculation is necessary for investment decisions, for planning systems, processes and projects, for cost accounting and benchmarking of future periods and for the calculation of prices and tariffs.Accompanying Cost CalculationAccompanying cost calculation aims for a continuous control of all costs caused by the execution of logistic tasks and services during the current accounting period. The result of accompanying cost calculation is information for management about the current costs and utilization of resources.Knowing the costs and the utilization of the resources allows initiating appropriate measures for reducing costs, adaptation of resources and improving capacity utilization in due time. The results of the accompanying cost calculation can be used also for invoicing and compensation of logistic service providers, if costs-based prices have been agreed.Final Cost CalculationSubjects of final cost calculation or post calculation are the operating costs of closed periods in the past. The real logistic costs and cost rates can be compared with the respective target values and benchmarks. This allows conclusions for standard costing and pricing.Most important causes for deviations of real costs from the target values in logistics are:●Cost factors, especially personnel costs, have been planned, assumed orexpected too high or too low.●Utilization of resources, such as transport means, storage systems,machines, and production facilities, has been planned or expectedfalsely.●Empty runs of transport means and filling degrees of transport and loadunits were incorrectly planned.●The actual utilization structure of the logistic system differs from theanticipated structure.The first two reasons for differences between real and target costs are normally caused by the planner and the operator of a logistic system. A too high share of empty runs and bad utilization of storage capacities is in many cases also the result of unqualified planning or poor scheduling. However, this can be caused also by a user, who changed transport relations, demand structure or stock levels. Aninsufficient utilization can also be initiated by a wrong demand forecast or false information from the customers.For a dedicated logistic system, which is used for a longer period of time by one or a small number of companies based on individual contracts, the users must bear the risk of changing demand and the cost differences resulting from a deviating utilization of the ready held resources. Final cost calculation for dedicated logistic systems can be used for the utilization based allocation of surpluses or additional costs to the different usersFor a multi-user logistic system, where tasks and services are offered on the market and used only for shorter periods of time by many different customers, the risk for changing demand and insufficient utilization is born by the logistic service provider. This risk is compensated by the chances for higher profit from better utilization or favorable demand structure. Furthermore, the service provider can influence the demand by his sales efforts and by offering utilization dependent prices. For multi-user logistic systems the structure and utilization risk are incorporated in the pricesComponents of Logistic CostsThe total logistic costs are a sum of specific logistic costs, additional logistic costs and administrative costs:●Specific logistic costs are all costs of a performance station, a profit centeror a company, which are caused by executing the genuine operativelogistic tasks transport, handling, storing and commissioning.●Additional logistic costs are caused by executing additional operative taskswhich are directly connected with the genuine logistic tasks, such aspacking, labeling, loading and unloading, quality control or handling ofempties.●Administrative logistic costs are costs for related administrative services,such as scheduling, quality management and controlling, which go alongwith the execution of logistic performances and additional services.Costs for non-logistic tasks, such as research and development, construction, production, assembling, marketing, sales and general administration, are not part of the logistic costs. Also, the costs for buying and procuring merchandise, parts, material and equipment are not logistic costs as long as they are not directly caused by the execution of logistic tasks and related services. For instance, the costs for packing sales units are production costs, whereas the costs for packing material, pallets, bins and load carriers are material costs of logistics.When designing and optimizing company logistics as well as when scheduling orders and inventories, it is necessary to keep in mind that many logistic activities also have an effect on non-logistic costs and revenues. They influence setup costs, out-of-stock costs, disruption costs and ordering costs as well as prices, profit margins and turnover. Hence, logisticians always have to bear in mind the economic principle:Logistic activities as all other activities in the company should maximize the difference between revenues and costs at lowest capital investment.Elements of Logistic Costs●Personnel costs: wages for workers and salaries for employees with logisticresponsibilities, including personal taxes, vacation, illness, absence, etc.●Space and area costs: Depreciation and interest for the owned assets andbuildings, rents and leasing fees for external buildings, halls and areas,including related heating, climate, maintenance and surveillance costs.●Route and network costs: Depreciation and interest for own and fees forexternal driveways, routes, roads, highways, railroads and transshipmentpoints●Costs for logistic equipment: Depreciation, interest and operating costs forown as well as rental fees and leasing costs for external logistic equipmentsuch as racks, forklifts, transport means, cranes, conveyors and handlingequipment, control systems and process computers, including theequipment-caused energy, cleaning, repair and maintenance costs.●Load carrier costs: Depreciation and interest for own as well as rental feesand leasing costs for external load carriers, such as pallets, bins, barrels,racks, cassettes and containers, including the costs for cleaning, repair,maintenance and empties management.●Logistic material costs: Expenditures for packing material, transportpacking, load securing, labels and other material, which is needed in orderto perform logistic tasks and services.●Logistic IT-costs: Depreciation, interest and operating costs for ownIT-systems as well as costs for external IT-systems as far as used forlogistic purposes.●Third party logistic expenses: Freights, rental fees and other expenses forlogistic service providers.●Taxes, duties and insurance fees, which accumulate during the execution oflogistic tasks and services, as far as related to logistic purposes.●Planning and project costs: Depreciation and interest on activated expensesfor planning, project management and implementation accumulated up tothe start of the economic utilization of a logistic system.●Inventory holding costs: Interest and write offs on all stationary andmoving inventories, in stocks, on buffer places and in transport.In some companies the inventory holding costs include only the interest caused by the capital commitment. Obsolescence costs as well as write-offs due to non-marketability, deterioration or stock decline are often neglected. However, the write-offs on inventories of fashion, perishable, high value or electronic goods can be as high as or even higher than the interest.译文物流成本和控制物流成本定义在不同公司是不同的。