实验三 动压滑动轴承实验
实验三 动压滑动轴承实验

实验三动压滑动轴承实验一、实验目的1.验证动压滑动轴承油膜压力分布规律,了解影响油膜压力分布规律的因素,并根据油膜压力分布曲线确定端泄影响系数K b;2.测定动压滑动轴承的摩擦特征曲线,并考察影响摩擦系数的因素。
二、实验设备及仪器1.HZS-1型动压滑动轴承试验台图1 HZS-1型动压滑动轴承实验台图1为试验台总体布置,图中件号1为试验的轴承箱,通过联轴器与变速箱7相联,6为液压箱,装于底座9的内部,12为调速电动机,通过三角带与变速箱输入轴相联,8为调速电机控制旋钮,5为加载油腔压力表,由減压阀4控制油腔压力,2为轴承供油压力表,由减压阀控制其压力,油泵电机开关为10,主电机开关为11,试验台的总开关在其正面下方。
图2为试验轴承箱,件号31为主轴,由一对D级滚动轴承支承,32为试验轴承,空套在主轴上,轴承内径d=60mm,有效宽度=60mm。
在轴承中间横剖面上,沿周向开7个测压孔,在120°范围内的均匀分布,测压表21~27通过管路分别与测压孔相联。
距轴承中间剖面L/4(15mm)处,轴承上端有一个测压孔,表头28与其相联,件号33为加载盖板,固定在箱体上,加载油腔在水平面上的投影面积为60cm2在轴承外圆左侧装有测杆35,环34装在测杆上以供测量摩擦力矩用,环34与轴承中心的距离为150mm,轴承外圆上装有两个平衡锤36,用以在轴承安装前做静平衡。
图2 实验轴承箱箱体左侧装有一个重锤式拉力计如图3所示,测量摩擦力矩时,将拉力计上的吊钩与环34联接,即可测得摩擦力矩。
测杆通过环34作用在拉力计上的力F,由重锤予以平衡,其数值可由αsin1RWLF=求得。
式中R为圆盘半径,W为重锤之重量,L1为重锤重心到轴心之距离,α为圆盘之转角,圆盘转角α通过齿轮放大,可使表头指针转角放大10倍,表头刻度即为F的实际值,单位为克。
JZT型调速电动机的可靠调速范围为120~1200转/分,为了扩大调速范围,试验台传动系统中有一个两级变速箱,当手柄向右倾斜,主轴与电机转速相同;当手柄向右倾斜,主轴为电机转速的1/6。
动压滑动轴承实验
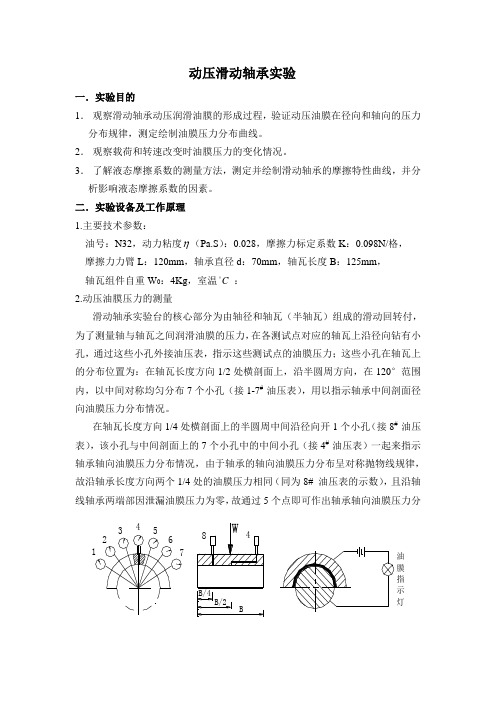
动压滑动轴承实验一.实验目的1.观察滑动轴承动压润滑油膜的形成过程,验证动压油膜在径向和轴向的压力分布规律,测定绘制油膜压力分布曲线。
2.观察载荷和转速改变时油膜压力的变化情况。
3.了解液态摩擦系数的测量方法,测定并绘制滑动轴承的摩擦特性曲线,并分析影响液态摩擦系数的因素。
二.实验设备及工作原理1.主要技术参数:油号:N32,动力粘度 (Pa.S):0.028,摩擦力标定系数K:0.098N/格,摩擦力力臂L:120mm,轴承直径d:70mm,轴瓦长度B:125mm,轴瓦组件自重W0:4Kg,室温C :2.动压油膜压力的测量滑动轴承实验台的核心部分为由轴径和轴瓦(半轴瓦)组成的滑动回转付,为了测量轴与轴瓦之间润滑油膜的压力,在各测试点对应的轴瓦上沿径向钻有小孔,通过这些小孔外接油压表,指示这些测试点的油膜压力;这些小孔在轴瓦上的分布位置为:在轴瓦长度方向1/2处横剖面上,沿半圆周方向,在120°范围内,以中间对称均匀分布7个小孔(接1-7# 油压表),用以指示轴承中间剖面径向油膜压力分布情况。
在轴瓦长度方向1/4处横剖面上的半圆周中间沿径向开1个小孔(接8# 油压表),该小孔与中间剖面上的7个小孔中的中间小孔(接4# 油压表)一起来指示布曲线。
3.油膜形成(摩擦状态)指示装置在实验台控制面板上,设有1个油膜指示灯;油膜指示灯电路通过轴径和轴瓦连成回路(如图所示)。
当轴不转动时,轴径和轴瓦直接接触,油膜指示灯电路接通,灯泡很亮;当轴低速转动时,润滑油进入轴和轴瓦之间形成很薄的油膜,2.打开电源前,应先将外载荷W卸掉,以避免因带载启动而造成轴瓦磨损。
3.接通电源,①通过载荷调零旋钮将载荷显示器调零;②将测力百分表调零。
4.启动电动机并调速至400r/min,分别加40Kg力、60Kg力外载荷,测量油膜压力分布数据;然后把电动机调速至300r/min,读出对应的百分表示数∆,再把电动机转速每次下调50转至250r/min、200r/min、150r/min、100r/min、50r/min,读出对应的百分表示数∆,用于计算摩擦系数f。
滑动轴承实验报告答案

滑动轴承实验报告答案滑动轴承实验报告答案引言:滑动轴承是一种常见的机械元件,广泛应用于各种机械设备中。
通过实验,我们可以了解滑动轴承的工作原理、性能特点以及影响其工作性能的因素。
本报告将对滑动轴承实验进行分析和总结,以期加深对滑动轴承的理解。
实验目的:1. 掌握滑动轴承的工作原理和结构特点;2. 了解滑动轴承的性能指标及其测试方法;3. 分析滑动轴承工作时的摩擦特性及其影响因素。
实验装置和方法:本次实验采用了滑动轴承实验装置,包括轴承座、轴承套、轴承外壳、轴承盖等组成部分。
实验方法是在轴承内壁涂抹润滑油,然后在轴上施加不同的负荷,通过测量轴承温度和摩擦力来分析轴承的工作情况。
实验结果与讨论:通过实验,我们得到了一系列数据,包括轴承温度和摩擦力的变化情况。
根据这些数据,我们可以得出以下结论:1. 轴承温度与负荷大小成正比:实验结果表明,随着负荷的增加,轴承温度也随之升高。
这是因为负荷增加会导致轴承内部的摩擦增加,从而产生更多的热量。
因此,在实际应用中,需要根据负荷大小来选择适当的润滑方式和材料,以保证轴承的正常工作温度。
2. 润滑油的选择对轴承性能有重要影响:实验中我们使用了不同种类的润滑油进行测试,发现不同润滑油的摩擦力和温度变化情况有所不同。
这说明润滑油的选择对轴承的工作性能有重要影响。
在实际应用中,需要根据轴承的工作条件和要求选择适当的润滑油,以提高轴承的工作效率和寿命。
3. 轴承摩擦力与轴承材料和表面处理方式有关:实验中我们使用了不同材料和表面处理方式的轴承进行测试,发现它们的摩擦力存在差异。
这是因为不同材料和表面处理方式会影响轴承与轴之间的接触面积和摩擦系数。
因此,在设计和选择轴承时,需要考虑材料和表面处理方式对轴承摩擦力的影响。
结论:通过本次实验,我们对滑动轴承的工作原理、性能特点以及影响因素有了更深入的了解。
我们发现轴承温度与负荷大小成正比,润滑油的选择对轴承性能有重要影响,轴承摩擦力与轴承材料和表面处理方式有关。
滑动轴承实验报告
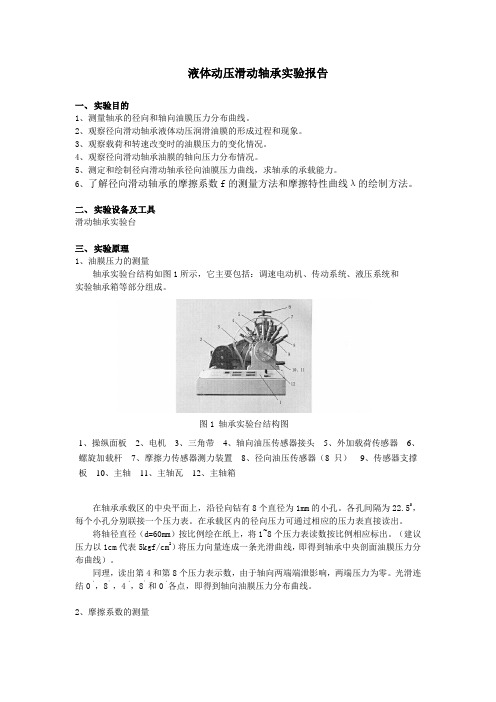
液体动压滑动轴承实验报告一、 实验目的1、测量轴承的径向和轴向油膜压力分布曲线。
2、观察径向滑动轴承液体动压润滑油膜的形成过程和现象。
3、观察载荷和转速改变时的油膜压力的变化情况。
4、观察径向滑动轴承油膜的轴向压力分布情况。
5、测定和绘制径向滑动轴承径向油膜压力曲线,求轴承的承载能力。
6、了解径向滑动轴承的摩擦系数f 的测量方法和摩擦特性曲线λ的绘制方法。
二、 实验设备及工具 滑动轴承实验台 三、 实验原理1、油膜压力的测量轴承实验台结构如图1所示,它主要包括:调速电动机、传动系统、液压系统和 实验轴承箱等部分组成。
在轴承承载区的中央平面上,沿径向钻有8个直径为1mm 的小孔。
各孔间隔为22.50,每个小孔分别联接一个压力表。
在承载区内的径向压力可通过相应的压力表直接读出。
将轴径直径(d=60mm )按比例绘在纸上,将1~8个压力表读数按比例相应标出。
(建议压力以1cm 代表5kgf/cm 2)将压力向量连成一条光滑曲线,即得到轴承中央剖面油膜压力分布曲线)。
同理,读出第4和第8个压力表示数,由于轴向两端端泄影响,两端压力为零。
光滑连结0‘,8’,4‘,8’和0‘各点,即得到轴向油膜压力分布曲线。
2、摩擦系数的测量图1 轴承实验台结构图1、操纵面板2、电机3、三角带4、轴向油压传感器接头5、外加载荷传感器6、螺旋加载杆7、摩擦力传感器测力装置8、径向油压传感器(8只)9、传感器支撑板 10、主轴 11、主轴瓦 12、主轴箱径向滑动轴承的摩擦系数f 随轴承的特性系数λ(λ=ηn/p )值的改变而改变。
在边界摩擦时,f 随λ值的增大而变化很小,进入混合摩擦后,λ值的改变引起f 急剧变化,在刚形成液体摩擦时f 达到最小值,此后,随λ值的增大油膜厚度亦随之增大,因而f 亦有所增大。
摩擦系数f 之值可通过测量轴承的摩擦力矩而得到。
轴转动时,轴对轴瓦产生周向摩擦力F ,其摩擦力矩为Fd2,它能使空套在轴上的轴瓦随轴转动,由于在轴瓦的外表面上固定一个测力杆,测力杆一端与轴瓦连接,另一端与弹簧片接触。
《机械设计实验》滑动轴承综合实验

四.实验步骤(5)
将轴承载荷 调至
0.5±0.05KN
四.实验步骤(6)
四.实验步骤(6)
测量间隔时间 至少3分钟
四.实验步骤(7)
四.实验步骤(7)
按翻பைடு நூலகம்按钮 记录油温值
四.实验步骤(7)
四.实验步骤(7)
记录结束 油温值
四.实验步骤(7)
测量间隔时间 至少2分钟
四.实验步骤(8)
F △
o1 D od
F
o1 o
hmin
F
a
o1 o
e
滑动轴承综合测试│二.实验原理
2.1.实验设备简介
滑动轴承综合测试│二.实验原理
2.2.实验设备简介
滑动轴承综合测试│三.实验要求
滑动轴承综合测试│四.实验步骤
1 开启实验台 2 打开测试用计算机
3 打开测试软件
4 将主轴转速调至330~335rpm 5 将外载荷调至0.50±0.05KN
滑动轴承综合测试
1. 实验目的 2. 实验原理 3. 实验要求 4 . 实验步骤 5. 实验守则 6. 反馈建议 7. 交流分享
滑动轴承综合测试│一.实验目的
一.实验目的: 1.测定和绘制滑动轴承周向即圆周方向油膜压力曲线与轴向油 膜压力曲线,计算轴承的承载能力; 2.观察、掌握载荷和转速改变时油膜压力的变化规律; 3.掌握滑动轴承的摩擦系数的测量方法,并绘制摩擦特性曲线 (即 f 曲线); 4.掌握液体动压轴承实验台的结构原理及测试方法。
1.载荷归零
逆时针旋转 螺旋机构卸载
2.转速归零
调节调速旋 钮转速归零
3.关闭电源
手动关闭实 验台电源
4.关闭计算机 操作鼠标或 键盘关机
动压滑动轴承实验指导书

动压滑动轴承实验指导书一、实验学时本实验2学时。
二、实验目的1. 观察油膜的形成与破裂现象、分析影响动压滑动轴承油膜承载能力的主要因素;2. 测量轴承周向及轴向的油膜压力、绘制其油膜压力分布曲线;3. 测定轴承的摩擦力、绘制轴承特性(λ−f )曲线;4. 掌握动压滑动轴承试验机的工作原理及其参数测试方法。
(1) 油膜压力(周向和轴向)的测量; (2) 转速的测量;(3) 摩擦力及摩擦系数的测量;三、实验机的构造及参数测试原理直流电机 2-V 形带 3-箱体 4-压力传感器 5-轴瓦 6-轴7-加载螺杆8-测力杆 9-测力传感器 10-载荷传感器 11-操作面板 图1 1.传动装置直流电机1通过V 带2驱动轴6旋转。
轴6由两个滚动轴承支承在箱体3上,其转速由面板11上的电位器进行无级调速。
本实验机的转速范围3~375转/分,转速由数码管显示。
2.加载方式由加载螺杆7和载荷传感器10组成加载装置,转动螺杆7可改变外加载荷的大小。
载荷传感器的信号经放大和A/D 转换后由数码管显示其载荷数值。
加载范围0~80㎏,不允许超过100㎏。
3. 油膜压力的测量在轴瓦5中间截面120°的承载区内(见图2左图)钻有七个均布的小孔,分别与七只压力传感器4接通,用来测量径向油膜压力。
距正中小孔的B/4轴承有效长度处,另钻一个小孔连接第八只压力传感器,用来测量轴向压力。
图2压力传感器的信号经放大、A/D 转换分别由数码管显示轴承径向油膜压力和周向油膜压力。
4. 摩擦系数的测量在轴瓦外圆的后端装有测力杆8(见图1),测力杆紧靠测力传感器9,轴旋转后,轴承间的摩擦力矩应由力臂作用于测力传感器所产生的摆动力矩相平衡。
即302F 2M L Fc D L Fc L F D F C M ⋅=⋅=⋅=⋅故 摩擦系数(3)式中:F — 轴承外载荷 (N) F=外加载荷 + 轴承自重=750 N 30FL Fc F f ⋅==F M L -力臂长度 (mm ) F M — 轴承的摩擦力 (N) F C — 测力传感器读数四、实验数据处理及绘制有关曲线为消除载荷对机械系统变形引起测量的误差,通常在载荷不变的情况下,分级改变转速,测量各级转速下有关参数,然后进行计算处理和绘制有关曲线。
滑动轴承的摩擦特性曲线和油膜压力分布

验证性实验指导书实验名称:滑动轴承的摩擦特性曲线和油膜压力分布实验简介:液体动压润滑径向滑动轴承的工作原理是通过轴颈旋转将润滑油带入轴承摩擦表面,因轴颈与轴承具有径向间隙,从而在轴与轴瓦的配合面之间产生楔形间隙,当轴回转时,会带动附在轴上的油层,由于油中分子之间存在附着力(粘度),这一油层也会带来邻近的油层,于是当轴达到足够的回转速度时油就被挤入楔形间隙里。
通过本实验对滑动轴承的摩擦特性及油膜压力分布情况进行验证,进一步巩固所学知识,同时拓宽学生的知识面。
适用课程:机械设计实验目的:A绘出周向和轴向油膜压力分布曲线,以验证其理论分布规律;B绘出轴承摩擦特性曲线,了解在液体润滑状态下摩擦系数与转速、压力之间的关系;C学习测量方法和掌握实验技能。
面向专业:机械类实验项目性质:验证性(课内必做)计划学时: 2学时实验分组:3人/组《机械设计》课程实验实验三滑动轴承的摩擦特性曲线和油膜压力分布液体动压润滑径向滑动轴承的工作原理是通过轴颈旋转将润滑油带入轴承摩擦表面,因轴颈与轴承具有径向间隙,从而在轴与轴瓦的配合面之间产生楔形间隙,当轴回转时,会带动附在轴上的油层,由于油中分子之间存在附着力(粘度),这一油层也会带来邻近的油层,于是当轴达到足够的回转速度时油就被挤入楔形间隙里。
由于通过间隙各径向截面的油量不变(流体连续条件),而间隙的界面逐渐减小,因此在油层中必然产生液体动压力,它总是力图楔开配合面,当油层中压力的大小能够平衡外载荷时,轴就好像浮动一样,这时在轴与轴瓦之间形成了稳定的油层,轴的中心相对轴瓦中心有一个偏距。
液体动压滑动油膜的形成过程及油膜压力分布形状如图3-1所示。
摩擦系数f是设计动压滑动轴承的重要参数之一,它的大小与润滑油粘度η(Pa•S)、轴的转速n(r/min)和轴承压力P(MPa)有关,通常令:λ=η•n/P称λ为轴承特性数。
观察滑动轴承形成液体动压润滑的过程,摩擦系数f随轴承特性数λ的变化如图3-2所示。
液体动压滑动轴承实验报告

液体动压滑动轴承实验报告液体动压滑动轴承实验报告引言液体动压滑动轴承是一种常见的摩擦副,广泛应用于工业领域。
本实验旨在通过实际操作和数据分析,探究液体动压滑动轴承的工作原理和性能特点。
实验目的1. 了解液体动压滑动轴承的结构和工作原理。
2. 探究液体动压滑动轴承的摩擦特性和承载能力。
3. 分析液体动压滑动轴承的性能优势和应用范围。
实验装置和方法实验装置包括液体动压滑动轴承、电机、压力传感器、转速传感器和数据采集系统。
实验步骤如下:1. 将液体动压滑动轴承装配在电机轴上。
2. 连接压力传感器和转速传感器,并将其与数据采集系统连接。
3. 调整电机转速,记录不同转速下的轴承压力和摩擦力。
4. 根据实验数据,分析轴承的摩擦特性和承载能力。
实验结果与分析通过实验记录的数据,我们可以得到不同转速下的轴承压力和摩擦力。
根据数据分析,我们可以得出以下结论:1. 随着转速的增加,轴承压力逐渐增大。
这是因为液体动压滑动轴承的工作原理是通过液体的动压效应来支撑轴承负荷,转速增加会导致液体的动压效应增强,从而增大轴承压力。
2. 随着转速的增加,轴承摩擦力逐渐减小。
这是因为液体动压滑动轴承的摩擦力主要来自于液体的黏滞阻力,转速增加会导致液体黏滞阻力减小,从而减小轴承摩擦力。
实验结论根据实验结果和分析,我们可以得出以下结论:1. 液体动压滑动轴承具有较好的承载能力。
通过增加转速,可以增大轴承的承载能力,适用于高速旋转设备。
2. 液体动压滑动轴承具有较低的摩擦力。
由于液体的黏滞阻力较小,轴承运行时的摩擦损失较小,有利于提高设备的效率和使用寿命。
3. 液体动压滑动轴承适用于高温和高速环境。
由于液体动压轴承不需要润滑油脂,可以在高温和高速环境下稳定工作,适用于一些特殊工况。
实验总结通过本实验,我们深入了解了液体动压滑动轴承的工作原理和性能特点。
液体动压滑动轴承具有较好的承载能力和较低的摩擦力,适用于高速旋转设备和高温环境。
然而,在实际应用中,还需要考虑到成本、维护和安装等因素,综合评估选择最适合的轴承类型。
- 1、下载文档前请自行甄别文档内容的完整性,平台不提供额外的编辑、内容补充、找答案等附加服务。
- 2、"仅部分预览"的文档,不可在线预览部分如存在完整性等问题,可反馈申请退款(可完整预览的文档不适用该条件!)。
- 3、如文档侵犯您的权益,请联系客服反馈,我们会尽快为您处理(人工客服工作时间:9:00-18:30)。
实验三动压滑动轴承实验
一、实验目的
1.验证动压滑动轴承油膜压力分布规律,了解影响油膜压力分布规律的因素,并根据油膜压力分布曲线确定端泄影响系数K b;
2.测定动压滑动轴承的摩擦特征曲线,并考察影响摩擦系数的因素。
二、实验设备及仪器
1.HZS-1型动压滑动轴承试验台
图1 HZS-1型动压滑动轴承实验台
图1为试验台总体布置,图中件号1为试验的轴承箱,通过联轴器与变速箱7相联,6为液压箱,装于底座9的内部,12为调速电动机,通过三角带与变速箱输入轴相联,8为调速电机控制旋钮,5为加载油腔压力表,由減压阀4控制油腔压力,2为轴承供油压力表,由减压阀控制其压力,油泵电机开关为10,主电机开关为11,试验台的总开关在其正面下方。
图2为试验轴承箱,件号31为主轴,由一对D级滚动轴承支承,32为试验轴承,空套在主轴上,轴承内径d=60mm,有效宽度=60mm。
在轴承中间横剖面上,沿周向开7个测压孔,在120°范围内的均匀分布,测压表21~27通过管路分别与测压孔相联。
距轴承中间剖面L/4(15mm)处,轴承上端有一个测压孔,表头28与其相联,件号33为加载盖板,固定在箱体上,加载油腔在水平面上的投影面积为60cm2在轴承外圆左侧装有测杆35,环34装在测杆上以供测量摩擦力矩用,环34与轴承中心的距离为150mm,轴承外圆上装有两个平衡锤36,用以在轴承安装前做静平衡。
图2 实验轴承箱
箱体左侧装有一个重锤式拉力计如图3所示,测量摩擦力矩时,将拉力计上的吊钩与环34联接,即可测得摩擦力矩。
测杆通过环34作用在拉力计上的力F,由重锤予以平衡,其
数值可由
α
sin
1
R
WL
F=
求得。
式中R为圆盘半径,W为重锤之重量,L1为重锤重心到轴
心之距离,α为圆盘之转角,圆盘转角α通过齿轮放大,可使表头指针转角放大10倍,表头刻度即为F的实际值,单位为克。
JZT型调速电动机的可靠调速范围为120~1200转/分,为了扩大调速范围,试验台传动系统中有一个两级变速箱,当手柄向右倾斜,主轴与电机转速相同;当手柄向右倾斜,主轴为电机转速的1/6。
因此主轴的可靠调速范围为20~1200转/分。
图3 重锤式拉力计工作原理图
2.测速仪表及温度计
三、实验步骤
1.
测定动压滑动轴承的油膜压力分布,确定轴承端泄影响系数K b
⑴测试方法:开启油泵,调节溢流阀及减压手柄,使加载油腔压力及及轴承供油压力均在1Kgf/ cm2以下;将变速手柄放在低速档上;调节控制器旋钮,使转速指针在最低速位置;将轴承左侧的测杆用卡板锁住;启动主电机,然后调节控制器旋钮,使指针读数在100~200mim-1,再将变速手柄旋到高速档,使主轴转速达到1000 mim-1,调节溢流阀,将加载油压调到P0=4kgf/ cm2,此时轴承载荷W=P0×60+8kgf(轴承自重为8kgf),运转几分钟,待各压力表指针稳定后,自左至右依次记录七个周向压力表及轴向压力表的读数;与此同时用温度计测量出口油温。
⑵做周向油膜压力分布曲线
按照图4所示做一圆,取其直径为轴承内径d,先在圆周上定出七个压力表所接油孔位置,通过这些点沿半径延长方向以一定比例尺量出所测量的相应压力表读数值,用曲线板将各压力向量的末端联成一光滑曲线,这就是轴承中间剖面的周向油膜压力分布曲线。
图4 周向油膜压力分布曲线图5
轴向油膜压力分布曲线
由油膜周向压力分布曲线,可求得轴承中间剖面上的平均压强。
如图4所示,将圆周上1、2、3…7各点投影到另一水平直线上,在相应点的垂线上画出对应的压力值,将其端点1′、
2′、3′…7′联成一光滑曲线,求出曲线所围的面积,然后取P m ,使其所围矩形面积与所求得的面积相等,此P m 值即为轴承中间剖面上的平均压强。
⑶做油膜轴向压力分布曲线
做一水平线取其长度为轴承有效宽度(B=60mm )。
在中点垂线上按一定比例画出该点的压力P 4,端点为4′在距中点两边各距B/4(即15mm )处,沿垂线方向画出压力P 8,轴承水平轴线两端的压力均为0,将0,8′、4′、8′、0五点联成一光滑曲线,此曲线即为轴承油膜轴向压力分布曲线如图5,用前述方法可求出其平均压强Pa 。
⑷确定端泄时油膜轴向压力分布的影响系数K b
由周向压力分布曲线求K b1值;
K b1=Bd P W
m
式中:W —轴承承载量,可按实际载荷计(kgf )
P m — 轴承中间剖面上的平均压强(kgf/m 2)
B — 轴承有效宽度(cm )
d — 轴承内径(cm )
由轴向压力分布曲线求K b2值:K b2= 4
P P a 式中:Pa — 前面所求得轴向平均压强(kgf/m 2)
P 4 — 轴承中间剖面中点的油膜压强(kgf/m 2)
比较K b1和K b2看其是否相符?是否符合抛物线分布规律。
2. 轴承摩擦特性曲线的测定
将轴承加载至Pa=4 kgf/m 2(即W=248Kgf ),再将主轴调至1000 mim -1,然后转动拉力
计表盘,使指针归零,解脱测杆卡板,把吊钩挂在测力杆的吊环上。
待指针稳定后,记录其数值。
然后依次将主轴转速到800,600,200,80,60,40,10,5,2,记录各转速时的拉
力计读数。
改变轴承载荷,使P 0=2 kgf/m 2,取W =128Kgf ,重复记录各转速时拉力计读数。
然后列表计算各转速时之摩擦系数f ,轴承特征值λ,计算公式如下:
摩擦系数
W F Wd FL d W L F f 522==⨯⨯=
式中:F — 拉力计读数(克)
W — 轴承载荷(克)
L — 测杆之力臂(l=150mm )
d — 轴承内径(d=60mm )
轴承特征值
P n ⨯=
ηλ
式中:η— 润滑油的动力粘度(Pa •s ),根据所测出口油温,及室温求出平均温度t m ,再从(机械设计)教材67页的粘度和温度曲线,查出20#或10#
机械油在轴承工作区的运动粘度,然后再转换成动力粘度;
n — 主轴转速(mim -1);
P — 主轴之平均压强(N/mm 2或MPa ) P=B d W
⨯
四、 实验注意事项
1. 启动主电机时,必须先开动油泵,然后再由低速启动电机,逐渐加大转速,不可把变速手柄放在高速档(右侧)启动,以免动力矩过大。
2. 为了保持拉力计的精度,只有在测轴承摩擦力矩时,才允许解脱测力杆卡板。
3. 在混合摩擦区工作时间尽量短,以避免轴承磨损。
4. 轴承供油压力必须保持在1kgf/m 2左右,以便消除静压对实验数据的影响,同时保护
硅胶进油管不致损坏。
5. 测出口油时务必注意水银玻璃温度计不可碰撞金属物体。
微机对滑动轴承实验数据的采集和处理系统
——计算机辅助滑动轴承实验
一、 系统组成
概图:
1. 实验台:现有滑动轴承实验台HZS-1型。
2. 传感器:通过三通接口与原实验台的压力表相并联,其输出电压与油压成正比;
1kg 压力≈10mv 左右
3. 放大器:8路单级自补偿运算放大器,芯片为7650。
4. A/D 转换:12位、16通道,将放大器输出的模拟电压信号转化为数字信号。
5. 计算机:PC ,386机以上。
6. 输出结果:屏幕显示并可接打印机,打印出实验结果报告。
二、 软件系统组成
1. 程序流程框图:(见图6)
2. 软件简要说明:
所有文件全部复制在两张盘内,即1号盘或2号盘。
1号盘内装有全部的运行文件及打印图形驱动程序,2号盘内装有一个BASICA ·EXE 文件。
软件将在213E 中文操作系统的前提上自动执行。
三、 系统的操作方法
1.启动实验台,将主轴转速调至800~1000rpm,压力调节到2~4kg,测量出口温度值。
将计算机测量系统联接好。
2.检查A/D板:
①将自检程序盘放入A驱动器,在“A>”下运行BASIC。
②运行ADDA13文件,进入菜单项。
③选“2”即可观察通道的工作状态,即:当输入悬空时,显示模拟量为9V,数字量为4095。
3.油膜压力的测量
①打开放大器电源,将1号盘放入A驱动器中,2号盘放入B 驱动器中。
②在“C>”下,启动213E,键入AUTO并回车,进入213E下的中文操作系统。
③由“C>”转入“A>”下,键入批处理文件名ZCSY,程序会自动执行。
用户只需根据自己的需要进行菜单选择并在屏幕提示下进行操作,键入压力测量对应的标示字母。
计算机将对压力进行数据采集(8个压力值)。
造表并计算,绘制周向及轴向压力分布曲线。
④执行完数据采集后,将数据处理的结果以数据文件的形式存入磁盘。
4.摩擦特性曲线的计算
在主菜单选择提示下,选择摩擦特性曲线计算对应标示字母。
由键盘键入测量摩擦特性实验数据,由计算机计算出实验结果,并显示f— 图形,并回到主菜单。
5.当需要实验结果报告时,调主菜单中“打印输出”,即可连续打印任意多份实验报告。
四、实验注意事项
1.实验开始或过程中请勿随意动插在计算机主机箱里的A/D转换板,以免损坏其中的某些芯片。
2.实验前应测试并消除计算机中的病毒。
图6 程序流程框图。