机械手抓取与检测板件系统的改进
基于液压传动的机械手爪设计与改进

基于液压传动的机械手爪设计与改进引言机械手爪是现代制造业中常见的一种设备,它广泛应用于装配线、仓储物流等领域。
机械手爪的设计与改进对于提高生产效率、优化生产流程具有重要意义。
本文将介绍基于液压传动的机械手爪的设计原理、存在的问题以及改进方向。
设计原理基于液压传动的机械手爪是利用液压系统的动力通过控制器对机械手爪的动作进行控制的一种装置。
其基本原理是利用液体介质传递力量,通过控制传动系统中的液压缸对机械爪的打开、闭合动作进行调控。
具体来说,液压传动系统由主控制器、液压泵、控制阀和液压缸组成。
存在的问题然而,在实际应用中,基于液压传动的机械手爪存在一些问题需要解决。
首先,传统液压系统的响应速度较慢,无法满足高速作业的需求。
其次,液压系统的维护成本较高,需要定期更换液压油和维修液压元件。
此外,传统液压系统的电气控制较为复杂,需要专业技术人员进行维护和操作。
改进方向一:提高响应速度为解决传统液压系统响应速度慢的问题,可以采用先进的电液比例控制技术。
通过引入电液比例阀,将电气信号转化为液压信号,实现对液压系统的精确控制。
电液比例控制技术具有响应速度快、控制精度高的优势,可以大幅提高机械手爪的动作速度。
改进方向二:降低维护成本为降低维护成本,可以通过采用新型液压元件和优质液压油来延长液压系统的使用寿命。
新型液压元件具有更好的耐磨性和密封性能,能够减少泄漏和故障的发生。
同时,优质液压油具有良好的抗氧化性和抗污染性,能够有效保护液压元件不受外界环境的影响。
改进方向三:简化电气控制为简化电气控制,可以采用先进的智能控制器。
智能控制器集成了传感器、执行机构和控制算法,能够实现对机械手爪的智能化控制。
通过智能控制器,操作人员可以方便地进行参数设置和调整,降低了对专业技术人员的依赖,同时提高了机械手爪的灵活性和自动化水平。
结论基于液压传动的机械手爪是一种应用广泛的装备,设计与改进对于提高生产效率具有重要意义。
通过引入先进的电液比例控制技术、采用新型液压元件和优质液压油,以及应用智能控制器,可以解决传统液压系统存在的问题,提升机械手爪的性能指标,进一步推动工业自动化的发展。
机器人抓握系统的机械手段优化设计
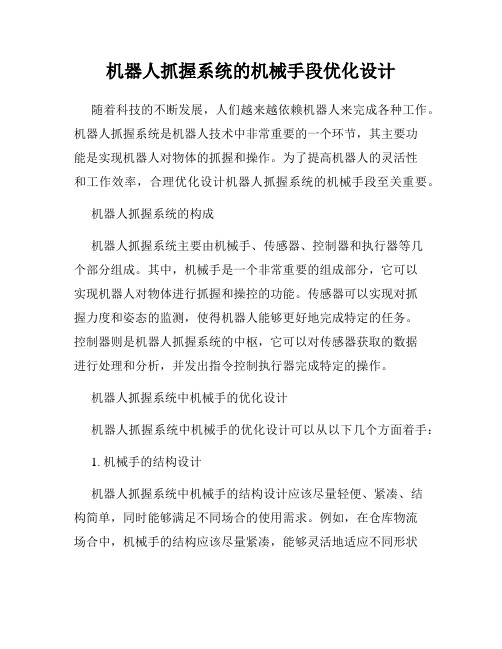
机器人抓握系统的机械手段优化设计随着科技的不断发展,人们越来越依赖机器人来完成各种工作。
机器人抓握系统是机器人技术中非常重要的一个环节,其主要功能是实现机器人对物体的抓握和操作。
为了提高机器人的灵活性和工作效率,合理优化设计机器人抓握系统的机械手段至关重要。
机器人抓握系统的构成机器人抓握系统主要由机械手、传感器、控制器和执行器等几个部分组成。
其中,机械手是一个非常重要的组成部分,它可以实现机器人对物体进行抓握和操控的功能。
传感器可以实现对抓握力度和姿态的监测,使得机器人能够更好地完成特定的任务。
控制器则是机器人抓握系统的中枢,它可以对传感器获取的数据进行处理和分析,并发出指令控制执行器完成特定的操作。
机器人抓握系统中机械手的优化设计机器人抓握系统中机械手的优化设计可以从以下几个方面着手:1. 机械手的结构设计机器人抓握系统中机械手的结构设计应该尽量轻便、紧凑、结构简单,同时能够满足不同场合的使用需求。
例如,在仓库物流场合中,机械手的结构应该尽量紧凑,能够灵活地适应不同形状的货物切换操作。
而在工业制造行业中,机械手的结构应该更加牢固、坚定,能够承受重物的抓握和操控。
2. 机械手的动力系统设计在机械手的动力系统设计中,需要注意机械手的驱动方式选择、驱动力的大小和平衡性的问题。
在机械手驱动方式选择方面,可以采用气动或液动驱动方式,这种方式下优点是驱动力相对稳定,但缺点是驱动力难以精细控制。
而在驱动力的大小和平衡性的问题上,一般要根据机械手的应用场合进行调整,以保证开发成果满足工业生产的实际需求。
3. 机械手的抓握器设计机器人抓握系统中机械手抓握器的设计直接关系到机械手在真正使用中的性能表现。
在设计抓握器时,应聚焦力度的控制和物体的稳定保持。
例如,在进行小零件装配的操作时,需要选用相对柔软的材质,以保证对被抓握的小零件能够轻松地“握住”,而在对较大物体的抓握时,需要选用结构更加坚固、牢靠并且持续维持紧密稳固掌握的抓握器。
机器人抓取力控制技术的优化与实现

机器人抓取力控制技术的优化与实现随着科技的不断发展,机器人在各个领域的应用越来越广泛。
而机器人的抓取力控制技术是其中一个重要的方面。
在许多工业生产中,机器人需要具备一定的抓取力来完成各种任务,如装配、搬运等。
因此,优化和实现机器人的抓取力控制技术对提高生产效率和质量具有重要意义。
首先,机器人抓取力控制技术的优化需要考虑到机器人与物体之间的接触力。
接触力是机器人抓取物体时产生的力量,它直接影响到机器人是否能够稳定地抓取物体。
为了实现精确的抓取力控制,需要对接触力进行准确的感知和测量。
目前,常用的接触力传感器有压力传感器、力传感器等。
通过这些传感器,机器人可以实时感知到与物体的接触力,并根据设定的控制算法进行力量的调整。
其次,机器人抓取力控制技术的优化还需要考虑到物体的表面特性。
不同的物体表面具有不同的摩擦系数和粘附性,这直接影响到机器人的抓取力控制。
例如,对于光滑的表面,机器人需要增加抓取力以防止物体滑落;而对于粗糙的表面,机器人则需要减小抓取力以避免损坏物体。
因此,机器人抓取力控制技术需要根据物体的表面特性进行优化,以实现更精确的抓取力控制。
此外,机器人抓取力控制技术的优化还需要考虑到机器人的力控制算法。
力控制算法是机器人实现抓取力控制的核心。
目前,常用的力控制算法有PID控制算法、模糊控制算法等。
这些算法可以根据实时的力量反馈信息,调整机器人的抓取力,以实现精确的力量控制。
同时,还可以结合机器学习算法,通过对大量的数据进行训练,提高机器人的抓取力控制能力。
最后,机器人抓取力控制技术的实现需要考虑到机器人的硬件设备。
机器人的抓取力控制需要依赖于机器人的执行器和传感器等硬件设备。
因此,优化和实现机器人的抓取力控制技术还需要考虑到硬件设备的性能和可靠性。
例如,机器人的执行器需要具备足够的力量输出和精确的位置控制能力;传感器需要具备高精度和高灵敏度,以实现准确的力量感知和测量。
总之,机器人抓取力控制技术的优化与实现是一个复杂而重要的课题。
机器人抓取算法的研究与改进

机器人抓取算法的研究与改进近年来,随着机器人技术的迅猛发展,机器人在各个领域展现出了广阔的应用前景。
而机器人的抓取功能是其中至关重要的一部分,它决定了机器人能否准确、高效地完成任务。
因此,机器人抓取算法的研究与改进显得尤为重要。
一、机器人抓取算法的研究进展机器人抓取算法的研究始于上世纪90年代,从最初的简单粗暴到现在的智能化、灵活性较高的抓取方式的突破。
最早的机器人抓取算法主要借鉴了传统工业机械抓取方法,如夹爪、磁铁等。
这些方法虽然能够完成基本的抓取任务,但缺乏智能化和自适应性。
随着计算机视觉技术、深度学习等技术的兴起,机器人抓取算法逐渐开始向智能化方向发展。
计算机视觉技术的应用可以使机器人通过图像识别目标物体的位置和形状,从而更加准确地抓取物体。
深度学习技术的引入,则使机器人能够通过学习大量数据,提高抓取物体的成功率和效果。
二、机器人抓取算法存在的问题尽管机器人抓取算法取得了一定的进展,但在实际应用中仍然存在一些问题。
首先,机器人抓取算法对物体的识别和姿态估计要求较高。
在复杂的环境中,物体可能存在遮挡、光照变化等问题,这会造成机器人难以准确地识别物体的位置和形状,从而导致抓取失败。
其次,机器人抓取算法在处理不规则、变形、易碎等物体时仍存在挑战。
这些物体的形状和结构复杂,传统的抓取算法很难找到合适的抓取点和抓取策略,导致抓取失败或者破坏物体。
另外,机器人抓取算法还存在抓取力控制不准确、精度不高等问题。
在某些需要精细操作的任务中,机器人的抓取力可能过大或过小,无法做到精准控制,这将影响到机器人的抓取效果和任务完成率。
三、机器人抓取算法的改进方向为了解决上述问题,未来机器人抓取算法可以从以下几个方面进行改进:1. 引入更先进的计算机视觉技术。
机器人抓取算法可以借鉴目标检测、目标跟踪等计算机视觉技术,提高对物体的识别和姿态估计准确度,进而改善抓取效果。
2. 结合深度学习和机器人学习。
利用深度学习技术,机器人可以学习大量的样本数据,提高抓取任务的成功率。
基于计算机视觉的智能机器人抓取系统设计与优化
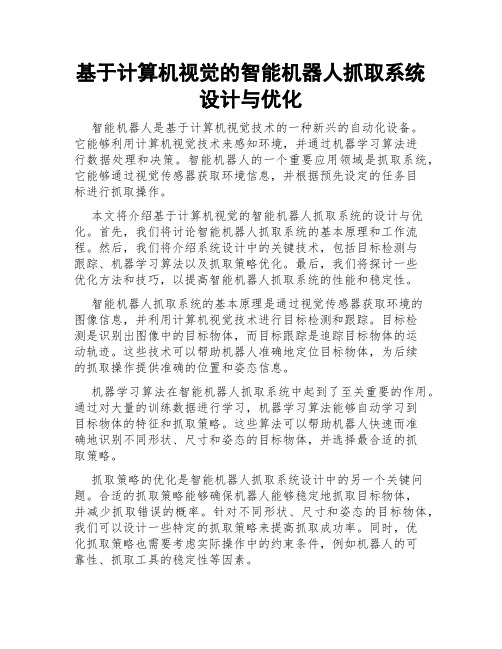
基于计算机视觉的智能机器人抓取系统设计与优化智能机器人是基于计算机视觉技术的一种新兴的自动化设备。
它能够利用计算机视觉技术来感知环境,并通过机器学习算法进行数据处理和决策。
智能机器人的一个重要应用领域是抓取系统,它能够通过视觉传感器获取环境信息,并根据预先设定的任务目标进行抓取操作。
本文将介绍基于计算机视觉的智能机器人抓取系统的设计与优化。
首先,我们将讨论智能机器人抓取系统的基本原理和工作流程。
然后,我们将介绍系统设计中的关键技术,包括目标检测与跟踪、机器学习算法以及抓取策略优化。
最后,我们将探讨一些优化方法和技巧,以提高智能机器人抓取系统的性能和稳定性。
智能机器人抓取系统的基本原理是通过视觉传感器获取环境的图像信息,并利用计算机视觉技术进行目标检测和跟踪。
目标检测是识别出图像中的目标物体,而目标跟踪是追踪目标物体的运动轨迹。
这些技术可以帮助机器人准确地定位目标物体,为后续的抓取操作提供准确的位置和姿态信息。
机器学习算法在智能机器人抓取系统中起到了至关重要的作用。
通过对大量的训练数据进行学习,机器学习算法能够自动学习到目标物体的特征和抓取策略。
这些算法可以帮助机器人快速而准确地识别不同形状、尺寸和姿态的目标物体,并选择最合适的抓取策略。
抓取策略的优化是智能机器人抓取系统设计中的另一个关键问题。
合适的抓取策略能够确保机器人能够稳定地抓取目标物体,并减少抓取错误的概率。
针对不同形状、尺寸和姿态的目标物体,我们可以设计一些特定的抓取策略来提高抓取成功率。
同时,优化抓取策略也需要考虑实际操作中的约束条件,例如机器人的可靠性、抓取工具的稳定性等因素。
为了进一步提高智能机器人抓取系统的性能和稳定性,我们可以采取一些优化方法和技巧。
例如,使用多传感器融合技术可以提高目标检测和跟踪的准确性;使用深度学习算法可以提高机器学习算法的学习能力和泛化能力;使用物体形状建模技术可以增加抓取策略的灵活性和鲁棒性。
总之,基于计算机视觉的智能机器人抓取系统的设计与优化是一个复杂而关键的问题。
机械手与目标物交互控制系统的设计与优化

机械手与目标物交互控制系统的设计与优化1.引言机械手是一种能够模拟人类手臂运动的自动化装置,广泛应用于工业生产线上的物料搬运、装配等任务中。
机械手在与目标物交互时,需要一个精确可靠的控制系统来实现精准的定位和力量控制。
本文将探讨机械手与目标物交互控制系统的设计与优化。
2.机械手与目标物交互控制系统的设计要求在机械手与目标物交互过程中,需要考虑以下设计要求:2.1.定位精度:机械手需要能够准确地定位到目标物的位置,以便进行下一步的操作。
定位精度是决定机械手性能的重要指标之一。
2.2.力量控制:机械手在抓取目标物时需要控制合适的力量,以免损坏目标物或无法抓取。
力量控制是保证机械手与目标物交互的关键。
2.3.运动平滑:机械手在与目标物交互时需要保持稳定、平滑的运动,避免荡秋千、颤抖等不稳定现象。
运动平滑是实现精确控制的前提。
3.机械手与目标物交互控制系统的优化方法3.1.传感器选择与安装在机械手与目标物交互控制系统中,传感器的选择与安装对控制效果有重要影响。
首先需要选择合适的传感器来获取目标物的位置信息和力量信息。
例如,光电传感器可用于检测目标物的位置,而扭矩传感器可用于测量抓取过程中的力量。
传感器的安装位置也需要合理选择,以保证测量的准确性和可靠性。
对于目标物位置的测量,可以将传感器安装在机械手臂的末端,以近似人类手的位置。
对于力量的控制,传感器可以安装在机械手爪部分或与目标物接触的部位。
3.2.控制算法优化控制算法是机械手与目标物交互控制系统的核心。
优化控制算法可以提高机械手的定位精度、力量控制和运动平滑性。
常用的优化控制算法包括PID控制算法、模糊控制算法和神经网络控制算法等。
在实际应用中,可以根据实际情况选择合适的算法,并进行参数调整和优化,以达到最佳的交互效果。
3.3.力反馈控制力反馈控制是机械手与目标物交互过程中重要的一环。
通过力反馈控制,机械手可以感知到与目标物的接触力,并根据接触力的大小和方向进行相应的控制。
机器人抓取和操作技术研究与设计

机器人抓取和操作技术研究与设计随着科技的不断发展,机器人技术正日益成为现实生活中的重要组成部分。
机器人的抓取和操作技术是机器人技术领域的关键技术之一,其研究和设计对于实现机器人在各个领域的应用具有重要意义。
在本文中,我们将探讨机器人抓取和操作技术的研究进展,并提出一种设计方案。
一、机器人抓取技术的研究机器人的抓取技术是机器人实现物体抓取和操控的基础。
目前,机器人抓取技术主要分为物体检测、抓取策略和控制三个方面。
1. 物体检测物体检测是机器人实现精确抓取的关键技术之一。
目前,常用的物体检测方法包括图像识别、深度学习和传感器融合等。
图像识别是一种基于视觉的物体检测方法,通过图像处理和模式识别算法来实现物体的识别和定位。
深度学习则是一种基于神经网络的物体检测方法,通过训练模型来实现物体的检测和分类。
传感器融合则是将多种传感器的数据进行融合,以提高物体检测的准确性和鲁棒性。
2. 抓取策略抓取策略是机器人抓取技术的关键环节,用于确定机器人应该如何抓取目标物体。
目前,常用的抓取策略包括力控抓取和视觉伺服抓取。
力控抓取是通过力传感器来控制机器人的抓取力度和位置,以实现对物体的精确抓取。
视觉伺服抓取则是利用相机和图像处理算法来实现对物体的视觉控制,使机器人能够根据实时图像调整抓取位置和力度。
3. 控制控制是机器人抓取技术的最后一环,用于控制机器人执行抓取任务。
目前,常用的控制方法包括PID控制、运动规划和轨迹跟踪等。
PID控制是一种基于反馈的控制方法,通过不断调节机器人关节的位置和力度,以达到期望的抓取效果。
运动规划则是根据机器人的动力学模型和环境信息,设计出合理的运动路径,使机器人能够有序地完成抓取任务。
轨迹跟踪则是将运动规划得到的路径转化为机器人关节的控制指令,实现对机器人运动的控制。
二、机器人操作技术的研究机器人操作技术是机器人实现各种操作任务的关键技术之一。
机器人操作技术包括视觉操作、力控操作和自主操作三个方面。
机器人抓取力控制策略的优化与实现

机器人抓取力控制策略的优化与实现近年来,随着科技的不断进步,机器人技术在各个领域得到了广泛应用。
机器人的抓取力控制是机器人操作中一个非常重要的技术。
本文将探讨机器人抓取力控制策略的优化与实现。
一、机器人抓取力控制的意义机器人抓取力控制是指机器人在进行物体抓取时,能够根据物体的特性和需求,调整抓取力的大小和方式。
这对于机器人操作的成功与否至关重要。
如果抓取力过大,可能会导致物体损坏或者机器人本身受到损伤;而抓取力过小,则无法稳定地抓取物体。
因此,优化机器人抓取力控制策略具有重要的实际意义。
二、机器人抓取力控制策略的研究现状目前,机器人抓取力控制策略的研究主要分为两个方向:传感器反馈控制和模型预测控制。
传感器反馈控制是指机器人通过传感器获取物体的力信息,并根据这些信息进行力控制。
这种方法具有实时性强的特点,能够快速地调整抓取力的大小。
然而,由于传感器的精度和噪声等问题,传感器反馈控制存在一定的局限性。
模型预测控制是指机器人通过建立物体的力学模型,预测物体的力学行为,并根据这些预测结果进行力控制。
这种方法具有较高的精度和稳定性,但需要对物体的力学特性进行准确建模,且计算复杂度较高。
三、机器人抓取力控制策略的优化为了优化机器人抓取力控制策略,可以采用以下方法:1. 传感器融合:结合多种传感器,如力传感器、视觉传感器等,综合利用不同传感器的优势,提高力控制的准确性和稳定性。
2. 模型辨识:通过实验和数据分析,对物体的力学特性进行准确的辨识,建立更精确的力学模型,提高模型预测控制的精度。
3. 自适应控制:根据物体的特性和环境的变化,自适应地调整力控制策略,以适应不同情况下的抓取需求。
4. 强化学习:利用强化学习算法,通过与环境的交互,优化机器人的抓取力控制策略,使其能够在不断学习中不断提高。
四、机器人抓取力控制策略的实现机器人抓取力控制策略的实现需要结合硬件和软件的技术手段。
在硬件方面,需要选择合适的力传感器、执行器等设备,并进行合理的布局和连接。
- 1、下载文档前请自行甄别文档内容的完整性,平台不提供额外的编辑、内容补充、找答案等附加服务。
- 2、"仅部分预览"的文档,不可在线预览部分如存在完整性等问题,可反馈申请退款(可完整预览的文档不适用该条件!)。
- 3、如文档侵犯您的权益,请联系客服反馈,我们会尽快为您处理(人工客服工作时间:9:00-18:30)。
机械手抓取与检测板件系统的改进
阐述了在汽车制造冲压工艺中,当机械手为压力机自动化上下料时,对自动抓取和检测板件系统的一种技术改进,针对设备现状进行分析研究,基于现场综合需求对真空发生器和负压真空度检测进行调试实现相关功能。
通过本文介绍可以为气动技术类搬运设备的改进、维护保养等提供思路和帮助。
标签:机械手、抓取与检测板件、真空发生器、负压真空度
1前言
汽车制造冲压工艺是由压力机带动模具对板件进行冲压作业,常见模具设计决定每一板件从开始到成型一般要经过四到六次冲压,所以常见的生产线是由多台压力机以串联方式组成,板件按照工艺顺序依次经过各台压力机。
早期是靠人工在各台压力机之间上下料,后来随着工业机器人的普及和以GUDEL品牌机械手为代表的自动化设备出现,逐步取代了人工上下料,大大提升了安全保障和生产效率;
基于此,这些自动化上下料设备需要完成对板件的自动抓取和检测,抓取技术较常见的是用气动系统,此外还有电磁吸附技术等;检测技术较常见的有电磁开关接触板件来完成,或利用气动系统的负压真空度检测等。
本文主要以GUDEL 品牌单臂机械手为例,介绍关于抓取和检测系统基于现场综合需求的一种技术改进。
2改进前设计原理及缺陷
改进前抓取原理为:抓取工具称为端拾器,由铝合金杆和气管、吸盘等组成,由统一的电磁阀组和多个真空发生器分散在每一吸盘处形成真空以抓取板件;检测原理为:电磁开关置于端拾器上,随着端拾器吸放板件以接触和脱离板件的方式进行检测。
2.1抓取系统分析
机械手接近抓料点时吸气,吸附并检测到板件后搬运到放料点,放气后得到无板件信号返回原点,依次循环。
用PLC控制电磁阀组根据伯努利气动原理完成吸放气。
吸放功能要靠多组气路,比较复杂。
2.2检测系统分析
汽车板件有多种,如顶盖、发动机盖等,所以端拾器也对应多种,每生产完一种板件,更换模具同时还需要更换端拾器以生产下一种。
机械手本体有供端拾器拔插的公用底座,检测板件的电磁开关位于端拾器上,其信号线路跟随端拾器与底座间拔插,不可避免有过度接头。
在上下料过程中如该信号出现异常,机械
手会马上报警并停线。
2.3两套系统设计缺陷总结
1.分散式真空发生器逻辑复杂,数量多,结构易损,电气路需到末端,需随机械手旋转,配套件多。
主要有密封圈、接头、线束、拖链、固定板等,大端拾器吸盘多时尤为明显。
2.长期操作导致过度接头接触不良,故障率高,经常需要人工盯线以防止压坏设备或模具等,容易造成人员疲劳。
3抓取系统改进过程
硬件方面采用简捷逻辑,气源不经电磁阀组直接供给真空发生器进气口,出气口用一根气管到底,吸放功能都集成到该气管上。
末端连接吸盘用普通铝块即可,气路供所有吸盘共用。
电气接线方面根据吸放逻辑简化24V控制线路。
程序方面根据信号变化修改,吸件信号用功能块图取反,放件信号增加TOF指令等。
改进后抓取板件灵敏度提高,冲压工艺重复定位精度高,接触位置一般不发生变化,一次性调试成功可持续使用,并能及时获悉吸盘破损。
4检测系统改进过程
硬件方面拆除原检测系统,当吸盘接触到板件时真空度达到设置值时信号产生,相当于电磁开关接触并检测到有板件;当吸盘释放板件后真空度下降,相当于电磁开关脱离板件并检测到信号变化。
设置真空度检测值时需兼顾多个工艺点,不能过高或过低。
满足全部工艺点的条件主要有:1、工厂气压无大波动;2、负载无漏气;3、负压检测设置为0.5-0.6bar;4、迟滞设置为最小;5、气路无堵塞;6、其他。
综上所述,本改进删繁就简、安全实用,降低维护成本每年5万元左右,是基于现场综合需求技术改进比较成功的范例。
参考文献:
[1] 李新德.气动元件与系统[M].北京:中国电力出版社,2015.
[2] 王春生.冲压工艺设备的技术进步与发展[J].机械工人(热加工),2006.
作者簡介:
夏传江(1987~)男,山东临沂人;东北林业大学,自动化专业;上汽通用五
菱汽车股份有限公司青岛分公司制造科冲压设备工程师;研究方向:机电一体化。