轧制过程计算机控制系统
基于CSP轧机过程控制系统建立无取相硅钢轧制模型的研究
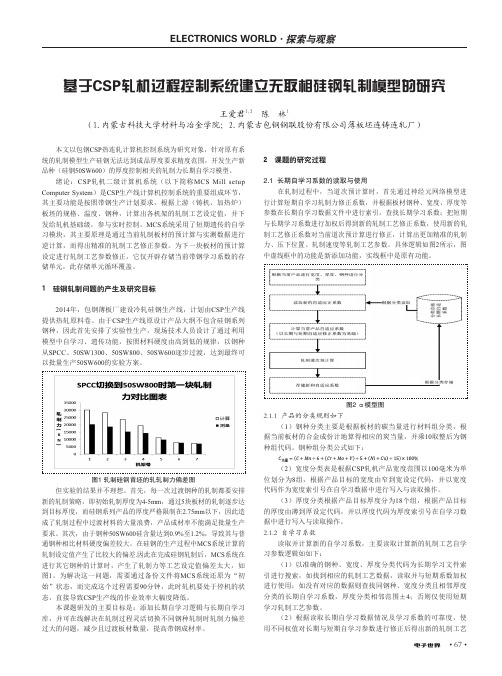
• 67•基于CSP轧机过程控制系统建立无取相硅钢轧制模型的研究王爱君1,2 陈 林1(1.内蒙古科技大学材料与冶金学院;2.内蒙古包钢钢联股份有限公司薄板坯连铸连轧厂)本文以包钢CSP 热连轧计算机控制系统为研究对象,针对原有系统的轧制模型生产硅钢无法达到成品厚度要求精度范围,开发生产新品种(硅钢50SW600)的厚度控制相关的轧制力长期自学习模型。
绪论:CSP 轧机二级计算机系统(以下简称MCS Mill setup Computer System )是CSP 生产线计算机控制系统的重要组成环节,其主要功能是按照带钢生产计划要求,根据上游(铸机、加热炉)板坯的规格、温度、钢种,计算出各机架的轧制工艺设定值,并下发给轧机基础级,参与实时控制。
MCS 系统采用了短期遗传的自学习模块,其主要原理是通过当前轧制板材的预计算与实测数据进行逆计算,而得出精准的轧制工艺修正参数。
为下一块板材的预计算设定进行轧制工艺参数修正,它仅开辟存储当前带钢学习系数的存储单元,此存储单元循环覆盖。
1 硅钢轧制问题的产生及研究目标2014年,包钢薄板厂建设冷轧硅钢生产线,计划由CSP 生产线提供热轧原料卷。
由于CSP 生产线原设计产品大纲不包含硅钢系列钢种,因此首先安排了实验性生产,现场技术人员设计了通过利用模型中自学习、遗传功能,按照材料硬度由高到低的规律,以钢种从SPCC 、50SW1300、50SW800、50SW600逐步过渡,达到最终可以批量生产50SW600的实验方案。
图1 轧制硅钢首坯的轧轧制力偏差图但实验的结果并不理想。
首先,每一次过渡钢种的轧制都要安排新的轧制策略,即初始轧制厚度为4-5mm ,通过5块板材的轧制逐步达到目标厚度,而硅钢系列产品的厚度严格限制在2.75mm 以下,因此造成了轧制过程中过渡材料的大量浪费,产品成材率不能满足批量生产要求。
其次,由于钢种50SW600硅含量达到0.9%至1.2%,导致其与普通钢种相比材料硬度偏差较大。
冷轧轧机TDC控制系统

目录冷轧轧机TDC控制系统一.硬件和组态二.系统软件1.处理器功能简介MON FUNCTIONS 通用功能3.MASTER FUNCTIONS 主令功能:4.STAND1-STAND5 机架控制系统1-5冷轧轧机TDC控制系统一.硬件和组态TDC工业控制系统西门子公司SIMADYN D的升级换代产品,也是一种多处理器并行远行的控制系统。
典型的TDC控制系统的配置是由电源框架、处理器摸板、I/O摸板和通讯摸板搭建构成。
电源框架含21个插槽,最多允许20个处理器同时运行。
框架上方的电源可单独拆卸,模板不可带电插拔。
CPU551是TDC控制系统的中央处理器,带有一个4M记忆卡,程序存储在记忆卡内,电源启动时被读入CPU551中执行。
可通过在线功能对处理器和存储卡中的程序作同步修改。
SM500是数字量/模拟量输入/输出模板,更换时注意跳线.CP50MO是MPI/PROFIBUS通讯摸板,更换时需要使用COM-PROFIBUS软件对其进行组态的软件下装。
CP5100是工业以态网的通讯摸板,更换时注意插槽跳线。
CP52A0是GDM通讯模板。
GDM是不同框架的TDC之间进行数据交换的特有通讯方式,不同框架的TDC通过光缆汇总到GDM内,点对点之间的通讯更加直接,传输速度更快。
TDC控制系统的硬件需要在软件程序中进行组态和编译,然后下装到CPU中。
二.系统软件包钢薄板厂冷轧轧机区域TDC控制系统按框架分为以下三个功能:12酸轧电气控制冷轧酸轧电气篇C S P B T2.1 处理器功能简介1.COMMON FUNCTIONS 通用功能:处理器1:SIL: 模拟功能SDH: 轧制参数管理IVI: 人机画面处理器2:MTR: 物料跟踪系统WDG: 楔形调整功能处理器3: ADP: 实际值管理2.MASTER FUNCTIONS 主令功能:处理器1: MRG-GT: 轧机区域速度主令处理器2: THC-TH: 轧机厚度控制入口区域处理器3: THC-TX: 轧机厚度控制出口区域处理器4: SLC: 轧机滑差计算ITG: 张力计接口处理器5: LCO-LT: 轧机区域生产线协调3.STAND1-STAND5 机架控制系统1-5处理器1: CAL: 机架标定SCO: 通讯接口MAI: 手动干涉ITC: 机架间张力控制处理器2: SDS: 机架压下系统处理器3: RBS: 机架弯辊系统12酸轧电气控制冷轧酸轧电气篇C S P B TRSS: 机架串辊系统处理器4:REC:轧辊偏心补偿(F1专有)FLC:板形控制系统(F5专有)以下将对每个功能中的笔者阅读过并认为重要的处理器的程序作说明,对于没有阅读和非重要的仅作简单介绍。
四辊铜带轧机轧制过程计算机控制系统的研究
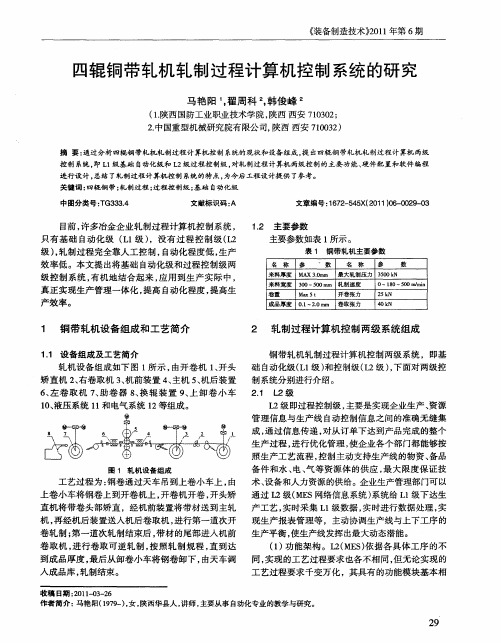
四辊铜 带轧机 轧制过程计算 机控 制 系统 的研 究
马 艳阳 , , 科z 翟周 , 峰z 韩俊
(. 1 陕西国防工业职业技术学院 , 陕西 西安 70 0 ; 132
2中国重型机械研究院有限公 司, . 陕西 西安 70 3 ) 10 2
级 )轧制过程完全靠人工控制 , , 自动化程度低 , 生产 效率低。本文提 出将基础 自动化级和过程控制级两 级控制 系统 , 有机地结合起来 , 应用到 生产实际 中 , 真正 实现生产管理一体化 , 提高 自动化程度 , 提高生 产效 率 。
0 8 — 0 / i —1 0 5 0m r n a
摘 要: 通过 分析 四辊铜 带轧机轧制过程计 算机控制 系统的现状和设备组成 , 出四辊铜 带轧机轧制过程 计算机两级 提
控 制 系统 , L 级基础 自动化 级和 L 级 过程控制级 , 即 1 2 对轧制过程计算机两级控制 的主要 功能 、 件 配置和软件 编程 硬
进行设 计 , 总结 了轧制过 程计算机控制 系统 的特 点 , 为今后工程设计提供 了 考。 参
图 1 轧 机 设 备 组 成
照生产工 艺流程 , 控制主动支持生产线的物资 、 备品 备件 和水 、 气等资源体的供应 , 电、 最大 限度保证技
工艺过程为 : 钢卷通过天车 吊到上卷小车上 , 术 、 由 设备和人力资源的供给。企业生产管理部门可以 上卷小车将钢卷上到开卷机上 , 开卷机开卷 , 开头矫 通过 L 级( E 2 M S网络信息系统 ) 系统给 L 级下达生 1 直机将带卷头部矫直 ,经机前装置将带材送到主轧 产工艺 , 实时采集 L 级数据 , l 实时进行数据处理 , 实
自动轧钢机的plc控制

PLC的编程语言和编程工具
PLC的编程语言通常采用类似于计算机高级语言的指令集,如Ladder Logic、Function Block Diagram(FBD)、Structured Text(ST)、Instruction List(IL)等。
常用的PLC编程工具包括PLC厂商提供的专用软件包和第三方软件,如Rockwell的RSLogix 5000、Siemens的STEP 7等。这 些软件提供了图形化编程界面,使得用户可以方便地编写、调试和监控PLC程序。
PLC控制技术基础
PLC的定义与特点
PLC(可编程逻辑控制器)是一种专为工业环境设计的数字电子设备,用于执行顺 序控制、逻辑运算、算术运算等操作,并通过数字或模拟输入/输出模块控制各种类 型的机器和设备。
PLC具有高可靠性、高灵活性、易于编程和易于扩展等特点,因此在工业自动化 领域得到了广泛应用。
程序优化与改进
优化算法
根据实际运行情况和性能要求,优化控制算 法,提高控制精度和响应速度。
改进功能
根据生产需求和设备升级,逐步增加或改进 控制功能,提高自动轧钢机的生产效率和产 品质量。
05
系统测试与运行
系统测试方案与实施
测试目的
确保PLC控制系统在自动轧钢机中的稳定性 和可靠性,提高生产效率。
PLC的基本组成和工作原理
PLC主要由中央处理单元(CPU)、存储器、 输入/输出模块、电源和编程设备等部分组成。
PLC的工作原理可以概括为输入采样、程序 执行和输出刷新三个阶段。在输入采样阶段 ,PLC读取输入信号的状态并将其存储在输 入映像寄存器中;在程序执行阶段,PLC按 照用户程序的顺序执行指令,并更新内部存 储器的值;在输出刷新阶段,PLC将输出映 像寄存器的值输出到输出模块,驱动外部设
中厚板轧制的计算机生产过程控制
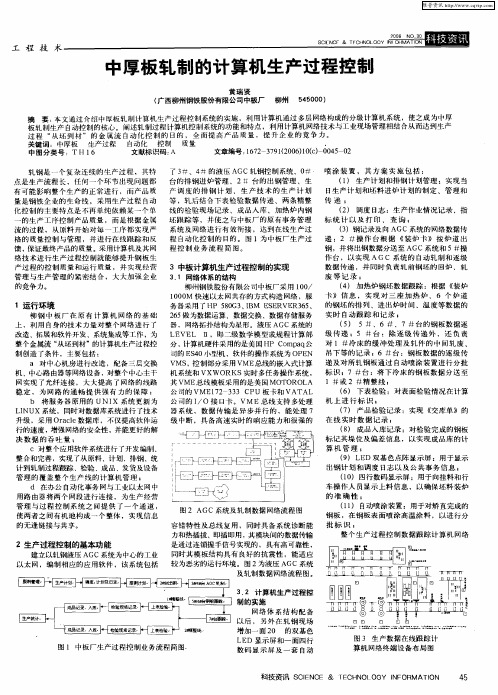
了3 #、4 的液 压 AGC轧钢控 制 系统 、0# # 喷涂装 置,其方案实施包括 : 台的 排钢进 炉管 理 、2# 台的 出钢 管理 、生 ( ) 生产计 划和 排钢计 划管 理 :实现 当 1 3 产 调 度 的 排钢 计划 、生 产技 术的 生 产 计 划 1生 产计划 和坯 料进 炉计 划的制 定 、管 理和 等 ,轧后 结合下 表检 验数据 传递 、两 条精整 传 递 ; 线的 检验 现场记 录 、成 品入 库 、加 热炉 内钢 ( ) 调度 1志 :生产 作业情 况记 录 、指 2 3 坯跟 踪等 ,并 使之 与 中板厂 的原 有事务 管理 标 统 计 以 及 打 印 、查 询 ; 系统 及 网络进 行有 效衔接 ,达到 在线生 产过 ( )钢 记录及 向 AGC系统的 网络 数据传 3 程 自动 化控制 的 目的 。图 l为 中板厂 生产过 递 :2 #操 作 台根 据 《 装炉 卡 》 按 炉 道 出 程 控 制业 务 流 程 简 图 。 钢 ,并将 出钢数据 分送 至 AGC系统 和 5#操 作 台 ,以 实现 AGC 系统 的 自动 轧制 和逐级 数据 传递 ,并 同时 负责 轧前 钢坯 的 回炉 、轧 3 中板计算机生产过程控制的实现 废等 记录 ; 3 1 网络体 系的结构 . ( ) 加热 炉钢 坯数 据跟踪 :根 据 《 炉 4 装 柳州钢 铁股份 有限公 司中板厂采 用 l 0 0/ l 0 M 快 速以太 网共存 的方式 构造 网络 ,服 卡 》 信 息 ,实 现 对 三 座 加 热 炉 、6 个 炉 道 O0 、 务 器 采 用 了 HP 5 0 、 B E ERVE 6 、 的钢 坯 的排列 、进 出炉 时 间 、温 度等 数据 的 8 G3 I M S R3 5 2 5 为数据运算 、数据交换 、数据存 储服务 实 时 自动跟 踪 和 记 录 ; 6做 器 ,网络拓扑结 构为星形 。液 压 AGC系统的 ( ) 5#、6# 、7#台 的钢板 数据 逐 5 L EVEL Ⅱ,即 二级 数学 模型或 规程计 算部 级 传 递 ;5 # 台 :除 逐 级 传 递 外 ,还 负 责 分, 计算机 硬件采用 的是 美国 HP Co a mp q公 对 l#冷 床的 缓 冲处 理 及轧 件 的 中 间轧废 、 司的 E 4 S 0小型机 ,软 件的操作 系统 为 OPE N 吊下 等的 记录 ;6#台 :钢 板数 据的 逐级 传 V , MS 控制部 分采用 V ME 总线的嵌 入式计算 递 及对 所轧 钢板 通过 自动喷 涂 装置进 行分 批 机 系统 和 VXW0RKS实时 多任务操 作系统 , 标 识 ;7#台 :将下 冷床 的 钢板 数据 分送 至 其 VME总线模板采 用的是美 国 MOTOROL A l#或 2 #精 整线 ; ( 6) 下表检 验 :对表 面检验 情况 在计算 公 司 的 VMEl 2 3 C 7 3 3 PU 板 卡 和 VATAL 公 司的 I /0接 口卡 。VME总线 支持 多处理 机 上 进 行 标 识 ; ( ) 产品检 验记 录 :实现 《 7 交库 单》 的 器 系统 ,数 据 传输 是异 步并 行 的 ,能 处理 7 级 中断 ,具 备高 速实时 的响 应能 力和很 强的 在 线 实时 数 据 记 录 ; ( ) 成品 入库记 录 :对检验 完成 的钢板 8 标 记 其垛 位及偏 差 信息 ,以 实现 成品 库的计 算机 管理 ; ( ) LED双基 色点阵显示 屏 :用于显 示 9 出钢 计 划 和调 度 1志以 及 公共 事 务信 息 ; 3 (0 1 )四行数码 显示屏 :用于 向挂料和 行 车操 作人 员显 示上料 信息 ,以确 保坯 料装 炉 的 准确性 ;
第一节 轧制过程的自动跟踪

11:06
6
轧制过程的计算机控制系统
(一)原始数据区 原始数据区IDA (Initial Data Area)存贮板坯和轧 制计划的原始数据。每根轧件都有自已的原始数 据,例如钢号、材质、钢坯尺寸、成品尺寸和质 量要求等。它们是设定计算和自动控制的必要参 数。原始数据是以数据结构的形式构成,它分为 钢坯数据和钢批数据。钢坯数据是指一块钢坯的 有关数据,而钢批数据则是指若干块材质和尺寸 等要求相接近的副坯组构成的一批数据。
11:06
3
轧制过程的计算机控制系统
计算机控制系统的跟踪功能是通过轧件跟踪等 一系列程序,根据生产线上各个区段的检测器(冷 钢区段为冷金属检测器CMD,热钢区段为热金属 检测器HMD)和负荷继电器LR等的状态,不断地更 新各个区段跟踪指示字的内容来实现的。 随着轧件在生产线上的移动,计算机根据各区 段跟踪指示字的内容判断每根轧件的实际位臵,针 对轧制生产中的原始数据、生产数据和具体要求等 分别进行自动控制。所以,本章以具有典型意义的 热连轧为例,研究轧制生产过程中的数据区、数据 流动以及轧件跟踪的基本方法。
11:06
16
轧制过程的计算机控制系统
(四)运输链数据区 运输链数据区CVDA (Con Veyer Data Area)用 来存贮已经在运输链上的钢卷数据。其中包括从精 轧PDA中传下来的数据、钢卷质量分类结果数据、钢 卷在运输链上的称重值和对钢卷的各种质量检查结 果。运输链数据区保存成品钢卷数据,供钢卷产品 报表使用。 以上4个数据区中的数据是顺序关联的。当一个 轧件沿着加热炉入口辊道到运输链分叉口流动时, 该轧件的数据也相应地按如下方式在各数据区之间 流动:IDA→SDA→PDA→CVDA。当轧件在某道工序进 行加工时,与控制这个轧件有关的数据不断地被加 17 11:06进相应的数据区里。
热连轧过程及计算机控制(L-2)

(3) 半连续式热带轧机(Semi-continuous Hot Strip Mills)(图2-3a) 粗轧机有两个以上的可逆机座,或者全部为可逆机座。
(4) 3/4连续式热带轧机(3/4 Continuous Hot Strip Mills)(图2-3c) 4座粗轧机中有一个可逆机座。
生产效率提高。 (5)热加工变形可引起组织性能的变化,以满足对产品某些组织与性能的要求。
WUST
图1-1 铁碳合金相图
WUST
热加工变形除具有上述优点,使之在生产实践中得到广泛的应用外,同其 他加工方法相比较它也有如下的不足:
(1) 对薄或细的轧件由于散热较快,在生产中保持热加工的温度条件比较 困难;
(2) 热加工后轧件的表面不如冷加工生产的尺寸精确和光洁; (3) 热加工后产品的组织及性能不如冷加工时均匀; (4) 从提高钢材的强度来看,热加工不及冷加工。
热加工变形可以认为是加工硬化和再结晶两个过程的相互重叠。在此过 程中由于再结晶能充分进行和变形时靠三向压应力状态等因素的作用,可使:
(1) 铸态金属组织中的缩孔、疏松、空隙、气泡等缺陷得到压密或焊合。 (2) 在热加工变形中可使晶粒细化和夹杂物破碎。 (3)金属在热变形过程中产生带状组织。
(5) 带卷取箱的热带轧机(图2-4)
WUST
Left Furnace Coiler
FourHight Mill
Right Furnace Coiler
Slab Feed roll
Fig.2-1 Schematic diagram of Steckel mill
轧钢生产过程中自动化控制技术的应用
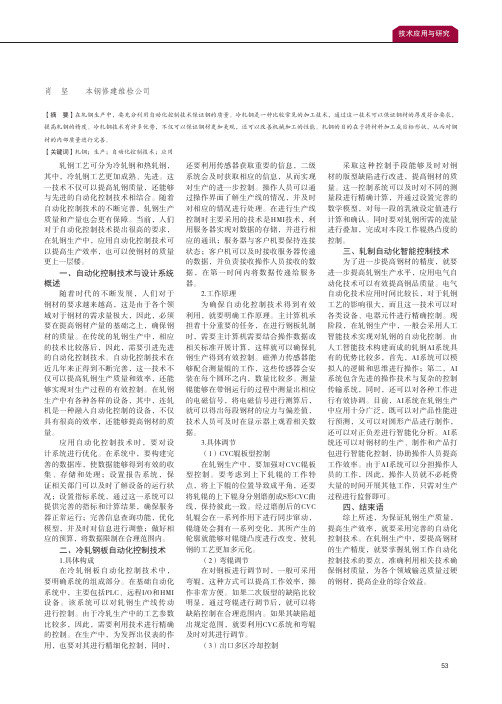
轧钢工艺可分为冷轧钢和热轧钢,其中,冷轧钢工艺更加成熟、先进。
这一技术不仅可以提高轧钢质量,还能够与先进的自动化控制技术相结合。
随着自动化控制技术的不断完善,轧钢生产质量和产量也会更有保障。
当前,人们对于自动化控制技术提出很高的要求,在轧钢生产中,应用自动化控制技术可以提高生产效率,也可以使钢材的质量更上一层楼。
一、自动化控制技术与设计系统概述随着时代的不断发展,人们对于钢材的要求越来越高,这是由于各个领域对于钢材的需求量极大,因此,必须要在提高钢材产量的基础之上,确保钢材的质量。
在传统的轧钢生产中,相应的技术比较落后,因此,需要引进先进的自动化控制技术。
自动化控制技术在近几年来正得到不断完善,这一技术不仅可以提高轧钢生产质量和效率,还能够实现对生产过程的有效控制。
在轧钢生产中有各种各样的设备,其中,连轧机是一种融入自动化控制的设备,不仅具有很高的效率,还能够提高钢材的质量。
应用自动化控制技术时,要对设计系统进行优化。
在系统中,要构建完善的数据库,使数据能够得到有效的收集、存储和处理;设置报告系统,保证相关部门可以及时了解设备的运行状况;设置指标系统,通过这一系统可以提供完善的指标和计算结果,确保服务器正常运行;完善信息查询功能,优化模型,并及时对信息进行调整;做好相应的预算,将数据限制在合理范围内。
二、冷轧钢板自动化控制技术1.具体构成在冷轧钢板自动化控制技术中,要明确系统的组成部分。
在基础自动化系统中,主要包括PLC、远程I/O和HMI 设备。
该系统可以对轧钢生产线传动进行控制。
由于冷轧生产中的工艺参数比较多,因此,需要利用技术进行精确的控制。
在生产中,为发挥出仪表的作用,也要对其进行精细化控制,同时,还要利用传感器获取重要的信息,二级系统会及时获取相应的信息,从而实现对生产的进一步控制。
操作人员可以通过操作界面了解生产线的情况,并及时对相应的情况进行处理。
在进行生产线控制时主要采用的技术是HMI技术,利用服务器实现对数据的存储,并进行相应的通讯;服务器与客户机要保持连接状态;客户机可以及时接收服务器传递的数据,并负责接收操作人员接收的数据,在第一时间内将数据传递给服务器。
- 1、下载文档前请自行甄别文档内容的完整性,平台不提供额外的编辑、内容补充、找答案等附加服务。
- 2、"仅部分预览"的文档,不可在线预览部分如存在完整性等问题,可反馈申请退款(可完整预览的文档不适用该条件!)。
- 3、如文档侵犯您的权益,请联系客服反馈,我们会尽快为您处理(人工客服工作时间:9:00-18:30)。
➢对以上60个参数定时制表;
➢对上限、下限、实时钟停等故障实现故障报 警;
0~10mA
+24V
土霉素车间的DDC控制框图
▪控制目标:厚度精度
▪被控量:辊缝
▪巡检参数:轧制力、辊缝、
▪应用特点:数据收集、记录;在线操 作指导,建立自适应模型。
H h H
应力状态系数QP用布兰德-福德公式的 希尔简化式计算。
Q p Learn 1.79 f
R' 1.02 H
Learn是自学习参数,其初值为1.08
轧制数据表
道次 厚度 轧制力 辊缝 实测厚度 实测压力 实测辊缝 反算压力 自适应参数
0 2.728
2.728
1.150
1 2.300 74.42 2.190 2.315 80.76 2.192 73.10
1.215
2 1.900 77.83 1.780 1.925 81.22 1.782 75.90
1.259
3 1.600 71.18 1.499 1.590 77.09 1.497 72.04
2020年4月28日星期二
5
实例:冷轧带钢平整机的计算机数据收集系统
光电编码器
模拟量输入通道 脉冲输入计数器板
压力传感器
光电编码器
❖控制目的:给予带钢小压下量改善板型平直度,使之达到国家标准;
❖被控量:平整延伸率
vout vin vin
、轧辊辊缝
S0
h
P P0 Cp
❖巡回检测数据:轧制力、轧制速度、辊缝。
2020年4月28日星期二
1
第一章 绪论
1.1 过程计算机控制系统的组成 1.2 过程计算机控制系统的发展概述 1.3 轧制过程计算机控制概述 1.4 过程计算机控制系统的基本类型
2020年4月28日星期二
2
1.4 计算机控制系统的主要类型
控制是作为一个系统与生产过程结合在一起的。根据应用特 点、控制目的、控制方法和系统的构成,过程计算机控制系 统大体上可分成以下几种基本类型: 1. 数据收集系统(Date Acquired System-DAS) 2. 操作指导控制系统( Direct Digital Control-DDC系统) 3. 直接数字控制( Direct Digital Control-DDC系统) 4. 集中型计算机控制系统(Concentric Control system-CCS) 5. 分布式控制系统(Distributed Control System-DCS系统 6. 现场总线控制系统(Fieldbus Control System-FCS系统)
数据收集系统
参数:压力、流量、温度的输入信号;
数据收集 装置
计算机
➢ 模拟量: ➢ 脉冲量: ➢ 开关量:
电机控制系统中的速度给定、电流给定的输入信号;
控制伺服阀、比例阀的输出信号。 通过光电编码器测量的速度、位移 信号。
操作台上的开关、按钮;行程开关、极限开关; 信号指示灯、音响报警、继电器的接通与断开、电磁阀的 打开与关闭;电机的启动与停止;计数器的预定数值计满; 定时器的预定时间已到达。
11
3.直接数字控制系统Direct Digital Control System,DDC
被测变量
…
操作变量
…
控制规律:基于经典控制理论和现代控制理论的程序算法。
DDC 特点: ➢信号转换
➢控制功能强大
➢控制方法灵活
2020年4月28日星期二
➢要求实时性好、可靠性高、适应性强。
12
实例:制药厂的DDC控制
1.302
输入测量厚度 h(1)=2.315 h(2)=1.925 h(3)=1.590
2020年4月28日星期二
9
3 直接数字控制 ( Direct Digital Control-DDC)
本质—— 用一台计算机取代一组模拟调节 器,构成闭环控制回路。
AI、DI
控制站
AO、DO
…
…
…
…
优点 —— 计算灵活,精度高,可以处理多个控制回路。不仅能实现常规 的PID控制规律,也能实现PID以外的多种复杂控制。
问题 —— 当时的计算机系统的价格昂贵,计算机运算速度不能满足快速 过程实时控制的需求。
2020年4月28日星期二
10
CRT 打印机 报警 操作台
计
输入通道 (AI.DI)算来自生 产机 输出通道
过 程
(AO.DO)
★ 要求:实时性好、可靠性高和适应性强
★ 一台计算机通常要控制几个或几十个回路
2020年4月28日星期二
2020年4月28日星期二
3
1 数据收集系统 (Date Acquired System-DAS)
轧制过程中的各种过程变量,计算机可以通过检测仪器检 测到,转换成数字量送入计算机内存,这种检测叫做计算机 采样。计算机还可以再将这些数据经过适当的计算,量纲 换算将它换成所需要的数值,或者进行其他的数学分析或 数据加工。
在这类系统中,计算机只对工业过程的各种参数进行巡回 检测、报警、结果处理,并在给定的时间间隔时,通过显 示、打印等方式向操作人员提供各种数据,即不参加对过 程的控制。这种巡回检测数据收集系统,现已成为各种计 算机控制系统的重要组成部分,它的连接形式如下图所示。
2020年4月28日星期二
4
工业 对象
❖应用特点:数据收集系统纪录和显示轧制过程中的各种不同情况,分
析和研究轧制过程,建立和改善数学模型。
2020年4月28日星期二
6
2.操作指导控制系统 P17
操作指导系统直接从现场输入实洲 参数,由计算机进行分析和计算并 给出操作指导,故称其为“在线” 操作指导系统。
优点:结构简单,控制灵活和安全。
土霉素生产车间20只发酵缸每个 缸有2-4个参数,共需60个参数进 行实时控制
温度 溶氧
pH
消沫
三级缸 10
10
10
10
二级缸
5
5
/
/
一级缸
5
5
/
/
Τ=40ms×60=2.4s
0~10mA
系统完成的功能:
➢对20只缸共50个参数(温度、溶氧、pH)实 现PID控制;
➢对10只三级缸实行消沫控制(开关量控制);
缺点:要由人工操作,速度受到限制,不能控制多个对象。
2020年4月28日星期二
7
计算机:利用所检测的数据,根据一定的 控制和管理方法进行计算,给出相应的操 作指导信息,通过CRT或打印机输出给操 作人员。
在线操作指导控制系统
离线操作指导控制系统
2020年4月28日星期二
8
实例:二辊可逆式冷轧机操作指导系统