超声振动磨削机构的建模与仿真
超声振动辅助磨削-脉冲放电复合加工磨削力模型研究
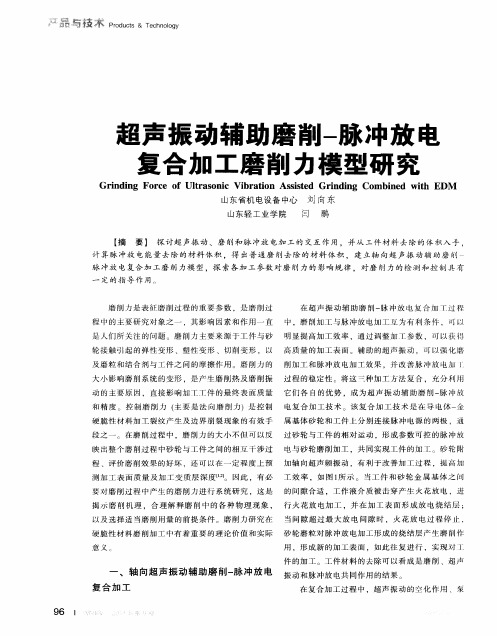
所 测 加 工 表 面 质 量 及 加 工 变 质 层 深 度 _. 因 此 ,有 必 工 效 率 , 如 图 1 示 。 当 工 件 和 砂 轮 金 属 基 体 之 间 1。 2 1 要 对磨 削 过 程 中产 生 的磨 削 力 进 行 系统 研 究 ,这 是 的 间 隙 合适 ,工作 液 介 质被 击 穿 产 生 火 花 放 电 ,进 揭示 磨 削 机 理 ,合 理 解 释 磨 削 中 的 各 种 物 理 现 象 , 行 火 花 放 电加 工 ,并 在 加 工 表 面 形 成 放 电 烧 结 层 ; 以及 选 择 适 当 磨 削 用 量 的前 提 条 件 。磨 削 力 研 究 在 当 间 隙 超 过 最 大 放 电 间 隙 时 ,火 花 放 电过 程 停 止 , 硬 脆 性 材料 磨 削 加 工 中有 着 重 要 的 理 论 价 值 和 实 际 砂 轮磨 粒对 脉 冲 放 电 加 工形 成 的 烧 结 层 产 生 磨 削 作
论 ,单位 时间内放 电痕熔化体积为 :
W
V=
K
c ( T P , C ( +q p o q p 一 )+ p,
式 中 , 为单 位 时 间 内 ,工 件 吸 收 的 电火 花 放
电 能 量 ;C为 热 容 量 ;P 密 度 ; 为 熔 点 ; 为 原 为
压 、放 电 电 流 和放 电 持 续 时 间 。 一 个 加 工 周 期 内 ,
等 ,在 建 立磨 削力 数学模 型 时 ,把 磨 削力分 成 切 屑 变 形 力 和 摩 擦 力 两 项 。磨 削力 可 写 成 如 下 形
式:
= +
电火 花 加 工 放 电总 能 量 为 :
Q∑ “ ) d = oi t )
液 等 密 切 相 关 ,通 过 大 量 的 试 验 总 结 获 得 。 在 电火 花 加 工 中 , 电极 与 工 件 材 料 的物 理 特
超声磨削装置结构设计

超声磨削装置结构设计1.振动源:超声磨削装置的核心是振动源,它产生高频的超声波振动。
振动源通常由发生器、转换器和振动工具组成。
发生器产生高频电能,通过转换器将电能转换成机械振动,然后通过振动工具传递到被加工的材料上。
2.振动工具:振动工具是超声磨削装置中的重要部件,它负责将振动源产生的超声波振动传递到被加工材料上。
振动工具通常采用金属材料制成,具有特定的形状和表面特征,例如凸轮形、圆柱形等。
振动工具的结构设计需要考虑振动传递的效率和加工性能。
3.加工台:加工台是超声磨削装置上用于支撑和夹持被加工材料的平台。
加工台通常由金属材料制成,具有坚固的结构和稳定的工作平面。
加工台的结构设计应考虑材料夹持的可靠性和加工精度的要求。
4.控制系统:超声磨削装置需要一个控制系统来控制振动源的工作参数,例如振动频率、振幅和工作时间等。
控制系统通常包括电子控制器和人机界面。
电子控制器负责控制振动源的工作状态,人机界面提供操作界面和参数设置功能。
5.辅助装置:为了提高超声磨削装置的效率和加工质量,常常需要一些辅助装置。
例如冷却系统可以冷却加工过程中产生的热量,减少工件的变形和表面质量的损坏;收集系统可以收集加工过程中产生的切削屑和废料,便于清理和回收利用。
1.功能需求:根据实际应用需求确定超声磨削装置的功能。
例如,不同的材料(金属、陶瓷、玻璃等)具有不同的物理性质和加工要求,需要针对性地设计不同的结构和参数。
2.材料选择:超声磨削装置的结构材料应具有高强度、高刚度和良好的耐磨性能,以满足高频振动的工作要求。
3.结构设计:超声磨削装置的结构设计应紧凑合理,以提高工作效率和加工精度。
同时,还需要考虑装置的稳定性和可靠性,以确保长时间连续工作的可行性。
4.参数调节:超声磨削装置应具有调节振动频率、振幅和工作时间等参数的功能,以适应不同材料和加工要求。
5.安全性设计:超声磨削装置的设计还需要考虑安全性,例如添加安全保护装置,防止误操作和意外伤害。
基于超声振动辅助车削的建模与仿真研究
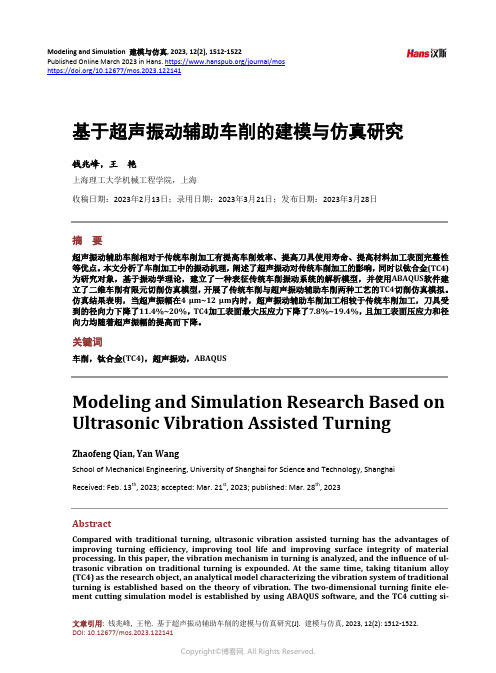
Modeling and Simulation 建模与仿真, 2023, 12(2), 1512-1522 Published Online March 2023 in Hans. https:///journal/mos https:///10.12677/mos.2023.122141基于超声振动辅助车削的建模与仿真研究钱兆峰,王 艳上海理工大学机械工程学院,上海收稿日期:2023年2月13日;录用日期:2023年3月21日;发布日期:2023年3月28日摘要超声振动辅助车削相对于传统车削加工有提高车削效率、提高刀具使用寿命、提高材料加工表面完整性等优点。
本文分析了车削加工中的振动机理,阐述了超声振动对传统车削加工的影响,同时以钛合金(TC4)为研究对象,基于振动学理论,建立了一种表征传统车削振动系统的解析模型,并使用ABAQUS 软件建立了二维车削有限元切削仿真模型,开展了传统车削与超声振动辅助车削两种工艺的TC4切削仿真模拟。
仿真结果表明,当超声振幅在4 μm~12 μm 内时,超声振动辅助车削加工相较于传统车削加工,刀具受到的径向力下降了11.4%~20%,TC4加工表面最大压应力下降了7.8%~19.4%,且加工表面压应力和径向力均随着超声振幅的提高而下降。
关键词车削,钛合金(TC4),超声振动,ABAQUSModeling and Simulation Research Based on Ultrasonic Vibration Assisted TurningZhaofeng Qian, Yan WangSchool of Mechanical Engineering, University of Shanghai for Science and Technology, ShanghaiReceived: Feb. 13th , 2023; accepted: Mar. 21st , 2023; published: Mar. 28th , 2023AbstractCompared with traditional turning, ultrasonic vibration assisted turning has the advantages of improving turning efficiency, improving tool life and improving surface integrity of material processing. In this paper, the vibration mechanism in turning is analyzed, and the influence of ul-trasonic vibration on traditional turning is expounded. At the same time, taking titanium alloy (TC4) as the research object, an analytical model characterizing the vibration system of traditional turning is established based on the theory of vibration. The two-dimensional turning finite ele-ment cutting simulation model is established by using ABAQUS software, and the TC4 cutting si-钱兆峰,王艳mulation of traditional turning and ultrasonic vibration assisted turning is carried out. The simu-lation results show that when the ultrasonic amplitude is within 4 μm~12 μm, compared with the traditional turning, the radial force of the tool is reduced by 11.4%~20%, and the maximum com-pressive stress of the TC4 machined surface is reduced by 7.8%~19.4%. The surface compressive stress and radial force decrease with the increase of ultrasonic amplitude.KeywordsTurning, Titanium Alloy (TC4), Ultrasonic Vibration, ABAQUSThis work is licensed under the Creative Commons Attribution International License (CC BY 4.0)./licenses/by/4.0/1. 引言钛合金(TC4)是一种难加工材料,具有材质较轻、强度硬度高、耐热性强、抗腐蚀性好等优点[1]。
超声内圆磨削系统新型振子的仿真和实验研究
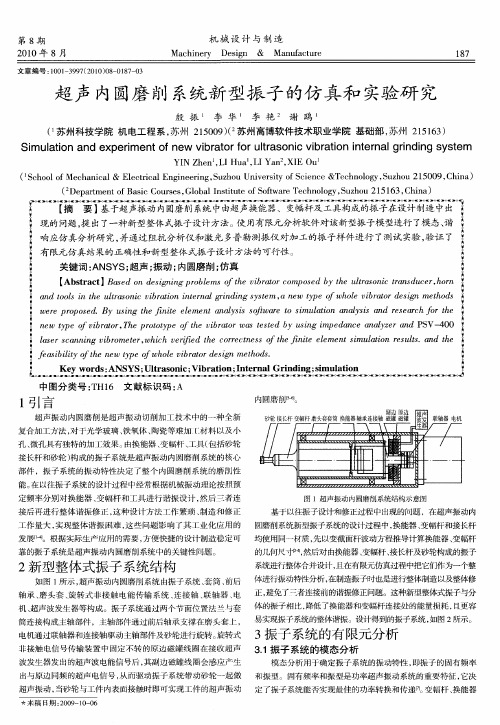
{ ail te e p w o ia r eg e os s bi o h wt e hlvb ods n t d. itf n y o y f e r i m h t
: K y od : N Y ; l ao i; irt n Itra G idn ; m l i e rsA S SU t sn Vb ai ; en l r igs ua o w r c o n n i tn
部件 ,振子系统的振动特性决定了整个 内圆磨削系统 的磨削性 能。 在以往振子系统 的设计过程中经常根据机械振动理论按照预
定 频 率 分 别 对 换 能 器 、 幅杆 和工 具 进 行 谐 振 设 计 , 后 i 者 连 变 然
L H l 【… … 一 … … … 一 … 一 一 ’ 。… 0… … … … 一 一 … 一 t ’
l
【 要】 摘 基于超声振动内 磨削系 圆 统中由 超声换能器、变幅杆及工具构成的振子在设计制造中出 l
{现的问题, 提出了一种新型整体式振子设计方法。 使用有限元分析软件对该新型振子模型进行了 j、 { 模态 谐 -
;w rpoo d B s gt ne l et nl is t r t s u i n y s n s r r e r s . y i e i e n aa s f a m l o aa s d e a h o e pe u n h f t e m y s ow e o i  ̄ n l i a r e c f ; i ;nwt e b t ,h rop t ia r a t t yui pdneaazr n S 一0 ; e p v ro Te o t e h v ro W s db s gi eac n ye adPV 40 y o ia r p ty o e b s e e f f t n m l
摩擦磨损试验机的虚拟设计与仿真分析

东北大学硕士学位论文目录目录独创性声明…………………………………………………………………I摘要……………………………………………………………………..IIAbstract………………………………………………………………………………………………………………..III第1章绪论……………………………………………………………..11.1课题研究的背景和意义…………………………………………………………………..11.2国内外研究现状及发展动态……………………………………………………………..21.3虚拟设计技术简介…………………………………………………………………………41.4课题研究的思路及主要内容……………………………………………………………..5第2章摩擦磨损试验机的总体设计……………………………………72.1试验机的功能及技术参数………………………………………………………………..72.2试验机的设计依据………………………………………………………………………..72.3试验机的系统组成…………………………………………………………………………92.3.1动力传动系统…………………………………………………………………….102.3.2加载系统…………………………………………………………………………..112.3.3感应加热系统…………………………………………………………………….112.3.4润滑系统………………………………………………………………………….122.4试验机的机械系统建模…………………………………………………………………122.4.1零部件三维实体模型的建立…………………………………………………….122.4.2机械系统虚拟装配模型的建立………………………………………………….1312.4.3机械系统装配模型干涉检验…………………………………………………….15.2.5本章小结…………………………………………………………………………………16第3章试验机关键零部件的有限元分析………………………………173.1轴承座和传动轴的结构静力分析………………………………………………………173.1.1轴承座的静力分析……………………………………………………………….173.1.2传动轴的静力分析……………………………………………………………….20f东北大学硕士学位论文目录5.3有限元分析模型的建立…………………………………………………………………625.3.1感应加热一维模型的建立……………………………………………………….625.3.2边晃条件、分析单元与网格划分……………………………………………….635.3.3电磁场与温度场相互耦合的实现……………………………………………….655.4感应加热实际工况模拟与分析…………………………………………………………665.4.1工况模拟工艺参数与材料特性参数…………………………………………….665。
轴承内圆轴向超声高速磨削理论建模与试验研究
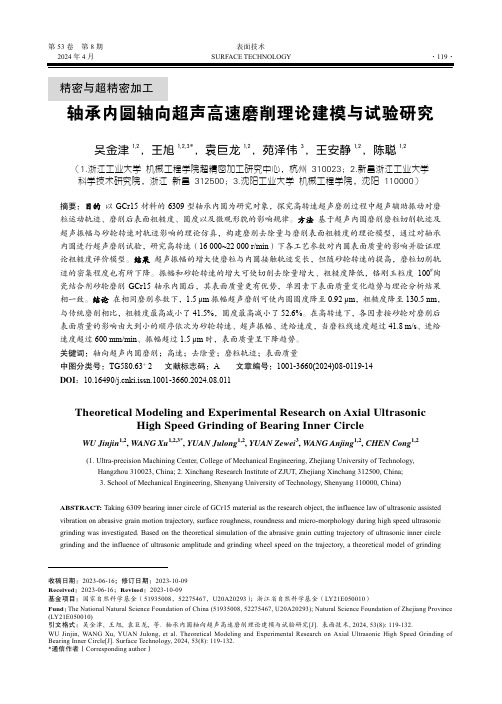
第53卷第8期表面技术2024年4月SURFACE TECHNOLOGY·119·精密与超精密加工轴承内圆轴向超声高速磨削理论建模与试验研究吴金津1,2,王旭1,2,3*,袁巨龙1,2,苑泽伟3,王安静1,2,陈聪1,2(1.浙江工业大学 机械工程学院超精密加工研究中心,杭州 310023;2.新昌浙江工业大学科学技术研究院,浙江 新昌 312500;3.沈阳工业大学 机械工程学院,沈阳 110000)摘要:目的以GCr15材料的6309型轴承内圆为研究对象,探究高转速超声磨削过程中超声辅助振动对磨粒运动轨迹、磨削后表面粗糙度、圆度以及微观形貌的影响规律。
方法基于超声内圆磨削磨粒切削轨迹及超声振幅与砂轮转速对轨迹影响的理论仿真,构建磨削去除量与磨削表面粗糙度的理论模型,通过对轴承内圆进行超声磨削试验,研究高转速(16 000~22 000 r/min)下各工艺参数对内圆表面质量的影响并验证理论粗糙度评价模型。
结果超声振幅的增大使磨粒与内圆接触轨迹变长,但随砂轮转速的提高,磨粒切削轨迹的密集程度也有所下降。
振幅和砂轮转速的增大可使切削去除量增大、粗糙度降低,铬刚玉粒度100#陶瓷结合剂砂轮磨削GCr15轴承内圆后,其表面质量更有优势,单因素下表面质量变化趋势与理论分析结果相一致。
结论在相同磨削参数下,1.5 μm振幅超声磨削可使内圆圆度降至0.92 μm,粗糙度降至130.5 nm,与传统磨削相比,粗糙度最高减小了41.5%,圆度最高减小了52.6%。
在高转速下,各因素按砂轮对磨削后表面质量的影响由大到小的顺序依次为砂轮转速、超声振幅、进给速度,当磨粒线速度超过41.8 m/s、进给速度超过600 mm/min、振幅超过1.5 μm时,表面质量呈下降趋势。
关键词:轴向超声内圆磨削;高速;去除量;磨粒轨迹;表面质量中图分类号:TG580.63+2 文献标志码:A 文章编号:1001-3660(2024)08-0119-14DOI:10.16490/ki.issn.1001-3660.2024.08.011Theoretical Modeling and Experimental Research on Axial UltrasonicHigh Speed Grinding of Bearing Inner CircleWU Jinjin1,2, WANG Xu1,2,3*, YUAN Julong1,2, YUAN Zewei3, WANG Anjing1,2, CHEN Cong1,2(1. Ultra-precision Machining Center, College of Mechanical Engineering, Zhejiang University of Technology,Hangzhou 310023, China; 2. Xinchang Research Institute of ZJUT, Zhejiang Xinchang 312500, China;3. School of Mechanical Engineering, Shenyang University of Technology, Shenyang 110000, China)ABSTRACT: Taking 6309 bearing inner circle of GCr15 material as the research object, the influence law of ultrasonic assisted vibration on abrasive grain motion trajectory, surface roughness, roundness and micro-morphology during high speed ultrasonic grinding was investigated. Based on the theoretical simulation of the abrasive grain cutting trajectory of ultrasonic inner circle grinding and the influence of ultrasonic amplitude and grinding wheel speed on the trajectory, a theoretical model of grinding收稿日期:2023-06-16;修订日期:2023-10-09Received:2023-06-16;Revised:2023-10-09基金项目:国家自然科学基金(51935008,52275467,U20A20293);浙江省自然科学基金(LY21E050010)Fund:The National Natural Science Foundation of China (51935008, 52275467, U20A20293); Natural Science Foundation of Zhejiang Province (LY21E050010)引文格式:吴金津, 王旭, 袁巨龙, 等. 轴承内圆轴向超声高速磨削理论建模与试验研究[J]. 表面技术, 2024, 53(8): 119-132.WU Jinjin, WANG Xu, YUAN Julong, et al. Theoretical Modeling and Experimental Research on Axial Ultrasonic High Speed Grinding of Bearing Inner Circle[J]. Surface Technology, 2024, 53(8): 119-132.*通信作者(Corresponding author)·120·表面技术 2024年4月removal and grinding surface roughness was established to analyze the changing trends of surface quality and grinding efficiency during high speed grinding. Through an ultrasonic grinding test on the bearing inner circle, the influence of process parameters on inner circle surface quality at high speed (16 000-22 000 r/min) was studied and the theoretical model was verified. The contact trajectory between the abrasive grain and the inner circle became longer with the increase of the ultrasonic amplitude, but the intensity of the abrasive grain cutting trajectory also decreased with the increase of the grinding wheel speed.The increase of the ultrasonic amplitude and the grinding wheel speed could increase the cutting removal and reduce the roughness. Compared with brown corundum and white corundum with the same parameters, the surface quality of the GCr15 bearing after grinding the inner circle with a chrome corundum 100# ceramic bonding wheel was superior, and the variation trend of surface quality under a single factor was consistent with the theoretical analysis. In conclusion, with the same grinding parameters, ultrasonic grinding with 1.5 μm amplitude can reduce the inner roundness to 0.92 μm and the roughness to 130.5 nm, which can reduce the roughness up to 41.5% and roundness up to 52.6% compared with the traditional grinding with the same parameters. Through the orthogonal test, it is concluded that the factors that have a great influence on the surface quality after grinding at high speed of the grinding wheel are as follows: grinding wheel speed, ultrasonic amplitude, feed speed.The optimal grinding process for this research object at high speed is as follows: grinding wheel speed 20 000 r/min, radial feed speed 600 mm/min, axial amplitude 1.5 μm, workpiece rotation 250 r/min, grinding depth 20 μm. Based on the optimal process obtained by orthogonal test, single factor tests are carried out on grinding wheel speed, ultrasonic amplitude and feed speed.According to the decline percentage of the single factor tests, the improvement effect of ultrasonic grinding on surface quality increases with the increase of grinding wheel speed when the speed is less than 20 000 r/min, and decreases with the increase of rotating speed when the speed is more than 20 000 r/min. When the radial feed speed of the workpiece is less than 600 mm/min, the improvement effect of ultrasonic grinding on the surface quality increases with the increase of the feed speed, and decreases with the increase of the feed speed when the radial feed speed is more than 600 mm/min. When the axial ultrasonic amplitude is applied to 6 μm, a sinusoidal vibration pattern will appear on the surface after grinding and the grinding effect will be weakened, while the uniform surface texture after 1.5 μm grinding can effectively reduce the cracks caused by high speed grinding.KEY WORDS: axial ultrasonic inner circle grinding; high speed; removal amount; abrasive trajectory; surface quality轴承是机械装备的核心基础零部件,其技术水平代表了一个国家的工业水平[1]。
机械系统振动建模与仿真的研究进展
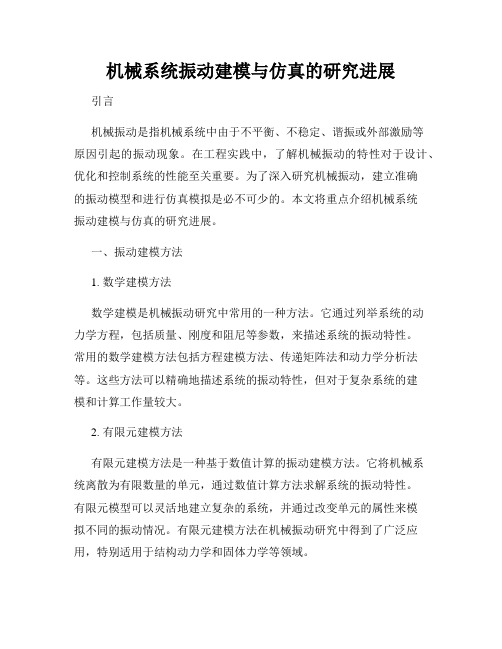
机械系统振动建模与仿真的研究进展引言机械振动是指机械系统中由于不平衡、不稳定、谐振或外部激励等原因引起的振动现象。
在工程实践中,了解机械振动的特性对于设计、优化和控制系统的性能至关重要。
为了深入研究机械振动,建立准确的振动模型和进行仿真模拟是必不可少的。
本文将重点介绍机械系统振动建模与仿真的研究进展。
一、振动建模方法1. 数学建模方法数学建模是机械振动研究中常用的一种方法。
它通过列举系统的动力学方程,包括质量、刚度和阻尼等参数,来描述系统的振动特性。
常用的数学建模方法包括方程建模方法、传递矩阵法和动力学分析法等。
这些方法可以精确地描述系统的振动特性,但对于复杂系统的建模和计算工作量较大。
2. 有限元建模方法有限元建模方法是一种基于数值计算的振动建模方法。
它将机械系统离散为有限数量的单元,通过数值计算方法求解系统的振动特性。
有限元模型可以灵活地建立复杂的系统,并通过改变单元的属性来模拟不同的振动情况。
有限元建模方法在机械振动研究中得到了广泛应用,特别适用于结构动力学和固体力学等领域。
二、振动仿真技术1. 模态分析模态分析是一种常用的振动仿真技术,它可以通过计算系统的固有振动模态和固有频率来了解系统的振动特性。
模态分析可以帮助工程师找到系统的主要振动模态和主要激励来源,从而进行合理的设计和优化。
2. 动态响应分析动态响应分析是一种通过施加外部激励,计算系统的动态响应的仿真技术。
通过动态响应分析,可以了解系统在不同激励条件下的振动响应情况,帮助工程师评估系统的稳定性和安全性。
3. 随机振动仿真随机振动仿真是一种用于研究随机激励下系统振动特性的仿真技术。
随机振动仿真常用于分析系统的可靠性和寿命,帮助工程师预测系统在不同激励条件下的振动情况。
三、应用案例1. 汽车振动仿真汽车振动是影响乘坐舒适性和车辆性能的重要因素。
通过振动建模和仿真技术,可以确定汽车系统中的振动源和主要振动路径,并进行优化设计,提高乘坐舒适性和车辆性能。
超声振动辅助铣削仿真及表面性质研究

超声振动辅助铣削仿真及表面性质研究现代科学技术的迅猛发展促使着新型材料领域的兴起,新型材料在市场中所占的地位越来越突出。
特别是航天、航海、电子、国防等现代工业部门对于具有高性能的新型材料更是迫切需求。
这些新材料具有高的应力应变、高硬度、高脆性、耐磨耐腐蚀等特点,更能适应现代尖端产品的性能。
虽然这些材料有着良好的机械性能,却给传统制造业带来了极大的挑战。
新的制造技术也在新型材料的驱动下不断涌现。
超声振动辅助加工就是新型制造技术当中的一个主要代表。
超声振动辅助加工是将高频率、小振幅的超声简谐运动与传统的制造技术相结合的一种特种加工技术。
超声振动辅助加工按照振动施加的方式可以划分成单方向振动辅助加工和正交式振动辅助加工。
通过施加超声振动,在加工的过程当中改变了刀具和工件两者之间的接触方式,促使切削力和表面质量均有一定程度的改善。
切削过程中由于刀具在工件上进行高频率的简谐运动,工件表面上会被加工出具有一定规律的表面微观织构,这些织构随着加工参数和振动参数的不同会呈现出很大的差异,同时也会对表面的性能产生很大的影响。
本文利用有限元仿真和实验研究的方法分析了超声振动辅助铣削加工的过程以及切削表面形貌和性质。
分析了超声振动辅助铣削加工的运动轨迹和受力情况。
利用切削仿真软件AdvantEdge对加工过程仿真进行了具体的实现。
包括加工参数的设置,材料本构参数、失效参数以及刀具和切屑接触模型的设置。
将超声振动加工与传统切削过程相对比,对比分析研究了切削加工中应力、应变、温度、切削力等参数。
变幅杆是超声振动辅助加工过程中非常关键的单元。
为了保证其在使用过程中的稳定性能,对变幅杆进行了振型分析和扫频分析。
振型分析获得变幅杆的不同阶共振频率和模态响应。
扫频分析研究其在外加超声振动载荷下的位移变化情况,提取变幅杆的端面位移,最终求解出变幅杆的放大倍数。
对铝合金2A12、45钢、Ti-6Al-4V三种材料进行超声振动辅助铣削实验。
- 1、下载文档前请自行甄别文档内容的完整性,平台不提供额外的编辑、内容补充、找答案等附加服务。
- 2、"仅部分预览"的文档,不可在线预览部分如存在完整性等问题,可反馈申请退款(可完整预览的文档不适用该条件!)。
- 3、如文档侵犯您的权益,请联系客服反馈,我们会尽快为您处理(人工客服工作时间:9:00-18:30)。
摘要:超声波加工是一门重要的特种加工技术,超声加工的总概述:其分为超声车、铣、磨、钻等。
超声振动磨削是一种特殊的切削加工的方法,这种加工技术对于加工陶瓷、高强度复合材料以及硬脆材料具有独到的优势。
本文从超声振动声学子系统设计超声振动磨削机构。
从声学角度和波动方程角度分别介绍了变幅杆设计的理论基础。
设计了机构与工件相连接以及机构与机床相连接装置。
这个超声振动磨削机构,可以直接装配到一般普通机床上直接使用,因此非常方便。
这种新型机构可以作为一种机床附件,它具有体积小、结构简单、成本低、可加工大型工件的优点,对超声波加工以及机床的发展具有十分重要的意义。
关键词:超声波发生器,换能器,变幅杆,珩磨头。
ABSTRACT:The ultrasonic machining is an important special machining technology, is the supersonic processing total outline: It divides into the supersonic vehicle, the mill, to rub, to drill and so on. The ultrasonic vibration grinding is one special machining method, this kind of process technology regarding the ceramics, the high strength compound materials as well as the hard crisp material has the original superiority. This article from ultrasonic vibration acoustics system design organization. Introduced the amplitude pole design rationale from acoustics angle and the wave equation angle. Has designed the organization and the work piece connects as well as the organization and the engine bed junction device. Designs this ultrasonic vibration grinding organization, may assemble directly to the engine bed on the direct use. This kind of new organization may take one kind of engine bed appendix, has the volume to be small, the structure is simple, the cost low merit, has the vital significance to the ultrasonic machining as well as engine bed‘s development.Key words:Ultrasonic generator, transducer, amplitude pole, top horizontal jade piece wheel head.目录第一章绪论 (5)1.1引言 (5)1.2超声振动磨削机构概述 (5)1.3超声波的产生及其特性 (5)1.4超声波加工发展概况 (6)1.5课题研究的内容 (7)第二章超声振动磨削系统的总体机构设计 (9)2.1引言 (9)2.2超声振动磨削系统的结构设计 (9)2.2.1 超声波机床与普通机床的异同点: (9)2.2.2 超声振动磨削系统基本结构的确定 (10)第三章超声振动磨削机构声学子系统的设计 (12)3.1超声波发生器与换能器 (12)3.2超声变幅杆的设计 (13)3.2.1 变幅杆的功用 (13)3.2.2 变幅杆的振动形式及特点 (14)3.2.3 变幅杆的类型分析和比较 (15)3.2.4 变幅杆类型的选择 (17)3.2.5 变幅杆材料的选择 (18)3.2.6 变幅杆的设计与解析 (19)3.2.7 变幅杆各参数的计算 (25)3.2.8 变幅杆与换能器的连接 (26)3.2.9 变幅杆的固定 (27)3.3轴瓦的设计与连接 (27)3.4外固定套的设计与连接 (28)3.5油石的选择 (29)3.6螺钉、双头螺柱、垫圈和梯形螺栓的选择 (31)3.6.1螺钉的选择 (31)3.6.2双头螺柱的选择 (31)3.6.3垫圈的选择 (32)3.6.4梯形螺栓的选择 (32)第四章超声振动磨削机构建模 (33)4.1三维建模软件 (33)4.2对超声振动磨削机构进行建模 (38)4.2.1 变幅杆的三维建模与三维建模步骤 (38)4.2.2 刀杆的三维建模与三维建模步骤 (39)4.2.3 轴瓦的三维建模与三维建模步骤 (40)4.2.4 支架的三维建模与三维建模步骤 (41)4.2.5 超声振动磨削机构的三维建模与三维建模步骤 (42)第五章结论和展望 (43)5.1结论 (43)5.2展望 (43)参考文献 (44)致谢 (45)附录一英文科技文献翻译 (46)附录二毕业设计任务书 (65)超声振动磨削机构的设计与建模第一章绪论1.1引言随着科学技术的迅速发展和激烈的市场竞争,加快了产品更新换代的步伐,为此,各种新材料、新结构、高要求的零部件大量涌现,这对机械制造业提出了新的要求。
解决各种难磨削材料尤其是硬脆材料及复合材料的加工问题成了一个急待解决的问题。
传统加工方法难度大、质量差、特种加工也就应运而生。
特种加工包括电火花加工、超声波加工以及激光加工等。
其中,超声波加工适合于加工各种硬脆材料,尤其是加工难以加工的材料,如玻璃、陶瓷、石英、金刚石、半导体等材料。
因此在现在的加工中得到了广泛的应用。
但是,超声波机床具有体积大、成本高的缺陷。
还有加工的尺寸受到限制。
为此,本文提出了一种新型的超声振动磨削机构,该新型结构可以作为一种机床附件,具有体积小、结构简单、成本低、可加工大型工件的优点,该机构可以直接安装在车床上即改变了传统的车床只能切削工件而不能珩磨工件的缺点,这对超声波加工以及机床的发展具有十分重要的意义。
1.2超声振动磨削机构概述超声振动磨削机构中的声学系统包括有:超声波发生器、换能器、变幅机构和珩磨头。
超声波发生器是将220V或380V的交流电变成有一定功率输出的超声频电信号,即把电信号转变成超声频电信号;而超声频电信号通过换能器的作用把其转换成机械信号,机械信号通过变幅杆的变幅作用把振幅或速度放大传递给珩磨头进行超声振动珩磨。
1.3超声波的产生及其特性声波与光波、电磁波一样,都是因物体在介质中发生振动,介质各点之间存在弹性联系,引起相邻各点的振动从而形成的纵波。
声波是人耳能感受到的一种纵波。
其频率范围是16—16000Hz。
当声波的频率低于16Hz时就叫次声波,高于16000Hz则称为超声波、加工用超声波的频率为16000-25000Hz。
图1-1压电晶片受外力影响下的形变它是由压电晶片(如石英、钦酸钡、错钦酸钡等)的逆压电效应产生的。
如图1- 1所示,当压电晶片受到某一规律的压缩和拉伸时(晶片厚薄亦产生规律性变化),在晶片两面产生相同电压变化,称为正压电效应。
反之,把某一规律变化的电压加在压电晶体片两面上,它就作相应机械振动,称为逆压电效应。
当压电晶片受到来自高频(>20kHz)发生器的高频电压作用而发生逆压电效应时,晶片在其厚度方向发生变薄及变厚的振动,晶片周围介质点亦相应振动,这个振动在介质中传播,即形成超声波。
在现在的生产加工中,超声波的应用非常广泛.它具有如下特性:1. 超声波可在气体、液体和固体介质中传播,其传播速度与频率、波长、介质密度等有关,2. 声波能传递很强的能量。
超声波的作用主要是对其传播方向上的障碍物施加压力。
因此可用压力大小来表示超声波的强度,传播的波动能力越强压力也就越大。
3. 超声波会产生反射、干涉和共振现象。
出现波的叠加作用,使弹性杆中某处质点始终不动。
1.4超声波加工发展概况国际方面:自19世纪末到20世纪初,在物理学上发现了压电效应与反压电效应之后,人们解决了利用电子学技术产生超声波的办法,从此迅速揭开了发展与推广超声技术的历史篇章。
1922年,德国出现了首例超声波治疗的发明专利。
1939年发表了有关超声波治疗取得临床效果的文献报道。
40年代末期超声治疗在欧美兴起,直到1949年召开的第一次国际医学超声波学术会议上,才有了超声治疗方面的论文交流,为超声治疗学的发展奠定了基础。
1956年第二届国际超声医学学术会议上已有许多论文发表,超声治疗进入了实用成熟阶段。
我国超声波加工始于50年代末期,曾掀起一阵群众性的“超声热”,由于超声电源、换能器、声振系统很不成熟,缺乏合理的组织和持续的研究工作,很快就冷了下来。
60年代末,哈尔滨工业大学应用超声车削,加工了一批飞机上的铝制细长轴,取得了良好的切削效果。
1976年,我国再次开展超声加工的试验研究和理论探讨工作。
1983年,机械电子工业部科技司委托《机械工艺师》杂志编辑部在西安召开了我国第一次“振动与切削专题讨论会”,1985年,机械电子工业部第11研究所研制成功旋转超声加工机,在玻璃、陶瓷等硬脆材料的钻孔、套料、端铣、内外圆磨削及螺纹加工中,取得了优异的工艺效果。
80年代后期,天津大学的李天基等人在高速磨削时对磨头施以超声振动,提出了高效的超声磨削复合加工方法,效率比传统的超声加工提高6倍以上,表面质量也有了大幅度提高。
北京装甲兵技术学院提出了一种“超声微振车削”的新工艺、其特点是功率小、振幅小,同样可获得一般振动车削效果。
清华大学王先速等进行了45号钢制成的超声砂带研抛的实验研究。
1.5课题研究的内容课题研究的内容有以下六点:1. 超声加工机床进行分析,通过和普通机床的比较,研究一种新的机构,使其可以安装在普通机床上便可进行超声加工。
2. 变幅杆是超声波机床振动系统的重要组成部分,本文将从声学角度和波动方程角度来探讨变幅杆的设计和珩磨头的设计问题。
3. 对变幅杆进行结构分析和动力学分析。
4. 为满足不同用户的要求,以超声电源功率250W的磨削头结构为基型产品,对其进行系列化设计。
5. 对超声振动磨削机构进行三维建模。
6. 对本课题的内容做出结论和展望。