广安轻烃回收工艺方案选择
轻烃回收(寇杰)

轻烃回收
油吸收法的主要设备有吸收塔、富油稳定塔和富油蒸馏塔。若为低温
油吸收法,还需增加制冷系统。在吸收塔内,吸收油与天然气逆流接
触,将气体中大部分丙烷、丁烷及戊烷以上烃类吸收下来。从吸收塔 底部流出的富吸收油(简称富油)进入富油稳定塔中脱出不需要回收的
轻组分如甲烷等,然后在富油蒸馏塔中将富油中所吸收的乙烷、丙烷
可以达到-35℃~-30℃,在新建设的装置中基本都采用丙烷制冷法。
轻烃回收
冷剂制冷法的优点是天然气冷凝分离所需要的冷量由独立 的外部制冷系统提供,制冷系统所产生冷量的多少与被分离天
然气本身无直接的关系。该法制冷量不受原料Байду номын сангаас贫富程度的限
制,对原料气的压力无严格要求,装置运行中可改变制冷量的 大小以适应原料气量、原料组成的变化以及季节性气候温度的 变化。 在我国,大多数浅冷装置都采用丙烷制冷法。
轻烃回收
2) 膨胀制冷法
膨胀制冷法应用的前提条件是原料气与外输干气是否有一个较高 的压力差可以利用,其核心是通过膨胀机将气体的压力能转化为机械 能并产生冷量。膨胀机的膨胀过程热力学上近似于等熵膨胀过程。 膨胀制冷法的特点是流程简单、设备数量少、维护费用低、占用 地少、适合于原料气很贫的气体。 我国采用单纯的膨胀制冷工艺(ISS)轻烃回收装置,规模一般较小, 且都采用中低压膨胀机,膨胀比较小,制冷温度一般仅能达到20℃~-60℃,也有部分装置制冷温度达到-70℃~-86℃,为了获得 更大的轻烃收率,或者有更高的原料气压力资源利用时,可采用多级 膨胀工艺(MTP),以满足更低的制冷温度要求。 膨胀机制冷法的典型装置是四川中坝的30×104Nm/d膨胀机制冷 分离装置,其膨胀机出口温度达-90℃。
3. 低温分离法
小气量低压气轻烃回收工艺方案

低压伴生气轻烃回收工艺方案在油田开发过程中, 油田伴生气和油罐挥发气都是关键资源, 因气量小, 地点分散, 气体集输困难, 没有得到合理利用。
小流量、低压伴生气中回收轻烃,对于降低油气损耗, 取得较高经济效益和良好社会效益, 都含相关键现实意义。
从轻烃回收工艺来看, 关键有油吸收法、低温分离法、压缩法、吸附法、复合回收法等。
在气量较大, 含烃量高时低温分离法与其它轻烃回收方法相比, 含有投资少、操作费用低、效率高等优点。
现在广泛采取回收方法是低温分离法或低温分离法与其它方法组合——复合回收法。
天然气(含伴生气) 经过以上某一个或多个方法, 把其中丙烷以上重组分从气体中分离出来而得到混合液烃。
对于少许低压气回收, 我企业依据多年实践, 采取我企业专利技术, 提出了合理工艺回收方案。
1 基础数据气体处理量:原料气压力:气体温度:原料气组成:工艺要求技术指标: 从原油伴生气回收混合轻烃。
产品收率≥90%2 轻烃回收方案因为原料气气压低, 无压力能可利用, 所以, 对原料气实施增压。
对于小流量、低压气轻烃回收工艺技术路线可概括为:原料气增压→脱水→节流, 膨胀, 冷凝→产品(混烃, 干气)。
实践证实混烃液化率伴随压力升高、温度降低而增加。
一样若压力太低, 要想使丙烷达成较高液化率, 需要很低冷凝温度(- 50℃以下) ,将使步骤复杂化, 增加投资。
对于小流量、低压气轻烃回收路径, 通常单纯采取节流膨胀制冷法, 液烃回收率很低, 达不到工艺要求。
我企业消化吸收中国外优异技术和设备, 推出涡流管节流膨胀制冷工艺, 使得工艺简化, 投资节省, 混烃回收率高。
产品收率≥90%。
3 轻烃回收工艺标准步骤经过工艺方案和操作参数优选后, 确定轻烃回收工艺标准步骤图: 原料气经二级压缩(25-30MPa)→脱水→涡流管膨胀制冷→节流膨胀制冷(0℃)→混烃分离,该工艺步骤含有以下特点:(1) 采取涡流管膨胀制冷+ 节流膨胀复合制冷方案, 提升了轻烃回收率。
轻烃回收
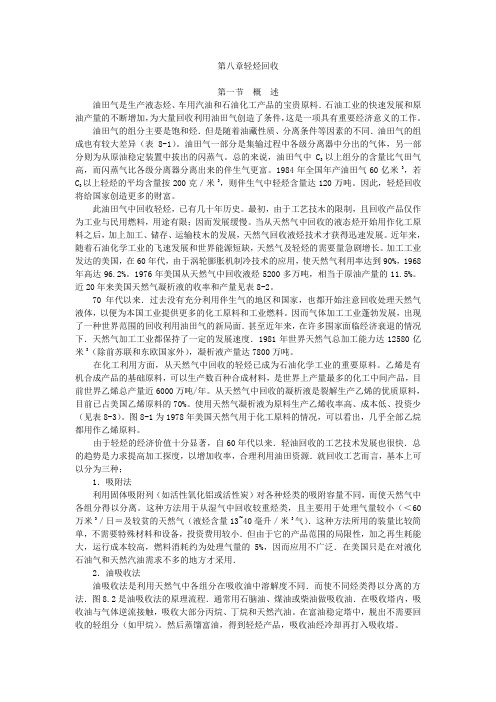
第八章轻烃回收第一节概述油田气是生产液态烃、车用汽油和石油化工产品的宝贵原料.石油工业的快速发展和原油产量的不断增加,为大量回收利用油田气创造了条件,这是一项具有重要经济意义的工作。
油田气的组分主要是饱和烃.但是随着油藏性质、分离条件等因素的不同.油田气的组成也有较大差异(表8-1)。
油田气一部分是集输过程中各级分离器中分出的气体,另一部分则为从原油稳定装置中拔出的闪蒸气。
总的来说,油田气中C3以上组分的含量比气田气高,而闪蒸气比各级分离器分离出来的伴生气更富。
1984年全国年产油田气60亿米3,若C3以上轻烃的平均含量按200克/米3,则伴生气中轻烃含量达120万吨。
因此,轻烃回收将给国家创造更多的财富。
此油田气中回收轻烃,已有几十年历史。
最初,由于工艺技木的限制,且回收产品仅作为工业与民用燃料,用途有限;因而发展缓慢。
当从天然气中回收的液态烃开始用作化工原料之后,加上加工、储存、运输枝木的发展,天然气回收液烃技术才获得迅速发展。
近年来,随着石油化学工业的飞速发展和世界能源短缺,天然气及轻烃的需要量急剧增长。
加工工业发达的美国,在60年代,由于涡轮膨胀机制冷技术的应用,使天然气利用率达到90%,1968年高达96.2%。
1976年美国从天然气中回收液烃5200多万吨,相当于原油产量的11.5%。
近20年来美国天然气凝析液的收率和产量见表8-2。
70年代以来.过去没有充分利用伴生气的地区和国家,也都开始注意回收处理天然气液体,以便为本国工业提供更多的化工原料和工业燃料。
因而气体加工工业蓬勃发展,出现了一种世界范围的回收利用油田气的新局面.甚至近年来,在许多围家面临经济衰退的情况下.天然气加工工业都保持了一定的发展速度.1981年世界天然气总加工能力达12580亿米3(除前苏联和东欧国家外),凝析液产量达7800万吨。
在化工利用方面,从天然气中回收的轻烃已成为石油化学工业的重要原料。
乙烯是有机合成产品的基础原料,可以生产数百种合成材料,是世界上产量最多的化工中间产品,目前世界乙烯总产量近6000万吨/年。
轻烃回收工艺的发展趋势及新技术研讨

一、国内外轻烃回收当前的发展情况1.国外轻烃回收的相关工艺概述国外的轻质烃采收工艺最早出现于1904年。
第一座轻油采收工厂建于美国,已有100多年的历史。
国外的轻烃回收过程起步较早,因此比我国的过程要先进。
轻烃的产量以及油气资源的有效利用在国外加工中均取得了巨大成就。
行业在1970年代,其技术的研发目标开始不断提高公司自身的运营效率,以提高轻质烃的产量以及节能和减少能耗。
比较成熟的点主要是低温分离法。
该轻烃工艺具有深层分离,投资少,能耗低,效率高和撬装技术的技术优势,并且目前正在朝自动化方向发展。
2.我国轻烃回收工艺的相关概述我们国家的天然气轻烃分离技术开始在上个世纪的60年代产生,因为这一工艺当前的发展起步的相对来说会比较晚,只是发展只是停留在上个世纪的30到40年代国外的轻烃上的回收水平,这样的一种情况使得我国天然气企业受到了轻烃回收工艺的制约,产品的质量不能够满足预期的标准,并且轻烃自身的收率也并不高,企业完成生产得产品主要是被当成是民用以及工业燃料使用。
二、轻烃回收的相关技术概述1.轻烃回收技术的基础原理轻烃回收当前主要是运用气体混合物里很多不同的组成成分的一种液体溶解度之间出现的差别去完成所需要的吸收,从而使其能够达成气体混合物之间的物质分离。
整体进行吸收的过程主要是在固定的压力以及温度条件下去完成的,气液两相其在塔板上完成接触,通过多种液体烃类构成在吸收剂里溶解度产生的差异去完成阶段性分离吸收。
2.轻烃回收的相关工艺装置一般我国选择的轻烃回收工艺装置其本身属于一种使用煤液化的装置;其原料的分离尾气其主要是运用煤液化膜;塔顶气选择的主要是一种加氢的稳定装置;含硫气使用加氢改质装置,其他构成部分则属于间接的液化富气和净化中压气回收氢气后的尾气以与接液化富液等一系列的回收装置。
轻烃回收的核心目标主要是把液化气和石脑油等部分产品完成回收,并且为提供原料干气作为全厂使用的燃料气。
三、轻烃回收的核心工艺低温回收工艺其本身属于一种低温的分离方式,主要是按照原料中多种不同烃类气体其自身的冷凝温度差异完成不断分离的一种技术方法,实际的操作主要是先把原料气完成有效的冷却,然后不断的提高装置自身的反应温度,使用原料气中多种烃类在其沸点上的差异不断完成冷凝分离,再进行凝液精馏分离使其生成一种符合要求的产品。
伴生气轻烃回收液化气工艺设计

伴生气轻烃回收液化气工艺设计引言伴生气轻烃回收液化气工艺设计是一种对伴生气中的轻烃进行回收利用的技术。
伴生气是指在石油、化工等生产过程中产生的含有各种轻烃物质的气体。
传统上,伴生气中的轻烃往往被视为废气,大量的轻烃被直接排放到大气中,不仅造成了能源的浪费,还对环境造成了污染。
通过伴生气轻烃回收液化气工艺设计,可以将这些轻烃回收利用,并转化为液化气,实现能源的有效利用和环境的净化。
工艺步骤伴生气轻烃回收液化气工艺设计包括以下几个步骤:1. 原料准备在进行伴生气轻烃回收液化气工艺设计之前,需要先准备好所需的原料。
原料主要包括伴生气和液化气。
伴生气是从生产过程中获取的含有轻烃物质的气体,而液化气则可以通过石油气或天然气等途径获得。
2. 气体分离在伴生气中,常见的轻烃有丙烷、丁烷等。
在进行气体分离时,可以利用不同轻烃的沸点差异实现。
一种常见的气体分离方法是通过冷却和压缩来将伴生气中的轻烃物质分离出来。
这一步骤可以使用分离塔等设备来完成。
3. 液化处理在分离出轻烃物质后,需要将其进行液化处理。
液化处理是将轻烃物质转化为液体状态的过程。
这可以通过降低温度或增加压力来实现。
常见的液化处理方法包括冷凝和压缩。
4. 气体再生在液化处理后,得到的液化气可以作为能源使用。
但是,为了实现循环利用,还需要对剩余的气体进行再生。
再生是指将剩余的气体经过各种化学反应或物理处理后,使其重新变为伴生气中的轻烃物质。
这一步骤可以采用吸附、脱附等方法。
5. 产品分离在再生后,可以得到纯度较高的轻烃物质。
这些物质可以经过进一步处理和分离,得到所需的液化气产品。
这一步骤可以使用分离设备来实现。
设计要点在进行伴生气轻烃回收液化气工艺设计时,需要考虑以下几个要点:1. 能源消耗在工艺设计中,需要考虑能源的消耗情况。
为了减少能源的浪费,可以通过优化设备结构、改进工艺流程等方式来实现。
2. 环境影响伴生气轻烃回收液化气工艺设计涉及到大量的气体处理和转化过程。
450万吨年轻烃回收装置工艺分析

1 轻烃回收装置预期产品轻烃回收装置的产品分别是:吸收塔顶富含C 2组分的干气、脱乙烷塔顶富含C 2组分干气、C 3H 8、C 4H 10、正丁烷、石脑油、C 5轻石脑油。
2 工艺技术路线2.1 采用三塔分馏工艺轻烃回收部分通常采用“吸收-脱丁烷-脱乙烷”的后脱乙烷流程,原料适应性强,可以在脱丁烷塔前后分别加工C 5含量不同的原料。
同时,在装置原料性质变化、操作波动时,具有灵活的调节手段,操作时根据原料的性质,甚至可以单独切除脱乙烷塔。
作为全厂性的轻烃回收装置,加工原料复杂,特别是需要加工大量的来自柴油加氢裂化装置和蜡油加氢裂化装置的粗液化气,这些液化气C 5+含量较少,C 2含量高,不需要进脱丁烷塔二次重沸分离C 5,只需要进脱乙烷塔脱除C 2即可。
同时,采用“吸收-脱丁烷-脱乙烷”的后脱乙烷流程具有原料适应性强、抗波动能力强等优点。
由于常减压蒸馏装置的初馏塔采用了提压操作方式,常减压的轻烃可以通过液化石油气组分溶解在初顶油中以液体的形态进行回,同时液化气吸收塔的设置也可以回收柴油加氢裂化装置、蜡油加氢裂化装置、渣油加氢装置和重整装置来的酸性尾气中的轻烃。
通过采用上述工艺,可以使该单元避免设置压缩机,从而避开因有压缩机而带来的流程复杂、操作不便、投资高、噪音大、能耗高、机械故障多、设备维修困难等问题。
此外,由于轻烃回收单元处理多个装置的物料,采用无压缩机回收轻烃,也为其他相关装置的平稳运行提供了更好的保障。
0 引言恒力石化450万吨/年轻烃回收装置于2019年12月建成投产,装置的原料为来常减压的液态烃石脑油、渣油加氢气体、重整含硫燃料气及蜡油加氢含硫液化气等[1]。
轻烃回收单元包含液化气吸收、脱丁烷和脱乙烷;液化气分离单元包含脱丙烷、脱异丁烷。
轻烃回收单元集中对全厂的常减压装置、加氢装置、连续重整装置等液态烃石脑油和含烃类气体进行处理,以回收其中高附加值轻烃组分;液化气分离部分将轻烃回收部分的液化气进一步分离成C 3H 8和C 4H 10,原料性质如表1所示。
膨胀制冷轻烃回收工艺参数优化分析

关键词: 温分 离器 ; 低 操作 温度 ; 操作 压 力 ; 膨胀 比 ; 回流 比
文 章 编 号 : 0 -59 2 1 )10 2 - 1 65 3 (0 0 0 - 40 0 0 5 文 献标 识 码 : B
程 见 图 1 。
0 前 言
液 化气作 为一 种优 质 、 洁 、 清 高热 值 的燃 料 , 无
c 原 料气 处理 量 :0 . 3 0×1 d 0m/; d 干 气外 输压 力 :. P ; . 6 1M a e 干气 外 输温度 :0~ 5 ; . 3 4% f要求 C 回收量 : 8 % 。 . > I 0
12 0 0
星 90 0
接 0 0
u 3 0 0
1 1 低 温 分 离器操 作压 力 的确定 .
—0 6
—O 5
一0 4
.O 3
-0 2
冷 温 度 /o  ̄
图 3 不 同 温 度 及 压 力 下 低 温 分 离 器 液 相 的 c 一 流 率 的
故 低 温 分 离器 中 的操作 压力 并 不是 越 高 越好 , 操 作 温 度 亦 并 非 越 低 越 好 , 工 况 原 料 气 压 力 为 本 3 6 M a 干 气外 输压 力为 6 1MP 。考 虑 原 料气 经 . P , . a 冷 箱压 力 损 失 , 温 分 离 器 操 作 压 力 拟 定 为 3 5 低 .7
原料气
Q 10 一0
Q-0 14
=_ :
水冷 器 2
冷箱
阀
收 稿 日期 :0 91 —3 2 0 —01
低温分离器
机熙 7
I
晦
水冷器 1
80万方每天轻烃回收装置工艺设计

摘要轻烃又称为天然气凝液(NGL ),在组成上覆盖+62~C C ,含有凝析油组分(52~C C )。
轻烃回收是指天然气中比甲烷或乙烷更重的组分以液态形式回收的过程。
轻烃回收的目的一方面是为了控制天然气的烃露点以达到商品气质量指标,避免气液两相流动;另一方面,回收的液烃有很大的经济价值,可直接用作燃料或进一步分离为乙烷、丙烷、丁烷、或丙丁烷化合物(液化气)、轻油等,也可以用做化工原料。
另外,轻烃作为一种新型的清洁能源,市场前景非常可观。
所以,设计合理的轻烃回收装置,在化工生产中具有很大的必要性。
本设计主要针对轻烃的回收装置进行,根据原料气的组成及产品指标,计算出合理的分离序列。
通过计算可以得到脱乙烷塔和丙丁烷塔的塔径分别是1.5m 和1.8m ,理论板数分别为10块和11块,回流比分别为1.500和1.083。
脱乙烷塔的操作条件为塔顶-31.75C ︒,1.164MPa ,塔底为40.52C ︒,1.400MPa ,丙丁烷塔的操作条件为29.58C ︒,0.910MPa ,塔底为107.9C ︒,0.930MPa 。
确定塔的形式都为浮阀塔,分别对两个塔的各项参数进行了设计,并对塔进行了水力学校核,所得的塔能较好的达到分离要求。
关键词: 轻烃;分离;精馏;设计ABSTRACTLight hydrocarbon, which is also called the Natural gas condensate, in the composition is covered by +62~C C , and contains oil condensate components. Light hydrocarbon is point to the process that to recovery the composition as liquid that more heavy than methane or ethane in the Natural gas. The purpose of the light hydrocarbon recovery is to control the gas hydrocarbon dew point in order to achieve quality goods gas index, avoid gas-liquid two phase flow; On the other hand, the liquid hydrocarbon recovery has a great economic value, it can be directly used for fuel or further separation for ethane ,propane ,butane ,or propane and butane compounds (liquefied petroleum gas) , light oil etc ,also can be used as raw material for chemical industry. In addition, as a new clean energy, light hydrocarbon’s market foreground is very considerable. So ,to design the reasonable light hydrocarbon recycling equipment has great necessity in chemical production.The design for the main light recovery device ,according to the composition of the gas material and product index ,calculate reasonable separation sequence. Through the calculation can get to take off the ethane tower and the tower propane and butane tower diameter are 1.5 m and 1.8 m, respectively ,theory respectively numbers of plate are 10 and 11 piece ,reflux ratio are 1.500 and 1.083,respectively.The operation condition for take off ethane tower are -31.75C ︒,1.164MPa for the top and 40.52C ︒,1.400MPa for the bottom of propane and butane tower are 29.58C ︒,0.910MPa for the top and 107.9C ︒,0.930MPa for the bottom .Determine the form of tower for the float valve tower, design various parameters for the two towers ,check them from hydraulics and then they can achieve separation requirements.Keywords : Light ;hydrocarbon ;Abruption ;Distillation ;Design目录1 前言 (1)1.1 气质条件及生产要求 (1)1.2 轻烃回收方法 (2)1.3 轻烃回收装置设计意义 (3)2工艺方案及流程 (4)2.1 工艺方案 (4)2.2 装置原则工艺流程图 (4)2.3 生产流程简述 (4)3 物料衡算 (5)3.1 脱乙烷塔的物料衡算 (5)3.1.1 清晰分割 (5)3.1.2 确定最小理论板数 (7)3.1.3最小回流比及实际回 (7)3.1.4 确定实际板数及进料位置 (7)3.1.5 确定适宜的进料温度 (8)3.2 丙丁烷塔的物料衡算 (8)3.2.1 清晰分割 (8)3.2.2 确定最小理论板数 (10)3.2.3最小的回流比及实际回流比计算 (10)3.2.4 确定实际板数及进料位置 (10)3.2.5 确定适宜的进料温度 (10)4能量衡算 (11)4.1 脱乙烷塔的能量衡算 (11)4.1.1 D-104热负荷 (11)4.1.2 D-105热负荷 (11)4.1.3 循环水用量 (12)4.2 丙丁烷塔的能量衡算 (12)4.2.1 D-106热负荷 (12)4.2.2 D-107热负荷 (13)4.2.3循环水用量 (14)4.3 其他热量衡算 (14)4.3.1 热负荷计算 (14)4.3.2 水循环计算 (14)5 设备的工艺计算及选型 (15)5.1 压缩机的工艺计算与选型 (15)5.2 分子筛干燥器的设计与计算 (15)5.3 低温分离器的设计与计算 (16)5.3.1 D-101的设计与计算 (16)5.3.2 D-102的设计与计算 (18)5.4 膨胀机的设计与计算 (21)5.5 精馏塔的设计与选型 (21)5.5.1 脱乙烷塔的设计与选型 (21)5.5.2 丙丁烷塔的设计与选型 (27)5.6 换热器的设计与选型 (34)5.7 换热器选型一览表 (36)6 原材料,动力消耗定额及消耗量 (37)6.1 原材料 (37)6.2 动力消耗 (37)6.2.1 冷却水及蒸汽用量 (37)6.2.2 压缩机及膨胀机功率 (37)7设计结果汇总 (39)8结论与建议 (43)8.1 结论 (43)8.2 建议 (43)谢辞 (44)参考文献 (45)1前言1.1 气质条件及生产要求表1.1 原料气组成序号 组成名称摩尔组成,n%1 1C 0.7192 2 2C 0.11163 3C0.0797 4 4iC0.0189 5 4nC 0.0271 6 5iC 0.0035 7 5nC0.0063 8 +5C 0.0052 9 2N0.0280 10 O H 20.0005 总结1.0000原料气处理量d Nm /108034⨯,条件为MPa C 37.030,︒(绝)。
- 1、下载文档前请自行甄别文档内容的完整性,平台不提供额外的编辑、内容补充、找答案等附加服务。
- 2、"仅部分预览"的文档,不可在线预览部分如存在完整性等问题,可反馈申请退款(可完整预览的文档不适用该条件!)。
- 3、如文档侵犯您的权益,请联系客服反馈,我们会尽快为您处理(人工客服工作时间:9:00-18:30)。
组分少 , 轻烃回收工艺方案选择较为困难 , 需做进一
图 2 广安区块原料气相包络图
以下是膨胀制冷工艺流程 , 如图 4 所示 。 以 C 能耗 值为目标 函数 , 利用 H Y S Y S 3 收率 / 软件对以上三方案进行优化分析 , 得到最优化工艺 参数 , 见表 2。
+
由图 2 可知广安 区块原料气多组分烃类体系 中 , 在 4. 5M P a 、40℃右边的区域处于压力反凝析
。 当原料
气被冷到 50℃时 , C 3 冷凝率为 57%, 当原料气 被冷凝到 70℃时 , C 3 冷凝率为 87%。 可见 , 针对 广安区块较贫的气质条件 , 在 3. 6M P a 下采用浅冷 回收工艺 , C 3 收率极低 , 采用深冷工艺液烃产量较 高。
+ +
+
图 3 天然气冷凝曲线
2. 3 原料气冷凝特性 由表 1 所示的广安区块原料气条件 , 作出原料 气相包络图 , 如图 2所示 。
[ 5]
,
表 3 浅冷 油吸收法主要物流参数表
图 6 D H X工艺流程图
经 H Y S Y S 软件对整个流程模拟计算 , 得到各物 流节点数据 , 见表 4。
表 4 D H X主要物流 参数表 物流号 温度 /℃ 压力 /k P a 1 30 3 600 2 -51 3 570 3 -51 3 570 221. 8 9 -81. 5 1 700 231. 4 液化气 40 5 -79. 2 1 700 4 974. 7 12 5 1 660 584 轻油 40
1 流量 /k m o l ·h
C 3 、C 4 组分将由于传质推动力 , 溶解到吸收油中 , 其
6 -89. 3 1 500 4 867. 6 10 20. 8 1 470 5 046. 5 23 40. 2 1 500 193. 29
3 4 -58 -58 3 570 3 570 4 867. 8 328. 7 8 9 59. 1 -84. 75 1 550 1 500 149. 9 5 046. 5 轻油 液化气 166. 2 40. 2 1 400 1 500 21. 2( 产量 128. 6( 产量 321. 9 41. 8t /d ) 141. 9t /d )
3 轻烃回收工艺方案的选择
广安气 田 原料 气较 贫 , 且 原 料气 压 力为 3. 6 M P a , 干气外输压力为 6. 1M P a , 无压差可利用 , C 3 步的多方案对比分析 。 膨胀制冷工艺 : 用于原料气与外输干气有一个 较高的压力差可以 利用的场合 , C 3 收率取决于膨 胀机前后压力差的大小 。 适合于四川气田气质较贫 的天然气轻烃回收 。 C 3 组分收率一般大于 80%。
第 27 卷第 4 期
汪宏伟 , 等 : 广安轻烃回收工艺方案选择
21
图 4 膨胀制冷工艺流程图 表 2 膨胀制冷工艺主要物流参数表 物流号 1 温度 /℃ 30 压力 /k P a 3 600 1 5 196. 4 流量 /k m o l ·h 物流号 7 温度 /℃ 15. 0 压力 /k P a 1 550 1 441. 9 流量 /k m o l ·h 物流号 14 温度 /℃ 62. 3 压力 /k P a 1 350
+
3
2 原料气气质条件及特性曲线
2. 1 原料气气质条件 原料气含饱和水 、含微量凝析油 。 凝析油分子
收稿日期 : 20090105 作者简介 : 汪宏伟 ( 1982) , 男 , 四川眉山 人 , 助理工程师 , 硕士 , 毕业于西南石油大学化学工艺 专业 , 主要从事天 然气 处理与加工的研究与设计工作 。 电话 : ( 028) 86014540。
第 27 卷第 4 期 2009 年 8 月
天 然 气 与 石 油 N a t u r a l G a s A n dO i l
V o l . 27, N o . 4 A u g . 2009
广安轻烃回收工艺方案选择
汪宏伟 , 西南分 公司 , 四川 成都 610017) 摘 要 : 针对广安气田低渗透 、 低压气藏 、 初期原料气压力衰减速度快的特点 , 结合原料气
气质条件 , 按照轻烃回收工艺方案选择原则 , 初步选择膨胀机制冷 、D H X 工艺和浅冷 油吸收 法三种工艺方案 , 采用 H Y S Y S 模拟软件对各方案进行流程模拟优化计算 , 通过各方案的 C 3 收率和装置运行能耗两项指标进行对比分析 , 最终采用膨胀制冷工艺 。
关键词 : 轻烃回收 ; 工艺方案 ; 膨胀制冷 ; D H X 工艺 文章编号 : 10065539( 2009) 04-001905 文献标识码 : B
4 各方案收率与能耗 、固定投资对比 分析
经工艺计算 , 各工艺方案产品产量与运行能耗 , 见表 5 所示 。
表 5 各工艺方案产品产量与运行能耗 对比 膨胀机 浅冷 油 制冷法 吸收法 + C %) 90. 8 81. 5 3 收率 /( 1 液化气产量 /t ·d 141. 9 138. 85 1 轻油产量 /t ·d 41. 8 25. 48 压缩机入口压力 /MP a 1. 4 ~ 1. 7 3. 45 3 1 燃料气 /m ·h 1540 729 1 能 循环水 /t ·d 150 160 1 耗 蒸汽 /t 5. 2 8. 8 ·d 电 /k W 307. 5 1 522. 4 1 年综合能耗 /106 MJ ·a 693. 86 563. 75 工艺方案 D H X法 92. 3 143. 9 41. 6 1. 6 ~ 1. 9 1 483 190 3. 4 460 712. 38
20 原料气的边界条件如下 : 原料气温度 : 20 ~ 30℃;
天 然 气 与 石 油
2009 年
区和温度反凝析区 , 当等温升压或等压降温时 , 反而 凝析液量减少 , 对低温分离器中液烃的冷凝不利 , 工 艺参数的选 择应避开此区域
[ 1]
原料气压力 : 1. 5 ~ 5. 7M P a; 原料气产量 : 300 × 10 m /d ; 干气外输压力 : 6. 1M P a ; 干气外输温度 : 30 ~ 45℃; 原料气含水量 : 928 × 10
+
压力 , 低温分离器的温度下降 , D H X塔塔顶进料乙 烷浓度增加 , 也可使 D H X 塔的 C 3 回收效果增强 D H X 工艺流程图如图 6所示 。
4 -35 3 570 2 21. 8 9 -32. 6 1 720 655. 4 液 化气 67. 7 1 400 126. 3( 产量 138. 85 t /d ) 5 -36. 9 3 590 200 10 114. 8 1 650 331. 7 轻油 40 1 350 12. 6( 产量 25. 4t /d )
+
1 概述
广安气田地处四川盆地中部 , 由广安 106 井区 和广安 2 号井区 构成 , 因气 田具有低渗透 、低压气 藏 , 初期原料气压力衰减速度快等特点 , 在未来 20 年间 , 天然气年产量不稳定 。 天然气产能期分为以 下四个阶段 : 2007 ~ 2008 年开井初期增产 、 2009 ~ 2016年 加密 接 替稳 产 、 2017 ~ 2018 年增 压稳 产 、 2019年开始递减等四个阶段 , 由 图 1 所示 , 广安区 块天然气 在未来 20 年内累计产 量为 192. 42 ×10 m。 该气田原料气另一显著特点是原料气压力变化 较大 , 气田开发初期原料气压力为 5. 7M P a , 然后压 力逐年 开 始衰 减 , 4 年后 原料 气 压力 控 制 在 3. 6 M P a 。 到气 田 开 发末 期 , 原 料 气 压 力 衰 减到 1. 5 M P a 。
[ 4] + +
浅冷 + 轻油吸收工艺 : 该工艺首先采用丙烷制 冷 , 再利用脱丁烷塔底轻油换热到 -36℃后循环到 吸收塔顶 , 与天然气逆流接触 , 进一步吸收低温分离 器出口气相中的 C 3 、C 4 组分 。 同时 , 入塔吸收油中 C 3 、C 4 组分含量低 , 其饱和蒸汽压低 , 所以天然气中
[ 2] +
+
要求 C ≥ 80%。 3 回收量 : 2. 2 原料气进厂压力下限值的确定 随着气田的开采 , 气田压力逐年递减 。 在未来 20 年内原料气压力变化范围较大 ( 1. 5 ~ 5. 7M P a ) , 将使装置运行不稳定 。 原料气进厂压力高 , 能提高 液化气和轻油产量 。 原料气进厂压力低 , 能延长装 置对气田压力的适应年限 , 但液化气和轻油产量低 。 根据广 安 气 田 开 发 方 案 , 气 田 开 发 的 前 期 ( 2009 ~ 2013 年 ) 原料 气 进 厂 压 力 变 化 明 显 , 从 2014 ~ 2029年 , 原料气压力将长期稳定在 3. 6M P a 。 为使装置保持长期的平稳运行状态 , 本文在轻烃回 收方案选择和模拟优化计算时 , 原料气进口压力取 3. 6M P a 。 到气田 开发末期 , 原料 气压力在 1. 5~ 3. 6M P a 时 , 将采用压缩机增压至 3. 6M P a 进轻烃 装置 。
。
D H X 工艺的特点是当原料气中 C 1 /C 2 比值较 低时 , 低温分离器液相将产生大量的 C 1 、C 2 液烃 , 从
图 5 浅冷 油吸收法工艺流程图
22
天 然 气 与 石 油
2009 年
而提高了 D H X 塔塔顶进料 C 2 组分浓度 , 并提供充 足的冷量 , 即可获得较高的 C 对于原料气中 3 收率 ; C 1 /C 2 比值较大的工况 , 通过适当降低膨胀机出口
物流号 温度 /℃ 压力 /k P a 1 摩尔流量 /k mo l ·h 物流号 温度 /℃ 压力 /k P a 1 摩尔流量 /k mo l ·h 物流号 温度 /℃ 压力 /k P a 1 摩尔流量 /k mo l ·h 1 30 3 600 5 196. 4 6 -41. 5 1 750 655. 4 15 132 1 640 331. 6 2 -26 3 580 5527 7 -24. 2 3 500 5 071 16 177 1 450 212. 07