挤出发泡工艺三个因素
挤出发泡原理
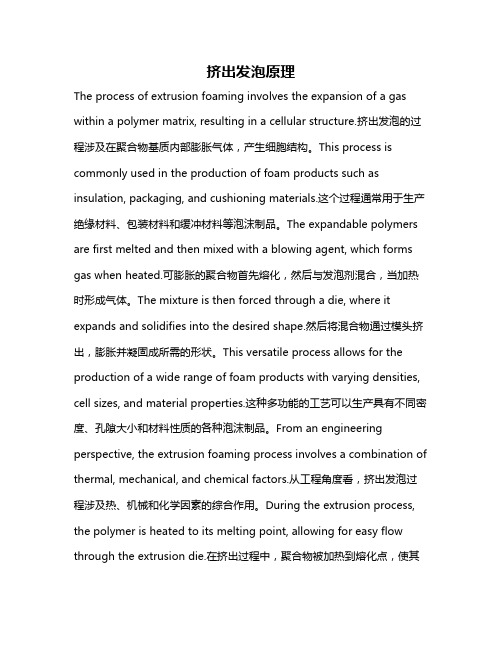
挤出发泡原理The process of extrusion foaming involves the expansion of a gas within a polymer matrix, resulting in a cellular structure.挤出发泡的过程涉及在聚合物基质内部膨胀气体,产生细胞结构。
This process is commonly used in the production of foam products such as insulation, packaging, and cushioning materials.这个过程通常用于生产绝缘材料、包装材料和缓冲材料等泡沫制品。
The expandable polymers are first melted and then mixed with a blowing agent, which forms gas when heated.可膨胀的聚合物首先熔化,然后与发泡剂混合,当加热时形成气体。
The mixture is then forced through a die, where it expands and solidifies into the desired shape.然后将混合物通过模头挤出,膨胀并凝固成所需的形状。
This versatile process allows for the production of a wide range of foam products with varying densities, cell sizes, and material properties.这种多功能的工艺可以生产具有不同密度、孔隙大小和材料性质的各种泡沫制品。
From an engineering perspective, the extrusion foaming process involves a combination of thermal, mechanical, and chemical factors.从工程角度看,挤出发泡过程涉及热、机械和化学因素的综合作用。
挤出压延法内衬层气泡原因分析及措施

挤出压延法内衬层气泡原因分析及措施前言我国庞大的汽车需求量带动了轮胎行业的快速增长。
其中子午胎的接地面积大,附着性能好,滚动阻力小,使用寿命长,散热性能好,可适应高温、高速行驶,大量应用于载重和乘用轮胎。
内衬层作为子午胎的重要组成部分,特别是无内胎子午胎,因为它的透气率小,有助于减少气体向胎体扩散,从而减少因气压扩散而引起的带束层脱层,保持气压的稳定。
这也直接关系到汽车行驶的安全和司乘人员的安全。
这就对内衬层生产设备提出了更高的要求,内衬层半制品挤出是轮胎制造过程中的重要工序之一,内衬层胶片挤出质量的好坏与轮胎质量息息相关。
当前冷喂料销钉挤出机+压延机的生产方法是国际国内比较先进的内衬层生产方式,但是挤出压延的半成品内衬层气泡会影响轮胎的气密性,轮胎硫化后容易出现气泡、鼓包、漏气等质量缺陷,因此解决冷喂料销钉挤出机挤出气泡是个很重要的课题。
原因分析对于内衬层半成品挤出压延过程中存在的主要问题——气泡问题。
我们从全面质量管理的4M1E五个影响产品质量的主要因素分析。
1、操作人员要熟悉挤出压延法内衬层生产设备,熟悉挤出工艺知识,培训到位,掌握操作方法。
2、设备方面要确保设备正常工作,满足生产工艺要求。
3、胶料方面要求确保材料成分、物理性能和化学性能满足要求。
4、生产工艺方面要确保温度设定、速度匹配、压力合理、操作规程满足工艺规范、产品作业标准明确,测量方法要标准、科学、正确。
5、生产环境的温度、湿度、照明和清洁条件满足要求。
考虑到现代轮胎生产企业厂房建设规范,员工培训到位,环境对气泡问题的影响很小,可以排除人员和环境方面的影响因素。
从以上全面质量管理分析可以看出,气泡产生的主要原因可能出现在机、料、法这三个因素。
例如:挤出机的吃料是否密实,挤出速度是否过快,胶料中的气体有没有及时排出;机头的流道是否合理,是否压力过低或者流道不均匀,导致气体没有及时排出;供胶不足;原材料含水量或者挥发物过多,挤出过程中容易出现气泡;胶料的可塑性低,温度过高导致小料分解;胶料储存时间过长,产生凝露;挤出温度设定是否合理等。
挤出成型PVC低发泡制品的技术1

挤出成型PVC低发泡制品的技术12007-12-15 11:251、前言挤出成型PVC发泡制品,在上个世纪60年代初国际上就已经有了应用,PVC发泡技术经过近40年的不断研究开发,在技术与应用这两方面都有了很大的发展,近几年来发展的更加迅速,而且它的重要性还在不断的提高,这是因为PVC发泡制品具有很多优异性能所决定的,特别是PVC低发泡制品它的综合性能非常突出,和普通不发泡PVC制品相比具有下列优点:(1)低导热性,即隔热保温效果好;(2)优异声波阻尼性,即有良好的隔音效果;(3)二次成型加工性能好,类似于木材,可锯、可钉、可刨、可钻,同时也可粘结;(4)高阻燃性,即防火性能好;(5)化学性能稳定,有优异的抗化学腐蚀性;(6)优异的耐候性,同时有防蛀、防水等性能;(7)利用PVC的发泡技术可有效地降低制品单位体积内树脂的含有量,从而降低制品的成本;(8)PVC低发泡制品对环境没有污染,并可再生利用,是绿色环保产品。
(国外专家实验证明,PVC对环境无害,欧洲PVC制品委员会本世纪初公布的一份研究报告显示,PVC 不易分解,在需要进行深埋处理的垃圾中掺有PVC制品不会对环境造成危害。
从而否定了长期以来认为PVC 会对环境造成污染的推测,这项研究是由瑞典国家环保局以及三所瑞典和德国的大学联合完成的。
)由于PVC低发泡制品有上述这些特点,而且这些特点和木材十分相似,因此PVC低发泡制品又称为合成木材,其综合物理性能要优于天然木材,已能与天然木材相抗衡。
我国PVC低发泡制品(有时也被称为PVC微发泡制品)在《全国塑胶工业"十五规划和2015规划" 》中已确定,在建筑用塑胶方面将大力推行以塑代木,鼓励研制和生产PVC低发泡型材与板材等仿木材料。
上世纪90年代末,国外有关资料论述,塑料仿木材料已经被认定是木材良好的替代品,在未来50年里没有其它的类似材料能代替。
我国已把PVC低发泡大型板材等定为国家级高新技术产品,(高新技术产品目录中代码为)。
PVC发泡板挤出过程中常出现的问题
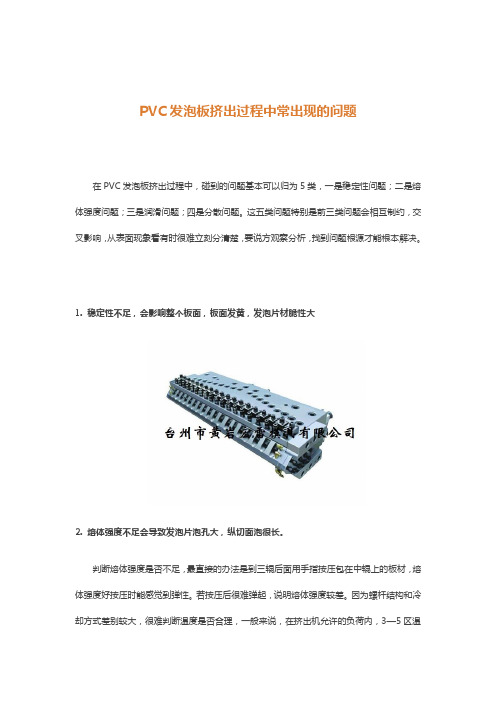
PVC发泡板挤出过程中常出现的问题在PVC发泡板挤出过程中,碰到的问题基本可以归为5类,一是稳定性问题;二是熔体强度问题;三是润滑问题;四是分散问题。
这五类问题特别是前三类问题会相互制约,交叉影响,从表面现象看有时很难立刻分清楚,要说方观察分析,找到问题根源才能根本解决。
1. 稳定性不足,会影响整个板面,板面发黄,发泡片材脆性大2. 熔体强度不足会导致发泡片泡孔大,纵切面泡很长。
判断熔体强度是否不足,最直接的办法是到三辊后面用手指按压包在中辊上的板材,熔体强度好按压时能感觉到弹性。
若按压后很难弹起,说明熔体强度较差。
因为螺杆结构和冷却方式差别较大,很难判断温度是否合理,一般来说,在挤出机允许的负荷内,3—5区温度以低为好。
在发泡管材中要想获得发泡均匀制品,也需要保证PVC物料有良好的融体强度。
所以发泡调节剂的质量和型号至关重要,当然黄白发泡剂也要配合好。
3. 润滑剂润滑剂分为外润滑剂和内润滑剂,外滑有利于脱模,对板材表面的光洁性有好处,外滑太少,挤出机5区温度不易控制,易升温,这会导致合流芯温度高,板材中间出大泡、串泡、发黄等问题,板材表面也不光滑;外滑多,析出会变得严重,表现在模具内的结构和板材表面外滑的析出,也会表现为某些个别现象在板面上不定期的来回移动。
内滑有利于塑化和熔体的流动性,内滑不足板面难以控制厚度,表现为板材中间厚两边薄;内滑多,易出现合流芯温度高的现象。
4. 分散不好会带来板材表面不光滑的现象工艺温度控制问题:上面提到的四个问题属于根本性问题,是基础,是深层次问题。
相对于上面四个问题,工艺温度控制则要直观得多,是表面问题,但温度控制不好,会诱发根本问题的出现。
提高加工工艺温度,材料稳定时间会降低,出现稳定性问题;原有的润滑平衡会被打破,一般表现为外润滑不足,特别是后期外润滑,需提高外润滑添加量;温度提高也会导致熔体强度降低,发泡片材泡孔增大,泡孔数量减少,片材发脆易断裂;温度提高降低了熔体强度也会降低熔体粘度,粘度降低剪切分散能力降低,对分散能力不强的螺杆而言,有时会出现分散不均匀。
化学发泡法挤出PE低发泡材料研究
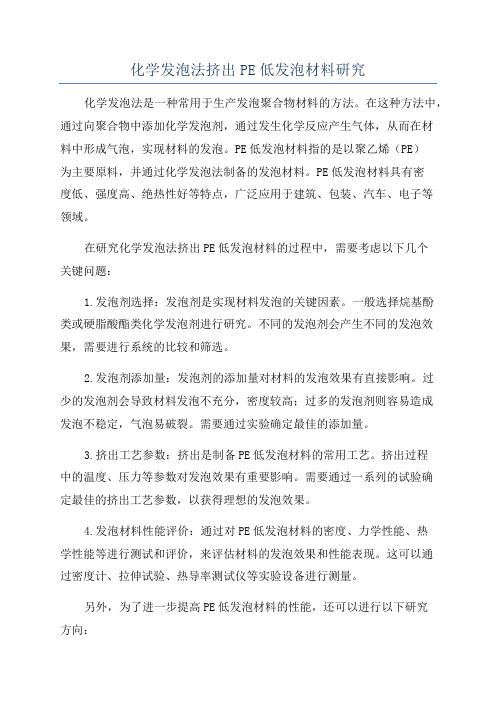
化学发泡法挤出PE低发泡材料研究化学发泡法是一种常用于生产发泡聚合物材料的方法。
在这种方法中,通过向聚合物中添加化学发泡剂,通过发生化学反应产生气体,从而在材料中形成气泡,实现材料的发泡。
PE低发泡材料指的是以聚乙烯(PE)为主要原料,并通过化学发泡法制备的发泡材料。
PE低发泡材料具有密度低、强度高、绝热性好等特点,广泛应用于建筑、包装、汽车、电子等领域。
在研究化学发泡法挤出PE低发泡材料的过程中,需要考虑以下几个关键问题:1.发泡剂选择:发泡剂是实现材料发泡的关键因素。
一般选择烷基酚类或硬脂酸酯类化学发泡剂进行研究。
不同的发泡剂会产生不同的发泡效果,需要进行系统的比较和筛选。
2.发泡剂添加量:发泡剂的添加量对材料的发泡效果有直接影响。
过少的发泡剂会导致材料发泡不充分,密度较高;过多的发泡剂则容易造成发泡不稳定,气泡易破裂。
需要通过实验确定最佳的添加量。
3.挤出工艺参数:挤出是制备PE低发泡材料的常用工艺。
挤出过程中的温度、压力等参数对发泡效果有重要影响。
需要通过一系列的试验确定最佳的挤出工艺参数,以获得理想的发泡效果。
4.发泡材料性能评价:通过对PE低发泡材料的密度、力学性能、热学性能等进行测试和评价,来评估材料的发泡效果和性能表现。
这可以通过密度计、拉伸试验、热导率测试仪等实验设备进行测量。
另外,为了进一步提高PE低发泡材料的性能,还可以进行以下研究方向:1.材料改性:可通过添加增韧剂、阻燃剂或增强剂等进行材料改性,以提高材料的强度、韧性或阻燃性能。
2.发泡机理研究:通过对发泡机理的深入研究,可以揭示发泡过程中的主要反应和物理过程。
这有助于进一步理解发泡机制,为优化发泡剂选择、发泡条件等提供理论指导。
3.发泡材料应用研究:可以对PE低发泡材料在建筑、包装、汽车、电子等领域的应用进行研究,开发出更具创新性和实用性的应用产品。
总之,化学发泡法挤出PE低发泡材料的研究是一个多方面的工作,需要综合考虑发泡剂的选择与添加量、挤出工艺参数的优化、材料的性能评价以及材料的改性和应用等方面的问题。
挤出发泡成型原理
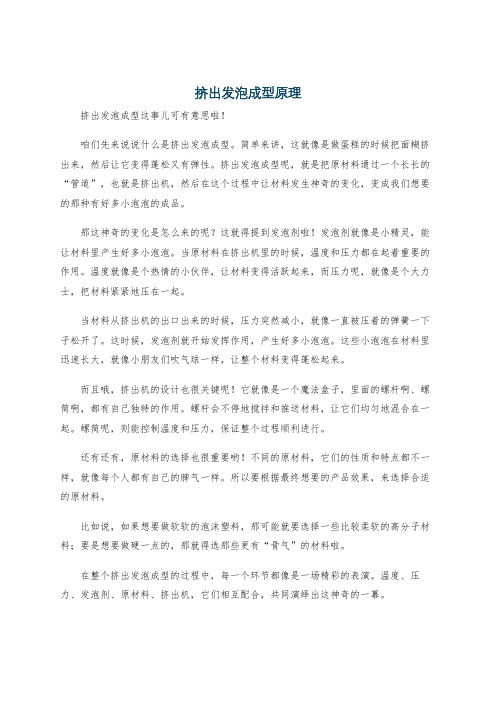
怎么样,朋友,这下你对挤出发泡成型的原理是不是有了一些了解啦?下次看到那些发泡的东西,你就可以想到这背后有趣的过程啦!
挤出发泡成型原理
挤出发泡成型这事儿可有意思啦!
咱们先来说说什么是挤出发泡成型。简单来讲,这就像是做蛋糕的时候把面糊挤出来,然后让它变得蓬松又有弹性。挤出发泡成型呢,就是把原材料通过一个长长的“管道”,也就是挤出机,然后在这个过程中让材料发生神奇的变化,变成我们想要的那种有好多小泡泡的成品。
那这神奇的变化是怎么来的呢?这就得提到发泡剂啦!发泡剂就像是小精灵,能让材料里产生好多小泡泡。当原材料在挤出机里的时候,温度和压力都在起着重要的作用。温度就像是个热情的小伙伴,让材料变得活跃起来,而压力呢,就像是个大力士,把材料紧紧地压在一起。
当材料从挤出机的出口出来的时候,压力突然减小,就像一直被压着的弹簧一下子松开了。这时候,发泡剂就开始发挥作用,产生好多小泡泡。这些小泡泡在材料里迅速长大,就像小朋友们吹气球一样,让整个材料变得蓬松起来。
而且哦,挤出机的设计也很关键呢!它就像是一个魔法盒子,里面的螺杆啊、螺筒啊,都有自己独特的作用。螺杆会不停地搅拌和推送材料,让它们均匀地混合在一起。螺筒呢,则能控制温度和压力,保证整个过程顺利进行。
还有还有,原材料的选择也很重要哟!不同的原材料,它们的性质和特点都不一样,就像每个人都有自己的脾气一样。所以要根据最终想要的产品效果,来选择合适的原材料。
比如说,如果想要做Байду номын сангаас软的泡沫塑料,那可能就要选择一些比较柔软的高分子材料;要是想要做硬一点的,那就得选那些更有“骨气”的材料啦。
低发泡硬PVC异型材挤出技术简介

低发泡硬P V C异型材挤出技术简介(总2页)--本页仅作为文档封面,使用时请直接删除即可----内页可以根据需求调整合适字体及大小--低发泡硬PVC异型材挤出技术简介硬PVC低发泡门窗异型材挤出是20世纪70年代在国外发展起来的新型技术,近年在世界各地迅速发展,这类产品主要有以下优点:1、节省原材料消耗,生产费用及制品体积价格比低,符合当前全球范围内对能源保护的意识;2、在同等长度和重量的情况下,发泡制品因横截面增大而刚性提高;3、制品内残余的内应力很小,产品尺寸稳定性好;4、隔音,保温性能优良。
硬PVC低发泡材料通常采用自由发泡,结皮控制发泡或共挤出发泡三种工艺之一进行生产,门窗异型材一般采用结皮控制发泡工艺,此种工艺是指,采用一个特殊的,内有型芯的口模,使塑化的料束分流,当料束被送入口模前的有冷却装置的定型套中时,其表面冷却形成皮层,发泡在内部进行,通过控制冷却温度和强度,可以获得皮层厚度在~毫米,制品壁厚大于6毫米的制品。
这种采用一步法生产而成的形状复杂的型材制品,具有密度低,硬度高和表面光滑的特点。
与非发泡制品相比,发泡异型材的挤出对配方、设备、工艺的要求更为严格,发泡挤出的关键就是使发泡剂的分解、成核、气泡的长大及固定等系列过程和PVC树脂的熔融塑化及面型过程相适应。
其原料配方、成型工艺和设备模具与非发泡制品均存在很多相同点和不同处。
一、原料配方1、PVC树脂:生产发泡制品的主要原料是悬浮法疏松型PVC树脂,其特点是吸收添加剂快、易塑化、热稳定性好,易获得泡孔结构均匀,表面平整的制品,一般宜选用K值62~65的树脂。
2、发泡剂及其它促进剂:PVC常用的发泡剂是偶氮二甲酰胺(AC),其发气量大,分解时放出的气体和分解残渣无毒、无害,与PVC树脂相容性、分散性均好,纯AC的分解温度较高,为保证发泡剂的分解温度介于PVC树脂的塑化温度和降解温度之间,使用时必须加入一些稳定剂做发泡促进剂,别外为了获得致密又均匀的泡孔,成核剂是必不可少的。
聚丙烯挤出发泡工艺技术

聚丙烯挤出发泡工艺技术聚丙烯挤出发泡工艺技术指的是通过挤出机将聚丙烯熔融后,加入发泡剂,然后通过模具挤出成型。
聚丙烯是一种常见的塑料材料,具有优良的物理性能和成型性能,所以广泛应用于各行各业。
发泡技术则是为了改善聚丙烯的密度和吸音性能,提高其综合性能而开发的一种技术。
下面将介绍聚丙烯挤出发泡工艺技术的过程和优势。
聚丙烯挤出发泡工艺技术主要包括以下几个步骤:首先是将聚丙烯颗粒经过熔融机熔融。
熔融机可以通过电加热方式将聚丙烯颗粒加热到一定温度,使其熔化成为熔融聚丙烯。
然后,将发泡剂加入熔融聚丙烯中,通过混合机均匀搅拌。
发泡剂的添加可以根据需求选择不同的种类和含量,以达到不同的发泡效果。
接下来,将聚丙烯熔融发泡料送入挤出机的螺杆筒中。
螺杆筒会将发泡料推到机头端,然后通过模具挤出成型。
最后,待挤出的发泡聚丙烯冷却后,即可得到所需的发泡聚丙烯制品。
聚丙烯挤出发泡工艺技术的优势主要体现在以下几个方面:首先,聚丙烯材料本身具有优良的物理性能和成型性能,发泡后能够保持这些优点的同时,又增加了一定的低密度特性,使其广泛应用于各种领域。
其次,聚丙烯挤出发泡工艺技术可以根据需要进行发泡剂的选择和添加,从而制备出不同密度和性能的发泡聚丙烯制品,满足不同行业和产品的需求。
再次,聚丙烯挤出发泡工艺技术具有工艺简单、成本低廉的优势,相比于其他发泡工艺,具有较高的经济性和适用性。
总之,聚丙烯挤出发泡工艺技术是一种应用广泛、经济实用的工艺技术。
通过这种技术可以制备出密度低、性能优良的发泡聚丙烯制品,适用于各种领域。
随着科技的不断进步,聚丙烯挤出发泡工艺技术也会不断改进和完善,为各行各业提供更优质的产品和解决方案。
- 1、下载文档前请自行甄别文档内容的完整性,平台不提供额外的编辑、内容补充、找答案等附加服务。
- 2、"仅部分预览"的文档,不可在线预览部分如存在完整性等问题,可反馈申请退款(可完整预览的文档不适用该条件!)。
- 3、如文档侵犯您的权益,请联系客服反馈,我们会尽快为您处理(人工客服工作时间:9:00-18:30)。
挤出发泡工艺三个因素。
一:挤出温度。
挤出温度对发泡板片材性能及成型影响很大。
如果开始在较低温度下挤出,泡孔较大,逐渐升高温度,泡孔会缩小,再继续升高温度,泡孔反而增大。
这是因为挤出温度低时,含气体的熔体由于混合不匀,成核少及不均匀分散而形成大气泡,所制得的发泡板片材密度大;当温度升高到一定值时,挤出熔体由于不能承受内部膨胀力而很快崩塌。
挤出温度的确定应考虑交联剂、AC各自与体系凝胶化量的关系。
若温度越高交联剂的交联温度和AC分解速率过高,从而导致成型时间不易控制;温度过低,导致AC分解速度和交联速交联剂度不相适应,使体系的凝胶量较小,不能获得良好的泡体。
此外,机头口模温度对聚乙烯板片材的发泡倍率也起决定性作用。
通常挤出机机身温度在140~190C,机头温度在180~210C,并尽可能采取低温挤出工艺,以获得细密均匀的泡孔结构。
二:熔体在挤出机内停留时间。
螺杆转速较低时,物料在机筒内停留时间长,发泡剂分解程度大,易出现并泡,使泡孔数目少而尺寸较大,泡孔结构差;还可以由于物料停留时间过长,使熔体交联度过大,出现泡材收缩;另外,熔体内的气体向外部表面扩散的概率也较大,导致制品的密度增大。
螺杆转速较大时,物料在机筒内停留时间较短,发泡剂分解历程较短,产生气体不足,往往使泡孔数目多,尺寸小,过程进行太快,在挤出口模后,再分解的残余发泡剂也得不到完全分解,导致制品密度较大;再者,物料停留时间短,无疑交联时间短,交联度低,熔体粘壁,随着AC分解气体量的增多,低交联熔体承受不了气体压力而引起熔体破裂。
一般情况下,转速较小时,密度较大,随着转速增加,密度减小,当减至一定值时,又逐渐增大。
由此可见,螺杆转速太大或太小,泡孔尺寸差别大,有并泡或破泡发生。
转速过快还会导致物料塑化不良不匀,造成部分气体逸出。
三:挤出压力。
挤出压力过低,AC分解产生的气体在熔体中扩散系数太大而溶解度很小,会造成气体大量逃逸;挤出压力增大,气体对熔体溶解度增加,成核数增多,其泡孔较小,密度也小。
助剂在发泡中作用
一般交联剂分解温度为120C,可满足高于PE熔融温度而低于AC发泡剂分解温度的要求。
在这种温度下,交联剂分解成化学活性较高的游离基并能夺取PE直链分子中氢原子,使大分子的碳原子变为活性游离基,两个或多个
分子链上活性游离基相互结合生成C—C化学键,构成网状结构。
PE交联后,交联度可达80%,熔体黏度增大,从而获得精细均匀多孔结构的高膨胀率泡沫片板材。
但是,当用量过交联剂大时,其交联速率过大,此时AC还来不及分解,熔体的黏度已经很大,气泡没有充分膨胀,故泡体内压很大,当卸去外压时,产品出现龟裂、皱纹。
当交联剂为一合适的用量时,获得优良的泡孔结构时的凝胶量至少为60%。
一般来讲,制品的拉伸强度随交联剂的用量的增加,先增加,后减小。
形成泡孔尺寸大、数量少的劣质发泡板片材,其原因是发泡剂在挤出机内基本完全分解,过饱和熔体中绝大部分气体向熔体外部扩散逸出,气泡核不足。
因此,在挤出机的熔体应保证含有大量的气体或少量的AC发泡剂,实际上熔体中留有少量的发泡剂还能起成核的作用,一旦离模即可发泡。
AC发泡剂用量对泡孔结构及发泡板片材性能的影响。
发泡过程是一个复杂的物理化学过程,发泡时要求气体向外膨胀的压力与泡孔壁熔体表面张力达到动态平衡。
根据发泡的“热点”成核机理,如果成型时,在某一段时间内不能形成大量的泡核,则得不到泡孔均匀细密的发泡体。
成型过程中,能否形成大量的泡核,体系中AC的用量是重要的因素之一。
在理论上,随AC含量增加发气量增大,但并非AC含量越高越好。
当用量超过某一极限值时,发气量增加,AC的分解速率增大,大于的交联交联剂速率,故熔体内的气体逸出量逐渐增多,导致制品的表面总密度逐渐增加。
制品的断裂伸长率随AC用量的增加先减小后增大。
这是因为当AC用量较小时,AC 分解速率与交联剂交联速率相适应,随着AC用量的增加,其分解速率也随之增加,气体在熔体中不能充分膨胀,故制品的韧度降低。