8.1(Hazardous Large-scale Lift) Pre-lift Check List 起重吊装前安全检查表
浩博兄姐铅电极安全指南说明书

SDS # 412HBC8676801S afety Latest Revision: June 2015 D ata Page 1 of 8 S heet Hobart Brothers Co. 1. PRODUCT AND COMPANY IDENTIFICATION:PRODUCT NAME: Electrodes, Nickel 55 (H500631-RDP, H500644-RDP)SUPPLIER: Hobart Brothers Co.2200 Corporate DriveTroy, OH 45373 U.S.A.Phone: 937-332-4000E-mail:**********************Website: EMERGENCY TELEPHONE NUMBER: 1-800-424-9300 (Chemtrec CCN11662)____________________________________________________________________________________2. HAZARD IDENTIFICATION:Emergency Overview: This product is normally not considered hazardous as shipped. Avoid eye contact or inhalation of dust from the product. When this product is used in a welding process, the most important hazards are welding fumes, heat, radiation and electric shock.Classification of the Substance/MixtureCLP/GHS Classification (1272/2008):Skin Irritation, Category 2Skin Sensitization, Category 1Eye Irritation, Category 2Carcinogenicity, Category 2Specific Target Organ Toxicity (Repeated Exposure), Category 1EU Classification (67/548/EEC):Toxic (T), Harmful (Xn), Irritant (Xi), Carcinogen Category 3, R48/23, R40, R36/38, R43Hazardous Classification per 29CFR 1910.1200 (Rev. July 1, 2012):Skin Irritation, Category 2Skin Sensitization, Category 1Eye Irritation, Category 2Carcinogenicity, Category 2Specific Target Organ Toxicity (Repeated Exposure), Category 1Labelling:Symbols:Signal Word: DangerHazard Statements:H315 –Causes skin irritation.H317 –May cause an allergic skin reaction.H319 –Causes serious eye irritation.H351–Suspected of causing cancer.H372–C ause damage to respiratory system, eyes, brain and nervous system through prolonged or repeated exposure. Precautionary Statements:P201 –Obtain special instructions before use.P202 –Do not handle until all safety precautions have been read and understood.P260 –Do not breathe dust/fume/gas/mist/vapours/spray.S heet Hobart Brothers Co. P264 –Wash skin and hair thoroughly after handling.P270 –Do not eat, drink or smoke when using this product.P272 –Contaminated work clothing should not be allowed out of the workplace.P280 –Wear protective gloves/eye protection/face protection.P281 –Use personal protective equipment as required.P302+P352 –IF ON SKIN: Wash with plenty of soap and water.P305+P351+P338 –IF IN EYES: Rinse cautiously with water for several minutes. Remove contact lenses, if present and easy to do. Continue rinsing.P308+P313 –IF exposed or concerned: Get medical advice/attention.P314 –Get medical advice/attention if you feel unwell.P333+P313 –IF skin irritation or rash occurs: Get medical advice/attention.P337+P313 –IF eye irritation persists: Get medical advice/attention.P362 –Take off contaminated clothing and wash before reuse.P405 –Store locked up.P501 –Dispose of contents/container in accordance with local/regional/national/international regulations.___________________________________________________________________________________R36/37/38Irrit.. 2(H319) EyeIrrit.. 2(H335) STOTSE 3Irrit.. 2(H319) EyeIrrit.. 2(H335) STOTSE 3R36/37/38(H315) SkinIrrit.. 2(H319) EyeIrrit.. 2(H335) STOTSE 3(H315) SkinIrrit.. 2(H319) EyeIrrit.. 2(H335) STOTSE 3(H319) EyeIrrit.. 2(H335) STOTSE 3(H319) EyeIrrit.. 2(H335) STOTSE 3Not Hazardous Not Hazardous Not Hazardous Not Hazardous(H373) STOTRE 2(H373) STOTRE 2( H302) AcuteTox. 4( H302) AcuteTox. 4(H317) SkinSens. 1(H351) Carc.2(H372) STOTRE 1(H317) SkinSens. 1(H351) Carc.2(H372) STOTRE 1Not Hazardous Not HazardousS heet Hobart Brothers Co.Corr. 1B (H335) STOT SE 3 Corr. 1B (H335) STOT SE 3Important This section covers the materials of which the products manufactured. The fumes and gases produced during normal use of this product are covered in section 10. The term “Hazardous” in “Hazardous Material” should be interpreted as a term required and defined in OSHA Hazard Communication Standard 29CFR 1910-1200 and it does not necessarily imply the existence of hazard. The chemicals or compounds reportable by Section 313 of SARA are marked by the symbol #.___________________________________________________________________________________4. FIRST AID MEASURES:Inhalation: Remove to fresh air immediately or administer oxygen. Get medical attention immediately.Skin: Flush skin with large amounts of water. If irritation develops and persists, get medical attention.Eye: Flush eyes with water for at least 15 minutes. Get medical attention.Ingestion: Obtain medical attention immediately if ingested.Electric Shock: Disconnect and turn off the power. Use a nonconductive material to pull victim away from contact with live parts or wires. Immediately contact a physician.___________________________________________________________________________________5. FIRE-FIGHTING MEASURES:Suitable Extinguishing Media: Use water spray, alcohol-resistant foam, dry chemical or carbon dioxide. Welding arcs and sparks can ignite combustible and flammable materials. Use the extinguishing media recommended for the burning material and fire situation.Unsuitable Extinguishing Media:Do not use water on molten metal. Large fires may be flooded with water from a distance.Specific Hazards Arising From Chemical: Keep away from heat/spark/open flames/hot surfaces –No smoking. Hydrogen fluoride, Calcium oxide, Iron oxides, Carbon oxides, Strontium oxides, Manganese/manganese oxides, Barium oxide, Nickel/nickel oxides, Aluminum oxide, Sodium oxides, Silicon oxidesProtective Equipment: Fire fighters should wear complete protective clothing including self-contained breathing apparatus.___________________________________________________________________________________6. ACCIDENTAL RELEASE MEASURES:Personal Precautions: Refer to section 8.Environment Precautions: Refer to section 13.Cleaning Measures: Solid objects may be picked up and placed into a container. Liquids or pastes should be scooped up and placed into a container. Wear proper protective equipment while handling these materials. Do not discard as refuse.___________________________________________________________________________________7. HANDLING AND STORAGE:Precautions for Safe Handling: Handle with care to avoid stings or cuts. Wear gloves when handling welding consumables. Avoid exposure to dust. Do not ingest. Some individuals can develop an allergic reaction to certain materials. Retain all warning and identity labels.Conditions for Safe Storage: Store in dry place in closed packages. Keep separate from chemical substances like acids and strong bases, which could cause chemical reactions. Ground/Bond container and receiving equipment.___________________________________________________________________________________8. EXPOSURE CONTROLS/ PERSONAL PROTECTION:Engineering Controls:Avoid exposure to welding fumes, radiation, spatter, electric shock, heated materials and dust. Ensure sufficient ventilation, local exhaust, or both, to keep welding fumes and gases from breathing zone and general area. Keep work place and protective clothing clean and dry. Train welders to avoid contact with live electrical parts and insulate conductive parts. Check condition of protective clothing and equipment on a regular basis.Exposure limits: Use industrial hygiene equipment to ensure that exposure does not exceed applicable national exposure limits. The limits defined under section 3 can be used as guidance. Unless noted, all values are for 8 hour time weighted average. For information about welding fume analysis refer to section 10.Biological limits: No available dataPersonal protection:S heet Hobart Brothers Co. Respiratory protection: Use an air purifying dust respirator when welding or brazing in a confined space, or when local exhaust or ventilation is not sufficient to keep exposure values within safe limits.Hands protection: Wear appropriate gloves to prevent skin contact.EN 12477: Protection gloves for weldersType B gloves are recommended when high dexterity is required as for TIG welding, while type A gloves are recommended for other welding processes. The contact temp (ºC) is 100 and the threshold time (seconds) >15. Eyes protection:Welder’s helmet or face shield with colour absorbing lenses. Shield and filter to provide protection from harmful UV radiation, infra red and molten metal approved to standard EN379. Filter shade to be a minimum of shade 9.Skin protection: Heat-resistant protective clothing. Wear safety boots, apron, arm and shoulder protection. Keep protective clothing clean and dry. Clothing should be selected to suit the level, duration and purpose of the welding activity.S heet Hobart Brothers Co.9. PHYSICAL AND CHEMICAL PROPERTIES:Appearance:Solid.Color: Black 1144/ BlackOdour:OdourlessOdour Threshold: Not AvailablepH Value: Not AvailableMelting Point/Melting Range: >2300° F, >1300° CFreezing Point: Not AvailableBoiling Point/Boiling Range: Not AvailableFlash point: Not AvailableEvaporation Rate: Not AvailableSelf-in flammability:Not AvailableExplosion limits: Not AvailableVapour pressure: Not AvailableVapour density: Not AvailableDensity at 20ºC: Not AvailableRelative density: 6-9 g/cm3Solubility:Insoluble in water.Partition coefficient: Not AvailableAuto-ignition temperature: Not AvailableDecomposition temperature: Not AvailableOther Information:No available data.___________________________________________________________________________________10. STABILITY AND REACTIVITY:Chemical Stability: This product is stable under normal conditions.Hazardous Reactions: Contact with chemical substances like acids or strong bases cause generation of gas. Conditions to Avoid: Not applicable.Incompatible Materials: Reacts with acid.Hazardous Decomposition Products: When this product is used in a welding process, hazardous decomposition product would include those from volatilization, reaction or oxidation of the material listed in section 3 and those from the base metal and coating. The amount of fumes generated from this product varies with welding parameters and dimensions.Refer to applicable national exposure limits for fume compounds, including those exposure limits for fume compounds found in section 3. Reasonably expected gaseous products would include carbon oxides, nitrogen oxides and ozone. Air contaminants around the welding area can be affected by the welding process and influence the composition and quality of fumes and gases produced.S heet Hobart Brothers Co. ___________________________________________________________________________________11. TOXICOLOGICAL INFORMATION:Signs and Symptoms of Overexposure: Inhalation of welding fumes and gases can be dangerous to your health. Classification of welding fumes is difficult because of varying base materials, coatings, air contaminants and processes. The Internal Agency for Research on Cancer has classified welding fumes as possible carcinogenic to humans (Group 2B).Acute Effects: Overexposure to welding fumes may result in symptoms like metal fume fever, dizziness, nausea, dryness or irritation of the nose, throat or eyes. May cause sensitisation by skin contactChronic Effects:Overexposure to welding fumes may affect pulmonary function. Overexposure to manganese and manganese compounds above safe exposure limits can cause irreversible damage to the central nervous system, including the brain, symptoms of which may include slurred speech, lethargy, tremor, muscular weakness, psychological disturbances and spastic gait. Prolonged inhalation of nickel (Classified 2B by IARC and R by NTP) above safe exposure limits may cause cancer. Long term inhalation exposure to iron (oxide fume or dust) can cause siderosis.___________________________________________________________________________________12. ECOLOGICAL INFORMATION:Toxicity: Welding rods contain metals which are considered to be very toxic towards aquatic organisms. Finely divided welding rods are therefore considered harmful to aquatic organisms.Persistence and Degradability: The welding rods consist of elements that can not degrade any further in the environment.S heet Hobart Brothers Co. Bio accumulative Potential: Welding rods contain heavy metals which bio accumulates in the food chain. The following figures are the bio concentration factor (BCF) for the substances on their own.BCF:Manganese, BCF: 59052Nickel, BCF: 16Iron, BCF: 140000Mobility in Soil: Welding rods are not soluble in water or soil. Particles formed by working welding rods can be transported in the air.Other Adverse Effects: In massive form, welding rods present no hazards to the aquatic environment.Welding materials could degrade into components originating from the materials used in the welding process. Avoid exposure to conditions that could lead to accumulation in soils or groundwater. Harmful to aquatic organisms, may cause long-term adverse effects in the aquatic environment.___________________________________________________________________________________13. DISPOSAL CONSIDERATIONS:Product:For product elimination, consult recycling companies or appropriate local authority.USA RCRA: This product is not considered hazardous waste if discarded.Residue from welding consumables and processes could degrade and accumulate in soils and groundwater.Package:May be disposed in approved landfills provided local regulations are observed.___________________________________________________________________________________14. TRANSPORT INFORMATION:UN-number: Welding rods are not classified as dangerous goods for transport and has no UN number.UN proper shipping name: Welding rods are not classified as dangerous goods for transport and has no UN proper shipping name.Transport hazard class: Welding rods are not classified as dangerous goods for transport.Packing group: There are not any special precautions with which a user should or must comply or be aware of in connection with transport or conveyance either within or outside premises.Environmental hazards: Welding rods are not environmentally hazardous according to the criteria of the UN Model Regulations (as reflected in the IMDG Code, ADR, RID and AND) and/or a marine pollutant to the IMDG Code.Special precautions for users: There are not any special precautions which a user should or must comply or be aware of in connection with transport or conveyance either within or outside premises of the welding rod.Transport in Bulk According to Annex III MARPOL 73/78 and the IBC Code: Welding rods in massive form do not subject under MARPOL 73/78 and the IBC Code. Not applicable – product is transported only in packaged form.__________________________________________________________________________________15. REGULATORY INFORMATION:Safety, health and environment regulations/legislation specific for the substance or mixture: Read and understand the manufacturer’s instructions, your employer’s safety practices and the health and safety instructions on the label. Observe a ny federal and local regulations. Take precautions when welding and protect yourself and others.Warning: Welding fumes and gases are hazardous to your health and may damage lungs and other organs. Use adequate ventilation.Electric shock can kill. Arc rays and sparks can injure eyes and burn skin. Wear correct hand, head, eye and body protection.Chemical safety assessment: NoUSA: Under the OSHA Hazard Communication Standard, this product is considered hazardous. This product contains or produces a chemical known to the state of California to cause cancer and birth defects (or other reproductive harm). (California Health & Safety Code § 25249.5 et seq.) United States EPA Toxic Substance Control Act: All constituents of this product are on the TSCA inventory list or are excluded from listing.EPCRA/SARA Title III Toxic ChemicalsThe following metallic components are listed as SARA 313 “Toxic Chemicals” and potential subject to annual SARA reporting. See Section 3 for weight percentage.S heet Hobart Brothers Co.16. OTHER INFORMATION:The information in this document is believed to be correct as of the date issued. However, no warranty is expressed to be implied regarding the accuracy or completeness of this information. This information and product are furnished on the condition that the person receiving them shall make his own determinations as to the suitability of the product for his particular purpose and on the condition that he assumes the risk of his use thereof.This Material Safety Data Sheet complies with the EC directives 91/155/EEC and 93/112/EEC, including modifications 2001/58/EC.Complies with OSHA Communication Standard 29 CFR 1910.1200 and Superfund Amendments and Reauthorization Act (SARA) of 1986 Public Law 99-499Hazard Statements:H302 –Harmful if swallowed.H314– Causes severe skin burns and eye damage.H315 –Causes skin irritation.H317– May cause an allergic skin reaction.H319– Causes serious eye irritation.H335 –May cause respiratory irritation.H351– Suspected of causing lung cancer.H372– Causes damage to organs through prolonged or repeated exposure.H373– May cause damage to organs through prolonged or repeated exposure.R-Phrases:R22 –Harmful if swallowed.R34 –Causes burns.R36/37 –Irritating to eyes and respiratory system.R36/37/38 –Irritating to eyes, respiratory system and skin.R37 –Irritating to respiratory system.R40 –Limited evidence of a carcinogenic effect.R43 –May cause sensitization by skin contact.R48 –Danger of serious damage to health by prolonged.R48/23 –Toxic: danger of serious damage to health by prolonged exposure through inhalation and if swallowed.S-Phrases:S22 –Do not breathe dust.S24/25 –Avoid contact with skin and eyes.S26 –In case of contact with eyes, rinse immediately with plenty of water and seek medical advice.S28 –After contact with skin, wash immediately with plenty of water.S36/37/39 –Wear suitable protective clothing, gloves and eye/face protection.S43 –In case of fire, use fire-fighting equipment on basis class D.End of the document.。
Controlling the sensitivity of support vector machines

ber of real world problems such as handwritten charac-
ter and digit recognition Scholkopf, 1997; Cortes, 1995;
LeteCalu.,n1e9t9a7l].,a1n9d9s5p;eVaakperniikd,e1n9ti95c]a, tfiaocne
cients
i are found by
L = Xp
i=1
i
?
1 2
Xp
i;j=1
i
jyiyjK(xi; xj)
(1)
subject to constraints:
i0
Xp iyi = 0
(2)
i=1
Only those points which lie closest to the hyperplane
pdoeicnitssionxifumncatpiopningis
to targets formulated
yini
(i = terms
of these kernels:
f(x) = sign
Xp
!
iyiK(x; xi) + b
i=1
where b is the bias and the coe maximising the Lagrangian:
have In
thie>p0re(stehnecesuopfpnoortisve,ecttworos
). techniques
can
be
used
to allow for, and control, a trade o between training
蓝晓生物科技 Q Large Scale HP 层析介质说明书

Q Large Scale HP说明书1.产品介绍Q Large Scale HP层析介质是蓝晓科技自主研发的一种新型高度交联的琼脂糖层析介质,是将三甲胺基烷基季铵基团键合在小粒度高流速琼脂糖微球上形成的一种强阴离子交换介质,其具有高流速、高分辨率、高动态载量、良好的化学稳定性和机械性能,非特异性吸附低,回收率高,方便进行规模放大,可缩短生产时间,提高生产效率。
广泛用于生物制药和生物工程下游蛋白质、核酸及多肽的离子交换制备。
2.性能介绍产品牌号Q Large Scale HP外观白色球状,无臭无味种类强阴离子交换填料基质Large Scale HP微球配基三甲胺基烷基季铵基团形态氯型粒径d50v(μm)~36-44pH稳定性2~12(长期),2~14(短期,在位清洗[CIP])在以下液体中稳定:所有常用的水相缓冲液;1mol/L 氢氧化钠;化学稳定性8mol/L 尿素;6mol/L 盐酸胍;70% 乙醇;30%异丙醇;1M 醋酸动态载量,Q B,10% >50mgBSA /ml离子交换量(mmol /ml)0.15~0.18Cl-工作温度4~30℃耐热性121℃,水中30min流速*柱床高20cm,压力0.3MPa,流速大于220cm/h应用用于生物制药和生物工程下游蛋白质、核酸及多肽的离子交换层析纯化3.使用方法3.1 装柱装柱按照标准操作规程操作。
必须保证每种材料都处于工作温度,凝胶装柱前需要脱气。
3.2平衡使用2~5倍柱床体积的上样平衡液平衡柱子,务必使流出液的电导和pH同上样缓冲液的电导和pH完全一致。
平衡液是低浓度的缓冲溶液,如T ris、PBS等。
3.3上样(1)样品用平衡液配制,浑浊的样品要离心和过滤后上样。
盐浓度太大的样品处理后再配。
(2)一般情况是让目标产品结合在柱子上,用平衡液洗去杂质,再选择一种洗脱液洗下目标产品。
(3)介质对样品组分吸附的程度取决于样品的带电性质、流动相的离子强度和pH值。
物流英语专业术语
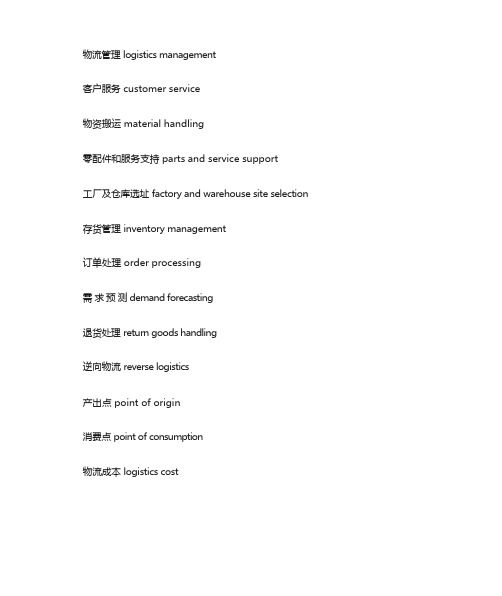
物流管理 logistics management客户服务 customer service物资搬运 material handling零配件和服务支持 parts and service support工厂及仓库选址 factory and warehouse site selection 存货管理 inventory management订单处理 order processing需求预测 demand forecasting退货处理 return goods handling逆向物流 reverse logistics产出点 point of origin消费点 point of consumption物流成本 logistics cost销售损失 lost sales退货处理成本 cost of return goods handling潜在的销售 potential sales运输成本 transportation cost进货渠道 inbound channel出货渠道 outbound channel订单处理成本 order processing cost需求预测 deman forecast销售沟通 distribution communications电子数据交换系统 electronic data interchange (EDI) 卫星数据传输 satellite data transmission条码 bar coding内部成本 internal cost外部成本 external cost订单传输 order transmittal订单输入 order entry批量成本 lot quantity cost缺货 stock-out库存成本 inventory carrying/ holding cost 资金成本 capital cost仓储空间成本 storage space cost风险成本 risk cost供应链 supply chain供应链管理 supply chain management核心能力 core competency人力资源 human resources供应链整合 supply chain integration 物资采购 material procurement最终用户 end customer货物流 product flow信息流 information flow上游供应商 upstream supplier下游供应商 downstream firm供应链战略 supply chain strategy多供应商 many suppliers strategy少数供应商战略 few suppliers strategy 纵向整合战略 vertical integration日式企业联合 keiretsu networks虚拟企业 virtual company前向整合 forward integration后向整合 backward integration规模经济 economy of scale成本降低 cost reduction产品移动 product movement在途库存 in-transit inventory有害物质 hazardous material远洋运输 Ocean going ships价格优势 price advantage门到门 d o o r-to-d o o r有效利用能源 energy-efficient灵活性和通用性 flexibility and versatility 建筑材料 building materials跨西伯利亚铁路 he Trans Siberian railway多式联运 multi-modal transport空箱 empty container拼箱 groupage container公铁运输 road-rail transportLASH: lighter abroad ship 子母船CFS: container freight station 集装箱货运站FCL: full container load 集装箱整箱货物LCL: less than c ontainer load 拼箱装TEU:twenty-foot equivalent units 标准箱工业中心 industrial center装货地 place of loading系统化运输 systematic transfe长距离运输 long distance movement资金周转 cash flow运输成本 transport cost现场仓库 field warehouse中间商 intermediary-consumer/user网络结构 network structure运输设施 transport vestment延期交货订单 back-orders分拨渠道 distribution channel库存周转 inventory turnover库存管理 inventory management存置成本 holding cost生产时间进度安排 production schedule按程序工作 work in process库存单位 stock keeping units前置期 lead time搬运成本 carrying cos t容量计划 capacity planning撤回 withdraw分类 assortment竞争武器 competitive weapon库存水平 inventory levels潜在的问题 potential problem物流活动 logistics activities最终顾客 ultimate customer信息技术 information technologies物流信息系统logistic information s ystem 实时销售信息real-time sales data决策相关信息 decision-relevant information 决策支持系统 decision support systems 长期预测 long-term forecast库存控制 inventory controllogistics information system通信标准 communication standard人工参与 human intervention采购订单 purchase orders贸易伙伴 trading partners数字网络 digital networks操作系统 operating systems资本投资 capital investment电子扫描 electronic scanning最终用户和销售伙伴end-use customers and reseller p artners. 替代程序 alternative program客户服务 customers service产品和价格信息 products and price information网上销售 on-line sales运营成本 operating cost前置期 lead time软件下载 download software复印成本 duplicate costs技术支持 technical support订单递交 order submission仓储操作 warehousing operation基本布局 basic layout按订单分拣 order pick储存区 storage area大批量运输 large quantity shipments办公管理 clerical/office administration装运检验 shipment content checking升降货车 lift truck运送路线 delivery route标识 marking产品编号 product number仓库管理系统 warehouse management system 订单要求 order requirement运输目的地 shipping destination 运输工具 transportation facilities 搬运信息 handling information 仓储设施 warehouse facility公共仓库 public warehousing自用仓库 private warehousing广告成本 advertising cost首笔投资 initial investment客户服务 customer service服务水平 service level竞争动力 competitive drive制造商 manufacturer经销商 distributor温控仓库 temperature-controlled warehouse进口税 imported duty罐装储存 tank storage易腐物品 perishable products农产品 agricultural products大宗散装存储产品 bulk storage products普通商品仓库 general commodity warehouse冷藏仓库 refrigerated warehouse特种商品仓库 special commodity warehouse保税仓库 bonded warehouse物资操作系统 materials handling system机械化操作系统 mechanized materials handling system 自动化操作系统 automated materials handling system信息导向操作系统 information-directed materials handling system 存储和订单处理设备storage and order picking equipment运输和分类设备 transportation and sorting equipment出货设备 shipping equipment自动导向车辆系统 automated guided vehicle systems(AGVS)计算机分类 computerized sortation活动货架 live rack高层自动化存取系统high-rise storage and retrieval systems射频波控制设备RF-controlled equipment光导向操作 light-directed operations订货拣选系统 order selection system。
航线理论考试(ATPL)最后复习笔记

航线理论考试(ATPL)最后复习笔记(1) 以下是在航线理论(ATPL)考试前最后复习阶段做的笔记,包括一些相关知识总结、难点、容易考到的原文等等。
由于是最后复习的笔记,所以覆盖面有限,另外多为总结性质的,所以没有按章节分类。
其中直接引用《The Aviation Theory Course for Airline Transport Pilot》(民航飞行学院那本英文的航线教材)中的原文或者从原文截取拼凑而成的句子,都以斜体标记。
一些重要名称以加粗标记,容易混淆和忽略信息用下划线标记。
该笔记主要面向航线考试,但与私商仪也有很多重合,可以参考复习。
FAA题的内容没有涉及。
1. RAIM: Receiver Autonomous Integrity Monitoring Without RAIM capability, the pilot has no assurance of accuracy of the GPS.也就是说,RAIM既影响位置信息,也影响高度信息。
2. If RAIM is not available:a) Another type of navigation and approaching system must be used;b) Another destination selected;c) Or, the trip delayed until RAIM is predicated to be available on arrival.3. VASI的种类和特点:VASI种类 Three-bar VASI Upwind for high cockpitTri-color VASI Red, green, whitePulsating VASI Below Pulsating redAbove Pulsating whiteon Standing white or alternatingred and white4. 指点标的一些属性:Marker Color Sound Rate Identified with theOM Blue Continuous dashes 2/s First 2 letters of the LLZIM White Continuous dashes 2/sMM amber Alternate dashes and dots6/s Last 2 letters of the LLZ 5. 油量要求:国内航线航程油量 国际航线航程油量备降油量(最远备降场) 备降油量等待油量(45分钟) 等待油量(1500ft等待30分钟)应急油量(航线飞行时间10%的油量)6. 着陆机场无边灯或机长无夜航最低天气标准,着陆时限为:平原:日落前10分钟;丘陵山区:日落前20分钟。
IATA AHM目录
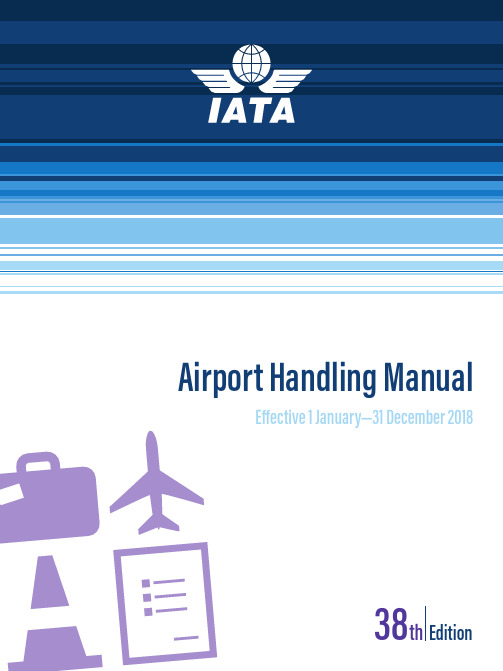
Airport Handling ManualEffective 1 January—31 December 201838NOTICEDISCLAIMER. The information contained in thispublication is subject to constant review in the lightof changing government requirements and regula-tions. No subscriber or other reader should act onthe basis of any such information without referringto applicable laws and regulations and/or withouttak ing appropriate professional advice. Althoughevery effort has been made to ensure accuracy, theInternational Air Transport Association shall not beheld responsible for any loss or damage caused byerrors, omissions, misprints or misinterpretation ofthe contents hereof. Furthermore, the InternationalAir Transport Association expressly disclaims anyand all liability to any person or entity, whether apurchaser of this publication or not, in respect ofanything done or omitted, and the consequencesof anything done or omitted, by any such person orentity in reliance on the contents of this publication.Opinions expressed in advertisements appearing inthis publication are the advertiser’s opinions and donot necessarily reflect those of IATA. The mentionof specific companies or products in advertisementdoes not imply that they are endorsed or recom-mended by IATA in preference to others of a simi-lar nature which are not mentioned or advertised.© International Air Transport Association. AllRights Reserved. No part of this publication maybe reproduced, recast, reformatted or trans-mitted in any form by any means, electronic ormechanical, including photocopying, record-ing or any information storage and retrieval sys-tem, without the prior written permission from:Senior Vice PresidentAirport, Passenger, Cargo and SecurityInternational Air Transport Association800 Place VictoriaP.O. Box 113Montreal, QuebecCANADA H4Z 1M1Airport Handling ManualMaterial No.: 9343-38ISBN 978-92-9229-505-9© 2017 International Air Transport Association. All rights reserved.TABLE OF CONTENTSPage Preface (xv)Introduction (xvii)General (1)AHM001Chapter0—Record of Revisions (1)AHM011Standard Classification and Numbering for Members Airport Handling Manuals (2)AHM012Office Function Designators for Airport Passenger and Baggage Handling (30)AHM020Guidelines for the Establishment of Airline Operators Committees (31)AHM021Guidelines for Establishing Aircraft Ground Times (34)AHM050Aircraft Emergency Procedures (35)AHM070E-Invoicing Standards (53)Chapter1—PASSENGER HANDLING (91)AHM100Chapter1—Record of Revisions (91)AHM110Involuntary Change of Carrier,Routing,Class or Type of Fare (92)AHM112Denied Boarding Compensation (98)AHM120Inadmissible Passengers and Deportees (99)AHM140Items Removed from a Passenger's Possession by Security Personnel (101)AHM141Hold Loading of Duty-Free Goods (102)AHM170Dangerous Goods in Passenger Baggage (103)AHM176Recommendations for the Handling of Passengers with Reduced Mobility(PRM) (105)AHM176A Acceptance and Carriage of Passengers with Reduced Mobility(PRM) (106)AHM180Carriage of Passengers with Communicable Diseases (114)AHM181General Guidelines for Passenger Agents in Case of SuspectedCommunicable Disease (115)Chapter2—BAGGAGE HANDLING (117)AHM200Chapter2—Record of Revisions (117)AHM210Local Baggage Committees (118)AHM211Airport Operating Rules (124)Airport Handling ManualPageChapter2—BAGGAGE HANDLING(continued)AHM212Interline Connecting Time Intervals—Passenger and Checked Baggage (126)AHM213Form of Interline Baggage Tags (128)AHM214Use of the10Digit Licence Plate (135)AHM215Found and Unclaimed Checked Baggage (136)AHM216On-Hand Baggage Summary Tag (138)AHM217Forwarding Mishandled Baggage (139)AHM218Dangerous Goods in Passengers'Baggage (141)AHM219Acceptance of Firearms and Other Weapons and Small Calibre Ammunition (142)AHM221Acceptance of Power Driven Wheelchairs or Other Battery Powered Mobility Aidsas Checked Baggage (143)AHM222Passenger/Baggage Reconciliation Procedures (144)AHM223Licence Plate Fallback Sortation Tags (151)AHM224Baggage Taken in Error (154)AHM225Baggage Irregularity Report (156)AHM226Tracing Unchecked Baggage and Handling Damage to Checked and UncheckedBaggage (159)AHM230Baggage Theft and Pilferage Prevention (161)AHM231Carriage of Carry-On Baggage (164)AHM232Handling of Security Removed Items (168)AHM240Baggage Codes for Identifying ULD Contents and/or Bulk-Loaded Baggage (169)Chapter3—CARGO/MAIL HANDLING (171)AHM300Chapter3—Record of Revisions (171)AHM310Preparation for Loading of Cargo (172)AHM311Securing of Load (174)AHM312Collection Sacks and Bags (177)AHM320Handling of Damaged Cargo (178)AHM321Handling of Pilfered Cargo (179)AHM322Handling Wet Cargo (180)AHM330Handling Perishable Cargo (182)AHM331Handling and Protection of Valuable Cargo (184)AHM332Handling and Stowage of Live Animals (188)AHM333Handling of Human Remains (190)Table of ContentsPageChapter3—CARGO/MAIL HANDLING(continued)AHM340Acceptance Standards for the Interchange of Transferred Unit Load Devices (191)AHM345Handling of Battery Operated Wheelchairs/Mobility AIDS as Checked Baggage (197)AHM350Mail Handling (199)AHM351Mail Documents (203)AHM353Handling of Found Mail (218)AHM354Handling of Damaged Mail (219)AHM355Mail Security (220)AHM356Mail Safety (221)AHM357Mail Irregularity Message (222)AHM360Company Mail (224)AHM380Aircraft Documents Stowage (225)AHM381Special Load—Notification to Captain(General) (226)AHM382Special Load—Notification to Captain(EDP Format and NOTOC Service) (231)AHM383Special Load—Notification to Captain(EDP NOTOC Summary) (243)AHM384NOTOC Message(NTM) (246)Chapter4—AIRCRAFT HANDLING AND LOADING (251)AHM400Chapter4—Record of Revisions (251)AHM411Provision and Carriage of Loading Accessories (252)AHM420Tagging of Unit Load Devices (253)AHM421Storage of Unit Load Devices (263)AHM422Control of Transferred Unit Load Devices (268)AHM423Unit Load Device Stock Check Message (273)AHM424Unit Load Device Control Message (275)AHM425Continued Airworthiness of Unit Load Devices (279)AHM426ULD Buildup and Breakdown (283)AHM427ULD Transportation (292)AHM430Operating of Aircraft Doors (295)AHM431Aircraft Ground Stability—Tipping (296)AHM440Potable Water Servicing (297)AHM441Aircraft Toilet Servicing (309)Airport Handling ManualPageChapter4—AIRCRAFT HANDLING AND LOADING(continued)AHM450Standardisation of Gravity Forces against which Load must be Restrained (310)AHM451Technical Malfunctions Limiting Load on Aircraft (311)AHM453Handling/Bulk Loading of Heavy Items (312)AHM454Handling and Loading of Big Overhang Items (313)AHM455Non CLS Restrained ULD (316)AHM460Guidelines for Turnround Plan (323)AHM462Safe Operating Practices in Aircraft Handling (324)AHM463Safety Considerations for Aircraft Movement Operations (337)AHM465Foreign Object Damage(FOD)Prevention Program (340)Chapter5—LOAD CONTROL (343)AHM500Chapter5—Record of Revisions (343)AHM501Terms and Definitions (345)AHM503Recommended Requirements for a New Departure Control System (351)AHM504Departure Control System Evaluation Checklist (356)AHM505Designation of Aircraft Holds,Compartments,Bays and Cabin (362)AHM510Handling/Load Information Codes to be Used on Traffic Documents and Messages (368)AHM513Aircraft Structural Loading Limitations (377)AHM514EDP Loading Instruction/Report (388)AHM515Manual Loading Instruction/Report (404)AHM516Manual Loadsheet (416)AHM517EDP Loadsheet (430)AHM518ACARS Transmitted Loadsheet (439)AHM519Balance Calculation Methods (446)AHM520Aircraft Equipped with a CG Targeting System (451)AHM530Weights for Passengers and Baggage (452)AHM531Procedure for Establishing Standard Weights for Passengers and Baggage (453)AHM533Passengers Occupying Crew Seats (459)AHM534Weight Control of Load (460)AHM536Equipment in Compartments Procedure (461)AHM537Ballast (466)Table of ContentsPageChapter5—LOAD CONTROL(continued)AHM540Aircraft Unit Load Device—Weight and Balance Control (467)AHM550Pilot in Command's Approval of the Loadsheet (468)AHM551Last Minute Changes on Loadsheet (469)AHM561Departure Control System,Carrier's Approval Procedures (471)AHM562Semi-Permanent Data Exchange Message(DEM) (473)AHM564Migration from AHM560to AHM565 (480)AHM565EDP Semi-Permanent Data Exchange for New Generation Departure Control Systems (500)AHM570Automated Information Exchange between Check-in and Load Control Systems (602)AHM571Passenger and Baggage Details for Weight and Balance Report(PWR) (608)AHM580Unit Load Device/Bulk Load Weight Statement (613)AHM581Unit Load Device/Bulk Load Weight Signal (615)AHM583Loadmessage (619)AHM587Container/Pallet Distribution Message (623)AHM588Statistical Load Summary (628)AHM590Load Control Procedures and Loading Supervision Responsibilities (631)AHM591Weight and Balance Load Control and Loading Supervision Training and Qualifications (635)Chapter6—MANAGEMENT AND SAFETY (641)AHM600Chapter6—Record of Revisions (641)AHM610Guidelines for a Safety Management System (642)AHM611Airside Personnel:Responsibilities,Training and Qualifications (657)AHM612Airside Performance Evaluation Program (664)AHM615Quality Management System (683)AHM616Human Factors Program (715)AHM619Guidelines for Producing Emergency Response Plan(s) (731)AHM620Guidelines for an Emergency Management System (733)AHM621Security Management (736)AHM633Guidelines for the Handling of Emergencies Requiring the Evacuation of an Aircraft During Ground Handling (743)AHM650Ramp Incident/Accident Reporting (745)AHM652Recommendations for Airside Safety Investigations (750)AHM660Carrier Guidelines for Calculating Aircraft Ground Accident Costs (759)Airport Handling ManualChapter7—AIRCRAFT MOVEMENT CONTROL (761)AHM700Chapter7—Record of Revisions (761)AHM710Standards for Message Formats (762)AHM711Standards for Message Corrections (764)AHM730Codes to be Used in Aircraft Movement and Diversion Messages (765)AHM731Enhanced Reporting on ATFM Delays by the Use of Sub Codes (771)AHM780Aircraft Movement Message (774)AHM781Aircraft Diversion Message (786)AHM782Fuel Monitoring Message (790)AHM783Request Information Message (795)AHM784Gate Message (797)AHM785Aircraft Initiated Movement Message(MVA) (802)AHM790Operational Aircraft Registration(OAR)Message (807)Chapter8—GROUND HANDLING AGREEMENTS (811)AHM800Chapter8—Record of Revisions (811)AHM801Introduction to and Comments on IATA Standard Ground Handling Agreement(SGHA) (812)AHM803Service Level Agreement Example (817)AHM810IATA Standard Ground Handling Agreement (828)AHM811Yellow Pages (871)AHM813Truck Handling (872)AHM815Standard Transportation Documents Service Main Agreement (873)AHM817Standard Training Agreement (887)AHM830Ground Handling Charge Note (891)AHM840Model Agreement for Electronic Data Interchange(EDI) (894)Chapter9—AIRPORT HANDLING GROUND SUPPORT EQUIPMENT SPECIFICATIONS (911)AHM900Chapter9—Record of Revisions (911)AHM901Functional Specifications (914)AHM904Aircraft Servicing Points and System Requirements (915)AIRBUS A300B2320-/B4/C4 (917)A300F4-600/-600C4 (920)A310–200/200C/300 (926)A318 (930)A319 (933)Table of ContentsPageChapter9—AIRPORT HANDLING GROUND SUPPORT EQUIPMENT SPECIFICATIONS(continued) AHM904Aircraft Doors,Servicing Points and System Requirements for the Use of Ground Support Equipment(continued)A320 (936)A321 (940)A330-200F (943)A330-300 (948)A340-200 (951)A340-300 (955)A340-500 (959)A340-600 (962)Airbus350900passenger (965)AIRBUS A380-800/-800F (996)ATR42100/200 (999)ATR72 (1000)AVRO RJ70 (1001)AVRO RJ85 (1002)AVRO RJ100 (1003)B727-200 (1004)B737–200/200C (1008)B737-300,400,-500 (1010)B737-400 (1013)B737-500 (1015)B737-600,-700,-700C (1017)B737-700 (1020)B737-800 (1022)B737-900 (1026)B747–100SF/200C/200F (1028)B747–400/400C (1030)B757–200 (1038)B757–300 (1040)Airport Handling ManualPageChapter9—AIRPORT HANDLING GROUND SUPPORT EQUIPMENT SPECIFICATIONS(continued) AHM904Aircraft Doors,Servicing Points and System Requirements for the Use of Ground Support Equipment(continued)B767—200/200ER (1041)B767—300/300ER (1044)B767—400ER (1048)B777–200/200LR (1051)B777–300/300ER (1055)Boeing787800passenger (1059)BAe ATP(J61) (1067)Bombardier CS100 (1068)Bombardier CS300 (1072)CL-65(CRJ100/200) (1076)DC8–40/50F SERIES (1077)DC8–61/61F (1079)DC8–62/62F (1081)DC8–63/63F (1083)DC9–15/21 (1085)DC9–32 (1086)DC9–41 (1087)DC9–51 (1088)DC10–10/10CF (1089)DC10–30/40,30/40CF (1091)EMBRAER EMB-135Regional Models (1092)EMBRAER EMB-145Regional Models (1094)Embraer170 (1096)Embraer175 (1098)Embraer190 (1100)Embraer195 (1102)FOKKER50(F27Mk050) (1104)FOKKER50(F27Mk0502) (1106)Chapter9—AIRPORT HANDLING GROUND SUPPORT EQUIPMENT SPECIFICATIONS(continued) AHM904Aircraft Doors,Servicing Points and System Requirements for the Use of Ground Support Equipment(continued)FOKKER70(F28Mk0070) (1108)FOKKER100(F28Mk0100) (1110)FOKKER100(F28Mk0100) (1112)IL-76T (1114)MD-11 (1116)MD–80SERIES (1118)SAAB2000 (1119)SAAB SF-340 (1120)TU-204 (1122)AHM905Reference Material for Civil Aircraft Ground Support Equipment (1125)AHM905A Cross Reference of IATA Documents with SAE,CEN,and ISO (1129)AHM909Summary of Unit Load Device Capacity and Dimensions (1131)AHM910Basic Requirements for Aircraft Ground Support Equipment (1132)AHM911Ground Support Equipment Requirements for Compatibility with Aircraft Unit Load Devices (1136)AHM912Standard Forklift Pockets Dimensions and Characteristics for Forkliftable General Support Equipment (1138)AHM913Basic Safety Requirements for Aircraft Ground Support Equipment (1140)AHM914Compatibility of Ground Support Equipment with Aircraft Types (1145)AHM915Standard Controls (1147)AHM916Basic Requirements for Towing Vehicle Interface(HITCH) (1161)AHM917Basic Minimum Preventive Maintenance Program/Schedule (1162)AHM920Functional Specification for Self-Propelled Telescopic Passenger Stairs (1164)AHM920A Functional Specification for Towed Passenger Stairs (1167)AHM921Functional Specification for Boarding/De-Boarding Vehicle for Passengers withReduced Mobility(PRM) (1169)AHM922Basic Requirements for Passenger Boarding Bridge Aircraft Interface (1174)AHM923Functional Specification for Elevating Passenger Transfer Vehicle (1180)AHM924Functional Specification for Heavy Item Lift Platform (1183)AHM925Functional Specification for a Self-Propelled Conveyor-Belt Loader (1184)AHM925A Functional Specification for a Self-Propelled Ground Based in-Plane LoadingSystem for Bulk Cargo (1187)Chapter9—AIRPORT HANDLING GROUND SUPPORT EQUIPMENT SPECIFICATIONS(continued) AHM925B Functional Specification for a Towed Conveyor-Belt Loader (1190)AHM926Functional Specification for Upper Deck Catering Vehicle (1193)AHM927Functional Specification for Main Deck Catering Vehicle (1197)AHM930Functional Specification for an Upper Deck Container/Pallet Loader (1201)AHM931Functional Specification for Lower Deck Container/Pallet Loader (1203)AHM932Functional Specification for a Main Deck Container/Pallet Loader (1206)AHM933Functional Specification of a Powered Extension Platform to Lower Deck/Container/ Pallet Loader (1209)AHM934Functional Specification for a Narrow Body Lower Deck Single Platform Loader (1211)AHM934A Functional Specification for a Single Platform Slave Loader Bed for Lower DeckLoading Operations (1213)AHM936Functional Specification for a Container Loader Transporter (1215)AHM938Functional Specification for a Large Capacity Freighter and Combi Aircraft TailStanchion (1218)AHM939Functional Specification for a Transfer Platform Lift (1220)AHM941Functional Specification for Equipment Used for Establishing the Weight of aULD/BULK Load (1222)AHM942Functional Specification for Storage Equipment Used for Unit Load Devices (1224)AHM950Functional Specification for an Airport Passenger Bus (1225)AHM951Functional Specification for a Crew Transportation Vehicle (1227)AHM953Functional Specifications for a Valuable Cargo Vehicle (1229)AHM954Functional Specification for an Aircraft Washing Machine (1230)AHM955Functional Specification for an Aircraft Nose Gear Towbar Tractor (1232)AHM956Functional Specification for Main Gear Towbarless Tractor (1235)AHM957Functional Specification for Nose Gear Towbarless Tractor (1237)AHM958Functional Specification for an Aircraft Towbar (1240)AHM960Functional Specification for Unit Load Device Transport Vehicle (1242)AHM961Functional Specification for a Roller System for Unit Load Device Transportation on Trucks (1245)AHM962Functional Specification for a Rollerised Platform for the Transportation of Twenty Foot Unit Load Devices that Interfaces with Trucks Equipped to Accept Freight ContainersComplying with ISO668:1988 (1247)AHM963Functional Specification for a Baggage/Cargo Cart (1249)AHM965Functional Specification for a Lower Deck Container Turntable Dolly (1250)AHM966Functional Specification for a Pallet Dolly (1252)Chapter9—AIRPORT HANDLING GROUND SUPPORT EQUIPMENT SPECIFICATIONS(continued) AHM967Functional Specification for a Twenty Foot Unit Load Device Dolly (1254)AHM968Functional Specification for Ramp Equipment Tractors (1256)AHM969Functional Specification for a Pallet/Container Transporter (1257)AHM970Functional Specification for a Self-Propelled Potable Water Vehicle with Rear orFront Servicing (1259)AHM971Functional Specification for a Self-Propelled Lavatory Service Vehicle with Rear orFront Servicing (1262)AHM972Functional Specifications for a Ground Power Unit for Aircraft Electrical System (1265)AHM973Functional Specification for a Towed Aircraft Ground Heater (1269)AHM974Functional Specification for Aircraft Air Conditioning(Cooling)Unit (1272)AHM975Functional Specifications for Self-Propelled Aircraft De-Icing/Anti-Icing Unit (1274)AHM976Functional Specifications for an Air Start Unit (1278)AHM977Functional Specification for a Towed De-Icing/Anti-Icing Unit (1280)AHM978Functional Specification for a Towed Lavatory Service Cart (1283)AHM979Functional Specification for a Towed Boarding/De-Boarding Device for Passengers with Reduced Mobility(PRM)for Commuter-Type Aircraft (1285)AHM980Functional Specification for a Self-Propelled Petrol/Diesel Refueling Vehicle forGround Support Equipment (1287)AHM981Functional Specification for a Towed Potable Water Service Cart (1289)AHM990Guidelines for Preventative Maintenance of Aircraft Towbars (1291)AHM994Criteria for Consideration of the Investment in Ground Support Equipment (1292)AHM995Basic Unit Load Device Handling System Requirements (1296)AHM997Functional Specification for Sub-Freezing Aircraft Air Conditioning Unit (1298)Chapter10—ENVIRONMENTAL SPECIFICATIONS FOR GROUND HANDLING OPERATIONS (1301)AHM1000Chapter10—Record of Revisions (1301)AHM1001Environmental Specifications for Ground Handling Operations (1302)AHM1002Environmental Impact on the Use of Ground Support Equipment (1303)AHM1003GSE Environmental Quality Audit (1305)AHM1004Guidelines for Calculating GSE Exhaust Emissions (1307)AHM1005Guidelines for an Environmental Management System (1308)Chapter11—GROUND OPERATIONS TRAINING PROGRAM (1311)AHM1100Chapter11—Record of Revisions (1311)AHM1110Ground Operations Training Program (1312)Appendix A—References (1347)Appendix B—Glossary (1379)Alphabetical List of AHM Titles (1387)IATA Strategic Partners..............................................................................................................................SP–1。
毕业设计论文外文文献翻译泄压阀的最低要求中英文对照
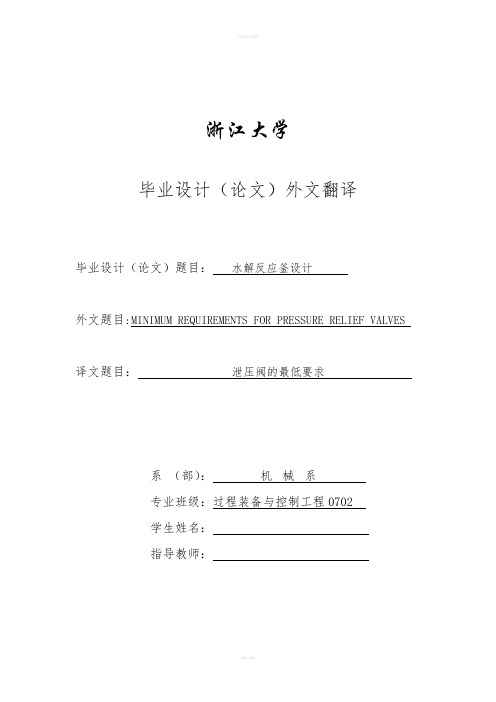
浙江大学毕业设计(论文)外文翻译毕业设计(论文)题目:水解反应釜设计外文题目:MINIMUM REQUIREMENTS FOR PRESSURE RELIEF VALVES 译文题目:泄压阀的最低要求系(部):机械系专业班级:过程装备与控制工程0702学生姓名:指导教师:指导教师评阅意见MINIMUM REQUIREMENTS FORPRESSURE RELIEF VALVESUG-136(a) Mechanical RequirementsUG-136(a) (1) the design shall incorporate guiding arrangements necessary to ensure consistent operation and tightness.UG-136(a) (2) The spring shall be designed so that the full lift spring compression shall be no greater than 80% of the nominal solid defection. The permanent set of the spring (defined as the difference between the freeheight and height measured 10 min after the spring has been compressed solid three additional times after presetting at room temperature) shall not exceed 0.5% of the free height.UG-136(a)(3) Each pressure relief valve on air, water over 140°F (60°C), or steam service shall have a substantial lifting device, which when activated will release the seating force on the disk when the pressure Relief valve is subjected to a pressure of at least 75% of the set pressure of the valve. Pilot operated pressure relief valves used on these services shall be provided with either a lifting device as described above or means for connecting and applying pressure to the pilot adequate to verify that the moving parts critical to proper operation are free to move.UG-136(a) (4) the seat of a pressure relief valve shall be fastened to the body of the pressure relief valve in such a way that there is no possibility of the seat lifting.UG-136(a) (5) in the design of the body of the pressure relief valve, consideration shall be given to minimizing the effects of deposits.UG-136(a) (6) Pressure relief valves having screwed inlet or outlet connections shall be provided with wrenching surfaces to allow for normal installation without damaging operating parts.UG-136(a) (7) Means shall be provided in the design of all pressure relief valves for use under this Division for sealing all initial adjustments which can be made without disassembly of the valve. Seals shall be installed by the Manufacturer or Assembler at the time of initial adjustment. Seals shall be installed in a manner to prevent changing the adjustment without breaking the seal. For pressure relief valves largerThan NPS 1|2 (DN 15), the seal shall serve as a means of identifying the Manufacturer Or Assembler making the initial adjustment.UG-136(a) (8) If the design of a pressure relief valve is such that liquid can collect on the discharge side of the disk, except as permitted in (a)(9) below, the valve shall be equipped with a drain at the lowest point where liquid can collect (for installation, see UG-135).UG-136(a) (9) Pressure relief valves that cannot be equipped with a drain as required in (a) (8) above because of design or application may be used provided:(a) The pressure relief valves are used only on gas service where there is neither liquid discharged from the valve nor liquid formed by condensation on the discharge side of the valve; and(b) the pressure relief valves are provided with a cover or discharge piping per UG-135(f) to prevent liquid or other contaminant from entering the discharge side of the valve; and(c) The pressure relief valve is marked FOR GAS SERVICE ONLY in addition to the requirements of UG-129.UG-136(a) (10) for pressure relief valves of the diaphragm type, the space above the diaphragm shall be vented to prevent a buildup of pressure above the diaphragm. Pressure relief valves of the diaphragm type shall be designed so that failure or deterioration of the diaphragm material will not impair the ability of the valve to relieve at the rated capacity. UG-136(b) Material SelectionsUG-136(b) (1) Cast iron seats and disks are not permitted.UG-136(b) (2) Adjacent sliding surfaces such as guides and disks or disk holders shall both be of corrosion resistant material. Springs of corrosion resistant material or having a corrosion resistant coating are required. The seats and disks of pressure relief valves shall be of suitable material to resist corrosion by the fluid to be contained. NOTE: The degree of corrosion resistance, appropriate to the intended service, shall be a matter of agreement between the manufacturer andThe purchaser.UG-136(b)(3) Materials used in bodies and bonnets or yokes shall be listed in Section II and this Division.Carbon and low alloy steel bodies, bonnets, yokes and bolting (UG-20) subject to in-service temperatures colder than −20°F(−30°C) shall meet the requirements of UCS-66, unless exempted by the following.(a) The coincident ratio defined in Fig. UCS-66.1 is 0.35 or less.(b) The material(s) is exempted from impact testing per Fig. UCS-66. UG-136(b) (4) Materials used in nozzles, disks, and other parts contained within the external structure of the pressure relief valves shall be one of the following categories:(a) Listed in Section II;(b) listed in ASTM specifications;(c) Controlled by the Manufacturer of the pressure relief valve by a specification ensuring control of chemical and physical properties and quality at least equivalent to ASTM standards.UG-136(c) Inspection of Manufacturing and/or Assembly of Pressure Relief ValvesUG-136(c)(1) A Manufacturer or Assembler shall demonstrate to the satisfaction of a representative from an ASME designated organization that his manufacturing, production, and testing facilities and quality control procedures will insure close agreement between the performance of random production samples and the performance of those valves submitted for Capacity Certification.UG-136(c) (2) Manufacturing, assembly, inspection, and test operations including capacity are subject to inspections at any time by a representative from an ASME designated organization.UG-136(c) (3) A Manufacturer or Assembler may be granted permission to apply the UV Code Symbol to production pressure relief valves capacity certified in accordance with UG-131 provided the following tests are Successfully completed. This permission shall expire on the fifth anniversary of the date it is initially granted. The permission may be extended for 5 year periods if the following tests are successfully repeated within the 6-month period before expiration.(a) Two sample production pressure relief valves of a size and capacity within the capability of an ASME accepted laboratory shall be selected by a representative from an ASME designated organization.(b) Operational and capacity tests shall be conducted in the presence of a representative from an ASME designated organization at an ASME accepted laboratory. The pressure relief valve Manufacturer or Assembler shall be noticed of the time of the test and may have representatives present to witness the test. Pressure relief valves having an adjustable blow down construction shall be adjusted by the Manufacturer or Assembler following successful testing for operation but prior to flow testing so that the blow down does not exceed 7% of the set pressure or 3 psi (20 kPa), whichever is greater. This adjustment may be made on the flow test facility.(c) Should any pressure relief valve fail to relieve at or above its certified capacity or should it fail to meet performance requirements of this Division, the test shall be repeated at the rate of two replacement pressure relief valves, selected in accordance with (c)(3)(a) above, for Each pressure relief valve that failed.(d) Failure of any of the replacement pressure relief valves to meet the capacity or the performance requirements of this Division shall be cause for revocation within 60 days of the authorization to use the Code Symbol on that particular type of pressure relief valve. During this period, the Manufacturer or Assembler shall demonstrate the cause of such decadency and the action taken to guard against future occurrence, and the requirements of (c) (3) above shall apply.UG-136(c) (4) Use of the Code Symbol Stamp by an Assembler indicates the use of original, unnoticed parts in strict accordance with the instructions of the Manufacturer of the pressure relief valve.(a) An assembler may transfer original and unnoticed pressure relief parts produced by the Manufacturer to other Assemblers provided the following conditions are met:(1) Both Assemblers have been granted permission to apply the V or UV Code Symbol to the specifi c valve type in which the parts are to be used;(2) The Quality Control System of the Assembler receiving the pressure relief valve parts shall define the controls for the procurement and acceptance of those parts; and(3) The pressure relief valve parts are appropriately packaged, marked, or sealed by the Manufacturer to ensure that the parts are:(a) Produced by the Manufacturer; and(b) The parts are original and unnoticed. However, an Assembler may convert original finished parts by machining to another finished part fora specifi c application under the following conditions:(1) Conversions shall be specified by the Manufacturer. Drawings and/or written instructions used for part conversion shall be obtained from the Manufacturer and shall include a drawing or description of the converted Part before and after machining.(2) The Assembler’s quality control system, as accepted by a representative from an ASME designated organization, must describe in detail the conversion of original parts, provisions for inspection and acceptance, personnel training, and control of current Manufacturer’s Drawings and/or written instructions.(3) The Assembler must document each use of a converted part and that the part was used in strict accordance with the instructions of the Manufacturer.(4) The Assembler must demonstrate to the Manufacturer the ability to perform each type of conversion. The Manufacturer shall document all authorizations granted to perform part conversions. The Manufacturer And Assembler shall maintain a file of such authorizations.(5) At least annually a review shall be performed by the Manufacturer of an Assembler’s system and machining capabilities. The Manufacturer shall document the results of these reviews. A copy of this documentation shall be kept onfile by the Assembler. The review results shall be made available to a representative from an ASME designated organization.UG-136(c) (5) In addition to the requirements of UG-129, the marking shall include the name of the Manufacturer and the finalAssembler. The Code Symbol Stamp shall be that of the final Assembler.NOTE: Within the requirements of UG-136(c) and (d): A Manufacturer is defined as a person or organization who is completely responsible for design, material selection, capacity cortication, manufacture of all component parts, assembly, testing, sealing, and shipping of pressure relief valves credited under this Division. An Assembler is defined as a person or organization who purchases or receives from a Manufacturer or another Assembler the necessary component parts or pressure relief valves and assembles, adjusts, tests, seals, and ships pressure relief valves credited under this Division, at a geographical location other than and using facilities other than those used by the Manufacturer. An Assembler may be organizationally independent of a Manufacturer or may be wholly or partly owned by a Manufacturer.UG-136(d) Production Testing by Manufacturers and Assemblers UG-136(d) (1) each pressure relief valve to which the Code Symbol Stamp is to be applied shall be subjected to the following tests by the Manufacturer or Assembler. A Manufacturer or Assembler shall have a documented program for the application, calibration, and maintenance Of gages and instruments used during these tests.UG-136(d)(2) The primary pressure parts of each pressure relief valve exceeding NPS 1 (DN 25) inlet size or 300 psi (2100 MPa) set pressure where the materials used are either cast or welded shall be tested at a pressure Of at least 1.5 times the design pressure of the parts. These tests shall be conducted after all machining operations on the parts have been completed. There shall be no visible sign of leakage.UG-136(d) (3) the secondary pressure zone of each closed bonnet pressure relief valve exceeding NPS 1 (DN 25) inlet size when such pressure relief valves are designed for discharge to a closed system shall be tested With air or other gas at a pressure of at least 30 psi (200 kPa). There shall be no visible sign of leakage.UG-136(d) (4) each pressure relief valve shall be tested to demonstrate its popping or set pressure. Pressure relief valves marked for steam service or having special internal parts for steam service shall be tested with steam, except that pressure relief valves beyond the capability Of the production steam test facility either because of size or set pressure may be tested on air. Necessary corrections for differentials in popping pressure between steam and air shall be established by the Manufacturer and applied to the popping point on air. Pressure relief valves marked for gas or vapor may be tested with air. Pressure relief Valves marked for liquid service shall be tested with water or other suitable liquid. When a valve is adjusted to correct for service conditions of superimposed back pressure, temperature, or the differential in popping pressure between steam and air, the actual test pressure (cold differential test pressure) shall be marked on the valve perUG-129. Test fixtures and test drums where applicable shall be of adequate size and capacity to ensure that pressure relief valve action is consistent with the stamped set pressure within the tolerances required by UG-134(d).UG-136(d) (5) after completion of the tests required by (d) (4) above, a seat tightness test shall be conducted. Unless otherwise designated by a Manufacturer’s published pressure relief valve specification or another specification agreed to by the user, the seat tightness test and acceptance criteria shall be in accordance with API 527.UG-136(d) (6) Testing time on steam pressure relief valves shall be sufficient, depending on size and design, to insure that test results are repeatable and representative of held performance.UG-136(e) Design Requirements.At the time of the submission of pressure relief valves for capacity cortication, or testing in accordance with (c) (3) above, the ASME designated organization has the authority to Review the design for conformity with the requirements of UG-136(a) and UG-136(b) and to reject or require medication of designs which do not conform, prior to capacity testing.UG-136(f) Welding and Other Requirements.All welding, brazing, heat treatment, and nondestructive examination used in the construction of bodies, bonnets, and yokes shall be performed in accordance with the Applicable requirements of this Division. Selections from:ASME BOILER AND PRESSURE VESSEL CODE AN INTERNATIONAL CODE泄压阀的最低要求UG(a)136机械需求UG 136(a)(1)设计应纳入指导和进行必要安排以确保一致的行动和密封性。
USP 干燥失重法中英文对照

<731>LOSS ON DRYINGThe procedure set forth in this chapter determines the amount of volatile matter of any kind that is driven off under the conditions specified.For substances appearing to contain water as the only volatile constituent, the procedure given in the chapter,Water Determination921,is appropriate,and is specified in the individual monograph.Mix and accurately weigh the substance to be tested,and,unless otherwise directed in the individual monograph,conduct the determination on1to 2g.If the test specimen is in the form of large crystals,reduce the particle size to about2mm by quickly crushing.Tare a glass-stoppered, shallow weighing bottle that has been dried for30minutes under the same conditions to be employed in the determination.Put the test specimen in the bottle,replace the cover,and accurately weigh the bottle and the contents.By gentle,sidewise shaking,distribute the test specimen as evenly as practicable to a depth of about5mm generally,and not more than10mm in the case of bulky materials.Place the loaded bottle in the drying chamber,removing the stopper and leaving it also in the chamber. Dry the test specimen at the temperature and for the time specified in the monograph.[NOTE—The temperature specified in the monograph is to be regarded as being within the range of±2of the stated figure.]Upon opening the chamber,close the bottle promptly,and allow it to come to room temperature in a desiccator before weighing.If the substance melts at a lower temperature than that specified for the determination of Loss on drying,maintain the bottle with its contents for1to2hours at a temperature5to10below the melting temperature, then dry at the specified temperature.Where the specimen under test is Capsules,use a portion of the mixed contents of not fewer than4capsules.Where the specimen under test is Tablets,use powder from not fewer than 4tablets ground to a fine powder.Where the individual monograph directs that loss on drying be determined by thermogravimetric analysis,a sensitive electrobalance is to be used.Where drying in vacuum over a desiccant is directed in the individual monograph,a vacuum desiccator or a vacuum drying pistol,or other suitable vacuum drying apparatus,is to be used.Where drying in a desiccator is specified,exercise particular care to ensure that the desiccant is kept fully effective by frequent replacement.Where drying in a capillary-stoppered bottle*in vacuum is directed in the individual monograph,use a bottle or tube fitted with a stopper having a225±25µm diameter capillary,and maintain the heating chamber at a pressure of5mm or less of mercury.At the end of the heating period, admit dry air to the heating chamber,remove the bottle,and with the capillary stopper still in place allow it to cool in a desiccator before weighing.本章中给出的方法阐述了在特定的条件下物质中的挥发性成分的测定。
- 1、下载文档前请自行甄别文档内容的完整性,平台不提供额外的编辑、内容补充、找答案等附加服务。
- 2、"仅部分预览"的文档,不可在线预览部分如存在完整性等问题,可反馈申请退款(可完整预览的文档不适用该条件!)。
- 3、如文档侵犯您的权益,请联系客服反馈,我们会尽快为您处理(人工客服工作时间:9:00-18:30)。
Project Name 项目名称:Contractor 施工单位:
Date 检查时间:Pass
合格Fail 不合格
1
Rigging &Lifting Plan/MS 吊装方案1、If L&R MS is available 起重吊装作业方案2、If L&R MS has been formally approved or not 作业方案是否经审批2Crane
起重机
1、Safety pin on the lifting hook 吊钩保险装置
2、Qualification of crane 起重机是否取得准用证
3、All safety devices 各种安全装置3Slings
吊索具
1、Wire rope 吊装用钢丝绳
2、Safety coefficient of sling(>6) 钢丝绳及索具安全系数是否大于6倍
3、Effective protection on sharp surface 捆绑时锐利部位有有效保护
4、Correct use of sling 正确使用吊索4Technical Hand-over
Meeting before
operation.
吊装方案技术交底
1、If L&R oeperation team have attended the technical hand-over meeting for that L&R operation and if there is complete record.吊装操作人员是否接受过吊装方案技术交底,记录是否齐全。
5Hanging point
吊点
1、Correct lifting point 正确的吊点6Working crew
吊装操作人员
1、Qualification 吊装操作人员资质
2、Dedicated crane operator 指定吊车操作手
3、PPE (including seat belt) 是否按规定穿戴防护用品(包括座椅安全带)7Ground condition
地面状况1、Ground condition (complying with MS or crane instruction?) 起重机作业地面状况(是否符合作业方案要求或起重机说明书要求?)
2、Pads under outrigger 支腿垫护措施
8Overload operation 超负荷作业1、Whether lifting weight is specified and correct
被吊物体重量是否明确
2、If belongs to overload operation or not
是否属于超载作业
3、Whether have a trial test before every operation
每次作业前是否经试吊检验
9Work at heights 高空作业1、Proper fall protection for WAH 高空作业防坠措施
2、Proper working platform 合适的工作平台
10
Signal communication 信号传递Proper and effective signal communication 正确有效的信号传递措施11
Material stacking 吊物堆放Orderliness and stability 整齐及稳定性12Working area isolation
作业区域隔离
1、Proper barricading and clear sign 正确隔离围护和醒目警示标识
2、Dedicated L&R supervisor 专人警戒13
Operation environment
作业环境
Any particular risks that need special control measures or method statement: overhead lines, poor foundation, crane movement with load, crosswork. …. 是否有任何特殊的风险需要特别的控制措施或施工方案,比如高架线,地基不牢固,吊车载物行走,交叉作业等。
Note :L&R operation is forbidden to start-up once any items of the above failed to pass inspection.注:如果所有项目中有一项检查不合格,将不允许进行吊装作业。
Inspected by 检查人Inspection Item 检查项目 Pre-lift Check List (For Hazardous/Large-scale Lifts )
起重吊装前安全检查表 (针对危险性/大型吊装)
No .
序号Inspection Content 检查内容Result 检查结果Name of Contractor Safety representative 承包商安全代表Signature
签名1 of 1。