柱塞泵毕业设计外文文献翻译
机械设计过程外文文献翻译、中英文翻译

附录英文Machine design processThe machine is the organization with other components combinations, transforms,the transmission or using the energ,the strength or the movementexample for the beneficial use has the engine.the turbine wheel,the vehicles.the hoist,the printer,the washer and the movie camera Many is suitable tbr themachine design principle and the strength law also is suitable to is not thegenuine machine finished product.the driven wheel hub and the file cabinet tothe measuring appl iance and the nuclear pressure vessel.”Machine designt thisterminology compared to”machine design”more generalized,it including machine design.But regarding certain instruments.1ike uses to determine hot,the mobile line and the volume thermal energy as well as the fluid aspect question needs alone to consider.But when machine design must consider themovement and the structure aspect question as well as preserved and the sealstipulation.In the mechanical engineering domain and all that project domainapplication machine design,all need such as mechanism and so on the svdtch,cam,valve,vessel and mixer.The design beginning tO being true or the imagination need.The existing instrument possibly needs in the durability,the efficiency,the weight,the speedor the cost performs to improve.]he possible need new instrument tO completebefore made the function by the person.1ike t was abundant Assembly or maintenance.After the goal completely or partially determines,the design nextstep is the idea carl complete needs the ffmction the organization and its thearrangement for this,the free hand drawing schematic diagram value is enormous,it not only takes a person idea the recording and the auxiliary.methodwhich if the other people discusses,moreover especially is suitable for with ownidea exchange,also needs to concern as the creative mentality stimulant to thepart widespread knowledge,because a new machine frequently by knew very well each kind of components rearrange or the replace become,perhaps changedthe size and the material.Regardless of after idea process or,a designer callcarry on fast either the sketchy computation or the analysis determines thegeneral size and the feasibility.After about need or may use the spatial meteidea determination,may start according to the proportion picture schematicdiagram.When several components approximate shapes and several sizes come out,the analysis was allowed truly to start.The analysis goal lies in enable it to havesatisfying or the superior performance,as well as will seek the best proportionand the size under the smallest weight security and the durability and thecompetitive cost designer for each essential load bearing section,as well asseveral components intensities balance then choice material and processingmethod.These important goals only have through only then may obtain based on the mechanism analysis,like about reacting force and friction most superioruse principie of statics;About inertia,acceleration and energy principle ofdynamics:About stress and deflection material elasticity and intensity principle;About material physical behavior principle;About lubrication and water poweractuation hydromechanics principle.The analysis may identical engineer whicharranges by the idea machinery do,or makes the analysis in the big company bythe independent analysis department or the research group the result,possibleneed new arrangement and new size.No matter is officially does orunofficialdoes,supposes Japan is relapse and the cooperation process.the analysis staffmay play the role to all stages but not merely is he stage.Some design criteriaIn this part,some people suggested carries on the analysis using the creative manner,this kind of analysis may cause the significant improvement aswell as to the spare product idea and the consummation,the product functionmore.more economical,is perhaps more durable. The creation stage does notneed is at first and the independent stage.Alttlough the analysis staff possiblycertainlv is not responsible for the entire design,but he not meyely is can fromthe numeral proposc wants question correct answer which he soIVes,not merelyis Droduces the stress value,the size or the work limit. He may propose a morewidespread opinion,in order to improvement standard or plan. Because beforethe analysis or in the analysis process,he can familiar install and its the workingcondition.he is in an idea to prepare chooses the plan the rantage Poinl.Best hecan propose the suggestion transfigure eliminates the moment of force or thestress concentration,but was not the permission constructs has the blgsectlonand the excessively many dynamic loads organization should better be he discards his careful desi{;n but is not afterwards saw the machinery discarded.In order to stimulate the creative thought,below suggested designs thepersonnel and the analysis staff uses the criterion.The first 6 criteria especially are suitable for the analysis staff,although he possibly involves to possesses this l o items.1.Creatively the use needs the physical performance and the control doesnot need.2.Knows the practical load and its the importance.3.D00s not consider the function load in advance.4.Invents the more advantageous loading environment.5.Provides the minimurn weight the most advantageous stress distributionand the rigidity.6.uses the fundamental equation computation proportion and causes thesize optimization.7.The selection material obtains the perlbrmance combination.8.In between spare parts and integrated components carefid choice. 9.Revisions functional design adapts the production process and reduces thecost.10.In the consideration assembly causes the part pintpointing and mutuallydoes not disturb.Designs the personnel to have in such domain,like the statics,the inematics,dynamics and the materials mechanics have the good accomplishment,in addition.but also must familiar make the material and themanufacture craft.Designs the personnel to have to be able to combine allcollrelations the fact,carries on teaches Wei.the manufacture schematic diagramand the charting comes the manufacture request totransmit the workshop. Any product design one of first step of work is the choice uses in to makeeach part the material.Today design personnel may obtain innumerably.When choice,the product function,the outward appearance,the material cost and theproduction cost very are all important.Before any computation must carefullyappraise the material the performance.It is the necessary careful computation toguarantee the design the validity The computation ever does not appear on thechart,but is saved by ten each kind of reason.Once any part expires,had makeclear when is designing at first this had the flaw the components has made any;Moreover,。
机械毕业设计英文外文翻译201混凝土运输车中液压泵压力的影响 (2)

附录AInvestigation on Pressure Impact in ConcretePumping Hydraulic SystemAbstract:The pressure impact in hydraulic systems of such concrete pumping machinery as trailer concrete pump,transported concrete pump,and truck mounted concrete pump,is a key factor affecting their reliability and usage life.Based on the pressure forming principle of the oil in a hydrostatic closed pressure chamber,the mechanism of producing pressure impact is analyzed synthetically,and the theory that oil flow matches requirement,and pump displacement control harmonizes valve shifting time control,to mitigate pressure impact,is put forward.The quantitative controlling parameters about shifting time and displacement control are introduced to realize accurate control.The experiment investigations of pressure impact property and its control are carried through on an experimental system which is able to simulate concrete pumping condition.The basic law that pressure impact and controlling parameters vary with working condition respectively.The feasibility and validity of the technology proposed in this paper to control pressure impact are confirmed.Keywords: Pressure impact;Hydraulic system;Concrete pumping machinery.1 IntroductionDuring working process of such concrete machinery as trailer concrete pump,transported concrete pump,and truck mounted concrete pump,two oil cylinders drive two concrete delivery cylinders respectively,and quickly switch direction with the possible highest frequency of more than 30 times per minute,which generates serious hydraulic impact.It is an important factor resulting in bad performance and low use reliability of the machine,and vibration,noise and overheating etc.so it’s a key of improving concrete pumping machinery’s reliability to gain a mastery of pressure impact property in concrete pumping hydraulic system and its controlling technology.Such technological measures as follows were taken to reduce pressure impact:(1)installation of a hydraulic accumulator or unloading valves,(2) change of sliding spool’s structure,(3)control of the switching speed of sliding spool,etc[1].Though these measures play an important role in absorption of pressure surges,there are obvious limitations,and they are passive measures.Literature.2. investigated the switching process of concrete pumping hydraulic system,and put forward active measure of regulating oil pump’s displacement to reduce pressureimpact.Literature[3]studied the intrinsic relationship between shifting time and pressure impact,and proposed a new concept of optimal shifting time.Therefore,in this paper, experiments were conducted to find out pressure impact forming law,and both oil pump’s displacement and directional—control valve’s shifting time were controlled simultaneously to seek optimal control scheme for effective reduction of pressure impact.2 Experimental principleThe pressure variation of the oil in a pressure chamber depends upon the difference between volumes of the oil flowing in and out the chamber[2].It’s obvious that effective reduction of this difference is of positive significance for depressing pressure impact.As far as concrete pumping hydraulic system is concerned, the pressure impact resulting from the main oil cylinders’stroke terminal lies upon the suitability of shifting time to a great extent[3].So it’s feasible and effective for absorbing pressure impact to accurately control oil pump’s displacement according to hydraulic system’s requirement,and combine it with shifting time control technique.What is shown in Fig.1 is the principle drawing of the experimental system sued to study characteristics of pressure impact in concrete pumping hydraulic system and its controlling techniques.The main oil pump(1)is a swash-plate type axial piston pump,which is provided with the function of constant horsepower control。
液压系统外文文献翻译中英文

外文文献翻译(含:英文原文及中文译文)英文原文Hydraulic systemW Arnold1 IntroductionThe hydraulic station is called a hydraulic pump station and is an independent hydraulic device. It is step by step to supply oil. And control the direction of hydraulic oil flow, pressure and flow, suitable for the host and hydraulic equipment can be separated on the various hydraulic machinery.After the purchase, the user only needs to connect the hydraulic station and the actuator (hydraulic or oil motor) on the mainframe with different tubings. The hydraulic machine can realize various specified actions and working cycles.The hydraulic station is a combination of manifolds, pump units or valve assemblies, electrical boxes, and tank electrical boxes. Each part function is:The pump unit is equipped with a motor and an oil pump, which is the power source of the hydraulic station and can convert mechanical energy into hydraulic oil pressure energy.V alve combination - its plate valve is mounted on the vertical plate, and the rear plate is connected with the same function as the manifold.Oil manifolds - assembled from hydraulic valves and channel bodies. It regulates hydraulic oil pressure, direction and flow.Box--a semi-closed container for plate welding. It is also equipped with an oil screen, an air filter, etc., which is used for cooling and filtering of oil and oil.Electrical box - divided into two types: one is to set the external lead terminal board; one is equipped with a full set of control appliances.The working principle of the hydraulic station: The motor drives the oil pump to rotate, then the pump sucks oil from the oil tank and supplies oil, converts the mechanical energy into hydraulic pressure energy, and the hydraulic oil passes through the manifold (or valve assembly) to adjust the direction, pressure and flow and then passes through the external tube. The way to the hydraulic cylinder or oil motor in the hydraulic machinery, so as to control the direction of the hydraulic motor, the strength of the speed and speed, to promote all kinds of hydraulic machinery to do work.(1) Development history of hydraulic pressureThe development history of hydraulics (including hydraulic power, the same below), pneumatics, and seals industry in China can be roughly divided into three stages, namely: the starting stage in the early 1950s to the early 60s; and the professional in the 60s and 70s. The growth stage of the production system; the 80-90's is a stage of rapid development. Among them, the hydraulic industry began in the early 1950s with thedevelopment of hydraulic machines such as Grinding Machines, broaching machines, and profiling lathes, which were produced by the machine tool industry. The hydraulic components were produced by the hydraulic workshop in the machine tool factory, and were produced for self use. After entering the 1960s, the application of hydraulic technology was gradually promoted from the machine tool to the agricultural machinery and engineering machinery. The original hydraulic workshop attached to the main engine plant was independent and became a professional manufacturer of hydraulic components. In the late 1960s and early 1970s, with the continuous development of mechanization of production, particularly in the provision of highly efficient and automated equipment for the second automobile manufacturing plant, the hydraulic component manufacturing industry witnessed rapid development. The batch of small and medium-sized enterprises also began to become specialized manufacturers of hydraulic parts. In 1968, the annual output of hydraulic components in China was close to 200,000 pieces. In 1973, in the fields of machine tools, agricultural machinery, construction machinery and other industries, the professional factory for the production of hydraulic parts has grown to over 100, and its annual output exceeds 1 million pieces. Such an independent hydraulic component manufacturing industry has taken shape. At this time, the hydraulic product has evolved from the original imitation Su product intoa combination of imported technology and self-designed products. The pressure has been developed towards medium and high pressures, and electro-hydraulic servo valves and systems have been developed. The application of hydraulics has been further expanded. The pneumatic industry started a few years later than hydraulics, and it was only in 1967 that it began to establish a professional pneumatic components factory. Pneumatic components began to be manufactured and sold as commodities. Its sealing industry including rubber seals, flexible graphite seals, and mechanical seals started from the production of common O-rings, oil seals, and other extruded rubber seals and asbestos seal products in the early 1950s. In the early 1960s, it began to develop and produce flexible products. Graphite seals and mechanical seals and other products. In the 1970s, a batch of batches of professional production plants began to be established one after another in the systems of the former Ministry of Combustion, the Ministry of Agriculture, and the Ministry of Agricultural Machinery, formally forming the industry, which laid the foundation for the development of the seal industry.In the 1980s, under the guidance of the national policy of reform and opening up, with the continuous development of the machinery industry, the contradiction between the basic components lags behind the host computer has become increasingly prominent and caused the attention of all relevant departments. To this end, the former Ministry of Machinesestablished the General Infrastructure Industry Bureau in 1982, and unified the original pneumatic, hydraulic, and seal specialties that were scattered in the industries of machine tools, agricultural machinery, and construction machinery, etc. The management of a piece of office, so that the industry in the planning, investment, the introduction of technology and scientific research and development and other aspects of the basic parts of the bureau's guidance and support. This has entered a period of rapid development, it has introduced more than 60 foreign advanced technology, of which more than 40 hydraulic, pneumatic 7, after digestion and absorption and technological transformation, are now mass production, and has become the industry's leading products . In recent years, the industry has intensified its technological transformation. From 1991 to 1998, the total investment of national, local, and corporate self-raised funds totaled about 2 billion yuan, of which more than 1.6 billion were hydraulic. After continuous technological transformation and technological breakthroughs, the technical level of a group of major enterprises has been further improved, and technological equipment has also been greatly improved, laying a good foundation for forming a high starting point, specialization, and mass production. In recent years, under the guidance of the principle of common development of multiple ownership systems in the country, various small and medium-sized enterprises with different ownership have rapidly emerged and haveshown great vitality. With the further opening up of the country, foreign-funded enterprises have developed rapidly, which plays an important role in raising industry standards and expanding exports. So far China has established joint ventures with famous manufacturers in the United States, Germany, Japan and other countries or directly established piston pumps/motors, planetary speed reducers, hydraulic control valves, steering gears, hydraulic systems, hydrostatic transmissions, and hydraulic components. The company has more than 50 manufacturing enterprises such as castings, pneumatic control valves, cylinders, gas processing triplets, rubber seals, and mechanical seals, and has attracted more than 200 million U.S. dollars in foreign capital.(2) Current statusBasic profileAfter more than 40 years of hard work, China's hydraulics, pneumatics and seals industry has formed a complete industrial system with a certain level of production capacity and technical level. According to the statistics of the third n ational industrial census in 1995, China’s state-owned, privately-owned, cooperative, village-run, individual, and “funded enterprises” have annual sales income of more than 1 million yuan in hydraulic, pneumatic, and seal industrial townships and above. There are a total of more than 1,300 companies, including about 700 hydraulics, and about 300 pneumatic and sealing parts. According to thestatistics of the international industry in 1996, the total output value of the hydraulic industry in China was about 2.448 billion yuan, accounting for the 6th in the world; the total output value of the pneumatic industry was about 419 million yuan, accounting for the world’s10 people.2. Current supply and demand profileWith the introduction of technology, independent development and technological transformation, the technical level of the first batch of high-pressure plunger pumps, vane pumps, gear pumps, general hydraulic valves, oil cylinders, oil-free pneumatic components and various types of seals has become remarkable. Improve, and can be stable mass production, provide guarantees for all types of host to improve product quality. In addition, certain achievements have also been made in the aspects of CAD, pollution control, and proportional servo technology for hydraulic pneumatic components and systems, and have been used for production. So far, the hydraulic, pneumatic and seal products have a total of about 3,000 varieties and more than 23,000 specifications. Among them, there are about 1,200 types of hydraulic pressure, more than 10,000 specifications (including 60 types of hydrodynamic products, 500 specifications); about 1350 types of pneumatic, more than 8,000 specifications; there are also 350 types of rubber seals, more than 5000 The specifications are now basically able to adapt to the general needs ofvarious types of mainframe products. The matching rate for major equipment sets can reach more than 60%, and a small amount of exports has started.In 1998, the domestic production of hydraulic components was 4.8 million pieces, with sales of about 2.8 billion yuan (of which mechanical systems accounted for 70%); output of pneumatic components was 3.6 million pieces, and sales were about 550 million yuan (including mechanical systems accounting for about 60%) The production of seals is about 800 million pieces, and the sales volume is about 1 billion yuan (including about 50% of mechanical systems). According to the statistics of the annual report of the China Hydraulic and Pneumatic Sealing Industry Association in 1998, the production and sales rate of hydraulic products was 97.5% (101% of hydraulic power), 95.9% of air pressure, and 98.7% of seal. This fully reflects the basic convergence of production and sales.Although China's hydraulic, pneumatic and sealing industries have made great progress, there are still many gaps compared with the development needs of the mainframe and the world's advanced level, which are mainly reflected in the variety, performance and reliability of products. . Take hydraulic products as an example, the product varieties are only 1/3 of the foreign country, and the life expectancy is 1/2 of that of foreign countries. In order to meet the needs of key hosts, imported hosts, and majortechnical equipment, China has a large number of imported hydraulic, pneumatic, and sealing products every year. According to customs statistics and relevant data analysis, in 1998, the import volume of hydraulic, pneumatic and seal products was about 200 million U.S. dollars, of which the hydraulic pressure was about 140 million U.S. dollars, the pneumatics were 30 million U.S. dollars, and the seal was about 0.3 billion U.S. dollars. The year is slightly lower. In terms of amount, the current domestic market share of imported products is about 30%. In 1998, the total demand for hydraulic parts in the domestic market was about 6 million pieces, and the total sales volume was 4 billion yuan; the total demand for pneumatic parts was about 5 million pieces, and the total sales volume was over 700 million yuan; the total demand for seals was about 1.1 billion yuan. Pieces, total sales of about 1.3 billion yuan. (3) Future developments1. The main factors affecting development(1) The company's product development capability is not strong, and the level and speed of technology development can not fully meet the current needs for advanced mainframe products, major technical equipment and imported equipment and maintenance;(2) Many companies have lagged behind in manufacturing process, equipment level and management level, and their sense of quality is not strong, resulting in low level of product performance, unstable quality,poor reliability, and insufficiency of service, and lack of user satisfaction. And trusted branded products;(3) The degree of professional specialization in the industry is low, the power is scattered, the duplication of the low level is serious, the product convergence between the region and the enterprise leads to blind competition, and the prices are reduced each other, thus the efficiency of the enterprise is reduced, the funds are lacking, and the turnover is difficult. Insufficient investment in development and technological transformation has severely restricted the overall level of the industry and its competitive strength.(4) When the degree of internationalization of the domestic market is increasing, foreign companies have gradually entered the Chinese market to participate in competition, coupled with the rise of domestic private, cooperative, foreign-funded, and individual enterprises, resulting in increasing impact on state-owned enterprises. .2. Development trendWith the continuous deepening of the socialist market economy, the relationship between supply and demand in the hydraulic, pneumatic and sealed products has undergone major changes. The seller market characterized by “shortage” has basically become a buyer’s market characterized by “structured surplus”. Replaced by. From the perspective of overall capacity, it is already in a trend of oversupply, and in particular,general low-grade hydraulic, pneumatic and seals are generally oversupply; and like high-tech products with high technological content and high value and high value-added products that are urgently needed by the host, Can not meet the needs of the market, can only rely on imports. After China's entry into the WTO, its impact may be greater. Therefore, during the “10th Five-Y ear Plan” period, the growth of the industry’s output value must not only rely on the growth of quantity. Instead, it should focus on the structural contradiction of the industry and intensify efforts to adjust the industrial structure and product structure. It should be based on the improvement of quality. Product technology upgrades in order to adapt to and stimulate market demand, and seek greater development.2. Hydraulic application on power slide(1) Introduction of Power Sliding TableUsing the binding force curve diagram and the state space analysis method to analyze and study the sliding effect and the smoothness of the sliding table of the combined machine tool, the dynamics of the hydraulic drive system of the sliding table—the self-regulating back pressure regulating system are established. mathematical model. Through the digital simulation system of the computer, the causes and main influencing factors of the slide impact and the motion instability are analyzed. What kind of conclusions can be drawn from those, if we canreasonably design the structural dimensions of hydraulic cylinders and self-regulating back pressure regulators ——The symbols used in the text are as follows:s 1 - flow source, that is, the flow rate of the governor valve outlet;S el —— sliding friction of the sliding table;R - the equivalent viscous friction coefficient of the slide;I 1 - quality of slides and cylinders;12 - self-adjusting back pressure valve core quality;C 1, c 2 - liquid volume without cylinder chamber and rod chamber;C 2 - Self-adjusting back pressure valve spring compliance;R 1, R2 - Self-adjusting back pressure valve damping orifice fluid resistance;R 9 - Self-adjusting back pressure valve valve fluid resistance;S e2——initial pre-tightening force of self-adjusting back pressure valve spring;I 4, I5 - Equivalent liquid sense of the pipeline;C 5, C 6 - equivalent liquid capacity of the pipeline;R 5, R7 - Equivalent liquid resistance of the pipeline;V 3, V4 - cylinder rodless cavity and rod cavity volume;P 3, P4—pressure of the rodless cavity and rod cavity of the cylinder;F - the slide bears the load;V - speed of slide motion;In this paper, the power bond diagram and the state space splitting method are used to establish the system's motion mathematical model, and the dynamic characteristics of the slide table can be significantly improved.In the normal operation of the combined machine tool, the magnitude of the speed of the slide, its direction and the load changes it undergoes will affect its performance in varying degrees. Especially in the process of work-in-process, the unsteady movement caused by the advancing of the load on the slide table and the cyclical change of the load will affect the surface quality of the workpiece to be machined. In severe cases, the tool will break. According to the requirements of the Dalian Machine Tool Plant, the author used the binding force curve diagram and the state space analysis method to establish a dynamic mathematical model of a self-adjusting back pressure and speed adjustment system for the new hydraulic drive system of the combined machine tool slide. In order to improve the dynamic characteristics of the sliding table, it is necessary to analyze the causes and main influencing factors of the impetus and movement of the sliding table. However, it must pass the computer's digital simulation and the final results obtained from the research.(2) Dynamic Mathematical ModelThe working principle diagram of the self-adjusting back pressure speedregulation system of the combined machine tool slide hydraulic drive system is shown in the figure. This system is used to complete the work-cycle-stop-rewind. When the sliding table is working, the three-position four-way reversing valve is in the illustrated position. The oil supply pressure of the oil pump will remain approximately constant under the effective action of the overflow valve, and the oil flow passes through the reversing valve and adjusts the speed. The valve enters the rodless chamber of the cylinder to push the slide forward. At the same time, the pressurized oil discharged from the rod chamber of the cylinder will flow back to the tank through the self-regulating back pressure valve and the reversing valve. During this process, there was no change in the operating status of both the one-way valve and the relief valve. The complex and nonlinear system of the hydraulic drive system of the self-adjusting back pressure governor system is a kind of self-adjusting back-pressure governor system. To facilitate the study of its dynamic characteristics, a simple and reasonable dynamic mathematical model that only considers the main influencing factors is established. Especially important [1][2]. From the theoretical analysis and the experimental study, we can see that the system process time is much longer than the process time of the speed control valve. When the effective pressure bearing area of the rodless cavity of the fuel tank is large, the flow rate at the outlet of the speed control valve is instantaneous. The overshoot is reflected in thesmall change in speed of the slide motion [2]. In order to further broaden and deeply study the dynamic characteristics of the system so that the research work can be effectively performed on a miniature computer, this article will further simplify the original model [2], assuming that the speed control valve is output during the entire system pass. When the flow is constant, this is considered to be the source of the flow. The schematic diagram of the dynamic model structure of this system is shown in Fig. 2. It consists of a cylinder, a sliding table, a self-adjusting back pressure valve, and a connecting pipe.The power bond graph is a power flow graph. It is based on the transmission mode of the system energy, based on the actual structure, and uses the centralized parameters to represent the role of the subsystems abstractly as a resistive element R, a perceptual element I, and a capacitive element. Three kinds of role of C. Using this method, the physical concept of modeling is clear, and combined with the state-space analysis method, the linear system can be described and analyzed more accurately. This method is an effective method to study the dynamic characteristics of complex nonlinear systems in the time domain. According to the main characteristics of each component of the self-adjusting back pressure control system and the modeling rules [1], the power bond diagram of the system is obtained. The upper half of each key in the figure represents the power flow. The two variables that makeup the power are the force variables (oil pressure P and force F) and the flow variables (flow q and velocity v). The O node indicates that the system is connected in parallel, and the force variables on each key are equal and the sum of the flow variables is zero; 1 The nodes represent the series connection in the system, the flow variables on each key are equal and the sum of the force variables is Zero. TF denotes a transformer between different energy forms. The TF subscripted letter represents the conversion ratio of the flow variable or the force variable. The short bar on the key indicates the causal relationship between the two variables on the key. The full arrow indicates the control relationship. There are integral or differential relationships between the force and flow variables of the capacitive and perceptual elements in the three types of action elements. Therefore, a complex nonlinear equation of state with nine state variables can be derived from Fig. 3 . In this paper, the research on the dynamic characteristics of the sliding table starts from the two aspects of the slide's hedging and the smoothness of the motion. The fourth-order fixed-length Runge-Kutta is used for digital simulation on the IBM-PC microcomputer.(3) Slide advanceThe swaying phenomenon of the slide table is caused by the sudden disappearance of the load acting on the slide table (such as drilling work conditions). In this process, the table load F, the moving speed V, and thepressure in the two chambers of the cylinder P3 and P4 can be seen from the simulation results in Fig. 4. When the sliding table moves at a uniform speed under the load, the oil pressure in the rodless cavity of the oil cylinder is high, and a large amount of energy is accumulated in the oil. When the load suddenly disappears, the oil pressure of the cavity is rapidly reduced, and the oil is rapidly reduced. When the high-pressure state is transferred to the low-pressure state, a lot of energy is released to the system, resulting in a high-speed forward impact of the slide. However, the front slide of the sliding table causes the pressure in the rod cavity of the oil cylinder to cause the back pressure to rise, thereby consuming part of the energy in the system, which has a certain effect on the kicking of the slide table. We should see that in the studied system, the inlet pressure of the self-adjusting back pressure valve is subject to the comprehensive effect of the two-chamber oil pressure of the oil cylinder. When the load suddenly disappears, the pressure of the self-adjusting back pressure valve rapidly rises and stably exceeds the initial back pressure value. It can be seen from the figure that self-adjusting back pressure in the speed control system when the load disappears, the back pressure of the cylinder rises more than the traditional speed control system, so the oil in the rod cavity of the cylinder absorbs more energy, resulting in the amount of forward momentum of the slide It will be about 20% smaller than traditionalspeed control systems. It can be seen from this that the use of self-adjusting back-gear speed control system as a drive system slider has good characteristics in suppressing the forward punch, in which the self-adjusting back pressure valve plays a very large role.(4) The smoothness of the slideWhen the load acting on the slide changes periodically (such as in the case of milling), the speed of the slide will have to fluctuate. In order to ensure the processing quality requirements, it must reduce its speed fluctuation range as much as possible. From the perspective of the convenience of the discussion of the problem, assume that the load changes according to a sine wave law, and the resulting digital simulation results are shown in Figure 5. From this we can see that this system has the same variation rules and very close numerical values as the conventional speed control system. The reason is that when the change of the load is not large, the pressure in the two chambers of the fuel tank will not have a large change, which will eventually lead to the self-regulating back pressure valve not showing its effect clearly.(5) Improvement measuresThe results of the research show that the dynamic performance of a sliding table with self-regulating back pressure control system as a drive system is better than that of a traditional speed control system. To reduce the amount of kick in the slide, it is necessary to rapidly increase the backpressure of the rod cavity when the load disappears. To increase the smoothness of the sliding table, it is necessary to increase the rigidity of the system. The main measure is to reduce the volume of oil. From the system structure, it is known that the cylinder has a large volume between the rod cavity and the oil discharge pipe, as shown in Fig. 6a. Its existence in terms of delay and attenuation of the self-regulating back pressure valve function, on the other hand, also reduces the rigidity of the system, it will limit the further improvement of the propulsion characteristics and the smoothness of the motion. Thus, improving the dynamic characteristics of the sliding table can be handled by two methods: changing the cylinder volume or changing the size of the self-regulating back pressure valve. Through the simulation calculation of the structural parameters of the system and the comparison of the results, it can be concluded that the ratio of the volume V4 between the rod cavity and the oil discharge pipe to the volume V3 between the rodless cavity and the oil inlet pipe is changed from 5.5 to 5.5. At 1 oclock, as shown in the figure, the diameter of the bottom end of the self-adjusting back pressure valve is increased from the original 10mm to 13mm, and the length of the damper triangle groove is reduced from the original lmm to 0.7mm, which will enable the front of the slide table. The impulse is reduced by 30%, the transition time is obviously shortened, and the smoothness of the slide motion will also be greatly improved.中文译文液压系统W Arnold1. 绪论液压站称液压泵站,是独立的液压装置。
机械设计外文文献翻译、中英文翻译

机械设计外文文献翻译、中英文翻译unavailable。
The first step in the design process is to define the problem and XXX are defined。
the designer can begin toXXX evaluated。
and the best one is XXX。
XXX.Mechanical DesignA XXX machines include engines。
turbines。
vehicles。
hoists。
printing presses。
washing machines。
and XXX and methods of design that apply to XXXXXX。
cams。
valves。
vessels。
and mixers.Design ProcessThe design process begins with a real need。
Existing apparatus may require XXX。
efficiency。
weight。
speed。
or cost。
while new apparatus may be XXX。
To start。
the designer must define the problem and XXX。
ideas and concepts are generated。
evaluated。
and refined until the best one is XXX。
XXX.XXX。
assembly。
XXX.During the preliminary design stage。
it is important to allow design XXX if some ideas may seem impractical。
they can be corrected early on in the design process。
泵外文翻译
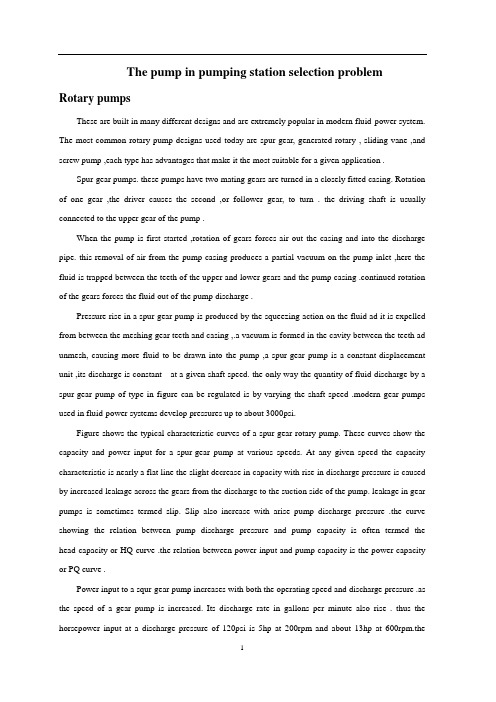
The pump in pumping station selection problem Rotary pumpsThese are built in many different designs and are extremely popular in modern fluid-power system. The most common rotary-pump designs used today are spur-gear, generated-rotary , sliding-vane ,and screw pump ,each type has advantages that make it the most suitable for a given application .Spur-gear pumps. these pumps have two mating gears are turned in a closely fitted casing. Rotation of one gear ,the driver causes the second ,or follower gear, to turn . the driving shaft is usually connected to the upper gear of the pump .When the pump is first started ,rotation of gears forces air out the casing and into the discharge pipe. this removal of air from the pump casing produces a partial vacuum on the pump inlet ,here the fluid is trapped between the teeth of the upper and lower gears and the pump casing .continued rotation of the gears forces the fluid out of the pump discharge .Pressure rise in a spur-gear pump is produced by the squeezing action on the fluid ad it is expelled from between the meshing gear teeth and casing ,.a vacuum is formed in the cavity between the teeth ad unmesh, causing more fluid to be drawn into the pump ,a spur-gear pump is a constant-displacement unit ,its discharge is constant at a given shaft speed. the only way the quantity of fluid discharge by a spur-gear pump of type in figure can be regulated is by varying the shaft speed .modern gear pumps used in fluid-power systems develop pressures up to about 3000psi.Figure shows the typical characteristic curves of a spur-gear rotary pump. These curves show the capacity and power input for a spur-gear pump at various speeds. At any given speed the capacity characteristic is nearly a flat line the slight decrease in capacity with rise in discharge pressure is caused by increased leakage across the gears from the discharge to the suction side of the pump. leakage in gear pumps is sometimes termed slip. Slip also increase with arise pump discharge pressure .the curve showing the relation between pump discharge pressure and pump capacity is often termed the head-capacity or HQ curve .the relation between power input and pump capacity is the power-capacity or PQ curve .Power input to a squr-gear pump increases with both the operating speed and discharge pressure .as the speed of a gear pump is increased. Its discharge rate in gallons per minute also rise . thus the horsepower input at a discharge pressure of 120psi is 5hp at 200rpm and about 13hp at 600rpm.thecorresponding capacities at these speed and pressure are 40 and 95gpm respectively, read on the 120psi ordinate where it crosses the 200-and 600-rpm HQ curves .Figure is based on spur-gear handing a fluid of constant viscosity , as the viscosity of the fluid handle increases (i.e. ,the fluid becomes thicker and has more resistance to flow ),the capacity of a gear pump decreases , thick ,viscous fluids may limit pump capacity t higher speeds because the fluid cannot into the casing rapidly enough fill it completely .figure shows the effect lf increased fluid biscosity on the performance of rotary pump in fluid-power system .at 80-psi discharge pressure the pp has a capacity lf 220gpm when handling fluid of 100SSU viscosity lf 500SSU . the power input to the pump also rises ,as shown by the power characteristics.Capacity lf rotary pump is often expressed in gallons per revolution of the gear or other internal element .if the outlet of a positive-displacement rotary pump is completely closed, the discharge pressure will increase to the point where the pump driving motor stalls or some part of the pump casing or discharge pipe ruptures .because this danger of rupture exists systems are filled with a pressure –relief valve. This relief valve may be built as of the pump or it may be mounted in the discharge piping.Sliding-Vane Pumps,These pumps have a number of vanes which are free to slide into or out of slots in the pup rotor . when the rotor is turned by the pump driver , centrifugal force , springs , or pressurized fluid causes the vanes to move outward in their slots and bear against the inner bore of the pump casing or against a cam ring . as the rotor revolves , fluid flows in between the vanes when they pass the suction port. This fluid is carried around the pump casing until the discharge port is reached. Here the fluid is forced out of the casing and into the discharge pipe.In the sliding-vane pump in Figure the vanes in an oval-shaped bore. Centrifugal force starts the vanes out of their slots when the rotor begins turning. The vanes are held out by pressure which is bled into the cavities behind the vanes from a distributing ring at the end of the vane slots. Suction is through two ports A and AI, placed diametrically opposite each other. Two discharge ports are similarly placed. This arrangement of ports keeps the rotor in hydraulic balance, reliving the bearing of heavy loads. When the rotor turns counterclockwise, fluid from the suction pipe comes into ports A and AI is trapped between the vanes, and is carried around and discharged through ports B and BI. Pumps of this design are built for pressures up to 2500 psi. earlier models required staging to attain pressures approximating those currently available in one stage. Valving , uses to equalize flow and pressure loads as rotor sets areoperated in series to attain high pressures. Speed of rotation is usually limited to less than 2500rpm because of centrifugal forces and subsequent wear at the contact point of vanes against the cam-ring surface..Two vanes may be used in each slot to control the force against the interior of the casing or the cam ring. Dual vanes also provide a tighter seal , reducing the leakage from the discharge side to the suction side of the pump . the opposed inlet and discharge port in this design provide hydraulic balance in the same way as the pump, both these pumps are constant-displacement units.The delivery or capacity of a vane-type pump in gallons per minute cannot be changed without changing the speed of rotation unless a special design is used. Figure shows a variable-capacity sliding-vane pump. It dose not use dual suction and discharge ports. The rotor rums in the pressure-chamber ring, which can be adjusted so that it is off-center to the rotor. As the degree of off-center or eccentricity is changed, a variable volume of fluid is discharged. Figure shows that the vanes create a vacuum so that oil enters through 180 of shaft rotation. Discharge also takes place through 180 of rotation. There is a slight overlapping of the beginning of the fluid intake function and the beginning of the fluid discharge.Figure shows how maximum flow is available at minimum working pressure. As the pressure rises, flow diminishes in a predetermined pattern. As the flow decreases to a minimum valve, the pressure increases to the maximum. The pump delivers only that fluid needed to replace clearance floes resulting from the usual slide fit in circuit components.A relief valve is not essential with a variable-displacement-type pump of this design to protect pumping mechanism. Other conditions within the circuit may dictate the use of a safety or relief valve to prevent localized pressure buildup beyond the usual working levels.For automatic control of the discharge , an adjustable spring-loaded governor is used . this governor is arranged so that the pump discharge acts on a piston or inner surface of the ring whose movement is opposed by the spring . if the pump discharge pressure rises above that for which the by governor spring is set , the spring is compressed. This allows the pressure-chamber ring to move and take a position that is less off center with respect to the rotor. The pump theb delivers less fluid, and the pressure is established at the desired level. The discharge pressure for units of this design varies between 100 and 2500psi.The characteristics of a variable-displacement-pump compensator are shown in figure. Horsepowerinput values also shown so that the power input requirements can be accurately computed. Variable-volume vane pumps are capacity of multiple-pressure levels in a predetermined pattern. Two-pressure pump controls can provide an efficient method of unloading a circuit and still hold sufficient pressure available for pilot circuits.The black area of the graph of figure shows a variable-volume pump maintaining a pressure of 100psi against a closed circuit. Wasted power is the result of pumping oil at 100psi through an unloading or relief valve to maintain a source of positive pilot pressure. Two-pressure –type controls include hydraulic, pilot-operated types and solenoid-controlled, pilot-operated types. The pilot oil obtained from the pump discharge cannot assist the governor spring. Minimum pressure will result. The plus figure shows the solenoid energized so that pilot oil assists compensator spring. The amount of assistance is determined by the small ball and spring, acting as a simple relief valve. This provides the predetermined maximum operating pressure.Another type of two-pressure system employs what is termed a differential unloading governor. It is applied in a high-low or two-pump circuit. The governor automatically, Through pressure sensing, unloads the large volume pump to a minimum deadhead pressure setting. Deadhead pressure refers to a specific pressure level established as resulting action of the variable-displacement-pump control mechanism. The pumping action and the resulting flow at deadhead condition are equal to the leakage in the system and pilot-control flow requirements. No major power movement occurs at this time, even though the hydraulic system may be providing a clamping or holding action while the pump is in deadhead positionThe governor is basically a hydraulically operated, two-pressure control with a differential piston that allows complete unloading when sufficient external pilot pressure is applied to pilot unload port.The minimum deadhead pressure setting is controlled by the main governor spring A. the maximum pressure is controlled by the relief-valve adjustment B. the operating pressure for the governor is generated by the large-volume pump and enters through orifice C.To use this device let us assume that the circuit require a maximum pressure of 1000psi, which will be supplied by a 5-gpm pump. It also needs a large flow (40gpm) at pressure up to 500psi; it continues to 1000pso at the reduced flow rate. A two-pump system with an unloading governor on the 40-gpm pump at 500psi to a minimum pressure setting of 200psi (or another desired value) , which the 5-gpm pump takes the circuit up to1000psi or more.Note in figure that two sources of pilot pressure are required. One ,the 40-gpm pump, provides pressure within the housing so that maximum pressure setting can be obtained. The setting of the spring, plus the pressure within the governor housing, determines the maximum pressure capacity of the 40-gpm pump. The second pilot source is the circuit proper, which will go to 1000psi. this pilot line enters the governor through orifice D and acts on the unloading piston E . the area of piston E is 15 percent greater than the effective area of the relief poppet F. the governor will unload at 500psi and be activated at 15percent below 500psi, or 425psi. By unloading, we mean zero flow output of the 40-gpm pump.As pressure in the circuit increases from zero to 500psi, the pressure within the governor housing also increases until the relief-valve setting is reached, at which time the relief valve cracks open, allowing flow to the tank.The pressure drop in the hosing is a maximum additive value, allowing the pump to deadhead. Meanwhile, the system pressure continues to rise above 700psi, resulting in a greater force on the bottom of piston E than on the top. The piston then completely unseats poppet F, which results in a further pressure drop within the governor horsing to zero pressure because of the full-open position of the relief poppet F. flow entering the housing through orifice is directed to the tank pass the relief poppet without increasing the pressure in housing. The deadhead pressure of the 40-gpm pump then decreases to the lower set value. Thus , at the flow rate to the unloading governor ,the 40gpm pump goes to deadhead. The flow rate to the circuit decreases to 5gpm as the pressure to 1000psi, the 5-gpm pump is also at its deadhead setting, thus only holding system pressure.The 4-gpm pump unloads its volume at 500psi. It requires a system pressure of 600psi to unload the 40-gpm pump to its minimum pressure of 200psi. the 600-psi pilot supply enters through orifice D and acts on the differential piston E. The pumps volume is reduced to zero circuit-flow output at 500psi. The additional 100-psi pilot pressure is required to open poppet F completely and allow the pressure within the housing to decrease to zero.As circuit pressure decreases ,both pumps come back into service in a similar pattern.Axial Piston PumpsIn axial piston pumps of the in-line type, where the cylinders and the drive shaft are parallel ,the reciprocating motion is created by a cam plate, also known as a wobble plate ,tilting plate ,or swash plate .This plate lies in a plane plate that cuts across the center line of the drive shaft and cylinder barrel and does not rotate .In a fixed-displacement pump ,the cam plate will be rigidly mounted in a positionso that it intersects the center line of the cylinder barrel at an angle approximately 25 degrees from perpendicular .Variable-delivery axial piston pumps are designed ,so that the angle that the cam plate makes with a perpendicular to the center line of the cylinder barrel may be varied from zero to 20 or 25 degrees to one or both sides. One end of each piston rod is held in contact with the cam plate as the cylinder block and piston assembly rotates with the drive shaft This causes the pistons to reciprocate within the cylinders .The length of the piston stroke is proportional to the angle that the cam plate is set from perpendicular to the center line of the cylinder barrel .A variation of axial piston pump is the bent-axis type is shown in 1-1 .This type does not have a tilting cam plate as the in-line pump does .Instead ,the cylinder block axial is varied from the drive shaft axis .The ends of the connecting rods are retained in sockets on a disc that turns with the drive shaft .The cylinder block is turned with the drive shaft by a universal joint assembly at the intersection of the drive shaft and the cylinder block shaft ,In order to vary the pump displacement ,the cylinder block shaft and valve plate are mounted in a yoke and the entire assembly is swung in an are around a pair of mounting pintles attacked to the pump housing .Figure 1-1 Bent –axis axial piston pumpThe pumping action of the axial piston pump is made possible by a universal joint or link .Figure1-2is a series of drawings that illustrates how the universal joint is used in the operation of this pump .First ,a rocker arm is installed on a horizontal shaft .(See fig 1-1view A )The arm is joined to the shaft by a pin so that it can be swung back and forth ,as indicated in view B。
毕业设计水利水电工程英文文献翻译

外文文献:hydraulicturbines and hydro—electric powerAbstractPower may be developed from water by three fundamental processes :by action of its weight, of its pressure,or of its velocity,or by a combination of any or all three。
In modern practice the Pelton or impulse wheel is the only type which obtains power by a single process the action of one or more high-velocity jets. This type of wheel is usually found in high—head developments. Faraday had shown that when a coil is rotated in a magnetic field electricity is generated. Thus, in order to produce electrical energy, it is necessary that we should produce mechanical energy,which can be used to rotate the ‘coil’。
The mechanical energy is produced by running a prime mover (known as turbine )by the energy of fuels or flowing water. This mechanical power is converted into electrical power by electric generator which is directly coupled to the shaft of turbine and is thus run by turbine. The electrical power, which is consequently obtained at the terminals of the generator,is then transited to the area where it is to be used for doing work.he plant or machinery which is required to produce electricity (i.e。
机械 外文翻译 外文文献 英文文献 液压机械及泵
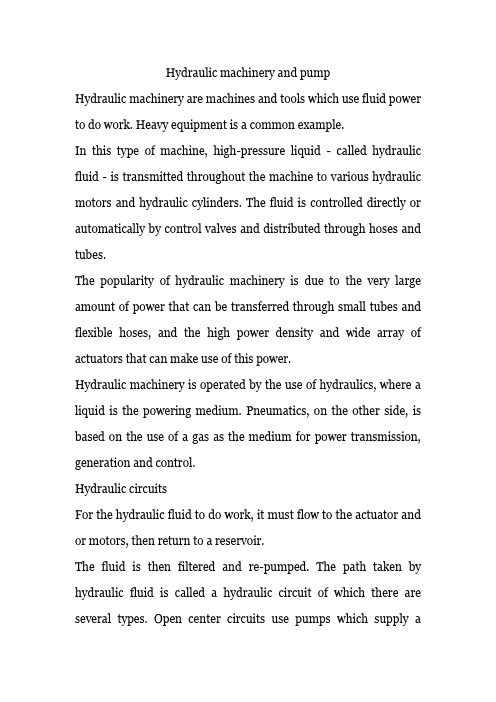
Hydraulic machinery and pumpHydraulic machinery are machines and tools which use fluid power to do work. Heavy equipment is a common example.In this type of machine, high-pressure liquid - called hydraulic fluid - is transmitted throughout the machine to various hydraulic motors and hydraulic cylinders. The fluid is controlled directly or automatically by control valves and distributed through hoses and tubes.The popularity of hydraulic machinery is due to the very large amount of power that can be transferred through small tubes and flexible hoses, and the high power density and wide array of actuators that can make use of this power.Hydraulic machinery is operated by the use of hydraulics, where a liquid is the powering medium. Pneumatics, on the other side, is based on the use of a gas as the medium for power transmission, generation and control.Hydraulic circuitsFor the hydraulic fluid to do work, it must flow to the actuator and or motors, then return to a reservoir.The fluid is then filtered and re-pumped. The path taken by hydraulic fluid is called a hydraulic circuit of which there are several types. Open center circuits use pumps which supply acontinuous flow. The flow is returned to tank through the control valve's open center; that is, when the control valve is centered, it provides an open return path to tank and the fluid is not pumped to a high pressure. Otherwise, if the control valve is actuated it routes fluid to and from an actuator and tank. The fluid's pressure will rise to meet any resistance, since the pump has a constant output. If the pressure rises too high, fluid returns to tank through a pressure relief valve.Hydraulic pumps supply fluid to the components in the system. Pressure in the system develops in reaction to the load. Hence, a pump rated for 5,000 psi is capable of maintaining flow against a load of 5,000 psi.Pumps have a power density about ten times greater than an electric motor (by volume). They are powered by an electric motor or an engine, connected through gears, belts, or a flexible elastomeric coupling to reduce vibration.Common types of hydraulic pumps to hydraulic machinery applications are;Gear pump: cheap, durable, simple. Less efficient, because they are constant displacement, and mainly suitable for pressures below 20 MPa (3000 psi).Vane pump: cheap and simple, reliable (especially in g-rotor form). Good for higher-flow low-pressure output.Axial piston pump: many designed with a variable displacement mechanism, to vary output flow for automatic control of pressure. There are various axial piston pump designs, including swashplate and checkball. The most common is the swashplate pump.Radial piston pump: A pump that is normally used for very high pressure at small flows.Piston pumps are more expensive than gear or vane pumps, but provide longer life operating at higher pressure, with difficult fluids and longer continuous duty cycles. Piston pumps make up one half of a hydrostatic transmission.Control valvesDirectional control valves route the fluid to the desired actuator. They usually consist of a spool inside a cast iron or steel housing. Directional control valves are usually designed to be stackable, with one valve for each hydraulic cylinder, and one fluid input supplying all the valves in the stack.The spool position may be actuated by mechanical levers, hydraulic pilot pressure, or solenoids which push the spool left or right.The main valve block is usually a stack of off the shelf directional control valves chosen by flow capacity and performance. Some valves are designed to be proportional (flow rate proportional to valve position), while others may be simply on-off. The controlvalve is one of the most expensive and sensitive parts of a hydraulic circuit.Pressure relief valves are used in several places in hydraulic machinery; on the return circuit to maintain a small amount of pressure for brakes, pilot lines, etc... On hydraulic cylinders, to prevent overloading and hydraulic line rupture. On the hydraulic reservoir, to maintain a small positive pressure which excludes moisture and contamination.Pressure reducing valves reduce the supply pressure as needed for various circuits.Check valves are one-way valves, allowing an accumulator to charge and maintain its pressure after the machine is turned off, for example.Counterbalance valves are in fact a special type of pilot controlled check valve. Whereas the check valve is open or closed, the counterbalance valve acts a bit like a pilot controlled flow control. Hydraulic pump typesGear pumpsGear pumps (with external teeth) (fixed displacement) are simple and economical pumps. The swept volume or displacement of gearpumps for hydraulics will be between about 1 cm3 (0.001 litre) and 200 cm3(0.2 litre). These pumps create pressure through the meshing of the gear teeth, which forces fluid around the gears to pressurize the outlet side. Some gear pumps can be quite noisy, compared to other types, but modern gear pumps are highly reliable and much quieter than older models.Rotary vane pumpsRotary vane pumps(fixed and simple adjustable displacement) have higher efficiencies than gear pumps, but are also used for mid pressures up to 180 bars in general. Some types of vane pumps can change the centre of the vane body, so that a simple adjustable pump is obtained. These adjustable vane pumps are in general constant pressure or constant power pumps: the displacement is increased until the required pressure or power is reached and subsequently the displacement or swept volume is decreased until an equilibrium is reached.Screw pumpsScrew pumps (fixed displacement) are a double Archimedes' screw, but closed. This means that two screws are used in one body. The pumps are used for high flows and relatively low pressure (max 100 bar). They were used on board ships where the constant pressure hydraulic system was going through the whole ship,especially for the control of ball valves, but also for the steering gear and help drive systems. The advantage of the screw pumps is the low sound level of these pumps; the efficiency is not that high. Bent axis pumpsBent axis pumps, axial piston pumps and motors using the bent axis principle, fixed or adjustable displacement, exists in two different basic designs. The Thoma-principle (engineer Hans Thoma, Germany, patent 1935) with max 25 degrees angle and the Wahlmark-principle (Gunnar Axel Wahlmark, patent 1960) with spherical-shaped pistons in one piece with the piston rod, piston rings, and maximum 40 degrees between the driveshaft centerline and pistons (Volvo Hydraulics Co.). These have the best efficiency of all pumps. Although in general the largest displacements are approximately one litre per revolution, if necessary a two-liter swept volume pump can be built. Often variable-displacement pumps are used, so that the oil flow can be adjusted carefully. These pumps can in general work with a working pressure of up to 350–420 bars in continuous work.Axial piston pumps swashplate principleAxial piston pumps using the swashplate principle (fixed and adjustable displacement) have a quality that is almost the same as the bent axis model. They have the advantage of being morecompact in design. The pumps are easier and more economical to manufacture; the disadvantage is that they are more sensitive to oil contamination.Radial piston pumpsRadial piston pumps(fixed displacement) are used especially for high pressure and relatively small flows. Pressures of up to 650 bar are normal. In fact variable displacement is not possible, but sometimes the pump is designed in such a way that the plungers can be switched off one by one, so that a sort of variable displacement pump is obtained.Peristaltic pumpsPeristaltic pumps are not generally used for high pressures. Pumps for open and closed systemsMost pumps are working in open systems. The pump draws oil from a reservoir at atmospheric pressure. It is very important that there is no cavitation at the suction side of the pump. For this reason the connection of the suction side of the pump is larger in diameter than the connection of the pressure side. In case of the use of multi-pump assemblies, the suction connection of the pump is often combined. It is preferred to have free flow to the pump (pressure at inlet of pump at least 0.8 bars). The body of the pump is often in open connection with the suction side of the pump.In case of a closed system, both sides of the pump can be at high pressure. The reservoir is often pressurized with 6-20 bars boost pressure. For closed loop systems, normally axial piston pumps are used. Because both sides are pressurized, the body of the pump needs a separate leakage connection.Multi pump assemblyIn a hydraulic installation, one pump can serve more cylinders and motors. The problem however is that in that case a constant pressure system is required and the system always needs the full power. It is more economic to give each cylinder and motor its own pump. In that case multi pump assemblies can be used. Gearpumps can often be obtained as multi pumps. The different chambers (sometimes of different size) are mounted in one body or built together. Also vane pumps can often be obtained as a multi pump. Gerotor pumps are often supplied as multi pumps. Screw pumps can be built together with a gear pump or a vane pump. Axial piston swashplate pumps can be built together with a second pump of the same or smaller size, or can be built together with one or more gear pumps or vane pumps (depending on the supplier). Axial plunger pumps of the bent axis design can not be built together with other pumps.翻译液压机械及泵液压机械是机械和工具,它使用流体的力量去做的工作。
研究的可靠性,滑动轴承支撑斜盘式轴向柱塞泵型水液压外文翻译、外文文献翻译、中英文翻译
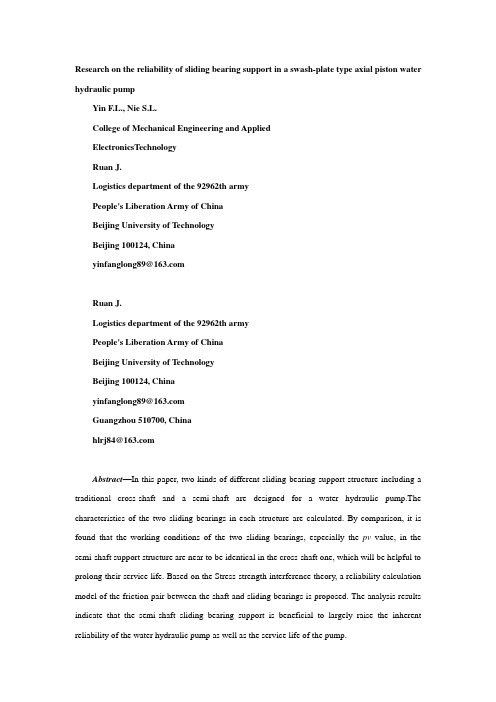
Research on the reliability of sliding bearing support in a swash-plate type axial piston water hydraulic pumpYin F.L., Nie S.L.College of Mechanical Engineering and AppliedElectronicsTechnologyRuan J.Logistics department of the 92962th armyPeople's Liberation Army of ChinaBeijing University of TechnologyBeijing 100124, Chinayinfanglong89@Ruan J.Logistics department of the 92962th armyPeople's Liberation Army of ChinaBeijing University of TechnologyBeijing 100124, Chinayinfanglong89@Guangzhou 510700, Chinahlrj84@Abstract—In this paper, two kinds of different sliding bearing support structure including a traditional cross-shaft and a semi-shaft are designed for a water hydraulic pump.The characteristics of the two sliding bearings in each structure are calculated. By comparison, it is found that the working conditions of the two sliding bearings, especially the pv value, in the semi-shaft support structure are near to be identical in the cross-shaft one, which will be helpful to prolong their service life. Based on the Stress-strength interference theory, a reliability calculation model of the friction pair between the shaft and sliding bearings is proposed. The analysis results indicate that the semi-shaft sliding bearing support is beneficial to largely raise the inherent reliability of the water hydraulic pump as well as the service life of the pump.Keywords—water hydraulic pump; sliding bearing; pv value;ReliabilityⅠ.IntroductionWater hydraulic system is operated with raw water(pure tap water) substituting for mineral oil. Such systems are becoming more and more popular, especially in the fields of steel and glass production, nuclear power generation, coal and gold mining, food and medicine processing, ocean exploration, and underwater pared with conventional mineral oil, raw water that acts as hydraulic fluid has several inherent advantages,including low operating cost, sound environmental compatibility, non-flammability, and low pollution potential to products [1-2].Water hydraulic axial piston pump (WHAP) is one of key power components in water hydraulic systems. There are several challenging issues associated with the pump,such as conflicts between lubrication and wear, and between sealing and leakage. Especially, shaft and bearings form key friction pairs, which will result in significant influences on the pump’s performance.Generally, the hydrodynamic sliding bearing is extensively used for supporting the water hydraulic pump’s shaft. Therefore, in order to improve the pump’s efficiency and reliability, it is crucial to study the force distribution of sliding bearings thoroughly. According to hydrodynamic lubrication theory, the critical points,which satisfies the wear resistance for sliding bearing and shaft of WHAP includes: (1) An optimal load distributed strategy should be used to determine optimal dimensions for achieving the even distributing of the load. (2) Several suitable materials should be selected to meet the water lubrication working conditions and to ensure a long life with lower friction losses [3].The concepts of both stress and strength relating to reliability design are generalized. In this paper, thereliability of sliding bearing support will be investigated using Stress-strength interference model to calculate the reliability value of the sliding bearings, which will include the effect of the flow fluctuation in WHAP.II. Description of sliding bearing supportFigure (a) shows a schematic of a typical cross-shaft supporting structure. The cylinder block is supported on the shaft. Two sliding bearings are located on the cylinder’s left and right ends to support the shaft. Figure (b) shows a schematic of a novel design, where a semi-shaft supportingstructure is employed. The front sliding bearing is used to support the input shaft (spline shaft). And the rear sliding bearing inside the cylinder is used to support the cylinder block. In the semi-shaft support structure, the spline shaft and cylinder are interference fit, and they are combined by a spline.During pump running, the motor drives input shaft rotating, bringing along the rotation of the cylinder.Because of the presence of the angle of swash plate, the whirling motion of the cylinder is translated into straight reciprocating motion of the pistons. When the cylinder rotated a period, the pistons reciprocate a round-trip to complete a process of suction and discharge of the pump.(a)cross-shaft support(b) semi-shaft supportFig. 1 Schematic diagram of sliding bearing supportIII. Theoretical analysesA. Load characteristics of the bearings.As shown in Figure 1, the reaction component force that act on a single slipper along X-axis and Z-axis can be respectively described as follows:In terms of the axial piston pump, the hydraulic pressure in each piston hole can be represented as:Then the radial resultant force is located in point O (as shown in Figure 1), and the radial resultant force can be expressed as:Furthermore, with the radial force equilibrium along the X-axis of the supporting structure, we have:The torque equilibrium along the X-axis can be written as:Through solving Eqs. (4) –(6), the supporting force of the front and rear bearings can be obtained, respectively:B. PV value of the bearingsFor the valve plate distribution of axial piston pump,the number of pistons within the discharge pressure area (Zg) during one operating period is variably along with the reciprocatingmotion of the pistons. Ignoring the influence of the pressure pulsation in the pre-loading and pre-unloading areas, and the cylinder weight, affected by the alternative vibration of the number of piston in the discharge pressure area, the sliding bearing is subjected to periodic unstable loads. Water is characterized by very low dynamical viscosity, which is regarded as poor lubricating properties affecting the performance of sliding and rolling contacts [4]. Here it appears that it is impossible to obtain an acceptable film thickness in water lubricated sliding bearings. Consequently, in practical work, the sliding bearings in WHAP are usually working under the condition of an incomplete liquid lubrication. Especially, at the points of turn on / off, the direct contacts between the matching pairs of the shaft and sliding bearings may take place. Moreover, since it is necessary for the sliding bearings the surface hardness should be as high as possible in order to sustain contacting pressure, and thus, the abrasion between the shaft and bearings would be as low as possible in order to improve the sliding bearings’ reliability.It is essential to select several suitable materials and matching pair. The siding bearings in this paper are made of WR525, which is a thermoplastic composite consisting of carbon fiber in a PEEK matrix. Due to its unique thermal expansion properties, WR525 is ideal for use as impeller wear rings, bushings and case wear rings.WR525 allows the pump user to increase pump efficiency by running tighter wear ring clearances, while decreasing potential pump damage when pumps are cavitated or experience down-line bearing failures. WR525 bearings are specified as standard material on all HGM/HGM-RO boiler feed pumps.As it is known, the critical pv value is a very important parameter for polymers or their composites in tribological applications, and has been widely used in investigation of ploymers’ sliding wear behaviors. Besides, pv limits are affected by variations in temperature, speed,loading,lubrication and surface finish. Exceeding pv limits will result in accelerated wear and premature bearing failure, where p is the intensity of pressure applied to a bearing surface and v is the relative velocity [5]. Furthermore, the pv value is proportional to bearing’s wear, friction power loss and friction heat [6]. Wear, friction power loss and temperature conditions are the three key index of the service life of the bearings. Therefore, the pv value can be used to preliminarily evaluate the sliding bearings’working life in a WHAP. Generally speaking, in order to guarantee the boundary lubricated bearing running reliably, it is necessary to meet the following three conditions [7]:Bearing’s average working specific pressure is:Substituting Eqs. (7) and (8) into Eq. (10), average working specific pressure of the front bearing can be obtained as:And average working specific pressure of the rear bearing can be represented as:Radial circumferential velocity of the shaft is:The friction specific work rate of sliding bearing can be expressed asSubstituting Eqs. (11) – (13) into Eq. (14), the friction specific work rate of the front bearing can be obtained as follows:And the friction specific work rate of the rear bearing is calculated as follows:Based on the structure parameters of the WHAP, taking the peak number of pistons in the discharge pressure area (Zg), the working conditions of the bearings under the two different structures are calculated in Table1.C. Scale factorActually, analyzing Eqs. (10), (11), (14) and (15), it is found that the dz, Band influence the match of the two bearings’ working conditions. Define the bearing s’linear velocity ratio as a verage specific work rate ratio as Then we have:The three parameters mentioned above can be calculated (as shown in Table 2).D. Reliability model and evaluationIn terms of a WHAP, design of the sliding bearing is an important part for raising its reliability. In this paper, the pv value is defined as the stress between the sliding bearing friction pair-Y, and it is a random variable. The allowable pv value [pv] can be defined as the strength-X.Generally speaking, the contact stress p between the friction pair and the relative linear velocity v are mutually independent random variables, and they are all distributed normally, so the product pv is also distributed normally.Thus, according to the formula when the stress and strengthare all distributed normally, the reliability coefficient can be determined by means of the equation:In fact, the pv or allowable pv value can be expressed by the two random variables Pd and :K is constant coefficient. Pd is the working pressure of the pump and ω is the relative angular velocity. Based on probability theory, the average value and the standard deviation can be obtained, respectively:Through solving Eqs. (22) and (23), we have:The rated pressure of the WHAP can be allowed for fluctuating within ±5%. According to the definition of mean value and the principle of3σ , we have:The allowable pv value [pv] of WR 525 is 8.89MPa m/s, and its standard deviation [ pv] s is 0.315.Substituting Eqs. (24) –(28) and their corresponding data into Eq. (20), the reliability coefficient R u of the two kinds of structure can be calculated respectively. Hence, the corresponding reliability R for each structure can be obtained, as listed in Table 3.IV. DiscussionIn terms of the WHAP, the failure of any sliding bearing could destroy the pump’s supporting and balance to cause severe noise and vibration. It also could lead to the invalidation of the flow distribution and make the volumetric efficiency decrease sharply. Thus, service life of WHAP is determined by the bearing which has the severe working condition.Table 1 presents the calculated results of the key parameters in two different sliding bearings distribution structure. It indicates that the working conditions of the sliding bearings in each distribution structure are different.Firstly, the center distance L2 in the semi-shaft structure is smaller than the cross-shaft one. This means that the rear bearing in the semi-shaft structure is closer to the center point of the resultant force, and the distance between the front and bearing is also smaller. Thus it is favorable to balance the torque of F1 and F2 so that making the sliding bearings work smoothly. Secondly, the loads on the sliding bearings in each structure are different.In the cross-shaft structure, the loads on the front bearing are much larger than on the rear one. However, in the semi-shaft structure, the loads on the front bearing reduced, while the loads on the rear bearing increased, so as to make the bearings’ supported load condition in the front and rear location closely and their loads distributed evenly. Additionally, th e front bearing’s average working specific pressure (pz) and its pv value in the cross-shaft structure, are much larger than the rear one. However, in the semi-shaft structure, the front bearing’s pz and pv value reduced slightly, for which the rear bearing increases a little. Comparing the results listed in Table 2, it can be seen that the value of the semi-shaft structure are smaller than which are in the cross-shaft structure. Moreover, these values are close to 1. It is revealed that in the semi-shaft structure, the working conditions of the two sliding bearings are near to be identical.From Table 3, the reliability value of the siding bearings support in the semi-shaft structure are higher. It is indicated that the sliding bearings of the semi-shaft have longer service life than those in the cross-shaft.Consequently, it can be concluded that the distribution of sliding bearings in the semi-shaft structure is beneficial to make the bearings’ working conditions equilibrium and to improve the reliability of the pump.V. ConclusionIn this research, two sliding bearings of the WHAP which have the same size work in the same water medium in same time. So the change law of loads on the bearings similar. Besides, they are made of the same material:WR525. Hence, the life of the two sliding bearing support structure depends on the bearing which has higher working conditions especially the pv value. So it is important to design a rational structure arrangement to make the two bearings’ working conditions as equal a s possible. Consequently, for the sake of raising the sliding bearing’s life in the WHAP, the scalefactors must be close to 1. Additionally, the degree of reliability is a main indicator for the reliability of the sliding bearing support structure. So the reliability value of the sliding bearing support structure should be as large as possible for improving the WHAP’s reliability.By comparing the working conditions of the sliding bearings in each structure, it is found thatthe pv value of the two sliding bearings in the semi-shaft structure are closer than in thecross-shaft one. And the scale factor of the semi-shaft structure are closer to 1, compared to the cross-shaft one. Additionally, the reliability value of the sliding bearings in the semi-shaft structure is higher than which in the cross-shaft one.Obviously, all the comparisons mentioned above show that the arrangement of sliding bearings in the semi-shaft structure does a better job in achieve the purpose of distributing the load averagely and raising the service life of the sliding bearings in the water hydraulic piston pump as well as improving the reliability of WHAP.ACKNOWLEDGMENTThis research was funded by Natural Science Foundations of China (№s 50675074 and 51075007), NCET of State Education Ministry (№ NCET-07-0330), and PHR (IHLB) 20090203.REFERENCESNomenclatureThe author;Yin F.L. Nie S.L. Ruan J.Nationality:ChinaSource:The 2011 International Conference on Fluid Power and Mechatronics, Beijing, August 16-17, 2011, 282-286.研究的可靠性,滑动轴承支撑斜盘式轴向柱塞泵型水液压Yin F.L., Nie S.L.大学的机械工程和应用ElectronicsTechnologyRuan J.中国北京北京科技大学中国人民解放军物流部门的92962部队 100124 Yinfanglong89@中国广州 hlrj84@ 510700文摘-在本文中,两种不同的滑动轴承支撑结构包括一个传统的十字轴和半轴,被设计为--水液压泵。
- 1、下载文档前请自行甄别文档内容的完整性,平台不提供额外的编辑、内容补充、找答案等附加服务。
- 2、"仅部分预览"的文档,不可在线预览部分如存在完整性等问题,可反馈申请退款(可完整预览的文档不适用该条件!)。
- 3、如文档侵犯您的权益,请联系客服反馈,我们会尽快为您处理(人工客服工作时间:9:00-18:30)。
利用神经网络预测轴向柱塞泵的性能Mansour A Karkoub a, Osama E Gad a, Mahmoud G Rabie ba--就读于科威特的科威特大学工程与石油学院b--就读于埃及开罗的军事科技大学摘要本文推导了应用于轴向柱塞泵(斜轴式)的神经网络模型。
该模型采用的数据是由一个实验装置获得的。
这个正在进行的研究的目的是降低柱塞泵在高压下工作时的能量损耗。
然而,在最初我们要做一些研究来预测当前所设计的泵的响应。
神经网络模型具有前反馈的结构,并在测验过程中使用Levenberg-Marquardt优化技术。
该模型能够准确地预测柱塞泵的动态响应。
1、简介可变排量轴向柱塞泵是在流体动力系统中经常要用到的重要设备,如液压动力供应控制和静液压传动驱动器的控制。
本装置具有变量机制和功率-重量比特性,使其最适合于高功率电平的控制。
所设计的这种轴向柱塞泵拥有可靠性和简便的特点,然而其最重要的特征是可以变量输出。
人们在轴向柱塞泵领域已经做了很多研究,但是本文将只论述一下少数几人所做的贡献。
Kaliafetis和Costopoulos[5]用调压器研究了轴向柱塞变量泵的静态和动态特性。
所提出的模型的精确度依赖于制造商提供的动态运行曲线等数据。
他们得出结论,运行条件对泵的动态行为是非常关键的,而泵的动态行为可以通过减小压力设定值进行改善。
Harris等人[4]模拟和测量了轴向柱塞泵的缸体压力和进油流量脉动。
Kiyoshi和Masakasu[7]研究了斜盘式变量输送的轴向柱塞泵在运行时刻的实验上和理论上的静态和动态特性。
并提出了一种新的方法来预测泵在运行过程中的响应。
也对研究泵特性的新方法的有效性进行了实验验证,实验中使用了一个有宽、短而深的凹槽的配流盘。
Edge和Darling[2]研究了液压轴向柱塞泵的缸体压力和流量。
这个得出的模型经过了实验检验。
对于配流盘、缸体上设计的退刀槽和泵的流量脉动对泵特性的影响都进行了验证。
人们已证实了一种可替代的建模技术——神经网络(NN)能取得良好的效果,特别是对于高度非线性的系统。
这种技术是模仿人脑获取信息的功能。
Karkoub 和Elkamel[6]用神经网络模型预测了一个长方形的气压轴承的压力分布。
所设计的这种模型在预测压力分布和承载能力方面比其他可用的工具更加精确。
Gharbi 等人[3]利用神经网络预测了突破采油。
其表现远远优于常见的回归模型或有限差分法。
李等人[8]用神经网络模型NNS和鲍威尔优化技术对单链路和双链路的倒立摆进行了建模和控制。
研究者们取得了理想的结果。
Panda等人[9]应用NNS在普拉德霍湾油田对流体接触进行了建模。
所得到的模型预测的目标油井中的流量分配比传统的以回归为基础的技术更准确。
Aoyama等人[1]已经推导出一个神经网络模型来预测非最小相系统的响应。
所开发出的的模型被应用于Van de Vuss反应器和连续搅拌式生物反应器,所得到的结果是令人满意的。
本文研究利用神经网络解决轴向柱塞泵(斜轴式)在一定的供油压力下的建模。
本文首先会描述用于收集实验数据的实验装置,然后将会简要介绍神经网络建模程序。
2、实验装置实验数据是从这个将在本节中进行讨论的实验装置上得到的。
该装置的主要组成部分是轴向柱塞泵。
在下面的章节中,我们将描述泵的工作原理,然后描述如何收集实验数据。
2.1、斜轴式轴向柱塞泵示意图2显示出了在实验中使用的轴向柱塞泵的基本组件,而此泵的控制单元如图3所示。
该泵由两个主要部分组成。
第一部分是旋转组,其中包括驱动轴(31)、柱塞(32)、缸体(33)和配流盘(34)。
七个柱塞安装在一个位于前表面的球形组件上,并且他们同时动作使缸体旋转。
缸体通过弹簧(35)推压控制区域的配流盘。
在运行过程中,带有柱塞的配流盘和缸体可以在一个球形的滑动表面(36)上移动。
配流盘采用了在进油口和出油口的前缘和后缘都带有半圆形凹槽的双向配流盘。
第二部分是泵的控制部分,其中包含了控制柱塞(37)、控制元件(38、39和40)、调节弹簧(41)和控制弹簧(42)和(43)。
两个主要部分是用调节销(44)连接在一起的。
体积为V的泵出口腔与体积为V1和V2的控制腔通过孔(45)和(46)分别连通。
控制柱塞连通开口孔(47)、该开口孔的大小是由活塞(40)(参照图2和图3)控制的。
当操作压力P超过了弹簧(41)的预设值,控制元件(38、39和40)就会推压弹簧。
与此同时,液压油通过节流孔(45)和(46)从泵的出口流出。
在体积为V1的腔体内的高压油就从开口孔(47)流到了控制柱塞(37)的大端面上。
如果作用在控制柱塞上的压力大于弹簧力,控制柱塞(37)就会移动,直到液压力和机械力恢复平衡。
缸体、柱塞和配流盘在球形滑动表面(36)以相反的方向移动,以减少旋转角度αmax<α<αmax。
此运动会导致泵的流速降低。
2.2、数据测量装置利用神经网络设计的模型必须要使用从上述系统获得的一些实际数据进行检验。
检验的过程对于神经网络了解它试图预测的模型是必要的。
数据是从图1所示的实验装置中收集的。
此数据是通过测量图2所示的轴向柱塞泵的稳态和瞬态响应获得的。
图1 实验装置的照片图 2 斜轴式轴向柱塞泵的示意图图3 柱塞泵的控制单元的示意图实验研究是在如图1所示的测试平台上进行的,液压回路图如图4所示。
试验泵的进油管和出油管分别与吸油管和高流量计的端口(24)和(25)直接连接在一起。
试验泵(16)是由一个高功率的可控速度的液压马达(13)驱动的。
液压回路的工作过程如下:油从油箱(1)流入增压泵(4)的进油口。
减压阀(7)是用来保护增压泵回路以避免其压力过高。
增压泵溢出的液压油通过一个单向阀(6)流入主泵(3)的吸油和供油线路。
减压阀(8)是用于保护主泵回路防止压力过高。
从主泵流出的液压油通过用于控制主泵流向的方向控制阀(9)和(10)流入主驱动马达回路(12)。
试验泵的流速由数字式的流量计(20)显示。
试验泵的从动轴的转速是由转速计(15)测量的,可以通过改变电动机(5)的速度来控制从动轴的速度。
在操作过程中工作油的温度要保持在50±5℃的范围内。
图4 液压系统示意图在稳态测量期间,当开关阀(30)完全关闭时供给压力P的变化是由控制阀(29)调节的。
压力计(23)用来测量进油管路中的油压,数字压力计(21)测量出油线路中的油压。
减压阀(28)是用来保护试验泵回路以防过载。
而在瞬态测量期间,阀(30)是完全打开的而阀(29)是完全关闭的。
2.3、泵的稳态响应的测量所研究的泵的稳态性能的实验测定是通过测量不同的供给压力P下的泵的排出流量Qp来进行的。
试验泵的参数如表1所示。
供给压力P是由节流阀(29)控制的,其压力值由数字压力计(21)测得。
相应的泵排量Qp是由数字流量计(20)测量的。
测量时预设压力相同而泵的转速不同,泵的转速分别为550、800和1000 rpm。
泵的排量Qp也是在不同的预设压力值下测量的。
测量值如图7和图8所示。
表1 泵的参数参数描述数值A控制柱塞的大端面0.000531 m2cA柱塞面积0.000531 m2pA控制元件(38)的面积0.0000246 m2ppA控制柱塞的小端面面积0.0000785 m2sV泵输油管道体积 2.6×10−3 m3V第一控制腔的体积8.2×10−6 m31V第二控制腔的体积 1.7×10−7 m32V第三控制腔的体积 1.6×10−5 m33α缸体最小倾斜角4°minα缸体最大倾斜角23°max2.4 泵的瞬态响应的测量图2所示的待研究的泵的瞬态响应的实验测定是通过测量不同控制腔的工作压力来进行的。
在泵体的不同位置安装着三个电控压力传感器,该泵体是和体积分别为V1、V2和V3的控制腔直接连接在一起的,如图3所示。
另一个压力传感器被安装在泵出口体积V的管路上来测量供给压力P。
这些传感器都是压阻式的,可以测量的压力范围为0.1到400bar之间。
每个传感的输入电压为10〜30V,而输出电压是在0到5V之间。
这些传感器是用来测量控制压力P1、P2、P3和P (参照图3)的。
压力信号的时域图谱是使用PC机和数据采集板采集的。
转换时间为12μs的12位逐次逼近转换器的数据采集板能实现70 kHz的最大吞吐率。
泵的出口管路上安装有节流口大小固定的节流阀(18)和方向控制阀DCV(17)(参照图1和图4)。
这些阀可以使泵的出口管路的压力P快速变化。
当DCV的电磁阀通电时,阀门迅速关闭,泵的排出流量Qp就被迫流经节流阀。
这样设置试验台就能使电磁阀中的电流能触发数据采集系统,从而拾取瞬间变化的压力P1、P2、P3和P的值。
这些数据的测量是在泵的转速为550、800和1000 rpm的情况下进行。
测量结果如图9、图10和图11所示。
3、神经网络在本文中,用于预测斜轴式轴向柱塞泵的动作的装置是一个被称为神经网络的计算工具。
这些网络都只是一些相互联接在一起的被称为神经元的元素。
这些神经元或处理单元是精心挑选的线性或非线性函数,这些函数可以处理任何应用输入以得到其输出。
神经元的输入是外部输入的加权总和,或是紧挨着它的上一个神经元的输出。
一个小的加权施加到神经元的输出上就会使接下来的神经元不能处理其输入。
人们就能以这种方式建立每个模式或输入的具体路线图。
这种类型的模型就能使神经网络能够捕捉通常未能被普通建模技术发现的非线性信号。
一个特定的神经元的输出是关于三个主要因子:加权输入、该神经元的偏压和传递函数(参见图5)的函数。
任何神经元的输出都可按下式计算:a=f(x+β)其中传递函数f可以选自一组现成可用的函数。
在我们的研究中所选用的是S型函数:该函数以能得到理想的结果而著名,特别是对于给定的输入其输出是已知的情况。
图5 单个神经元的示意图任何网络通常都可划分为各个子网或我们通常所称呼的层。
每个网络包含两个基本层即输入层和输出层,而且如果任务需要就会有一个或多个隐藏层。
图6显示出了一种典型的前馈式结构的神经网络。
输出层的输出是网络中所有神经元的组合效果的结果。
图6 多层、前馈式神经网络的示意图3.1、测验设计一个神经网络至少需要四个主要步骤:(1)确定网络层的层数:(2)确定神经元数量:(3)确定传递函数的类型:(4)确定一个能描述系统行为实验数据组。
测验过程非常耗费时间但对于网络的成功非常关键。
测验中要应用几项技术,其中有一项是势能的反向传播。
每一个神经元的每一个输入的权重都是从输出层和工作反馈开始连续变化更新的。
在此过程中,要使目标函数最小化,而目标函数通常是误差的平方和函数。
文献中应用到了几项优化技术,包括鲍威尔算法和Levenberg-Marquardt算法。